Fabricación MIM: una guía completa
Índice
Visión general de Fabricación MIM
El moldeo por inyección de metal (MIM) es un proceso de fabricación de pulvimetalurgia que se utiliza para producir piezas metálicas pequeñas y complejas en grandes volúmenes.
Los pasos clave en MIM incluyen:
- Mezclar polvo metálico fino con aglutinante para crear una materia prima
- Inyectar la materia prima en un molde mediante moldeo por inyección de plástico.
- Desligado para eliminar el aglutinante dejando solo el polvo metálico.
- Sinterización para densificar el polvo en un componente metálico sólido.
MIM combina la flexibilidad de diseño del moldeo por inyección de plástico con la resistencia y el rendimiento de los metales mecanizados. Es un proceso rentable para la producción compleja y de gran volumen de piezas pequeñas.
Cómo funciona la fabricación MIM
El proceso de fabricación MIM implica:
- Formulación de una materia prima mezclando y peletizando polvo metálico fino con aglutinantes poliméricos.
- Calentar la materia prima y moldearla por inyección en la forma deseada.
- Eliminación química del aglutinante mediante disolvente o desaglomerado térmico.
- Sinterizar el componente metálico liberado en un horno para producir una pieza completamente densa
- Operaciones de acabado secundario opcionales como mecanizado, taladrado y enchapado.
MIM permite la producción económica de componentes con geometrías complejas, tolerancias estrictas y excelentes propiedades mecánicas.
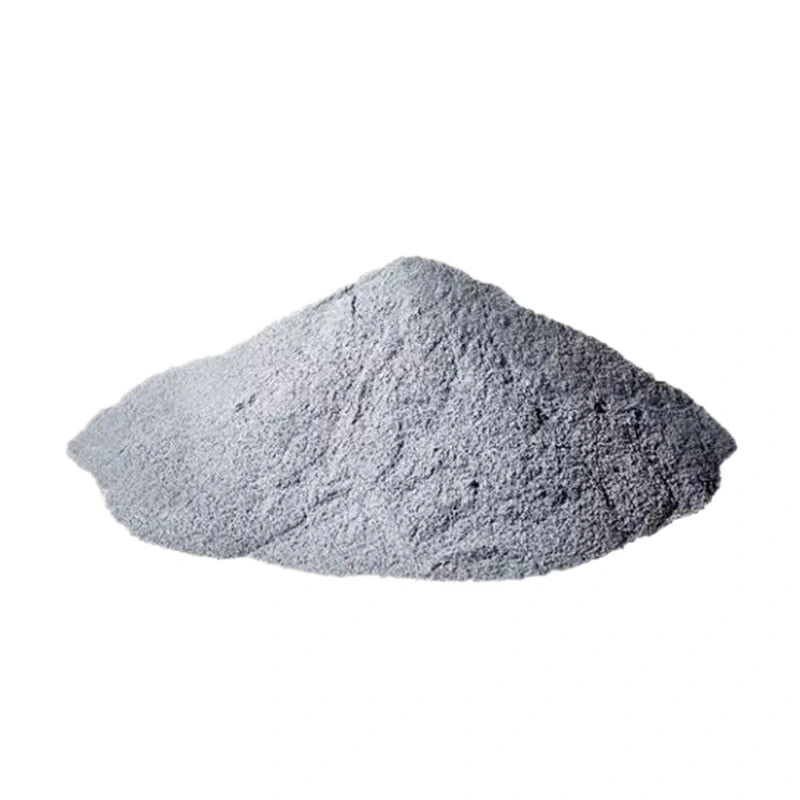
Tipos de metales utilizados en MIM
Se puede procesar una amplia gama de metales con la tecnología MIM:
- Aceros inoxidables: 316L, 17-4PH, 410, 420
- Aceros para herramientas: H13, P20, A2, D2
- Aleaciones magnéticas – Ferritas blandas y duras
- Aleaciones de cobre – Latón, bronce
- Aceros de baja aleación – 4100, 4600
- Superaleaciones – Inconel 625, 718
- Aleaciones pesadas de tungsteno
- Aleaciones de titanio: Ti6Al4V, Ti6Al4V ELI
MIM generalmente es adecuado para cualquier material que pueda sinterizarse a alta densidad. Se prefieren los metales con puntos de fusión inferiores a 1000°C.
