Diferencia entre la tecnología EBM y la tecnología DMLS
Índice
Imagine construir objetos metálicos complejos capa a capa, con cada capa meticulosamente fusionada para crear una obra maestra tridimensional final. Esto no es ciencia ficción; es la magia de la fabricación aditiva de metales, también conocida como impresión 3D. Pero en este reino de la creación hay dos titanes: La fusión por haz de electrones (EBM) y el sinterizado directo de metal por láser (DMLS). Aunque ambas utilizan polvos metálicos para dar vida a diseños digitales, difieren en su enfoque, como dos artistas hábiles que manejan herramientas diferentes. Adentrémonos en la intrincada danza de estas tecnologías, exploremos sus matices e identifiquemos la opción ideal para su próximo proyecto.
Diferentes fuentes de energía
EBM aprovecha la potencia de un haz de electrones focalizado, que actúa como un acelerador de partículas en miniatura. Este haz de alta energía funde partículas de polvo metálico dentro de una cámara de alto vacío, creando un baño fundido que se fusiona con las capas circundantes. Piense en ello como un diminuto pincel sobrealimentado que funde meticulosamente el polvo metálico para construir su diseño.
Por otro lado, DMLS emplea un potente láser de fibra como fuente de calor. Este rayo láser recorre el lecho de polvo metálico, fundiendo selectivamente las partículas para formar la geometría deseada. Imagínese utilizar un cortador láser sobre una lámina de polvo metálico, pero con una precisión increíble, construyendo el objeto capa a capa.
He aquí una tabla que resume las principales diferencias entre las fuentes de energía:
Característica | Fusión por haz de electrones (EBM) | Sinterización directa de metales por láser (DMLS) |
---|---|---|
Fuente de energía | Haz de electrones | Láser de fibra de alta potencia |
Medio ambiente | Cámara de alto vacío | Atmósfera de gas inerte |
¿Qué significa esta diferencia? El entorno de alto vacío del EBM minimiza la oxidación, por lo que es ideal para metales reactivos como el titanio y el tantalio. Por el contrario, el DMLS utiliza una atmósfera de gas inerte, lo que ofrece una mayor compatibilidad con el polvo metálico.
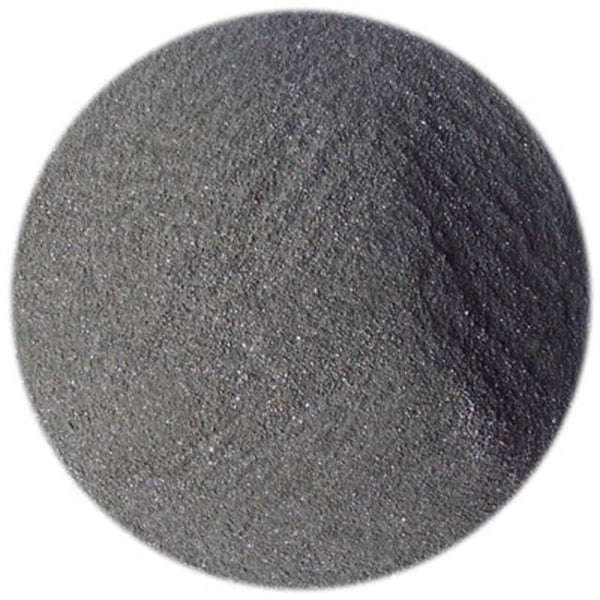
Dos producciones tienen diferente velocidad de conformado
EBM cuenta con velocidades de conformado impresionantes gracias al haz de electrones altamente concentrado y potente. Esto se traduce en tiempos de fabricación más rápidos, especialmente para componentes de mayor tamaño. Imagínese a un artista cualificado trabajando rápidamente con una herramienta potente, completando la obra de arte en un plazo de tiempo más corto.
DMLSaunque es más lento que el EBM, ofrece un control más preciso del rayo láser. Esto permite crear rasgos intrincados y detalles más finos. Piense en un paciente artista tallando meticulosamente detalles intrincados con una herramienta afilada por láser.
He aquí una tabla que resume las principales diferencias en la velocidad de conformado:
Característica | Fusión por haz de electrones (EBM) | Sinterización directa de metales por láser (DMLS) |
---|---|---|
Velocidad de conformado | Más rápido | Más lento |
Precisión de los detalles | Baja | Más alto |
¿Cuál es la conclusión? Si la velocidad es tu prioridad, EBM puede ser la mejor opción. Sin embargo, si los detalles intrincados y las características de alta precisión son primordiales, el DMLS podría ser el camino a seguir.
