High-Temp Turbine Shrouds
İçindekiler
Introduction – The Critical Role of High-Temperature Turbine Shrouds in Jet Engines
The relentless pursuit of efficiency and power in jet engines demands components capable of withstanding increasingly extreme conditions. Among these critical parts, the high-temperature turbine shroud stands as a linchpin, playing a vital role in directing the flow of combustion gases across the turbine blades. These intricate components, often operating in environments exceeding 1000°C, are subjected to immense thermal stress, oxidation, and creep. Their precise design and material selection are paramount to engine performance, fuel efficiency, and overall operational safety. Traditionally manufactured through complex and often time-consuming processes like casting and machining, turbine shrouds are now experiencing a transformative shift with the advent of metal additive manufacturing. This innovative technology offers unprecedented design freedom, material optimization, and the potential for enhanced performance characteristics. As industries like aerospace and power generation continue to push the boundaries of engine technology, the role of advanced manufacturing techniques, particularly metal 3D baskı, in producing high-performance turbine shrouds becomes ever more significant. At Metal3DP, we understand these critical demands and are at the forefront of providing cutting-edge metal 3D printing solutions tailored for the production of complex, high-temperature components like turbine shrouds. Our expertise in advanced metal powders and state-of-the-art printing technology ensures the delivery of parts that meet the stringent requirements of demanding applications.
What are High-Temperature Turbine Shrouds Used For? – Applications Across Aerospace and Industrial Gas Turbines
High-temperature turbine shrouds are integral components in the hot section of gas turbine engines, serving several crucial functions. Primarily, they act as a stationary structural element that surrounds the rotating turbine blades. This containment is essential for maintaining the optimal flow path of the high-velocity, high-temperature combustion gases. By minimizing leakage between the stationary shroud and the rotating blades, these components significantly improve the engine’s thermodynamic efficiency, leading to increased power output and reduced fuel consumption.
Beyond flow management, turbine shrouds also play a role in:
- Thermal Barrier: They often incorporate or are coated with thermal barrier coatings (TBCs) to protect the underlying metallic structure from the extreme heat of the combustion gases, extending the lifespan of the component.
- Vibration Damping: The shroud can contribute to the overall structural integrity of the turbine stage and help dampen vibrations, ensuring smooth and reliable engine operation.
- Clearance Control: Maintaining precise clearance between the shroud and the blade tips is critical for performance. Some advanced shroud designs incorporate features for active or passive clearance control to optimize efficiency across different operating conditions.
The applications for high-temperature turbine shrouds span a range of critical industries:
- Havacılık ve uzay: In aircraft engines, these shrouds are found in both commercial and military aircraft, contributing to the thrust and efficiency of the propulsion system. The demand for lighter and more fuel-efficient aircraft drives the need for advanced shroud designs and manufacturing techniques.
- Endüstriyel Gaz Türbinleri: Used for power generation in power plants and for mechanical drive applications in the oil and gas industry, these turbines also rely on high-performance shrouds to operate efficiently and reliably under demanding conditions.
- Marine Propulsion: Large gas turbines used in naval vessels also incorporate turbine shrouds that must withstand high temperatures and corrosive marine environments.
The specific requirements for turbine shrouds can vary depending on the application, but the need for materials capable of withstanding high temperatures, significant mechanical stresses, and harsh chemical environments remains constant. Metal 3D printing offers a unique pathway to create complex shroud geometries optimized for these specific demands, using advanced materials like those offered by Metal3DP. You can learn more about our capabilities in metal 3D printing for such demanding applications on our Metal 3D Baskı sayfa.
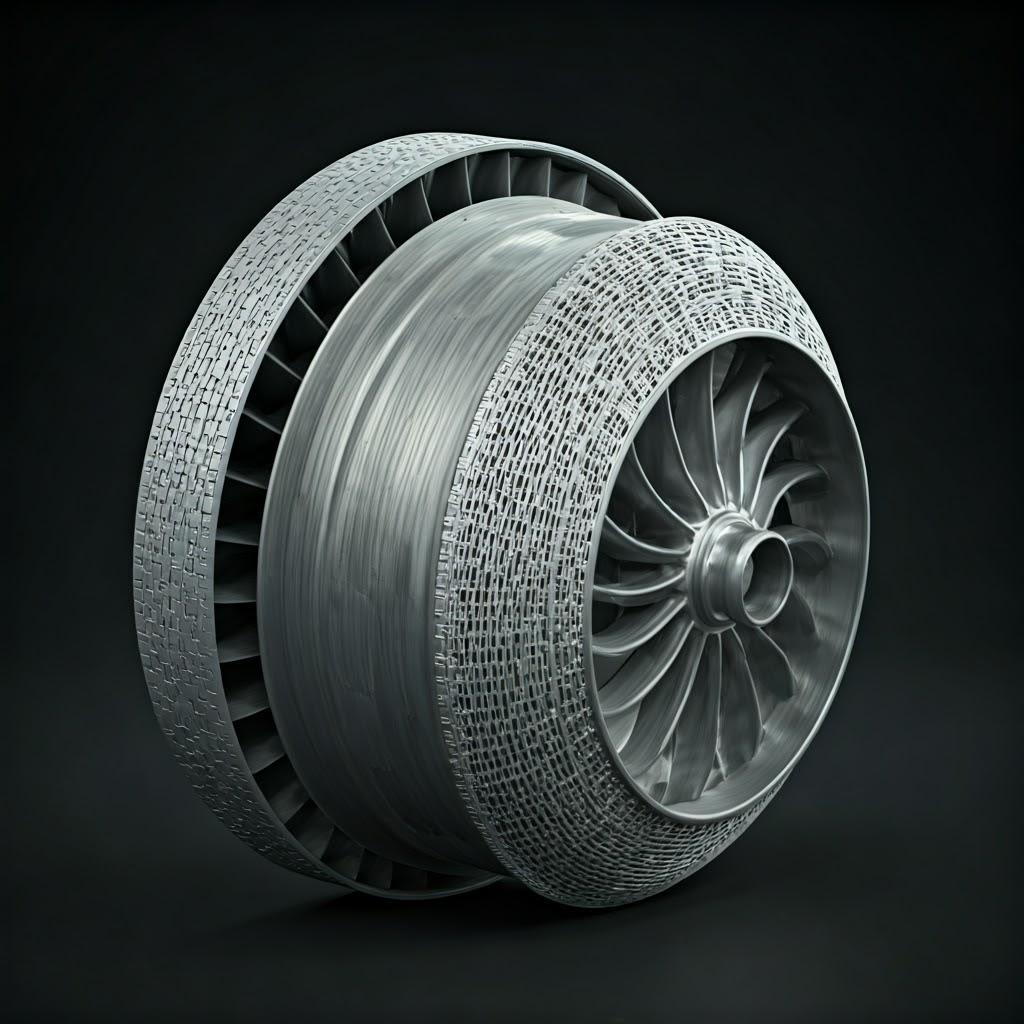
Why Use Metal 3D Printing for High-Temperature Turbine Shrouds? – Advantages of Additive Manufacturing
Adopting metal 3D printing for the production of high-temperature turbine shrouds presents a compelling array of advantages over traditional manufacturing methods:
