Polvo de aleación de aluminio
Índice
Polvo de aleación de aluminio se refiere a las formas pulvimetalúrgicas de las aleaciones de aluminio. El polvo de aluminio se utiliza en diversas aplicaciones por su ligereza, alta resistencia, resistencia a la corrosión, conductividad térmica y conductividad eléctrica.
Visión general de la aleación de aluminio en polvo
El polvo de aleación de aluminio se produce por atomización de aleaciones fundidas en finas gotitas que se solidifican en partículas de polvo. La composición y las propiedades del polvo de aleación pueden adaptarse en función de las necesidades.
Detalles clave sobre el polvo de aleación de aluminio:
- Producido por atomización de aleaciones de aluminio en polvo fino
- El tamaño de las partículas oscila entre unas micras y milímetros
- Formas de partículas esféricas, irregulares o en copos
- Variedad de elementos de aleación utilizados: Si, Mg, Zn, Cu, etc.
- Propiedades dependientes de la composición de la aleación
- Ligereza, alta resistencia, resistencia a la corrosión
- Se utiliza para fabricación aditiva, proyección térmica, MIM, etc.
Tipos de aleaciones de aluminio en polvo
Tipo | Composición | Características |
---|---|---|
Al pura | 99%+ Al | Baja resistencia, alta conductividad eléctrica |
Serie 1000 | Al + Mn, Fe, Si | Endurecible, mayor resistencia |
Serie 2000 | Al-Cu | Tratable térmicamente, alta resistencia |
Serie 5000 | Al-Mg | Resistencia de moderada a alta |
Serie 6000 | Al-Mg-Si | Resistencia media a alta |
Serie 7000 | Al-Zn | Máxima resistencia |
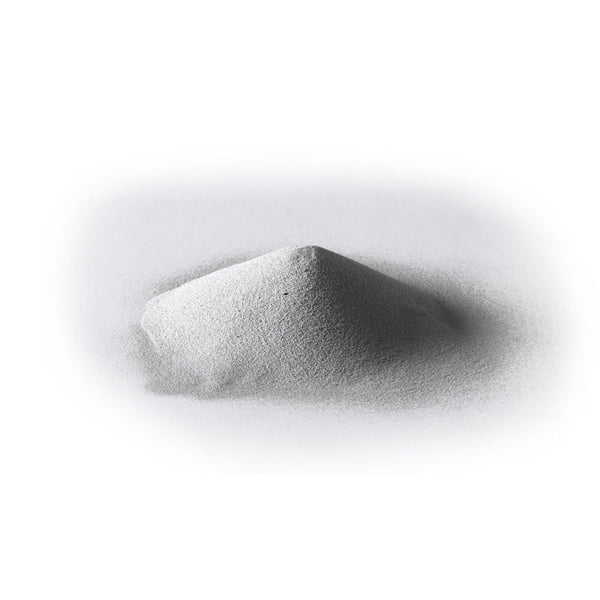
Polvo de aleación de aluminio Composición
Los polvos de aleación de aluminio contienen aluminio como metal base junto con elementos de aleación. Algunos de los elementos de aleación más comunes son:
Serie Alloy | Elementos de aleación primarios | Aplicaciones | Propiedades mejoradas por elementos de aleación |
---|---|---|---|
Serie 1XXX | > 99% Aluminio (Al) | * Conductores eléctricos * Intercambiadores de calor * Envasado de alimentos | * Alta conductividad eléctrica * Excelente conformabilidad * Resistencia superior a la corrosión |
Serie 2XXX | Al + Cobre (Cu) (Hasta 5,5%) | * Componentes aeroespaciales * Barras colectoras * Piezas de automóvil | * Mayor resistencia * Mejor maquinabilidad * Buena soldabilidad |
Serie 3XXX | Al + Manganeso (Mn) (Hasta 1,3%) | * Materiales de construcción * Señales y paneles * Tanques de almacenamiento | * Endurecimiento por deformación mejorado * Conformabilidad superior * Excelente soldabilidad |
Serie 4XXX | Al + Silicio (Si) (Hasta 12%) | * Bloques de motor * Culatas * Alambres de soldadura | * Excelentes características de fundición * Bajo coeficiente de dilatación térmica * Resistencia al desgaste |
Serie 5XXX | Al + Magnesio (Mg) (Hasta 5,6%) | * Construcción naval * Recipientes a presión * Tanques de almacenamiento de productos químicos | * Alta relación resistencia-peso * Excelente resistencia a la corrosión * Buena soldabilidad |
Serie 6XXX | Al + Magnesio (Mg) + Silicio (Si) (Hasta 1 Mg & 0,6 Si) | * Estructuras aeronáuticas * Puentes * Componentes de transporte | * Excelente maquinabilidad * Buena resistencia * Conformabilidad superior |
Serie 7XXX | Al + Zinc (Zn) (Hasta 6,5%) | * Alas de avión * Artículos deportivos * Elementos de fijación de alta resistencia | * Alta resistencia * Buena resistencia a la fatiga * Resistencia al desgaste (con elementos de aleación adicionales) |
Serie 8XXX | Al + Litio (Li) (Hasta 12%) | * Componentes aeroespaciales que requieren un peso muy reducido * Vehículos de altas prestaciones | * Densidad extremadamente baja * Elevada relación resistencia/peso * Aplicaciones limitadas debido al elevado coste y a las dificultades de procesamiento |
Características del polvo de aleación de aluminio
Características del polvo de aleación de aluminio
Propiedad | Descripción | Ventajas de la fabricación aditiva |
---|---|---|
Tamaño y distribución de partículas | Los polvos de aleaciones de aluminio están disponibles en una amplia gama de tamaños de partícula, normalmente entre 10 y 150 micrómetros. La distribución de estos tamaños de partícula en el lecho de polvo también es crucial. | El tamaño y la distribución de las partículas influyen significativamente en las propiedades finales de la pieza fabricada aditivamente. <br> – Partículas más finas generalmente crean acabados superficiales más lisos, pero pueden ser más difíciles de procesar debido a los mayores problemas de fluidez y a la mayor superficie de oxidación. <br> – Partículas más grandes mejoran la fluidez, pero pueden dar lugar a un acabado superficial más rugoso y a una posible porosidad en la pieza acabada. <br> - A distribución granulométrica ajustada con una variación mínima garantiza una densidad de empaquetado constante y minimiza las tensiones internas dentro de la pieza impresa. |
Forma de las partículas | La forma de las partículas de polvo de aleación de aluminio puede influir en la densidad de empaquetamiento, la fluidez y la microestructura final del componente fabricado aditivamente. | – Partículas esféricas se empaquetan de forma más eficaz, lo que aumenta su densidad y puede mejorar sus propiedades mecánicas. <br> – Partículas de forma irregular pueden crear características de enclavamiento que mejoran la adherencia de las capas, pero también pueden provocar mayores tensiones internas y posibles grietas. |
