Las fases del proceso de la tecnología DMLS
Índice
¿Alguna vez ha soñado con crear complejos objetos metálicos de la nada? Pues bien, con el Sinterizado Directo de Metales por Láser (DMLS), ese sueño se hace realidad. El DMLS, también conocido como fusión selectiva por láser (SLM), es un revolucionario proceso de impresión 3D que utiliza un láser de alta potencia para fusionar meticulosamente partículas de polvo metálico, capa a capa, para crear piezas metálicas intrincadas y funcionales.
Imagine construir un engranaje intrincado o un componente aeroespacial ligero con canales internos, todo a partir de un archivo digital: ése es el poder del DMLS. Pero, ¿cómo se produce exactamente esta magia? Abróchese el cinturón, porque estamos a punto de adentrarnos paso a paso en el fascinante mundo del DMLS.
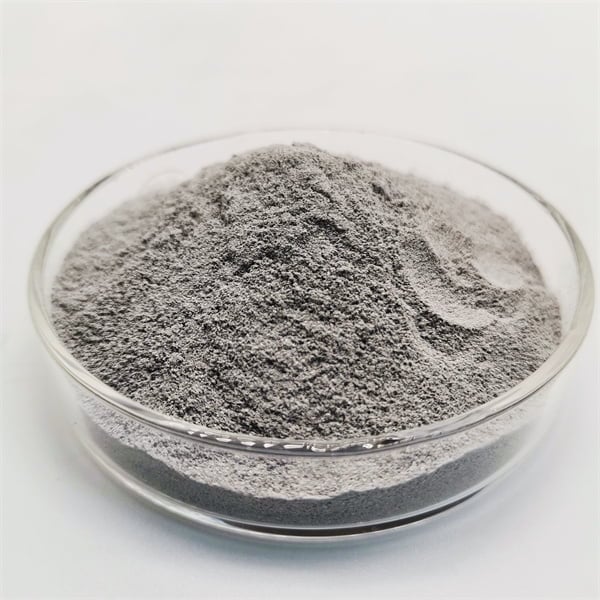
Los bloques de construcción: Una mirada a DMLS Polvos metálicos
La base de cualquier creación DMLS reside en el propio polvo metálico. Estos finos gránulos metálicos, que suelen tener un tamaño de entre 15 y 63 micras (¡increíblemente diminutos!), se presentan en una gran variedad de sabores, cada uno de los cuales ofrece propiedades únicas para aplicaciones específicas. A continuación le mostramos algunas de las opciones de polvo metálico DMLS más populares:
Polvo metálico | Composición | Propiedades | Aplicaciones |
---|---|---|---|
Acero inoxidable 316L | 16-18% Cromo, 10-14% Níquel, 2% Molibdeno | Excelente resistencia a la corrosión, alta resistencia, biocompatible | Implantes médicos, componentes aeroespaciales, joyería |
Titanio 6Al-4V (Grado 23) | 90% Titanio, 6% Aluminio, 4% Vanadio | Elevada relación resistencia/peso, buena biocompatibilidad, excelente resistencia a la corrosión | Componentes aeroespaciales, implantes médicos, artículos deportivos |
Inconel 625 | Superaleación a base de níquel-cromo | Excepcional resistencia a altas temperaturas y a la corrosión | Álabes de turbina, intercambiadores de calor, reactores nucleares |
Aluminio AlSi10Mg | Aleación de aluminio con 10% de silicio y 0,5% de magnesio | Ligero, buena resistencia a la corrosión, alta conductividad térmica | Piezas de automóvil, disipadores térmicos, carcasas de electrónica |
Cobre | 100% Cobre | Alta conductividad eléctrica, buena conductividad térmica | Intercambiadores de calor, componentes eléctricos, guías de ondas |
Acero para herramientas (H13) | Acero aleado con alto contenido de cromo | Alta resistencia al desgaste, buena estabilidad térmica | Moldes, matrices, herramientas de corte |
Níquel | 100% Níquel | Excelente resistencia a la corrosión, buena ductilidad | Equipos de procesamiento químico, componentes eléctricos, intercambiadores de calor |
Cromo-cobalto (CoCrMo) | Aleación de cobalto-cromo con molibdeno | Alta resistencia, resistencia al desgaste, biocompatible | Implantes médicos, prótesis dentales, piezas de desgaste |
Oro | 100% Oro | Alta ductilidad, maleabilidad, excelente resistencia a la corrosión | Joyería, electrónica, aplicaciones decorativas |
Esta tabla ofrece una visión del variado mundo de los polvos metálicos DMLS. Cada material tiene sus propias ventajas, por lo que son adecuados para una amplia gama de aplicaciones. A la hora de elegir un polvo metálico, factores como las propiedades mecánicas deseadas, la resistencia a la corrosión, el peso y la biocompatibilidad (para aplicaciones médicas) desempeñan un papel crucial.
