MIM Metal Tozunu Anlamak
İçindekiler
MIM Metal Tozu (MIM), plastik enjeksiyon kalıplamanın tasarım esnekliğini işlenmiş metal parçaların gücü ve özellikleriyle birleştiren verimli bir üretim sürecidir. MIM için temel malzeme, bu proses için özel olarak tasarlanmış metal tozudur. Bu kılavuz, bileşim, üretim, özellikler, uygulamalar ve daha fazlası dahil olmak üzere MIM metal tozu hakkında kapsamlı bir genel bakış sağlar.
Genel Bakış MIM Metal Tozu
MIM metal tozu, metal enjeksiyon kalıplama işlemi için hammadde olarak kullanılan ince metal tozlarını ifade eder. Karmaşık, net şekilli yeşil parçalar oluşturmak için kalıplara enjekte edilen ince metal tozu ve bağlayıcı karışımıdır.
MIM tozunun temel özellikleri şunlardır:
- 10-20 mikron boyutunda ultra ince küresel toz
- 55-65%'nin bağlayıcı içinde hacimce toz yüklemesi
- Kalıp dolumu için mükemmel akışkanlık
- Tutarlı partikül boyutu dağılımı
- MIM için optimize edilmiş alaşım bileşimleri
- Çelikler, paslanmaz çelikler, titanyum alaşımları, tungsten ağır alaşımları vb. gibi geniş malzeme seçenekleri.
- Karmaşık, dar toleranslı metal bileşenlerin uygun maliyetli üretimi
Küresel MIM toz pazarı 2020 yılında $350 milyonun üzerindeydi. Sektörün, çeşitli sektörlerdeki talep nedeniyle 8%'nin üzerinde bir CAGR ile istikrarlı bir şekilde büyümesi beklenmektedir.
MIM Metal Tozu Türleri
MIM hammaddesi için çeşitli metal tozu bileşimleri kullanılmaktadır. En yaygın türleri şunlardır:
Malzeme | Anahtar Özellikler | Uygulamalar |
---|---|---|
Paslanmaz çelikler | Korozyon direnci, mukavemet | Medikal, otomotiv, tüketici ürünleri |
Takım çelikleri | Yüksek sertlik, aşınma direnci | Kesici takımlar, kalıplar, dişliler |
Düşük alaşımlı çelikler | Manyetik özellikler, işlenebilirlik | Elektromekanik bileşenler |
Titanyum alaşımları | Yüksek mukavemet/ağırlık oranı | Havacılık ve uzay, askeri, biyomedikal |
Tungsten ağır alaşımları | Yoğunluk, titreşim sönümleme | Otomotiv, spor ekipmanları |
Süper alaşımlar | Yüksek sıcaklık dayanımı | Türbin ve roket bileşenleri |
Uygun toz metal alaşımları seçilerek, belirli uygulamalar için özel olarak tasarlanmış özelliklere sahip bileşenler üretilebilir.
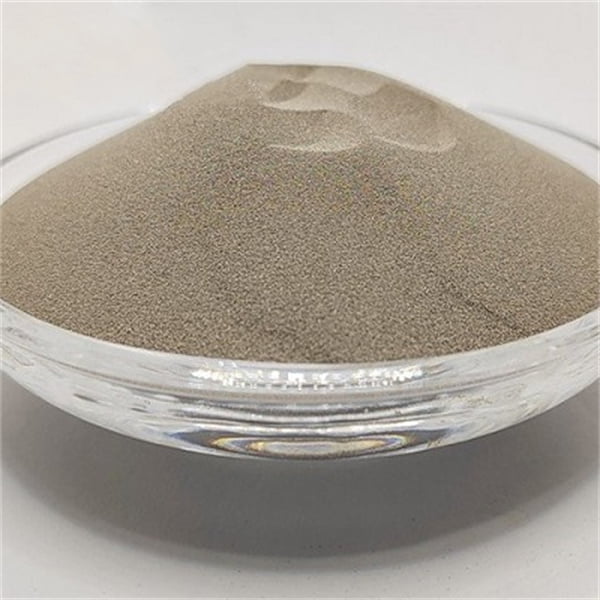
MIM Metal Tozu Üretimi
MIM hammaddesi için ince metal tozları üretmek üzere ticari olarak çeşitli yöntemler kullanılmaktadır:
Gaz Atomizasyonu - Yüksek hızlı inert gaz jetleri, ince bir erimiş metal akışını, MIM için ideal olan küresel tozlar halinde katılaşan ince damlacıklara ayırır. Çelikler, süper alaşımlar ve demir dışı alaşımlar için yaygındır.