Fluidez del polvo | La fluidez del polvo se refiere a la facilidad con la que las partículas de polvo pueden moverse y esparcirse dentro de la cámara de impresión de la máquina. | Una buena fluidez es esencial para garantizar una deposición uniforme de las capas y una geometría precisa de las piezas. <br> - Los polvos poco fluidos pueden provocar una deposición irregular, incoherencias en la densidad y posibles defectos de impresión. |
Densidad aparente | La densidad aparente de un polvo de aleación de aluminio es la masa de polvo por unidad de volumen, teniendo en cuenta los espacios entre las partículas. | La densidad aparente es un factor crucial para determinar la cantidad de material necesario para un volumen de construcción específico y puede influir en la contracción de la pieza durante el proceso de impresión. |
Densidad de embalaje | La densidad de empaquetamiento se refiere a la relación entre el volumen sólido de las partículas de polvo y el volumen total ocupado por el polvo. | La densidad de empaquetamiento suele ser inferior a la densidad aparente debido a la presencia de huecos entre las partículas. Una mayor densidad de empaquetamiento suele mejorar las propiedades mecánicas de la pieza final. |
Composición química | Los elementos de aleación específicos presentes en el polvo de aluminio influyen significativamente en las propiedades finales de la pieza fabricada aditivamente. Los elementos de aleación más comunes son el silicio, el cobre, el magnesio, el manganeso y el zinc. | La selección del polvo de aleación de aluminio adecuado depende de las propiedades deseadas de la pieza acabada, como la resistencia, la resistencia a la corrosión y la resistencia al calor. <br> Por ejemplo, añadir cobre puede aumentar la resistencia pero reducir la resistencia a la corrosión. |
Química de superficies | La química de la superficie de las partículas de polvo de aleación de aluminio puede influir en su fluidez, reactividad y adhesión durante el proceso de impresión. | En la superficie de las partículas de aluminio se forma de forma natural una fina capa de óxido. <br> – Técnicas de modificación de superficies puede emplearse para mejorar la fluidez y promover la unión entre partículas durante el proceso de fabricación aditiva. |
Contenido de humedad | Los polvos de aleación de aluminio son higroscópicos, lo que significa que absorben fácilmente la humedad del entorno. | Un contenido excesivo de humedad en el polvo puede provocar porosidad por hidrógeno en la pieza fabricada aditivamente, lo que repercute negativamente en las propiedades mecánicas. <br> - Unas técnicas de almacenamiento y manipulación adecuadas son cruciales para mantener bajos los niveles de humedad en el polvo. |
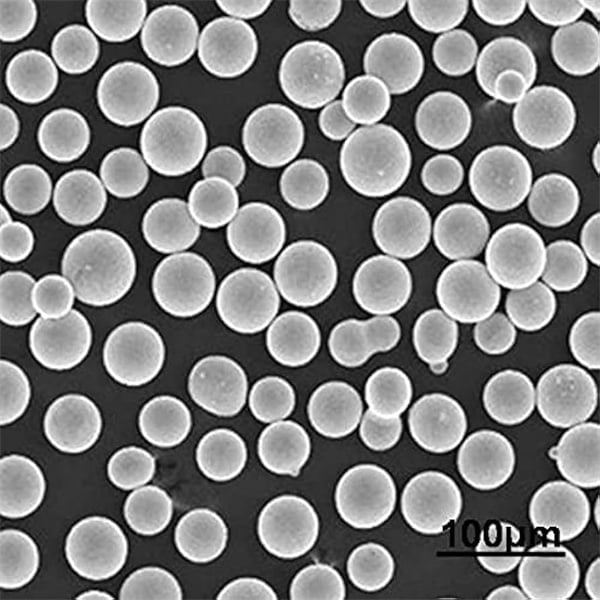
Aplicaciones de la aleación de aluminio en polvo
Aplicación | Descripción | Ventajas de los polvos de aleaciones de aluminio | Limitaciones |
---|---|---|---|
Componentes aeroespaciales | Los polvos de aleaciones de aluminio se utilizan ampliamente para la fabricación aditiva (AM) de componentes aeroespaciales de alto rendimiento debido a su excelente relación resistencia-peso y a sus favorables propiedades mecánicas. Las aplicaciones más comunes son: - Fuselajes y componentes de las alas de los aviones - Componentes del motor - Estructuras satélite | – Construcción ligera: Las aleaciones de aluminio ofrecen una importante reducción de peso en comparación con materiales tradicionales como el acero, lo que permite mejorar la eficiencia del combustible y la capacidad de carga útil en vehículos aeroespaciales. – Libertad de diseño: La AM permite crear estructuras complejas y ligeras con canales internos y entramados difíciles o imposibles de conseguir con los métodos de fabricación convencionales. – Adaptación del rendimiento: Se pueden elegir aleaciones de aluminio específicas para satisfacer los exigentes requisitos de las aplicaciones aeroespaciales, como alta resistencia, buena resistencia a la fatiga y excelente resistencia a la corrosión. | – Coste del polvo: Los polvos de aleaciones de aluminio pueden ser más caros que algunos materiales alternativos utilizados en el sector aeroespacial, como las aleaciones de titanio. – Rugosidad de la superficie: Aunque los procesos de AM mejoran continuamente, los componentes de aluminio fabricados aditivamente pueden seguir presentando un acabado superficial más rugoso que las piezas mecanizadas. Para determinadas aplicaciones pueden ser necesarias técnicas de postprocesado como el mecanizado o el pulido. |
