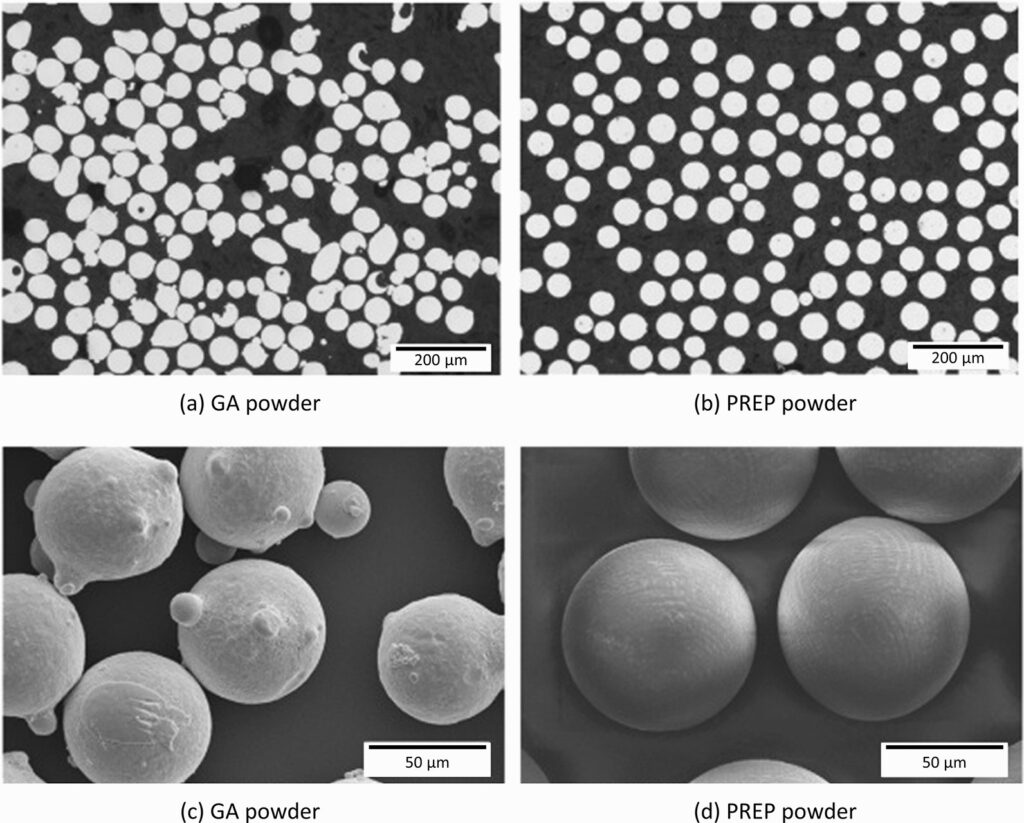
Triballoy T400 Toz: Aşırı Aşınma ve Yıpranma için Rakipsiz Alaşım
Düşük MOQ
Farklı ihtiyaçları karşılamak için düşük minimum sipariş miktarı sağlayın.
OEM & ODM
Benzersiz müşteri ihtiyaçlarını karşılamak için özelleştirilmiş ürünler ve tasarım hizmetleri sağlayın.
Yeterli Stok
Hızlı sipariş işleme ve güvenilir ve verimli hizmet sağlayın.
Müşteri Memnuniyeti
Müşteri memnuniyetini merkeze alarak yüksek kaliteli ürünler sunmak.
bu makaleyi paylaş
İçindekiler
Üstün kalite sunan bir malzeme aradığınızda aşınma direnci, korozyon direncive yüksek sıcaklık performansı, Triballoy T400 tozu piyasadaki en iyi seçeneklerden biridir. İster aşağıdaki gibi sektörlerde çalışıyor olun havacılık ve uzay, petrol ve gazveya imalatBu alaşım, en zorlu ortamlarda gelişmek için özel olarak tasarlanmıştır. Ama tam olarak ne yapar Triballoy T400 tozu öne çıkıyor? Neden bu kadar çok mühendis ve üretici kritik uygulamalar için bu alaşıma yöneliyor?
Bu kapsamlı kılavuzda, aşağıdakiler hakkında bilmeniz gereken her şeyi ortaya çıkaracağız Triballoy T400 tozu-kendisinden ki̇myasal bi̇leşi̇m onun için gerçek dünya uygulamalarive hatta diğer malzemelerle kıyaslandığında nasıl durduğu. Teknik ayrıntıları sohbet tarzında ele alacağız, böylece ister deneyimli bir mühendis olun ister malzeme bilimine yeni başlıyor olun, bu kılavuzu hem bilgilendirici hem de ilgi çekici bulacaksınız.