- Tasarım Özgürlüğü ve Karmaşıklık: Additive manufacturing allows for the creation of intricate geometries that are often impossible or prohibitively expensive to produce using conventional techniques like casting or machining. This design freedom enables engineers to optimize shroud designs for improved aerodynamic performance, enhanced cooling features, and integrated functionalities. For instance, complex internal cooling channels can be incorporated directly into the shroud structure, leading to more efficient thermal management and extended component life.
- Malzeme Optimizasyonu: Metal 3D printing facilitates the processing of advanced high-temperature alloys, such as IN738LC and Hastelloy X, which are crucial for the demanding operating conditions of turbine shrouds. Furthermore, techniques like powder blending and custom alloy development can be explored to tailor material properties to specific application requirements. Metal3DP geniş bir ürün yelpazesi sunar yüksek kaliteli metal tozları specifically optimized for additive manufacturing processes.
- Azaltılmış Malzeme Atığı: Unlike subtractive manufacturing processes that involve material removal, 3D printing builds parts layer by layer, significantly reducing material waste. This is particularly beneficial when working with expensive specialty alloys used in turbine shrouds.
- Faster Prototyping and Iteration: Metal 3D printing enables rapid prototyping, allowing engineers to quickly iterate on designs and test different configurations. This accelerated development cycle can significantly reduce time-to-market for new engine designs or performance upgrades.
- Customization and Low-Volume Production: Additive manufacturing is well-suited for producing customized shrouds or smaller batch quantities cost-effectively. This is particularly advantageous for specialized aerospace applications or for producing spare parts for legacy engine systems.
- Integrated Features: 3D printing allows for the integration of multiple components into a single part, reducing the need for assembly and potential weak points. This can lead to lighter, more robust, and easier-to-maintain turbine shroud designs.
Considering these benefits, metal 3D printing emerges as a powerful tool for revolutionizing the design and manufacturing of high-temperature turbine shrouds, offering enhanced performance, reduced costs, and faster development cycles.
Recommended Materials and Why They Matter – Exploring IN738LC and Hastelloy X for Extreme Environments
The selection of appropriate materials is paramount for high-temperature turbine shrouds that must endure extreme operating conditions. Two exceptional nickel-based superalloys, IN738LC and Hastelloy X, stand out for their proven performance in such demanding environments, and are readily processable using advanced metal 3D printing techniques offered by Metal3DP.
IN738LC: This precipitation-hardened nickel-base superalloy is renowned for its excellent high-temperature strength, creep resistance, and hot corrosion resistance up to approximately 980°C (1800°F). The “LC” designation signifies low carbon content, which enhances its ductility and weldability compared to the standard IN738 alloy. Key properties that make IN738LC suitable for turbine shrouds include:
- High Creep Rupture Strength: Ability to withstand prolonged exposure to high temperatures and mechanical stress without significant deformation or failure.
- Excellent Hot Corrosion Resistance: Resistance to degradation caused by the reaction of the alloy with molten salts formed from impurities in the fuel and air at high temperatures.
- Good Oxidation Resistance: Ability to resist the formation of scale and degradation of the material’s surface when exposed to high-temperature air.
- Good Castability and Weldability: While traditionally cast, its enhanced weldability due to low carbon content makes it more amenable to repair and potentially hybrid manufacturing approaches involving 3D printing.
Hastelloy X: This nickel-chromium-molybdenum superalloy is characterized by its exceptional oxidation resistance up to approximately 1200°C (2200°F) and its good strength at elevated temperatures. It also exhibits excellent resistance to carburization and nitriding. Key properties that make Hastelloy X a strong candidate for turbine shrouds include:
- Üstün Oksidasyon Direnci: Maintains its integrity in extremely high-temperature oxidizing environments.
- Good High-Temperature Strength: Offers sufficient strength for many turbine shroud applications at elevated temperatures.
- Excellent Fabrication Characteristics: Exhibits good weldability and formability, making it well-suited for complex geometries achievable through metal 3D printing.
- Resistance to Carburization and Nitriding: Important in certain gas turbine environments where these chemical reactions can occur and degrade material properties.
