3D-gedruckte Drohnenschalen aus leichtem Aluminium
Inhaltsübersicht
Einleitung: Die entscheidende Rolle fortschrittlicher Drohnenhüllen für die Leistung von UAVs
Der Himmel wird zunehmend bevölkert. Unbemannte Luftfahrzeuge (UAVs), gemeinhin als Drohnen bekannt, haben ihren Ursprung in militärischen Nischenanwendungen hinter sich gelassen und sind zu unverzichtbaren Werkzeugen in einem breiten Spektrum von Branchen geworden. Von der Aufnahme atemberaubender Filmaufnahmen und der Lieferung wichtiger medizinischer Güter bis hin zur Überwachung riesiger landwirtschaftlicher Felder und der Inspektion komplexer Infrastrukturen - Drohnen verändern die betriebliche Effizienz und eröffnen völlig neue Möglichkeiten. Im Mittelpunkt dieser Revolution steht das ständige Streben nach höherer Leistung: längere Flugzeiten, größere Nutzlastkapazitäten, verbesserte Manövrierfähigkeit und höhere Haltbarkeit. Entscheidend für diese Fortschritte ist die Hülle oder das Flugwerk der Drohne - das Skelett und die Haut, die ihre Fähigkeiten definieren.
Die Hülle der Drohne ist weit mehr als nur eine äußere Hülle. Sie erfüllt mehrere wichtige Funktionen:
- Strukturelle Integrität: Sie bildet das Kerngerüst, das alle Komponenten, einschließlich Motoren, Batterien, Sensoren, Navigationssysteme und Nutzlasten, trägt. Sie muss den Belastungen von Flug, Start, Landung und Umweltfaktoren standhalten.
- Aerodynamischer Wirkungsgrad: Die Form und die Oberfläche der Hülle haben einen erheblichen Einfluss auf den Luftwiderstand, den Auftrieb und die Stabilität, was sich direkt auf die Flugdauer, die Geschwindigkeit und den Batterieverbrauch auswirkt. Eine optimierte Aerodynamik ist entscheidend für die Maximierung der Leistung.
- Schutz von Bauteilen: Die Hülle schützt die empfindliche Elektronik und die Nutzlasten vor Umwelteinflüssen wie Staub, Feuchtigkeit, Stößen und Temperaturschwankungen.
- Integration der Nutzlast: Es bietet Befestigungspunkte und Platz für Kameras, Sensoren, Liefermechanismen und andere missionsspezifische Ausrüstung, die eine präzise Konstruktion und robuste Unterstützung erfordert.
- Wärmemanagement: Bei Hochleistungsdrohnen kann die Hülle dazu beitragen, die von den Motoren und der Elektronik erzeugte Wärme abzuleiten, eine Überhitzung zu verhindern und die Betriebssicherheit zu gewährleisten.
Traditionell wurden Drohnenschalen mit Methoden wie Spritzguss (hauptsächlich für Kunststoffe) oder CNC-Bearbeitung (für Metalle und einige Kunststoffe) hergestellt. Diese Methoden eignen sich zwar für die Massenproduktion einfacher Designs, stoßen aber oft an ihre Grenzen, wenn Spitzenleistungen angestrebt werden, insbesondere in Bezug auf Gewicht und Designkomplexität. Das Spritzgießen erfordert teure Werkzeuge, was die Anpassung an Kundenwünsche und die Produktion von Kleinserien kostspielig macht, und ist oft auf Materialien angewiesen, bei denen die Festigkeit auf Kosten des Gewichts geht. Die CNC-Bearbeitung ist zwar in der Lage, starke Metallteile herzustellen, kann aber sehr subtraktiv sein, was zu Materialabfall führt, und hat Probleme mit hochkomplexen Geometrien oder internen Merkmalen, die oft für eine maximale Gewichtsreduzierung und Komponentenintegration gewünscht werden.
Hier ist Additive Fertigung von Metall (AM)gemeinhin als Metall bekannt 3D-Druckentwickelt sich zu einer transformativen Kraft. Technologien wie Laser Powder Bed Fusion (LPBF) - die das selektive Laserschmelzen (SLM) und das direkte Metall-Lasersintern (DMLS) umfassen - ermöglichen den schichtweisen Aufbau von hochkomplexen Metallteilen direkt aus digitalen Entwürfen. Dieses Verfahren befreit die Konstrukteure von vielen traditionellen Fertigungsbeschränkungen und ebnet den Weg für radikal optimierte Drohnenhüllen.
Insbesondere bei Anwendungen, die eine hohe Festigkeit und ein geringes Gewicht erfordern, liegt der Schwerpunkt dieser Entwicklung zunehmend auf leichte Aluminiumlegierungen. Werkstoffe wie AlSi10Mg und der Hochleistungswerkstoff Scalmalloy® bieten ein außergewöhnliches Verhältnis von Festigkeit zu Gewicht, eine gute Korrosionsbeständigkeit und sind für die hohen Anforderungen moderner Drohnen gut geeignet. In Kombination mit der geometrischen Freiheit, die das Metall-AM bietet, ermöglichen diese Materialien die Herstellung von Drohnenhüllen, die deutlich leichter, stärker und funktionell integrierter sind als je zuvor.
Dieser Artikel taucht in die Welt der 3D-gedruckten Drohnenschalen ein und konzentriert sich dabei auf die Verwendung von leichten Aluminiumlegierungen wie AlSi10Mg und Scalmalloy®. Wir erkunden die verschiedenen Anwendungen, die von dieser Technologie profitieren, erläutern die überzeugenden Vorteile der Metall-AM gegenüber herkömmlichen Methoden, untersuchen die wichtigsten Materialeigenschaften und geben Einblicke in Designüberlegungen, Nachbearbeitung, Qualitätskontrolle und Lieferantenauswahl. Für Ingenieure, die die Grenzen des UAV-Designs ausloten, und für Beschaffungsmanager, die zuverlässige, leistungsstarke Anbieter von Drohnenkomponenten
ist das Verständnis der Möglichkeiten von 3D-gedrucktem Aluminium von größter Bedeutung. Unternehmen wie Met3dpmit ihrem umfassenden Fachwissen im Bereich der additiven Fertigungsanlagen für Metalle, fortschrittliche Systeme zur Pulverherstellung
und hochleistungsfähige Metallpulver stehen an vorderster Front und liefern die Werkzeuge und Materialien, die für die Realisierung der nächsten Generation von UAV-Leistungen erforderlich sind. Seien Sie dabei, wenn wir erkunden, wie diese Synergie aus fortschrittlichen Materialien und Fertigungstechnologien leichtere, stärkere und leistungsfähigere Drohnen für eine Vielzahl von Anwendungen ermöglicht.
Anwendungen: Wo werden die leichten Aluminium-Drohnenhüllen eingesetzt?
Die Vorteile leichter, hochfester und geometrisch komplexer Drohnenschalen, die mit 3D-gedruckten Aluminiumlegierungen hergestellt werden, sind nicht nur theoretisch, sondern werden in einer rasch wachsenden Zahl anspruchsvoller UAV-Anwendungen aktiv genutzt. Die Möglichkeit, Designs für spezifische Missionen zuzuschneiden, komplexe Funktionen zu integrieren und erhebliche Gewichtseinsparungen zu erzielen, macht diese Technologie besonders attraktiv, wenn Leistung, Langlebigkeit und individuelle Anpassung entscheidend sind. Beschaffungsmanager, die sich für Großhandel Drohne Teile
oder spezialisierte Komponenten finden, dass AM Lösungen bietet, die zuvor unerreichbar waren.
Im Folgenden finden Sie eine Aufschlüsselung der wichtigsten Sektoren und Anwendungen, in denen 3D-gedruckte Drohnenschalen aus Aluminium einen bedeutenden Einfluss haben:
1. Luft- und Raumfahrt & Verteidigung: In diesem Sektor, der oft der Schmelztiegel für Spitzentechnologie ist, werden in großem Umfang fortschrittliche UAVs eingesetzt, bei denen Leistung und Zuverlässigkeit nicht verhandelbar sind.
- Überwachung und Aufklärung (ISR): Drohnen, die für die Nachrichtengewinnung eingesetzt werden, benötigen eine lange Lebensdauer (geringes Gewicht), Tarnkappen (möglicherweise komplexe Formen zur Verringerung der Radarsignatur) und die Fähigkeit, anspruchsvolle Sensornutzlasten zu tragen. 3D-gedruckte Aluminiumschalen ermöglichen hochgradig optimierte aerodynamische Formen, integrierte Sensorhalterungen, die für spezifische Hardware entwickelt wurden, und robuste Strukturen, die auch anspruchsvollen Einsatztempi standhalten. Die hohe Festigkeit von Scalmalloy® ist besonders für kritische Strukturelemente von Vorteil.
- Taktische UAVs: Kleinere, schnell einsetzbare Drohnen, die von Bodentruppen eingesetzt werden, müssen robust, tragbar und flexibel einsetzbar sein. AM ermöglicht die Herstellung langlebiger, stoßfester Gehäuse mit integrierten Griffen, modularen Nutzlastschächten und optimierten Innenstrukturen, um die erforderliche Ausrüstung kompakt unterzubringen. Die Konsolidierung von Bauteilen reduziert potenzielle Fehlerquellen in rauen Umgebungen.
- Ziel-Drohnen: Zieldrohnen, die manchmal als Wegwerfartikel angesehen werden, müssen bestimmte Flugeigenschaften und Radarsignaturen genau nachbilden. AM ermöglicht die kosteneffiziente Herstellung komplexer aerodynamischer Formen in geringeren Stückzahlen, möglicherweise unter Verwendung von AlSi10Mg, um ein ausgewogenes Verhältnis zwischen Leistung und Kosten zu erreichen.
- Kundenspezifische Militärplattformen: Für spezielle Einsätze sind oft einzigartige Flugzeugkonstruktionen erforderlich. Metall-AM macht teure Werkzeuge für Sonderanfertigungen überflüssig und ermöglicht die schnelle Entwicklung und den Einsatz von UAVs, die auf spezifische Verteidigungsanforderungen zugeschnitten sind.
2. Gewerbliche und industrielle Tätigkeiten: Effizienz, Zuverlässigkeit und spezielle Funktionen treiben die Einführung von Drohnen in der kommerziellen Welt voran.
- Inspektion der Infrastruktur: Drohnen, die Stromleitungen, Windturbinen, Brücken, Pipelines und Eisenbahnlinien inspizieren, brauchen Stabilität, präzise Manövrierbarkeit (oft unter windigen Bedingungen) und robuste Halterungen für hochauflösende Kameras und Sensoren. Leichte Aluminiumschalen tragen zur Stabilität bei und ermöglichen längere Inspektionsrouten. In komplexe Geometrien können schwingungsdämpfende Merkmale integriert werden, um eine bessere Bildqualität zu erreichen.
- Präzisionslandwirtschaft: UAVs überwachen den Gesundheitszustand von Pflanzen, kartieren Felder und führen gezielte Sprüharbeiten durch. Die Gehäuse müssen gegen Umwelteinflüsse (Staub, Feuchtigkeit, landwirtschaftliche Chemikalien) resistent sein und verschiedene Sensoren (Multispektral- und Hyperspektralsensoren) sowie potenzielle Sprühgeräte aufnehmen können. 3D-gedrucktes Aluminium bietet Haltbarkeit und die Möglichkeit, individuelle Halterungen und Gehäuse zu erstellen.
- Logistik und Lieferung: Der aufstrebende Bereich der Drohnenzustellung erfordert aerodynamische Effizienz für Geschwindigkeit und Reichweite, strukturelle Integrität für den Transport von Paketen unterschiedlicher Größe und Gewichte sowie Haltbarkeit für häufige Starts und Landungen. Topologieoptimierte Aluminiumschalen bieten das erforderliche Verhältnis von Festigkeit zu Gewicht und maximieren die Nutzlastkapazität und die Batterielebensdauer.
Herstellung kundenspezifischer Drohnen
ist hier unerlässlich, da die Lieferplattformen oft sehr spezialisiert sind. - Kinematographie und Luftbildaufnahmen: Professionelle Kameradrohnen erfordern extreme Stabilität, Vibrationsdämpfung und die Fähigkeit, schwere, hochwertige Kameranutzlasten zu tragen. Leichte, steife Aluminiumrahmen, die möglicherweise komplexe, mittels AM entwickelte Gitterstrukturen enthalten, minimieren Vibrationen und ermöglichen flüssigere Aufnahmen. Kundenspezifische Halterungen können direkt in das Gehäusedesign integriert werden.
- Kartierung und Vermessung: Ähnlich wie bei Inspektionen benötigen diese Drohnen stabile Plattformen für die genaue Datenerfassung mit LiDAR- oder Photogrammetriesensoren. Die Gewichtsreduzierung verlängert die Flugzeit und ermöglicht die Abdeckung größerer Gebiete pro Einsatz.
3. Notdienste und öffentliche Sicherheit: Drohnen werden zu wichtigen Hilfsmitteln für Ersthelfer.
- Suche und Rettung (SAR): SAR-Drohnen werden in schwierigem Gelände und unter schwierigen Wetterbedingungen eingesetzt. Die Schalen müssen robust und wetterfest sein und Wärmebildkameras, Scheinwerfer und möglicherweise Kommunikationsrelais oder kleine medizinische Geräte tragen können. 3D-gedrucktes Aluminium sorgt für die nötige Widerstandsfähigkeit und ermöglicht die Integration spezieller Halterungen für die Ausrüstung.
- Katastrophenhilfe und Überwachung: Nach Naturkatastrophen bieten Drohnen ein schnelles Situationsbewusstsein. Robuste, leicht einsetzbare Drohnen mit anpassungsfähiger Nutzlast sind unerlässlich. AM erleichtert die schnelle Herstellung von Ersatzteilen oder maßgeschneiderten Konfigurationen nach Bedarf.
Zusammenfassende Tabelle: Anwendungen und Vorteile von 3D-gedruckten Aluminiumschalen
Anwendungsbereich | Spezifische Beispiele für Anwendungsfälle | Wichtige Shell-Anforderungen | Wie 3D-gedrucktes Aluminium (AlSi10Mg/Scalmalloy®) die Anforderungen erfüllt |
---|---|---|---|
Luft- und Raumfahrt & Verteidigung | ISR, taktische UAVs, Zieldrohnen | Geringes Gewicht, hohe Festigkeit, Langlebigkeit, Tarnfunktionen, Sensorintegration, individuelle Anpassung | Optimiertes Verhältnis von Festigkeit zu Gewicht, komplexe Geometrien für Aerodynamik/Tarnkappe, integrierte Halterungen, Rapid Prototyping/Anpassung |
Kommerziell/Industriell | Infrastruktur-Inspektion, Landwirtschaft, Lieferung, Kino | Stabilität, Nutzlastkapazität, Langlebigkeit, Umweltbeständigkeit, aerodynamische Effizienz | Gewichtsreduzierung für Langlebigkeit/Nutzlast, kundenspezifische/integrierte Halterungen, robuste Konstruktion, optimierte Formen für Effizienz |
Notfalldienste | Suche und Rettung, Katastrophenhilfe | Robustheit, Witterungsbeständigkeit, Nutzlastflexibilität, schnelle Einsetzbarkeit | Langlebige Materialien, Designfreiheit für integrierte Funktionen/Dichtungen, Teilekonsolidierung für Zuverlässigkeit, Produktion auf Abruf |
In Blätter exportieren
Die Vielfalt dieser Anwendungen unterstreicht die Vielseitigkeit und das Hochleistungspotenzial von Drohnenschalen, die mit additiver Fertigung und modernen Aluminiumlegierungen hergestellt werden. Als Ingenieure und Lieferanten von Drohnenteilen
Durch weitere Innovationen wird 3D-gedrucktes Aluminium zunehmend zu einer Standardlösung, um die Grenzen der UAV-Fähigkeiten in allen Sektoren zu erweitern.
