Produktion av 3D-printat metallpulver
Innehållsförteckning
Imagjinoni këtë: keni një dizajn kompleks për një komponent të lehtë dhe me forcë të lartë. Prodhimi tradicional mund të hasë pengesa - format e ndërlikuara janë të shtrenjta për t'u përpunuar, dhe derdhja mund të mos japë vetitë e dëshiruara. Por çfarë nëse mund ta ndërtonit atë komponent shtresë pas shtrese, me liri pothuajse të pakufizuar të dizajnit, duke përdorur një lloj special pluhuri metali? Kjo është magjia e metalit të printuar 3D, dhe përbërësi sekret? Metallpulver.
Por si saktësisht një copë metali shndërrohet në këtë pluhur të imët, të rrjedhshëm që ushqen mrekullitë e printimit 3D? Përgatituni, sepse jemi gati të thellohemi në botën magjepsëse të 3D-utskrivet metallpulver prodhimit!
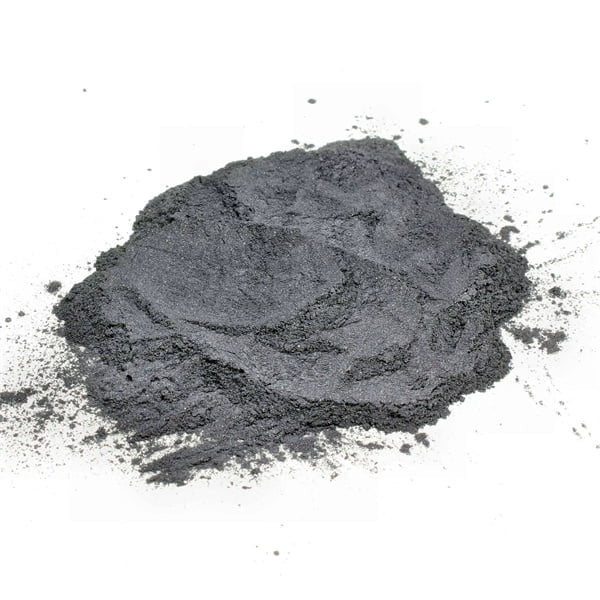
Lëndët e para për pluhurin metalik të printuar 3D
Hapi i parë është zgjedhja e blloqeve të duhura të ndërtimit. Ndryshe nga rëra mesatare e plazhit, pluhurat metalikë për printimin 3D janë krijuar me kujdes për të siguruar veti specifike në produktin përfundimtar. Zgjedhjet e zakonshme përfshijnë:
- Metale të pastra: Mendoni për titanin për biokompatibilitetin e tij, ose aluminin për forcën e tij të lehtë.
- Lidhje: Kombinimi i metaleve të ndryshme hap një gamë më të gjerë vetish. Për shembull, pluhuri i çelikut inox ofron rezistencë të shkëlqyer ndaj korrozionit.
Karakteristikat e pluhurit: Një akt balancimi
Cilësia e pluhurit ndikon ndjeshëm në procesin e printimit 3D dhe performancën përfundimtare të pjesës. Këtu janë disa karakteristika kryesore që prodhuesit përpiqen t'i arrijnë:
- Partikelstorlek och -fördelning: Imagjinoni sheqerin kundrejt rërës së trashë - madhësia dhe variacioni i grimcave të pluhurit metalik ndikojnë se sa lehtë ato rrjedhin dhe ndërveprojnë me lazerin ose rrezen e elektronit të printerit 3D.
- Sfäriskhet: Idealja është që grimcat të jenë afër sferave perfekte. Kjo siguron paketim të qëndrueshëm gjatë printimit, duke çuar në një pjesë përfundimtare më të dendur dhe më të fortë.
- Flytbarhet: Pluhuri duhet të rrjedhë lirshëm brenda printerit 3D për të siguruar formimin e lëmuar të shtresave.
- Kemisk sammansättning: Ruajtja e përbërjes kimike të dëshiruar gjatë gjithë procesit të prodhimit të pluhurit është thelbësore për arritjen e vetive të synuara në pjesën përfundimtare.