The choice between IN738LC and Hastelloy X for a specific turbine shroud application depends on the precise operating conditions, including the maximum service temperature, stress levels, and environmental factors. Both alloys, available in high-quality powder form from Metal3DP, can be effectively processed using powder bed fusion technologies like Selective Electron Beam Melting (SEBM), a printing method we specialize in. To understand more about the different printing methods suitable for these materials, please visit our Baskı Yöntemleri page. The spherical morphology and controlled particle size distribution of our powders ensure optimal flowability and packing density, leading to dense, high-performance 3D printed turbine shrouds with superior mechanical properties. Sources and related content
Design Considerations for Additive Manufacturing of Turbine Shrouds – Optimizing Geometry and Support Structures
Leveraging the full potential of metal 3D printing for high-temperature turbine shrouds necessitates a shift in design thinking compared to traditional manufacturing. Design for Additive Manufacturing (DfAM) principles become paramount to optimize performance, minimize material usage, and ensure successful fabrication. Key considerations include:
- Topology Optimization: This computational approach can be employed to identify the most efficient material distribution for a given set of loads and constraints. By removing unnecessary material, lighter and potentially better-performing shroud designs can be achieved. Metal 3D printing’s ability to create complex internal lattices and intricate geometries makes topology optimization a powerful tool.
- Kafes Yapılar: Incorporating lattice structures within the shroud design can provide significant weight reduction without compromising structural integrity. These internal support networks can be tailored to specific load requirements and can also enhance heat transfer characteristics.
- Internal Cooling Channels: As mentioned earlier, additive manufacturing allows for the integration of complex internal cooling channels directly into the shroud. These channels can be designed to optimize the flow of cooling air, effectively managing the extreme temperatures encountered during engine operation and extending the lifespan of the component.
- Surface Finish Optimization: While post-processing can improve surface finish, designing features that minimize the need for extensive finishing can reduce manufacturing time and cost. Considerations include part orientation on the build platform and the use of optimized printing parameters.
- Support Structure Design: Support structures are often required in metal 3D printing to prevent part deformation during the build process and to anchor overhanging features. Careful design of these supports is crucial for ease of removal, minimizing surface damage, and reducing material waste. Factors to consider include support type (e.g., tree-like, block), contact area, and density. Metal3DP‘s extensive experience in metal additive manufacturing allows us to advise on optimal support strategies for complex geometries like turbine shrouds.
- Part Orientation: The orientation of the shroud on the build platform can significantly impact surface finish, support requirements, and the overall build time. Careful consideration of the part’s geometry and critical features is necessary to determine the most advantageous orientation.
- Wall Thickness and Feature Size: Minimum wall thicknesses and feature sizes are dictated by the capabilities of the chosen printing technology and material. It’s essential to design within these limitations to ensure successful printing and the structural integrity of the final part.
By thoughtfully addressing these design considerations, engineers can harness the unique capabilities of metal 3D printing to create high-temperature turbine shrouds with enhanced performance, reduced weight, and optimized manufacturing processes.
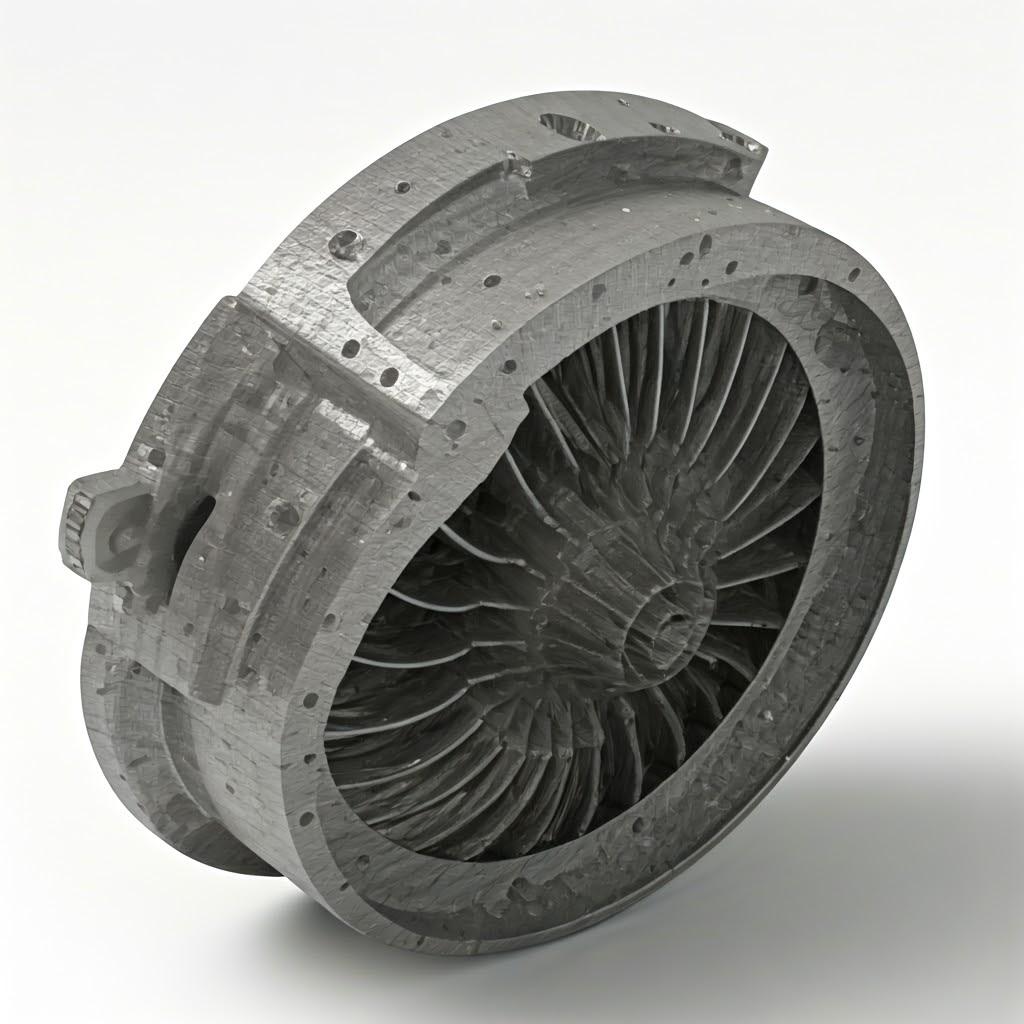
Achieving Precision: Tolerance, Surface Finish, and Dimensional Accuracy in 3D Printed Shrouds
In the demanding realm of aerospace and industrial gas turbines, the precision of components like turbine shrouds is paramount for ensuring optimal engine performance and safety. Metal 3D printing technologies have made significant strides in achieving tight tolerances, good surface finishes, and high dimensional accuracy. However, it’s crucial to understand the factors influencing these aspects:
- Tolerance: The achievable tolerance in metal 3D printing depends on several factors, including the printing technology (e.g., DMLS, SLM, EBM), the material being used, and the complexity and size of the part. Generally, tolerances in the range of ±0.1 to ±0.05 mm can be achieved for critical features. Post-processing techniques like CNC machining can further refine tolerances when necessary. Metal3DP‘s advanced SEBM technology is known for its high accuracy and ability to produce dimensionally precise parts.
