Katmanlı Üretim için Paslanmaz Çelik Tozları
İçindekiler
Paslanmaz çelik tozları geleneksel metal üretimiyle kıyaslanamayacak katkı tekniklerini kullanarak karmaşık geometrilerin basılmasını sağlar. Bu kılavuz, paslanmaz toz tedarikini bilgilendirmek için alaşım varyantlarını, partikül özelliklerini, özellik verilerini, fiyatlandırma içgörülerini ve karşılaştırmaları kapsar.
Paslanmaz Çelik Tozlarına Giriş
Paslanmaz çelik tozlarının sunduğu temel özellikler:
- Karmaşık, hafif bileşenlerin imalatı
- Üstün korozyon direnci elde edin
- Hızlı prototip oluşturma ve özelleştirme olanağı
Kullanılan yaygın alaşımlar şunlardır:
- 304L - Mükemmel korozyon direnci ile uygun maliyetli
- 316L - Molibden ilavesi ile üstün korozyon direnci
- 17-4PH - Yüksek mukavemetli, en sert paslanmaz toz
Bu kılavuzda paslanmaz tozların seçiminde dikkat edilmesi gereken hususlar yer almaktadır:
- Alaşım Bileşimleri ve Üretim Yöntemleri
- Mekanik Özellikler Test Verileri
- Partikül Boyutu Dağılımı Tavsiyeleri
- Morfoloji, Akış Hızı ve Görünür Yoğunluk
- Hacimlere Göre Tedarikçi Fiyat Aralıkları
- Korozyon Direnci Karşılaştırmaları
- Katı Çubuk Stoğa Göre Artıları ve Eksileri
- Baskı Parametresi Optimizasyonu Hakkında SSS
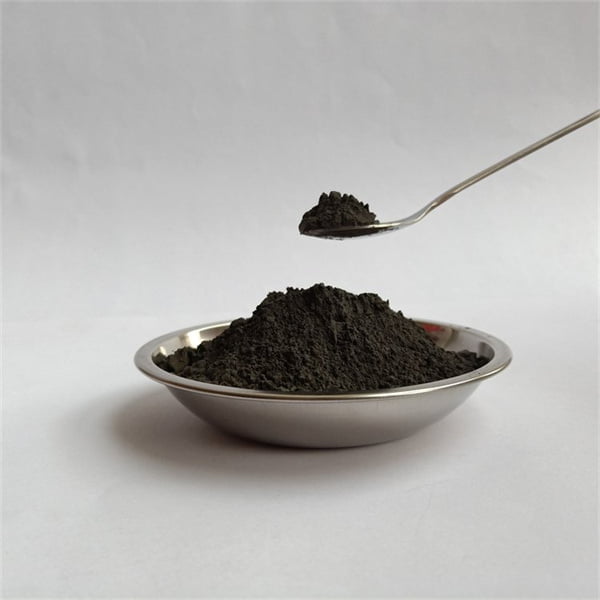
Paslanmaz Çelik Toz Bileşimleri
Tablo 1 paslanmaz çelik toz alaşım bileşimlerini, toz üreticileri arasında bazı farklılıklar gösteren birincil element ilavelerine göre göstermektedir:
Alaşım | Başlıca Alaşım Elementleri |
---|---|
304L | Cr, Ni |
316L | Cr, Ni, Mo |
17-4PH | Cr, Ni, Cu |
Karbür çökelmesini önlemek ve korozyon direnci ile kaynaklanabilirliği korumak için 304L ve 316L'de karbon sınırlandırılmıştır (≤0,03%).
17-4PH'deki daha yüksek karbon, martensitik sertleştirme ısıl işlemleri yoluyla mukavemeti artırır.
