El proceso de atomización
Índice
Imagínese a un escultor tallando meticulosamente un enorme bloque de piedra para transformarlo en una delicada figura. En proceso de atomización funciona según un principio similar, pero en lugar de cinceles y piedra, utiliza chorros de alta potencia para descomponer metales o líquidos fundidos en partículas minúsculas altamente funcionales.
Este artículo profundiza en el fascinante mundo de la atomización, explorando sus complejidades, los tipos específicos de polvos metálicos que produce y sus diversas aplicaciones en distintos sectores.
Visión general de la atomización
En esencia, la atomización es un proceso que transforma un líquido -por lo general, metal fundido- en una fina niebla o polvo. Esto se consigue sometiendo el líquido a una corriente de gas o agua a alta presión, que interrumpe su flujo y crea una multitud de gotitas diminutas. Estas gotitas se solidifican rápidamente al caer por una cámara de recogida, lo que da como resultado una colección de polvos metálicos muy codiciados con propiedades únicas.
Existen dos métodos principales de atomización:
- Atomización de gases: En este método, se utiliza un gas inerte, como nitrógeno o argón, para descomponer el metal fundido. Esta técnica produce polvos muy esféricos con excelentes características de fluidez y una oxidación mínima.
- Atomización del agua: En este caso, un chorro de agua a alta presión interrumpe la corriente de metal fundido. Este método suele ser más rentable, pero da lugar a polvos menos esféricos y potencialmente más oxidados en comparación con la atomización con gas.
La elección entre estos métodos depende de las características deseadas del polvo, del tipo de material y de consideraciones de coste.
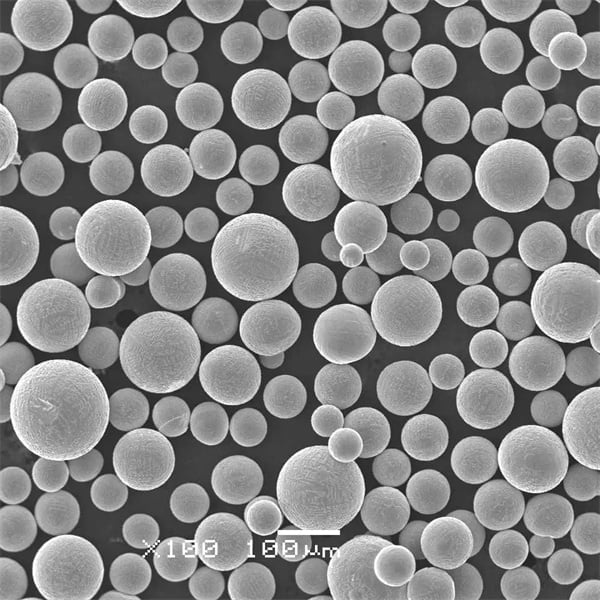
Exploración de diferentes polvos metálicos
En proceso de atomización descubre un tesoro de polvos metálicos, cada uno de ellos con propiedades y aplicaciones distintas. Profundicemos en diez de estos fascinantes polvos metálicos:
1. Polvos de acero inoxidable:
- Composición: Principalmente hierro, cromo, níquel y cantidades variables de otros elementos como molibdeno y nitrógeno.
- Propiedades: Excelente resistencia a la corrosión, alta resistencia, buena conformabilidad.
- Aplicaciones: Fabricación aditiva (impresión 3D) de componentes complejos, moldeo por inyección para piezas intrincadas, pulverización térmica para resistencia al desgaste y la corrosión.
2. Polvos de superaleación a base de níquel:
- Composición: Níquel como elemento base, combinado con cromo, cobalto, molibdeno y otros elementos en función de la aleación específica.
- Propiedades: Excepcional resistencia a altas temperaturas, a la oxidación y a la fluencia (deformación bajo tensión a altas temperaturas).
- Aplicaciones: Componentes de motores de turbina de gas, piezas aeroespaciales, intercambiadores de calor que funcionan en entornos extremos.
3. Polvos de titanio:
- Composición: Principalmente titanio, con pequeñas cantidades de oxígeno, nitrógeno y otros elementos según el grado.
- Propiedades: Elevada relación resistencia/peso, excelente biocompatibilidad, resistencia a la corrosión.
