Komplexe Lüftungskanäle aus Leichtmetalllegierungen 3D-gedruckt
Inhaltsübersicht
Einführung: Revolutionierung von Rohrleitungen mit additiver Fertigung von Metall
Lüftungskanäle sind die Arterien technischer Systeme, wichtige Leitungen, die für die Lenkung des Luft- und Gasflusses oder der klimatisierten Umgebungen in Anwendungen verantwortlich sind, die von hochentwickelten Luft- und Raumfahrzeugen und Hochleistungsautomobilen bis hin zu komplizierten Industriemaschinen und speziellen medizinischen Geräten reichen. Traditionell wurden diese Komponenten, insbesondere solche mit komplexen Geometrien oder leichten Materialien, in aufwändigen Verfahren wie Blechbearbeitung, Gießen oder mehrteiligen Baugruppen hergestellt. Diese Methoden schränkten die Komplexität des Designs, die Gewichtsoptimierung und die Produktionszeiten oft erheblich ein. Doch mit dem Aufkommen der <a href=”[ungültige URL entfernt]” target=”_blank”>Additive Fertigung von Metallen</a> (AM), allgemein bekannt als Metall-3D-Druck, verändert grundlegend die Art und Weise, wie komplexe Lüftungskanäle entworfen, produziert und implementiert werden.
Stellen Sie sich vor, Sie könnten direkt aus einer digitalen Datei ein kompliziertes, organisch geformtes Rohrsystem erstellen, das perfekt für die Dynamik des Luftstroms und ein minimales Gewicht optimiert ist. Dies ist die Realität, die durch Metall-AM-Technologien wie Laser Powder Bed Fusion (L-PBF) ermöglicht wird. Durch selektives Schmelzen und Verschmelzen feiner Schichten von Metallpulver - insbesondere von leichten Aluminiumlegierungen wie AlSi10Mg und AlSi7Mg - können Hersteller jetzt monolithische (einteilige) Kanäle mit einer noch nie dagewesenen geometrischen Freiheit herstellen. Diese Fähigkeit bringt zahlreiche Vorteile mit sich:
- Verbesserte Leistung: Kanäle können mit glatteren Innenflächen, optimierten Strömungswegen und integrierten Merkmalen gestaltet werden, was zu einer verbesserten aerodynamischen oder thermodynamischen Effizienz führt.
- Signifikante Gewichtsreduzierung: Die Kombination aus Topologie-Optimierungssoftware und Leichtmetalllegierungen ermöglicht die Herstellung von Rohren, die wesentlich leichter sind als ihre herkömmlich hergestellten Gegenstücke - ein entscheidender Faktor in der Luft- und Raumfahrt, im Automobilbau und im Motorsport.
- Teil Konsolidierung: Komplexe Baugruppen, für die bisher mehrere Komponenten, Befestigungselemente und Dichtungen erforderlich waren, können oft in einem einzigen 3D-gedruckten Teil zusammengefasst werden, was die Montagezeit, potenzielle Leckstellen und die Gesamtkomplexität des Systems reduziert.
- Rapid Prototyping und Iteration: Entwürfe können schnell prototypisiert, getestet und verfeinert werden, wodurch sich der Entwicklungszyklus für neue Systeme und Komponenten beschleunigt.
- On-Demand & Verteilte Fertigung: Die Teile können näher am Ort des Bedarfs produziert werden, was die Komplexität der Lieferkette und die Anforderungen an die Lagerhaltung verringern kann.
Dieser technologische Wandel wirkt sich besonders auf Anwendungen aus, die hohe Leistung bei geringem Platzbedarf und Gewicht erfordern. Leichte Aluminiumlegierungen, wie AlSi10Mg und AlSi7Mg, stehen an der Spitze dieser Revolution. Ihr hervorragendes Verhältnis von Festigkeit zu Gewicht, ihre guten thermischen Eigenschaften und ihre Verarbeitbarkeit mittels L-PBF machen sie zu idealen Kandidaten für die Herstellung robuster und dennoch leichter Lüftungskomponenten. Unternehmen wie Met3dp, die über Fachwissen im Bereich der fortschrittlichen Metallpulverproduktion mit Techniken wie der Gasverdüsung und der hochpräzisen 3D-Druck systeme sind von zentraler Bedeutung, wenn es darum geht, das volle Potenzial von AM für anspruchsvolle Anwendungen auszuschöpfen. Durch den Einsatz von hochwertigen, sphärischen Metallpulvern, die für AM-Prozesse optimiert sind, hilft Met3dp bei der Herstellung von dichten, zuverlässigen Teilen mit hervorragenden mechanischen Eigenschaften, die für unternehmenskritische Komponenten wie Lüftungsrohre unerlässlich sind. Dieser Blog-Beitrag taucht in die Welt der 3D-gedruckten Lüftungskanäle ein und untersucht deren Anwendungen, die Vorteile der Verwendung von Metall-AM, die Eigenschaften der empfohlenen Aluminiumlegierungen und wichtige Überlegungen für Design, Herstellung und Lieferantenauswahl.
Vielfältige Anwendungen: Wo 3D-gedruckte Lüftungskanäle überzeugen
Die einzigartigen Möglichkeiten der additiven Fertigung von Metallen, insbesondere in Kombination mit leichten Aluminiumlegierungen, machen 3D-gedruckte Lüftungskanäle zu einer überzeugenden Lösung für eine Vielzahl anspruchsvoller Branchen. Die Fähigkeit, komplexe, optimierte und konsolidierte Rohrleitungen zu erstellen, löst spezifische Herausforderungen und ermöglicht neue Leistungsniveaus, die mit konventionellen Methoden bisher unerreichbar waren. Beschaffungsmanager und Ingenieure, die nach innovativen Lösungen für den Transport von Flüssigkeiten oder Luft suchen, sollten die folgenden wichtigen Anwendungsbereiche in Betracht ziehen:
1. Luft- und Raumfahrt und Verteidigung: Bei der Entwicklung von Flugzeugen und Raumfahrzeugen ist das Gewicht ein zentrales Thema. Jedes eingesparte Kilogramm wirkt sich direkt auf die Treibstoffeffizienz, die Nutzlastkapazität oder die Reichweite aus.
- Umweltkontrollsysteme (ECS) Kanalisation: Oft ist eine komplexe Verlegung erforderlich, um die Kanäle in den engen Räumen von Flugzeugkabinen, Avionikräumen und Frachträumen unterzubringen. AM ermöglicht organisch geformte Kanäle, die Hindernisse nahtlos überwinden, Druckverluste minimieren und die Raumnutzung maximieren. AlSi10Mg und AlSi7Mg bieten die erforderliche geringe Dichte in Kombination mit ausreichender Festigkeit und Steifigkeit für diese nicht strukturellen Anwendungen.
- Avionik-Kühlung: Hochleistungselektronik erzeugt erhebliche Wärme. Maßgeschneiderte, 3D-gedruckte Kanäle können Kühlluft präzise auf kritische Komponenten leiten und so die Effizienz und Zuverlässigkeit des Wärmemanagements verbessern. Die Designfreiheit ermöglicht integrierte Kühlkörper oder komplexe interne Kanäle innerhalb des Kanals selbst.
- Motorkomponenten-Kühlung/Bleed Air Systeme: Während für Komponenten, die sich näher am Triebwerkskern befinden, möglicherweise Superlegierungen mit höheren Temperaturen benötigt werden, eignen sich leichte Aluminiumlegierungen für Leitungen in kühleren Abschnitten oder für Bodengeräte.
- Unbemannte Luftfahrzeuge (UAVs): Die extreme Gewichtsempfindlichkeit und das oft komplexe Innenleben von UAVs machen 3D-gedruckte Aluminiumkanäle zu einer idealen Lösung für verschiedene Belüftungs- und Kühlungsanforderungen.
- Großhandel für Luft- und Raumfahrtkanäle Lieferanten: AM ermöglicht es den Herstellern, als flexible Zulieferer zu agieren und kundenspezifische, hochkomplexe Lösungen für Luft- und Raumfahrt-OEMs und Tier-1-Zulieferer direkt anzubieten, ohne dass die traditionellen Einschränkungen bei der Werkzeugherstellung berücksichtigt werden müssen.
2. Automobilindustrie (Hochleistungsfahrzeuge; Elektrofahrzeuge): Effizienz, Verpackung und Wärmemanagement sind entscheidende Faktoren im Automobilsektor, insbesondere bei Hochleistungsfahrzeugen und dem schnell wachsenden Markt für Elektrofahrzeuge.
- HVAC-Systeme: Die Optimierung des Luftstroms für den Fahrgastkomfort und die Entfeuchtung erfordert oft komplexe Kanalformen, die in die beengten Platzverhältnisse im Armaturenbrett und unter der Motorhaube passen müssen. AM ermöglicht integrierte Designs, die den Luftstrom verbessern, Geräusche reduzieren und die Komplexität der Montage im Vergleich zu herkömmlichen mehrteiligen Kunststoff- oder Blechkanälen minimieren. Die Gewichtsreduzierung trägt auch zur Gesamteffizienz des Fahrzeugs bei.
- Thermisches Management der Batterie: Die Aufrechterhaltung optimaler Batterietemperaturen ist entscheidend für die Leistung, Langlebigkeit und Sicherheit von Elektrofahrzeugen. mit 3D-gedruckten Aluminiumkanälen können hochgradig angepasste und effiziente Luft- oder Flüssigkeitskühlkanäle geschaffen werden, die direkt in oder um die Batteriemodule herum integriert sind und im Vergleich zu Standardlösungen eine überlegene thermische Leistung bieten.
- Motorlufteinlass & Lampe; Auspuffkomponenten (kalte Seite): Bei Hochleistungsfahrzeugen ist die Optimierung des Ansaugluftstroms von entscheidender Bedeutung. Obwohl sie nicht für heiße Auspuffabschnitte geeignet sind, können kundenspezifische Ansaugrohre oder Kanalabschnitte aus Aluminium als Prototyp schnell hergestellt werden.
- Kühlkanäle für die Bremsen: Im Motorsport und bei Hochleistungsfahrzeugen ist die Lenkung des Luftstroms zur Kühlung der Bremsen unerlässlich. AM ermöglicht die Herstellung aerodynamisch effizienter, leichter Bremskanäle, die auf die spezifischen Geometrien des Fahrzeugunterbodens und der Aufhängung zugeschnitten sind.
- Verteiler für HVAC-Kanäle in der Automobilindustrie: Anbieter von Metall-AM können kundenspezifische Lösungen für Fahrzeugplattformen in Nischenbereichen, Prototypen oder Leistungsverbesserungen auf dem Nachrüstungsmarkt liefern und bieten damit eine Flexibilität, die Massenproduktionsverfahren nicht bieten können.
3. Industrielle Ausrüstung und Maschinen: Komplexität, Leistungsanforderungen und der Bedarf an maßgeschneiderten Lösungen treiben die Einführung von AM im industriellen Sektor voran.
- Elektronik-Gehäuse Kühlung: Komplexe Maschinen enthalten oft empfindliche Elektronik, die eine robuste Kühlung erfordert. 3D-gedruckte Kanäle können einen gezielten Luftstrom in engen Gehäusen gewährleisten, die Zuverlässigkeit verbessern und Überhitzung verhindern.
- Prozessgas-Förderung: In spezialisierten Fertigungsprozessen (z. B. Halbleiter, chemische Verarbeitung) können maßgeschneiderte Rohre aus korrosionsbeständigen Materialien (wobei die Eignung von Aluminium vom jeweiligen Gas abhängt) erforderlich sein, um Prozessgase effizient und sicher zu transportieren. AM ermöglicht die schnelle Erstellung anwendungsspezifischer Designs.
- Komponenten für Wärmetauscher: Während für die primären Wärmeaustauschelemente möglicherweise andere Materialien oder Verfahren verwendet werden, können die zugehörigen Kanäle und Verteiler von der Designfreiheit und dem Leichtbaupotenzial von 3D-gedrucktem Aluminium profitieren.
- Kundenspezifische Maschinenbelüftung: Für maßgeschneiderte Industriemaschinen oder Roboterzellen kann die Entwicklung effektiver Belüftungssysteme eine Herausforderung sein. AM bietet eine Möglichkeit, passgenaue, optimierte Lüftungskanäle zu erstellen, ohne dass teure Spezialwerkzeuge erforderlich sind.
- Lieferanten für industrielle Belüftungssysteme: Unternehmen, die spezialisierte, kleinvolumige oder hochkomplexe Kanäle für einzigartige industrielle Anwendungen benötigen, können sich für maßgeschneiderte Lösungen mit Metall-AM-Dienstleistern zusammenschließen.
4. Medizinische Ausrüstung: Präzises Luftstrom- und Gasmanagement ist in vielen medizinischen Geräten von entscheidender Bedeutung.
- Atemschutzgeräte: Komponenten in Beatmungs- oder Anästhesiegeräten, die eine präzise Zufuhr von Luft-/Gasgemischen über komplexe Wege erfordern, können möglicherweise mit AM hergestellt werden, wodurch die Genauigkeit gewährleistet und die Teile möglicherweise konsolidiert werden können. Biokompatibilitätsaspekte wären von größter Bedeutung, und es könnten spezielle Legierungen oder Beschichtungen erforderlich sein. (Hinweis: Während AlSi-Legierungen üblich sind, erfordern medizinische Anwendungen oft spezielle Zertifizierungen und möglicherweise andere Materialien wie Titan oder Edelstahl, je nach direktem Patientenkontakt).
- Ausstattung Kühlung: Diagnostische Geräte wie MRT- oder CT-Scanner haben oft komplizierte Kühlungsanforderungen, bei denen kundenspezifische Kanäle die Effizienz verbessern und die Geräuschentwicklung reduzieren können.
Tabelle: Anwendungsbereiche und Hauptvorteile
Industrie Sektor | Spezifische Anwendungen | Die wichtigsten Vorteile des 3D-Drucks (Al-Legierungen) | Ziel-Schlüsselwörter |
---|---|---|---|
Luft- und Raumfahrt & Verteidigung | ECS-Kanäle, Avionik-Kühlung, UAV-Systeme | Gewichtsreduzierung, Komplexe Geometrie, Teilekonsolidierung, Rapid Prototyping | Lieferant für Luft- und Raumfahrtkanäle, leichte Flugzeugteile, ECS AM |
Automobilindustrie | HVAC-Systeme, EV-Batteriekühlung, Bremsenkühlung | Verpackungseffizienz, Wärmemanagement, Gewichtsersparnis, kundenspezifische Anpassung | Automobil HVAC-Kanäle Großhandel, EV Wärmemanagement, kundenspezifische Autoteile |
Industriell | Anlagenkühlung, Prozessgasförderung, Maschinen | Gestaltungsfreiheit, Anpassung, Leistungsoptimierung, schneller Austausch | Hersteller von industriellen Lüftungsanlagen, kundenspezifische Maschinenteile, AM-Lieferant |
Medizinische | Beatmungsgeräte, Gerätekühlung | Präzise Durchflusskontrolle, Teilekonsolidierung, komplexe Innenkanäle | Komponenten für medizinische Geräte, Präzisionsluftstrom, medizinische AM-Teile |
In Blätter exportieren
Die Vielseitigkeit, die Metall-AM bietet, ermöglicht es Ingenieuren und Beschaffungsspezialisten, die Konstruktion von Rohren neu zu überdenken und die Einschränkungen herkömmlicher Methoden zu überwinden, um eine bessere Leistung, Effizienz und Integration in diesen wichtigen Branchen zu erreichen.
Der Additiv-Vorteil: Warum 3D-Druck von Metall für Lüftungskanäle?