Mekanik Özellikler ve Test Yöntemleri
Mülkiyet | Açıklama | Test Yöntemi (Standart) | Katmanlı Üretim (AM) için Önemi |
---|---|---|---|
Görünür Yoğunluk | Gevşek, sıkıştırılmamış haliyle birim hacim başına toz kütlesi | ASTM B922 | AM süreçlerinde toz akışkanlığını ve kullanım kolaylığını etkiler |
Akışkanlık | Toz partiküllerinin yerçekimi altında akma kolaylığı | ASTM B2132 | AM yapılarında paketleme yoğunluğunu ve toz tabakası homojenliğini etkiler |
Musluk Yoğunluğu | Standartlaştırılmış bir kılavuz çekme rutininden sonra toz yoğunluğu | ASTM B854 | Toz paketleme verimliliğinin temel bir değerlendirmesini sağlar |
Yeşil Yoğunluk | Sinterleme öncesi sıkıştırılmış toz kütlesinin yoğunluğu | ASTM B970 | AM parçalarının nihai yoğunluğu ve boyutsal doğruluğu üzerine влияет (vliyaniyet) (influyats na final'nuyu plotnost' i razmernuyu tochnost' detaley AM) |
Sinterlenmiş Yoğunluk | Sinterleme sonrası toz kütlesinin yoğunluğu | ASTM B962 | AM parçalarında istenen mekanik özellikleri ve korozyon direncini elde etmek için kritik |
Parçacık Boyutu Dağılımı | Bir toz popülasyonunda bulunan boyut aralığı | ASTM B822 | Toz akışkanlığını, paketleme davranışını ve AM parçalarının nihai mikroyapısını etkiler |
Parçacık Şekli | Toz partiküllerinin morfolojik özellikleri (küresel, açısal vb.) | Taramalı Elektron Mikroskobu (SEM) | влияет (vliyaniyet) on packing density, inter-particle bonding, and flowability (influyats na plotnost' upakovki, mezhchastichnoe svyazyvanie i tekuchest') |
Yüzey Pürüzlülüğü | Bir toz parçacığının yüzeyindeki mikroskobik değişimler | Atomik Kuvvet Mikroskopisi (AFM) | Parçacıklar arası bağlanmayı ve sinterleme davranışını etkileyebilir |
Kimyasal Bileşim | Toz malzemenin elementel yapısı | X-Işını Floresansı (XRF) | Nihai malzeme özelliklerini, korozyon direncini ve belirli uygulamalar için uygunluğu belirler |
Çekme Dayanımı | Bir toz metalurjisi (PM) numunesinin ayrılmadan önce dayanabileceği maksimum gerilim | ASTM E8 | Yüksek yük taşıma kapasitesi gerektiren uygulamalar için çok önemlidir |
Akma Dayanımı | Bir PM numunesinin plastik deformasyon sergilediği gerilim seviyesi | ASTM E8 | Malzemenin elastik limitini anlamak ve kalıcı deformasyonu tahmin etmek için önemlidir |
Uzama | Bir PM numunesinin çekme testinde kırılmadan önce yaşadığı uzunluktaki yüzde artış | ASTM E8 | Malzemenin sünekliğini ve kırılmadan deforme olma kabiliyetini gösterir |
Basınç Dayanımı | Bir PM numunesinin basınç yükü altında ezilmeden önce dayanabileceği maksimum gerilim | ASTM E9 | Sıkıştırma kuvvetlerine maruz kalan uygulamalar için gereklidir |
Sertlik | Bir malzemenin daha sert bir nesne tarafından çentiklenmeye karşı direnci | ASTM E384 | Aşınma direnci ve yüzey özellikleri ile ilgilidir |
Yorulma Dayanımı | Bir PM numunesinin tekrarlanan yükleme ve boşaltma döngüleri altında arızalanmadan dayanabileceği maksimum gerilim | ASTM E466 | Döngüsel gerilimlere maruz kalan bileşenler için kritik |
Kırılma Tokluğu | Malzemenin çatlak ilerlemesine direnme kabiliyeti | ASTM E399 | Ani arızaların tolere edilemediği güvenlik açısından kritik uygulamalar için önemlidir |
Paslanmaz Çelik Tozu Partikül Boyutu Önerileri
