Custom Bone Screws via Metal 3D Printing: A New Era in Orthopedic Solutions
목차
Introduction – Revolutionizing Orthopedics with Additive Manufacturing
The landscape of orthopedic surgery is undergoing a significant transformation, driven by advancements in materials science and innovative manufacturing technologies. Among these groundbreaking developments, metal additive manufacturing, commonly known as metal 3D 프린팅, stands out as a revolutionary force. This technology is enabling the creation of highly customized medical implants, and one area where its impact is particularly profound is the production of custom bone screws.
Traditional bone screws, often mass-produced in standard sizes and designs, may not always provide the optimal fit and stability required for complex orthopedic procedures. Metal 3D printing overcomes these limitations by allowing for the fabrication of bone screws tailored to the unique anatomical requirements of each patient. Utilizing high-performance metal powders like Ti-6Al-4V ELI, this advanced manufacturing method enables intricate geometries and porous structures that enhance osseointegration and improve patient outcomes.
에서 Metal3DP, we are at the forefront of this revolution, providing cutting-edge metal 3D printing solutions and high-quality metal powders. Our industry-leading Selective Electron Beam Melting (SEBM) printers, developed in our state-of-the-art facility in Qingdao, China, offer unparalleled accuracy and reliability for producing mission-critical medical devices like custom bone screws. We also manufacture a comprehensive range of advanced metal powders, including Ti-6Al-4V ELI, specifically optimized for additive manufacturing to ensure the highest quality and performance of the final implant.
What are Custom Bone Screws Used For? – Diverse Applications in Orthopedic Surgery
Bone screws are fundamental components in a wide array of orthopedic surgical procedures, serving various critical functions in fracture fixation, joint reconstruction, and spinal fusion. Traditionally, surgeons have relied on a limited selection of standardized screw designs and sizes. However, the advent of custom bone screws produced via metal 3D printing opens up a new realm of possibilities, allowing for tailored solutions that address the specific needs of each patient and surgical scenario.
Here are some key applications of custom bone screws in orthopedic surgery:
- Complex Fracture Fixation: In cases of intricate fractures with irregular bone fragments, standard screws may not provide adequate stability. Custom-designed screws can precisely match the fracture lines and bone morphology, ensuring optimal compression and promoting faster healing.
- Revision Surgeries: Patients undergoing revision surgeries often present with unique anatomical challenges due to previous implants or bone resorption. Custom screws can be designed to accommodate these altered anatomies, providing secure fixation where standard implants may fail.
- Small Bone Fixation: Procedures involving small bones in the hand, foot, or face require precise and often miniaturized fixation devices. Metal 3D printing allows for the creation of custom screws with specific dimensions and thread patterns suitable for these delicate structures.
- Spinal Fusion: In spinal fusion procedures, bone screws play a crucial role in stabilizing the vertebrae while new bone growth occurs. Custom screws can be designed with optimized thread profiles and lengths to achieve maximum purchase and stability in the patient’s unique spinal anatomy.
- Joint Reconstruction: While larger components like hip and knee replacements often receive the most attention regarding customization, bone screws used in these procedures can also benefit from patient-specific designs, ensuring secure fixation of辅助部件 and improved long-term stability.
- Pediatric Orthopedics: Children’s bones have unique growth patterns and anatomical considerations. Custom bone screws can be designed to accommodate these specific needs, ensuring effective fixation while minimizing the risk of growth plate disruption.
- Oncology: In cases where bone tumors have been resected, custom bone screws can be used in conjunction with bone grafts or other reconstruction techniques to provide immediate stability and support the healing process.
By leveraging the design freedom offered by metal 3D printing, surgeons can utilize custom bone screws to achieve more precise, stable, and anatomically congruent fixation, ultimately leading to improved surgical outcomes and enhanced patient recovery. Metal3DP is proud to offer solutions that empower medical professionals with these advanced capabilities. Our 금속 3D 프린팅 서비스 및 high-performance Ti-6Al-4V ELI powder are ideally suited for producing custom bone screws that meet the most demanding requirements of modern orthopedic surgery.
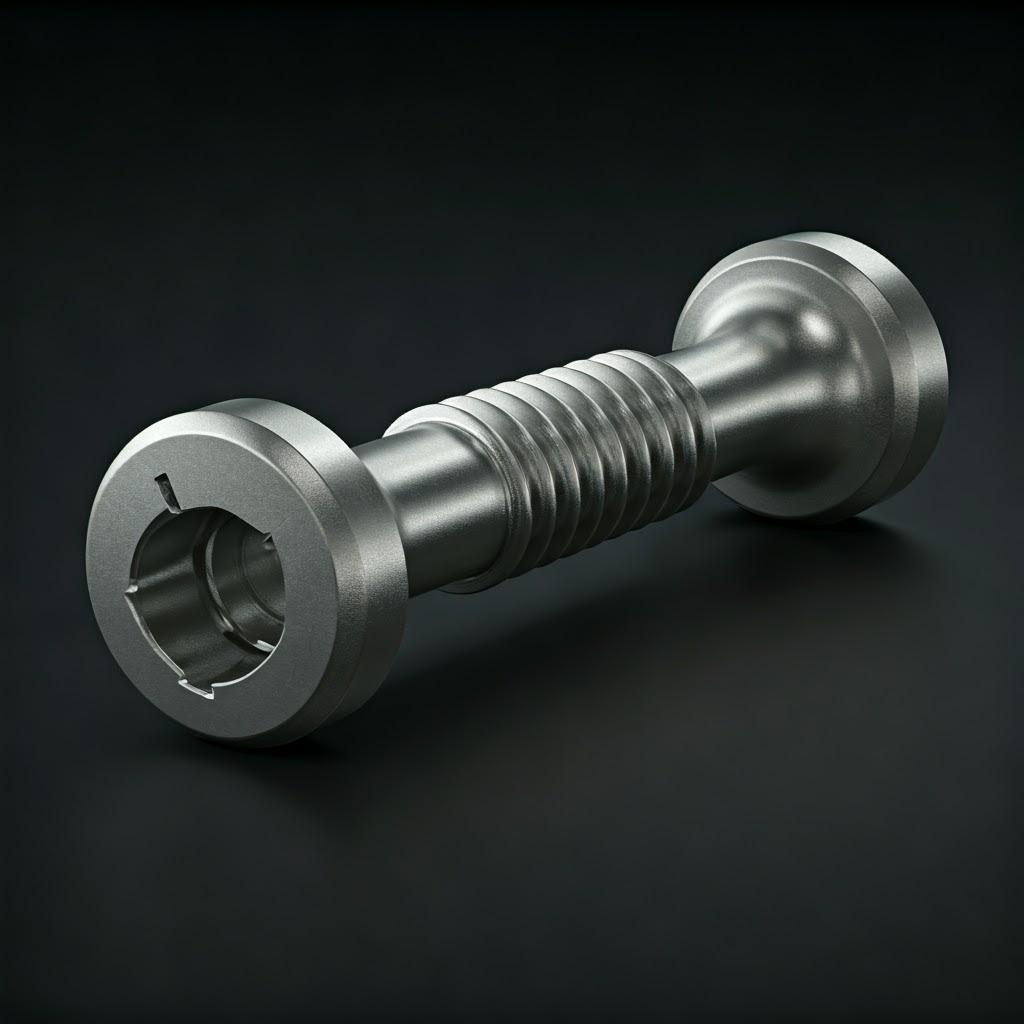
Why Use Metal 3D Printing for Custom Bone Screws? – Advantages Over Traditional Manufacturing
The shift towards metal 3D printing for the production of custom bone screws represents a significant advancement over traditional manufacturing methods, offering a multitude of advantages for both surgeons and patients. Conventional techniques, such as machining, often involve subtractive processes that can be wasteful, time-consuming, and limited in the complexity of geometries they can produce. Metal 3D printing, on the other hand, builds parts layer by layer from metal powder, enabling unprecedented design freedom, material efficiency, and the creation of patient-specific implants.
