Präzisionsinstrumentenhalterungen für Raumfahrzeuge mittels 3D-Druck
Inhaltsübersicht
Einführung: Die entscheidende Rolle von Instrumentenhalterungen in Weltraummissionen
Raumfahrzeuge stellen den Höhepunkt menschlicher Ingenieurskunst dar und wagen sich in Umgebungen vor, die weit von den schonenden Bedingungen auf der Erde entfernt sind. Vom niedrigen Erdorbit (LEO) bis in die entferntesten Bereiche unseres Sonnensystems tragen diese hochentwickelten Maschinen Nutzlasten, die zur Beobachtung, Messung, Kommunikation und Erforschung bestimmt sind. Entscheidend für den Erfolg jeder Weltraummission ist die Fähigkeit dieser Instrumente – der Augen, Ohren und Sinne des Raumfahrzeugs – einwandfrei zu funktionieren. Dies erfordert nicht nur robuste Instrumente selbst, sondern hängt auch entscheidend von den Strukturen ab, die sie halten: den Instrumentenhalterungen.
Eine Instrumentenhalterung für Raumfahrzeuge ist weit mehr als eine einfache Halterung. Sie ist eine präzisionsgefertigte Schnittstelle, die zur sicheren Befestigung empfindlicher Geräte wie Kameras, Spektrometer, Antennen, Sensoren oder Antriebskomponenten an der Hauptstruktur des Satelliten, der Sonde, des Landers oder des Rovers konzipiert ist. Ihr grundlegender Zweck ist vielfältig:
- Strukturelle Unterstützung: Sie muss den statischen und dynamischen Belastungen standhalten, die während des gesamten Missionslebenszyklus auftreten, von der Handhabung am Boden und den Startschwingungen bis hin zu Manövern im Orbit und potenziellen Belastungen beim Einsatz.
- Präzises Ausrichten: Viele Instrumente, insbesondere optische Systeme oder gerichtete Kommunikationsarrays, erfordern eine außergewöhnlich stabile und präzise Ausrichtung relativ zum Raumfahrzeugkörper oder zu bestimmten Himmelszielen. Die Halterung muss diese Ausrichtung unter wechselnden thermischen und mechanischen Bedingungen beibehalten.
- Umweltisolierung: Sie spielt oft eine Rolle bei der Abschwächung der Auswirkungen der rauen Weltraumumgebung. Dies kann die Dämpfung von Schwingungen umfassen, die sich von der Raumfahrzeugstruktur ausbreiten (z. B. Reaktionsräder, Triebwerkszündungen), oder einen gewissen Grad an thermischer Isolierung oder kontrollierter Wärmeleitfähigkeit zwischen dem Instrument und dem Raumfahrzeugbus bieten.
Die Herausforderungen, die mit der Konstruktion und Herstellung dieser kritischen Weltraummissionshardware Komponenten verbunden sind, sind erheblich. Die Weltraumumgebung ist einzigartig feindselig:
- Extreme Temperaturen: Komponenten können Temperaturschwankungen von Hunderten von Grad Celsius erfahren und zwischen direktem Sonnenlicht und tiefem Schatten wechseln. Materialien müssen ihre strukturelle Integrität und Dimensionsstabilität über diesen Bereich beibehalten, und die differentielle Wärmeausdehnung zwischen der Halterung, dem Instrument und der Raumfahrzeugstruktur muss sorgfältig gesteuert werden.
- Vibrationen & Akustik: Die Startphase setzt das gesamte Raumfahrzeug intensiven Vibrationen und akustischen Belastungen aus. Instrumentenhalterungen müssen so konstruiert sein, dass sie diesen Kräften standhalten, ohne zu versagen oder übermäßige Vibrationen zu verursachen, die die empfindliche Nutzlast beschädigen könnten.
- Vakuum: Das Vakuum des Weltraums birgt Herausforderungen wie das Ausgasen, bei dem Materialien eingeschlossene flüchtige Stoffe freisetzen, die empfindliche optische Oberflächen oder Elektronik verunreinigen können. Materialien müssen auf geringe Ausgasungseigenschaften ausgewählt werden. Auch Kaltverschweißen kann zwischen sich berührenden Metalloberflächen im Vakuum auftreten.
- Strahlung: Abhängig von der Umlaufbahn oder Flugbahn sind Komponenten verschiedenen Formen von Strahlung (Protonen, Elektronen, kosmische Strahlung) ausgesetzt, die die Materialeigenschaften im Laufe der Zeit verschlechtern können.
- Massenbeschränkungen: Jedes Gramm, das in die Umlaufbahn gebracht wird, birgt einen erheblichen Kostenaufwand. Daher ist das Erreichen der erforderlichen Leistung mit dem geringstmöglichen Gewicht (Leichtbau) ein primärer Faktor in Raumfahrttechnik für satelliten-Hardware.
Traditionell wurden bei der Herstellung von Präzisionshalterungen Strukturen für Raumfahrzeuge subtraktive Verfahren eingesetzt, hauptsächlich CNC-Bearbeitung aus Blockmaterialien wie Aluminium- oder Titanlegierungen. Obwohl hochpräzise, stößt dieser Ansatz auf Einschränkungen, insbesondere wenn die Instrumentenkonstruktionen komplexer werden und die Ziele zur Gewichtsreduzierung aggressiver werden. Die Bearbeitung komplizierter, organisch geformter, leichter Strukturen kann extrem zeitaufwändig sein, erhebliche Materialverschwendung verursachen (Buy-to-Fly-Verhältnis) und komplexe mehrteilige Baugruppen mit zugehörigen Befestigungselementen erfordern, was das Gewicht, die Komplexität und potenzielle Fehlerpunkte erhöht. Die Herstellung von Hohlstrukturen oder inneren Merkmalen wie konformen Kühlkanälen ist oft unmöglich.
Hier ist Additive Fertigung von Metall (AM)oft auch als Metall bezeichnet 3D-Druck, entwickelt sich zu einer transformativen Lösung für Raumfahrzeugkomponenten. Technologien wie das Laser Powder Bed Fusion (L-PBF) und das Electron Beam Melting (EBM) bauen Teile Schicht für Schicht direkt aus digitalen Modellen mit Hochleistungsmetallpulvern auf. Dieser Ansatz verändert das Designparadigma grundlegend und ermöglicht die Herstellung von hochoptimierten, leichten und komplexen Instrumentenhalterungen, die zuvor nicht herstellbar waren. Additive Fertigung Luft- und Raumfahrt Anwendungen expandieren rasant und bieten Ingenieuren beispiellose Freiheit, nach Funktion und Leistung zu entwerfen, viele traditionelle Einschränkungen zu überwinden und den Weg für leistungsfähigere und kostengünstigere Weltraummissionen zu ebnen. Unternehmen, die sich auf diese fortschrittlichen Techniken spezialisiert haben, wie z. B. Met3dp, bieten das entscheidende Fachwissen und die Fähigkeiten, die erforderlich sind, um diese Vorteile für anspruchsvolle Raumfahrttechnik herausforderungen.
Anwendungen und Anwendungsfälle: Wo werden 3D-gedruckte Instrumentenhalterungen eingesetzt?
Die Vielseitigkeit und die Leistungsvorteile der additiven Metallfertigung haben zu ihrer Einführung in einem breiten Spektrum von Raumfahrzeug- und Missionstypen für die Herstellung anspruchsvoller Instrumentenhalterungen und Nutzlastbefestigungsstrukturengeführt. Die Fähigkeit, Designs auf spezifische funktionale Anforderungen zuzuschneiden, auf Gewicht zu optimieren und Funktionen zu integrieren, macht den 3D-Druck besonders attraktiv für hochwertige, leistungskritische Raumfahrtanwendungen. Beschaffungsmanager, die mit Lieferanten von Verteidigungsunternehmen und kommerziellen NewSpace Unternehmen zusammenarbeiten, beziehen zunehmend diese fortschrittlichen kommerziellen Weltraumkomponenten.
Hier sind einige wichtige Anwendungsbereiche, in denen 3D-gedruckte Instrumentenhalterungen einen erheblichen Einfluss haben:
- Optische Nutzlasten:
- Teleskope & Bildgeber: Die Aufrechterhaltung der präzisen Ausrichtung von Spiegeln, Linsen, Detektoren und Brennebeneinheiten ist von größter Bedeutung. 3D-gedruckte Halterungen, die oft die Topologieoptimierung nutzen, bieten außergewöhnliche Steifigkeits-Gewichts-Verhältnisse und gewährleisten Stabilität unter thermischen Belastungen und Mikrovibrationen. Materialien wie Ti-6Al-4V bieten eine geringe Wärmeausdehnung, die für die optische Stabilität entscheidend ist. Halterungen für große Haupt- oder Sekundärspiegel, komplexe Kameraarrays und Stützstrukturen für Blenden profitieren stark.
- Spektrometer & Interferometer: Diese Instrumente sind auf die präzise Positionierung von Gittern, Strahlteilern und Detektoren angewiesen. AM ermöglicht komplexe Geometrien, die Befestigungsmerkmale, Wärmeableitungspfade (wie integrierte Heatpipes oder leitfähige Bänder) und Schwingungsdämpfungselemente direkt in die Satelliteninstrumentenhalterung.
- integrieren. Star Tracker & Sonnensensoren:
- Diese Sensoren sind für die Lageregelung und -steuerung unerlässlich und erfordern stabile Montageplattformen. AM ermöglicht leichte Halterungen mit optimierten Geometrien, die die Behinderung minimieren und die Ausrichtungsgenauigkeit beibehalten.
- Hochfrequenz (HF)-Systeme: Antennen & Speisungen:
- Halterungen für verschiedene Antennentypen (Parabolantennen, Phased-Array-Antennen, Helixantennen) profitieren von der Fähigkeit von AM, komplexe Formen zu erzeugen, die für die HF-Leistung und die strukturelle Integrität optimiert sind. Leichtbau ist entscheidend, insbesondere für große ausfahrbare Antennenstrukturen. Wellenleiterkomponenten und Speisehornstützen können direkt in die Halterungsstruktur integriert werden, wodurch die Teileanzahl und die Schnittstellen reduziert werden. Transponder & Verstärker:
- Diese Komponenten erzeugen Wärme und erfordern eine stabile Montage mit effektivem Wärmemanagement. 3D-gedruckte Halterungen können konforme Kühlkanäle oder optimierte leitfähige Pfade integrieren, um Wärme effizient abzuleiten und so die Zuverlässigkeit und Leistung zu verbessern.
- Sensoren & Detektoren: Umweltsensoren:
- Instrumente zur Messung von Magnetfeldern, Plasmaeigenschaften, Strahlungswerten oder der atmosphärischen Zusammensetzung erfordern oft eine spezifische Positionierung und Isolierung. 3D-gedruckte Halterungen ermöglichen kundenspezifische Designs, die auf die Bedürfnisse des Sensors zugeschnitten sind und potenziell Abschirmungen oder spezifische thermische Eigenschaften integrieren. Gyroskope und Beschleunigungsmesser in IMUs benötigen extrem stabile Montageplattformen, um eine präzise Navigation und Lagenerkennung zu gewährleisten. Hochsteife, niedrig-CTE (Coefficient of Thermal Expansion) 3D-gedruckte Halterungen sind von Vorteil.
- Wissenschaftliche Sonden: Instrumente auf planetaren Landern oder Tiefraumsonden, die Oberflächeneigenschaften, seismische Aktivitäten messen oder Proben sammeln, benötigen robuste und zuverlässige Halterungen, die rauen Umgebungen und potenziellen Stößen standhalten.
- Antriebs- & Fluidsysteme:
- Triebwerkshalterungen: Kleine Satellitentriebwerke (Kaltgas, elektrischer Antrieb) erfordern eine präzise Ausrichtung und eine robuste Montage. AM kann Halterungen mit optimierten Lastpfaden und reduziertem Gewicht herstellen.
- Ventil- & Schlauchunterstützungen: Eine komplexe Führung von Flüssigkeitsleitungen kann durch kundenspezifisch gestaltete, leichte 3D-gedruckte Halterungen unterstützt werden, wodurch mehrere herkömmliche Klemmen und Halterungen in einzelnen Komponenten zusammengefasst werden.
Branchen und Missionstypen:
- Kommerzieller Weltraum (NewSpace): Große Satellitenkonstellationen für die Kommunikation (Starlink, OneWeb) oder Erdbeobachtung sind stark auf die Reduzierung der Startkosten durch Gewichtsreduzierung angewiesen. AM ermöglicht die schnelle Herstellung von optimierten Komponenten wie Instrumentenhalterungen für Hunderte oder Tausende von Satelliten. CubeSats und SmallSats profitieren ebenfalls erheblich von den Miniaturisierungs- und Integrationsmöglichkeiten, die der 3D-Druck bietet.
- Regierung & Verteidigung: Behörden wie NASA, ESA, JAXA und Verteidigungsorganisationen nutzen AM für einzigartige, hochleistungsfähige Hardware für Flaggschiff-Wissenschaftsmissionen (z. B. Weltraumteleskope, Mars-Rover, Tiefraumsonden) sowie Aufklärungs- oder Kommunikationssatelliten. Die Fähigkeit, maßgeschneiderte Designs zu erstellen und möglicherweise die Vorlaufzeiten für kritische Missionen zu verkürzen, ist von hohem Wert. Als wichtiger Zulieferer für die Verteidigung ist eine sichere und zuverlässige Fertigung von größter Bedeutung.
- Forschungseinrichtungen: Universitäten und Forschungslabore, die experimentelle Nutzlasten oder CubeSat-Missionen entwickeln, nutzen AM aufgrund seiner Zugänglichkeit, der Geschwindigkeit beim Prototyping und der Fähigkeit, kundenspezifische Hardware für spezifische wissenschaftliche Ziele zu erstellen.
Konkrete Beispiele sind beispielsweise topologieoptimierte Halterungen zur Aufnahme wissenschaftlicher Instrumente auf dem Mars-Rover Perseverance, leichte Antennenhalterungen für Kommunikationssatelliten oder komplexe optische Bänke für Erdbeobachtungs-Imager, bei denen die Stabilität von größter Bedeutung ist. Der Trend ist eindeutig: Da die Missionsanforderungen immer anspruchsvoller werden und die Startkosten ein entscheidender Faktor bleiben, werden Metall- additive Fertigung Luft- und Raumfahrt Lösungen wie 3D-gedruckte Instrumentenhalterungen in allen Bereichen der Raumfahrtindustrie eine immer wichtigere Rolle spielen.
