Jämförelse av plasmaatomisering med annan metallpulverproduktion
Innehållsförteckning
Tänk dig att skulptera komplicerade föremål, inte av lera eller trä, utan av små, nästan magiska, metallpartiklar. Denna futuristiska vision ligger till grund för den revolutionerande världen av additiv tillverkning (AM)även kallat 3D-printing. Men dessa metalliska byggstenar, som kallas metallpulver, behöver en specialiserad skapandeprocess - och det är där’s där Plasmaatomisering står i centrum.
Men vad är egentligen plasmaatomisering och hur står den sig mot andra metoder för produktion av metallpulver? Spänn fast dig, för nu ska vi ge oss ut på en resa in i hjärtat av metallpulverproduktionen!
Metallpulver: Byggstenarna för en ny era
Metallpulver är finfördelade metallpartiklar som vanligtvis är mellan 10 och 150 mikrometer (μm) stora. Dessa små jättar kan skryta med unika egenskaper som:
- Hög flytbarhet: De är lätta att flytta och packa, vilket gör dem idealiska för AM-processer.
- Sfärisk form: Detta säkerställer en jämn packningstäthet och minimerar hålrum i slutprodukten.
- Hög renhet: De innehåller minimalt med orenheter, vilket leder till överlägsna mekaniska egenskaper i den färdiga produkten.
Dessa anmärkningsvärda egenskaper gör metallpulver ovärderliga i olika branscher, bland annat:
- Aerospace: Lättviktiga och höghållfasta komponenter för raketer och flygplan.
- Fordon: Skapar komplexa motordelar och lättviktskarosser.
- Medicinsk: Biokompatibla implantat och specialanpassad protetik.
- Konsumentelektronik: Intrikata antennstrukturer och kylflänsar.
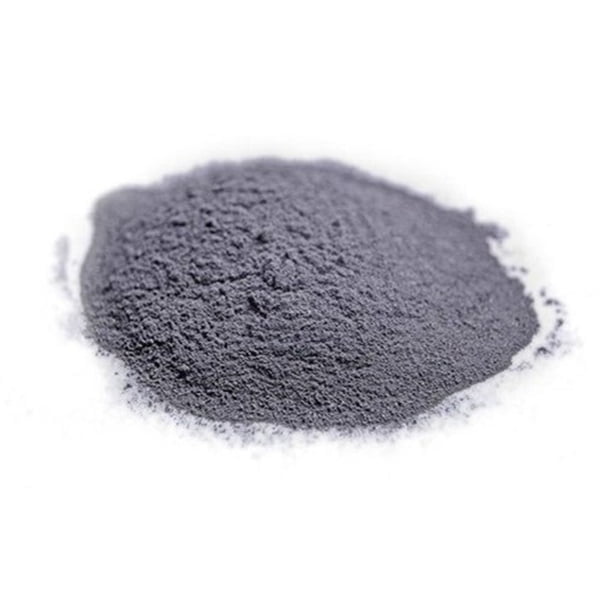
Kraften i plasma: Avslöjar tekniken
Plasmaatomisering (PA) är en högenergiprocess som använder en joniserad gas, så kallad plasma, för att skapa metallpulver. Här’är en uppdelning av magin bakom PA:
- Förberedelse av råmaterial: Den önskade metallen, vanligtvis i form av tråd eller stång, matas in i systemet.
- Plasmagenerering: Inert gas (som argon eller helium) överhettas med hjälp av en elektrisk båge och omvandlas till plasma med extremt höga temperaturer (cirka 15 000 °C).
- Atomisering: Den smälta metallråvaran sprutas in i plasmaströmmen med hög hastighet, vilket gör att den sönderdelas i fina droppar.
- Solidifiering: De snabbt svalnande dropparna stelnar i luften och bildar sfäriska metallpulverpartiklar.
- Insamling och klassificering: Pulvret samlas upp, kyls och siktas till olika storlekar baserat på specifika applikationskrav.
Jämfört med traditionella metoder som mekanisk fräsningerbjuder PA flera fördelar:
- Finare och mer sfäriska pulverpartiklar: Detta leder till bättre flytbarhet, packningstäthet och slutproduktkvalitet.
