Metal Enjeksiyon Kalıplamayı (MIM) Anlamak
İçindekiler
Metal enjeksiyon kalıplama (MIM), dar toleranslara sahip küçük, karmaşık metal parçalar üretmek için kullanılan bir üretim sürecidir. MIM, plastik enjeksiyon kalıplamanın çok yönlülüğünü işlenmiş metallerin gücü ve bütünlüğü ile birleştirir. Bu makale MIM teknolojisi, uygulamaları, ekipmanı, süreci, tasarım hususları ve daha fazlası hakkında ayrıntılı bir genel bakış sunmaktadır.
Metal enjeksiyon kalıplamaya genel bakış
Metal enjeksiyon kalıplama, enjeksiyon kalıplama teknikleri kullanılarak küçük, hassas metal bileşenlerin yüksek hacimli üretimini sağlayan bir toz metalurjisi işlemidir.
MIM Nasıl Çalışır?
MIM süreci, kalıplara enjekte edilebilen bir hammadde oluşturmak için ince metal tozunun bir bağlayıcı malzeme ile karıştırılmasını içerir. Yeşil parçalar olarak bilinen kalıplanmış parçalar daha sonra bağlayıcıyı çıkarmak ve metal tozunu katı bir yapıda birleştirmek için sinterlenir. Temel adımlar şunlardır:
- Karıştırma - İnce metalik toz, homojen bir hammadde oluşturmak için bağlayıcılarla karıştırılır
- Enjeksiyon Kalıplama - Hammadde eritilir ve yeşil parçalar oluşturmak için kalıba enjekte edilir
- Debinding - Bağlayıcı, solvent, termal veya katalitik debinding yoluyla uzaklaştırılır
- Sinterleme - Sökülen parçalar metal yapıyı yoğunlaştırmak ve güçlendirmek için sinterlenir
- İkincil Operasyonlar - İşleme, delme, kılavuz çekme vb. gibi ek bitirme adımları.
MIM'in Avantajları
MIM, diğer üretim tekniklerine kıyasla çeşitli avantajlar sunmaktadır:
- Parça başına düşük maliyetle yüksek hacimli üretim
- Dar toleranslara sahip karmaşık geometriler
- Paslanmaz çelik, titanyum, tungsten, kobalt krom vb. gibi çeşitli malzemeler.
- Minimum hurda kaybı ve malzeme israfı
- Ağ şekline yakın fabrikasyon azaltıcı işleme
- Küçük parça boyutları 0,005 lbs'den 0,5 lbs'ye kadar
- Montajları birleştirerek parça konsolidasyonu
- Pürüzsüz yüzeyler ve iyi finisaj
MIM'in Sınırlamaları
Metal enjeksiyon kalıplamanın bazı sınırlamaları şunlardır:
- Yüksek başlangıç ve takım maliyetleri
- Parçalar için sınırlı boyut aralığı
- Özel ekipman gereklidir
- Daha yavaş üretim ile çok adımlı süreç
- Toz özelliklerine dayalı boyutsal sınırlamalar
- Toz akışına bağlı olarak parça geometrisindeki kısıtlamalar
MIM Uygulamaları
MIM, aşağıdaki gibi sektörlerde dar toleranslara sahip küçük, karmaşık parçaların üretiminde yaygın olarak kullanılmaktadır:
- Medikal - ortopedik implantlar, diş implantları, cerrahi aletler
- Otomotiv - motor bileşenleri, valfler, dişliler
- Havacılık ve uzay - türbin kanatları, pervaneler, nozullar
- Elektronik - konektörler, mikro dişliler, ekranlama
- Ateşli silahlar - tetikler, çekiçler, emniyetler
- Saatler - saat kasaları, bilezikler, kurma kolu
- Endüstriyel - topuzlar, bağlantı elemanları, kesici aletler
MIM, metal parça üretimi için hassas döküm, talaşlı imalat ve damgalama gibi diğer süreçlerle rekabet etmektedir.