Genel Bakış: Triballoy T400 Tozu Nedir?
Triballoy T400 tozu bir parçası olan kobalt bazlı bir alaşımdır. Triballoy ailesi-özellikleriyle bilinen bir grup alaşım olağanüstü aşınma direnci ve sürtünme, aşınma ve korozyonun sürekli zorluk teşkil ettiği ortamlarda performans gösterme kabiliyeti. Alaşım tipik olarak geleneksel malzemelerin aşağıdakiler nedeniyle başarısız olacağı uygulamalarda kullanılır aşırı aşınma veya yüksek sıcaklıklar.
Toz olarak, Triballoy T400 gibi süreçlerde yaygın olarak kullanılmaktadır. termal püskürtme, lazer kaplamave eklemeli üretim. Onun benzersiz kompozisyon yüksek sıcaklıklarda bile sertliğini koruyabilmesini sağlar, bu da onu yüksek sıcaklık altında çalışan bileşenler için ideal hale getirir. yüksek stres ve aşındırıcı koşullar.
Triballoy T400 Toz Bileşimi ve Özellikleri
Arkasındaki sır Triballoy T400'ler olağanüstü performansında yatmaktadır ki̇myasal bi̇leşi̇m. Her bir element alaşımın genel mukavemetine, aşınma direncine ve yüksek sıcaklık özelliklerine katkıda bulunur.
Triballoy T400 Tozunun Kimyasal Bileşimi
Element | Yüzde (%) | Alaşımdaki Rolü |
---|---|---|
Kobalt (Co) | 55-65% | Yüksek sıcaklık kararlılığı, aşınma direnci ve tokluk sağlayan temel eleman. |
Krom (Cr) | 8-12% | Korozyon direncini artırır ve alaşımın genel sertliğine katkıda bulunur. |
Molibden (Mo) | 28-32% | Özellikle aşındırıcı ve yüksek sürtünmeli ortamlarda mükemmel aşınma direnci sağlar. |
Nikel (Ni) | ≤ 3% | Tokluk katar ve özellikle indirgeyici ortamlarda korozyon direncini daha da artırır. |
Silikon (Si) | ≤ 1,5% | Oksidasyon direncine yardımcı olur ve alaşımın genel üretilebilirliğini artırır. |
Triballoy T400 Tozunun Temel Özellikleri
Mülkiyet | Değer/Açıklama |
---|---|
Yoğunluk | 8,5 g/cm³ |
Erime Noktası | 1,260°C - 1,350°C |
Sertlik | 55-60 HRC (Rockwell Sertliği) |
Aşınma Direnci | Özellikle aşındırıcı ve yüksek sürtünmeli ortamlarda olağanüstü. |
Korozyon Direnci | Özellikle tuzlu ve asidik ortamlarda mükemmel. |
Termal Kararlılık | 870°C'ye kadar olan sıcaklıklarda sertliğini ve mekanik özelliklerini korur. |
Çekme Dayanımı | 900 MPa |
Oksidasyon Direnci | Yüksek, bu da onu aşırı ısı ve oksijene maruz kalma içeren uygulamalarda kullanıma uygun hale getirir. |
Sertlik | Orta düzeyde olmasına rağmen aşınma direncinde üstündür, bu da onu sürekli sürtünme altındaki uygulamalar için ideal kılar. |
Triballoy T400 Tozu Aşınmanın Yoğun Olduğu Uygulamalar İçin Neden En İyi Seçimdir?
1. Benzersiz Aşınma Direnci
Aşınmaya karşı direnç söz konusu olduğunda, Triballoy T400 tozu sayesinde üstünlük sağlar yüksek molibden içeriği. Bu, alaşımı özellikle aşağıdaki ortamlarda etkili kılar AŞINMA, Sürtünmeve Erozyon önemli endişelerdir. Bu endişeler sertlik altında bile iyi dayanmasını sağlar. yüksek stresli koşullar.
Sürekli metal-metal temasına maruz kalan bir makine parçası düşünün; zamanla çoğu malzeme aşınacaktır, ancak Triballoy T400 bu tür suistimallere çok daha uzun süre dayanabilir ve bakım maliyetleri ve artan operasyonel veri̇mli̇li̇k.