Here are the key benefits of using metal 3D printing for custom bone screws:
- Unparalleled Patient-Specific Anatomical Fit: Perhaps the most significant advantage is the ability to create screws that perfectly match a patient’s unique bone anatomy. By utilizing CT or MRI scans, intricate digital models can be generated, and screws can be designed to the exact dimensions and contours required for optimal fixation. This level of customization is simply not achievable with traditional manufacturing methods.
- Design Freedom for Complex Geometries: Metal 3D printing allows for the creation of complex internal and external features that can enhance the functionality of bone screws. This includes optimized thread designs for increased pull-out strength, porous structures to promote osseointegration (bone ingrowth), and internal channels for potential drug delivery. These intricate designs can be tailored to specific clinical needs.
- Enhanced Osseointegration through Porous Structures: A key advantage of 3D-printed bone screws is the ability to incorporate porous structures into the implant design. These porous regions mimic the trabecular structure of natural bone, encouraging bone cells to grow into the implant. This biological fixation leads to stronger, more stable integration of the screw with the surrounding bone, reducing the risk of loosening and improving long-term outcomes. Metal3DP’s SEBM technology excels at creating these intricate porous structures with high precision.
- Reduced Surgical Time and Complexity: The precise fit of custom bone screws can streamline surgical procedures. Surgeons spend less time adapting or modifying implants, leading to shorter operating times, reduced anesthesia exposure for patients, and potentially lower risks of complications.
- 재료 효율성 및 낭비 감소: Unlike subtractive manufacturing processes that remove material to create the final shape, metal 3D printing only uses the material needed for the part. This significantly reduces material waste, making it a more sustainable and cost-effective manufacturing approach, especially for complex, patient-specific designs.
- Faster Turnaround Times for Custom Implants: While traditional manufacturing of custom implants can be lengthy, metal 3D printing offers the potential for faster turnaround times. Once the digital design is finalized, the printing process can be completed relatively quickly, allowing for more timely delivery of patient-specific screws.
- Integration of Advanced Materials: Metal 3D printing is compatible with a wide range of high-performance metal powders, including Ti-6Al-4V ELI, which is known for its excellent biocompatibility, strength, and corrosion resistance – crucial properties for medical implants. Metal3DP offers a portfolio of these advanced materials, ensuring the production of high-quality, reliable bone screws.
By embracing metal 3D printing, the orthopedic industry can move beyond the limitations of standard implants and enter an era of personalized medicine, where custom bone screws contribute to more successful surgeries and improved patient well-being. Metal3DP에 문의하세요 today to learn more about how our advanced additive manufacturing solutions can power your organization’s goals in producing cutting-edge medical devices.
Recommended Materials and Why They Matter – The Superiority of Ti-6Al-4V ELI
The choice of material is paramount in the manufacturing of medical implants, as it directly impacts biocompatibility, mechanical properties, and long-term performance. 대상 custom bone screws produced via metal 3D printing, Ti-6Al-4V ELI (Extra Low Interstitials) stands out as the recommended powder due to its exceptional combination of characteristics that are crucial for orthopedic applications.
Ti-6Al-4V ELI is a specific grade of titanium alloy composed primarily of titanium, along with aluminum (6%) and vanadium (4%). The “ELI” designation signifies that this particular variant has significantly lower levels of interstitial elements such as oxygen, nitrogen, and carbon compared to standard Ti-6Al-4V. This reduction in interstitials results in enhanced ductility, improved fracture toughness, and superior biocompatibility, making it particularly well-suited for permanent medical implants that will reside within the human body for extended periods.
Here’s a detailed look at why Ti-6Al-4V ELI is the preferred material for 3D-printed custom bone screws:
- Exceptional Biocompatibility: Titanium and its alloys are renowned for their excellent biocompatibility, meaning they are well-tolerated by the human body and do not typically cause adverse reactions or implant rejection. The ELI grade further enhances this biocompatibility by minimizing impurities that could potentially trigger inflammation or other biological responses. This is critical for bone screws that need to integrate seamlessly with the surrounding bone tissue.
- 높은 중량 대비 강도 비율: Ti-6Al-4V ELI possesses a remarkable strength-to-weight ratio. It is significantly stronger than pure titanium while being considerably lighter than many other metallic implant materials like stainless steel or cobalt-chromium alloys. This high strength ensures that the bone screw can withstand the stresses and loads experienced within the body, providing stable fixation without adding unnecessary bulk.
- 뛰어난 내식성: The human body is a corrosive environment due to the presence of bodily fluids and salts. Titanium alloys, including Ti-6Al-4V ELI, exhibit outstanding resistance to corrosion. This property is essential for the long-term integrity of bone screws, preventing degradation of the implant material and the release of potentially harmful ions into the surrounding tissues.
- Low Modulus of Elasticity (Compared to Other Metals): While still a rigid material, titanium’s modulus of elasticity is closer to that of natural bone compared to stiffer metals like stainless steel. This closer match in stiffness helps to reduce stress shielding, a phenomenon where a significantly stiffer implant bears too much of the load, potentially leading to bone resorption around the implant.
- Osseointegration Potential: Titanium and its alloys have the inherent ability to promote osseointegration, the direct bonding of bone to the implant surface. This process is crucial for the long-term stability of bone screws. Furthermore, as mentioned earlier, the ability to create porous structures with Ti-6Al-4V ELI through metal 3D printing can significantly enhance osseointegration.