Uygulama | Medyan Partikül Boyutu (D₅₀) | Parçacık Boyutu Dağılımı (PSD) | Şekil | Önemli Hususlar |
---|---|---|---|---|
Metal Katmanlı Üretim (Lazer Ergitme, Elektron Işını Ergitme) | 15-45 mikron | Dar (D₅₀ etrafında sıkı dağılım) | Küresel | – Akışkanlık: Küresel partiküller daha kolay akarak tutarlı katman oluşumuna olanak sağlar. - Paketleme Yoğunluğu: Daha küçük partiküller daha sıkı paketlenerek nihai üründeki gözenekliliği azaltabilir. - Yüzey İşlemi: Son derece ince partiküller (<10 mikron) yüzey pürüzlülüğüne neden olabilir. - Lazer Absorpsiyonu: Partikül boyutu lazer emilim verimliliğini etkileyerek erime davranışını etkileyebilir. |
Metal Enjeksiyon Kalıplama (MIM) | 10-100 mikron | Geniş (Paketleme ve sinterleme için daha geniş dağılım) | Düzensiz | – Toz Akışı: Düzensiz şekiller birbirine kenetlenerek enjeksiyon kalıplama sırasında toz akışını iyileştirebilir. - Paketleme Yoğunluğu: Daha geniş bir boyut dağılımı, sinterleme sırasında büzülmeyi azaltarak daha iyi paketleme sağlar. - Sinterleme Verimliliği: Daha büyük partiküller tam sinterlemeyi engelleyerek mekanik özellikleri etkileyebilir. - Debinding: Büyük partiküller ve geniş dağılımlar bağ çözücü maddeleri hapsederek artık gözenekliliğe yol açabilir. |
Plazma Püskürtme | 45-150 mikron | Geniş (MIM'e benzer) | Düzensiz | – Darbe Dayanımı: Daha büyük partiküller nihai kaplamada darbe direncini artırır. - Biriktirme Verimliliği: Düzensiz şekiller mekanik kenetlenmeyi artırarak kaplama yapışmasını iyileştirebilir. - Sıçrama Morfolojisi: Partikül boyutu, püskürtme sırasında sıçrama oluşumunu etkileyerek kaplama mikroyapısını etkiler. - Geri kazanılabilirlik: Daha geniş dağılımlar pürüzsüz, katmanlı kaplamalar oluşturma yeteneğini geliştirebilir. |
Termal Püskürtme (Yüksek Hızlı Oksijen Yakıtı, Patlatma Tabancası) | 45-250 mikron | Geniş (MIM'e benzer) | Düzensiz | – Birikme Oranı: Daha büyük partiküller daha hızlı biriktirme hızları sağlar. - Parçacık Hızı: Yüksek hızlı prosesler, uçuş sırasında kırılmayı en aza indirmek için sağlam partiküller gerektirir. - Kaplama Yoğunluğu: Daha geniş dağılımlar daha yoğun kaplamaları teşvik edebilir, ancak partikül boyutu da paketleme verimliliğini etkileyebilir. - Oksidasyon Direnci: Daha büyük partikül boyutları yüzey alanını azaltarak potansiyel olarak oksidasyon direncini artırabilir. |
Katmanlı Üretim (Binder Jetting) | 10-50 mikron | Dar (Lazerle Eritmeye Benzer) | Küresel | – Çözüm: Daha küçük partiküller, basılı parçada daha ince özellik detayları sağlar. - Yeşil Güç: Partikül boyutu ve dağılımı, fırınlanmamış parçanın mukavemetini etkileyebilir. - Cilt Uyumluluğu: Partikül yüzey alanı bağlayıcı yapışmasını ve basılabilirliği etkileyebilir. - Nem Hassasiyeti: Son derece ince tozlar nem emilimine karşı daha hassas olabilir ve bu da elleçlemeyi etkileyebilir. |
Toz Morfolojisi, Akış Hızı ve Yoğunluğu
Mülkiyet | Açıklama | Toz İşlemedeki Önemi |
---|---|---|