2. Üstün Korozyon Direnci
Gibi sektörlerde petrol ve gaz veya DENİZCİLİKmalzemeler genellikle aşağıdakilere maruz kalır sert kimyasallar, tuzlu suveya asi̇tler. Triballoy T400 tozu teklifler mükemmel korozyon direnciözellikle de asidik ve tuzlu ortamlar. Bu, onu aşağıdaki gibi bileşenler için güvenilir bir seçim haline getirir valf yuvaları, pompa parçalarıve rulmanlar sürekli olarak korozif maddelere maruz kalan.
3. Yüksek Sıcaklık Performansı
Triballoy T400 tozu iyi performans gösterecek şekilde tasarlanmıştır yüksek sıcaklıklarsürdürerek güç ve sertlik aşan ısıya maruz kaldığında bile 870°C. Bu, onu aşağıdaki gibi uygulamalar için tercih edilen malzeme yapar türbi̇n kanatlari, motor bileşenlerive diğer parçaların çalışması yüksek ısılı ortamlar.
4. Orta Sertlik
Bir yandan Triballoy T400 tozu geleneksel anlamda (darbeye dayanıklılık gibi) sertliği ile bilinmese de, aşağıdaki durumlarda üstünlük sağlar giymek ve AŞINMA öncelikli kaygılardır. Aşağıdakilerle başa çıkabilecek bir malzeme arıyorsanız darbe yükleri, diğer alaşımlar, örneğin Stellite 31daha uygun olabilir. Ancak, sürekli sürtünme ile karşılaşan bileşenler için, Triballoy T400 en iyi yarışmacıdır.
Triballoy T400 Toz Uygulamaları
Şimdi bu konuyu ele aldığımıza göre Kompozisyon ve Özellikler . Triballoy T400 tozuŞimdi de gerçek dünyadaki uygulamalarına bakalım. Tahmin edebileceğiniz gibi, bu malzemenin benzersiz özellikleri onu çok çeşitli sektörlerde popüler bir seçim haline getirmektedir.
Triballoy T400 Tozunun Birincil Uygulamaları
Endüstri | Uygulama |
---|---|
Havacılık ve Uzay | Yüksek sıcaklıklarda ve sürekli sürtünme altında çalışan türbin kanatları, motor bileşenleri ve rulmanlar. |
Petrol ve Gaz | Aşındırıcı sıvılara ve aşındırıcı ortamlara maruz kalan valf yuvaları, pompa parçaları ve sondaj bileşenleri. |
Denizcilik | Pervane şaftları, pompa bileşenleri ve sürekli olarak tuzlu suya ve deniz ortamına maruz kalan diğer parçalar. |
Enerji Üretimi | Buhar türbini bileşenleri, ısı eşanjörleri ve enerji santrallerinde kullanılan diğer yüksek sıcaklık parçaları. |
Kimyasal İşleme | Aşındırıcı kimyasallara ve aşındırıcı sıvılara maruz kalan vanalar, contalar ve pompa bileşenleri. |
Otomotiv | Yakıt enjektörleri, valf yuvaları ve yüksek aşınma ve ısıya maruz kalan diğer motor bileşenleri. |
Genel İmalat | Üretim süreçlerinde kullanılan kesici takımlar, ekstrüzyon kalıpları ve diğer aşınmaya dayanıklı takımlar. |
Triballoy T400 Toz Özellikleri, Boyutları, Kaliteleri ve Standartları
Seçerken Triballoy T400 tozu bir sonraki projeniz için, aşağıdaki hususları anlamak önemlidir spesifikasyonlar, boyutlarıve notlar mevcuttur. Bu ayrıntılar, özel gereksinimlerinize bağlı olarak malzemenin performansını büyük ölçüde etkileyebilir.
Şartname | Detaylar |
---|---|
Parçacık Boyutu | Uygulamaya bağlı olarak tipik olarak 15 ila 53 mikron arasında değişir (örn. termal sprey, katkılı üretim). |
Toz Morfolojisi | Termal püskürtme ve katkılı üretim proseslerinde optimum akışkanlık için küresel partiküller. |
ASTM Standartları | Tıbbi ve endüstriyel uygulamalarda kullanılan kobalt bazlı alaşımlar için ASTM F75. |
ISO Standartları | Tıbbi implantlarda kullanılan kobalt-krom-molibden alaşımları için ISO 5832-12. |
UNS Numarası | UNS R40010 |
Sertlik Aralığı | 55-60 HRC, uygulamaya ve ısıl işleme bağlı olarak. |
Bu spesifikasyonlar aşağıdakileri sağlar Triballoy T400 tozu karşılar titiz talepler gibi sektörlerin havacılık ve uzay, otomotivve petrol ve gaz.
