3D Printing Metal Powders:Raw Materials for Mechanical Alloying
Innehållsförteckning
Imagine a world where complex metal parts materialize from a digital blueprint, layer by layer, with intricate details and exceptional strength. This futuristic vision is becoming a reality thanks to the magic of 3D printing. But just like any masterpiece, a successful 3D-utskrift av metallpulver object starts with the right foundation – the raw materials. In this article, we’ll delve into the fascinating world of mechanical alloying, a technique used to create the perfect blend of ingredients for remarkable 3D printing outcomes.
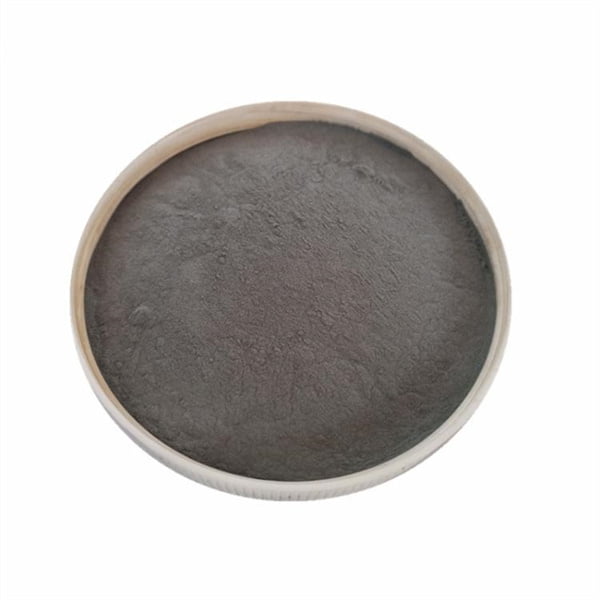
Selection of Raw Materials for Mechanical Alloying
Just as a chef carefully selects their ingredients for a gourmet meal, choosing the right raw materials is crucial for successful mechanical alloying in 3D Printing Metal Powder. Here’s a breakdown of the key players:
1. Metal Powders: These are the stars of the show, forming the base material for the final printed object. They need to possess specific characteristics:
- Partikelstorlek och fördelning: Imagine a smooth beach versus a rocky terrain – that’s the difference between desired and undesired particle size distribution. Ideally, the particles should be fine and uniformly sized to ensure consistent flow and precise layering during printing.
- Particle Morphology: Picture smooth, spherical balls versus jagged, irregular shapes. Spherical particles offer better flowability, packing density, and ultimately, superior print quality compared to their irregularly shaped counterparts.
- Kemisk sammansättning: Purity matters! The metal powders used in mechanical alloying should be of high purity to avoid introducing unwanted elements that could compromise the final product’s properties.
2. Additives: These are the supporting actors, playing a crucial role in enhancing the performance of the metal powders
- Binders: Imagine glue holding sand together in a sandcastle. Binders act similarly, improving the flowability and packing density of the metal powders during the printing process. Once the printing is complete, the binders are typically removed through a subsequent heat treatment.
- Porosity Control Agents: Think of tiny air pockets in bread dough. Porosity control agents help minimize the formation of pores within the printed object, leading to denser and ultimately, stronger parts.
- Lubricants: Friction can be a real drag, even in the microscopic world of metal powders. Lubricants help reduce friction between the particles, ensuring smooth and efficient powder flow during printing.
3. Alloying Elements: These are the secret ingredients, used to modify the properties of the final material. By carefully selecting and adding specific elements, manufacturers can tailor the printed object’s characteristics, such as:
- Strength and Hardness: Imagine a delicate teacup versus a sturdy iron skillet. Adding specific alloying elements can significantly enhance the strength and hardness of the printed metal.
- Motståndskraft mot korrosion: Think of a rusty car versus a gleaming chrome bumper. Certain alloying elements can significantly improve the material’s resistance to corrosion, making it suitable for harsh environments.
- Elektrisk konduktivitet: Picture the difference between a wooden spoon and a copper wire. By carefully choosing alloying elements, manufacturers can control the electrical conductivity of the printed object, making it suitable for various electronic applications.
