High-Temperature Exhaust Nozzles via 3D Printing
Índice
Introduction – The Critical Role of High-Temperature Exhaust Nozzles
In demanding industries like aerospace, power generation, and high-performance automotive, turbine exhaust nozzles stand as critical components. These intricate parts are responsible for directing the high-velocity, high-temperature gases expelled from the turbine, playing a crucial role in the efficiency and performance of the overall system. The extreme operating conditions – intense heat, corrosive environments, and significant mechanical stresses – demand materials and manufacturing processes capable of withstanding these challenges. Metal Impresión 3D, also known as metal additive manufacturing, has emerged as a transformative technology for producing these complex geometries with enhanced material properties, offering a compelling alternative to traditional manufacturing methods. At https://met3dp.com/, we are at the forefront of this revolution, providing advanced metal 3D printing solutions tailored to the stringent requirements of high-temperature applications.
What are High-Temperature Exhaust Nozzles Used For?
High-temperature exhaust nozzles are integral to various systems where the efficient and controlled release of hot gases is paramount. Their primary functions include:
- Directing Exhaust Flow: Precisely channeling the hot gases to generate thrust in jet engines or to efficiently expel them in power turbines.
- Optimizing Performance: The nozzle’s design significantly impacts the efficiency of the turbine by influencing the expansion and velocity of the exhaust gases.
- Managing Back Pressure: Properly designed nozzles help regulate the pressure within the turbine, ensuring optimal operating conditions.
- Reducing Noise and Emissions: Advanced nozzle designs can incorporate features to mitigate noise pollution and control exhaust emissions.
These critical components find widespread application across several key industries:
- Aeroespacial: In jet engines for commercial and military aircraft, as well as in rocket propulsion systems, where extreme temperature resistance and lightweighting are crucial.
- Generación de energía: In gas turbines used in power plants, where efficiency and durability under high thermal loads are essential for reliable energy production.
- Automóvil: In high-performance vehicles and racing applications, where managing exhaust flow and temperature is vital for engine performance and longevity.
- Fabricación industrial: In specialized machinery and processes that involve high-temperature gas expulsion.
The complex geometries often required for optimized performance, coupled with the demanding material requirements, make the manufacturing of these nozzles a significant engineering challenge.
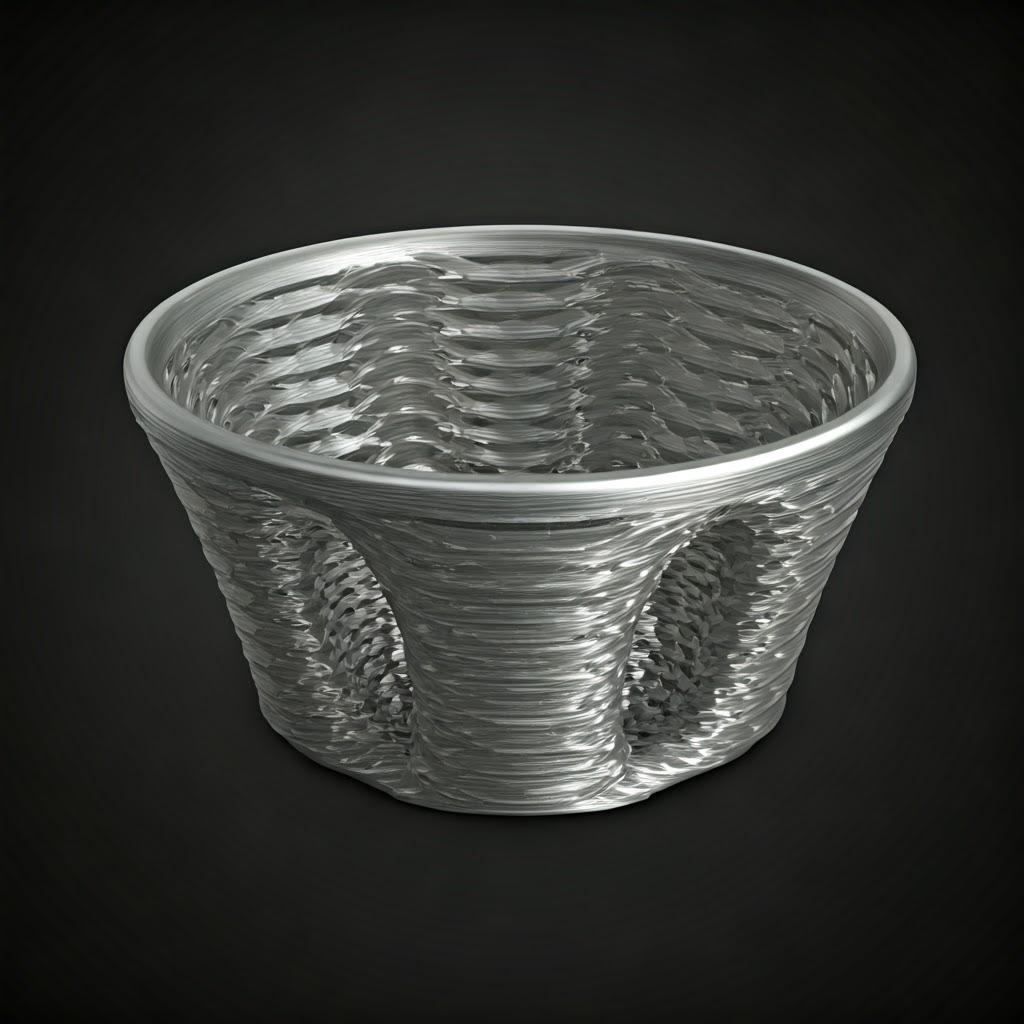
Why Use Metal 3D Printing for High-Temperature Exhaust Nozzles?
