Tillämpningsfall av metallpulver för 3D-utskrift i olika branscher
Innehållsförteckning
Tänk dig att bygga komplexa föremål lager för lager, inte med tegelstenar och murbruk, utan med mikroskopiska metallpartiklar. Detta är inte science fiction, det är verkligheten i Metallpulver för 3D-utskrift, a revolutionary technology rapidly transforming how we design and manufacture across various industries.
Metal 3D Printing: A Revolution in the Making
Traditional metalworking methods like casting, forging, and machining have served us well for centuries. However, they often come with limitations. Complex geometries can be challenging to achieve, and machining inevitably creates waste. 3D Printing Metal Powder disrupts this paradigm. It allows for the creation of intricate, lightweight structures with minimal material waste. Think of it like building intricate sandcastles, but with metal and unparalleled precision.
How Does Metal 3D Printing Work?
There are several metal 3D printing techniques, each with its own advantages and applications. Here’s a simplified breakdown of two popular methods:
- Selektiv lasersmältning (SLM): A high-powered laser beam selectively melts metal powder particles together, building the object layer by layer according to a digital blueprint. Imagine a laser acting like a tiny welding torch, meticulously fusing metal particles to create the desired shape.
- Smältning med elektronstråle (EBM): Similar to SLM, but in a vacuum chamber using an electron beam instead of a laser. This method is particularly well-suited for reactive metals like titanium, which can be prone to oxidation in a traditional laser melting environment.
The beauty of 3D printing lies in its design freedom. Unlike traditional methods where the form often dictates the function, metal 3D printing allows for complex, lightweight designs that optimize performance. Think of creating intricate internal structures within a part, something impossible with traditional techniques. This opens doors for innovation across various industries.
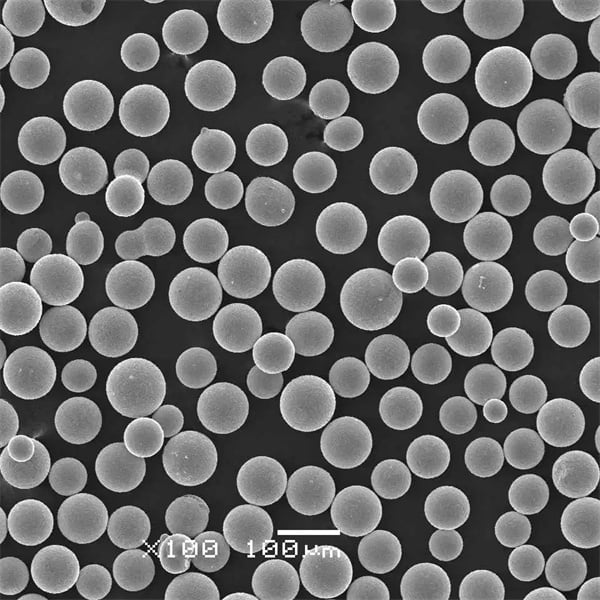
Tillämpning av Metallpulver för 3D-utskrift inom flyg- och rymdindustrin
The aerospace industry has been an early adopter of 3D Printing Metal Powder. Here’s why:
- Lättvikt: Every gram counts when it comes to fuel efficiency in airplanes. Metal 3D printing allows for the creation of strong, lightweight components with intricate internal structures, reducing overall weight and increasing fuel efficiency.
- Del Konsolidering: Imagine combining multiple parts into a single, 3D-printed component. This not only reduces weight but also simplifies assembly and improves overall part performance. Think of a complex engine bracket that used to be several machined parts, now consolidated into a single, lighter, and more robust component.
- Snabb prototypframtagning: Developing new aircraft designs is a complex and time-consuming process. Metal 3D printing allows for the rapid creation of functional prototypes, enabling engineers to test and iterate on designs quickly and efficiently. This can significantly reduce development time and costs.
Exempel på detta:
- GE Aviation uses 3D printing to create complex fuel nozzles for the LEAP jet engine, reducing weight by 10% compared to traditionally manufactured versions [Source 1].
- Flygbuss is exploring the use of 3D-printed metal components for its next-generation A350 XWB aircraft [Source 2].
The application of 3D printed metal powder in Automobiles
The automotive industry is also embracing the potential of 3D Printing Metal Powder:
- Anpassning: Imagine creating lightweight, high-performance components for high-end sports cars or even personalized parts for classic car restorations. 3D printing allows for this level of customization that traditional manufacturing struggles to achieve.
