3D-gedruckte Wärmeschutzmäntel für Raumfahrtanwendungen
Inhaltsübersicht
Revolutionierung des Schutzes von Raumfahrzeugen: Der Aufstieg der 3D-gedruckten Wärmeschutzhüllen
Die letzte Grenze, der Weltraum, stellt eine der extremsten Umgebungen dar, die man sich vorstellen kann. Geräte, die jenseits der Erdatmosphäre betrieben werden, sehen sich einer unerbittlichen Flut von Herausforderungen gegenüber: dramatische Temperaturschwankungen von direkter Sonneneinstrahlung bis hin zur kalten Leere, Mikrometeoriteneinschläge, Vakuumbedingungen und starke Vibrationen beim Start. Der Schutz empfindlicher Instrumente, Antriebssysteme und Strukturkomponenten vor diesen rauen Bedingungen ist für den Erfolg der Mission von größter Bedeutung. Hier kommt die thermische Hülle ins Spiel - eine kritische Komponente, die als Schutzbarriere fungiert, die Wärmeübertragung steuert und die Betriebsintegrität von Raumfahrzeugen, Satelliten und Trägerraketen sicherstellt. Die Herstellung dieser komplexen Strukturen erforderte bisher komplizierte mehrteilige Baugruppen, eine umfangreiche Bearbeitung von Knüppelmaterialien oder spezielle Umformtechniken. Diese Methoden sind oft mit erheblichen Einschränkungen verbunden: lange Vorlaufzeiten, hoher Materialabfall, Designbeschränkungen, die die geometrische Komplexität einschränken, und beträchtliche Kosten, insbesondere bei Kleinserien und hochgradig kundenspezifischer Raumfahrtausrüstung.
Die Fertigungslandschaft befindet sich jedoch in einem tiefgreifenden Wandel, der durch Fortschritte in der Additive Fertigung von Metall (AM)gemeinhin als Metall bekannt 3D-Druck. Diese Technologie stellt einen Paradigmenwechsel dar, denn sie ermöglicht die Herstellung hochkomplexer, leichter und integrierter Wärmeschutzhüllen direkt aus digitalen Modellen, Schicht für Schicht, unter Verwendung spezieller Metallpulver. Für Beschaffungsmanager und Ingenieure in der Luft- und Raumfahrt und im Verteidigungssektor ist das Verständnis des Potenzials von 3D-gedruckten Wärmeschutzschilden nicht mehr optional, sondern eine strategische Notwendigkeit. Die additive Fertigung ermöglicht eine noch nie dagewesene Designfreiheit, erleichtert eine schnelle Iteration, reduziert die Anzahl der Teile, minimiert den Materialabfall und kann die Entwicklungs- und Produktionszeiten erheblich verkürzen - entscheidende Faktoren in der schnelllebigen Raumfahrtindustrie.
Unternehmen, die auf Metall-AM spezialisiert sind, wie Met3dpstehen bei dieser Revolution an vorderster Front. Durch den Einsatz modernster Technologien wie Selective Electron Beam Melting (SEBM) und Laser Powder Bed Fusion (LPBF), gepaart mit Fachwissen in Werkstoffkunde und Prozessoptimierung, bietet Met3dp umfassende Lösungen für die Herstellung einsatzkritischer Komponenten für die Luft- und Raumfahrt. Unsere Fähigkeiten reichen von der Entwicklung und Herstellung von Hochleistungsmetallpulvern mit fortschrittlichen Gaszerstäubungs- und Plasma-Rotations-Elektroden-Verfahren (PREP) bis hin zum Betrieb von Druckern in Industriequalität, die außergewöhnliche Genauigkeit und Zuverlässigkeit bieten. Dieser integrierte Ansatz stellt sicher, dass Ingenieure die Vorteile von AM in vollem Umfang nutzen können, um thermische Abschirmungen zu entwerfen und zu produzieren, die nicht nur funktional sind, sondern auch in Bezug auf Gewicht, thermische Leistung und strukturelle Integrität in bisher unerreichter Weise optimiert sind. Wenn wir uns eingehender mit den Anwendungen, Vorteilen, Materialien und Überlegungen zu 3D-gedruckten Wärmeschutzvorrichtungen befassen, wird deutlich, dass diese Technologie nicht nur eine alternative Herstellungsmethode ist, sondern die Erforschung und Nutzung des Weltraums der nächsten Generation ermöglicht. Partnerschaften mit erfahrenen Metal 3D-Druck-Lieferanten und dienstleistungsbüros für die additive Fertigung die mit den strengen Anforderungen der Luft- und Raumfahrtindustrie vertraut sind, ist der Schlüssel zur erfolgreichen Implementierung dieser Technologie für die Großserienproduktion von Komponenten und die Entwicklung kritischer Raumfahrtprodukte.
Definieren Sie die Rolle: Wofür werden Wärmeschutzmäntel in der Luft- und Raumfahrt verwendet?
Thermische Abdeckungen für die Luft- und Raumfahrt sind spezielle Gehäuse oder Abdeckungen, die in erster Linie dazu dienen, die Wärmeenergie zu verwalten und kritische Systeme in Trägerraketen, Satelliten, Raumfahrzeugen und anderen orbitalen oder interplanetaren Plattformen zu schützen. Ihre Funktion ist vielschichtig und geht über die einfache Isolierung hinaus. Das Verständnis ihrer genauen Aufgaben ist entscheidend für die Beurteilung des Nutzens, den der Einsatz fortschrittlicher Fertigungstechniken wie des 3D-Metalldrucks für ihre Herstellung bietet.
Kernfunktionen von Wärmeschutzmänteln:
- Thermische Kontrolle: Dies ist die Hauptfunktion. Thermische Abdeckungen steuern den Wärmefluss und schützen empfindliche Komponenten vor extremen Temperaturen.
- Isolierung: Verhinderung eines übermäßigen Wärmeverlusts an das kalte Vakuum des Weltraums oder eines übermäßigen Wärmegewinns durch Sonneneinstrahlung oder interne Wärmequellen (z. B. Elektronik, Triebwerke).
- Strahlungsabschirmung: Reflektieren oder Absorbieren von Wärmestrahlung (Sonne, planetarische Albedo, Infrarot) zur Aufrechterhaltung stabiler Betriebstemperaturen für Nutzlasten, Instrumente oder Treibstofftanks.
- Wärmeverteilung: Bei einigen Konstruktionen können Abdeckungen dazu beitragen, die Wärme gleichmäßiger über die Struktur zu verteilen und so örtlich begrenzte heiße oder kalte Stellen zu vermeiden, die die Leistung beeinträchtigen oder Materialspannungen verursachen könnten.
- Schutz der Umwelt: Neben dem Wärmemanagement dienen Abdeckungen auch als physische Barriere.
- Abschirmung von Mikrometeoriten und Orbitalschrott (MMOD): Sie bieten einen gewissen Schutz gegen den Aufprall von winzigen Partikeln, die sich mit Überlichtgeschwindigkeit fortbewegen und ansonsten empfindliche Systeme beschädigen könnten. Mehrschichtige Isoliermatten (MLI) werden zu diesem Zweck oft zusammen mit strukturellen Abdeckungen eingesetzt.
- Kontrolle der Kontamination: Schutz empfindlicher optischer Instrumente oder Sensoren vor ausgasenden Produkten oder Partikelkontamination während des Starts, des Einsatzes und des Betriebs.
- Schutz vor atomarem Sauerstoff (AO): In der erdnahen Umlaufbahn (LEO) kann atomarer Sauerstoff bestimmte Materialien erodieren. Abdeckungen aus widerstandsfähigen Materialien oder mit Schutzbeschichtungen schirmen die darunter liegenden Komponenten ab.
- Strukturelle Unterstützung & Integration: Obwohl sie oft leicht sind, können sie zur allgemeinen strukturellen Integrität eines Raumfahrzeugs beitragen oder als Befestigungspunkte dienen.
- Belastbar (begrenzt): Bei bestimmten Konstruktionen können sie geringfügige strukturelle Lasten tragen oder bestimmten Baugruppen Steifigkeit verleihen.
- Integrationsplattform: Abdeckungen enthalten oft Schnittstellen für die Montage von Sensoren, Kabelbäumen, Flüssigkeitsleitungen oder anderen Subsystemen, was eine präzise Geometrie und Funktionsintegration erfordert.
- Aerodynamische Funktion (beim Start): Die Abdeckungen an Trägerraketen (z. B. Nutzlastverkleidungen, obwohl es sich dabei in der Regel um viel größere Strukturen handelt) sorgen für ein aerodynamisches Profil während des Aufstiegs in die Atmosphäre und schützen die Nutzlast vor aerodynamischen Kräften und Erhitzung. Kleinere thermische Abdeckungen an internen Komponenten der Trägerrakete dienen ebenfalls der Steuerung der Luftströmung und der thermischen Belastung während dieser Phase.
Typische Anwendungen und Branchen:
Da ein robustes Wärmemanagement erforderlich ist, sind Abdeckungen in verschiedenen Luft- und Raumfahrtanwendungen allgegenwärtig:
- Satelliten: Schutz von empfindlicher Elektronik, Batterien, Antriebstanks, wissenschaftlichen Instrumenten (Teleskope, Sensoren, Kameras) und Kommunikationsnutzlasten vor extremen Temperaturschwankungen zwischen Sonnenlicht und Schatten.
- Trägerraketen: Abschirmung der Triebwerke der Oberstufe, der Avionik und der Nutzlasten während des Aufstiegs durch die Atmosphäre und im Vakuum des Weltraums vor dem Ausbringen der Nutzlast. Schutz der Zwischenstufensektionen.
- Raumschiff (Interplanetarer Weltraum/Deep Space): Kritische thermische Kontrolle für Missionen, die in sehr unterschiedlichen thermischen Umgebungen weit weg von der Erde stattfinden, zum Schutz von Systemen bei Langzeitreisen und Planetenbegegnungen. Beispiele hierfür sind Ummantelungen von thermoelektrischen Radioisotopengeneratoren (RTGs) oder empfindlichen Detektoren.
- Raumstationen & Lebensräume: Thermische Ummantelung auf Komponentenebene für externe Geräte, Experimente und Versorgungsleitungen.
- Wiederverwendbare Raumfahrtsysteme: Entwicklung haltbarer thermischer Abdeckungen, die den harten Bedingungen des Wiedereintritts und der wiederholten Nutzung standhalten.
Bediente Branchen:
- Luft- und Raumfahrt & Verteidigung: Der primäre Markt umfasst staatliche Raumfahrtbehörden (NASA, ESA usw.), militärische Raumfahrtkommandos und kommerzielle Raumfahrtunternehmen (Trägerraketenanbieter, Satellitenhersteller, Betreiber von Konstellationen).
- Telekommunikation: Satellitenhersteller, die weltweite Kommunikationsdienste anbieten.
- Erdbeobachtung & Fernerkundung: Unternehmen und Agenturen, die Satelliten zur Umweltüberwachung, Kartierung und Informationsbeschaffung betreiben.
- Wissenschaftliche Forschung: Universitäten und Forschungseinrichtungen, die Instrumente und Nutzlasten für wissenschaftliche Weltraummissionen entwickeln.
Beschaffungsmanager, die Luft- und Raumfahrtkomponenten, lieferanten von Satellitenhardwareund hersteller von Komponenten für Trägerraketen wenden sich zunehmend der additiven Fertigung zu, um die komplexen Anforderungen an Wärmeschutzhüllen zu erfüllen. Die Möglichkeit, maßgeschneiderte, hoch optimierte Designs zu erstellen, die auf spezifische Einsatzanforderungen zugeschnitten sind, und das oft mit kürzeren Vorlaufzeiten als bei herkömmlichen Methoden, macht den 3D-Metalldruck zu einer attraktiven Lösung für die Herstellung dieser wichtigen Produkte thermomanagement für Raumfahrzeuge Systeme.
Der additive Vorteil: Warum 3D-Metalldruck für Wärmeschutzhüllen verwenden?
Während herkömmliche Fertigungsverfahren wie CNC-Bearbeitung, Blechumformung und Gießen seit langem für die Herstellung von Wärmeschutzhüllen verwendet werden, bietet die additive Fertigung von Metallen (AM) eine Reihe überzeugender Vorteile, die speziell auf die anspruchsvollen Anforderungen von Luft- und Raumfahrtanwendungen zugeschnitten sind. Mit diesen Vorteilen lassen sich die wichtigsten Herausforderungen bei der Herstellung von Raumfahrthardware bewältigen, wie z. B. Gewichtsreduzierung, Designkomplexität, Vorlaufzeit und Kosteneffizienz, insbesondere bei den in der Branche üblichen kleinen bis mittleren Produktionsserien. Für Ingenieure und Beschaffungsspezialisten, die Fertigungsoptionen evaluieren, ist das Verständnis dieser AM-Vorteile entscheidend für die Optimierung des Designs und der Beschaffung von thermischen Abdeckungen.
Hauptvorteile von Metal AM für thermische Abdeckungen:
- Beispiellose Gestaltungsfreiheit & Komplexität:
- Geometrische Komplexität: AM eignet sich hervorragend für die Herstellung komplizierter Formen, innerer Kanäle, dünner Wände und komplexer Gitterstrukturen, die mit subtraktiven Methoden nur schwer oder gar nicht zu erreichen sind. Dies ermöglicht es den Ingenieuren, Abdeckungen zu entwerfen, die sich genau an die darunter liegenden Komponenten anpassen und so die Volumennutzung und die thermische Leistung optimieren.
- Topologie-Optimierung: Mit Hilfe von Algorithmen kann Material aus unkritischen Bereichen entfernt werden, so dass organisch geformte, hocheffiziente Strukturen entstehen, die thermische und strukturelle Anforderungen bei minimaler Masse erfüllen.
- Integrierte Funktionen: Befestigungspunkte, Halterungen, interne Umlenkungen zur Strahlungssteuerung oder sogar Kanäle für Wärmeträgerkreisläufe können direkt in das Abdeckungsdesign integriert werden, was die Anzahl der Teile und die Komplexität der Montage reduziert.
- Gewichtsreduzierung:
- Massenreduzierung: In der Luft- und Raumfahrt ist das Gewicht ein entscheidendes Kriterium; jedes eingesparte Kilogramm bedeutet eine erhebliche Senkung der Startkosten oder eine Erhöhung der Nutzlastkapazität. AM ermöglicht Leichtbau durch Topologieoptimierung, die Verwendung komplexer Gitterstrukturen und die Möglichkeit, dünnwandige Konstruktionen ohne die Zwänge der traditionellen Werkzeugherstellung zu erstellen. Materialien wie Aluminiumlegierungen (z. B. AlSi10Mg) bieten ein hervorragendes Verhältnis von Festigkeit zu Gewicht, was diesen Vorteil noch verstärkt.
- Optimierte Materialverteilung: Das Material wird nur dort platziert, wo es für die thermische oder strukturelle Leistung benötigt wird, wodurch die übermäßige Masse, die bei maschinell bearbeiteten Teilen oft entsteht, vermieden wird.
- Teil Konsolidierung:
- Reduzierte Montage: Für komplexe Abdeckungen mussten bisher mehrere Einzelteile hergestellt und dann zusammengesetzt (geschweißt, geschraubt, genietet) werden. Mit AM können diese Mehrkomponenten-Baugruppen als ein einziges, monolithisches Teil gedruckt werden.
- Verbesserte Verlässlichkeit: Weniger Verbindungen und Befestigungselemente bedeuten weniger potenzielle Fehlerpunkte, was die Gesamtzuverlässigkeit des Bauteils erhöht - ein entscheidender Faktor für den Erfolg der Mission im Weltraum.
- Vereinfachte Lieferkette: Die Verwaltung weniger einzelner Teilenummern vereinfacht die Logistik, den Bestand und die Qualitätskontrolle.
- Rapid Prototyping und Iteration:
- Geschwindigkeit: Funktionale Metallprototypen können innerhalb von Tagen statt Wochen oder Monaten direkt aus CAD-Modellen hergestellt werden, was eine schnelle Designüberprüfung und Testzyklen ermöglicht.