- Yüzey İşlemi: The as-built surface finish in metal 3D printing is typically rougher compared to conventionally machined surfaces due to the layer-by-layer manufacturing process and the partially sintered powder particles. Surface roughness values (Ra) can range from 5 to 20 µm depending on the printing parameters and material. Post-processing methods such as polishing, grit blasting, and machining can be employed to achieve smoother surface finishes as required by the application. For turbine shrouds, a smooth internal surface is often desired to minimize flow losses.
- Boyutsal Doğruluk: Dimensional accuracy refers to the degree to which the printed part matches the intended design dimensions. Factors affecting accuracy include machine calibration, material shrinkage during solidification, and thermal gradients during the build process. Careful process control and optimized printing parameters are essential to maximize dimensional accuracy. Simulation tools can also be used to predict and compensate for potential distortions.
Özellik | Typical Achievable Range (Metal 3D Printing) | Factors Influencing | Son İşleme Seçenekleri | Relevance to Turbine Shrouds |
---|---|---|---|---|
Hoşgörü | ±0.05 – ±0.1 mm | Technology, material, part size, complexity | CNC Machining, Grinding | Critical for proper fitment with turbine blades and sealing efficiency. |
Surface Roughness (Ra) | 5 – 20 µm | Layer thickness, powder size, printing parameters | Polishing, Grit Blasting, Machining | Smooth internal surfaces minimize flow losses; external surfaces may require specific finishes. |
Boyutsal Doğruluk | 0.1% – 0.3% of nominal dimension | Machine calibration, material shrinkage, thermal control | Measurement and Iterative Adjustments | Ensures proper integration within the engine assembly and adherence to design specifications. |
Sayfalara Aktar
Achieving the required tolerance, surface finish, and dimensional accuracy for 3D printed turbine shrouds often involves a combination of optimized printing parameters and appropriate post-processing techniques. Metal3DP possesses the expertise and equipment to deliver high-precision metal 3D printed parts that meet the stringent requirements of the aerospace and industrial gas turbine industries.
Post-Processing of 3D Printed Turbine Shrouds – Heat Treatment, Coating, and Inspection
While metal 3D printing offers significant advantages in creating complex geometries, post-processing steps are often necessary to achieve the final desired properties and functionality of high-temperature turbine shrouds. Common post-processing requirements include:
- Stress Relief and Heat Treatment: Metal 3D printed parts can have residual stresses due to the rapid heating and cooling cycles during the build process. Stress relief annealing is often performed to reduce these stresses and prevent distortion or cracking. Further heat treatments, such as solution annealing and aging for nickel-based superalloys like IN738LC and Hastelloy X, are crucial for achieving the desired microstructure and mechanical properties, including high-temperature strength and creep resistance. Metal3DP has extensive knowledge in the appropriate heat treatment cycles for the metal powders we offer.
- Destek Kaldırma: Support structures, essential for printing complex geometries, need to be carefully removed after the build is complete. The method of removal depends on the support type and the part geometry. Techniques include manual removal, machining, and chemical dissolution. Minimizing the contact area and optimizing support design during the design phase can simplify this process.
- Yüzey İşlemi: As mentioned earlier, post-processing techniques like machining, grinding, polishing, and grit blasting can be employed to improve the surface finish of the turbine shroud to meet specific requirements for aerodynamic performance or aesthetics.
- Kaplama: In many high-temperature applications, coatings are applied to enhance the performance and durability of turbine shrouds. These can include:
- Termal Bariyer Kaplamalar (TBC'ler): Applied to the hot gas path surfaces to protect the metallic substrate from extreme temperatures, allowing for higher operating temperatures and improved efficiency.
- Oxidation and Corrosion Resistant Coatings: Applied to protect the shroud from degradation due to oxidation and hot corrosion in the harsh engine environment.
- Inspection and Quality Control: Rigorous inspection is crucial to ensure that the 3D printed turbine shrouds meet the required dimensional accuracy, material integrity, and quality standards. Techniques employed can include:
- Dimensional Metrology: Using coordinate measuring machines (CMMs) or laser scanners to verify the accuracy of the part dimensions.
- Tahribatsız Muayene (NDT): Methods like dye penetrant inspection (DPI), magnetic particle inspection (MPI), ultrasonic testing (UT), and X-ray computed tomography (CT) to detect internal defects such as porosity or cracks.
The specific post-processing steps required for a 3D printed turbine shroud will depend on the material, the intended application, and the required performance characteristics. Metal3DP can provide guidance and access to a network of trusted partners for comprehensive post-processing services, ensuring the delivery of fully functional and high-quality components.