Herkömmliche Fertigungsverfahren wie Blechumformung, Strangpressen, Gießen und Spritzgießen (für Kunststoffe) haben zwar lange Zeit dem Zweck der Herstellung von Lüftungskanälen gedient, sind jedoch mit inhärenten Beschränkungen behaftet, insbesondere wenn es um komplexe Konstruktionen, Leichtbauanforderungen und die Produktion kleiner bis mittlerer Mengen geht. Die additive Fertigung von Metallen, insbesondere das Laser Powder Bed Fusion (L-PBF) unter Verwendung von Aluminiumlegierungen wie AlSi10Mg und AlSi7Mg, bietet eine Reihe überzeugender Vorteile, die sich direkt auf diese Einschränkungen auswirken und sie zu einer zunehmend attraktiven Option für Ingenieure und Großabnehmer machen, die auf Leistung und Innovation setzen.
1. Unerreichte Gestaltungsfreiheit und Komplexität:
- Traditionell: Bleche müssen gebogen, gefaltet, geschweißt oder genietet werden, wodurch die Formen auf entwicklungsfähige Oberflächen beschränkt sind oder komplexe Baugruppen erforderlich sind. Gießen ermöglicht mehr Komplexität, erfordert aber teure Werkzeuge (Formen) und kann Einschränkungen bei der Wandstärke und den inneren Merkmalen haben.
- Zusatzstoff (L-PBF): AM baut Teile Schicht für Schicht direkt aus einem 3D-CAD-Modell auf. Dies ermöglicht:
- Organische Formen: Kanäle können hochkomplexen, nichtlinearen Pfaden folgen, um enge Räume optimal zu durchqueren.
- Interne Merkmale: Komplexe Innenstrukturen wie Drehflügel, Strömungsgleichrichter oder Mischeinrichtungen können ohne Montage direkt in den Kanal integriert werden.
- Topologie-Optimierung: Mithilfe von Software kann Material in Bereichen mit geringer Beanspruchung entfernt werden, wodurch hocheffiziente, leichte Strukturen entstehen, die auf herkömmliche Weise nicht hergestellt werden können.
- Gitterförmige Strukturen: Interne oder externe Gitterstrukturen können zur Erhöhung der Steifigkeit, zur Gewichtsreduzierung oder zur Verbesserung der thermischen Leistung eingebaut werden.
2. Signifikante Gewichtsreduzierung:
- Traditionell: Um ein geringes Gewicht zu erreichen, müssen oft dünne Materialien (die die Steifigkeit beeinträchtigen) oder teure Materialien wie Kohlenstoffverbundwerkstoffe verwendet werden. Die Optimierung des Designs wird durch den Herstellungsprozess eingeschränkt.
- Zusatzstoff (L-PBF): Die Kombination aus Designfreiheit (Topologieoptimierung) und der Verwendung von inhärent leichten Aluminiumlegierungen ermöglicht erhebliche Gewichtseinsparungen im Vergleich zu konventionell hergestellten Metallkanälen, die oft mehr als 30-50 % betragen, bei gleichbleibender oder sogar verbesserter Leistung. Dies ist von entscheidender Bedeutung für Anwendungen in der Luft- und Raumfahrt sowie in der Automobilindustrie, die Effizienzsteigerungen anstreben.
3. Teil Konsolidierung:
- Traditionell: Komplexe Kanalsysteme bestehen oft aus mehreren Abschnitten, die durch Flansche, Schellen, Dichtungen und Verbindungselemente miteinander verbunden sind. Jede Verbindung stellt einen potenziellen Leckagepfad, zusätzliches Gewicht sowie erhöhte Montagezeit und -kosten dar.
- Zusatzstoff (L-PBF): Mit AM können mehrere Komponenten einer Kanalbaugruppe (z. B. Bögen, Abzweigungen, Halterungen, Sensoranschlüsse) in ein einziges, monolithisch gedrucktes Teil integriert werden. Dies reduziert die Kosten drastisch:
- Anzahl der Teile
- Montagearbeiten
- Potenzielle Leckstellen
- Gesamtgewicht und Komplexität des Systems
4. Rapid Prototyping und beschleunigte Entwicklung:
- Traditionell: Die Erstellung von Prototypen erfordert häufig eine weiche Werkzeugkonstruktion oder eine manuelle Fertigung, was zeitaufwändig und teuer sein kann. Konstruktionsänderungen machen neue Werkzeuge oder erhebliche Nacharbeiten erforderlich.
- Zusatzstoff (L-PBF): Funktionale Metallprototypen können innerhalb weniger Tage, manchmal sogar Stunden, direkt aus CAD-Daten gedruckt werden. Dies ermöglicht es Ingenieuren,:
- Testen Sie schnell Form, Passform und Funktion.
- Führen Sie aerodynamische oder strömungstechnische Tests an physischen Teilen in einem frühen Stadium des Designzyklus durch.
- Schnelles Iterieren von Entwürfen auf der Grundlage von Testergebnissen, ohne dass hohe Werkzeugkosten anfallen.
- Verkürzen Sie den gesamten Zeitrahmen für die Produktentwicklung erheblich.
5. Beseitigung von Werkzeugen:
- Traditionell: Verfahren wie Gießen, Spritzgießen oder komplexe Blechumformung erfordern erhebliche Vorabinvestitionen in Formen, Gesenke oder Vorrichtungen. Diese Kosten sind für die Produktion von Kleinserien oder stark individualisierten Teilen unerschwinglich.
- Zusatzstoff (L-PBF): AM ist ein werkzeugloses Verfahren. Die Teile werden direkt aus der digitalen Datei erstellt, was es wirtschaftlich rentabel macht:
- Kleine bis mittelgroße Produktionsläufe.
- Hochgradig kundenspezifische oder maßgeschneiderte Kanalkonstruktionen.
- Herstellung von Altteilen, für die es keine Originalwerkzeuge mehr gibt.
6. Potenzial für verteilte Fertigung:
- Traditionell: Die Fertigung ist oft zentralisiert, wo spezifische Werkzeuge und Fachwissen vorhanden sind.
- Zusatzstoff (L-PBF): Da die AM-Technologie immer zugänglicher wird, könnten Teile wie Lüftungskanäle möglicherweise näher am Montage- oder Verwendungsort gedruckt werden (z. B. in MRO-Einrichtungen für die Luft- und Raumfahrt oder in regionalen Fertigungszentren), wodurch sich die Transportkosten und Vorlaufzeiten verringern. Dies steht im Einklang mit dem Trend zu widerstandsfähigeren und flexibleren Lieferketten.
Tabelle: Traditionelle vs. Additive Fertigung für Lüftungskanäle
Merkmal | Traditionelle Methoden (Blech, Guss) | Additive Fertigung von Metall (L-PBF) | Vorteil von AM | Schlüsselwörter für das Beschaffungswesen |
---|---|---|---|---|
Entwurfskomplexität | Begrenzt durch Einschränkungen bei der Umformung/Formgebung | Nahezu unbegrenzte geometrische Freiheit, innere Merkmale | Optimierte Leistung, Verpackungseffizienz | Komplexe Kanalfertigung, kundenspezifische Lüftungslösungen |
Gewicht | Optimierung eingeschränkt; oft schwerer | Ermöglicht Topologieoptimierung, leichte Legierungen | Signifikante Gewichtsreduzierung möglich | Leichte Kanäle, Gewichtseinsparungen in der Luftfahrt |
Anzahl der Teile | Erfordert oft mehrteilige Baugruppen, Verbindungselemente, Dichtungen | Ermöglicht die Konsolidierung in monolithische Teile | Geringere Montagezeit, weniger Leckstellen, geringeres Gewicht | Teilekonsolidierung AM, integriertes Kanaldesign |
Prototyping | Langsam, erfordert oft Werkzeuge oder manuelle Fertigung | Schnell, werkzeuglos, direkt vom CAD | Schnellere Iteration, kürzere Entwicklungszeit | Rapid Metal Prototyping, Funktionsprototypen |
Werkzeugkosten | Hohe Vorabinvestitionen für Formen, Gesenke, Vorrichtungen | Keine (werkzeuglose Fertigung) | Wirtschaftliche Tragfähigkeit für Kleinserien & Produktion; kundenspezifische Teile | Werkzeuglose Fertigung, Zulieferer von Metallteilen in kleinen Stückzahlen |
Vorlaufzeit | Kann langwierig sein, vor allem wenn es um Werkzeuge geht | Möglicherweise kürzer, insbesondere bei komplexen Prototypen | Kürzere Markteinführungszeiten, bedarfsgerechte Produktionsmöglichkeiten | Schnelle Durchlaufzeiten beim 3D-Druck, Metall-AM-Vorlaufzeiten |
Materialabfälle | Subtraktive Verfahren können erheblichen Ausschuss erzeugen | Additives Verfahren, im Allgemeinen weniger Abfall (Pulverrecycling) | Nachhaltigere Produktion (Potenzial) | Nachhaltige Fertigung, additive Materialeffizienz |
In Blätter exportieren
Durch die Nutzung dieser inhärenten Vorteile ermöglicht der 3D-Metalldruck Ingenieuren die Entwicklung und Herstellung von Lüftungskanälen, die leichter, effizienter, zuverlässiger und schneller zu entwickeln sind als je zuvor, was einen klaren Wettbewerbsvorteil in anspruchsvollen Branchen darstellt. Die Zusammenarbeit mit einem erfahrenen Metall-AM-Anbieter sichert den Zugang zu diesen Vorteilen.
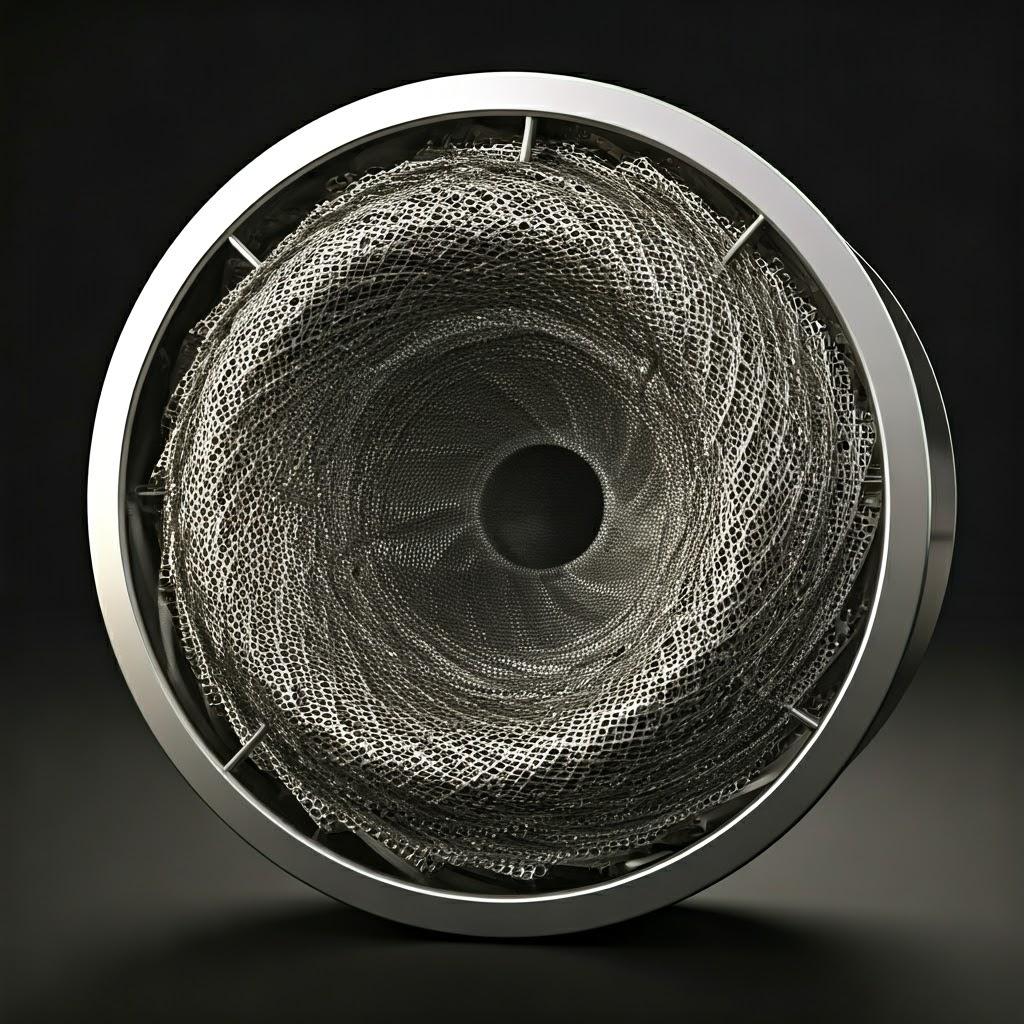
Werkstoff-Fokus: AlSi10Mg & AlSi7Mg-Aluminiumlegierungen für optimale Leistung
Die Wahl des Materials ist von grundlegender Bedeutung für den Erfolg eines jeden technischen Bauteils, und 3D-gedruckte Lüftungskanäle bilden da keine Ausnahme. Während verschiedene Metalle mittels additiver Fertigung verarbeitet werden können, haben sich Aluminiumlegierungen - insbesondere AlSi10Mg und AlSi7Mg - aufgrund ihrer überzeugenden Mischung aus Eigenschaften, guter Verarbeitbarkeit mittels Laser Powder Bed Fusion (L-PBF) und angemessenen Kosten als Spitzenreiter für Leichtbaukanäle erwiesen. Das Verständnis der Eigenschaften dieser Legierungen ist für Designer, Ingenieure und Beschaffungsspezialisten, die Metall-AM-Lösungen evaluieren, von entscheidender Bedeutung.
Aluminium-Silizium-Legierungen: Die Grundlagen AlSi10Mg und AlSi7Mg gehören zur Familie der hypoeutektischen Aluminium-Silizium-Gusslegierungen, die für die additive Fertigung modifiziert wurden. Der Siliziumgehalt (Si) verbessert die Fließfähigkeit und die Gießbarkeit (was sich in einer guten Verarbeitbarkeit im Schmelzbad während der L-PBF niederschlägt), während Magnesium (Mg) eine Verfestigung durch Wärmebehandlung (Ausscheidungshärtung) ermöglicht.
- AlSi10Mg: Enthält etwa 9-11% Silizium und 0,2-0,45% Magnesium. Es ist bekannt für sein hervorragendes Verhältnis von Festigkeit zu Gewicht, seine gute Wärmeleitfähigkeit und seine im Vergleich zu anderen Aluminiumlegierungen relativ hohe Härte und Verschleißfestigkeit nach der Wärmebehandlung. Es ist wohl die am häufigsten in L-PBF verwendete Aluminiumlegierung.
- AlSi7Mg: Enthält etwa 6,5-7,5 % Silizium und 0,25-0,45 % Magnesium. Es bietet in der Regel eine etwas bessere Duktilität und Bruchzähigkeit im Vergleich zu AlSi10Mg, möglicherweise auf Kosten einer gewissen Zugfestigkeit. Sein Verarbeitungsfenster in L-PBF kann manchmal breiter oder nachsichtiger sein.
Warum diese Legierungen für Lüftungskanäle wichtig sind:
- Ausgezeichnetes Verhältnis von Stärke zu Gewicht: Dies ist für Anwendungen in der Luft- und Raumfahrt, in der Automobilindustrie und bei tragbaren Geräten von größter Bedeutung. Diese Legierungen bieten eine gute mechanische Festigkeit (ausreichend für die Bewältigung von Luftstromdrücken und Systemvibrationen in typischen Kanalszenarien) bei einer sehr geringen Dichte (ca. 2,67 g/cm³). Dies ermöglicht direkt die erhebliche Gewichtsreduzierung, die durch AM-Designoptimierung erreicht werden kann.
- Gute thermische Eigenschaften: Aluminiumlegierungen weisen eine relativ hohe Wärmeleitfähigkeit auf. Dies ist vorteilhaft für Leitungen in Wärmemanagementanwendungen (z. B. Elektronikkühlung, Batteriekühlung, Wärmetauscherkomponenten), da die Leitung selbst zur Wärmeableitung beitragen kann.