- Flexibilität: Konstruktionsänderungen können schnell umgesetzt werden, ohne dass teure Werkzeugänderungen erforderlich sind. Diese Flexibilität ist in der Entwicklungsphase von komplexen Raumfahrtsystemen von unschätzbarem Wert.
- Materialeffizienz & Abfallreduzierung:
- Fast-Netzform: Beim AM werden die Teile schichtweise aufgebaut, wobei nur das für das Bauteil und seine Stützstrukturen erforderliche Material verwendet wird. Dies steht in scharfem Kontrast zur subtraktiven Fertigung, bei der erhebliche Mengen an teurem Rohmaterial (häufig Legierungen in Luftfahrtqualität) als Späne abgetragen werden.
- Nachhaltigkeit: Die Verringerung des Materialabfalls trägt zu nachhaltigeren Fertigungsverfahren bei. Das Pulverrecycling innerhalb des AM-Prozesses verbessert die Materialnutzung weiter.
- Personalisierung & Fertigung auf Abruf:
- Maßgeschneiderte Designs: AM eignet sich ideal für die geringen Stückzahlen und den hohen Individualisierungsgrad vieler Luft- und Raumfahrtkomponenten. Jede Abdeckung kann auf die spezifischen thermischen und geometrischen Anforderungen der jeweiligen Anwendung zugeschnitten werden, ohne dass hohe Werkzeugkosten anfallen.
- Verteilte Fertigung: Potenziell kann die Fertigung näher am Ort des Bedarfs oder der Montage erfolgen, wodurch die Logistik rationalisiert wird.
- Leistungsverbesserung:
- Optimierte Wärmewege: Komplexe Innengeometrien können so gestaltet werden, dass sie den Wärmefluss gezielt lenken oder die Oberfläche für die Strahlungskühlung maximieren.
- Neuartige Materialien: AM-Verfahren können manchmal mit fortschrittlichen Legierungen oder Metallmatrix-Verbundwerkstoffen arbeiten, die speziell für additive Verfahren entwickelt wurden und einzigartige Eigenschaftskombinationen bieten.
Nutzung von Fachwissen für optimale Ergebnisse:
Um diese Vorteile zu erreichen, ist ein umfassendes Fachwissen sowohl über das Design für die additive Fertigung (DfAM) als auch über das Druckverfahren selbst erforderlich. Unternehmen wie Met3dp bieten dieses entscheidende Fachwissen. Unser Verständnis für verschiedene 3D-Druck von Metall verfahren (SEBM, LPBF), kombiniert mit unserer hochwertigen Pulverproduktion und strengen Prozesskontrolle, stellen sicher, dass die theoretischen Vorteile von AM in greifbare Vorteile für Ihre Wärmeschutzanwendung umgesetzt werden. Wir arbeiten eng zusammen mit teams für Luft- und Raumfahrttechnik und einkaufsabteilungen um Entwürfe zu optimieren, die geeigneten Materialien (wie IN625 oder AlSi10Mg) auszuwählen und die Herstellung zuverlässiger, weltraumtauglicher Komponenten zu gewährleisten. Zusammenarbeit mit Fachleuten anbieter von additiven Fertigungslösungen ist der Schlüssel zur Maximierung des Potenzials des 3D-Drucks für komplexe Wärmemanagement-Hardware.
Tabelle: Vergleich zwischen AM und traditioneller Fertigung für Thermal Shrouds
Merkmal | Additive Fertigung von Metall (AM) | Traditionelle Fertigung (Zerspanung, Umformung, Montage) | Vorteil von AM |
---|---|---|---|
Entwurfskomplexität | Hoch (komplexe Geometrien, interne Kanäle, Gitter machbar) | Mäßig bis niedrig (begrenzt durch Werkzeuge, Bearbeitungszugang) | Ermöglicht hoch optimierte, integrierte und konforme Designs. |
Gewichtsreduzierung | Ausgezeichnet (Topologieoptimierung, dünne Wände, Gitterstrukturen) | Gut (Taschenbildung, Materialauswahl) | Erhebliches Potenzial zur Massenreduzierung durch optimierte Geometrie. |
Teil Konsolidierung | Hoch (mehrere Teile in einem Druck kombiniert) | Niedrig (erfordert den Zusammenbau mehrerer Komponenten) | Reduziert die Montagezeit, die Kosten und mögliche Fehlerquellen. |
Vorlaufzeit (Proto) | Kurz (Tage bis Wochen) | Mäßig bis lang (Wochen bis Monate, abhängig von der Werkzeugausstattung) | Schnellere Entwurfsiteration und -überprüfung. |
Vorlaufzeit (Prod) | Mäßig (abhängig von der Größe des Gebäudes, der Menge und der Nachbearbeitung) | Kann bei sehr hohem Volumen schneller sein, bei geringem Volumen langsamer | Wettbewerbsfähig bei kleinen bis mittleren Mengen, wie sie in der Luft- und Raumfahrt üblich sind. |
Materialabfälle | Niedrig (netzähnliche Form, Pulverrecycling) | Hoch (erheblicher Materialabtrag als Späne bei der Bearbeitung) | Nachhaltigere und kosteneffizientere Nutzung von teuren Materialien für die Luft- und Raumfahrt. |
Werkzeugkosten | Keine (direkte digitale Fertigung) | Hoch (Formen, Gesenke, Vorrichtungen oft erforderlich) | Kostengünstig für kleine Mengen und kundenspezifische Teile. |
Personalisierung | Hoch (leicht zu ändernde Designs pro Einheit) | Gering (Konstruktionsänderungen erfordern oft neue Werkzeuge) | Ideal für maßgeschneiderte Hardware für die Luft- und Raumfahrt. |
Ursprüngliche Teilkosten | Kann bei einfachen Teilen/sehr großen Mengen höher sein | Kann bei einfachen Teilen/sehr großen Mengen niedriger sein | Kostengünstig für komplexe, kleinvolumige oder konsolidierte Teile. |
Potenzieller Durchsatz | Geringere Kosten pro Maschine im Vergleich zu Massenproduktionsverfahren | Höher für etablierte Massenproduktionslinien | Die Skalierbarkeit nimmt mit größeren Maschinen und Multilasersystemen zu. |
In Blätter exportieren
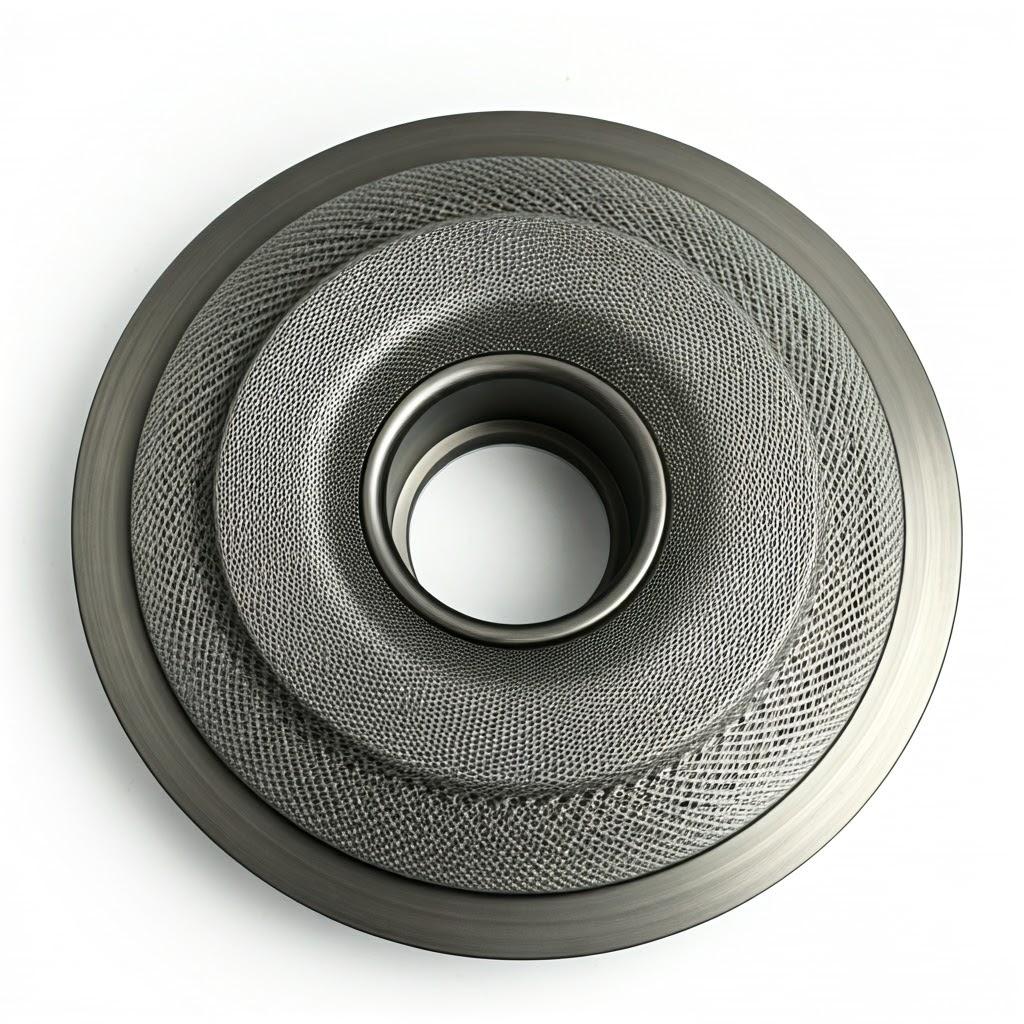
Das Material ist entscheidend: Die Auswahl von IN625 und AlSi10Mg für optimale Leistung
Die Wahl des Werkstoffs ist von grundlegender Bedeutung für die Leistung und Zuverlässigkeit eines jeden Bauteils in der Luft- und Raumfahrt, insbesondere eines Bauteils, das den extremen thermischen und umweltbedingten Bedingungen ausgesetzt ist, denen Wärmeschutzvorrichtungen ausgesetzt sind. Die additive Fertigung von Metallen bietet die Flexibilität, mit einer Reihe von Hochleistungslegierungen zu arbeiten. Bei 3D-gedruckten Wärmeschutzhüllen zeichnen sich zwei Materialien durch eine hervorragende Kombination von Eigenschaften aus, die für Raumfahrtanwendungen relevant sind: IN625 (Inconel 625)einer Nickel-Chrom-Superlegierung, und AlSi10Mgeine Aluminium-Silizium-Magnesium-Legierung. Das Verständnis ihrer Eigenschaften ist der Schlüssel für Ingenieure, die das Bauteil entwerfen, und für Beschaffungsmanager, die die metall-AM-Pulver oder den endgültigen gedruckten Teil.
IN625 (Nickel-Chrom-Superlegierung): Der Hochtemperatursieger
IN625 ist für seine außergewöhnliche Leistung in rauen Umgebungen bekannt, was es zu einem erstklassigen Kandidaten für thermische Abdeckungen macht, die unter erheblichen thermischen Belastungen arbeiten oder eine hohe Festigkeit und Korrosionsbeständigkeit erfordern.
- Wichtige Eigenschaften:
- Ausgezeichnete Hochtemperaturfestigkeit: Behält auch bei hohen Temperaturen (bis zu ~815°C / 1500°F und darüber hinaus bei kurzen Ausschlägen) eine hohe Festigkeit und strukturelle Integrität bei, was für Abdeckungen in der Nähe von Motoren oder bei direkter Sonneneinstrahlung entscheidend ist.
- Hervorragende Korrosionsbeständigkeit: Hochgradig resistent gegen Oxidation, korrosive Umgebungen (einschließlich Beständigkeit gegen Lochfraß und Spaltkorrosion) und Spannungsrisskorrosion, was für die Langlebigkeit in der Weltraumumgebung und die Beständigkeit gegen Treibstoffrückstände entscheidend ist.
- Hohe Ermüdungsfestigkeit: Widersteht zyklischen Belastungen und Vibrationen, die beim Start und bei Raumfahrtmanövern auftreten.
- Gute Verarbeitbarkeit & Schweißbarkeit (in traditionellen Formen): Während AM seine eigenen Überlegungen mit sich bringt, tragen die inhärenten Eigenschaften zur Verarbeitbarkeit in additiven Verfahren bei.
- Kryogenische Zähigkeit: Behält seine gute Duktilität und Zähigkeit auch bei sehr niedrigen Temperaturen, wie sie im Weltraum vorkommen.
- Warum IN625 für thermische Abdeckungen verwenden?
- Anwendungen mit hohem Wärmestrom (z. B. in der Nähe von Antriebssystemen, Hochleistungselektronik).
- Komponenten, die eine lange Lebensdauer bei minimaler Verschlechterung aufweisen müssen.
- Situationen, in denen eine Exposition gegenüber ätzenden Stoffen möglich ist.
- Wenn hohe Festigkeit und Ermüdungsbeständigkeit neben der thermischen Leistung entscheidende Konstruktionsfaktoren sind.
- Seine relativ hohe Dichte im Vergleich zu Aluminium bedeutet, dass es oft gewählt wird, wenn seine einzigartigen Hochtemperatur-/Korrosionseigenschaften wichtig sind und das Gewicht an bestimmten Orten überwiegt.
- AM-Überlegungen für IN625:
- Erfordert eine sorgfältige Kontrolle der Parameter während LPBF oder EBM, um Eigenspannungen zu bewältigen und Risse zu vermeiden.
- Erfordert oft Wärmebehandlungen nach dem Druck (Spannungsabbau, Lösungsglühen, Alterung), um optimale mechanische Eigenschaften zu erzielen.
- Stützstrukturen können aufgrund der Zähigkeit des Materials schwer zu entfernen sein.
AlSi10Mg (Aluminium-Silizium-Magnesium-Legierung): Das leichte Arbeitspferd
AlSi10Mg ist eine der am häufigsten verwendeten Aluminiumlegierungen in der additiven Fertigung, die für ihre hervorragende Kombination aus geringer Dichte, guten mechanischen Eigenschaften und Druckbarkeit geschätzt wird.
- Wichtige Eigenschaften:
- Geringe Dichte / hohes Verhältnis von Festigkeit zu Gewicht: Deutlich leichter als Stahl oder Nickellegierungen (~2,67 g/cm³), daher ideal für gewichtssensible Luft- und Raumfahrtanwendungen. Bietet eine gute Festigkeit nach entsprechender Wärmebehandlung.
- Gute Wärmeleitfähigkeit: Es leitet Wärme effizient, was bei Konstruktionen, die thermische Lasten verteilen oder Wärme abstrahlen sollen, von Vorteil sein kann.
- Ausgezeichnete Druckbarkeit: Im Vergleich zu vielen Hochtemperaturlegierungen gilt LPBF im Allgemeinen als einfacher zu verarbeiten und ermöglicht feinere Merkmale und komplexe Geometrien.
- Gute Korrosionsbeständigkeit: Weist eine gute Beständigkeit gegen atmosphärische Korrosion auf.
- Moderate Temperaturfähigkeit: Geeignet für Anwendungen, bei denen die Temperaturen im Allgemeinen unter ~150-200°C (300-390°F) bleiben, je nach Belastung und Dauer.
- Warum AlSi10Mg für Wärmeschutzmäntel verwenden?
- Allgemeine Abdeckungen, bei denen extreme Temperaturen nicht das Hauptanliegen sind.
- Anwendungen, bei denen die Minimierung der Masse oberste Priorität hat (z. B. große Abdeckungen bei Satelliten).
- Komponenten, die eine gute Wärmeleitfähigkeit benötigen, um die Wärmeableitung zu steuern.
- Schnelles Prototyping und Entwicklung aufgrund der bewährten Verarbeitbarkeit.
- Kostensensitive Anwendungen, bei denen die extreme Leistung des IN625 nicht erforderlich ist.
- AM-Überlegungen für AlSi10Mg:
- Erzielt optimale mechanische Eigenschaften durch spezielle Wärmebehandlungszyklen (z. B. T6) nach dem Druck.
- Die Oberfläche muss in der Regel nachbearbeitet werden (z. B. durch Perlstrahlen), um die Glätte zu erhöhen.
- Kann zu Porosität neigen, wenn die Druckparameter nicht sorgfältig kontrolliert werden.
