MIM Teknolojisini Anlamak
İçindekiler
Genel Bakış MIM Teknolojisi
Toz enjeksiyon kalıplama (PIM) olarak da bilinen metal enjeksiyon kalıplama (MIM), küçük, karmaşık metal parçaları yüksek hacimlerde üretmek için kullanılan gelişmiş bir üretim sürecidir.
MIM, plastik enjeksiyon kalıplamanın tasarım esnekliğini ve hassasiyetini işlenmiş metal parçaların gücü ve performansıyla birleştirir. Gelişmiş metal alaşımlarından iyi mekanik özelliklere sahip karmaşık bileşenlerin uygun maliyetli üretimini sağlar.
MIM süreci, bir bağlayıcı malzeme ile karıştırılmış ince metalik tozdan oluşan bir hammadde ile başlar. Bu hammadde daha sonra plastik enjeksiyon kalıplama ekipmanı kullanılarak bir kalıba enjekte edilir. Bağlayıcı metal tozunu bir arada tutar ve kalıplama için akışkanlık kazandırır.
Kalıplamadan sonra bağlayıcı, kalıplanmış yeşil parçadan bir bağ çözme işlemi ile çıkarılır. Kahverengi parça olarak adlandırılan ayrıştırılmış parça daha sonra yüksek sıcaklıklarda sinterlenerek metal parçacıkları birbirine kaynaştırılır ve böylece işlenmiş parçanınkine yakın malzeme özelliklerine sahip katı bir metal parça elde edilir.
MIM, paslanmaz çelik, düşük alaşımlı çelikler, takım çelikleri, manyetik alaşımlar, süper alaşımlar, titanyum alaşımları ve tungsten ağır alaşımları gibi çeşitli metalleri kullanarak küçük, karmaşık parçalar yapmak için uygundur. Plastik enjeksiyon kalıplamanın çok yönlülüğünü toz metalürjisinin malzeme esnekliği ile birleştirir.
MIM teknolojisinin temel faydaları şunlardır:
- Karmaşık, detaylı metal bileşenler için yüksek hacimli üretim kapasitesi
- İsrafı azaltan ve işleme sürecini en aza indiren net şekle yakın üretim
- Dövülmüş malzemelere yakın iyi mekanik özellikler
- Paslanmaz çelik, takım çeliği, süper alaşımlar dahil olmak üzere geniş metal seçenekleri
- Parçaların tek bir bileşen halinde birleştirilmesini sağlar
- Yüksek hacimler nedeniyle düşük birim maliyet
- Otomatikleştirilmiş süreçten gelen tutarlılık ve tekrarlanabilirlik
MIM teknolojisi, tıbbi cihazlar, ateşli silah bileşenleri, saat bileşenleri ve otomotiv parçaları gibi hassasiyet, güç, ekonomi ve seri üretim ölçeği gerektiren küçük, karmaşık parçalar için idealdir.
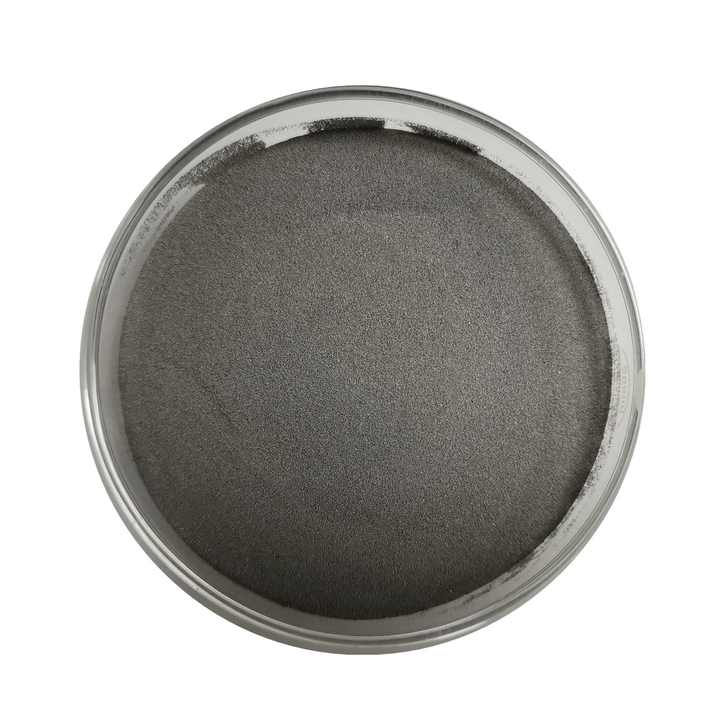