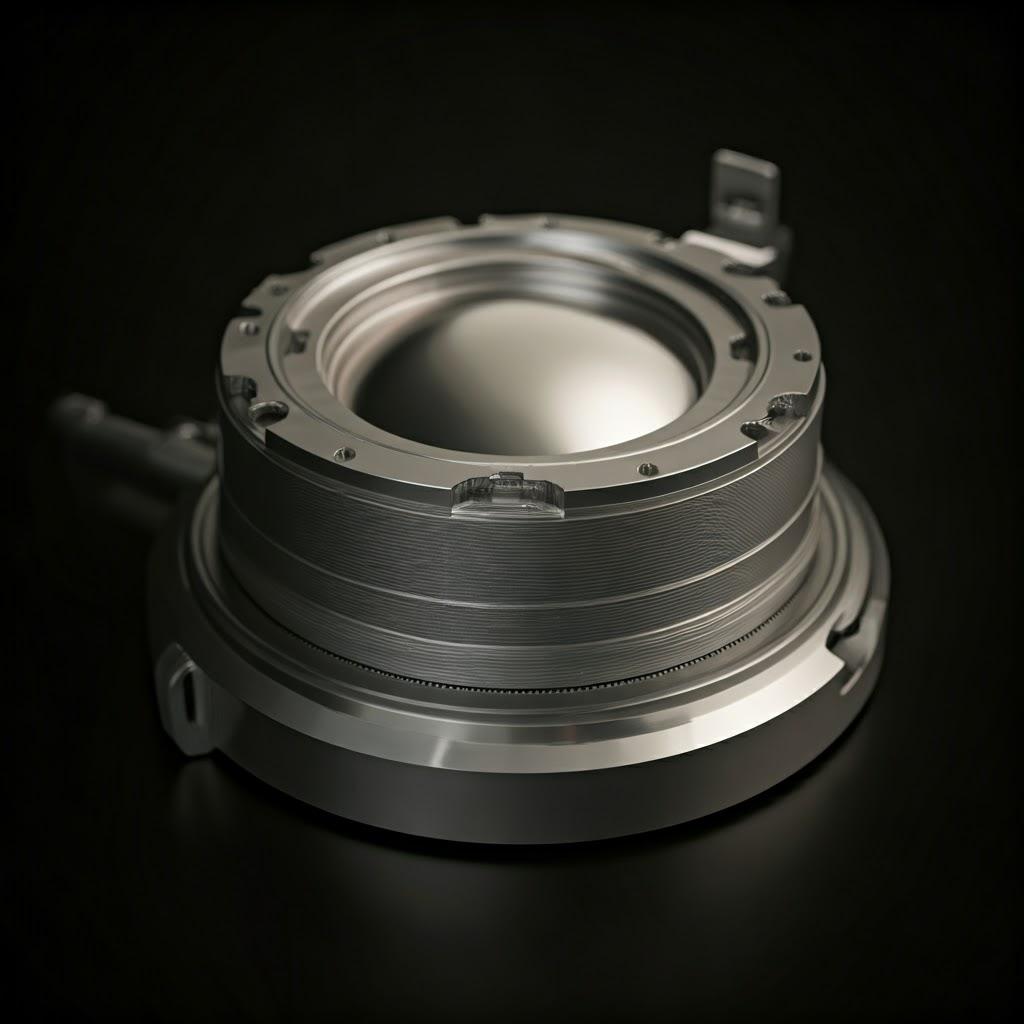
Warum Metall-3D-Druck für Instrumentenhalterungen in Raumfahrzeugen? Freisetzung von Leistungsvorteilen
Die Annahme von metall 3D-Druck Luft- und Raumfahrt Technologien für die Herstellung von Instrumentenhalterungen in Raumfahrzeugen wird durch eine überzeugende Reihe von Vorteilen gegenüber herkömmlichen subtraktiven Verfahren wie der CNC-Bearbeitung angetrieben. Diese Vorteile führen direkt zu verbesserter Leistung, reduzierten Kosten, schnelleren Entwicklungszyklen und erweiterten Missionsfähigkeiten. Für Ingenieure, die die Grenzen von Raumfahrttechnik und Beschaffungsmanager, die kostengünstige, hochwertige Raumfahrzeugkomponentensuchen, ist das Verständnis dieser Vorteile von entscheidender Bedeutung.
Hier ist eine Aufschlüsselung, warum die additive Fertigung die Herstellung dieser kritischen Teile revolutioniert:
- Beispiellose Leichtbauweise:
- Topologie-Optimierung: AM ermöglicht die praktische Anwendung von Topologieoptimierungsalgorithmen. Diese Werkzeuge bestimmen die effizienteste Materialverteilung innerhalb eines definierten Designraums, um spezifische Last- und Steifigkeitsanforderungen zu erfüllen. Das Ergebnis sind oft organische, skelettartige Strukturen, die erhebliche Mengen an nicht essentiellem Material entfernen und das Teilegewicht im Vergleich zu herkömmlich bearbeiteten Komponenten, die mit einfacheren Geometrien entworfen wurden, drastisch reduzieren. Dies senkt direkt die Startkosten (geschätzt auf Tausende bis Zehntausende von Dollar pro Kilogramm) und kann eine höhere Nutzlastkapazität ermöglichen.
- Gitterförmige Strukturen: AM ermöglicht die Integration komplexer interner Gitterstrukturen. Diese periodischen zellularen Materialien bieten außergewöhnliche Steifigkeits-Gewichts-Verhältnisse, Energieabsorptionsfähigkeiten (zur Schwingungsdämpfung) und können den Wärmeübergang erleichtern. Sie sind mit subtraktiven Verfahren praktisch unmöglich herzustellen.
- Geometrische Komplexität & Gestaltungsfreiheit:
- „Komplexität ist kostenlos“: Im Gegensatz zur Zerspanung, bei der komplexe Merkmale die Bearbeitungszeit und -kosten erheblich erhöhen, bedeutet die schichtweise Natur der AM, dass komplizierte Designs (innerhalb der Prozessgrenzen) nicht zwangsläufig erhebliche Kosten- oder Zeitstrafen verursachen. Dies gibt Ingenieuren die Freiheit, Teile zu entwerfen, die für die Funktion optimiert sind, anstatt durch die Herstellbarkeit mit herkömmlichen Mitteln eingeschränkt zu werden.
- Integrierte Funktionen: Funktionale Merkmale wie Kabelführungskanäle, Fluidwege (konforme Kühlung/Heizung), integrierte Befestigungselemente, kinematische Montagepunkte und komplexe Schnittstellen können direkt in die Halterungsstruktur eingebaut werden.
- Teil Konsolidierung:
- Reduzierte Montage: Mehrere Einzelkomponenten, die traditionell separat bearbeitet und dann mit Befestigungselementen montiert würden, können oft neu gestaltet und als ein einziges, monolithisches Teil gedruckt werden.
- Vorteile: Dies reduziert die Montagezeit und die Arbeitskosten erheblich, eliminiert potenzielle Fehlerquellen, die mit Verbindungen und Befestigungselementen verbunden sind (was die Zuverlässigkeit verbessert), und trägt ferner zur Gewichtsreduzierung bei, indem die Masse der Befestigungselemente selbst entfernt wird. Dies ist ein wichtiger Faktor für Teilekonsolidierung AM strategien.
- Verbesserte Leistungseigenschaften:
- Schwingungsdämpfung: Die Fähigkeit, optimierte Geometrien und Gitterstrukturen zu integrieren, ermöglicht die Konstruktion von Halterungen mit spezifischen Schwingungsdämpfungseigenschaften, wodurch empfindliche Instrumente besser vor Startbelastungen und raumfahrtbedingten Vibrationen geschützt werden.
- Wärmemanagement: AM ermöglicht die Herstellung von Halterungen mit integrierten, hocheffizienten thermischen Steuerungsmerkmalen. Konforme Kühlkanäle, die den Konturen wärmeerzeugender Komponenten folgen, oder optimierte leitfähige Pfade können direkt in das Teil konstruiert werden, wodurch die thermische Stabilität und die Instrumentenleistung verbessert werden. Materialien wie Scalmalloy® bieten eine gute Wärmeleitfähigkeit für die Wärmeableitung.
- Maßgeschneiderte Steifigkeit: Die Topologieoptimierung ermöglicht es Ingenieuren, Material präzise dort zu platzieren, wo es am meisten benötigt wird, wodurch eine außergewöhnliche Steifigkeit in kritischen Richtungen erreicht und gleichzeitig die Masse an anderer Stelle minimiert wird.
- Schnelles Prototyping, Iteration und kürzere Vorlaufzeiten:
- Geschwindigkeit: AM ermöglicht die direkte Herstellung von Teilen aus CAD-Modellen, wodurch die Notwendigkeit herkömmlicher Werkzeuge (Vorrichtungen, Halterungen, Formen) entfällt. Dies verkürzt die Vorlaufzeit von der Designfinalisierung bis zum Vorliegen eines physischen Teils drastisch, oft von Wochen oder Monaten auf Tage.
- Schnellere Iteration: Designmodifikationen können schnell im CAD-Modell implementiert und ein neues Teil schnell gedruckt werden, wodurch schnellere Design-Build-Test-Zyklen während der Entwicklung ermöglicht werden. Dies beschleunigt die Innovation und ermöglicht optimiertere endgültige Designs. Dieser Vorteil in rapid Prototyping Luft- und Raumfahrt ist von unschätzbarem Wert.
- Fertigung auf Abruf: AM bietet das Potenzial für die On-Demand-Produktion, wodurch der Bedarf an großen Lagerbeständen reduziert und die Risiken der Lieferkette, die mit traditionellen Fertigungsabhängigkeiten verbunden sind, gemindert werden.
- Fortschrittliche Materialverwendung:
- Optimierte Materialien: AM-Verfahren sind mit fortschrittlichen Hochleistungslegierungen kompatibel, die speziell für die Weltraumumgebung geeignet sind, wie z. B. hochfeste Aluminiumlegierungen (Scalmalloy®) und Titanlegierungen (Ti-6Al-4V). Diese Weltraumwerkstoffe bieten eine überlegene spezifische Festigkeit, Korrosionsbeständigkeit und Stabilität über extreme Temperaturen hinweg.
- Weniger Abfall: Während das Pulvermanagement von entscheidender Bedeutung ist, erzeugen AM-Verfahren im Allgemeinen weniger Materialabfall im Vergleich zur subtraktiven Bearbeitung, insbesondere bei komplexen Teilen, bei denen das Buy-to-Fly-Verhältnis (Gewicht des gekauften Rohmaterials im Vergleich zum Gewicht des fertigen Teils) für die Bearbeitung sehr hoch sein kann.
Vergleich: AM vs. traditionelle Bearbeitung für Instrumentenhalterungen
Merkmal | Additive Fertigung von Metall (AM) | Traditionelle CNC-Bearbeitung |
---|---|---|
Gewichtsreduzierung | Ausgezeichnet (Topologieoptimierung, Gitter) | Begrenzt (durch Barrenform, Zugang eingeschränkt) |
Komplexität | Hohe geometrische Freiheit, „Komplexität ist kostenlos“ | Kosten/Zeit steigen erheblich |
Teil Konsolidierung | Ausgezeichnete Fähigkeit | Begrenzt, erfordert Montage |
Integrierte Funktionen | Hoch (Kühlkanäle, Routing usw.) | Schwierig oder unmöglich |
Vorlaufzeit | Fasten (Tage/Wochen) | Langsamer (Wochen/Monate, werkzeugabhängig) |
Materialabfälle | Niedriger (Wiederverwendung des Pulverbetts, nahezu endkonturnahe Form) | Höher (Erhebliche Späne-/Spanerzeugung) |
Werkzeugkosten | Keine (Direkte digitale Fertigung) | Kann erheblich sein (Vorrichtungen, Halterungen) |
Entwurf Iteration | Schnell | Langsamer |
Erreichbare Präzision | Gut (Erfordert oft Nachbearbeitung für kritische Merkmale) | Ausgezeichnet |
Oberfläche | Gut bis sehr gut (wie gebaut), erfordert Endbearbeitung | Ausgezeichnet |
In Blätter exportieren
Während die traditionelle Bearbeitung immer noch in der Erzielung des höchsten Niveaus an Oberflächengüte und Toleranz direkt hervorragend ist, bietet die Metall-AM eine leistungsstarke Alternative, insbesondere wenn Designkomplexität, Gewichtsreduzierung und integrierte Funktionalität die wichtigsten Treiber sind. Oft wird ein hybrider Ansatz verwendet, bei dem der Großteil der komplexen Struktur im 3D-Druckverfahren hergestellt wird, gefolgt von einer gezielten CNC-Bearbeitung kritischer Schnittstellen, um die endgültigen Toleranzen zu erreichen. Die Zusammenarbeit mit einem erfahrenen AM-Anbieter wie Met3dp stellt sicher, dass die optimale Fertigungsstrategie eingesetzt wird, um diese überzeugenden Vorteile für Ihre spezifische Luft- und Raumfahrtanwendung.
Empfohlene Materialien: Scalmalloy® und Ti-6Al-4V für extreme Umgebungen
Die Auswahl des richtigen Materials ist von grundlegender Bedeutung für den Erfolg jeder Raumfahrtkomponente, insbesondere für Präzisionsinstrumentenhalterungen, die unter extremen Bedingungen betrieben werden. Das Material muss die erforderliche strukturelle Integrität, Stabilität und Umweltbeständigkeit bieten und gleichzeitig strenge Massenbeschränkungen einhalten. Die additive Metallfertigung eröffnet die Möglichkeit, fortschrittliche Legierungen zu verwenden, die besonders gut für diese anspruchsvollen Anforderungen geeignet sind Raumfahrtanwendungen. Zwei herausragende Materialien, die mit Pulverbettfusionstechniken (PBF) wie L-PBF und EBM verarbeitet werden, sind Scalmalloy® (eine Aluminiumlegierung) und Ti-6Al-4V (eine Titanlegierung). Das Verständnis ihrer einzigartigen Eigenschaften und Vorteile ist für Ingenieure und Einkaufsmanager, die spezifizieren, von entscheidender Bedeutung Weltraumwerkstoffe.
Scalmalloy® (Al-Mg-Sc-Legierung): Das Hochleistungsaluminium
Scalmalloy® ist eine patentierte hochfeste Aluminium-Magnesium-Scandium-Legierung, die speziell für die additive Fertigung entwickelt wurde. Entwickelt von APWorks (einer Airbus-Tochtergesellschaft), hat es in der Luft- und Raumfahrt aufgrund seiner außergewöhnlichen Kombination von Eigenschaften schnell an Bedeutung gewonnen, die oft über denen herkömmlicher hochfester Luft- und Raumfahrtaluminiumlegierungen liegen.
- Wichtige Eigenschaften:
- Hohe spezifische Festigkeit: Bietet ein Festigkeits-Gewichts-Verhältnis, das deutlich höher ist als bei herkömmlichen Luft- und Raumfahrtaluminiumlegierungen (z. B. AlSi10Mg) und mit einigen Titansorten vergleichbar ist, was es ideal für die Gewichtsreduzierung macht.
- Ausgezeichnete Duktilität und Zähigkeit: Im Gegensatz zu vielen hochfesten Aluminiumlegierungen behält Scalmalloy® eine gute Duktilität und Bruchzähigkeit, selbst bei kryogenen Temperaturen, was die strukturelle Zuverlässigkeit erhöht.
- Gut schweißbar: Kann effektiv geschweißt werden, was für potenzielle Nachbearbeitungs- oder Montagevorgänge von Vorteil ist, obwohl AM oft darauf abzielt, solche Anforderungen durch Konsolidierung zu eliminieren.
- Korrosionsbeständigkeit: Weist eine gute Korrosionsbeständigkeit auf.
- Verarbeitbarkeit über L-PBF: Gut charakterisiert und für Laser Powder Bed Fusion-Prozesse optimiert.
- Mikrostruktur: Zeigt nach dem Drucken und der Wärmebehandlung eine feinkörnige Mikrostruktur, die zu seinen überlegenen mechanischen Eigenschaften beiträgt.
- Vorteile für Instrumentenhalterungen:
- Erhebliche Gewichtseinsparungen: Sein Hauptvorteil. Ermöglicht die Konstruktion von Halterungen mit dünnen Wänden und komplexen, topologieoptimierten Geometrien, die die Masse im Vergleich zu Teilen aus herkömmlichem Aluminium oder sogar Titan in einigen steifigkeitsgetriebenen Designs drastisch reduzieren.
- Steifigkeitskritische Anwendungen: Wo die Aufrechterhaltung von Form und Ausrichtung unter Last entscheidend ist (z. B. optische Bänke, Spiegelhalterungen), ist seine hohe spezifische Steifigkeit sehr vorteilhaft.
- Kryogene Leistung: Geeignet für Missionen, die der Einwirkung sehr niedriger Temperaturen ausgesetzt sind.
