la aplicación del DMLS en el sector aeroespacial
Índice
Imagínese fabricar piezas aeronáuticas complejas con una libertad de diseño sin precedentes, reduciendo el peso y aumentando el rendimiento: esa es la magia del Sinterizado Directo de Metal por Láser (DMLS) en la industria aeroespacial. Esta revolucionaria tecnología de impresión 3D está transformando rápidamente la forma en que diseñamos, fabricamos y utilizamos componentes en aviones, satélites y otros ámbitos. Abróchese el cinturón para adentrarnos en el fascinante mundo del DMLS en el sector aeroespacial, explorando sus aplicaciones, los polvos metálicos específicos que utiliza y el apasionante futuro que promete.
DMLS: Un motor de impresión 3D para el sector aeroespacial
El DMLS, también conocido como fusión directa de metales por láser (DMLS®), es un proceso de fabricación aditiva que utiliza un láser de alta potencia para fundir selectivamente partículas de polvo metálico capa a capa, construyendo un objeto 3D a partir de un modelo de diseño asistido por ordenador (CAD). A diferencia de las técnicas tradicionales de fabricación sustractiva, como el mecanizado, el DMLS crea piezas desde cero, lo que ofrece un tesoro de ventajas para las aplicaciones aeroespaciales:
- Libertad de diseño sin igual: El DMLS se libera de las limitaciones de los métodos convencionales. Imagine estructuras reticulares internas para reducir el peso, canales de refrigeración complejos para mejorar la eficiencia del motor o piezas con geometrías antes imposibles: el DMLS lo hace todo posible.
- Proeza de aligeramiento: Cada gramo cuenta en la industria aeroespacial. El DMLS permite a los ingenieros diseñar componentes intrincados y ligeros que reducen significativamente el peso total de las aeronaves, lo que se traduce en una mayor eficiencia del combustible y una mayor autonomía de vuelo.
- Creación rápida de prototipos e iteración: La capacidad de fabricar piezas complejas con rapidez y directamente a partir de modelos CAD permite crear prototipos e iteraciones de diseño con rapidez. Esto acelera el proceso de desarrollo y reduce el plazo de comercialización de nuevas tecnologías aeroespaciales.
- Reducción de residuos y ahorro de material: El DMLS utiliza únicamente el polvo metálico necesario, lo que minimiza los residuos en comparación con los métodos tradicionales, que generan una gran cantidad de material de desecho. Esto se traduce en un ahorro de costes y en un proceso de fabricación más respetuoso con el medio ambiente.
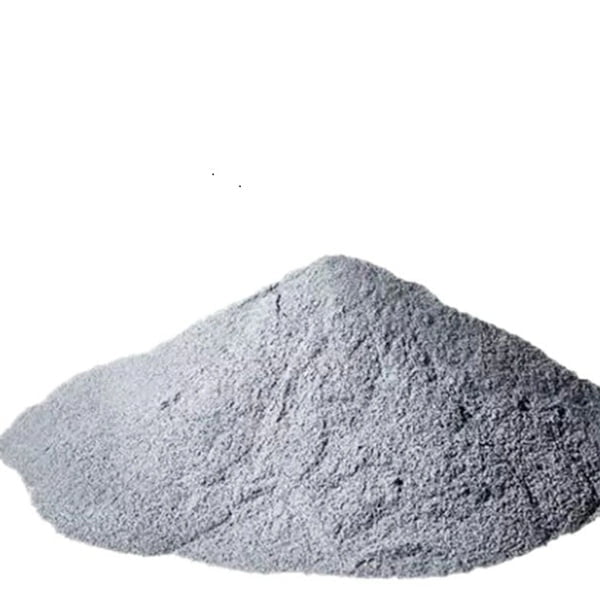
DMLS en acción: Un escaparate de aplicaciones
El DMLS no es sólo teórico; está revolucionando el sector aeroespacial en aplicaciones reales:
- Motores de aviación: Cada vez se fabrican más con DMLS componentes de motor complejos, como cámaras de combustión, inyectores de combustible y álabes de turbina ligeros con intrincados canales de refrigeración internos, lo que mejora la eficiencia del combustible y el rendimiento del motor.
- Estructuras de fuselaje: El DMLS permite crear componentes de fuselaje ligeros y de alta resistencia, como soportes, costillas y accesorios, lo que contribuye a reducir el peso total y a mejorar el rendimiento de los aviones.