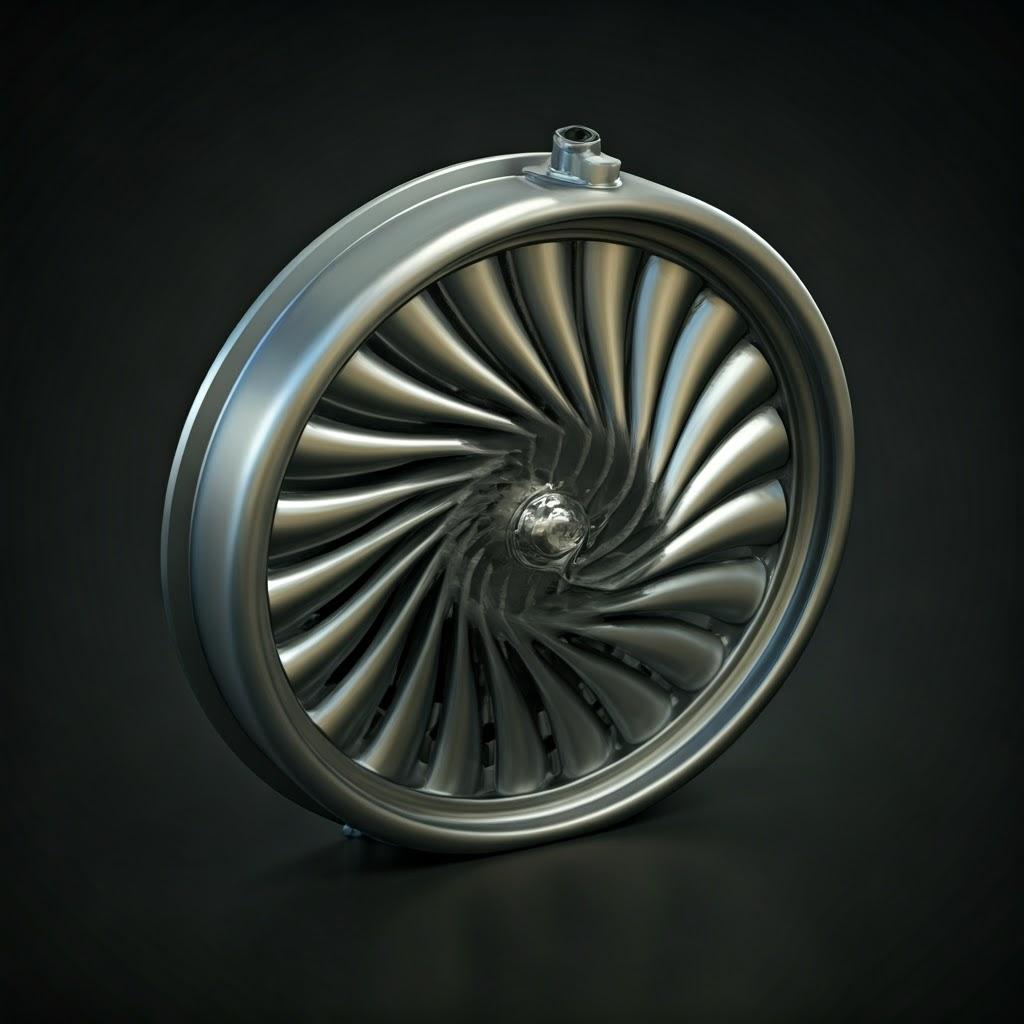
Common Challenges in 3D Printing Turbine Shrouds and How to Overcome Them – Warping, Cracking, and Porosity
While metal 3D printing offers numerous advantages, the production of complex components like high-temperature turbine shrouds can present certain challenges that need to be addressed through careful process control, design optimization, and material selection. Some common challenges include:
- Çarpıtma ve Bozulma: Thermal gradients and residual stresses during the printing process can lead to warping or distortion of the part, particularly for large or complex geometries.
- Hafifletme: Optimizing part orientation, employing effective support structures, and carefully controlling the build parameters (e.g., laser power, scan speed, bed temperature) can minimize warping. Stress relief heat treatment after printing is also crucial. Simulation tools can help predict and compensate for potential distortions.
- Çatırdıyor: High residual stresses, combined with the inherent brittleness of some high-temperature alloys at certain temperatures, can lead to cracking during or after the build process.
- Hafifletme: Preheating the build platform, optimizing laser scanning strategies to reduce thermal gradients, and employing stress relief heat treatments are essential to prevent cracking. Selecting alloys with good hot ductility and optimizing the powder properties can also help.
- Gözeneklilik: The presence of pores within the printed part can compromise its mechanical properties, especially fatigue strength and creep resistance, which are critical for turbine shrouds. Porosity can arise from insufficient powder fusion, entrapped gas, or improper process parameters.
- Hafifletme: Using high-quality, spherical metal powders with controlled particle size distribution, optimizing laser power and scan speed, and ensuring a proper shielding gas environment are crucial for minimizing porosity. Techniques like hot isostatic pressing (HIP) can be employed as a post-processing step to further reduce porosity and enhance density. Metal3DP‘s advanced powder manufacturing processes are designed to produce powders that minimize porosity in the final printed parts.
- Destek Yapısının Kaldırılması: Removing support structures from intricate geometries like turbine shrouds can be challenging and may leave surface imperfections if not done carefully.
- Hafifletme: Designing self-supporting geometries where possible, optimizing support structure design for ease of removal, and employing appropriate removal techniques (e.g., dissolvable supports, careful machining) can mitigate this challenge.
- Yüzey İşlemi: Achieving a smooth surface finish directly from the printing process can be difficult. Rough surfaces can lead to increased friction and reduced aerodynamic efficiency in turbine shrouds.
- Hafifletme: Optimizing printing parameters (e.g., smaller layer thicknesses, optimized scan strategies) can improve as-built surface finish. Post-processing techniques like polishing, grinding, or machining are often necessary to achieve the desired smoothness.
