Surgical Drill Guides via Precision Metal 3D Printing
İçindekiler
Introduction: Enhancing Surgical Precision with Metal 3D Printed Drill Guides
In the intricate world of modern surgery, precision is not just a goal; it’s a fundamental requirement for successful patient outcomes. Millimeters, even micrometers, can dictate the difference between optimal recovery and potential complications. Surgical drill guides, essential tools used across various disciplines like orthopedics, neurosurgery, and dental implantology, play a pivotal role in achieving this necessary accuracy. Traditionally manufactured through methods like CNC machining, these guides are now increasingly being produced using advanced metal 3D baskı, also known as eklemeli üretim (AM). This technological shift represents a significant leap forward, enabling the creation of highly customized, complex, and functional patient-specific instruments that were previously difficult or impossible to produce efficiently.
Metal additive manufacturing offers unparalleled design freedom, allowing surgical guides to be tailored perfectly to individual patient anatomy derived from CT or MRI scans. This customization translates directly into enhanced surgical accuracy, reduced operating times, and potentially less invasive procedures. Imagine a guide for spinal surgery that precisely matches the unique curvature of a patient’s vertebrae, or a dental implant guide ensuring perfect placement angle and depth based on detailed oral scans. This level of personalization is where metal 3D baskı truly shines, moving beyond the limitations of one-size-fits-all instruments.
Furthermore, the materials used in metal AM for surgical applications, such as biocompatible Titanium alloys (like Ti-6Al-4V) and Stainless Steels (like 316L), offer excellent mechanical properties, durability, and resistance to sterilization processes. These are critical attributes for tools that come into direct contact with bone and tissue in the demanding environment of the operating room. The ability to print intricate internal channels for cooling or irrigation, lightweight yet robust structures through topology optimization, and complex surface features further underscores the advantages of this technology.
For engineers and procurement managers in the tibbi̇ ci̇haz sector, understanding the capabilities and implications of metal 3D baskı üretmek için surgical drill guides is crucial. It opens doors to innovative product development, streamlined supply chains, and improved clinical performance. Companies specializing in additive manufacturing medical solutions, like Met3dp, are at forefront of this revolution. With expertise in both advanced printing technologies and the production of high-purity metal tozları specifically designed for demanding applications, Met3dp provides comprehensive solutions from material science to finished part production. Their commitment to quality, evidenced by industry-leading gas atomization and PREP technologies for powder manufacturing, ensures that the foundational materials meet the stringent requirements of the medical field. This introduction sets the stage for exploring how precision metal 3D printing is not just an alternative but often a superior method for manufacturing the next generation of surgical drill guides, ultimately contributing to safer and more effective surgical interventions. The transition towards eklemeli üretim in this space signifies a paradigm shift towards more personalized, efficient, and precise surgical care, demanding attention from wholesale buyers, hospital procurement teams, and surgical instrument distributors looking for cutting-edge solutions.
Applications Across Specialties: Where Are Metal Surgical Drill Guides Used?
The utility of metal 3D printed surgical drill guides extends across a surprisingly diverse range of medical and dental specialties. Their ability to provide patient-specific accuracy and handle the mechanical demands of drilling into bone makes them invaluable tools for improving outcomes in complex procedures. Procurement managers sourcing medical device applications and engineers designing custom surgical instruments should be aware of the breadth of these applications. Let’s explore some key areas where these precision instruments are making a significant impact:
1. Orthopedic Surgery: Perhaps one of the most prominent fields utilizing custom drill guides is orthopedics. Metal AM guides are employed in: * Joint Replacement Surgery (Arthroplasty): For knee, hip, and shoulder replacements, guides ensure accurate bone resection, precise placement of implant components (like femoral stems or acetabular cups), and correct screw trajectory fixation. Patient-specific guides derived from CT/MRI data can significantly improve implant alignment and longevity. * Spinal Surgery: In procedures like spinal fusion or vertebroplasty, guides assist in the precise placement of pedicle screws, cages, or instrumentation, minimizing the risk of nerve damage or improper fixation in complex spinal anatomy. The strength of metal guides is crucial here. * Travma Cerrahisi: For complex fracture fixation, especially in areas like the pelvis or calcaneus, custom guides help surgeons accurately place screws and plates according to the pre-operative plan, reducing surgical time and improving fixation stability. * Osteotomies: Corrective bone cutting procedures benefit immensely from guides that dictate the precise angle and location of the cut, crucial for correcting deformities.
2. Dental Implantology: Precision is paramount when placing dental implants to ensure proper osseointegration, function, and aesthetics. Metal 3D printed guides, often based on cone-beam computed tomography (CBCT) scans, offer: * Accurate Implant Placement: Guides dictate the exact location, angle, and depth for drilling the implant site, avoiding critical structures like nerves or sinuses. * Predictable Outcomes: Reduces variability compared to freehand placement, leading to more predictable and reliable results. * Flapless Surgery Potential: In some cases, highly accurate guides allow for minimally invasive flapless surgery, reducing patient discomfort and healing time. * Complex Cases: Essential for full-arch reconstructions or cases with limited bone availability where precision is non-negotiable.
3. Maxillofacial Surgery: This field deals with reconstructive surgery of the face, jaw, and skull. Metal drill guides are used for: * Craniofacial Reconstruction: Guiding drills and saws for precise bone cuts and segment repositioning in corrective jaw surgery (orthognathic surgery) or after trauma/tumor removal. * Mandibular/Maxillary Reconstruction: Ensuring accurate placement of fixation plates and screws when reconstructing the jaw using bone grafts or implants. * Distraction Osteogenesis: Guiding the placement of distraction devices used to gradually lengthen bone.
4. Neurosurgery: While less common than in orthopedics due to the extremely delicate nature of the brain and surrounding structures, specialized applications exist: * Stereotactic Biopsy: Guiding needles or probes to precise locations within the brain for biopsy, minimizing damage to surrounding tissue. * Deep Brain Stimulation (DBS) Electrode Placement: Assisting in the accurate trajectory and depth for placing electrodes used to treat conditions like Parkinson’s disease. * Cranial Fixation: Guiding drills for placing screws or fixation devices during craniotomies or skull reconstruction. The rigidity and accuracy of metal guides can be beneficial.
5. Podiatric Surgery: In foot and ankle surgery, guides can assist with: * Bunion Correction (Hallux Valgus): Guiding osteotomies and screw placement for deformity correction. * Arthrodesis (Joint Fusion): Ensuring accurate alignment and fixation for fusing joints in the foot or ankle.
Key Advantages Driving Adoption Across Specialties:
- Patient-Specificity: Tailored to individual anatomy from medical imaging (CT, MRI, CBCT).
- Enhanced Accuracy: Translates pre-operative digital plans into precise intraoperative actions.
- Azaltılmış Cerrahi Süre: Predictable drilling paths can streamline procedures.
- Minimally Invasive Potential: Enables smaller incisions or flapless approaches in some cases.
- Improved Consistency: Reduces reliance on surgeon experience alone for drilling accuracy.
- Handling Complex Anatomy: Facilitates navigation around critical structures (nerves, vessels).
- Material Strength & Durability: Metal (Ti-6Al-4V, 316L) provides the necessary rigidity and wear resistance for drilling into bone, unlike some polymer alternatives.
- Sterilizability: Metal guides can withstand standard autoclaving and sterilization protocols required for surgical instruments.
The increasing availability of medical device AM suppliers capable of producing high-quality, validated metal surgical guides, combined with sophisticated 3D planning software, is accelerating adoption. For hospitals and surgical centers, partnering with knowledgeable manufacturers who understand the specific requirements of these medical device applications is key. Companies like Met3dp, with their focus on high-performance metal tozları and precision printing systems, are well-positioned to support the growing demand for these critical custom surgical instruments across multiple disciplines. Procurement teams looking for reliable wholesale surgical guides veya bulk order medical devices should consider the proven benefits and expanding applications of metal AM in this domain.
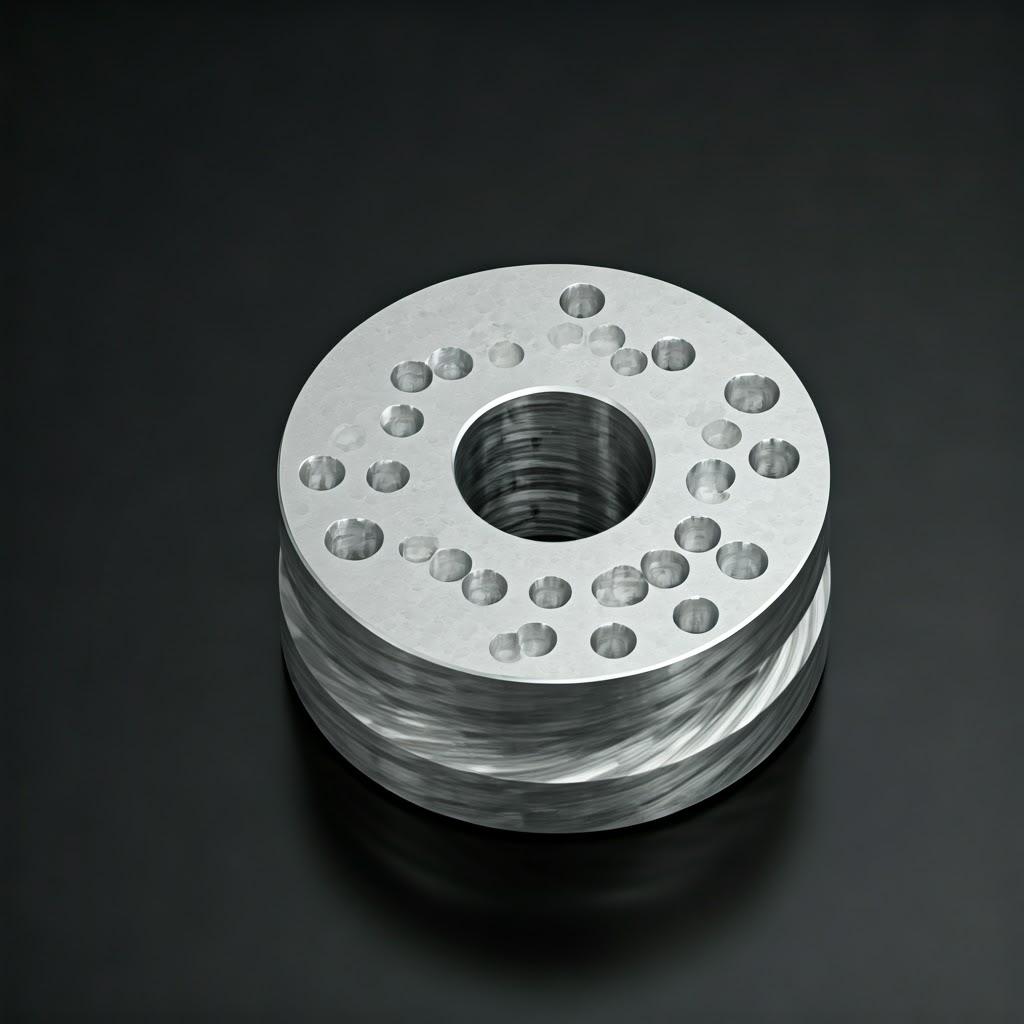
The Additive Advantage: Why Choose Metal 3D Printing for Surgical Guides?