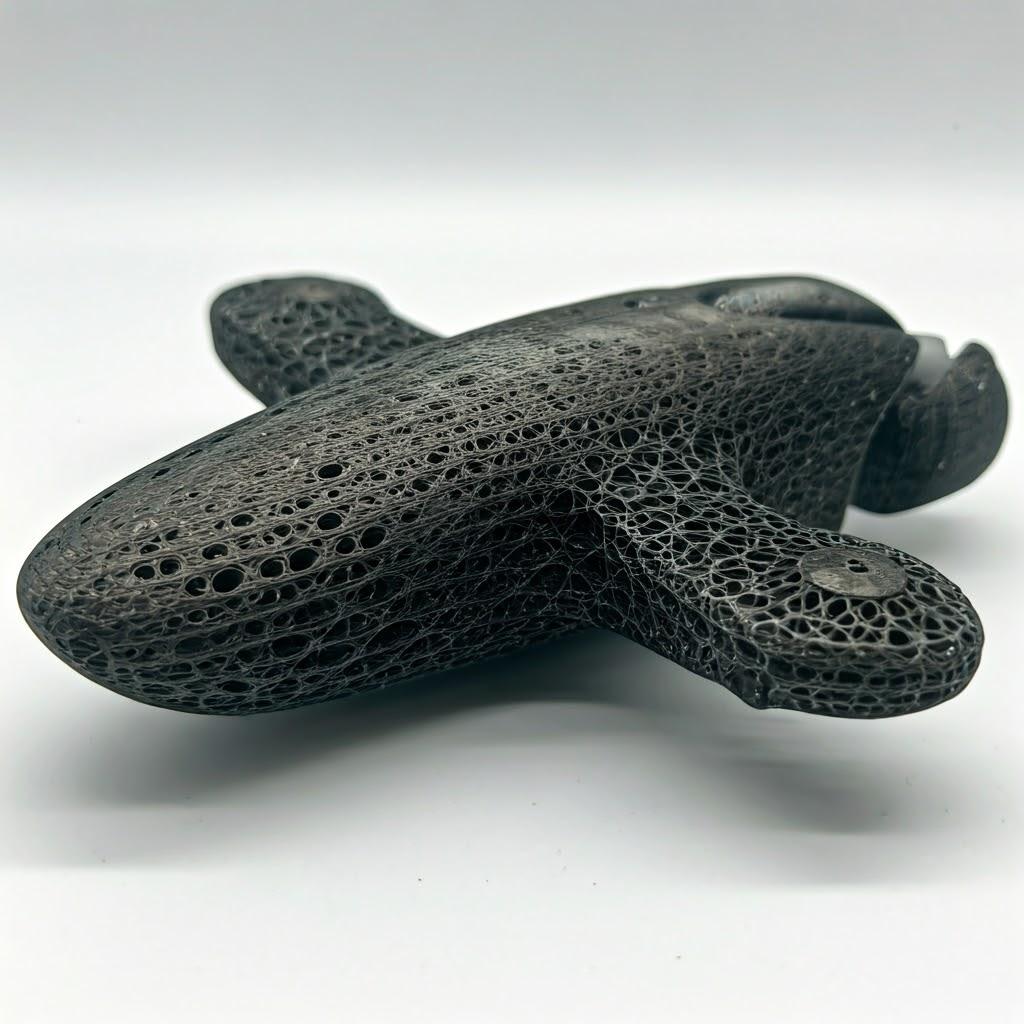
Warum 3D-Metalldruck für Drohnenschalen? Designfreiheit und Leistung freisetzen
Die Entscheidung für den Einsatz der additiven Fertigung von Metallen, insbesondere der Laser Powder Bed Fusion (LPBF), zur Herstellung von Drohnengehäusen beruht auf einer Reihe von überzeugenden Vorteilen, die die Grenzen herkömmlicher Fertigungsmethoden direkt ansprechen und perfekt mit den Zielen der modernen Drohnenentwicklung übereinstimmen: geringeres Gewicht, höhere Leistung und größere Designflexibilität. Für Ingenieure, die nach Innovation streben, und für Beschaffungsmanager, die nach innovativen, zuverlässigen Komponenten suchen, bietet Metal AM einen Paradigmenwechsel. Sehen wir uns die wichtigsten Gründe an, warum diese Technologie für Hochleistungsdrohnenstrukturen unverzichtbar wird.
1. Unerreichte Gestaltungsfreiheit und geometrische Komplexität: Dies ist wohl der transformativste Vorteil von AM. Im Gegensatz zu subtraktiven Verfahren (CNC-Bearbeitung), bei denen das Material abgetragen wird, oder zu formgebenden Verfahren (Gießen, Formen), die auf vordefinierte Formen oder Gesenke angewiesen sind, baut AM Teile Schicht für Schicht auf. Dieser additive Ansatz erschließt das Potenzial für:
- Hochkomplexe Geometrien: Die Konstrukteure können komplizierte Formen, interne Kanäle (für Kühlung oder Verkabelung), konforme Strukturen und organische Formen schaffen, die auf herkömmliche Weise nur schwer oder gar nicht zu realisieren sind. Dies ermöglicht eine extreme aerodynamische Optimierung, die auf bestimmte Flugbereiche zugeschnitten ist.
- Topologie-Optimierung: Ausgefeilte Softwarealgorithmen können Lastpfade und Spannungen innerhalb einer Drohnenschalenkonstruktion analysieren und Material aus unkritischen Bereichen entfernen, während hochbelastete Regionen verstärkt werden. Das Ergebnis sind leichte, hocheffiziente Strukturen, bei denen das Material nur dort eingesetzt wird, wo es strukturell notwendig ist.
Topologieoptimierung für Drohnenrahmen
ist eine wichtige Voraussetzung für eine drastische Gewichtsreduzierung. - Gitterförmige Strukturen: AM ermöglicht die Integration interner Gitterstrukturen - komplexe, sich wiederholende Netze aus Streben oder Zellen. Diese Strukturen können das Gewicht erheblich reduzieren und gleichzeitig eine hohe Steifigkeit und Festigkeit beibehalten. Außerdem können sie so konstruiert werden, dass sie bestimmte Schwingungsdämpfungs- oder Energieabsorptionseigenschaften aufweisen, die für den Schutz empfindlicher Nutzlasten entscheidend sind.
- Teil Konsolidierung: Mehrere Komponenten, die traditionell separat hergestellt und dann zusammengebaut werden (z. B. Halterungen, Befestigungen, Abschnitte des Gehäuses), können oft neu entworfen und als ein einziges, monolithisches Teil gedruckt werden. Dies reduziert die Anzahl der Teile, die Montagezeit, das Gewicht und potenzielle Fehlerquellen (Befestigungselemente, Verbindungen).
- Integrierte Funktionalitäten: Merkmale wie Befestigungspunkte für Sensoren, Antennen, Kabelkanäle, Batterieanschlüsse und sogar Flüssigkeitskanäle können direkt in das Gehäusedesign integriert werden, was die Montage vereinfacht und die Systemintegration insgesamt verbessert.
2. Erhebliches Leichtbaupotenzial: Das Gewicht ist ein Hauptfeind der Drohnenleistung. Jedes Gramm, das eingespart wird, führt direkt zu greifbaren Vorteilen: längere Flugzeiten, höhere Nutzlastkapazität, verbesserte Agilität und Manövrierbarkeit sowie geringerer Energieverbrauch. Metall-AM erleichtert die Gewichtsreduzierung durch mehrere Mechanismen, die durch Designfreiheit ermöglicht werden:
- Topologie-Optimierung: Wie bereits erwähnt, führt das Entfernen von strukturell unnötigem Material zu leichteren Teilen. Im Vergleich zu traditionell konstruierten Metallteilen sind oft Einsparungen von 20-50% möglich.
- Gitterförmige Strukturen: Das Ersetzen von Volumenkörpern durch optimierte Gitter ermöglicht eine drastische Gewichtsreduzierung bei gleichzeitiger Wahrung der strukturellen Integrität.
- Materialien mit hoher Festigkeit im Verhältnis zum Gewicht: AM-Verfahren eignen sich hervorragend für Materialien wie AlSi10Mg und insbesondere Scalmalloy®, die im Vergleich zu vielen konventionell verwendeten Materialien (einschließlich einiger Kunststoffe und Standardaluminiumsorten) eine höhere Festigkeit im Verhältnis zu ihrer Dichte aufweisen. Dies ermöglicht dünnere Wände und schlankere Strukturelemente, ohne die Festigkeit zu beeinträchtigen.
- Teil Konsolidierung: Durch den Wegfall von Verbindungselementen (Schrauben, Nieten, Bolzen) und Montageschnittstellen wird das Gesamtgewicht weiter reduziert.
3. Verbesserte Materialleistung und -auswahl: Bei der Metall-AM geht es nicht nur um die Form, sondern auch um den Einsatz fortschrittlicher Materialien, die speziell für das Verfahren geeignet sind oder sogar dafür entwickelt wurden.
- Optimierte Mikrostrukturen: Die schnelle Erwärmung und Abkühlung, die LPBF-Prozessen eigen ist, kann zu feinkörnigen Mikrostrukturen in Legierungen wie AlSi10Mg und Scalmalloy® führen, was oft zu mechanischen Eigenschaften (wie Festigkeit und Härte) führt, die denen von gegossenen oder gekneteten Gegenstücken entsprechen oder diese übertreffen, insbesondere nach entsprechenden Wärmebehandlungen nach dem Prozess.
- Zugang zu Hochleistungslegierungen: AM ermöglicht den praktischen Einsatz von Legierungen wie Scalmalloy®, die speziell für die additive Fertigung entwickelt wurden und Leistungsmerkmale bieten, die bei komplexen Aluminiumkomponenten bisher nur schwer zu erreichen waren.
- Konsistente Materialeigenschaften: Eine fortschrittliche Prozesssteuerung und hochwertige Pulver, wie sie mit Met3dp's
fortschrittliche Systeme zur Pulverherstellung
gewährleisten gleichbleibende Materialeigenschaften über das gesamte gedruckte Teil, was für eine zuverlässige Leistung entscheidend ist.
4. Rapid Prototyping, Iteration und Anpassung: Das Innovationstempo in der Drohnenindustrie ist rasant. Metall-AM beschleunigt den Entwicklungszyklus erheblich.
- Werkzeugfreie Produktion: AM erfordert keine Gussformen, Matrizen oder spezielle Werkzeuge. Die Teile können direkt aus einer CAD-Datei gedruckt werden. Dadurch werden die Vorlaufzeit und die Kosten für die Herstellung erster Prototypen oder für Designänderungen drastisch reduziert.
- Schnelle Design-Iteration: Ingenieure können eine Drohnenhülle entwerfen, einen funktionalen Prototyp aus Aluminium drucken, ihn testen, verbesserungswürdige Bereiche identifizieren, den digitalen Entwurf ändern und eine überarbeitete Version innerhalb von Tagen oder Wochen statt Monaten drucken. Dieser iterative Kreislauf ermöglicht eine schnelle Optimierung und Verfeinerung.
- Kosteneffiziente Anpassung: Die Herstellung einzigartiger oder in Kleinserien hergestellter Drohnenschalen ist mit AM wirtschaftlich machbar. Ganz gleich, ob es sich um eine spezifische Nutzlast für eine Mission, ein einzigartiges Sensorsystem oder eine maßgeschneiderte Forschungsplattform handelt, AM ermöglicht
Partner für die Herstellung kundenspezifischer Drohnen
um maßgeschneiderte Lösungen zu liefern, ohne die unerschwinglichen Kosten der traditionellen Werkzeugherstellung für kleine Serien.
5. Vorteile der Lieferkette und bedarfsorientierte Fertigung: AM bietet ein flexibleres und potenziell widerstandsfähigeres Lieferkettenmodell.
- Reduzierte Vorlaufzeiten: Bei komplexen Teilen kann die Gesamtdurchlaufzeit von der Fertigstellung des Designs bis zum fertigen Teil mit AM oft kürzer sein als mit der Koordination mehrerer traditioneller Fertigungsschritte und der Montage.
- Produktion auf Abruf: Die Teile können je nach Bedarf gedruckt werden, wodurch sich der Bedarf an großen Lagerbeständen von Fertigwaren oder Komponenten verringert. Dies ist besonders für spezialisierte, hochwertige Drohnenschalen von Vorteil.
- Verteilte Fertigung: Die Produktion kann potenziell dezentralisiert werden, wodurch die Herstellung näher an den Ort des Bedarfs rückt und die Transportkosten und die logistische Komplexität reduziert werden.
Vergleich: Metall-AM vs. traditionelle Methoden für Drohnenhüllen
Merkmal | Metall AM (LPBF - Al-Legierungen) | CNC-Bearbeitung (Aluminium) | Spritzgießen (Kunststoffe) | Verbundwerkstoff-Layup (z. B. Kohlefaser) |
---|---|---|---|---|
Geometrische Komplexität | Sehr hoch (interne Merkmale, Gitter) | Mäßig (begrenzt durch den Zugang zu Werkzeugen) | Hoch (erfordert jedoch komplexe Formen) | Mäßig-Hoch (Einschränkungen durch die Form) |
Potenzial zur Gewichtsreduzierung | Sehr hoch (Topologie opt., Gitternetze) | Mäßig (subtraktive Grenzen) | Mäßig (Materialdichte begrenzt) | Sehr hoch (ausgezeichnetes Verhältnis von Festigkeit zu Gewicht) |
Materialstärke | Hoch (AlSi10Mg) bis sehr hoch (Scalmalloy®) | Hoch (abhängig von der Legierung) | Gering bis mäßig | Sehr hoch |
Vorlaufzeit für Prototyping | Fasten (Tage/Wochen) | Mäßig (Wochen) | Langsam (Monate - wegen der Werkzeugherstellung) | Mäßig langsam (manueller Prozess/Tooling) |
Produktionsvorlaufzeit | Mäßig (abhängig von der Skalierbarkeit) | Schnell (für hohes Volumen) | Sehr schnell (für hohes Volumen) | Langsam (arbeitsintensiv) |
Kosten der Anpassung | Niedrig (keine Werkzeuge) | Hoch (Programmierung/Einrichtung) | Sehr hoch (Werkzeugänderung) | Hoch (Änderung der Form/Werkzeuge) |
Werkzeugkosten | Keiner | Niedrig-Mäßig (Vorrichtungen) | Sehr hoch | Mäßig-hoch |
Teil Konsolidierung | Ausgezeichnet | Begrenzt | Begrenzt | Begrenzt |
In Blätter exportieren
Während Verbundwerkstoffe wie Karbonfasern ein hervorragendes Leichtgewicht darstellen, bietet Metall-AM Vorteile bei der Herstellung extrem komplexer monolithischer Strukturen, isotrope Materialeigenschaften (vorhersagbare Festigkeit in allen Richtungen) und oft eine einfachere Integration von Gewindeelementen oder komplexen Montageschnittstellen im Vergleich zu Verbundwerkstoffen. Darüber hinaus bieten das Know-how und die fortschrittlichen Systeme von Unternehmen, die sich auf 3D-Druck von Metall stellen sicher, dass das Potenzial dieser Aluminiumlegierungen voll ausgeschöpft wird und Teile entstehen, die den strengen Anforderungen der Luft- und Raumfahrt und der Industrie entsprechen. Die Kombination aus Designfreiheit, Leichtbau, Materialleistung und schneller Iteration macht Metall-AM zu einem unverzichtbaren Werkzeug für die Entwicklung der nächsten Generation von Hochleistungsdrohnenschalen.
Werkstoff-Fokus: AlSi10Mg und Scalmalloy® für leistungsstarke Drohnenstrukturen
Die Wahl des richtigen Materials ist von grundlegender Bedeutung für die Konstruktion von Hochleistungskomponenten, und Drohnenschalen bilden da keine Ausnahme. Während in der additiven Fertigung verschiedene Materialien verwendet werden können, haben sich Aluminiumlegierungen aufgrund ihrer überzeugenden Kombination aus geringer Dichte, guten mechanischen Eigenschaften, Korrosionsbeständigkeit und Verarbeitbarkeit mit Laser Powder Bed Fusion (LPBF)-Verfahren als beliebte Wahl für Drohnenstrukturen herausgestellt. Innerhalb der Familie des druckbaren Aluminiums stechen zwei Legierungen für Drohnenanwendungen hervor: das Arbeitspferd AlSi10Mg und die leistungsstarke Scalmalloy®. Für Ingenieure und Beschaffungsmanager, die das Design von UAVs optimieren wollen, ist es entscheidend, ihre Eigenschaften, Vorteile und idealen Anwendungsfälle zu kennen. Darüber hinaus ist die Beschaffung dieser Materialien von seriösen Lieferanten von Metallpulver
die Qualität und Konsistenz garantieren, wie Met3dp mit seinem hochmodernen fortschrittliche Systeme zur Pulverherstellung
ist für die Erzielung zuverlässiger und wiederholbarer Ergebnisse unerlässlich.
Einführung in Aluminiumlegierungen in der Metall-AM:
Aluminiumlegierungen sind wesentlich leichter als Stähle oder Titanlegierungen, was sie für Anwendungen in der Luft- und Raumfahrt, bei denen Gewichtseinsparungen im Vordergrund stehen, von Natur aus attraktiv macht. Im Zusammenhang mit LPBF stellen Aluminiumlegierungen aufgrund ihres hohen Reflexionsvermögens und ihrer Wärmeleitfähigkeit einige Herausforderungen dar, aber dank der Fortschritte in der Maschinentechnologie und der Entwicklung von Prozessparametern ist das Drucken hochwertiger Aluminiumteile inzwischen Routine. Die verwendeten Legierungen enthalten in der Regel Elemente wie Silizium (zur Verbesserung der Fließfähigkeit und zur Verringerung der Rissneigung), Magnesium (zur Verfestigung durch Wärmebehandlung) und im Falle von Scalmalloy® Scandium und Zirkonium (für außergewöhnliche Festigkeit).
AlSi10Mg: Das vielseitige Arbeitspferd
- Zusammensetzung und Merkmale: AlSi10Mg ist im Wesentlichen eine Aluminiumgusslegierung für die additive Fertigung. Sie enthält etwa 9-11% Silizium und 0,2-0,45% Magnesium. Der Siliziumgehalt sorgt für eine gute "Schweißbarkeit" während des schichtweisen Schmelzprozesses und minimiert die Rissbildung, während das Magnesium eine Ausscheidungshärtung der Legierung durch Wärmebehandlung ermöglicht.
- Vorteile für Drone Shells:
- Breite Verfügbarkeit und Reifegrad: Es ist eine der gängigsten und am besten charakterisierten Aluminiumlegierungen, die in der Metall-AM verwendet werden, was bedeutet, dass die Prozessparameter gut bekannt sind und eine Fülle von Daten verfügbar ist.
- Gute Verarbeitbarkeit: Er druckt im Allgemeinen zuverlässig mit guter Dichte und Oberflächengüte, die mit verschiedenen LPBF-Plattformen erreicht werden können.
- Ausgezeichnete thermische Eigenschaften: Es weist eine gute Wärmeleitfähigkeit auf, was für die Wärmeableitung von Motoren oder der in die Drohnenhülle integrierten Elektronik von Vorteil sein kann.