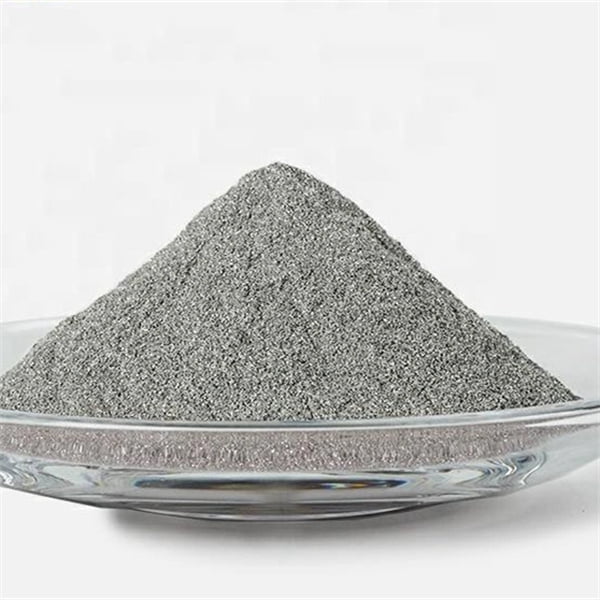
metal enjeksiyon kalıplama Ekipman Kılavuzu
MIM sürecinin her aşaması için özel ekipman gereklidir. İşte temel MIM ekipman türleri:
Ekipman | Fonksiyon |
---|---|
Toz besleyiciler | İnce tozları doğru şekilde ölçer |
Mikserler | Toz ve bağlayıcıyı homojen olarak karıştırın |
Granülatörler | Hammaddeyi kalıplama için granül haline getirme |
Enjeksiyon kalıplama makineleri | Hammaddeyi istenen şekillerde kalıplama |
Debinding fırınları | Bağlayıcıyı kalıplanmış parçalardan çıkarın |
Sinterleme fırınları | Metal yapıyı yoğunlaştırır ve güçlendirir |
Taşlama makineleri | Kapıları, rayları ve düz yüzeyleri kaldırın |
İşleme merkezleri | Sinterlenmiş parçalar için delme, tornalama, frezeleme özellikleri |
Süreci entegre etmek ve üretkenliği en üst düzeye çıkarmak için gelişmiş otomasyon, taşıma sistemleri ve kontroller kullanılır. Ekipman, malzeme, parça boyutu, üretim hacmi ve kalite gereksinimleri gibi faktörlere göre dikkatlice seçilmelidir.
Adım Adım Metal Enjeksiyon Kalıplama Süreci
MIM işleme, ince metal tozunu tamamen yoğun son kullanım bileşenlerine dönüştürmek için birden fazla adım içerir.
Adım 1 - Karıştırma
- Metal tozu ve bağlayıcı, homojen bir hammadde üretmek için bir karıştırıcıda iyice karıştırılır
- Toz partikül boyutu, şekli, dağılımı kalıplanabilirliği ve sinterlemeyi etkiler
- Bağlayıcılar enjeksiyon kalıplama sırasında akış ve yapışma sağlar
- Mumlar, PP, PE, PVC gibi termoplastikler ve bağlayıcı olarak kullanılan polimerler
- Sigma bıçaklı, Z bıçaklı, çift planet mikserler kullanılarak karıştırma yapılır
Adım 2 - Granülasyon
- Hammadde karışımı enjeksiyon kalıplama için küçük peletler halinde granüle edilir
- Malzeme akışını iyileştirir ve varil içinde ayrışmayı önler
- Granülatörler, hammaddeyi düzgün granüller halinde kesmek için dönen bıçaklar kullanır
- Granül şekli ve boyutu paketleme yoğunluğunu ve kalıplanabilirliği etkiler
Adım 3 - Enjeksiyon Kalıplama
- Hammadde granülleri gerekli parça şekli ve boyutuna göre kalıplanır
- Kontrollü sıcaklık ve basınca sahip modifiye enjeksiyon kalıplama makineleri kullanır
- Hataları en aza indirmek için kalıplama parametrelerini optimize etmek önemlidir
- Yeşil parçalar olarak adlandırılan kalıplanmış parçalara şekil verilmiş ancak mukavemet kazandırılmamıştır
Adım 4 - Debinding
- Bağlayıcı, solvent, termal veya katalitik yollarla yeşil kısımlardan çıkarılır
- Solventle bağlayıcı çözme, bağlayıcıyı çözmek için kılcal hareket kullanır
- Termal debinding bağlayıcıyı bir fırında ayrıştırır