- Aplicaciones: Fabricación aditiva de piezas aeroespaciales ligeras y resistentes, implantes biomédicos para una integración ósea superior.
4. Polvos de aluminio:
- Composición: Principalmente aluminio, con niveles variables de silicio, hierro y otros elementos según la aleación.
- Propiedades: Ligero, buena conductividad eléctrica, altamente reciclable.
- Aplicaciones: Fabricación aditiva para la creación rápida de prototipos y componentes ligeros, pirotecnia (para producir chispas y efectos de humo).
5. Polvos de cobre:
- Composición: Principalmente cobre, con posibles trazas de oxígeno y otros elementos.
- Propiedades: Excelente conductividad eléctrica y térmica, buena maquinabilidad.
- Aplicaciones: Contactos y conectores eléctricos, disipadores de calor para gestionar la transferencia térmica, fabricación aditiva de componentes conductores.
6. Polvos de hierro:
- Composición: Principalmente hierro, con niveles variables de carbono, oxígeno y otros elementos según el tipo (por ejemplo, polvo de hierro atomizado, polvo de hierro carbonilado).
- Propiedades: Propiedades magnéticas (varían según el tipo), buena maquinabilidad, alta densidad.
- Aplicaciones: Componentes magnéticos blandos para transformadores e inductores, moldeo por inyección de metales para formas complejas, materiales de fricción para frenos y embragues.
7. Polvos de cobalto:
- Composición: Principalmente cobalto, con posibles trazas de hierro, níquel y otros elementos.
- Propiedades: Alta fuerza magnética, resistencia al desgaste, buena dureza.
- Aplicaciones: Herramientas de corte, imanes permanentes, recargue para la resistencia al desgaste de los componentes.
8. Polvos de wolframio:
- Composición: Principalmente tungsteno, con posibles trazas de oxígeno, carbono y otros elementos.
- Propiedades: Punto de fusión extremadamente alto, excelente densidad, buena resistencia al desgaste.
- Aplicaciones: Electrodos de soldadura de gas inerte de tungsteno (TIG), filamentos para lámparas incandescentes, munición perforante.
9. Polvos de molibdeno:
- Composición: Principalmente molibdeno, con posibles trazas de oxígeno, carbono y otros elementos.
Visión general de la atomización
Además de los métodos básicos, la atomización puede clasificarse en función de la presión utilizada para descomponer el líquido:
- Atomización por gas a alta presión (HGPA): Este método utiliza presiones de gas extremadamente altas (hasta 30 MPa o 4.351 psi) para producir polvos excepcionalmente finos con una distribución de tamaños estrecha. Los polvos HGPA son ideales para aplicaciones que exigen alta precisión y propiedades uniformes.
- Atomización de gas a baja presión (LGPA): Aquí se emplean presiones de gas más bajas (normalmente inferiores a 10 MPa o 1.450 psi). Esto da lugar a polvos más gruesos en comparación con el HGPA, pero ofrece un enfoque más rentable. Los polvos LGPA son adecuados para aplicaciones en las que el tamaño exacto de las partículas es menos crítico.
Factores adicionales que influyen en el proceso de atomización:
- Temperatura de fusión: La temperatura a la que se atomiza el metal influye significativamente en las características finales del polvo. A temperaturas más altas se obtienen partículas más grandes y esféricas, mientras que a temperaturas más bajas se obtienen polvos más pequeños y menos esféricos.
- Caudal de gas de atomización: La velocidad a la que se introduce el gas en la corriente de metal fundido afecta al tamaño y la distribución de las partículas resultantes. Los caudales más altos suelen producir polvos más finos.
Más allá de los metales: Atomización para materiales diversos
El poder de la atomización va más allá de los metales. Este versátil proceso puede utilizarse para crear polvos a partir de una amplia gama de materiales, incluidos:
- Cerámica: Los polvos de alúmina, circonio y carburo de silicio se producen para aplicaciones como componentes resistentes al desgaste y herramientas de corte de alto rendimiento.
- Plásticos: Polímeros como el nailon y el polietileno pueden atomizarse para crear polvos finos para su uso en fabricación aditiva, revestimientos y materiales compuestos.