Componentes de automoción | Los polvos de aleaciones de aluminio se utilizan cada vez más en AM para la producción de componentes de automoción ligeros y complejos. Algunos ejemplos son: - Componentes estructurales como soportes y carcasas - Disipadores térmicos para electrónica de potencia - Componentes de motor a medida | – Reducción de peso: Los componentes de aluminio AM contribuyen a mejorar la eficiencia del combustible y el rendimiento general del vehículo. – Integración funcional: La AM permite diseñar y crear piezas con funcionalidades integradas, reduciendo el número de componentes y simplificando los procesos de montaje. – Optimización del rendimiento: Las aleaciones de aluminio pueden elegirse para proporcionar propiedades específicas, como alta resistencia para componentes estructurales o buena conductividad térmica para disipadores de calor. | – Calificación parcial: Las piezas de automoción críticas para la seguridad fabricadas mediante AM pueden requerir pruebas y certificaciones exhaustivas. – Volumen de producción: Aunque la AM se utiliza cada vez más para la creación de prototipos y la producción de series cortas, su escalabilidad para la fabricación de grandes volúmenes de automóviles aún está en fase de desarrollo. |
Implantes médicos | Se están estudiando polvos de aleaciones de aluminio con propiedades biocompatibles para la AM de implantes médicos personalizados, como: - Placas y tornillos de reparación ósea - Implantes dentales - Componentes protésicos | – Biocompatibilidad: Ciertas aleaciones de aluminio presentan una buena biocompatibilidad, lo que minimiza el riesgo de rechazo por el cuerpo humano. – Personalización: La AM permite crear implantes específicos para cada paciente que se adaptan perfectamente a la anatomía individual, mejorando el ajuste y la función del implante. – Estructuras porosas: Las estructuras porosas de aluminio creadas mediante AM pueden favorecer el crecimiento óseo y mejorar la osteointegración del implante (unión con el hueso). | – Gama limitada de aleaciones biocompatibles: Actualmente, sólo unas pocas aleaciones de aluminio se consideran biocompatibles para aplicaciones médicas. – Propiedades mecánicas: Algunas aleaciones de aluminio pueden no poseer la solidez o la resistencia a la fatiga necesarias para determinados implantes que soportan cargas elevadas. – Requisitos reglamentarios: Los productos sanitarios fabricados mediante AM deben someterse a estrictos procesos de aprobación reglamentaria. |
Electrónica de consumo | Los polvos de aleaciones de aluminio se utilizan para la AM de diversos componentes de electrónica de consumo debido a su buena conductividad térmica y a sus propiedades de ligereza. Algunos ejemplos son: - Disipadores de calor para dispositivos electrónicos - Carcasas ligeras para portátiles y teléfonos móviles | – Gestión térmica: La buena conductividad térmica del aluminio ayuda a disipar el calor generado por los componentes electrónicos, mejorando el rendimiento y la fiabilidad de los dispositivos. – Diseño ligero: Los componentes de aluminio AM contribuyen a la reducción general del peso de los dispositivos electrónicos, mejorando su portabilidad y la experiencia del usuario. | – Fuerza limitada: El aluminio puro o algunas aleaciones de aluminio pueden no ser adecuados para componentes estructurales que requieran una gran resistencia. – Acabado superficial: Al igual que en otras aplicaciones de AM, la rugosidad de la superficie puede requerir un postprocesado adicional para determinados requisitos estéticos. |
Fabricación aditiva con aleación de aluminio en polvo
Algunas ventajas de la AM con polvo de aleación de Al:
Beneficio | Descripción | Impacto |
---|---|---|
Libertad de diseño y complejidad | La fabricación aditiva (AM) permite crear geometrías intrincadas y complejas que son difíciles o imposibles de conseguir con técnicas de fabricación tradicionales como el mecanizado o la fundición. Los polvos de aleación de aluminio aumentan aún más esta libertad de diseño gracias a su fluidez y a su capacidad para fundirse o aglutinarse selectivamente. | – Estructuras ligeras: La AM permite diseñar componentes ligeros con celosías y canales internos, optimizando la relación resistencia-peso para aplicaciones como la aeroespacial y la automoción. – Integración funcional: Las piezas pueden diseñarse con funcionalidades integradas, lo que reduce la necesidad de múltiples componentes y simplifica los procesos de montaje. – Personalización: La AM permite crear piezas personalizadas adaptadas a necesidades específicas, como implantes médicos específicos para pacientes o carcasas de electrónica de consumo a medida. |
Eficiencia material y reducción de residuos | A diferencia de los métodos tradicionales de fabricación sustractiva, que generan gran cantidad de material de desecho, la AM con polvo de aleación de aluminio ofrece un enfoque más sostenible. El material solo se utiliza cuando es necesario durante el proceso de fabricación capa a capa, lo que minimiza los residuos. | – Reducción del impacto medioambiental: El menor consumo de materiales se traduce en una menor huella medioambiental en comparación con los procesos de fabricación tradicionales. – Fabricación a la carta: La AM permite la producción de piezas a la carta, lo que elimina la necesidad de grandes inventarios y reduce potencialmente los requisitos de transporte. |