- Überlegungen zur Verarbeitung: Erfordert eine sorgfältige Kontrolle der L-PBF-Parameter und spezifische Nachbearbeitungs-Wärmebehandlungen (Lösungsglühen und Aushärten), um optimale Eigenschaften zu erzielen. Anfällig für Heißrisse, wenn die Prozessparameter nicht optimiert sind.
Ti-6Al-4V (Titan Grad 5): Das Arbeitspferd der Luft- und Raumfahrt
Ti-6Al-4V (Titan-6 % Aluminium-4 % Vanadium), oft als Titan Grad 5 bezeichnet, ist wohl die am häufigsten verwendete Titanlegierung in der Luft- und Raumfahrt und in medizinischen Anwendungen und lässt sich gut auf die additive Fertigung sowohl über L-PBF als auch über EBM (Electron Beam Melting) übertragen.
- Wichtige Eigenschaften:
- Hohes Verhältnis von Festigkeit zu Gewicht: Ausgezeichnete spezifische Festigkeit, die bis zu mäßig erhöhten Temperaturen (etwa 300-400 °C) erhalten bleibt.
- Außergewöhnliche Korrosionsbeständigkeit: Sehr korrosionsbeständig in verschiedenen Umgebungen, einschließlich oxidierender Säuren und Chloridlösungen, was für Langzeitmissionen und die Verhinderung von Kontamination von entscheidender Bedeutung ist.
- Geringe thermische Ausdehnung: Hat einen relativ niedrigen Wärmeausdehnungskoeffizienten (CTE), was für die Aufrechterhaltung der Dimensionsstabilität in optischen Systemen oder Präzisionsausrichtungen während des thermischen Zyklus sehr vorteilhaft ist.
- Ausgezeichnete Biokompatibilität: Weniger relevant für Instrumentenhalterungen als für medizinische Implantate, weist es auf die Trägheit des Materials hin.
- Gute Dauerfestigkeit und Bruchzähigkeit: Robustes Verhalten unter zyklischen Belastungsbedingungen.
- Verarbeitbarkeit über L-PBF & EBM: Kann effektiv mit beiden großen PBF-Technologien verarbeitet werden. EBM führt oft zu geringeren Eigenspannungen, aber typischerweise zu einer raueren Oberflächengüte im Vergleich zu L-PBF.
- Vorteile für Instrumentenhalterungen:
- Festigkeitsgetriebene Designs: Ideal, wenn hohe absolute Festigkeit, Dauerfestigkeit und Bruchzähigkeit die primären Anforderungen sind.
- Thermische Stabilität: Sein niedriger CTE macht es zur bevorzugten Wahl für Halterungen, die eine extreme Dimensionsstabilität über Temperaturbereiche hinweg erfordern, wie z. B. solche, die in hochpräzisen optischen Baugruppen verwendet werden.
- Raue Umgebungen: Überlegene Korrosionsbeständigkeit macht es für Anwendungen geeignet, die potenziell Resttreibstoffen oder bestimmten planetarischen Atmosphären ausgesetzt sind.
- Anwendungen bei erhöhten Temperaturen: Behält die Festigkeit bei höheren Betriebstemperaturen besser als Aluminiumlegierungen.
- Überlegungen zur Verarbeitung: Titanpulver sind reaktiv und erfordern eine sorgfältige Handhabung in inerten Atmosphären, um die Aufnahme von Sauerstoff zu verhindern, was die mechanischen Eigenschaften beeinträchtigen kann. Die Nachbearbeitung umfasst oft Spannungsarmglühen und heißes isostatisches Pressen (HIP), um die innere Porosität zu reduzieren und die Ermüdungseigenschaften zu verbessern, insbesondere bei flugkritischen Teilen.
Materialauswahl: Ein vergleichender Blick
Eigentum | Scalmalloy® | Ti-6Al-4V (Klasse 5) | Relevanz für Instrumentenhalterungen |
---|---|---|---|
Dichte | ~2,67 g/cm³ | ~4,43 g/cm³ | Geringere Dichte begünstigt Scalmalloy® für reine Gewichtsreduzierung. |
Streckgrenze (typisch AM) | ~450-500 MPa | ~900-1100 MPa (wärmebehandelt/HIPed) | Ti-6Al-4V bietet eine höhere absolute Festigkeit. |
Spezifische Stärke | Sehr hoch | Sehr hoch | Beide ausgezeichnet; Scalmalloy® unter bestimmten Bedingungen etwas besser. |
Steifigkeit (Young's Modulus) | ~70 GPa | ~110-115 GPa | Ti-6Al-4V ist deutlich steifer. |
Spezifische Steifigkeit | Sehr hoch | Hoch | Scalmalloy® zeichnet sich aus, wenn die Steifigkeit pro Masseneinheit entscheidend ist. |
Max. Betriebstemperatur | ~125-150 °C | ~350-400 °C | Ti-6Al-4V geeignet für den Betrieb bei höheren Temperaturen. |
Wärmeausdehnung (CTE) | ~21-23 µm/m·K | ~8,6-9,2 µm/m·K | Ti-6Al-4V bietet eine überlegene Dimensionsstabilität bei Temperaturänderungen. |
Wärmeleitfähigkeit | ~110-120 W/m·K | ~6,7-7,5 W/m·K | Scalmalloy® ist viel besser für die Wärmeableitung, falls erforderlich. |
Kosten | Hoch (Scandiumgehalt) | Hoch (Titanbasis, Verarbeitung) | Beide sind Premiummaterialien; die Kosten hängen von Anwendung/Volumen ab. |
In Blätter exportieren
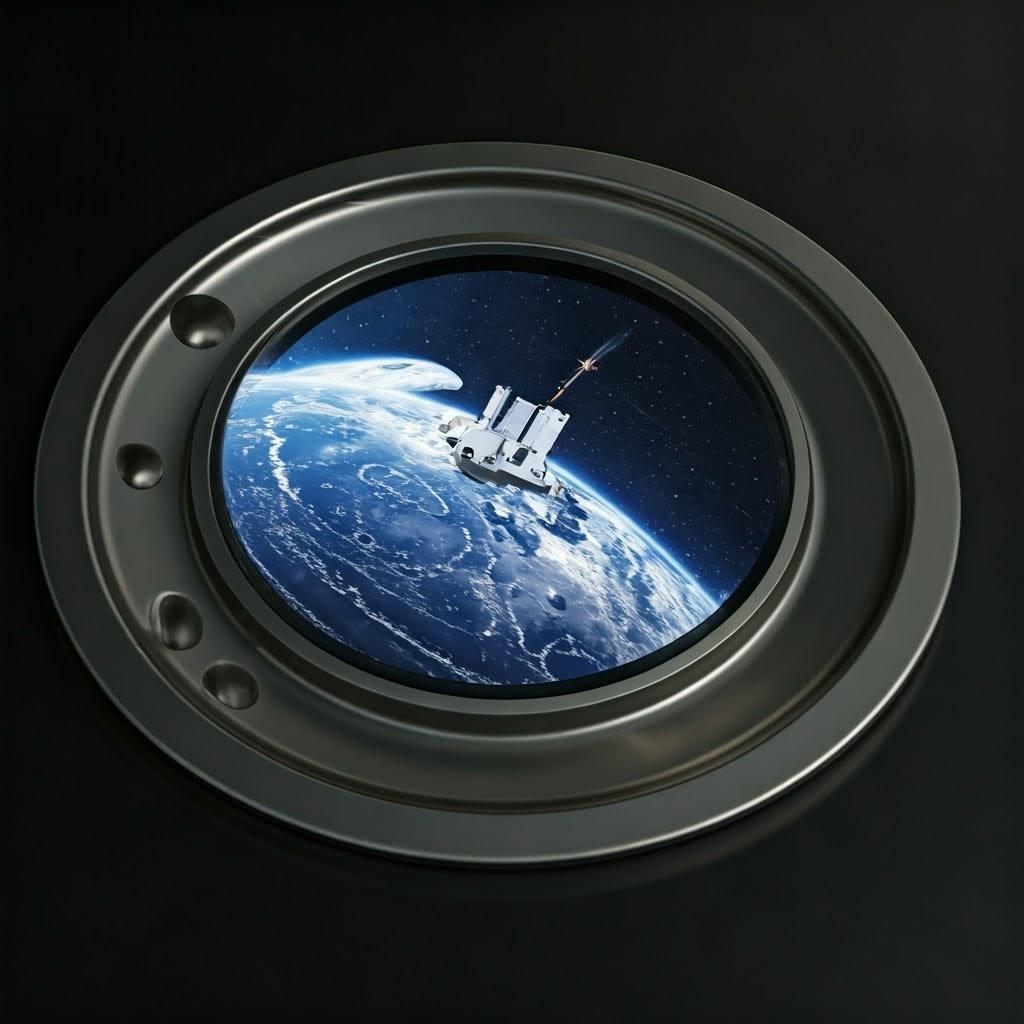
Die Bedeutung der Pulverqualität: Der Met3dp-Vorteil
Die ultimative Leistung einer im 3D-Druckverfahren hergestellten Komponente, ob Scalmalloy®, Ti-6Al-4V oder andere fortschrittliche Legierungen wie Inconel oder Spezialstähle, hängt grundlegend von der Qualität des eingebrachten Metallpulvers ab. Faktoren wie Partikelgrößenverteilung (PSD), Sphärizität, Fließfähigkeit, Reinheit und innere Porosität wirken sich direkt auf die Dichte, die mechanischen Eigenschaften und die Oberflächengüte des fertigen Teils aus.
Hier bietet die Partnerschaft mit einem vertikal integrierten Anbieter wie Met3dp erhebliche Vorteile. Met3dp verfügt nicht nur über Fachwissen in 3D-Druck von Metall Verfahren wie SEBM (Selective Electron Beam Melting – ähnlich EBM), sondern ist auch auf die Herstellung des Feedstocks selbst spezialisiert. Unser Unternehmen setzt branchenführende Pulverherstellungstechnologien ein:
- Gaszerstäubung (GA): Verwendet Hochdruck-Inertgasstrahlen, um einen Strom geschmolzenen Metalls in feine, kugelförmige Tröpfchen zu zerlegen, die schnell erstarren. Unsere fortschrittlichen Gaszerstäubungsanlagen verwenden einzigartige Düsen- und Gasströmungsdesigns, um metallische Kugeln mit außergewöhnlicher Sphärizität und Fließfähigkeit herzustellen, die für eine gleichmäßige Schichtverteilung in PBF-Verfahren unerlässlich sind.
- Plasma-Rotations-Elektroden-Verfahren (PREP): Diese Methode verwendet eine sich schnell drehende Elektrodenstange aus der gewünschten Legierung, die an der Spitze durch einen Plasmabrenner geschmolzen wird. Die Zentrifugalkraft schleudert geschmolzene Tröpfchen aus, die sich im Flug zu hochkugelförmigen Pulvern mit sehr geringer innerer Porosität und Satellitengehalt verfestigen, ideal für die anspruchsvollsten Anwendungen.
Durch die Steuerung des Pulverherstellungsprozesses gewährleistet Met3dp eine gleichbleibende Versorgung mit hochwertige Metallpulver für die additive Fertigung optimiert, einschließlich Legierungen wie TiNi, TiTa, TiAl, TiNbZr, CoCrMo, verschiedene Edelstähle und Superlegierungen, sowie Standards wie Ti-6Al-4V. Dieses Engagement für die Pulverqualität, kombiniert mit jahrzehntelanger gemeinsamer Erfahrung in der Metall-AM, ermöglicht es uns, Luft- und Raumfahrtkomponenten mit überlegener Dichte, mechanischen Eigenschaften und Zuverlässigkeit, wodurch unsere Partner die Vorteile von Materialien wie Scalmalloy® und Ti-6Al-4V für ihre kritischen Instrumentenhalterungen für Raumfahrzeuge voll ausschöpfen können. Die Wahl des richtigen Lieferanten für Luft- und Raumfahrtmetallpulver ist ebenso wichtig wie die Wahl des Druckdienstes selbst.
Design for Additive Manufacturing (DfAM): Optimierung von Instrumentenhalterungen für den 3D-Druck
Der Übergang von traditionellen Designbeschränkungen zur Nutzung des vollen Potenzials der additiven Metallfertigung erfordert ein Umdenken. Design for Additive Manufacturing (DfAM) bedeutet nicht nur, bestehende Designs druckbar zu machen; es geht darum, die Bauteilgeometrie grundlegend zu überdenken, um die Vorteile des Schicht-für-Schicht-Fertigungsprozesses zu maximieren, was besonders wichtig für risikoreiche Raumfahrtanwendungen wie Instrumentenhalterungen für Raumfahrzeuge. Die Anwendung von DfAM Luft- und Raumfahrt Prinzipien ermöglicht es Ingenieuren, eine überlegene Leistung zu erzielen, das Gewicht zu reduzieren, Teile zu konsolidieren und Entwicklungszyklen zu verkürzen. Die Nichtbeachtung von DfAM führt oft zu suboptimalen Ergebnissen, erhöhten Nachbearbeitungsherausforderungen, höheren Kosten und potenziell fehlgeschlagenen Drucken.
Hier sind wichtige DfAM-Prinzipien und -Überlegungen zur Optimierung von Instrumentenhalterungen für metall 3D-Druck Luft- und Raumfahrt Prozesse wie L-PBF und EBM:
- Topologie-Optimierung und generatives Design einsetzen:
- Konzept: Diese Berechnungswerkzeuge sind die Stars im DfAM. Ingenieure definieren den Designraum (maximal zulässiges Volumen), Lastfälle (Kräfte, Drücke, thermische Belastungen), Einschränkungen (Ausschlusszonen, Montagepunkte) und Leistungsziele (Masse minimieren, Steifigkeit maximieren). Die Software zur Topologieoptimierung entfernt dann iterativ Material aus unkritischen Bereichen und enthüllt so die effizienteste tragende Struktur. Generatives Design untersucht oft mehrere optimierte Lösungen basierend auf Parametern.
- Das Ergebnis: Die Ergebnisse sind oft organische, „bionische“ Strukturen, die in ihrer Materialausnutzung hocheffizient sind und zu erheblichen Gewichtseinsparungen (oft 20-50 % oder mehr) führen, während sie die Leistungsanforderungen erfüllen oder übertreffen. Dies ist ideal zur Reduzierung der Startkosten im Zusammenhang mit satelliten-Hardware.
- Erwägung: Optimierte Designs können komplex sein und erfordern möglicherweise eine sorgfältige Analyse, um die Herstellbarkeit sicherzustellen (z. B. das Vermeiden von Merkmalen, die zu dünn sind, um zuverlässig gedruckt zu werden).
- Nutzen Sie Gitterstrukturen strategisch:
- Konzept: AM ermöglicht die Integration von komplizierten internen Gitter- oder Zellstrukturen. Diese können einheitlich oder abgestuft (variierende Dichte) sein und in verschiedenen Zelltypen (kubisch, Oktaeder-Truss, Gyroid usw.) vorliegen, die jeweils unterschiedliche mechanische, thermische oder Strömungseigenschaften bieten.
- Anwendungen für Halterungen:
- Leichte Füllung: Der Ersatz von Festkörpervolumina durch Gitter mit geringer Dichte erhält die strukturelle Integrität und reduziert gleichzeitig die Masse drastisch.
- Schwingungsdämpfung: Bestimmte Gittertopologien zeichnen sich durch die Absorption von Schwingungsenergie aus und tragen dazu bei, empfindliche Instrumente zu isolieren.
- Wärmemanagement: Gitter können so konzipiert werden, dass sie den Wärmeübergang verbessern oder behindern oder den Flüssigkeitsfluss für die aktive Kühlung erleichtern.