- Korrosionsbeständigkeit: Aluminium bildet von Natur aus eine passive Oxidschicht, die eine gute Beständigkeit gegen atmosphärische Korrosion bietet. Obwohl es nicht gegen alle chemischen Umgebungen immun ist, eignet es sich für Standard-Luftaufbereitung, HVAC und viele industrielle atmosphärische Bedingungen. Spezielle Oberflächenbehandlungen können die Widerstandsfähigkeit bei Bedarf weiter erhöhen.
- Verarbeitbarkeit mit L-PBF: Sowohl AlSi10Mg als auch AlSi7Mg wurden umfassend charakterisiert und für das L-PBF-Verfahren optimiert. Es gibt ausgereifte Parametersätze, die die Herstellung von Teilen mit hoher Dichte (typischerweise >99,5 %) und vorhersehbaren mechanischen Eigenschaften ermöglichen. Ihr relativ niedriger Schmelzpunkt im Vergleich zu Stählen oder Titanlegierungen führt auch zu allgemein schnelleren Fertigungsgeschwindigkeiten.
- Wärmebehandelbarkeit: Durch das Vorhandensein von Magnesium können diese Legierungen lösungsgeglüht und künstlich gealtert werden (z. B. T6-Anlass). Dieses Verfahren erhöht die Streckgrenze und die Zugfestigkeit erheblich, indem feine Mg₂Si-Partikel in der Aluminiummatrix ausgefällt werden. Auf diese Weise lassen sich die endgültigen mechanischen Eigenschaften an die spezifischen Anforderungen der Anwendung anpassen (z. B. Maximierung der Festigkeit oder Ausgleich von Festigkeit und Duktilität).
- Schweißbarkeit/Fügbarkeit: Während AM auf die Konsolidierung von Teilen abzielt, weisen diese Legierungen, wenn sie mit anderen Komponenten verbunden werden müssen, im Allgemeinen eine gute Schweißbarkeit unter Verwendung geeigneter Techniken (z. B. WIG- oder MIG-Schweißen) auf, obwohl eine Wärmebehandlung nach dem Schweißen erforderlich sein kann, um optimale Eigenschaften wiederherzustellen.
- Kosten-Nutzen-Verhältnis: Im Vergleich zu Titanlegierungen oder Hochleistungssuperlegierungen sind Aluminiumpulver wesentlich kostengünstiger, was sie zu einer praktikablen Option für ein breiteres Spektrum von Kanalanwendungen macht, bei denen extreme Temperaturbeständigkeit nicht die Hauptrolle spielt.
Die kritische Rolle der Pulverqualität: Die endgültige Qualität und Leistung eines 3D-gedruckten Metallteils sind untrennbar mit der Qualität des Rohmaterials - des Metallpulvers - verbunden. Bei anspruchsvollen Anwendungen wie Lüftungskanälen, insbesondere in der Luft- und Raumfahrt oder bei kritischen Industriesystemen, ist die Verwendung von hochwertigem Pulver nicht verhandelbar. Zu den wichtigsten Eigenschaften des Pulvers gehören:
- Sphärizität: Hochkugelförmige Pulverpartikel gewährleisten eine gute Fließfähigkeit, die für eine gleichmäßige Verteilung dünner Schichten im L-PBF-Verfahren unerlässlich ist. Eine schlechte Fließfähigkeit kann zu Hohlräumen und Defekten im fertigen Teil führen.
- Partikelgrößenverteilung (PSD): Ein kontrollierter PSD, der für die jeweilige L-PBF-Maschine optimiert ist, ist entscheidend für eine hohe Packungsdichte im Pulverbett und ein gleichmäßiges Schmelzverhalten. Feinanteile können Probleme verursachen, während zu große Partikel möglicherweise nicht vollständig schmelzen.
- Chemische Zusammensetzung: Die strikte Einhaltung der vorgegebenen Legierungszusammensetzung (z. B. AlSi10Mg, AlSi7Mg-Normen) ist für das Erreichen der gewünschten mechanischen und thermischen Eigenschaften von entscheidender Bedeutung. Verunreinigungen müssen auf ein Minimum reduziert werden.
- Geringe Porosität/Gasgehalt: Pulver, das mit fortschrittlichen Zerstäubungstechniken hergestellt wird, wie dem Gaszerstäubungs- und Plasma-Rotations-Elektroden-Verfahren (PREP), das von Met3dpminimiert die interne Gasporosität innerhalb der Pulverpartikel. Dies führt zu dichteren, zuverlässigeren Endteilen mit verbesserter Ermüdungslebensdauer. Met3dp’s Fokus auf den Einsatz von branchenführenden Zerstäubungstechnologien gewährleistet ihre <a href=”[ungültige URL entfernt]” target=”_blank”>Hochwertige Metallpulver</a>einschließlich Aluminiumlegierungen, weisen eine ausgezeichnete Sphärizität und Fließfähigkeit auf, was direkt zur Integrität von einsatzkritischen gedruckten Komponenten beiträgt.
- Konsistenz der Chargen: Zuverlässige Lieferanten gewährleisten eine hohe Konsistenz von Charge zu Charge, was für wiederholbare Fertigungsprozesse und eine vorhersehbare Leistung der Teile entscheidend ist - eine wichtige Voraussetzung für Großabnehmer und die Serienproduktion.
Tabelle: Eigenschaftsvergleich (Typische Werte für L-PBF AlSi10Mg & AlSi7Mg – Wärmebehandelt T6)
Eigentum | AlSi10Mg (T6) | AlSi7Mg (T6) | Einheit | Bedeutung für Kanäle |
---|---|---|---|---|
Dichte | ~2.67 | ~2.67 | g/cm³ | Kernstück der Leichtbauweise |
Streckgrenze (Rp0,2) | 240 – 300 | 230 – 280 | MPa | Widerstand gegen bleibende Verformung unter Druck/Last |
Endgültige Zugfestigkeit | 360 – 450 | 330 – 400 | MPa | Maximale Spannung vor dem Bruch |
Dehnung beim Bruch | 3 – 10 | 6 – 12 | % | Duktilität, Fähigkeit, sich vor dem Bruch zu verformen (Zähigkeit) |
Elastizitätsmodul | ~70 | ~70 | GPa | Steifigkeit, Widerstand gegen elastische Verformung |
Wärmeleitfähigkeit | 130 – 150 | 140 – 160 | W/(m-K) | Fähigkeit, Wärme zu leiten (wichtig für Kühlanwendungen) |
Maximale Betriebstemperatur | ~150-180 (je nach Belastung/Zeit) | ~150-180 (je nach Belastung/Zeit) | °C | Obere Grenze für Dauerbetrieb |
Hauptmerkmal | Höhere Festigkeit/Härte | Höhere Duktilität/Zähigkeit | – | Leitet die Auswahl nach dem primären Leistungsbedarf |
In Blätter exportieren
Hinweis: Die tatsächlichen Eigenschaften können je nach Druckparametern, Bauausrichtung, Wärmebehandlung und Testbedingungen erheblich variieren.
Zusammenfassend lässt sich sagen, dass AlSi10Mg und AlSi7Mg ein ausgewogenes Profil aus Leichtgewicht, Festigkeit, Wärmeleitfähigkeit und Verarbeitbarkeit bieten, was sie zu einer ausgezeichneten Wahl für die Herstellung komplexer Lüftungskanäle im Metall-3D-Druck macht. Die Auswahl eines qualitativ hochwertigen Pulvers von renommierten Anbietern wie Met3dp ist von entscheidender Bedeutung, um das volle Potenzial dieser Werkstoffe auszuschöpfen und die Zuverlässigkeit und Leistung des fertigen Bauteils zu gewährleisten.
Additives Entwerfen: Wichtige Überlegungen für 3D-gedruckte Lüftungskanäle
Der Übergang von traditionellen Fertigungsparadigmen zur additiven Fertigung erschließt ein immenses Potenzial für die Konstruktion von Lüftungskanälen, erfordert aber auch ein Umdenken. Entwerfen für Additive Manufacturing (DfAM) ist entscheidend, um die Vorteile des 3D-Metalldrucks voll auszuschöpfen und ein erfolgreiches, kosteneffizientes Ergebnis zu gewährleisten. Die einfache Konvertierung eines traditionell entworfenen Kanals in eine STL-Datei für den Druck führt selten zu optimalen Ergebnissen. Ingenieure und Designer müssen bei der Entwicklung von Lüftungskanälen mit L-PBF und leichten Aluminiumlegierungen AM-spezifische Prinzipien berücksichtigen.
1. Topologie-Optimierung und generatives Design einsetzen:
- Konzept: Diese Berechnungswerkzeuge verwenden Algorithmen zur Optimierung der Materialverteilung innerhalb eines definierten Konstruktionsraums auf der Grundlage von Belastungsbedingungen (z. B. Innendruck, Schwingungsformen, Befestigungspunkte) und Leistungszielen (z. B. Minimierung des Gewichts, Maximierung der Steifigkeit, Optimierung der Strömung).
- Anwendung für Rohrleitungen: Beginnen Sie mit den Einlass-/Auslasspunkten und allen räumlichen Beschränkungen. Definieren Sie die erwarteten Druckbelastungen und Schwingungsfrequenzen. Die Software erzeugt dann eine organische, lastpfadoptimierte Struktur, die nur dort Material einsetzt, wo es benötigt wird. Dies führt oft zu hocheffizienten, nicht intuitiven Geometrien, die deutlich leichter sind als von Menschen entworfene Gegenstücke, aber ebenso oder sogar noch leistungsfähiger.
- Nutzen: Maximiert die Gewichtsreduzierung, verbessert die strukturelle Effizienz und kann sogar dazu beitragen, die internen Strömungswege durch Glätten von Biegungen zu optimieren.
2. Strategische Umsetzung von Gitterstrukturen:
- Konzept: Gitter sind sich wiederholende Einheitszellstrukturen (z. B. strebenbasiert wie kubisch oder oktettisch; oberflächenbasiert wie Kreisel oder Schwarzite – TPMS), die feste Volumen ausfüllen oder Häute bilden können.
- Anwendung für Rohrleitungen:
- Gewichtsreduzierung: Ersetzen Sie massive Teile (z. B. Montageflansche, Versteifungsrippen) durch leichte Gitterfüllungen.
- Kontrolle der Steifigkeit: Passen Sie die Steifigkeit der Kanalwände oder bestimmter Abschnitte an.
- Schwingungsdämpfung: Bestimmte Gittertypen weisen hervorragende Energieabsorptionseigenschaften auf.
- Verbessertes Wärmemanagement: TPMS-Gitter bieten ein sehr hohes Oberflächen-Volumen-Verhältnis, was die Wärmeübertragung verbessern kann, wenn die Kanalwand Teil eines Kühlsystems ist.
- Flussmanagement: Sorgfältig gestaltete innere Gitter könnten als Strömungsgleichrichter oder -mischer fungieren, was allerdings eine fortgeschrittene Simulation erfordert.
- Erwägung: Die Komplexität eines Gitters kann die Entwurfs- und Simulationszeit erhöhen. Stellen Sie sicher, dass die Dichte des Gitters und die Dicke der Streben/Wände für die Druckbarkeit und die strukturellen Anforderungen geeignet sind. Die Pulverentfernung aus komplexen inneren Gittern kann eine Herausforderung sein.
3. Optimieren Sie die Wanddicke:
- Bedruckbare Mindestdicke: Bei L-PBF-Verfahren mit AlSi10Mg/AlSi7Mg können je nach Maschine, Parametern und Geometrie in der Regel Wanddicken bis zu 0,4-0,8 mm erreicht werden. Dünnere Wände sind jedoch anfälliger für Verformungen während des Drucks und der Handhabung.
- Funktionale Anforderungen: Die Wandstärke muss ausreichend sein, um:
- Sie halten Betriebsdrücken stand, ohne sich zu verformen oder zu versagen.
- Ausreichende Steifigkeit, um Verformungen während der Handhabung und des Betriebs zu vermeiden.
- Auf Dichtigkeit achten.
- Variable Dicke: DfAM ermöglicht es, die Wandstärke entlang des Kanals zu variieren, indem nur dort Material hinzugefügt wird, wo die Belastung am höchsten ist (z. B. an Kurven oder Befestigungspunkten) und die Wände in Bereichen mit geringer Belastung dünner werden, um Gewicht zu sparen.
4. Selbsttragende Konstruktion und Minimierung von Überhängen:
- L-PBF-Beschränkung: Das L-PBF-Verfahren erfordert Stützstrukturen für Merkmale, die über einen bestimmten Winkel über die horizontale Ebene hinausragen (in der Regel etwa 45 Grad bei Aluminiumlegierungen). Die direkte Herstellung auf losem Pulver ist nicht möglich.
- Strategien zur Schadensbegrenzung:
- Orientierung: Richten Sie den Kanal innerhalb der Baukammer so aus, dass die Anzahl und das Ausmaß der Überhänge, die abgestützt werden müssen, möglichst gering sind.
- Fase/Fillet-Kanten: Verwenden Sie an nach unten gerichteten Kanten Fasen oder große Ausrundungen anstelle von scharfen 90-Grad-Überhängen.
- Interne Kanäle: Entwerfen Sie horizontale Innenkanäle mit selbsttragenden Formen wie Rauten, Tropfen oder Ellipsen anstelle von perfekten Kreisen oder Rechtecken, so dass keine schwer oder gar nicht zu entfernenden Innenstützen erforderlich sind.
- Allmähliche Übergänge: Vermeiden Sie abrupte Querschnittsänderungen, die zu freitragenden Überhängen führen.
5. Integrieren Sie Funktionen und vereinfachen Sie die Montage:
- Hebelwirkung Teilkonsolidierung: Entwerfen Sie Halterungen, Flansche, Sensornasen, Kabelklemmen und andere angrenzende Teile direkt in die einzelne Kanalkomponente.
- Optimieren Sie Verbindungen: Wenn eine Verbindung mit anderen Bauteilen unvermeidlich ist, konstruieren Sie robuste, leicht zugängliche Flanschverbindungen. Berücksichtigen Sie die Möglichkeit, Standarddichtungen oder O-Ringe einzubauen. Achten Sie auf eine ausreichende ebene Fläche für die Abdichtung.
- Stressabbau: Verwenden Sie großzügige Verrundungen an scharfen Innenecken und Übergängen, um Spannungskonzentrationen zu verringern und so die Lebensdauer und Haltbarkeit zu verbessern.
6. Plan für den Ausbau der Stützstruktur und die Nachbearbeitung:
- Zugänglichkeit: Wenn Abstützungen unvermeidlich sind (insbesondere interne), konstruieren Sie den Kanal mit Zugangsöffnungen speziell für Abstützungsentfernungswerkzeuge und Inspektionen. Überlegen Sie, wie das Pulver aus den inneren Hohlräumen entfernt werden soll.
- Geopferte Merkmale: Manchmal kann das Hinzufügen von kleinen, leicht entfernbaren Merkmalen (z. B. Markierungen für Bearbeitungsnullpunkte, temporäre Stützen) die Nachbearbeitungsgenauigkeit verbessern.
- Zulagen für die Bearbeitung: Wenn bestimmte Oberflächen (z. B. Flanschflächen, Dichtungsbereiche) hohe Präzision oder glatte Oberflächen erfordern, die durch CNC-Bearbeitung erreicht werden, fügen Sie zusätzliches Rohmaterial (z. B. 0,5-1,0 mm) zu diesen Merkmalen in der Konstruktionsdatei hinzu.