While traditional manufacturing methods like CNC machining have long served the medical industry, metal katkılı üretim (AM) presents a compelling suite of advantages specifically tailored to the demands of producing surgical drill guides. For engineers designing the next generation of surgical tools and procurement managers evaluating manufacturing options, understanding these benefits is crucial for making informed decisions that impact clinical efficiency, cost-effectiveness, and patient outcomes. Let’s delve into why metal 3D baskı is rapidly becoming the preferred method for these critical instruments.
1. Unparalleled Design Freedom & Complexity:
- Hastaya Özel Özelleştirme: AM’s core strength lies in its ability to create parts directly from digital models. This allows surgical guides to be designed based on individual patient CT/MRI scans, perfectly conforming to unique anatomical contours. This level of personalization is extremely difficult, time-consuming, and costly to achieve with subtractive methods like CNC machining.
- Karmaşık Geometriler: Metal AM can produce intricate internal channels (e.g., for irrigation or cooling during drilling), complex lattice structures (for weight reduction while maintaining stiffness), and highly organic shapes that follow anatomical curves naturally. Machining such features is often impractical or impossible.
- Parça Konsolidasyonu: Multiple components of a traditional guide assembly can potentially be consolidated into a single, monolithic printed part, reducing assembly time, potential failure points, and sterilization challenges.
2. Rapid Prototyping and Iteration:
- Speed from Design to Part: Metal AM allows for the rapid production of prototypes directly from CAD files. This drastically accelerates the design iteration cycle, enabling surgeons and engineers to test and refine guide designs quickly before final production.
- İsteğe Bağlı Üretim: Guides can be printed as needed, reducing the need for large inventory stockpiles of standardized sizes. This is particularly beneficial for patient-specific instruments which are, by definition, unique. This aligns well with Just-in-Time (JIT) supply chain models increasingly adopted by healthcare providers.
3. Material Performance and Selection:
- Biocompatible Metals: AM processes commonly utilize well-established, biocompatible medical-grade alloys like Titanium (Ti-6Al-4V) and Stainless Steel (316L). These materials offer an excellent combination of strength, durability, corrosion resistance, and proven compatibility with human tissue. Learn more about Met3dp’s metal 3D baskı capabilities and material options.
- Optimized Material Usage: AM is an additive process, meaning material is added layer by layer only where needed. While powder feedstock requires careful handling, this often results in less material waste compared to subtractive machining, especially for complex parts where significant material removal is required from a solid block.
- Potential for Novel Alloys: AM opens possibilities for using advanced or custom metal alloys specifically engineered for medical applications, although standard Ti-6Al-4V and 316L remain the workhorses for guides due to regulatory acceptance and proven performance.
4. Enhanced Surgical Efficiency and Accuracy:
- Improved Precision: Patient-specific guides translate the digital pre-operative plan directly to the surgical site, minimizing deviations and improving the accuracy of drill placement, cutting angles, and implant positioning.
- Reduced Operating Time: By simplifying the drilling or cutting process and ensuring accuracy, custom guides can potentially reduce the overall time spent in the operating room, benefiting both the patient and the hospital system.
- Minimally Invasive Procedures: Highly accurate guides can facilitate less invasive surgical approaches, potentially leading to smaller incisions, less tissue disruption, reduced blood loss, and faster patient recovery.
5. Cost-Effectiveness for Complexity and Low Volumes:
- Complexity is (Almost) Free: Unlike traditional manufacturing where complexity significantly drives up cost (due to tooling, machining time, multiple setups), the cost of AM is primarily driven by material volume and print time. Highly complex geometries do not incur the same cost penalty.
- Viable for Low Volumes/Single Pieces: AM eliminates the need for expensive custom tooling or molds, making it economically viable to produce unique, patient-specific guides (a batch size of one) or small series runs. Traditional methods become prohibitively expensive for such low volumes.
Comparison: Metal AM vs. CNC Machining for Surgical Guides
Özellik | Metal Katmanlı Üretim (AM) | Geleneksel CNC İşleme |
---|---|---|
Özelleştirme | High (Patient-specific, complex geometry easily achieved) | Lower (Complex shapes require intricate programming & tooling) |
Complexity Cost | Relatively low impact | High impact (Increases machining time, tooling needs) |
Lead Time (Prototype) | Fast (Hours to days) | Moderate to Slow (Requires setup, programming, tooling) |
Lead Time (Production) | Moderate (Depends on build size/complexity) | Can be fast for simple parts, slower for complex ones |
Malzeme Atıkları | Generally lower (Additive process, powder recycling possible) | Higher (Subtractive process, generates chips) |
İç Özellikler | Easily produces complex internal channels, lattices | Difficult or impossible to machine complex internal features |
Minimum Volume | Economical for single pieces (Batch size = 1) | Less economical for very low volumes due to setup costs |
Yüzey İşlemi | Typically requires post-processing for smooth finish | Can achieve very smooth finishes directly |
Initial Setup Cost | Lower (No custom tooling required) | Higher (Tooling, fixtures may be needed) |
Sayfalara Aktar
While CNC machining still holds advantages in achieving extremely tight tolerances and fine surface finishes directly off the machine for simpler geometries, the specific requirements of surgical drill guides – customization, complex shapes matching anatomy, and relatively low volume per design – strongly favor the additive advantage. Partnering with an experienced medical device AM supplier like Met3dp, who understands the nuances of metal AM vs CNC and possesses robust quality systems alongside advanced metal tozu production and printing technology, ensures access to these benefits for creating superior custom surgical instruments. Bu da metal 3D baskı a strategically sound choice for healthcare providers and medical device companies seeking innovation and efficiency.
Material Matters: Selecting Biocompatible Metal Powders for Surgical Guides (316L & Ti-6Al-4V Focus)
The choice of material is paramount when manufacturing any medical device, especially surgical instruments like drill guides that come into direct or indirect contact with patient tissues and bone. Metal 3D baskı offers a selection of robust, biyouyumlu malzemeler, but two stand out as the primary choices for surgical guides due to their proven track record, excellent properties, and regulatory acceptance: 316L Stainless Steel (316L) ve Titanium Alloy Ti-6Al-4V (Ti64). Understanding the characteristics, advantages, and specific considerations for each is vital for engineers, designers, and procurement specialists involved in sourcing or developing these critical tools. The quality of the metal tozu feedstock is the foundation for producing reliable, high-performance parts, making partnerships with expert powder manufacturers like Met3dp invaluable.
1. 316L Stainless Steel (Austenitic Stainless Steel): 316L is a widely used medical-grade stainless steel known for its excellent corrosion resistance, good mechanical strength, and established biocompatibility. The “L” signifies low carbon content (typically < 0.03%), which minimizes carbide precipitation during welding or high-temperature exposure (like stress relief post-printing), thereby enhancing its resistance to intergranular corrosion.
- Key Properties & Advantages for Surgical Guides:
- Mükemmel Korozyon Direnci: Highly resistant to corrosion in bodily fluids and cleaning/sterilization chemicals (e.g., autoclaving). This is critical for reusable surgical instruments.
- Good Biocompatibility: Long history of safe use in temporary contact medical devices and surgical instruments. Meets standards like ISO 10993 for biocompatibility.
- High Ductility and Formability: While less relevant for the finished guide, it influences powder production and processing characteristics.
- Good Mechanical Strength and Hardness: Provides sufficient rigidity and wear resistance for guiding drills accurately without significant deformation or wear during a procedure.
- Maliyet-Etkinlik: Generally more cost-effective than Titanium alloys, making it an attractive option for guides where the extreme strength-to-weight ratio of Titanium is not strictly necessary.
- Ease of Post-Processing: Relatively easy to machine, polish, and finish compared to Titanium alloys.
- Established Use: Widely recognized and accepted by regulatory bodies (FDA, CE) for surgical instrument applications.
- Düşünceler:
- Yoğunluk: Significantly denser than Titanium (approx. 8 g/cm³ vs 4.4 g/cm³), which can make larger guides feel heavier.
- Nickel Content: Contains nickel (typically 10-14%), which can be a concern for patients with severe nickel allergies, although leaching is minimal in properly processed 316L. Careful material selection and validation are necessary.
- Lower Strength-to-Weight Ratio: Compared to Ti-6Al-4V.
2. Titanium Alloy Ti-6Al-4V (Grade 5 or Grade 23 ELI): Ti-6Al-4V (often abbreviated as Ti64) is the workhorse of medical Titanium alloys, renowned for its high strength-to-weight ratio, excellent corrosion resistance, and outstanding biocompatibility, making it suitable for both temporary instruments and permanent implants. Grade 23, or ELI (Extra Low Interstitials), has reduced oxygen, nitrogen, and iron content, leading to improved ductility and fracture toughness, often preferred for critical applications.
- Key Properties & Advantages for Surgical Guides:
- Exceptional Biocompatibility: Considered highly biocompatible and bioinert, forming a stable passive oxide layer upon contact with air or bodily fluids. Widely used for implants (hip stems, dental implants) and instruments. Meets rigorous ISO 10993 and ASTM F136 (for ELI) standards.