- Proven Track Record in Medical Applications: Ti-6Al-4V ELI has a long and successful history of use in various medical implants, including hip and knee replacements, dental implants, and spinal fixation devices. Its biocompatibility and mechanical properties are well-documented and supported by extensive research and clinical experience.
Metal3DP recognizes the critical importance of material selection for medical implants. That’s why we offer high-quality Ti-6Al-4V ELI powder specifically optimized for our SEBM 3D printing technology. Our advanced powder making system ensures that our 티타늄 분말 possess high sphericity and excellent flowability, which are essential for producing dense, high-quality custom bone screws with superior mechanical properties. 다음을 선택하면 Metal3DP 및 Ti-6Al-4V ELI, you are selecting a trusted solution for creating reliable and biocompatible orthopedic implants. Sources and related content
Design Considerations for Additive Manufacturing of Custom Bone Screws
The transition from traditional manufacturing to metal 3D printing opens up exciting possibilities for the design of custom bone screws. However, to fully leverage the capabilities of additive manufacturing and ensure the production of functional and high-quality implants, specific design considerations must be taken into account. Optimizing the screw geometry, wall thickness, and support requirements are crucial for successful printing and the long-term performance of the device.
Here are key design considerations for additively manufactured custom bone screws:
- Thread Design Optimization: The thread profile is critical for the screw’s holding power and stability within the bone. Metal 3D printing allows for the creation of complex and customized thread designs that can:
- Increase Pull-Out Strength: Variable thread pitch or specialized thread forms can enhance the screw’s resistance to being pulled out of the bone.
- Improve Insertion Torque: Optimizing the thread angle and sharpness can reduce the torque required for insertion, minimizing stress on the bone.
- Enhance Osseointegration: Micro-features or porous surfaces on the threads can promote better bone ingrowth and long-term fixation.
- Customization for Anatomical Fit: The primary advantage of 3D printing is the ability to tailor the screw’s overall shape and dimensions to the patient’s specific anatomy. This includes:
- Variable Length and Diameter: Screws can be designed with precisely the required length and diameter for the specific surgical site.
- Curved or Contoured Designs: For complex anatomical regions, screws can be designed with curvature to better match the bone’s surface.
- Fenestrations or Cannulations: Internal channels or holes can be incorporated for potential drug delivery or guidance during surgery.
- Incorporation of Porous Structures for Osseointegration: As discussed earlier, integrating porous regions within the screw body or along the threads is a significant benefit of metal 3D printing. Design considerations for these features include:
- Controlled Pore Size and Interconnectivity: The size and interconnectedness of the pores influence bone cell infiltration and vascularization. Optimal pore sizes typically range from 100 to 500 micrometers.
- Targeted Porosity: Porous regions can be strategically placed in areas where osseointegration is most critical for stability.
- Mechanical Strength Considerations: The design of the porous structure must balance the need for bone ingrowth with maintaining the overall mechanical strength of the screw.
- Wall Thickness and Structural Integrity: The wall thickness of hollow or partially hollow screw designs must be carefully considered to ensure sufficient mechanical strength to withstand the forces encountered during and after surgery. Finite element analysis (FEA) can be a valuable tool for optimizing wall thickness and structural integrity based on anticipated loads.
- Support Structure Optimization: During the metal 3D printing process, support structures are often required to prevent warping, sagging, or collapse of overhanging features. Design considerations for supports include:
- Minimizing Support Volume: Excessive support material increases printing time and post-processing effort. Optimizing the design to minimize the need for supports is crucial.
- Ease of Support Removal: The design should facilitate easy and clean removal of support structures without damaging the delicate features of the bone screw.
- Support Placement: Strategic placement of supports can minimize their impact on critical surfaces and ensure dimensional accuracy.
- Surface Finish Considerations: The surface finish of the bone screw can influence osseointegration and friction during insertion. Design considerations include:
- Roughness for Osseointegration: A slightly rough surface can promote better bone cell attachment. Surface treatments or specific printing parameters can be used to achieve the desired roughness.
- Smoothness for Insertion: Smooth surfaces in certain areas, such as the screw head, can facilitate easier insertion.
- Minimizing Stress Concentrations: Sharp corners or abrupt changes in geometry can create stress concentrations, potentially leading to fatigue failure under load. The design should incorporate smooth transitions and fillets to distribute stress more evenly.
- 제조 가능성을 위한 디자인(DFM): It is essential to consider the limitations and capabilities of the chosen metal 3D printing technology (e.g., SEBM) during the design process. Features that are too small or intricate may be difficult to print accurately. Collaboration with experienced metal 3D printing service providers like Metal3DP can help optimize designs for manufacturability.
By carefully considering these design factors, engineers and surgeons can harness the full potential of metal 3D printing to create custom bone screws that offer superior anatomical fit, enhanced osseointegration, and improved long-term performance, ultimately benefiting patients undergoing orthopedic procedures. Our team at Metal3DP possesses the expertise and technology to assist in the design and manufacturing of these advanced medical devices.

Tolerance, Surface Finish, and Dimensional Accuracy of 3D-Printed Bone Screws
In the realm of medical implants, particularly load-bearing devices like custom bone screws, achieving precise tolerances, appropriate surface finishes, and high dimensional accuracy is paramount. These factors directly influence the implant’s fit, stability, functionality, and long-term success within the patient’s body. Metal 3D printing technologies, such as Selective Electron Beam Melting (SEBM) utilized by Metal3DP, are capable of achieving impressive levels of precision, although careful process control and post-processing may be required to meet the stringent demands of orthopedic applications.
Here’s a breakdown of what can be expected regarding tolerance, surface finish, and dimensional accuracy for 3D-printed bone screws:
Tolerance:
- 정의: Tolerance refers to the allowable variation in a specified dimension of a manufactured part. It defines the acceptable upper and lower limits for a given measurement.
- Capabilities of Metal 3D Printing: Metal 3D printing technologies like SEBM can typically achieve tolerances in the range of ±0.1 to ±0.2 mm (±0.004 to ±0.008 inches) for overall dimensions. However, tighter tolerances may be achievable for smaller features or with optimized printing parameters and post-processing.
- Factors Influencing Tolerance: Several factors can affect the achievable tolerance in metal 3D printing, including:
- Machine Accuracy: The inherent accuracy and calibration of the 3D printer. Metal3DP’s industry-leading SEBM printers are known for their high accuracy.
- 머티리얼 속성: The thermal expansion and contraction behavior of the metal powder during the printing process.