Tabelle: DfAM-Checkliste für 3D-gedruckte Rohre
Prinzip der Gestaltung | Schlüsselaktion | Nutzen Sie | Schlüsselwort Fokus |
---|---|---|---|
Topologieoptimierung | Verwendung von Software zur Optimierung der Materialanordnung auf der Grundlage von Lasten/Einschränkungen. | Maximale Gewichtsreduzierung und strukturelle Effizienz. | Topologieoptimierte Teile, Leichtbauweise AM |
Gitterförmige Strukturen | Strategischer Einsatz aus Gewichts-, Steifigkeits-, Wärme- oder Dämpfungsgründen. | Multifunktionales Design, weitere Gewichtseinsparungen. | AM-Gitterstrukturen, TPMS-Design |
Wanddicke | Optimieren Sie auf der Grundlage von Druck und Steifigkeit; verwenden Sie variable Dicken. | Gleichgewicht zwischen Leistung, Gewicht und Bedruckbarkeit. | Mindestwandstärke L-PBF, variable Dichte |
Selbsttragende Konstruktion | Teile effektiv ausrichten; >45°-Winkel verwenden; selbsttragende Kanäle entwerfen. | Minimierung der Stützstrukturen, Reduzierung der Nachbearbeitungskosten und -zeit. | Selbsttragende Winkel AM, stützenfreies Design |
Integration von Merkmalen | Konsolen, Flansche, Anschlüsse konsolidieren; Ecken verrunden. | Reduzieren Sie die Anzahl der Teile, die Montagezeit und die Leckstellen; verbessern Sie die Haltbarkeit. | Teilekonsolidierung AM, integrierte AM-Komponenten |
Nachbearbeitungsplanung | Konstruktion für den Zugang zur Abstützung/Pulverentfernung; bei Bedarf ist ein Bearbeitungsmaterial hinzuzufügen. | Sicherstellung der Herstellbarkeit, der erreichbaren Toleranzen und der Oberflächenbeschaffenheit. | DfAM-Nachbearbeitung, Bearbeitungszugabe AM |
In Blätter exportieren
Durch die durchdachte Anwendung dieser DfAM-Prinzipien können Ingenieure das wahre Potenzial von Metall erschließen <a href=”[ungültige URL entfernt]” target=”_blank”>Druckverfahren</a> wie L-PBF für die Herstellung hochwertiger Lüftungskanäle, die den anspruchsvollen Anforderungen der Luft- und Raumfahrt, der Automobilbranche und industrieller Anwendungen gerecht werden. Die Zusammenarbeit mit erfahrenen AM-Dienstleistern, die diese Prinzipien verstehen, ist der Schlüssel zur erfolgreichen Umsetzung.
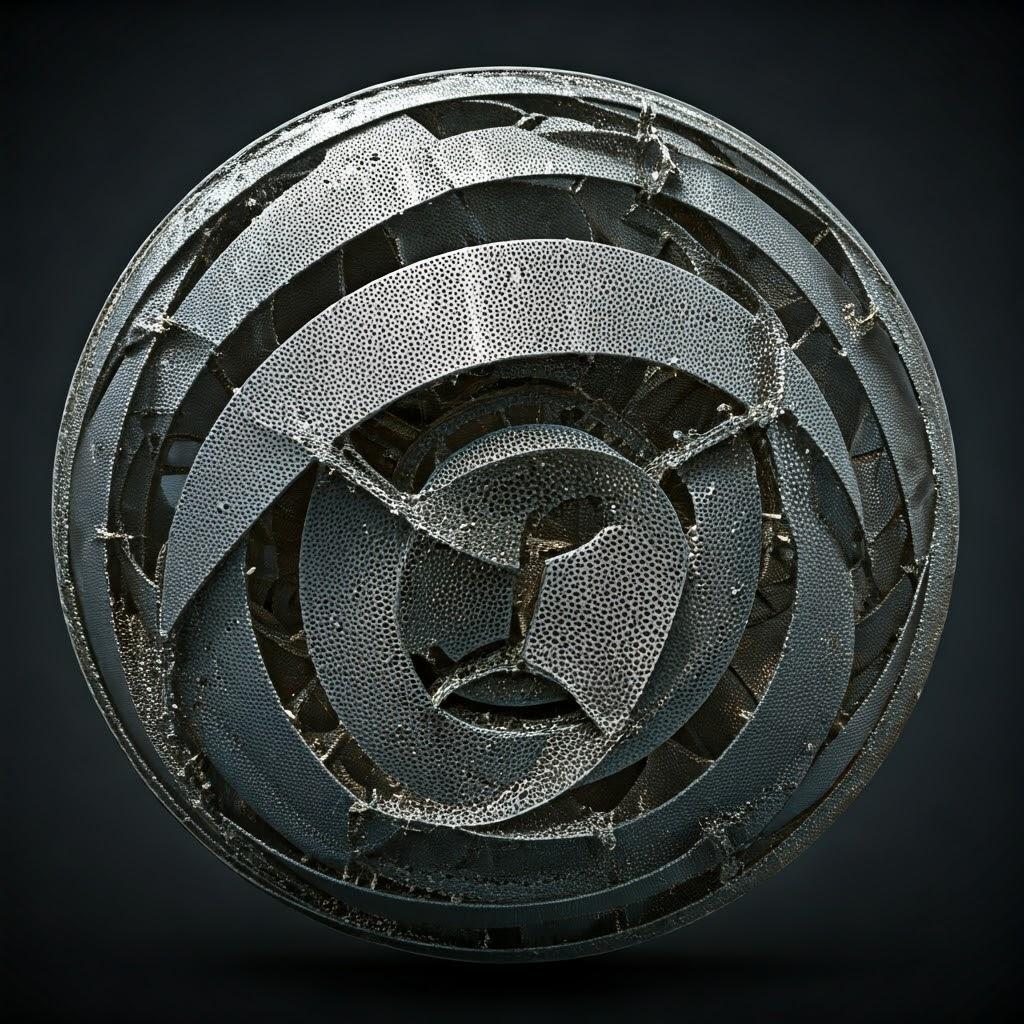
Erreichen von Präzision: Toleranz, Oberflächengüte und Maßgenauigkeit
Während die additive Fertigung von Metallen eine unglaubliche geometrische Freiheit bietet, ist das Verständnis des erreichbaren Präzisionsniveaus entscheidend für die Steuerung der Erwartungen und die Gewährleistung, dass der endgültige Lüftungskanal die funktionalen Anforderungen erfüllt. Toleranz, Oberflächengüte und Gesamtmaßgenauigkeit bei L-PBF werden von den Maschinenfähigkeiten, Prozessparametern, Materialeigenschaften, der Teilegeometrie und den Nachbearbeitungsschritten beeinflusst.
Abmessungstoleranzen:
- Allgemeine L-PBF-Fähigkeit: Hochwertige L-PBF-Systeme, wie sie von erfahrenen Anbietern eingesetzt werden, können in der Regel Maßtoleranzen erreichen, die mit den allgemeinen Toleranzen des Metallfeingusses oder der CNC-Bearbeitung vergleichbar sind. Ein häufig erreichbarer Standard ist ISO 2768-m (mittel) oder manchmal ISO 2768-f (fein) für kleinere, gut unterstützte Merkmale.
- ISO 2768-m Beispiel: Bei einer Featuregröße von 100 mm würde die Toleranz ±0,3 mm betragen. Bei 300 mm könnte sie ±0,5 mm betragen.
- Faktoren, die die Verträglichkeit beeinflussen:
- Thermische Belastung & Verformung: Die wiederholten Erwärmungs- und Abkühlungszyklen, die bei L-PBF auftreten, führen zu Eigenspannungen, die insbesondere bei großen oder dünnwandigen Teilen wie Kanälen zu Verformungen führen können. Dies ist ein Hauptfaktor, der die endgültige Genauigkeit beeinflusst.
- Orientierung aufbauen: Die Ausrichtung des Teils auf der Bauplatte wirkt sich auf thermische Gradienten, Unterstützungsanforderungen und potenzielle Schrumpfung aus und beeinflusst die Maßgenauigkeit entlang der X-, Y- und Z-Achsen unterschiedlich.
- Kalibrierung der Maschine: Eine regelmäßige Kalibrierung des Lasersystems, des Scanners und des Pulverbeschichtungsmechanismus ist für eine gleichbleibende Genauigkeit unerlässlich.
- Geometrie des Teils: Komplexe Geometrien, große ebene Flächen und dünne freitragende Wände sind im Allgemeinen schwieriger genau zu drucken.
- Nachbearbeiten: Eine Spannungsarmglühung ist unerlässlich, um den Verzug zu verringern und die Abmessungen zu stabilisieren. Durch maschinelle Bearbeitung können bei bestimmten Merkmalen wesentlich engere Toleranzen erreicht werden.
- Spezifikation: Kritische Abmessungen, vor allem an Schnittstellen oder Dichtungsflächen, sollten auf Zeichnungen mit spezifischen Toleranzen deutlich gekennzeichnet werden. Es kann notwendig sein, diese engeren Toleranzen durch Nachbearbeitung zu erreichen.
Oberflächengüte (Rauhigkeit):
- Oberflächenrauhigkeit (Ra) im Ist-Zustand: Die Oberflächenbeschaffenheit von L-PBF-Teilen ist aufgrund der schichtweisen Verschmelzung der Pulverpartikel naturgemäß rauer als bei maschinell bearbeiteten Oberflächen.
- Typische Ra-Werte (AlSi10Mg/AlSi7Mg):
- Seitenwände (vertikal): 8 – 15 µm Ra (320 – 600 µin Ra)
- Nach oben gerichtete Oberflächen (Oberseite): 10 – 20 µm Ra (400 – 800 µin Ra) – Kann je nach Parameter glatter sein.
- Nach unten gerichtete Oberflächen (unterstützt): 15 – 30 µm Ra (600 – 1200 µin Ra) – rauer durch den Kontakt mit Stützstrukturen oder teilweise gesintertem Pulver.
- Interne Kanäle: Das Erreichen glatter Innenflächen, insbesondere in komplexen oder engen Kanälen, ist eine Herausforderung. Die Rauheit kann deutlich höher sein als bei Außenflächen, was sich auf die Fluiddynamik auswirkt (erhöhter Druckabfall).
- Typische Ra-Werte (AlSi10Mg/AlSi7Mg):
- Faktoren, die die Oberflächenbeschaffenheit beeinflussen:
- Schichtdicke: Dünnere Schichten ergeben im Allgemeinen glattere Oberflächen, verlängern aber die Bauzeit.
- Laser-Parameter: Die Größe des Strahlflecks, die Scangeschwindigkeit und die Energiedichte wirken sich auf die Eigenschaften des Schmelzbades und die Oberflächenbeschaffenheit aus.
- Partikelgrößenverteilung: Feinere Puder können zu einem glatteren Finish beitragen.
- Orientierung aufbauen: Nach oben gerichtete Flächen sind in der Regel glatter als nach unten gerichtete oder steil abfallende Flächen.
- Verbesserung der Oberflächengüte: Nachbearbeitungsschritte wie Perlstrahlen, Fließschleifen (AFM) für Innenkanäle, Trommeln oder Polieren sind erforderlich, wenn aus ästhetischen oder funktionalen Gründen (z. B. zur Verringerung des Reibungsverlusts bei der Luftströmung) eine glattere Oberfläche als im Ist-Zustand gewünscht wird.
Hohe Genauigkeit erreichen & Finish:
- Partnerschaften mit Experten: Die Zusammenarbeit mit einem AM-Dienstleister wie Met3dp, der Wert auf branchenführende Druckgenauigkeit und Zuverlässigkeit legt, ist entscheidend. Ihr Know-how bei der Optimierung von Druckparametern und der Steuerung des Fertigungsprozesses wirkt sich direkt auf die erreichbare Präzision aus.
- DfAM: Die Gestaltung von Merkmalen, die selbsttragend oder für die Nachbearbeitung leicht zugänglich sind, trägt zu einer besseren Verarbeitung bei.
- Nachbearbeiten: Bei kritischen Toleranzen (z. B. enger als ±0,1 mm) oder sehr glatten Oberflächen (z. B. < 3,2 µm Ra) ist die CNC-Bearbeitung bestimmter Merkmale nach dem Druck und der Wärmebehandlung oft die zuverlässigste Methode. Entwerfen Sie Gegenflansche oder Dichtflächen mit ausreichendem Bearbeitungsmaterial.
- Klare Kommunikation: Stellen Sie Ihrem AM-Lieferanten klare Zeichnungen und Spezifikationen zur Verfügung, in denen kritische Abmessungen, Toleranzen und Anforderungen an die Oberflächenbeschaffenheit aufgeführt sind.
Tabelle: Typische L-PBF-Präzision für AlSi10Mg/AlSi7Mg-Rohre
Parameter | As-Built-Fähigkeit | Beeinflussende Faktoren | Methoden zur Verbesserung | Überlegungen zur Beschaffung |
---|---|---|---|---|
Toleranz | ISO 2768-m (~ ±0,3% des Nennwertes) | Thermische Belastung, Ausrichtung, Geometrie, Maschinenkalibrierung. | Spannungsabbau HT, Nachbearbeitung | Geben Sie kritische Toleranzen klar an; berücksichtigen Sie das zu bearbeitende Material |
Oberflächengüte Ra | 10-25 µm (extern, typisch) | Orientierung, Parameter, Schichtdicke, Pulvergröße | Perlstrahlen, AFM, Trommeln, Polieren | Definieren Sie die Anforderungen an das Finish (Ästhetik vs. Funktion – Fluss) |
Interner Abschluss | Im Allgemeinen rauer als extern | Rinnengeometrie, Zugänglichkeit für die Nachbearbeitung | AFM (potenziell), Entwurf für Strömung | Kritisch für den Druckabfall; kann die Eignung für AM einschränken |
Leckdichtigkeit | Hohe Dichte (>99,5%) erzielbar | Porositätskontrolle (Pulver/Params), Designintegrität | Bearbeitende Dichtungen, Beschichtungen, strenge Prüfungen | Spezifizieren Sie die Anforderungen an die Dichtheitsprüfung (Menge, Druck) |
In Blätter exportieren
Beschaffungsmanager sollten die spezifischen Anforderungen an Toleranzen und Oberflächenbeschaffenheit mit potenziellen Großhandelslieferanten für den Metall-3D-Druck frühzeitig im Prozess besprechen, um die Machbarkeit sicherzustellen und die notwendigen Nachbearbeitungsschritte und die damit verbundenen Kosten zu verstehen.
Mehr als der Druck: Wichtige Nachbearbeitungsschritte für Lüftungskanäle
Die Herstellung eines maßgenauen Lüftungskanals mittels Laser Powder Bed Fusion ist nur der erste Fertigungsschritt. Um das fertige Bauteil in eine funktionsfähige, zuverlässige und integrationsbereite Komponente zu verwandeln, sind in der Regel eine Reihe wichtiger Nachbearbeitungsschritte erforderlich. In diesen Schritten werden Eigenspannungen beseitigt, Stützstrukturen entfernt, die gewünschte Oberflächenbeschaffenheit erreicht und die Integrität des Bauteils überprüft. Das Verständnis dieser Anforderungen ist für die Projektplanung, die Kostenkalkulation und die Auswahl eines kompetenten AM-Lieferanten von entscheidender Bedeutung.
1. Stressabbau Wärmebehandlung:
- Warum es so wichtig ist: Die schnelle Erwärmung und Abkühlung bei L-PBF führt zu erheblichen Eigenspannungen innerhalb des gedruckten Teils. Diese Spannungen können Folgendes verursachen:
- Verzerrung oder Verformung, insbesondere nach der Entnahme von der Bauplatte.
- Reduzierte Maßhaltigkeit.
- Erhöhte Anfälligkeit für Rissbildung oder vorzeitiges Versagen, insbesondere bei Ermüdungsbelastung.
- Prozess: Die Teile werden in der Regel in einem Ofen mit Schutzgasatmosphäre (z. B. Argon) auf eine bestimmte Temperatur unterhalb der Lösungstemperatur der Legierung (z. B. 250-350 °C für AlSi10Mg/AlSi7Mg) erhitzt, für eine bestimmte Dauer (z. B. 1-2 Stunden) gehalten und dann langsam abgekühlt. Dadurch können sich die inneren Spannungen entspannen, ohne dass sich das Gefüge wesentlich verändert.
- Zeitplan: Stressabbau wird in der Regel durchgeführt vor entfernen des Teils von der Bauplatte, um die Verformung während der Trennung zu minimieren.
- Obligatorischer Schritt: Für praktisch alle funktionalen AM-Teile aus Metall, insbesondere für solche mit komplexen Geometrien oder engen Toleranzanforderungen, wie z. B. Rohre, ist die Spannungsentlastung ein obligatorischer Schritt.