La precisión del moldeo es diferente
Como ya se ha dicho, DMLS destaca por su precisión de conformado gracias al control preciso del rayo láser. Esto permite la creación de piezas con características más finas y tolerancias más ajustadas. Imagine a un maestro joyero elaborando meticulosamente una delicada pieza de joyería con una precisión milimétrica.
EBMaunque no es tan preciso como el DMLS, puede producir piezas con una buena precisión dimensional. Sin embargo, debido a la naturaleza del proceso de fusión por haz de electrones, el grosor de la capa tiende a ser ligeramente mayor en comparación con el DMLS. Piense en un escultor experto que trabaja con herramientas ligeramente más grandes, lo que resulta en un producto final ligeramente menos preciso en comparación con un joyero delicado.
He aquí una tabla que resume las principales diferencias en la precisión del conformado:
Característica | Fusión por haz de electrones (EBM) | Sinterización directa de metales por láser (DMLS) |
---|---|---|
Precisión de moldeo | Bien | Excelente |
Espesor de capa | Ligeramente más grueso | Más fino |
¿En resumidas cuentas? Si la precisión dimensional y las características intrincadas son cruciales, el DMLS destaca. Sin embargo, la EBM ofrece suficiente precisión para muchas aplicaciones, sobre todo las que dan prioridad a la velocidad frente a la precisión extrema.
Materiales utilizados de EBM Y los DMLS son diferentes
Aunque ambas tecnologías utilizan polvos metálicos, los materiales específicos compatibles con cada sistema difieren ligeramente.
EBM destaca en el procesamiento de metales reactivos como:
- Titanio (Ti): Metal ligero y resistente que suele utilizarse en la industria aeroespacial, implantes médicos y componentes de alto rendimiento.
- Tántalo (Ta): Metal biocompatible y resistente a la corrosión utilizado en implantes médicos y equipos de procesamiento químico.
- Circonio (Zr): Metal resistente a la corrosión utilizado en reactores nucleares y equipos de procesamiento químico.
DMLS ofrece una gama más amplia de materiales compatibles, incluidos:
Especificaciones, tamaños, calidades y normas
Pasando de un tono conversacional a un enfoque más profesional, nos adentraremos en el crítico mundo de los polvos metálicos utilizados tanto en EBM como en DMLS. Estos materiales finamente granulares actúan como bloques de construcción de los componentes metálicos impresos en 3D, y sus características influyen significativamente en las propiedades finales de la pieza. A diferencia de lo que ocurre al hornear un pastel, donde pequeñas variaciones en la harina pueden afectar a la textura, incluso pequeñas inconsistencias en los polvos metálicos pueden afectar drásticamente a la resistencia, el acabado superficial y la calidad general del objeto impreso. A continuación se muestra una tabla completa con las principales especificaciones, tamaños, grados y normas de los polvos metálicos utilizados en la fabricación aditiva:
Característica | Descripción |
---|---|
Distribución del tamaño de las partículas | Los polvos metálicos se fabrican meticulosamente para conseguir distribuciones específicas del tamaño de las partículas, que suelen oscilar entre 15 y 100 micras. Imagine un tamiz calibrado con precisión; el tamaño de partícula elegido se correlaciona directamente con el acabado superficial alcanzable en la pieza impresa. Los polvos más finos, similares a la harina tamizada, generan superficies más lisas. Sin embargo, hay una contrapartida crucial. Los polvos excesivamente finos pueden presentar una menor fluidez, lo que dificulta su distribución uniforme durante el proceso de impresión. Esto puede dar lugar a inconsistencias y defectos en el producto final. Por el contrario, los polvos más gruesos pueden fluir más fácilmente, pero pueden dar lugar a un acabado superficial más rugoso y a una posible porosidad (pequeños espacios de aire) en el componente impreso. La selección de la distribución óptima del tamaño de partícula requiere una cuidadosa consideración de la aplicación específica y del resultado deseado. |