Toz Morfolojisi | Tek tek toz partiküllerinin boyutu, şekli ve yüzey özellikleri. | Morfoloji, Katmanlı Üretimde (AM) paketleme yoğunluğunu, akışkanlığı ve lazer emiciliğini önemli ölçüde etkiler. İdeal olarak, pürüzsüz yüzeylere sahip küresel partiküller en iyi paketleme yoğunluğunu ve akış özelliklerini sunar. Ancak atomizasyon süreçleri farklılıklara yol açabilir. Gaz atomize tozlar daha küresel olma eğilimindeyken, su atomize tozlar daha düzensiz, sıçramış bir morfoloji sergiler. Ek olarak, uydular (daha büyük parçacıklara bağlı küçük parçacıklar) ve uydular gibi yüzey özellikleri akışı engelleyebilir ve AM'de lazer eritme davranışını etkileyebilir. |
Parçacık Boyutu Dağılımı (PSD) | Bir toz partisindeki partikül boyutlarındaki varyasyonun istatistiksel gösterimi. Tipik olarak kümülatif bir dağılım eğrisi olarak veya belirli yüzdelik dilimleri raporlayarak ifade edilir (örneğin, d10 - partiküllerin 10%'si bu boyuttan daha küçüktür, d50 - medyan partikül boyutu). | PSD, toz yatağı paketlemesinde çok önemli bir rol oynar ve AM parçalarının nihai yoğunluğunu ve mekanik özelliklerini etkiler. İyi tanımlanmış bir medyan boyuta (d50) sahip dar bir PSD, tutarlı paketleme ve lazer eritme derinliği için tercih edilir. Tersine, geniş bir dağılım, AM sürecinde taşıma ve düzensiz eritme sırasında ayrışmaya (daha büyük partiküllerin daha ince olanlardan ayrılması) yol açabilir. |
Görünür Yoğunluk & Tap Yoğunluğu | * Görünür yoğunluk: Bir kaba serbestçe döküldüğünde birim hacim başına düşen toz kütlesi. * Dokunma yoğunluğu: Standartlaştırılmış bir dokunma veya titreşim protokolünden sonra elde edilen yoğunluk. | Bu özellikler tozun paketleme davranışını yansıtır ve verimli toz taşıma ve depolama için çok önemlidir. Görünür yoğunluk gevşek paketleme durumunu temsil ederken, dokunma yoğunluğu mekanik çalkalama yoluyla elde edilen daha yoğun bir paketlemeyi gösterir. Carr açısı olarak bilinen bu değerler arasındaki fark, akışkanlığın dolaylı bir ölçüsüdür. Daha düşük Carr açısına sahip tozlar (görünür yoğunluğa yakın daha yüksek kademe yoğunluğu) daha iyi akış özellikleri sergiler. |
Akış Hızı | Tozun bir delikten veya hazneden yerçekimi altında akma hızı. | Akış hızı, AM ve metal enjeksiyon kalıplama (MIM) gibi çeşitli toz işleme tekniklerinde tutarlı malzeme beslemesi için kritik öneme sahiptir. İyi akışkanlık, düzgün toz katmanı oluşumunu sağlar ve yapı işlemi sırasında kesintileri önler. Düzensiz partikül şekilleri, uyduların varlığı ve nem içeriği akış hızını engelleyebilir. Üreticiler toz akışını iyileştirmek için genellikle yağlayıcılar gibi akışkanlık katkı maddeleri kullanır. |
Toz Yoğunluğu | Parçacıklar arasındaki boşluklar hariç olmak üzere, katı parçacıkların kendi birim hacmi başına toz kütlesi. | Toz yoğunluğu, spesifik paslanmaz çelik bileşimine özgü bir malzeme özelliğidir. Sinterleme veya eritme sonrasında bitmiş üründe elde edilebilecek nihai yoğunluğu etkiler. Daha yüksek toz yoğunluğu tipik olarak daha yüksek nihai ürün yoğunluğu ve gelişmiş mekanik özellikler anlamına gelir. |
Paslanmaz Çelik Toz Fiyatlandırma
Faktör | Açıklama | Fiyat Üzerindeki Etkisi |
---|---|---|
Sınıf | Üç basamaklı bir sayı ile belirtilen özel paslanmaz çelik türü (örneğin, 304, 316L, 17-4PH). Farklı kaliteler farklı derecelerde korozyon direnci, mukavemet ve şekillendirilebilirlik sunar. | Gelişmiş korozyon direnci için molibden içeren 316L gibi daha yüksek dereceli paslanmaz çelik tozları, 304 gibi temel derecelere kıyasla tipik olarak yüksek bir fiyata sahiptir. |