Procesi i Prodhimit i 3D-utskrivet metallpulver
Għandhom diversi metodi biex jinħoloq trab tal-metall, kull wieħed bil-vantaġġi u l-limitazzjonijiet tiegħu stess. Ejja nesploraw dawk l-aktar komuni:
- Atomisering av gas: Dan il-proċess ta' teknoloġija għolja jinvolvi metall imdewweb li jiġi mitmugħ fi fluss ta' gass bi pressjoni għolja. Il-gass li jespandi malajr ikisser il-metall f'qtar żgħar li jissolidifikaw fl-arja, u jiffurmaw partiċelli sferiċi. Aħseb fih bħallikieku qed toħloq xita tal-metall, b'kull qatra ssir partiċella perfetta tat-trab! L-atomizzazzjoni tal-gass toffri kontroll eċċellenti fuq id-daqs u l-isferiċità tal-partiċelli, u tagħmilha ideali għal applikazzjonijiet impenjattivi.
- Atomisering av vatten: Hawnhekk, metall imdewweb jiġi mġiegħel minn ġett ta' ilma bi pressjoni għolja, li mill-ġdid jirriżulta f'frammentazzjoni f'partiċelli fini. Immaġina kanun tal-ilma qawwi li jiddiżintegra metall imdewweb f'sħaba ta' trab! L-atomizzazzjoni tal-ilma hija għażla aktar kosteffettiva meta mqabbla mal-atomizzazzjoni tal-gass, iżda l-partiċelli għandhom it-tendenza li jkunu inqas sferiċi.
- Plasmaatomisering: Dan il-metodu juża torċa tal-plażma b'temperatura għolja biex idub u jattomizza l-materjal tal-metall. Immaġina torċa supercharged li tivvaporizza l-metall u tikkondensah f'trab! L-atomizzazzjoni tal-plażma tippermetti l-ipproċessar ta' metalli reattivi bħat-titanju li jistgħu jkunu ta' sfida b'metodi oħra.
- Atomizzazzjoni tal-Induzzjoni tal-Elettrodu (EIA): Din it-teknika tuża kurrent elettriku biex idub il-metall ġewwa griġjol. Il-metall imdewweb imbagħad jiġi mkeċċi minn żennuna bl-użu ta' fluss ta' gass bi pressjoni għolja, li jwassal għall-atomizzazzjoni. Immaġina forn elettriku sofistikat li jdub il-metall u mbagħad juża splużjoni tal-gass taħt pressjoni biex jibdlu f'trab! L-EIA toffri kontroll tajjeb fuq id-daqs tal-partiċelli u tista' tintuża għal varjetà ta' metalli.
Ipproċessar ta' wara: Irfinar tat-Trab
Ladarba l-proċess inizjali tal-atomizzazzjoni jkun lest, it-trab jista' jgħaddi minn passi ta' pproċessar ulterjuri:
- Klassificering: It-trabijiet spiss jiġu mgħarbula biex tinkiseb distribuzzjoni tad-daqs tal-partiċelli mixtieqa.
- Degassifikazzjoni: Kwalunkwe gassijiet maqbuda fil-partiċelli tat-trab jistgħu jitneħħew bl-użu ta' forn tal-vakwu, li jtejjeb il-fluss u jnaqqas ir-riskju ta' difetti waqt l-istampar.
Tagħmir tal-Produzzjoni għal Trab tal-Metall Stampat 3D
Iru ẹrọ ti a lo fun iṣelọpọ lulú irin jẹ amọja ati pe o le jẹ idiju pupọ:
- Awọn iyẹwu atomization: Awọn iyẹwu wọnyi ni ilana atomization, ni idaniloju agbegbe iṣakoso fun mimu irin yo.
- Awọn adiro: Awọn adiro otutu giga ni a lo lati yo ifunni irin ṣaaju atomization.
- Awọn eto ipin: Awọn ẹrọ sisẹ tabi awọn ẹrọ ipin afẹfẹ ya lulú naa si awọn ẹgbẹ iwọn oriṣiriṣi.
- Awọn adiro degasification: Awọn adiro amọja wọnyi yọ awọn gaasi ti a dẹkun kuro ninu awọn patikulu lulú.