Overcoming these challenges requires a deep understanding of the metal 3D printing process, material behavior, and design principles. Metal3DP‘s expertise in these areas enables us to guide our customers in effectively addressing these potential issues and achieving successful outcomes in the additive manufacturing of high-performance turbine shrouds.
How to Choose the Right Metal 3D Printing Service Provider for Turbine Shrouds – Key Evaluation Criteria
Selecting the appropriate metal 3D printing service provider is a critical decision for companies seeking to leverage additive manufacturing for high-temperature turbine shrouds. The right partner can ensure the successful production of high-quality, performance-critical components. Here are key evaluation criteria to consider:
- Material Capabilities: Ensure the service provider has experience processing the specific high-temperature alloys required for your application, such as IN738LC and Hastelloy X. Verify their expertise in optimizing printing parameters for these materials to achieve desired mechanical properties and microstructures. Metal3DP specializes in a wide range of yüksek kaliteli metal tozları, including those ideal for turbine shroud applications.
- Baskı Teknolojisi: Different metal 3D printing technologies (e.g., DMLS/SLM, EBM) have varying strengths and limitations in terms of achievable accuracy, surface finish, and build volume. Understand the technology the provider utilizes and whether it is well-suited for the size, complexity, and performance requirements of your turbine shrouds. Metal3DP utilizes advanced SEBM technology known for its accuracy and reliability. You can learn more about different baskı yöntemleri on our website.
- Quality Assurance and Certifications: In highly regulated industries like aerospace and power generation, robust quality assurance processes are essential. Inquire about the service provider’s certifications (e.g., AS9100 for aerospace), inspection procedures, and material traceability protocols.
- Design and Engineering Support: A strong service provider should offer design for additive manufacturing (DfAM) expertise to help optimize your turbine shroud design for the 3D printing process. This includes guidance on topology optimization, support structure design, and material selection. Metal3DP provides comprehensive solutions, including application development services.
- Post-Processing Capabilities: Understand the in-house or partnered post-processing services offered, such as heat treatment, surface finishing, and coating. Ensure they can meet the specific post-processing requirements for your turbine shrouds.
- Experience and Expertise: Evaluate the service provider’s track record and experience in producing similar high-performance components for demanding applications. Case studies and testimonials can provide valuable insights into their capabilities.
- Build Volume and Capacity: Ensure the provider has sufficient build volume and production capacity to meet your current and future needs, especially for larger turbine shroud components or serial production. Metal3DP‘s printers deliver industry-leading print volume.
- Lead Times and Pricing: Understand the typical lead times for production and obtain transparent pricing information, including material costs, printing fees, and post-processing charges.
- Communication and Collaboration: Effective communication and a collaborative approach are crucial for a successful partnership. 1 Assess the provider’s responsiveness, technical support, and willingness to work closely with your team. 1. ominfowave.com ominfowave.com
By carefully evaluating potential metal 3D printing service providers based on these criteria, you can select a partner that aligns with your specific requirements and ensures the successful production of high-quality turbine shrouds. You can learn more about Metal3DP and our commitment to quality on our Hakkımızda sayfa.
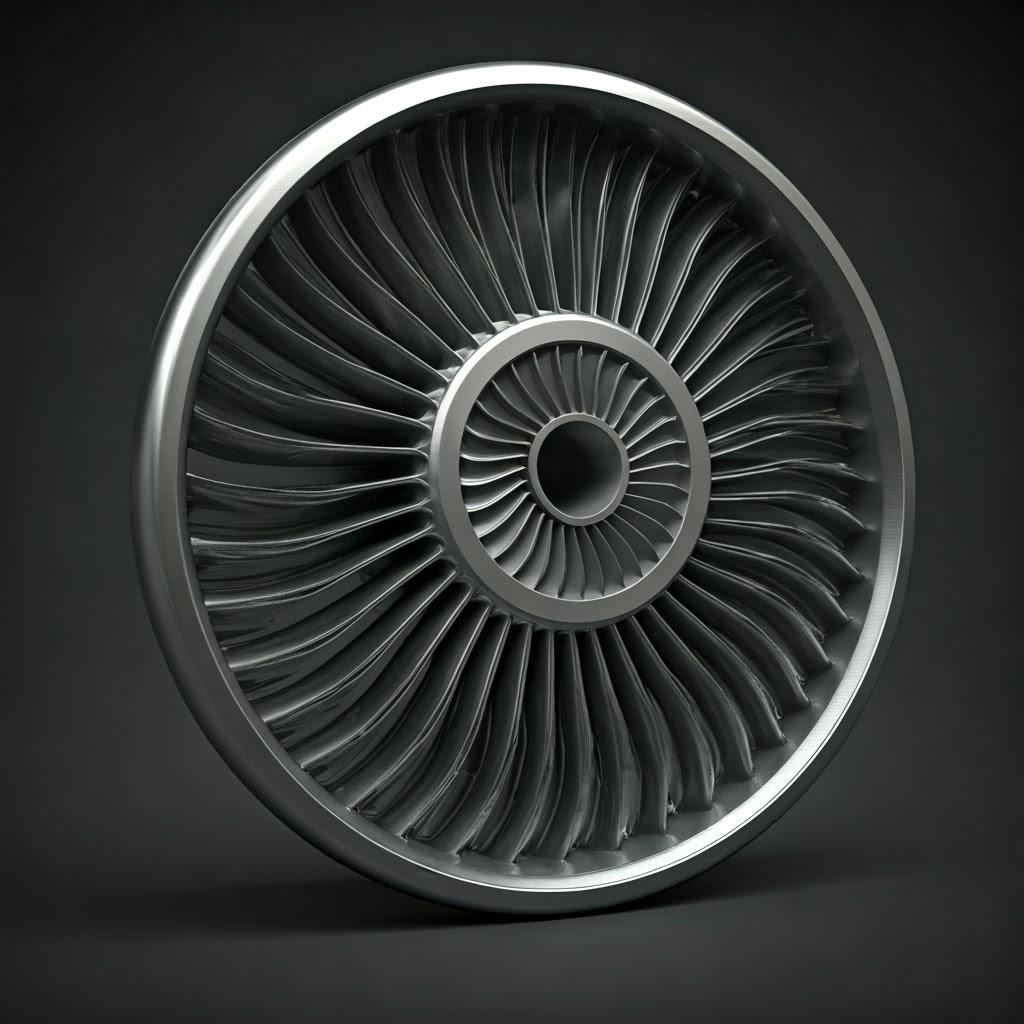
Cost Factors and Lead Time for 3D Printed High-Temperature Turbine Shrouds – Understanding the Economics
The cost and lead time associated with metal 3D printing high-temperature turbine shrouds are influenced by several interconnected factors. Understanding these factors is crucial for budgeting and project planning:
Maliyet Faktörleri:
- Malzeme Maliyetleri: High-performance nickel-based superalloys like IN738LC and Hastelloy X are inherently expensive. The volume of material required for the shroud and support structures significantly impacts the overall cost.