Partikül Boyutu ve Dağılımı | Toz partiküllerinin boyutu ve homojenliği. Mikron (μm) veya ağ boyutu (bir elekte doğrusal inç başına düşen açıklık sayısı) olarak ölçülen partikül boyutu, nihai ürünün özelliklerini ve üretim sürecini önemli ölçüde etkiler. | Daha ince tozlar (daha küçük mikronlar / daha yüksek ağ boyutu), daha dar bir partikül boyutu dağılımı elde etmek için gereken ek işlem nedeniyle genellikle daha maliyetlidir. Bununla birlikte, daha ince tozlar, 3D baskılı parçalarda karmaşık ayrıntılar ve daha pürüzsüz yüzey kaplamaları sağlayabilir. |
Yüzey Alanı | Parçacık boyutuyla yakından bağlantılı olan toz parçacıklarının birim ağırlık başına toplam yüzey alanıdır. Daha yüksek yüzey alanına sahip tozlar daha reaktif olma eğilimindedir ve daha sıkı işleme protokolleri gerektirir. | Yüksek yüzey alanına sahip tozlar, kontaminasyonu veya nem emilimini önlemek için özel taşıma ve depolama gereksinimleri nedeniyle ek maliyetlere neden olabilir. |
Üretim Süreci | Paslanmaz çelik tozu üretmek için kullanılan yöntem. Yaygın teknikler arasında atomizasyon (gaz veya su) ve kimyasal buhar biriktirme (CVD) yer alır. | Atomizasyon prosesleri genellikle daha yerleşik ve uygun maliyetli iken, CVD daha ince ve saf tozlar üretir, ancak daha yüksek bir fiyat noktasındadır. |
Saflık | Tozun kimyasal bileşimi, istenmeyen elementlerin minimum varlığı ile. | Daha düşük oksijen, nitrojen ve diğer safsızlık seviyelerine sahip daha yüksek saflıktaki tozlar, daha sıkı üretim kontrolleri nedeniyle genellikle daha yüksek bir maliyete sahiptir. |
Küresel Morfoloji | Toz partiküllerinin şekli. Küresel partiküller üstün akış özellikleri ve paketleme yoğunluğu sunarak daha iyi basılabilirlik ve malzeme kullanımı sağlar. | Küresel paslanmaz çelik tozları, ek işleme adımları nedeniyle düzensiz şekilli parçacıklara kıyasla genellikle daha pahalıdır. |
Miktar | Satın alınan paslanmaz çelik tozu miktarı. | Toplu alımlar, tedarikçiler tarafından sunulan ölçek ekonomileri nedeniyle genellikle önemli fiyat indirimlerinden yararlanır. |
Piyasa Dalgalanmaları | Paslanmaz çelik hammaddesinin taban fiyatını önemli ölçüde etkileyen krom ve nikel gibi hammaddeler için küresel arz ve talep dinamikleri. | Yüksek talep dönemleri veya tedarik zinciri kesintileri paslanmaz çelik tozları için fiyat artışlarına neden olabilir. |
Tedarikçi | Toz üreticisinin itibarı ve uzmanlığı. Titiz kalite kontrol prosedürlerine sahip köklü markalar, daha az bilinen tedarikçilere kıyasla biraz daha yüksek bir fiyata sahip olabilir. | Saygın tedarikçiler genellikle teknik destek ve malzeme sertifikaları gibi ek hizmetler sağlar ve bu da hafif bir fiyat primini haklı çıkarabilir. |
Paslanmaz Çelik Toz Korozyon Direnci
Mülkiyet | Açıklama | Korozyon Direnci Üzerindeki Etkisi |
---|---|---|
Krom İçeriği | Paslanmaz çeliğin korozyon direncindeki temel unsurdur. Oksijene maruz kaldığında yüzeyde ince, görünmez bir krom oksit tabakası oluşturarak daha fazla oksidasyona (pas) karşı bir bariyer görevi görür. | Daha yüksek krom içeriği (tipik olarak 10.5%'nin üzerinde) daha iyi korozyon direnci anlamına gelir. Farklı paslanmaz çelik tozu sınıfları, belirli ortamlara hitap eden farklı krom seviyelerine sahiptir. |