Opting for metal 3D printing for the production of high-temperature exhaust nozzles offers a multitude of advantages over conventional manufacturing techniques:
- Libertad de diseño y complejidad: Additive manufacturing allows for the creation of intricate internal channels, complex curves, and optimized aerodynamic designs that are difficult or impossible to achieve with traditional methods like casting or machining. This design flexibility can lead to improved performance and efficiency of the nozzle.
- Optimización de materiales: Metal 3D printing enables the use of high-performance alloys specifically tailored for extreme temperatures, such as IN718 and Haynes 282. These materials exhibit exceptional high-temperature strength, creep resistance, and oxidation resistance, crucial for the longevity of exhaust nozzles. Metal3DP fabrica una amplia gama de polvos metálicos de alta calidad. optimized for such demanding applications.
- Reducción de los residuos materiales: Unlike subtractive manufacturing processes that remove material from a solid block, 3D printing builds parts layer by layer, significantly reducing material waste and associated costs.
- Prototipos y producción más rápidos: Metal 3D printing can drastically shorten lead times for both prototypes and production parts, allowing for quicker design iterations and faster deployment.
- Personalización y fabricación bajo demanda: Additive manufacturing is ideal for producing customized nozzle designs or small batch quantities efficiently, catering to specific application requirements without the need for expensive tooling.
- Enhanced Performance through Integrated Features: 3D printing allows for the integration of features like cooling channels directly into the nozzle structure, improving thermal management and extending the component’s lifespan. Metal3DP’s Sistema avanzado de fabricación de polvo ensures the quality and consistency of powders needed for such intricate builds.
Recommended Materials and Why They Matter
For high-temperature exhaust nozzles, the choice of material is paramount to ensure structural integrity and performance under extreme conditions. Two exemplary materials well-suited for this application in metal 3D printing are IN718 and Haynes 282:
IN718 (Inconel 718)
IN718 is a nickel-chromium-based superalloy renowned for its exceptional high-temperature strength, corrosion resistance, and weldability. Its key properties make it an excellent choice for exhaust nozzles:
- Alta resistencia a temperaturas elevadas: IN718 maintains significant mechanical strength even at temperatures up to 700°C (1300°F), crucial for withstanding the hot exhaust gases.
- Excellent Creep and Stress-Rupture Properties: This alloy exhibits high resistance to deformation under constant load at high temperatures, ensuring the nozzle maintains its shape and functionality over extended periods.
- Superior Corrosion and Oxidation Resistance: IN718 can withstand harsh environments, including exposure to combustion byproducts and oxidizing atmospheres, contributing to the nozzle’s durability.
- Buena soldabilidad: While often 3D printed, the good weldability of IN718 is beneficial for potential post-processing or integration with other components.
Chemical Composition of IN718 (Typical)
Elemento | Weight (%) |
---|---|
Níquel (Ni) | 50-55 |
Cromo (Cr) | 17-21 |
Hierro (Fe) | Saldo |
Molibdeno (Mo) | 2.8-3.3 |
Niobio (Nb) | 4.75-5.5 |
Aluminio (Al) | 0.2-0.8 |
Titanio (Ti) | 0.65-1.15 |
Silicio (Si) | ≤ 0.35 |
Manganeso (Mn) | ≤ 0.35 |
Carbono (C) | ≤ 0.08 |
Exportar a hojas
Haynes 282
Haynes 282 is a gamma-prime strengthened nickel-chromium-cobalt superalloy specifically developed for high-temperature structural applications. It offers a superior balance of properties for demanding exhaust nozzle environments:
- Resistencia excepcional a la fluencia: Haynes 282 exhibits outstanding creep resistance in the temperature range of 649 to 927°C (1200 to 1700°F), surpassing many other superalloys.
- Excelente estabilidad térmica: The alloy maintains its microstructure and mechanical properties after prolonged exposure to high temperatures.
- Good Weldability and Fabricability: Similar to IN718, Haynes 282 offers good processing characteristics, which is advantageous for complex 3D printed parts.
- High Oxidation Resistance: It provides excellent resistance to oxidation at elevated temperatures, crucial for maintaining the integrity of the exhaust nozzle.
Chemical Composition of Haynes 282 (Typical)
Elemento | Weight (%) |
---|---|
Níquel (Ni) | Saldo |
Cromo (Cr) | 19.0-21.0 |
Cobalto (Co) | 9.0-11.0 |
Molibdeno (Mo) | 7.5-9.5 |
Aluminio (Al) | 1.0-2.0 |
Titanio (Ti) | 1.5-2.5 |
Hierro (Fe) | ≤ 2.0 |
Manganeso (Mn) | ≤ 0.3 |
Silicio (Si) | ≤ 0.15 |
Carbono (C) | ≤ 0.05 |
Boro (B) | ≤ 0.006 |
Exportar a hojas
The selection of either IN718 or Haynes 282 depends on the specific performance requirements and operating conditions of the turbine exhaust nozzle. Both alloys, available as high-quality powders from Metal3DP, are excellent candidates for producing durable and high-performing components through metal 3D printing. Our expertise at Metal3DP ensures that customers can leverage the unique advantages of these materials for their critical applications.