Morfología de las partículas | La forma de las partículas de polvo desempeña un papel fundamental en la densidad de empaquetamiento y la fluidez. Las partículas esféricas, parecidas a rodamientos de bolas microscópicos, suelen ser las preferidas para obtener un rendimiento de impresión óptimo. Presentan unas características de fluidez superiores, se empaquetan firmemente y minimizan los huecos en el lecho de polvo. Esto se traduce en una mayor precisión dimensional, mejores propiedades mecánicas y un acabado superficial más liso en la pieza impresa. Sin embargo, producir polvos metálicos perfectamente esféricos puede resultar difícil y caro. Las partículas equiaxiales, aunque no son esferas perfectas, ofrecen un buen equilibrio entre fluidez y densidad de empaquetamiento. Las partículas de forma irregular pueden ser problemáticas. Pueden fluir mal, crear huecos en el lecho de polvo y afectar negativamente a la integridad estructural del producto final. |
Química de polvos | La composición exacta del polvo, incluidos los oligoelementos y las adiciones de aleación, influye significativamente en las propiedades finales de la pieza impresa. Al igual que los ingredientes exactos de una fórmula farmacéutica determinan su eficacia, la composición química del polvo metálico dicta las características del componente impreso. Por ejemplo, el polvo de titanio para aplicaciones aeroespaciales puede tener niveles ligeramente diferentes de oxígeno y nitrógeno en comparación con el polvo de titanio de grado médico para implantes. Estas variaciones aparentemente menores pueden influir en factores como la fuerza, la resistencia a la corrosión, la biocompatibilidad y el rendimiento general de la pieza impresa. Los fabricantes de polvo metálico emplean rigurosas medidas de control de calidad para garantizar que sus polvos cumplen las normas específicas del sector y los requisitos de las aplicaciones. |
Fluidez del polvo | La capacidad del polvo para fluir libremente es crucial para una distribución uniforme durante el proceso de impresión. Imagínese verter arena para un reloj de arena; debe fluir suave y uniformemente. Una buena fluidez permite la formación de un lecho de polvo uniforme, un paso crítico tanto en EBM como en DMLS. Los polvos con poca fluidez pueden provocar una deposición desigual, lo que da lugar a incoherencias y defectos en la pieza impresa final. Los fabricantes miden la fluidez mediante pruebas estandarizadas para garantizar que sus polvos cumplen los requisitos específicos de cada tecnología de impresión. |
Pureza del polvo | La pureza del polvo metálico afecta directamente a las propiedades mecánicas y al rendimiento de la pieza impresa. Impurezas como el oxígeno, el nitrógeno y otros elementos pueden dificultar el proceso de unión entre las partículas metálicas durante la impresión. Esto puede dar lugar a piezas más débiles con mayor susceptibilidad a grietas y fracturas. Los fabricantes de polvo metálico emplean estrictas medidas de control de calidad para minimizar las impurezas y garantizar que sus polvos cumplen las normas de pureza requeridas para diversas aplicaciones. |
Normas industriales para polvos metálicos en la fabricación aditiva:
Varias normas industriales establecidas rigen las especificaciones y la calidad de los polvos metálicos para la fabricación aditiva:
- ASTM Internacional (ASTM): Organización mundialmente reconocida que desarrolla y publica normas técnicas para una amplia gama de materiales, incluidos los polvos metálicos para AM. Las normas ASTM definen los requisitos para la distribución del tamaño de las partículas, la composición química, la fluidez y otros parámetros críticos.
- Sociedad Americana de Materiales y Pruebas (AMSTM): Sociedad estadounidense dedicada al avance de los ensayos, la ciencia de los materiales y tecnologías como la fabricación aditiva. AMSTM elabora especificaciones y normas para los polvos metálicos utilizados en los procesos de AM.
- EOS GmbH: Uno de los principales fabricantes de sistemas de impresión 3D en metal. EOS también publica hojas de datos de materiales para aplicaciones específicas de diversos polvos metálicos, en las que se describen sus propiedades y los parámetros de impresión recomendados.
- Fabricantes de materiales: Los proveedores de polvo metálico de renombre suelen proporcionar fichas técnicas detalladas de sus productos, que incluyen la distribución granulométrica, la composición química, la fluidez y otras especificaciones relevantes.
Un mundo de polvos metálicos: Ejemplos concretos
Ahora que hemos explorado las características clave de los polvos metálicos para la fabricación aditiva, vamos a profundizar en algunos ejemplos concretos que se utilizan habitualmente en ambos procesos EBM y DMLS. Se ofrecerá una perspectiva práctica de las opciones disponibles y su idoneidad para diversas aplicaciones.