- Katalitik debinding, bir katalizör ile bağlayıcı giderimini hızlandırır
- Debinding, metal parçacıklardan oluşan gözenekli bir yapıya sahip kahverengi parçalar oluşturur
Adım 5 - Sinterleme
- Kahverengi parçalar kontrollü atmosfer fırınında sinterlenir
- Metal parçacıklar arasındaki bağlar difüzyon ve kütle taşınımı yoluyla oluşur
- Sinterleme sırasında 96-99%'ye kadar neredeyse tam yoğunluk elde edilir
- Atmosfer, sıcaklık, zaman kusurları önlemek için optimize edilmiştir
- Kalıplama sırasında hesaba katılan sinterleme büzülmesi
Adım 6 - İkincil İşlemler
- Tavlama, işleme, delme, kaplama gibi ek metal işleme adımları
- Tavlama, sinterlemeden kaynaklanan iç gerilimleri azaltır
- CNC işleme yollukları kaldırır, yüzeyleri pürüzsüzleştirir, özellikler ekler
- İyileştirme veya korozyon koruması için uygulanan kaplama ve boyama
MIM süreci, plastik enjeksiyon kalıplama ve toz metalürjisinin avantajlarını birleştirerek karmaşık, yüksek hassasiyetli metal parçalar sağlar.
MIM Parçaları için Tasarım Hususları
MIM, talaşlı imalatla mümkün olmayan geometrik özgürlükler sağlar, ancak belirli tasarım hususları gerektirir:
- Duvar kalınlığı - Bazı tozlar 6 mm'ye kadar duvarları desteklerken tipik aralık 0,3 - 4,0 mm'dir
- Yüzey kaplaması - Dökümden daha pürüzsüz yüzey, ancak talaşlı imalat kadar ince değil; 1 - 4 μm Ra değeri MIM için tipiktir
- Boyutsal toleranslar - Parça geometrisine bağlı olarak ±0,1% ile ±0,5% arasında mikron düzeyinde hassasiyet mümkündür
- Yoğunluk - Optimize edilmiş sinterleme ile 99%'ye kadar tam yoğunluk elde edilebilir
- Geometri - Sıkışmış tozlardan kaçınmak ve bağlayıcının kaçmasına izin vermek kritik öneme sahiptir
- Taslak açıları - Parça fırlatmayı kolaylaştırmak için 1-3° çekim açılı konik duvarlar
- Yarıçaplar ve filetolar - Keskin köşeler yerine kademeli geçişler tercih edilir
- Delikler ve boşluklar - Açık delikler için minimum 0,25 - 0,5 mm çaplar
- İplikler - Kalıplanabilir ancak daha iyi doğruluk için genellikle sinterlemeden sonra işlenir
- Yüzey detayları - Kalıp aşınmasını azaltmak için ince ayrıntıları sınırlayın; kalıplama sonrası süreçler geliştirilebilir
MIM tasarımı, imalat kolaylığından ziyade performansı en üst düzeye çıkaran geometriye odaklanmalıdır. Süreç, çok parçalı montajların önemli maliyet ve ağırlık tasarruflarıyla tek bir parçada birleştirilmesini sağlar.
Metal Enjeksiyon Kalıplamada Kullanılan Malzemeler
MIM, çeşitli endüstrilerde çok çeşitli metallerden, alaşımlardan ve seramiklerden parçalar üretebilir.