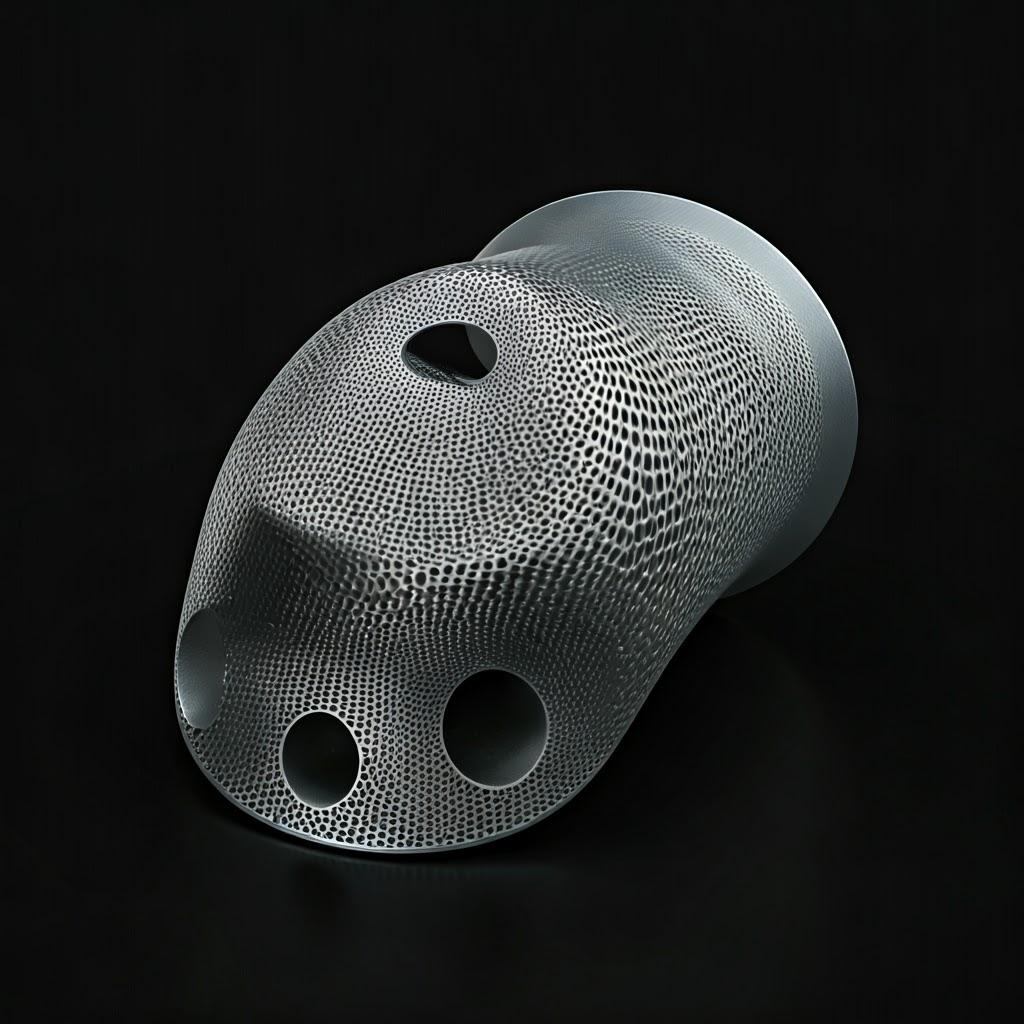
Design Considerations for Additive Manufacturing of Exhaust Nozzles
Optimizing the design of high-temperature exhaust nozzles for metal 3D printing is crucial to fully leverage the technology’s capabilities and ensure the final part meets performance requirements. Several key design considerations come into play:
- Optimización de la topología: Utilizing specialized software to analyze stress distribution and material usage can lead to lightweight yet structurally robust designs. By strategically removing material from low-stress areas, the weight of the nozzle can be significantly reduced, which is particularly beneficial in aerospace applications.
- Estructuras reticulares: Incorporating lattice structures within the nozzle walls or internal features can provide high strength-to-weight ratios and enhance heat dissipation. These intricate internal geometries are often only achievable through additive manufacturing.
- Canales de refrigeración internos: Designing complex internal cooling channels allows for efficient thermal management of the exhaust nozzle. These channels can be tailored to the specific heat flux areas, improving the component’s lifespan and performance under extreme temperatures. Metal 3D printing offers the freedom to create intricate and conformal cooling pathways.
- Wall Thickness and Support Structures: Careful consideration of wall thickness is essential to balance structural integrity and build time. Appropriate support structures are necessary to prevent warping or collapse during the printing process, especially for overhanging features. The design should aim to minimize the need for extensive support structures to reduce post-processing effort and material waste.
- Orientación de las características: The orientation of the part during printing can significantly impact surface finish, mechanical properties, and the need for support structures. Optimizing the build orientation can lead to improved part quality and reduced post-processing.