Tabelle: Eigenschaftsvergleich – IN625 vs. AlSi10Mg (typische AM-Werte)
Eigentum | IN625 (LPBF, wärmebehandelt) | AlSi10Mg (LPBF, wärmebehandelt – T6) | Relevanz für Wärmeschutzmäntel |
---|---|---|---|
Dichte | ~8,44 g/cm³ | ~2,67 g/cm³ | Gewichtsreduzierung (AlSi10Mg-Vorteil) |
Endgültige Zugfestigkeit | >950 MPa | ~350-450 MPa | Strukturelle Integrität, Widerstandsfähigkeit gegen Abschusslasten |
Streckgrenze | >600 MPa | ~250-350 MPa | Widerstandsfähigkeit gegen dauerhafte Verformung |
Dehnung beim Bruch | >30% | ~3-10% | Duktilität, Bruchzähigkeit |
Maximale Betriebstemperatur | Hoch (~800°C+) | Mäßig (~150-200°C) | Eignung für Hochtemperaturanwendungen vs. allgemeine thermische Anwendungen |
Wärmeleitfähigkeit | Niedrig (~10 W/m-K) | Hoch (~130-150 W/m·K) | Wärmeableitung vs. Isolierfähigkeit |
Korrosionsbeständigkeit | Ausgezeichnet | Gut | Langlebigkeit in der Weltraumumgebung, Resistenz gegen Verunreinigungen |
Druckbarkeit | Mäßig (erfordert sorgfältige Kontrolle) | Ausgezeichnet | Leichtere Herstellung komplexer Formen, Möglichkeit für feinere Merkmale |
Relative Kosten (Puder) | Hoch | Mäßig | Beitrag der Materialkosten zum Endpreis des Teils |
In Blätter exportieren
Die Bedeutung von qualitativ hochwertigen Pulvern: Der Met3dp-Vorteil
Die endgültigen Eigenschaften und die Zuverlässigkeit eines 3D-gedruckten Wärmeschutzmantels hängen entscheidend von der Qualität des verwendeten Metallpulvers ab. Faktoren wie Partikelgrößenverteilung (PSD), Morphologie (Sphärizität), Fließfähigkeit, Reinheit und innere Porosität wirken sich direkt auf die Dichte, Festigkeit und Konsistenz des gedruckten Teils aus. Met3dp hat diesen kritischen Zusammenhang erkannt und legt großen Wert auf die Pulverproduktion.
- Fortschrittliche Zerstäubung: Wir verwenden branchenführende Gaszerstäubungs- und PREP-Technologien (Plasma Rotating Electrode Process). Unsere Gaszerstäubungssysteme nutzen einzigartige Düsen- und Gasströmungsdesigns, die für die Herstellung hochsphärischer Metallpulver mit hervorragender Fließfähigkeit optimiert sind - unerlässlich für eine gleichmäßige Pulverbettschichtung in AM-Prozessen. Die PREP-Technologie ist bekannt für die Herstellung von Pulvern mit extrem hoher Reinheit und minimalen Satellitenpartikeln oder interner Porosität - ideal für anspruchsvolle Anwendungen.
- Qualitätskontrolle: Während des gesamten Pulverherstellungsprozesses werden strenge Qualitätskontrollmaßnahmen durchgeführt, von der Rohmaterialkontrolle bis zur endgültigen Pulvercharakterisierung (PSD-Analyse, Morphologiebewertung, Überprüfung der chemischen Zusammensetzung, Fließprüfung).
- 5. Flexibilität der Lieferkette und On-Demand-Fertigung Metall-Pulver: Met3dp stellt eine breite Palette hochwertiger Metallpulver her, darunter IN625 und AlSi10Mg, die speziell für Laser- (LPBF) und Elektronenstrahl- (SEBM) Pulverbettschmelzverfahren optimiert sind. Unser Portfolio umfasst auch andere für die Luft- und Raumfahrt relevante Werkstoffe wie Titanlegierungen (Ti6Al4V) und verschiedene nichtrostende Stähle.
Durch die Gewährleistung der höchsten Standards bei der Pulverherstellung bietet Met3dp Luft- und Raumfahrtunternehmen und tier-1-Lieferanten mit den grundlegenden Materialien auszustatten, die für die zuverlässige Herstellung von 3D-gedruckten Hochleistungs-Wärmeleitblechen erforderlich sind, die den strengen Anforderungen der Raumfahrt entsprechen. Die Wahl eines Partners wie Met3dp mit integrierten Fähigkeiten, die eine fortschrittliche Pulverproduktion und hochmoderne Druckdienstleistungen umfassen, erleichtert die Einführung der additiven Fertigung für kritische Komponenten. Quellen und verwandte Inhalte
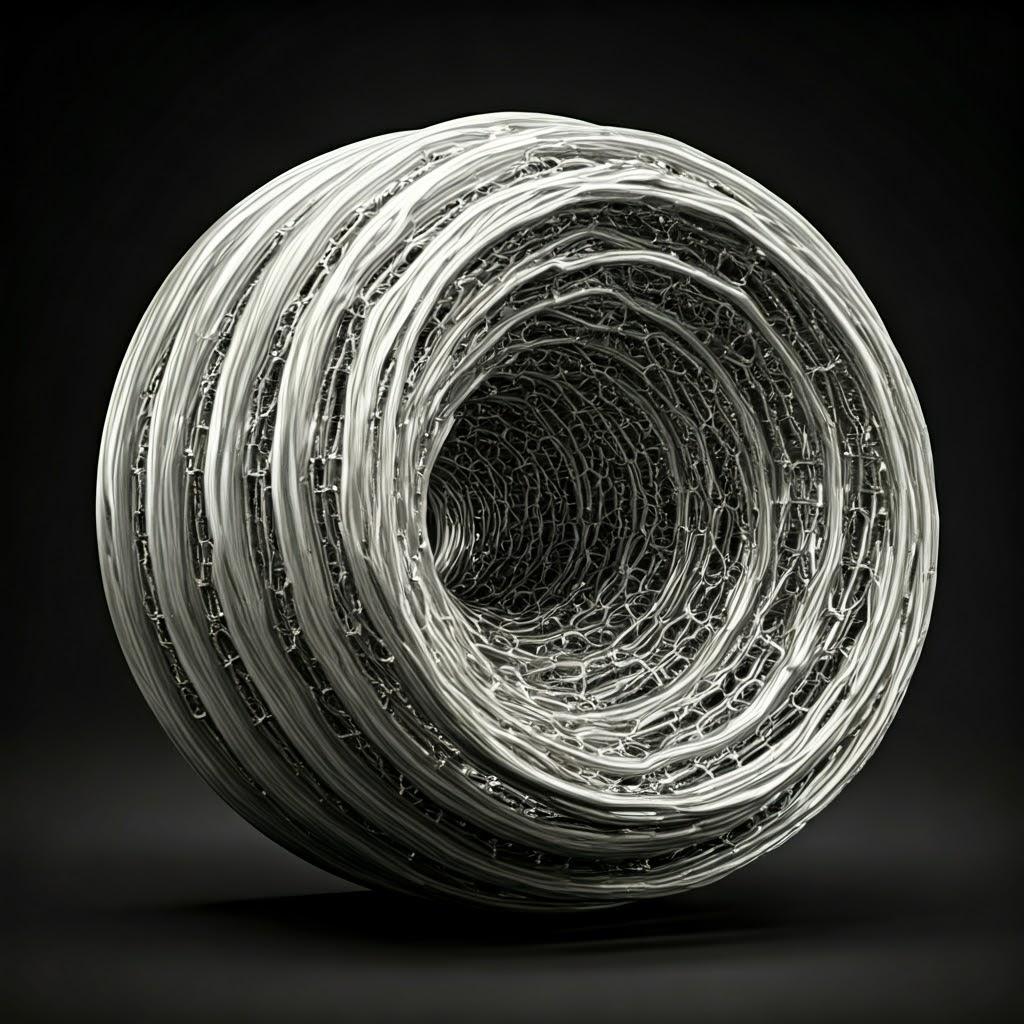
Entwerfen für die Bauplatte: Wichtige DfAM-Überlegungen für thermische Abdeckungen
Der Übergang von traditionellen Fertigungsparadigmen zur additiven Fertigung erfordert ein grundlegendes Umdenken in der Konstruktion. Die einfache Konvertierung eines CAD-Modells, das für die maschinelle Bearbeitung oder die Blechfertigung entworfen wurde, in eine STL-Datei für den Druck schöpft selten das volle Potenzial der additiven Fertigung aus und kann sogar zu suboptimalen Ergebnissen oder Druckfehlern führen. Dies ist der Punkt, an dem Design für additive Fertigung (DfAM) unverzichtbar wird. DfAM ist eine Reihe von Prinzipien und Techniken, die darauf abzielen, das Design eines Teils zu optimieren, um die einzigartigen Fähigkeiten des gewählten AM-Prozesses (wie LPBF oder SEBM) und des Materials (IN625, AlSi10Mg) zu nutzen und die Einschränkungen zu umgehen. Bei thermischen Abdeckungen für die Luft- und Raumfahrt kann die konsequente Anwendung von DfAM zu erheblichen Verbesserungen bei Leistung, Gewicht, Kosten und Herstellbarkeit führen. Beschaffungsmanager sollten sicherstellen, dass ihre Ingenieurteams oder die von ihnen ausgewählten AM-Dienstleister über ein ausgeprägtes DfAM-Fachwissen verfügen.
Grundlegende DfAM-Prinzipien für 3D-gedruckte Wärmeschutzhüllen:
- Topologie-Optimierung:
- Konzept: Verwendung von Software-Algorithmen zur iterativen Entfernung von Material aus einem Entwurfsbereich auf der Grundlage der angewendeten Lasten, Einschränkungen (thermisch, strukturell) und Leistungsziele (z. B. Minimierung der Masse, Maximierung der Steifigkeit).
- Anwendung für Leichentücher: Dies ist wohl eines der leistungsfähigsten DfAM-Werkzeuge für die Luft- und Raumfahrt. Thermal Shrouds haben oft komplexe Belastungsszenarien (Vibrationen beim Start) und thermische Anforderungen, sind aber in erster Linie volumenfüllende oder schützende Abdeckungen. Die Topologieoptimierung kann die Struktur der Hülle formen und organische, knochenähnliche Formen schaffen, die die notwendige Unterstützung und die thermischen Pfade mit einem absoluten Minimum an Material bieten. Dies führt direkt zu erheblichen Gewichtseinsparungen.
- Erwägungen: Optimierte Designs können komplex und nicht intuitiv sein und erfordern eine sorgfältige Validierung durch Simulation (FEA, CFD). Einschränkungen der Herstellbarkeit (z. B. Mindestgröße des Merkmals, Überhangswinkel) müssen in den Optimierungsprozess einbezogen werden.
- Gitterstrukturen und Ausfachung:
- Konzept: Ersetzen von Volumenkörpern durch innere Gitterstrukturen (Streben, Kreisel, Waben, TPMS – Triply Periodic Minimal Surfaces) oder gemusterte Ausfachungen.
- Anwendung für Leichentücher:
- Gewichtsreduzierung: Ähnlich wie bei der Topologieoptimierung reduzieren Gitter die Masse drastisch und bieten gleichzeitig strukturelle Unterstützung über große Flächen.
- Schwingungsdämpfung: Bestimmte Gittergeometrien können so konstruiert werden, dass sie Schwingungen absorbieren oder dämpfen, wodurch empfindliche Bauteile im Inneren der Abdeckung geschützt werden können.
- Wärmemanagement: Gitterstrukturen können die Wärmeleitfähigkeit beeinflussen (im Allgemeinen verringern sie diese im Vergleich zu festen Materialien) oder die Oberfläche für die Strahlungskühlung vergrößern, wenn sie strategisch ausgelegt sind. TPMS-Gitter bieten ein hohes Verhältnis von Oberfläche zu Volumen.
- Reduzierung der Unterstützung: Interne Gitter können manchmal als selbsttragende Strukturen für darüber liegende Schichten dienen.
- Erwägungen: Der Entwurf von Gittern erfordert eine spezielle Software. Die vollständige Entfernung des Pulvers aus komplexen inneren Gittern ist entscheidend und kann eine Herausforderung sein. Die Überprüfung der Integrität des inneren Gitters erfordert häufig eine CT-Untersuchung. Die strukturellen und thermischen Eigenschaften von Gittern hängen in hohem Maße von der Art der Einheitszelle, der Größe und dem Strebendurchmesser bzw. der Wanddicke ab und müssen daher sorgfältig charakterisiert werden.
- Konformes Design:
- Konzept: Entwicklung von Komponenten, die sich eng an die Konturen der Systeme anpassen, mit denen sie interagieren oder die sie schützen.
- Anwendung für Leichentücher: Mit AM können Abdeckungen mit komplexen Krümmungen entworfen werden, die genau der Geometrie der darunter liegenden Instrumente, Elektronikgehäuse oder Treibstoffleitungen entsprechen. Dies minimiert verschwendetes Volumen, verbessert die Verpackungseffizienz innerhalb des Raumfahrzeugs und kann den thermischen Kontakt oder die Strahlungskopplung verbessern, wo dies beabsichtigt ist. Mit herkömmlichen Methoden lassen sich solche maßgeschneiderten, passgenauen Formen oft nur schwer wirtschaftlich herstellen.
- Wanddicke und Größe der Merkmale:
- Mindestdicke: AM-Prozesse haben Grenzen für die Mindestwandstärke, die sie zuverlässig herstellen können (typischerweise ~0,3-0,5 mm für LPBF, potenziell dicker für EBM, je nach Material und Parametern). Die Konstruktionen müssen diese Grenzen einhalten.
- Variable Dicke: Die Wandstärke kann über das gesamte Bauteil hinweg variiert werden, um die Steifigkeit dort zu erhöhen, wo sie benötigt wird, oder um die Masse in weniger kritischen Bereichen zu reduzieren, ohne dass die Werkzeuganforderungen des Gießens oder Formens erfüllt werden müssen. Sanfte Übergänge in der Dicke sind abrupten Änderungen vorzuziehen, die zu Spannungskonzentrationen führen können.
- Merkmal Auflösung: Mindestdurchmesser für Löcher, Mindestbreiten für Schlitze und die erreichbare Detailgenauigkeit für kleine Merkmale oder integrierten Text (Teilenummern, Markierungen) hängen vom AM-Prozess (LPBF bietet im Allgemeinen eine feinere Auflösung als EBM) und den Parametereinstellungen ab.
- Stützkonstruktionen & Überhänge:
- Selbsttragende Winkel: Pulverbettschmelzverfahren erfordern Stützstrukturen für überhängende Merkmale, die in der Regel einen bestimmten Winkel relativ zur Bauplatte überschreiten (häufig um 45 Grad, aber abhängig von Material und Parametern). Die Konstruktionen sollten darauf abzielen, die selbsttragenden Geometrien zu maximieren, indem die Oberflächen entsprechend ausgerichtet werden oder Fasen/Feilen anstelle von scharfen horizontalen Überhängen verwendet werden.
- Minimierung von Unterstützungen: Halterungen verlängern die Druckzeit, verbrauchen Material, erfordern eine Nachbearbeitung für die Entfernung und können sich negativ auf die Oberflächenbeschaffenheit des unterstützten Bereichs auswirken (‘down-skin’). Die strategische Ausrichtung der Teile auf der Bauplatte ist entscheidend, um die Menge der benötigten Stützen zu minimieren.
- Entwerfen für die Beseitigung: Wenn Stützen unvermeidbar sind, sollten sie so gestaltet sein, dass sie sich leichter entfernen lassen (z. B. mit kleineren Kontaktpunkten, Perforation, zugänglichen Stellen). Dies ist besonders wichtig bei zähen Materialien wie IN625, deren Entfernung arbeitsintensiv sein kann. Erwägen Sie den Einsatz spezieller Software zur Erstellung von Halterungen.
- Umgang mit thermischem Stress:
- Konzept: Die schnelle Erwärmung und Abkühlung, die mit AM einhergeht, führt zu inneren Spannungen, die zu Verformungen führen können, insbesondere bei großen, flachen Abschnitten oder Teilen mit starken Temperaturgradienten.