- Satélites y naves espaciales: La capacidad de crear piezas complejas con una elevada relación resistencia-peso hace que el DMLS sea ideal para estructuras de satélites, mecanismos desplegables e incluso componentes de propulsión, lo que allana el camino hacia naves espaciales más ligeras y eficientes.
- Vehículos aéreos no tripulados (UAV): El DMLS se adapta perfectamente a la creación rápida de prototipos y a la producción de componentes ligeros y personalizados para vehículos aéreos no tripulados, fomentando la innovación en el sector de los drones, en rápido crecimiento.
El arsenal de los polvos metálicos
El éxito del DMLS depende de los polvos metálicos que se utilicen. He aquí un vistazo a algunos de los principales contendientes, cada uno con sus propiedades únicas:
Polvo metálico | Descripción | Propiedades | Aplicaciones aeroespaciales |
---|---|---|---|
Aleaciones de titanio (Ti-6Al-4V, Ti-6Al-4V ELI): | El caballo de batalla del DMLS aeroespacial, que ofrece una excelente relación resistencia-peso, alta resistencia a la corrosión y biocompatibilidad (útil para sistemas de soporte vital de naves espaciales). | Excelentes propiedades mecánicas, buena soldabilidad, biocompatible. | Álabes de turbina, componentes de fuselaje, estructuras de naves espaciales. |
Inconel 625: | Superaleación de níquel-cromo de alto rendimiento conocida por su excepcional resistencia a altas temperaturas y a la oxidación. | Excepcional rendimiento a altas temperaturas, buena resistencia a la corrosión. | Cámaras de combustión de motores, componentes de la sección caliente, aplicaciones aeroespaciales de alta temperatura. |
Aleaciones de aluminio (AlSi10Mg, Scalmalloy): | Las aleaciones de aluminio, que ofrecen un buen equilibrio entre resistencia, peso e imprimibilidad, se utilizan cada vez más en el DMLS aeroespacial, sobre todo para componentes no críticos. | Ligero, buena imprimibilidad, algunas limitaciones de resistencia. | Componentes ligeros de fuselajes, carcasas, piezas no críticas. |
Acero inoxidable (316L): | Una opción versátil y rentable, que ofrece buena resistencia a la corrosión y maquinabilidad. | Buena resistencia a la corrosión, maquinabilidad, resistencia moderada. | Carcasas, conductos, componentes no críticos que requieren resistencia a la corrosión. |
Cromo-cobalto (CoCr): | Aleación biocompatible con una excelente resistencia al desgaste, lo que la convierte en una valiosa opción para determinadas aplicaciones aeroespaciales. | Alta resistencia al desgaste, biocompatible, buena resistencia. | Componentes del tren de aterrizaje, aplicaciones específicas de desgaste. |
Aleaciones de cobre (CuNi) (continuación): | Las aleaciones de cobre, que ofrecen una elevada conductividad térmica y eléctrica, están encontrando nichos de aplicación en el sector aeroespacial para intercambiadores de calor y componentes eléctricos. | conductividad, buena conductividad eléctrica. | Intercambiadores de calor, componentes eléctricos en naves espaciales. |
Molibdeno (Mo): | Metal refractario conocido por su excepcional resistencia a altas temperaturas y su buena conductividad térmica. | Excelente comportamiento a altas temperaturas, buena conductividad térmica. | Componentes refractarios para motores de cohetes, escudos térmicos. |
Tántalo (Ta): | Otro metal refractario con un punto de fusión muy elevado y una excelente resistencia a la corrosión. | Punto de fusión ultraalto, buena resistencia a la corrosión. | Crisoles para manipulación de metal fundido, aplicaciones específicas de alta temperatura. |
Aleaciones de níquel (Rene 41, Inconel 718): | Familia de aleaciones de níquel de alto rendimiento que ofrecen una combinación de solidez, rendimiento a altas temperaturas y buena resistencia a la oxidación. | Excelentes propiedades mecánicas, buen comportamiento a altas temperaturas. | Álabes de turbina, discos y otros componentes estructurales de alta temperatura en motores a reacción. |
Elegir el polvo metálico adecuado
Selección del polvo metálico óptimo para un DMLS es como el trabajo de un casamentero: requiere una cuidadosa consideración de diversos factores:
- Propiedades requeridas: Las necesidades específicas del componente determinan la elección del polvo. Las piezas de alta temperatura de los motores requieren polvos como Inconel 625 o René 41, mientras que los componentes ligeros de los fuselajes pueden utilizar aleaciones de aluminio.
- Imprimibilidad: No todos los polvos metálicos son iguales en términos de imprimibilidad. Factores como el tamaño, la forma y la fluidez de las partículas influyen considerablemente en el éxito del proceso DMLS.