- Erwägung: Erfordert spezielle Designsoftware und sorgfältige Berücksichtigung der Druckbarkeit (minimale Strebenabmessung, Pulverentfernung aus inneren Hohlräumen). Entwurf einer Gitterstruktur ist eine fortschrittliche DfAM-Technik.
- Design für minimale Stützstrukturen:
- Die Herausforderung: Stützstrukturen sind in PBF-Prozessen oft erforderlich, um das Teil an der Bauplatte zu verankern, überhängende Merkmale (typischerweise Winkel unter 45 Grad zur Horizontalen) zu unterstützen und die Wärmeableitung zu unterstützen, um Verformungen zu verhindern. Stützen verbrauchen jedoch zusätzliches Material, erhöhen die Druckzeit und erfordern einen erheblichen Nachbearbeitungsaufwand für die Entfernung, was Oberflächen beschädigen und in komplexen Innenbereichen schwierig sein kann.
- Strategien:
- Selbsttragende Winkel: Gestalten Sie Überhänge nach Möglichkeit über dem kritischen Winkel (oft ~45°, aber material-/maschinenabhängig).
- Merkmal Orientierung: Durch geschicktes Ausrichten des Teils auf der Bauplattform können Überhänge in selbsttragende Merkmale umgewandelt werden. Dies ist ein kritischer Schritt in der Bauausrichtungsstrategie.
- Opfernde Merkmale einbauen: Manchmal können Merkmale wie Fasen oder Rundungen anstelle von scharfen horizontalen Überhängen diese selbsttragend machen.
- Interne Kanäle: Entwerfen Sie Kanäle mit Diamant- oder Tropfenquerschnitten anstelle von kreisförmigen, um das „Dach“ selbsttragend zu machen.
- Das Ziel: Minimieren Sie die Abhängigkeit von Stützen, insbesondere komplexen internen, um Kosten, Vorlaufzeit und Nachbearbeitungskomplexität zu reduzieren.
- Optimierung der Teileausrichtung:
- Abstriche: Die Ausrichtung der Instrumentenhalterung innerhalb der Baukammer hat erhebliche Auswirkungen auf mehrere Faktoren:
- Oberfläche: Nach unten gerichtete Oberflächen und direkt gestützte Oberflächen weisen oft eine schlechtere Oberfläche (höherer Ra-Wert) auf als nach oben gerichtete oder vertikale Wände. Kritische Oberflächen sollten idealerweise für die beste Oberfläche ausgerichtet werden.
- Mechanische Eigenschaften: Anisotropie (richtungsabhängige Eigenschaften) kann in AM-Teilen vorhanden sein, wird jedoch oft durch geeignete Parameter und Nachbearbeitung (wie HIP) minimiert. Die Ausrichtung kann die Festigkeit und Duktilität relativ zu den Hauptlastrichtungen beeinflussen.
- Anforderungen an die Unterstützung: Wie erwähnt, ist die Ausrichtung der Schlüssel zur Minimierung der Stützen.
- Bauzeit und Kosten: Höhere Ausrichtungen erhöhen im Allgemeinen die Bauzeit. Das Anbringen von mehr Teilen auf einer einzigen Bauplatte reduziert die Kosten pro Teil.
- Verformung: Die Ausrichtung beeinflusst Temperaturgradienten und das Potenzial für Verformungen.
- Bewährte Praxis: Verwenden Sie Simulationstools und Prozessexpertise (wie sie von Met3dp angeboten wird), um die optimale Ausrichtung zu bestimmen, die diese konkurrierenden Faktoren basierend auf den spezifischen Teilanforderungen ausgleicht.
- Abstriche: Die Ausrichtung der Instrumentenhalterung innerhalb der Baukammer hat erhebliche Auswirkungen auf mehrere Faktoren:
- Halten Sie sich an prozessspezifische Konstruktionsregeln:
- Mindestwanddicke: Teile benötigen eine ausreichende Dicke, um gehandhabt zu werden und zu funktionieren; zu dünne Merkmale können sich verziehen oder während des Druckens nicht richtig auflösen. Typische Mindestwerte liegen oft im Bereich von 0,4 mm – 1,0 mm, abhängig von Maschine, Material und Merkmalshöhe.
- Lochgrößen und -durchmesser: Kleine Löcher (z. B. < 0,5 mm) können sich während des Druckens verschließen oder nur schwer von Pulver befreien lassen. Die Vertikalität der Löcher beeinflusst die Rundheit.
- Aspekt-Verhältnisse: Hohe, dünne Wände sind anfällig für Verformungen oder Ausfälle während des Druckens.
- Eingeschlossene Volumina und Pulverentfernung: Vermeiden Sie die Konstruktion von geschlossenen Hohlquerschnitten, aus denen ungeschmolzenes Pulver nach dem Drucken nicht entfernt werden kann. Entwerfen Sie strategisch Fluchtlöcher.
- Maschinenlimits verstehen: Beachten Sie die spezifischen Bauvolumen-, Laser-/Strahlfleckgrößen- und Schichtdickenfähigkeiten des verwendeten AM-Systems.
- Funktionalität direkt integrieren:
- Denkweise der Teilekonsolidierung: Suchen Sie aktiv nach Möglichkeiten, mehrere traditionell getrennte Teile (Halterungen, Klemmen, Thermobänder, Gehäuse) in einer einzigen, multifunktionalen gedruckten Komponente zu kombinieren.
- Beispiele: Entwerfen Sie integrierte Kanäle für Kabelbäume, konforme Kühl-/Heizkanäle, die genau den Instrumentenkonturen folgen, eingebaute kinematische Befestigungsmerkmale für eine präzise Ausrichtung oder spezifische Oberflächenstrukturen für thermische Strahlungseigenschaften.
- Design für die Nachbearbeitung:
- Zulagen für die Bearbeitung: Wenn enge Toleranzen oder bestimmte Oberflächengüten für bestimmte Merkmale (z. B. Passflächen, Lagersitze) erforderlich sind, fügen Sie diesen Bereichen in der Designphase zusätzliches „Opfer“-Material (Bearbeitungszugabe, typischerweise 0,5-2 mm) hinzu. Dies stellt sicher, dass genügend Material für die Reinigung durch CNC-Bearbeitung nach dem Drucken und der Wärmebehandlung vorhanden ist.
- Unterstützung bei der Entfernung Zugang: Sorgen Sie für einen ausreichenden physischen und visuellen Zugang zum Entfernen von Stützstrukturen, insbesondere von internen. Vermeiden Sie Designs, bei denen Stützen effektiv eingeschlossen sind.
- Inspektionsmerkmale: Erwägen Sie das Hinzufügen von Bezugsmerkmalen oder Referenzpunkten, um die CMM-Inspektion später zu erleichtern.
Durch die sorgfältige Anwendung dieser regeln für die additive Fertigungkönnen Ingenieure das wahre Potenzial von Metall-AM freisetzen, um Instrumentenhalterungen für Raumfahrzeuge der nächsten Generation zu erstellen, die leichter, stärker, funktionaler und oft schneller herzustellen sind als ihre traditionell hergestellten Pendants. Die frühzeitige Zusammenarbeit mit erfahrenen AM-Dienstleistern wie Met3dp in der Designphase kann unschätzbares Feedback liefern und sicherstellen, dass Designs für eine erfolgreiche Produktion optimiert werden.
Erreichen von Präzision: Toleranz, Oberflächengüte und Maßgenauigkeit bei Metall-AM
Während die additive Metallfertigung eine beispiellose Designfreiheit bietet, betrifft eine häufige Frage von Ingenieuren und Beschaffungsmanagern, insbesondere von solchen, die an die Präzision der CNC-Bearbeitung gewöhnt sind, die erreichbaren Toleranzniveaus, die Oberflächengüte und die allgemeine Maßgenauigkeit. Das Verständnis der Fähigkeiten und Einschränkungen von Toleranzen beim 3D-Druck von Metall und Oberfläche ist entscheidend für die Festlegung realistischer Erwartungen und die Gewährleistung, dass Komponenten die strengen Anforderungen von Inspektion von Luft- und Raumfahrtkomponenten und Funktion erfüllen.
Maßgenauigkeit und Toleranzen:
- Allgemeine Fähigkeiten: Metall-Pulverbett-Fusionsprozesse (PBF) wie L-PBF und EBM können direkt aus der Maschine eine recht gute Maßgenauigkeit erzielen. Typische Toleranzen werden oft im Bereich von ±0,1 mm bis ±0,3 mm für kleinere Merkmale (z. B. bis zu 50-100 mm) angegeben, mit potenziell größeren Abweichungen (z. B. ±0,1 % bis ±0,2 % der Länge) für größere Abmessungen. Einige Anbieter können Toleranzen relativ zu Standards wie ISO 2768 (mittlere „m“- oder grobe „c“-Klassen) für allgemeine Abmessungen angeben, aber die spezifisch erreichbaren Toleranzen hängen stark von den folgenden Faktoren ab.
- Faktoren, die die Genauigkeit beeinflussen:
- Thermische Effekte: Das wiederholte Erhitzen und Abkühlen während des schichtweisen Prozesses induziert thermische Spannungen. Wenn sich das Teil abkühlt, können diese Spannungen zu Schrumpfung und Verformung führen, was zu Maßabweichungen führt. Dies ist eine primäre Herausforderung, die Maßhaltigkeit additive Fertigung.
- Geometrie und Größe des Teils: Größere Teile und komplexe Geometrien mit unterschiedlichen Querschnitten sind im Allgemeinen anfälliger für Verformungen. Hohe, dünne Merkmale sind ebenfalls eine Herausforderung.
- Material: Unterschiedliche Materialien haben unterschiedliche thermische Eigenschaften (Leitfähigkeit, Ausdehnung), die den Spannungsaufbau und die Schrumpfung beeinflussen.
- Strategie unterstützen: Die Art, Dichte und Position der Stützstrukturen wirken sich erheblich auf die Wärmeableitung und die Bauteilstabilität während des Baus aus und beeinflussen die endgültige Genauigkeit. Ungeeignete Stützen können die Verformung verschlimmern.
- Kalibrierung und Zustand der Maschine: Laser-/Strahlenausrichtung, Scannergenauigkeit, Pulverschichtkonsistenz und der allgemeine Zustand der Maschine sind entscheidend. Anbieter wie Met3dp legen Wert auf eine strenge Kalibrierung und Wartung ihrer branchenführenden Präzisionsdrucker.
- Orientierung aufbauen: Wie in DfAM besprochen, beeinflusst die Ausrichtung die thermische Historie und den Stützbedarf und damit die Genauigkeit.
- Nachbearbeiten: Wärmebehandlungen zur Spannungsarmglühen können geringfügige Maßänderungen verursachen. Die Entfernung der Stützen kann sich auch auf nahegelegene Oberflächen auswirken.
- Erzielung engerer Toleranzen: Für kritische Schnittstellen, Befestigungslöcher oder Merkmale, die engere Toleranzen als die Standard-AM-Prozessfähigkeit erfordern (z. B. enger als ±0,1 mm), ist in der Regel eine Nachbearbeitung durch CNC-Bearbeitung erforderlich. Dieser hybride Ansatz nutzt die Fähigkeit von AM, die komplexe Gesamtform effizient zu erstellen, und die Präzision der Bearbeitung für die Endbearbeitung kritischer Merkmale. Das Design mit geeigneten Bearbeitungszugaben (Materialvorrat) ist für diesen Arbeitsablauf unerlässlich.
Oberflächengüte (Rauhigkeit):
- As-Built Oberflächenbeschaffenheit: Die Oberflächengüte, typischerweise quantifiziert durch die durchschnittliche Rauheit (Ra), von direkt aus dem Metall-AM-Verfahren hergestellten Teilen ist im Allgemeinen rauer als bearbeitete Oberflächen.
- L-PBF: Erreicht typischerweise Ra-Werte im Bereich von 6 µm bis 15 µm (oder höher), abhängig von Material, Ausrichtung, Parametern und Oberflächenart (Up-Skin, Down-Skin, vertikal).
- EBM: Erzeugt im Allgemeinen rauere Oberflächen als L-PBF, oft mit Ra-Werten von 20 µm bis 40 µm oder mehr, aufgrund größerer Pulverpartikel und höherer Strahlenergie, die mehr Schmelzspritzer und teilweise gesinterte Partikel verursachen, die an Oberflächen haften.
- Faktoren, die die Oberflächenbeschaffenheit beeinflussen:
- Schichtdicke: Dünnere Schichten führen im Allgemeinen zu glatteren Oberflächen, insbesondere bei geneigten Merkmalen, erhöhen aber die Bauzeit.
- Pulver Partikelgröße: Feinere Pulver führen typischerweise zu glatteren Oberflächen. Der Fokus von Met3dp auf die Pulverqualität unter Verwendung fortschrittlicher Zerstäubung trägt zu besseren erreichbaren Oberflächen bei.
- Laser-/Strahlparameter: Energieeintrag, Scangeschwindigkeit und Strategie beeinflussen die Schmelzbaddynamik und die Oberflächenstruktur.
- Orientierung: Nach oben gerichtete Oberflächen und vertikale Wände neigen dazu, glatter zu sein als nach unten gerichtete Oberflächen (gestützt) oder stark geneigte Oberflächen, was auf den „Treppeneffekt“ zurückzuführen ist, der den schichtbasierten Prozessen innewohnt.
- Verbesserung der Oberflächengüte: Wenn ein glatteres oberflächenbehandlung Metall AM Teil erforderlich ist als das, was direkt hergestellt werden kann, werden verschiedene Nachbearbeitungstechniken eingesetzt:
- Abrasives Strahlen (Perlen-/Sandstrahlen): Bietet eine gleichmäßige matte Oberfläche, die effektiv zum Entfernen von teilweise gesinterten Partikeln ist, aber im Allgemeinen den Ra-Wert im Vergleich
- Taumeln/Gleitschleifen: Verwendet Schleifmittel in einer rotierenden oder vibrierenden Trommel, um Oberflächen und Kanten zu glätten, geeignet für Chargen kleinerer Teile.
- CNC-Bearbeitung: Bietet die beste Kontrolle, um glatte, präzise Oberflächen an bestimmten Merkmalen zu erzielen.
- Polieren (manuell oder automatisiert): Kann sehr niedrige Ra-Werte (Spiegelglanz) erzielen, ist aber oft arbeitsintensiv und in der Regel bestimmten funktionalen Anforderungen vorbehalten (z. B. optische Oberflächen, Dichtflächen).
- Elektropolieren: Ein elektrochemischer Prozess, der vorzugsweise Spitzen entfernt, die Oberfläche glättet und gleichzeitig die Reinigungsfähigkeit und Korrosionsbeständigkeit verbessert (gängig für Ti-6Al-4V).
- Abrasive Fließbearbeitung (AFM): Leitet Schleifkitt durch interne Kanäle oder über externe Oberflächen, um feine Oberflächen in schwer zugänglichen Bereichen zu erzielen.
Metrologie und Inspektion:
Angesichts der Prozessvariabilität und der Kritikalität von Raumfahrtkomponenten ist eine strenge Inspektion unabdingbar.
- Koordinatenmessmaschinen (KMG): Tastsonden liefern hochgenaue Dimensionsmessungen bestimmter Merkmale und Bezugspunkte. Unverzichtbar zur Überprüfung kritischer Toleranzen nach dem Drucken und der Nachbearbeitung.
- 3D-Scannen (Laser oder strukturiertes Licht): Erfasst die vollständige 3D-Geometrie des Teils und ermöglicht den Vergleich mit dem ursprünglichen CAD-Modell (geometrische Bemaßung und Tolerierung – GD&T-Analyse) und die Identifizierung von Gesamtverformungen oder Abweichungen über komplexe Oberflächen. Schneller als CMM für die Gesamtform, aber im Allgemeinen weniger genau für einzelne Funktionsmessungen.