- Minimización de las concentraciones de tensión: Sharp corners and abrupt transitions can lead to stress concentrations under high thermal and mechanical loads. Designing smooth contours and gradual transitions is crucial for the longevity of the exhaust nozzle.
- Assembly Integration: Metal 3D printing allows for the consolidation of multiple components into a single part, reducing the need for assembly and potential weak points. Complex exhaust nozzle designs with integrated flanges or mounting features can be realized.
- Consideraciones sobre el acabado de la superficie: The as-printed surface finish may not always meet the requirements for optimal gas flow or sealing. Designing with consideration for necessary post-processing steps, such as polishing or machining, is important.
By carefully considering these design aspects, engineers can harness the full potential of metal 3D printing to create high-performance, durable, and lightweight exhaust nozzles tailored to demanding applications. Our team at Metal3DP possesses extensive expertise in design for additive manufacturing and can assist customers in optimizing their designs for our advanced printing processes.
Tolerancia, acabado superficial y precisión dimensional
Achieving the required tolerance, surface finish, and dimensional accuracy is paramount for the functional performance and integration of high-temperature exhaust nozzles. Metal 3D printing technologies have made significant strides in these areas:
- Capacidades de tolerancia: The achievable tolerances in metal 3D printing depend on the specific technology (e.g., Selective Laser Melting (SLM), Electron Beam Melting (EBM)), the material used, and the part geometry. Typically, tolerances in the range of ±0.1 to ±0.5 mm can be achieved for critical dimensions. Precision machining as a post-processing step can further refine tolerances to meet tighter specifications where necessary.
- Acabado superficial: The as-printed surface finish in metal 3D printing is generally rougher compared to machined surfaces. The surface roughness (Ra) typically ranges from 5 to 20 µm, depending on the printing parameters and material. For applications requiring smoother surfaces to minimize flow resistance or improve sealing, post-processing techniques like polishing, abrasive blasting, or chemical etching can be employed.
- Precisión dimensional: Dimensional accuracy refers to the ability of the 3D printing process to produce parts that closely match the intended design dimensions. Factors influencing dimensional accuracy include material shrinkage during solidification, thermal gradients, and the calibration of the printer. With careful process control and optimized build parameters, high levels of dimensional accuracy can be achieved.
Factors Affecting Tolerance and Accuracy in Metal 3D Printing:
Factor | Descripción | Impact on Tolerance/Accuracy |
---|---|---|
Tecnología de impresión | SLM generally offers finer details and tighter tolerances compared to EBM. | Significativo |
Material | Different materials exhibit varying levels of shrinkage and thermal expansion, affecting final dimensions. | Moderado |
Orientación de la construcción | Part orientation can influence thermal gradients and support structure interaction, impacting accuracy. | Moderado |
Altura de la capa | Thinner layers generally result in better surface finish and potentially higher accuracy. | Moderado |
Parámetros del proceso | Laser power, scan speed, and powder feed rate all influence the melting and solidification process. | Significativo |
Tratamiento posterior | Techniques like stress relieving, heat treatment, and machining can affect final dimensions and tolerances. | Significativo |
Printer Calibration | Accurate calibration of the 3D printer is crucial for consistent and accurate results. | Significativo |
Exportar a hojas
At Metal3DP, we employ advanced metal 3D printing equipment and rigorous process control to achieve high levels of tolerance and dimensional accuracy for our customers’ exhaust nozzle applications. We also offer a range of post-processing services to meet specific surface finish requirements.
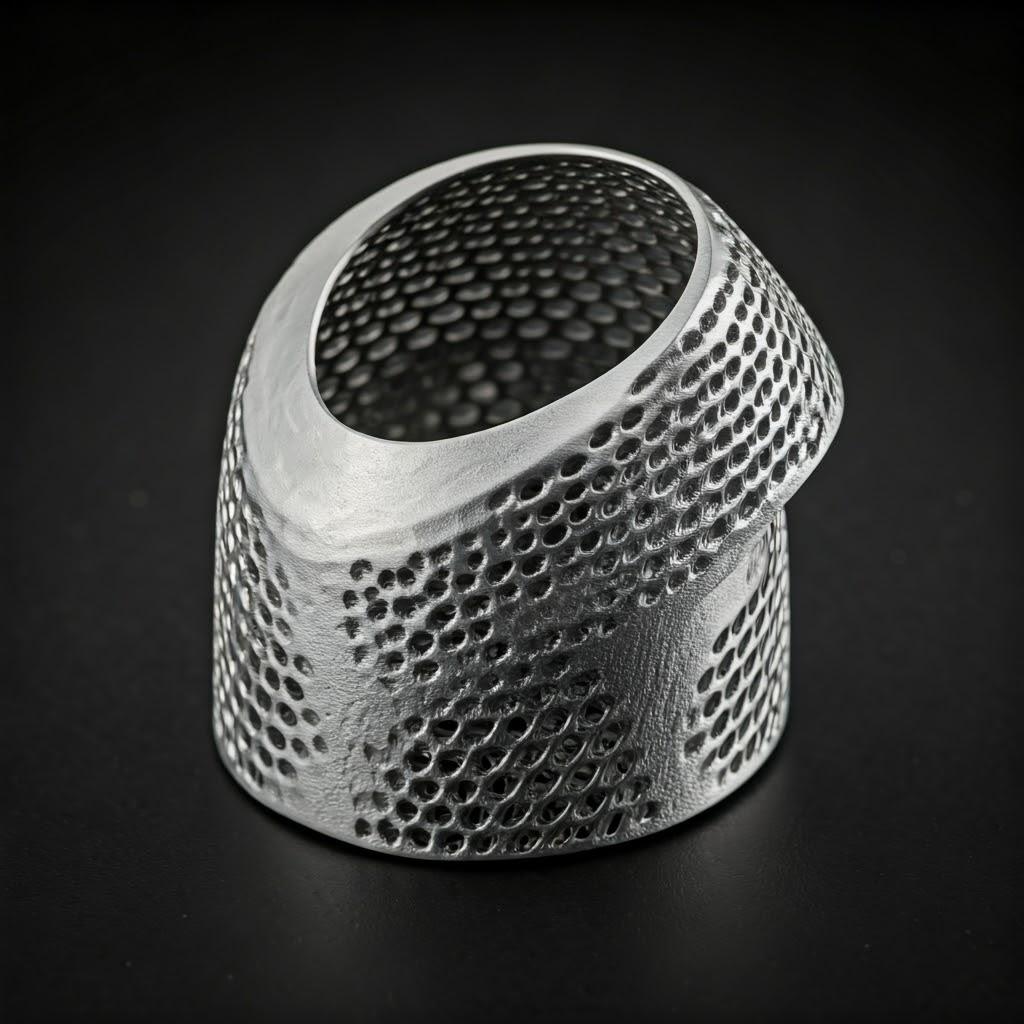
Post-Processing Requirements for 3D Printed Exhaust Nozzles