Triballoy T400 Tozu Tedarikçileri ve Fiyatlandırması
Uzmanlaşmış doğası göz önüne alındığında Triballoy T400 tozu'den temin etmek çok önemlidir. güveni̇li̇r tedari̇kçi̇ler Malzemenin kalitesini ve tutarlılığını garanti edebilen tedarikçiler. Aşağıda, en iyi tedarikçilerden bazılarını ve tipik fiyat bilgilerini listeledik.
Triballoy T400 Toz Tedarikçiler ve Fiyatlandırma
Tedarikçi | Fiyat Aralığı (kg başına) | Notlar |
---|---|---|
Kennametal | $350 – $450 | Yüksek performanslı uygulamalar için Triballoy tozları da dahil olmak üzere kobalt bazlı alaşımların lider tedarikçisi. |
Oerlikon Metco | $360 – $470 | Özellikle termal püskürtme ve katkılı üretim için gelişmiş malzemelerle tanınır. |
Marangoz Teknolojisi | $370 – $480 | Havacılık, enerji ve sanayi sektörleri için yüksek performanslı metaller konusunda uzmanlaşmıştır. |
Höganäs AB | $380 – $490 | Aşınma direnci uygulamaları için Triballoy T400 de dahil olmak üzere çok çeşitli metal tozları sunar. |
Toz Alaşım Şirketi | $360 – $470 | Özellikle termal püskürtme ve lazer kaplama için yüksek kaliteli Triballoy tozları sağlar. |
Çoğu yüksek performanslı alaşımlarda olduğu gibi, Triballoy T400 tozu daha yaygın malzemelere göre daha yüksek fiyatlıdır. Ancak, onun uzatılmış hizmet ömrü ve güvenilirlik zorlu koşullarda genellikle daha düşük bakım maliyetleriBu da onu uzun vadede uygun maliyetli bir seçenek haline getirir.
Triballoy T400 Tozunun Artıları ve Eksilerinin Karşılaştırılması
Karar vermeden önce Triballoy T400 tozu uygulamanız için doğru olup olmadığını tartmak çok önemlidir. avantajlar ve sınırlamalar. Aşağıda, ana hatlarıyla profesyoneller ve eksileri bu yüksek performanslı alaşımın.
Triballoy T400 Tozunun Avantajları
Avantaj | Neden Önemli |
---|---|
Olağanüstü Aşınma Direnci: Aşınma ve erozyona birçok alaşımdan daha iyi dayanır. | Kesici takımlar, türbin kanatları ve valf yuvaları gibi yüksek aşınma uygulamaları için mükemmeldir. |
Yüksek Sıcaklık Kararlılığı: 870°C'ye kadar sıcaklıklarda sertliğini ve mukavemetini korur. | Motorlar, türbinler ve diğer yüksek sıcaklıklı ortamlardaki bileşenler için idealdir. |
Korozyon Direnci: Asidik ve tuzlu ortamlarda korozyona karşı dayanıklıdır. | Petrol ve gaz, kimyasal işleme ve denizcilik endüstrilerindeki uygulamalar için uygundur. |
Toz Formunda İyi Akışkanlık: Küresel partiküller termal spreyde pürüzsüz uygulama sağlar. | Uygulamayı kolaylaştırır ve kaplama ve giydirme işlemlerinde tutarlı sonuçlar sağlar. |
Uzun Hizmet Ömrü: Sık değiştirme ihtiyacını azaltarak genel bakım maliyetlerini düşürür. | Özellikle havacılık ve enerji üretimi gibi arıza süresinin pahalı olduğu sektörlerde faydalıdır. |
Triballoy T400 Tozunun Sınırlamaları
Sınırlama | Bu Neden Bir Zorluk |
---|---|
Pahalı: Daha yaygın aşınmaya dayanıklı malzemelere kıyasla daha yüksek maliyet. | Düşük talepli uygulamalar veya bütçe bilincine sahip projeler için uygun maliyetli olmayabilir. |
Orta Sertlik: Yüksek darbe dayanımı gerektiren uygulamalar için ideal değildir. | Stellite gibi diğer alaşımlar, yüksek darbe yükleri içeren uygulamalar için daha uygun olabilir. |
İşlenmesi Zor: Yüksek sertlik, işlemeyi zorlaştırabilir. | Üretim maliyetlerini ve teslim sürelerini artırabilecek özel araçlar ve süreçler gerektirir. |
Sınırlı Kullanılabilirlik: Tüm bölgelerde veya büyük miktarlarda her zaman hazır bulunmaz. | Tedarikçiye ve talebe bağlı olarak daha uzun teslim sürelerine neden olabilir. |
Triballoy T400 Toz Hakkında SSS
Daha iyi anlamanıza yardımcı olmak için Triballoy T400 tozuBu yüksek performanslı malzeme hakkında en sık sorulan bazı soruların yanıtlarını derledik.