- DfAM-Strategien: Vermeiden Sie große, dünne, flache Bereiche parallel zur Bauplatte, insbesondere in der Nähe des Bodens. Führen Sie gegebenenfalls spannungsentlastende Merkmale wie Rippen oder Riffelungen ein. Optimieren Sie die Teileausrichtung, um ein Gleichgewicht zwischen Überhängen und thermischer Stabilität herzustellen. Simulationswerkzeuge können die Spannungsakkumulation vorhersagen und über Konstruktionsänderungen informieren.
- Teil Konsolidierung:
- Konzept: Bewusstes Umgestalten von Mehrkomponenten-Baugruppen, die als eine einzige, integrierte Einheit gedruckt werden sollen.
- Anwendung für Leichentücher: Eine Abdeckungsbaugruppe besteht traditionell aus einem Hauptkörper, Befestigungsklammern, Verstärkungsrippen und Befestigungslöchern, die alle separat hergestellt werden. DfAM regt an, dies als ein monolithisches Teil neu zu gestalten. Dies reduziert den Arbeitsaufwand bei der Montage, eliminiert Befestigungselemente (potenzielle Fehlerquellen), vereinfacht die Lagerhaltung und reduziert oft das Gesamtgewicht.
- Erwägungen: Konsolidierte Designs können in Bezug auf Druck und Inspektion komplexer werden. Der Zugang für interne Merkmale (Reinigung, Inspektion) muss berücksichtigt werden.
Die Zusammenarbeit mit AM-Spezialisten, wie dem Ingenieurteam von Met3dp, während der frühen Entwurfsphase ist sehr zu empfehlen. Unser Team kennt die Feinheiten von DfAM für Materialien wie IN625 und AlSi10Mg und kann Sie bei der Optimierung von Wärmeschutzmantelkonstruktionen für eine erfolgreiche Produktion beraten, wobei wir unsere Erfahrung mit additive Fertigungslösungen für die Luft- und Raumfahrt. Gemeinsame Entwurfsprüfungen, die sich auf die Herstellbarkeit konzentrieren, können kostspielige Umgestaltungen verhindern und sicherstellen, dass das endgültige Teil alle Leistungs- und Qualitätsanforderungen erfüllt.
Präzision in der Umlaufbahn: Toleranzen, Oberflächengüte und Genauigkeit verstehen
Bei Komponenten für die Luft- und Raumfahrt ist Präzision nicht nur wünschenswert, sondern zwingend erforderlich. Wärmeschutzabdeckungen haben vielleicht nicht immer die gleichen Präzisionsanforderungen im Mikrometerbereich wie einige Triebwerkskomponenten oder optische Bänke, erfordern aber dennoch ein bestimmtes Maß an Maßgenauigkeit, kontrollierte Toleranzen an den Schnittstellen und eine geeignete Oberflächenbeschaffenheit, um die richtige Passform, Funktion und thermische Leistung zu gewährleisten. Um realistische Erwartungen zu formulieren und die Anforderungen effektiv zu spezifizieren, ist es wichtig zu verstehen, was die additive Fertigung von Metallen in Bezug auf die Präzision leisten kann und welche Faktoren diese beeinflussen.
Schlüsselaspekte der Präzision bei AM:
- Toleranzen:
- Definition: Die zulässige Abweichung eines Maßes von seinem angegebenen Nennwert.
- Erreichbare Niveaus: Die gedruckten Toleranzen bei der Metall-AM (LPBF/EBM) werden oft mit den Guss- oder allgemeinen Bearbeitungstoleranzen verglichen. Ein gängiger Bezugspunkt ist die ISO 2768, wobei die erreichbaren Allgemeintoleranzen oft in die mittleren (m) oder manchmal in die f) Klassen für kleinere Abmessungen fallen. Typische erreichbare Toleranzen liegen im Bereich von ±0,1 mm bis ±0,3 mm für mittlere Abmessungen, aber dies hängt stark von mehreren Faktoren ab.
- Beeinflussende Faktoren:
- Kalibrierung der Maschine: Genauigkeit des Laser-/Elektronenstrahl-Positionierungssystems, Scannerkalibrierung.
- Materialeigenschaften: Wärmeausdehnung/Kontraktionsverhalten von IN625 oder AlSi10Mg während der Verarbeitung.
- Größe und Geometrie des Teils: Größere Teile sind anfälliger für thermische Verformung; komplexe Geometrien können eine Herausforderung darstellen.
- Position auf der Bauplatte: Geringfügige Abweichungen können je nach Bauplattform auftreten.
- Parameter drucken: Schichtdicke, Strahlleistung und Scangeschwindigkeit beeinflussen die Stabilität des Schmelzbades und die Schrumpfung.
- Strategie unterstützen: Wie das Teil abgestützt wird, kann die endgültige Geometrie nach dem Entfernen der Abstützung beeinflussen.
- Nachbearbeiten: Spannungsabbau und Wärmebehandlung können geringfügige Maßänderungen bewirken; durch maschinelle Bearbeitung lassen sich bei bestimmten Merkmalen wesentlich engere Toleranzen erzielen.
- Spezifikation: Kritische Toleranzen (z. B. an Montageschnittstellen, Dichtungsflächen) werden oft durch CNC-Bearbeitung nach dem Druck erreicht, anstatt sich ausschließlich auf die Genauigkeit des Drucks zu verlassen. Es ist von entscheidender Bedeutung, kritische Abmessungen und ihre erforderlichen Toleranzen auf technischen Zeichnungen klar zu definieren.
- Oberflächengüte (Rauhigkeit):
- Definition: Das Maß für die feinen Unregelmäßigkeiten auf einer Oberfläche, in der Regel quantifiziert durch Ra (durchschnittliche Rauheit).
- As-Printed-Werte: Die Oberflächenbeschaffenheit von AM-Metallteilen ist von Natur aus rauer als die von bearbeiteten Oberflächen. Typische Ra-Werte für LPBF reichen von 6 µm bis 20 µm (240 µin bis 800 µin), beeinflusst durch:
- Orientierung: Senkrechte Wände sind in der Regel glatter als nach oben oder unten gerichtete Flächen. Nach unten gerichtete (gestützte) Oberflächen sind aufgrund der Kontaktpunkte mit den Stützen in der Regel am rauesten.
- Pulver Partikelgröße: Feinere Puder können zu etwas glatteren Oberflächen führen.
- Schichtdicke: Dünnere Schichten führen im Allgemeinen zu einer besseren Oberflächenqualität auf gekrümmten oder abgewinkelten Flächen (geringerer Treppeneffekt).
- Strahlparameter: Der Energieeintrag wirkt sich auf die Eigenschaften des Schmelzbades und die Oberflächenstruktur aus.
- Material: Verschiedene Legierungen können leicht unterschiedliche Oberflächeneigenschaften aufweisen.
- Verbesserung der Oberflächengüte: Wenn die gedruckte Rauheit nicht ausreicht (z. B. für bestimmte Wärmestrahlungseigenschaften, Abdichtung oder Ästhetik), ist eine Nachbearbeitung erforderlich. Zu den üblichen Methoden gehören Perlstrahlen (gleichmäßige matte Oberfläche), Trommeln, Bearbeiten oder Polieren (obwohl das Polieren großer, komplexer Abdeckungen schwierig und teuer sein kann). Bestimmte Beschichtungen können auch die Strahlungseigenschaften der Oberfläche verändern.
- Maßgenauigkeit:
- Definition: Die Gesamtkonformität des gedruckten Teils mit der im 3D-CAD-Modell definierten Sollgeometrie. Dies umfasst Toleranzen, berücksichtigt aber auch Formfehler wie Ebenheit, Rundheit und Verzug.
- Beeinflussende Faktoren: In erster Linie durch dieselben Faktoren beeinflusst, die die Toleranz beeinflussen (Maschinenkalibrierung, thermische Effekte, Materialschrumpfung, Stützen), aber auf einer globalen Teileskala betrachtet. Wärmemanagement während der Fertigung (z. B. beheizte Bauplatten, kontrollierte Kammertemperatur) und wirksame Spannungsentlastung sind entscheidend für die Minimierung von Verzug und die Gewährleistung einer guten Gesamtgenauigkeit, insbesondere bei großen Abdeckungen.
- Der Ansatz von Met3dp: Bei Met3dp setzen wir branchenführende Drucker ein, die für ihre Genauigkeit und Zuverlässigkeit bekannt sind. Unsere strenge Prozesskontrolle, unsere Kalibrierungsroutinen und unser Fachwissen im Bereich des Wärmemanagements während des Druckvorgangs zielen darauf ab, die erreichbare Maßgenauigkeit für anspruchsvolle Materialien wie IN625 und AlSi10Mg zu maximieren.
Inspektion und Metrologie für AM-Luftfahrtteile:
Die Überprüfung, ob die gedruckte und nachbearbeitete Wärmeschutzhülle den vorgegebenen Toleranzen, der Oberflächenbeschaffenheit und den Genauigkeitsanforderungen entspricht, ist ein entscheidender Qualitätssicherungsschritt.
- Koordinatenmessmaschinen (KMG): Messtaster bieten hochpräzise Messungen spezifischer Merkmale und Abmessungen, ideal für die Überprüfung kritischer Toleranzen an Schnittstellen nach der Bearbeitung.
- 3D-Scannen: Laser- oder strukturierte Lichtscanner erfassen die Gesamtgeometrie des Teils und ermöglichen den Vergleich mit dem ursprünglichen CAD-Modell (geometrische Bemaßung und Toleranzanalyse) sowie die Bewertung der Gesamtgenauigkeit und des Verzugs. Nützlich bei komplexen, durch Topologieoptimierung erzeugten Freiformflächen.
- Computertomographie (CT) Scannen: Verwendet Röntgenstrahlen, um eine 3D-Rekonstruktion des Teils zu erstellen, die die Messung interner Merkmale (z. B. Wandstärke interner Kanäle, Geometrie der Gitterstruktur) und die Erkennung interner Defekte (Porosität) ermöglicht, ohne das Teil zu zerstören. Zunehmend wichtig für die Qualifizierung komplexer AM-Bauteile.
- Oberflächenrauhigkeitsprüfgeräte (Profilometer): Messen Sie Ra oder andere Rauheitsparameter auf bestimmten Oberflächen.
- Konventionelle Werkzeuge: Messschieber, Mikrometer, Höhenmessgeräte für grundlegende Maßkontrollen.
Beschaffungsmanager sollten mit Lieferanten zusammenarbeiten, die über solide Messkapazitäten verfügen und umfassende Prüfberichte vorlegen können, die die Einhaltung der Zeichnungsspezifikationen dokumentieren. Diese Rückverfolgbarkeit ist für flugkritische Hardware unerlässlich. Die Zusammenarbeit mit einem qualitätsorientierten Unternehmen wie Met3dp stellt sicher, dass die notwendigen Investitionen in hochpräzise Ausrüstung und qualifiziertes Personal getätigt werden, um Teile zu liefern, die den strengen Anforderungen der Luft- und Raumfahrtindustrie entsprechen.
Tabelle: Typische, mit Metall-AM erreichbare Präzision (LPBF)
Parameter | Wie gedruckt Typischer Bereich | Erreichbar mit Nachbearbeitung | Faktoren & Überlegungen |
---|---|---|---|
Allgemeine Toleranz | ±0,1 mm bis ±0,3 mm (ISO 2768-m/f) | ±0,01 mm bis ±0,05 mm | Maschinenfähigkeit, Teilegröße, Material, Halterungen, Auswirkungen der Wärmebehandlung. |
Oberflächenrauhigkeit (Ra) | 6 µm – 20 µm | < 3,2 µm (bearbeitet) < 0,8 µm (poliert) | Ausrichtung, Parameter, Pulvergröße. Signifikante Verbesserung durch Nachbearbeitung. |
Min. Wanddicke | ~0,3 mm – 0,5 mm | K.A. | Prozessgrenzen, Maschinenauflösung, Fließfähigkeit des Materials. |
Min. Lochdurchmesser | ~0,5 mm | Kleiner durch Bohren möglich | Größe des Laserspots, Wärmeeinflusszone. |
Gesamtgenauigkeit | Gut, aber Verzug möglich | Hoch (begrenzt durch Bearbeitungseinstellungen) | Wärmemanagement und Spannungsabbau sind entscheidend für die Genauigkeit des Drucks. Die maschinelle Bearbeitung korrigiert bestimmte Bereiche. |
In Blätter exportieren
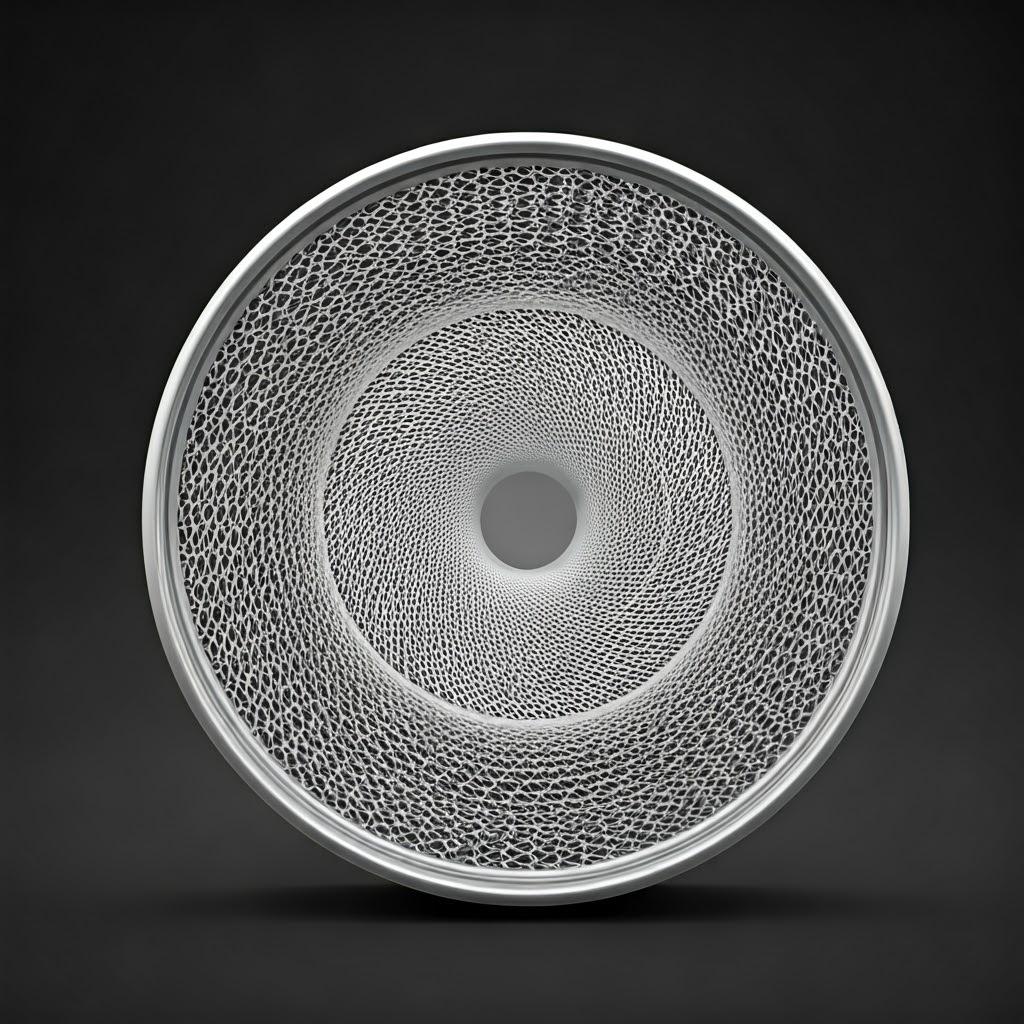
Jenseits des Drucks: Unverzichtbare Nachbearbeitung für weltraumtaugliche Leichentücher
Die Herstellung einer metallischen Wärmeschutzhülle mittels additiver Fertigung ist nur selten ein "Print and Ship"-Prozess, insbesondere bei anspruchsvollen Luft- und Raumfahrtanwendungen. Das gedruckte Teil ist zwar geometrisch komplex, erfordert aber in der Regel eine Reihe von nachfolgenden Nachbearbeitung schritte, um die erforderlichen Materialeigenschaften, Maßtoleranzen, Oberflächenmerkmale und die allgemeine Qualitätssicherung zu erreichen, die für Raumfahrthardware erforderlich sind. Diese Schritte sind integraler Bestandteil des Fertigungsablaufs und müssen bei der Produktionsplanung, den Vorlaufzeiten und den Kosten berücksichtigt werden. Das Verständnis dieser Prozesse ist sowohl für die Ingenieure, die das Teil entwerfen, als auch für die Beschaffungsmanager, die einen fähigen Hersteller auswählen, von entscheidender Bedeutung AM-Herstellungspartner.