While metal 3D printing offers significant advantages, post-processing steps are often necessary to achieve the final desired properties and surface finish for high-temperature exhaust nozzles:
- Retirada de la estructura de soporte: Support structures are often required during the printing process to prevent part deformation. These structures need to be carefully removed, which can involve manual breaking, cutting, or machining. The design of the part should aim to minimize the complexity and volume of support structures.
- Alivia el estrés: Residual stresses can build up during the rapid heating and cooling cycles of the 3D printing process. Stress relieving heat treatment is often performed to reduce these internal stresses and improve the mechanical properties and dimensional stability of the part.
- Prensado isostático en caliente (HIP): HIP is a process that applies high pressure and temperature to the printed part, reducing internal porosity and improving density, which is crucial for high-performance applications like exhaust nozzles operating under extreme conditions.
- Tratamiento térmico: Specific heat treatment cycles are often required to achieve the desired microstructure and mechanical properties of the chosen metal alloy (e.g., age hardening for IN718 or Haynes 282). The specific heat treatment protocol is tailored to the material and application requirements.
- Acabado superficial: As mentioned earlier, post-processing techniques like polishing, abrasive blasting, or machining may be necessary to achieve the required surface finish for optimal gas flow and sealing. CNC machining can also be used to achieve tighter tolerances on critical dimensions.
- Inspección y control de calidad: Thorough inspection using techniques like coordinate measuring machines (CMM), non-destructive testing (NDT) such as dye penetrant inspection or ultrasonic testing, is essential to ensure the printed exhaust nozzle meets the required quality standards and dimensional accuracy.
- Revestimiento (opcional): In some cases, protective coatings may be applied to enhance the corrosion or oxidation resistance of the exhaust nozzle, further extending its service life in harsh operating environments.
The specific post-processing requirements depend on the application, the chosen material, and the desired final properties of the high-temperature exhaust nozzle. At Metal3DP, we offer comprehensive post-processing services to ensure that our 3D printed parts meet the most demanding specifications.
Common Challenges and How to Avoid Them in 3D Printing Exhaust Nozzles
While metal 3D printing offers numerous benefits, several challenges can arise during the production of complex parts like high-temperature exhaust nozzles. Understanding these challenges and implementing appropriate strategies to mitigate them is crucial for successful outcomes:
- Deformación y distorsión: Thermal stresses during the printing process can lead to warping or distortion of the part, especially for large or complex geometries.
- Avoidance: Optimize part orientation, use appropriate support structures, employ stress-relieving heat treatments, and carefully control the build parameters.
- Dificultades para retirar la estructura de soporte: Intricate support structures can be challenging and time-consuming to remove, potentially damaging the part’s surface.
- Avoidance: Design parts with self-supporting features where possible, optimize support structure design for easier removal, and utilize dissolvable support materials if compatible with the chosen metal.
- Porosity and Density Issues: Insufficient melting or solidification can lead to internal porosity, reducing the mechanical strength and fatigue life of the nozzle.
- Avoidance: Optimize printing parameters such as laser power, scan speed, and layer thickness; utilize high-quality metal powders with good flowability (as provided by Metal3DP); and consider Hot Isostatic Pressing (HIP) for densification.
- Rugosidad superficial: The as-printed surface finish may not meet the requirements for aerodynamic performance or sealing.
- Avoidance: Optimize printing parameters, consider using finer powder particle sizes, and implement appropriate post-processing techniques like polishing or machining.
- Dimensional Inaccuracies: Shrinkage during solidification and other factors can lead to deviations from the intended dimensions.