2. Entfernen von der Bauplatte & Entfernen der Stützstruktur:
- Abtrennung: Nach dem Spannungsabbau wird das Teil in der Regel durch Drahterodieren (Electrical Discharge Machining) oder mit einer Bandsäge von der Bauplatte getrennt.
- Unterstützung bei der Entfernung: Dies kann einer der arbeitsintensivsten und schwierigsten Nachbearbeitungsschritte sein, insbesondere bei Kanälen mit komplizierten internen Kanälen. Methoden umfassen:
- Manuelles Brechen/Clipping: Die Stützen sind oft mit Schwachstellen versehen, die ein manuelles Entfernen mit Zangen oder Handwerkzeugen erleichtern.
- Bearbeitungen: Möglicherweise ist eine CNC-Bearbeitung oder ein Schleifen erforderlich, um hartnäckige Stützen zu entfernen oder eine bündige Oberfläche an den Stellen zu erzielen, an denen Stützen angebracht waren.
- Abrasive Fließbearbeitung (AFM) / Strangpresshonen: Bei internen Kanälen kann ein Schleifspachtel durch den Kanal gepresst werden, um die Oberflächen zu glätten und möglicherweise interne Stützen zu entfernen, aber die Zugänglichkeit ist entscheidend.
- Elektrochemische Bearbeitung (ECM): Weniger häufig, kann aber Stützen ohne mechanische Kraft auflösen.
- Designauswirkungen: Das DfAM spielt hier eine große Rolle. Die Minimierung der brauchen für Stützen und die Gestaltung von Stützen für einen einfachen Zugang und eine einfache Entfernung reduzieren die Nachbearbeitungszeit und -kosten erheblich.
3. Lösungsglühen und Altern (z.B. T6-Temperierung):
- Zweck: Deutliche Verbesserung der mechanischen Eigenschaften (Festigkeit, Härte) von wärmebehandelbaren Aluminiumlegierungen wie AlSi10Mg und AlSi7Mg.
- Prozess:
- Lösungsfindung: Erhitzen des Teils auf eine höhere Temperatur (z. B. ~500-540 °C), um die Mg- und Si-Elemente in der Aluminiummatrix aufzulösen, gefolgt von einem schnellen Abschrecken (z. B. in Wasser), um sie in einer übersättigten festen Lösung einzufangen.
- Alterung (Ausscheidungshärtung): Durch mehrstündiges Erwärmen des Teils auf eine niedrigere Temperatur (z. B. ~150-180 °C) (künstliche Alterung) bilden sich feine Mg₂Si-Ausscheidungen, die die Versetzungsbewegung behindern und die Festigkeit deutlich erhöhen.
- Erwägung: Die Wärmebehandlung kann zu leichten Maßänderungen (Wachstum oder Schrumpfung) führen, die berücksichtigt werden müssen, insbesondere wenn zuvor eine spanende Bearbeitung erfolgt. Sie wird oft nach der Vorbearbeitung, aber vor der Endbearbeitung durchgeführt.
Die Entfernung der Stützen kann arbeitsintensiv sein und birgt die Gefahr, die Oberfläche des Teils zu beschädigen, wenn sie nicht sorgfältig durchgeführt wird. Dies unterstreicht die Bedeutung der DfAM-Prinzipien, die darauf abzielen, den Stützbedarf zu minimieren und Stützen für eine einfachere Entfernung zu konstruieren.
- Das Ziel: Um die gewünschte Oberflächenstruktur aus funktionalen oder ästhetischen Gründen zu erreichen.
- Gemeinsame Methoden für Kanäle:
- Perlenstrahlen / Sandstrahlen: Treibt feine Medien (Glasperlen, Aluminiumoxid) auf die Oberfläche, um ein gleichmäßiges, ungerichtetes, mattes Finish zu erzeugen. Entfernt effektiv teilweise gesinterte Partikel und kleinere Oberflächenfehler. Standardoberfläche für viele industrielle AM-Teile.
- Taumeln / Vibrationsgleitschleifen: Die Teile werden in eine Wanne mit Schleifmitteln gelegt, die vibrieren oder taumeln, um die Kanten zu entgraten und eine glattere, gleichmäßigere Oberfläche zu erzeugen. Geeignet für Chargen von kleineren Teilen.
- CNC-Bearbeitung: Wird auf speziellen Oberflächen (Flansche, Dichtflächen, kritische Schnittstellen) eingesetzt, um enge Toleranzen und sehr glatte Oberflächen (Ra < 3,2 µm oder besser) zu erzielen.
- Polieren: Manuelles oder automatisiertes Polieren kann spiegelglatte Oberflächen erzielen, ist aber arbeitsintensiv und in der Regel spezifischen ästhetischen oder funktionalen Anforderungen vorbehalten (z. B. extrem geringe Reibung).
- Abrasive Fließbearbeitung (AFM): Kann zur Verbesserung der inneren Oberflächengüte von Kanälen eingesetzt werden, wenn die Geometrie einen ausreichenden Durchfluss des Schleifmittels ermöglicht.
5. Inspektion und Qualitätskontrolle:
- Prüfung der Abmessungen: Einsatz von CMM (Coordinate Measuring Machine), 3D-Scanning oder herkömmlichen Messinstrumenten zur Überprüfung kritischer Abmessungen und Toleranzen anhand der Spezifikation.
- Dichtheitsprüfung: Unverzichtbar für Lüftungskanäle. Methoden umfassen:
- Druckabfalltest: Druckbeaufschlagung des Kanals und Überwachung des Druckabfalls im Laufe der Zeit.
- Helium-Lecktest: Verwendung von Helium als Prüfgas für die hochempfindliche Lecksuche (üblich in der Luft- und Raumfahrt und bei Vakuumanwendungen).
- Zerstörungsfreie Prüfung (NDT): Je nach Kritikalität kann ein CT-Scan (Computertomographie) eingesetzt werden, um innere Strukturen zu untersuchen, Porosität zu erkennen und die Wandstärke zu überprüfen, ohne das Teil zu zerstören. In einigen Fällen kann auch eine Farbeindringprüfung oder eine Durchstrahlungsprüfung durchgeführt werden.
Tabelle: Post-Processing-Workflow für AM-Lüftungskanäle
Schritt | Zweck | Gemeinsame Methoden | Wichtige Überlegungen | B2B-Lieferanten-Checkpoint |
---|---|---|---|---|
1. Stressabbau HT | Eigenspannungen reduzieren, Verzug verhindern | Ofenheizung (inerte Atmosphäre), langsames Abkühlen | Obligatorisch; wenn möglich auf der Bauplatte durchführen | Verfügt der Lieferant über kalibrierte HT-Kapazitäten? |
2. Entfernen von Teilen/Trägern | Von der Platte abtrennen, Stützen entfernen | Drahterodieren/Säge; manuelles Brechen, Bearbeitung, AFM | Design für Barrierefreiheit; arbeitsintensiv | Was sind die Techniken/Beschränkungen für die Entfernung der Unterstützung? |
3. Stärkung der HT (T6) | Erhöhung der Festigkeit und Härte | Solubilisierung, Abschrecken, Alterung | Kann zu leichten Maßveränderungen führen; geeigneten Härtegrad wählen | Können sie zertifizierte Wärmebehandlungen durchführen? |
4. Oberflächenveredelung | Erreichen der gewünschten Textur, Glätte | Perlstrahlen, Taumeln, Maschine, Polieren, AFM | Definition der Anforderungen (Ra); interne Herausforderungen bei der Fertigstellung | Welche Standard-/Optionsausführungen bieten sie an? |
5. Bearbeitung (Gezielt) | Erzielen enger Toleranzen/Glätte bei wichtigen Merkmalen | CNC-Fräsen, Drehen | Erfordert Zulage für Bearbeitungsmaterial in der Konstruktion | Bieten sie integrierte Bearbeitungsdienstleistungen an? |
6. Inspektion & Prüfung | Überprüfung der Abmessungen, Integrität und Dichtigkeit | CMM, 3D-Scan, Dichtheitsprüfung (Druck/Helium), NDT | Definieren Sie kritische Spezifikationen; wichtig für kritische Teile | Wie sehen die QA/QC-Verfahren und die Ausrüstung aus? |
In Blätter exportieren
Die Zusammenarbeit mit einem Full-Service-Anbieter für Metall-AM, der umfassende Nachbearbeitungsmöglichkeiten intern oder über qualifizierte Partner anbietet, vereinfacht die Lieferkette und gewährleistet die Verantwortung für die Qualität des Endprodukts. Beschaffungsmanager sollten sich nach diesen Fähigkeiten erkundigen, wenn sie potenzielle Lieferanten für Großhandels- oder projektbezogene Aufträge evaluieren.
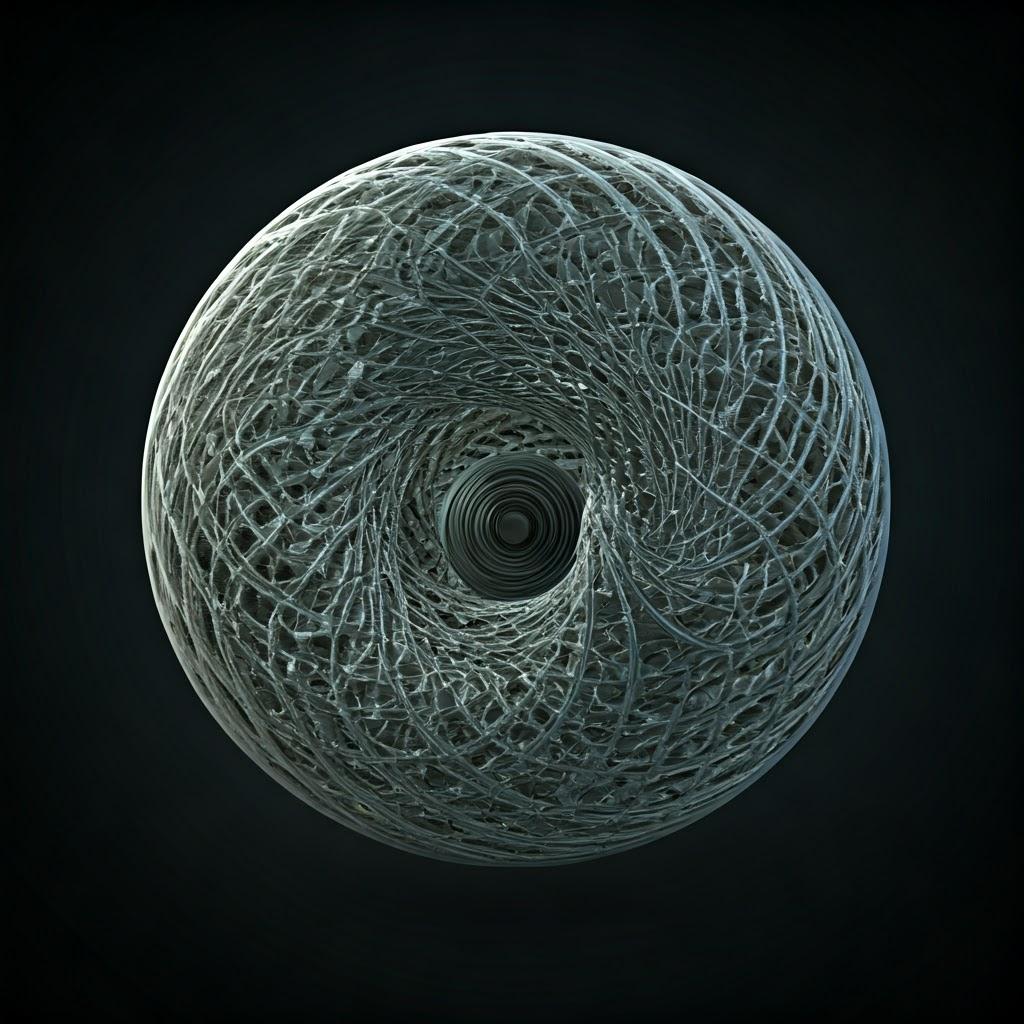
Herausforderungen meistern: Erfolg beim 3D-Druck komplexer Rohre sicherstellen
Der 3D-Metalldruck bietet zwar erhebliche Vorteile für die Herstellung komplexer Lüftungskanäle, ist aber auch nicht ohne Herausforderungen. Das Bewusstsein für potenzielle Probleme und die Umsetzung von Strategien zur Schadensbegrenzung während der Konstruktion, des Drucks und der Nachbearbeitung sind der Schlüssel zur Gewährleistung erfolgreicher Ergebnisse, der Maßhaltigkeit und der Zuverlässigkeit der Komponenten. Ingenieure und Beschaffungsteams sollten sich dieser allgemeinen Hürden bewusst sein:
1. Verformung und Verzerrung:
- Die Ursache: Ungleichmäßige Erwärmung und Abkühlung während des schichtweisen L-PBF-Verfahrens erzeugen innere Spannungen. Wenn sich diese Spannungen akkumulieren, können sie die Streckgrenze des Materials oder die Verankerungswirkung von Stützen überwinden und dazu führen, dass sich das Teil verzieht oder verformt, insbesondere bei großen, flachen oder dünnwandigen Abschnitten, wie sie in Kanälen üblich sind.
- Milderung:
- Optimierte Ausrichtung: Positionieren Sie den Kanal auf der Bauplatte, um große flache Bereiche parallel zur Platte zu minimieren und thermische Gradienten zu verringern.
- Robuste Stützstrukturen: Verwenden Sie gut konzipierte Stützen (ausreichende Dichte und Kontaktpunkte), um das Teil fest auf der Bauplatte zu verankern und thermischen Spannungen entgegenzuwirken. Ziehen Sie Block- oder konische Stützen für eine bessere Wärmeleitung feinen Gittern vor.
- Build Plate Heating: Die Verwendung von beheizten Bauplatten (die in vielen L-PBF-Systemen üblich sind) trägt zur Verringerung des Wärmegradienten zwischen dem Teil und der Platte bei.
- Optimierung der Prozessparameter: Erfahrene AM-Anbieter nehmen eine Feinabstimmung von Laserleistung, Scangeschwindigkeit und Schraffurstrategien vor, um den Wärmeeintrag zu steuern und die Stressakkumulation zu minimieren.
- Obligatorischer Stressabbau: Die Durchführung einer Spannungsarmglühung, idealerweise vor der Entnahme der Platte, ist der wichtigste Schritt, um die induzierten Spannungen abzubauen und das Teil zu stabilisieren.
2. Reststress-Management:
- Die Ursache: Wie bereits erwähnt, sind Eigenspannungen für L-PBF typisch. Selbst wenn sie keine sichtbaren Verformungen verursachen, können sich hohe Eigenspannungen negativ auswirken:
- Dimensionsstabilität: Teile können nach der Bearbeitung ihre Form geringfügig verändern, wenn die Spannungen nicht abgebaut werden.
- Mechanische Eigenschaften: Insbesondere die Ermüdungslebensdauer kann erheblich reduziert werden.
- Rissanfälligkeit: Vor allem bei der Nachbearbeitung oder unter betrieblicher Belastung.
- Milderung:
- DfAM: Vermeiden Sie abrupte Dickenänderungen; verwenden Sie Filets.
- Strategie unterstützen: Die Stützen helfen, den Stress, der sich während des Drucks aufbaut, zu bewältigen.
- Steuerung der Parameter: Wie oben erwähnt, sind optimierte Parameter der Schlüssel.
- Stressabbau Wärmebehandlung: Unbedingt erforderlich, um die negativen Auswirkungen von Eigenspannungen abzuschwächen. Für hochkritische Anwendungen können weitere Behandlungen wie spezielle Glühzyklen in Betracht gezogen werden.