MIM Teknolojisinin Uygulamaları ve Kullanım Alanları
MIM teknolojisi, küçük, yüksek hassasiyetli metal parçaları büyük hacimlerde verimli bir şekilde üretmek için çeşitli sektörlerde kullanılmaktadır. İşte MIM teknolojisinin temel uygulama alanlarından ve kullanımlarından bazıları:
Endüstri | Uygulamalar ve Kullanım Alanları |
---|---|
Tıp ve Diş Hekimliği | Cerrahi aletler, diş implantları, ortopedik implantlar, kateter bileşenleri, iğne kanülleri, neşter sapları, forsepsler, klempler, cerrahi bağlantı elemanları, yeniden kullanılabilir cerrahi aletler |
Ateşli Silahlar ve Savunma | Tetikler, çekiçler, emniyetler, ejektörler, şarjörler, kullanılmış kovanlar, mermiler, savaş başlığı bileşenleri |
Otomotiv | Yakıt sistemi bileşenleri, yağ pompası dişlileri, pervaneler, valfler, turboşarj parçaları, elektronik parçalar, direksiyon/şanzıman bileşenleri |
Havacılık ve Uzay | Türbin kanatları, çarklar, dişli dişleri, burçlar, pompa bileşenleri, motor parçaları |
Tüketici Ürünleri | Saat parçaları, mücevher bulguları, çatal bıçak takımı, makas, jilet, el aletleri, fermuar parçaları |
Endüstriyel Donanım | Topuzlar, bağlantı parçaları, bağlantı elemanları, soketler, konektörler, fıskiyeler, nozullar |
Elektronik | Konektörler, anahtarlar, mikromotorlar, mikro dişliler, perdeleme maskeleri, indüktörler, mıknatıs rotorları |
** Belirli Uygulamalar için MIM'in Avantajları**
- Hassasiyet: Karmaşık geometrilere sahip tıbbi cihazlar veya saat bileşenleri gibi minyatür parçalar için idealdir.
- Mukavemet: Otomotiv turboşarjları ve ateşli silah tetikleri gibi yüksek mukavemet gerektiren bileşenler için uygundur.
- Aşınma Direnci: Takım çeliği alaşımlarından yapılan MIM parçaları, uzun hizmet ömrü için mükemmel aşınma direncine sahiptir.
- Korozyon Direnci: Paslanmaz çelik MIM parçalar, yeniden kullanılabilir cerrahi aletler, implantlar vb. için korozyona karşı dayanıklıdır.
- Yüksek Sertlik: MIM, çatal bıçak takımı, takımlar, kalıplar vb. gibi 40 HRC'nin üzerinde sertliğe sahip parçalar üretebilir.
- Elektriksel Özellikler: MIM, indüktörler, motor rotorları vb. gibi yumuşak manyetik bileşenler yapmak için kullanılır.
- Uygun Maliyetli: Yüksek hacimler, parça maliyetini talaşlı imalata kıyasla önemli ölçüde azaltır.
