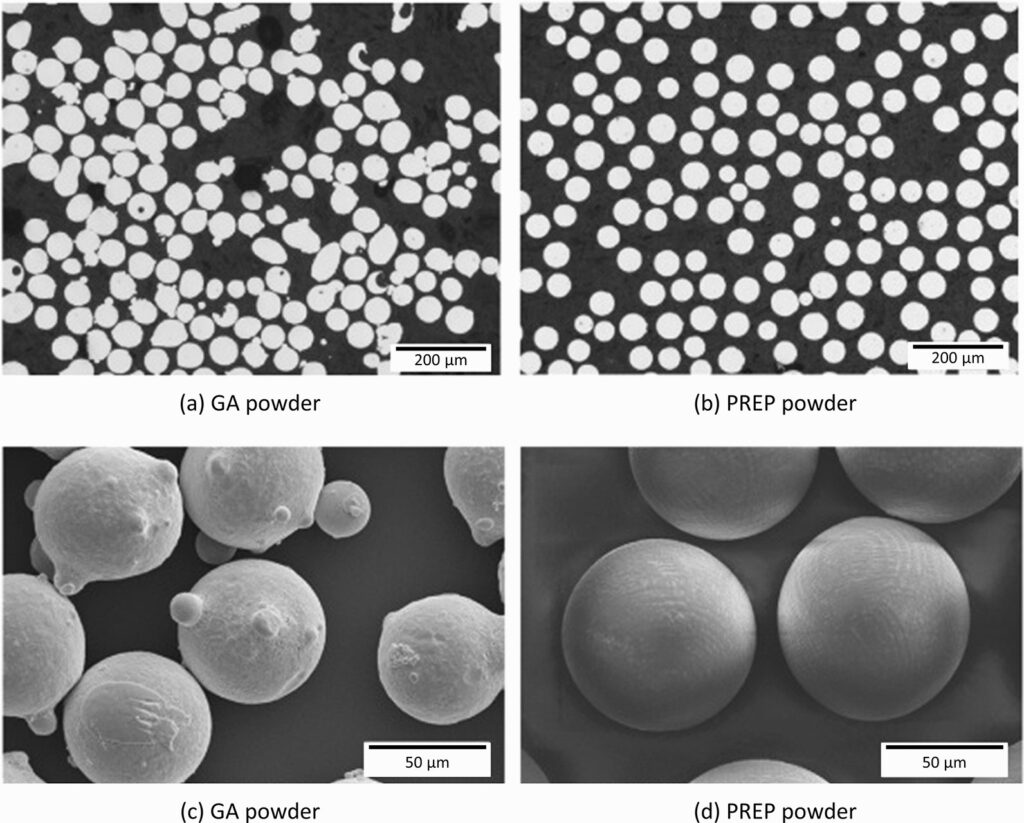
Polvo IN718: aleación superior para aplicaciones de alta tensión y alta temperatura
MOQ bajo
Proporcionamos una cantidad mínima de pedido baja para satisfacer diferentes necesidades.
OEM & ODM
Proporcionar productos y servicios de diseño personalizados para satisfacer las necesidades exclusivas de los clientes.
Existencias adecuadas
Garantizar una tramitación rápida de los pedidos y ofrecer un servicio fiable y eficaz.
Satisfacción del cliente
Ofrecer productos de alta calidad centrados en la satisfacción del cliente.
compartir este artículo
Índice
Cuando se trata de materiales de alto rendimiento capaces de soportar temperaturas extremas, presiones y entornos corrosivos, pocas aleaciones son comparables a Polvo IN718. Esta superaleación es una material a base de níquel ampliamente reconocida por su versatilidad, fuerzay resistencia a la corrosión en algunas de las industrias más exigentes, como aeroespacial, generación de energíay petróleo y gas. Pero, ¿qué hace exactamente que el polvo IN718 sea tan especial y cómo puede beneficiar a su próximo proyecto?