- Prestanda delar: Metal 3D printing allows for the creation of intricate internal structures within engine components, optimizing performance and reducing weight. Think of a lighter, stronger piston with internal cooling channels, leading to a more efficient engine.
- Snabb prototypframtagning: Similar to the aerospace industry, car manufacturers can leverage 3D printing to rapidly prototype and test new car parts, accelerating the development process.
Exempel på detta:
- BMW uses 3D-printed metal components for the cylinder head cover and brake calipers in its i8 sports car [Source 3].
- Vadställe is exploring the use of 3D-printed metal parts for lightweighting applications in its future vehicles [Source 4].
The application of 3D-utskrivet metallpulver in Healthcare
The impact of 3D Printing Metal Powder is revolutionizing healthcare in several ways:
- Customized Implants: Imagine creating personalized prosthetics or implants that perfectly match a patient’s unique anatomy. 3D printing allows for this level of customization, leading to improved patient outcomes and faster recovery times.
- Complex Surgical Tools: Surgeons can leverage 3D-printed metal instruments with intricate features, enabling minimally invasive procedures and improved surgical precision.
- Bioprintning: This emerging field utilizes 3D printing technology with biocompatible materials to create complex living tissues and even organs. While still in its early stages, bioprinting holds immense promise for personalized medicine and regenerative therapies.
Exempel på detta:
- Dutch medical technology company Ossur uses 3D printing to create customized cranial implants for patients with complex skull defects [Source 5].
- Surgeons at Mayo Clinic have successfully implanted a 3D-printed titanium rib cage on a patient suffering from a rare chest wall deformity [Source 6].
The application of 3D-utskrivet metallpulver in Consumer Goods
Metal 3D printing isn’t just for high-tech industries. It’s making its way into consumer goods as well:
- Anpassning: Imagine owning a pair of eyeglasses or a bicycle frame with a design completely unique to you. 3D printing allows for this level of personalization, opening doors for mass customization in the consumer goods market.
- Luxury Goods: High-end brands are utilizing 3D printing to create unique and intricate jewelry pieces or watch components, adding a touch of exclusivity to their products.
- Functional Applications: 3D printing can be used to create durable and lightweight components for sporting goods, such as custom-fit bicycle handlebars or high-performance climbing gear.
Exempel på detta:
- Jewelry designer Lucy Yin uses 3D printing to create intricate and personalized jewelry pieces [Source 7].
- German bicycle manufacturer Canyon offers custom-made bicycle handlebars using 3D printing technology [Source 8].
The Advantages and Challenges of 3D Printing with Metal Powder
While 3D Printing Metal Powder offers exciting possibilities, it’s important to acknowledge some challenges:
- Kostnad: Metal 3D printing machines and materials can be expensive compared to traditional manufacturing methods. However, as the technology matures, costs are expected to decrease.
- Komplexitet: The process requires a high level of technical expertise to operate and maintain the 3D printers and ensure quality control.
- Efterbearbetning: Metal 3D printed parts often require additional post-processing steps like support removal and surface finishing, adding to the overall production time and cost.
Despite these challenges, the advantages of 3D Printing Metal Powder are significant:
- Designfrihet: Unleash your creativity with the ability to create complex geometries that were previously impossible with traditional methods.
- Lättvikt: Create strong, lightweight components for applications where weight reduction is critical, such as aerospace and automotive industries.
- Snabb prototypframtagning: Accelerate the development process by quickly creating functional prototypes for testing and iteration.
- Del Konsolidering: Combine multiple parts into a single, 3D-printed component, simplifying assembly and improving overall part performance.
- Hållbarhet: Metal 3D printing can potentially reduce material waste compared to traditional subtractive manufacturing techniques.
The Future of Metal 3D Printing
The future of metal 3D printing is bright. As the technology continues to develop, we can expect to see:
- Minskade kostnader: Advancements in printer technology and materials will make 3D Printing Metal Powder more accessible and cost-effective.
- Snabbare utskriftshastigheter: Printing times will continue to decrease, making 3D printing a viable option for larger-scale production runs.
- Nya material: The development of new and improved metal powders will expand the range of applications for 3D printing.