- Alimentación y productos farmacéuticos: Alimentos como la leche y el café pueden atomizarse para aplicaciones instantáneas, mientras que los productos farmacéuticos aprovechan este proceso para crear sistemas de liberación controlada de fármacos.
Ventajas de la Proceso de atomización
El proceso de atomización ofrece multitud de ventajas, lo que lo convierte en una piedra angular en diversas industrias:
- Producción de polvos de gran pureza: La atomización permite crear polvos con una contaminación mínima, lo que garantiza unas propiedades del material uniformes y predecibles.
- Control preciso de la morfología del polvo: El ajuste de diversos parámetros permite controlar con precisión el tamaño, la forma y la distribución de las partículas de polvo para satisfacer los requisitos específicos de cada aplicación.
- Propiedades del material mejoradas: La rápida solidificación inherente a la atomización puede dar lugar a microestructuras únicas dentro de las partículas de polvo, mejorando propiedades como la resistencia, la ductilidad y la resistencia a la corrosión.
- Polvos a medida para diversas aplicaciones: La capacidad de atomizar una amplia gama de materiales crea una vasta biblioteca de polvos adecuados para innumerables aplicaciones.
- Proceso eficiente y escalable: Las técnicas modernas de atomización son eficaces y pueden ampliarse para producir grandes volúmenes, lo que las hace adecuadas para aplicaciones industriales.
Desventajas de la atomización
Aunque es una herramienta potente, la atomización tiene ciertos inconvenientes:
- Alto consumo de energía: El proceso requiere una energía considerable para generar las altas presiones o los chorros de alta velocidad necesarios para la atomización.
- Consideraciones de costos: La instalación y el funcionamiento de una planta de atomización pueden resultar caros, lo que repercute en el coste final de los polvos producidos.
- Oxidación en polvo: Durante la atomización, sobre todo con agua, existe el riesgo de que las partículas de polvo se oxiden, lo que puede afectar a sus propiedades.
- Cuestiones de seguridad: El proceso puede implicar la manipulación de metales fundidos a alta temperatura y gases a alta presión, lo que exige estrictos protocolos de seguridad.
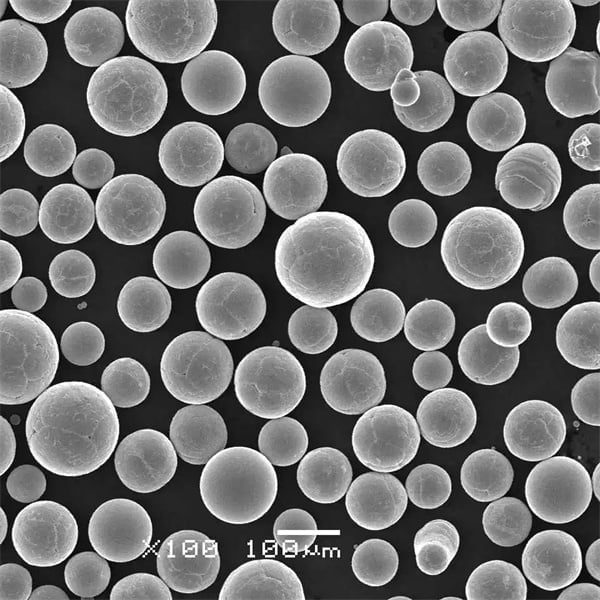
Comparación de la atomización con gas y agua
A la hora de elegir entre la atomización con gas o con agua, entran en juego varios factores clave:
Características del polvo:
- Esfericidad: La atomización con gas suele producir polvos más esféricos que la atomización con agua. Las partículas esféricas ofrecen una mejor fluidez, densidad de empaquetamiento y son más adecuadas para los procesos de fabricación aditiva.
- Oxidación: La atomización con agua puede introducir más oxígeno en las partículas de polvo que la atomización con gas. Esto puede ser un problema en aplicaciones que requieren una alta resistencia a la corrosión.
Consideraciones de costos:
- Inversión inicial: Los equipos de atomización por gas suelen requerir una mayor inversión inicial en comparación con las instalaciones de atomización por agua.
- Costes operativos: El coste del gas de atomización (por ejemplo, argón, nitrógeno) puede ser un factor significativo en la atomización con gas, mientras que la atomización con agua tiene menores costes operativos asociados al medio de atomización.