Su Atomizasyonu - Gaz atomizasyonuna benzer ancak daha düşük soğutma hızı, bazı uygulamalar için uygun olan daha düzensiz toz şekilleri üretir. Demir, bakır gibi yaygın alaşımlar için kullanılan daha düşük maliyetli bir işlemdir.
Plazma Atomizasyonu - Titanyum, niyobyum ve tantal gibi reaktif alaşımlardan daha ince küresel tozlar üretmek için son derece yüksek sıcaklıkta plazma arkı kullanılır.
Mekanik Yıpranma - Bilyalı öğütme, metal tozu karışımlarının parçacık boyutlarını MIM aralığına düşürmek için kullanılır. Verimli kuru proses.
Karbonil Süreci - Demir ve nikel karboniller, 1-5 mikron partikül boyutunda yüksek saflıkta küresel tozlar üretmek için ayrıştırılır.
Toz üretim yöntemi, akışkanlık, musluk yoğunluğu ve safsızlıklar gibi nihai toz özelliklerini kontrol eder.
Özellikleri MIM Metal Tozu
MIM hammadde tozunun temel özellikleri şunlardır:
Parçacık boyutu - 1 ila 20 mikron arasında, optimum dolum için tipik olarak yaklaşık 10 mikron. Bu aralıkta yüksek verim.
Parçacık şekli - Ağırlıklı olarak küresel morfoloji, karmaşık kalıplara düzgün akış sağlar. Bazı düzensizlikler kabul edilebilir.
Parçacık boyutu dağılımı - Dar dağılım homojen sinterlemeyi geliştirir. Genellikle 10 +/- 5 mikron aralığında 80-90% partikül.
Musluk yoğunluğu - Nihai parça yoğunluğunu gösterir. Yüksek mekanik özellikler için 3 g/cc'nin üzerinde daha yüksek kademe yoğunluğu gereklidir.
Akış hızı - Saniye/50g olarak ölçülür. Boşluksuz düzgün kalıp dolumu için kritiktir. 40 sn/50g'ın altında olması arzu edilir.
Görünür yoğunluk - Hammaddede, tipik olarak toz yükleme fraksiyonunu gösteren nihai sinterlenmiş yoğunluğun 40-50%'si.
Piknometrik yoğunluk - Katı alaşım parçacıklarının gerçek yoğunluğu. Nihai parça yoğunluğu ile eşleşmesi saflığı gösterir.
Spesifik yüzey alanı - Yüksek değerler MIM için arzu edilen daha ince partikül boyutu dağılımını gösterir. 0,1 ila 1 m2/g arasında değişir.
MIM Metal Tozu için Alaşım Seçenekleri
MIM toz hammaddesi olarak aşağıdakiler de dahil olmak üzere çok çeşitli alaşımlar mevcuttur:
Alaşım | Kompozisyon | Özellikler | Uygulamalar |
---|---|---|---|
Paslanmaz çelik 316L | Cr, Ni, Mo | Mükemmel korozyon direnci | Tıbbi, gıda ile temas |
Paslanmaz çelik 17-4PH | Cr, Ni, Cu | Yüksek mukavemet, sertlik | Havacılık ve uzay bileşenleri |
Takım çeliği H13 | Cr, Mo, V | Sıcak sertlik, termal yorulma direnci | Enjeksiyon kalıplama |
Maraging çelik | Ni, Co, Mo, Ti | Ultra yüksek mukavemet | Havacılık ve uzay, takım |
Alaşımlı çelik | Cr, Mo, C | Isıl işlem uygulanabilir, manyetik | Yapısal parçalar |
Nikel alaşımı 718 | Ni, Fe, Nb, Mo | Yüksek sıcaklık dayanımı | Havacılık ve Uzay |
Titanyum Ti-6Al-4V | Ti, Al, V | Hafif, biyouyumluluk | Tıbbi implantlar |
Tungsten ağır alaşım | W, Ni, Fe | Yüksek yoğunluk, radyasyon kalkanı | Askeri, motor sporları |
Geniş bir alaşım yelpazesine sahip olan MIM, gerekli malzeme özelliklerine ve performansa ulaşmada esneklik sağlar.