- 파트 지오메트리: Complex geometries with significant overhangs or thin features can be more challenging to print with tight tolerances.
- 빌드 오리엔테이션: The orientation of the part on the build platform can influence dimensional accuracy in different directions.
- 후처리: Secondary processes like machining or grinding can be used to achieve tighter tolerances on critical surfaces.
- Implications for Bone Screws: Precise tolerances are crucial for ensuring proper fit and engagement of the screw threads with the bone. Inaccuracies can lead to reduced stability, increased stress on the surrounding bone, and potential implant failure.
표면 마감:
- 정의: Surface finish refers to the microscopic texture of a part’s surface, often quantified by parameters like surface roughness (Ra).
- As-Built Surface Finish in Metal 3D Printing: Metal 3D-printed parts typically have a rougher surface finish compared to machined parts. The surface roughness is influenced by the size of the metal powder particles and the layer-by-layer building process. Ra values for as-built metal 3D-printed parts can range from 5 to 20 µm (200 to 800 µin) or even higher, depending on the technology and parameters.
- 표면 마감에 영향을 미치는 요소:
- 파우더 입자 크기: Finer powders generally result in smoother surface finishes. Metal3DP’s advanced powder making system produces high-quality metal powders with controlled particle size distribution.
- 레이어 두께: Thinner layers can lead to smoother surfaces but may increase build time.
- 인쇄 매개변수: Laser or electron beam power and scan speed can affect the surface finish.
- 지원 구조: The points where support structures contact the part can leave surface marks.
- Post-Processing for Improved Surface Finish: For medical implants like bone screws, post-processing techniques are often employed to achieve the desired surface finish. These techniques include:
- Media Blasting: Using abrasive media to remove loose powder and reduce surface roughness.
- 연마: Mechanical or chemical polishing to achieve smoother surfaces.
- 전기 연마: Using an electrochemical process to smooth metallic surfaces.
- Surface Coatings: Applying biocompatible coatings that can also influence surface roughness and promote osseointegration.
- Implications for Bone Screws: The surface finish of a bone screw can affect its insertion characteristics, friction with the bone, and the rate of osseointegration. A slightly rough surface is often preferred for promoting bone ingrowth.
치수 정확도:
- 정의: Dimensional accuracy refers to how closely the actual dimensions of a manufactured part match the intended dimensions in the design.
- Achievable Accuracy in Metal 3D Printing: Metal 3D printing can achieve good dimensional accuracy, but it is influenced by the factors mentioned under tolerance. Overall deviations from the nominal dimensions can be within ±0.2 to ±0.5 mm (±0.008 to ±0.020 inches) for larger parts, with better accuracy for smaller features.
- Importance for Bone Screws: Accurate dimensions are critical for ensuring proper fit within the prepared bone site and for the correct engagement of the screw head with surgical instruments. Misaligned or poorly fitting screws can compromise the stability of the fixation and potentially lead to surgical complications.
Metal3DP’s Commitment to Quality:
에서 Metal3DP, we understand the critical importance of tolerance, surface finish, and dimensional accuracy for medical implants. Our 업계를 선도하는 SEBM 프린터 are operated by experienced professionals who meticulously control the printing process to maximize precision. Furthermore, we offer a range of post-processing services to achieve the specific requirements for custom bone screws, ensuring that they meet the highest standards of quality and performance. We work closely with our clients to understand their specific 1 needs and deliver implants with the required level of precision for successful orthopedic outcomes.
Post-Processing Requirements for 3D-Printed Custom Bone Screws
While metal 3D printing offers significant advantages in creating complex geometries for custom bone screws, the as-printed parts often require several post-processing steps to achieve the final desired properties, surface finish, and dimensional accuracy necessary for medical applications. These post-processing procedures are crucial for ensuring the safety, efficacy, and long-term performance of the implants.
Here are common post-processing requirements for 3D-printed custom bone screws:
- Powder Removal: After the printing process, loose metal powder remains adhered to the surface and within any internal channels or porous structures of the bone screw. Thorough removal of this residual powder is essential to prevent contamination and ensure the proper functioning of the implant. Techniques used for powder removal include:
- Brushing and Air Blasting: For external surfaces and easily accessible internal features.
- Ultrasonic Cleaning: To dislodge powder from intricate geometries and porous structures.
- Vacuuming: To extract loose powder from internal cavities.
- 지원 구조 제거: As discussed earlier, support structures are often necessary during printing to prevent deformation. These supports must be carefully removed without damaging the delicate features of the bone screw. Methods for support removal include:
- Manual Breakaway: For designs where supports are intentionally weakened at the contact points.
- 가공: Using CNC machining to precisely remove supports from critical surfaces.
- 와이어 EDM(방전 가공): For removing supports in hard-to-reach areas or for complex geometries.
- 열처리: Heat treatment is a critical step to relieve internal stresses that may have built up during the rapid heating and cooling cycles of the 3D printing process. It also helps to optimize the mechanical properties of the Ti-6Al-4V ELI material, such as strength, ductility, and fatigue resistance. Common heat treatment processes for titanium alloys include:
- Stress Relieving: To reduce residual stresses and prevent distortion.
- Annealing: To improve ductility and reduce hardness.
- Solution Treatment and Aging: To achieve optimal strength and toughness.
- 표면 마감: As mentioned previously, the as-built surface finish of 3D-printed parts may not be suitable for medical implants. Various post-processing techniques are employed to achieve the desired surface roughness for osseointegration and a smooth finish in other critical areas:
- Media Blasting: To remove surface oxides and reduce roughness.
- Polishing (Mechanical or Chemical): To create a smoother surface.
- 전기 연마: To achieve a bright, smooth, and corrosion-resistant surface.
- CNC 가공: In some cases, CNC machining may be required to achieve tighter tolerances on critical dimensions, such as the screw threads or the head features that interface with surgical instruments. This hybrid manufacturing approach combines the design flexibility of 3D printing with the precision of traditional machining.
- Cleaning and Sterilization: Before implantation, the custom bone screws must undergo rigorous cleaning and sterilization processes to remove any remaining contaminants and ensure they are safe for patient use. Standard medical device sterilization methods, such as autoclaving or gamma irradiation, are typically employed.
- Inspection and Quality Control: Throughout the post-processing steps, rigorous inspection and quality control procedures are essential to verify that the bone screws meet the required dimensional accuracy, surface finish, and material properties. This may involve:
- Coordinate Measuring Machine (CMM) inspection: For precise dimensional measurements.
- Surface roughness testing: To quantify the surface finish.
- Non-destructive testing (NDT): Such as dye penetrant inspection or ultrasonic testing, to detect any internal defects.