- Avoidance: Calibrate the 3D printer regularly, optimize build orientation, compensate for material shrinkage in the design phase, and employ post-processing metrology for verification.
- Material Property Variability: Inconsistent melting or cooling can lead to variations in the microstructure and mechanical properties throughout the printed part.
- Avoidance: Utilize well-characterized printing parameters, ensure a stable printing environment, and employ process monitoring technologies.
- Coste y plazo de entrega: While 3D printing can reduce lead times for prototyping and small batches, the cost per part can be higher for large-scale production compared to traditional methods.
- Avoidance: Optimize part design for efficient printing, consider hybrid manufacturing approaches for high-volume production, and carefully evaluate the overall cost-benefit analysis.
By proactively addressing these potential challenges through careful design, optimized printing parameters, and appropriate post-processing, the successful production of high-performance metal 3D printed exhaust nozzles can be ensured. Metal3DP’s expertise and advanced equipment are geared towards mitigating these challenges and delivering high-quality parts.
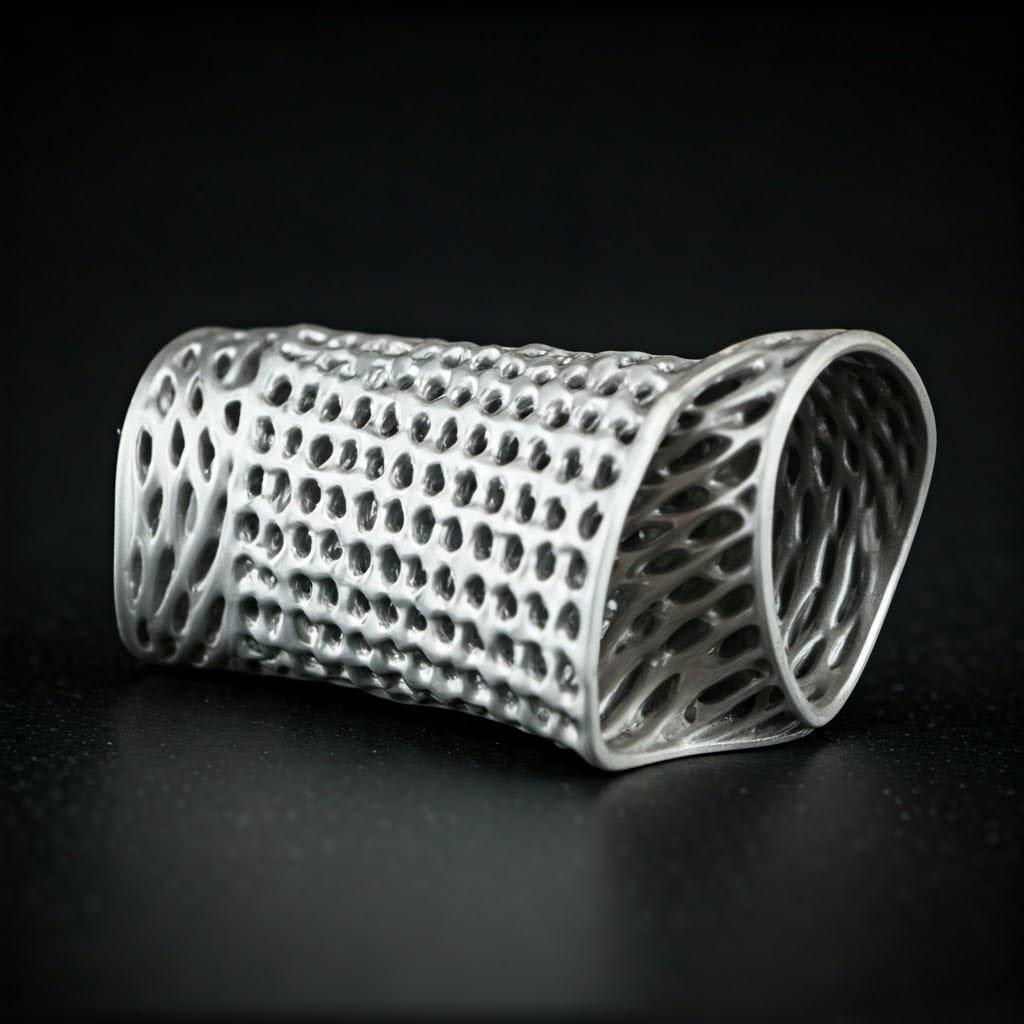
How to Choose the Right Metal 3D Printing Service Provider for Exhaust Nozzles
Selecting the appropriate metal 3D printing service provider is a critical decision that significantly impacts the quality, cost, and lead time of your high-temperature exhaust nozzles. Consider the following factors when evaluating potential suppliers:
- Capacidades de los materiales: Ensure the provider has experience working with the specific high-temperature alloys required for your application, such as IN718 and Haynes 282. Verify their expertise in processing these materials to achieve the desired mechanical properties and performance characteristics. Metal3DP specializes in a wide range of high-performance metal powders, including those ideal for extreme temperature environments.
- Tecnología y equipamiento: Inquire about the types of metal 3D printing technologies they utilize (e.g., SLM, EBM). Different technologies offer varying levels of precision, surface finish, and build volume. Ensure their equipment is well-maintained and capable of handling the size and complexity of your exhaust nozzle design. Metal3DP boasts industry-leading print volume, accuracy, and reliability with our advanced SEBM printers. You can learn more about our métodos de impresión en nuestro sitio web.