- Costo: El precio de los polvos metálicos varía considerablemente. Por ejemplo, las aleaciones de titanio suelen ser más caras que el acero inoxidable. Hay que encontrar un equilibrio entre el coste y los requisitos de rendimiento.
Ventajas y limitaciones de DMLS
Aunque el DMLS ofrece un tesoro de ventajas, no está exento de limitaciones:
Ventajas:
- Libertad de diseño sin igual: El DMLS abre posibilidades de diseño antes inimaginables, fomentando la innovación y el aumento del rendimiento.
- Aligeramiento: La capacidad de crear estructuras intrincadas y ligeras se traduce en una reducción significativa del peso en las aplicaciones aeroespaciales.
- Creación rápida de prototipos e iteración: El DMLS agiliza el proceso de desarrollo al permitir la creación rápida de prototipos y cambios de diseño.
- Reducción de residuos: El DMLS minimiza el desperdicio de material en comparación con los métodos tradicionales, fomentando la sostenibilidad.
Limitaciones:
- Disponibilidad de material: La selección de polvos metálicos fácilmente disponibles para DMLS sigue evolucionando en comparación con los materiales de fabricación tradicionales.
- Acabado superficial: Las piezas DMLS pueden tener un acabado superficial más rugoso en comparación con los componentes mecanizados, lo que puede requerir pasos adicionales de posprocesamiento.
- Limitaciones del tamaño de las piezas: Las máquinas DMLS actuales tienen limitaciones en cuanto al tamaño de las piezas que pueden producir.
- Costo: Aunque el DMLS ofrece ventajas a largo plazo, el coste inicial de las máquinas DMLS y los polvos metálicos puede ser superior al de los métodos tradicionales para determinadas aplicaciones.
El futuro del DMLS en el sector aeroespacial: Alcanzando nuevas cotas
El futuro del DMLS en el sector aeroespacial es muy prometedor. A medida que avanza la tecnología, podemos esperar:
- Desarrollo de nuevos polvos metálicos: La gama de polvos metálicos disponibles diseñados específicamente para aplicaciones de DMLS seguirá ampliándose, ampliando los límites de lo posible.
- Mayores volúmenes de construcción: Las máquinas de DMLS con envolventes más grandes serán cada vez más comunes, lo que permitirá la creación de componentes aeroespaciales aún más grandes y complejos.
- Acabado superficial mejorado: Los avances en la tecnología DMLS permitirán obtener acabados superficiales más lisos, lo que reducirá potencialmente la necesidad de un tratamiento posterior exhaustivo.
- Costes reducidos: A medida que la tecnología DMLS madure y aumente su adopción, es probable que el coste global de las máquinas DMLS y los polvos metálicos disminuya, haciéndola más accesible para una gama más amplia de aplicaciones aeroespaciales.
El DMLS no es sólo una tecnología de fabricación; es un catalizador de la innovación en el sector aeroespacial. Al liberar la libertad de diseño, reducir el peso y acelerar los ciclos de desarrollo, el DMLS nos impulsa hacia un futuro de aviones, satélites y naves espaciales más ligeros, eficientes y de alto rendimiento. El cielo es realmente el límite para DMLS en el sector aeroespacial
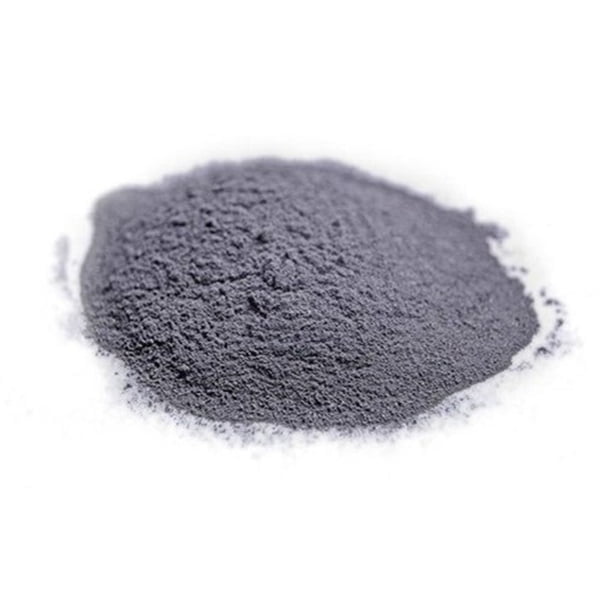
PREGUNTAS FRECUENTES
P: ¿Cuáles son las ventajas de utilizar DMLS para aplicaciones aeroespaciales?