En esta completa guía, profundizaremos en los composición, propiedades, aplicacionesy especificaciones de polvo IN718. También exploraremos la pros y contras de utilizar esta superaleación, su preciosy responder a algunas de las preguntas más frecuentes sobre sus usos. Así pues, ¡empecemos!
Información general: ¿Qué es el polvo IN718?
Polvo IN718 es un superaleación de níquel-cromo conocida por su alta resistencia, resistencia a la corrosióny resistencia a la oxidación a temperaturas elevadas. La forma en polvo del IN718 se utiliza ampliamente en fabricación aditiva, pulvimetalurgiay pulverización térmica debido a su excelente soldabilidad y formabilidad.
Esta aleación puede mantener sus propiedades mecánicas en entornos de alta temperatura hasta 700°C (1.292°F)por lo que es ideal para motores de turbina, componentes de aeronavesy entornos de alta presión. También es un aleación endurecida por precipitaciónEsto significa que su resistencia se debe a la formación de precipitados durante el tratamiento térmico, lo que mejora sus propiedades mecánicas.
Características principales del polvo IN718:
- Alta resistencia a la tracción y resistencia al deslizamiento a temperaturas de hasta 700°C (1.292°F).
- Excelente soldabilidad en comparación con otras aleaciones a base de níquel.
- Superior resistencia a la oxidación y corrosión en entornos extremos.
- Muy utilizado en aeroespacial, petróleo y gasy energía industrias.
- Ideal para fabricación aditiva y pulvimetalurgia debido a su microestructura de grano fino.
Desglosemos ahora los aspectos específicos composición y propiedades que hacen del polvo IN718 una elección tan popular en aplicaciones de alto rendimiento.
Composición y propiedades principales del polvo IN718
El rendimiento de Polvo IN718 es el resultado directo de su composición química compleja. Comprender los elementos individuales que componen esta aleación y su impacto le ayudará a apreciar por qué la IN718 es tan versátil.
Composición química del polvo IN718
Elemento | Porcentaje (%) | Papel en la aleación |
---|---|---|
Níquel (Ni) | 50.0-55.0 | Forma la base de la aleación, proporcionando resistencia a altas temperaturas y a la corrosión. |
Cromo (Cr) | 17.0-21.0 | Mejora la resistencia a la oxidación y la corrosión, especialmente a altas temperaturas. |
Hierro (Fe) | Saldo | Añade resistencia y durabilidad a la vez que reduce el coste total. |
Molibdeno (Mo) | 2.8-3.3 | Aumenta la resistencia a la fluencia y a las altas temperaturas. |
Niobio (Nb) | 4.75-5.50 | Ayuda al endurecimiento por precipitación, formando precipitados ricos en niobio que aumentan la resistencia. |
Titanio (Ti) | 0.65-1.15 | Contribuye a la resistencia de la aleación mediante el endurecimiento por precipitación. |
Aluminio (Al) | 0.20-0.80 | Mejora la resistencia a la oxidación y contribuye al endurecimiento por precipitación. |
Cobalto (Co) | 1,00 máx. | Elemento opcional que puede mejorar la resistencia a altas temperaturas. |
Carbono (C) | 0,08 máx. | Aumenta la dureza y la resistencia al desgaste. |
Fósforo (P) | 0,015 máx. | Impureza que debe limitarse para evitar la fragilización. |
Azufre (S) | 0,015 máx. | Impureza que puede afectar negativamente a la ductilidad y soldabilidad de la aleación. |
Propiedades principales del polvo IN718
En propiedades mecánicas y térmicas de la pólvora IN718 son las que la convierten en una elección tan común para entornos de alto estrés. A continuación se desglosan sus propiedades más críticas.