- Gutes Verhältnis von Stärke zu Gewicht: Es ist zwar nicht so stark wie Scalmalloy®, bietet aber eine deutliche Verbesserung gegenüber den meisten Kunststoffen und ein ausgewogenes Verhältnis von Festigkeit, Steifigkeit und geringem Gewicht, das sich für viele Strukturkomponenten eignet.
- Kosten-Nutzen-Verhältnis: Im Allgemeinen ist AlSi10Mg-Pulver preiswerter als Hochleistungslegierungen wie Scalmalloy® und eignet sich daher für Prototypen, weniger anspruchsvolle Strukturteile und Anwendungen, bei denen das Budget eine wichtige Rolle spielt.
- Typische mechanische Eigenschaften: Die Eigenschaften können je nach den Druckparametern und der Wärmebehandlung variieren. Eine typische T6-Wärmebehandlung (Lösungsglühen und künstliche Alterung) verbessert die Festigkeit und Härte erheblich. | Eigenschaft | Zustand | Typischer Wertebereich | Einheit | Anmerkungen | | :------- | :----- | :--------- | :---- | :-------------- | | Dichte | Druckzustand | ~ 2,67 | g/cm³ | Deutlich leichter als Stahl oder Titan | | Höchstzugkraft | Druckzustand | 330 - 430 | MPa | | | Höchstzugkraft | Wärmebehandelt (T6) | 440 - 480 | MPa | Vergleichbar mit mittelfesten Al-Knetlegierungen | | | Streckgrenze (0.2%)| Druckfrisch | 180 - 250 | MPa | | Streckgrenze (0.2%)| Wärmebehandelt (T6) | 280 - 330 | MPa | Deutliche Erhöhung nach der Wärmebehandlung | | Bruchdehnung | Druckfrisch | 6 - 11 | % | Angemessene Duktilität | | Bruchdehnung | Wärmebehandelt (T6) | 8 - 15 | % | Verbessert sich oft leicht mit T6 | | Härte | Wärmebehandelt (T6) | 110 - 130 | HV | Gute Härte für Verschleißfestigkeit |
- Ideale Anwendungen: Allzweck-Drohnenschalen, Prototypen, die Metalleigenschaften erfordern, strukturelle Halterungen, in Rahmen integrierte Kühlkörper, Komponenten, bei denen die Kosten im Vordergrund stehen, aber eine über Kunststoff hinausgehende Festigkeit erforderlich ist.
Scalmalloy®: Der Hochleistungschampion
- Zusammensetzung und Merkmale: Die von APWORKS (einer Airbus-Tochtergesellschaft) entwickelte Scalmalloy® ist eine Aluminium-Magnesium-Scandium-Zirkonium-Legierung (Al-Mg-Sc-Zr), die speziell für die harten Anforderungen der additiven Fertigung entwickelt wurde. Durch die geringen Zusätze von Scandium und Zirkonium entstehen während des Drucks und der Wärmebehandlung extrem feine Ausscheidungen, die zu außergewöhnlichen mechanischen Eigenschaften führen.
- Vorteile für Drone Shells:
- Außergewöhnliches Verhältnis von Stärke zu Gewicht: Dies ist die entscheidende Eigenschaft von Scalmalloy®. Seine spezifische Festigkeit (Festigkeit geteilt durch Dichte) erreicht oder übertrifft die einiger hochfester Stähle und Titanlegierungen, was wirklich minimale Konstruktionen ermöglicht.
- Hohe Duktilität: Im Gegensatz zu vielen anderen hochfesten Aluminiumlegierungen weist Scalmalloy® eine gute Duktilität auf, was es widerstandsfähiger gegen Brüche unter Belastung macht.
- Ausgezeichnete Ermüdungsfestigkeit: Entscheidend für Komponenten, die zyklischen Belastungen und Vibrationen ausgesetzt sind, wie z. B. Flugwerke von Drohnen und Motorhalterungen.
- Gute Schweißbarkeit und Korrosionsbeständigkeit: Es zeichnet sich durch gute Schweißbarkeit (nützlich für eventuelle Nachbearbeitungen oder Reparaturen) und Korrosionsbeständigkeit aus, die für Luft- und Raumfahrt und Außenanwendungen geeignet ist.
- Ermöglicht extremes Lightweighting: Dank seiner hohen Festigkeit können die Konstrukteure die Topologieoptimierung und dünnwandige Designs weiter vorantreiben, als dies mit AlSi10Mg möglich ist, was zu einer maximalen Gewichtsreduzierung führt.
- Typische mechanische Eigenschaften: Scalmalloy® erfordert in der Regel eine spezielle Wärmebehandlung, um seine optimalen Eigenschaften zu erreichen. | Eigenschaft | Zustand | Typischer Wertebereich | Einheit | Anmerkungen | | :------- | :------ | :------ | :-- | :--------------------- | | Dichte | Druckfrisch | ~ 2,66 | g/cm³ | Ähnliche Dichte wie AlSi10Mg | | Höchstzugkraft | Wärmebehandelt | 520 - 540 | MPa | Deutlich höher als AlSi10Mg T6, annähernd auf dem Niveau von Ti-6Al-4V | | Streckgrenze (0.2%)| Wärmebehandelt | 480 - 500 | MPa | Außergewöhnlich hohe Streckgrenze für eine Aluminiumlegierung | | Bruchdehnung | Wärmebehandelt | 11 - 15 | % | Ausgezeichnete Duktilität für sein Festigkeitsniveau | | Ermüdungsfestigkeit | Wärmebehandelt | Hoch | MPa | Überragende Ermüdungseigenschaften, die für dynamische Belastungen entscheidend sind |
- Ideale Anwendungen: Primäre Strukturbauteile für Hochleistungsdrohnen, einsatzkritische Teile der Flugzeugzelle, Anwendungen, die eine größtmögliche Gewichtsreduzierung erfordern, Bauteile, die hohen zyklischen Belastungen oder Vibrationen ausgesetzt sind, wobei schwerere Materialien wie Titan oder Stahl nach Möglichkeit ersetzt werden.
Die Wahl zwischen AlSi10Mg und Scalmalloy®:
Die Auswahl hängt stark von den spezifischen Anforderungen an die Drohnenhülle und den Projektbedingungen ab:
- Leistungsbedürfnisse: Wenn die Maximierung von Festigkeit-Gewichts-Verhältnis, Ermüdungsbeständigkeit und Gesamtleistung oberste Priorität hat, ist Scalmalloy® trotz seiner höheren Kosten die überlegene Wahl.
- Kostenzwänge: Wenn das Budget knapper ist oder die strukturellen Anforderungen weniger extrem sind, bietet AlSi10Mg eine sehr leistungsfähige und wirtschaftlichere Lösung.
- Prototyping vs. Produktion: AlSi10Mg wird aufgrund seiner geringeren Kosten und breiteren Verfügbarkeit oft für funktionale Prototypen im Frühstadium bevorzugt, während Scalmalloy® möglicherweise für Produktionsteile von Hochleistungsdrohnen ausgewählt wird.
- Betriebsumgebung: Beide bieten eine gute Korrosionsbeständigkeit, aber spezifische Umweltfaktoren könnten das eine oder andere leicht begünstigen oder spezifische Oberflächenbehandlungen erforderlich machen (später besprochen).
Letztendlich stellen sowohl AlSi10Mg als auch Scalmalloy® ausgezeichnete Optionen für 3D-gedruckte Aluminium-Drohnenhüllen dar, die durch fortschrittliche LPBF-Technologie und hochwertige Metallpulver ermöglicht werden. Die Partnerschaft mit einem sachkundigen AM-Dienstleister wie Met3dp, der Fachwissen in beiden Druckverfahren und der Materialwissenschaft kombiniert – unterstützt durch seine Investition in die Herstellung von Premium-Pulvern durch Methoden wie Gasverdüsung – stellt sicher, dass das gewählte Material sein volles Potenzial entfaltet und zu leichteren, stärkeren und leistungsfähigeren UAVs führt.
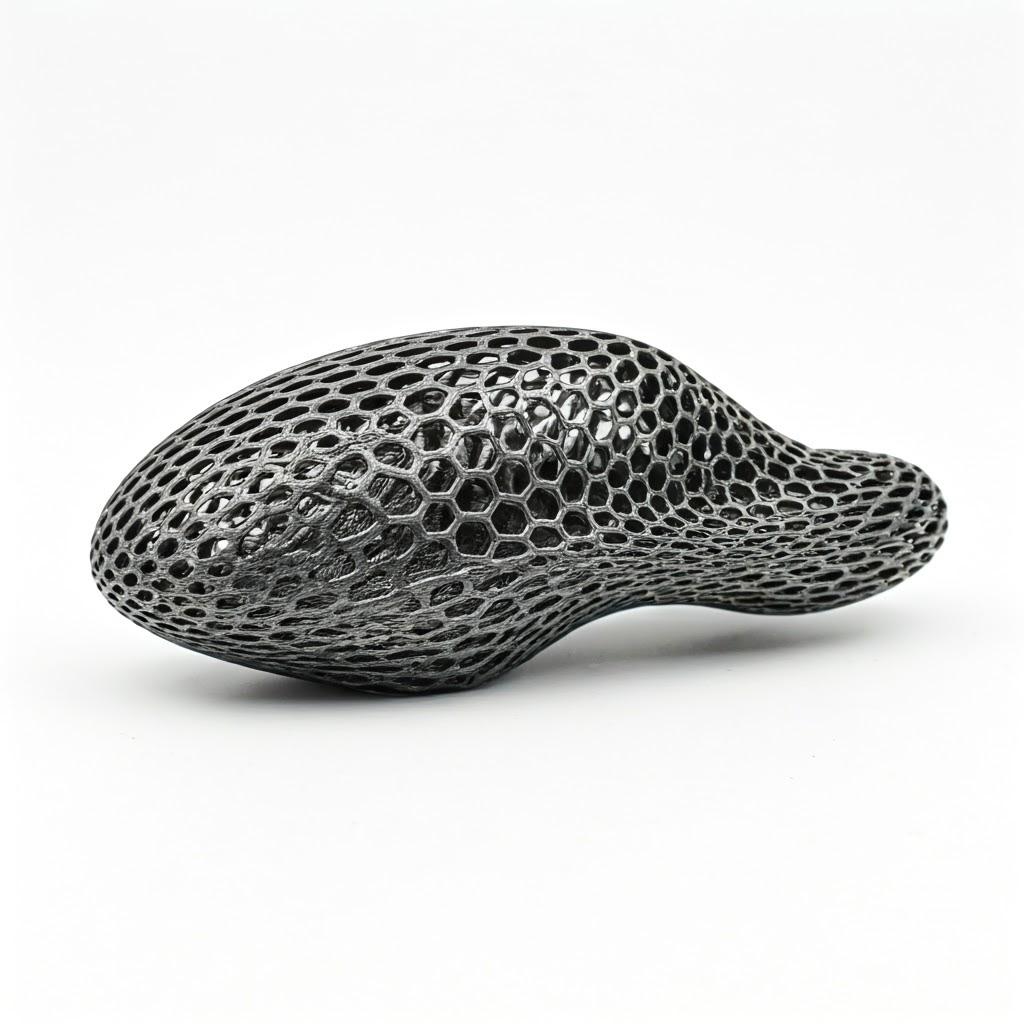
Design for Additive Manufacturing (DfAM): Optimierung von Drohnenhüllen für den 3D-Druck
Die erfolgreiche Nutzung des Metall-3D-Drucks für Drohnenhüllen besteht nicht nur darin, ein bestehendes Design zu übernehmen und „Drucken“ zu drücken. Um das transformative Potenzial der additiven Fertigung wirklich zu erschließen – maximale Gewichtsreduzierung zu erreichen, komplexe Funktionalitäten zu integrieren und eine kostengünstige, qualitativ hochwertige Produktion sicherzustellen – ist die Anwendung einer Methodik erforderlich, die als Design für additive Fertigung (DfAM)bekannt ist. DfAM ist eine grundlegende Denkweise, die sich von den Einschränkungen der traditionellen Fertigung entfernt und Teile speziell so konstruiert, dass sie die Vorteile des Schicht-für-Schicht-Aufbauprozesses nutzen, der durch Technologien wie das Laser Powder Bed Fusion (LPBF) geboten wird. Für Ingenieure, die die nächste Generation von UAVs entwerfen, ist die Beherrschung der DfAM-Prinzipien von größter Bedeutung; für Beschaffungsmanager ist das Verständnis dieser Prinzipien hilfreich bei der Bewertung der Fähigkeiten potenzieller DfAM-Dienstleistungen
und AM-Partner.
Warum ist DfAM für Aluminium-Drohnenhüllen so wichtig? Denn die einfache Nachbildung eines für CNC-Bearbeitung oder Spritzguss vorgesehenen Designs mit AM führt oft zu suboptimalen Ergebnissen: Teile, die unnötig schwer sind, übermäßige Stützstrukturen erfordern (was die Kosten und die Nachbearbeitungszeit erhöht), unter höheren Eigenspannungen leiden oder die einzigartigen geometrischen Möglichkeiten von AM nicht nutzen. Effektives DfAM führt hingegen zu überlegenen Komponenten, die sowohl hinsichtlich Leistung als auch Fertigbarkeit innerhalb des AM-Prozesses optimiert sind.
Hier sind wichtige DfAM-Prinzipien, die für die Optimierung von Aluminium-Drohnenhüllen für LPBF unerlässlich sind:
1. Strategische Teileausrichtung und Minimierung der Stützstruktur: Wie ein Teil auf der Bauplatte ausgerichtet ist, wirkt sich tiefgreifend auf mehrere Faktoren aus:
- Stützbedarf: LPBF erfordert Stützstrukturen für überhängende Merkmale, die typischerweise unter einem bestimmten Winkel liegen (oft etwa 45 Grad für Aluminium, obwohl material- und parameterabhängig). Die strategische Ausrichtung zielt darauf ab, das Volumen und die Komplexität dieser Stützen zu minimieren.
- Oberfläche: Unterschiedliche Oberflächen (nach oben, nach unten, vertikale Wände) weisen unterschiedliche Rauheiten auf. Die Ausrichtung kann der Oberflächenqualität auf kritischen Oberflächen Priorität einräumen. Nach unten gerichtete Oberflächen neigen aufgrund des Kontakts mit Stützen dazu, rauer zu sein.
- Eigenspannung: Die Ausrichtung beeinflusst die Wärmeverteilung und die Abkühlraten und wirkt sich auf den inneren Spannungsaufbau aus.
- Druckzeit & Kosten: Höhere Drucke dauern im Allgemeinen länger. Die Minimierung der Höhe (Z-Achse) kann die Bauzeit verkürzen.
- Feature-Genauigkeit: Feine Merkmale lösen sich möglicherweise besser in bestimmten Ausrichtungen auf.
- DfAM-Ziel: Richten Sie die Drohnenhülle so aus, dass steile Überhänge minimiert werden. Verwenden Sie nach Möglichkeit selbsttragende Winkel. Entwerfen Sie Merkmale wie Fasen oder Rundungen anstelle von scharfen horizontalen Überhängen. Wenn Stützen unvermeidlich sind, entwerfen Sie sie so, dass sie leicht entfernt werden können, ohne die Oberfläche des Teils zu beschädigen, und integrieren Sie möglicherweise bestimmte Sollbruchstellen oder verwenden Sie Gitterstützen, die weniger Material verbrauchen und leichter zu lösen sind.
2. Nutzung von Topologieoptimierung und Gitterstrukturen: Diese leistungsstarken Berechnungswerkzeuge sind untrennbar mit DfAM verbunden:
- Topologie-Optimierung: Software analysiert die Lastbedingungen (z. B. Motorschub, Landeaufprall, Nutzlastgewicht) auf der Drohnenhülle und entfernt intelligent Material aus Bereichen mit geringer Belastung, wodurch eine optimierte, oft organisch aussehende tragende Struktur entsteht. Dies ist ein Haupttreiber für die Erzielung dramatischer Gewichtsreduzierungen (z. B. die Umwandlung einer massiven Montagehalterung in einen Skelettrahmen) bei gleichzeitiger Beibehaltung oder sogar Erhöhung der Steifigkeit in kritischen Bereichen.
- Gitterförmige Strukturen: Anstelle einer massiven Füllung können Designer interne Gitter (Waben, Gyroid, stochastische Schäume usw.) integrieren. Diese bieten bemerkenswerte Gewichtseinsparungen mit maßgeschneiderten strukturellen Eigenschaften (Steifigkeit, Energieabsorption). Für Drohnenhüllen können Gitter nichtkritische Volumina füllen, Schwingungen dämpfen oder bestimmte Knautschzonen für den Aufprallschutz schaffen. Die Auswahl des geeigneten Gittertyps, der Zellgröße und der Strebenstärke ist entscheidend.
3. Anwendung der Teilekonsolidierung: Die Fähigkeit von AM, komplexe Einzelteile herzustellen, ermöglicht es Designern, Baugruppen neu zu überdenken:
- Konzept: Kombinieren Sie mehrere, traditionell getrennte Komponenten (z. B. Hüllenteile, Motorhalterungen, Batteriefächer, Kabelclips, Antennengehäuse) zu einem einzigen, integrierten gedruckten Teil.
- Vorteile:
- Reduzierte Teileanzahl: Vereinfacht die Bestands- und Lieferkettenverwaltung.
- Eliminierte Montageschritte: Spart erhebliche Zeit und Arbeitskosten.
- Gewichtsreduzierung: Eliminiert die Notwendigkeit von Befestigungselementen (Schrauben, Nieten, Bolzen, Klebstoffe) und überlappenden Verbindungsflanschen.