- Baskı Süresi: The duration of the printing process is a major cost driver. Factors influencing print time include the part’s volume, complexity, layer height, and the chosen printing technology. Larger and more intricate shrouds will typically require longer build times, increasing machine usage costs.
- Machine Usage and Overhead: Service providers factor in the cost of operating and maintaining their 3D printing equipment, as well as general overhead expenses.
- İşlem Sonrası Maliyetler: The extent of post-processing required (e.g., heat treatment, support removal, surface finishing, coating, inspection) will contribute to the overall cost. Complex post-processing steps can be time-consuming and may involve specialized equipment or external vendors.
- Design and Engineering Fees: If you require design optimization or engineering support from the service provider, these services will also factor into the cost.
- Quantity and Scale: While 3D printing can be cost-effective for low to medium volumes and customized parts, the unit cost may decrease with larger production runs due to economies of scale in material procurement and process optimization.
Lead Time Factors:
- Part Complexity and Size: More complex and larger turbine shrouds will generally require longer design, printing, and post-processing times.
- Malzeme Durumu: The availability of the specific metal powder can impact lead times. While Metal3DP maintains a stock of high-quality powders, lead times for specialized alloys may vary.
- Printing Queue and Capacity: The service provider’s current workload and the availability of suitable printing equipment will influence the lead time.
- Post-Processing Duration: The time required for heat treatment, surface finishing, and other post-processing steps can add significantly to the overall lead time.
- Quality Control and Inspection: Thorough inspection processes are essential but can also contribute to the lead time.
- Shipping and Logistics: The time required for shipping the finished parts to your location should also be considered.
Faktör | Maliyet Üzerindeki Etkisi | Impact on Lead Time |
---|---|---|
Malzeme | Yüksek | Orta düzeyde |
Printing Time | Yüksek | Yüksek |
Parça Karmaşıklığı | Orta düzeyde | Yüksek |
Parça Boyutu | Orta düzeyde | Orta düzeyde |
İşlem Sonrası | Orta ila Yüksek | Orta ila Yüksek |
Miktar | Decreases unit cost with scale | May increase overall lead time for large volumes |
Design/Engineering | Orta düzeyde | Orta düzeyde |
Sayfalara Aktar
Understanding these cost and lead time factors will enable you to make informed decisions when selecting a metal 3D printing service provider for your high-temperature turbine shroud needs and to plan your projects effectively. Contact Metal3DP for a detailed consultation and quotation tailored to your specific requirements.
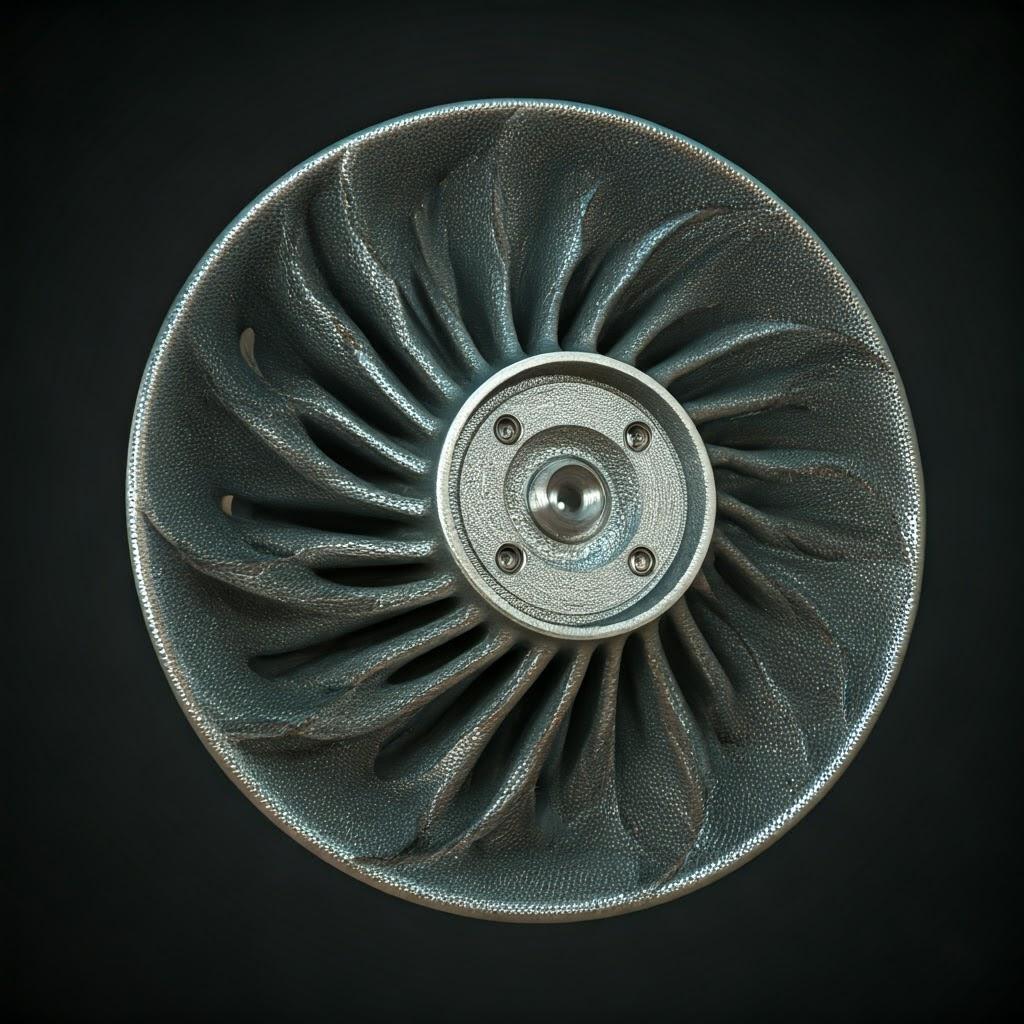
Frequently Asked Questions (FAQ) – Addressing Common Inquiries About 3D Printed Shrouds
- Q: Can metal 3D printed turbine shrouds withstand the same high temperatures and stresses as traditionally manufactured ones?