Aplicaciones:
- Aplicaciones de alto rendimiento: Cuando la morfología precisa del polvo y una oxidación mínima son cruciales (por ejemplo, en la fabricación aditiva de componentes aeroespaciales), la atomización con gas suele ser la opción preferida.
- Aplicaciones sensibles a los costes: Para aplicaciones menos críticas en las que el coste es una preocupación primordial (por ejemplo, la producción de materias primas para el moldeo por inyección de metales), la atomización con agua podría ser una opción más viable.
- Impacto medioambiental: El elevado consumo de energía asociado a la atomización puede contribuir a las emisiones de gases de efecto invernadero. Además, la eliminación de las aguas residuales generadas durante la atomización del agua debe gestionarse cuidadosamente para minimizar el impacto medioambiental.
Mitigar los inconvenientes: Estrategias de optimización
A pesar de las limitaciones, se pueden emplear varias estrategias para optimizar el proceso de atomización y abordar sus posibles inconvenientes:
- Tecnologías energéticamente eficientes: Los avances en la tecnología de atomización están conduciendo al desarrollo de procesos más eficientes desde el punto de vista energético, como la atomización ultrasónica, que utiliza ondas sonoras para la atomización.
- Reciclaje de materiales: El reciclaje de los desechos y polvos metálicos en el proceso de atomización puede reducir el impacto medioambiental y los costes de producción.
- Sistemas de circuito cerrado de agua: La implantación de sistemas de circuito cerrado en la atomización del agua puede reducir significativamente el consumo de agua y la generación de aguas residuales.
- Estrictas medidas de seguridad: La aplicación de protocolos de seguridad estrictos durante la atomización, que incluyan una ventilación adecuada, equipos de protección individual y formación de los operarios, puede minimizar los riesgos de seguridad.
las aplicaciones de proceso de atomización
Los polvos atomizados se aplican en un amplio espectro de industrias y desempeñan un papel vital en la configuración de nuestro mundo:
Fabricación aditiva (impresión 3D): Los polvos metálicos como el acero inoxidable, el titanio y las superaleaciones de níquel son los componentes básicos para crear componentes complejos y de alto rendimiento mediante tecnologías de impresión 3D.
Moldeo por inyección de metales (MIM): Este proceso utiliza polvos atomizados para crear piezas metálicas complejas mediante una combinación de moldeo y sinterización. El MIM es adecuado para la producción en serie de componentes pequeños y complejos.
Pulverización térmica: Los polvos atomizados se utilizan para recubrir superficies con una capa de metal, cerámica u otros materiales. La pulverización térmica mejora propiedades como la resistencia al desgaste, la resistencia a la corrosión y el aislamiento térmico.
Tecnologías de baterías: Los polvos de níquel y litio son componentes cruciales en la producción de baterías de alto rendimiento para vehículos eléctricos y dispositivos electrónicos.
Catalizadores: Los polvos finamente atomizados con áreas superficiales elevadas se utilizan como catalizadores en diversas reacciones químicas, acelerando la velocidad de reacción y mejorando la eficacia del proceso.
Productos farmacéuticos: La atomización permite crear partículas de fármaco de tamaño y perfiles de liberación controlados, lo que posibilita la administración selectiva de fármacos en el organismo.
Alimentación y agricultura: El café instantáneo, la leche en polvo y los fertilizantes suelen utilizar ingredientes atomizados para mejorar su conservación, funcionalidad y propiedades de liberación controlada.
El cambiante panorama de la atomización
El futuro de la atomización rebosa de posibilidades apasionantes:
- Atomización de nanopartículas: La capacidad de producir polvos aún más finos, del tamaño de nanopartículas, mediante técnicas avanzadas de atomización abrirá las puertas a nuevas aplicaciones en nanotecnología y medicina.
- Atomización multimaterial: Los avances en las técnicas de coatomización permitirán crear polvos con una mezcla de distintos materiales, lo que conducirá al desarrollo de materiales compuestos con propiedades únicas.
- Atomización sostenible: Investigación sobre eficiencia energética procesos de atomización y una mayor utilización de materiales reciclados contribuirán a un futuro de atomización más sostenible.