- Integration with AI: Artificial intelligence will play a role in optimizing the 3D printing process, from design optimization to predictive maintenance of printers.
Metal 3D printing is poised to revolutionize how we design and manufacture across various industries. From creating lightweight aircraft components to personalized medical implants, the possibilities are endless. As this technology continues to evolve, we can expect to see even more innovative applications emerge in the years to come.
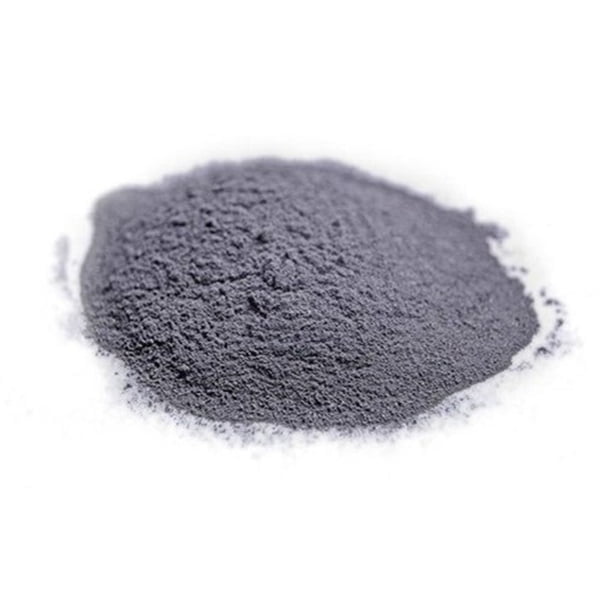
VANLIGA FRÅGOR
Fråga | Svar |
---|---|
What are the different types of metal 3D printing techniques? | Selective Laser Melting (SLM) and Electron Beam Melting (EBM) are two popular techniques. There are also binder jetting and metal deposition methods. |
What are the limitations of 3D printing with metal powder? | Cost, complexity of the process, and post-processing requirements are some current challenges. |
What are the benefits of 3D printing with metal powder? | Design freedom, lightweighting, rapid prototyping, part consolidation, and potential for sustainability are some key advantages. |
What industries are using metal 3D printing? | Aerospace, automotive, healthcare, and consumer goods are among the leading industries adopting metal 3D printing. |
What are some examples of metal 3D printed products? | In aerospace, complex fuel nozzles and lightweight engine components are being created. In automotive, customizable brake calipers and high-performance pistons are finding applications. The medical field is utilizing 3D printing for personalized prosthetics and intricate surgical tools. Even consumer goods like custom jewelry and high-end bicycle components are being produced with metal 3D printing. |
How is metal 3D printing impacting sustainability? | While the technology is still developing, 3D printing has the potential to reduce material waste compared to traditional manufacturing methods that rely on subtractive processes. Additionally, the ability to create lightweight components can contribute to improved fuel efficiency in vehicles and aircraft, leading to a lower environmental footprint. |
What are some considerations for businesses looking to adopt metal 3D printing? | The initial investment cost of metal 3D printers and materials needs to be weighed against the potential benefits like design flexibility, production time reduction, and part performance improvements. Additionally, expertise in operating and maintaining the printers, as well as quality control procedures, are crucial for successful implementation. |
Is metal 3D printing suitable for all applications? | Currently, metal 3D printing might not be the most cost-effective option for high-volume production of simple parts. However, for complex geometries, low-volume production runs, or applications requiring lightweighting and design freedom, 3D printing offers significant advantages. |
Dela på
MET3DP Technology Co, LTD är en ledande leverantör av lösningar för additiv tillverkning med huvudkontor i Qingdao, Kina. Vårt företag är specialiserat på 3D-utskriftsutrustning och högpresterande metallpulver för industriella tillämpningar.
Förfrågan för att få bästa pris och anpassad lösning för ditt företag!
Relaterade artiklar
Om Met3DP
Senaste uppdateringen
Vår produkt
KONTAKTA OSS
Har du några frågor? Skicka oss meddelande nu! Vi kommer att betjäna din begäran med ett helt team efter att ha fått ditt meddelande.
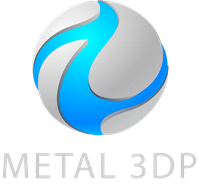
Metallpulver för 3D-printing och additiv tillverkning