Malzeme | Uygulamalar | Özellikler |
---|---|---|
Paslanmaz çelik | Tıbbi, ateşli silahlar, denizcilik | Korozyon direnci, mukavemet |
Düşük alaşımlı çelik | Otomotiv, endüstriyel | Manyetik tepki, işlenebilirlik |
Yumuşak manyetik alaşımlar | Sensörler, aktüatörler | Yüksek geçirgenlik |
Sert metal alaşımları | Kesici aletler | Aşınma direnci, sertlik |
Bakır alaşımları | Elektronik, termal | Elektriksel iletkenlik |
Alüminyum alaşımlar | Elektrik, termal | Hafiflik, iletkenlik |
Titanyum alaşımları | Havacılık ve uzay, otomotiv | Güç, biyouyumluluk |
Tungsten alaşımları | Radyasyon kalkanı | Yüksek yoğunluk |
Sermetler | Elektronik, optik | Oksidasyon direnci |
Parça işlevi, maliyet, işlem sonrası adımlar ve alaşım uyumluluğu gibi faktörler ideal MIM malzeme seçimini belirler.
MIM Tedarikçileri ve Ekipman Üreticileri
Birçok şirket küresel olarak MIM malzemeleri, hizmetleri, üretimi ve ekipmanı sunmaktadır. İşte değer zincirindeki başlıca MIM tedarikçilerinden bazıları:
Şirket | Ürünler/Hizmetler |
---|---|
BASF | Hammaddeler, bağlayıcılar |
Sandvik Osprey | Metal tozları |
Höganäs | Metal tozları |
CNPC Toz | Metal tozları |
Indo-Mim | MIM ürünleri, hizmetleri |
MPP | MIM ürünleri, hizmetleri |
ARC Grup | MIM ürünleri, hizmetleri |
Atlas Preslenmiş Metaller | MIM parça üretimi |
Epson Atmix | MIM ekipmanı |
Milacron | Enjeksiyon kalıplama makineleri |
Elnik | Sinterleme fırınları |
TCN | Debinding, sinterleme fırınları |
MIM tedarik zincirinde yer alan çok sayıda küçük bölgesel oyuncu da bulunmaktadır. MIM'i benimsemek isteyen son kullanıcılar, gerekli yeteneklere bağlı olarak malzeme tedarikçileri ve fason üreticilerle ortaklık kurabilir.
MIM Parçalarının Alternatiflere Karşı Maliyet Analizi
Burada, farklı üretim süreçleri kullanılarak 1000 parça üretmek için tahmini maliyetlerin bir karşılaştırması yer almaktadır:
Süreç | Kurulum Maliyetleri | Makine Maliyetleri | Kalıp Maliyetleri | Parça Maliyeti | Toplam (1000 parça) |
---|---|---|---|---|---|
CNC İşleme | Düşük | $100,000 | $2,000 | $50 | $52,000 |
Yatırım Döküm | Yüksek | $500,000 | $40,000 | $20 | $60,000 |
Metal Enjeksiyon Kalıplama | Yüksek | $750,000 | $100,000 | $15 | $115,000 |
Damgalama | Yüksek | $1,000,000 | $150,000 | $10 | $160,000 |
- CNC işleme düşük hacimlere, yüksek parça maliyetlerine, sınırlı karmaşıklığa sahiptir
- Hassas döküm 10.000 adede kadar olan hacimler için daha iyidir
- MIM, karmaşık geometriye sahip orta ve yüksek hacimli ürünler için avantajlıdır
- Damgalama çok yüksek takım maliyetlerine sahiptir, ancak 100 bin parçanın üzerindeki yüksek hacimlerde en düşük parça fiyatı
MIM'in diğer proseslere göre daha ekonomik hale geldiği geçiş noktası hacimlere, karmaşıklığa ve boyuta bağlıdır.