Molibden | Genellikle metalde derin delikler oluşturan lokalize bir saldırı şekli olan çukur korozyonuna karşı direnci artırmak için eklenir. Molibden, özellikle klorür içeren ortamlarda (örneğin deniz suyu) krom oksit tabakasının stabilitesini artırır. | Molibdenli paslanmaz çelik tozları denizcilik uygulamaları, klorür içeren kimyasal işlemler ve yüksek tuzluluktaki ortamlar için idealdir. |
Nikel | Özellikle yüksek sıcaklık ortamlarında genel korozyon direncine katkıda bulunur. Nikel, pasif oksit tabakasının stabilitesinin korunmasına yardımcı olur ve indirgeyici asitlere karşı direnci artırır. | Nikel içeren paslanmaz çelik tozları, sıcak asidik ortamlar veya yüksek basınçlı buhar içeren uygulamalar için çok uygundur. |
Toz Üretim Yöntemi | Tozu oluşturmak için kullanılan işlem, mikro yapısını ve dolayısıyla korozyon direncini etkileyebilir. Yaygın bir yöntem olan gaz atomizasyonu, partiküller içinde oksijeni hapsederek potansiyel olarak lokal korozyona yol açabilir. | Su atomizasyonu gibi iç oksidasyonu en aza indiren yöntemlerle üretilen tozların seçilmesi korozyon performansını artırabilir. |
Gözeneklilik | Toz parçacıklarını birleştirme işlemi olan sinterleme, nihai ürün içinde küçük gözenekler bırakabilir. Bu gözenekler, kirleticileri veya nemi hapsederse korozyon için başlangıç bölgeleri olarak hareket edebilir. | Optimize edilmiş parçacık boyutu dağılımına ve uygun sinterleme parametrelerine sahip tozların seçilmesi, gözenekliliği en aza indirerek korozyon direncinin artmasını sağlar. |
Yüzey İşlemi | Bitmiş bileşenin yüzey topografisi, çevre ile ne kadar kolay etkileşime gireceğini etkileyebilir. Daha pürüzlü yüzeyler, kirletici maddelerin ve nemin yapışması için daha fazla alan sunarak korozyon riskini artırır. | Parlatma veya özel üretim teknikleriyle elde edilebilen daha pürüzsüz yüzeyler, bu potansiyel alanları en aza indirerek korozyon direncini artırır. |
Tane Büyüklüğü | Sinterlenmiş bileşen içindeki münferit metal tanelerinin boyutu korozyon davranışını etkileyebilir. Daha ince tane boyutları, korozif maddelere karşı daha az geçirgen bir bariyer oluşturduklarından genellikle daha iyi korozyon direnci sunarlar. | Sinterleme sırasında ince taneli yapılar elde etmek için optimize edilmiş tozların seçilmesi, bileşenin korozyona direnme kabiliyetini artırabilir. |
Artıları ve Eksileri: Toz ve Katı Çubuk Stoğu
Tablo 7
Avantajlar | Dezavantajlar | |
---|---|---|
Paslanmaz Çelik Toz | Karmaşık şekiller | Daha yüksek maliyet |
Mükemmel korozyon direnci özellikleri | İşlem sonrası | |
Hafifletme | Baskı parametresi optimizasyonu | |
Paslanmaz Çelik Masif Çubuk | Uygun maliyetli | Şekil sınırları |
Kullanılabilirlik | Çok daha ağır | |
İşlenebilirlik | Malzeme atıkları |
Genel olarak paslanmaz çelik tozu, korozyon direnci ve ağırlık azaltmanın hayati önem taşıdığı düşük hacimli karmaşık bileşenler için daha yüksek fiyatları haklı çıkarmaktadır. Çubuk formlar, yüksek üretim kullanım durumlarında basit şekiller için uygun fiyat sunar.
