Polvo moldeable por inyección
Índice
Polvo moldeable por inyección se refiere a un tipo de materia prima utilizada en el moldeo por inyección de polvo, un proceso de fabricación industrial para producir piezas metálicas complejas y de alta precisión. Este polvo es una mezcla de polvos metálicos finos y aglutinantes poliméricos que pueden moldearse por inyección en piezas complejas con forma de red en grandes volúmenes.
Ventajas del polvo moldeable por inyección
Ventaja | Descripción | Beneficio |
---|---|---|
Geometrías complejas: IMP permite la creación de formas intrincadas con características finas que son difíciles o imposibles de lograr con las técnicas tradicionales de moldeo por inyección. Esta libertad de diseño abre las puertas a componentes innovadores en diversos sectores. | A diferencia de los materiales de moldeo tradicionales, como los plásticos fundidos, el IMP utiliza un sistema aglutinante que mantiene unidas las partículas de polvo durante el proceso de moldeo. Esto permite crear piezas con canales internos, muescas y otras geometrías complejas. | |
Eficiencia del material: El IMP favorece la fabricación de formas casi netas, minimizando el desperdicio de material en comparación con técnicas sustractivas como el mecanizado. Esto es especialmente beneficioso para materiales caros o de alto rendimiento. | El control preciso de la distribución del polvo durante el moldeo por inyección minimiza el uso excesivo de material. Además, a diferencia de los procesos tradicionales que generan piezas desechadas durante las pruebas, el IMP permite iteraciones de diseño más rápidas con un desperdicio mínimo de material. | |
Amplia selección de materiales: El IMP ofrece una gama más amplia de opciones de materiales en comparación con el moldeo por inyección tradicional. Esta versatilidad permite crear piezas con propiedades específicas adaptadas a la aplicación. | Además de los polímeros estándar utilizados en el moldeo por inyección, IMP puede utilizar polvos metálicos, cerámica e incluso materiales compuestos. Esto abre las puertas a la creación de piezas con combinaciones únicas de resistencia, conductividad o biocompatibilidad. | |
Piezas de alto rendimiento: La capacidad de utilizar polvos metálicos y cerámicos en IMP permite fabricar piezas de alto rendimiento con una fuerza, una resistencia al calor o unas propiedades de desgaste excepcionales. | Los componentes metálicos moldeados por inyección (MIM) pueden alcanzar propiedades mecánicas comparables a las de los metales forjados (a granel), lo que los hace adecuados para aplicaciones exigentes. Del mismo modo, las piezas cerámicas MIM ofrecen una excelente resistencia al desgaste y rendimiento a altas temperaturas. | |
Potencial de producción en masa: Aunque inicialmente se utilizó para la creación de prototipos, la tecnología IMP ha madurado hasta permitir la producción en serie rentable de piezas complejas. | El alto grado de automatización alcanzable en los procesos IMP permite una producción eficaz de grandes cantidades de piezas con una calidad constante. Esto la convierte en una opción viable para aplicaciones de gran volumen. | |
Acabado superficial mejorado: En comparación con las técnicas tradicionales de fundición de metales, el IMP puede conseguir a veces un acabado superficial más liso en las piezas finales. | El uso de polvos finos y el proceso de moldeo controlado pueden minimizar las imperfecciones de la superficie, reduciendo potencialmente la necesidad de extensos pasos de postprocesado como el pulido. |
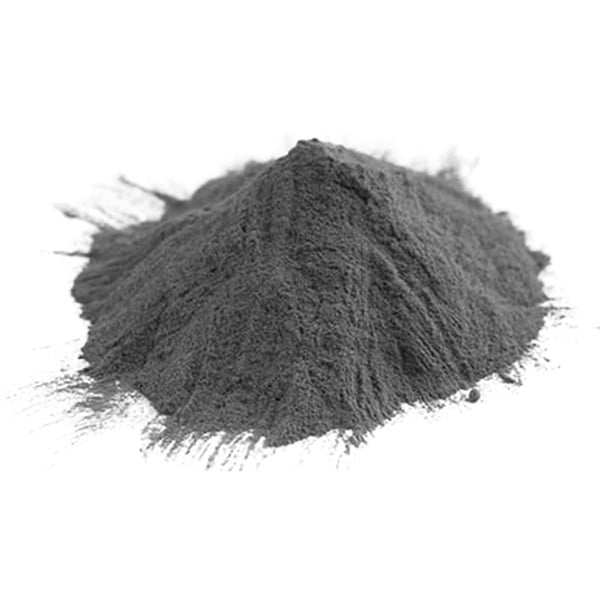
Composición del polvo moldeable por inyección
Componente | Descripción | Función |
---|---|---|
Polvos base | Constituyen el material funcional primario de la pieza final y pueden clasificarse en tres tipos principales: Polvos metálicos: Partículas metálicas finamente divididas de diversas aleaciones, como acero inoxidable, acero para herramientas o superaleaciones. Polvos cerámicos: Materiales cerámicos como la alúmina, la circonia o el nitruro de silicio en forma de polvo. Polvos de polímero: Polímeros termoplásticos utilizados habitualmente en el moldeo por inyección, como el nailon o el polipropileno. | La elección del polvo base determina las propiedades finales de la pieza moldeada, como la solidez, la resistencia al desgaste o el rendimiento térmico. |
