3D-utskrift av metallpulver
Innehållsförteckning
Översikt över 3d-utskrift metallpulver
3D printing metal powder refers to fine metallic powders that are used as raw materials in various metal additive manufacturing processes to fabricate metal parts and products. The most common metal powders used for 3D printing include stainless steel, titanium, nickel alloys, aluminum, and cobalt-chrome.
Metal powder bed fusion and directed energy deposition are the two main families of metal 3D printing processes that utilize metal powders to construct parts layer-by-layer from CAD models. The characteristics and material properties of the metal powders have a significant impact on the final part quality, accuracy, surface finish and performance.
Viktiga detaljer:
- Common metal powders: stainless steel, titanium, nickel alloys, aluminum, cobalt-chrome
- Main metal 3D printing processes: Powder bed fusion, Directed energy deposition
- Powder characteristics critical for part quality
- Range of alloy options depending on application
- Most widely used for prototyping and production across industries
- Provides benefits like complex geometries, lightweighting, part consolidation
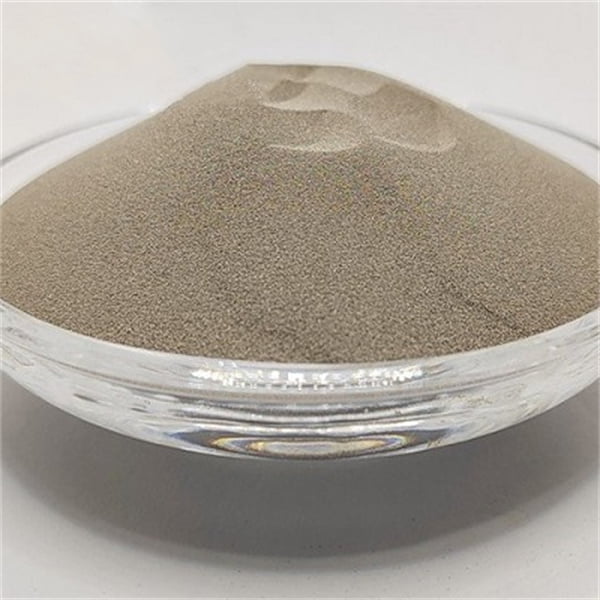
Metal Powder Types and Compositions
There are many standard and custom metal alloy powders available for 3D printing across various material manufacturers. Most alloys are optimized specifically for additive manufacturing processes.
Metall | Vanliga legeringar | Typisk sammansättning |
---|---|---|
Rostfritt stål | 316L, 17-4PH, 304L, 420 | Fe, Cr, Ni, Mo |
Titan | Ti-6Al-4V, Ti 6242 | Ti, Al, V, Sn |
Aluminium | AlSi10Mg, AlSi7Mg | Al, Si, Mg |
Nickellegeringar | Inconel 718, Inconel 625 | Ni, Cr, Fe, Nb, Mo |
Kobolt Krom | CoCrMo, CoCrW | Co, Cr, W, Si, Mn |
Rostfritt stål 316L och Ti-6Al-4V are the most popular alloys used for metal 3D printing currently. New alloys with enhanced properties are continually being developed and introduced for demanding applications in aerospace, medical, automotive and general engineering domains.
Metal Printing Powder Properties
The main properties of metal powders that determine part quality and process stability include:
Partikelstorlek – Between 15-45 microns
Morfologi – Spheroidal, good flowability
Kemi – Alloy composition within tight tolerances
Täthet – Apparent density and tap density key indicators
Flödeshastighet – Critical for uniform layer thickness
Återanvändbarhet – Recycle up to 5-10 times typically
Fastighet | Recommended Range | Betydelse |
---|---|---|
Partikelstorlek | 15 - 45 mikrometer | Affects powder flow, spreadability, resolution |
Partikelns form | Sfärisk | Enables good flow and packing density |
Kemisk sammansättning | Alloy specific | Determines mechanical properties |
Skenbar densitet | Above 50% of material density | Indikerar packningseffektivitet |
Tappdensitet | Above 80% of material density | Indicates flow and spreadability |
Flödeshastighet | 25 – 35 sec for 50 g | Essential for uniform layers |
Reuse cycles | Up to 10x | Minskar materialspill |
Fördelning av partikelstorlek is especially critical within the optimal size range – Too many fines or large particles outside the ideal fraction causes defects. Manufacturers aim for high yield within the narrow specification and consistent batch quality.
Metal 3D Printing Powder Applications
3D printing metal parts is gaining traction across industries from aerospace, medical devices and automotive to general engineering applications.
Some typical applications of common materials include:
Rostfritt stål – Food handling equipment, surgical tools, pipes, pumps housings
Titan – Aircraft and rotorcraft structural parts, biomedical implants
Aluminium – Automotive components, heat exchangers, sporting goods
Superlegeringar av nickel – Turbine blades, rocket engine parts, nuclear applications
Kobolt Krom – Knee/hip replacements, dental crowns and bridges
Metal additive enables lighter, stronger and higher performance products. It makes economic sense for expensive materials used in low volumes with custom geometries like aerospace components. 3D printing also greatly simplifies the fabrication of complex designs with internal channels for conformal cooling in injection molds.