- Computertomographie (CT) Scannen: Eine unschätzbare zerstörungsfreie Prüfmethode (ZfP) für AM-Teile. Röntgenstrahlen werden verwendet, um eine 3D-Rekonstruktion der inneren Struktur des Teils zu erstellen, was Folgendes ermöglicht:
- Überprüfung der internen Geometrie: Überprüfung komplexer interner Kanäle oder Merkmale.
- Erkennung von Porosität: Identifizierung und Quantifizierung interner Hohlräume oder mangelnder Verschmelzungsdefekte, die die strukturelle Integrität gefährden könnten.
- Dimensionsanalyse: Messung interner und externer Merkmale ohne Zerteilen des Teils.
- Messung der Oberflächenrauhigkeit: Stylus-Profilometer oder optische Profilometer werden verwendet, um den Ra-Wert oder andere Oberflächentexturparameter auf bestimmten Oberflächen zu quantifizieren.
Zusammenfassend lässt sich sagen, dass das Metall-AM zwar möglicherweise nicht die inhärente Mikron-Präzision der Bearbeitung über alle Merkmale direkt aus der Maschine erreicht, aber eine gute Basisgenauigkeit und -oberfläche bietet. Das Verständnis der Prozessfähigkeiten, die Anwendung von DfAM-Prinzipien und die Planung einer geeigneten Nachbearbeitung (Bearbeitung, Endbearbeitung) sowie eine strenge Inspektion ermöglichen es den Herstellern, die anspruchsvolle Präzision zuverlässig zu erreichen, die für flugkritische Instrumentenhalterungen für Raumfahrzeuge erforderlich ist. Die Zusammenarbeit mit sachkundigen Anbietern, die eine strenge Prozesskontrolle aufrechterhalten und eine umfassende Messtechnik anbieten, ist der Schlüssel zum Erfolg. Inspektion von Luft- und Raumfahrtkomponenten Erfolg.
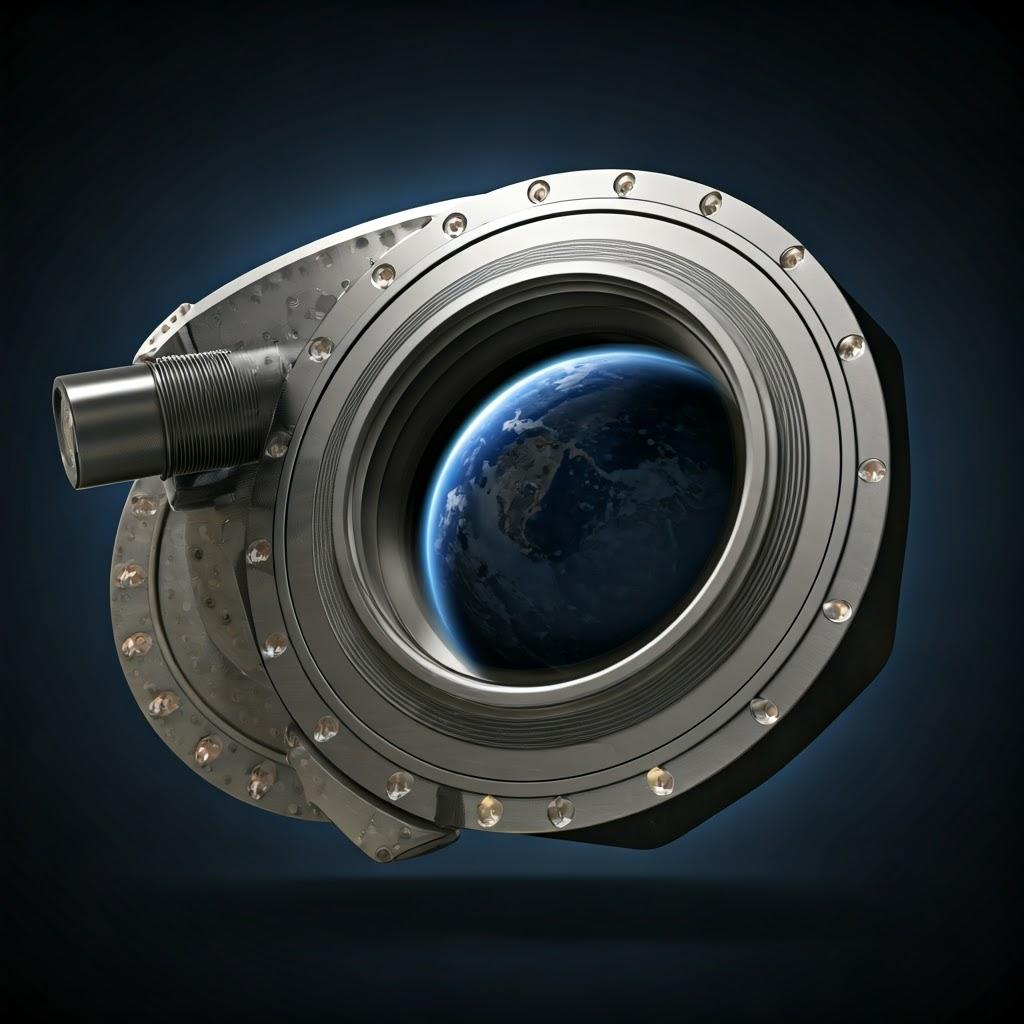
Nachbearbeitungspfade: Verfeinern von 3D-gedruckten Instrumentenhalterungen für den Flug
Die Herstellung eines Metallteils Schicht für Schicht durch additive Fertigung ist oft nur der erste große Schritt. Für anspruchsvolle Anwendungen wie Instrumentenhalterungen für Raumfahrzeuge, insbesondere für solche, die als flugkritisch gelten, sind in der Regel eine Reihe von Schritten erforderlich, um die gebaute Komponente in einen fertigen, flugfertigen Artikel umzuwandeln. Diese Schritte sind entscheidend, um innere Spannungen abzubauen, die Materialeigenschaften zu verbessern, endgültige Maßtoleranzen und Oberflächengüte zu erreichen, temporäre Strukturen zu entfernen und die Sauberkeit zu gewährleisten. Das Verständnis dieser Pfade ist für die Planung von Produktionszeitplänen und -kosten unerlässlich. Nachbearbeitung von Metall AM Das Verständnis dieser Pfade ist für die Planung von Produktionszeitplänen und -kosten unerlässlich.
Hier sind die gängigen Nachbearbeitungsschritte für 3D-gedruckte Scalmalloy®- und Ti-6Al-4V-Instrumentenhalterungen:
- Stressabbau Wärmebehandlung:
- Warum? Die schnellen Heiz- und Kühlzyklen, die den PBF-Prozessen innewohnen, erzeugen erhebliche Eigenspannungen innerhalb des gedruckten Teils. Diese Spannungen können während oder nach dem Bau zu Verformungen führen (insbesondere beim Entfernen von der Bauplatte) und die mechanischen Eigenschaften negativ beeinflussen (z. B. die Ermüdungslebensdauer verringern).
- Wie? Das Teil, oft noch an der Bauplatte befestigt, wird in einem Ofen mit kontrollierter Atmosphäre (Inertgas wie Argon für Titan, manchmal Luft oder Vakuum für Aluminium, je nach dem genauen Zyklus) auf eine bestimmte Temperatur unterhalb der Transformations- oder Alterungstemperaturen der Legierung erhitzt. Es wird für eine bestimmte Zeit (typischerweise 1-4 Stunden) auf dieser Temperatur gehalten und dann langsam abgekühlt. Dadurch können sich innere Spannungen entspannen, ohne die Mikrostruktur wesentlich zu verändern.
- Das Ergebnis: Verbesserte Dimensionsstabilität, geringeres Rissrisiko, Vorbereitung für nachfolgende Schritte wie HIP oder Bearbeitung. Dies ist fast immer der erste thermische Schritt in der additiven Fertigung. Wärmebehandlung additive Fertigung.
- Entfernen von der Bauplatte und Entfernen der Stützstruktur:
- Warum? Das Teil wird an einer dicken Metallplatte befestigt gebaut und verwendet Stützstrukturen zur Verankerung und für Überhänge. Diese müssen entfernt werden.
- Wie?
- Entfernen der Bauplatte: Typischerweise unter Verwendung von Draht-Funkenerosion (EDM) oder einer Bandsäge, um das Teil von der Grundplatte zu trennen.
- Unterstützung bei der Entfernung: Dies kann einer der arbeitsintensivsten Schritte sein, insbesondere bei komplexen Teilen oder starken Materialien wie Titan. Zu den Methoden gehören:
- Manuelles Brechen/Schneiden: Für leicht zugängliche, leichte Stützen.
- Bearbeitung (Fräsen/Schleifen): Für die Massenentfernung oder präzise Entfernung in der Nähe kritischer Oberflächen.
- Drahterodieren: Präzises Schneiden für schwer zugängliche Stützen.
- Spezialisierte Werkzeuge: Zangen, Meißel, Rotationswerkzeuge.
- Herausforderungen: Die Entfernung der Stützen kann die Oberfläche des Teils beschädigen, wenn sie nicht sorgfältig durchgeführt wird. Der Zugang zu internen Stützen kann sehr schwierig sein, was die Bedeutung von DfAM zur Minimierung derselben unterstreicht. Stützentfernung AM Kosten und Zeit sollten nicht unterschätzt werden.
- Heiß-Isostatisches Pressen (HIP):
- Warum? Während die Prozessoptimierung darauf abzielt, vollständig dichte Teile (>99,5 % Dichte) herzustellen, können manchmal mikroskopisch kleine innere Poren (aufgrund von eingeschlossenem Gas oder unvollständiger Verschmelzung) verbleiben. Diese Poren wirken als Spannungskonzentratoren und können die Ermüdungslebensdauer und die Bruchzähigkeit erheblich verringern, was für kritische Komponenten inakzeptabel ist.
- Wie? Die HIP-Prozess Metallteile beinhaltet das Aussetzen der Komponenten sowohl hohen Temperaturen (unter dem Schmelzpunkt) als auch hohem isostatischem Druck (typischerweise 100-200 MPa) unter Verwendung eines hochreinen Inertgases (normalerweise Argon) in einem speziellen Druckbehälter. Die Kombination aus Wärme und Druck bewirkt, dass sich das Material auf mikroskopischer Ebene plastisch verformt und kriecht, wodurch innere Hohlräume effektiv geschlossen und diffusionsgebunden werden.
- Das Ergebnis: Deutlich verbesserte Materialdichte (annähernd 100 %), erhöhte Ermüdungsfestigkeit, erhöhte Duktilität und Zähigkeit, reduzierte Streuung der Eigenschaften, was zu einem zuverlässigeren und vorhersehbaren Verhalten führt. Oft obligatorisch für flugkritische Ti-6Al-4V-Teile. Kann auch für Scalmalloy® in anspruchsvollen Anwendungen erforderlich sein.
- Weitere Wärmebehandlungen (Lösungsglühen & Auslagern):
- Warum? Um die endgültige gewünschte Mikrostruktur und die maximalen mechanischen Eigenschaften (Festigkeit, Härte) für bestimmte Legierungen wie Scalmalloy® und Ti-6Al-4V zu erreichen. Die gebaute oder HIP-Mikrostruktur ist möglicherweise nicht optimal.
- Wie?
- Lösungsglühen: Erhitzen der Legierung auf eine hohe Temperatur, um Ausscheidungen aufzulösen und eine homogene feste Lösung zu erzeugen, gefolgt von schnellem Abschrecken.
- Alterung (Ausscheidungshärtung): Erneutes Erhitzen des lösungsgeglühten Teils auf eine Zwischentemperatur für eine bestimmte Zeit, wodurch eine kontrollierte Ausscheidung feiner Sekundärphasen innerhalb der Metallmatrix ermöglicht wird. Diese Ausscheidungen behindern die Bewegung von Versetzungen und erhöhen die Festigkeit und Härte erheblich.
- Das Ergebnis: Maßgeschneiderte mechanische Eigenschaften, die den Konstruktionsspezifikationen entsprechen. Spezifische Temperaturen und Zeiten sind kritisch und legierungsabhängig.
- CNC-Bearbeitung:
- Warum? Um enge Toleranzen (typischerweise besser als ±0,1 mm), präzise geometrische Merkmale (z. B. Ebenheit, Rechtwinkligkeit) und glatte Oberflächengüten an kritischen Schnittstellen zu erreichen, die durch den AM-Prozess allein nicht erreicht werden können.
- Wie? Verwendung von Standard-CNC-Fräs-, Dreh- oder Schleifmaschinen, um den vorgegebenen Bearbeitungsaufmaß von bestimmten Oberflächen zu entfernen (z. B. Montageplatten, Schraubenlöcher, Passflächen, Lagerbohrungen). Ein sorgfältiges Vorrichtungsdesign ist erforderlich, um das potenziell komplexe AM-Teil sicher und ohne Verformung zu halten.
- Das Ergebnis: Endgültige Maßgenauigkeit und Oberflächengüte an kritischen Merkmalen, um eine ordnungsgemäße Montage und Funktion zu gewährleisten. CNC-Bearbeitung von 3D-Drucken ist ein gängiger hybrider Fertigungsansatz.
- Oberflächenveredelung:
- Warum? Um eine bestimmte Oberflächenrauheit (Ra), ein ästhetisches Erscheinungsbild zu erzielen oder die Oberfläche für Beschichtungen vorzubereiten.
- Wie? Wie bereits beschrieben: Kugelstrahlen, Trommeln, Polieren, Elektropolieren, AFM, je nach den Anforderungen und der Teilegeometrie. Die Auswahl hängt davon ab, ob eine gleichmäßige matte Oberfläche benötigt wird, ob bestimmte Ra-Werte eingehalten werden müssen oder ob sehr glatte Oberflächen aus Dichtungs- oder optischen Gründen erforderlich sind.
- Das Ergebnis: Gewünschte Oberflächenbeschaffenheit und Sauberkeit. Oberflächenveredelung in der Luft- und Raumfahrt erfordert oft bestimmte Verfahren und Kontrollen.
- Reinigung & Passivierung:
- Warum? Die Gewährleistung der Weltraumsauberkeit ist von größter Bedeutung, um das Ausgasen oder die Kontamination empfindlicher Instrumente oder Raumfahrzeugsysteme zu verhindern. Restöle, metallische Ablagerungen oder eingebettete Verunreinigungen müssen entfernt werden. Passivierung (insbesondere für Titan) verbessert die natürliche Schutzoxidschicht.
- Wie? Mehrstufige Reinigungsprozesse mit Detergentien, Lösungsmitteln, Ultraschallbädern und Spülungen mit hochreinem Wasser oder bestimmten Flüssigkeiten (z. B. Isopropylalkohol). Die Passivierung beinhaltet typischerweise die kontrollierte Exposition gegenüber bestimmten Säurelösungen (wie Salpetersäure für Ti). Die Verfahren müssen strenge Luft- und Raumfahrtstandards (z. B. NASA-Spezifikationen) einhalten.
- Das Ergebnis: Eine saubere, passivierte, flugfertige Oberfläche, die die Missionsanforderungen für erfüllt. Weltraumkomponentenreinigung.
Die spezifische Reihenfolge und Notwendigkeit dieser Nachbearbeitungsschritte hängen stark vom Material, den Anwendungsanforderungen (Kritikalität, Toleranzen, Belastungen) und dem gewählten AM-Prozess ab. Eine gründliche Planung und Koordination zwischen Konstrukteuren, dem AM-Dienstleister (wie Met3dp mit seinem umfassenden Lösungsansatz) und Nachbearbeitungsspezialisten ist unerlässlich, um diese Wege erfolgreich zu beschreiten und zuverlässige, hochleistungsfähige Instrumentenhalterungen für Raumfahrzeuge zu liefern.
