3D-metallpulver
Innehållsförteckning
3D metallpulver är material som används i additiv tillverkningsteknik för att tillverka metalldelar och komponenter. Den här guiden ger en detaljerad översikt över olika typer av metallpulver, deras sammansättning och egenskaper, tillämpningar, specifikationer, priser och jämförelser för att förstå deras roll vid 3D-utskrift av metaller.
Översikt över 3D-metallpulver
3D-metallpulver används som råmaterial i tekniker som selektiv lasersintring (SLS), direkt metallasersintring (DMLS), elektronstrålesmältning (EBM) och bindemedelssprutning för att tillverka komplicerade metallkomponenter med komplexa geometrier. De finns i olika elementära former eller legeringar.
Pulver skiljer sig avsevärt från metallmaterial som används i traditionella subtraktiva tillverkningsmetoder. Viktiga egenskaper som flytbarhet, form, partikelstorleksfördelning och renhet kontrolleras noggrant för att möjliggöra exakt konsolidering lager för lager under tryckningen.
Fördelar med att använda metallpulver i additiv tillverkning:
- Designflexibilitet - producera lätta gitterstrukturer och komplexa delar som inte kan bearbetas
- Minskat avfall - använd bara material som behövs till skillnad från subtraktiva metoder
- Kortare ledtider - snabb iteration och analys för optimering av konstruktionen
- Kundanpassade legeringar - skräddarsy sammansättning och egenskaper enligt tillämpning
- Konsolidering - smälta och förtäta pulver för att forma solida metalldelar
- Ytfinish - uppnå jämnhet och noggrannhet utan ytterligare efterbearbetning
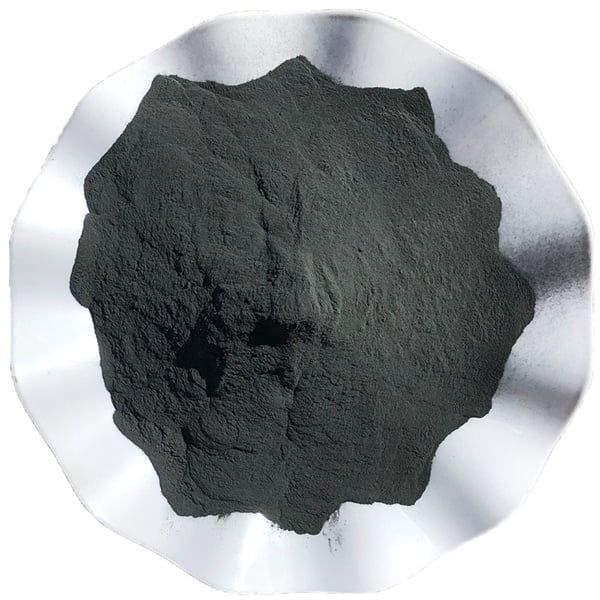
Olika typer av metallpulver
Flera elementära metaller och legeringar finns tillgängliga i pulverform för användning inom olika branscher:
Material | Vanliga legeringar/kvaliteter | Fastigheter | Tillämpningar |
---|---|---|---|
Rostfritt stål | 316L, 17-4PH, 304L, 420 | Korrosionsbeständighet, hög hållfasthet | Flyg- och rymdindustrin, fordonsindustrin, konsumentprodukter |
Aluminium | AlSi10Mg, AlSi7Mg0,6 | Låg vikt, utmärkt värmeledningsförmåga | Fordon, värmeväxlare |
Titan | Ti64, Ti6Al4V ELI | Högt förhållande mellan styrka och vikt, biokompatibilitet | Flyg- och rymdindustrin, medicinska implantat |
Superlegeringar av nickel | Inconel 718, Inconel 625 | Värmebeständighet, korrosionsbeständighet | Komponenter för flyg- och rymdindustrin som turbiner och förbränningskammare |
Kobolt Krom | CoCr MP1, CoCrMo ASTM F75 | Biokompatibilitet, hög hårdhet | Tandimplantat, ortopediska knä- och höftledsimplantat |
Koppar | CuSn10, CuZn | Elektrisk/termisk ledningsförmåga, duktilitet | Elektriska kontakter, värmeväxlare |
Verktygsstål | H13, P20 | Hög hårdhet, värmebeständighet | Formsprutningsverktyg, Kantpressverktyg |
Partikelform: Oftast sfäriska men kan också vara polygonala beroende på produktionsmetod. Förbättrar flöde och packningsdensitet.