Más allá de la mesa: Una inmersión más profunda en las características del polvo metálico
Es importante entender que estos polvos metálicos no son un polvo cualquiera. Están meticulosamente diseñados para garantizar un rendimiento óptimo durante el proceso DMLS. He aquí algunas características clave que hay que tener en cuenta:
- Tamaño y distribución de las partículas: Un tamaño y una distribución uniformes de las partículas son cruciales para que el polvo fluya sin problemas y la fusión por láser sea uniforme.
- Esfericidad: Las partículas esféricas ofrecen una mejor fluidez y densidad de empaquetamiento, lo que permite un proceso de fabricación más uniforme.
- Fluidez: La capacidad del polvo para fluir libremente dentro de la máquina DMLS es esencial para la formación de capas consistentes.
- Densidad aparente: Se refiere a la relación entre la masa del polvo y su volumen total. Una mayor densidad aparente permite empaquetar más material en cada capa, lo que da como resultado una pieza final más densa.
- Absortividad del láser: La capacidad del polvo metálico para absorber eficazmente la energía del láser determina el proceso de fusión y la calidad general de la construcción.
Los fabricantes hacen todo lo posible para garantizar que sus polvos metálicos DMLS cumplan estos estrictos requisitos. Al controlar cuidadosamente estas características, crean polvos diseñados específicamente para un rendimiento óptimo en DMLS.
Del sueño digital a la realidad metálica: El proceso DMLS paso a paso
Ahora que hemos explorado los componentes básicos, adentrémonos en el cautivador mundo del DMLS en sí. He aquí un desglose del proceso, paso a paso:
1. Elija el polvo metálico adecuado: Como ya se ha comentado, seleccionar el polvo metálico adecuado es fundamental para conseguir las propiedades deseadas en la pieza final.
2. Crea un modelo 3D utilizando un programa de modelado 3D: La magia del DMLS comienza con una representación digital del objeto deseado. El software de modelado 3D, similar al cincel de un escultor en la era digital, permite a los ingenieros diseñar geometrías complejas que serían imposibles de crear con los métodos de fabricación tradicionales. Estos modelos 3D dictan cada detalle de la pieza final, desde su forma general hasta los canales internos y las características intrincadas.
3. Prepare la plataforma de construcción: Imagine que un lienzo digital cobra vida. La plataforma de construcción de la máquina DMLS actúa como la base sobre la que se construirá el objeto metálico capa a capa. Esta plataforma se limpia y nivela meticulosamente para garantizar un punto de partida suave y uniforme para el proceso de construcción.
4. Coloque el polvo metálico sobre la plataforma de impresión: Una fina capa de polvo metálico, normalmente de 20 a 100 micras de grosor, se deposita uniformemente sobre la plataforma de impresión. Esta capa actúa como el primer bloque de construcción del objeto. Pueden emplearse varias técnicas, como un sistema de recubrimiento por cuchillas o un mecanismo de rodillos, para conseguir una capa de polvo uniforme y consistente.
5. El láser derrite la magia: Aquí es donde se produce la verdadera magia. Un rayo láser de alta potencia, meticulosamente guiado por el modelo digital en 3D, recorre el lecho de polvo metálico, fundiendo las partículas de forma selectiva. La densidad de potencia del láser y la trayectoria de exploración se controlan con precisión para crear la geometría deseada para cada capa. A medida que el láser funde el polvo, fusiona las partículas en una masa sólida, construyendo el objeto capa a capa.
6. Capa a capa, el objeto va tomando forma: El proceso DMLS sigue un ciclo repetitivo. Una vez fundida la primera capa, se deposita encima una nueva capa de polvo metálico. A continuación, el láser recorre esta nueva capa, fundiendo el polvo y fusionándolo con la capa anterior. Este ciclo continúa capa a capa, construyendo meticulosamente el objeto desde abajo hacia arriba hasta que todo el diseño está completo.
7. Enfriamiento: Una vez fundida la última capa, la máquina DMLS deja que el objeto construido se enfríe lentamente en una atmósfera controlada. Este proceso de enfriamiento controlado ayuda a minimizar las tensiones residuales y las deformaciones dentro de la pieza, garantizando su precisión dimensional y su integridad estructural.
8. Extracción del soporte: Al igual que los andamios utilizados en la construcción tradicional, las construcciones DMLS suelen requerir estructuras de soporte para evitar que los elementos delicados se derrumben durante el proceso de impresión. Estas estructuras de soporte suelen estar hechas del mismo polvo metálico, pero están diseñadas para poder retirarse fácilmente una vez finalizada la construcción. Se pueden utilizar técnicas como el mecanizado, el corte por chorro de agua o la extracción mecánica para separar estas estructuras de soporte, dejando al descubierto el objeto metálico final en todo su esplendor.