MIM Ekipman ve Alet Kılavuzları
MIM sürecinde kullanılan başlıca ekipmanlar arasında enjeksiyon kalıplama makineleri, debinding ve sinterleme fırınları yer almaktadır. İşte genel bir bakış:
Ekipman | Amaç | Dikkate Alınması Gerekenler |
---|---|---|
Enjeksiyon Kalıplama Makinesi | MIM hammaddesini ısı ve basınç altında kalıp boşluklarına enjekte etmek | Kalıp bağlama kuvveti, enjeksiyon hızı ve basınç kapasitesi, hassasiyet ve tekrarlanabilirlik, kontroller ve otomasyon özellikleri. |
Bağlayıcı Sökme Fırını | Bağlayıcıyı kalıplanmış parçalardan termal veya kimyasal olarak çıkarmak için | Sıcaklık aralığı, atmosfer kontrolü, yükleme kapasitesi, debinding'in homojenliği. |
Sinterleme Fırını | Çözünmüş kahverengi parçaları erime noktasına yakın bir noktaya kadar ısıtarak yoğunlaştırmak | Sıcaklık aralığı, atmosfer kontrolü, ısıtma homojenliği, parti kapasitesi, tam otomatik tercih edilir. |
Kalıplar ve takımlar | MIM hammaddesini gerekli geometriye dönüştürmek için şekillendirilmiş boşluklar | Kalıplama basınçlarına ve sıcaklıklarına dayanıklı, hassas işlenmiş, iyi yüzey kalitesi, hızlı ısıtma/soğutma sağlar. |
Hammadde Ekipmanları | Metal tozu ve bağlayıcıyı homojen MIM hammaddesine karıştırmak için | Karıştırıcılar, sıcaklık kontrolörleri, peletleyiciler. |
İkincil İşleme | İşleme, birleştirme, yüzey işleme gibi ek adımlar | CNC işleme, kaynak, EDM, kaplama gibi parça ihtiyaçlarına göre. |
Kalite Kontrol | Hammadde, sinterlenmiş parça özelliklerini test etmek | Toz morfolojisi, yoğunluk, akış hızı, viskozite analizörleri, mekanik test ekipmanları. |
Güvenlik Ekipmanları | İnce tozları güvenli bir şekilde işlemek için | Eldivenler, solunum maskeleri, toz toplama sistemleri. |
Tasarım ve Performans Standartları
- ISO 21227 - Metal enjeksiyon kalıplama için tozlar
- ASTM F2885 - Metal Enjeksiyon Kalıplama Süreci
- MPIF 35 - MIM hammaddesi için standartlar
- ASTM E2781 - MIM Çekme Testi Numune Tasarımı
- ISO 2740 - Sinterlenmiş Metal Enjeksiyon Kalıplama parçaları
Maliyet Dağılımı
MIM üretimindeki tipik maliyet dağılımı şöyledir:
- Hammaddeler (Toz + Bağlayıcı): 50-60%
- Üretim (Kalıplama + Debinding + Sinterleme): 25-35%
- İkincil İşlem: 5-10%
- Kalite Kontrol: 2-5%
- Mühendislik (Ar-Ge, Tasarım): 2-5%
Tedarikçiler ve Fiyatlandırma
İşte MIM ekipmanlarının önde gelen bazı küresel tedarikçileri ve fiyat aralıkları:
Tedarikçi | Ürün Kategorisi | Fiyat Aralığı |
---|---|---|
ARBURG | Enjeksiyon kalıplama makineleri | $100,000 – $500,000 |
Hint-ABD MIM | MIM hammadde ve hizmetleri | Kg başına $5 - $50 |
Elnik | Debinding ve sinterleme fırınları | $50,000 – $1,000,000 |
FineMIM | Uçtan uca MIM üretimi | Parça başına $0.5 - $5 |
Parmatech | Metal tozu atomizasyonu | $250,000 – $1,000,000 |
Meridian Teknolojileri | Takım ve kalıp tasarımı | $5,000 – $100,000 |
Kurulum, İşletim ve Bakım
MIM otomatik bir süreçtir ancak optimum performans için dikkatli kurulum, işletim ve bakım gerektirir:
Etkinlik | Detaylar |
---|---|
Kurulum | Enjeksiyon kalıplama makinesi ve kalıpların hassas hizalanması. Sıcaklık kontrol cihazlarını kalibre edin. Deneme partileri ile test çalıştırması. |
Operasyon | Standartlara göre hammadde kalite kontrolünü sağlamak. Enjeksiyon basıncı, sıcaklık ve hız gibi proses parametrelerine ulaşmak. |
Bakım | Kalıplama makinesi varilleri, vidaları, kalıpları için önleyici bakım planlayın. Kalıp sökme fırını atmosferini koruyun. Aletleri kalibre edin. |
Temizlik | Çalışmalardan sonra makine varil temizliği için SOP'leri takip edin. Fırın veya kanallarda toz birikmediğinden emin olun. Tasarlanmış medya ile kalıp temizliği. |
Güvenlik | İnce tozları kullanırken kişisel koruyucu ekipman kullanın. Kimyasal bağlayıcıların uygun şekilde bertaraf edilmesi. Bakımdan önce fırının soğumasını bekleyin. |
Eğitim | Makine ve fırın operatörlerini prosedürler konusunda eğitin. Güvenlik ve bakım konusunda tazeleme oturumları düzenleyin. |
Optimizasyon | Parça kalitesi spesifikasyonlar dahilinde stabilize olana kadar proses parametrelerini ayarlayın. Ayrıntılı süreç kayıtlarını muhafaza edin. |
Tipik Bakım Faaliyetleri ve Sıklığı
Etkinlik | Frekans |
---|---|
Enjeksiyon kalıplama makinesi nozul temizliği | Her partiden sonra |
Kalıp parlatma | Haftalık |
Makine namlu temizliği | Aylık |
Bağlayıcı çıkarma fırını atmosfer kontrolü | Aylık |
Sinterleme fırını termokupl kalibrasyonu | 6 ay |
Kalıp akış çalışmaları | Yıllık |
MIM Tedarikçisi Nasıl Seçilir?