Gemeinsame Nachbearbeitungsschritte für AM-Thermoabdeckungen:
- Pulverentfernung (Depowdering):
- Zielsetzung: Entfernen Sie alles ungeschmolzene Metallpulver, das sich im Inneren des Teils befindet, insbesondere aus internen Kanälen, Gitterstrukturen oder geschlossenen Hohlräumen.
- Methoden: Manuelles Bürsten, Absaugen, Abblasen mit Druckluft, Ultraschall-Reinigungsbäder, automatische Entleerungsstationen mit Vibration oder Flüssigkeitsstrom.
- Wichtigkeit: Pulverrückstände können zusätzliches Gewicht verursachen, bei der Wärmebehandlung versintern (wodurch sich die Abmessungen oder Eigenschaften ändern), zu losen Partikeln werden (ein kritisches Problem im Weltraum) oder nachfolgende Prozesse wie Beschichtung oder Prüfung beeinträchtigen. Die vollständige Entfernung ist von entscheidender Bedeutung, insbesondere bei komplexen Innengeometrien, die besondere konstruktive Überlegungen erfordern (z. B. Entwässerungslöcher), um die Reinigung zu erleichtern.
- Stressabbau:
- Zielsetzung: Reduzieren Sie die inneren Eigenspannungen, die während der schichtweisen Erwärmungs- und Abkühlungszyklen des AM-Prozesses entstehen. Diese Spannungen können Verwerfungen, Verformungen beim Entfernen von der Bauplatte oder sogar Risse verursachen, insbesondere bei Materialien mit hohem Wärmegradienten wie IN625.
- Methode: Erhitzen des Teils (oft noch auf der Bauplatte) in einem Ofen mit kontrollierter Atmosphäre auf eine bestimmte Temperatur (unterhalb der Alterungs- oder Glühtemperatur des Materials), Halten des Teils für einen bestimmten Zeitraum und anschließendes langsames Abkühlen. Die Parameter hängen stark vom Material (z. B. höhere Temperaturen für IN625 als für AlSi10Mg) und der Geometrie/Masse des Teils ab.
- Wichtigkeit: Dies ist oft der erste Schritt nach dem Drucken und Abkühlen. Er stabilisiert die Geometrie des Teils vor der weiteren Handhabung oder Bearbeitung und verringert das Risiko einer späteren Verformung oder eines Versagens.
- Wärmebehandlung (Lösungsglühen, Alterung usw.):
- Zielsetzung: Modifizierung der Mikrostruktur des Materials, um die gewünschten mechanischen Eigenschaften (Festigkeit, Duktilität, Härte, Ermüdungsfestigkeit) zu erreichen, die in den Konstruktionsanforderungen angegeben sind. Die gedruckten Mikrostrukturen unterscheiden sich oft erheblich von denen aus Knete oder Guss.
- Methoden: Spezifische thermische Zyklen, die in kalibrierten, atmosphärisch kontrollierten Öfen durchgeführt werden.
- Lösungsglühen: Löst Ausscheidungen auf und homogenisiert das Gefüge.
- Alterung (Ausscheidungshärtung): Fördert die Bildung von feinen Ausscheidungen, die das Material verstärken (z. B. beinhaltet der T6-Zustand für AlSi10Mg eine Lösungsglühung, gefolgt von einer künstlichen Alterung; IN625 kann je nach Anforderungen einer Lösungsglühung und möglicherweise einer Alterung unterzogen werden).
- Wichtigkeit: Dies ist von entscheidender Bedeutung, um sicherzustellen, dass die Ummantelung die Leistungsanforderungen erfüllt. Unterschiedliche Wärmebehandlungszyklen können bei ein und demselben gedruckten Teil zu sehr unterschiedlichen Eigenschaften führen. Erfordert Fachwissen in Werkstoffkunde und Prozesskontrolle.
- Entfernung der Stützstruktur:
- Zielsetzung: Entfernen Sie die temporären Strukturen, die zur Unterstützung von Überhängen und zur Verankerung des Teils auf der Bauplatte während des Drucks verwendet wurden.
- Methoden:
- Handbuch: Brechen oder Schneiden von Stützen mit Handwerkzeugen (möglich bei zugänglichen Stützen aus weicheren Materialien wie AlSi10Mg).
- Bearbeitungen: Durch CNC-Fräsen oder -Schleifen werden Stützen entfernt, was oft zu einer saubereren Oberfläche führt.
- Drahterodieren (Electrical Discharge Machining): Häufig bevorzugt für zähe Materialien wie IN625 oder für Stützen in schwer zugänglichen Bereichen, da sie einen präzisen Schnitt mit minimaler mechanischer Kraft ermöglicht.
- Wichtigkeit: Erforderlich für die endgültige Teilegeometrie. Kann zeit- und arbeitsintensiv sein, insbesondere bei komplexen Teilen oder zähen Materialien. Die Abtragsmethode beeinflusst die Oberflächengüte in den unterstützten Bereichen.
- Oberflächenveredelung:
- Zielsetzung: Modifizierung der Oberflächenrauheit im Druckzustand zur Erfüllung funktionaler Anforderungen (thermische Eigenschaften, Abdichtung), ästhetischer Anforderungen oder zur Vorbereitung nachfolgender Beschichtungen.
- Methoden (wie zuvor beschrieben):
- Gedruckte Oberflächen sind typischerweise rau und können teilsinterte Partikel zurückhalten. Verschiedene Techniken werden verwendet, um die gewünschte Oberfläche zu erzielen: Erzeugt eine gleichmäßige, saubere, matte Oberfläche. Entfernt kleinere Oberflächenfehler.
- Taumeln / Massenabfertigung: Glättet Außenkanten und Oberflächen durch Reibung mit dem Medium (weniger häufig bei großen/zarten Abdeckungen).
- CNC-Bearbeitung: Erzielt glatte, präzise Oberflächen an spezifischen Merkmalen (Schnittstellen, Dichtungsbereiche).
- Elektropolieren/Chemisches Polieren: Kann Oberflächen glätten, erfordert jedoch spezielle Elektrolyte/Chemikalien und Prozesskontrolle.
- Manuelle Endbearbeitung/Polieren: Arbeitsintensiv, typischerweise reserviert für sehr spezifische Anforderungen auf kleinen Flächen.
- Bearbeitung für kritische Abmessungen:
- Zielsetzung: Erzielen Sie enge Toleranzen bei bestimmten Merkmalen (z. B. Montagebohrungen, Schnittstellenebenen, Dichtungsnuten), die mit dem Druckverfahren allein nicht zuverlässig eingehalten werden können.
- Methode: Anwendung konventioneller CNC-Fräs-, Dreh-, Bohr- oder Schleifarbeiten am wärmebehandelten AM-Teil.
- Wichtigkeit: Gewährleistet die korrekte Passform und den Zusammenbau mit den entsprechenden Komponenten in der Struktur des Raumfahrzeugs oder der Trägerrakete. Erfordert eine sorgfältige Konstruktion der Halterung, um das potenziell komplexe AM-Teil genau zu halten.
- Beschichtung & Oberflächenbehandlungen:
- Zielsetzung: Aufbringen spezieller Oberflächenschichten zur Verbesserung der thermischen Eigenschaften (Emissivität, Absorptionsvermögen), zur Verbesserung der Korrosionsbeständigkeit, zur elektrischen Isolierung/Leitung oder zur Identifizierung.
- Methoden:
- Anstriche/Beschichtungen für die Luft- und Raumfahrt: Auftragen von qualifizierten Wärmeschutzbeschichtungen (z. B. weiße Farben wie SPU-787, Z-93 für Strahlungskühlung; schwarze Farben für Absorption). Erfordert eine sorgfältige Oberflächenvorbereitung.
- Eloxieren (für Aluminium): Erzeugt eine harte, korrosionsbeständige Oxidschicht. Kann zur Farbcodierung eingefärbt werden.
- Chemische Konversionsbeschichtungen (z. B. Alodine): Verbessert die Korrosionsbeständigkeit und die Lackhaftung auf Aluminium.
- Beschichtung (z. B. Nickel, Gold): Für besondere Anforderungen an die Leitfähigkeit oder das Reflexionsvermögen (weniger häufig für den Hauptabdeckungskörper).
- Wichtigkeit: Maßgeschneiderte Oberflächeninteraktion mit der thermischen Umgebung, die für die primäre Funktion der Abdeckungen entscheidend ist.
- Zerstörungsfreie Prüfung (NDT):
- Zielsetzung: Prüfen Sie das Teil auf innere und äußere Mängel (Risse, Porosität, Einschlüsse, fehlende Verschmelzung), ohne es zu beschädigen, um die strukturelle Integrität und Qualität zu gewährleisten.
- Methoden: Sichtprüfung (VT), Flüssigkeitseindringprüfung (LPT/DPT) für Oberflächenrisse, Magnetpulverprüfung (MPT – für ferromagnetische Materialien), Ultraschallprüfung (UT) für Fehler im Untergrund, Durchstrahlungsprüfung (RT – Röntgen) und Computertomographie (CT) für eine detaillierte Innenprüfung.
- Wichtigkeit: Obligatorisch für die Flugqualifikation in der Luft- und Raumfahrt. Die spezifischen ZfP-Anforderungen hängen von der Kritikalität des Teils ab und werden in der Regel durch Luft- und Raumfahrtnormen definiert (z. B. NASA, ESA, AS9100-Anforderungen).
Fähigkeit der Lieferanten:
Die erfolgreiche Durchführung dieser vielfältigen und oft komplexen Nachbearbeitungsschritte erfordert eine umfangreiche Infrastruktur, Spezialausrüstung (Öfen, CNC-Maschinen, Beschichtungsanlagen, NDT-Labors) und qualifiziertes Personal. Bei der Auswahl eines Lieferant für additive Fertigungdie Beschaffungsverantwortlichen müssen ihre Fähigkeiten (oder die ihrer qualifizierten Partner) über die gesamte erforderliche Nachbearbeitungskette hinweg überprüfen. Met3dp und sein Netzwerk sind in der Lage, diese kritischen Schritte zu bewältigen und einen nahtlosen Arbeitsablauf vom Pulver bis zum fertigen, raumtauglichen Wärmeschutzmantel zu gewährleisten.
Herausforderungen meistern: Überwindung von Hürden bei der additiven Fertigung von Wärmeschutzmänteln
Obwohl die additive Fertigung von Metallen für die Herstellung komplexer Komponenten wie Wärmeschutzschalen für die Luft- und Raumfahrt entscheidende Vorteile bietet, ist es wichtig, die potenziellen Herausforderungen dieser Technologie zu erkennen und zu bewältigen. Ein proaktiver Ansatz, der robuste DfAM-Praktiken, eine sorgfältige Prozesskontrolle und eine fortschrittliche Qualitätssicherung kombiniert, ist der Schlüssel zur Risikominimierung und zur erfolgreichen Produktion von zuverlässigen, leistungsstarken Teilen. Das Verständnis dieser allgemeinen Hürden hilft Ingenieuren und Beschaffungsmanagern, sich effektiver mit AM-Dienstleistungsbüros und komponentenhersteller.
Gemeinsame Herausforderungen und Abhilfestrategien:
- Eigenspannung, Verformung und Verzerrung:
- Herausforderung: Die schnelle, örtlich begrenzte Erwärmung und Abkühlung während des Schichtschmelzens erzeugt innere Spannungen. Wenn diese Spannungen die Streckgrenze des Materials überschreiten oder ungleichmäßig verteilt sind, können sie dazu führen, dass sich das Teil verzieht, verformt (insbesondere nach dem Entfernen von der Bauplatte) oder sogar reißt. Dies ist besonders häufig bei großen Teilen oder Materialien mit hoher Wärmeausdehnung wie IN625 der Fall.
- Strategien zur Schadensbegrenzung:
- Simulation: Verwenden Sie Prozesssimulationssoftware, um thermische Gradienten und Spannungsakkumulationen vorherzusagen, die als Grundlage für Konstruktionsänderungen (z. B. Hinzufügen von Spannungsentlastungsmerkmalen) und die Optimierung von Bauausrichtung und Stützstrukturen dienen.
- DfAM: Vermeiden Sie große, flache Abschnitte, die parallel zur Bauplatte verlaufen; verwenden Sie unterschiedliche Dicken; arbeiten Sie Rippen oder Riffelungen ein.
- Strategie aufbauen: Optimieren Sie Scanmuster (z. B. Insel-Scanning, Sektorisierung), um den Wärmeeintrag zu steuern. Vorheizen der Bauplatte oder -kammer (üblich bei EBM- und einigen LPBF-Systemen).
- Unterstützende Strukturen: Entwerfen Sie robuste Halterungen, um das Teil sicher zu verankern und den Verformungskräften während des Baus zu widerstehen.
- Sofortige Spannungsarmglühung nach dem Druck: Führen Sie einen thermischen Entlastungszyklus durch, bevor Sie das Teil von der Bauplatte nehmen, um innere Spannungen abzubauen.
- Porosität (Gas und Lack-of-Fusion):
- Herausforderung: Im gedruckten Material können sich kleine Hohlräume oder Poren bilden. Gasporosität entsteht durch gelöste Gase im Pulver oder Schutzgas, die während der Verfestigung eingeschlossen werden. Schmelzverluste entstehen, wenn die Energie nicht ausreicht, um Pulverpartikel oder aufeinanderfolgende Schichten vollständig zu schmelzen und zu verschmelzen. Porosität kann die mechanischen Eigenschaften (insbesondere die Ermüdungsfestigkeit) erheblich verschlechtern und als Rissauslöser dienen.
- Strategien zur Schadensbegrenzung:
- Hochwertiges Pulver: Verwenden Sie Pulver mit geringem internen Gasgehalt, kontrollierter Partikelgrößenverteilung und hoher Sphärizität (wie die von Met3dp’s fortschrittlicher Zerstäubung produzierten). Achten Sie auf die richtige Lagerung und Handhabung des Pulvers, um die Aufnahme von Feuchtigkeit zu vermeiden.
- Optimierung der Parameter: Stellen Sie die Prozessparameter (Laser-/Strahlleistung, Scangeschwindigkeit, Schraffurabstand, Schichtdicke) sorgfältig auf das jeweilige Material und die Maschine ein, um ein vollständiges Schmelzen und Verschmelzen zu gewährleisten. Verwenden Sie Daten von Schmelzbadüberwachungssystemen, falls vorhanden.
- Prozessumgebung: Sorgen Sie für eine hochreine Inertgasatmosphäre (Argon oder Stickstoff) in der Baukammer, um die Oxidation und Gasaufnahme zu minimieren.
- Heiß-Isostatisches Pressen (HIP): Ein Nachbearbeitungsschritt mit hoher Temperatur und Hochdruck-Inertgas. HIP kann innere Poren (sowohl Gas- als auch Schmelzfehler) wirksam schließen und so die Dichte und die mechanischen Eigenschaften erheblich verbessern. Es verursacht jedoch zusätzliche Kosten und Vorlaufzeiten und kann zu geringfügigen Maßveränderungen führen.
- Rissbildung (Verfestigungs- oder Verflüssigungsrissbildung):
- Herausforderung: Bestimmte Legierungen, insbesondere einige Nickelsuperlegierungen wie IN625, können unter bestimmten Bedingungen während der Erstarrung oder in der Wärmeeinflusszone aufgrund von thermischen Spannungen und Gefügeeffekten zu Rissen neigen.