- Quality Assurance and Certifications: Verify if the provider has robust quality management systems and relevant certifications (e.g., ISO 9001, AS9100 for aerospace). This ensures that their processes are controlled and that the manufactured parts meet stringent quality standards.
- Experiencia en diseño para la fabricación aditiva (DfAM): A knowledgeable service provider should be able to offer guidance on optimizing your exhaust nozzle design for metal 3D printing, helping to improve performance, reduce material usage, and minimize post-processing requirements. Our team at Metal3DP has decades of collective expertise in metal additive manufacturing and offers comprehensive application development services.
- Post-Processing Services: Determine if the provider offers the necessary post-processing services, such as support removal, stress relieving, HIP, heat treatment, surface finishing, and inspection. A comprehensive service offering can streamline the production process and ensure the final part meets all specifications.
- Experience and Case Studies: Review the provider’s track record and experience in producing similar high-temperature components for demanding industries like aerospace, automotive, or power generation. Case studies and testimonials can provide valuable insights into their capabilities and customer satisfaction.
- Communication and Support: Effective communication and responsive customer support are essential for a smooth and successful project. Evaluate the provider’s responsiveness, technical expertise, and willingness to collaborate. Feel free to Contacta con Metal3DP to explore how our capabilities can power your organization’s additive manufacturing goals.
- Coste y plazo de entrega: Obtain detailed quotes and lead times for your project. While cost should not be the sole determining factor, it’s important to understand the pricing structure and ensure it aligns with your budget. 1 Compare lead times to ensure they meet your project timelines. 1. au.ruli.com au.ruli.com
By carefully evaluating these factors, you can select a metal 3D printing service provider that is well-equipped to handle the complexities of manufacturing high-temperature exhaust nozzles and deliver high-quality, reliable parts.
Cost Factors and Lead Time for 3D Printed Exhaust Nozzles
The cost and lead time for producing high-temperature exhaust nozzles using metal 3D printing are influenced by several factors:
Factores de coste:
- Coste del material: The cost of the metal powder (e.g., IN718, Haynes 282) is a significant contributor to the overall cost. Specialized high-performance alloys tend to be more expensive.
- Build Volume and Complexity: Larger parts and those with intricate geometries require more printing time and material, increasing the cost. The complexity of the design, including the need for extensive support structures, also impacts cost.
- Tiempo de impresión: The duration of the printing process depends on the part size, complexity, layer height, and the chosen printing technology. Longer print times translate to higher machine operating costs.
- Costes de postprocesamiento: The extent of post-processing required (e.g., support removal, heat treatment, HIP, machining, coating) significantly affects the final cost. More demanding surface finish or tighter tolerance requirements will increase post-processing expenses.
- Costes laborales: The expertise required for design optimization, print setup, operation, and post-processing contributes to the overall cost.
- Equipment and Overhead: The cost of operating and maintaining the metal 3D printing equipment and the overhead costs of the service provider are factored into the pricing.
- Cantidad: While 3D printing is advantageous for low to medium volumes and customized parts, the cost per part may decrease with larger production runs due to economies of scale in material procurement and process optimization.
Factores del plazo de entrega:
- Design Complexity and Optimization: The time required for design and optimization for additive manufacturing can impact the overall lead time, especially for intricate exhaust nozzle designs.
- Disponibilidad de material: The availability of the specific metal powder required can influence the start of the printing process. Metal3DP maintains a stock of high-quality metal powders to minimize delays.
- Tiempo de impresión: As mentioned earlier, the build time is a direct factor in the lead time.
- Duración del post-procesamiento: The time required for each post-processing step (e.g., heat treatment cycles, machining time, coating application) adds to the overall lead time.
- Control de Calidad e Inspección: Thorough inspection processes can take time but are crucial for ensuring part quality.
- Scheduling and Capacity: The service provider’s current workload and machine availability can affect the lead time.
It’s important to discuss these factors with your metal 3D printing service provider to get an accurate estimate of both the cost and lead time for your high-temperature exhaust nozzles. Understanding these variables will help you plan your project effectively. You can request a quote from Metal3DP to get a detailed understanding of the cost and lead time for your specific requirements.