Parámetros del proceso de fabricación MIM
Los parámetros de proceso críticos en MIM incluyen:
Desarrollo de materias primas:
- Morfología del polvo, distribución de tamaño.
- Composición aglutinante
- Carga de polvo: normalmente 60-65 vol%
- Proceso de mezcla: temperatura, tiempo, atmósfera.
Moldura:
- Material del molde: se prefiere acero para herramientas P20
- Temperatura, presión y velocidad de inyección.
- Diseño de puerta
- Diseño del sistema de refrigeración.
Desbobinado:
- Desaglomerado con disolvente, térmico o catalítico.
- Temperatura, tiempo y atmósfera de desvinculación.
Sinterización:
- Perfil de temperatura: pasos de desaglomerado y sinterización
- Velocidad de calentamiento, tiempo de sinterización, atmósfera.
- Temperatura y presión de sinterización.
Diseño MIM y consideraciones de piezas
El proceso MIM permite libertad de diseño, pero se deben seguir algunas pautas:
- Espesor de pared: rango posible de 0,3 a 4 mm
- Acabado de la superficie: La sinterización es de alrededor de Ra 1,5 μm.
- Tolerancias dimensionales: ±0,5% es estándar pero se puede lograr ±0,1%
- Evitar el polvo atrapado: sin cavidades internas completamente cerradas
- Ángulos de inclinación: > 1° de ángulo de inclinación preferido
- Contracción de sinterización: Contracción volumétrica aproximada de 20%
- Reducción de defectos: los radios de esquina generosos minimizan las grietas
Las herramientas de simulación avanzadas permiten la optimización virtual del proceso MIM durante el diseño para reducir la prueba y el error.
Beneficios de Fabricación MIM
Las ventajas clave de utilizar MIM incluyen:
- Geometrías complejas y tolerancias estrictas
- Excelentes propiedades mecánicas
- Amplia gama de opciones de materiales
- Altas cantidades de producción a bajo costo.
- Minimiza el desperdicio: proceso casi en forma neta
- Mecanizado y acabado reducidos
- Integración de componentes y consolidación de piezas.
- Proceso automatizado adecuado para operación sin luces
- Más ecológico que el mecanizado
- Escalable desde prototipos hasta producción completa
Los beneficios hacen que MIM sea adecuado para la fabricación rentable de componentes metálicos de precisión en grandes volúmenes en todas las industrias.
Limitaciones y desafíos de MIM
Algunas limitaciones asociadas con MIM:
- Tamaño limitado: normalmente <45 g de masa terminada por pieza
- Restringido a metales capaces de sinterizarse a alta densidad.
- Se requiere una amplia experiencia en la formulación de materias primas
- Costos iniciales para el desarrollo de moldes y procesos.
- Secciones rectas y esquinas afiladas propensas a agrietarse
- Mayor plazo de entrega en comparación con otros procesos
- A menudo se requiere posprocesamiento para lograr las propiedades finales.
- Falta de libertad de diseño en algunas características como hilos.
- El mecanizado secundario puede resultar complicado en metales sinterizados
Con una materia prima adecuada y un diseño de procesos adaptado a la aplicación, estos desafíos se pueden superar para utilizar todo el potencial de la tecnología MIM.
Aplicaciones de piezas fabricadas MIM
MIM encuentra un uso generalizado en los siguientes sectores:
Automoción: Hardware de bloqueo, sensores, sistema de combustible y componentes del motor.
Aeroespacial: Impulsores, boquillas, válvulas, sujetadores.
Médico: Implantes dentales, mangos de bisturí, instrumentos ortopédicos.
Armas de fuego: Gatillos, cargadores, correderas, martillos.
Relojes: Cajas, eslabones de pulsera, cierres y hebillas.
Eléctrico: Conectores y marcos conductores para mayor confiabilidad
Los tamaños de piezas típicos oscilan entre 0,1 gramos y 110 gramos, con los mayores volúmenes de producción comercial en conectores, sujetadores, instrumentos quirúrgicos y aparatos de ortodoncia.
Análisis de costos de fabricación MIM
Los costos de fabricación de MIM incluyen:
- Desarrollo de materias primas – Formulación, mezcla, caracterización.
- fabricación de moldes – Mecanizado de moldes de alta precisión
- máquina MIM – Gran inversión en bienes de capital
- Operación – Mano de obra, servicios públicos, consumibles.
- Operaciones secundarias – Desaglutinado, sinterizado, acabado.