Specifikationer för metallpulver
International and industry standards have been established to ensure quality requirements are met for industrial production use of metal AM powders:
Standard | Beskrivning | Specifikationer |
---|---|---|
ASTM F3049 | Standard guide for characterizing metal powders | Chemistry, size distribution, shape, flow rate |
ASTM F3301 | Specification for additive manufacturing steel powder | Composition, size, morphology, defects |
ASTM F3318 | Specification for additive manufacturing Ti powder | Particle size, chemistry, fill density, reuse |
ISO/ASTM 52900 | General principles for metal powder AM | Powder production methods, testing procedures |
ASME PPC-2019 | American Society of Mechanical Engineers | Powder quality guidelines |
Manufacturers provide powder lot certificates with test results demonstrating compliance with the standards for most common materials like 316L or Ti64.
Metal Powder Manufacturing Suppliers and Costs
A wide range of metal powder options for additive manufacturing are available from both large conglomerates and smaller specialist producers globally. Some leading suppliers include:
Metal Powder Manufacturers
Företag | Huvudkontor | Material |
---|---|---|
Snickare | USA | Tool steel, stainless steel, superalloys |
Hoganas | Sverige | Rostfria stål, legeringar |
AP&C | Kanada | Titan, Inconel |
Sandvik | Sverige | Stainless, tool steel, cobalt chrome |
Praxair | USA | Titanium, reactive metals |
LPW | STORBRITANNIEN | Stainless steel, aluminum, Inconel |
EOS | Tyskland | Tool Steel, Stainless, Titanium |
Kostnader för metallpulver
Material | Kostnad per kg |
---|---|
Titan Ti64 | $150 – $500 |
Aluminium AlSi10Mg | $90 – $150 |
Rostfritt stål 316L | $40 – $120 |
Inconel 718 | $180 – $300 |
Kobolt Krom | $250 – $500 |
Cost depends on alloy, quality standard, manufacturer, purchase volume, region etc. Custom alloys can cost multiple times more than standard grades. Powder is the major contributor to AM build costs so users aim to reuse it as much as possible.
Comparison of Metal 3D Printing Processes
There are two main families of additive manufacturing techniques suitable for metal materials – Fusion av pulverbäddar (PBF) och Deposition med riktad energi (DED). Within these, there are different methods with minor variations based on the heat source used for localized melting of metal powder layers.
Powder Bed Fusion methods:
- Selektiv lasersmältning (SLM)
- Selektiv lasersintring (SLS)
- Smältning med elektronstråle (EBM)
Directed Energy Deposition methods:
- Lasermetalldeponering (LMD)
- Laserteknisk nätformning (LENS)
Jämförelse av 3D-utskriftsmetoder för metall
Parameter | Fusion av pulverbäddar | Deposition med riktad energi |
---|---|---|
Värmekälla | Laser or electron beam | Laser or arc |
Avsättning | Entire layers | Focused melt pools |
Material | Limited, medium strength | Very wide range |
Upplösning | Higher <100 μm | Lower ~500 μm |
Ytfinish | Smidigare | Comparatively rough |
Byggstorlek | Smaller < 1 m^3 | Larger > 1 m^3 |
Produktivitet | Slower, single laser spot | Faster, larger melt areas |
DED is better suited for large metal parts like repairing molds or turbine housings where dimensional accuracy is not too critical. PBF offers substantially better surface finish and resolution for small components with intricate details like lattices. Materials options for DED are more expansive, including reactive alloys.
Both processes leverage the key benefits of metal AM like customization, part consolidation and lightweight structures. For production use, hybrid manufacturing combining metal 3D printing and CNC machining provides the optimal balance of geometric complexity and precision.
Advantages of Metal Additive Manufacturing
Using 3D printing for metal component production offers various technical and economic benefits driving adoption across industries:
Benefits of Metal AM
- Design freedom for complex, organic shapes with topology optimization
- Significant weight reduction through lattices and thin walls
- Part count reduction by consolidating assemblies
- Customized geometries tailored to loads and functions
- Zero tooling, fixtures and quick changeovers ideal for low volumes
- Minskat materialspill jämfört med subtraktiv teknik
Lighter forged titanium brackets for aircraft, patient-matched cranial implants, and simplified engine fuel nozzles are some examples where metal AM delivers value over conventional manufacturing approaches.