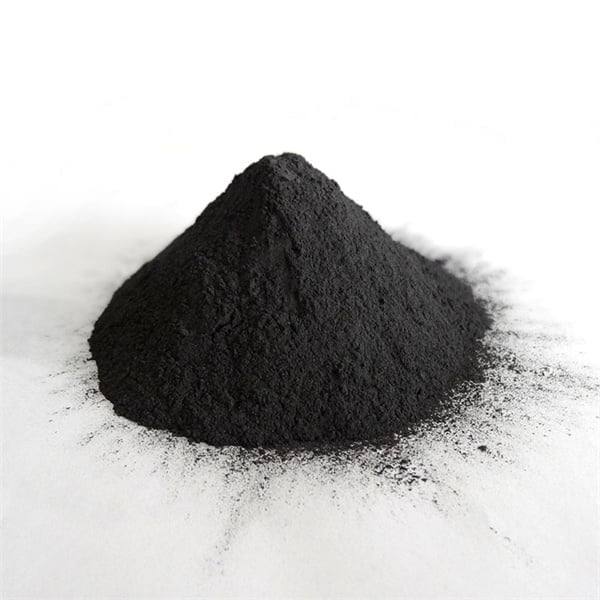
Here are 10 specific metal powder examples commonly used in mechanical alloying for 3D-utskrift av metallpulver, along with their key characteristics:
Metallpulvermodell | Sammansättning | Viktiga egenskaper | Tillämpningar |
---|---|---|---|
316L rostfritt stål | Fe-18Cr-10Ni-2Mo | Hög korrosionsbeständighet, goda mekaniska egenskaper | Aerospace, medical implants, chemical processing equipment |
Inconel 625 | Ni-20Cr-9Mo-4Fe | Excellent heat and corrosion resistance, good high-temperature strength | Turbine blades, rocket engine components, heat exchangers |
Ti-6Al-4V | Ti-6Al-4V | High strength-to-weight ratio, good biocompatibility | Flyg- och rymdkomponenter, medicinska implantat, sportartiklar |
Aluminium 6061 | Al-Mg-Si | Lightweight, good machinability, good corrosion resistance | Automotive parts, electronics enclosures, consumer goods |
Koppar | Cu | Utmärkt elektrisk ledningsförmåga, god värmeledningsförmåga | Heat sinks, electrical conductors, printed circuit boards |
Nickel | Ni | Good corrosion resistance, good ductility | Electrical components, catalysts, chemical processing equipment |
Kobolt-krom (CoCr) | Co-Cr | Hög slitstyrka, biokompatibel | Medical implants, dental prosthetics, wear-resistant components |
Hastelloy C-276 | Ni-Mo-Cr-W | Excellent corrosion resistance, high-temperature strength | Chemical processing equipment, oil and gas industry components, pollution control equipment |
Volfram | W | High melting point, high density, good wear resistance | Armor piercing ammunition, cutting tools, rocket engine nozzles |
Maråldrat stål | Fe-Ni-Mo-Cr | High strength, good ductility, good toughness | Aerospace components, firearms, golf clubs |
Selection of Raw Materials
The quality and selection of raw materials play a critical role in determining the success of the mechanical alloying process and the final 3D Printing Metal Powder object. Here’s how:
- Particle size and morphology directly impact flowability and packing density. Poor flowability can lead to inconsistencies in the printed layers, compromising the dimensional accuracy and surface quality of the final object.
- The chemical composition of the metal powder and any added elements influence the final properties. For example, the presence of impurities can weaken the material, while specific alloying elements can enhance its strength, corrosion resistance, or other desired characteristics.
- The selection of binders and lubricants affects printability and the final surface finish. The wrong binder can lead to delamination (separation of layers) or difficulty removing the binder after printing. Similarly, inadequate lubrication can cause friction issues, hindering smooth powder flow and potentially damaging the printing equipment.
In essence, the right combination of raw materials acts as the foundation for a successful 3D printing experience. By carefully selecting and optimizing each component, manufacturers can unlock the full potential of mechanical alloying and create high-quality, functional metal parts.
Comparison of Different Raw Material Options and their Advantages and Limitations
Choosing the right raw materials for mechanical alloying involves carefully weighing the advantages and limitations of each option:
Metallpulver:
- Fördelar: Wide variety of materials available, allowing for diverse applications; Can be precisely controlled for specific properties.
- Begränsningar: Cost can be higher compared to other manufacturing methods; Powder handling can be challenging and requires careful control to avoid contamination.
Additives:
- Fördelar: Improve printability and final part quality; Can be tailored to specific applications.
- Begränsningar: Can add complexity to the process; May introduce unwanted elements that need to be removed later.
Alloying Elements:
- Fördelar: Allow for precise control of the final material properties; Can create unique combinations not achievable with traditional manufacturing methods.
- Begränsningar: Can significantly increase the cost and complexity of the process; May require specialized expertise and equipment to handle.
the Future of Raw Materials for Mechanical Alloying 3D-utskrift av metallpulver
The future of mechanical alloying in 3D Printing Metal Powder is brimming with exciting possibilities. Here are some key trends to watch:
- Development of new and improved metal powders: Researchers are constantly striving to create metal powders with tighter size distribution, improved morphology, and even finer particle sizes for even greater detail and resolution in printed parts.
- Exploration of novel alloying elements: The introduction of new elements and the exploration of their combinations hold immense potential for creating materials with unique properties, pushing the boundaries of what’s achievable with traditional manufacturing methods.
- Sustainable and environmentally friendly materials: As sustainability concerns rise, the development of eco-friendly metal powders and biodegradable binders is gaining traction, paving the way for a more responsible and sustainable future for 3D printing.