Polvos metálicos para EBM:
Debido al entorno de alto vacío dentro de la cámara de EBM, los polvos metálicos elegidos deben presentar unas propiedades de desgasificación excepcionales. La desgasificación se refiere a la liberación de gases atrapados en las partículas de polvo durante el proceso de fusión. Una desgasificación excesiva puede alterar el entorno de vacío y afectar negativamente a la calidad de la pieza impresa. Estos son algunos de los polvos metálicos más utilizados en EBM:
- Polvo de titanio atomizado por gas (Ti-6Al-4V): Este material de trabajo es una aleación de titanio que contiene aluminio 6% y vanadio 4%. Ofrece una excelente combinación de resistencia, ligereza y resistencia a la corrosión. Ampliamente utilizado en la industria aeroespacial, implantes médicos y componentes de automoción de alto rendimiento debido a su biocompatibilidad y propiedades mecánicas favorables cuando se procesa mediante EBM.
- Inconel 718 atomizado con gas: Esta superaleación a base de níquel-cromo presenta una excepcional resistencia a altas temperaturas y a entornos agresivos. Su capacidad para soportar temperaturas extremas la hace ideal para aplicaciones en motores de turbinas de gas, intercambiadores de calor y otros componentes expuestos a altas cargas térmicas. El procesamiento EBM ofrece un riesgo mínimo de contaminación, preservando las propiedades deseables de Inconel 718.
- Cobre atomizado con gas (Cu): El polvo de cobre puro se utiliza en aplicaciones que requieren una alta conductividad térmica y eléctrica. La EBM permite crear complejos disipadores de calor y componentes eléctricos con una oxidación mínima debido al entorno de vacío.
Polvos metálicos para DMLS:
El DMLS ofrece una mayor compatibilidad de materiales en comparación con el EBM debido a la atmósfera de gas inerte. Estos son algunos de los polvos metálicos más utilizados en DMLS:
- Acero inoxidable 316L atomizado con gas: Este versátil grado de acero inoxidable ofrece una excelente resistencia a la corrosión y biocompatibilidad. Muy utilizado en implantes médicos, equipos de procesamiento químico y aplicaciones que requieren resistencia a entornos agresivos. El procesamiento DMLS permite crear geometrías intrincadas con buenas propiedades mecánicas.
- Aleaciones de aluminio atomizadas con gas (AlSi10Mg, etc.): Las aleaciones de aluminio ofrecen un buen equilibrio entre resistencia, ahorro de peso y asequibilidad. La adición de silicio (Si) y magnesio (Mg) mejora las características de fundición y las propiedades mecánicas. Se utilizan habitualmente en aplicaciones aeroespaciales, de automoción y de electrónica de consumo debido a su ligereza. El procesamiento DMLS permite crear componentes complejos y ligeros con un buen acabado superficial.
- Acero para herramientas atomizado con gas (H13, etc.): Los aceros para herramientas son conocidos por su excepcional resistencia al desgaste y dureza. El H13 es una opción popular para moldes y matrices debido a su capacidad para soportar altas temperaturas y tensiones mecánicas. El procesamiento DMLS permite crear insertos de herramientas complejos con una buena precisión dimensional.
He aquí una tabla que resume algunas características clave de estos polvos metálicos:
Polvo metálico | Aplicaciones típicas (EBM) | Aplicaciones típicas (DMLS) | Consideraciones clave |
---|---|---|---|
Ti-6Al-4V atomizado con gas | Aeroespacial, Implantes médicos | Aeroespacial, Implantes médicos | Excelente relación resistencia/peso, biocompatible |
Inconel 718 atomizado con gas | Motores de turbina de gas, intercambiadores de calor | Motores de turbina de gas, intercambiadores de calor | Resistencia a altas temperaturas y a entornos agresivos |
Cobre atomizado con gas (Cu) | Disipadores de calor, componentes eléctricos | Disipadores de calor, componentes eléctricos | Alta conductividad térmica y eléctrica |
Acero inoxidable 316L atomizado con gas | Implantes médicos, procesamiento químico | Implantes médicos, procesamiento químico | Resistencia a la corrosión, biocompatible |
Aleaciones de aluminio atomizadas con gas (AlSi10Mg) | Aeroespacial, automoción, electrónica de consumo | Aeroespacial, automoción, electrónica de consumo | Ligero, buena relación resistencia/peso |
Acero para herramientas atomizado con gas (H13) | Moldes y matrices | Moldes y matrices | Excepcional resistencia al desgaste, dureza |
Recuerde que no se trata de una lista exhaustiva. Los fabricantes ofrecen una amplia selección de polvos metálicos para la fabricación aditiva, cada uno con propiedades y certificaciones únicas. Para seleccionar el material más adecuado para su proyecto de impresión 3D, es fundamental consultar a proveedores de polvo metálico de confianza y conocer los requisitos específicos de su aplicación.