Sistema de encuadernación | Se trata de un componente crucial que actúa como pegamento temporal, manteniendo unidas las partículas de polvo base durante el proceso de moldeo. El sistema aglutinante suele estar compuesto por: Polímero termoplástico: Una resina termoplástica que se funde durante la etapa de moldeo por inyección, permitiendo la fluidez y la adhesión con el polvo base. * Ceras o aditivos: Pueden mejorar las propiedades de fluidez, la eficacia del desligado o la dispersión del polvo en el aglutinante. | El sistema aglutinante garantiza que el polvo se comporte como una materia prima moldeable durante la inyección y permite crear formas complejas. |
Formadores de poros | Son aditivos opcionales que crean poros temporales dentro de la pieza moldeada. Pueden ser: * Materiales orgánicos: Estos se queman durante el desencolado, dejando tras de sí una red de poros que facilitan la eliminación del sistema aglutinante. * Agentes químicos de lixiviación: Éstos se disuelven en un disolvente específico durante un paso posterior al tratamiento, creando una estructura de poros controlada. | Los formadores de poros permiten crear estructuras porosas en la pieza final, lo que puede ser beneficioso para aplicaciones como filtros o implantes óseos. |
Características de los polvos metálicos utilizados
Característica | Descripción | Importancia en MIM |
---|---|---|
Tamaño y distribución de partículas | El tamaño y la distribución de las partículas de polvo metálico influyen significativamente en los siguientes aspectos del MIM: Relleno de molde y resistencia verde: Los polvos más finos suelen ofrecer una mayor densidad de empaquetamiento y pueden mejorar el llenado del molde durante la inyección. Sin embargo, las partículas excesivamente finas pueden dificultar la fluidez y provocar problemas durante el procesamiento. Una distribución granulométrica estrecha garantiza un empaquetado homogéneo y minimiza los huecos dentro de la pieza moldeada, lo que contribuye a una buena resistencia en verde (resistencia de la pieza antes de la sinterización). Comportamiento de sinterización y propiedades finales: El tamaño de las partículas influye en el proceso de sinterización, en el que las partículas se unen para formar una estructura sólida. Los polvos con una distribución de tamaños más amplia pueden dar lugar a una sinterización no homogénea y afectar potencialmente a las propiedades mecánicas finales de la pieza. | La selección cuidadosa del tamaño y la distribución de las partículas es crucial para conseguir un buen llenado del molde, resistencia en verde y un rendimiento óptimo en el componente sinterizado final. |
Morfología de las partículas | Se refiere a la forma de las partículas de polvo metálico. Idealmente, los procesos MIM favorecen los polvos con morfologías esféricas o casi esféricas. | Las partículas esféricas fluyen más fácilmente, mejorando el llenado del molde y la densidad de empaquetado. Las partículas de forma irregular pueden crear huecos y dificultar la fluidez, lo que puede provocar defectos en la pieza moldeada. |
Densidad aparente y de toma | Estas propiedades representan la densidad aparente del polvo en diferentes condiciones. Densidad aparente: Se refiere a la densidad del polvo en reposo, considerando los espacios entre partículas. Densidad del grifo: Esto refleja un estado más denso logrado mediante un proceso de golpeo normalizado. | En general, es deseable una mayor densidad de colada en el MIM para lograr una utilización eficaz del material y una buena precisión dimensional en la pieza final. También contribuye a mejorar el empaquetado durante el moldeo y minimiza la contracción durante la sinterización. |