The selection of raw materials plays a pivotal role in the success of mechanical alloying 3D printing. By understanding the different options, their properties, and their impact on the final product, manufacturers can unlock the full potential of this revolutionary technology and create high-quality, functional metal parts for diverse applications.
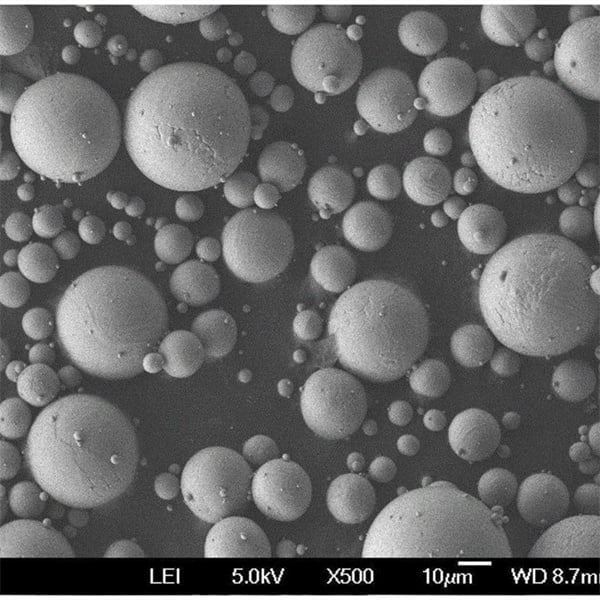
VANLIGA FRÅGOR
Q: What are the benefits of using mechanical alloying for 3D-utskrift av metallpulver?
A: Mechanical alloying offers several advantages, including:
- The ability to create unique and tailored material properties: By carefully selecting and combining different metal powders and alloying elements, manufacturers can create materials with specific characteristics not achievable with traditional manufacturing methods.
- Improved powder quality and printability: Mechanical alloying can help refine the powder particles, leading to improved flowability, packing density, and ultimately, better print quality.
Q: What are some of the challenges associated with using mechanical alloying for 3D printing metal powders?
A: While offering significant benefits, mechanical alloying also presents some challenges:
- Process complexity: Compared to traditional powder production methods, mechanical alloying can be a more complex and time-consuming process, requiring specialized equipment and expertise.
- Cost considerations: The cost of raw materials, particularly high-purity metal powders and specific alloying elements, can be higher compared to other 3D printing techniques.
- Quality control: Maintaining consistent powder quality and ensuring minimal contamination throughout the process requires rigorous control measures.
Q: What are the typical applications of mechanical alloying 3D printing?
A: Mechanical alloying 3D printing finds application in various industries due to its ability to create high-performance metal parts with unique properties. Here are some examples:
- Aerospace: Manufacturing lightweight and high-strength components for aircraft, satellites, and spacecraft.
- Medical implants: Creating customized implants with biocompatible materials for knees, hips, and other body parts.
- Fordon: Developing custom-designed parts for engines, transmissions, and other automotive components.
- Elektronik: Producing intricate components for heat sinks, electrical connectors, and printed circuit boards.
- Tooling and machinery: Creating wear-resistant and high-precision tools for various industrial applications.
Q: How does the future of mechanical alloying 3D printing look?
The future of mechanical alloying 3D printing is promising, with several exciting developments on the horizon:
- Advancements in automation: Increased automation can streamline the process, reduce costs, and improve consistency in powder production.
- Sustainability focus: The development of eco-friendly materials and processes will be crucial for a more sustainable future of 3D printing.
- Emerging applications: As the technology matures and costs decrease, we can expect to see mechanical alloying 3D printing applied in new and innovative ways across various industries.
In conclusion, the selection of raw materials plays a critical role in the success of mechanical alloying 3D printing. By understanding the different options, their properties, and their impact on the final product, manufacturers can unlock the immense potential of this technology and contribute to its continued development and diverse applications in the years to come.
Dela på
MET3DP Technology Co, LTD är en ledande leverantör av lösningar för additiv tillverkning med huvudkontor i Qingdao, Kina. Vårt företag är specialiserat på 3D-utskriftsutrustning och högpresterande metallpulver för industriella tillämpningar.
Förfrågan för att få bästa pris och anpassad lösning för ditt företag!
Relaterade artiklar
Om Met3DP
Senaste uppdateringen
Vår produkt
KONTAKTA OSS
Har du några frågor? Skicka oss meddelande nu! Vi kommer att betjäna din begäran med ett helt team efter att ha fått ditt meddelande.
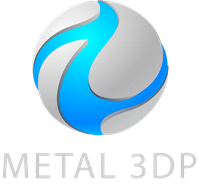
Metallpulver för 3D-printing och additiv tillverkning
FÖRETAG
PRODUKT
cONTACT INFO
- Qingdao City, Shandong, Kina
- [email protected]
- [email protected]
- +86 19116340731