MIM Metal Tozu Uygulamaları
MIM teknolojisi ve hammadde tozunun kullanıldığı başlıca uygulama alanları şunlardır:
Tıbbi ve Diş İmplantları
MIM, eklemler, sabitleme vidaları, aletler gibi küçük, karmaşık paslanmaz çelik ve titanyum implant bileşenlerinin yüksek hacimli üretimi için idealdir. Biyouyumluluk, korozyon direnci, mukavemet ve üretim hassasiyeti sunar.
Otomotiv Bileşenleri
MIM tarafından üretilen turboşarj rotorları, enjektör nozulları, valf kilitleme kapakları gibi küçük hassas parçalar, modern motorlarda ve güç aktarma organlarında performans avantajları sağlar.
Tüketici Elektroniği
Saat dişlileri, dekoratif bağlantı parçaları, konektör pimleri gibi minyatür bileşenler paslanmaz çelikler, bakır alaşımları ve takım çeliklerinden MIM yoluyla üretilmektedir.
Havacılık ve Savunma
Hafif, yüksek mukavemetli Ti ve Ni alaşımları MIM bileşenleri türbinlerde ve uçak gövdelerinde ağırlığı azaltır. Tungsten alaşımları uzay ve savunma kullanımları için radyasyon kalkanı sunar.
Ateşli Silahlar
Tetikler, çekiçler, emniyetler, ejektörler gibi küçük, karmaşık ateşli silah bileşenleri, paslanmaz çeliklerden ve takım çeliği alaşımlarından yüksek hacimlerde MIM ile üretilebilir.
Saat Endüstrisi
MIM, karmaşık şekilli paslanmaz çelik saat kasalarının, bileziklerin, tokaların ve dişliler ve yaylar gibi minyatür hareketli bileşenlerin ekonomik bir şekilde üretilmesini sağlar.
Tasarım esnekliği sayesinde MIM, tüketici ürünlerinden kritik endüstriyel bileşenlere kadar çeşitli sektörlerde uygulama alanı bulmaya devam ediyor.
Nasıl Seçilir MIM Metal Tozu
MIM hammadde tozunu seçerken dikkat edilmesi gereken temel hususlar:
- Alaşım bileşimi - Toz alaşımını korozyon direnci, mukavemet, aşınma özellikleri vb. gibi son uygulama gereklilikleriyle eşleştirin.
- Partikül boyutu ve şekli - Optimum akış ve paketleme için 10 mikron civarında dar dağılımlı küresel morfolojiyi tercih edin.
- Toz saflığı - Kirlenmeyi önlemek için tıbbi gibi özel uygulamalar için 99%'nin üzerinde yüksek saflık gereklidir.
- Musluk yoğunluğu - Yoğunluğun 3 g/cc'nin üzerinde olması kalıp dolumunu ve sinterleme sonrası nihai parça yoğunluğunu iyileştirir.
- Toz yükleme - 30-50 vol% arasındaki bağlayıcı içeriği tipiktir. Viskozite ve kalıplanmış yeşil mukavemeti etkiler.
- Toz üreticisi - Sandvik, BASF ve Kymera gibi onaylanmış süreçlere sahip saygın toz üreticileri.
- Lottan lota tutarlılık - Tutarlı hammadde özellikleri, uzun üretim çalışmaları boyunca istikrarlı kalıplama parametrelerine olanak tanır.
- Teknik Destek - Detaylı uygulama verileri ve geliştirme denemeleri sırasında toz tedarikçisinden yardım.
Sandvik Osprey, BASF Ultraform, Kymera International ve Epson Atmix gibi önde gelen küresel tedarikçiler, optimum sonuçlar için parça ve süreç geliştirme sırasında son kullanıcılarla işbirliği yapmaktadır.