Kaliteli parçaları zamanında ve makul maliyetle elde etmek için yetkin bir MIM tedarikçisi seçmek kritik önem taşır. İşte dikkate alınması gereken önemli faktörler:
Faktör | Kriterler |
---|---|
Teknik Yeterlilik | Gelişmiş ekipman, yılların deneyimi, teknik uzmanlık |
Malzeme Seçenekleri | Paslanmaz çelik, takım çeliği, tungsten alaşımları gibi çeşitli malzemeler |
İkincil İşleme | Şirket içi işleme, birleştirme, kaplama tesisleri |
Kalite Sistemleri | ISO 9001 sertifikası, kalite kontrol ve denetim prosedürleri |
Üretim Kapasitesi | İstikrar için yüksek hacimli üretim yeteneği |
Teslim Süresi | Tasarımdan teslimata kadar hızlı geri dönüş süresi |
Konum | Lojistik verimliliği için coğrafi yakınlık |
Maliyet | Fiyatlandırma modeli - parça başına fiyatlandırma tercih edilir |
Müşteri Hizmetleri | Sorulara yanıt verme, teknik destek, proje yönetimi |
Potansiyel MIM Tedarikçilerine Sorulacak Sorular
- Hangi malzemeler ve parça boyutları konusunda deneyiminiz var?
- İşleme veya kaplama gibi ikincil işlemler sunuyor musunuz?
- Hangi kalite sertifikaları ve denetim prosedürleri takip ediliyor?
- Titanyum alaşımları veya tungsten karbürler gibi hassas malzemelerin kullanımı nasıl yapılıyor?
- Aylık bazda hangi üretim hacimlerini güvenilir bir şekilde sağlayabilirsiniz?
- Hurda nasıl en aza indirilir ve verim nasıl en üst düzeye çıkarılır?
- Boyut ve özelliklerde parçadan parçaya değişkenlik nedir?
- MIM süreci için tasarım optimizasyonu nasıl yapılacak?
- Hangi kalite raporları ve kontrol çizelgeleri sağlanacak?
MIM'in Diğer Süreçlerle Karşılaştırılması
MIM ve diğer metal üretim süreçleri arasında karşılaştırma:
Süreç | Avantajlar | Dezavantajlar |
---|---|---|
MIM | Karmaşık geometriler, seri üretim, net şekle yakın, geniş malzeme seçenekleri | Ön takım yatırımı, boyut sınırlamaları |
CNC İşleme | Malzeme esnekliği, prototiplerin hızlı geri dönüşü | Sınırlı karmaşıklık, daha düşük hacimler |
Metal Döküm | Düşük parça maliyeti, yüksek hacimler | Şekil sınırlamaları, daha düşük mukavemet |
Metal Damgalama | Yüksek hız, yüksek hacim, düşük maliyet | Sadece 2D geometrilere uygundur |
3D Baskı | Tasarım özgürlüğü, hızlı prototipleme | Daha düşük mukavemet, daha yüksek maliyet, sınırlı boyutlar ve malzemeler |
MIM'in Talaşlı İmalata Göre Faydaları
- Nete yakın şekil ile daha yüksek malzeme kullanımı
- Karmaşık şekiller için pahalı işleme yok
- Üstün mekanik özellikler
- İşleme kalıplarına kıyasla daha düşük takım maliyetleri
- Otomatik süreç seri üretime olanak sağlar
- Daha iyi yüzey kaplamaları mümkün
MIM'in Metal Dökümüne Göre Avantajları
- Daha iyi boyutsal doğruluk ve yüzey kalitesi
- Döküm parçalara kıyasla daha az gözeneklilik gibi kusurlar
- Yönlü dökümden farklı olarak izotropik özellikler
- Dökümlerin aksine düşük parlama veya açılma yok
- Eriyikle ilgili reaksiyonlar veya bileşimsel değişiklikler yok
- Dökümden farklı olarak maçalar ve alt kesimler mümkündür
- Dökülebilir alaşımların ötesinde geniş malzeme seçenekleri
- Toz metalurjisi ile özelliklerin tutarlılığı
CNC İşlemeye Karşı MIM'in Sınırlamaları
- Boyut, enjeksiyon kalıplama makinesi kapasitesi ile sınırlıdır
- Takımlama için daha fazla ön zaman ve maliyet
- CNC işleme için +/- 0,1%'ye karşı +/- 0,5% sıkı toleranslar
- Geometri sınırlamaları ve kısıtlamasız işleme
- Talaşlı imalata kıyasla daha düşük maksimum sertlik elde edilebilir
- Toleranslara ulaşmak için genellikle ikincil işlemeye ihtiyaç duyulur
MIM Ne Zaman Kullanılmamalıdır?