- Yüksek Mukavemet-Ağırlık Oranı: Offers strength comparable to many steels but at nearly half the density. This allows for lightweight yet very strong and rigid guides, reducing surgeon fatigue and improving handling, especially for larger or more complex guides.
- Mükemmel Korozyon Direnci: Superior resistance to corrosion in harsh physiological environments.
- Osseointegration Potential: While not typically desired for a removable guide, its ability to integrate with bone is a testament to its biocompatibility.
- Non-magnetic: Important for compatibility with MRI imaging, should pre- or post-operative imaging be required with the guide potentially nearby (though typically removed well before).
- Dayanıklılık: High fatigue strength and toughness ensure longevity and resistance to damage during use and handling.
- Düşünceler:
- Daha Yüksek Maliyet: Titanium alloys and the associated metal tozları are generally more expensive than stainless steels.
- İşleme Zorlukları: Can be more challenging to machine and polish than 316L due to its reactivity and tendency to gall. Requires specific expertise in post-processing.
- Reaktivite: Requires controlled atmosphere (inert gas like Argon) during laser or electron beam melting (LPBF/EBM) to prevent contamination, particularly with oxygen.
The Importance of High-Quality Metal Powders:
The performance of the final 3D printed surgical guide heavily depends on the quality of the initial metal tozu. Key powder characteristics influencing print quality and final part properties include:
- Parçacık Boyutu Dağılımı (PSD): Affects powder bed density, flowability, and the achievable resolution and surface finish of the printed part. Optimized PSD is crucial for consistent melting and layer adhesion.
- Küresellik: Highly spherical powder particles promote good flowability and packing density, leading to more uniform layers and denser final parts with fewer voids.
- Akışkanlık: Essential for uniform powder spreading across the build platform in powder bed fusion processes (LPBF, EBM). Poor flowability can lead to defects.
- Chemical Purity: Must meet stringent medical-grade specifications (e.g., ASTM F1580 for 316L, ASTM F136/F3001 for Ti-6Al-4V ELI) with low levels of impurities (especially interstitials like Oxygen, Nitrogen in Titanium) that can compromise mechanical properties and biocompatibility.
- Absence of Satellites: Small particles attached to larger ones (satellites) can hinder flowability and packing.
Şirketler gibi Met3dp üretme konusunda uzmanlaşmak yüksek kaliteli metal tozları tailored for additive manufacturing. Utilizing advanced Powder Making Systems like vacuum induction melting gas atomization (VIGA) and plasma rotating electrode process (PREP), Met3dp ensures their 316L ve Ti-6Al-4V powders exhibit high sphericity, excellent flowability, controlled PSD, and exceptional purity. This commitment to powder quality is fundamental to achieving the dimensional accuracy, mechanical integrity, and biocompatibility required for demanding medical device applications gibi surgical drill guides.
Material Selection Summary Table:
Özellik | 316L Paslanmaz Çelik | Ti-6Al-4V Titanyum Alaşımı |
---|---|---|
Primary Advantage | Cost-effectiveness, Ease of processing | High Strength-to-Weight, Superior Biocompatibility |
Biyouyumluluk | Good (ISO 10993) | Excellent (ISO 10993, ASTM F136/F3001) |
Korozyon Direnci | Mükemmel | Üstün |
Yoğunluk | ~8,0 g/cm³ | ~4.4 g/cm³ |
Güçten Ağırlığa | İyi | Çok Yüksek |
Maliyet | Daha düşük | Daha yüksek |
İşlem Sonrası | Daha kolay | More Challenging |
Allergy Concern | Potential Nickel Sensitivity | Generally Considered Hypoallergenic |
Common Use Case | General surgical instruments, cost-sensitive guides | Implants, lightweight/high-strength guides |
Met3dp Powder Quality | High Purity, Good Sphericity & Flowability | High Purity, Good Sphericity & Flowability (incl. ELI) |
Sayfalara Aktar
Ultimately, the choice between 316L ve Ti-6Al-4V için surgical drill guide depends on the specific application requirements, budget constraints, and design considerations. For guides requiring maximum lightweighting, rigidity, or where even minute concerns about nickel exist, Ti-6Al-4V is often preferred despite its higher cost and processing demands. For many standard guide applications where cost is a significant factor and the exceptional properties of Titanium are not strictly necessary, 316L provides a robust and reliable solution. Consulting with an experienced metal 3D printing service provider like Met3dp, who offers both materials and understands their nuances, is crucial for making the optimal selection. Their expertise ensures that the chosen biocompatible metal powder meets the necessary specifications for producing safe and effective surgical drill guides via precision metal 3D printing.
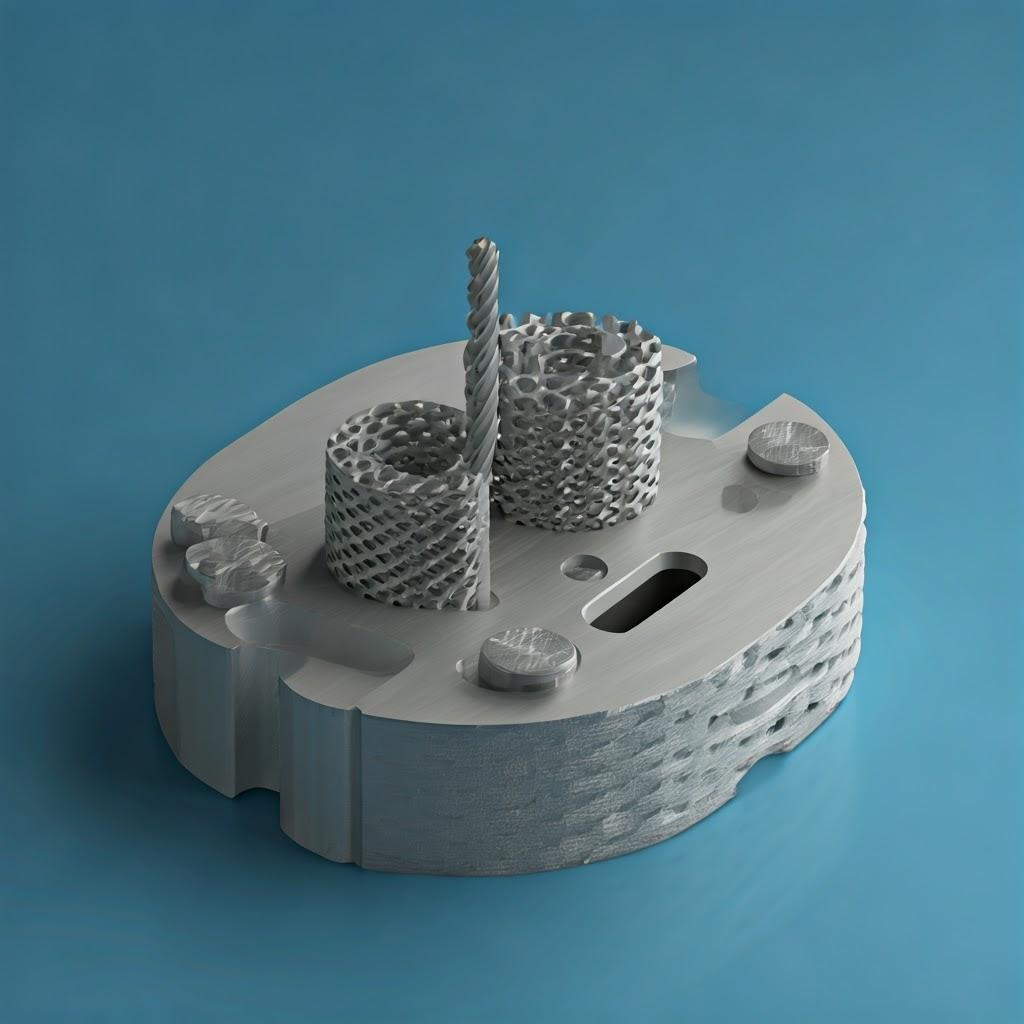
Design for Manufacturability (DfAM): Optimizing Surgical Guides for Metal Additive Manufacturing
Creating an effective surgical drill guide involves more than just replicating patient anatomy in CAD software. To fully leverage the capabilities of metal katkılı üretim (AM) and ensure a successful, functional, and cost-effective final product, designers must embrace Katmanlı Üretim Tasarımı (DfAM) principles. DfAM is not just about making a part printable; it’s about optimizing the design to enhance performance, minimize post-processing, reduce print time and cost, and improve overall quality. For tibbi̇ ci̇hazlar gibi surgical drill guides, applying DfAM is critical for achieving the necessary precision, usability, and safety. Engineers and designers working with metal 3D baskı hizmeti sağlayıcıları must consider these factors early in the development process.
Key DfAM Principles for Metal Surgical Guides:
- Optimize for Orientation and Support Structures:
- Yapı Oryantasyonu: How the guide is oriented on the build platform significantly impacts surface finish quality (up-facing vs. down-facing surfaces), the number and location of required support structures, print time, and potential for distortion. Critical features, like the internal bore of drill cylinders or surfaces contacting bone, should ideally be oriented to minimize supports or achieve the best possible as-printed surface finish.
- Support Minimization: Support structures are often necessary in metal AM (especially Laser Powder Bed Fusion – LPBF) to anchor the part to the build plate, prevent warping, and support overhanging features. However, supports consume extra material, add print time, and require removal during post-processing, which can be labor-intensive and potentially damage delicate features or leave surface marks. DfAM aims to minimize the need for supports by:
- Designing features with self-supporting angles (typically > 45 degrees from the horizontal plane, though process-dependent).
- Using chamfers or fillets instead of sharp horizontal overhangs.
- Orienting the part strategically.
- Incorporating sacrificial layers or features designed for easy support removal.
- Support Accessibility: When supports are unavoidable, they must be designed for easy access and removal without compromising the guide’s functionality or structural integrity. Avoid placing supports on critical functional surfaces or within intricate internal channels where removal is difficult.