Iṣakoso Didara ti 3D-utskrivet metallpulver
Awọn olupilẹṣẹ lulú irin ṣe imuse awọn iwọn iṣakoso didara ti o muna lati rii daju pe ọja wọn pade awọn ibeere ti o muna ti titẹ sita 3D. Eyi ni wiwo sinu agbaye ti idaniloju lulú ti o ga julọ:
- Kemisk analys: Akopọ kemikali ti lulú naa ni a ṣe atupale ni pẹkipẹki nipa lilo awọn imuposi bii fluorescence X-ray (XRF) tabi spectroscopy itujade opitika (OES). Eyi ṣe idaniloju pe lulú naa pade awọn pato alloy ti o fẹ ati dinku wiwa awọn aimọ.
- Onínọmbà pinpin iwọn patiku: Iwọn ati pinpin awọn patikulu lulú ni a wọn nipa lilo diffraction laser tabi awọn ọna sisẹ. Iwọn patiku ti o tọ jẹ pataki fun ṣiṣan lulú didan ati iwuwo iṣakojọpọ to dara julọ lakoko titẹ, ti o yori si apakan ipari ti o lagbara.
- Idanwo sisan: A ṣe iṣiro sisan ti lulú nipa lilo ẹrọ amọja ti o ṣe iwọn bi o ṣe rọrun to. Sisan ti o dara jẹ pataki fun dida fẹlẹfẹlẹ deede ni awọn ilana titẹ sita 3D bii Selective Laser Melting (SLM) tabi Electron Beam Melting (EBM).
- Onínọmbà iwa: Apẹrẹ ati awọn abuda dada ti awọn patikulu lulú ni a ṣe ayẹwo nipa lilo awọn imuposi bii microscopy itanna wiwa (SEM). Eyi ṣe iranlọwọ lati ṣe idanimọ eyikeyi aiṣedeede ti o le ni ipa lori iwuwo iṣakojọpọ tabi ibaraenisepo laser lakoko titẹ.
Awọn imuposi To ti ni ilọsiwaju fun Didara Ti o dara si
Wiwa fun awọn lulú didara paapaa dara julọ jẹ ilana ti nlọ lọwọ. Eyi ni diẹ ninu awọn imuposi gige-eti ti n gba ifamọra:
- Sfärikalisering: Vissa tillverkare använder ytterligare processer som plasmarostning för att förbättra sfäriciteten hos pulverpartiklarna. Detta kan ytterligare förbättra packningstätheten och förbättra de mekaniska egenskaperna hos den slutliga tryckta delen.
- Additiv tillverkning av pulver: Nya tekniker som laserbeklädnad eller metallbläckstråle kan användas för att skapa pulver med specifika kompositioner eller graderade egenskaper. Föreställ dig 3D-utskrift av själva pulvret för ännu mer kontroll över den slutliga delens egenskaper!
Användningar av 3D-tryckta metallpulver
Det är nästan obegränsat när det gäller användningsområden för 3D-tryckta metallpulver. Här är några spännande områden där de gör avtryck:
- Aerospace: Förmågan att skapa lätta komponenter med hög hållfasthet gör 3D-tryckta metaller idealiska för flygplans- och rymdfarkostdelar. Från intrikata motorkomponenter till skräddarsydda värmeväxlare tänjer metallpulver på gränserna för flygplansdesign.
- Medicinska implantat: Biokompatibla metaller som titan och tantal, som produceras som pulver, revolutionerar medicinska implantat. Föreställ dig skräddarsydda proteser eller intrikata kranieimplantat, perfekt anpassade efter varje patients behov! 3D-utskrift med metallpulver möjliggör komplexa geometrier och porösa strukturer som främjar beningrowth.
- Fordon: Bilindustrin använder i allt högre grad 3D-tryckta metallkomponenter för viktminskning och prestandaoptimering. Tänk på lättare, starkare bildelar eller till och med skräddarsydda motorblock! Metallpulver möjliggör skapandet av komplexa kylkanaler och interna strukturer som skulle vara omöjliga med traditionella tillverkningstekniker.
- Konsumentvaror: Från skräddarsydda cykelramar till designersmycken hittar 3D-tryckta metallpulver sin väg in på konsumentmarknaden. Förmågan att producera intrikata metallföremål med hög detaljrikedom öppnar dörrar för innovativ produktdesign.