- MIM ekipman kapasitesini aşan çok büyük parçalar
- 0,5%'nin altında son derece sıkı toleranslara ihtiyaç duyan parçalar
- Yüzey sertliğinin 50 HRC'nin üzerinde olmasını gerektiren uygulamalar
- Çok düşük hacim gereksinimi olan ürünler
- Kalıplama için uygun olmayan aşırı en-boy oranlarına sahip bileşenler
- MIM süreci için tasarım optimizasyonuna zaman kalmadığında
- Daha ucuz üretim seçenekleri ile maliyete duyarlı uygulamalar
MIM Tasarım ve Modelleme Hususları
Doğru parça ve hammadde tasarımı, MIM'in gerekli özellikleri ve performansı elde etmesi için çok önemlidir. İşte önemli tasarım hususları:
Parça Tasarım Aşaması
- Enjeksiyon sırasında eşit kalıp dolumu için duvar kalınlıklarını optimize edin
- Doldurmayı kolaylaştırmak için cömert iç yarıçaplar ve filetolar içerir
- Akış yolu boyunca enine kesitte ciddi değişikliklerden kaçının
- Uygun akış modelleri için uygun kalıp kapıları ve yolluklar tasarlayın
- Sarkma veya çarpılmayı önlemek için güçlendirici nervürler ve köşebentler ekleyin
- Başlangıç boyutlarında sinterleme sırasında parça büzülmesini hesaba katın
- Tam üretimden önce tasarım doğrulaması için prototip kalıplar geliştirmek
Hammadde Geliştirme
- Kalıplama sıcaklıklarında hammadde viskozitesini kalıp karmaşıklığı ile eşleştirme
- İstenen sinterlenmiş yoğunluk için yeterli toz yüklemesi sağlayın
- Karışabilirlik için uygun bağlayıcı bileşenleri ve toz oranını seçin
- Toz paketleme yoğunluğu için toz partikül boyutu dağılımını optimize edin
- Kusursuz bağlayıcı giderimi için hammadde formülasyonlarını ayarlayın
- Kalıp akış simülasyonları aracılığıyla hammadde özelliklerini doğrulama
- Tam kalıplanabilirlik elde etmek için birden fazla hammadde iterasyonunu test edin
Simülasyon ve Modelleme
- Kapı konumlarını ve yollukları optimize etmek için kalıp akış modellemesi
- Çarpılmayı tahmin etmek ve parça geometrisini optimize etmek için yapısal FEA
- Düzgün bağlayıcı giderimi ve sinterleme için CFD simülasyonları
- Artık gerilmeleri en aza indirmek için termal modelleme
- Güç ve performansı en üst düzeye çıkarmak için mekanik modelleme
- Parametreler arasındaki etkileşimleri incelemek için süreç modelleme yazılımı
- Prototip kalıplar aracılığıyla yazılım tahminlerinin deneysel doğrulaması