- Topoloji Optimizasyonu ve Hafifletme:
- Strength with Reduced Mass: While metal guides (especially Ti-6Al-4V) are inherently strong, excessive weight can lead to surgeon fatigue and awkward handling. Topology optimization software can analyze load paths and remove material from non-critical areas, creating organic, load-bearing structures that maintain stiffness while significantly reducing weight.
- Kafes Yapılar: AM excels at creating complex internal lattice structures. These can be strategically incorporated within the guide’s body to drastically reduce mass and material consumption while preserving structural integrity and rigidity. This is particularly advantageous for larger guides used in orthopedic or spinal surgery.
- Feature Design Considerations:
- Drill Cylinder Design: The core function revolves around the drill cylinders. DfAM involves:
- Clearance: Designing the inner diameter with appropriate clearance for the surgical drill bit, accounting for manufacturing tolerances and potential thermal expansion during drilling.
- Length: Ensuring sufficient length for guidance accuracy but not so long as to obstruct visibility or access.
- Duvar Kalınlığı: Balancing rigidity to prevent deflection during drilling with minimizing bulk.
- Lead-in Chamfers: Adding chamfers at the cylinder entrance can aid drill bit insertion.
- Visibility Features: Incorporate cut-outs or windows in the guide body to allow the surgeon visual confirmation of seating against bone landmarks and visibility of the surgical site around the drilling area.
- Handling Features: Add ergonomic grips, handles, or textured surfaces to improve the surgeon’s grasp and control over the guide, especially when wearing surgical gloves.
- Anatomical Fit: Leverage AM’s ability to create surfaces that perfectly conform to the patient’s bone anatomy for stable and accurate positioning. Smooth transitions and avoidance of sharp edges contacting soft tissues are important.
- Drill Cylinder Design: The core function revolves around the drill cylinders. DfAM involves:
- Wall Thickness and Minimum Feature Size:
- Minimum Wall Thickness: Metal AM processes have limitations on the minimum printable wall thickness (often around 0.3-0.5 mm, depending on the machine, material, and geometry). Designs must respect these limits to ensure features are fully formed and robust. Thin walls may be prone to distortion or damage.
- Minimum Özellik Boyutu: Similarly, small pins, holes, or intricate details have minimum size constraints based on the laser/electron beam spot size and powder particle size. Ensure critical small features are designed within printable limits.
- Internal Channels and Powder Removal:
- Irrigation/Cooling Channels: If designing internal channels for irrigation or cooling, ensure they are large enough and have smooth paths to allow for effective fluid flow and, crucially, complete removal of unfused metal powder during post-processing. Trapped powder is a contamination risk and unacceptable for medical devices.
- Drainage Holes: Incorporate strategically placed drainage holes to facilitate powder removal from internal cavities and channels after printing. Consider accessibility for cleaning tools or compressed air.
- Designing for Post-Processing:
- Machining Allowances: If certain features require tolerances tighter than achievable with AM alone, design those features with extra stock material (“machining allowance”) to be finished via CNC machining.
- Surface Finish Considerations: Understand that different surfaces will have varying roughness based on orientation and support contact. Design critical surfaces (e.g., bone-contacting areas, drill bores) anticipating required finishing steps like polishing or machining.
- Cleaning Accessibility: Ensure the overall design allows for thorough cleaning and sterilization, avoiding deep, inaccessible pockets where bioburden could accumulate.
By applying these DfAM medical devices principles, manufacturers can significantly improve the quality, functionality, and cost-effectiveness of metal 3D printed surgical guides. Collaborating with experienced eklemeli üretim partners like Met3dp, who possess deep knowledge of various baskı yöntemleri and material behaviors, can streamline the design optimization process. Their engineers can provide valuable feedback on design feasibility, suggest optimizations for printability and performance, and ensure the final design aligns with the capabilities and limitations of the chosen metal AM technology, ultimately leading to superior custom surgical instruments. Thinking about manufacturability from the outset transforms metal 3D baskı from just a production method into an integrated design and manufacturing solution.
Achieving Precision: Tolerances, Surface Finish, and Dimensional Accuracy in Metal AM Guides
One of the primary drivers for using surgical drill guides is to enhance procedural accuracy. Therefore, the boyutsal doğruluk, achievable Toleranslar, and resulting yüzey kaplaması . metal 3D printed guides are critical parameters for success. Engineers and procurement managers must understand the capabilities and limitations of metal katkılı üretim in these areas to set realistic expectations and ensure the final product meets stringent clinical requirements. Precision manufacturing surgical tools using AM requires careful process control and often involves post-processing steps.
Dimensional Accuracy and Tolerances:
- General Capabilities: Modern metal AM systems, like the high-precision printers utilized by specialists such as Met3dp, can achieve relatively high levels of dimensional accuracy. Typical general tolerances for metal Laser Powder Bed Fusion (LPBF) or Electron Beam Melting (EBM) are often cited in the range of:
- +/- 0.1 mm to +/- 0.2 mm for smaller features (e.g., up to 20-50 mm).
- +/- 0.2% to +/- 0.5% of the nominal dimension for larger parts.
- Factors Influencing Accuracy: Achievable accuracy is not uniform and depends on various factors:
- Machine Calibration: Regular calibration and maintenance of the AM system are crucial.
- Süreç Parametreleri: Laser/beam power, scan speed, layer thickness, and hatching strategies significantly impact melt pool stability and final dimensions.
- Malzeme Özellikleri: Different metal alloys (e.g., 316L vs. Ti-6Al-4V) exhibit different shrinkage and thermal behavior during processing.
- Part Geometry & Size: Larger parts or those with significant thermal gradients are more prone to distortion and deviation.
- Thermal Stress: Residual stresses built up during the layer-by-layer heating and cooling cycles can cause warping, especially after removal from the build plate. Stress relief heat treatment is often essential to minimize this.
- Destek Yapıları: The location and density of supports influence thermal behavior and potential distortion upon removal.
- Critical Dimensions: For surgical guides, critical dimensions include the inner diameter of the drill cylinder, the position and orientation of the cylinder relative to anatomical landmarks, and the fit of the guide against the bone surface. While general AM tolerances might be sufficient for the overall shape, critical features like the drill bore often require tighter control, potentially necessitating post-machining.
- Validation: Dimensional accuracy must be verified through rigorous quality control, typically using coordinate measuring machines (CMM), 3D scanning, or traditional metrology tools. This is a standard part of the quality control additive manufacturing process for medical devices.
Yüzey İşlemi (Pürüzlülük):
- As-Printed Roughness: The surface finish of as-printed metal AM parts is inherently rougher than machined surfaces. This is due to the layer-by-layer nature of the process and the partially melted powder particles adhering to the surface. Typical as-printed surface roughness (Ra) values for metal LPBF can range from 6 µm to 20 µm (or higher), depending on:
- Oryantasyon: Up-facing and vertical surfaces tend to be smoother than down-facing surfaces or those supported by structures.
- Katman Kalınlığı: Thinner layers generally produce smoother surfaces but increase print time.
- Toz Özellikleri: Finer, more spherical powder can lead to smoother finishes.
- Süreç Parametreleri: Optimized parameters minimize surface irregularities.
- Why Surface Finish Matters for Guides:
- Friction: Roughness within the drill cylinder can increase friction with the drill bit.
- Wear: Rough surfaces may wear more quickly.
- Cleaning & Sterilization: Rougher surfaces have a higher surface area and more potential sites for bacteria or debris to adhere, making cleaning and sterilization more challenging.
- Tissue Contact: While guides are typically temporary contact devices, excessively rough surfaces contacting soft tissues could cause irritation (though bone contact is the primary interface).
- Yüzey İşleminin İyileştirilmesi: Post-processing is almost always required to achieve the smoother surface finishes needed for surgical instruments. Common methods include:
- Support Removal Marks: Initial grinding or finishing is needed where supports were attached.
- Bead Blasting/Sandblasting: Creates a uniform, matte finish, typically reducing Ra values but not achieving a polished look. Effective for general surface smoothing.
- Tumbling/Vibratory Finishing: Uses abrasive media in a rotating or vibrating bowl to smooth surfaces and edges, suitable for batches of parts.
- CNC İşleme: Used for critical features requiring very smooth finishes and tight tolerances (e.g., drill bores).
- Manual Polishing: Labor-intensive but can achieve very smooth, mirror-like finishes where required.
- Elektro parlatma: An electrochemical process that removes a microscopic layer of material, resulting in a very smooth, clean, and often brighter surface. Particularly effective for 316L stainless steel, enhancing its corrosion resistance and cleanability.
Surface Roughness (Ra) Comparison (Typical Values):
Process/Finish | Typical Ra Range (µm) | Notlar |
---|---|---|
As-Printed (LPBF) | 6 – 20+ | Highly dependent on orientation, parameters, material |
Bead Blasted | 2 – 6 | Uniform matte finish, good for general smoothing |
Tumbled/Vibratory | 1 – 5 | Depends on media and time, good for deburring |
Electropolished (316L) | < 0.8 | Very smooth, bright, clean finish, enhances corrosion res. |
CNC Machined (Fine) | < 1.6 (often < 0.8) | Can achieve very smooth finishes |
Polished (Manual) | < 0.4 (Mirror < 0.1) | Labor-intensive, highest level of smoothness |
Sayfalara Aktar
Achieving the required metal 3D printing accuracy and surface finish for surgical drill guides necessitates a combination of precise printing processes and appropriate post-processing techniques. Partnering with a service provider like Met3dp, which emphasizes process control, utilizes yüksek kaliteli tozlar, and offers comprehensive post-processing capabilities, is essential. They understand the critical relationship between printing parameters, material choice (316L, Ti-6Al-4V), and finishing steps needed to meet the demanding dimensional stability medical parts require. Procurement managers should inquire about a supplier’s metrology capabilities and documented procedures for ensuring consistent precision manufacturing surgical Bileşenler.