- Material testing: To verify the mechanical properties of the heat-treated material.
- 코팅(옵션): In some cases, biocompatible coatings may be applied to the surface of the bone screw to further enhance osseointegration or provide antimicrobial properties.
Metal3DP’s Comprehensive Post-Processing Services:
에서 Metal3DP, we offer a comprehensive suite of post-processing services specifically tailored for metal 3D-printed medical devices, including custom bone screws. Our experienced team utilizes advanced equipment and adheres to strict quality control standards to ensure that our products meet the most demanding requirements of the medical industry. From meticulous powder removal and support removal to precise CNC machining and biocompatible surface finishing, we provide end-to-end solutions that deliver high-quality, ready-to-use medical implants. Our commitment to quality extends to rigorous cleaning, sterilization, and inspection procedures, ensuring the safety and efficacy of every 3D-printed bone screw we produce.
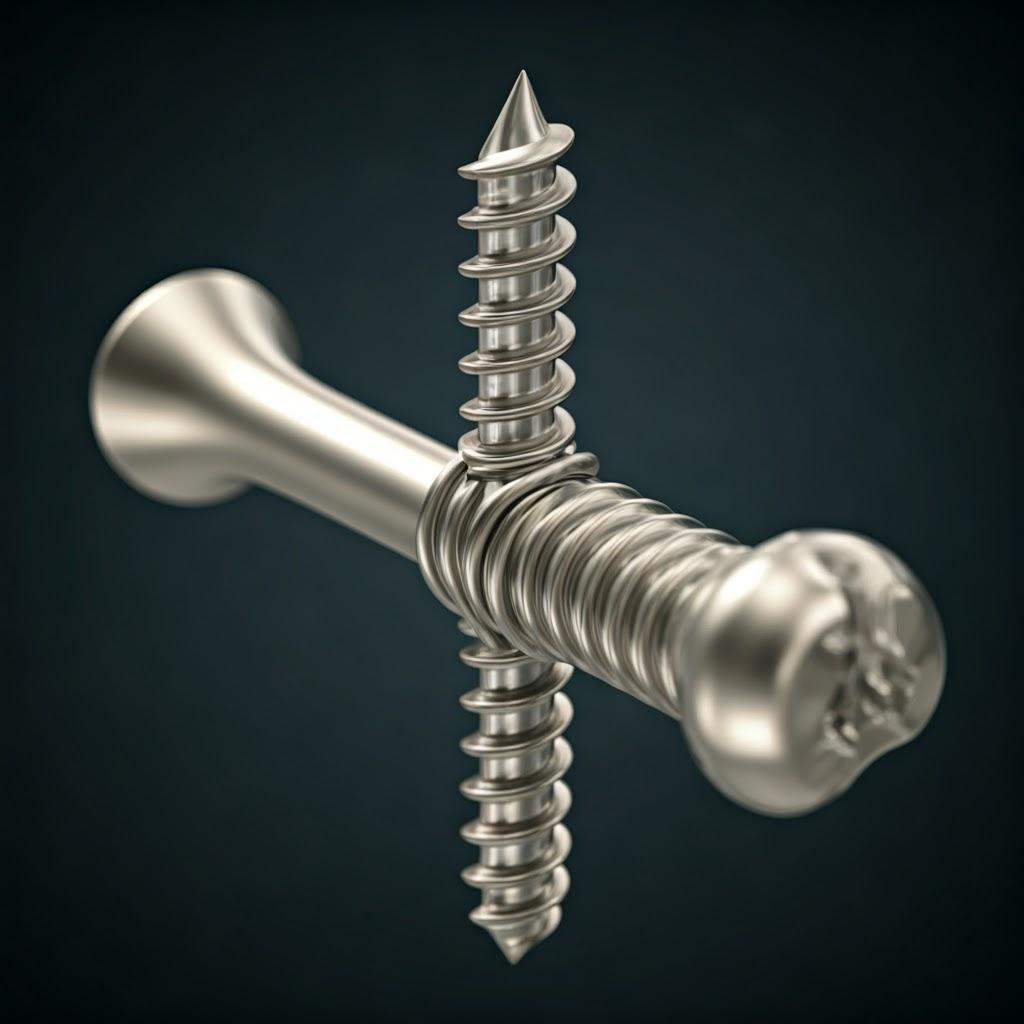
Common Challenges and How to Avoid Them in 3D Printing Bone Screws
While metal 3D printing offers numerous advantages for creating custom bone screws, several challenges can arise during the design and manufacturing process. Understanding these potential issues and implementing strategies to avoid them is crucial for achieving high-quality, functional medical implants.
Here are some common challenges in 3D printing bone screws and how to mitigate them:
- Warping and Distortion: Thermal stresses during the printing process can lead to warping or distortion of the bone screw, particularly for complex geometries or thin-walled sections.
- How to Avoid: Optimize part orientation on the build platform to minimize stress buildup. Employ appropriate support structures to anchor the part. Carefully control printing parameters and consider preheating the build platform. Utilize stress-relieving heat treatments post-printing.
- Support Removal Difficulties: Removing support structures from intricate features or delicate areas of the bone screw can be challenging and may risk damaging the part’s surface.
- How to Avoid: Design self-supporting geometries whenever possible. Optimize support placement and minimize contact areas. Utilize breakaway supports or dissolvable support materials (if compatible with the chosen metal and printer). Employ specialized support removal tools and techniques.
- Porosity and Internal Defects: Incomplete fusion of metal powder layers can result in porosity or internal voids within the printed bone screw, compromising its mechanical strength and potentially leading to failure.
- How to Avoid: Optimize printing parameters such as laser/electron beam power, scan speed, and layer thickness to ensure complete melting and fusion. Use high-quality metal powders with good flowability, such as those produced by Metal3DP’s advanced powder making system. Implement inert gas environments during printing to minimize oxidation. Employ non-destructive testing methods to detect internal defects.
- 표면 거칠기: As-built metal 3D-printed surfaces can be too rough for medical implant applications, potentially affecting osseointegration or causing issues during surgical insertion.
- How to Avoid: Optimize printing parameters to achieve a smoother initial surface finish (e.g., using finer powder or thinner layers). Employ appropriate post-processing techniques such as media blasting, polishing, or electropolishing to achieve the desired surface roughness.
- Dimensional Inaccuracies: Deviations from the intended dimensions can occur due to factors like material shrinkage, thermal expansion, or machine calibration issues, potentially affecting the fit and functionality of the bone screw.
- How to Avoid: Calibrate the 3D printer regularly. Account for material shrinkage in the design phase. Optimize build orientation. Consider using sacrificial features for dimensional control. Employ precise post-processing techniques like CNC machining for critical dimensions.