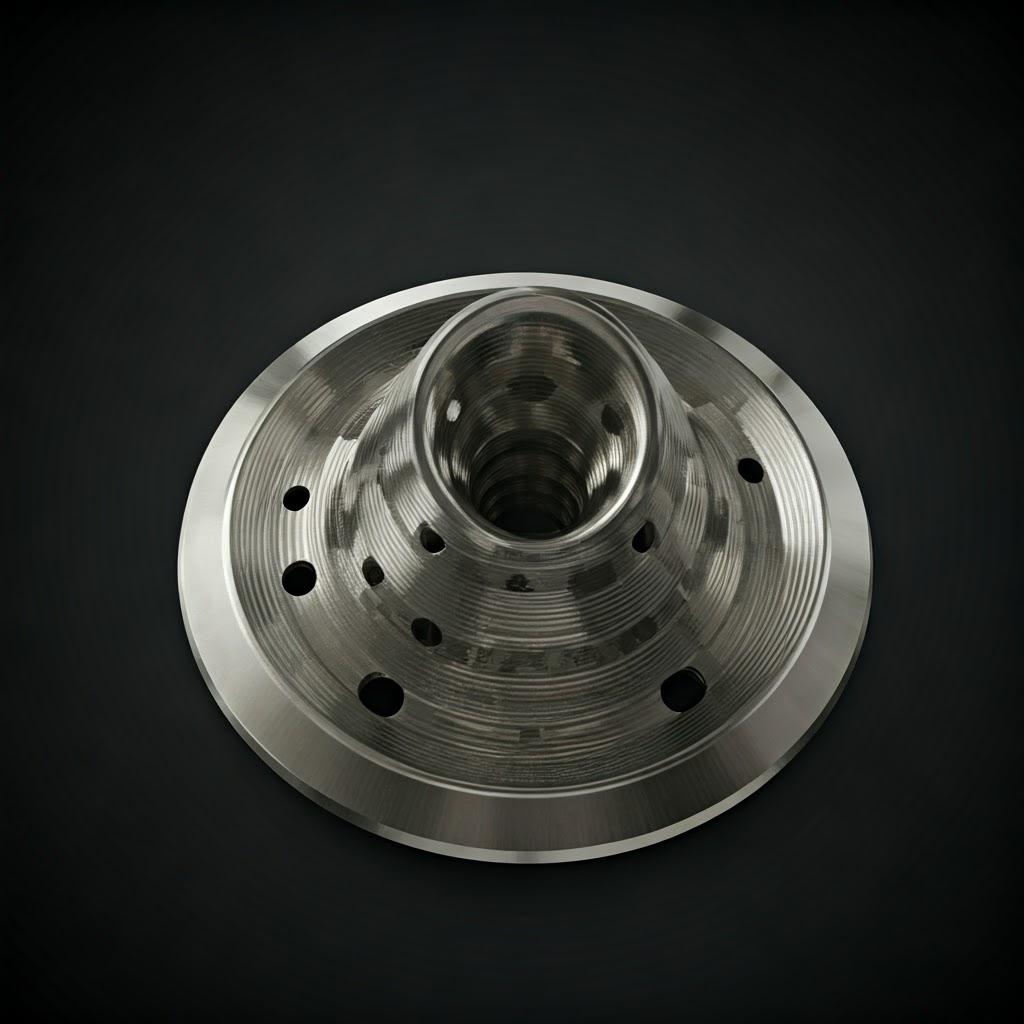
Preguntas más frecuentes (FAQ)
- What are the typical applications for metal 3D printed high-temperature exhaust nozzles? Metal 3D printed high-temperature exhaust nozzles are commonly used in aerospace (jet engines, rocket engines), power generation (gas turbines), high-performance automotive, and specialized industrial machinery where efficient and controlled expulsion of hot gases is required under extreme thermal and mechanical loads.
- Can metal 3D printing produce exhaust nozzles with internal cooling channels? Yes, metal 3D printing excels at creating complex internal geometries, including intricate cooling channels within the nozzle structure. This allows for improved thermal management and enhanced performance compared to conventionally manufactured nozzles.
- What are the advantages of using IN718 and Haynes 282 for 3D printed exhaust nozzles? Both IN718 and Haynes 282 are nickel-based superalloys that offer exceptional high-temperature strength, creep resistance, and oxidation resistance, making them ideal for the demanding operating conditions of exhaust nozzles. Haynes 282 generally offers superior creep strength at higher temperatures compared to IN718.
Conclusion – Embracing the Future of High-Temperature Component Manufacturing
Metal 3D printing offers a transformative approach to the manufacturing of high-temperature exhaust nozzles. The ability to create complex geometries, optimize designs for performance, utilize advanced materials like IN718 and Haynes 282, and potentially reduce lead times and material waste presents significant advantages for industries operating in extreme environments. Companies like Metal3DP are at the forefront of this technology, providing the expertise, advanced equipment, and high-quality metal powders necessary to realize the full potential of metal additive manufacturing for critical applications. By embracing metal 3D printing, industries can unlock new possibilities for innovation, efficiency, and performance in their high-temperature systems. We invite you to learn more about Metal3DP and explore how our comprehensive solutions can meet your specific needs for advanced metal components.
Compartir
MET3DP Technology Co., LTD es un proveedor líder de soluciones de fabricación aditiva con sede en Qingdao, China. Nuestra empresa está especializada en equipos de impresión 3D y polvos metálicos de alto rendimiento para aplicaciones industriales.
Solicite información para obtener el mejor precio y una solución personalizada para su empresa.
Artículos relacionados
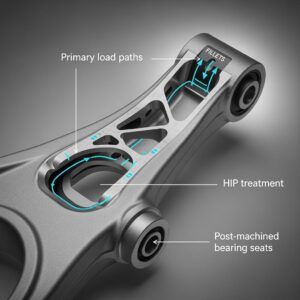
Metal 3D Printing for U.S. Automotive Lightweight Structural Brackets and Suspension Components
Leer Más "Acerca de Met3DP
Actualización reciente
Nuestro producto
CONTACTO
¿Tiene alguna pregunta? ¡Envíenos un mensaje ahora! Atenderemos su solicitud con todo un equipo tras recibir su mensaje.