Prototipos rápidos y producción a corto plazo | La AM con polvo de aleación de aluminio destaca en la creación rápida de prototipos, lo que permite crear rápidamente prototipos funcionales para verificar y probar el diseño. Además, la AM facilita la producción en tiradas cortas de piezas complejas sin necesidad de costosas herramientas, lo que la hace ideal para aplicaciones de bajo volumen. | – Ciclos de desarrollo de productos más rápidos: La creación rápida de prototipos permite iteraciones de diseño y ciclos de retroalimentación más rápidos, lo que acelera el proceso de desarrollo del producto. – Reducción del tiempo de comercialización: La AM permite producir piezas bajo demanda, eliminando los largos plazos de entrega asociados a los métodos de fabricación tradicionales. – Rentable para volúmenes reducidos: Para series de producción de bajo volumen, el coste de la AM con polvo de aleación de aluminio puede ser competitivo en comparación con los métodos tradicionales que requieren una inversión en utillaje. |
Adaptación del rendimiento y aligeramiento | Existe una amplia gama de aleaciones de aluminio en forma de polvo, cada una de las cuales ofrece propiedades distintas como resistencia, resistencia a la corrosión y conductividad térmica. Esto permite seleccionar el polvo de aleación de aluminio óptimo para conseguir las características de rendimiento deseadas para una aplicación específica. | – Aligerar para mejorar el rendimiento: La ligereza inherente al aluminio, unida a la libertad de diseño de la AM, permite crear componentes más ligeros que mejoran la eficiencia del combustible en vehículos o la capacidad de carga útil en aplicaciones aeroespaciales. – Optimización funcional: Se pueden elegir aleaciones de aluminio específicas para satisfacer las exigencias de rendimiento de una aplicación. Por ejemplo, las aleaciones de alta resistencia pueden utilizarse para componentes estructurales, mientras que las aleaciones con buena conductividad térmica son ideales para disipadores de calor. |
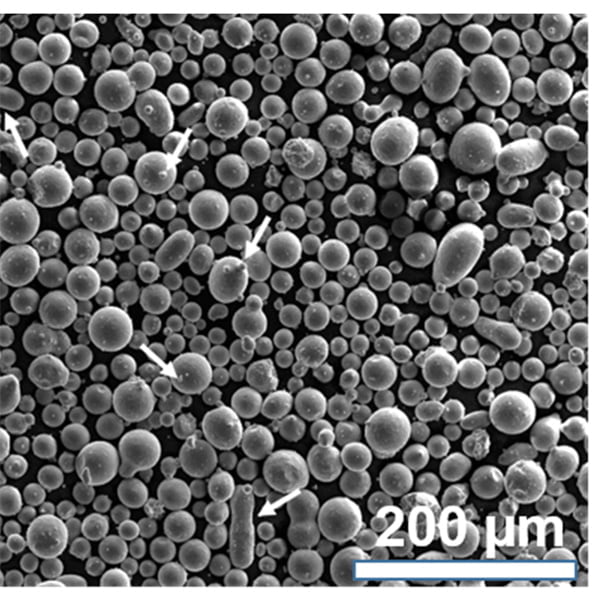
Limitaciones actuales de la AM con polvo de Al
Aspecto | Limitación | Impacto | Posibles soluciones |
---|---|---|---|
Características del polvo | Forma y distribución irregular del tamaño de las partículas | Absorción láser inconsistente, poca fluidez, aumento de la porosidad en las piezas finales | Desarrollo de técnicas de atomización más eficaces para polvos esféricos, control más estricto de la distribución del tamaño de las partículas. |
Fluidez del polvo | Un flujo deficiente puede dificultar el esparcimiento uniforme | Densidad de capa inconsistente, débil unión entre capas | Utilización de agentes de fluidez o sistemas vibratorios para mejorar el esparcimiento del polvo, explorando técnicas alternativas de fusión del lecho de polvo como el chorro de aglutinante. |
Reciclabilidad del polvo | Ciclos de reutilización limitados debido a la oxidación y la contaminación | Mayor coste de los materiales, impacto medioambiental | Desarrollo de sistemas de gestión de polvo de circuito cerrado con procesos integrados de limpieza y tamizado, explorando aleaciones de Al menos susceptibles a la oxidación. |
Calidad de la superficie | Elevada rugosidad superficial debida a las partículas no fundidas | Pasos de postprocesamiento necesarios, posibilidad de iniciación de grietas por fatiga | Optimización de los parámetros láser para mejorar la eficacia de la fusión, explorando técnicas de acabado alternativas como el granallado o el electropulido. |
Propiedades mecánicas | La porosidad puede reducir la resistencia y la ductilidad. | Las piezas pueden no cumplir los requisitos de diseño | Utilización del prensado isostático en caliente (HIP) para el cierre de poros, explorando técnicas de postprocesado láser como el refinamiento del baño de fusión. |
Estrés residual | La solidificación rápida puede inducir tensiones residuales elevadas | Mayor riesgo de alabeo y agrietamiento | Precalentamiento del lecho de polvo, optimización de las estrategias de escaneado láser para minimizar los gradientes térmicos, utilización de tratamientos térmicos de alivio de tensiones... |
Coste | Alto coste de producción del polvo de Al | Limita la viabilidad económica de determinadas aplicaciones | Desarrollo de técnicas de atomización más eficientes desde el punto de vista energético, explorando métodos de fabricación alternativos para geometrías más sencillas. |
Impacto medioambiental | Elevado consumo de energía durante la producción de polvo | Aumento de la huella de carbono | Investigación de técnicas de AM ecológicas, como la pulverización en frío o el chorro de ligante con ligantes a base de agua, explorando el uso de fuentes de aluminio reciclado. |
Limitaciones del tamaño de las piezas | Restricciones del volumen de construcción de las máquinas AM | No es fácil fabricar componentes de aluminio a gran escala | Desarrollo de máquinas de AM más grandes con mayores volúmenes de construcción, explorando técnicas híbridas de AM para combinar funcionalidades. |
Consideraciones sobre el diseño | Necesidad de optimizar el diseño para la AM | Las normas de diseño convencionales pueden no traducirse directamente | Desarrollo de directrices de diseño y herramientas informáticas específicas para la AM de componentes de Al, fomentando el intercambio de conocimientos y mejores prácticas dentro de la comunidad de AM. |
Moldeo por inyección de metal con polvo de aleación de aluminio
El moldeo por inyección de metales (MIM) puede producir componentes metálicos complejos, de tolerancia ajustada y forma neta, utilizando como materia prima polvo de aleación de aluminio a costes relativamente bajos.