Atomize ve Öğütülmüş MIM Tozlarının Karşılaştırılması
Parametre | Atomize Tozlar | Mekanik Olarak Öğütülmüş Tozlar |
---|---|---|
Parçacık şekli | Küresel | Düzensiz, köşeli |
Boyut aralığı | 1 - 20 mikron | 10 - 100+ mikron |
Boyut dağılımı | Çok dar | Geniş |
Musluk yoğunluğu | Daha yüksek ~3-4 g/cc | Daha düşük ~2-3 g/cc |
Akış hızı | Mükemmel | Orta düzeyde |
Saflık | Yüksek | Daha düşük |
Maliyet | Daha yüksek | Daha düşük |
Mevcut alaşımlar | Çoğu standart ve özel alaşımlar | Sınırlı alaşımlar |
Uygulamalar | Çoğu MIM bileşeni | Daha büyük, daha az kritik MIM parçaları |
Atomize tozlar daha karmaşık, daha yüksek performanslı MIM bileşenlerine izin verir. Öğütülmüş tozlar bazı uygulamalar için maliyet tasarrufu sağlayan bir seçenek sunar.
MIM Toz Üretim Tesisi Kurulumu
Bir MIM toz üretim tesisinin kurulmasındaki temel adımlar:
- Yer seçimi - Yeterli alan, kamu hizmetleri tedariki, atık işleme, erişim yolları ve yükleme alanları.
- Bina ve yerleşim planı - Malzeme ve insan akışı, güvenlik, üretim bölgeleri, gelecekteki genişleme için tesis yerleşimini tasarlayın.
- Hizmet bağlantıları - Yüksek kapasiteli elektrik beslemesi, arıtılmış su, basınçlı hava hatları, sıvı nitrojen.
- Makine temelleri - Atomizörler, değirmenler, fırınlar için güçlü betonarme temeller. Titreşim sönümleme.
- Ekipman kurulumu - Eldiven kutularını, atomizörleri, elekleri, konveyörleri, hazneleri, kontrolleri tedarikçi talimatlarına göre kurun.
- Yardımcı sistemler - Borulama, havalandırma, hava filtreleme, yangın güvenliği, malzeme taşıma, atık su arıtma.
- Kontrol sistemleri - Sensörleri, aktüatörleri, HMI'ları kurun. Proses kontrol sistemlerini entegre edin ve programlayın.
- Devreye alma - Tam ölçekli üretimden önce toz kalitesini, güvenliği ve çevresel uygunluğu doğrulamak için test üretim çalışmaları.
MIM toz tesisi kurulumu, kapsamlı planlama ve kamu hizmetleri, kontroller, güvenlik ve mevzuat ihtiyaçlarına dikkat gerektirir.
MIM Toz Ekipmanının Çalıştırılması ve Bakımı
MIM toz üretim ekipmanının güvenilir şekilde çalışması gerekir:
- Önleyici bakım - OEM tavsiyelerine göre atomizörlerin, fırınların, değirmenlerin, konveyörlerin periyodik bakımını planlayın.
- Ekipman izleme - Akış, basınç, sıcaklık, güç tüketimi gibi proses parametrelerinin sürekli izlenmesi.
- Denetimler - Sızıntılar, anormal sesler veya titreşim, güvenlik sorunları için günlük görsel denetimler.
- Servis ve onarımlar - Azot jeneratörleri, soğutucu üniteleri ve elektrik sistemleri için yıllık servis sözleşmeleri planlayın.
- Yedek parçalar - Arıza süresini en aza indirmek için ısıtma elemanları, motorlar, rulmanlar gibi yaygın yedek parçalardan stok bulundurun.
- Ekipman kayıtları - Varlık kullanımını optimize etmek için üretim oranı, onarımlar, arızalar için günlükler tutun.
- Kat Hizmetleri - Temiz, düzenli ekipmanı korumak ve toz işleme alanlarında herhangi bir tutuşma riskini önlemek için günlük temizlik.
- Personel eğitimi - Operasyonel verimliliği ve sorun giderme becerilerini geliştirmek için uygulamalı ekipman eğitimi vermek.
Mükemmel bakım uygulamaları ile MIM toz üretim ekipmanı yıllarca güvenli ve güvenilir üretim sağlayabilir.
MIM Toz Tedarikçisi Nasıl Seçilir
Bir MIM toz tedarikçisi seçerken temel faktörler:
- Teknik uzmanlık tozlarda - MIM için toz özelliklerini ve bağlayıcı formülasyonunu optimize etme deneyimi.