- Erhöhte Zuverlässigkeit: Weniger Verbindungen bedeuten weniger potenzielle Fehlerstellen oder Eintrittsstellen für Staub/Feuchtigkeit.
- Verbesserte Leistung: Monolithische Strukturen können eine höhere Steifigkeit und eine bessere Lastverteilung bieten.
- Beispiel: Ein Drohnenarm könnte von einem Rohr, einer separaten Motorhalterung und Kabelclips in eine einzige gedruckte Komponente umgestaltet werden, die eine optimierte Innenstruktur, integrierte Motorbefestigungspunkte und interne Kanäle für die Verkabelung aufweist.
4. Berücksichtigung von Wandstärke und Merkmalsgrößenbeschränkungen: LPBF-Prozesse haben physikalische Einschränkungen:
- Mindestwanddicke: Es gibt eine Grenze, wie dünn eine strukturell solide Wand zuverlässig gedruckt werden kann (oft etwa 0,4-0,8 mm für Aluminium, abhängig von der Maschine und den Parametern). Designer müssen sicherstellen, dass strukturelle Wände dieses Minimum erfüllen oder überschreiten.
- Minimale Featuregröße: Sehr kleine Stifte, Löcher oder komplizierte Details haben ebenfalls Auflösungsgrenzen. Konsultieren Sie die spezifischen Fähigkeiten des AM-Anbieters.
- Nicht unterstützte Spannen: Große horizontale Spannen oder flache Dächer können nicht ohne Stützen gedruckt werden. Das Entwerfen mit selbsttragenden Winkeln oder die Integration von Opferrippen kann erforderlich sein, wenn Stützen in bestimmten Bereichen unerwünscht sind.
- Bildseitenverhältnis: Sehr hohe, dünne Merkmale können während des Druckens zu Verformungen oder Vibrationen neigen.
5. Intelligentes Lochdesign: Löcher sind übliche Merkmale, erfordern aber beim AM Überlegung:
- Vertikal vs. Horizontal: Vertikale Löcher (parallel zur Baurichtung) werden im Allgemeinen mit besserer Genauigkeit und besserem Finish gedruckt.
- Selbsttragende horizontale Löcher: Kleine horizontale Löcher können oft ohne Stützen gedruckt werden, größere benötigen sie jedoch. Das Entwerfen horizontaler Löcher mit einer „Tränenform“ oder Diamantform an der Oberseite ermöglicht es ihnen, bis zu einem bestimmten Durchmesser selbsttragend zu sein.
- Die Genauigkeit: Für hochpräzise Löcher (z. B. für Lager oder Presspassungen) ist es oft am besten, sie etwas unterdimensioniert zu konstruieren und sie dann während der Nachbearbeitung auf die endgültige Toleranz zu reiben oder zu bearbeiten. Das Gewindeschneiden erfolgt typischerweise nach dem Drucken durch Gewindebohren oder unter Verwendung von Gewindeeinsätzen.
6. Konstruktion für Wärmemanagement (während des Drucks & Betriebs):
- Während des Druckens: Vermeiden Sie große, massive Abschnitte, die durch sehr dünne Merkmale verbunden sind, da dies zu einer ungleichmäßigen Wärmeverteilung führen und die Eigenspannung erhöhen kann. Stufenweise Übergänge in der Dicke werden bevorzugt.
- Während des Betriebs: DfAM ermöglicht die nahtlose Integration von Wärmemanagementfunktionen direkt in die Drohnenhülle, wie z. B. Kühlrippen in der Nähe von Motoren oder Elektronik oder interne Kanäle, die für passive oder aktive Luftkühlung ausgelegt sind.
7. Planung für die Nachbearbeitung: Effektives DfAM antizipiert nachgelagerte Schritte:
- Unterstützung bei der Entfernung Zugang: Stellen Sie sicher, dass Stützen in Bereichen platziert werden, die für Werkzeuge zum Entfernen zugänglich sind, ohne kritische Merkmale zu beschädigen.
- Zulagen für die Bearbeitung: Wenn Oberflächen hohe Präzision oder bestimmte Oberflächen erfordern, die nur durch Bearbeitung erreicht werden können, entwerfen Sie diese Merkmale mit zusätzlichem „Roh“-Material (z. B. 0,5-1,0 mm), das während der CNC-Bearbeitung entfernt werden soll.
- Überlegungen zur Oberflächenbehandlung: Konstruieren Sie Teile so, dass Merkmale vermieden werden, die Strahlmittel einschließen oder eine gleichmäßige Beschichtungsanwendung verhindern könnten.
Zusammenarbeit ist der Schlüssel: Die erfolgreiche Implementierung von DfAM erfordert oft eine enge Zusammenarbeit zwischen dem Produktdesigner und dem Dienstleister für additive Fertigung. Erfahrene AM-Spezialisten wie das Team von Met3dpkönnen unschätzbares Feedback zur Designmachbarkeit geben, Optimierungen für Druckbarkeit und Wirtschaftlichkeit vorschlagen und helfen, die Nuancen der Materialauswahl und der Prozessparameter zu navigieren. Die Nutzung ihres Fachwissens frühzeitig im Designzyklus stellt sicher, dass die endgültige Drohnenhülle in vollem Umfang von den Fähigkeiten der additiven Fertigung profitiert. Die Erkundung des umfassenden Met3dp-Sortiments an Produkten und Dienstleistungen kann Einblicke geben, wie solche Partnerschaften den Weg vom Konzept zum Hochleistungs-Druckteil rationalisieren können. Die Zusammenarbeit mit AM-Experten verwandelt DfAM von einer theoretischen Übung in einen praktischen Weg für Innovationen.
Erreichbare Präzision: Toleranz, Oberflächengüte und Maßgenauigkeit in Aluminium-Drohnenhüllen
Bei der Spezifizierung von Komponenten für Luft- und Raumfahrt- und Hochleistungsanwendungen wie Drohnenhüllen ist Präzision von größter Bedeutung. Ingenieure und Beschaffungsmanager benötigen ein klares Verständnis der dimensionalen Fähigkeiten und Einschränkungen der metallischen additiven Fertigung unter Verwendung von Aluminiumlegierungen wie AlSi10Mg und Scalmalloy®. Während Metall-AM beispiellose Designfreiheit bietet, ist es entscheidend, zwischen den „as-printed“-Fähigkeiten und der Präzision zu unterscheiden, die nach Sekundäroperationen erreichbar ist. Lassen Sie uns die Konzepte der Toleranz, Oberflächengüte und Maßgenauigkeit im Kontext des Laser Powder Bed Fusion (LPBF) für Aluminium-Drohnenteile verdeutlichen.
Definieren der Begriffe:
- Maßgenauigkeit: Bezieht sich auf die Gesamtkonformität des gedruckten Teils mit den in der CAD-Modell angegebenen Nenndimensionen. Es beschreibt, wie genau das fertige Teil in seiner gesamten Geometrie mit der beabsichtigten Größe und Form übereinstimmt. Es wird oft als allgemeine Abweichung ausgedrückt, z. B. ±0,1 % der Abmessung, oder als fester Wert, z. B. ±0,1 mm über eine bestimmte Länge.
- Verträglichkeit: Definiert den zulässigen Variationsbereich für eine bestimmte Abmessung. Toleranzen werden auf einzelne Merkmale angewendet (z. B. Lochdurchmesser, Wandstärke, Abstand zwischen Merkmalen) und sind in der Regel viel enger als die allgemeine Maßgenauigkeit. Sie bestimmen die akzeptablen oberen und unteren Grenzwerte für eine Abmessung, um eine ordnungsgemäße Passung und Funktion sicherzustellen (z. B. 10,0 mm ±0,05 mm).
- Oberflächengüte (Oberflächenrauhigkeit): Quantifiziert die Textur der Oberfläche eines Teils. Sie wird typischerweise als Ra (durchschnittliche Rauheit) oder Rz (durchschnittliche maximale Profilhöhe) in Mikrometern (µm) gemessen. Niedrigere Ra/Rz-
Typische Erwartungen für LPBF-Aluminium (AlSi10Mg & Scalmalloy®):
Es ist wichtig zu beachten, dass die erreichbare Präzision stark von der spezifischen LPBF-Maschine, ihrer Kalibrierung, den gewählten Prozessparametern, der Materialcharge, der Bauteilgeometrie und -größe, der Ausrichtung auf der Bauplatte und der Effektivität der Nachbearbeitung (insbesondere der Wärmebehandlung) abhängt. Wir können jedoch allgemeine Richtlinien geben:
- Maßgenauigkeit:
- Wie gedruckt: Bei gut kalibrierten industriellen LPBF-Systemen, die Aluminiumlegierungen drucken, liegt die allgemeine Maßgenauigkeit typischerweise im Bereich von ±0,1 mm bis ±0,2 mm für kleinere Abmessungen (z. B. bis zu 100 mm), möglicherweise bis zu ±0,1 % bis ±0,2 % für größere Abmessungen. Faktoren wie thermisches Verziehen während des Bauprozesses, insbesondere bei großen, flachen Abschnitten, können dies beeinflussen. Met3dp unterstreicht die
branchenführendes Druckvolumen, Genauigkeit und Zuverlässigkeit
ihrer Drucksysteme und demonstriert damit das Bestreben, ein hohes Maß an Maßhaltigkeit zu erreichen. - Nachbearbeitet: Die spanende Bearbeitung spezifischer Merkmale nach dem Druck ermöglicht eine viel höhere Genauigkeit, die im Wesentlichen den Standard-CNC-Bearbeitungsmöglichkeiten entspricht, wo sie angewendet wird.
- Wie gedruckt: Bei gut kalibrierten industriellen LPBF-Systemen, die Aluminiumlegierungen drucken, liegt die allgemeine Maßgenauigkeit typischerweise im Bereich von ±0,1 mm bis ±0,2 mm für kleinere Abmessungen (z. B. bis zu 100 mm), möglicherweise bis zu ±0,1 % bis ±0,2 % für größere Abmessungen. Faktoren wie thermisches Verziehen während des Bauprozesses, insbesondere bei großen, flachen Abschnitten, können dies beeinflussen. Met3dp unterstreicht die
- Toleranzen:
- Wie gedruckt: Das Einhalten enger Toleranzen direkt aus dem Drucker ist eine Herausforderung. Während die allgemeine Genauigkeit ±0,1 mm betragen kann, ist das Erreichen einer spezifischen Toleranz wie ±0,02 mm an einem Merkmal in der Regel ohne Sekundäroperationen nicht realisierbar. Toleranzen von ±0,1 mm können an kleineren, gut abgestützten Merkmalen erreichbar sein, aber ±0,2 mm oder größer ist realistischer für allgemeine, gedruckte Merkmale.
- Nachbearbeitet (bearbeitet): Kritische Merkmale, die enge Toleranzen erfordern (z. B. Lagergehäuse, Passflansche, Ausrichtstifte), sollten mit Bearbeitungszugabe konstruiert und durch CNC-Bearbeitung fertiggestellt werden. Toleranzen von ±0,01 mm bis ±0,05 mm sind durch Nachbearbeitung leicht erreichbar, abhängig vom Merkmal und dem Bearbeitungsprozess.
- Oberflächengüte (Rauhigkeit - Ra):
- Wie gedruckt: LPBF-Teile weisen aufgrund der an der Oberfläche haftenden, teilweise geschmolzenen und gesinterten Pulverpartikel naturgemäß eine etwas raue, körnige Textur auf. Typische Ra-Werte liegen im Bereich von 6 µm bis 20 µm.
- Vertikale Mauern: bieten im Allgemeinen die beste gedruckte Oberfläche innerhalb dieses Bereichs.
- Nach oben gerichtete Oberflächen (flach oder leicht geneigt): Neigen ebenfalls zu einer relativ guten Oberfläche.
- Nach unten gerichtete Oberflächen (Überhänge/gestützt): Weisen typischerweise die rauesten Oberflächen auf, da sie mit Stützstrukturen in Kontakt kommen, was potenziell 20 µm Ra übersteigt.
- Nachbearbeitet: Deutliche Verbesserungen sind möglich:
- Perlstrahlen: Erzeugt eine gleichmäßige, matte Oberfläche, typischerweise Ra 3 µm bis 10 µm.
- Taumeln/Gleitschleifen: Kann Ra erreichen 1 µm bis 5 µm.
- Bearbeitungen: Erzeugt glatte Oberflächen, die mit konventioneller Bearbeitung vergleichbar sind, potenziell Ra 0,8 µm bis 3,2 µm oder besser.
- Polieren: Kann sehr niedrige Ra-Werte erreichen, < 0,8 µm, für spiegelähnliche Oberflächen.
- Wie gedruckt: LPBF-Teile weisen aufgrund der an der Oberfläche haftenden, teilweise geschmolzenen und gesinterten Pulverpartikel naturgemäß eine etwas raue, körnige Textur auf. Typische Ra-Werte liegen im Bereich von 6 µm bis 20 µm.
Zusammenfassungstabelle: Präzisionsfähigkeiten für LPBF-Aluminium
Parameter | Zustand | Typischer erreichbarer Bereich | Anmerkungen |
---|---|---|---|
Maßgenauigkeit | Wie gedruckt | ±0,1 bis ±0,2 mm (oder ±0,1-0,2 %) | Maschinen-/Prozess-/Geometrieabhängig |
Nachbearbeitet | Bestimmt durch die Bearbeitungsfähigkeit | Hohe Genauigkeit bei spezifischen Merkmalen | |
Toleranz | Gedruckt (allgemein) | ±0,2 mm oder größer | Losere Toleranzen typisch |
Gedruckt (optimiertes Merkmal) | ±0,1 mm möglich | Kleinere Merkmale, ideale Ausrichtung | |
Nachbearbeitet | ±0,01 bis ±0,05 mm typisch | Standard-Bearbeitungstoleranzen erreichbar | |
Oberflächengüte (Ra) | Gedruckt (vertikal) | 6 – 15 µm | Beste gedruckte Oberflächen |
Gedruckt (nach unten gerichtet) | 15 – 25+ µm | Rauher durch Stützen | |
Kugelgestrahlt | 3 – 10 µm | Gleichmäßige matte Oberfläche | |
Getrommelt/Vibrationsbearbeitung | 1 – 5 µm | Glattere Kantenverfeinerung | |
Bearbeitet | 0,8 – 3,2 µm (oder besser) | Standard-Bearbeitungsoberfläche | |
Poliert | < 0,8 µm | Spiegeloberfläche möglich |
In Blätter exportieren
Faktoren, die die Präzision beeinflussen:
Das Erreichen der bestmöglichen Präzision erfordert eine sorgfältige Kontrolle über zahlreiche Faktoren:
- Maschinenqualität und Kalibrierung: Regelmäßige Wartung und präzise Kalibrierung des LPBF-Systems sind von grundlegender Bedeutung.
- Prozessparameter: Laserleistung, Scangeschwindigkeit, Schichtdicke, Schraffurstrategie usw. beeinflussen alle die Schmelzbad-Dynamik und die endgültige Teilequalität.
- Qualität des Pulvers: Eine gleichmäßige Partikelgrößenverteilung, Kugelform und ein geringer Feuchtigkeitsgehalt, wie von Lieferanten wie Met3dpbetont wird, sind entscheidend für einen stabilen Prozess und dichte Teile.
- Wärmemanagement: Die Kontrolle des Wärmeaufbaus und der Wärmeableitung während des Drucks minimiert Verzug und Eigenspannungen.
- Strategie unterstützen: Robuste Stützen verhindern Verformungen während des Drucks, können aber die Oberflächenbeschaffenheit der gestützten Bereiche beeinträchtigen.
- Geometrie und Größe des Teils: Große, komplexe Teile sind im Allgemeinen anfälliger für Abweichungen als kleinere, einfachere Teile.
Erwartungsmanagement und Kommunikation:
Für Ingenieure und Einkaufsmanager ist eine klare Kommunikation mit dem AM-Dienstleister von entscheidender Bedeutung.
- Geben Sie kritische Abmessungen und erforderliche Toleranzen auf Zeichnungen unter Verwendung von geometrischer Bemaßung und Tolerierung (GD&T) an.
- Unterscheiden Sie zwischen Merkmalen, die gedruckte Toleranzen akzeptieren können, und solchen, die eine Nachbearbeitung erfordern.
- Besprechen Sie die Anforderungen an die Oberflächenbeschaffenheit für verschiedene Bereiche der Drohnenhülle (z. B. aerodynamische Oberflächen vs. interne Strukturen).
- Verstehen Sie die spezifischen Fähigkeiten und Qualitätskontrollverfahren des Anbieters.
Durch das Verständnis der erreichbaren Toleranzniveaus, der Oberflächenbeschaffenheit und der Maßgenauigkeit sowie durch die Konstruktion von Teilen unter Berücksichtigung dieser Fähigkeiten und der notwendigen Nachbearbeitungsschritte (DfAM) können die Beteiligten den LPBF-Aluminiumdruck effektiv nutzen, um hochwertige, leistungsstarke Drohnenhüllen herzustellen, die anspruchsvolle Anwendungsanforderungen erfüllen.