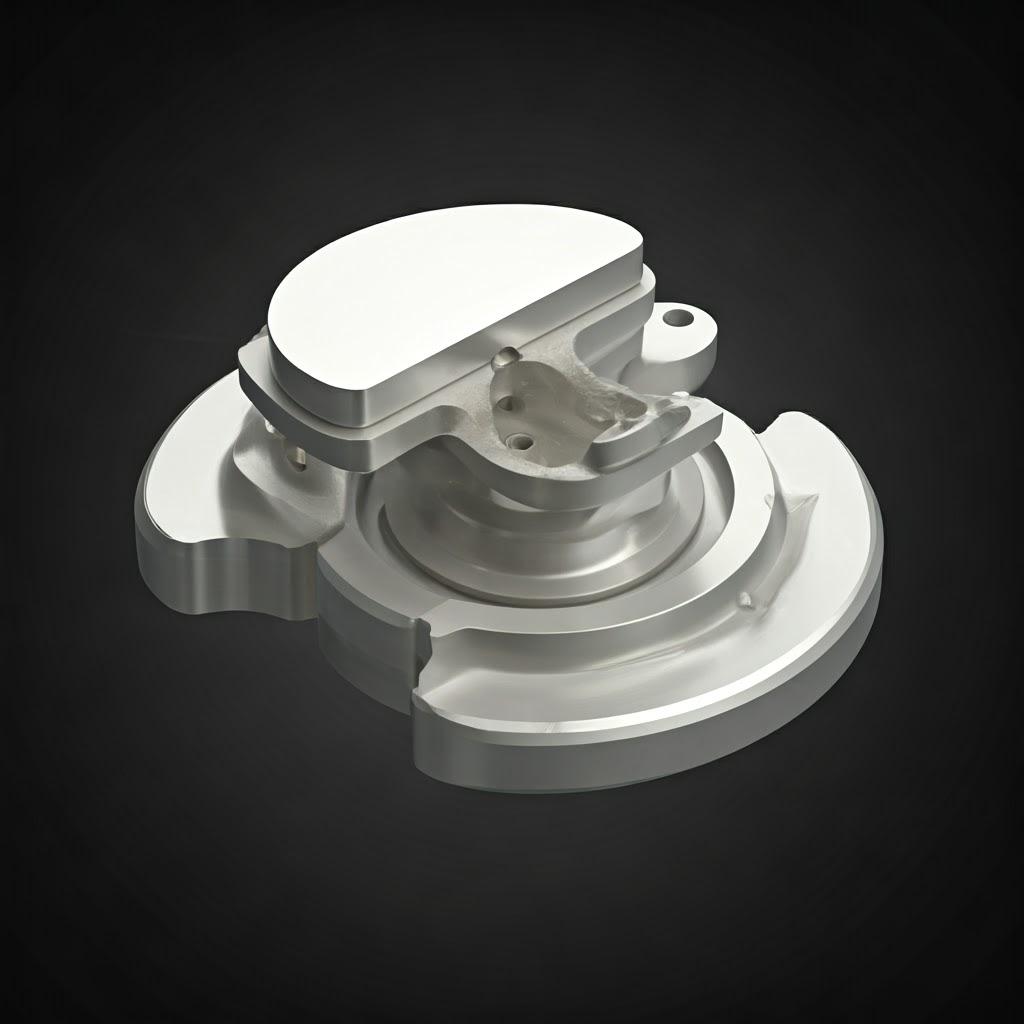
Beyond the Print: Essential Post-Processing Steps for Metal Surgical Guides
The journey of a metal 3D printed surgical drill guide doesn’t end when the printer stops. The “as-printed” part, while geometrically complete, requires several crucial post-processing steps to transform it from a raw component into a finished, functional, and safe medical device ready for clinical use. These steps are critical for achieving the required mechanical properties, dimensional accuracy, surface finish, and biocompatibility. Understanding this workflow is vital for engineers planning production and procurement managers assessing supplier capabilities and total lead times. Neglecting or improperly executing post-processing can compromise the guide’s performance and safety.
Standard Post-Processing Workflow for Metal AM Surgical Guides:
- Powder Removal / Depowdering:
- Objective: Remove all unfused metal powder trapped within the guide’s internal channels, cavities, and surfaces.
- Yöntemler: Typically involves manual brushing, vacuuming, and using compressed air within a controlled environment or specialized depowdering station to contain the fine metal powder. For complex internal geometries (like irrigation channels), specialized techniques might be needed.
- Criticality: Incomplete powder removal is a major contamination risk, compromising biocompatibility and potentially interfering with function. This step requires meticulous attention, especially for intricate designs. DfAM considerations (drainage holes) play a role here.
- Stress Relief Heat Treatment:
- Objective: Reduce the internal residual stresses built up during the rapid heating and cooling cycles inherent in the layer-by-layer printing process. These stresses can cause warping or distortion, especially after the part is removed from the build plate or during subsequent machining.
- Yöntemler: Controlled heating of the part (while often still attached to the build plate) in a vacuum or inert atmosphere furnace to a specific temperature (below the material’s transformation point), holding it for a defined period, and then cooling slowly. Parameters (temperature, time, atmosphere) are material-specific (e.g., different cycles for Ti-6Al-4V vs. 316L).
- Criticality: Essential for maintaining dimensional stability and preventing unexpected failures. Almost always required for metal AM parts, especially titanium alloys.
- Yapı Plakasından Parça Çıkarma:
- Objective: Separate the printed guide(s) from the metal build plate they were fused to during printing.
- Yöntemler: Typically done using wire Electrical Discharge Machining (EDM) or a bandsaw. Care must be taken to avoid damaging the parts.
- Destek Yapısının Kaldırılması:
- Objective: Remove the temporary support structures required during printing.
- Yöntemler: Can involve manual breaking/cutting (for easily accessible supports), CNC machining, grinding, or sometimes specialized tools. This can be labor-intensive and requires skill to avoid damaging the part surface.
- Criticality: Supports must be fully removed. The areas where supports were attached often have a rougher surface finish and require subsequent finishing. DfAM significantly impacts the ease of this step.
- Hot Isostatic Pressing (HIP) – (Optional but sometimes considered):
- Objective: Eliminate any remaining internal microporosity, improving density (approaching 100% theoretical density), fatigue life, and overall mechanical properties.
- Yöntemler: Subjects the parts to high temperature (below melting point) and high isostatic pressure (using an inert gas like Argon) simultaneously in a specialized HIP vessel.
- Criticality: While standard for critical load-bearing implants (like hip stems), HIP is less commonly mandated for temporary-contact surgical guides unless exceptional fatigue resistance or guaranteed absence of porosity is required by the design specification or risk assessment. It adds significant cost and time. HIP processing titanium is common for implants, less so for typical guides.
- Yüzey İşlemi:
- Objective: Achieve the desired surface roughness (Ra), remove support witness marks, and potentially improve aesthetics or cleanability.
- Yöntemler: As discussed previously, this can include:
- Basic Finishing: Grinding/filing support contact points.
- Mass Finishing: Bead blasting, tumbling, vibratory finishing for overall smoothing and a uniform matte finish.
- Targeted Finishing: CNC machining for critical tolerances/surfaces, manual polishing for high smoothness.
- Chemical Finishing: Electropolishing (especially for 316L) for ultimate smoothness and enhanced corrosion resistance/cleanability. Passivation for stainless steel to restore the passive chromium oxide layer.
- Criticality: Essential for function (e.g., smooth drill bore), cleanability, and potentially biocompatibility (smoother surfaces are easier to clean and sterilize).
- Cleaning and Inspection:
- Objective: Remove all residues from manufacturing and post-processing (oils, machining fluids, blasting media, polishing compounds, fingerprints) and verify critical dimensions and quality attributes.
- Yöntemler:
- Temizlik: Multi-stage cleaning processes, often involving ultrasonic baths with validated medical-grade detergents, followed by thorough rinsing (e.g., with deionized water) and drying. Procedures must be validated to ensure effective removal of contaminants without damaging the part.
- Teftiş: Dimensional verification (CMM, scanning), visual inspection for defects, surface roughness measurement, and potentially NDT (Non-Destructive Testing) like CT scanning if internal integrity needs verification (rare for guides unless highly complex or critical).
- Criticality: Absolutely essential for medical devices. Inadequate cleaning compromises sterilization effectiveness and biocompatibility. Rigorous inspection ensures the guide meets specifications.
- Sterilization Compatibility:
- Not: The final sterilization (e.g., steam autoclaving, gamma radiation, EtO) is typically performed by the hospital or medical device manufacturer packaging the final product, not the AM service provider. However, the AM provider must ensure the guide, as delivered, is compatible with standard sterilization methods. Both 316L ve Ti-6Al-4V are readily compatible with steam autoclaving, the most common method for reusable surgical instruments. The cleaning process must effectively reduce bioburden to allow for successful sterilization.
Supplier Capability:
Successfully navigating these intricate post-processing steps requires significant expertise, specialized equipment, and robust quality management systems (QMS), particularly for tibbi̇ ci̇haz manufacturing which often requires adherence to standards like ISO 13485. When selecting a metal 3D printing service provider, procurement managers must evaluate their in-house post-processing capabilities or their network of qualified partners for heat treatment metal AM, surface finishing medical devices, hassas CNC machining 3D prints, and validated cleaning and sterilization surgical tools preparation.
Companies like Met3dp, focusing on integrated solutions from high-quality ürünler (including printers and powders) to application support, understand the importance of the entire workflow. While specific post-processing services offered may vary, a competent provider will manage or coordinate these steps to deliver a finished component meeting all specifications. Failure to adequately plan for and execute post-processing can lead to delays, unexpected costs, and potentially unusable parts, undermining the benefits of using metal AM için surgical drill guides.
Navigating Challenges: Overcoming Hurdles in Metal 3D Printing Surgical Guides
Bir yandan metal katkılı üretim offers significant advantages for producing surgical drill guides, the technology is not without its challenges. Recognizing potential hurdles and understanding how experienced manufacturers mitigate them is crucial for successful implementation. Engineers, designers, and procurement teams should be aware of these common issues to collaborate effectively with their AM service provider and ensure the final product meets expectations for quality, performance, and safety.
Common Challenges and Mitigation Strategies:
- Warping and Distortion (Residual Stress):
- Meydan okumak: The rapid heating and cooling inherent in layer-by-layer fusion builds up internal stresses within the metal part. Upon removal from the build plate or during post-processing heat treatments, these stresses can cause the guide to warp, distort, or deviate from the intended dimensions. Residual stress AM is a primary concern, especially with materials like Ti-6Al-4V.