MIM Tedarikçisi veya Ortağı Seçme
Uygun maliyetli parça üretimi için yetkin bir MIM tedarikçisi veya üretim ortağı seçmek çok önemlidir. İşte dikkate alınması gereken temel noktalar:
- Teknik uzmanlık - Benzer MIM parçaları, malzemeleri ve endüstrisi ile ilgili önceden deneyim
- Kalite sistemleri - ISO 9001 sertifikası, kalite kontrol uygulamaları
- Üretim kapasitesi - Mevcut ve gelecekteki hacim gereksinimlerini karşılama becerisi
- İkincil süreçler - İşleme, damgalama, kaplama, boyama yetenekleri
- Parça optimizasyonu - Faydaları en üst düzeye çıkarmak için MIM desteği için tasarım
- Prototipleme - Tasarımları doğrulamak için hızlı prototipleme hizmetleri
- Takımlama yetenekleri - Şirket içi kalıp tasarımı ve imalatı tercih edilir
- Hammadde erişimi - Hammaddeler için yerleşik tedarik kanalları
- Ar-Ge yetenekleri - Gelişmiş malzemeler ve üretim tekniklerinde devam eden Ar-Ge
- Müşteri odaklılık - İhtiyaçlara duyarlılık ve işbirliği yaklaşımı
- Maliyet yapısı - Fiyatlandırma modeli ve öngörülen hacimler için rekabet gücü
- Lojistik - Teslim süresi gereksinimlerini karşılarken parçaları güvenilir bir şekilde teslim etme becerisi
Bu faktörlerin önceliklendirilmesi, belirli bir uygulama için doğru stratejik MIM ortağının belirlenmesine yardımcı olacaktır.
MIM Ekipmanının Kurulumu
MIM kapasitesini şirket içinde kuran şirketler için doğru ekipman kurulumu hayati önem taşır. İşte dikkate alınması gereken temel noktalar:
- MIM hattı için yaklaşık 2000 - 5000 metrekarelik alan gereklidir
- 200-600 kVA kapasiteli kararlı güç kaynağı gereklidir
- Basınçlı hava hatları 100 psi basınç için derecelendirilmiştir
- Isı, emisyon ve toz toplama için egzoz havalandırması
- Azot, proses suyu ve gaz tedariği gibi kamu hizmetleri
- Yaklaşık 20±3 °C, 50±20% sıcaklık ve nem kontrolü
- Asma katlar, yardımcı ekipman montajı için platformlar
- Vinçler, forkliftler, depolar gibi malzeme taşıma sistemleri
- Kontrol odası, izleme için bilgisayar sistemleri
- Proses güvenliği ve ekipman kullanımı konusunda personel eğitimi
- Süreç simülasyonları, kurulumu doğrulamak için test çalışmaları
- Kalibrasyon ve önleyici bakım programları
MIM ekipmanının sorunsuz çalışması için yeterli alan, yardımcı tesisler ve kontrollü koşullar şarttır. Kapsamlı test ve eğitim gerçek üretime hazırlar.
MIM Ekipman Bakımı
Tutarlı bakım, MIM üretim ekipmanının çalışma süresini ve performansını artırır. Önemli hususlar:
- Her makine için belgelenmiş önleyici bakım programı
- Malzeme dökülmeleri, sızıntılar, toz ve döküntülerin günlük olarak temizlenmesi
- Sıvı seviyelerinin, sızıntıların, olağandışı seslerin, titreşimlerin kontrol edilmesi
- Basınçların, sıcaklıkların, güç tüketiminin izlenmesi
- Isıtma, soğutma ve kontrol sistemlerinin test edilmesi
- Elekler, vidalar, variller gibi aşınan parçaların değiştirilmesi
- Bileşen yorgunluğu, hasar, hizalama için denetimler
- Çalışma saatlerine bağlı olarak düzenli yeniden inşa ve revizyonlar
- Analiz için bakım kayıtlarının izlenmesi
- Kritik bileşenler için yedek parça envanterinin depolanması
- Ekipmanın doğru kullanımı ve güvenliği konusunda eğitim
- Ekipman tedarikçilerinden zamanında servis ve destek
İyi eğitimli personel ve ekipman tedarikçileriyle işbirliği, MIM ekipmanının verimliliğini en üst düzeye çıkarırken arıza süresini en aza indirmeye yardımcı olur.