Überwindung von Herausforderungen in der additiven Fertigung für Raumfahrtkomponenten
Während die additive Metallfertigung enorme Möglichkeiten für die Luft- und Raumfahrt bietet, insbesondere für komplexe Komponenten wie Instrumentenhalterungen, ist sie nicht ohne ihre Herausforderungen. Die erfolgreiche Implementierung von 3D-Druck von Metall flugkritischer Hardware erfordert ein tiefes Verständnis der potenziellen Fallstricke und robuster Strategien zu deren Minderung. Ingenieure und Beschaffungsmanager sollten sich dieser Hürden bewusst sein, wenn sie AM-Lösungen evaluieren und Fertigungspartner auswählen.
- Eigenspannung und Verformung:
- Herausforderung: Die intensive lokale Erwärmung durch den Laser oder Elektronenstrahl, gefolgt von raschem Abkühlen, erzeugt während des Baus steile Temperaturgradienten innerhalb des Teils. Dies führt zum Aufbau von inneren Eigenspannungen. Wenn diese Spannungen die Streckgrenze des Materials bei erhöhter Temperatur überschreiten, können sie dazu führen, dass sich das Teil während des Baus, beim Entfernen von der Bauplatte oder sogar während der Nachbearbeitung (wie z. B. der Bearbeitung) verzieht oder verformt. Eigenspannung AM ist ein Hauptanliegen.
- Milderung:
- Prozess-Simulation: Die Verwendung von Simulationssoftware zur Vorhersage des thermischen Verlaufs und der Spannungsakkumulation hilft bei der Optimierung der Bauausrichtung und der Stützstrategien vor dem Drucken.
- Optimierte Scan-Strategien: Techniken wie Inselscannen oder Schachbrettmuster können helfen, die Wärmeverteilung zu steuern.
- Build Plate Heating: Die Aufrechterhaltung einer erhöhten Temperatur in der Baukammer (insbesondere bei EBM üblich) reduziert die Temperaturgradienten.
- Robuste Stützstrukturen: Gut gestaltete Stützen verankern das Teil effektiv und helfen, Wärme abzuleiten.
- Stressabbau nach der Bauphase: Ein kritischer Wärmebehandlungsschritt, der unmittelbar nach dem Drucken durchgeführt wird, oft vor der Entfernung der Stützen, um innere Spannungen abzubauen.
- Änderungen am Design: Das Vermeiden großer, abrupter Querschnittsänderungen kann helfen.
- Kontrolle der Porosität:
- Herausforderung: Innere Hohlräume oder Poren innerhalb des gedruckten Materials können als Rissausgangsstellen wirken und die Ermüdungslebensdauer, die Duktilität und die allgemeine strukturelle Integrität erheblich verringern. Porosität ist einer der kritischsten Defekte bei der Pulverbettfusion. Pulverbettfusionsdefekte. Quellen umfassen:
- Gas Porosität: Eingeschlossenes Inertgas (aus der Bauatmosphäre) innerhalb des Schmelzbades.
- Lack-of-Fusion-Porosität: Unzureichender Energieeintrag oder falsche Strahl-/Laserüberlappung, was zu unvollständigem Schmelzen zwischen den Schichten oder benachbarten Scanbahnen führt.
- Fragen zur Pulverqualität: Hohle Pulverpartikel oder Verunreinigungen.
- Milderung:
- Optimierte Prozessparameter: Eine sorgfältige Entwicklung und Kontrolle der Laser-/Strahlleistung, der Scangeschwindigkeit, der Schichtdicke, des Schlupfabstands und der atmosphärischen Bedingungen sind von entscheidender Bedeutung. Fachwissen von Anbietern wie Met3dp bei der Parameterentwicklung ist der Schlüssel.
- Qualitätskontrolle des Pulvers: Verwendung hochwertiger, kugelförmiger Pulver mit geringem inneren Gasgehalt und gleichmäßiger Partikelgrößenverteilung, wie sie von den fortschrittlichen Zerstäubungssystemen von Met3dp hergestellt werden. Strenge Pulverhandhabungsprotokolle sind unerlässlich.
- Heiß-Isostatisches Pressen (HIP): Sehr effektiv beim Schließen interner Poren (sowohl Gas- als auch Nicht-Verschmelzungsarten) durch hohe Temperatur und Druck, wodurch die Dichte und die mechanischen Eigenschaften erheblich verbessert werden. Oft obligatorisch für kritische Teile.
- Zerstörungsfreie Prüfung (NDT): Die Verwendung von CT-Scans zur Erkennung und Quantifizierung der inneren Porosität ist für die Qualitätssicherung unerlässlich.
- Herausforderung: Innere Hohlräume oder Poren innerhalb des gedruckten Materials können als Rissausgangsstellen wirken und die Ermüdungslebensdauer, die Duktilität und die allgemeine strukturelle Integrität erheblich verringern. Porosität ist einer der kritischsten Defekte bei der Pulverbettfusion. Pulverbettfusionsdefekte. Quellen umfassen:
- Pulvermanagement, Handhabung und Rückverfolgbarkeit:
- Herausforderung: Metall
- Milderung:
- Kontrollierte Umgebungen: Handhabung von Pulvern in Inertgas-Handschuhkästen oder speziellen Reinräumen.
- Strenge Protokolle: Dokumentierte Verfahren für das Laden/Entladen, Sieben, Lagern und Recyceln von Pulvern.
- Charakterisierung des Pulvers: Regelmäßige Prüfung der Pulvereigenschaften (PSD, Morphologie, Chemie, Fließfähigkeit). Das Fachwissen von Met3dp beginnt mit seinem fortschrittliches Pulverherstellungssystem.
- Dedizierte Ausrüstung: Vermeidung von Kreuzkontaminationen durch den Einsatz spezieller Maschinen oder rigoroser Reinigungsverfahren zwischen verschiedenen Materialien.
- Chargenverfolgung: Implementierung robuster Systeme zur Verfolgung von Pulverchargen während des gesamten Herstellungsprozesses. Metallpulver-Handhabung in der Luft- und Raumfahrt Standards sind streng.
- Konsistenz und Wiederholbarkeit der Materialeigenschaften:
- Herausforderung: Die Gewährleistung, dass die mechanischen Eigenschaften (Festigkeit, Duktilität, Lebensdauer) innerhalb eines einzelnen Teils, von Teil zu Teil innerhalb eines Aufbaus und von Aufbau zu Aufbau im Laufe der Zeit konsistent sind, kann aufgrund der Empfindlichkeit von AM-Prozessen gegenüber zahlreichen Variablen eine Herausforderung darstellen.
- Milderung:
- Prozessüberwachung & Steuerung: Verwendung von In-situ-Überwachungswerkzeugen (Schmelzbadüberwachung, Wärmebildgebung) und enge Kontrolle aller Prozessparameter (Laserleistung, Gasfluss, Temperatur usw.).
- Kalibrierung der Maschine: Regelmäßige und gründliche Kalibrierung von AM-Systemen.
- Standardisierte Verfahren: Betrieb gemäß gut dokumentierten und validierten Verfahren.
- Konsistenter Ausgangsstoff: Verwendung von Pulvern mit gleichbleibender Qualität und Eigenschaften von Charge zu Charge.
- Gutscheine bezeugen: Einschluss von Testproben (Zeugen-Coupons) in die Aufbauten, die dann zerstörend geprüft werden, um die in diesem spezifischen Bauzyklus erreichten mechanischen Eigenschaften zu überprüfen.
- Qualifizierung und Zertifizierung:
- Herausforderung: Die additive Fertigung ist im Vergleich zu herkömmlichen Verfahren wie Schmieden oder Zerspanen noch relativ neu. Die Etablierung der notwendigen Prozessreife, Wiederholbarkeit und Dokumentation zur Erfüllung der strengen Qualifizierungs- und Zertifizierungsanforderungen der Luft- und Raumfahrt (z. B. AS9100 additive Fertigung Standards, spezifische NASA/ESA/FAA-Anforderungen) ist ein erhebliches Unterfangen. Der Nachweis der Gleichwertigkeit oder Überlegenheit gegenüber älteren Verfahren erfordert oft umfangreiche Tests und Analysen.
- Milderung:
- Entwicklung von Prozessspezifikationen: Erstellung detaillierter Spezifikationen, die alle Aspekte des Herstellungsprozesses definieren, von der Pulverhandhabung bis zur Endprüfung.
- Statistische Prozesskontrolle (SPC): Implementierung von SPC zur Überwachung der Prozessstabilität und -fähigkeit.
- Umfassende Tests: Durchführung einer umfassenden Materialcharakterisierung (statische, dynamische, Ermüdungsprüfung) an Teilen, die im Rahmen des definierten Prozesses hergestellt wurden.
- Robustes Qualitätsmanagementsystem (QMS): Betrieb unter einem zertifizierten QMS wie AS9100.
- Kollaboration: Enge Zusammenarbeit mit Zertifizierungsstellen und Kunden während des gesamten Qualifizierungsprozesses. AM-Prozessqualifizierung ist oft eine gemeinsame Anstrengung.
Die Bewältigung dieser Herausforderungen erfordert erhebliche Investitionen in Technologie, Prozesskontrolle, materialwissenschaftliches Fachwissen, rigoroses Qualitätsmanagement und qualifiziertes Personal. Die Partnerschaft mit einem erfahrenen und kompetenten Metall-AM-Anbieter wie Met3dp, der über fundiertes Fachwissen in Materialien, Prozessen wie SEBM, Pulverherstellung und Qualitätssicherung verfügt, ist entscheidend, um diese Komplexitäten erfolgreich zu bewältigen und die vollen Vorteile der additiven Fertigung für anspruchsvolle Raumfahrtanwendungen zu realisieren.
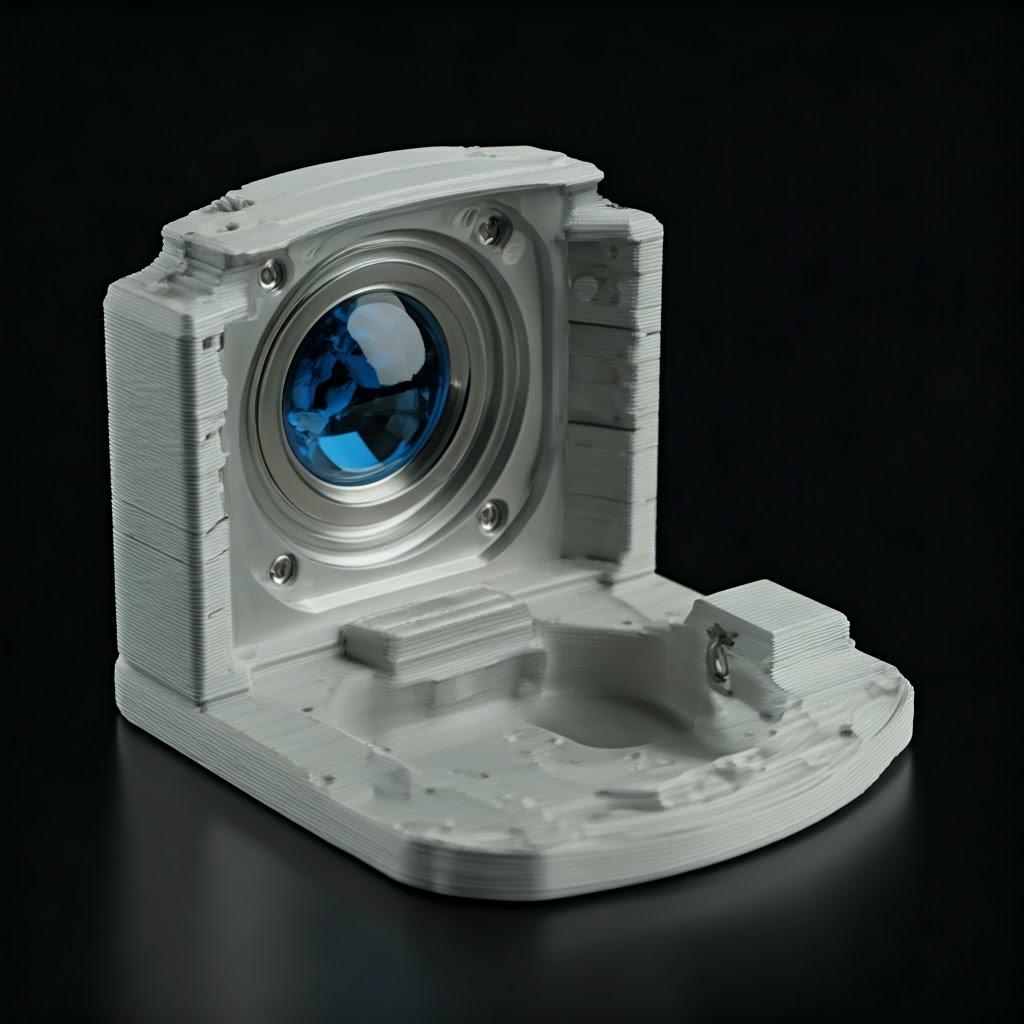
Auswahl Ihres Metall-Additive-Manufacturing-Partners für Weltraumkomponenten
Die Wahl des richtigen Fertigungspartners ist wohl eine der wichtigsten Entscheidungen bei der Implementierung der Metall-Additiven Fertigung für anspruchsvolle Anwendungen wie Weltrauminstrumentenhalterungen. Der Unterschied zwischen Erfolg und Misserfolg hängt oft vom Fachwissen, den Fähigkeiten, den Qualitätssystemen und dem kollaborativen Ansatz des Partners ab. Dies ist nicht nur ein Transaktionskauf; es ist die Auswahl eines Partners, der in die Lieferung von flugfähiger Hardware investiert. Für Beschaffungsmanager und leitende Ingenieure, die metall-AM-Dienstleister für die Luft- und Raumfahrt Optionen evaluieren, ist ein strukturierter Bewertungsprozess, der sich auf bestimmte Kriterien konzentriert, unerlässlich.
Hier ist eine Checkliste mit Schlüsselfaktoren, die bei der Auswahl Ihres Lieferanten für den 3D-Druck in der Luft- und Raumfahrt:
- Nachweisliche Erfahrung und Erfolgsbilanz in der Luft- und Raumfahrt:
- Nachgewiesener Erfolg: Hat der Anbieter erfolgreich Komponenten für ähnliche Luft- und Raumfahrt- oder Verteidigungsanwendungen hergestellt? Kann er relevante (nicht-proprietäre) Fallstudien oder Beispiele weitergeben?
- Branchenverständnis: Versteht er die besonderen Anforderungen, Standards und Herausforderungen der Raumfahrtindustrie (z. B. Umweltbedingungen, Zuverlässigkeitsanforderungen, Sauberkeitsstandards)?
- ITAR-Konformität (falls zutreffend): Wenn Sie mit verteidigungsbezogenen Projekten zu tun haben, die den US International Traffic in Arms Regulations unterliegen, stellen Sie sicher, dass der Anbieter ITAR-registriert und konform ist.
- Qualitätsmanagementsystem und Zertifizierungen:
- AS9100-Zertifizierung: Dies ist die Standard-QMS-Anforderung für die Luftfahrt-, Raumfahrt- und Verteidigungsindustrie. Suchen Sie nach AS9100 zertifizierte AM Anbieter. Dies zeigt ein Engagement für strenge Prozesskontrolle, Rückverfolgbarkeit, Risikomanagement und kontinuierliche Verbesserung, die auf die Erwartungen der Luft- und Raumfahrt abgestimmt sind.