Limitations of Metal Additive Manufacturing
Despite the benefits, metal additive has some inherent process constraints that currently inhibit its use for many applications:
Limitations of Metal AM
- High equipment and material costs
- Constrained choice of alloys and mechanical properties
- Lower throughput relative to mass production methods
- Post-processing like supports removal and surface treatment add time
- Qualification and certification requirements in regulated sectors
- Dimensional inaccuracies and lower repeatability
- Higher surface roughness necessitating finishing
- Residual stresses developing during the build
These technical and economic barriers mean AM is best suited for small batch sizes where the benefits outweigh the limitations. Hybrid subtractive techniques help resolve the deficiencies for precision components. Ongoing hardware and materials R&D focused on quality, speed and parameters optimization is improving industrial viability.
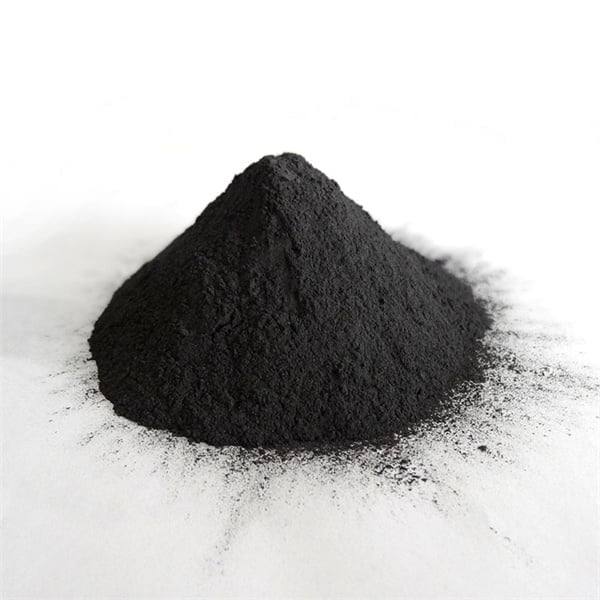
VANLIGA FRÅGOR
Here are some common questions related to metal powders for AM processes:
Q: What are the most widely used metal alloys for 3D printing currently?
A: 316L stainless steel, Ti-6Al-4V titanium alloy, AlSi10Mg aluminum alloy, Inconel 625 & 718 nickel superalloys, and CoCr cobalt chrome alloys.
Q: What testing is done to ensure batch quality consistency of the metal printing powders?
A: Suppliers conduct testing as per industrial standards to verify chemistry composition is within tolerances, particle size distribution meets ideal fractions optimized for AM processes, powder morphology and shape is spherical, apparent and tap densities match the range for good flow, and flow rate is suitable.
Q: Is virgin metal powder mandatory or can recycled powder also be used?
A: Both virgin powder as well as recycled powder from prior builds can be utilized depending on applications, typically up to 5-10 reuse cycles before refreshing with virgin stock.
Q: How are metal powders for AM produced?
A: Common manufacturing techniques include gas atomization, plasma atomization, and electrolytic processes. These yield fine spherical powders suitable for spreading thin uniform layers required in metal PBF.
Q: What causes defects in 3D printed metal parts related to powders?
A: Contaminants in powders, too many satellites or irregular particles outside size range specifications, powder degradation issues over reuse cycles, and problems in layer thickness or uniformity during spreading and recoating.
Q: How can buyers select and source the optimal metal powder type and quality?
A: Reputable manufacturers providing comprehensive material data sheets, certificates of analysis for production lots, compliance with industrial standards like ASTM F3049, evidence of rigorous quality control testing data, and guarantees around chemistry, size distribution yields etc. provide reliability and consistency essential for industrial AM applications.
Slutsats
In summary, fine spherical metallic powders with tightly controlled characteristics play a vital role as base feedstock for additive manufacturing of precision metal components across aerospace, medical, automotive and engineering domains.
Stainless steel, titanium, aluminum, nickel superalloys, and cobalt chrome are the predominantly used materials for industrial production applications currently. Part quality, accuracy, material properties and process stability depend heavily on powder size, shape, chemistry, density and flow parameters.
As the quality and choice of alloys expands, and equipment productivity increases, 3D printing looks poised to transform manufacturing across multiple sectors by enabling lighter, stronger and high-performance products with previously impossible designs for topology-optimized parts consolidated from assemblies.
Dela på
MET3DP Technology Co, LTD är en ledande leverantör av lösningar för additiv tillverkning med huvudkontor i Qingdao, Kina. Vårt företag är specialiserat på 3D-utskriftsutrustning och högpresterande metallpulver för industriella tillämpningar.
Förfrågan för att få bästa pris och anpassad lösning för ditt företag!
Relaterade artiklar
Om Met3DP
Senaste uppdateringen
Vår produkt
KONTAKTA OSS
Har du några frågor? Skicka oss meddelande nu! Vi kommer att betjäna din begäran med ett helt team efter att ha fått ditt meddelande.
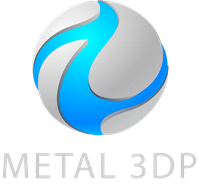
Metallpulver för 3D-printing och additiv tillverkning