9. Post-procesado de la tecnología DMLS: En algunos casos, el objeto fabricado mediante DMLS puede requerir pasos adicionales de postprocesado para conseguir el acabado superficial o las propiedades mecánicas deseadas. Estos pasos pueden incluir el tratamiento térmico para aliviar la tensión o mejorar la resistencia, el chorreado de arena para un acabado superficial más suave o el mecanizado para una mayor precisión dimensional.
Desvelar las ventajas y limitaciones del DMLS
La tecnología DMLS ofrece un sinfín de ventajas sobre los métodos de fabricación tradicionales:
- Libertad de diseño: El DMLS permite crear geometrías increíblemente complejas, como canales internos, celosías y otras características intrincadas que serían imposibles o prohibitivas de producir con las técnicas tradicionales.
- Creación rápida de prototipos: La capacidad de crear piezas funcionales directamente a partir de un modelo 3D permite crear prototipos con rapidez, lo que permite a los ingenieros iterar en los diseños con rapidez y eficacia.
- Aligeramiento: El DMLS permite crear estructuras ligeras con una elevada relación resistencia-peso, lo que lo hace ideal para aplicaciones en las industrias aeroespacial y automovilística.
- Personalización: El DMLS facilita fácilmente la producción de piezas personalizadas y lotes de bajo volumen, por lo que es perfecto para aplicaciones especializadas o proyectos únicos.
Sin embargo, el DMLS también tiene limitaciones que hay que tener en cuenta:
- Costo: Las máquinas DMLS y los polvos metálicos pueden ser caros, lo que hace que el proceso sea menos adecuado para grandes volúmenes de producción.
- Limitaciones de tamaño de los edificios: El volumen de fabricación de las máquinas DMLS suele ser limitado en comparación con las técnicas tradicionales.
- Acabado superficial: Mientras que algunas piezas DMLS pueden conseguir un buen acabado superficial, otras pueden requerir un postprocesado adicional para conseguir una estética más suave.
- Limitaciones materiales: La gama de materiales disponibles para DMLS sigue evolucionando, aunque se amplía constantemente.
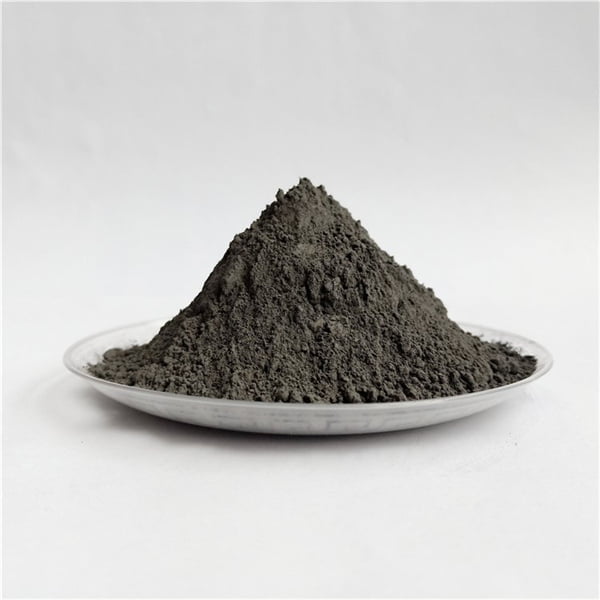
PREGUNTAS FRECUENTES
P: ¿Cuál es la diferencia entre DMLS y SLS?
R: Tanto el DMLS como el Sinterizado Láser Selectivo (SLS) son procesos de impresión 3D que utilizan un láser para crear objetos capa a capa. Sin embargo, hay una diferencia clave en los materiales que emplean. El DMLS trabaja con polvos metálicos que se funden para formar un objeto sólido. En cambio, el SLS suele utilizar polvos de plástico o nailon, sinterizando (fusionando) las partículas sin fundirlas completamente. Esta diferencia da lugar a varias variaciones clave:
- Propiedades del material: Los objetos impresos mediante DMLS suelen ser mucho más resistentes y duraderos que las piezas SLS debido a las propiedades inherentes del metal en comparación con el plástico.
- Aplicaciones: El DMLS es adecuado para crear piezas metálicas funcionales para aplicaciones aeroespaciales, de automoción y médicas. SLS destaca en la creación de prototipos y la producción de piezas de plástico con buena estética.