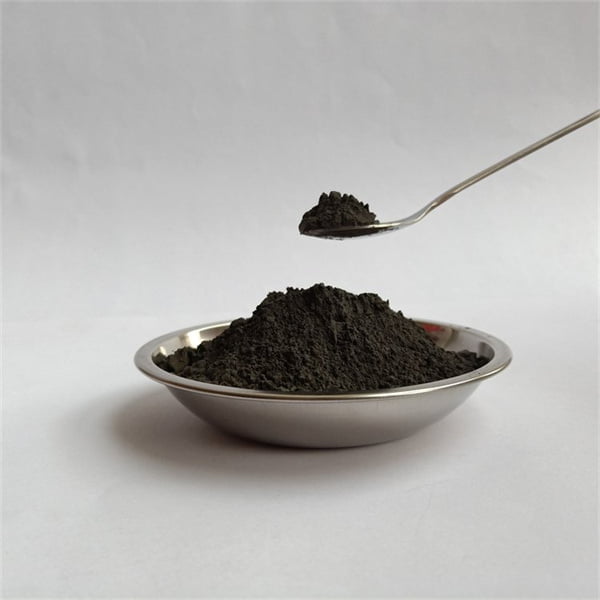
Comparación de EBM y DMLS
Una vez exploradas las complejidades de las tecnologías EBM y DMLS, junto con el mundo de los polvos metálicos utilizados en cada proceso, ha llegado el momento de comparar directamente estos dos titanes de la impresión 3D. Esto le ayudará a tomar una decisión informada basada en las necesidades específicas de su proyecto.
He aquí una tabla que resume las principales diferencias entre EBM y DMLS:
Característica | Fusión por haz de electrones (EBM) | Sinterización directa de metales por láser (DMLS) |
---|---|---|
Fuente de energía | Haz de electrones | Láser de fibra de alta potencia |
Medio ambiente | Cámara de alto vacío | Atmósfera de gas inerte |
Velocidad de conformado | Más rápido | Más lento |
Precisión de moldeo | Bien | Excelente |
Compatibilidad de materiales | Limited (Metales reactivos) | Gama más amplia de materiales |
Acabado superficial | Ligeramente más áspero | Más suave |
Porosidad | Baja | Potencialmente superior |
Pros | Tiempos de construcción más rápidos, bueno para metales reactivos, mínima oxidación | Mayor precisión, mayor compatibilidad de materiales, buen acabado superficial |
Contras | Menor precisión, opciones de material limitadas, mayor consumo de energía | Tiempos de fabricación más lentos, posibilidad de mayor porosidad, algunos materiales pueden requerir tratamiento posterior. |
Profundicemos en estas diferencias clave para entender qué tecnología puede encajar mejor en su proyecto:
- Velocidad de construcción: Si la velocidad es un factor crítico, la EBM puede ser la mejor opción. Su haz de electrones de alta potencia permite una fusión más rápida y tiempos de fabricación más cortos, especialmente para componentes más grandes. Sin embargo, si los detalles intrincados y la precisión dimensional son primordiales, el DMLS puede ser una mejor opción, aunque se tarde un poco más en imprimir.
- Compatibilidad de materiales: La EBM destaca en el procesamiento de metales reactivos como el titanio y el tantalio debido al entorno de alto vacío que minimiza la oxidación. El DMLS, por su parte, ofrece una gama más amplia de compatibilidad de materiales, como el acero inoxidable, las aleaciones de aluminio y los aceros para herramientas. Esta selección más amplia permite una mayor flexibilidad de diseño en DMLS.
- Precisión de las piezas y acabado superficial: El DMLS reina en términos de precisión de conformado y acabado superficial. El control preciso del rayo láser permite crear piezas muy detalladas con un acabado superficial suave. El EBM ofrece una buena precisión, pero la naturaleza del proceso de fusión por haz de electrones puede dar lugar a un acabado superficial ligeramente más rugoso en comparación con el DMLS.