Ventajas del MIM con polvo de aleación de aluminio
Característica | Beneficio | Ejemplo de aplicación |
---|---|---|
Geometrías complejas | El MIM de aleación de aluminio es excelente para producir formas complejas con tolerancias estrechas. A diferencia de los métodos de fundición tradicionales, el MIM no está limitado por las líneas de partición del molde, lo que permite realizar rebajes, paredes finas y canales internos. | Engranajes en miniatura en un dispositivo médico con dientes entrelazados y canales internos de lubricante. |
Producción de gran volumen | El MIM ofrece una solución rentable para la producción de grandes volúmenes de piezas metálicas pequeñas. El proceso de moldeo por inyección permite tiempos de ciclo rápidos y un procesamiento posterior mínimo, lo que se traduce en un importante ahorro de costes en comparación con el mecanizado de componentes intrincados. | Conectores eléctricos para electrónica de consumo con configuraciones de patillas complejas, producidos en grandes cantidades. |
Versatilidad de materiales | En el MIM puede utilizarse una amplia gama de aleaciones de aluminio, cada una de las cuales ofrece propiedades únicas. Esto permite una selección basada en las necesidades específicas de la aplicación, como una alta resistencia (por ejemplo, Al7075), una buena resistencia a la corrosión (por ejemplo, Al5052) o una excelente conductividad térmica (por ejemplo, Al6061). | Disipadores de calor ligeros para dispositivos electrónicos, que utilizan Al6061 para una disipación eficaz del calor. |
Fabricación en red | Las piezas MIM requieren un procesamiento posterior mínimo tras la sinterización. Las dimensiones casi finales se obtienen directamente del molde, lo que minimiza la necesidad de mecanizado o acabado adicionales. | Componentes de biosensores con canales microfluídicos integrados, que requieren alta precisión y un procesamiento posterior mínimo para su biocompatibilidad. |
Aligeramiento | Las aleaciones de aluminio son intrínsecamente ligeras, por lo que el MIM es ideal para aplicaciones en las que la reducción de peso es fundamental. Esto es especialmente beneficioso en las industrias aeroespacial, automovilística y de electrónica de consumo. | Componentes estructurales de drones, aprovechando la elevada relación resistencia-peso de las aleaciones de Al producidas mediante MIM. |
Libertad de diseño | El MIM permite integrar múltiples características en un único componente. Esto reduce la complejidad del ensamblaje, mejora la funcionalidad de la pieza y puede reducir los costes generales de producción. | Componentes de válvulas multifuncionales para sistemas de fluidos, que combinan elementos de control de caudal, filtros y funciones de regulación de la presión. |
Mejor acabado superficial | Las piezas MIM suelen tener un acabado superficial liso, lo que reduce la necesidad de pasos adicionales de pulido o acabado. Esto puede ser crucial para aplicaciones que requieren un alto grado de calidad superficial, como los implantes médicos o los componentes ópticos. | Tornillos óseos biocompatibles con un acabado superficial liso para favorecer la integración tisular y minimizar los riesgos de infección. |
Eficiencia material | El MIM utiliza un proceso de fabricación de forma casi neta, lo que minimiza el desperdicio de material en comparación con las técnicas de mecanizado tradicionales. Esta ventaja está en consonancia con las prácticas de fabricación sostenible. | Producción de engranajes y ruedas dentadas complejos con un mínimo de material de desecho, lo que favorece la conservación de los recursos. |
Limitaciones del MIM con polvo de aluminio
Factor | Limitación | Impacto |
---|---|---|
Retos de la sinterización | La alta reactividad del aluminio con el oxígeno puede provocar la formación de óxidos superficiales durante el proceso de sinterización. Estos óxidos dificultan la unión de las partículas, lo que se traduce en una menor resistencia mecánica y una mayor porosidad en comparación con las piezas MIM fabricadas con otros materiales, como el acero. | Los componentes que requieren una gran integridad estructural o resistencia a la presión pueden no ser adecuados para el MIM de aluminio debido a las posibles limitaciones de resistencia. |
Características del polvo | El polvo de aluminio utilizado en el MIM suele ser más fino que el de otros metales. Este tamaño de partícula tan fino puede dificultar una buena fluidez de la materia prima, lo que puede provocar defectos en el moldeo por inyección, como rugosidad superficial o llenado incompleto de la pieza. | Para garantizar el éxito de la producción de piezas es necesario un control estricto de las características del polvo y una cuidadosa optimización de la receta de la materia prima. |
Restricciones de tamaño de las piezas | Debido a la elevada contracción que se produce durante la sinterización (hasta 20% para el aluminio), el tamaño y la complejidad de las piezas que pueden fabricarse eficazmente utilizando MIM de aluminio son limitados. Los componentes grandes o complejos pueden ser propensos a agrietarse o alabearse. | El MIM de aluminio es el más adecuado para piezas pequeñas y medianas con geometrías relativamente sencillas. |
Consideraciones económicas | Aunque el MIM ofrece ventajas económicas para la producción de grandes volúmenes, los costes iniciales asociados al desarrollo de herramientas y polvos pueden ser considerables. Además, los polvos de aluminio para MIM suelen ser más caros que otros polvos metálicos. | Para aplicaciones de bajo volumen, el mecanizado tradicional o las técnicas de fabricación alternativas pueden resultar más rentables. |
Requisitos de postprocesamiento | Aunque se pueden conseguir formas casi netas, las piezas MIM de aluminio pueden requerir algunos pasos de postprocesado, como desbarbado, tratamiento térmico o acabado superficial, en función de los requisitos específicos de la aplicación. | Estos pasos adicionales pueden aumentar el tiempo y el coste totales de fabricación. |
Limitaciones de las propiedades materiales | En comparación con otros metales aptos para el MIM, las aleaciones de aluminio suelen tener menor solidez y resistencia al desgaste. Esto puede restringir su uso en aplicaciones que exigen un alto rendimiento mecánico en condiciones de funcionamiento duras. | Las piezas MIM de aluminio pueden no ser adecuadas para aplicaciones que requieran cargas elevadas, temperaturas extremas o entornos abrasivos. |
Rugosidad superficial | Aunque las piezas de aluminio MIM pueden lograr buenos acabados superficiales, es posible que no sean tan lisos como los que se consiguen con otras técnicas metalúrgicas. Esto puede suponer una limitación para aplicaciones que requieren una calidad superficial excepcional por motivos estéticos o funcionales. | Para determinadas aplicaciones pueden ser necesarios pasos de alisado o pulido. |