- Alaşım yelpazesi - Paslanmaz çeliklerden titanyuma, takım çeliklerine vb. kadar çok çeşitli alaşımların mevcudiyeti.
- Kalite sistemleri - ISO 9001 sertifikası. Toz özelliklerinin iç kalite kontrolü.
- Tutarlılık - Toz özellikleri partiden partiye tutarlı kalarak istikrarlı bir kalıplama süreci sağlar.
- Ar-Ge yetkinliği - Zorlu uygulamalar için yeni özel alaşımlar ve bağlayıcılar geliştirmek üzere sürekli araştırma.
- Müşteri Hizmetleri - Duyarlı teknik destek ve satış desteği. Denemeler ve hızlanma sırasında yerinde yardım.
- Lojistik kabiliyet - Bölgeler arasında verimli, zamanında toz teslimatları sağlamak için sistemler.
Önde gelen küresel tedarikçiler arasında MIM toz teknolojisine odaklanmış Sandvik Osprey, BASF, Kymera International ve Epson Atmix yer almaktadır.
MIM Tozunun Artıları ve Eksileri
Artıları
- Düşük maliyetlerle yüksek hacimlerde karmaşık, net şekilli parçalar
- İşlenmesi zor metaller de dahil olmak üzere çok çeşitli alaşımlar mevcuttur
- Dövülmüş malzemelere yakın iyi mekanik özellikler
- Yüksek doğruluk ve tekrarlanabilirlik
- Talaşlı imalata kıyasla minimum hurda kaybı
- Sinterlenmiş parçalarda sınırlı son işlem gerekir
- Talaşlı imalattan daha az atıkla çevresel açıdan daha temiz süreç
Eksiler
- Daha düşük üretim hacimleri için daha yüksek parça maliyeti
- Boyut, tipik olarak 500 g'ın altındaki küçük bileşenlerle sınırlıdır
- MIM toz karışımları olarak mevcut alaşımlarla sınırlıdır
- Sinterlenmiş parçalar dövme metallere göre daha düşük sünekliğe sahiptir
- Özel ekipman ve uzmanlık ihtiyacı
- İlave debinding ve sinterleme adımları
MIM Tozu ve Diğer Uygulamalar için Metal Tozları
Parametre | MIM Toz | Katmanlı Üretim Tozu | Pres ve Sinter Tozu |
---|---|---|---|
Alaşımlar | Geniş paslanmaz, takım çelikleri, Ti alaşımları yelpazesi | 17-4PH, Ti-6Al-4V, CoCr gibi sınırlı alaşımlar | Düşük alaşımlı ve paslanmaz çelikler |
Parçacık şekli | Ağırlıklı olarak küresel | Son derece küresel | Düzensiz kabul edilebilir |
Boyut aralığı | 1-20 mikron | 15-45 mikron | 150 mikrona kadar |
Boyut dağılımı | Çok dar | Dar | Daha geniş kabul edilebilir |
Saflık | Orta ila yüksek | Yüksek | Orta |
Maliyet | Orta | Yüksek | Düşük |
Tipik üretim yöntemi | Gaz veya su atomizasyonu | Gaz veya plazma atomizasyonu | Su atomizasyonu, mekanik frezeleme |
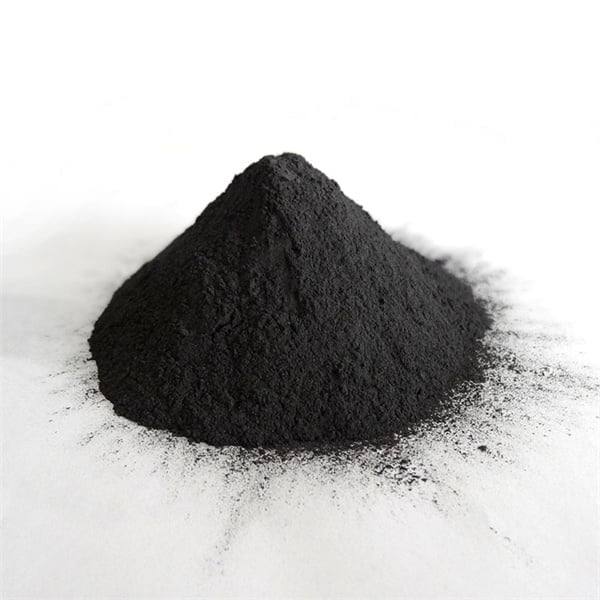
SSS
S: MIM tozunun tipik boyut dağılımı nedir?