- Costo: El DMLS suele ser un proceso más caro que el SLS debido al mayor coste de los polvos metálicos y a la mayor complejidad de la maquinaria.
P: ¿Qué resistencia tienen las piezas impresas por DMLS?
R: La resistencia de las piezas impresas con DMLS depende del polvo metálico específico utilizado y de las técnicas de posprocesamiento empleadas. Sin embargo, las piezas de DMLS pueden ser increíblemente resistentes, alcanzando a menudo propiedades mecánicas comparables a las de sus homólogas forjadas (fabricadas tradicionalmente). Faktoren como el tratamiento térmico pueden aumentar aún más la resistencia del producto final.
P: ¿Cuáles son las opciones de acabado superficial para las piezas DMLS?
R: Las piezas impresas con DMLS suelen tener un acabado superficial algo rugoso debido a la naturaleza del proceso por capas. Sin embargo, pueden utilizarse varias técnicas de postprocesado para conseguir un acabado más liso:
- Mecanizado: Las técnicas de mecanizado tradicionales, como el fresado y el torneado, pueden utilizarse para crear un acabado superficial suave y preciso.
- Chorro de arena: Esta técnica utiliza un chorro de partículas abrasivas para alisar la superficie de la pieza.
- Pulido: El pulido mecánico o químico puede utilizarse para conseguir un acabado superficial altamente reflectante.
La elección del acabado superficial depende de la estética deseada y de los requisitos funcionales de la pieza final.
P: ¿Cuáles son las consideraciones medioambientales del DMLS?
R: El DMLS, como cualquier proceso de fabricación, tiene algunas repercusiones medioambientales. Estos son algunos factores clave que hay que tener en cuenta:
- Consumo de energía: Las máquinas DMLS requieren una cantidad significativa de energía para hacer funcionar el láser de alta potencia y mantener una atmósfera controlada.
- Residuos materiales: Dependiendo de la geometría de la pieza y del diseño de la estructura de soporte, es posible que se desperdicie algo de polvo metálico durante el proceso de DMLS. Sin embargo, algunas máquinas ofrecen la posibilidad de reciclar el polvo para minimizar los residuos.
- Emisiones: El proceso DMLS puede generar pequeñas cantidades de polvo y humos en función del material que se imprima. Unos sistemas de ventilación adecuados son cruciales para mitigar estas emisiones.
Los fabricantes se esfuerzan constantemente por mejorar la eficiencia y sostenibilidad de la tecnología DMLS. Se está investigando para desarrollar máquinas más eficientes energéticamente y minimizar la generación de residuos.
El futuro del DMLS: Un vistazo a las innovaciones del mañana
La tecnología DMLS es un campo en rápida evolución que amplía constantemente los límites de lo posible. Estas son algunas de las interesantes tendencias que configuran el futuro del DMLS:
- DMLS multimaterial: La posibilidad de imprimir objetos utilizando varios polvos metálicos en la misma construcción abre las puertas a la creación de piezas con combinaciones únicas de propiedades.
- Mayores volúmenes de construcción: En la actualidad se están desarrollando máquinas DMLS con mayores envolventes, lo que permitirá crear objetos metálicos aún más grandes y complejos.
- Mayor velocidad de impresión: Los avances en la tecnología láser y en los mecanismos de manipulación del polvo están acelerando los tiempos de impresión, lo que hace que el DMLS sea más eficaz para las aplicaciones de producción.
- Nuevos materiales: La gama de materiales compatibles con el DMLS se amplía constantemente, incluyendo nuevas aleaciones e incluso materiales exóticos como el aluminuro de titanio (TiAl).
A medida que la tecnología DMLS sigue evolucionando, tiene el potencial de revolucionar varios sectores, desde el aeroespacial y la automoción hasta la medicina, entre otros. Gracias a su capacidad para crear piezas metálicas complejas, funcionales y ligeras, el DMLS está llamado a desempeñar un papel importante en la configuración del futuro de la fabricación.
Compartir
MET3DP Technology Co., LTD es un proveedor líder de soluciones de fabricación aditiva con sede en Qingdao, China. Nuestra empresa está especializada en equipos de impresión 3D y polvos metálicos de alto rendimiento para aplicaciones industriales.
Solicite información para obtener el mejor precio y una solución personalizada para su empresa.
Artículos relacionados
Acerca de Met3DP
Actualización reciente
Nuestro producto
CONTACTO
¿Tiene alguna pregunta? ¡Envíenos un mensaje ahora! Atenderemos su solicitud con todo un equipo tras recibir su mensaje.
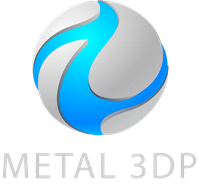
Polvos metálicos para impresión 3D y fabricación aditiva