- Strategien zur Schadensbegrenzung:
- Materialauswahl/Chemiekontrolle: Stellen Sie sicher, dass die Pulverchemie den Spezifikationen entspricht; einige Legierungsvarianten sind weniger anfällig für Risse.
- Optimierung der Parameter: Sorgfältige Kontrolle der Energiezufuhr und der Kühlleistung.
- Strategie aufbauen: Vorheizen, optimierte Scanmuster zur Minimierung von Wärmegradienten.
- Wärmebehandlung nach dem Drucken: Geeignete Wärmebehandlungen zum Spannungsabbau und zur Homogenisierung.
- Probleme bei der Entfernung von Stützstrukturen:
- Herausforderung: Das Entfernen von Halterungen kann schwierig, zeitaufwändig und kostspielig sein, insbesondere bei zähen Materialien (IN625), komplexen Geometrien oder internen Halterungen. Außerdem kann das Entfernen die Oberfläche des Teils beschädigen, wenn es nicht sorgfältig durchgeführt wird.
- Strategien zur Schadensbegrenzung:
- DfAM: Minimieren Sie den Bedarf an Stützen durch optimale Ausrichtung und selbsttragende Konstruktionsmerkmale (>45°-Winkel, Abschrägungen).
- Design unterstützen: Verwenden Sie spezielle Software, um Halterungen mit geeigneter Dichte, Perforation und leicht abbrechbaren Kontaktpunkten zu erstellen. Entwerfen Sie für Barrierefreiheit.
- Geeignete Entfernungstechniken: Wählen Sie das richtige Verfahren je nach Material und Geometrie (z. B. Drahterodieren für IN625 an engen Stellen).
- Einschränkungen der Oberflächenbeschaffenheit:
- Herausforderung: Die Rauheit der bedruckten Oberfläche entspricht möglicherweise nicht den Anforderungen an die Wärmestrahlung, die Dichtigkeit oder die aerodynamischen Eigenschaften. Die Oberflächen der Unterseite sind besonders rau.
- Strategien zur Schadensbegrenzung:
- Optimierung der Parameter: Die Feinabstimmung der Parameter kann geringfügige Verbesserungen bringen.
- Orientierungsstrategie: Richten Sie kritische Flächen nach Möglichkeit vertikal oder als Oberseite aus.
- Nachbearbeiten: Planen Sie die erforderlichen Schritte der Oberflächenbearbeitung (Strahlen, Bearbeiten, Beschichten) je nach Bedarf. Berücksichtigen Sie diese bei den Kosten und der Vorlaufzeit.
- Materialverschmutzung & Pulverhandhabung:
- Herausforderung: Eine Kreuzkontamination zwischen verschiedenen Metallpulvern kann die Chemie der Legierung verändern und die Eigenschaften verschlechtern. Reaktive Pulver (wie Aluminium- und Titanlegierungen) können empfindlich gegenüber Sauerstoff oder Feuchtigkeit sein.
- Strategien zur Schadensbegrenzung:
- Strenge Protokolle: Führen Sie strenge Verfahren für die Handhabung, Lagerung, Siebung und Be-/Entladung von Pulver ein. Verwenden Sie nach Möglichkeit spezielle Geräte für verschiedene Materialtypen.
- Atmosphärenkontrolle: Sicherstellung der Integrität des Inertgassystems im Drucker. Überwachen Sie den Sauerstoffgehalt.
- Lebenszyklusmanagement für Pulver: Verfolgen Sie den Pulververbrauch und die Recyclinghistorie, um die Qualität zu erhalten.
- Konsistenz, Wiederholbarkeit und Qualifizierung:
- Herausforderung: Für die Qualifizierung in der Luft- und Raumfahrt ist es von entscheidender Bedeutung, dass Teile, die in verschiedenen Fertigungsstätten, auf verschiedenen Maschinen oder zu verschiedenen Zeiten hergestellt wurden, dieselben Eigenschaften aufweisen und die Spezifikationen durchgängig erfüllen.
- Strategien zur Schadensbegrenzung:
- Robustes Qualitätsmanagementsystem (QMS): Implementierung und Einhaltung von Luft- und Raumfahrtstandards wie AS9100. Standardisieren Sie Arbeitsabläufe und Verfahren.
- Prozessüberwachung & Steuerung: Nutzen Sie die Überwachung des Schmelzepools, Sensordaten und statistische Prozesskontrolle (SPC), um die Konsistenz der Herstellung zu verfolgen.
- Kalibrierung und Wartung von Maschinen: Regelmäßige Kalibrierung und vorbeugende Wartung von AM-Systemen.
- Qualitätskontrolle des Pulvers: Konsistente Prüfung und Charakterisierung von eingehenden und recycelten Pulverchargen.
- Standardisierte Nachbearbeitung: Strenge Kontrolle der Parameter für Wärmebehandlung, Bearbeitung usw.
- Strenge Prüfung & Validierung: Entwicklung umfassender Prüfpläne (Materialcharakterisierung, zerstörungsfreie Prüfung, Funktionstests) zur Qualifizierung des Teils, des Materials und des Verfahrens.
Die Bewältigung dieser Herausforderungen erfordert ein tiefes Verständnis der Materialwissenschaft, der Physik des AM-Prozesses, der DfAM und der strengen Qualitätskontrolle. Die Zusammenarbeit mit einem erfahrenen und gut ausgerüsteten anbieter für die additive Fertigung von Metallen wie Met3dp, die nicht nur über fortschrittliche Ausrüstung, sondern auch über technisches Fachwissen und robuste Qualitätssysteme verfügt, ist der effektivste Weg für oEMs der Luft- und Raumfahrtindustrie, systemintegratorenund beschaffungsspezialisten um diese Komplexität zu bewältigen und AM erfolgreich für anspruchsvolle Anwendungen wie Wärmeschutzabdeckungen zu nutzen.
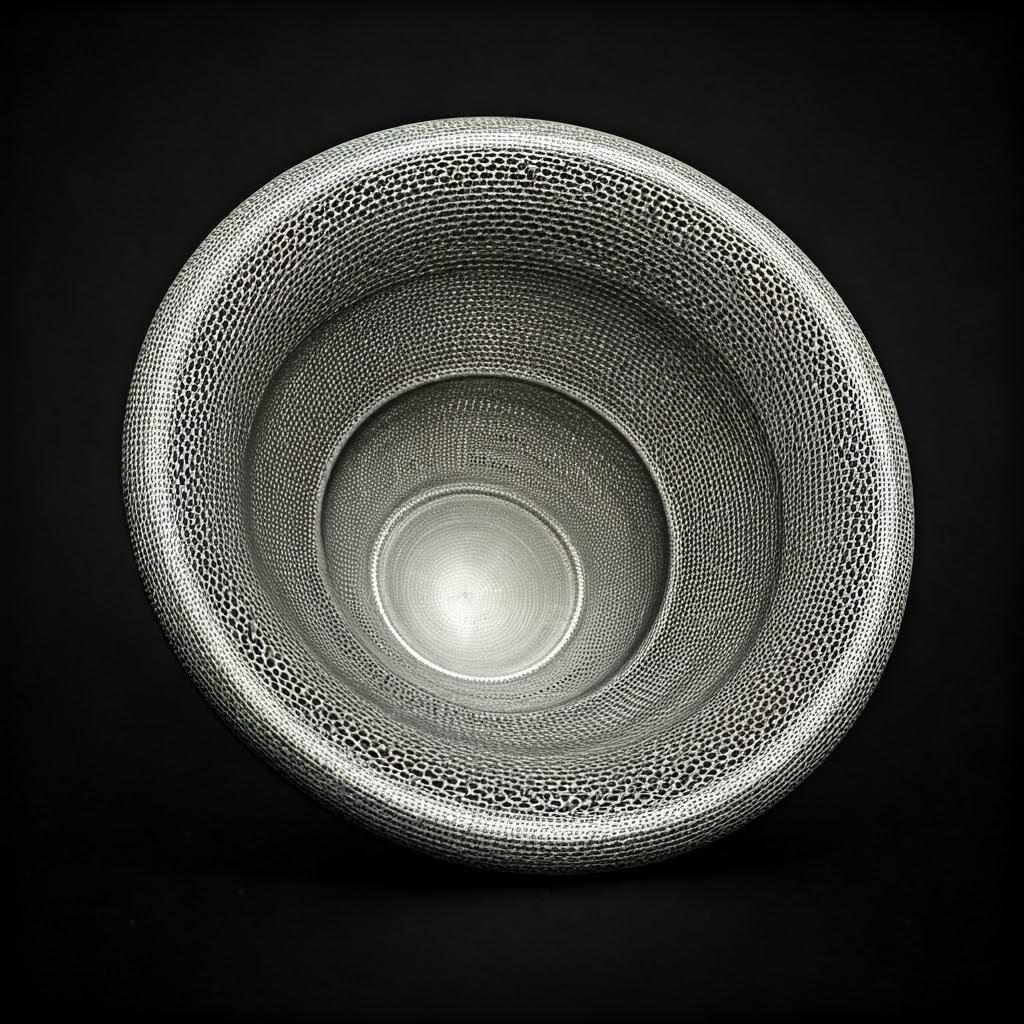
Partnerschaften für den Erfolg: Wie Sie den richtigen Metall-AM-Dienstleister auswählen
Die Auswahl eines Fertigungspartners für kritische Luft- und Raumfahrtkomponenten wie Wärmeschutzmäntel geht über eine einfache Transaktionsbeziehung hinaus. Es gilt, einen Anbieter mit der richtigen Mischung aus technischem Know-how, robusten Qualitätssystemen, einschlägiger Erfahrung und einem kooperativen Ansatz zu finden. Die einzigartigen Anforderungen der additiven Fertigung in Verbindung mit den strengen Anforderungen der Raumfahrtindustrie machen diesen Auswahlprozess zu einem entscheidenden Faktor für den Missionserfolg. Ingenieure und Beschaffungsmanager müssen eine gründliche Due-Diligence-Prüfung durchführen, um sicherzustellen, dass die gewählte Metall-AM-Dienstleister oder Lieferant für additive Fertigung kann zuverlässig hochwertige, weltraumtaugliche Hardware liefern.
Schlüsselkriterien für die Bewertung von Metall-AM-Anbietern für Luft- und Raumfahrtkomponenten:
- Luft- und Raumfahrtexpertise & Zertifizierungen:
- Erfolgsbilanz: Hat der Anbieter nachweislich Erfahrung in der Herstellung von Komponenten für Luft- und Raumfahrt- oder Verteidigungsanwendungen? Kann er relevante (nicht vertrauliche) Fallstudien oder Referenzen nennen?
- Zertifizierungen: Der Besitz einschlägiger Zeugnisse ist oft nicht verhandelbar. Suchen Sie nach:
- AS9100: Der international anerkannte Standard für Qualitätsmanagementsysteme (QMS) für die Luft-, Raumfahrt- und Verteidigungsindustrie. Dies bedeutet eine Verpflichtung zu strenger Prozesskontrolle, Rückverfolgbarkeit, Risikomanagement und kontinuierlicher Verbesserung, die auf die Anforderungen der Luft- und Raumfahrt zugeschnitten ist.
- ISO 9001: Eine grundlegende QMS-Zertifizierung, aber AS9100 ist spezifischer und anspruchsvoller für die Luft- und Raumfahrt.
- ITAR/EAR-Konformität: Wenn das Projekt Verteidigungsgüter oder kontrollierte Technologie gemäß den US-Vorschriften (International Traffic in Arms Regulations / Export Administration Regulations) betrifft, muss der Anbieter registriert sein und die Vorschriften einhalten.
- Vertrautheit mit Normen: Erfahrung in der Arbeit mit NASA-, ESA- und MIL-STD-Normen oder spezifischen Anforderungen von Hauptauftragnehmern ist von großem Vorteil.
- Materialfähigkeiten & Fachwissen:
- Spezifische Materialerfahrung: Tiefgreifende Erfahrung in der Verarbeitung der benötigten Materialien (z. B. IN625, AlSi10Mg) mit der gewählten AM-Technologie (LPBF, EBM). Dazu gehören etablierte, validierte Parametersätze und das Verständnis für materialspezifische Herausforderungen (z. B. Spannungsmanagement bei IN625, Wärmebehandlung bei AlSi10Mg).
- Pulverbeschaffung & Qualität: Robuste Verfahren für die Beschaffung von hochwertigen Metallpulvern in Luft- und Raumfahrtqualität. Strenge Eingangskontrolle, ordnungsgemäße Lagerung, Handhabung und Rückverfolgbarkeit (Chargenverfolgung). Fähigkeit, die Wiederverwendung und das Recycling von Pulver nach validierten Verfahren zu verwalten, um die Qualität zu erhalten.
- Eigene Pulverproduktion: Anbieter wie Met3dp, die ihre eigenen Hochleistungsmetallpulver mit fortschrittlichen Techniken wie Gaszerstäubung und PREP herstellen, bieten eine zusätzliche Ebene der Qualitätskontrolle und Materialkonsistenz, die sich direkt auf die Integrität des endgültigen Teils auswirken.
- Technologie & Ausrüstung:
- Prozess-Eignung: Bieten sie das am besten geeignete AM-Verfahren an (z. B. LPBF für feine Merkmale und Oberflächengüte, EBM für bestimmte Materialien wie Ti6Al4V oder für reduzierte Eigenspannungen)?
- Fähigkeiten der Maschine: Beurteilen Sie das Bauvolumen (kann es die Größe der Ummantelung aufnehmen?), die Maschinengenauigkeit, die verfügbare Laser-/Strahlleistung, die Möglichkeiten der Schichtdicke und die prozessbegleitenden Überwachungssysteme (z. B. Schmelzbadüberwachung, Wärmebildtechnik), die die Qualitätssicherung verbessern.
- Wartung & Kalibrierung von Geräten: Nachweis von regelmäßigen Wartungsplänen und Kalibrierungsroutinen für Drucker, Öfen und Messgeräte.
- Technik & DfAM-Unterstützung:
- Anwendungstechnik: Verfügbarkeit von erfahrenen Ingenieuren, die an der Designoptimierung mitarbeiten, DfAM-Anleitungen geben, Fertigungssimulationen (Wärme, Spannung, Verformung) durchführen, bei der Materialauswahl beraten und bei der Behebung von Fertigungsproblemen helfen können.
- Kollaborativer Ansatz: Bereitschaft zur engen Zusammenarbeit mit Ihrem Entwicklungsteam bereits in der Anfangsphase, um die Herstellbarkeit zu gewährleisten und Leistung und Kosten zu optimieren.
- Umfassende Nachbearbeitungsmöglichkeiten:
- Integrierter Arbeitsablauf: Im Idealfall sollte der Anbieter eine breite Palette der erforderlichen Nachbearbeitungsschritte intern oder über ein engmaschiges Netz qualifizierter Partner anbieten. Dazu gehören Spannungsabbau, Wärmebehandlung (mit zertifizierten Öfen und Atmosphärenkontrolle), Entfernen von Halterungen, CNC-Bearbeitung, verschiedene Optionen der Oberflächenveredelung, Auftragen von Beschichtungen (einschließlich weltraumtauglicher thermischer Beschichtungen) und umfassende zerstörungsfreie Prüfung.
- Stufenübergreifende Qualitätskontrolle: Es ist von entscheidender Bedeutung, dass die Qualität und Rückverfolgbarkeit während der gesamten Nachbearbeitungskette gewährleistet ist.
- Robustes Qualitätsmanagementsystem (QMS):
- Jenseits der Zertifizierung: Schauen Sie über das Zertifikat hinaus. Beurteilen Sie den Reifegrad ihres QMS. Erkundigen Sie sich nach den Verfahren zur Änderungskontrolle, zum Management von Nichtkonformitäten, zu Korrektur-/Vorbeugungsmaßnahmen, zum Risikomanagement und zur Schulung der Mitarbeiter.
- Dokumentation und Rückverfolgbarkeit: Fähigkeit zur Bereitstellung vollständiger Dokumentationspakete, einschließlich Materialzertifikaten, Fertigungsprotokollen, Prozessparametern, Wärmebehandlungsprotokollen, Maßprüfungsberichten und NDT-Ergebnissen. Eine vollständige Rückverfolgbarkeit von der Pulvercharge bis zum fertigen Teil ist unerlässlich.