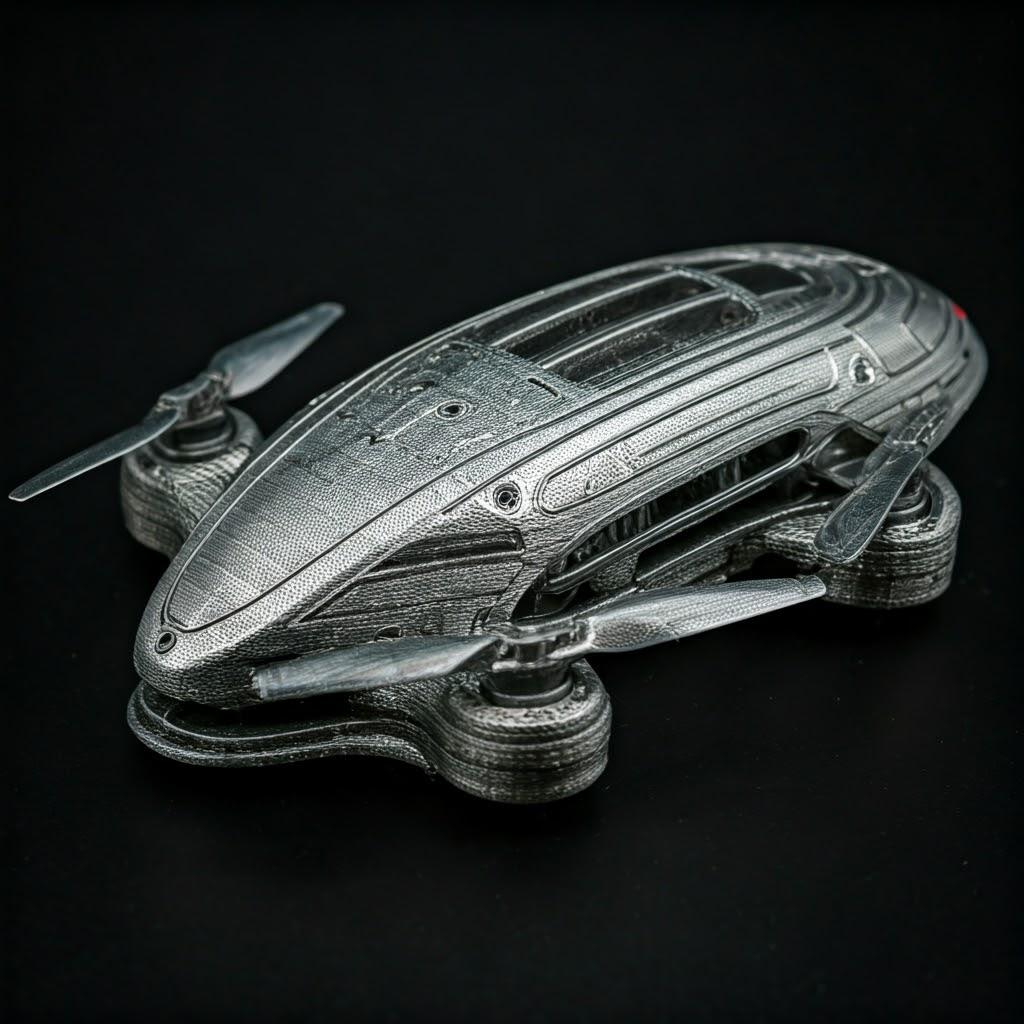
Wesentliche Nachbearbeitungsschritte für 3D-gedruckte Aluminium-Drohnenhüllen
Ein weit verbreitetes Missverständnis über den Metalldruck im 3D-Verfahren ist, dass Teile aus dem Drucker kommen und sofort einsatzbereit sind. In Wirklichkeit ist der Druckprozess für anspruchsvolle Anwendungen wie Drohnenhüllen, die mit LPBF mit AlSi10Mg oder Scalmalloy® hergestellt werden, nur der erste wichtige Schritt. Eine Reihe von wesentlichen Nachbearbeitungsschritten sind erforderlich, um das gedruckte Teil in eine funktionelle, zuverlässige Komponente zu verwandeln, die den Maßspezifikationen entspricht, die gewünschten mechanischen Eigenschaften erreicht und die entsprechenden Oberflächeneigenschaften aufweist. Das Verständnis dieser Schritte ist für Ingenieure, die Projektzeitpläne planen, und für Einkaufsmanager, die den vollen Arbeits- und Kostenumfang bewerten, wenn sie sich mit AM-Dienstleistern oder dedizierten Nachbearbeitungsanbietern
.
befassen, von entscheidender Bedeutung.
1. Stressabbau / Wärmebehandlung:
- Hier ist eine Aufschlüsselung des typischen Nachbearbeitungs-Workflows für 3D-gedruckte Aluminium-Drohnenhüllen: Warum es kritisch ist:
- Stressabbau: Die schnellen, lokalisierten Erhitzungs- und Abkühlzyklen, die dem LPBF innewohnen, erzeugen erhebliche Eigenspannungen innerhalb des gedruckten Aluminiumteils. Diese inneren Spannungen können zu Verzug oder Rissen (insbesondere nach dem Entfernen von der Bauplatte), zu zeitlicher Maßinstabilität führen und sich negativ auf die Lebensdauer auswirken. Dies ist typischerweise der allererste Schritt nach Abschluss des Baus, der oft durchgeführt wird, während das Teil noch an der Bauplatte innerhalb der Maschine befestigt ist oder unmittelbar nach der Entfernung in einem separaten Ofen. Es beinhaltet das Erhitzen des Teils auf eine moderate Temperatur (z. B. etwa 300 °C für AlSi10Mg
- für etwa 2 Stunden), gefolgt von langsamer Abkühlung. Dadurch kann sich die Mikrostruktur entspannen, wodurch die inneren Spannungen erheblich reduziert werden, ohne die grundlegende Härte oder Festigkeit dramatisch zu verändern. Lösungsglühen & Auslagern (z. B. T6-Behandlung):
- Lösungsfindung: Um die optimalen mechanischen Eigenschaften (insbesondere Streckgrenze und Zugfestigkeit) zu erzielen, die von Legierungen wie AlSi10Mg und Scalmalloy® versprochen werden, ist eine umfassendere Wärmebehandlung erforderlich. Dies beinhaltet typischerweise:
- Abschrecken: Erhitzen auf eine höhere Temperatur (z. B. ~500-540 °C), um Legierungselemente in die Aluminiummatrix aufzulösen.
- Künstliche Alterung: Schnelles Abkühlen (z. B. in Wasser oder Polymer), um die Elemente in Lösung zu halten.
- Wichtigkeit: Wiedererhitzen auf eine niedrigere Temperatur (z. B. ~160-180 °C) für eine bestimmte Dauer, um eine kontrollierte Ausscheidung von verstärkenden Phasen (wie Mg2Si in AlSi10Mg oder Al3(Sc,Zr) in Scalmalloy®) zu ermöglichen.
2. Entfernen des Teils von der Bauplatte:
- Prozess: Das Überspringen oder unsachgemäße Durchführen der Wärmebehandlung kann dazu führen, dass Teile vorzeitig ausfallen oder die Konstruktionsspezifikationen nicht erfüllen. Es ist wohl der kritischste Nachbearbeitungsschritt für die strukturelle Integrität.
- Draht-Elektroerosion (Wire EDM): Die gedruckte Drohnenhülle wird während des LPBF-Prozesses mit einer dicken Metallbauplatte verschmolzen. Die Trennung wird typischerweise mit folgenden Verfahren erreicht:
- Bandsägen: Bietet hohe Präzision und minimale mechanische Belastung des Teils, ideal für empfindliche Strukturen.
- Erwägung: Eine schnellere und oft kostengünstigere Methode für robuste Teile, wenn auch weniger präzise. Erfordert sorgfältige Handhabung.
3. Entfernung der Stützstruktur:
- Die Notwendigkeit: Die Berücksichtigung der Schnittbreite (Schnittfuge) kann in der anfänglichen Baukonfiguration erforderlich sein.
- Methoden: Überhängende Merkmale und Teile, die eine Erhebung von der Bauplatte erfordern, benötigen während des Drucks Stützstrukturen. Diese metallischen Stützen müssen entfernt werden.
- Dies kann von einfachen manuellen Brech- oder Schneidverfahren für leicht zugängliche Stützen bis hin zu komplexeren und zeitaufwändigeren Methoden für komplizierte oder interne Stützen reichen: Manuelle Werkzeuge:
- Bearbeitungen: Zangen, Schneider, Schleifer.
- CNC-Fräsen kann verwendet werden, um Stützgrenzschichten präzise zu entfernen. Manuelle Nachbearbeitung:
- Herausforderungen: Feilen, Rotationswerkzeuge für detaillierte Reinigung.
Die Entfernung der Stützen kann arbeitsintensiv sein und birgt die Gefahr, die Oberfläche des Teils zu beschädigen, wenn sie nicht sorgfältig durchgeführt wird. Dies unterstreicht die Bedeutung der DfAM-Prinzipien, die darauf abzielen, den Stützbedarf zu minimieren und Stützen für eine einfachere Entfernung zu konstruieren. 4. Oberflächenbearbeitung:
- Gedruckte Oberflächen sind typischerweise rau und können teilsinterte Partikel zurückhalten. Verschiedene Techniken werden verwendet, um die gewünschte Oberfläche zu erzielen: Die gebräuchlichste Methode. Das Antreiben von Strahlmitteln (Glaskugeln, Aluminiumoxid usw.) auf die Oberfläche entfernt losem Pulver, glättet die Rauheit leicht und erzeugt eine gleichmäßige, typischerweise matte, kosmetische Oberfläche. Unterschiedliche Medien und Drücke ergeben unterschiedliche Texturen.
- Taumeln / Vibrationsgleitschleifen: Teile werden in einem Behälter mit Strahlmittel platziert, der vibriert oder getrommelt wird. Dieser Prozess glättet Oberflächen und entgratet Kanten, was für Chargen kleinerer Teile effektiv ist oder ein polierteres Aussehen als nur das Strahlen erzielt.
- CNC-Bearbeitung: Wird selektiv auf kritischen Oberflächen verwendet, die enge Toleranzen, spezifische Ebenheit oder sehr glatte Oberflächen (Ra < 1,6 µm) erfordern, die durch Strahlen oder Trommeln nicht erreicht werden können. Dies schafft einen hybriden Fertigungsansatz.
- Manuelles Polieren / Läppen: Für Anwendungen, die Spiegeloberflächen erfordern (z. B. spezifische aerodynamische Anforderungen oder ästhetische Komponenten), wird manuelles oder automatisiertes Polieren mit progressiv feineren Schleifmitteln eingesetzt. Dies ist sehr arbeitsintensiv und kostspielig.
- Elektropolieren: Ein elektrochemischer Prozess, der Oberflächen glätten kann, wenn auch weniger verbreitet für strukturelle Drohnenhüllen als für medizinische oder lebensmitteltaugliche Teile.
5. Reinigung: Eine gründliche Reinigung ist erforderlich, um restliches Pulver (insbesondere aus internen
6. Inspektion und Qualitätskontrolle (QC):
- Prüfung der Abmessungen: Verwendung von Messschiebern, Mikrometern, Koordinatenmessgeräten (KMGs) oder 3D-Scannern zur Überprüfung kritischer Abmessungen und Toleranzen anhand der Konstruktionsspezifikationen.
- Überprüfung der Materialeigenschaften: Je nach Kritikalität können neben dem Bauteil gedruckte Probenkörper Zug- oder Härteprüfungen unterzogen werden, um die Wirksamkeit der Wärmebehandlung und die Materialeigenschaften zu überprüfen.
- Zerstörungsfreie Prüfung (NDT): Für flugkritische Drohnenkomponenten können ZfP-Verfahren zur Erkennung interner Defekte erforderlich sein:
- Computertomographie (CT) Scannen: Bietet eine 3D-Ansicht der inneren Struktur und zeigt Porosität, Einschlüsse oder Risse.
- Farbeindringprüfung / Magnetpulverprüfung: Oberflächenprüfverfahren (obwohl weniger üblich für interne Kontrollen).
- Visuelle Inspektion: Überprüfung auf Oberflächenfehler, unvollständige Stützentfernung usw.
Die spezifische Reihenfolge und Kombination dieser Nachbearbeitungsschritte hängt stark von der Designkomplexität der Drohnenhülle, dem Material (AlSi10Mg vs. Scalmalloy® kann leicht unterschiedliche Wärmebehandlungsprotokolle haben) und den endgültigen Anwendungsanforderungen hinsichtlich Toleranzen, Oberflächenbeschaffenheit und struktureller Integrität ab. Die Zusammenarbeit mit einem Full-Service-AM-Anbieter, der über eigene Kapazitäten oder starke Partnerschaften mit vertrauenswürdigen Partnern verfügt, Nachbearbeitungsanbietern
gewährleistet einen optimierten Arbeitsablauf und die Verantwortlichkeit für die endgültige Teilequalität.
Herausforderungen meistern: Sicherstellung der Qualität beim Druck von Drohnenhüllen aus Aluminium
Obwohl die additive Fertigung von Metallen erhebliche Vorteile für die Herstellung von leichten, komplexen Drohnenhüllen aus Aluminium bietet, ist die Technologie nicht ohne Herausforderungen. Um konsistente, qualitativ hochwertige Ergebnisse mit Legierungen wie AlSi10Mg und Scalmalloy® unter Verwendung von Laser Powder Bed Fusion (LPBF) zu erzielen, sind eine sorgfältige Prozesskontrolle, Materialverwaltung, die Einhaltung von DfAM-Prinzipien und eine strenge Qualitätssicherung erforderlich. Das Erkennen potenzieller Probleme und das Verständnis, wie erfahrene AM-Anbieter diese mindern, ist sowohl für Konstrukteure als auch für Beschaffungsmanager, die zuverlässige Fertigungspartner suchen, von entscheidender Bedeutung.
Im Folgenden werden einige häufige Herausforderungen beim Aluminium-LPBF und die Strategien zu deren Bewältigung vorgestellt:
1. Verformung und Verzerrung:
- Herausforderung: Die intensive, lokalisierte Wärme des Lasers, gefolgt von rascher Abkühlung, erzeugt während des Aufbaus erhebliche Temperaturgradienten innerhalb des Bauteils. Dies führt zum Aufbau von Eigenspannungen, die dazu führen können, dass sich das Bauteil verzieht, krümmt oder verformt, insbesondere dünne Abschnitte oder große flache Bereiche, wodurch es sich möglicherweise sogar mitten im Druck von den Stützen löst.
- Lösungen:
- Optimierte Teileausrichtung: Ausrichtung des Bauteils, um große, flache Oberflächen parallel zur Bauplatte zu minimieren und die Konzentration der thermischen Masse zu reduzieren.
- Robuste Unterstützungsstrategie: Konstruktion von Stützen, die nicht nur Überhänge verankern, sondern auch als Wärmeableiter fungieren, die Wärme von kritischen Bereichen ableiten und das Bauteil während des Aufbaus mechanisch einschränken. Finite-Elemente-Analyse (FEA)-Simulationen können helfen, Spannungen vorherzusagen und die Stützenplatzierung zu optimieren.
- Optimierung der Prozessparameter: Feinabstimmung von Laserleistung, Scangeschwindigkeit und Scanstrategie (z. B. Inselscannen), um den Wärmeeintrag zu steuern und Temperaturgradienten zu reduzieren.
- Wirksamer Stressabbau: Die Durchführung eines thermischen Spannungsabbaus unmittelbar nach dem Drucken und vor der Entfernung der Stützen ist absolut entscheidend, um innere Spannungen abzubauen und die Geometrie des Bauteils zu stabilisieren.
2. Reststress-Management:
- Herausforderung: Selbst wenn während des Drucks keine nennenswerte Verformung auftritt, können hohe Eigenspannungen in dem gedruckten Bauteil verbleiben. Dies kann sich negativ auf die Lebensdauer auswirken, zu unerwarteten Verformungen während der Nachbearbeitung führen und möglicherweise zu verzögerten Rissen führen.
- Lösungen:
- Obligatorische Wärmebehandlung: Geeignete Spannungsarmglühungen und/oder vollständige Lösungsglühungen und Alterungswärmebehandlungen sind unerlässlich, nicht nur für die mechanischen Eigenschaften, sondern grundsätzlich zur Reduzierung schädlicher Eigenspannungen.
- Build Plate Heating: Einige LPBF-Maschinen verwenden beheizte Bauplattformen, um den Temperaturgradienten zwischen dem geschmolzenen Material und dem umgebenden Pulver/Bauteil zu reduzieren und so den Spannungsaufbau zu verringern.
- Simulation & Designanpassung: Prädiktive Software kann die Eigenspannungsverteilung abschätzen, sodass Konstrukteure geringfügige Änderungen vornehmen können (z. B. Hinzufügen von Opferrippen, Anpassen der Dicken), um Bereiche mit hoher Spannung zu mindern.
3. Schwierigkeiten bei der Stützenentfernung und Oberflächenqualität:
- Herausforderung: Stützen sind notwendig, aber ihre Entfernung kann zeitaufwändig, arbeitsintensiv sein und möglicherweise die Bauteiloberfläche beschädigen, insbesondere bei komplexen Gitter- oder konformen Stützen in schwer zugänglichen Innenbereichen. Die Schnittstelle zwischen der Stütze und dem Bauteil hinterlässt oft eine rauhere Oberflächenbeschaffenheit.
- Lösungen:
- DfAM für die Minimierung der Unterstützung: Das Konstruieren mit selbsttragenden Winkeln (>45°), die Verwendung von Verrundungen anstelle von scharfen Überhängen und die strategische Ausrichtung des Bauteils sind die ersten Verteidigungslinien.
- Optimiertes Support-Design: Verwendung von Stützentypen (z. B. dünnwandiges Gitter, konisch), die leichter zu entfernen sind und minimale Kontaktpunkte aufweisen. Konstruktion von Ausbrechfunktionen oder spezifischen Zugangspunkten für Werkzeuge.