Propiedad | Valor/Descripción |
---|---|
Densidad | 8,19 g/cm³ |
Intervalo de fusión | 1.260°C - 1.335°C |
Resistencia a la tracción | 1.100 MPa |
Límite elástico | 1.035 MPa |
Alargamiento a la rotura | 12-20% |
Resistencia a la fluencia | Excelente, hasta 700°C |
Dureza | Típicamente 331 HB (Dureza Brinell) |
Conductividad térmica | 11,4 W/m-K a 20°C |
Resistencia a la oxidación | Excelente, especialmente en entornos de hasta 980°C |
Resistencia a la corrosión | Superior en ambos oxidante y reduciendo como en la industria del petróleo y el gas. |
Soldabilidad | Excelente, especialmente en comparación con otras aleaciones de níquel de alta resistencia. |
Ventajas del polvo IN718: ¿Por qué elegir esta aleación?
¿Qué hace que Polvo IN718 una opción tan popular para aeroespacial y aplicaciones industriales? Analicemos las principales ventajas que distinguen a esta aleación de otras del mercado. superaleación de níquel categoría.
1. Excelente resistencia a altas temperaturas y a la fluencia
Cuando se trata de entornos de alta temperaturanecesita una aleación que resista las tensiones. Polvo IN718 está diseñado para mantener su fuerza a temperaturas de hasta 700°C. Esto lo convierte en el material motores a reacción, turbinasy generación de energía.
En endurecimiento por precipitación mecanismo que implica niobio y molibdeno garantiza la durabilidad a largo plazo, incluso en entornos en los que otros materiales fallarían debido a deformación por fluencia.
2. Resistencia superior a la corrosión y la oxidación
Otra gran ventaja de Polvo IN718 es su capacidad para resistir ambientes corrosivos. Desde el atmósferas oxidantes en centrales eléctricas a la condiciones corrosivas en el industria petrolera y del gas, IN718 ofrece resistencia superior.
En cromo y molibdeno contenido en la aleación protegen contra oxidación y corrosión por picadurapor lo que es ideal para su uso en entornos expuestos a agua salada, gas ácidoy soluciones ácidas.
3. Capacidad de fabricación versátil
Tanto si desea utilizar fabricación aditiva, pulvimetalurgiao pulverización térmica, Polvo IN718 ofrece la versatilidad necesarios para producir piezas complejas con propiedades mecánicas mejoradas. La forma en polvo permite deposición precisa y capaspor lo que es perfecto para Impresión 3D o revestimiento.
4. Excelente soldabilidad
A diferencia de muchos otros superaleaciones a base de níquel, Polvo IN718 es altamente soldable. Esto facilita su incorporación a conjuntos complejos sin riesgo de agrietamiento o fallo de soldadura. Esta es una ventaja significativa en industrias como aeroespacialdonde integridad de la soldadura es fundamental para la seguridad y el rendimiento de los componentes.
Aplicaciones del polvo IN718: ¿Dónde se utiliza?
Dadas sus extraordinarias propiedades, Polvo IN718 se utiliza en una amplia gama de industrias, especialmente en aplicaciones que requieren alta resistencia, resistencia a la corrosióny estabilidad a altas temperaturas.
Aplicaciones comunes del polvo IN718
Industria | Aplicación |
---|---|
Aeroespacial | Álabes de turbina, piezas de compresor, postquemadores y otros componentes de alta temperatura en motores a reacción y turbinas de gas. |
Petróleo y gas | Herramientas de fondo de pozo, válvulas y elementos de fijación expuestos a presiones, temperaturas y entornos corrosivos extremos. |
Generación de energía | Turbinas de gas, cámaras de combustión e intercambiadores de calor que funcionan en entornos de alta temperatura. |
Automoción | Turbocompresores, sistemas de escape y otras piezas de alto rendimiento expuestas a calor y desgaste extremos. |
Marina | Componentes expuestos a agua salada y entornos de alta presión, como ejes de hélices y tornillería. |
Nuclear | Componentes de reactores e intercambiadores de calor que requieren resistencia a altas temperaturas y a la radiación. |
Especificaciones, tamaños, calidades y normas del polvo IN718
Al seleccionar Polvo IN718 para su proyecto, es esencial elegir el especificaciones y grados para satisfacer las exigencias de su aplicación. A continuación se ofrece un desglose de los principales especificaciones y normas asociado con el polvo IN718.