Temel Modelleme Çıktıları
- Kalıp doldurma süresi, hammadde viskozitesi, akış önü sıcaklığı
- Kaynak hattı, hava kapanı ve diğer kalıplama kusur tahminleri
- Mekansal bağlayıcı içeriği, sıcaklık ve çözünme gradyanları
- Sinterleme hızı, yoğunluk gradyanları, büzülme, çarpılma eğilimleri
- Artık gerilme dağılımı, sıcak yırtılma ve çatlak tahminleri
- Mekanik dayanım, yorulma ömrü, hasar tolerans analizi
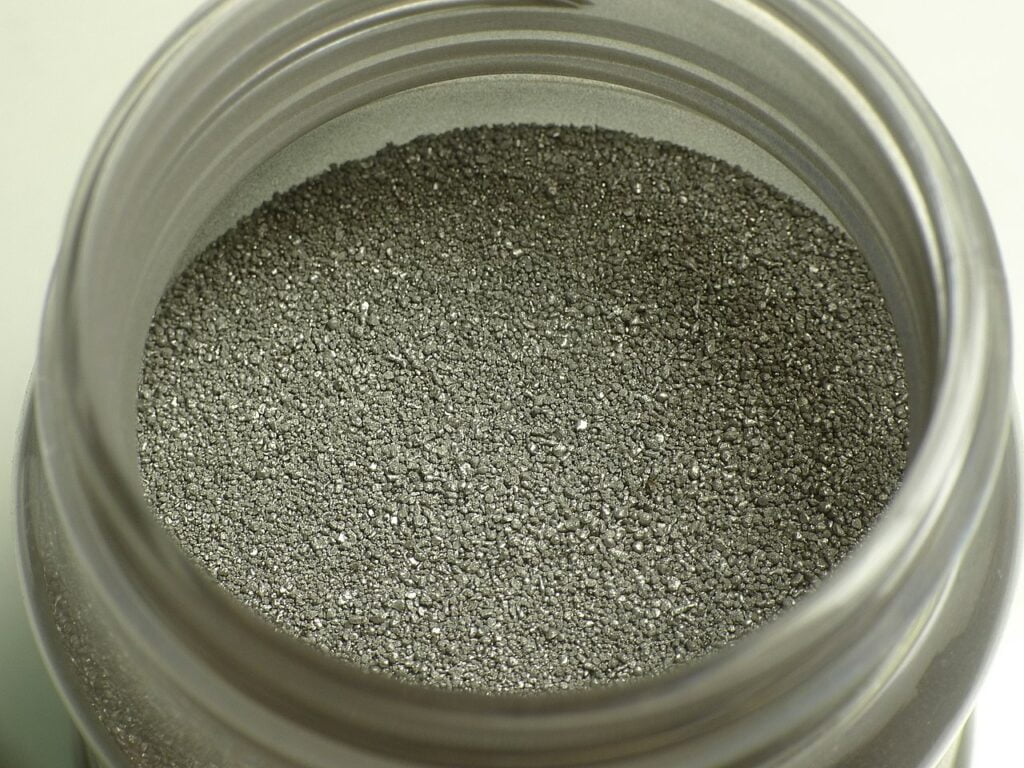
MIM Kusurları ve Azaltma Yöntemleri
Optimize edilmemiş hammadde, kalıplama parametreleri veya fırın koşulları nedeniyle MIM parçalarında kusurlar ortaya çıkabilir. İşte yaygın MIM kusurları ve azaltma yöntemleri:
Kusur | Kök Nedenler | Etki Azaltma Yöntemleri |
---|---|---|
Yüzey kusurları | Düşük kalıp sıcaklığı, yüksek sürtünme, bağlayıcı bileşenler | Kalıp parlatmayı optimize edin, kalıp ayırıcı maddeler kullanın, kalıp sıcaklığını kademeli olarak düşürün |
Kaynak hatları | İstenmeyen hammadde akış cepheleri | Kaynak hatlarını önlemek için modelleme yoluyla kapı ve yolluk tasarımını optimize edin |
Çarpıklık | Fırında üniform olmayan ısıtma, artık gerilmeler | Yapısal optimizasyon, sinterleme öncesi gerilim giderme, optimize edilmiş fırın ayarları |
Çatlaklar | Hızlı sinterleme, yüksek bağlayıcı içeriği, dik termal gradyanlar | Daha düşük ısıtma hızı, bağlayıcı sisteminin optimizasyonu, yapısal yeniden tasarım |
Gözeneklilik | Hammaddede düşük toz yüklemesi, zayıf karıştırma | Hammaddedeki toz içeriğini artırın, karıştırma işlemini iyileştirin |
Boyutsal değişim | Tutarsız büzülme, kalıp aşınması, yoğunluk gradyanları | İstatistiksel proses kontrolü, kalıp bakımı, optimize debinding ve sinterleme |
Kirlenme | Kötü kullanım, fırın atmosferi kontrolü | Uygun KKD, hava filtrelerinin iyileştirilmesi, fırın partilerinde çapraz kontaminasyonun önlenmesi |
Eksik doldurma | Yüksek kalıp sıcaklığı, yüksek viskozite | Kalıp ve hammadde sıcaklığını artırın, daha düşük viskoziteli bağlayıcı kullanın |
MIM Sektörü Verileri ve Trendleri
MIM Küresel Pazar Büyüklüğü
Küresel MIM pazarı 2022 yılında 1,5 milyar ABD doları değerindeydi ve sağlık, otomotiv ve havacılık sektörlerinden gelen talebin etkisiyle 8,7% YBBO ile büyüyerek 2030 yılına kadar 3,1 milyar ABD dolarına ulaşacağı tahmin edilmektedir.