3. Schwierigkeiten beim Entfernen der Stützen:
- Die Ursache: Komplexe Innengeometrien, tiefe Kanäle oder Gitter in Kanälen können es extrem schwierig oder unmöglich machen, Stützstrukturen nach dem Druck zu erreichen und vollständig zu entfernen. Verbleibendes Stützmaterial kann den Durchfluss behindern, sich später lösen und Schäden verursachen oder unerwünschtes Gewicht hinzufügen.
- Milderung:
- DfAM ist überragend: Entwerfen Sie die inneren Kanäle so, dass sie selbsttragend sind (z. B. tropfen- oder rautenförmig). Richten Sie das Teil so aus, dass interne Überhänge minimiert werden.
- Lösliche/Breakaway-Träger: Die Forschung ist im Gange, aber zuverlässige lösliche Metallträger sind noch nicht Standard. Entwerfen Sie Halterungen mit leicht abbrechbaren Verbindungspunkten.
- Planung der Zugänglichkeit: Wenn interne Abstützungen unvermeidbar sind, sollten spezielle Zugangsöffnungen für Werkzeuge oder Spülvorgänge (z. B. AFM) in den Kanal eingebaut werden. Diese Öffnungen müssen möglicherweise später verschlossen oder verschweißt werden.
- Konsultation der Lieferanten: Besprechen Sie komplexe Innengeometrien frühzeitig mit Ihrem AM-Lieferanten. Er kann Sie aufgrund seiner Erfahrung und Ausrüstung (z. B. Spezialwerkzeuge, AFM) über die Machbarkeit und mögliche Entfernungsstrategien beraten.
4. Porosität:
- Die Ursache: Lücken im gedruckten Material können entstehen durch:
- Gas Porosität: Eingeschlossenes Gas (z. B. Argon, das in der Baukammer verwendet wird) im Schmelzbad, das oft durch nicht kugelförmiges oder innerlich poröses Pulver verschlimmert wird.
- Schlüsselloch-Porosität: Instabile Schmelzbaddynamik aufgrund falscher Laserparameter (z. B. zu hohe Energiedichte), die zu einem Kollaps des Dampfraums führt.
- Fehlende Fusion: Unzureichender Energieeintrag, der zu nicht aufgeschmolzenen Pulverpartikeln zwischen Schichten oder Scannerspuren führt.
- Auswirkungen: Porosität verringert die Materialdichte, verschlechtert die mechanischen Eigenschaften (insbesondere die Ermüdungsfestigkeit) und kann zu Leckagen führen.
- Milderung:
- Hochwertiges Pulver: Die Verwendung von Pulvern mit hoher Sphärizität, kontrollierter PSD und geringem internen Gasgehalt (wie die von Met3dp durch fortschrittliche Zerstäubung hergestellten Pulver) ist von grundlegender Bedeutung. Pulverhandhabung und Recyclingprotokolle sind ebenfalls entscheidend.
- Optimierte Druckparameter: Eine umfangreiche Prozessentwicklung durch den AM-Anbieter gewährleistet ein stabiles Schmelzbadverhalten und ausreichend Energie für die vollständige Fusion.
- Heiß-Isostatisches Pressen (HIP): Bei kritischen Anwendungen, die eine Dichte von nahezu 100 % erfordern, kann das HIP-Verfahren (Hochdruck-Hochtemperatur-Verfahren) nach dem Druck eingesetzt werden, um innere Hohlräume zu schließen. Dies verursacht jedoch erhebliche Kosten und Vorlaufzeiten und ist bei typischen Aluminiumrohren weniger üblich, sofern sie nicht für die Luft- und Raumfahrt spezifiziert sind.
5. Erreichen und Überprüfen der Dichtheit:
- Die Ursache: Die vollständige Abdichtung eines Kanals gegen Leckagen kann aufgrund möglicher Porosität, Mikrorisse (wenn die Spannungen nicht beherrscht werden) oder Unvollkommenheiten an den Dichtungsschnittstellen eine Herausforderung darstellen.
- Milderung:
- Design for Sealing: Einbau von gut gestalteten Flanschen oder Schnittstellen, die für Standarddichtungen oder O-Ringe geeignet sind. Sorgen Sie für eine ausreichende Oberfläche und Ebenheit (oft durch Nachbearbeitung erreicht).
- Prozesskontrolle: Die Erzielung einer hohen Dichte (>99,5 %) während des Drucks durch Qualitätspulver und optimierte Parameter ist der Schlüssel.
- Nachbearbeiten: Die maschinelle Bearbeitung der Dichtungsflächen garantiert Ebenheit und Glätte. Bestimmte Beschichtungen können möglicherweise dazu beitragen, kleinere Porositäten zu versiegeln.
- Strenge Tests: Die Implementierung geeigneter Lecktestprotokolle (Druckabfall, Helium) als Teil des Qualitätskontrollprozesses ist unerlässlich, um die Integrität vor dem Versand zu überprüfen. Legen Sie gemeinsam mit dem Lieferanten akzeptable Leckraten fest.
Tabelle: Häufige AM-Duct-Herausforderungen und Lösungen
Herausforderung | Hauptursache(n) | Minderungsstrategien | Wichtigkeitsstufe |
---|---|---|---|
Verwerfung/Verzerrung | Akkumulation von thermischem Stress | Ausrichtung, Stützen, Wärme der Bauplatte, Parameter Opt., Stressabbau HT | Hoch |
Eigenspannung | Inhärente thermische Zyklen | DfAM, Unterstützt, Parameter Opt., Stressabbau HT (Mögliche weitere HT) | Hoch |
Entfernen der Stütze | Komplexe interne Geometrie, schlechter Zugang | DfAM (selbsttragend)design von Zugangsöffnungen, zerbrechliche Halterungen, AFM, Lieferantenberatung | Hoch |
Porosität | Pulverqualität, Parameter (Keyhole/Fusion) | Hochwertiges Pulverparameter Opt., (HIP wenn kritisch) | Mittel-Hoch |
Leckdichtigkeit | Porosität, Mikrorisse, Grenzflächenmängel | Design for Seal, Prozesskontrolle (Dichte), Nachbearbeitungsschnittstellen, Dichtheitsprüfung | Hoch |
In Blätter exportieren
Die erfolgreiche Bewältigung dieser Herausforderungen erfordert eine Kombination aus intelligentem Design (DfAM), sorgfältiger Prozesskontrolle während des Drucks, angemessener Nachbearbeitung und strenger Qualitätssicherung. Für Beschaffungsmanager, die zuverlässige, qualitativ hochwertige 3D-gedruckte Lüftungskanäle suchen, ist es entscheidend, mit einem erfahrenen Anbieter von additiver Fertigung aus Metall zusammenzuarbeiten, der diese potenziellen Fallstricke kennt und über etablierte Prozesse verfügt, um sie zu entschärfen.
Auswahl des Lieferanten: Die Wahl des richtigen 3D-Metalldruck-Partners für Rohrleitungsbau
Die Auswahl des richtigen Partners für die additive Fertigung ist für die Herstellung hochwertiger, zuverlässiger 3D-gedruckter Lüftungskanäle wohl ebenso entscheidend wie das Design selbst. Die Feinheiten der L-PBF-Verarbeitung, insbesondere bei reaktiven Materialien wie Aluminiumlegierungen, erfordern spezifisches Fachwissen und eine solide Qualitätskontrolle. Für Beschaffungsmanager, Ingenieure und Großeinkäufer, die konsistente Ergebnisse und zuverlässigen Service suchen, ist die Bewertung potenzieller Lieferanten auf der Grundlage einer umfassenden Reihe von Kriterien unerlässlich.
Hier finden Sie eine Checkliste, die Sie bei der Auswahl eines Metall-AM-Dienstleisters unterstützt:
1. Bewährte Erfahrung mit leichten Aluminiumlegierungen:
- Erfordernis: Nachgewiesene Erfahrung speziell mit AlSi10Mg und/oder AlSi7Mg unter Verwendung von L-PBF. Verlangen Sie Nachweise über erfolgreiche Projekte mit diesen Werkstoffen.
- Warum das wichtig ist: Jede Legierung verhält sich anders. Die richtige Entwicklung von Parametern, Handhabungsprotokollen (zur Vermeidung von Verunreinigungen und zur Beherrschung der Reaktivität) und das Verständnis der Wärmebehandlungsreaktionen sind entscheidend für das Erreichen der gewünschten Eigenschaften und der Integrität der Teile.
2. Erweiterte Fähigkeiten des L-PBF-Systems:
- Erfordernis: Zugang zu gut gewarteten, industrietauglichen L-PBF-Maschinen mit Eigenschaften wie:
- Ausreichendes Bauvolumen für die Abmessungen Ihres Kanals.
- Kontrolle der inerten Atmosphäre (Argon).
- Möglichkeiten der prozessbegleitenden Überwachung (z. B. Schmelzbadüberwachung) können für die Qualitätssicherung von Vorteil sein.
- Gleichbleibende Laserleistung und Strahlqualität.
- Warum das wichtig ist: Maschinenqualität und -kalibrierung wirken sich direkt auf die Dichte der Teile, die Maßgenauigkeit, die Oberflächenbeschaffenheit und die allgemeine Konsistenz aus. Anbieter wie Met3dp betonen, dass ihre Drucker’ branchenführendes Druckvolumen, Genauigkeit und Zuverlässigkeitdie bei anspruchsvollen Bauteilen wie komplexen Kanälen kritische Faktoren sind.
3. Strenges Qualitätsmanagement bei Pulver:
- Erfordernis: Strenge Verfahren für die Beschaffung, Prüfung, Handhabung, Lagerung und das Recycling von Metallpulvern. Dies beinhaltet:
- Beschaffung bei renommierten Lieferanten mit fortschrittlichen Zerstäubungsmöglichkeiten (wie Met3dp’s Verwendung von Gaszerstäubung und PREP).
- Qualitätskontrolle der eingehenden Pulver (Chemie, PSD, Morphologie, Fließfähigkeit).
- Kontrollierte Lagerumgebung (niedrige Luftfeuchtigkeit).
- Dokumentierte Pulverrecycling- und Mischstrategie zur Aufrechterhaltung der Qualität im Laufe der Zeit (Verfolgung der Pulververwendungszyklen).
- Rückverfolgbarkeit des Materials von der Rohpulvercharge bis zum fertigen Teil.
- Warum das wichtig ist: Die Qualität des Pulvers ist von grundlegender Bedeutung für die Qualität des Endprodukts, da sie sich direkt auf Dichte, Porosität und mechanische Eigenschaften auswirkt. Inkonsistentes oder verunreinigtes Pulver führt zu unzuverlässigen Teilen.
4. Robustes Qualitätsmanagementsystem (QMS) & Zertifizierungen:
- Erfordernis: Achten Sie auf einschlägige Zertifizierungen, die ein Engagement für Qualität und Prozesskontrolle belegen.
- ISO 9001: Grundlage für das Qualitätsmanagement.
- AS9100: Wird häufig von Zulieferern der Luft- und Raumfahrtindustrie verlangt, um die Einhaltung der strengen Qualitätsstandards der Luft- und Raumfahrtindustrie zu belegen.
- ISO 13485: Relevant bei der Herstellung von Kanälen für medizinische Geräte.
- Warum das wichtig ist: Zertifizierungen zeigen, dass der Lieferant über dokumentierte Prozesse verfügt, standardisierte Verfahren anwendet, die Rückverfolgbarkeit aufrechterhält und sich externen Audits unterzieht, was ein höheres Maß an Vertrauen in seine Tätigkeit schafft.
5. Unterstützung des Designs für additive Fertigung (DfAM):
- Erfordernis: Der Anbieter sollte die DfAM-Prinzipien verstehen und idealerweise Beratungs- oder Co-Design-Dienste anbieten. Er sollte in der Lage sein, Ihr Design zu überprüfen und Feedback zu Druckbarkeit, Supportstrategie, Ausrichtung und Funktionsoptimierung zu geben.
- Warum das wichtig ist: Ein Zulieferer, der einfach eine beliebige Datei druckt, liefert möglicherweise kein optimales Teil. Ein echter Partner arbeitet zusammen, um sicherzustellen, dass das Design gut für den AM-Prozess geeignet ist, um die Vorteile zu maximieren und die Risiken zu minimieren.
6. Umfassende Post-Processing-Funktionen:
- Erfordernis: Interne oder engmaschig verwaltete externe Kapazitäten für alle erforderlichen Nachbearbeitungsschritte, die zuvor identifiziert wurden:
- Zertifizierte Wärmebehandlung (Spannungsarmglühen, T6-Alterung) mit kalibrierten Öfen.
- Effiziente und wirksame Techniken zum Entfernen von Stützen (ggf. auch für interne Merkmale).
- Gezielte CNC-Bearbeitung für kritische Toleranzen und Oberflächen.
- Verschiedene Möglichkeiten der Oberflächenbearbeitung (Perlstrahlen usw.).
- Gründliche Reinigungsverfahren.
- Wesentliche Inspektions- und Prüfgeräte (CMM, Dichtheitsprüfung).
- Warum das wichtig ist: Ein vertikal integrierter Anbieter oder ein Anbieter mit starken Partnerschaften vereinfacht die Lieferkette, verkürzt die Vorlaufzeiten und gewährleistet die Verantwortung für die Qualität des Endprodukts von Anfang bis Ende. Met3dp positioniert sich als Anbieter von umfassende Lösungen die Drucker, Pulver und Anwendungsentwicklung umfassen.
7. Erfolgsbilanz und einschlägige Erfahrung:
- Erfordernis: Fragen Sie nach Fallstudien, Referenzen oder Beispielen von hergestellten Teilen, die in Bezug auf Komplexität, Material oder industrielle Anwendung mit Ihrem Lüftungskanal vergleichbar sind.
- Warum das wichtig ist: Erfolg in der Vergangenheit ist ein guter Indikator für zukünftige Leistungen. Erfahrung mit spezifischen Branchenanforderungen (z. B. Dokumentation für die Luft- und Raumfahrt, PPAP für die Automobilindustrie) ist entscheidend.
8. Kapazität, Vorlaufzeit, Kommunikation und Skalierbarkeit:
- Erfordernis: Vergewissern Sie sich, dass der Lieferant die Kapazität hat, Ihre Projektfristen einzuhalten, sei es für Prototypen oder für eine mögliche Kleinserienproduktion. Er sollte realistische und transparente Schätzungen der Vorlaufzeit abgeben. Erkundigen Sie sich, ob er die Produktion bei Bedarf skalieren kann.
- Warum das wichtig ist: Unrealistische Versprechungen führen zu Verzögerungen. Eine offene Kommunikation über Kapazitäten und potenzielle Engpässe ist der Schlüssel zur Projektplanung.
9. Kostentransparenz und Wert:
- Erfordernis: Der Anbieter sollte ein detailliertes, aufgeschlüsseltes Angebot vorlegen, in dem die Kosten für Material, Druck, Nachbearbeitung, Inspektion usw. klar aufgeführt sind. Bewerten Sie auf der Grundlage des Gesamtwerts, nicht nur der anfänglichen Druckkosten.
- Warum das wichtig ist: Das Verständnis der Kostenaufschlüsselung hilft beim Vergleich von Anbietern und bei der Identifizierung potenzieller Bereiche für die Kostenoptimierung durch Designänderungen. Das billigste Angebot bietet möglicherweise nicht den besten Wert, wenn die Qualität oder Nachbearbeitung beeinträchtigt wird.
10. Kundenservice und partnerschaftlicher Ansatz:
- Erfordernis: Suchen Sie nach einem Lieferanten, der reaktionsschnell und kommunikativ ist und der bereit ist, als echter technischer Partner und nicht nur als Auftragsfertiger zu agieren. Er sollte für technische Diskussionen zugänglich sein und mögliche Probleme proaktiv angehen.
- Warum das wichtig ist: Komplexe Projekte profitieren in hohem Maße von der Zusammenarbeit. Ein guter Partner, der z. B. das Ziel hat <a href=”[ungültige URL entfernt]” target=”_blank”>Partnerschaften mit Organisationen</a> um 3D-Druck zu implementieren und Transformationen zu beschleunigen, investiert in das Verständnis Ihrer Bedürfnisse und stellt den Projekterfolg sicher.