- Högre renhet: De höga temperaturerna i plasmakammaren minimerar oxidation och kontaminering.
- Större kontroll över pulverstorlek och morfologi: PA gör det möjligt att skräddarsy pulveregenskaperna efter specifika behov.
PA kommer dock också med sin egen uppsättning utmaningar:
- Hög energiförbrukning: Processen kräver en betydande mängd elkraft, vilket påverkar miljöpåverkan och kostnaden.
- Komplex och dyr utrustning: Att sätta upp och underhålla ett PA-system är mer kapitalintensivt jämfört med andra metoder.
- Begränsad materialkompatibilitet: Det är inte alla metaller som klarar de extrema temperaturerna i plasmaströmmen, vilket begränsar utbudet av pulver som produceras.
Ett landskap av alternativ: Att utforska andra Metallpulver Produktionsmetoder
Även om PA har en särställning i vissa tillämpningar används flera andra metoder för metallpulverproduktion, var och en med sina egna styrkor och begränsningar:
Metod | Beskrivning | Fördelar | Nackdelar |
---|---|---|---|
Gasatomisering (GA) | Liknar PA, men använder en höghastighetsström av inert gas i stället för plasma för finfördelning. | Lägre energiförbrukning än PA, bredare materialkompatibilitet. | Grovare och mindre sfäriska pulverpartiklar jämfört med PA. |
Vattenatomisering (WA) | Använder en högtrycksvattenstråle för att finfördela smält metall. | Kostnadseffektiv, lämplig för storskalig produktion. | Relativt hög oxidhalt, oregelbundna partikelformer, begränsad storlekskontroll. |
Centrifugal atomisering (CA) | Smält metall finfördelas av centrifugalkraften när den kommer ut ur en roterande skiva. | Hög produktionshastighet, lämplig för metaller med låg smältpunkt. | Begränsad kontroll av pulverstorlek, bred partikelstorleksfördelning. |
Elektrolytisk atomisering (EA) | Använder en elektrolytisk process för att bryta ner metalljoner till fina partiklar. | Pulver med hög renhet, lämpliga för reaktiva metaller. | Långsam produktionshastighet, hög energiförbrukning, begränsat pulverstorleksintervall. |
Metallpulver i aktion: En uppvisning av olika tillämpningar
Den specifika typ av metallpulver som väljs för en applikation beror på olika faktorer, bland annat
- Önskade egenskaper hos den slutliga produkten: Styrka, vikt, korrosionsbeständighet etc.
- AM-process används: Varje AM-process kan ha specifika krav på pulverstorlek och flytbarhet.
- Överväganden om kostnader: Olika produktionsmetoder är förknippade med varierande kostnader.
Här är några specifika exempel på metallpulver och deras tillämpningar:
Metallpulver | Sammansättning | Produktionsmetod | Tillämpningar |
---|---|---|---|
Pulver av titan (Ti): | 99% Ti | PA, GA | Komponenter till flyg- och rymdindustrin (t.ex. landningsställ till flygplan, delar till raketmotorer), biomedicinska implantat, sportutrustning |
Pulver av aluminium (Al): | 99% Al | WA, GA | Fordonskomponenter (t.ex. motorblock, kylflänsar), konsumentelektronik (t.ex. höljen, kylflänsar), livsmedelsförpackningar |
Pulver av rostfritt stål (SS): | Varierar beroende på den specifika SS-graden | PA, GA | Medicinska instrument, kemisk bearbetningsutrustning, smycken, verktyg |
Pulver av nickel (Ni): | 99% Ni | PA, GA | Komponenter av superlegeringar för högtemperaturtillämpningar (t.ex. turbinblad, värmeväxlare), batterielektroder |
Pulver av kobolt (Co): | > 99% Co | PA, GA | Hårdbeläggningsmaterial för slitstyrka, tandimplantat, magnetiska komponenter |
Det är viktigt att notera att denna lista inte är uttömmande och att nya metallpulver och applikationer ständigt utvecklas. I takt med att AM-tekniken fortsätter att utvecklas förväntas efterfrågan på högkvalitativa, mångsidiga metallpulver öka betydligt.