- Hafifletme:
- Simulation: Using thermal simulation software during the build preparation phase to predict stress accumulation and optimize part orientation and support structures.
- Optimized Build Strategy: Careful selection of scan patterns, laser/beam parameters, and layer thickness to manage heat input and cooling rates.
- Sağlam Destek Yapıları: Well-designed supports anchor the part effectively during printing, resisting deformation forces.
- Stress Relief Heat Treatment: Applying a validated post-print heat treatment cycle (often before removal from the build plate) is the most effective way to relieve residual stresses and ensure dimensional stability.
- Malzeme Seçimi: While both 316L and Ti64 experience stress, the specific parameters and heat treatments differ.
- Incomplete Powder Removal:
- Meydan okumak: Unfused metal powder can become trapped in narrow internal channels (e.g., for irrigation), complex lattice structures, or small crevices within the guide design. Powder removal challenges are significant because trapped powder compromises biocompatibility, can interfere with function, and adds unwanted weight.
- Hafifletme:
- DfAM: Designing channels with sufficient diameter, smooth pathways, and accessible entry/exit points or drainage holes specifically for powder removal. Avoiding features known to trap powder.
- Optimized Depowdering Processes: Utilizing specialized equipment like vibrating stations, ultrasonic assistance during cleaning, and targeted compressed air/vacuum systems.
- Teftiş: Implementing methods to verify complete powder removal, potentially including visual inspection with borescopes or even CT scanning for highly critical or complex internal geometries.
- Achieving Consistent and Required Surface Finish:
- Meydan okumak: As-printed surfaces are relatively rough and variable depending on orientation. Achieving the smooth, cleanable surface finish required for surgical instruments necessitates effective post-processing, which can be complex and labor-intensive. Support removal can also leave undesirable marks.
- Hafifletme:
- DfAM: Orienting the part to achieve the best possible as-printed finish on critical surfaces and designing supports for minimal impact and easy removal.
- Controlled Post-Processing: Utilizing appropriate and validated surface finishing techniques (bead blasting, tumbling, polishing, electropolishing) tailored to the material and requirements.
- Skilled Labor: Support removal and manual polishing require experienced technicians.
- Process Consistency: Implementing standardized procedures and quality checks to ensure consistent surface finish across batches.
- Destek Yapısı Kaldırma Zorlukları:
- Meydan okumak: Supports, especially dense ones needed for materials like Ti-6Al-4V or for large overhangs, can be difficult and time-consuming to remove without damaging the guide’s delicate features or leaving significant witness marks.
- Hafifletme:
- DfAM: Minimizing the need for supports through smart design choices (self-supporting angles, orientation). Designing supports with specific geometries (e.g., conical points, lower density) that break away more easily or require less force. Ensuring adequate access for removal tools.
- Appropriate Removal Techniques: Using the right tools (manual tools, CNC machining, wire EDM) based on the support type and location.
- Nitelikli Teknisyenler: Experienced personnel are better able to remove supports efficiently and cleanly.
- Gözeneklilik Kontrolü:
- Meydan okumak: If printing parameters (laser/beam power, scan speed, focus, gas flow) are not perfectly optimized, or if powder quality is poor, small voids or pores can form within the printed metal. Excessive porosity control metal AM failure can compromise mechanical properties (especially fatigue strength) and potentially create sites for bacterial adhesion if surface-breaking.
- Hafifletme:
- Yüksek Kaliteli Toz: Using powder with controlled particle size distribution, high sphericity, good flowability, and high purity, such as those produced by Met3dp using advanced atomization techniques.
- Optimize Edilmiş Süreç Parametreleri: Developing and validating robust printing parameters specific to the material, machine, and part geometry. Extensive process development is key.
- Inert Atmosphere Control: Maintaining a high-purity inert gas environment (Argon or Nitrogen, depending on material) in the build chamber to prevent oxidation and contamination during melting.
- Kalite Kontrol: Implementing density checks or NDT (like CT scanning) on sample coupons or critical parts if porosity is a major concern (though less common for guides than implants). HIP processing can eliminate residual porosity but adds cost.
- Ensuring Biocompatibility and Cleanliness:
- Meydan okumak: The final guide must be demonstrably biocompatible and clean enough for sterilization. This requires not only using biyouyumlu malzemeler (316L, Ti-6Al-4V) but also ensuring that no harmful residues from printing, machining, polishing, or cleaning remain on the final part. Ensuring biocompatibility 3D prints requires rigorous process control.
- Hafifletme:
- Material Certification & Traceability: Using certified medical-grade powders with full traceability.
- Validated Cleaning Processes: Developing and validating multi-stage cleaning protocols specifically designed to remove all potential contaminants associated with the AM and post-processing workflow. Testing for cleaning efficacy (e.g., residual testing).
- Controlled Handling: Maintaining cleanliness throughout the post-processing chain.
- Biocompatibility Testing: While the base materials are known to be biocompatible, testing may occasionally be required on finished parts processed through the entire manufacturing chain, especially if novel surface treatments or processes are used, according to risk assessment based on ISO 10993.
Overcoming these challenges requires a deep understanding of materials science, AM process physics, DfAM principles, and rigorous quality control methodologies. This is why partnering with an experienced metal 3D printing service provider uzmanlaşmış tibbi̇ ci̇haz manufacturing, such as Met3dp, is often the most effective approach. Their expertise in powder production, process optimization, post-processing, and quality management systems (like those adhering to ISO 13485) allows them to proactively address these hurdles and reliably deliver high-quality, safe, and effective metal 3D printed surgical guides. Addressing these potential issues upfront in collaboration with the supplier leads to smoother project execution and better clinical tools.
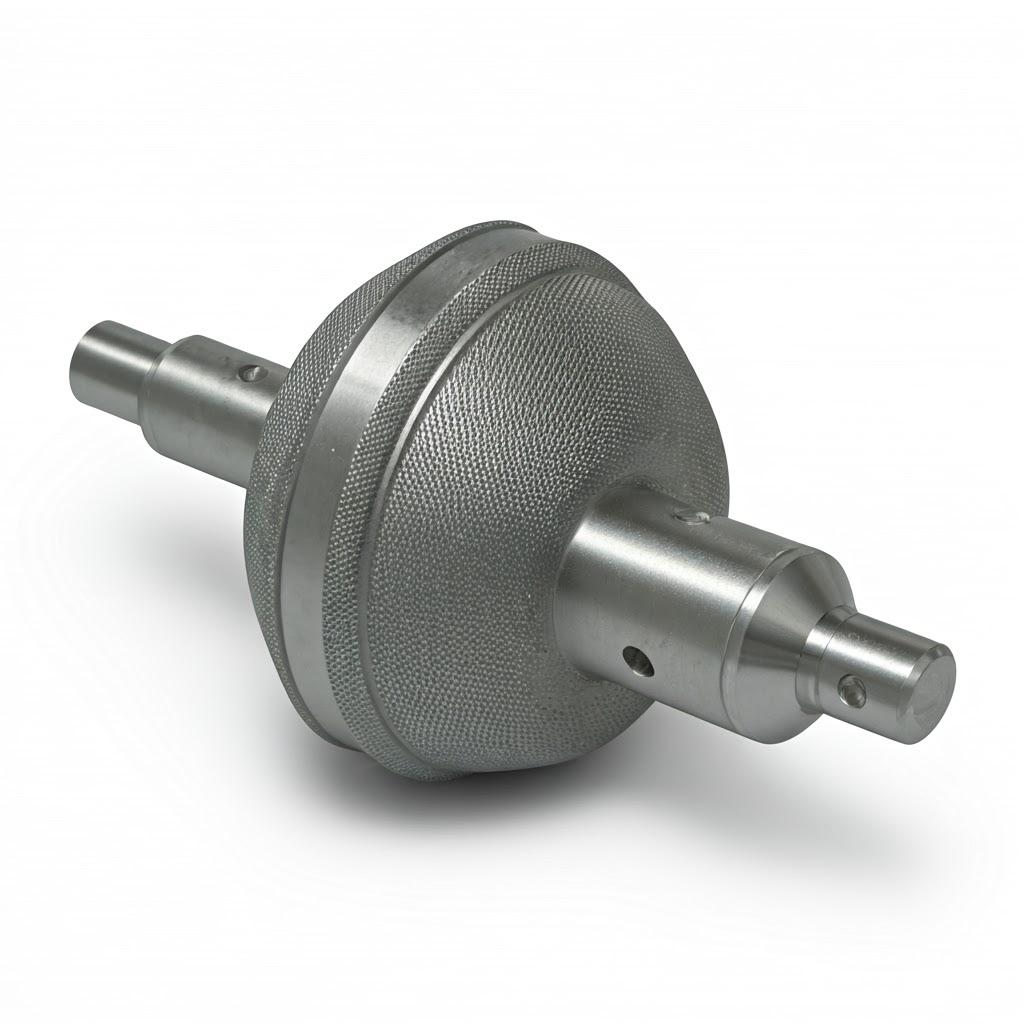
Choosing Your Partner: Selecting the Right Metal 3D Printing Service Provider for Medical Devices
The success of producing high-quality, safe, and effective metal 3D printed surgical drill guides hinges significantly on the capabilities and expertise of your chosen manufacturing partner. Not all eklemeli üretim service providers are equipped to handle the stringent requirements of the tibbi̇ ci̇haz industry. Selecting the right medical device AM supplier is a critical decision for engineers developing new instruments and procurement managers responsible for sourcing reliable manufacturing solutions. It requires careful evaluation based on specific criteria beyond just quoting the lowest price.
Key Criteria for Evaluating Metal AM Service Providers for Surgical Guides:
- ISO 13485 Certification:
- Why it Matters: This is the international standard for Quality Management Systems (QMS) for medical device manufacturing. Certification demonstrates that the provider has implemented rigorous processes for design (if applicable), production, traceability, risk management, and validation specific to medical devices. It is often a non-negotiable requirement for regulatory compliance and ensures a baseline level of quality control.