Composición química | Los elementos o aleaciones específicos utilizados en el polvo metálico determinan las propiedades finales de la pieza sinterizada. | La elección de la composición del polvo metálico permite adaptar propiedades como la solidez, la resistencia a la corrosión o la resistencia al desgaste a los requisitos específicos de la aplicación. El MIM puede utilizar diversas aleaciones metálicas, como acero inoxidable, acero para herramientas e incluso aleaciones de alto rendimiento como el Inconel. |
Fluidez | Se refiere a la facilidad con la que el polvo fluye bajo la gravedad o las fuerzas aplicadas. | Una buena fluidez es esencial para una distribución uniforme del polvo durante el moldeo por inyección. Los polvos poco fluidos pueden provocar incoherencias en la densidad de empaquetado y posibles defectos en la pieza final. |
Normas para polvos metálicos
Los polvos metálicos utilizados deben cumplir las normas de composición y granulometría:
Cuerpo estándar | Estándar | Descripción | Importancia en la PMI |
---|---|---|---|
ASTM Internacional (ASTM) | ASTM B930 - Guía estándar para la caracterización de polvos de materias primas para moldeo por inyección de metales (MIM) | Esta norma describe varios métodos de ensayo para caracterizar las propiedades de los polvos metálicos utilizados en MIM. | Proporciona un marco para evaluar factores como la distribución del tamaño de las partículas, la morfología, la fluidez y la densidad aparente. Esto garantiza la coherencia y el control de calidad de los polvos metálicos utilizados para aplicaciones IMP. |
** | ** | * ASTM B783 - Especificación estándar para polvos de acero inoxidable para aplicaciones de moldeo por inyección de metal (MIM). | Esta norma define los requisitos específicos para la composición química, la distribución granulométrica y la fluidez de los polvos de acero inoxidable utilizados en MIM. |
** | ** | * ASTM D4000 - Sistema de clasificación estándar para especificar materiales plásticos | Aunque no es exclusiva de la IMP, esta norma proporciona un sistema de clasificación para varios tipos de materiales plásticos, incluidos los potencialmente utilizados como aglutinantes en la materia prima de la IMP. |
Organización Internacional de Normalización (ISO) | * ISO 3095 - Metallic powders - Determination of flow rate by means of a Hall flowmeter | Esta norma especifica un método para medir la fluidez de polvos metálicos utilizando un caudalímetro Hall. | Proporciona un enfoque estandarizado para evaluar la fluidez, una característica crítica para lograr un buen llenado del molde y una calidad constante de las piezas en IMP. |
** | ** | * ISO 4497 - Plastics - Determination of the melt flow rate (MFR) and melt volume-flow rate (MVR) of thermoplastics (Plásticos - Determinación del índice de flujo de fusión (MFR) y del índice de flujo de volumen de fusión (MVR) de termoplásticos) | Esta norma describe un método para medir el índice de fluidez (MFR) de los materiales termoplásticos, que puede ser relevante para el componente aglutinante de la materia prima IMP. |
Etapas del proceso de fabricación
El proceso de fabricación consta de los siguientes pasos clave:
Paso | Descripción | Importancia |
---|---|---|
1. Preparación y mezcla del polvo | El polvo base (metal, cerámica o polímero) se selecciona y pretrata cuidadosamente en función de las propiedades finales deseadas. Pueden incluirse aditivos como formadores de poros o lubricantes. A continuación, el polvo se pesa con precisión y se mezcla con el sistema aglutinante para formar una materia prima homogénea. | Este paso sienta las bases de las propiedades de la pieza final. Una selección cuidadosa y una mezcla precisa garantizan un comportamiento uniforme del material durante el procesamiento. |
2. Moldeo por inyección | La materia prima IMP preparada se calienta hasta un estado semifundido y se inyecta en una cavidad de molde cerrada a alta presión. El molde reproduce la forma deseada de la pieza final. | Esta etapa define la geometría de la pieza. Un flujo y una presión constantes durante la inyección son cruciales para conseguir unas dimensiones precisas de la pieza y unos defectos mínimos. |