Sektör Büyüme Etkenleri
- Otomotiv, havacılık ve elektronik sektörlerinde hafifletme trendleri
- Tıbbi cihazlarda küçük, karmaşık metal bileşenlere yönelik talep
- Daha geniş bir MIM uygulanabilir malzeme yelpazesi ile daha uygulanabilir
- Üretim maliyetlerini düşüren otomasyon
- Hassas bileşenlerin üretiminde büyüme
- Saatçilik gibi gelişmekte olan uygulamalarda artan benimseme
Bölgelere Göre Öngörülen CAGR
- Asya Pasifik: 9,3% CAGR
- Avrupa: 10,2% CAGR
- Kuzey Amerika: 7,6% CAGR
- Dünyanın Geri Kalanı: 7,9% CAGR
Sektöre Göre MIM Parçalarının Payı
- Tüketici ürünleri: 22%
- Otomotiv: 21%
- Ateşli Silahlar: 15%
- Tıbbi: 14%
- Endüstriyel: 13%
- Havacılık ve Uzay: 8%
- Diğerleri: 7%
MIM Teknoloji Geliştirme Trendleri
- Kusurları azaltmak ve karmaşık geometrileri mümkün kılmak için yeni bağlayıcı sistemleri
- Daha iyi toz yükleme ve sinterleme için yeni hammadde formülasyonları
- Farklı tozları tek bir bileşende birleştiren çok malzemeli MIM
- İşleme, birleştirme, diş açma vb. gibi son işlemlerin otomasyonu.
- Hibrit MIM + Katmanlı Üretim teknikleri
- Daha hızlı işleme için mikrodalga sinterleme gibi yeni ısıtma yöntemleri
- Çoklu fizik ve üretim adımlarını birleştiren entegre simülasyonlar
- Kalite yönetim sistemlerinin benimsenmesinde artış
Özet
Önemli çıkarımlar:
- MIM, enjeksiyon kalıplama ve toz metalürjisini birleştirerek karmaşık metal bileşenlerin yüksek hacimli üretimini sağlar.
- Medikal, ateşli silahlar, otomotiv, havacılık ve tüketici endüstrilerindeki küçük, karmaşık, yüksek hassasiyetli parçalar için uygundur.
- Avantajları arasında ağa yakın şekil, geniş malzeme seçeneği, dövme malzemelere yakın iyi mekanik özellikler bulunmaktadır.
- Özel ekipman kullanılarak hammaddenin kalıplanması, bağının çözülmesi ve sinterleme adımlarını içerir.
- Parça tasarımı, hammadde geliştirme, süreç modelleme, hata kontrolü ve kalite yönetimi konularında uzmanlık gerektirir.
- Sektörler arası talebin etkisiyle küresel olarak 8,7% YBBO ile büyümesi beklenmektedir.
- Daha hızlı işleme, daha fazla malzeme, daha fazla otomasyon ve daha iyi parça kalitesi için devam eden teknolojik gelişmeler.