Especificaciones del polvo IN718
Especificación | Detalles |
---|---|
Tamaño de las partículas | Normalmente oscila entre 15 y 53 micras, dependiendo de la aplicación (por ejemplo, fabricación aditiva, pulverización térmica). |
Morfología del polvo | Partículas esféricas para una mayor fluidez y una deposición óptima en los procesos de fabricación aditiva y pulverización térmica. |
Normas ASTM | ASTM B637 para aleaciones de níquel endurecidas por precipitación utilizadas en aplicaciones aeroespaciales e industriales. |
Normas ISO | ISO 15156 para materiales utilizados en entornos de gases sulfurosos. |
Normas AMS | AMS 5662 para IN718 en forma de barra, forja y anillo, garantizando la uniformidad en aplicaciones aeroespaciales. |
Número UNS | UNS N07718 |
Elegir bien especificación garantiza que su Polvo IN718 se reunirá el requisitos de rendimiento y normas del sector para su aplicación.
Proveedores y precios del polvo IN718
El coste de Polvo IN718 puede variar mucho en función de factores como proveedor, tamaño de las partículasy cantidad ordenado. Mientras que Polvo IN718 suele ser más caro que los materiales estándar, su alto rendimiento y durabilidad a menudo justifican la inversión.
Proveedores y precios del polvo IN718
Proveedor | Gama de precios (por kg) | Notas |
---|---|---|
Oerlikon Metco | $500 – $750 | Especializada en materiales avanzados para aplicaciones aeroespaciales e industriales, incluido el polvo IN718. |
Tecnología Carpenter | $520 – $780 | Ofrece aleaciones premium de alto rendimiento, incluida la IN718, para industrias exigentes como la aeroespacial y la de generación de energía. |
Kennametal | $490 – $730 | Conocida por sus polvos de níquel de alta calidad, incluido el IN718 para fabricación aditiva y pulverización térmica. |
Höganäs AB | $510 – $760 | Proveedor líder de polvos metálicos, incluido el IN718 para aplicaciones de impresión 3D y pulvimetalurgia. |
Powder Alloy Corporation | $500 – $750 | Proporciona polvos IN718 de máxima calidad para aplicaciones de revestimiento láser y fusión en lecho de polvo. |
De media, Polvo IN718 puede oscilar entre $500 a $780 por kilogramodependiendo de su requisitos específicos. Aunque pueda parecer caro, el beneficios a largo plazo en términos de durabilidad y rendimiento a menudo superan el coste inicial.
Comparación de ventajas e inconvenientes
Antes de decidir si Polvo IN718 es el material adecuado para su proyecto, es esencial sopesar las ventajas y limitaciones. Aunque es una aleación muy versátil y de alto rendimiento, hay algunos factores que pueden hacerla menos adecuada para determinadas aplicaciones.
Ventajas
Ventaja | Descripción |
---|---|
Resistencia a altas temperaturas: Conserva las propiedades mecánicas hasta 700°C. | Ideal para aplicaciones como turbinas de gas, motores a reacción y hornos industriales. |
Resistencia a la corrosión y a la oxidación: Excelente en entornos difíciles. | Perfecta para industrias como la del petróleo y el gas, la generación de energía y la marina. |
Soldabilidad: Más fácil de soldar que otras aleaciones a base de níquel. | Reduce el riesgo de fisuración de las soldaduras, especialmente en ensamblajes complejos. |
Polvo versátil: Compatible con la fabricación aditiva, la pulverización térmica y la pulvimetalurgia. | Permite la fabricación flexible de piezas complejas y revestimientos finos. |
Vida útil prolongada: Reduce la necesidad de sustituir piezas con frecuencia, lo que disminuye los costes de mantenimiento. | Beneficioso para industrias en las que los tiempos de inactividad son costosos, como la generación de energía y la industria aeroespacial. |
Limitaciones
Limitación | Descripción |
---|---|
Coste elevado: Más caro que los materiales estándar. | Puede no ser adecuado para aplicaciones sensibles al presupuesto o de baja demanda. |
Difícil de mecanizar: Requiere herramientas especializadas debido a su dureza y resistencia. | Aumenta el tiempo y el coste de mecanizado, especialmente para geometrías complejas. |
Disponibilidad limitada: Puede que no siempre estén disponibles en grandes cantidades. | Puede dar lugar a plazos de entrega más largos, especialmente para pedidos personalizados o proyectos a gran escala. |
Preguntas frecuentes
Vamos a abordar algunas de las preguntas más frecuentes sobre Polvo IN718 y su uso en diversas industrias.