Selección limitada de aleaciones | Actualmente, la gama de aleaciones de aluminio disponibles para el MIM es menor que la de otros metales utilizados habitualmente en este proceso. Esto limita la capacidad de adaptar las propiedades del material a las necesidades específicas de rendimiento. | La investigación y el desarrollo en curso están ampliando la selección de aleaciones de aluminio adecuadas para el MIM, pero las opciones pueden seguir siendo limitadas en comparación con otros materiales. |
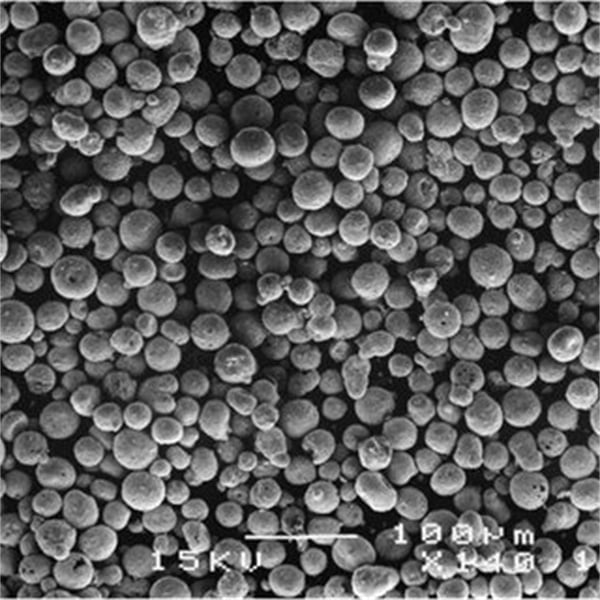
Polvo de aleación de aluminio para proyección térmica
Propiedad | Descripción | Ventajas | Desventajas |
---|---|---|---|
Composición de la aleación | Las aleaciones de aluminio en polvo se presentan en una gran variedad de composiciones, cada una de las cuales ofrece propiedades distintas. Los elementos de aleación más comunes son el silicio (Si), el magnesio (Mg), el cobre (Cu) y el manganeso (Mn). | – Si: Mejora la resistencia al desgaste y la colabilidad. - Mg: Reduce el peso y mejora la resistencia a la corrosión. – Cu: Aumenta la resistencia y la conductividad térmica. – Mn: Mejora la trabajabilidad y la resistencia a altas temperaturas. | - La selección depende en gran medida de las propiedades finales deseadas del revestimiento. - Se requiere un conocimiento específico de la aleación para una elección óptima. |
Tamaño y morfología de las partículas | El tamaño y la forma de las partículas de polvo influyen considerablemente en las características del revestimiento. Los polvos van de más finos de 10 micras a más gruesos de 100 micras, con morfologías esféricas o irregulares. | – Polvos finos (< 45 micras): Producen revestimientos más densos con superficies más lisas, ideales para aplicaciones que requieren resistencia al desgaste y protección contra la corrosión. – Polvos más gruesos (> 45 micras): Ofrecen velocidades de deposición más rápidas y una mayor fuerza de adherencia, adecuadas para reconstruir componentes desgastados. – Polvos esféricos: Mejoran la fluidez y la eficacia del empaquetado, lo que da lugar a revestimientos más uniformes. – Polvos irregulares: Puede crear una superficie más rugosa pero puede mejorar el enclavamiento mecánico dentro del revestimiento. | - Los polvos más finos requieren un equipo de proyección térmica especializado para su correcta alimentación. - Los polvos más gruesos pueden aumentar la porosidad del revestimiento. |
Técnica de proyección térmica | Diferentes procesos de pulverización térmica utilizan polvos de aleaciones de aluminio con distintos grados de eficacia. Las técnicas más comunes son: - Oxicorte de alta velocidad (HVOF) - Pulverización con plasma (PS) - Pulverización en frío (CS) | – HVOF: Proporciona altas velocidades de partícula, dando lugar a recubrimientos densos con excelente resistencia al desgaste y a la corrosión. Adecuado para polvos aleados con Si- y Cu. – PS: Ofrece versatilidad de proceso para una gama más amplia de polvos de aleaciones de aluminio. – CS: Utiliza temperaturas de partícula más bajas, minimizando los cambios metalúrgicos en el polvo y reduciendo la tensión residual en el revestimiento. Más adecuado para polvos aleados con Mg. | - La selección depende del punto de fusión del polvo y de las propiedades de recubrimiento deseadas. - Cada técnica tiene sus propias limitaciones en cuanto a velocidad de deposición, grosor del revestimiento y coste. |
Preparación de la superficie | El estado de la superficie del sustrato influye significativamente en la adherencia y el rendimiento del recubrimiento por pulverización térmica. | - Garantiza una superficie limpia y rugosa para una adhesión mecánica óptima. - Suelen emplearse técnicas como el granallado o el grabado. | - Una preparación inadecuada de la superficie puede provocar una adherencia débil y el fallo prematuro del revestimiento. |
Propiedades del revestimiento | Los recubrimientos por pulverización térmica de aleaciones de aluminio ofrecen una combinación única de propiedades: – Conductividad eléctrica: Varía en función de la composición de la aleación. El aluminio puro ofrece la mayor conductividad, mientras que las adiciones de Si y Mg pueden reducirla. – Conductividad térmica: Generalmente inferior a la del aluminio a granel, pero puede mejorarse con determinados elementos de aleación como el Cu. – Resistencia a la corrosión: El aluminio presenta una buena resistencia a la corrosión, que se ve reforzada por la adición de Mg. – Resistencia al desgaste: Mejorado mediante adiciones de Si y Cu, lo que hace que el revestimiento sea adecuado para aplicaciones de desgaste. | - Adaptado para satisfacer los requisitos específicos de la aplicación mediante la selección de aleaciones y la optimización del proceso. - Por ejemplo, maximizar la resistencia al desgaste puede comprometer la conductividad eléctrica. | |
Aplicaciones | Los recubrimientos por pulverización térmica de aleaciones de aluminio se utilizan en diversos sectores gracias a su versatilidad: – Automóvil: Pistones, culatas, pinzas de freno (para la resistencia al desgaste y la disipación del calor). – Aeroespacial: Componentes del tren de aterrizaje, componentes del fuselaje (para protección contra la corrosión y reducción del peso). – Electrónica: Disipadores térmicos, barras colectoras eléctricas (en función de la aleación elegida para la conductividad). – Procesamiento químico: Recipientes químicos, tuberías (por su resistencia a la corrosión). | - Ofrecen una solución rentable para la reparación de componentes, la mejora del rendimiento y la prolongación de la vida útil. - La selección de materiales y el control del proceso son cruciales para lograr los resultados deseados en cada aplicación. |
Especificaciones del polvo de aleación de aluminio
Los polvos de aleaciones de aluminio se producen de acuerdo con diversas especificaciones estándar que definen los límites de composición aceptables, los rangos de tamaño de las partículas, el control de la forma, etc.
Estándar | Descripción |
---|---|
AMS 4200 | Especificación de material aeroespacial para polvo de aleación de Al atomizado |
ASTM B602 | Especificación estándar para polvos de aleaciones de Al |
EN 1706 | Especificación de la norma europea para el polvo de Al atomizado |
ISO 13318 | Norma internacional para polvos de Al atomizados con gas y agua |
DIN 50125 | Norma nacional alemana para polvos de Al atomizados |
Las especificaciones permiten a los clientes adquirir el polvo adecuado para sus requisitos específicos de aplicación y proceso.
Tamaños de aleación de aluminio en polvo
El polvo de aleación de aluminio se produce en varios tamaños en función del uso final:
- Polvo ultrafino < 10 micras para aplicaciones reactivas
- Polvo fino 15 - 45 micras comúnmente para proyección térmica
- Polvo medio 45 - 100 micras tamaño ampliamente utilizado
- Polvo grueso de hasta 150 micras para aplicaciones especiales
Las partículas más grandes, de más de 180 micras, se utilizan principalmente en procesos de pulverización en frío para revestimientos más gruesos. El control de la distribución del tamaño de las partículas también es importante para algunas aplicaciones.