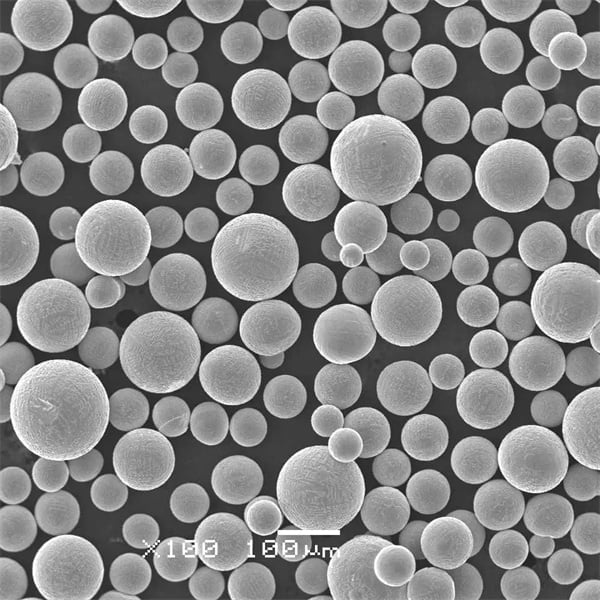
PREGUNTAS FRECUENTES
P: ¿Cuál es la diferencia entre atomización y pulverización?
R: Aunque ambos procesos crean partículas más pequeñas, la atomización suele tratar líquidos, transformándolos en polvos finos. La pulverización, en cambio, se centra en descomponer materiales sólidos en trozos más pequeños.
P: ¿Se puede atomizar cualquier líquido?
R: La atomización se utiliza sobre todo con metales y otros materiales que pueden fundirse. Sin embargo, con las técnicas adecuadas, algunos líquidos viscosos (como ciertos polímeros) también pueden atomizarse.
P: ¿Cómo se controla el tamaño de las partículas de polvo atomizado?
R: El tamaño de las partículas de polvo depende de varios factores, como la presión del gas de atomización o del chorro de agua, la temperatura de la masa fundida y el diseño de la boquilla. Ajustando estos parámetros, se puede conseguir la distribución de tamaño de partícula deseada.
P: ¿Qué precauciones de seguridad son necesarias durante la atomización?
R: Los procesos de atomización implican altas temperaturas y materiales potencialmente peligrosos. Por lo tanto, una ventilación adecuada, equipos de protección individual (EPI) para los operarios y el cumplimiento de los protocolos de seguridad son esenciales para minimizar los riesgos.
P: ¿Cuál es el futuro de la atomización?
R: El futuro de la atomización es prometedor, con avances tecnológicos que conducirán al desarrollo de procesos de atomización más eficientes, sostenibles y precisos. Esto allanará el camino para la creación de nuevos materiales y aplicaciones en diversas industrias.
Compartir
MET3DP Technology Co., LTD es un proveedor líder de soluciones de fabricación aditiva con sede en Qingdao, China. Nuestra empresa está especializada en equipos de impresión 3D y polvos metálicos de alto rendimiento para aplicaciones industriales.
Solicite información para obtener el mejor precio y una solución personalizada para su empresa.
Artículos relacionados
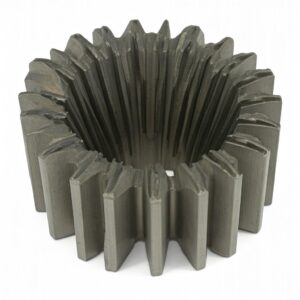
Segmentos de álabe de tobera de alto rendimiento: Revolucionando la eficiencia de las turbinas con la impresión metálica en 3D
Leer Más "Acerca de Met3DP
Actualización reciente
Nuestro producto
CONTACTO
¿Tiene alguna pregunta? ¡Envíenos un mensaje ahora! Atenderemos su solicitud con todo un equipo tras recibir su mensaje.
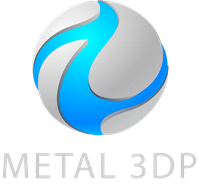
Polvos metálicos para impresión 3D y fabricación aditiva
PRODUCTO
cONTACT INFO
- Ciudad de Qingdao, Shandong, China
- [email protected]
- [email protected]
- +86 19116340731