- A: Yes, when the appropriate high-temperature alloys (like IN738LC or Hastelloy X from Metal3DP) are used and the printing process is optimized, 3D printed turbine shrouds can achieve comparable or even superior high-temperature strength, creep resistance, and other critical mechanical properties. Proper post-processing, including optimized heat treatments, is crucial to achieving these performance levels.
- Q: What are the typical tolerances achievable with metal 3D printing for turbine shroud features?
- A: Typical achievable tolerances range from ±0.05 mm to ±0.1 mm, depending on the printing technology, material, and part geometry. For critical dimensions, post-processing techniques like CNC machining can be employed to achieve tighter tolerances if required. Metal3DP‘s SEBM technology offers high dimensional accuracy.
- Q: Is surface finishing always necessary for 3D printed turbine shrouds?
- A: The necessity of surface finishing depends on the specific application and the required performance. For internal flow surfaces, a smoother finish can improve aerodynamic efficiency. External surfaces may require specific finishes for coatings or integration with other components. Post-processing options range from basic polishing to precision machining.
- Q: Can complex internal cooling channels be incorporated into 3D printed turbine shrouds?
- A: Absolutely. One of the key advantages of metal 3D printing is the ability to create intricate internal geometries, including complex cooling channels optimized for efficient thermal management. This design freedom is often difficult or impossible to achieve with traditional manufacturing methods.
- Q: What is the typical lead time for producing a prototype turbine shroud using metal 3D printing?
- A: Lead times for prototypes can vary depending on the complexity and size of the shroud, material availability, and the service provider’s current workload. However, metal 3D printing generally offers significantly faster prototyping compared to traditional tooling-based methods, potentially reducing lead times from weeks or months to days or weeks.
Conclusion – Unleashing the Potential of Metal 3D Printing for Advanced Turbine Shroud Manufacturing
Metal 3D printing stands as a transformative technology for the design and manufacturing of high-temperature turbine shrouds. Its ability to create complex geometries, process advanced materials like IN738LC and Hastelloy X offered by Metal3DP, and enable rapid prototyping offers significant advantages to the aerospace, automotive, medical, and industrial manufacturing sectors. By embracing additive manufacturing, companies can achieve enhanced component performance, reduced material waste, faster development cycles, and the potential for innovative design solutions.
As a leading provider of metal additive manufacturing solutions, Metal3DP is committed to empowering our customers with industry-leading printing equipment, high-quality metal powders, and comprehensive application development services. Our expertise in Selective Electron Beam Melting (SEBM) technology and our focus on delivering accurate, reliable, and high-performance parts make us a trusted partner for organizations looking to leverage the power of metal 3D printing for critical components like turbine shrouds.
We invite you to explore the possibilities of metal additive manufacturing with Metal3DP. Contact us today to discuss your specific requirements and discover how our cutting-edge systems and materials can help you achieve your manufacturing goals and accelerate your digital transformation. Visit our website at https://met3dp.com/ to learn more about our capabilities and how we can partner with you to drive innovation in your industry.
Paylaş
MET3DP Technology Co, LTD, merkezi Qingdao, Çin'de bulunan lider bir katmanlı üretim çözümleri sağlayıcısıdır. Şirketimiz, endüstriyel uygulamalar için 3D baskı ekipmanları ve yüksek performanslı metal tozları konusunda uzmanlaşmıştır.
İşletmeniz için en iyi fiyatı ve özelleştirilmiş Çözümü almak için sorgulayın!
İlgili Makaleler
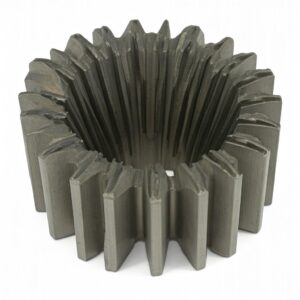
Yüksek Performanslı Nozul Kanat Segmentleri: Metal 3D Baskı ile Türbin Verimliliğinde Devrim
Daha Fazla Oku "Met3DP Hakkında
Son Güncelleme
Bizim Ürünümüz
BİZE ULAŞIN
Herhangi bir sorunuz var mı? Bize şimdi mesaj gönderin! Mesajınızı aldıktan sonra tüm ekibimizle talebinize hizmet edeceğiz.
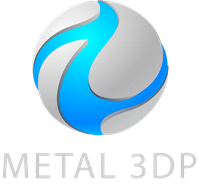
3D Baskı ve Katmanlı Üretim için Metal Tozları