- Facharbeiter & Werkzeuge: Vertrauen auf erfahrene Techniker mit geeigneten Werkzeugen (Handwerkzeuge, möglicherweise Spezialschneider oder sogar lokale Bearbeitung) für die sorgfältige Entfernung der Stützen.
- Nachbearbeiten: Verwendung von Strahl- oder Trommelstrahlen zur Verbesserung der Oberflächenbeschaffenheit von gestützten Bereichen nach der Entfernung. Planung der Bearbeitung, wenn eine sehr glatte Oberfläche auf diesen Oberflächen erforderlich ist.
4. Porositätskontrolle:
- Herausforderung: Kleine Hohlräume oder Poren können sich manchmal innerhalb des gedruckten Materials bilden, was auf unvollständiges Schmelzen, Gaseinschlüsse (z. B. gelöster Wasserstoff in Aluminium) oder Pulverinkonsistenzen (Keyholing) zurückzuführen ist. Übermäßige Porosität kann die mechanischen Eigenschaften wie die Ermüdungsfestigkeit und die Duktilität beeinträchtigen.
- Lösungen:
- Optimierte Druckparameter: Entwicklung robuster Parametersätze (Laserleistung, Geschwindigkeit, Schlupfabstand, Schichtdicke), die validiert wurden, um eine hohe Dichte (>99,5 %, oft >99,8 %) für die spezifische Legierung und Maschine zu erreichen.
- Hochwertiges Pulver: Verwendung von Pulver mit konsistenter sphärischer Morphologie, kontrollierter Partikelgrößenverteilung (PSD), guter Fließfähigkeit und geringem Feuchtigkeits-/Gasgehalt. Strenge Pulverhandhabungs- und Recyclingprotokolle sind unerlässlich. Met3dp's Konzentration auf die Herstellung hochwertiger sphärischer Pulver unter Verwendung fortschrittlicher Zerstäubungstechniken, die diesem Bedarf direkt gerecht werden.
- Kontrolle der inerten Atmosphäre: Aufrechterhaltung einer hochreinen Inertgasumgebung (Argon oder Stickstoff) innerhalb der Baukammer, um Oxidation und Gasaufnahme während des Schmelzens zu minimieren.
- Heiß-Isostatisches Pressen (HIP): Für kritische Anwendungen, die eine nahezu 100-prozentige Dichte erfordern, kann HIP (Anwendung von hoher Temperatur und isostatischem Gasdruck) nach dem Drucken verwendet werden, um innere Poren zu schließen. Dies erhöht jedoch die Kosten erheblich und ist bei Aluminium-AM im Vergleich zu Titan oder Superlegierungen weniger häufig erforderlich, es sei denn, die Ermüdung ist absolut kritisch.
- NDT-Inspektion: Verwendung von CT-Scans zur Erkennung und Quantifizierung der inneren Porosität in fertigen Teilen zur Qualitätssicherung.
5. Erreichen enger Toleranzen und glatter Oberflächen:
- Herausforderung: Wie bereits erwähnt, weist der gedruckte Zustand typischerweise Einschränkungen hinsichtlich der erreichbaren Toleranzen und der Oberflächenglätte auf.
- Lösungen:
- Hybrider Fertigungsansatz: Akzeptieren der gedruckten Einschränkungen für nicht kritische Merkmale und Einbeziehung geplanter Nachbearbeitungsschritte für Oberflächen und Merkmale, die hohe Präzision oder spezifische glatte Oberflächen erfordern.
- Geeignete Oberflächenbehandlungen: Auswahl der richtigen Nachbearbeitungsmethode (Strahlen, Trommeln, Polieren) basierend auf den erforderlichen Oberflächeneigenschaften. Das Verständnis der Fähigkeiten verschiedener Druckverfahren und ihre inhärente Oberflächenqualität hilft, realistische Erwartungen zu setzen.
- Klare Spezifikation: Die präzise Definition von Toleranz- und Oberflächenanforderungen auf Zeichnungen unter Verwendung von GD&T stellt sicher, dass der AM-Anbieter die kritischen Aspekte des Designs versteht.
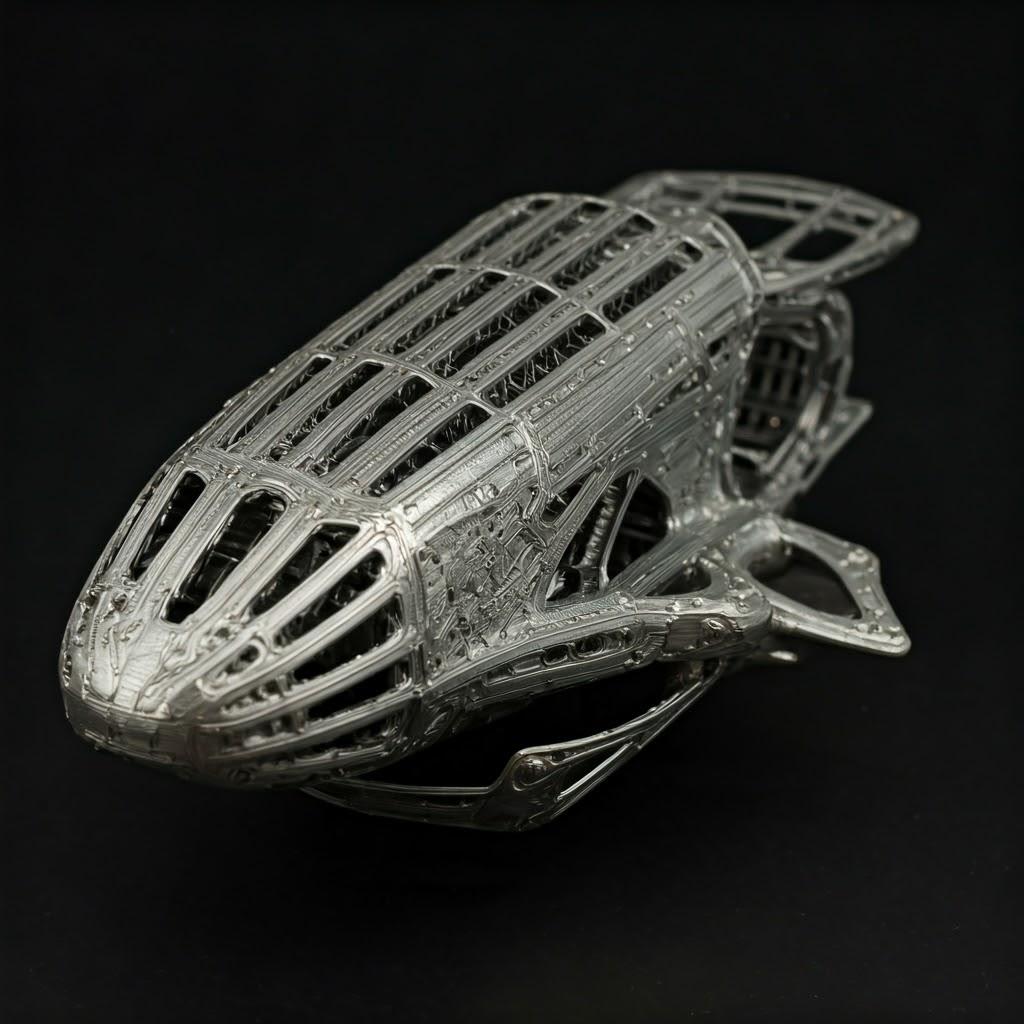
Qualitätssicherung als übergreifende Lösung:
Die konsequente Bewältigung dieser Herausforderungen beruht auf einem robusten Qualitätsmanagementsystem, das vom AM-Dienstleister implementiert wird. Dies beinhaltet:
- Eingangskontrolle und Rückverfolgbarkeit des Pulvers.
- Regelmäßige Maschinenwartung und -kalibrierung.
- In-Prozess-Überwachung (Schmelzbadüberwachung, Sensordaten).
- Strikte Einhaltung der validierten Prozessparameter.
- Kontrollierte Nachbearbeitungsverfahren (insbesondere Wärmebehandlung).
- Gründliche Endkontrolle unter Verwendung geeigneter Messtechnik und ZfP-Verfahren.
Durch die Partnerschaft mit einem erfahrenen und qualitätsorientierten Metall-AM-Anbieter wie Met3dp, der diese Herausforderungen versteht und strenge Prozesse zu deren Minderung implementiert - unter Nutzung seiner Expertise von der Pulverherstellung bis zur Endteilprüfung - können Ingenieure und Beschaffungsmanager 3D-gedrucktes Aluminium für anspruchsvolle Drohnenhüllenanwendungen sicher einsetzen und so sowohl Leistung als auch Zuverlässigkeit
.
Auswahl Ihres Partners: Auswahl des richtigen Metall-3D-Druck-Dienstleisters für Drohnenkomponenten
Die Entscheidung, die Leistungsfähigkeit der additiven Metallfertigung für kritische Komponenten wie Drohnenhüllen zu nutzen, ist von Bedeutung. Die Realisierung des vollen Potenzials dieser Technologie - die Erzielung optimaler Leistung, die Sicherstellung gleichbleibender Qualität und die effektive Kostenkontrolle - hängt jedoch entscheidend von der Auswahl des richtigen Fertigungspartners ab. Die Auswahl eines Metall-3D-Druck-Dienstleisters ist nicht nur eine transaktionale Beschaffungsentscheidung; es geht darum, eine kollaborative Partnerschaft aufzubauen, insbesondere wenn es um komplexe Hochleistungsteile geht, die aus fortschrittlichen Materialien wie AlSi10Mg und Scalmalloy® hergestellt werden. Für Ingenieure, die technische Präzision fordern, und Beschaffungsmanager, die zuverlässige, langfristige Lieferanten von Drohnenteilen
, ist ein gründlicher Bewertungsprozess unerlässlich.
Die Auswahl eines unzureichenden Anbieters kann zu einer mangelhaften Teilequalität, verpassten Terminen, unerwarteten Kosten und letztendlich zu einer Beeinträchtigung der Drohnenleistung oder einem Projektausfall führen. Umgekehrt wird ein kompetenter und kollaborativer Partner zu einer Erweiterung Ihres Entwicklungsteams, bietet Fachwissen, sichert die Qualität und hilft Ihnen bei Innovationen.
Im Folgenden werden wichtige Kriterien für die Bewertung und Auswahl eines Metall-AM-Dienstleisters für Ihre Anforderungen an Drohnenhüllen aus Aluminium aufgeführt:
1. Fachwissen und nachgewiesene Erfahrung:
- Spezifität des Materials: Verfügen sie über nachweisliche Erfahrung im erfolgreichen Drucken mit der von Ihnen benötigten Aluminiumlegierung (AlSi10Mg oder dem anspruchsvolleren Scalmalloy®)? Bitten Sie um Nachweise, z. B. Datenblätter, die von ihren Maschinen abgeleitet wurden, oder nicht-proprietäre Fallstudien.
- Technologiekompetenz: Sind sie Experten für Laser Powder Bed Fusion (LPBF)? Wie ist ihr Verständnis der Prozessparameteroptimierung für Aluminiumlegierungen?
- Branchenrelevanz: Haben sie an Projekten in anspruchsvollen Bereichen wie Luft- und Raumfahrt, Verteidigung oder Automobil gearbeitet? Erfahrung mit UAV-Komponenten ist ein erheblicher Vorteil. Suchen Sie nach Anbietern wie Met3dp, die ihren Fokus explizit auf missionskritische Teile legen und über
jahrzehntelange Erfahrung in der additiven Fertigung von Metallen
. - Technische Unterstützung: Bieten sie DfAM-Beratung an? Können ihre Ingenieure Ihr Design auf Druckbarkeit überprüfen, Optimierungen vorschlagen und bei der Fehlerbehebung potenzieller Probleme helfen?
2. Maschinenfähigkeiten, Kapazität und Qualität:
- Ausrüstung: Welche spezifischen LPBF-Maschinen betreiben sie? Handelt es sich um industrielle Systeme, die für Zuverlässigkeit und Genauigkeit mit Aluminium bekannt sind? (z. B. EOS, SLM Solutions, Trumpf, Renishaw, Velo3D, möglicherweise die eigenen SEBM-Drucker von Met3dp, falls zutreffend, oder vergleichbare LPBF-Systeme).
- Bauvolumen: Ist der Bauraum der Maschine groß genug, um Ihre Drohnenhüllenabmessungen aufzunehmen, wodurch möglicherweise mehrere Teile pro Bauvorgang (Verschachtelung) ermöglicht werden?
- Kapazität & Redundanz: Verfügen sie über eine ausreichende Maschinenkapazität, um Ihre erforderlichen Vorlaufzeiten sowohl für Prototypen als auch für eine potenzielle Kleinserienproduktion zu erfüllen? Verfügen sie über mehrere kompatible Maschinen, um Risiken im Zusammenhang mit Maschinenausfallzeiten zu mindern?
- Prozessüberwachung: Integrieren ihre Maschinen In-Prozess-Überwachungsfunktionen (z. B. Schmelzbadüberwachung, Thermografie), die Einblicke in die Bauqualität und -konsistenz geben können?
3. Materialqualitätskontrolle und -handhabung:
- Pulverbeschaffung & Zertifizierung: Wo beziehen sie ihre Aluminiumpulver? Können sie Materialzertifizierungen vorlegen, die die Einhaltung relevanter Standards (z. B. ASTM) bestätigen? Wird das Pulver von seriösen Lieferanten bezogen, oder verfügen sie, wie Met3dp, über fortschrittliche interne Pulverproduktionskapazitäten, die eine strenge Qualitätskontrolle gewährleisten? Die Über uns Seite beschreibt oft die vertikale Integration und das Engagement eines Unternehmens für hochwertige Inputs.
- Pulvermanagement: Wie sehen ihre Verfahren für die Pulverhandhabung, -lagerung (Verhinderung der Feuchtigkeitsaufnahme, entscheidend für Aluminium), das Sieben, das Mischen und das Recycling aus? Ein rigoroses Pulvermanagement ist entscheidend für eine gleichbleibende Teilequalität.
4. Umfassende Post-Processing-Fähigkeiten:
- In-House vs. Outsourced: Welche wesentlichen Nachbearbeitungsschritte (Spannungsarmglühen/Wärmebehandlung, Stützenentfernung,
- Fachwissen in der Wärmebehandlung: Verfügen sie über ordnungsgemäß kalibrierte Öfen und nachgewiesene Fachkenntnisse in der Durchführung der spezifischen Wärmebehandlungszyklen, die für AlSi10Mg (T6) und Scalmalloy® erforderlich sind, um optimale Eigenschaften zu erzielen? Dies ist nicht verhandelbar.
- Bearbeitung & Endbearbeitung: Verfügen sie über CNC-Bearbeitungsmöglichkeiten zur Fertigstellung kritischer Merkmale? Welche Bandbreite an Oberflächenausführungen können sie anbieten (Strahlen, Trommeln, Polieren)?
5. Robustes Qualitätsmanagementsystem (QMS) & Zertifizierungen:
- ISO 9001: Diese Zertifizierung ist ein grundlegender Indikator für ein dokumentiertes QMS.
- AS9100: Dies ist der entscheidende Standard für Hersteller und Zulieferer in der Luft- und Raumfahrt. Wenn Ihre Drohnenhülle für Luft- und Raumfahrt- oder Verteidigungsanwendungen bestimmt ist, ist eine AS9100-Zertifizierung (oder eine gleichwertige Zertifizierung) oft obligatorisch, um eine strenge Qualitätskontrolle, Rückverfolgbarkeit und Risikomanagementprozesse nachzuweisen.
- Rückverfolgbarkeit: Können sie eine vollständige Material- und Prozessrückverfolgbarkeit für jedes Teil gewährleisten?
- Inspektionskapazitäten: Welche Messtechnik verwenden sie (CMMs, 3D-Scanner, Messgeräte)? Bieten sie zerstörungsfreie Prüfdienste (z. B. CT-Scannen) an, falls dies zur Erkennung interner Defekte erforderlich ist?
6. Zusammenarbeit im Bereich Engineering und Designunterstützung:
- DfAM-Dienstleistungen: Bieten sie proaktiv DfAM-Überprüfungen an und arbeiten sie aktiv mit Ihren Ingenieuren zusammen, um Designs für die additive Fertigung zu optimieren?
- Simulation: Können sie Simulationen durchführen (z. B. Prozesssimulation für Spannungen/Verformungen, Topologieoptimierung), um das Design und die Fertigungsplanung zu unterstützen?
- Kommunikation: Sind sie reaktionsschnell, transparent und leicht zu kommunizieren? Ein effektives Projektmanagement ist der Schlüssel.
7. Vorlaufzeit, Reaktionsfähigkeit und Skalierbarkeit:
- Zitierte Vorlaufzeiten: Sind ihre angegebenen Vorlaufzeiten realistisch und wettbewerbsfähig, sowohl für Prototypen als auch für potenzielle Serienfertigungen?
- Flexibilität: Können sie dringende Anfragen oder Änderungen im Zeitplan berücksichtigen?
- Skalierbarkeit: Wenn Ihr Projekt vom Prototyp zum Kleinserienprodukt übergeht, können sie ihre Kapazität entsprechend skalieren?
8. Kostenstruktur und Gesamtwert:
- Transparente Preisgestaltung: Ist ihr Angebot klar und detailliert und listet die Kosten für Material, Druck, Support, Nachbearbeitung und alle zusätzlichen Dienstleistungen auf? Hüten Sie sich vor Angeboten, die zu niedrig erscheinen – sie könnten notwendige Nachbearbeitungen auslassen oder Kompromisse bei den Qualitätskontrollen eingehen.