R: El DMLS ofrece numerosas ventajas, como una libertad de diseño inigualable, capacidad de aligeramiento, creación rápida de prototipos y reducción de residuos en comparación con los métodos de fabricación tradicionales.
P: ¿Cuáles son algunas de las limitaciones del DMLS?
R: Las limitaciones incluyen la selección actual de polvos metálicos fácilmente disponibles, los posibles problemas de acabado superficial, las limitaciones de tamaño de las piezas y los costes iniciales más elevados en comparación con algunos métodos tradicionales.
P: ¿Cuáles son algunas de las tendencias futuras del DMLS en el sector aeroespacial?
R: El futuro del DMLS en el sector aeroespacial es increíblemente prometedor. Podemos esperar avances en varias áreas clave:
Desarrollo de nuevos polvos metálicos: Los fabricantes de polvo metálico están innovando constantemente, formulando nuevos polvos con propiedades superiores específicamente adaptados al DMLS. Esto ampliará aún más las posibilidades de diseño, permitiendo la creación de componentes con una relación resistencia-peso aún mayor, un mejor rendimiento a altas temperaturas y una mayor resistencia a la corrosión. Imagine aleaciones exóticas que amplíen los límites de lo que es posible en la actualidad, revolucionen el rendimiento de los motores y conduzcan al desarrollo de la próxima generación de vehículos aeroespaciales.
Mayores volúmenes de construcción: Las máquinas DMLS actuales están limitadas en cuanto al tamaño de las piezas que pueden producir. Sin embargo, el futuro está lleno de máquinas de mayor tamaño. Esto cambiará las reglas del juego, ya que permitirá crear secciones enteras de fuselajes, grandes componentes de motores de cohetes e incluso estructuras completas de satélites directamente desde una impresora 3D. Esto abre las puertas a reducciones significativas en el número de piezas y en la complejidad del montaje, lo que dará lugar a naves espaciales más ligeras y eficientes.
Acabado superficial mejorado: Aunque las piezas DMLS ofrecen una funcionalidad excepcional, su acabado superficial puede ser más rugoso que el de los componentes mecanizados tradicionalmente. En ocasiones, esto puede requerir pasos de posprocesamiento adicionales, como el pulido o el mecanizado. Sin embargo, los avances en la tecnología DMLS están permitiendo obtener acabados superficiales más suaves directamente desde el proceso de impresión. Esto no sólo reducirá las necesidades de postprocesado, sino que también mejorará potencialmente el rendimiento de determinados componentes al crear trayectorias de flujo de aire más suaves o reducir la fricción.
Costes reducidos: A medida que madure la tecnología DMLS y aumente su adopción, se espera que disminuya el coste global de las máquinas DMLS y de los polvos metálicos. Esto hará que el DMLS sea una opción más viable para una gama más amplia de aplicaciones aeroespaciales, no sólo para componentes de gama alta y rendimiento crítico. Esta democratización del DMLS tiene el potencial de acelerar la innovación en todo el sector aeroespacial.
En conclusión
El DMLS no es sólo una tecnología de fabricación; es una revolución en ciernes para la industria aeroespacial. Al liberar la libertad de diseño, reducir el peso, agilizar los ciclos de desarrollo y promover la sostenibilidad, el DMLS nos impulsa hacia un futuro de máquinas voladoras más ligeras, eficientes y de alto rendimiento. A medida que la tecnología DMLS sigue evolucionando, las posibilidades son realmente ilimitadas. Sin duda, el futuro de la industria aeroespacial está marcado por el DMLS, y el cielo no es el límite, ¡sólo es el principio!
Compartir
MET3DP Technology Co., LTD es un proveedor líder de soluciones de fabricación aditiva con sede en Qingdao, China. Nuestra empresa está especializada en equipos de impresión 3D y polvos metálicos de alto rendimiento para aplicaciones industriales.
Solicite información para obtener el mejor precio y una solución personalizada para su empresa.
Artículos relacionados
Acerca de Met3DP
Actualización reciente
Nuestro producto
CONTACTO
¿Tiene alguna pregunta? ¡Envíenos un mensaje ahora! Atenderemos su solicitud con todo un equipo tras recibir su mensaje.
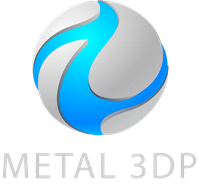
Polvos metálicos para impresión 3D y fabricación aditiva