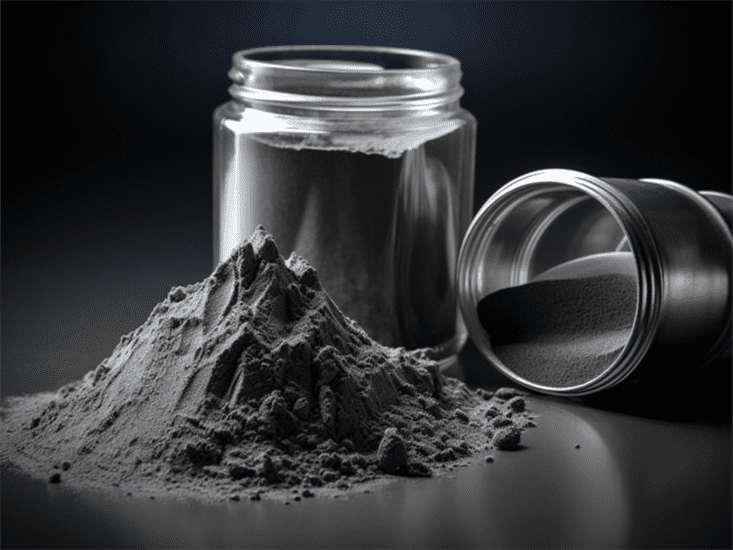
SSS
S: MIM teknolojisinin temel avantajları nelerdir?
C: MIM'in başlıca avantajları şunlardır:
- Talaşlı imalat veya döküm yoluyla mümkün olmayan küçük, karmaşık geometrileri üretme yeteneği
- Ağ şekline yakın üretim sonucunda
S: MIM'in tipik tolerans kapasitesi nedir?
C: MIM genellikle +/- 0,5% toleranslara ulaşabilir, ancak bazı geometriler için +/- 0,3% mümkündür ve daha dar toleranslar için işleme gerekebilir.
S: MIM kullanılarak hangi boyutta parçalar üretilebilir?
C: MIM, 0,1 gramdan yaklaşık 250 grama kadar kütlede parçalar üretebilir. Daha büyük parçalar mümkündür ancak kalıplama makinesi boyutundaki sınırlamalar nedeniyle zordur.
S: MIM plastik enjeksiyon kalıplama ile nasıl karşılaştırılır?
C: Her ikisi de enjeksiyon kalıplama ekipmanı kullanırken, MIM metal parçalar üretebilir, plastikler ise çok daha düşük mukavemete sahiptir. Ancak MIM, plastik enjeksiyon kalıplamaya göre daha düşük üretim oranlarına ve daha yüksek maliyetlere sahiptir.
S: MIM'de hangi ısıl işlem kullanılır?
C: MIM'deki sinterleme işlemi, metal tozunun neredeyse erime noktasına kadar ısıtılmasını içerir, bu nedenle tipik olarak başka bir ısıl işleme gerek yoktur. Özellikleri değiştirmek için gerektiğinde ek ısıl işlemler yapılabilir.
S: MIM'de hangi malzemeler kullanılabilir?
C: Paslanmaz çelikler, takım çelikleri, süper alaşımlar, titanyum, tungsten ağır alaşımlar ve manyetik alaşımlar dahil olmak üzere çok çeşitli malzemeler MIM ile üretilebilir. Yeni malzeme geliştirme, MIM'de önemli bir araştırma alanıdır.
S: MIM metal 3D baskı ile nasıl karşılaştırılır?
C: MIM, daha iyi yüzey kalitesi ve mekanik özelliklerle daha yüksek hacimler üretebilir. Ancak 3D baskı, prototipler veya özel parçalar için daha fazla tasarım özgürlüğü ve daha hızlı pazara sunma süresi sunar.
Paylaş
MET3DP Technology Co, LTD, merkezi Qingdao, Çin'de bulunan lider bir katmanlı üretim çözümleri sağlayıcısıdır. Şirketimiz, endüstriyel uygulamalar için 3D baskı ekipmanları ve yüksek performanslı metal tozları konusunda uzmanlaşmıştır.
İşletmeniz için en iyi fiyatı ve özelleştirilmiş Çözümü almak için sorgulayın!
İlgili Makaleler
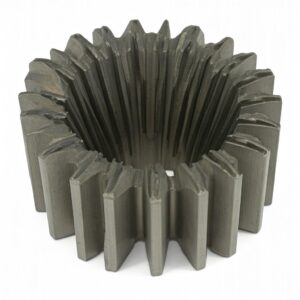
Yüksek Performanslı Nozul Kanat Segmentleri: Metal 3D Baskı ile Türbin Verimliliğinde Devrim
Daha Fazla Oku "Met3DP Hakkında
Son Güncelleme
Bizim Ürünümüz
BİZE ULAŞIN
Herhangi bir sorunuz var mı? Bize şimdi mesaj gönderin! Mesajınızı aldıktan sonra tüm ekibimizle talebinize hizmet edeceğiz.