C: MIM toz partiküllerinin yaklaşık 80-90%'si, optimum paketleme yoğunluğu ve akış için 10 +/- 5 mikron içinde kalır.
S: Bağlayıcıdaki toz yükünü etkileyen faktörler nelerdir?
C: Toz yüklemesini kontrol eden temel faktörler % partikül boyutu dağılımı, şekil, kademe yoğunluğu ve toz-bağlayıcı etkileşimidir.
S: MIM parçalarının yüksek sıcaklık dayanımı dövme alaşımlara kıyasla nasıldır?
C: Optimum sinterleme ile 316L ve 17-4PH paslanmaz çelik gibi alaşımlardaki MIM parçaları 90%'nin üzerinde dövme mukavemetine ulaşır.
S: MIM'de eksik kalıp doldurma hatalarına ne sebep olur?
C: Yanlış toz yüklemesi, geniş partikül dağılımı, zayıf toz akışkanlığı ve düşük enjeksiyon hızı dolum hatalarına neden olabilir.
S: MIM, kalıplama basınçları açısından plastik enjeksiyon kalıplama ile nasıl karşılaştırılır?
C: MIM enjeksiyon basınçları 70-140 MPa arasında değişir ve 15-60 MPa'lık tipik plastik kalıplama basınçlarından daha yüksektir.
S: MIM tozlarını kullanırken hangi güvenlik önlemleri gereklidir?
C: MIM tozları yanıcı olabilir. İnert gaz eldiven kutuları kullanın, kıvılcım kaynaklarından kaçının, ekipmanı topraklayın ve toz emme kullanın.
Sonuç
MIM, yüksek performanslı, karmaşık metal bileşenleri düşük maliyetle ve yüksek hacimlerde üretmek için net şekle yakın bir teknoloji olarak öne çıkmaya devam ediyor. MIM tozları, gelişmiş toz metalurjisi teknikleriyle bu süreç için özel olarak formüle edilmiş kritik hammaddelerdir. Genişletilmiş alaşımlar ve geliştirilmiş tozlarla, MIM'in benimsenmesi, işlenmiş ve dökme bileşenlerin yerini daha iyi maliyet ve teslim süresi ile almak için sektörler arasında artmaya devam edecektir.
Paylaş
MET3DP Technology Co, LTD, merkezi Qingdao, Çin'de bulunan lider bir katmanlı üretim çözümleri sağlayıcısıdır. Şirketimiz, endüstriyel uygulamalar için 3D baskı ekipmanları ve yüksek performanslı metal tozları konusunda uzmanlaşmıştır.
İşletmeniz için en iyi fiyatı ve özelleştirilmiş Çözümü almak için sorgulayın!
İlgili Makaleler
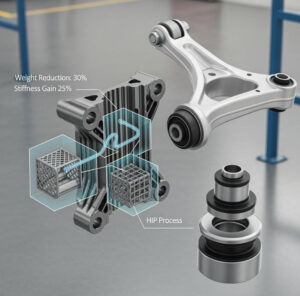
Metal 3D Printed Subframe Connection Mounts and Blocks for EV and Motorsport Chassis
Daha Fazla Oku "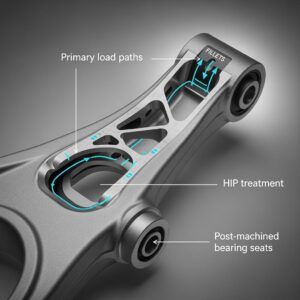
Metal 3D Printing for U.S. Automotive Lightweight Structural Brackets and Suspension Components
Daha Fazla Oku "Met3DP Hakkında
Son Güncelleme
Bizim Ürünümüz
BİZE ULAŞIN
Herhangi bir sorunuz var mı? Bize şimdi mesaj gönderin! Mesajınızı aldıktan sonra tüm ekibimizle talebinize hizmet edeceğiz.