Pregunta | Respuesta |
---|---|
¿Para qué se utiliza el polvo IN718? | Se utiliza habitualmente en industrias como aeroespacial, generación de energíay petróleo y gas para componentes de alta temperatura. |
¿Cuánto cuesta el polvo IN718? | Los precios suelen oscilar entre $500 a $780 por kilogramoDependiendo del proveedor y de los requisitos específicos. |
¿Se puede utilizar el polvo IN718 en la impresión 3D? | Sí, se utiliza con frecuencia en fabricación aditiva procesos como fusión en lecho pulvígeno para crear piezas de alto rendimiento. |
¿Qué industrias utilizan el polvo IN718? | Se utiliza en sectores como aeroespacial, automoción, generación de energíay petróleo y gas para componentes en entornos extremos. |
¿Es el polvo IN718 resistente a la corrosión? | Sí, IN718 ofrece excelentes resistencia a la corrosiónespecialmente en oxidante y reduciendo entornos. |
¿En qué se diferencia el polvo IN718 de otras aleaciones de níquel? | IN718 ofrece resistencia a altas temperaturas y resistencia a la corrosión en comparación con muchas otras aleaciones a base de níquel. |
¿Es el polvo IN718 fácil de mecanizar? | Debido a su dureza, el IN718 puede ser difícil de mecanizar y puede requerir herramientas especializadas y técnicas. |
¿Cuáles son las principales ventajas del polvo IN718? | IN718 proporciona resistencia a altas temperaturas, resistencia a la corrosióny soldabilidadpor lo que es adecuado para aplicaciones extremas. |
¿Puede el polvo IN718 soportar el calor extremo? | Sí, el IN718 mantiene sus propiedades mecánicas a temperaturas de hasta 700°Cpor lo que es ideal para turbinas de gas y cámaras de combustión. |
¿Cuáles son los retos del mecanizado del polvo IN718? | Su dureza y resistencia hacen que sea más difícil de mecanizar, requiriendo a menudo herramientas especiales y técnicas para una fabricación de precisión. |
Conclusión: ¿Es el polvo IN718 adecuado para su proyecto?
A la hora de elegir un material que resista condiciones extremas, it destaca como una de las mejores opciones disponibles. Su resistencia a altas temperaturas, resistencia a la corrosióny soldabilidad lo convierten en la mejor opción para sectores como aeroespacial, petróleo y gasy generación de energía.
Sin embargo, con su mayor coste y retos de mecanizadoes esencial sopesar pros y contras antes de tomar una decisión. En it ofrece rendimiento superiorEl inversión inicial y requisitos de procesamiento puede no adaptarse a todas las aplicaciones.
En resumen, si su proyecto implica alto estrés, calor extremoo ambientes corrosivos, it es una excelente inversión que le proporcionará larga durabilidad y rendimiento fiable.
Obtener el último precio
Acerca de Met3DP
Categoría de productos
OFERTAS
CONTACTO
¿Tiene alguna pregunta? ¡Envíenos un mensaje ahora! Atenderemos su solicitud con todo un equipo tras recibir su mensaje.
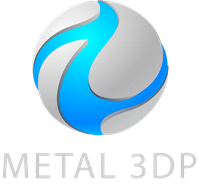
Polvos metálicos para impresión 3D y fabricación aditiva