3. Desencuadernación | La pieza moldeada, también llamada "pieza verde", se somete a un proceso de desaglomerado para eliminar el sistema aglutinante. Esto puede conseguirse mediante: * Desencolado con disolvente: La pieza se sumerge en un disolvente que disuelve el aglutinante, dejando tras de sí la estructura en polvo. * Desbobinado térmico: La pieza se expone a un ciclo de calentamiento controlado, en el que el aglutinante se descompone térmicamente y escapa en forma de gas. | Para conseguir la forma y la porosidad finales deseadas sin dañar la delicada estructura del polvo, es fundamental un desbastado eficaz. |
4. Sinterización | La pieza desbastada se somete a altas temperaturas en una atmósfera controlada (a menudo al vacío o con gas inerte). Este proceso favorece la difusión y la unión entre las partículas de polvo, lo que da lugar a un componente sólido y con forma casi de red. | La sinterización determina las propiedades mecánicas finales de la pieza, como la resistencia, la densidad y la estabilidad dimensional. El control preciso de la temperatura y la gestión de la atmósfera son esenciales. |
5. Tratamiento posterior | En función de los requisitos de la aplicación, la pieza sinterizada puede someterse a etapas de acabado adicionales como: * Mecanizado o rectificado: Para conseguir tolerancias dimensionales o acabados superficiales precisos. * Tratamiento térmico: Para mejorar propiedades mecánicas específicas como la resistencia o la dureza. * Recubrimiento o infiltración: Para mejorar las propiedades de la superficie, como la resistencia al desgaste o a la corrosión. | Los tratamientos posteriores pueden mejorar aún más la funcionalidad y la estética de la pieza IMP final. |
Aplicaciones de las piezas moldeadas por inyección
Polvo moldeable por inyección puede utilizarse para fabricar diversas piezas complejas y de alta precisión en todos los sectores industriales:
Industria | Ejemplos de aplicación | Ventajas del moldeo por inyección |
---|---|---|
Automoción | Componentes interiores ( salpicaderos, paneles de puertas, consolas) Piezas bajo el capó (cubiertas de ventilador, colectores de admisión) Componentes funcionales (engranajes, ruedas dentadas) | Producción de gran volumen de formas complejas con características precisas. Piezas ligeras para mejorar la eficiencia del combustible. Amplia gama de opciones de materiales para diversas necesidades de rendimiento (durabilidad, resistencia al calor). |
Electrónica de consumo | Carcasas electrónicas (teléfonos, portátiles, tabletas) Conectores y botones Componentes internos (soportes, engranajes) | Producción en serie de piezas complejas con gran precisión dimensional. Acabados de superficie lisa para mayor estética y comodidad del usuario. Variedad de colores y texturas gracias a la selección de materiales y técnicas de moldeado. |
Productos sanitarios | Instrumental quirúrgico (mangos, empuñaduras) Componentes protésicos (articulaciones de rodilla, implantes dentales) Componentes médicos desechables (jeringuillas, viales) | Materiales esterilizables para mayor higiene y seguridad. Materiales biocompatibles para su uso en el cuerpo humano (determinados polímeros y aleaciones metálicas). Geometrías complejas para una funcionalidad precisa en aplicaciones médicas. |
Aeroespacial y defensa | Componentes de aeronaves (conductos, piezas del tren de aterrizaje) Componentes de satélites (soportes, carcasas) Equipos de defensa (cascos, componentes de armas) | Materiales ligeros y de alta resistencia para reducir el peso en aplicaciones aeroespaciales. Materiales ignífugos o resistentes al calor para requisitos específicos. Piezas duraderas para entornos duros y condiciones de funcionamiento exigentes. |
Bienes de consumo | Juguetes y juegos Electrodomésticos (carcasas, pomos, diales) Artículos deportivos (cascos, piezas de bicicleta) | Producción rentable de productos de consumo de gran volumen. Amplia variedad de colores y acabados para mayor atractivo visual. Piezas duraderas y funcionales para el uso diario. |
Ventajas del moldeo por inyección para la fabricación de piezas
Ventaja | Descripción | Beneficio |
---|---|---|