- Material Contamination: Introducing impurities during the printing process or subsequent handling can compromise the biocompatibility and mechanical properties of the Ti-6Al-4V ELI or other metal powders.
- How to Avoid: Maintain a clean printing environment. Use high-purity metal powders from reputable suppliers like Metal3DP. Follow strict material handling protocols. Implement thorough cleaning procedures during post-processing.
- 비용 고려 사항: The cost of metal 3D printing can be a concern, especially for complex, custom-designed bone screws.
- How to Avoid: Optimize the design for material efficiency and reduced build time. Carefully evaluate different metal 3D printing technologies and service providers to find the most cost-effective solution for the specific application. Consider the long-term benefits of customization and improved patient outcomes, which may outweigh the initial cost.
- 규정 준수: Medical devices like bone screws are subject to stringent regulatory requirements. Ensuring compliance throughout the design, manufacturing, and post-processing stages is crucial.
- How to Avoid: Partner with experienced metal 3D printing service providers like Metal3DP who have a strong understanding of medical device regulations and quality management systems (e.g., ISO 13485). Maintain thorough documentation of the entire process, from design to final inspection.
By proactively addressing these potential challenges through careful design, optimized printing parameters, appropriate post-processing, and adherence to quality control measures, it is possible to consistently produce high-quality, custom bone screws via metal 3D printing that meet the demanding requirements of orthopedic surgery and ultimately
How to Choose the Right Metal 3D Printing Service Provider for Custom Bone Screws
Selecting the appropriate metal 3D printing service provider is a critical decision for companies looking to manufacture custom bone screws. The choice of partner will significantly impact the quality, cost, and timeliness of the final product. Given the stringent requirements for medical implants, it is essential to choose a provider with the expertise, technology, and quality systems necessary to meet these demands.
Here are key factors to consider when evaluating metal 3D printing service providers for custom bone screws:
- Experience and Expertise in Medical Device Manufacturing: Look for a provider with a proven track record in manufacturing medical devices, ideally orthopedic implants. They should have a deep understanding of the regulatory landscape (e.g., FDA, ISO 13485), material requirements for biocompatibility, and the critical quality control measures necessary for medical applications. Metal3DP has extensive experience in providing additive manufacturing solutions for the medical industry.
- Material Capabilities: Ensure the service provider offers the specific metal powders required for your application, such as Ti-6Al-4V ELI. They should have expertise in processing these materials and provide material certifications and traceability. Metal3DP manufactures a wide range of high-quality metal powders optimized for laser and electron beam powder bed fusion, including Ti-6Al-4V ELI.
- Printing Technology and Equipment: Understand the types of metal 3D printing technologies the provider utilizes (e.g., DMLS, SLM, EBM). Each technology has its own strengths and limitations in terms of accuracy, surface finish, and material properties. Metal3DP specializes in Selective Electron Beam Melting (SEBM), which offers high accuracy and is well-suited for producing complex medical implants. You can learn more about our 인쇄 방법 on our website.
- Post-Processing Capabilities: As discussed earlier, post-processing is crucial for medical implants. Evaluate whether the provider offers a comprehensive range of services, including powder removal, support removal, heat treatment, surface finishing (e.g., polishing, electropolishing), and CNC machining. Metal3DP provides end-to-end solutions with a full suite of post-processing services.
- Quality Management System (QMS) and Certifications: The service provider should have a robust QMS in place and relevant certifications, such as ISO 13485 (Medical devices — Quality management systems — Requirements for regulatory purposes). This demonstrates their commitment to quality and compliance.
- Design Support and Engineering Expertise: A good service provider will offer design consultation and engineering support to optimize your bone screw design for additive manufacturing, ensuring manufacturability and performance. Metal3DP has decades of collective expertise in metal additive manufacturing and offers application development services.
- Inspection and Quality Control Procedures: Inquire about the provider’s inspection processes and quality control measures. They should have capabilities for dimensional measurement (e.g., CMM), surface roughness testing, and potentially non-destructive testing.
- Scalability and Production Capacity: Consider the provider’s ability to scale up production if your needs increase in the future. Assess their production capacity and lead times.
- Communication and Customer Support: Effective communication and responsive customer support are essential for a successful partnership. Evaluate the provider’s responsiveness and willingness to collaborate.
- Cost and Pricing Structure: Understand the provider’s pricing model and ensure it aligns with your budget. Consider the total cost, including design, printing, post-processing, and quality control.
- Confidentiality and Intellectual Property Protection: Ensure the provider has strong confidentiality agreements and measures in place to protect your intellectual property.
By carefully evaluating potential metal 3D printing service providers based on these factors, you can select a partner that will deliver high-quality custom bone screws that meet your specific requirements and regulatory standards. Metal3DP에 문의하세요 to explore how our capabilities can power your organization’s additive manufacturing goals for medical devices. You can also find more information 우리에 대하여 on our website.