- Robustes QMS: Bewerten Sie auch über AS9100 hinaus die Reife und Implementierung ihres gesamten Qualitätsmanagementsystems. Wie gehen sie mit Nonkonformitäten, Korrekturmaßnahmen, Dokumentenkontrolle und Konfigurationsmanagement um?
- Rückverfolgbarkeit von Materialien: Können sie die vollständige Rückverfolgbarkeit für Metallpulver nachweisen, von der ersten Pulverchargenzertifizierung über die Verarbeitung, das Recycling (falls verwendet) bis hin zur Verknüpfung mit der Seriennummer des fertigen Teils?
- Materialkenntnis und Handhabung:
- Spezifische Legierungserfahrung: Verfügen sie über fundierte Erfahrung in der Verarbeitung der spezifischen Legierungen, die benötigt werden (z. B. Scalmalloy-Druckservice, Ti-6Al-4V-Druckservice)? Dies umfasst validierte Parametersätze, das Verständnis der Mikrostrukturentwicklung und das entsprechende Wissen über die Nachbearbeitung.
- Pulverqualität & -management: Wie sehen ihre Verfahren für die Eingangsprüfung, Lagerung, Handhabung (insbesondere für reaktive Metalle), Siebung/Recycling und die Vermeidung von Kreuzkontaminationen aus? Beziehen sie hochwertige Pulver oder produzieren sie, wie Met3dp, ihre eigenen mit fortschrittlichen Techniken?
- Breiteres Materialportfolio: Auch wenn Sie jetzt bestimmte Legierungen benötigen, arbeitet der Anbieter mit einer Reihe relevanter Luft- und Raumfahrtmaterialien (z. B. Inconel, andere Titansorten, Edelstähle)? Dies deutet auf ein breiteres Fachwissen hin. Met3dp beispielsweise stellt Pulver wie TiNi, TiTa, TiAl, TiNbZr, CoCrMo, Edelstähle und Superlegierungen her.
- Technische Fähigkeiten und Ausrüstung:
- Prozessexpertise (L-PBF, EBM usw.): Verfügen sie über die richtige AM-Technologie (z. B. Laser Powder Bed Fusion, Electron Beam Melting), die für Ihr Material und Ihre Anwendung geeignet ist? Beherrschen sie die Prozessparameter?
- Maschinenqualität und Kalibrierung: Sind ihre AM-Maschinen gut gewartet, regelmäßig kalibriert und für die Herstellung hochwertiger Luft- und Raumfahrtteile geeignet? Wie ist der Zustand und das Alter ihrer Flotte? Met3dp ist stolz auf Drucker, die liefern branchenführendes Druckvolumen, Genauigkeit und Zuverlässigkeit.
- Bauvolumen: Können ihre Maschinen die Größe Ihrer Instrumentenhalterung aufnehmen?
- Umweltkontrollen: Werden die Baukammern richtig kontrolliert (Inertgasatmosphäre, Temperatur), um die Materialintegrität zu gewährleisten?
- Technische und DfAM-Unterstützung:
- Kollaborativer Ansatz: Sind sie bereit und in der Lage, mit Ihrem Designteam zusammenzuarbeiten? Können sie Experten-DfAM-Feedback geben, um das Design auf Druckbarkeit, Leistung und Wirtschaftlichkeit zu optimieren?
- Simulationsfähigkeiten: Verwenden sie Prozesssimulationstools, um potenzielle Probleme wie Verformungen vorherzusagen und zu mindern?
- Problemlösungskompetenz: Wie gehen sie bei der Entwicklung oder Produktion mit technischen Herausforderungen um?
- Nachbearbeitungsmöglichkeiten:
- In-House vs. Outsourced: Bieten sie wichtige Nachbearbeitungsschritte (Spannungsarmglühen, HIP, Bearbeitung, Endbearbeitung, Reinigung) im eigenen Haus an oder verwalten sie ein Netzwerk qualifizierter Subunternehmer? Eigene Kapazitäten straffen oft den Arbeitsablauf und verbessern die Qualitätskontrolle.
- Qualität der Nachbearbeitung: Stellen Sie sicher, dass ihre Nachbearbeitungsverfahren den Luft- und Raumfahrtstandards entsprechen, insbesondere für die Wärmebehandlung (kalibrierte Öfen, geeignete Atmosphären) und die CNC-Bearbeitung (geeignete Maschinen, erfahrene Zerspaner).
- Inspektion und Metrologie:
- Umfassende Fähigkeiten: Verfügen sie über die notwendige Ausrüstung (CMM, 3D-Scanner, Oberflächenprofilometer) und das Fachwissen für eine gründliche Dimensionsprüfung gemäß Ihren Zeichnungen und GD&T-Anforderungen?
- NDT-Fähigkeiten: Können sie vor allem erforderliche zerstörungsfreie Prüfungen durchführen oder verwalten, insbesondere CT-Scans zur Erkennung interner Defekte in kritischen AM-Teilen?
- Kapazität, Vorlaufzeit und Kommunikation:
- Produktionskapazität: Können sie Ihr erforderliches Volumen bewältigen und Ihre Projektzeitpläne einhalten? Wie sind ihre typischen Vorlaufzeiten?
- Reaktionsfähigkeit & Kommunikation: Reagieren sie auf Anfragen und sind sie während des gesamten Projektlebenszyklus transparent in ihrer Kommunikation? Wer ist Ihr primärer Ansprechpartner?
- Wettbewerbsfähigkeit bei den Kosten:
- Wert-Angebot: Auch wenn die Kosten immer ein Faktor sind, bewerten Sie sie im Kontext des Fachwissens, der Qualität, der Fähigkeiten und des Gesamtangebots des Anbieters, nicht nur des niedrigsten Preises. Ein billigeres Teil, das die Qualifizierung oder den Betrieb nicht besteht, ist unendlich teurer.
Wahl des AM-Partners geht es darum, Vertrauen aufzubauen und die Leistungsfähigkeit sicherzustellen. Suchen Sie nach Beweisen, die die Behauptungen in jedem dieser Bereiche untermauern. Standortaudits, Referenzprüfungen und Pilotprojekte können wertvolle Schritte im Auswahlprozess sein. Unternehmen wie Met3dp, mit jahrzehntelanger gemeinsamer Erfahrung und Umfassende Lösungen von Met3dp die fortschrittliche SEBM-Drucker, Hochleistungs-Metallpulver, die im eigenen Haus durch Gasverdüsung und PREP hergestellt werden, und dedizierte Anwendungsentwicklungsdienste umfassen, stellen die Art von vertikal integriertem und sachkundigem Partner dar, der für den Erfolg in der anspruchsvollen additiven Fertigung in der Luft- und Raumfahrt benötigt wird.
Verstehen der Kostentreiber und Vorlaufzeiten für 3D-gedruckte Halterungen
Während die Metall-Additive Fertigung erhebliche Leistungs- und Designvorteile bietet, ist das Verständnis der Faktoren, die die Kosten und die Vorlaufzeit beeinflussen, entscheidend für die Projektplanung, Budgetierung und den Vergleich mit herkömmlichen Fertigungsmethoden. Beide Kostenanalyse für den 3D-Druck von Metall und realistisch AM-Vorlaufzeit Schätzung erfordert die Berücksichtigung mehrerer Elemente, die über das Rohmaterial hinausgehen.
Die wichtigsten Kostentreiber bei Metal AM:
- Materialkosten:
- Pulver Preis: Die Kosten pro Kilogramm Metallpulver in Luft- und Raumfahrtqualität sind ein wesentlicher Faktor. Materialien wie Scalmalloy-Kosten (aufgrund von Scandium) und Ti-6Al-4V-Kosten sind deutlich höher als herkömmliche Aluminium- oder Stahllegierungen. Die Preise können je nach Lieferant, Pulverqualität (z. B. Kugelform, Reinheit, PSD) und gekaufter Menge variieren.
- Pulververbrauch & Recycling: Während AM oft nahezu endkonturnah ist, wird ein Teil des Pulvers durch Stützen verbraucht, und ein Teil kann nicht vollständig zurückgewonnen oder unbegrenzt wiederverwendet werden. Effektive Pulverrecyclingstrategien, die vom AM-Anbieter eingesetzt werden, können dazu beitragen, die Kosten zu senken, aber eine strenge Qualitätskontrolle des recycelten Pulvers ist unerlässlich. Buy-to-Fly-Verhältnisse sind im Allgemeinen viel besser als bei der Bearbeitung komplexer Teile, aber nicht zu vernachlässigen.
- Maschinenauslastung (Druckzeit):
- Maschine Stundensatz: AM-Maschinen stellen erhebliche Kapitalinvestitionen dar und haben Betriebskosten (Strom, Inertgas, Wartung). Anbieter berechnen in der Regel auf der Grundlage der Zeit, die die Maschine mit dem Drucken des Teils beschäftigt ist.
- Bauhöhe & Volumen: Die Bauzeit wird in erster Linie durch die Höhe des Teils (Anzahl der Schichten) bestimmt, aber auch durch das zu scannende Volumen/die zu scannende Fläche pro Schicht beeinflusst. Höhere Teile dauern länger.
- Teildichte & Komplexität: Feste, dichte Teile benötigen mehr Zeit zum Scannen als solche, die eine erhebliche Gewichtsreduzierung (z. B. Gitter) beinhalten. Hochkomplexe Geometrien erfordern möglicherweise langsamere Scangeschwindigkeiten für bestimmte Merkmale.
- Anzahl der Laser/Strahlen: Mehrfachlaser-/Strahlmaschinen können Schichten schneller verarbeiten, wodurch sich die Druckzeit für größere Teile oder mehrere Teile pro Aufbau potenziell verkürzt.
- Schichtdicke: Dünnere Schichten verbessern die Auflösung und Oberflächengüte an Hängen, erhöhen aber die Gesamtzahl der Schichten und damit die Druckzeit.
- Konstruktions- und Designaufwand:
- DfAM und Optimierung: Die Zeit, die Ingenieure mit der Optimierung des Designs für die additive Fertigung verbringen (Topologieoptimierung, Gittergenerierung, Stützstrategie), trägt zu den Gesamtkosten bei, insbesondere bei neuartigen oder hochkomplexen Teilen.
- Bauvorbereitung & Simulation: Das Einrichten der Bauakte, die Bestimmung der optimalen Ausrichtung, die Generierung von Stützstrukturen und möglicherweise die Durchführung von Prozesssimulationen erhöhen die anfänglichen Konstruktionskosten.
- Komplexität und Arbeitsaufwand der Nachbearbeitung:
- Unterstützung bei der Entfernung: Arbeitsintensiv, insbesondere bei komplexen Teilen oder zähen Materialien. Kann qualifizierte Techniker und Spezialwerkzeuge (z. B. EDM) erfordern.
- Wärmebehandlung (Spannungsarmglühen, HIP, Alterung): Erfordert Ofenzeit, Energie, kontrollierte Atmosphären und den damit verbundenen Arbeitsaufwand. HIP ist ein besonders spezialisiertes und kostspieliges Verfahren.
- CNC-Bearbeitung: Die Kosten hängen von der Menge des zu entfernenden Materials, der Anzahl der zu bearbeitenden Merkmale, den erforderlichen Toleranzen und den CNC-Maschinenzeiten/-Arbeitskosten ab.
- Oberflächenveredelung: Die Kosten variieren erheblich je nach Methode (Strahlen ist relativ billig, umfangreiches Polieren ist teuer) und dem erforderlichen endgültigen Ra-Wert.
- Reinigung und Inspektion: Arbeits- und Gerätezeit für strenge Reinigungsprotokolle, CMM-Messungen, 3D-Scannen, ZfP (insbesondere CT-Scannen) und Dokumentation erhöhen die Kosten.
- Qualifizierung & Prüfung:
- NDT-Kosten: CT-Scannen, FPI
- Zerstörende Prüfung: Wenn Zeugenmuster oder Probeteile im Rahmen des Qualifizierungsprozesses zerstörende Tests (Zug-, Ermüdungs-, Metallografie) erfordern, müssen diese Laborkosten berücksichtigt werden.
- Menge & Chargengröße:
- Skalenvorteile: Der Aufbau einer Fertigung beinhaltet fixe Gemeinkosten. Das Drucken mehrerer Teile in einem einzigen Bauvorgang (sofern Geometrie und Bauvolumen dies zulassen) verteilt diese Einrichtungskosten und reduziert die kosten pro Teil 3D-Druck. Größere Produktionsläufe ermöglichen im Allgemeinen eine höhere Effizienz und potenziell niedrigere Kosten pro Teil im Vergleich zu Einzelprototypen, obwohl AM auch für Einzelstücke im Vergleich zu werkzeugintensiven traditionellen Methoden kosteneffektiv ist. Großhandelspreise für 3D-Druck Anfragen sollten die erwarteten Mengen angeben.
Typische Vorlaufzeiten:
Einer der wichtigsten Vorteile von AM ist oft die Geschwindigkeit, insbesondere im Vergleich zu Verfahren, die Werkzeuge (Gießen, Schmieden) oder umfangreiche Bearbeitungseinrichtungen für komplexe Teile erfordern.
- AM-Prozess: Der Druck selbst kann je nach Größe der Teile von einigen Stunden bis zu mehreren Tagen oder sogar einer Woche+ für sehr große, komplexe Komponenten oder volle Bauplatten dauern.
- Nachbearbeiten: Dies macht oft einen erheblichen Teil der gesamten Vorlaufzeit aus. Wärmebehandlungen dauern Zeit (einschließlich kontrollierter Abkühlzyklen). Die Entfernung von Stützstrukturen und die Bearbeitung können je nach Komplexität zeitaufwändig sein. HIP erfordert eine Terminplanung mit spezialisierten Einrichtungen, falls diese nicht im eigenen Haus verfügbar sind.
- Insgesamt:
- Prototypen/Einfache Teile: Vorlaufzeiten von 1-3 Wochen sind oft erreichbar.
- Komplexe/Serienteile: Einschließlich vollständiger Nachbearbeitung und Inspektion sind Vorlaufzeiten von 4-8 Wochen für qualifizierte Luft- und Raumfahrtkomponenten üblich. Dies ist oft immer noch deutlich schneller als die Monate, die möglicherweise für traditionelle Fertigungsverfahren erforderlich sind, die die Beschaffung von Werkzeugen oder komplexe Lieferketten umfassen.
- Faktoren, die die Vorlaufzeit beeinflussen: Teilekomplexität, Materialauswahl, die spezifischen erforderlichen Nachbearbeitungsschritte, die Maschinenverfügbarkeit (Wartezeiten beim Anbieter), die Testanforderungen und die Dokumentationsanforderungen wirken sich alle auf den endgültigen Lieferplan aus.
Eine klare Kommunikation mit dem AM-Anbieter bezüglich aller Anforderungen (Toleranzen, Oberfläche, Prüfung, Standards) ist unerlässlich, um genaue Preisgestaltung bei der additiven Fertigung und realistische Vorlaufzeitschätzungen zu erhalten.