Partikelstorlek: Intervaller från 10 till 100 mikrometer. Smal fördelning ger jämn skikttjocklek och bättre densitet.
Storlek Specifikation System: Maskstorlek (siktar som separerar pulver), D-värden (statistiskt mått på genomsnittlig storlek).
Flytbarhet: Kvantifieras med hjälp av Hall-flödesmätare och trattprov. Avgörande för skiktets enhetlighet. Förbättras av sfäriska partiklar.
Övriga fastigheter: Pulverdensitet, tappdensitet, skenbar densitet, pyknometerdensitet, oxidativ stabilitet etc.
Tillämpningar och användning av metallpulver vid 3D-printing
Några vanliga användningsområden är:
- Lättviktskonstruktion av kritiska rörliga komponenter som impellrar och rotorer
- Konsolidering av monteringar för minskat antal detaljer - motorkonsoler, fästen
- Kundanpassade jiggar, fixturer, press- och formverktygsinsatser för kortare ledtider
- Värmeväxlare med hög komplexitet, pumpar, ventiler och grenrörsblock
- Patientanpassade implantat förbättrar kirurgiska resultat
- Miniatyrer med hög detaljrikedom som tärningstorn och spelpjäser
Fördelar jämfört med traditionell tillverkning:
- Minska vikten med 40-60% med gitterstrukturer samtidigt som hållfastheten bibehålls
- Stämmer exakt överens med CAD-modeller till skillnad från maskinbearbetning/gjutning
- Minskat antal detaljer genom konsolidering minskar monteringstiden/kostnaden
- Slät ytfinish med exakta mått eliminerar till stor del efterbearbetning
- Snabba omställningar utan dyra verktygsbyten
Överlägsen prestanda: Komponenter som utformats specifikt för additiv tillverkning överträffar konventionellt tillverkade motsvarigheter. Airbus uppnådde t.ex. viktbesparingar på 45% genom att använda 3D-printade metallfästen med bibehållen styrka och styvhet.
3D metallpulver Specifikationer
Pulveregenskaper som storleksfördelning och form styr noggrant de slutliga egenskaperna hos detaljerna så att de levereras enligt strikta specifikationer:
Attribut | Typiska värden | Standarder |
---|---|---|
Fördelning av partikelstorlek | 10 till 45 mikrometer | ASTM B214 |
Skenbar densitet | 2 till 5 g/cc | ASTM B212 |
Tappdensitet | 3 till 8 g/cc | ISO 3923/1 |
Flödeshastighet | 15 till 25 s/50 g | ASTM B213 |
Resterande syrehalt | 0,1% max | AMS 4999B |
Kvarvarande kväveinnehåll | 0,04% max | AMS 2769E |
Innehåll av kvarvarande kol | 0,03% max | AMS 2769E |
Storleksklasser och maskor: Maskstorlek hänvisar till siktklassificeringar. Typisk pulverstorlek varierar från -140 till +325 mesh. Finare fördelning mellan -100 och +325 mesh förbättrar densiteten och ytfinishen.
Överensstämmelse med kemi: Elementär sammansättning validerad mot specifikation (AMS, ASTM). Avgörande för förväntad mekanisk prestanda.
Fukthalt: Särskilt viktigt för reaktiva material som aluminium och titan. Begränsad till 0,1% enligt både ASTM B964 och ISO 22068. Kontrolleras genom lämplig försegling och torr förvaring.
Nivåer av förorenande ämnen: Magnesium, kisel, fosfor, svavel, bly begränsas till låga ppm-nivåer genom atomisering med inert gas och lämplig hantering.
Återvunnet pulver Överensstämmelse: Pulver som återvinns under tryckning övervakas noga. Generellt begränsat till 30% med noggrann kemikaliekontroll enligt ASTM F3055 och ISO/ASTM52904-standarderna.