Producción de gran volumen: El moldeo por inyección destaca en la producción eficiente de grandes cantidades de piezas idénticas. Las capacidades de automatización y los tiempos de ciclo rápidos permiten una producción en masa rentable. | Esto resulta especialmente ventajoso para productos que requieren millones de unidades, como la electrónica de consumo o los componentes de automoción. La calidad y repetibilidad constantes están garantizadas durante toda la tirada de producción. | |
Flexibilidad de diseño: El moldeo por inyección puede adaptarse a una amplia gama de complejidades geométricas, como formas intrincadas, paredes finas y características internas. Esta libertad de diseño permite crear piezas funcionales e innovadoras. | A diferencia de algunos métodos de fabricación sustractiva, el moldeo por inyección no está limitado por la geometría de la herramienta. Pueden moldearse directamente en la pieza socavados, canales y otras características complejas. | |
Precisión dimensional y repetibilidad: El control preciso del diseño del molde y de los parámetros de inyección permite obtener piezas de dimensiones uniformes y precisas en grandes volúmenes de producción. | Esto minimiza la necesidad de pasos de postprocesado para la corrección dimensional y garantiza piezas intercambiables para el montaje. La repetibilidad es crucial para mantener una calidad y funcionalidad constantes del producto. | |
Amplia selección de materiales: En el moldeo por inyección puede utilizarse una amplia gama de materiales, como termoplásticos, termoestables, elastómeros e incluso algunas aleaciones metálicas (a través del moldeo por inyección de metales - MIM). | Esta versatilidad permite seleccionar el material óptimo en función de las propiedades deseadas, como la solidez, la resistencia al calor, la resistencia química o la flexibilidad. | |
Acabado superficial y estética: El moldeo por inyección puede producir piezas con acabados superficiales suaves y de alta calidad, eliminando a menudo la necesidad de extensos pasos de postprocesado como el pulido. Además, pueden incorporarse diversos colorantes y texturas durante el moldeo. | Esto contribuye al atractivo visual y la funcionalidad del producto final. Las superficies lisas pueden ser esenciales para la higiene en dispositivos médicos o para facilitar la limpieza en bienes de consumo. | |
Eficiencia del material: El moldeo por inyección favorece la fabricación de formas casi netas, minimizando el desperdicio de material en comparación con técnicas sustractivas como el mecanizado. El material sobrante, llamado bebedero y canales, a menudo puede reciclarse y reutilizarse en series de producción posteriores. | Esto es beneficioso desde el punto de vista de los costes y la sostenibilidad. Minimizar los residuos también reduce el impacto medioambiental del proceso de fabricación. | |
Potencial de automatización: El proceso de moldeo por inyección puede ser altamente automatizado, con una mínima intervención humana necesaria para su funcionamiento. Esto permite una calidad de producción constante y reduce los costes de mano de obra. | La automatización es especialmente ventajosa para grandes volúmenes de producción y garantiza una calidad constante del producto, independientemente del nivel de habilidad del operario. |
Limitaciones del proceso de fabricación
También existen algunas limitaciones:
- Peso de la pieza limitado a < 400 g
- Espesor de pared > 0,4 mm
- Montajes necesarios para geometrías complejas
- Costoso utillaje para moldes
- Cambios dimensionales durante la sinterización
Proveedores mundiales de materias primas
Muchas empresas internacionales suministran materias primas listas para el moldeo por inyección:
Empresa | Ubicación | Materiales |
---|---|---|
BASF | Alemania | Acero inoxidable 316L, aleaciones de titanio |
Sandvik | Suecia | Aceros inoxidables, aceros para herramientas |
GKN | REINO UNIDO | Aleaciones de aluminio y magnesio |
Río Tinto | Australia | Mezclas inyectadas de metal y cerámica |
Precios indicativos
Material | Precios |
---|---|
Acero inoxidable | $50-70 por kg |
Acero para herramientas | $45-65 por kg |
Aleación pesada de wolframio | $130-170 por kg |
Los precios dependen del volumen de pedidos, las necesidades de personalización y factores económicos.