Priset på framsteg: En titt på kostnadsöverväganden
Kostnaden för metallpulver varierar beroende på flera faktorer, bland annat:
- Typ av metall: Sällsynta och exotiska metaller är i allmänhet dyrare än vanliga metaller.
- Produktionsmetod: PA-pulver är normalt dyrare än pulver som framställs med metoder som WA eller CA på grund av den högre energiförbrukningen och de högre utrustningskostnaderna.
- Pulverets renhet och storlek: Hög renhet och specifika storleksintervall betingar ett premiumpris.
Det är viktigt att ta hänsyn till kostnadsfaktorn när man väljer ett metallpulver för en AM-applikation, eftersom det kan ha en betydande inverkan på den totala projektkostnaden. Att hitta rätt balans mellan kostnad, prestanda och önskade egenskaper är nyckeln till framgångsrika AM-projekt.
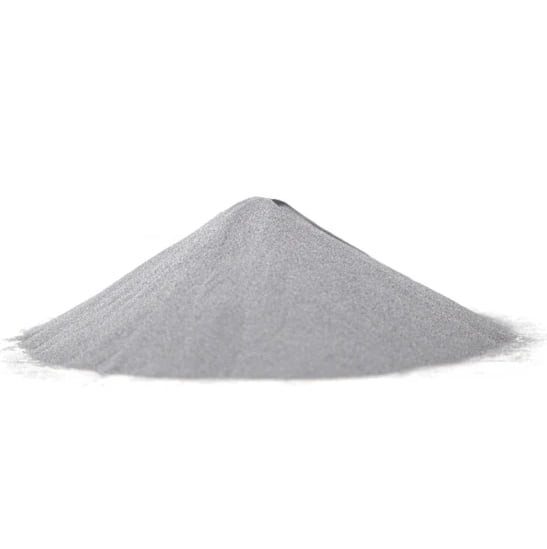
Vanliga frågor
Q: Vilka olika typer av metallpulver finns det?
Svar: Som vi tidigare nämnt finns det olika metallpulver, där de vanligaste är baserade på titan, aluminium, rostfritt stål, nickel och kobolt. Varje material har unika egenskaper som gör dem lämpliga för specifika tillämpningar.
F: Hur används metallpulver i 3D-utskrifter?
A: Metallpulver laddas i en 3D-skrivare, där de selektivt deponeras lager för lager baserat på en digital design. De deponerade lagren smälter sedan samman och skapar ett tredimensionellt objekt.
Q: Vilka är de viktigaste faktorerna att tänka på när man väljer ett metallpulver?
S: Flera faktorer spelar in, bland annat önskade egenskaper hos slutprodukten (hållfasthet, vikt etc.), kompatibilitet med den valda AM-processen, kostnadsaspekter och de specifika applikationskraven.
Q: Vilka är de framtida trenderna inom metallpulverproduktion?
S: I framtiden förväntas PA-tekniken utvecklas så att den blir mer energieffektiv och kostnadseffektiv. Dessutom pågår forskning för att utveckla nya metallpulver med förbättrade egenskaper och utöka utbudet av material som lämpar sig för AM-applikationer.
Med sina unika egenskaper och många olika användningsområden kommer metallpulvertekniken att spela en avgörande roll när det gäller att forma framtidens tillverkning. Genom att förstå de olika produktionsmetoderna, tillgängliga material och viktiga överväganden kan användarna frigöra metallpulvrets enorma potential och bidra till banbrytande framsteg inom olika branscher.
Dela på
MET3DP Technology Co, LTD är en ledande leverantör av lösningar för additiv tillverkning med huvudkontor i Qingdao, Kina. Vårt företag är specialiserat på 3D-utskriftsutrustning och högpresterande metallpulver för industriella tillämpningar.
Förfrågan för att få bästa pris och anpassad lösning för ditt företag!
Relaterade artiklar
Om Met3DP
Senaste uppdateringen
Vår produkt
KONTAKTA OSS
Har du några frågor? Skicka oss meddelande nu! Vi kommer att betjäna din begäran med ett helt team efter att ha fått ditt meddelande.
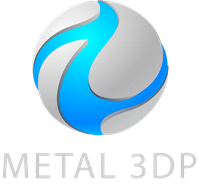
Metallpulver för 3D-printing och additiv tillverkning