Hur leverantörer av metallpulver för 3D-utskrift skiljer sig åt
Jämförelsegrund | Traditionella tillverkare | Producenter av AM-pulver för specialändamål |
---|---|---|
Fokus | Allmänna pulvermetallurgiska tillämpningar | Speciellt utvecklad för AM-processer |
Legeringsklasser | Endast standardkompositioner | Speciallegeringar skräddarsydda för AM |
Överensstämmelse med kvalitet | Avslappnad, endast grundläggande egenskaper | Extremt snävt - kemi, partikelform/storlek |
Ytans kvalitet | Inte kritisk, gasförstoftning valfritt | Jämn partikelmorfologi obligatorisk |
Pris | Lägre på grund av höga volymer | Högre på grund av strängare krav |
Beställ storlekar | Stora bulkkvantiteter | Så lågt som 5 kg beroende på applikation |
Ändringar för anpassning | Kräver höga MOQ:er, långa ledtider | Snabba justeringar av recept, snabb produktion |
Mervärdestjänster | Grundläggande | Designoptimering från början till slut, parameterutveckling, snabb provtagning, efterbearbetning, återvinning |
AM-pulverspecialisternas viktigaste särskiljande faktorer:
- Mycket sfäriska pulver med kontrollerad storleksfördelning skräddarsydda för varje AM-process
-kemikontroll betydligt utöver de vanliga ASTM-specifikationerna för att begränsa processvariabiliteten - Möjlighet att skräddarsy legeringar och ändra egenskaper som densitet, hårdhet etc.
- Livscykelhantering för pulver: återanvändning, blandning, återvinning, lagring och säker hantering
- Låga minsta orderkvantiteter och kortare ledtider
- Design- och tryckeritjänster från början till slut - parameteroptimering för bästa kvalitet
När särskilda betyg ger affärsnytta
För prototyper kan konventionella legeringar vara tillräckliga, men specialpulver ger mycket bättre mekaniska egenskaper för produktionstillämpningar i slutanvändarledet. De höga kostnaderna kompenseras snabbt genom prestandavinster som längre livslängd på komponenterna.
Prisvariationer hos leverantörer av metallpulver
Prisdrivare:
- Basmaterial och renhetsgrad
- Strängare kemikrav
- Nivåer för kvalitetsöverensstämmelse
- Testning och certifiering
- Ordervolymer
- Ytterligare tjänster - applikationsutveckling, parameteroptimering, efterbearbetning av detaljer, återvinning och återanvändning av pulver
Möjligheter till kostnadsminskningar:
Större orderstorlekar, pulveråtervinning, lagerplanering för just-in-time-leveranser, standardisering av tester, mindre stränga specifikationer för icke-kritiska applikationer, processautomation
Typiska prisintervall:
Material | Pris per kg |
---|---|
Aluminium AlSi10Mg | $55 – $120 |
Titan Ti6Al4V | $350 – $850 |
Nickel Inconel 718 | $120 – $500 |
Rostfritt stål 316L | $90 – $240 |
Kobolt Krom CoCrMo | $270 – $620 |
Koppar CuSn10 | $30 – $100 |
Verktygsstål H13 | $70 – $190 |
Kostnadsjämförelse mot solid barstock:
För små till medelstora detaljer som tillverkas additivt i låga volymer möjliggör metallpulver betydande kostnadsbesparingar per detalj trots högre priser på basmaterial.
Break-even kan uppnås vid produktionsvolymer så låga som 50-100 delar för komponenter som väger mer än 0,5 kg. Denna fördel ökar betydligt för större komponenter som väger mer än 5 kg.
Minskad maskinbearbetning och minimal slutbearbetning ger ytterligare kostnadsfördelar jämfört med subtraktiva tekniker.
Upphandling av metallpulver för 3D-printing
Viktiga kriterier för utvärdering av leverantörer:
- Utbud av material och kompatibla kvaliteter
- Certifieringar av pulverkvalitet
- Leveranssäkerhet och minsta orderkvantiteter
- Kapacitet för utveckling av kundanpassade legeringar
- Mervärdestjänster som parameteroptimering, återanvändning av pulver, efterbearbetning etc.
- Övergripande kostnadsbesparingar
Överväganden om säker hantering
Precis som vid andra metallbearbetningsprocesser kan säkerhetsfrågor uppstå:
Fara | Försiktighetsåtgärder |
---|---|
Brand/Explosion | Användning av inert gas under pulverhantering för att förhindra oxidation; eliminera antändningskällor |
Toxicitet | Använd dammutsug och andningsskydd för att förhindra inandning |
Reaktivitet | Isolera reaktiva pulver som aluminium/titan med inerta separatorer |
Särskild försiktighet måste iakttas vid laddning, användning, rengöring och förvaring av pulver för att minimera riskerna. Pulverbehållare måste vara elektriskt jordade.