- Porosidad: La porosidad se refiere a pequeños espacios de aire dentro del metal impreso. La EBM suele producir piezas con menor porosidad debido al entorno de alto vacío, que minimiza la presencia de gases atrapados. El DMLS, aunque ofrece una buena calidad general, puede tener una probabilidad ligeramente superior de porosidad, sobre todo cuando se utilizan determinados materiales o parámetros de impresión. En algunos casos, las piezas de DMLS pueden requerir técnicas de postprocesado como el prensado isostático en caliente (HIP) para eliminar los huecos internos.
- Consideraciones de costos: El coste de la impresión 3D de una pieza metálica mediante EBM o DMLS depende de varios factores, como el material elegido, la complejidad de la pieza y el posprocesamiento necesario. Sin embargo, en general, la EBM puede tener un mayor consumo de energía debido a la necesidad de un entorno de alto vacío. El DMLS puede ser una opción más rentable para algunas aplicaciones, especialmente si se tiene en cuenta la posible necesidad de postprocesado con EBM.
Elegir el arma adecuada: EBM frente a DMLS - El veredicto final
No hay un único "ganador" en la batalla entre EBM y DMLS. La tecnología ideal depende de las necesidades específicas de su proyecto. He aquí algunas reflexiones finales para orientarle en su decisión:
- Para proyectos que requieran la impresión a alta velocidad de metales reactivos como el titanio, y en los que se acepte un acabado superficial ligeramente más rugoso, la EBM puede ser una buena opción.
- Para proyectos que exigen detalles intrincados, una precisión dimensional excepcional, una gama más amplia de opciones de materiales y un acabado superficial liso, el DMLS puede ser la mejor opción, aunque se tarde un poco más en imprimir.
- Considere detenidamente las implicaciones económicas de cada tecnología, incluido el coste de los materiales, el consumo de energía y las posibles necesidades de tratamiento posterior.
Siempre es aconsejable consultar con profesionales experimentados en impresión 3D para analizar los requisitos específicos de su proyecto y determinar qué tecnología, EBM o DMLS, sería la opción más adecuada para obtener resultados óptimos.
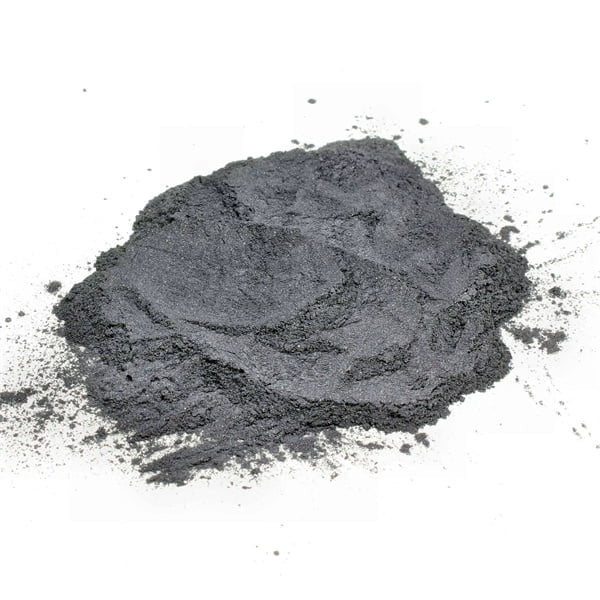
PREGUNTAS FRECUENTES
P: ¿Qué tecnología es más potente, EBM o DMLS?
R: Tanto el EBM como el DMLS pueden producir piezas metálicas de alta resistencia. La resistencia real depende del polvo metálico elegido y de los parámetros de impresión específicos utilizados. Sin embargo, debido al entorno de alto vacío y a una porosidad potencialmente menor, las piezas impresas con EBM pueden presentar una resistencia ligeramente superior en el caso de determinados metales reactivos, como el titanio.
P: ¿Puedo utilizar EBM o DMLS para imprimir piezas metálicas coloreadas?