- What to Look For: Ask for proof of current ISO 13485 certification relevant to the scope of manufacturing metal medical components.
- Robust Quality Management System (QMS):
- Why it Matters: Beyond the certification itself, the provider should demonstrate a deeply ingrained culture of quality. This includes documented procedures for every stage: order entry, build preparation, machine operation, powder handling, post-processing, inspection, calibration, non-conformance management, and corrective/preventive actions (CAPA).
- What to Look For: Inquire about their QMS documentation, quality control checkpoints, process validation protocols, and how they handle deviations or non-conformances.
- Medical Device Expertise and Experience:
- Why it Matters: Manufacturing surgical instruments is different from producing industrial prototypes. A provider with specific experience in printing medical devices, particularly surgical guides or orthopedic/dental instruments, will better understand the critical requirements for biocompatibility, cleanability, surface finish, accuracy, and regulatory expectations.
- What to Look For: Ask about their track record with similar medical projects, case studies (if available and non-confidential), and staff expertise in medical materials and applications.
- Material Expertise and Certified Powders:
- Why it Matters: The provider must offer the specific medical-grade materials required (316L, Ti-6Al-4V ELI) and use powders sourced from reputable suppliers that meet relevant ASTM or ISO standards (e.g., ASTM F1580 for 316L, ASTM F136/F3001 for Ti-6Al-4V ELI). They need expertise in handling and processing these specific alloys correctly.
- What to Look For: Verify they offer certified medical-grade powders. Inquire about their powder sourcing, handling procedures (preventing cross-contamination), and material testing capabilities. Companies like Met3dp, which manufacture their own yüksek kaliteli metal tozları using advanced systems like gas atomization and PREP, demonstrate a deep commitment to material quality right from the source. You can learn more about their approach and commitment on their Hakkımızda sayfa.
- Material Traceability:
- Why it Matters: Full traceability from raw powder batch to finished part is essential for medical devices. In case of any issues, it must be possible to trace the exact materials and processes used for a specific guide.
- What to Look For: Ask about their system for tracking powder batches, associating them with specific builds and parts, and maintaining records throughout the manufacturing process.
- Validated Processes:
- Why it Matters: Key manufacturing processes, especially printing, heat treatment, and cleaning, must be validated to ensure they consistently produce parts meeting specifications. Process validation provides objective evidence that the process reliably delivers the intended results.
- What to Look For: Inquire about their approach to process validation (IQ/OQ/PQ – Installation/Operational/Performance Qualification) for their AM machines and critical post-processing steps like cleaning protocols designed for medical device applications.
- Kapsamlı İşlem Sonrası Yetenekleri:
- Why it Matters: As discussed, post-processing is critical. An ideal partner has strong in-house capabilities or tightly managed partnerships for necessary steps like stress relief, support removal, HIP (if needed), CNC machining for critical tolerances, various surface finishing options (surface finishing medical devices), and validated cleaning.
- What to Look For: Assess their range of post-processing services, equipment, and expertise. Understand which steps are done in-house versus outsourced, and how quality is managed for outsourced processes.
- Metrology and Inspection Capabilities:
- Why it Matters: The provider must have the necessary equipment (CMM, 3D scanners, surface profilometers) and expertise to accurately measure and verify that the finished guides meet all dimensional and surface finish specifications.
- What to Look For: Ask about their inspection equipment, calibration schedules, and standard reporting procedures.
- Understanding of Regulatory Landscape:
- Why it Matters: While the AM provider may not be the final legal manufacturer responsible for FDA clearance or CE marking, they should understand the regulatory context and be able to provide the necessary documentation (material certs, traceability records, process validation summaries) to support regulatory submissions.
- What to Look For: Gauge their familiarity with medical device regulations and their willingness to support documentation requirements.
- Communication, Project Management, and Capacity:
- Why it Matters: Clear communication, responsive project management, and the capacity to meet required lead times are essential for a smooth partnership, especially when dealing with patient-specific instruments which often have tight surgical schedules.
- What to Look For: Evaluate their communication style during the quoting process, inquire about typical lead times, and understand their capacity for handling bulk order medical devices or urgent requests.
Selecting a partner based on these rigorous criteria ensures that your metal 3D printed surgical guides are manufactured to the highest standards of quality, safety, and performance. While cost is always a factor, compromising on quality by choosing an unqualified supplier for medical devices can have serious consequences. Investing time in supplier qualification and building a strong relationship with a knowledgeable and certified partner like Met3dp provides confidence and ensures access to cutting-edge katkı üretim çözümleri tailored for the demanding healthcare environment.
Understanding Investment: Cost Factors and Lead Times for Metal 3D Printed Surgical Guides
While the clinical benefits of precision metal 3D printed surgical guides are clear, understanding the associated costs and production timelines is crucial for budgeting, planning, and procurement. The investment required is influenced by a combination of factors related to design complexity, material choice, manufacturing processes, and order volume. Here’s a breakdown of the key drivers affecting the metal 3D printing cost medical components like surgical guides, and the typical lead times involved.
Key Cost Factors:
- Material Type and Volume:
- Malzeme Seçimi: Ti-6Al-4V powder is generally more expensive than 316L paslanmaz çelik powder. The selection significantly impacts the base material cost.
- Part Volume: The total volume of material required to print the guide, including any necessary support structures, is a primary cost driver. Larger, bulkier guides naturally cost more.
- DfAM Impact: Designs optimized using DfAM (e.g., topology optimization, lattice structures) reduce material volume and thus cost.
- Print Time (Machine Utilization):
- Build Height: Taller parts take longer to print as more layers are required. Printing multiple guides simultaneously in a single build can optimize machine time per part, potentially reducing unit cost for larger batches.
- Parça Karmaşıklığı: While AM handles complexity well, extremely intricate designs or those requiring very dense support structures can increase print time slightly.
- Katman Kalınlığı: Thinner layers improve resolution but increase the number of layers and overall print time.
- İşlem Sonrası Gereksinimler:
- Intensity Level: The extent and type of post-processing significantly impact cost. Basic stress relief, support removal, and bead blasting are standard. However, requiring extensive manual polishing, complex CNC machining for tight tolerances, or optional processes like HIP will add considerably to the final surgical guide price.
- İşçi: Manual steps like support removal and polishing are labor-intensive and contribute significantly to post-processing costs.
- Yüzey İşlemi: Achieving smoother surface finishes (e.g., electropolishing) requires additional process steps and associated costs.
- Quality Assurance and Inspection:
- Standard QA: Basic dimensional checks and visual inspection are typically included.
- Enhanced QA: Requiring more extensive inspection (e.g., full CMM reports for every part, NDT like CT scanning for internal validation) will increase costs due to the additional time and equipment usage. Documentation requirements for regulatory compliance also factor in.
- Design and Setup:
- One-Time Costs: Initial design optimization (DfAM) and build file preparation involve engineering time, which might be factored into the cost, especially for initial prototypes or complex patient-specific cases.
- Setup: Each unique build requires machine setup, which is generally amortized over the parts in the build.
- Order Volume (Economies of Scale):
- Unit Cost vs. Volume: While AM is excellent for single, patient-specific guides, there are still economies of scale. Printing multiple identical or similar guides in a single build optimizes machine utilization and can reduce the per-part cost. Procurement managers looking for wholesale surgical guides or placing bulk order medical devices can often negotiate better pricing.
- Batch Processing: Post-processing steps like heat treatment, tumbling, or bead blasting can often be performed on batches of parts, making them more cost-effective per unit at higher volumes.
Lead Time Considerations:
The total additive manufacturing lead time for a surgical guide, from final design approval to shipping, typically ranges from a few days to several weeks, depending on complexity, workload, and specific requirements.
- Design Finalization & Quoting: Initial phase, variable depending on complexity and communication.
- Build Preparation & Scheduling: Placing the part file into the build layout, optimizing orientation, generating supports, and scheduling on a machine (can be affected by queue/backlog). (Typically 1-3 days)
- Baskı: Actual machine time required to build the part. (Typically 1-4 days, depending on size/height/quantity)
- İşlem sonrası: This is often the most time-consuming phase, involving cooling, depowdering, stress relief, removal from build plate, support removal, surface finishing, cleaning, and inspection. (Typically 3-10 days, highly variable based on required steps)
- Quality Assurance & Shipping: Final checks, documentation, packaging, and shipping. (Typically 1-2 days)
Total Estimated Lead Time: ~ 1 to 3 weeks (can be expedited for urgent cases at potentially higher cost, or longer for very complex parts/finishes or high-volume orders).
It’s crucial to get a specific quote from your chosen metal 3D printing service provider, detailing all included steps and the expected timeline based on your final design files and requirements. Factors like supplier workload and shipping logistics also play a role. Understanding these cost and time drivers allows for better project planning and realistic expectation setting when incorporating metal AM into the surgical workflow.