Viktiga slutsatser
- 3D metallpulver uppvisar specifika storleks-, form- och kemiegenskaper som krävs för AM-processer. Vanliga material är aluminium, titan, rostfritt stål, superlegeringar av Inconel, verktygsstål och koboltkrom.
- Industrier drar nytta av optimerade lättviktskonstruktioner, konsolidering av delar och prestandaförbättringar jämfört med traditionell tillverkning.
- Specialiserade leverantörer har noggrann kontroll över kritiska pulveregenskaper och erbjuder anpassade legeringar och tjänster som matchar applikationskraven. Detta gör det möjligt för fler användare att få tillgång till lägre kvantiteter.
- Korrekt hantering och avfallshantering är nödvändig med tanke på reaktivitets- och brandfaran.
- Initialkostnaderna uppvägs av konstruktions- och tillverkningsfördelar vid produktionsvolymer så låga som 50-100 delar för medelstora komponenter.
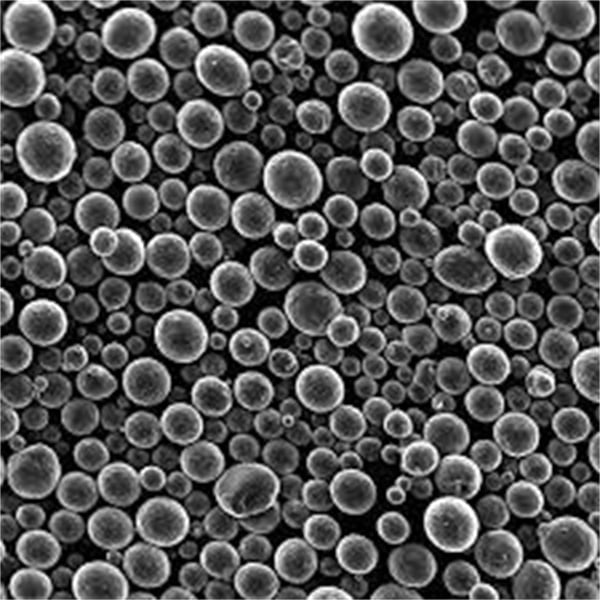
VANLIGA FRÅGOR
F: Hur tillverkas metallpulver?
A: Gasatomisering är den vanligaste tekniken där en smält metallström sönderdelas i droppar med hjälp av inerta gasstrålar. De sfäriska partiklarna stelnar snabbt i kontrollerade storlekar med hjälp av vatten- eller oljesläckning. Plasmaatomisering används också.
F: Vilken storlek på pulver är optimal för 3D-utskrift av vanlig metall?
A: Pulverstorleksintervallet 10 mikron till 45 mikron ger den bästa avvägningen mellan upplösning, ytfinish och bygghastighet för populära skrivare från EOS, Concept Laser etc.
F: Hur länge kan oanvänt metallpulver hålla sig vid korrekt förvaring?
A: Upp till 10 år i en fuktsäker behållare med torkmedelspåsar under 20 C lagring enligt ASTM-standarder. Torr kvävgasrening möjliggör ännu längre användning.
F: Kan metalltryckpulver återanvändas?
S: Ja, oanvänt pulver kan samlas in och blandas med nytt material efter analys upp till 30%-proportion. Detta minskar de totala delkostnaderna men tröskelvärdena för kemi och partikelstorleksfördelning måste uppfyllas enligt ASTM F3055-standarden.
F: Är det materialvalet som styr kostnaderna för 3D-metalltryck?
S: Ja, superlegeringar av titan och nickel har 3-5 gånger högre prispremie än rostfritt stål på grund av höga råvarukostnader. Begränsade konkurrenskraftiga källor bidrar också jämfört med stål.
Dela på
MET3DP Technology Co, LTD är en ledande leverantör av lösningar för additiv tillverkning med huvudkontor i Qingdao, Kina. Vårt företag är specialiserat på 3D-utskriftsutrustning och högpresterande metallpulver för industriella tillämpningar.
Förfrågan för att få bästa pris och anpassad lösning för ditt företag!
Relaterade artiklar
Om Met3DP
Senaste uppdateringen
Vår produkt
KONTAKTA OSS
Har du några frågor? Skicka oss meddelande nu! Vi kommer att betjäna din begäran med ett helt team efter att ha fått ditt meddelande.
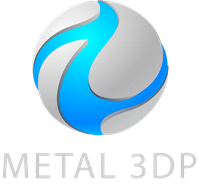
Metallpulver för 3D-printing och additiv tillverkning