- Metrologie-Fähigkeiten: Interner Zugang zu geeigneten Messgeräten (CMM, 3D-Scanner, Oberflächenprofilometer) und qualifiziertem Messpersonal.
- Kapazität, Skalierbarkeit & Redundanz:
- Die Nachfrage befriedigen: Können sie die von Ihnen benötigten Mengen (Prototypen, Kleinserien) innerhalb akzeptabler Vorlaufzeiten herstellen? Verfügen sie über ausreichende Maschinenkapazitäten?
- Skalierbarkeit: Hat der Anbieter Pläne oder Möglichkeiten, die Produktion zu erweitern, falls der Bedarf in Zukunft steigen sollte?
- Redundanz: Mehrere Maschinen, die denselben Prozess bzw. dasselbe Material verarbeiten können, sorgen für Redundanz und vermindern die Risiken, die mit einem Ausfall der Anlagen verbunden sind.
- Vorlaufzeit, Kommunikation & Reaktionsfähigkeit:
- Realistische Zeitpläne: Fähigkeit, klare, realistische Vorlaufzeitschätzungen zu geben, die alle Produktionsschritte, einschließlich möglicher Warteschlangen und Nachbearbeitungen, berücksichtigen.
- Kommunikation: Proaktive Kommunikation über den Projektstatus, mögliche Probleme und technische Fragen. Festgelegte Kontaktstellen.
- Reaktionsfähigkeit: Rechtzeitige Beantwortung von Angebotsanfragen (RFQs) und technischen Anfragen.
- Kostentransparenz & Gesamtwert:
- Eindeutig zitieren: Detaillierte Kostenvoranschläge, die die Kostenfaktoren aufschlüsseln.
- Wert-Angebot: Auch wenn die Kosten wichtig sind, sollten Sie sich auf das gesamte Wertangebot konzentrieren, einschließlich Qualität, Zuverlässigkeit, technische Unterstützung, pünktliche Lieferung und Risikominderung. Die billigste Option bietet möglicherweise nicht die erforderliche Qualität oder Zuverlässigkeit für Hardware in der Luft- und Raumfahrt.
Met3dp verkörpert viele dieser wesentlichen Eigenschaften. Mit unserem auf AS9100 ausgerichteten Fokus, integrierter hochwertiger Pulverherstellung, fortschrittlichen Druckverfahren einschließlich SEBM- und LPBF-Systemen, engagierter technischer Unterstützung und der Verpflichtung zu strenger Qualitätskontrolle positionieren wir uns als zuverlässiger Partner für anspruchsvolle Luft- und Raumfahrtanwendungen. Wir verstehen die kritische Natur von Komponenten wie Wärmeschutzmänteln und arbeiten zusammen mit oEMs der Luft- und Raumfahrtindustrie, Tier-1-Lieferantenund Beschaffungsteams um Lösungen zu liefern, die den höchsten Ansprüchen an Leistung und Zuverlässigkeit gerecht werden.
Tabelle: Checkliste zur Lieferantenbewertung für AM-Thermoabdeckungen
Kriterien | Wichtige Überlegungen | Met3dp-Ausrichtung |
---|---|---|
Erfahrung/Zertifizierungen in der Luft- und Raumfahrt | AS9100? Erfahrung mit Raumfahrtprojekten? Vertrautheit mit Normen (NASA/ESA)? ITAR? | Schwerpunkt Luft- und Raumfahrt, AS9100-konformes QMS, Erfahrung mit anspruchsvollen Anwendungen. |
Materialeigenschaften | IN625/AlSi10Mg Gutachten? Validierte Parameter? Qualitätskontrolle des Pulvers? Beschaffung/Handhabung des Pulvers? | Fachwissen über Legierungen für die Luft- und Raumfahrt, eigene Herstellung von hochreinem Pulver (Gaszerstäubung, PREP), strenge Qualitätskontrolle. |
Technologie & Ausstattung | Geeignetes Verfahren (LPBF/EBM)? Bauvolumen? Genauigkeit? Überwachung? Wartung? | Hochmoderne SEBM- und LPBF-Drucker, branchenführende Volumen/Genauigkeit, Prozessüberwachung. |
Technik & DfAM-Unterstützung | Anwendungsingenieure verfügbar? DfAM-Anleitung? Simulation? Kollaboration? | Ein engagiertes Ingenieurteam bietet umfassenden Support und DfAM-Fachwissen. |
Nachbearbeitung | Eigenes/verwaltetes Netzwerk für Spannungsarmglühen, Wärmebehandlung, Bearbeitung, Endbearbeitung, Beschichtung, NDT? | Bietet oder verwaltet die erforderlichen Nachbearbeitungsschritte über qualifizierte Kanäle. |
Qualitätsmanagement-System (QMS) | Ausgereiftes QMS? Dokumentation/Rückverfolgbarkeit? Metrologische Fähigkeiten? Risikomanagement? | Robustes QMS, vollständige Rückverfolgbarkeit, fortschrittliche Messtechnik, Fokus auf Prozesskontrolle. |
Kapazität & Skalierbarkeit | Bewältigung des erforderlichen Volumens? Redundanz? Skalierbarkeitspläne? | Kapazität für Prototyping und Kleinserienproduktion, skalierbare Lösungen. |
Vorlaufzeit & Kommunikation | Realistische Kostenvoranschläge? Pünktliche Lieferung? Proaktive Kommunikation? | Bemüht sich um eine klare Kommunikation und verlässliche Lieferzeiten. |
Kosten und Wert | Transparente Preisgestaltung? Fokus auf Qualität und Zuverlässigkeit vs. niedrigste Kosten? | Wettbewerbsfähige Preise mit Schwerpunkt auf der Lieferung hochwertiger, zuverlässiger Komponenten. |
In Blätter exportieren
Entmystifizierung der Kosten: Preisfaktoren und Vorlaufzeiten in der AM verstehen
Eine der häufigsten Fragen von Ingenieuren und Beschaffungsverantwortlichen, die sich mit der additiven Fertigung von Metallen befassen, betrifft die Kostenstruktur und die voraussichtlichen Lieferfristen. AM bietet zwar erhebliche Vorteile, aber die Kostentreiber und Vorlaufzeitkomponenten unterscheiden sich von den traditionellen Fertigungsmethoden. Das Verständnis dieser Faktoren ist entscheidend für eine genaue Budgetierung, Projektplanung und den Vergleich von AM mit Alternativen für die Produktion von thermischen Abdeckungen.
Aufschlüsselung der Kosten für 3D-gedruckte Wärmeschutzhüllen:
Der Endpreis eines 3D-gedruckten Wärmeschutzes wird durch eine Kombination von Faktoren beeinflusst, von denen einige nur bei additiven Verfahren auftreten:
- Materialkosten:
- Pulver Preis: Die Kosten pro Kilogramm des gewählten Metallpulvers sind ein wichtiger Faktor. Hochleistungslegierungen wie IN625 sind erheblich teurer als Aluminiumlegierungen wie AlSi10Mg oder Standardstähle. Für Pulver in Luft- und Raumfahrtqualität mit strengen Qualitätskontrollen wird ein Aufpreis verlangt.
- Materialverbrauch: Dazu gehört auch das Volumen des letzten Teils plus das Volumen der erforderlichen Stützstrukturen. Ein effizientes Design (DfAM) und eine optimierte Ausrichtung können das Volumen der Stützen und damit den Materialverbrauch minimieren.
- Pulver-Recycling: Die effiziente Wiederverwendung von ungesintertem Pulver trägt zur Kostensenkung bei, erfordert aber ein sorgfältiges Management, um die Qualität zu erhalten. Die effektiven Materialkosten beinhalten die Amortisation der Pulverabnutzung über mehrere Zyklen.
- Maschinenzeit (Bauzeit):
- Beherrschender Faktor: Oftmals der größte Einzelposten bei den Kosten. Dieser wird in der Regel auf der Grundlage eines Stundensatzes für die jeweilige AM-Maschine berechnet, der Abschreibung, Wartung, Energie, Verbrauchsmaterial (Filter, Schutzgas) und Aufsicht durch den Bediener abdeckt.
- Einflüsse:
- Teil Volumen/Höhe: Höhere Teile brauchen länger zum Drucken, was sich direkt auf die Maschinenzeit auswirkt. Größere Volumen erfordern auch mehr Scans pro Schicht.
- Komplexität: Sehr komplizierte Designs oder umfangreiche Gitterstrukturen können komplexere Scanpfade und möglicherweise längere Druckzeiten pro Schicht erfordern.
- Nesting-Effizienz: Durch den gleichzeitigen Druck mehrerer Teile in einem Bauprozess (Verschachtelung) amortisieren sich die Rüst- und Abkühlzeiten auf mehrere Teile, wodurch die Kosten für die Maschinenzeit pro Teil sinken. Die Dichte der Bauplatte ist entscheidend.
- Schichtdicke: Dünnere Schichten bieten eine bessere Auflösung und Oberflächengüte, erhöhen aber die Gesamtzahl der Schichten und damit die Bauzeit.
- Maschinentyp: Verschiedene Maschinen (LPBF vs. EBM, bestimmte Modelle) haben unterschiedliche Baugeschwindigkeiten und Betriebskosten.
- Arbeitskosten:
- Einrichtung aufbauen: Vorbereitung der Bauakte (Ausrichtung, Stützen), Laden des Pulvers, Einrichten der Maschine.
- Handhabung des Pulvers: Be- und Entladen, Sieben und Verwalten des Pulverbestands.
- Nachbearbeiten: Dies kann sehr arbeitsintensiv sein, insbesondere für:
- Unterstützung bei der Entfernung: Manuelle Entnahme, vor allem bei zähen Materialien oder komplexen inneren Stützen.
- Oberflächenveredelung: Manuelle Endbearbeitung, Polieren, Abdecken für Beschichtungen.
- Inspektion: Manuelle Sicht- und Maßkontrollen.
- Technische Unterstützung: Zeit, die von Anwendungsingenieuren für DfAM, Simulation oder technische Beratung aufgewendet wird, wenn sie separat in Rechnung gestellt wird.
- Nachbearbeitungskosten:
- Ausrüstung & Verbrauchsmaterial: Kosten im Zusammenhang mit dem Betrieb von Öfen für Spannungsabbau/Wärmebehandlung (Energie, kontrollierte Atmosphäre), CNC-Maschinen (Werkzeugverschleiß, Kühlmittel), Strahlmittel, Beschichtungsmaterialien, Verwendung von ZfP-Ausrüstung und Verbrauchsmaterialien (Eindringmittel, Film).
- Spezialisierte Dienstleistungen: Gebühren für ausgelagerte Verfahren wie HIP, Spezialbeschichtungen oder fortgeschrittene zerstörungsfreie Prüfungen, wenn sie nicht im eigenen Haus durchgeführt werden.
- Qualitätssicherung und Inspektion:
- Metrologie: Zeit und Ressourcen für CMM-Messungen, 3D-Scannen, Berichterstellung.
- ZFP: Kosten für die Durchführung der erforderlichen zerstörungsfreien Prüfungen und die Interpretation der Ergebnisse durch zertifiziertes Personal.
- Dokumentation: Zeitaufwand für die Erstellung umfassender Qualitätsdokumentationspakete, die für Luft- und Raumfahrtkomponenten erforderlich sind.
- Design & Technik:
- Wenn der Dienstleister im Rahmen des Projekts umfangreiche DfAM-Arbeiten, Topologieoptimierungen oder Prozesssimulationen durchführt, können diese Kosten für Ingenieurleistungen einbezogen werden.
- Menge:
- Amortisation: Die Rüstkosten (Bauvorbereitung, Maschineneinrichtung) werden über die Anzahl der Teile in einem Bau amortisiert. Höhere Stückzahlen führen im Allgemeinen zu einem niedrigeren Preis pro Teil.
- Keine Werkzeuge: Im Gegensatz zum Spritzgießen oder Gießen fallen bei AM keine hohen Vorlaufkosten für Werkzeuge an, was es für kleine bis mittlere Stückzahlen und Prototypen kosteneffizient macht. Allerdings ist die Kostenreduzierung pro Teil mit der Menge in der Regel weniger dramatisch als bei Massenproduktionsverfahren, bei denen der Werkzeugbau dominiert.
Verständnis der Vorlaufzeiten:
Die Vorlaufzeit - die Dauer von der Auftragserteilung bis zur Auslieferung des Teils - ist ein weiterer wichtiger Aspekt. Sie ist oft viel kürzer als bei traditionellen Methoden mit komplexem Werkzeugbau, aber es geht um mehr als nur um die Druckzeit.
Komponenten der AM-Vorlaufzeit:
- Vorverarbeitung (1-5+ Tage):
- Angebotserstellung und Auftragsbestätigung: Erstprüfung, Angebotserstellung, Auftragsabwicklung.
- Technische Überprüfung: DfAM-Prüfungen, Herstellbarkeitsanalyse, Simulation (falls erforderlich).
- Vorbereitung des Baus: Dateivorbereitung (Support-Generierung, Slicing), Terminierung des Auftrags auf einer Maschine.
- Maschinenwarteschlange (Variabel: 0 Tage – 2+ Wochen):
- Wartezeit, bis eine geeignete Maschine zur Verfügung steht. Dies kann je nach Arbeitsbelastung und Kapazität des Dienstleisters eine erhebliche Variable sein.
- Druckzeit (Stunden bis mehrere Tage):
- Die tatsächliche Zeit, in der das Teil Schicht für Schicht aufgebaut wird. Sie hängt in hohem Maße von der Höhe des Teils, dem Volumen und der Anzahl der Teile ab, die im Bauprozess verschachtelt werden. Der Druck einer komplexen Wärmeabschirmung kann 24-72 Stunden oder länger dauern.
- Abkühlzeit (mehrere Stunden bis über Nacht):
- Die Baukammer und die Teile müssen ausreichend abkühlen, bevor der Bau sicher entfernt und ausgepackt werden kann.
- Nachbearbeitung (variabel: 2 Tage – 2+ Wochen):
- Diese Reihenfolge bestimmt häufig die Gesamtdurchlaufzeit nach dem Druck.
- Erleichterung & Stressabbau: Es kann relativ schnell gehen (Stunden bis 1 Tag).
- Wärmebehandlung: Die Zyklen in den Öfen können viele Stunden oder Tage dauern, einschließlich des Hochfahrens, der Einweichzeit und der kontrollierten Abkühlung.
- Entfernen von Stützen & Bearbeitung: Je nach Komplexität und Material sehr unterschiedlich (Stunden bis Tage).
- Endbearbeitung/Beschichtung: Hängt von dem jeweiligen Verfahren ab (Stunden bis Tage).
- ZfP und Inspektion: Abhängig von der erforderlichen Stufe (Stunden bis Tage).
- Logistik: Transport von Teilen zwischen verschiedenen Verarbeitungsschritten (z. B. zu externen Partnern zur Beschichtung oder HIP).
- Versand (1-5+ Tage):
- Transitzeit zum Standort des Kunden.
Typische Reichweiten:
- Prototypen: Die Lieferung erfolgt oft innerhalb von 1 bis 4 Wochen, vorausgesetzt, es steht ausreichend Maschinenzeit zur Verfügung und es erfolgt eine Standardnachbearbeitung.
- Produktionsteile: Die Vorlaufzeiten liegen in der Regel zwischen mehreren Wochen und einigen Monaten, vor allem, wenn umfangreiche Nachbearbeitungen, Qualifikationstests oder große Mengen erforderlich sind.
Optimierung der Kosten und der Vorlaufzeit:
Eine enge Zusammenarbeit mit Ihrem AM-Anbieter ist entscheidend. Das Design für AM (Minimierung der Stützen, Optimierung der Topologie), die Wahl des richtigen Materials für die Anforderungen (Vermeidung von Überspezifikationen), die effektive Verschachtelung von Teilen und die klare Definition von Akzeptanzkriterien im Vorfeld können dazu beitragen, den Prozess zu optimieren. Anbieter wie Met3dp bemühen sich um die Optimierung interner Arbeitsabläufe und bieten eine transparente Kommunikation in Bezug auf Kosten und realistische Vorlaufzeiten für komplexe Projekte wie Wärmehüllen für die Luft- und Raumfahrt.