Grados de aleación de aluminio en polvo
El polvo de aleación de aluminio se fabrica en diferentes grados establecidos en función del tipo de aleación:
- Polvos de la serie 1xxx - AA1100, AA1350
- Polvos de la serie 2xxx - AA2014, AA2024, AA2219, AA2519
- Polvos serie 5xxx - AA5083, AA5654
- Polvos serie 6xxx - AA6061, AA6082
- Polvos de la serie 7xxx - AA7050, AA7075
Las series de números más altos indican mayores niveles de aleación y resistencia. También son posibles composiciones de aleación personalizadas para calidades patentadas.
Polvo de aleación de aluminio Comparación
Parámetro | Atomización de gas frío | Atomización del agua |
---|---|---|
Forma de las partículas | Muy esférica | Más irregulares, los satélites |
Gama de tamaños de partículas | 15 - 180 micras | 5 - 350 micras |
Distribución por tamaños | Control más estricto | Distribución más amplia |
Densidad aparente | Más alto | Baja |
Índice de producción | Baja | Más alto |
Coste | Más alto | Baja |
Los polvos atomizados con agua tienden a tener una ventaja de coste, pero adolecen de menor esfericidad y distribuciones de partículas más amplias en comparación con el polvo de aleación de aluminio atomizado con gas.
Normas sobre aleaciones de aluminio en polvo
Normas clave para el polvo de aleación de aluminio:
Estándar | Organización | Descripción |
---|---|---|
AMS4200 | SAE | Especificación de materiales aeroespaciales |
ASTM B602 | ASTM | Composición química y tamaño de los tamices |
EN1706 | CEN | Especificación de la norma europea |
ISO13318 | ISO | Norma internacional para formas atomizadas con gas y agua |
Diversas normas nacionales y organizativas contribuyen a garantizar la calidad y la coherencia del suministro de polvo de aleación de aluminio.
Proveedores mundiales de Polvo de aleación de aluminio
Proveedor | Ubicación | Capacidades |
---|---|---|
Valimet Inc. | EE.UU. | Amplia gama de atomización, gran capacidad |
Sandvik Osprey | REINO UNIDO | Proveedor líder de polvos controlados |
TLS Technik GmbH | Alemania | Especialista en polvos atomizados con gas y agua |
Fukuda Metal Foil & Powder Co. | Japón | Amplia oferta de aleaciones |
Productos metálicos SCM | Singapur | Aleaciones de aluminio y cobre |
Precios de los polvos de aleaciones de aluminio
El precio del polvo de aleación de aluminio varía en función de:
- Grado de aleación y características
- Especificaciones de forma y tamaño de las partículas
- Cantidad de compra y tamaño del lote
- Tarifas regionales y transporte
Tipo | Precios |
---|---|
Serie 1xxx | $5 - $15 por kg |
Serie 2xxx | $10 - $30 por kg |
Serie 5xxx | $15 - $35 por kg |
Serie 6xxx | $20 - $40 por kg |
Serie 7xxx | $30 - $60 por kg |
Los precios anteriores son aproximados y sólo sirven de referencia. Póngase en contacto con los proveedores para conocer los precios exactos en función de sus necesidades específicas.
Ventajas y limitaciones de Polvo de aleación de aluminio
Ventajas | Limitaciones |
---|---|
Elevada relación resistencia/peso | Manipulación de polvos |
El polvo de aleación de aluminio ofrece una resistencia excepcional para su peso. Por eso es ideal para aplicaciones en las que la reducción de peso es fundamental, como componentes aeroespaciales, piezas de automoción y prótesis. En comparación con metales tradicionales como el acero, las piezas de aleación de aluminio en polvo pueden alcanzar niveles de resistencia similares reduciendo considerablemente el peso total. | El polvo de aleación de aluminio, especialmente el de las calidades más finas, puede ser difícil de manipular debido a su fluidez y a la posibilidad de que se produzcan explosiones de polvo. Para garantizar una gestión segura y eficaz del polvo durante el almacenamiento, el transporte y los procesos de fabricación aditiva, es necesario disponer de equipos de manipulación especializados y tomar precauciones. |
Geometrías complejas | Rugosidad superficial |
El polvo de aleación de aluminio prospera en técnicas de fabricación aditiva (AM) como la impresión 3D. A diferencia de los métodos tradicionales de fabricación sustractiva, que eliminan material para crear la forma deseada, la AM construye piezas capa a capa a partir del polvo. Esto permite crear componentes intrincados y ligeros con geometrías complejas que serían difíciles o imposibles de conseguir con los métodos convencionales. | Las piezas fabricadas con polvo de aleación de aluminio pueden presentar un acabado superficial ligeramente más rugoso que los componentes mecanizados. Aunque las técnicas de postprocesado, como el pulido o el granallado, pueden mejorar la textura de la superficie, estos pasos aumentan el tiempo y el coste totales de fabricación. |
Versatilidad de materiales | Costo material |
Se puede utilizar una gran variedad de aleaciones de aluminio en polvo, cada una con sus propias propiedades. Esto permite a los ingenieros adaptar la selección del material a los requisitos específicos de la aplicación. Por ejemplo, algunas aleaciones priorizan la alta resistencia, mientras que otras ofrecen una mayor resistencia a la corrosión o una mejor maquinabilidad tras la fabricación. | El polvo de aleación de aluminio puede ser más caro que los lingotes de aluminio tradicionales o los productos forjados. Esto se debe en parte a los pasos de procesamiento adicionales que conlleva la producción de polvo y a los requisitos de manipulación especializada. Sin embargo, las ventajas de la AM, como la reducción del desperdicio de material y la fabricación de formas casi netas, pueden compensar el mayor coste del material en algunas aplicaciones. |
Fabricación en forma casi neta | Propiedades isótropas |