Soru | Cevap |
---|---|
Triballoy T400 tozu ne için kullanılır? | Triballoy T400 tozu, yüksek aşınma, yüksek sıcaklık uygulamaları için havacılık, petrol ve gaz ve enerji üretimi gibi endüstrilerde kullanılır. |
Triballoy T400 tozunun maliyeti nedir? | Fiyatlandırma, tedarikçiye ve sipariş boyutuna bağlı olarak genellikle kilogram başına $350 ile $490 arasında değişmektedir. |
Triballoy T400 tozu eklemeli imalatta kullanılabilir mi? | Evet, Triballoy T400 tozu, lazer kaplama ve toz yataklı füzyon gibi eklemeli üretim süreçlerinde yaygın olarak kullanılır. |
Triballoy T400 tozu hangi sektörlerde yaygın olarak kullanılır? | Havacılık, petrol ve gaz, denizcilik, otomotiv ve enerji üretimi endüstrileri, aşınma ve yüksek ısıya maruz kalan bileşenler için Triballoy T400 tozunu sıklıkla kullanır. |
Triballoy T400 tozunu aşınmaya karşı dirençli kılan nedir? | Yüksek molibden içeriği, özellikle önemli sürtünmenin olduğu aşındırıcı ortamlarda mükemmel aşınma direnci sağlar. |
Triballoy T400 tozu manyetik midir? | Hayır, Triballoy T400 tozu genellikle manyetik değildir, bu da onu manyetik olmayan özellikler gerektiren uygulamalar için uygun hale getirir. |
Triballoy T400 tozu diğer kobalt alaşımlarına kıyasla nasıldır? | Diğer kobalt bazlı alaşımlarla karşılaştırıldığında Triballoy T400, aşınma direnci ve yüksek sıcaklık performansında üstündür ancak işlenmesi daha zor olabilir. |
Triballoy T400 tozu kullanmanın başlıca avantajları nelerdir? | Başlıca avantajları arasında olağanüstü aşınma direnci, yüksek sıcaklık kararlılığı ve zorlu ortamlarda mükemmel korozyon direnci yer alır. |
Sonuç: Triballoy T400 Tozu Bir Sonraki Projeniz İçin Uygun mu?
Sunulan malzemeler söz konusu olduğunda olağanüstü aşınma direnci, yüksek sıcaklık kararlılığıve korozyon direnci, Triballoy T400 tozu yenilmesi zordur. Daha yüksek bir fiyat etiketi ve işlemede bazı zorluklarla birlikte gelse de performans içinde zorlu ortamlar havacılık, petrol ve gaz ve enerji üretimi gibi endüstriler için en iyi seçimdir.
Projenizde aşağıdakilerle karşılaşan bileşenler varsa sabit sürtünme, AŞINMAveya korozif ortamlar, yatırım yapmak Triballoy T400 tozu sonuçlanabilir uzun vadeli tasarruflar Bakım ve değiştirme maliyetlerini azaltarak. İster üzerinde çalışıyor olun türbi̇n kanatlari, valf yuvalarıveya kesici aletler, Triballoy T400 teslim eder güvenilirlik ve dayanıklılık en çok ihtiyaç duyduğunuz anda.
Yani, öyle mi? Triballoy T400 tozu bir sonraki projeniz için uygun mu? Eğer bir işle uğraşıyorsanız aşınmanın yoğun olduğu ortamlarcevap muhtemelen yankılanan bir Evet.!
Belki ürünlerimiz hakkında daha fazla bilgi edinmek istersiniz
Son Fiyat Alın
Met3DP Hakkında
Ürün Kategorisi
SICAK SATIŞ
BİZE ULAŞIN
Herhangi bir sorunuz var mı? Bize şimdi mesaj gönderin! Mesajınızı aldıktan sonra tüm ekibimizle talebinize hizmet edeceğiz.
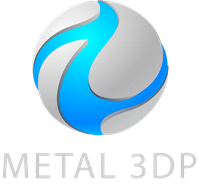
3D Baskı ve Katmanlı Üretim için Metal Tozları