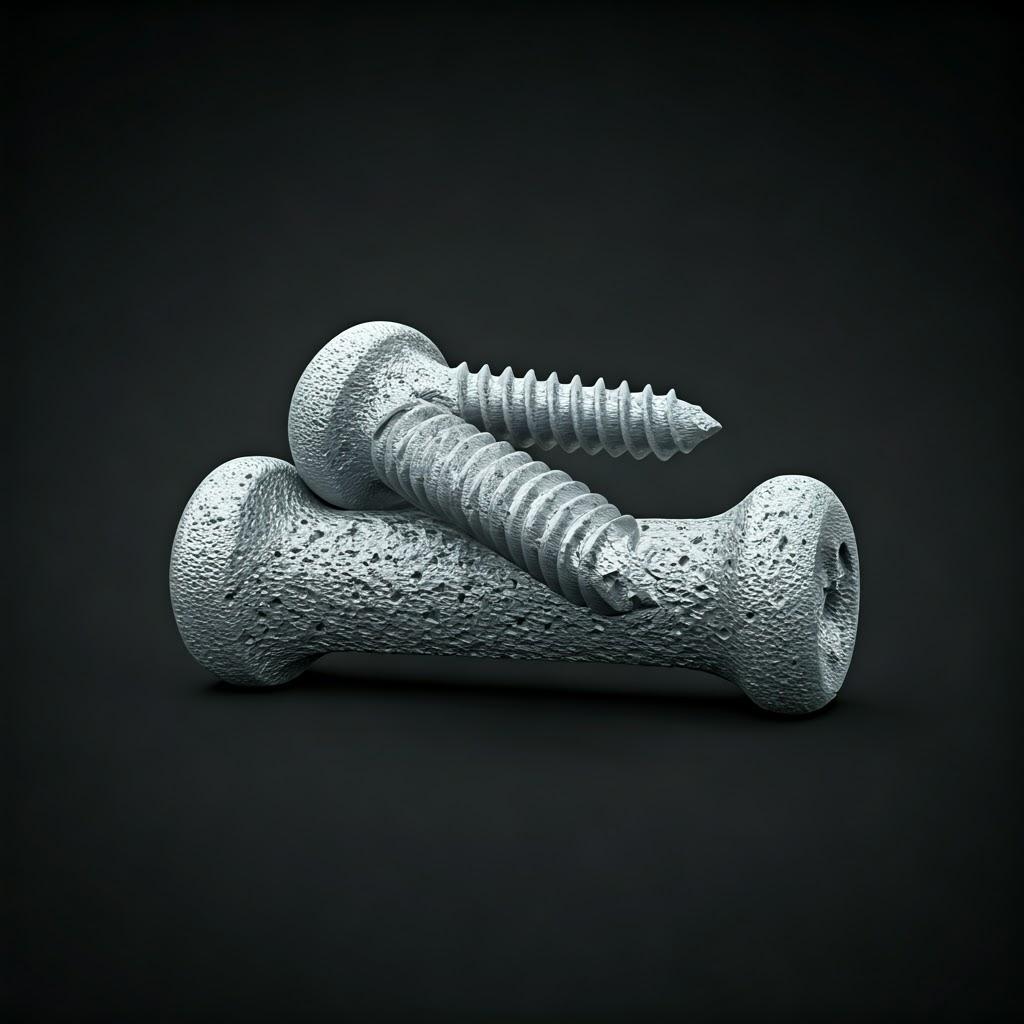
Cost Factors and Lead Time for 3D-Printed Custom Bone Screws
Understanding the cost factors and lead times associated with 3D-printed custom bone screws is crucial for budgeting and project planning. Unlike mass-produced standard implants, the cost and turnaround time for patient-specific devices are influenced by several unique variables.
비용 요소:
- Design Complexity and Customization: Highly complex designs and the level of customization required for each patient will impact the design and engineering time, thus affecting the overall cost.
- Material Selection and Usage: The type and quantity of metal powder used (e.g., Ti-6Al-4V ELI) are significant cost drivers. More intricate designs or larger screws will naturally require more material. The cost of specialized medical-grade powders also contributes. You can explore our range of 제품, including metal powders, on our website.
- 인쇄 시간: The duration of the 3D printing process depends on the size and complexity of the bone screw, as well as the chosen printing technology. Longer print times translate to higher machine operating costs.
- 사후 처리 요구 사항: The extent of post-processing needed (e.g., support removal, heat treatment, surface finishing, CNC machining) will influence the final cost. More demanding surface finishes or tighter tolerances requiring machining will add to the expense.
- Quality Control and Inspection: Rigorous quality control procedures, including dimensional inspection and material testing, are essential for medical implants and contribute to the overall cost.
- Regulatory Compliance and Documentation: The effort and resources required to ensure regulatory compliance and generate the necessary documentation can also factor into the cost.
- Service Provider’s Pricing Structure: Different service providers have varying pricing models, which may include hourly rates for design and engineering, per-part charges, or volume-based discounts.
리드 타임:
- Design and Engineering: The time required to create a patient-specific design based on medical imaging data and optimize it for 3D printing can vary depending on the complexity and the need for iterations.
- Pre-processing and Build Preparation: Preparing the 3D printer, loading the material, and setting up the build can take some time.
- 인쇄 시간: As mentioned earlier, the actual printing duration is a significant component of the lead time.
- 후처리: The time required for each post-processing step (e.g., heat treatment cycles, machining, surface finishing) will add to the overall turnaround time.
- Quality Control and Inspection: Thorough inspection processes can take time to ensure the implant meets all specifications.
- Shipping and Logistics: The time for packaging and shipping the final custom bone screw to the medical facility needs to be considered.
리드 타임에 영향을 미치는 요인:
- Complexity of the Design: More intricate designs may require more time for design, printing, and post-processing.
- Number of Parts in a Build: Printing multiple parts simultaneously can potentially reduce the per-part lead time but may increase the overall build duration.
- Availability of Materials: The lead time for acquiring specialized medical-grade metal powders can impact the overall turnaround. Metal3DP maintains a stock of high-quality metal powders to minimize delays.
- Service Provider’s Capacity and Workflow: The service provider’s current workload and efficiency of their processes will influence lead times.
- 사후 처리 요구 사항: More extensive post-processing will naturally extend the lead time.
- 규정 요구 사항: Stringent regulatory processes may add to the overall timeline.
While 3D-printed custom bone screws may have a higher initial cost and potentially longer lead times compared to off-the-shelf standard screws, the benefits of patient-specific fit, enhanced osseointegration, and potentially improved surgical outcomes can outweigh these factors. By carefully planning and collaborating with an experienced service provider like Metal3DP, you can optimize both cost and lead time for your specific needs. We are committed to providing efficient and cost-effective solutions for the production of high-quality medical implants.