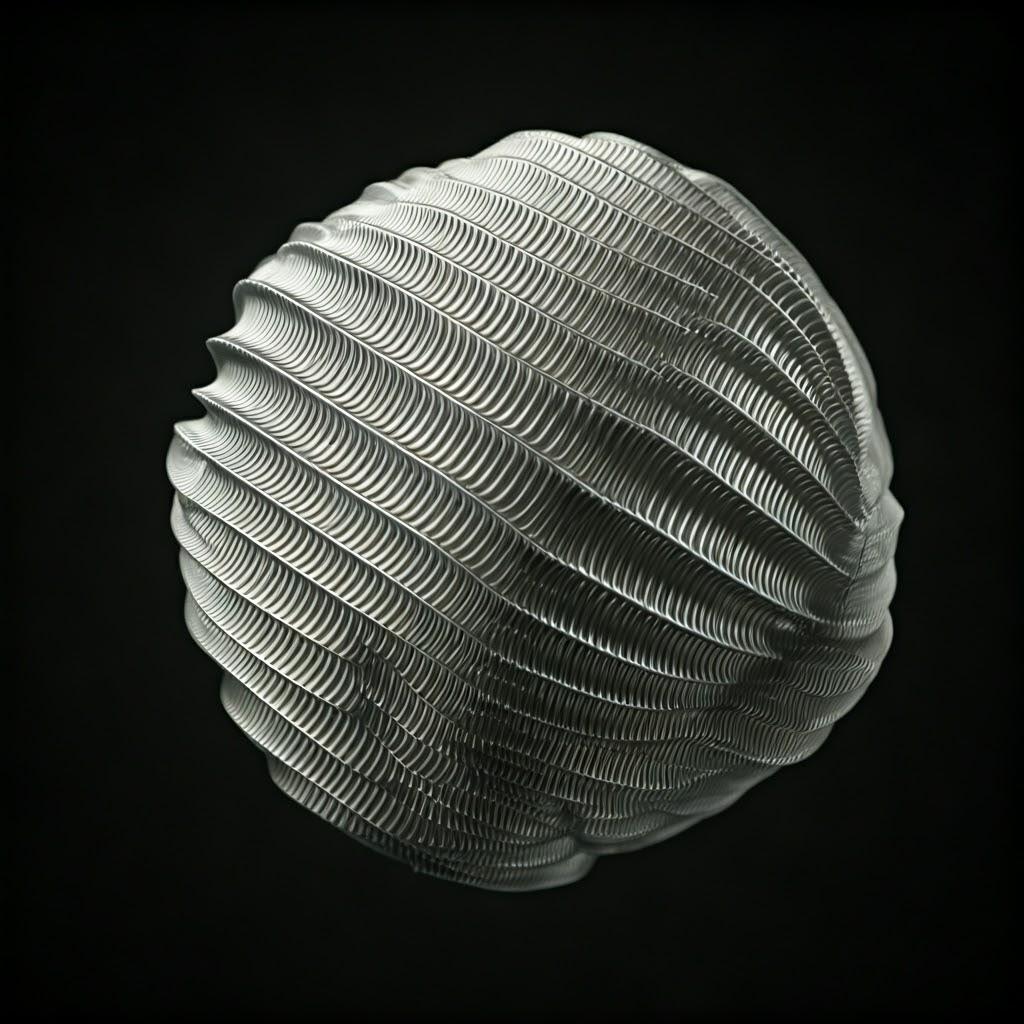
Häufig gestellte Fragen (FAQ) zu 3D-gedruckten Wärmeschutzmänteln
Hier finden Sie Antworten auf einige häufig gestellte Fragen von Ingenieuren und Beschaffungsexperten zum Einsatz der additiven Fertigung von Metall für Wärmeschutzschalen in der Luftfahrt:
F1: Wie sind die mechanischen Eigenschaften von 3D-gedrucktem IN625 und AlSi10Mg im Vergleich zu herkömmlichen Knet- oder Gusswerkstoffen?
A: Bei korrekter Verarbeitung und geeigneten Wärmebehandlungen nach dem Druck können die mechanischen Eigenschaften (wie Zugfestigkeit und Streckgrenze) von AM IN625 und AlSi10Mg sehr wettbewerbsfähig sein und oft denen von Gussäquivalenten entsprechen oder diese sogar übertreffen. Sie können sich den Eigenschaften von Knetwerkstoffen annähern, insbesondere in bestimmten Orientierungen relativ zur Baurichtung. Die Eigenschaften können jedoch manchmal eine Anisotropie aufweisen (je nach Messrichtung - X, Y oder Z relativ zur Fertigungsrichtung - leicht unterschiedlich). Ermüdungseigenschaften und Duktilität hängen in hohem Maße davon ab, dass eine nahezu vollständige Dichte (Minimierung der Porosität durch Parameteroptimierung oder HIP) und eine angemessene Wärmebehandlung erreicht wird. Umfassende Materialcharakterisierung und Bauteilprüfungen sind für die Qualifizierung in der Luft- und Raumfahrt unerlässlich, um zu bestätigen, dass die Eigenschaften den Konstruktionsanforderungen entsprechen.
F2: Wie groß darf ein 3D-gedruckter Wärmeschutzmantel maximal sein?
A: Die maximale Größe eines einzelnen Stücks wird durch das Bauvolumen der verfügbaren Metall-AM-Maschinen bestimmt. Führende industrielle LPBF- und EBM-Systeme bieten Bauumfänge von über 500 mm x 500 mm x 500 mm (etwa 20 x 20 x 20 Zoll), wobei einige spezialisierte Systeme sogar noch größer sind. Bei Abdeckungen, die diese Abmessungen überschreiten, besteht ein gängiger Ansatz darin, das Bauteil in mehreren Abschnitten zu drucken, die nach dem Druck zusammengefügt werden sollen, in der Regel durch Schweißen oder spezielle Befestigungsmethoden. Die Durchführbarkeit der Abschnittsbildung hängt von der Konstruktion und den strukturellen/thermischen Anforderungen an den Verbindungsstellen ab.
F3: Ist der 3D-Metalldruck für thermische Abdeckungen im Vergleich zur herkömmlichen Fertigung wirklich kostengünstig?
A: Die Wirtschaftlichkeit hängt stark von mehreren Faktoren ab:
- Komplexität: AM eignet sich hervorragend und ist oft kostengünstiger für hochkomplexe Geometrien, integrierte Merkmale oder topologieoptimierte Designs, die sich nur schwer oder gar nicht bearbeiten oder formen lassen.
- Lautstärke: AM ist im Allgemeinen am kosteneffizientesten für Prototypen, kleine bis mittlere Produktionsmengen (typisch für viele Raumfahrtkomponenten) und kundenspezifische Teile, da keine Werkzeugkosten anfallen. Bei sehr einfachen Formen, die in hohen Stückzahlen benötigt werden, können herkömmliche Methoden wie Stanzen oder Hochgeschwindigkeitsbearbeitung mit der Zeit pro Teil billiger werden, aber der Break-even-Punkt kann recht hoch sein.
- Vorlaufzeit: Wenn die schnelle Herstellung von Prototypen oder eine kürzere Entwicklungszeit entscheidend ist, kann der Geschwindigkeitsvorteil von AM einen erheblichen Wert darstellen, auch wenn die Kosten pro Teil etwas höher sind.
- Teil Konsolidierung: Wenn AM die Konsolidierung mehrerer traditionell getrennter Teile zu einem einzigen ermöglicht, können die Einsparungen bei der Montagearbeit, den Verbindungselementen und der Lagerverwaltung AM äußerst kosteneffizient machen.
- Materialabfälle: Bei teuren Materialien wie IN625 kann der deutlich geringere Materialabfall (Buy-to-Fly-Ratio) bei AM im Vergleich zur subtraktiven Bearbeitung zu erheblichen Kosteneinsparungen führen.
F4: Welcher Grad an zerstörungsfreier Prüfung (NDT) ist für 3D-gedruckte Wärmeschutzabdeckungen für die Raumfahrt normalerweise erforderlich?
A: Die Anforderungen an die zerstörungsfreie Prüfung richten sich nach der Kritikalität der Komponente, die in der Regel durch Missionssicherheits- oder Klassifizierungsstufen (z. B. NASA-Klasse A/B/C/D) definiert ist. Für kritische thermische Abdeckungen (z. B. zum Schutz empfindlicher Instrumente oder wichtiger Systeme) ist eine umfassende ZfP-Suite üblich. Dazu gehören häufig:
- Visuelle Prüfung (VT): Für äußere Oberflächenfehler.
- Prüfung der Abmessungen: Überprüfung der kritischen Toleranzen (CMM, 3D-Scan).
- Flüssigkeitseindringprüfung (LPT / DPT): Zur Erkennung von Rissen in der Oberfläche.
- Röntgenuntersuchung (RT) oder Computertomographie (CT): Unverzichtbar für die Erkennung interner Defekte wie Porosität, Einschlüsse oder fehlende Verschmelzung, insbesondere bei Teilen der Klasse A/B. Das CT-Scannen bietet eine detaillierte 3D-Visualisierung der inneren Strukturen. Die spezifischen ZfP-Methoden, die Häufigkeit und die Akzeptanzkriterien sollten in der Teilespezifikation klar definiert und mit dem AM-Anbieter vereinbart werden.
F5: Können wir einfach unser bestehendes (traditionell hergestelltes) Design für die thermische Abdeckung nehmen und es zum 3D-Druck schicken?
A: Es ist zwar technisch möglich, ein vorhandenes CAD-Modell in ein druckbares Format umzuwandeln, aber das einfache Drucken eines Designs, das für die maschinelle Bearbeitung oder für Bleche vorgesehen ist, nutzt die Hauptvorteile der additiven Fertigung oft nicht und kann sogar suboptimal oder schwer erfolgreich zu drucken sein. Um die Vorteile der additiven Fertigung (Leichtbau, Komplexität, Konsolidierung) zu maximieren, ist es sehr empfehlenswert das Bauteil mit Hilfe von Design for Additive Manufacturing (DfAM) neu konstruieren grundsätze. Dies bedeutet, dass die Geometrie überdacht werden muss, um sie an den schichtweisen Prozess anzupassen, die Stützen zu minimieren, die Topologie zu optimieren, Teile möglicherweise zu konsolidieren und AM-spezifische Überlegungen wie thermische Spannungen und Nachbearbeitungsanforderungen zu berücksichtigen. Die Zusammenarbeit mit AM-Experten während dieser Umgestaltungsphase ist entscheidend für den Erfolg.
Schlussfolgerung: Additive Fertigung für den Wärmeschutz der nächsten Generation in der Raumfahrt
Die raue Umgebung des Weltraums erfordert robuste und zuverlässige Wärmeschutzsysteme. Thermische Abdeckungen für die Luft- und Raumfahrt spielen eine wichtige Rolle beim Schutz kritischer Komponenten von Raumfahrzeugen, Satelliten und Trägerraketen, und die Methoden zu ihrer Herstellung entwickeln sich rasch weiter. Die additive Fertigung von Metallen hat sich zu einer leistungsstarken Technologie entwickelt, die transformative Fähigkeiten bietet, die perfekt für die Herausforderungen der Herstellung dieser komplexen Strukturen geeignet sind.
Wie wir erforscht haben, bietet die Nutzung von Metall-AM für thermische Abdeckungen erhebliche Vorteile gegenüber herkömmlichen Ansätzen. Die unvergleichliche Gestaltungsfreiheit ermöglicht die Erstellung hochkomplexer, topologieoptimierter und konformer Geometrien, was zu erheblichen Leichtbau - ein entscheidender Faktor für die Senkung der Startkosten und die Maximierung der Nutzlastkapazität. Die Fähigkeit zu erreichen Teilkonsolidierungdas Drucken von Mehrkomponenten-Baugruppen als einzelne monolithische Teile erhöht die Zuverlässigkeit, vereinfacht die Logistik und verkürzt die Montagezeit. Außerdem erleichtert AM rapid Prototyping und Iterationbeschleunigung der Entwicklungszyklen für neue Raumfahrthardware. Die Fähigkeit, mit Hochleistungsmaterialien wie dem hochtemperatur- und korrosionsbeständigen IN625 oder das leichte, bedruckbare AlSi10Mg gewährleistet, dass die Materialeigenschaften genau auf die anspruchsvollen thermischen und strukturellen Anforderungen der Anwendung abgestimmt werden können.
Die erfolgreiche Umsetzung der Metall-AM erfordert jedoch eine sorgfältige Berücksichtigung der DfAM-Prinzipien, der erreichbaren Toleranzen und Oberflächengüten, der wesentlichen Nachbearbeitungsschritte (vom Spannungsabbau und der Wärmebehandlung bis hin zur maschinellen Bearbeitung und zerstörungsfreien Prüfung) sowie der potenziellen Herausforderungen bei der Herstellung. Die Beherrschung dieser komplexen Zusammenhänge unterstreicht die Bedeutung von Auswahl des richtigen Produktionspartners. Der Erfolg hängt von der Zusammenarbeit mit einem Anbieter ab, der über fundiertes Fachwissen in der Luft- und Raumfahrt, validierte Prozesse für die relevanten Materialien, fortschrittliche Drucktechnologie, umfassende Nachbearbeitungsmöglichkeiten, robuste Qualitätsmanagementsysteme (wie AS9100) und ein Engagement für technischen Support verfügt.
Met3dp steht an der Spitze dieses technologischen Fortschritts und bietet integrierte Lösungen, die die gesamte Wertschöpfungskette der additiven Fertigung umfassen. Von unserem fortschrittlichen Metallpulverherstellung mit branchenführenden Zerstäubungstechniken zu unserem hochmodernen SEBM- und LPBF-Druckdienste und engagiert technische Unterstützungwir bieten das Fachwissen und die Fähigkeiten, die erforderlich sind, um innovative Entwürfe in weltraumtaugliche Realität umzusetzen. Wir wissen um die kritische Natur von Komponenten für die Luft- und Raumfahrt und sind bestrebt, Wärmeschutzbleche und andere Hardware zu liefern, die den höchsten Anforderungen an Qualität, Zuverlässigkeit und Leistung entsprechen.
Bei der Einführung der additiven Fertigung von Wärmeschutzschalen aus Metall geht es nicht nur um die Einführung einer neuen Fertigungstechnik, sondern auch darum, die nächste Generation effizienter, leistungsfähiger und widerstandsfähigerer Raumfahrtsysteme zu ermöglichen.
Sind Sie bereit zu erfahren, wie der 3D-Druck von Metallen Ihre Herausforderungen im Wärmemanagement revolutionieren kann? Kontaktieren Sie die Experten von Met3dp um Ihre Projektanforderungen zu besprechen und herauszufinden, wie unsere umfassenden Lösungen für die additive Fertigung Ihre Bemühungen in der Luft- und Raumfahrt vorantreiben können.
Teilen auf
MET3DP Technology Co., LTD ist ein führender Anbieter von additiven Fertigungslösungen mit Hauptsitz in Qingdao, China. Unser Unternehmen ist spezialisiert auf 3D-Druckgeräte und Hochleistungsmetallpulver für industrielle Anwendungen.
Fragen Sie an, um den besten Preis und eine maßgeschneiderte Lösung für Ihr Unternehmen zu erhalten!
Verwandte Artikel
Über Met3DP
Aktuelles Update
Unser Produkt
KONTAKT US
Haben Sie Fragen? Senden Sie uns jetzt eine Nachricht! Wir werden Ihre Anfrage mit einem ganzen Team nach Erhalt Ihrer Nachricht bearbeiten.
Holen Sie sich Metal3DP's
Produkt-Broschüre
Erhalten Sie die neuesten Produkte und Preislisten
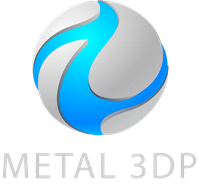
Metallpulver für 3D-Druck und additive Fertigung