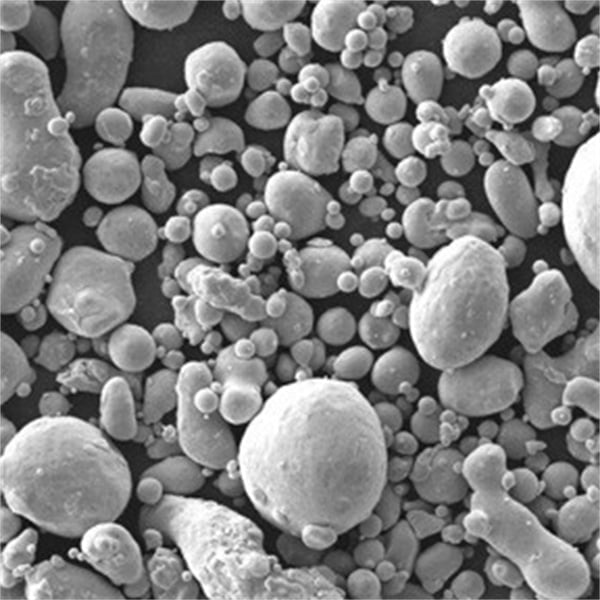
SSS
Tablo 8 - Sık sorulan sorular:
SSS | Cevap |
---|---|
Test raporlarını gözden geçirmeli miyim? | Evet, toz sertifikasyon verilerini iyice inceleyin |
Hangi boyutta toz parçacıkları ile başlamalıyım? | Sağlam baskı için 25-45 mikron |
Tutarlılığı etkileyen faktörler nelerdir? | Ham toz üretim tekniği değişkenliği etkiler |
Başlangıçta ne kadar toz almalıyım? | Baskı sürecini doğrulamak için küçük ölçekte başlayın |
Tablo 9 - Uygulama odaklı tavsiyeler:
SSS | Cevap |
---|---|
Gıda sınıfı paslanmaz ekipmana baskı yapmak için parametreleri nasıl ayarlamalıyım? | Düşük yüzey pürüzlülüğü için optimize edin ve çatlakları ortadan kaldırın |
Denizcilik parçaları için hangi son işlem gözenekliliği azaltabilir? | Korozyon direncini en üst düzeye çıkarmak için sıcak izostatik preslemeyi düşünün |
Hangi alaşım yük taşıyan bileşenler için akma dayanımını en üst düzeye çıkarır? | 17-4PH çökeltme ile sertleştirilmiş paslanmaz |
Yüksek sıcaklık fırın parçaları için en uygun paslanmaz toz hangisidir? | 316L toz mükemmel oksidasyon direnci sunar |
Paylaş
MET3DP Technology Co, LTD, merkezi Qingdao, Çin'de bulunan lider bir katmanlı üretim çözümleri sağlayıcısıdır. Şirketimiz, endüstriyel uygulamalar için 3D baskı ekipmanları ve yüksek performanslı metal tozları konusunda uzmanlaşmıştır.
İşletmeniz için en iyi fiyatı ve özelleştirilmiş Çözümü almak için sorgulayın!
İlgili Makaleler
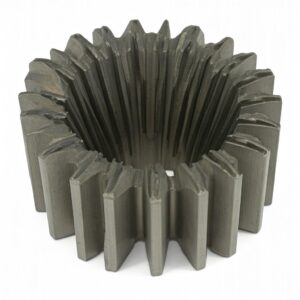
Yüksek Performanslı Nozul Kanat Segmentleri: Metal 3D Baskı ile Türbin Verimliliğinde Devrim
Daha Fazla Oku "Met3DP Hakkında
Son Güncelleme
Bizim Ürünümüz
BİZE ULAŞIN
Herhangi bir sorunuz var mı? Bize şimdi mesaj gönderin! Mesajınızı aldıktan sonra tüm ekibimizle talebinize hizmet edeceğiz.
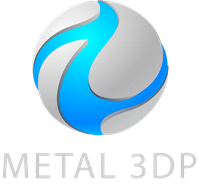
3D Baskı ve Katmanlı Üretim için Metal Tozları