Pros y contras del uso Polvos moldeables por inyección
Ventajas | Desventajas |
---|---|
Formas intrincadas y complejas | Tamaño y peso limitados |
Tolerancias más estrechas | Herramientas y equipos caros |
Acabado superficial fino | Cambios dimensionales durante la sinterización |
Gama de materiales | A menudo se necesita posprocesamiento |
Alta producción, bajo coste por pieza | Los materiales frágiles tienden a agrietarse |
Reducción de residuos | Restringe la elección del material |
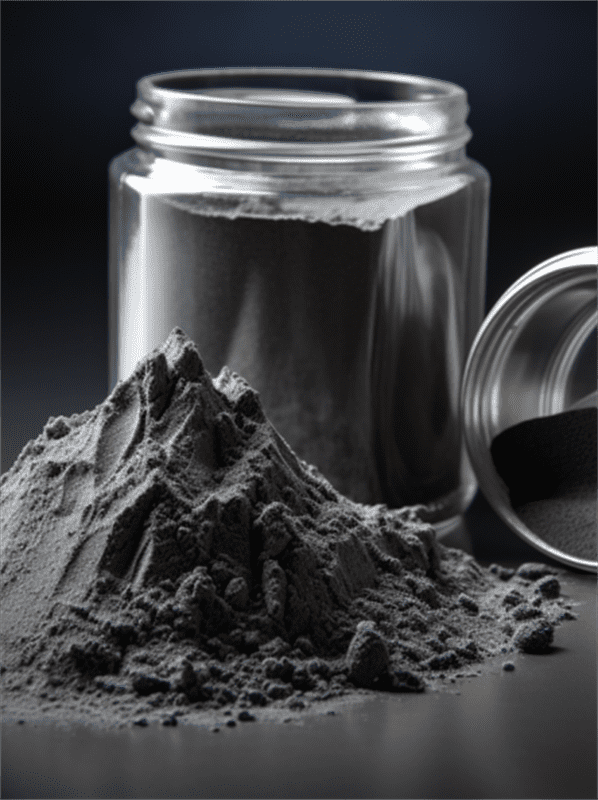
PREGUNTAS FRECUENTES
P: ¿Cuál es la composición típica de los polvos moldeables por inyección?
R: Contienen polvo metálico 80-90%, aglutinante 8-20% y lubricantes 1-2% en peso. Los aglutinantes habituales son cera, PP, PE y PEG.
P: ¿Qué gama de tamaños de polvo se utiliza?
R: Se utilizan polvos de entre 1 y 20 micras. El polvo más fino mejora la densidad, pero puede ser propenso a la aglomeración.
P: ¿Cuánta contracción se produce durante la sinterización?
R: Durante la sinterización en fase líquida se produce una contracción lineal de las piezas de hasta 20%. Se deben tener en cuenta en el diseño de las herramientas.
P: ¿Qué causa las grietas en las piezas moldeadas por inyección de metal sinterizado?
R: Calentamiento no uniforme en hornos, uso de enfriamiento rápido tras la sinterización, mezcla deficiente del polvo y elección de aleaciones quebradizas.
P: ¿Qué opciones de materiales existen para los polvos moldeables por inyección?
R: Aceros inoxidables, aceros para herramientas, aleaciones pesadas de tungsteno, aleaciones de cobre, titanio y aleaciones de titanio, entre otros.
Compartir
MET3DP Technology Co., LTD es un proveedor líder de soluciones de fabricación aditiva con sede en Qingdao, China. Nuestra empresa está especializada en equipos de impresión 3D y polvos metálicos de alto rendimiento para aplicaciones industriales.
Solicite información para obtener el mejor precio y una solución personalizada para su empresa.
Artículos relacionados
Acerca de Met3DP
Actualización reciente
Nuestro producto
CONTACTO
¿Tiene alguna pregunta? ¡Envíenos un mensaje ahora! Atenderemos su solicitud con todo un equipo tras recibir su mensaje.
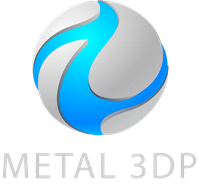
Polvos metálicos para impresión 3D y fabricación aditiva