- Wert-Angebot: Bewerten Sie den Gesamtwert und berücksichtigen Sie dabei nicht nur den Preis pro Teil, sondern auch das Fachwissen des Anbieters, die Qualitätssicherung, die Zuverlässigkeit und die Supportleistungen. Die günstigste Option ist selten der beste Wert für kritische Komponenten.
Checkliste zur Lieferantenbewertung (Beispiel):
Bewertungskriterium | Bedeutung | Wichtige Fragen, die Sie dem Anbieter stellen sollten |
---|---|---|
Technische Expertise (Legierung/LPBF) | Hoch | Beispiele/Fallstudien nennen? Erfahrung mit AlSi10Mg/Scalmalloy® detaillieren? DfAM-Supportprozess beschreiben? |
Maschinenfähigkeit & Kapazität | Hoch | Welche Maschinen? Bauvolumen? Wie viele Einheiten? Wie ist die typische Auslastung/Wartezeit? Verwendete Prozessüberwachung? |
Materialqualität & Handhabung | Hoch | Pulverquelle & Zertifikate? Handhabungs-/Lagerungs-/Recyclingprotokolle beschreiben? Eigene Pulverproduktion (wie Met3dp)? |
Nachbearbeitungsmöglichkeiten | Hoch | Welche Schritte im eigenen Haus? Detaillierter Wärmebehandlungsprozess/Ausrüstung? Bearbeitungstoleranzfähigkeit? Veredelungsoptionen? |
QMS & Zertifizierungen (AS9100?) | Hoch (insbesondere Aero) | ISO 9001-Zertifikat vorlegen? AS9100-Zertifikat vorlegen? Rückverfolgbarkeitsprozess beschreiben? Inspektionsausrüstung & ZfP-Fähigkeiten detaillieren? |
Engineering & Design-Unterstützung | Mittel bis Hoch | DfAM-Überprüfung anbieten? Simulationsdienste verfügbar? Wie verwalten Sie die Zusammenarbeit/Kommunikation? |
Vorlaufzeit & Reaktionsfähigkeit | Hoch | Standardvorlaufzeiten (Proto/Prod)? Beschleunigungsoptionen? Wie werden Projektaktualisierungen kommuniziert? |
Kosten und Wert | Hoch | Detaillierte Angebotsaufschlüsselung bereitstellen? Preismodell erläutern? Welche Qualitätssicherungsmaßnahmen sind standardmäßig enthalten? |
Standort & Logistik | Niedrig bis mittel | Wo befinden sich die Einrichtungen? Wie sind die typischen Versandvereinbarungen/Kosten? |
In Blätter exportieren
Die Auswahl des richtigen Metall-AM-Dienstleisters ist eine strategische Investition. Durch die sorgfältige Bewertung potenzieller Partner anhand dieser Kriterien, die Konzentration auf nachgewiesene Fachkenntnisse, robuste Qualitätssysteme und einen kollaborativen Ansatz, können Sie eine Beziehung aufbauen, die die erfolgreiche Herstellung von hochleistungsfähigen, zuverlässigen 3D-gedruckten Drohnenhüllen aus Aluminium gewährleistet und das Potenzial der fortschrittlichen Fertigung in greifbare betriebliche Vorteile verwandelt. Suchen Sie nach Partnern, die sich nicht nur als Drucker, sondern als umfassende Lösungsanbieter im Bereich der additiven Fertigung positionieren.
Kosten und Vorlaufzeiten für 3D-gedruckte Drohnenhüllen verstehen
Die additive Fertigung bietet bemerkenswerte Vorteile für die Herstellung komplexer, leichter Drohnenhüllen, aber das Verständnis der damit verbundenen Kosten und typischen Zeitrahmen ist für eine effektive Projektplanung, Budgetierung und das Management von Erwartungen unerlässlich. Im Gegensatz zu herkömmlichen Massenproduktionsmethoden mit hohen anfänglichen Werkzeugkosten, aber niedrigen Kosten pro Teil bei großen Mengen, hat die Metall-AM in der Regel minimale Einrichtungskosten, aber höhere Kosten pro Teil, die mit der Menge allmählicher sinken. Beschaffungsmanager, die nach Großhandel Drohne Teile
Preisen suchen, und Ingenieure, die schnell Prototypen benötigen, müssen die Faktoren verstehen, die diese Variablen beeinflussen.
Wichtige Kostenfaktoren für 3D-gedruckte Drohnenhüllen aus Aluminium:
Der Endpreis einer 3D-gedruckten Drohnenhülle aus Aluminium ist eine Mischung aus mehreren Faktoren:
- Materialkosten:
- Pulver Preis: Die Rohmaterialkosten pro Kilogramm. Hochleistungslegierungen wie Scalmalloy® sind deutlich teurer (oft 5-10x oder mehr) als Standard AlSi10Mg.
- Materialverbrauch: Dies umfasst das Material, aus dem das fertige Teil besteht plus das Material, das für die Stützstrukturen verwendet wird. Effizientes DfAM zielt darauf ab, sowohl das Teilvolumen als auch das Stützvolumen zu minimieren.
- Pulverauffrischung/Recycling: Nicht das gesamte Pulver in der Baukammer wird verwendet. Recyceltes Pulver muss oft mit neuem Pulver aufgefrischt werden, und Handhabungs-/Siebprozesse verursachen Gemeinkosten, die in der Materialkostenkomponente berücksichtigt werden. Anbieter mit effizienten Pulvermanagementsystemen können bessere Materialausnutzungsraten anbieten.
- Maschinenzeit (amortisierte Stundensatz):
- Haupttreiber: Dies ist oft die größte Kostenkomponente. Industrielle Metall-LPBF-Maschinen stellen eine erhebliche Kapitalinvestition dar, und ihre Betriebskosten (Strom, Gas, Wartung) sind beträchtlich.
- Berechnung der Bauzeit: Bestimmt durch:
- Teilband: Das Gesamtvolumen des zu schmelzenden Materials (Teil + Stützen).
- Teilhöhe (Z-Höhe): Jede Schicht fügt Zeit hinzu (erneutes Beschichten, Laserscannen). Höhere Teile dauern länger, was die Ausrichtung zu einem wichtigen Kostenfaktor macht.
- Teil Komplexität: Aufwendige Details oder ausgedehnte Gitterstrukturen erfordern komplexere Laserscanpfade pro Schicht.
- Nesting-Effizienz: Wie viele Teile können gleichzeitig auf einer einzigen Bauplatte gedruckt werden. Eine höhere Dichte reduziert die Maschinenzeit, die pro Teil aufgewendet wird.
- Maschinentarif: Variiert je nach Anbieter, Maschinentyp und Standort.
- Arbeitskosten:
- Vorverarbeitung: CAD-Datei-Vorbereitung, Planung des Bau-Layouts (Verschachtelung, Ausrichtung, Stützgenerierung). Dies erfordert qualifizierte Techniker oder Ingenieure.
- Maschineneinrichtung & Überwachung: Pulver einfüllen, den Bau einrichten, den Druckprozess überwachen (obwohl er während des Baus selbst weitgehend automatisiert ist).
- Nachbearbeiten: Dies ist oft die arbeitsintensivste Phase und wirkt sich erheblich auf die Endkosten aus. Es umfasst:
- Wärmebehandlung (Ofenbetrieb).
- Teileentfernung (Sägen/EDM).
- Stützenentfernung (kann bei komplexen Teilen sehr zeitaufwändig sein).
- Oberflächenbearbeitung (Strahlen, Trommeln, manuelles Polieren).
- Bearbeitung (Einrichtung und Betrieb von CNC-Maschinen).
- Inspektion & QS (Technikerzeit für Messungen, ZfP, Dokumentation).
- Konstruktions- und Engineering-Dienstleistungen (falls zutreffend):
- Wenn der AM-Anbieter DfAM-Beratung, Topologieoptimierungsdienste oder Bausimulation anbietet, werden diese Engineering-Stunden zu den Kosten hinzugerechnet. Investitionen hier können oft zu Einsparungen in nachgelagerten Bereichen durch optimierte Designs führen.
- Qualitätssicherung und Prüfung:
- Standardmäßige Maßprüfkosten werden in der Regel berücksichtigt.
- Eine strengere Qualitätssicherung, wie z. B. ZfP (CT-Scannen), Materialprüfungen (Zugversuche an Zeugen), oder umfangreiche CMM-Berichte, erhöhen die Kosten und sollten angegeben werden, falls erforderlich.
- Gemeinkosten und Gewinn:
- Wie jedes Unternehmen beinhaltet der Dienstleister betriebliche Gemeinkosten (Einrichtung, Versorgung, Verwaltung) und eine Gewinnspanne in seiner Preisgestaltung.
- Menge / Losgröße:
- Amortisation einrichten: Feste Kosten (Vorbereitung der Datei, Maschineneinrichtung) werden auf mehr Teile in größeren Chargen verteilt, wodurch die Kosten pro Teil reduziert werden.
- Nesting-Effizienz: Größere Chargen ermöglichen oft eine effizientere Packung des Bauvolumens, wodurch die Maschinenzeit pro Teil reduziert wird.
- Effizienz der Nachbearbeitung: Die Handhabung von Teilen in Chargen kann manchmal die Nachbearbeitungsschritte rationalisieren.
- Großhandelspreise: Für wiederkehrende Bestellungen oder deutlich große Chargen,
Großhandel Drohne Teile
können Preisstrukturen verhandelbar sein, aber die Kostenskalierung der AM unterscheidet sich vom Spritzguss.
Tabelle: Aufschlüsselung der Kostenfaktoren für 3D-gedruckte Drohnenhüllen aus Aluminium
Kostenfaktor | Beschreibung | Typische Auswirkungen auf die Gesamtkosten | Anmerkungen |
---|---|---|---|
Materialkosten | Preis für verbrauchtes AlSi10Mg- oder Scalmalloy®-Pulver (Teil + Stützen) | Mittel bis Hoch | Scalmalloy® deutlich höher. Volumen/Stützen minimieren. |
Maschinenzeit | Stundensatz, der auf die gesamte Bauzeit angewendet wird (Z-Höhe, Volumen, Komplexität) | Hoch | Ausrichtung, Verschachtelung optimieren. Oft der größte Einzelfaktor. |
Arbeit: Einrichtung | Vorbereitung der Bau-Datei, Maschineneinrichtung | Niedrig bis mittel | Kann über Chargen amortisiert werden. |
Arbeit: Nachbearbeitung | Wärmebehandlung, Stützenentfernung, Endbearbeitung, Bearbeitung, Inspektion | Mittel bis Hoch | Stark abhängig von Komplexität & Anforderungen. Oft unterschätzt. |
Engineering-Dienstleistungen | DfAM-Beratung, Simulation (falls angefordert) | Niedrig bis mittel (optional) | Kann langfristige Einsparungen bringen. |
Qualitätssicherung | Standardinspektion; ZfP oder erweiterte Messtechnik erhöhen die Kosten | Niedrig bis hoch (Anforderung Dep.) | Bedürfnisse klar angeben. |
Menge | Anzahl der bestellten identischen Teile | Mittel | Die Stückkosten sinken mit dem Volumen, aber weniger drastisch als bei der Massenproduktion. |
Gemeinkosten & Gewinn | Betriebskosten und Marge des Anbieters | Mittel | Standardgeschäftspraxis. |
In Blätter exportieren
Verständnis der Vorlaufzeiten:
AM-Vorlaufzeit
ist ein weiterer kritischer Faktor, der von mehreren Phasen beeinflusst wird:
- Angebotserstellung und Auftragsbestätigung: Typischerweise 1-3 Werktage, unter der Annahme klarer Eingangsdaten.
- Designüberprüfung & Dateivorbereitung: 1-2 Tage, möglicherweise länger, wenn eine DfAM-Optimierung erforderlich ist.
- Warteschlangenzeit der Maschine: Sehr variabel (Tage bis Wochen), abhängig von der aktuellen Arbeitsbelastung und Maschinenverfügbarkeit des Anbieters. Dies ist oft die größte Unsicherheit.
- Druckzeit: Reicht von ~12 Stunden für kleine Teile bis zu mehreren Tagen (z. B. 48-120+ Stunden) für große, komplexe Drohnenhüllen oder dicht gepackte Bauplatten.
- Abkühlen & Wärmebehandlung: Teile müssen abkühlen, bevor sie entfernt werden. Wärmebehandlungszyklen (Spannungsarmglühen + Alterung) können 1-2 Tage hinzufügen, einschließlich Ofenzeit und kontrollierter Abkühlung.
- Nachbearbeiten: Dies kann erhebliche Zeit hinzufügen:
- Teile-/Stützenentfernung: Stunden bis Tage, je nach Komplexität.
- Bearbeitung: Hängt von der Komplexität und der Terminplanung der Werkstatt ab (kann Tage oder Wochen hinzufügen, wenn sie ausgelagert wird).
- Veredelung/Inspektion: Typischerweise 1-3 Tage.
- Versand: Standardkurier-/Frachtzeiten (1-5 Tage im Inland, länger international).
Typische Vorlaufzeitspannen (Schätzungen):
- Prototypen (1-5 Einheiten): 1 bis 3 Wochen ist üblich, unter der Annahme verfügbarer Maschinenkapazität und Standard-Nachbearbeitung. Kann gegen Aufpreis
- Kleinserienproduktion (10-100 Einheiten): 3 bis 6 Wochen kann typisch sein, was eine optimierte Verschachtelung und Stapel-Nachbearbeitung ermöglicht. Stark abhängig von der Teilegröße und -komplexität.
Das Wichtigste zum Mitnehmen: Sowohl die Kosten als auch die Vorlaufzeit in der Metall-AM werden stark von der Designkomplexität, der Teilegröße (insbesondere der Höhe), der Materialauswahl, der erforderlichen Präzision/Oberfläche und der Kapazität und Effizienz des Dienstleisters beeinflusst. Eine frühzeitige Einbindung potenzieller Anbieter und eine klare Kommunikation der Anforderungen sind unerlässlich, um genaue Angebote und realistische Zeitpläne für Ihr 3D-gedrucktes Drohnengehäuse aus Aluminium zu erhalten.
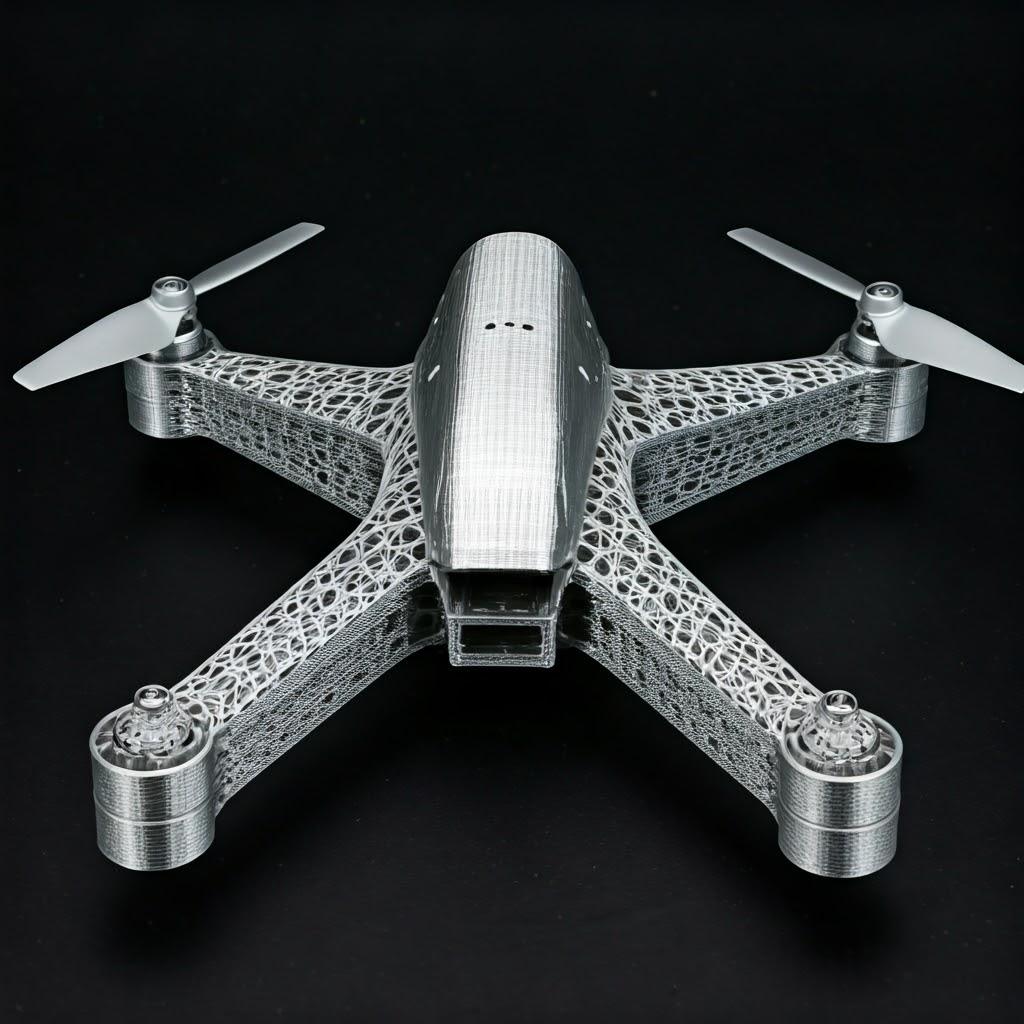
Häufig gestellte Fragen (FAQ) zu 3D-gedruckten Drohnengehäusen aus Aluminium
Wenn Ingenieure und Beschaffungsmanager die Verwendung der additiven Metallfertigung für Drohnenkomponenten untersuchen, tauchen einige häufige Fragen auf. Hier sind Antworten auf einige häufig gestellte Fragen zu 3D-gedruckten Drohnengehäusen aus Aluminium (AlSi10Mg und Scalmalloy®):
F1: Wie vergleicht sich die Festigkeit von 3D-gedrucktem AlSi10Mg / Scalmalloy® mit traditionell bearbeiteten Aluminiumlegierungen wie 6061-T6 oder 7075-T6?