Tabelle: Wichtige Kriterien für die Lieferantenbewertung
Kriterium | Warum es für Kanäle wichtig ist | Fragen an potenzielle Zulieferer | Ziel: Großhandel/Beschaffung Schwerpunkt |
---|---|---|---|
Fachwissen über Legierungen | Sorgt für korrekte Parameter, Eigenschaften, Handhabung | Was sind Ihre Erfahrungen mit AlSi10Mg/AlSi7Mg? Können Sie Daten/Beispiele mitteilen? | Nachweis der materialspezifischen Leistungsfähigkeit |
Qualität der Maschine | Beeinflusst Genauigkeit, Verarbeitung, Baugröße | Welche L-PBF-Maschinen verwenden Sie? Wie hoch ist das Bauvolumen? Häufigkeit der Kalibrierung? Überwachung? | Sicherstellung der technischen Eignung für die Anforderungen |
Pulver-Management | Garantiert Materialintegrität, reduziert Mängel | Beschreiben Sie Ihre Verfahren für die Beschaffung, Prüfung, Handhabung und das Recycling von Pulver. Wie stellen Sie die Rückverfolgbarkeit sicher? | Bewertung der Qualitätskontrolle von Einsatzmaterial |
QMS/Zertifikate | Nachweis der Prozesskontrolle & Einhaltung | Sind Sie nach ISO 9001 zertifiziert? AS9100? Können Sie Kopien der Zertifizierung vorlegen? | Überprüfung der Einhaltung von Industriestandards |
DfAM-Unterstützung | Optimiert das Design für Druckbarkeit, Leistung und Kosten | Bieten Sie DfAM-Beratung an? Können Sie unseren Entwurf auf AM-Tauglichkeit überprüfen? | Bewertung des Niveaus der technischen Partnerschaft |
Nachbearbeitung | Sicherstellen, dass das Teil alle funktionalen Anforderungen erfüllt | Welche Nachbearbeitungen führen Sie intern durch, welche extern? Beschreiben Sie Ihre HT, Bearbeitung, Endbearbeitung, Prüfung. | Bewertung der End-to-End-Dienstleistungsfähigkeit |
Erfolgsbilanz | Erbringt den Nachweis der Leistungsfähigkeit und Zuverlässigkeit | Können Sie Fallstudien oder Referenzen für ähnliche Teile/Industriezweige vorlegen? | Validierung von Erfahrungen und bisherigen Leistungen |
Kapazität/Vorlaufzeit | Gewährleistet rechtzeitige Lieferung | Wie hoch ist Ihre derzeitige Kapazität/typische Vorlaufzeit für diese Art von Teilen? Wie handhaben Sie die Terminplanung? | Bestätigung der Fähigkeit, die Projektfristen einzuhalten |
Kostentransparenz | Ermöglicht eine genaue Budgetierung und Wertbestimmung | Können Sie ein detailliertes Angebot erstellen? Was sind die wichtigsten Kostenfaktoren für dieses Teil? | Gewährleistung einer klaren und vorhersehbaren Preisgestaltung |
Partnerschaft | Erleichtert die Kommunikation und Problemlösung | Wer wäre unser technischer Hauptansprechpartner? Wie handhaben Sie die Kommunikation während der Projekte? | Bewertung der langfristigen Lieferantenbeziehungen |
In Blätter exportieren
Eine gründliche Bewertung potenzieller Zulieferer für die additive Fertigung von Metallprodukten anhand dieser Kriterien erhöht die Wahrscheinlichkeit erheblich, dass Sie qualitativ hochwertige und zuverlässige Lüftungskanäle erhalten, die Ihren Spezifikationen und Leistungserwartungen entsprechen.
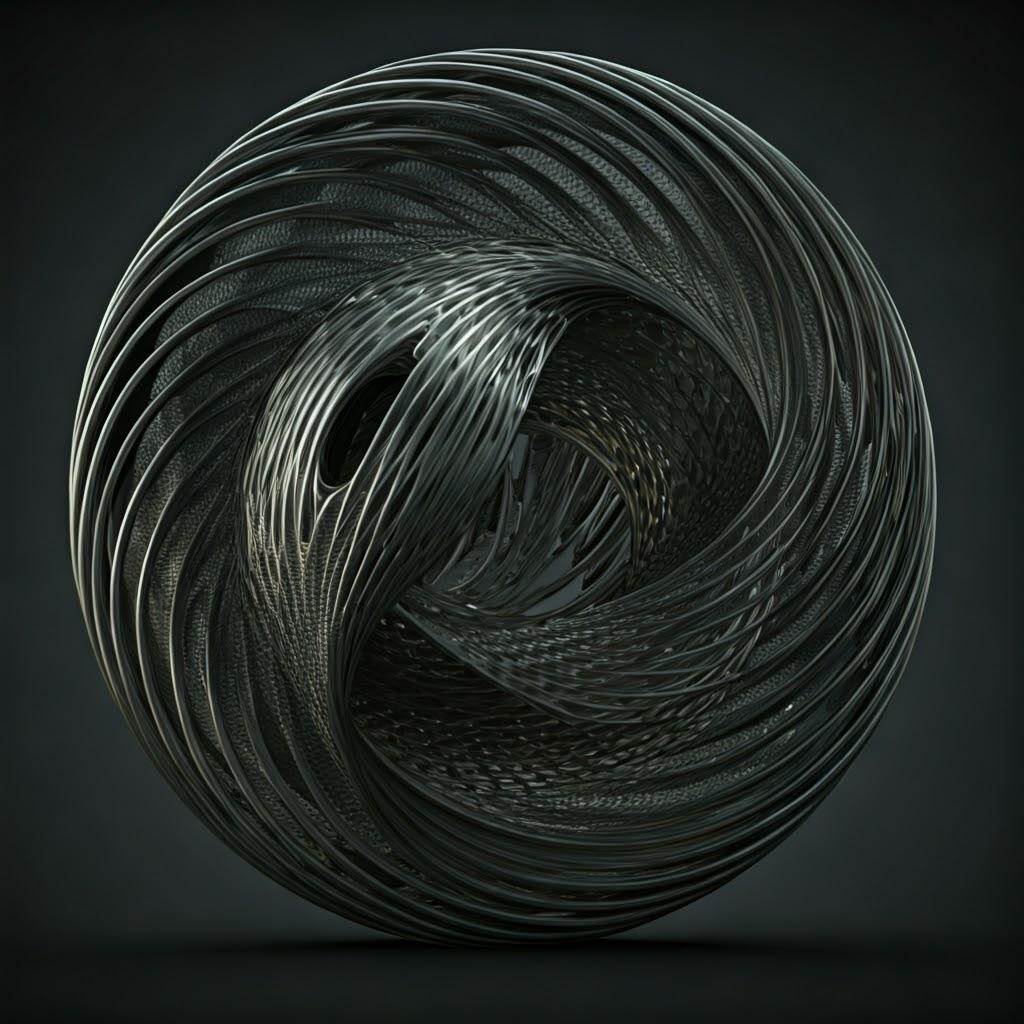
Die Investition verstehen: Kostenfaktoren und Vorlaufzeiten für AM-Rohre
Der 3D-Metalldruck bietet zwar überzeugende technische Vorteile für komplexe Lüftungskanäle, doch ist das Verständnis der damit verbundenen Kosten und typischen Fristen für die Projektbudgetierung und -planung entscheidend. Im Gegensatz zu Massenproduktionstechniken, bei denen die Amortisation von Werkzeugen dominiert, sind die Kosten von AM-Teilen direkter mit dem Materialverbrauch, der Maschinenzeit und der arbeitsintensiven Nachbearbeitung verbunden.
Die wichtigsten Kostentreiber für 3D-gedruckte Lüftungskanäle:
- Materialverbrauch:
- Teilband: Das physische Volumen des endgültigen Kanaldesigns. Die Gewichtsreduzierung durch Topologieoptimierung reduziert diese Kosten direkt.
- Unterstützungsstruktur Volumen: Materialverbrauch für Stützen, der bei komplexen Kanälen mit Überhängen oft erheblich ist. Die Bemühungen des DfAM, Stützen zu minimieren, führen zu direkten Kosteneinsparungen.
- Pulverkosten: Der Preis pro Kilogramm des gewählten Aluminiumlegierungspulvers (z. B. AlSi10Mg). Hochwertige Pulver, die für anspruchsvolle Anwendungen geeignet sind, sind teurer. Auch die Abfall-/Recyclingeffizienz spielt eine Rolle.
- Maschinenzeit (L-PBF-Drucker-Nutzung):
- Bauhöhe: Bestimmt in erster Linie die Anzahl der Schichten und damit die Gesamtdruckzeit. Höhere Teile brauchen länger.
- Teilvolumen/Dichte: Beeinflusst die zu scannende Fläche pro Schicht. Das Scannen von Vollprofilen dauert länger als das von dünnen Wänden oder Gittern.
- Anzahl der Teile pro Build: Durch das effiziente Verschachteln mehrerer Teile in der Baukammer wird die Maschinenzeit effektiver genutzt, wodurch die Kosten pro Teil gesenkt werden (relevant für Großhandels- oder Serienaufträge).
- Maschine Stundensatz: Variiert je nach AM-Anbieter, Ausgereiftheit der Maschine und Betriebskosten.
- Arbeitskosten:
- Vorverarbeitung: Vorbereitung von CAD-Dateien, Planung des Baulayouts (Verschachtelung, Ausrichtung, Erzeugung von Stützen). Kann für komplexe Konstruktionen von Bedeutung sein.
- Nachbearbeiten: Dies ist oft ein wichtiger Kostenfaktor:
- Entfernen der Halterung (kann sehr zeitaufwendig sein, insbesondere bei internen Halterungen).
- Wärmebehandlung (Ofenzeit, Energie, Arbeit).
- Manuelle Fertigstellung/Bearbeitung (Facharbeiterzeit).
- Inspektion & Lager; Qualitätskontrolle (Technikerzeit, Geräteeinsatz).
- Qualitätssicherung & Prüfung:
- Prüfung der Abmessungen: CMM-Programmierung und Messzeit.
- Dichtheitsprüfung: Einrichtungs- und Prüfzeit pro Teil.
- NDT (falls erforderlich): CT-Scans oder andere NDT-Methoden verursachen erhebliche Kosten.
- Gemeinkosten und Gewinn: Standardgeschäftskosten, die mit dem Betrieb einer fortschrittlichen Fertigungsanlage verbunden sind.
Faktoren, die die Gesamtkosten beeinflussen:
- Komplexität des Designs: Kompliziertere Designs erfordern oft mehr Trägermaterial und eine komplexere, zeitaufwändigere Entfernung und Nachbearbeitung der Träger.
- Teil Größe: Größere Teile verbrauchen mehr Material und Maschinenzeit. Die Bauhöhe ist ein wichtiger Faktor für die Druckzeit.
- Wanddicke: Sehr dünne Wände erfordern möglicherweise langsamere Druckgeschwindigkeiten oder robustere Halterungen, während sehr dicke Abschnitte den Materialverbrauch und die Druckzeit erhöhen.
- Toleranzen & Anforderungen an die Oberflächengüte: Engere Toleranzen oder glattere Oberflächen erfordern zusätzliche Nachbearbeitungsschritte, insbesondere Bearbeitung und Polieren, was die Arbeitskosten erheblich erhöht.
- Menge: Während bei AM keine Werkzeugkosten anfallen, sind die Skaleneffekte weniger dramatisch als bei traditionellen Methoden. Allerdings bedeuten die Rüstkosten und die Vorteile der Maschinenauslastung, dass die Kosten pro Teil bei größeren Losgrößen in der Regel etwas sinken (relevant für Großhandelsaufträge im Metall-3D-Druck).
- Wärmebehandlungszyklen: Spezifische oder mehrfache Wärmebehandlungszyklen erhöhen die Zeit- und Energiekosten des Ofens.
Typische Vorlaufzeiten:
Die Vorlaufzeit ist die Gesamtdauer von der Auftragserteilung bis zur Auslieferung des Teils. Sie ist sehr unterschiedlich, umfasst aber im Allgemeinen:
- Zeit in der Warteschlange: Wartezeit bis zur Verfügbarkeit der Maschine (kann je nach Auslastung des Lieferanten zwischen Tagen und Wochen variieren).
- Planung und Einrichtung von Gebäuden: Vorbereitung der Build-Datei (Stunden bis zu einem Tag).
- Druckzeit: Hängt stark von der Höhe und dem Volumen der Teile ab (kann von 12 Stunden bis zu mehreren Tagen reichen, bei sehr großen/komplexen Teilen sogar über eine Woche).
- Abkühlungszeit: Abkühlung der Baukammer und des Teils vor dem Ausbau (mehrere Stunden).
- Nachbearbeiten: Dies dauert oft genauso lange oder länger als der Druck selbst:
- Wärmebehandlung (einschließlich Hochfahren, Einweichen, Abkühlen): 1-2 Tage pro Zyklus.
- Entfernung der Stütze/Fertigstellung: Sehr variabel (Stunden bis Tage je nach Komplexität).
- Bearbeitungen: Abhängig von der Komplexität und der Terminplanung der Maschinenwerkstatt (Tage).
- Inspektion/Prüfung: Stunden bis Tage.
- Versand: Standard-Laufzeit.
Geschätzte Vorlaufzeitspannen (AlSi-Rohre):
- Prototypen (1-5 Einheiten): In der Regel 1 bis 3 Wochen, je nach Komplexität und Nachbearbeitungsbedarf.
- Kleinserienproduktion (10-50 Einheiten): In der Regel 3 bis 6 Wochen, abhängig von der Größe der Teile (wie viele passen pro Bau) und der Optimierung des Nachbearbeitungsworkflows.
Tabelle: Zusammenfassung der Faktoren für Kosten und Vorlaufzeit
Faktor | Primäre Auswirkungen auf | Wie man optimiert/verwaltet | Überlegungen zur Beschaffung |
---|---|---|---|
Teil Volumen/Gewicht | Materialkosten, Druckzeit | Topologieoptimierung, DfAM-Leichtbauweise | Design-Effizienz wirkt sich direkt auf die Kosten aus |
Stützvolumen | Materialkosten, Arbeitskosten | DfAM (selbsttragend), Orientierungsoptimierung | Minimierung von Stützen durch intelligentes Design |
Teil Höhe | Druckzeit, Maschinenkosten | Optimierung der Ausrichtung (kürzer ist schneller, benötigt aber möglicherweise mehr Stützen), effiziente Verschachtelung | Verstehen von Kompromissen zwischen Orientierung, Unterstützung und Zeit |
Komplexität | Arbeitskosten (Post-Proc) | Vereinfachen Sie das Design, wo es möglich ist, ohne die Funktion zu beeinträchtigen, und entwerfen Sie ein Design für die Entfernung von Stützen | Bewertung der Kostenauswirkungen komplexer interner Merkmale |
Toleranz/Finish | Arbeitskosten (Post-Proc) | Anforderungen klar spezifizieren; nur dort anziehen, wo es notwendig ist; Bearbeitungsmöglichkeiten einkalkulieren | Vermeiden Sie Überspezifizierungen; verstehen Sie die Kosten der Nachbearbeitung |
Menge | Kosten pro Teil | Bestellen Sie nach Möglichkeit in Losen; nutzen Sie die effiziente Verschachtelung | Erörterung möglicher Mengenrabatte mit Großhandelslieferanten |
Anforderungen an die Prüfung | Arbeitskosten, Ausrüstungskosten. Kosten | Klare Definition der erforderlichen Prüfungen (z. B. Leckrate) | Spezifizieren Sie wesentliche QC; vermeiden Sie unnötige Tests |
In Blätter exportieren
Das Einholen detaillierter Angebote von potenziellen Lieferanten auf der Grundlage ausgereifter Entwürfe ist der beste Weg, um genaue Kosten- und Vorlaufzeitschätzungen zu erhalten. Eine offene Kommunikation über Anforderungen und potenzielle Kompromisse bei der Konstruktion kann zur Optimierung beider Faktoren beitragen.