Framtiden för 3D-utskrivna metallpulver
Framtiden för 3D-tryckta metallpulver är full av potential. Här är några spännande trender att hålla utkik efter:
- Utveckling av nya material: Forskare utforskar ständigt nya metalllegeringar och kompositer som är speciellt utformade för 3D-utskrift. Dessa nya material kan erbjuda ännu bättre kombinationer av styrka, vikt och andra egenskaper.
- Förbättrade metoder för pulverproduktion: Framsteg inom atomiseringstekniker och efterbehandlingsmetoder lovar ännu snävare kontroll över partikelegenskaper, vilket leder till överlägsen utskriftsbarhet och slutlig delprestanda.
- Standardisering och certifiering: I takt med att 3D-utskriftsindustrin mognar läggs det allt större fokus på standardisering av specifikationer för metallpulver och certifieringsprocesser. Detta kommer att säkerställa konsekvent kvalitet och bredare användning av 3D-tryckta metalldelar i olika branscher.
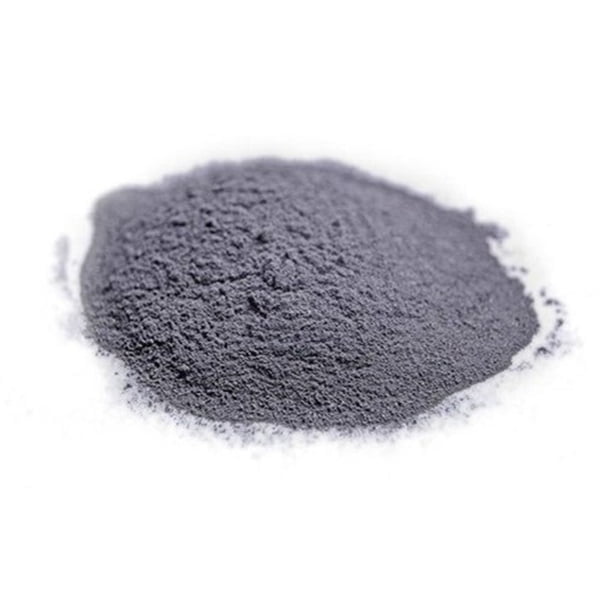
VANLIGA FRÅGOR
Här är några vanliga frågor om 3D-tryckta metallpulver, besvarade på ett tydligt och koncist sätt:
Fråga | Svar |
---|---|
Vilka är fördelarna med att använda metallpulver för 3D-utskrift? | Metallpulver erbjuder flera fördelar, inklusive designfrihet, förmågan att skapa komplexa geometrier, lätta komponenter med hög hållfasthet och potentialen för anpassning. |
Vilka är begränsningarna med metallpulver för 3D-utskrift? | För närvarande kan produktionen av metallpulver vara dyr jämfört med traditionella tillverkningsmetoder. Dessutom kan vissa metaller vara utmanande att bearbeta till pulverform. |
Hur väljer jag rätt metallpulver för mitt 3D-utskriftsprojekt? | Valet av metallpulver beror på de önskade egenskaperna hos den slutliga delen. Faktorer att beakta inkluderar materialets styrka, vikt, korrosionsbeständighet och biokompatibilitet (om tillämpligt). Att konsultera en 3D-utskriftsexpert är |
Dela på
MET3DP Technology Co, LTD är en ledande leverantör av lösningar för additiv tillverkning med huvudkontor i Qingdao, Kina. Vårt företag är specialiserat på 3D-utskriftsutrustning och högpresterande metallpulver för industriella tillämpningar.
Förfrågan för att få bästa pris och anpassad lösning för ditt företag!
Relaterade artiklar
Om Met3DP
Senaste uppdateringen
Vår produkt
KONTAKTA OSS
Har du några frågor? Skicka oss meddelande nu! Vi kommer att betjäna din begäran med ett helt team efter att ha fått ditt meddelande.
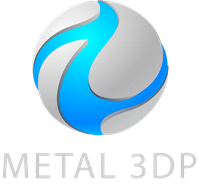
Metallpulver för 3D-printing och additiv tillverkning