- Utilización de materiales – El polvo metálico representa alrededor de 60% del costo total.
- Herramientas consumibles – Múltiples cavidades de molde para permitir un alto volumen.
- Volumen de producción – Costos de instalación amortizados sobre el volumen total
- Ratio de compra por vuelo – Sólo 2-4 veces en comparación con otros procesos de PM
- Optimización del diseño – Geometrías simples con mecanizado mínimo.
Para grandes volúmenes de producción, MIM ofrece costos muy favorables a altas tasas de fabricación con una excelente utilización del material y capacidades casi netas.
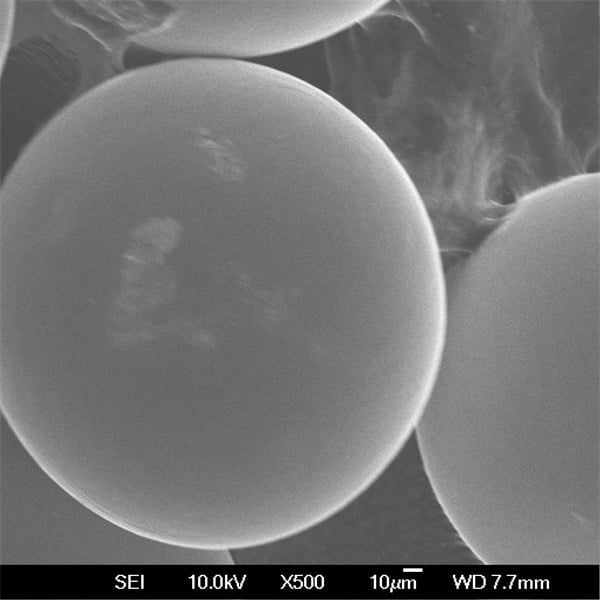
Seleccionando un Fabricación MIM Pareja
Factores clave a la hora de seleccionar un proveedor MIM:
- Experiencia demostrada y años de experiencia con MIM.
- Cartera de materiales: gama de opciones de acero inoxidable, acero para herramientas y superaleaciones
- Certificaciones de calidad: ISO 9001, ISO 13485 preferiblemente
- Capacidades de procesamiento secundario: mecanizado, tratamiento térmico, acabado de superficies.
- Estrictos procedimientos de control de calidad de procesos y productos.
- Capacidades de I+D para la formulación de materias primas y el desarrollo de procesos.
- Simulación de flujo de moldes y otros conocimientos especializados en análisis de diseño.
- Habilidades de gestión de programas para respaldar los proyectos de los clientes.
- Capacidad escalable capaz de crecer con las necesidades de producción.
- Precios competitivos con acuerdos de varios años.
- Ubicación que permite una estrecha colaboración y protección de la propiedad intelectual
Seleccionar un productor de MIM establecido con un enfoque especializado en MIM proporcionará los mejores resultados en comparación con un taller de mecanizado de metales CNC general.
Pros y contras del mecanizado MIM frente al mecanizado CNC
Ventajas de MIM:
- Excelente precisión dimensional y repetibilidad
- Geometrías complejas inalcanzables mediante mecanizado
- Casi forma neta con mínimo desperdicio de material.
- Escala eficientemente a volúmenes de producción muy altos
- El proceso automatizado permite el funcionamiento 24 horas al día, 7 días a la semana
- Plazos de entrega más cortos una vez configurado
- Costos de piezas significativamente más bajos en grandes volúmenes
- Las propiedades igualan o superan a los metales mecanizados.
Desventajas de MIM:
- Altos costos de instalación inicial para la materia prima y el molde.
- Capacidades de tamaño limitado
- Libertad de diseño restringida en algunas características.
- Menores cantidades de producción inicial son ineficientes
- Se requiere una amplia experiencia en la formulación de materias primas
- Es posible que aún sean necesarias operaciones de acabado secundarias.
- Plazos de entrega más largos y menor calidad para los prototipos iniciales
Para piezas metálicas pequeñas y complejas producidas en volúmenes muy elevados, MIM se convierte en el método de fabricación más eficiente en términos de tiempo y costes.