A: Der Vergleich hängt stark von der spezifischen gedruckten Legierung und der angewendeten Nachbehandlung ab.
- AlSi10Mg (wärmebehandelt – T6-Äquivalent): Zeigt im Allgemeinen eine Streckgrenze (YS) und Zugfestigkeit (UTS), die etwas niedriger oder vergleichbar mit der von Knetlegierung 6061-T6 Aluminium sind. Seine Dehnung (Duktilität) ist oft geringer als bei 6061-T6. Es ist deutlich weniger fest als 7075-T6. Sein Festigkeits-Gewichts-Verhältnis ist jedoch für viele Drohnenanwendungen immer noch sehr günstig, und AM ermöglicht komplexe Geometrien, die mit der Bearbeitung von 6061 oft nicht erreichbar sind.
- Scalmalloy® (wärmebehandelt): Diese Hochleistungs-AM-Legierung glänzt wirklich. Ihre Streckgrenze und Zugfestigkeit übersteigen die von 6061-T6 deutlich und sind vergleichbar mit oder übertreffen sogar die von hochfestem 7075-T6-Aluminium, insbesondere wenn die spezifische Festigkeit (Festigkeit geteilt durch Dichte) berücksichtigt wird. Darüber hinaus bietet Scalmalloy® im Allgemeinen eine bessere Duktilität und Ermüdungseigenschaften als 7075, was es zu einer außergewöhnlichen Wahl für anspruchsvolle, leichte Strukturbauteile macht, bei denen die Leistung mit herkömmlichen hochfesten Aluminiumoptionen konkurriert oder diese übertrifft.
F2: Was sind die wichtigsten Kostentreiber, auf die ich mich bei der Konstruktion eines Drohnengehäuses für die Metall-AM konzentrieren sollte, um sie zu minimieren?
A: Um die Kosten bei der Konstruktion für Aluminium-LPBF effektiv zu verwalten, konzentrieren Sie sich auf diese Schlüsselbereiche:
- Teilvolumen minimieren: Verwenden Sie Topologieoptimierung und Gitterstrukturen mit Bedacht, um unnötiges Material zu entfernen. Ein kleineres Volumen bedeutet weniger Pulververbrauch und schnelleres Drucken.
- Minimieren Sie die Teilehöhe (Z-Achse): Richten Sie das Teil auf der Bauplatte so aus, dass seine Höhe minimiert wird, da dies die Druckzeit (Anzahl der Schichten) direkt beeinflusst. Erwägen Sie, sehr hohe Teile zu teilen, wenn dies machbar ist, obwohl dies die Vorteile der Teilekonsolidierung zunichte macht.
- Konstruieren Sie für minimale Stützen: Verwenden Sie wann immer möglich selbsttragende Winkel (typischerweise >45°). Vermeiden Sie große horizontale Überhänge oder konstruieren Sie sie mit selbsttragenden Formen (z. B. Fasen, Tropfen). Stützen verbrauchen Material, erhöhen die Druckzeit und erfordern einen erheblichen Nachbearbeitungsaufwand für die Entfernung.
- Toleranzen und Oberflächengüten angemessen spezifizieren: Rufen Sie nur enge Toleranzen (die Nachbearbeitung erfordern) und glatte Oberflächengüten (die zusätzliche Veredelungsschritte erfordern) für Merkmale auf, bei denen sie funktionell erforderlich sind. Die Überspezifizierung der Präzision erhöht die Nachbearbeitungskosten dramatisch.
- Teil Konsolidierung: Während die Komplexität eines einzelnen Teils potenziell erhöht wird, kann die Konsolidierung mehrerer Komponenten in einem Druck den Montageaufwand und die Kosten für Befestigungselemente eliminieren, was häufig zu Gesamteinsparungen führt, insbesondere bei kleineren Produktionsläufen.
F3: Können komplexe interne Merkmale oder Kanäle innerhalb eines Drohnengehäuses effektiv von Restpulver gereinigt werden?
A: Ja, aber es erfordert eine sorgfältige Konstruktion und eine sorgfältige Nachbearbeitung. Restpulver, das in internen Hohlräumen eingeschlossen ist, kann nachteilig sein.
- Überlegungen zum Design: Stellen Sie sicher, dass interne Kanäle einen ausreichenden Durchmesser (typischerweise > 1-2 mm) haben und strategisch platzierte Auslasslöcher enthalten, damit das Pulver während des Bau- und Reinigungsprozesses entweichen kann. Vermeiden Sie komplexe Sacklöcher, in denen sich Pulver dauerhaft festsetzen kann.
- Reinigungsmethoden: Die Nachdruckreinigung umfasst die Verwendung von Druckluft, Vibrationen und manchmal speziellen Vakuum- oder Spültechniken, um Pulver aus internen Geometrien zu entfernen. Ultraschallreinigung kann auch helfen, Partikel zu lösen.
- Verifizierung: Für kritische Kanäle (z. B. Kühlkanäle) können Inspektionsmethoden wie Endoskopie oder sogar CT-Scannen eingesetzt werden, um die vollständige Pulverentfernung zu überprüfen, obwohl dies die Kosten erhöht. Besprechen Sie Reinigungsstrategien und -beschränkungen mit Ihrem AM-Anbieter.
F4: Eignet sich 3D-gedrucktes Aluminium für Drohnenteile, die rauen Umgebungen wie Salzwasserspray oder Industriechemikalien ausgesetzt sind?
A: Aluminiumlegierungen, einschließlich AlSi10Mg und Scalmalloy®, bieten eine gute inhärente Korrosionsbeständigkeit aufgrund der Bildung einer passiven Oxidschicht. Sie verhalten sich im Allgemeinen gut unter typischen atmosphärischen Bedingungen. Für eine längere Exposition gegenüber aggressiven Umgebungen wie Salzwasser (Marine-Drohnen) oder bestimmten Chemikalien gilt jedoch Folgendes:
- Grundwiderstand: Beide Legierungen halten sich recht gut, sind aber im Laufe der Zeit anfällig für Lochfraßkorrosion in chloridreichen Umgebungen.
- Oberflächenbehandlungen: Das Auftragen von Schutzoberflächenbehandlungen während der Nachbearbeitung wird für eine verbesserte Haltbarkeit unter rauen Bedingungen dringend empfohlen. Häufige Optionen sind:
- Eloxieren: Erzeugt eine dickere, härtere, korrosionsbeständigere Oxidschicht. Kann auch gefärbt werden.
- Konversionsbeschichtungen (z. B. Chromat, TCP): Bieten einen guten Korrosionsschutz und wirken als hervorragende Grundierung für Farbe.
- Anstrich/Pulverbeschichtung: Bietet eine robuste Barriere gegen die Umwelt.
- Empfehlung: Besprechen Sie die spezifische Betriebsumgebung mit Ihrem AM-Anbieter, um die am besten geeignete Legierung auszuwählen und festzustellen, ob zusätzliche Schutzbeschichtungen erforderlich sind.
F5: Welche Informationen muss ich einem Metall-AM-Dienstleister unbedingt zur Verfügung stellen, um ein genaues Angebot für mein Drohnengehäuseteil zu erhalten?
A: Um ein zeitnahes und genaues Angebot zu erhalten, geben Sie Folgendes an:
- 3D-CAD-Datei: Ein hochwertiges 3D-Modell, vorzugsweise im STEP-Format (.stp oder .step). Vermeiden Sie nach Möglichkeit Mesh-Dateien (wie .stl), da ihnen die präzisen Geometriedaten fehlen, die für die Fertigungsplanung benötigt werden.
- Spezifikation des Materials: Geben Sie die gewünschte Aluminiumlegierung (z. B. AlSi10Mg oder Scalmalloy®) eindeutig an.
- Menge: Geben Sie die Anzahl der benötigten Teile an (für Prototypen oder Produktionslauf).
- Kritische Toleranzen & Oberflächen: Idealerweise stellen Sie eine 2D-Zeichnung (z. B. PDF) mit geometrischer Bemaßung und Tolerierung (GD&T) bereit, die kritische Abmessungen, erforderliche Toleranzen und spezifische Oberflächengüteanforderungen (Ra-Werte) für wichtige Merkmale angibt. Wenn keine Zeichnung bereitgestellt wird, wird der Anbieter wahrscheinlich auf der Grundlage seiner Standardfähigkeiten „wie gedruckt“ zitieren, die möglicherweise nicht Ihren Anforderungen entsprechen.
- Wärmebehandlung: Geben Sie an, ob ein bestimmter Wärmebehandlungszustand erforderlich ist (z. B. T6 oder Äquivalent für AlSi10Mg, spezifisches Aushärten für Scalmalloy®) oder ob eine Standard-Spannungsarmglühung ausreicht.
- Post-Processing-Bedarf: Geben Sie alle obligatorischen Nachbearbeitungen wie bestimmte Bearbeitungsvorgänge, erforderliche Oberflächenbehandlungen (Anodisieren, Lackieren) oder ZfP-Prüfungen an.
- Gewünschtes Lieferdatum: Erwähnen Sie Ihren Zielzeitplan.
Die Bereitstellung umfassender Informationen im Voraus minimiert Verzögerungen und stellt sicher, dass das Angebot die erforderlichen Arbeiten zur Herstellung von Drohnengehäusen, die Ihren Spezifikationen entsprechen, genau widerspiegelt.
Fazit: Steigerung der UAV-Fähigkeiten mit 3D-gedruckten leichten Aluminiumgehäusen
Die Landschaft der unbemannten Luftfahrzeuge ist eine der unaufhörlichen Innovationen, die durch das kontinuierliche Streben nach größerer Leistung, erweiterten Fähigkeiten und verbesserter Betriebseffizienz angetrieben wird. Wie wir in dieser Diskussion untersucht haben, spielt das Drohnengehäuse – der Flugzeugrahmen selbst – eine entscheidende Rolle bei der Erreichung dieser Ziele. Das Aufkommen der additiven Metallfertigung, insbesondere die Laser Powder Bed Fusion, die auf fortschrittliche leichte Aluminiumlegierungen wie AlSi10Mg und die außergewöhnliche Scalmalloy®, stellt einen Paradigmenwechsel dar, wie diese kritischen Strukturen entworfen und hergestellt werden.
Die Vorteile sind überzeugend und gehen direkt auf die Kernherausforderungen ein, mit denen UAV-Designer konfrontiert sind:
- Beispiellose Leichtbauweise: Durch Topologieoptimierung und komplizierte Gitterstrukturen, die mit herkömmlichen Methoden unmöglich sind, ermöglicht die Metall-AM erhebliche Gewichtsreduzierungen, was sich direkt in längerer Flugausdauer, erhöhter Nutzlastkapazität und verbesserter Manövrierfähigkeit niederschlägt.
- Geometrische Freiheit: Designer werden von den Einschränkungen von Formen und Bearbeitungszugängen befreit, was hochkomplexe, aerodynamisch effiziente Formen, integrierte Funktionsmerkmale (Halterungen, Kanäle) und optimierte Innenstrukturen ermöglicht.
- Teil Konsolidierung: Die Fähigkeit, mehrere Komponenten in einem einzigen gedruckten Teil zu kombinieren, reduziert die Montagezeit, minimiert das Gewicht, das mit Befestigungselementen verbunden ist, und erhöht die Gesamtstrukturintegrität, indem potenzielle Fehlerpunkte eliminiert werden.
- Leistung des Materials: Der Zugang zu hochfesten Aluminiumlegierungen mit hohem Festigkeits-Gewichts-Verhältnis, die nach der Wärmebehandlung häufig mechanische Eigenschaften aufweisen, die herkömmlichen Gegenstücken entsprechen oder diese übertreffen, gewährleistet eine strukturelle Robustheit ohne Gewichtsnachteil.
- Schnelle Iteration und Anpassung: Die werkzeugfreie Natur der AM beschleunigt die Prototyping-Zyklen und macht die Kleinserienproduktion von kundenspezifischen oder missionsspezifischen Drohnengehäusen wirtschaftlich rentabel.
Diese technologischen Vorteile sind nicht nur theoretisch; sie ermöglichen greifbare Fortschritte in verschiedenen UAV-Anwendungen, von anspruchsvollen Luft- und Raumfahrt- und Verteidigungsmissionen, die maximale Leistung und Haltbarkeit erfordern, bis hin zu industriellen Inspektions- und Lieferdrohnen, die Effizienz und Nutzlastkapazität priorisieren, und spezialisierten Plattformen für Notfalldienste und wissenschaftliche Forschung.
Die Nutzung dieser Vorteile erfordert jedoch einen ganzheitlichen Ansatz. Es erfordert das Akzeptieren von Design für additive Fertigung (DfAM) Prinzipien, das Verständnis der erreichbaren Ebenen von Präzision und Oberflächengüte, die sorgfältige Planung für wesentliche Nachbearbeitungsschritte wie Wärmebehandlung und Veredelung sowie das Erkennen und Abmildern potenzieller Fertigungsherausforderungen durch robuste Prozesskontrolle und Qualitätssicherung.
Entscheidend ist, dass der Erfolg davon abhängt, Auswahl des richtigen Produktionspartners. Die Auswahl eines Metall-AM-Dienstleisters mit nachgewiesener Expertise in Aluminiumlegierungen, modernster Ausrüstung, umfassenden Nachbearbeitungsmöglichkeiten, strengen Qualitätssystemen (einschließlich relevanter Zertifizierungen wie AS9100, falls erforderlich) und einem kollaborativen Engineering-Ansatz ist von größter Bedeutung. Das Verständnis der Kostentreiber und Vorlaufzeitfaktoren ermöglicht eine realistische Budgetierung und Projektplanung.
Die Zukunft der Drohnenfertigung ist zunehmend mit der additiven Fertigung verbunden. Da sich die AM-Technologien weiterentwickeln und schnellere Druckgeschwindigkeiten, größere Bauvolumina, verbesserte Materialeigenschaften und anspruchsvollere Design- und Simulationstools bieten, wird ihre Rolle bei der Herstellung von hochwertigen, leistungskritischen UAV-Komponenten wie Drohnengehäusen nur noch zunehmen. Die Einführung von Metall-AM ist nicht mehr nur eine alternative Fertigungsmethode; sie entwickelt sich zu einer strategischen Fähigkeit für Unternehmen, die in der sich schnell entwickelnden Welt der unbemannten Luftfahrtsysteme führend sein wollen.
Für Unternehmen, die das transformative Potenzial des Metall-3D-Drucks für ihre Drohnenprojekte erkunden möchten, ist die Partnerschaft mit einem sachkundigen und vertikal integrierten Anbieter der Schlüssel. Met3dp, mit seiner fundierten Expertise in der fortschrittlichen Metallpulverherstellung, branchenführenden Druckgeräten, die Präzision und Zuverlässigkeit liefern, und umfassenden Anwendungsentwicklungsdiensten, ist bereit, zu helfen. Als führendes Unternehmen, das sich der Ermöglichung von Fertigung der nächsten Generationverschrieben hat, bietet Met3dp die Fähigkeiten und die Partnerschaft, die erforderlich sind, um komplexe Designs in Hochleistungsrealitäten zu verwandeln.
Wir laden Ingenieure, Designer und Beschaffungsmanager ein, tiefer in die Möglichkeiten einzutauchen. Erforschen Sie, wie Met3dp die Additive-Manufacturing-Ziele Ihres Unternehmens unterstützen und Ihnen helfen kann, leichtere, stärkere und leistungsfähigere Drohnenlösungen für die anspruchsvollen Anwendungen von heute und morgen zu schaffen.
Teilen auf
MET3DP Technology Co., LTD ist ein führender Anbieter von additiven Fertigungslösungen mit Hauptsitz in Qingdao, China. Unser Unternehmen ist spezialisiert auf 3D-Druckgeräte und Hochleistungsmetallpulver für industrielle Anwendungen.
Fragen Sie an, um den besten Preis und eine maßgeschneiderte Lösung für Ihr Unternehmen zu erhalten!
Verwandte Artikel
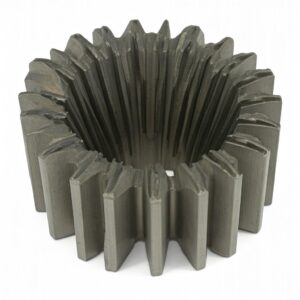
Hochleistungs-Düsenschaufelsegmente: Revolutionierung der Turbineneffizienz mit 3D-Metalldruck
Mehr lesen "Über Met3DP
Aktuelles Update
Unser Produkt
KONTAKT US
Haben Sie Fragen? Senden Sie uns jetzt eine Nachricht! Wir werden Ihre Anfrage mit einem ganzen Team nach Erhalt Ihrer Nachricht bearbeiten.
Holen Sie sich Metal3DP's
Produkt-Broschüre
Erhalten Sie die neuesten Produkte und Preislisten
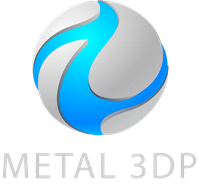
Metallpulver für 3D-Druck und additive Fertigung