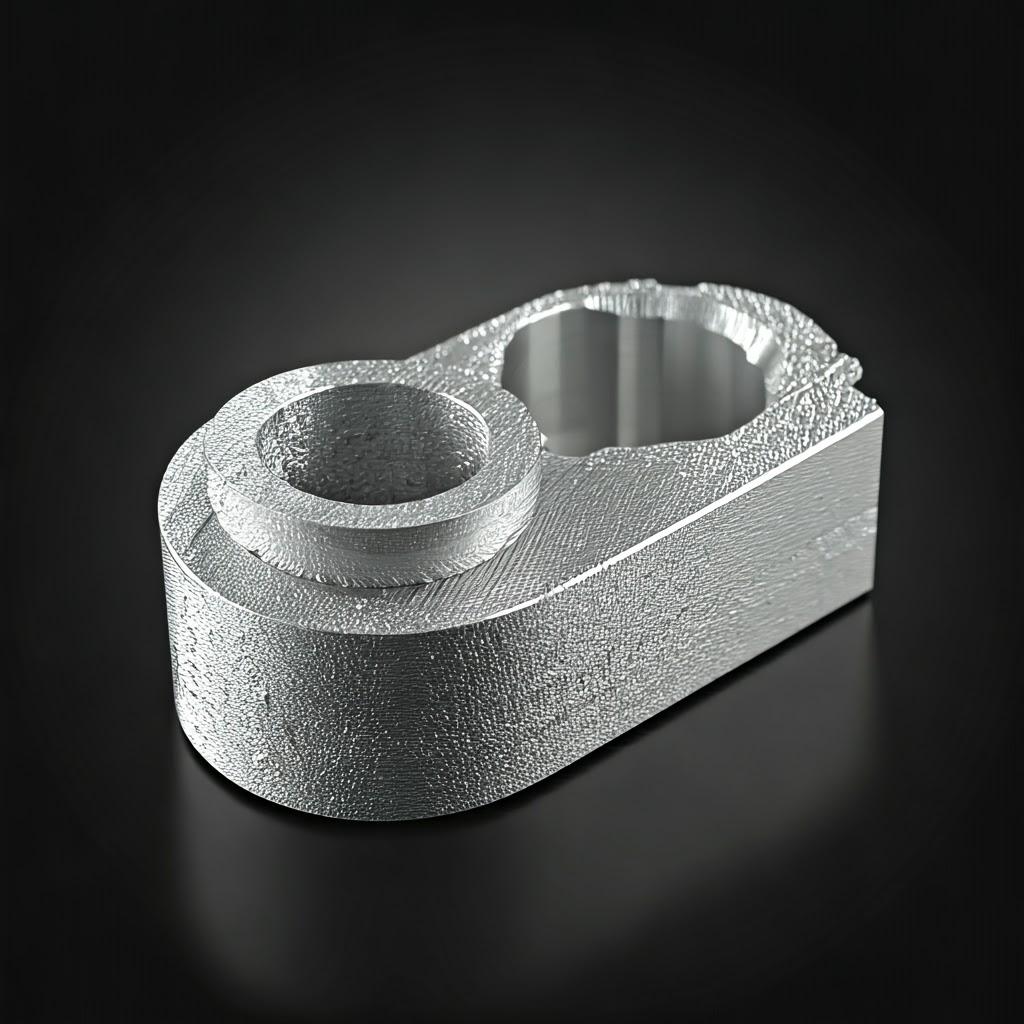
Frequently Asked Questions (FAQ) about Metal 3D Printed Surgical Guides
Here are answers to some common questions regarding the use of metal additive manufacturing for producing surgical drill guides:
1. Are metal 3D printed surgical guides truly biocompatible? Yes, provided they are manufactured correctly. The key factors are: * Malzeme: Using certified, medical-grade biocompatible metal powders like Ti-6Al-4V ELI (per ASTM F136/F3001) or 316L Paslanmaz Çelik (per ASTM F1580) is essential. These materials have a long history of safe use in medical devices. * Süreç Kontrolü: Ensuring the printing process doesn’t introduce contaminants and achieves full density (or near full density) minimizes potential issues. * Temizlik: Implementing validated cleaning processes to remove all residual powder, support material, and manufacturing fluids is critical. Improper cleaning is a primary risk to biocompatibility. * İşlem sonrası: Ensuring any surface treatments (like polishing or electropolishing) do not negatively impact biocompatibility. When produced by a qualified manufacturer adhering to standards like ISO 13485, using certified materials and validated processes, the resulting guides meet the biocompatibility requirements (e.g., ISO 10993) for their intended use (typically temporary tissue/bone contact).
2. How are metal 3D printed surgical guides sterilized? Metal surgical guides made from Ti-6Al-4V veya 316L are robust and compatible with standard hospital sterilization methods used for reusable surgical instruments. The most common method is steam autoclaving. The guides must be thoroughly cleaned according to validated procedures önce sterilization to ensure the sterilization process is effective. Compatibility with other methods like Gamma or EtO might be possible but should be confirmed based on the specific material and design, although autoclaving is typically preferred for reusable metal instruments.
3. Are metal 3D printed guides better than polymer (resin) 3D printed guides? It depends on the application. Each has advantages: * Metal Guides (Ti-6Al-4V, 316L): * Artıları: Superior strength, rigidity (less deflection during drilling), durability (reusable), high wear resistance, excellent biocompatibility, established sterilizability (autoclave). Crucial for orthopedic, spinal, or complex maxillofacial surgeries involving significant forces. * Eksiler: Higher cost, potentially heavier (though Ti64 is lightweight), longer manufacturing time, more complex post-processing. * Polymer Guides (e.g., Biocompatible Resins via SLA/DLP): * Artıları: Lower cost, faster production, often translucent (aiding visibility), good accuracy for less demanding applications. Commonly used in dental implantology. * Eksiler: Lower strength and rigidity (potential for deflection), generally single-use, may have limitations with certain sterilization methods (e.g., may not withstand high autoclave temperatures), potential long-term biocompatibility questions for some resins compared to metals. * Sonuç: Metal guides are preferred when high strength, rigidity, reusability, and durability under significant load are required. Polymer guides can be suitable for lower-force applications like many standard dental implant placements where cost and speed are primary drivers.
4. What level of accuracy can realistically be expected from a metal 3D printed surgical guide? As discussed earlier, typical dimensional accuracy for metal AM is in the range of +/- 0.1 mm to +/- 0.2 mm for smaller features, or +/- 0.2% to 0.5% for larger dimensions. This level of metal 3D printing accuracy is generally sufficient for guiding drills accurately in most surgical applications. For critical features like the inner diameter of a drill cylinder, tighter tolerances can often be achieved through optimized printing strategies or, more commonly, via post-processing steps like CNC işleme the bore to final specifications. The accuracy of the guide’s fit to the patient’s anatomy depends heavily on the quality of the initial CT/MRI scan data and the skill in the digital planning phase.
5. Is metal 3D printing an expensive option for surgical guides? Bu cost comparison surgical guides depends heavily on the alternative. * vs. Traditional CNC Machining: For highly complex, patient-specific guides, metal AM can often be more cost-effective than CNC machining because it eliminates the need for custom tooling, complex programming, and multiple setups required to machine intricate shapes from a solid block. * vs. Polymer 3D Printing: Metal AM is generally more expensive than printing guides from polymer resins due to higher raw material costs, more complex and energy-intensive printing processes, and more involved post-processing requirements. * Overall Value: While the upfront cost might be higher than polymers, the value proposition for metal guides lies in their superior performance (strength, rigidity), reusability (potentially lowering cost per surgery over time compared to single-use guides), and ability to enable complex procedures requiring robust instrumentation. The cost should be weighed against the clinical benefits of improved accuracy, potentially shorter OR times, and enhanced patient outcomes.
Consulting with an experienced provider like Met3dp can help clarify costs and determine the most suitable material and manufacturing approach for your specific surgical guide application.
Conclusion: The Future of Surgery is Precise, Personalized, and Powered by Metal AM
The integration of metal katkılı üretim into the production of surgical drill guides represents a significant advancement in surgical technology. Moving beyond the limitations of traditional manufacturing, metal 3D baskı empowers surgeons and medical device engineers with tools that offer unprecedented levels of patient-specific customization, geometric complexity, and functional performance. The ability to translate intricate digital plans derived from patient scans directly into robust, highly accurate physical guides made from proven biocompatible materials like Ti-6Al-4V ve 316L is fundamentally changing approaches to procedures across orthopedics, dental implantology, maxillofacial surgery, and beyond.
The key advantages are compelling: enhanced surgical precision leading to potentially better clinical outcomes, the capability to tackle complex anatomical challenges with tailored solutions, reduced operating times through streamlined workflows, and the potential for less invasive interventions. While challenges in design optimization, process control, and post-processing exist, they are effectively navigated by experienced manufacturers committed to quality and innovation.
Choosing the right material and, critically, the right manufacturing partner is paramount. Suppliers must possess not only the technological capabilities—advanced printers, high-quality powders, comprehensive post-processing—but also the rigorous quality systems (ISO 13485), process validation, and deep expertise required for the demanding medical field.
As metal katkılı üretim technology continues to mature, offering greater speed, accuracy, and material options, its role in creating custom surgical instruments like drill guides will only expand. It is a cornerstone technology enabling the broader shift towards personalized medicine and more efficient, effective healthcare.
Met3dp stands at the forefront of this transformation. With decades of collective expertise, industry-leading metal 3D baskı systems, advanced Powder Making System technologies delivering yüksek kaliteli metal tozları, and a commitment to partnership, Met3dp provides comprehensive solutions to accelerate the adoption of additive manufacturing in demanding fields like healthcare. We empower organizations to leverage the full potential of metal AM, turning complex challenges into innovative surgical solutions.
Explore how Met3dp’s capabilities can power your organization’s additive manufacturing goals for surgical instruments and other critical applications. Visit met3dp.com to learn more or contact our team today. The future of surgery is being built layer by layer, and metal AM is providing the foundation for a more precise and personalized approach to patient care.
Paylaş
MET3DP Technology Co, LTD, merkezi Qingdao, Çin'de bulunan lider bir katmanlı üretim çözümleri sağlayıcısıdır. Şirketimiz, endüstriyel uygulamalar için 3D baskı ekipmanları ve yüksek performanslı metal tozları konusunda uzmanlaşmıştır.
İşletmeniz için en iyi fiyatı ve özelleştirilmiş Çözümü almak için sorgulayın!
İlgili Makaleler
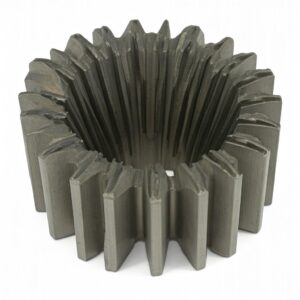
Yüksek Performanslı Nozul Kanat Segmentleri: Metal 3D Baskı ile Türbin Verimliliğinde Devrim
Daha Fazla Oku "Met3DP Hakkında
Son Güncelleme
Bizim Ürünümüz
BİZE ULAŞIN
Herhangi bir sorunuz var mı? Bize şimdi mesaj gönderin! Mesajınızı aldıktan sonra tüm ekibimizle talebinize hizmet edeceğiz.
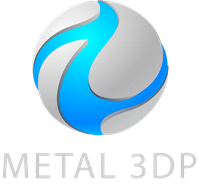
3D Baskı ve Katmanlı Üretim için Metal Tozları