Comparación entre MIM y la impresión 3D en metal
Principales diferencias entre MIM y la impresión 3D:
Parámetro | MIM | Impresión 3D |
---|---|---|
Proceso | Moldeo por inyección de aglutinante + sinterización | Fusión o unión de lecho de polvo |
Materiales | Amplia gama de aleaciones | Opciones de material limitadas |
Tamaño de la pieza | < 45 gramos | Hasta varios kg |
Precisión | Excelente, ±0,5% | Moderado, ±1% |
Acabado superficial | Muy buena | Media a mala |
Escala de producción | De 10.000 a millones | Creación de prototipos para volúmenes medios. |
Costo por pieza | Muy bajo | Media a alta |
acabado secundario | Puede ser requerido | Generalmente requerido |
Plazo de entrega | Más tiempo para el desarrollo del proceso. | Prototipos más rápidos pero producción en serie más lenta |
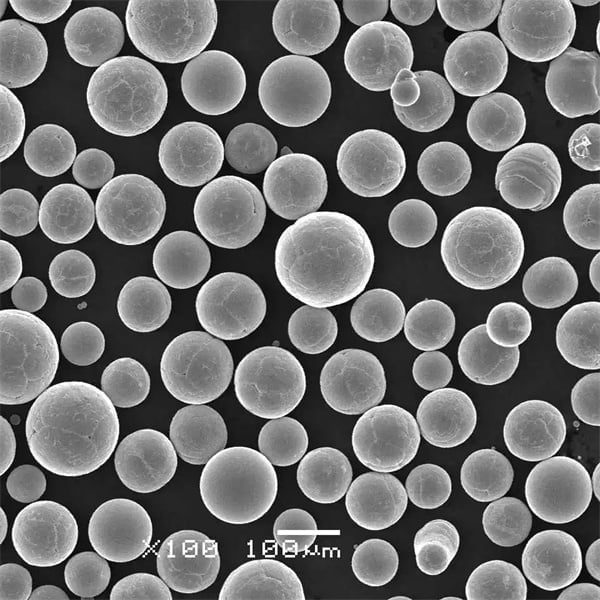
PREGUNTAS FRECUENTES
¿Cuál es la capacidad de tolerancia típica para la fabricación MIM?
MIM puede lograr de manera confiable tolerancias dimensionales de ±0,5% con procesos avanzados capaces de alcanzar una tolerancia de ±0,1% para componentes de precisión pequeños.
¿Cuáles son las composiciones comunes de materia prima MIM?
Las materias primas MIM típicas consisten en una carga de polvo metálico 60-65% con un aglutinante 35-40% que comprende polímeros como polipropileno, polietileno y poliestireno. Las ceras ayudan a mejorar el flujo del polvo.
¿Puede MIM fabricar piezas en múltiples materiales?
Sí, MIM puede producir estructuras compuestas y graduadas moldeando por inyección diferentes materias primas en cada cavidad del molde o utilizando aglutinantes con diferentes puntos de fusión.
¿Qué tamaño de pieza moldeada se puede lograr con MIM?
Las molduras MIM suelen estar restringidas a piezas de menos de 45 gramos de masa y dimensiones inferiores a 50 mm. Los componentes más grandes o más pesados resultan difíciles de llenar y densificar suficientemente.
¿Cómo se compara MIM con la fundición a presión para componentes metálicos pequeños?
MIM proporciona mayor precisión dimensional y resistencia del material, pero la fundición a presión tiene tiempos de ciclo más rápidos. MIM es más adecuado para geometrías complejas, mientras que la fundición a presión es preferible para formas más simples.
Compartir
MET3DP Technology Co., LTD es un proveedor líder de soluciones de fabricación aditiva con sede en Qingdao, China. Nuestra empresa está especializada en equipos de impresión 3D y polvos metálicos de alto rendimiento para aplicaciones industriales.
Solicite información para obtener el mejor precio y una solución personalizada para su empresa.
Artículos relacionados
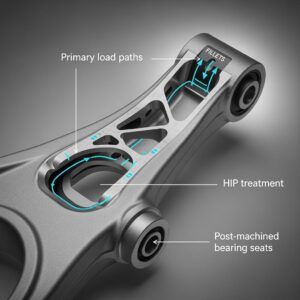
Metal 3D Printing for U.S. Automotive Lightweight Structural Brackets and Suspension Components
Leer Más "Acerca de Met3DP
Actualización reciente
Nuestro producto
CONTACTO
¿Tiene alguna pregunta? ¡Envíenos un mensaje ahora! Atenderemos su solicitud con todo un equipo tras recibir su mensaje.