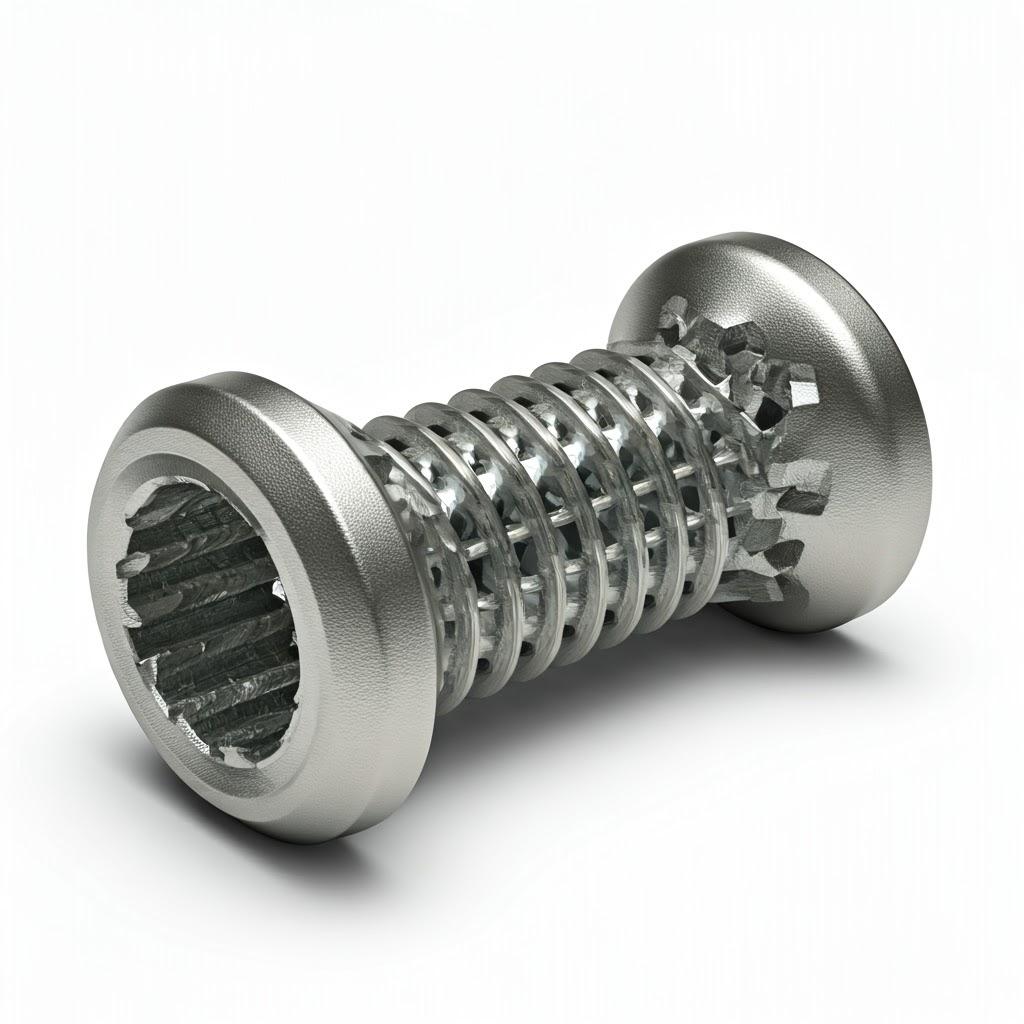
자주 묻는 질문(FAQ)
- What is the typical lifespan of a 3D-printed titanium bone screw?
- The lifespan of a 3D-printed titanium bone screw, particularly one made from Ti-6Al-4V ELI, is expected to be comparable to traditionally manufactured titanium implants. Titanium alloys are known for their excellent biocompatibility and corrosion resistance, allowing them to function effectively for many years, often decades, within the body. The actual lifespan can be influenced by factors such as the patient’s activity level, the specific surgical application, and the load-bearing requirements.
- Are 3D-printed bone screws as strong as traditionally manufactured ones?
- Yes, when manufactured using high-quality metal powders and optimized printing parameters, 3D-printed bone screws can achieve mechanical properties equivalent to or even exceeding those of traditionally manufactured screws. The 선택적 전자빔 용융(SEBM) 기술 used by Metal3DP produces dense parts with excellent strength and fatigue resistance. Furthermore, the ability to design intricate internal structures and optimize the material microstructure through controlled printing and heat treatment can enhance the mechanical performance of 3D-printed implants.
- How is the patient-specific design data for custom bone screws obtained?
- The patient-specific design data for custom bone screws is typically derived from medical imaging scans, such as computed tomography (CT) or magnetic resonance imaging (MRI). These scans provide detailed anatomical information about the patient’s bone structure. This data is then used to create a 3D digital model of the bone, and the bone screw is designed to precisely match the required dimensions and geometry for the specific surgical site. Specialized software is used for this design process, often in collaboration between surgeons and engineers.
- Can 3D-printed bone screws be used for pediatric patients?
- 예, custom bone screws produced via metal 3D printing can be particularly beneficial for pediatric patients. Children have unique bone geometries and growth considerations. The ability to create screws tailored to their specific anatomy can lead to more accurate and stable fixation, minimizing the risk of complications and accommodating future growth. The biocompatibility of materials like Ti-6Al-4V ELI is also crucial for pediatric applications.
- What are the regulatory requirements for 3D-printed custom bone screws?
- 3D-printed custom bone screws, like all medical devices, are subject to stringent regulatory requirements in most regions. These regulations aim to ensure the safety and efficacy of the devices. In the United States, the Food and Drug Administration (FDA) has specific guidelines for additive manufactured medical devices. Compliance typically involves demonstrating biocompatibility, mechanical performance, sterility, and adherence to quality management systems like ISO 13485. Working with an experienced manufacturer like Metal3DP, which understands these regulations, is crucial for navigating the approval process.
Conclusion – The Future of Orthopedics with Metal 3D-Printed Custom Bone Screws
Metal 3D printing is revolutionizing the field of orthopedic surgery, and the application of this technology to the creation of custom bone screws represents a significant leap forward in patient care. By enabling the production of implants tailored to individual patient anatomies, metal additive manufacturing offers the potential for improved surgical precision, enhanced osseointegration, reduced surgical time, and ultimately, better patient outcomes.
The unique design freedom afforded by metal 3D printing allows for the creation of complex geometries, optimized thread patterns, and porous structures that promote bone ingrowth – features that are often difficult or impossible to achieve with traditional manufacturing methods. Materials like Ti-6Al-4V ELI, with their exceptional biocompatibility and mechanical properties, are ideally suited for 3D printing long-lasting and reliable bone screws.
다음과 같은 회사 Metal3DP are at the forefront of this innovation, providing cutting-edge 금속 3D 프린팅 서비스 and high-quality metal powders. Our expertise in Selective Electron Beam Melting (SEBM) technology, coupled with our comprehensive post-processing capabilities and commitment to quality, makes us a trusted partner for the development and manufacturing of advanced medical devices.
As the technology continues to evolve and become more accessible, we can expect to see an increasing adoption of custom bone screws in a wider range of orthopedic procedures. This shift towards personalized medicine promises to transform the way surgeons approach fracture fixation, joint reconstruction, and spinal fusion, ushering in a new era of more precise, effective, and patient-centric orthopedic solutions. Metal3DP에 문의하세요 today to explore how our advanced additive manufacturing solutions can contribute to the future of orthopedics and benefit your organization.
공유
중국 칭다오에 본사를 둔 선도적인 적층 제조 솔루션 제공업체인 MET3DP Technology Co. 당사는 산업용 3D 프린팅 장비와 고성능 금속 분말을 전문으로 합니다.
관련 기사
Met3DP 소개
최근 업데이트
제품
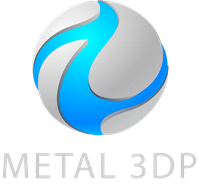
3D 프린팅 및 적층 제조용 금속 분말
문의 정보
- 칭다오시, 산둥성, 중국
- [email protected]
- [email protected]
- +86 19116340731