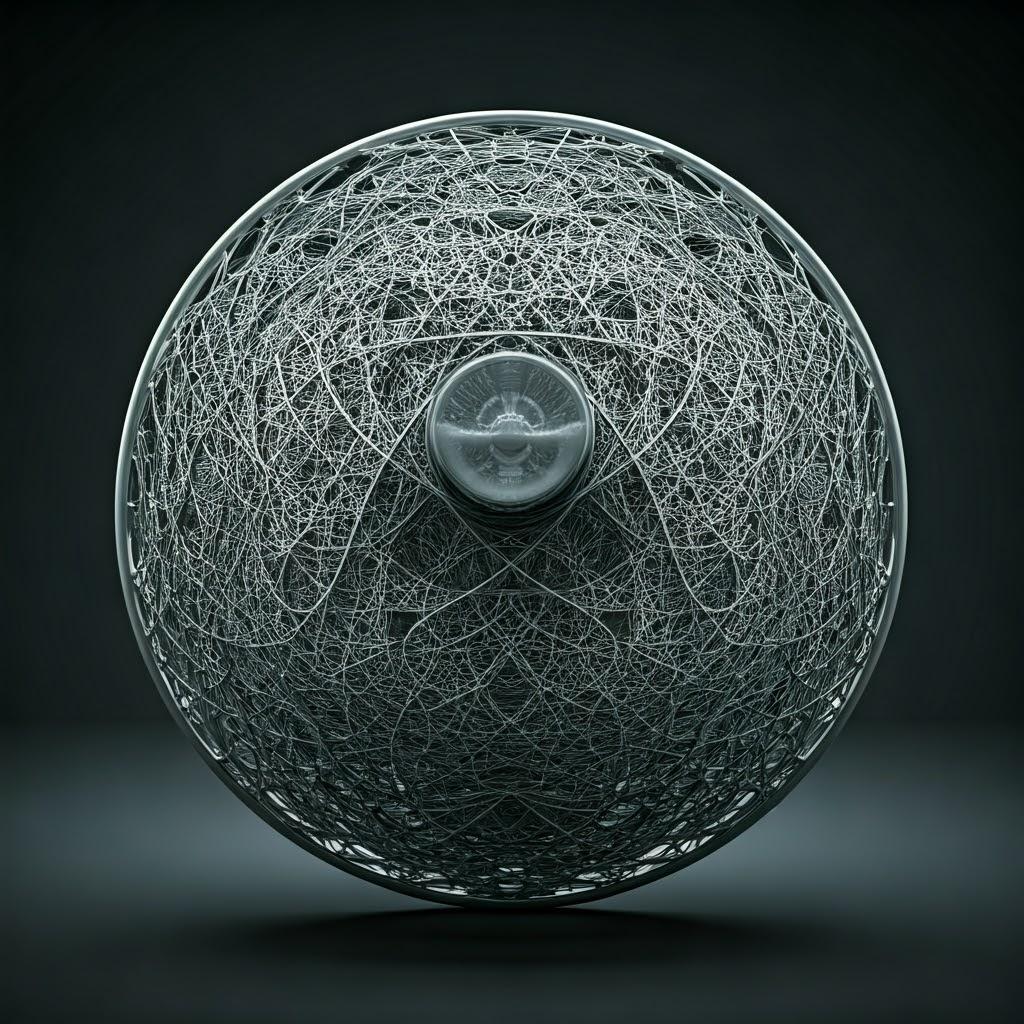
Häufig gestellte Fragen (FAQ) zu 3D-gedruckten Lüftungskanälen
Hier finden Sie Antworten auf einige häufig gestellte Fragen von Ingenieuren und Beschaffungsmanagern zum Einsatz der additiven Fertigung von Lüftungskanälen aus Metall:
1. Wie hoch sind die Kosten für 3D-gedruckte Aluminiumkanäle im Vergleich zu herkömmlichen Methoden wie Blechverarbeitung oder Gießen?
- Antwort: Sie hängt stark von der Komplexität und dem Volumen ab.
- Hohe Komplexität, geringes Volumen: Bei komplizierten Geometrien, integrierten Merkmalen oder Teilen, die mit herkömmlichen Methoden nur schwer zusammengesetzt werden können, ist der 3D-Druck oft die beste Lösung kostengünstigerbesonders für Prototypen und Kleinserien (z. B. 50-100 Stück) ist dies eine gute Lösung, da die Werkzeugkosten entfallen und der Arbeitsaufwand für die Montage reduziert wird.
- Einfache Designs, hohes Volumen: Für einfache Rohrformen, die in großen Mengen (Tausende) hergestellt werden, sind herkömmliche Verfahren wie Stanzen, Strangpressen oder Gießen in der Regel geeignet weniger teuer pro Teil aufgrund von Skaleneffekten und niedrigeren Zykluszeiten, trotz hoher anfänglicher Werkzeugkosten.
- Break-Even-Punkt: Der Übergangspunkt ist sehr unterschiedlich. Eine detaillierte Kostenanalyse, die AM (einschließlich aller Nachbearbeitungen) mit den voll belasteten Kosten traditioneller Methoden (einschließlich Werkzeugabschreibung und Montage) vergleicht, ist für bestimmte Fälle erforderlich.
2. Wie groß ist die maximale Größe eines Lüftungsschachts, der in 3D gedruckt werden kann?
- Antwort: Die maximale Größe wird in erster Linie durch das Bauvolumen der verwendeten L-PBF-Maschine begrenzt. Viele industrielle Systeme haben Bauumfänge im Bereich von 250x250x300 mm bis 400x400x400 mm. Es gibt auch größere Systeme, von denen einige Bauhöhen von über 1 Meter bieten. Met3dp hebt seine Drucker hervor’ branchenführendes Druckvolumen. Bei Kanälen, die das Bauvolumen der verfügbaren Maschinen überschreiten, besteht eine gängige Strategie darin, den Kanal in mehreren Abschnitten zu drucken, die mit entsprechenden Flanschen oder Verbindungselementen versehen sind und dann nach dem Druck zusammengeschweißt oder befestigt werden. Dies erfordert ein sorgfältiges Design, um die korrekte Ausrichtung und Abdichtung an den Verbindungsstellen zu gewährleisten.
3. Sind 3D-gedruckte Aluminiumrohre (AlSi10Mg, AlSi7Mg) für Hochtemperaturanwendungen geeignet?
- Antwort: Aluminiumlegierungen wie AlSi10Mg und AlSi7Mg haben relativ niedrige Schmelzpunkte und verlieren bei höheren Temperaturen erheblich an Festigkeit. Ihre maximale Dauergebrauchstemperatur ist im Allgemeinen auf etwa 150°C bis 180°C (300°F bis 350°F)die Leistung hängt jedoch von der spezifischen Belastung, der Dauer und den Bedingungen der Wärmebehandlung ab. Sie eignen sich für Umgebungsluft, HVAC, Elektronikkühlung und einige Automobilanwendungen, aber nicht für Hochtemperaturumgebungen wie Motorabgassysteme, Turbinenkomponenten oder industrielle Hochtemperaturprozesse. Für solche Anwendungen werden Superlegierungen auf Nickelbasis (z. B. Inconel 625, 718) oder möglicherweise Titanlegierungen benötigt, die ebenfalls durch AM verarbeitet werden können.
4. Wie haltbar sind 3D-gedruckte Aluminiumkanäle im Vergleich zu herkömmlichen Blechkanälen?
- Antwort: Richtig konstruiert, mit hoher Dichte gedruckt und entsprechend wärmebehandelt (z. B. T6-Temperierung), können 3D-gedruckte AlSi10Mg/AlSi7Mg-Rohre eine ausgezeichnete Festigkeit und Haltbarkeit aufweisen, die oft die Anforderungen für typische Lüftungsanwendungen übertreffen.
- Stärke: Die T6-Wärmebehandlung erhöht die Festigkeit erheblich. Die Topologie-Optimierung stellt sicher, dass das Material strategisch platziert wird, um Lasten zu bewältigen.
- Müdigkeit: Die Ermüdungsfestigkeit hängt von internen Defekten (Porosität) und der Oberflächenbeschaffenheit ab. Hochwertige Druckverfahren und eine angemessene Nachbearbeitung sind für eine gute Ermüdungsleistung entscheidend. Spannungskonzentrationen müssen durch das Design gesteuert werden (Verrundung).
- Schlagfestigkeit: Aluminiumlegierungen sind im Allgemeinen weniger dehnbar als einige für Bleche verwendete Stähle, bieten aber eine gute Zähigkeit, insbesondere AlSi7Mg.
- Vergleich: Ein gut konzipierter und hergestellter AM-Kanal kann deutlich leichter sein als ein entsprechendes Blechteil und gleichzeitig die erforderlichen strukturellen und drucktechnischen Anforderungen erfüllen oder übertreffen. Die Langlebigkeit hängt in hohem Maße von der Qualität des Designs, der Herstellung und der Nachbearbeitung ab.
5. Können die Innenflächen von 3D-gedruckten Kanälen genauso glatt sein wie die Außenflächen?
- Antwort: Glatte Innenoberflächen in komplexen, engen oder gewundenen Kanälen zu erzielen, ist eine der größten Herausforderungen bei AM.
- As-Built: Innenflächen, insbesondere nach unten gerichtete oder gestützte Bereiche, sind im Allgemeinen rauer als Außenflächen (höhere Ra-Werte). Dies ist auf die Wechselwirkung mit Stützstrukturen oder teilweise geschmolzenem Pulver zurückzuführen.
- Nachbearbeiten: Die Möglichkeiten zur Glättung interner Kanäle sind im Vergleich zu externen Oberflächen begrenzt.
- Abrasive Fließbearbeitung (AFM): Kann interne Kanäle effektiv glätten, erfordert jedoch Sichtkontakt für den Durchfluss des Schleifmittels und ist bei sehr scharfen Kurven oder komplexen Kreuzungen weniger effektiv.
- Chemisches Polieren: Möglich, aber bei Aluminium weniger üblich und kann die Abmessungen beeinflussen.
- Entwurf: Die Gestaltung von Rinnen mit größeren Radien, glatteren Übergängen und selbsttragenden Formen kann dazu beitragen, die innere Oberfläche im eingebauten Zustand zu verbessern.
- Auswirkungen: Innere Oberflächenrauhigkeit erhöht die Reibung und den Druckverlust, was bei aerodynamischen oder fluiddynamischen Leistungsberechnungen berücksichtigt werden muss. Sie ist zwar oft akzeptabel, kann aber nicht mit der Glätte extrudierter oder gezogener Rohre mithalten.
Schlussfolgerung: Die Zukunft der Hochleistungskanäle ist additiv
Die Landschaft der Herstellung von Lüftungskanälen erfährt einen bedeutenden Wandel, der durch die Möglichkeiten der additiven Fertigung von Metallen vorangetrieben wird. Wie wir erforscht haben, bietet die Verwendung der L-PBF-Technologie in Kombination mit leichten, hochleistungsfähigen Aluminiumlegierungen wie AlSi10Mg und AlSi7Mg überzeugende Vorteile, die herkömmliche Methoden für komplexe Anwendungen einfach nicht bieten können.
Die Fähigkeit zu erreichen beispiellose Designfreiheit ermöglicht es Ingenieuren, Kanäle zu entwickeln, die für die Strömungsdynamik optimiert sind, sich nahtlos in enge Räume integrieren lassen und Merkmale aufweisen, die zuvor unmöglich oder unerschwinglich waren. Dies führt direkt zu greifbaren Vorteilen: erhebliche Gewichtsreduzierung entscheidend für die Effizienz in der Luft- und Raumfahrt und in der Automobilindustrie, Teilkonsolidierung dies führt zu einer einfacheren Montage und verbesserter Zuverlässigkeit durch den Wegfall von Verbindungsstellen und der Möglichkeit, die schnelle Prototypenerstellung und Iteration entwürfe und beschleunigt die Innovationszyklen.
Zwar gibt es Herausforderungen wie die Bewältigung von Eigenspannungen, das Entfernen von Stützen aus komplizierten Innengeometrien und das Erreichen spezifischer Toleranzen und Oberflächen, doch werden diese durch Fortschritte bei den DfAM-Prinzipien, eine ausgefeilte Prozesssteuerung, strenge Nachbearbeitungstechniken und die Verwendung hochwertiger Materialien wirksam angegangen. Die Bedeutung von partnerschaft mit einem erfahrenen und kompetenten Metall-AM-Anbieter kann gar nicht hoch genug eingeschätzt werden. Fachwissen in den Bereichen Werkstoffkunde, Prozessoptimierung, Qualitätskontrolle und umfassende Nachbearbeitung ist von entscheidender Bedeutung, um das volle Potenzial dieser Technologie auszuschöpfen und die Lieferung zuverlässiger, leistungsstarker Komponenten zu gewährleisten.
Unternehmen wie Met3dp, deren Schwerpunkt auf branchenführende Ausrüstung, fortschrittliche Pulverherstellungstechnologien und umfassende Lösungenstehen an vorderster Front, wenn es darum geht, Branchen von der Luft- und Raumfahrt über die Automobilindustrie bis hin zur industriellen Fertigung in die Lage zu versetzen, Metall-AM für Komponenten der nächsten Generation zu nutzen.
Die Zukunft deutet darauf hin, dass der 3D-Metalldruck für spezialisierte und leistungskritische Kanäle immer häufiger eingesetzt wird. In dem Maße, in dem die Technologie reift, die Kosten weiter optimiert werden und die Ingenieure immer besser in der Lage sind, für das Verfahren zu konstruieren, wird AM zunehmend zur bevorzugten Lösung für Anwendungen werden, die ein Höchstmaß an Leichtbau, Leistung und Designintegration erfordern.
Steht Ihr Unternehmen vor der Herausforderung, komplexe Lüftungskanäle zu entwerfen, das Gewicht zu reduzieren oder lange Lieferzeiten mit herkömmlichen Methoden zu erreichen? Entdecken Sie die Möglichkeiten der additiven Fertigung von Metallen. Kontakt <a href=”[ungültige URL entfernt]” target=”_blank”>Met3dp</a> um Ihre spezifische Anwendung zu besprechen und zu erfahren, wie unsere hochmodernen Systeme, Hochleistungs-Metallpulver und unser fachkundiger Anwendungssupport Ihnen helfen können, Ihren Ansatz bei der Herstellung von Luftkanälen zu revolutionieren und Ihre Produktionsziele zu erreichen.
Teilen auf
MET3DP Technology Co., LTD ist ein führender Anbieter von additiven Fertigungslösungen mit Hauptsitz in Qingdao, China. Unser Unternehmen ist spezialisiert auf 3D-Druckgeräte und Hochleistungsmetallpulver für industrielle Anwendungen.
Fragen Sie an, um den besten Preis und eine maßgeschneiderte Lösung für Ihr Unternehmen zu erhalten!
Verwandte Artikel
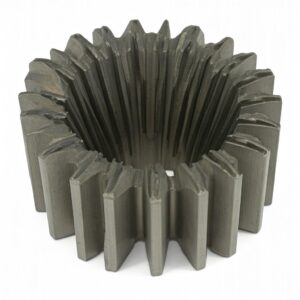
Hochleistungs-Düsenschaufelsegmente: Revolutionierung der Turbineneffizienz mit 3D-Metalldruck
Mehr lesen "Über Met3DP
Aktuelles Update
Unser Produkt
KONTAKT US
Haben Sie Fragen? Senden Sie uns jetzt eine Nachricht! Wir werden Ihre Anfrage mit einem ganzen Team nach Erhalt Ihrer Nachricht bearbeiten.
Holen Sie sich Metal3DP's
Produkt-Broschüre
Erhalten Sie die neuesten Produkte und Preislisten
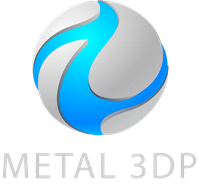
Metallpulver für 3D-Druck und additive Fertigung