R: Aunque tanto la EBM como el DMLS se centran principalmente en la creación de piezas metálicas funcionales, existen algunas técnicas limitadas de postprocesado que pueden introducir color en la superficie. Estas técnicas suelen implicar la aplicación de una fina capa de revestimiento coloreado o la infiltración con una resina coloreada. Sin embargo, conseguir colores vibrantes o uniformes puede ser complicado, y la durabilidad a largo plazo de estas aplicaciones de color puede ser limitada. Si el color es un requisito fundamental, otras tecnologías de impresión 3D como el chorro de aglutinante o la fusión multichorro podrían ser más adecuadas, ya que ofrecen una gama más amplia de opciones de color directamente en el proceso de impresión.
P: ¿Son respetuosas con el medio ambiente las piezas impresas con EBM o DMLS?
R: El impacto medioambiental de la EBM y el DMLS depende de varios factores, como el polvo metálico elegido, el consumo de energía durante el proceso de impresión y los pasos de posprocesamiento necesarios. La producción de polvo metálico en sí puede consumir mucha energía. La EBM, debido a su entorno de alto vacío, puede tener una huella energética ligeramente superior a la del DMLS. Sin embargo, ambas tecnologías ofrecen ventajas significativas en términos de complejidad de las piezas y uso de materiales en comparación con las técnicas tradicionales de fabricación sustractiva, como el mecanizado. Esto puede suponer menos residuos de material y, potencialmente, un enfoque de fabricación más sostenible para determinadas aplicaciones.
P: ¿Cuáles son los futuros avances previstos en las tecnologías EBM y DMLS?
R: El ámbito de EBM y DMLS está en constante evolución. He aquí algunas posibilidades interesantes en el horizonte:
- Mayor velocidad de impresión: Los investigadores están desarrollando técnicas para aumentar la velocidad de EBM y DMLS sin comprometer la calidad de las piezas. Esto podría implicar avances en la tecnología de fuentes de energía o mecanismos mejorados de manipulación del polvo.
- Mayor compatibilidad de materiales: Se espera que aumente la gama de metales aptos para la impresión EBM y DMLS. Esto ofrecería a los diseñadores una flexibilidad aún mayor a la hora de seleccionar el material óptimo para sus necesidades específicas.
- Impresión multimaterial: Se están estudiando técnicas que permitan imprimir piezas con distintos metales o incluso combinaciones de metal y otros materiales en una misma construcción. Esto podría abrir las puertas a la creación de componentes altamente funcionales y complejos.
- Mejora del acabado superficial: Los avances en la tecnología de control del láser y el haz de electrones podrían dar lugar a acabados superficiales aún más suaves para las piezas impresas con DMLS, lo que podría reducir la necesidad de postprocesado en algunas aplicaciones.
A medida que estas tecnologías innovadoras sigan desarrollándose, la EBM y el DMLS están preparados para desempeñar un papel cada vez más importante en la revolución de la forma en que diseñamos y fabricamos piezas metálicas en diversos sectores.
Conclusión
La intrincada danza entre las tecnologías EBM y DMLS ofrece un potente conjunto de herramientas para crear objetos metálicos complejos y funcionales. La comprensión de los puntos fuertes y débiles de cada enfoque, junto con el vasto mundo de los polvos metálicos utilizados como bloques de construcción, le permite tomar decisiones informadas para sus proyectos de impresión 3D. Tanto si da prioridad a la velocidad de los metales reactivos con EBM como si busca detalles excepcionales y una mayor selección de materiales con DMLS, ambas tecnologías amplían los límites de lo que es posible en la fabricación de metales. A medida que estas tecnologías sigan evolucionando, el futuro nos deparará un inmenso potencial de mayor libertad de diseño, innovación de materiales y un enfoque más sostenible de la creación de piezas metálicas.
Compartir
MET3DP Technology Co., LTD es un proveedor líder de soluciones de fabricación aditiva con sede en Qingdao, China. Nuestra empresa está especializada en equipos de impresión 3D y polvos metálicos de alto rendimiento para aplicaciones industriales.
Solicite información para obtener el mejor precio y una solución personalizada para su empresa.
Artículos relacionados
Acerca de Met3DP
Actualización reciente
Nuestro producto
CONTACTO
¿Tiene alguna pregunta? ¡Envíenos un mensaje ahora! Atenderemos su solicitud con todo un equipo tras recibir su mensaje.
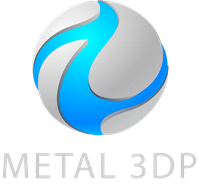
Polvos metálicos para impresión 3D y fabricación aditiva