Metal Enjeksiyon Kalıplama Simülasyon Yazılımı
Simülasyon yazılımı, gerçek üretimden önce MIM sürecini dijital olarak modellemek için kullanılır. Faydaları şunları içerir:
- Kalıp dolum modellerinin tahmini ve kapı konumlarının optimizasyonu
- Kusurları önlemek için kaynak hatlarının ve hava kapanlarının belirlenmesi
- Karmaşık geometrilerde termal gradyanların ve katılaşmanın incelenmesi
- Nihai şekil üzerinde debinding ve sinterleme profili etkilerinin simülasyonu
- İmalattan önce kalıp tasarımlarının doğrulanması
- Sanal prototipleme yoluyla deneme maliyetlerinin azaltılması
- Görsel temsiller aracılığıyla personel eğitimi
Bazı ticari MIM simülasyon paketleri şunları içerir:
- MIMSIM - Sinterleme yoluyla kalıplama için entegre simülasyon
- Sigma Soft - Kalıp dolumu ve distorsiyonunun 3D FEM analizi
- Netzsch MIMPre - MIM hammaddelerinin reolojik özelliklerinin modellenmesi
- Simufact Katkı Maddesi - AM süreçlerinin çoklu fizik simülasyonu
- EOS PSW - Sinterleme ve ısıl işlem odaklı simülasyon
MIM yazılımının kullanılması süreç tutarlılığını artırır, parça kalitesini optimize eder ve fiziksel prototipleme maliyetlerini azaltır. Simülasyondan üretime entegre bir iş akışı tercih edilir.
Yaygın MIM Kusurlarının Giderilmesi
MIM parçalarındaki bazı tipik kusurlar ve potansiyel kök nedenleri şunlardır:
Kusur | Nedenler |
---|---|
Kısa atışlar | Düşük enjeksiyon basıncı, erken katılaşma |
Flaş | Aşırı paketlenmiş kalıplar, küf hasarı |
Çarpıklık | Üniform olmayan soğutma, bağlayıcı sorunları |
Çatlaklar | Hızlı sinterleme, yüksek bağlayıcı içeriği |
Gözeneklilik | Zayıf homojenizasyon, sıkışmış gazlar |
Kirlenme | Çapraz kontaminasyon, fırın atmosferi |
Boyutsal varyasyonlar | Hammadde sorunları, kalıp aşınması, büzülme |
Yüzey kusurları | Gaz gözenekliliği, sıvı metal gevrekleşmesi |
İçerikler | Kirlenmiş hammaddeler, nozul tıkanmaları |
Kusurlara neden olan proses parametrelerini izole etmek ve hammadde formülasyonu, kalıplama parametreleri, hata giderme ve sinterleme profillerini ayarlamak gibi düzeltici eylemleri gerçekleştirmek için sistematik bir kusur analizi metodolojisi kullanılmalıdır.
MIM Teknolojisinin Avantajları
MIM, diğer metal parça üretim yaklaşımlarına göre önemli avantajlar sunmaktadır:
- Karmaşıklık - Karmaşık 3D geometriler mümkün, montajları birleştirir
- Tutarlılık - Düşük parça varyansı ile yüksek oranda tekrarlanabilir süreç
- Verimlilik - Daha az hammadde atığı ile net şekle yakın üretim
- Otomasyon - Yüksek otomasyonlu süreç işçiliği azaltır
- Esneklik - Metaller, seramikler, kompozitler gibi geniş malzeme yelpazesi
- Kalite - İyi yüzey kalitesi ve mekanik özellikler
- Üretkenlik - Parça başına düşük maliyetle yüksek hacimli çıktı
- Minyatürleştirme - Ayrıntıları 10 μm'ye kadar inen mikro bileşenler
- Sürdürülebilirlik - Talaşlı imalata kıyasla enerji verimliliği
- Maliyet - Orta ve yüksek üretim hacimleri için daha düşük toplam maliyet
MIM'in benzersiz yetenekleri otomotiv, havacılık, medikal ve elektronik gibi çeşitli sektörlerde benimsenmesini sağlıyor.
Metal Enjeksiyon Kalıplamanın Sınırlamaları
Birçok faydasına rağmen, MIM'in belirli sınırlamaları vardır:
- Yüksek ilk takım yatırımı
- Tipik olarak 65 gramın altında sınırlı boyut aralığı
- CNC işlemeye göre daha düşük hassasiyet
- Süreç kontrolleri gerektiren gözeneklilik riskleri
- Toz özelliklerine göre kısıtlı malzeme seçenekleri
- İnce tozların güvenlik tehlikeleri
- Kalıplanabilirlikle ilgili parça geometrisi kısıtlamaları
- Potansiyel lottan lota değişkenlik
- Dövme malzemelere göre daha düşük mekanik özellikler
- Düşük hacimlerde sınırlı prototip üretimi
- Birçok uygulamada ikincil işleme gereksinimi
- Özel ekipman ve eğitimli operatörler gereklidir
Düşük hacimlerde üretilen çok yüksek hassasiyetli veya daha büyük metal parçalar için diğer prosesler MIM'den daha uygun olabilir.