La fabricación aditiva con polvo de aleación de aluminio permite fabricar componentes de forma casi neta. Esto significa que la forma final del componente se consigue con un mínimo de residuos tras el procesamiento. Esto reduce el consumo de material y agiliza el proceso de producción en comparación con los métodos convencionales, que a menudo implican una importante eliminación de material. | Las piezas fabricadas con polvo de aleación de aluminio pueden presentar propiedades ligeramente anisótropas, lo que significa que su resistencia mecánica puede variar en función de la dirección de fabricación. Esto se debe a que las partículas de polvo tienden a alinearse a lo largo de la dirección de fabricación durante el proceso de AM. Sin embargo, los avances en la tecnología del polvo y las técnicas de AM están mejorando continuamente la isotropía de los componentes de aleación de aluminio. |
Reciclabilidad | Impacto medioambiental |
El polvo de aleación de aluminio ofrece una excelente reciclabilidad. Al igual que la chatarra de aluminio tradicional, el polvo usado puede reprocesarse y reutilizarse en procesos de AM, lo que minimiza los residuos y promueve prácticas de fabricación sostenibles. | La producción de polvo de aleaciones de aluminio puede requerir mucha energía y, dependiendo de la fuente de energía utilizada, puede tener una mayor huella medioambiental que los métodos de fabricación tradicionales. Sin embargo, las investigaciones en curso se centran en desarrollar técnicas de producción de polvo más eficientes desde el punto de vista energético para reducir el impacto medioambiental. |
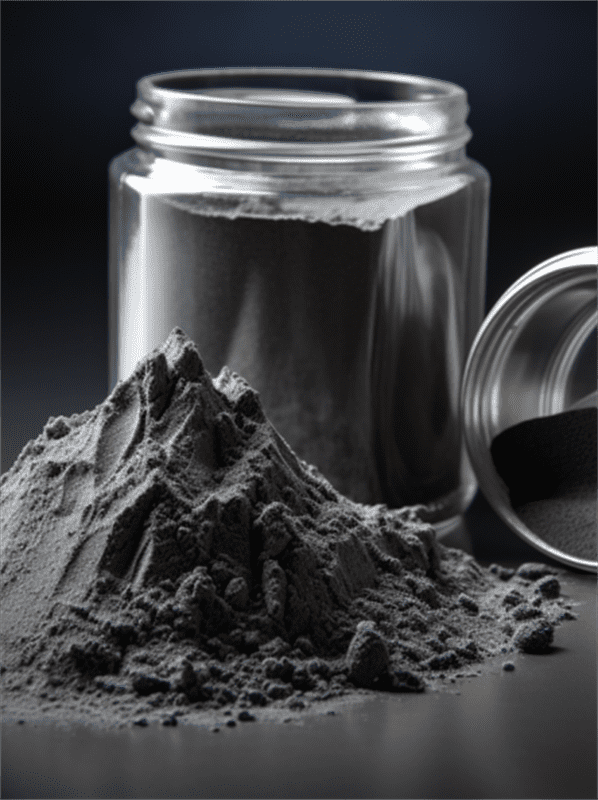
Preguntas frecuentes
¿Cuáles son las aleaciones más utilizadas como polvo de aleación de aluminio?
Las aleaciones en polvo más comunes son: Series 2xxx como 2014 y 2024, aleaciones 5xxx como 5083, aleaciones 6xxx incluyendo 6061 y 6082, y aleaciones 7xxx siendo populares 7050 y 7075.
¿Qué tamaño de partícula es mejor para el moldeo por inyección de metal utilizando polvos de aluminio?
Para el moldeo por inyección de metales con polvos de aleaciones de aluminio se suele recomendar un tamaño de partícula de entre 15 y 45 micras.
¿Qué tipos de procesos de atomización pueden producir polvo de aleación de aluminio?
La atomización con gas y la atomización con agua son los dos principales procesos industriales utilizados. El método de atomización con disco giratorio también puede producir polvos de aluminio.
¿Cuál es la ventaja de utilizar aleaciones de aluminio de la serie 5xxx para la pulverización térmica?
Las aleaciones de Al de la serie 5xxx, como la 5083, tienen una excelente resistencia a la corrosión, al tiempo que permanecen dimensionalmente estables a temperaturas elevadas, lo que las hace adecuadas para revestimientos por pulverización térmica para exposiciones marinas y químicas.
¿Qué afecta al precio del polvo de aleación de aluminio?
La composición de la aleación, las características de las partículas como el tamaño y la forma, el volumen del pedido, los aranceles regionales y los costes de transporte determinan el precio final de los distintos proveedores de polvo de aluminio.
¿Qué normas se aplican a los polvos de aleaciones de aluminio para usos de fabricación aditiva?
Entre las principales normas figuran ASTM B602, AMS4200, EN1706 e ISO 13318. Se están desarrollando otras normas específicas de AM para abordar los requisitos relacionados con el proceso.
¿Se puede reutilizar el polvo de aleación de aluminio?
En general, no se recomienda reutilizar el polvo de aluminio para aplicaciones críticas. Las condiciones de almacenamiento pueden permitir la captación de humedad y la oxidación, limitando el rendimiento del polvo. La reutilización menor puede ser posible en aplicaciones no críticas con las pruebas adecuadas.
¿Las aleaciones de aluminio de mayor número son siempre más resistentes que las de menor número?
En general, los polvos de las series 2xxx, 6xxx y 7xxx de mayor número tienen mayor resistencia que las aleaciones 1xxx o 5xxx, pero puede existir un solapamiento significativo en función de la composición exacta, las características del polvo y el historial de procesamiento. Compruebe siempre los datos del proveedor para conocer las propiedades garantizadas del polvo.
¿Por qué preocupan la porosidad y la anisotropía en los componentes de aluminio fabricados por AM?
La elevada conductividad térmica y reflectividad del aluminio, combinada con la rápida solidificación durante la fusión por láser o haz electrónico, dificulta una fusión óptima y la salida de burbujas de gas, lo que provoca defectos. También surgen diferentes propiedades mecánicas paralelas y transversales a las capas de construcción.
¿Puedo mezclar diferentes polvos de aleación de aluminio para crear calidades personalizadas?
Por lo general, no es aconsejable mezclar polvos para crear aleaciones intermedias o personalizadas debido a los riesgos de mezcla incompleta, reacciones de aleación o unión inadecuada de las partículas durante la fabricación de la pieza. Consulte estrechamente con su proveedor de polvo cuando explore combinaciones de propiedades.
Compartir
MET3DP Technology Co., LTD es un proveedor líder de soluciones de fabricación aditiva con sede en Qingdao, China. Nuestra empresa está especializada en equipos de impresión 3D y polvos metálicos de alto rendimiento para aplicaciones industriales.
Solicite información para obtener el mejor precio y una solución personalizada para su empresa.
Artículos relacionados
Acerca de Met3DP
Actualización reciente
Nuestro producto
CONTACTO
¿Tiene alguna pregunta? ¡Envíenos un mensaje ahora! Atenderemos su solicitud con todo un equipo tras recibir su mensaje.
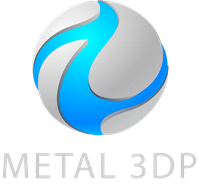
Polvos metálicos para impresión 3D y fabricación aditiva
PRODUCTO
cONTACT INFO
- Ciudad de Qingdao, Shandong, China
- [email protected]
- [email protected]
- +86 19116340731