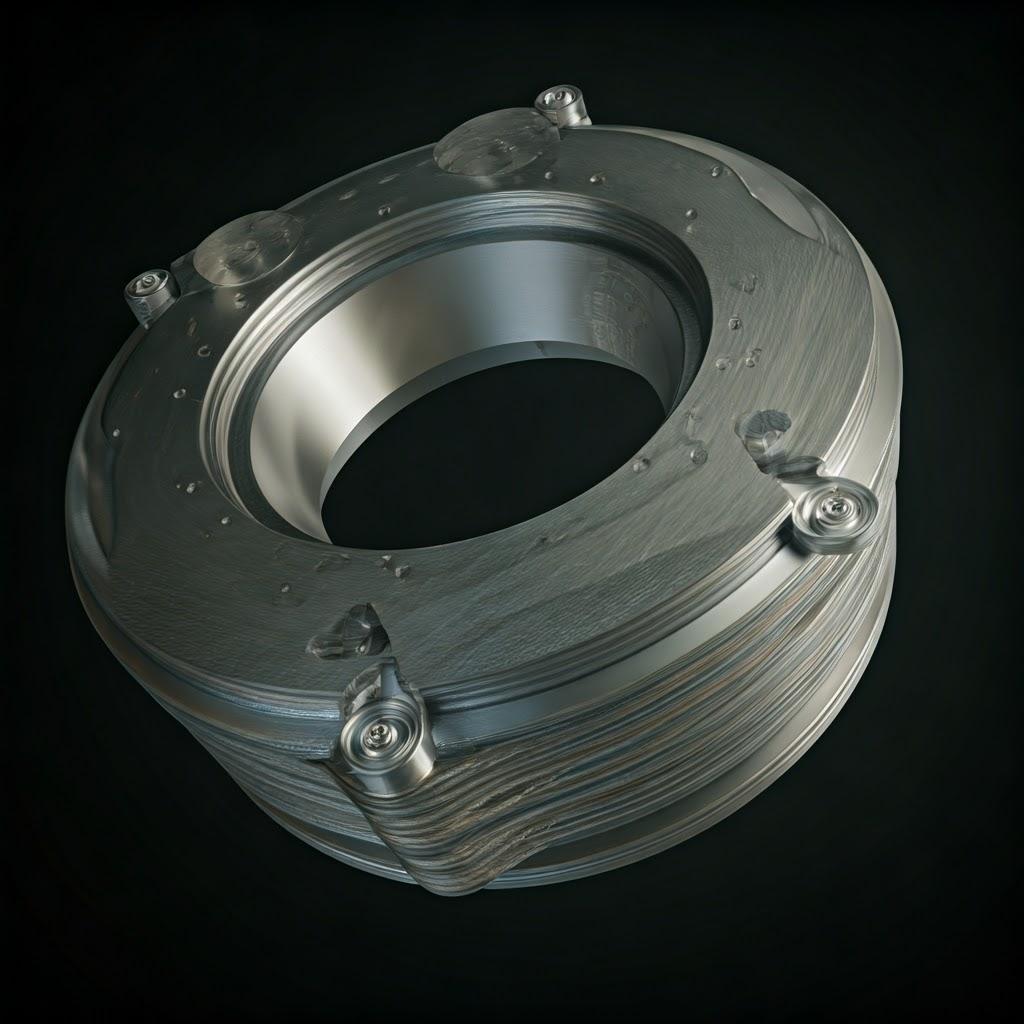
Häufig gestellte Fragen (FAQ)
Hier sind Antworten auf einige häufige Fragen, die Ingenieure und Einkaufsmanager zur Verwendung der additiven Metallfertigung für Instrumentenhalterungen für Raumfahrzeuge haben:
- F1: Welche Gewichtseinsparungen können für Instrumentenhalterungen mit AM im Vergleich zur herkömmlichen Bearbeitung realistisch erzielt werden?
- A: Oft sind erhebliche Gewichtseinsparungen erreichbar, typischerweise im Bereich von 20 % bis 50 %und manchmal sogar noch mehr. Die genauen Einsparungen hängen stark vom ursprünglichen Design, den funktionalen Anforderungen und dem Ausmaß ab, in dem DfAM-Prinzipien wie Topologieoptimierung und Gitterstrukturen eingesetzt werden. Bei Komponenten, die zuvor nicht auf Gewicht optimiert wurden, sind die potenziellen Einsparungen oft erheblich, was sich direkt auf die Startkosten auswirkt und möglicherweise eine erhöhte Nutzlastkapazität ermöglicht.
- F2: Wie verhalten sich die strukturelle Integrität und die Ermüdungslebensdauer von 3D-gedrucktem Scalmalloy® oder Ti-6Al-4V im Vergleich zu geschmiedeten oder gegossenen Gegenstücken?
- A: Bei der Herstellung unter Verwendung optimierter Prozessparameter und geeigneter Nachbearbeitung (insbesondere Spannungsarmglühen und HIP) können die mechanischen Eigenschaften von AM-Scalmalloy® und Ti-6Al-4V die von traditionellen Gusswerkstoffen erfüllen oder sogar übertreffen und sich oft den geschmiedeten Eigenschaften annähern oder entsprechen, insbesondere in Bezug auf die spezifische Festigkeit (Festigkeits-Gewichts-Verhältnis). HIP ist entscheidend für die Reduzierung der inneren Porosität, was zu Ermüdungseigenschaften führt, die oft mit geschmiedetem Material vergleichbar sind, wodurch sie für anspruchsvolle, zyklisch belastete Luft- und Raumfahrtanwendungen geeignet sind. Die Eigenschaften können jedoch anisotrop (richtungsabhängig) sein, was eine sorgfältige Berücksichtigung bei der Konstruktion und Qualifizierungstests erfordert.
- F3: Welche kritischen Qualitätskontroll- und Inspektionsschritte sind für flugkritische 3D-gedruckte Teile erforderlich?
- A: Qualitätskontrolle ist von größter Bedeutung. Zu den wichtigsten Schritten gehören in der Regel:
- Zertifizierung der Pulvercharge: Überprüfung der Chemie, PSD und Morphologie des eingehenden Metallpulvers.
- Prozessüberwachung: In-situ-Überwachung des Bauprozesses, sofern verfügbar.
- Inspektion nach der Fertigstellung: Sichtprüfung, Maßkontrollen (CMM, 3D-Scannen) gemäß GD&T-Anforderungen.
- Zerstörungsfreie Prüfung (NDT): Entscheidend ist, CT-Abtastung ist oft erforderlich, um die innere Festigkeit sicherzustellen und Defekte wie Porosität oder mangelnde Verschmelzung zu erkennen. Verfahren zur Oberflächenrisserkennung wie FPI können auch nach der Bearbeitung verwendet werden.
- Materialprüfung: Zerstörende Tests (Zug-, Ermüdungs-, Härte-, Metallografie), die an Zeugenmustern durchgeführt werden, die parallel zu den Teilen gebaut wurden, um die Materialeigenschaften zu überprüfen, die in diesem spezifischen Bauzyklus erreicht wurden.
- Dokumentation: Eine strenge Dokumentation, in der Materialien, Prozesse, Inspektionen und Testergebnisse erfasst werden, ist für die Flugzertifizierung unerlässlich.
- A: Qualitätskontrolle ist von größter Bedeutung. Zu den wichtigsten Schritten gehören in der Regel:
- F4: Können komplexe interne Kanäle für Wärmemanagement oder Flüssigkeitsfluss direkt in die 3D-gedruckte Halterung integriert werden?
- A: Ja, absolut. Dies ist einer der größten Vorteile der additiven Fertigung. AM ermöglicht die Erstellung komplizierter interner Durchgänge und konforme Kühl-/Heizkanäle , die den Konturen des Instruments oder der Wärmequelle präzise folgen. Diese Geometrien sind mit herkömmlichen Methoden wie Bohren oder Bearbeiten oft unmöglich oder unerschwinglich herzustellen. Dies ermöglicht hocheffiziente Wärmemanagementlösungen, die direkt in die Strukturhalterung integriert sind, wodurch Gewicht gespart und die Leistung verbessert wird. Eine sorgfältige Konstruktion (DfAM) ist erforderlich, um die Pulverentfernung aus diesen Kanälen sicherzustellen.
- F5: Welche Informationen benötigt ein Metall-3D-Druckdienstleister wie Met3dp , um ein genaues Angebot für eine Instrumentenhalterung zu erstellen?
- A: Um ein genaues Angebot und eine Machbarkeitsbewertung zu erstellen, benötigt der Anbieter in der Regel:
- 3D-CAD-Modell: Vorzugsweise im STEP-Format (.stp/.step). Native CAD-Dateien oder Netzdateien (STL) können manchmal verwendet werden, aber STEP wird im Allgemeinen für die Abfrage bevorzugt.
- Spezifikation des Materials: Eindeutig definierte Legierung (z. B. Ti-6Al-4V Grade 5, Scalmalloy®) und alle spezifischen Materialstandards (z. B. ASTM, AMS).
- 2D-Zeichnungen (falls zutreffend): Unverzichtbar, wenn spezifische geometrische Bemaßung und Tolerierung (GD&T), kritische Toleranzen, Oberflächengüteanforderungen oder Inspektionskriterien definiert sind, die nicht vollständig im 3D-Modell erfasst werden.
- Erforderliche Toleranzen: Angabe allgemeiner Toleranzen und Hervorhebung aller kritischen Abmessungen, die eine engere Kontrolle erfordern (was eine Nachbearbeitung implizieren kann).
- Anforderungen an die Oberflächenbeschaffenheit: Geben Sie die erforderlichen Ra-Werte oder Oberflächenbehandlungen für bestimmte Merkmale oder das gesamte Teil an.
- Post-Processing-Bedarf: Geben Sie die erforderlichen Wärmebehandlungen (Spannungsarmglühen, HIP, Alterung), Bearbeitungs-, Veredelungs- und Reinigungs-/Passivierungsanforderungen an.
- Menge: Anzahl der benötigten Teile (Prototyp vs. Produktionsmengen).
- Erforderliche Zertifizierungen/Standards: Alle spezifischen Industriestandards (z. B. AS9100-Konformität) oder kundenspezifischen Qualitätsanforderungen.
- Prüfung & Inspektionsanforderungen: Detaillieren Sie alle obligatorischen zerstörungsfreien Prüfungen oder zerstörenden Tests.
- A: Um ein genaues Angebot und eine Machbarkeitsbewertung zu erstellen, benötigt der Anbieter in der Regel:
Die Bereitstellung umfassender Informationen im Voraus ermöglicht es dem B2B Additive Fertigung Anbieter, um die genaueste Kostenschätzung, die Vorlaufzeitprognose und das Feedback zur Designmachbarkeit zu erhalten.
Fazit: Die Zukunft mit 3D-gedruckten Instrumentenhalterungen für Raumfahrzeuge starten
Die Reise in den Weltraum ist von Natur aus eine Herausforderung und erfordert Komponenten, die außergewöhnliche Leistung, unerschütterliche Zuverlässigkeit und minimales Gewicht bieten. Wie wir untersucht haben, sind Instrumentenhalterungen für Raumfahrzeuge kritische Schnittstellen, die den Missionserfolg direkt beeinflussen, indem sie die Stabilität und Funktion empfindlicher Nutzlasten gewährleisten. Die additive Metallfertigung hat sich als disruptive Kraft erwiesen, die die Art und Weise, wie diese wichtigen Komponenten entworfen und hergestellt werden, grundlegend verändert.
Durch den Einsatz von Technologien wie dem Laser Powder Bed Fusion und dem Electron Beam Melting und die Nutzung fortschrittlicher Materialien wie Scalmalloy® und Ti-6Al-4Vkann die Luft- und Raumfahrtindustrie transformative Vorteile erzielen:
- Beispiellose Leichtbauweise: Topologieoptimierung und Gitterstrukturen, die durch AM ermöglicht werden, reduzieren die Bauteilmasse drastisch, senken die Startkosten und setzen Kapazität für mehr funktionale Nutzlasten frei.
- Geometrische Freiheit: Ingenieure können hochkomplexe, integrierte Strukturen entwerfen, die auf Leistung optimiert sind und Funktionen wie konforme Kühlung oder komplizierte Lastpfade integrieren, die mit herkömmlichen Methoden unmöglich sind.
- Teil Konsolidierung: Reduzierung der Montagekomplexität, des Gewichts und potenzieller Fehlerquellen durch das Drucken mehrerer Komponenten als ein monolithisches Teil.
- Verbesserte Leistung: Maßgeschneiderte Steifigkeit, verbesserte Schwingungsdämpfung und optimiertes Wärmemanagement tragen zu einer besseren Instrumentenleistung und -stabilität bei.
- Beschleunigte Zeitpläne: Schnelle Prototypenentwicklung und schnellere Produktionszyklen im Vergleich zur werkzeugabhängigen traditionellen Fertigung verkürzen die Entwicklungs- und Einsatzpläne.
Die Zukunft der Luft- und Raumfahrtindustrie ist zunehmend mit additiven Prozessen verbunden. Bei Instrumentenhalterungen für Raumfahrzeuge ist Metall-AM nicht nur eine Alternative; es ist oft die überlegene Lösung, um die widersprüchlichen Anforderungen an extreme Leistung und minimales Gewicht zu erfüllen, die Weltraumanwendungen innewohnen.
Das erfolgreiche Navigieren durch die Komplexität von AM – von den Prinzipien des Design for Additive Manufacturing (DfAM) und der Materialauswahl bis hin zu komplizierten Nachbearbeitungswegen und einer strengen Qualitätssicherung – erfordert Fachwissen und kompetente Partner. Unternehmen wie Met3dp, deren Grundlage auf jahrzehntelanger gemeinsamer Erfahrung in der additiven Metallfertigung basiert, sind bereit, Organisationen dabei zu helfen, die Leistungsfähigkeit dieser Technologie zu nutzen. Unsere umfassenden Fähigkeiten, die sich über fortschrittliche SEBM-Drucker mit branchenführender Genauigkeit, hochwertige Metallpulver, die im eigenen Haus mit modernsten Gaszerstäubungs- und PREP-Technologien hergestellt werden, und dedizierten Support für die Anwendungsentwicklung erstrecken, bieten ein komplettes Lösungspaket.
Wir verstehen die anspruchsvollen Anforderungen des Luft- und Raumfahrtsektors und arbeiten mit Organisationen zusammen, um den 3D-Druck effektiv zu implementieren und die Transformation der digitalen Fertigung zu beschleunigen. Erfahren Sie, wie die fortschrittlichen Druckverfahren und überlegenen Materialien von Met3dp Ihre nächste Weltraummission verbessern können.
Kontaktieren Sie Met3dp noch heute, um Ihre spezifischen Anforderungen an Raumfahrtkomponenten zu besprechen und herauszufinden, wie unsere hochmodernen Systeme und Pulver die additiven Fertigungsziele Ihres Unternehmens vorantreiben und Ihre Projekte zu neuen Höhen führen können.
Teilen auf
MET3DP Technology Co., LTD ist ein führender Anbieter von additiven Fertigungslösungen mit Hauptsitz in Qingdao, China. Unser Unternehmen ist spezialisiert auf 3D-Druckgeräte und Hochleistungsmetallpulver für industrielle Anwendungen.
Fragen Sie an, um den besten Preis und eine maßgeschneiderte Lösung für Ihr Unternehmen zu erhalten!
Verwandte Artikel
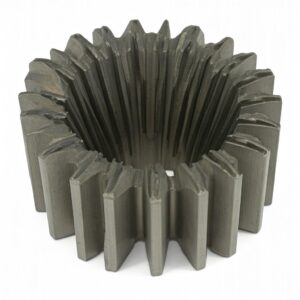
Hochleistungs-Düsenschaufelsegmente: Revolutionierung der Turbineneffizienz mit 3D-Metalldruck
Mehr lesen "Über Met3DP
Aktuelles Update
Unser Produkt
KONTAKT US
Haben Sie Fragen? Senden Sie uns jetzt eine Nachricht! Wir werden Ihre Anfrage mit einem ganzen Team nach Erhalt Ihrer Nachricht bearbeiten.
Holen Sie sich Metal3DP's
Produkt-Broschüre
Erhalten Sie die neuesten Produkte und Preislisten
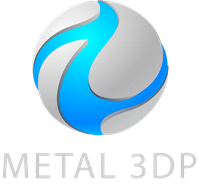
Metallpulver für 3D-Druck und additive Fertigung