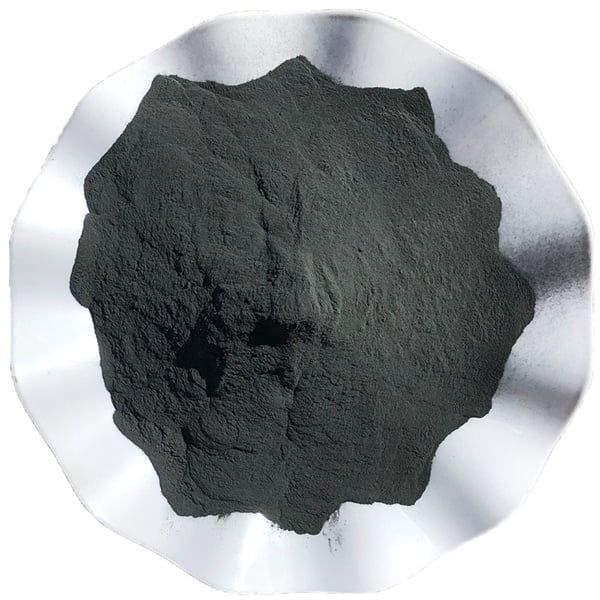
Metal Enjeksiyon Kalıplamanın Geleceği
Teknoloji ve malzemeler gelişmeye devam ettikçe MIM'in güçlü bir şekilde büyümeye devam etmesi beklenmektedir:
- Kalıplanabilirliği ve yeşil mukavemeti artırmak için yeni bağlayıcı sistemleri
- Nanokompozitler kullanılarak yeni hammadde formülasyonları
- Akım limitlerini aşan daha büyük boyutlu parçalar
- Seramik ve tungsten alaşımlarının benimsenmesinde artış
- Medikal ve elektronik sektörlerinde güçlü talep artışı
- MIM takımları yapmak için eklemeli üretim kullanımı
- Robotik ve Endüstri 4.0 entegrasyonu kullanarak otomasyon
- Zorlu ortamlarda daha fazla uygulama
- Bağlı metal biriktirme kullanarak metal 3D baskı ile yakınsama
Artan Ar-Ge ve daha kolay benimsenme ile MIM kullanımı önümüzdeki yıllarda çeşitli uygulamalarda hızla artacaktır.
Paylaş
MET3DP Technology Co, LTD, merkezi Qingdao, Çin'de bulunan lider bir katmanlı üretim çözümleri sağlayıcısıdır. Şirketimiz, endüstriyel uygulamalar için 3D baskı ekipmanları ve yüksek performanslı metal tozları konusunda uzmanlaşmıştır.
İşletmeniz için en iyi fiyatı ve özelleştirilmiş Çözümü almak için sorgulayın!
İlgili Makaleler
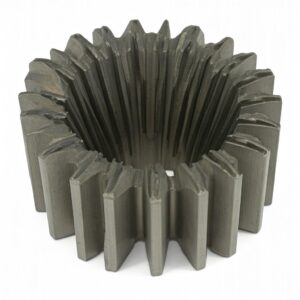
Yüksek Performanslı Nozul Kanat Segmentleri: Metal 3D Baskı ile Türbin Verimliliğinde Devrim
Daha Fazla Oku "Met3DP Hakkında
Son Güncelleme
Bizim Ürünümüz
BİZE ULAŞIN
Herhangi bir sorunuz var mı? Bize şimdi mesaj gönderin! Mesajınızı aldıktan sonra tüm ekibimizle talebinize hizmet edeceğiz.
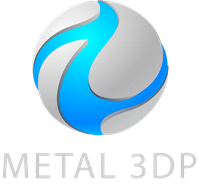
3D Baskı ve Katmanlı Üretim için Metal Tozları