Nickel 3D-utskrift Metallpulver
Innehållsförteckning
Nickel 3D-utskrift metallpulver revolutionerar tillverkningslandskapet och erbjuder en kraftfull kombination av styrka, värmebeständighet och intrikat designfrihet. Föreställ dig att skapa högpresterande komponenter för jetmotorer, medicinska implantat eller krävande kemisk processutrustning - allt med precisionen och flexibiliteten i 3D-utskrift. Den här artikeln dyker in i den fascinerande världen av nickel 3D-tryckmetallpulver och utforskar dess egenskaper, applikationer, fördelar och överväganden.
Vad är metallpulver för 3D-utskrift av nickel?
Nickel 3D-tryckmetallpulver är inte ditt genomsnittliga kontorsmaterial. Det är ett noggrant konstruerat material som vanligtvis tillverkas av rent nickel eller nickellegeringar. Dessa legeringar innehåller element som krom, järn och molybden, som var och en spelar en avgörande roll för att förbättra specifika egenskaper som styrka, korrosionsbeständighet och högtemperaturprestanda. Själva nickelpulvret är otroligt fint, med partikelstorlekar som sträcker sig från 15 till 150 mikrometer - det är ungefär 15-150 gånger tunnare än ett människohår! Denna finkorniga struktur möjliggör exceptionell detaljrikedom och intrikata geometrier under 3D-utskriftsprocessen.
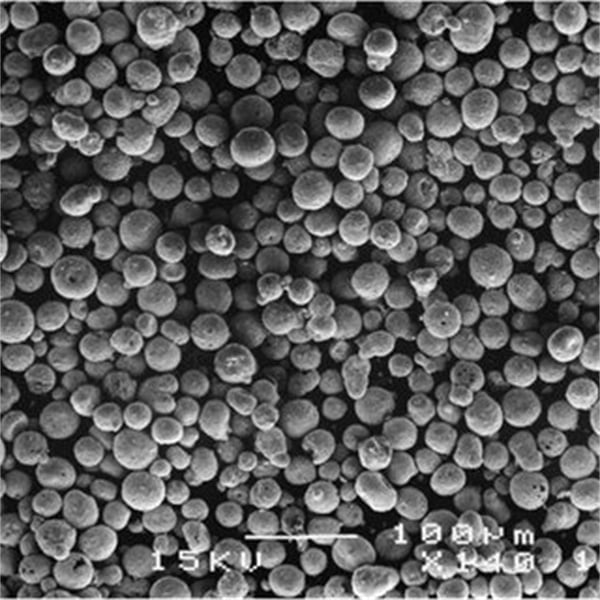
Vilka 3D-utskriftsprocesser är lämpliga för 3D-utskrivna metallpulver av nickel?
Nickel Metallpulver för 3D-utskrift lyser främst i två framstående 3D-utskriftsprocesser:
- Laserpulverbäddfusion (LPBF): Föreställ dig en laser som fungerar som en himmelsk skulptör, som omsorgsfullt smälter små nickelpulverpartiklar lager för lager för att bygga upp det önskade 3D-objektet. LPBF erbjuder otrolig precision och detaljrikedom, vilket gör den idealisk för komplexa geometrier och krävande applikationer.
- Smältning med elektronstråle (EBM): Denna teknik ökar värmen genom att använda en kraftfull elektronstråle för att smälta nickelpulvret. EBM utmärker sig genom att skapa detaljer med överlägsna mekaniska egenskaper, särskilt för applikationer som kräver hög hållfasthet och värmebeständighet.
Både LPBF och EBM erbjuder tydliga fördelar, och valet beror ofta på de specifika kraven i projektet. LPBF är allmänt känt för sina finare detaljer och intrikata funktioner, medan EBM levererar delar med exceptionell styrka och hög temperaturprestanda.
Fördelarna med metallpulver för 3D-utskrift av nickel
Nickel 3D-printing metallpulver har ett fängslande utbud av fördelar som förändrar olika industrier:
- Oöverträffad styrka: Nickel och dess legeringar är kända för sitt exceptionella förhållande mellan styrka och vikt. Jämfört med traditionella tillverkningsmetoder som maskinbearbetning eller gjutning gör 3D-utskrift med nickelpulver det möjligt att skapa lätta men ändå otroligt starka komponenter. Detta gör det idealiskt för tillämpningar inom flyg- och rymdindustrin, där varje gram räknas, eller för krävande maskinkomponenter som måste tåla betydande påfrestningar.
- Överlägsen värmebeständighet: Nickellegeringar är utmärkta i miljöer där temperaturen stiger. Föreställ dig jetmotordelar som uthärdar förbränningens brännande inferno eller utrustning för kemisk bearbetning som hanterar brännande heta reaktioner. 3D-printade metallpulver i nickel tål dessa extrema temperaturer med minimal nedbrytning, vilket gör dem till oersättliga material för sådana tillämpningar.
- Designfrihet släppt fri: 3D-printing bryter den traditionella tillverkningens bojor och gör det möjligt att skapa komplexa geometrier som skulle vara omöjliga med konventionella tekniker. Denna designfrihet gör det möjligt för ingenjörer att skapa lätta strukturer med interna kanaler för förbättrad värmeavledning eller invecklade komponenter med optimerad prestanda.
- Minskat materialavfall: Traditionell tillverkning resulterar ofta i betydande materialskrot. 3D-utskrift med nickelpulver erbjuder ett mer hållbart tillvägagångssätt. Det oanvända pulvret kan återvinnas och återanvändas i efterföljande tryckprocesser, vilket minimerar avfallet och optimerar materialutnyttjandet.
- Massanpassning möjliggjord: 3D-printing med nickelpulver är perfekt för applikationer som kräver små serier av kundanpassade komponenter. Till skillnad från traditionella metoder med höga installationskostnader möjliggör 3D-utskrift snabbt skapande av unika delar utan behov av omfattande verktyg eller produktionslinjeändringar.
Nackdelar med Nickel 3D-utskrift Metallpulver
Samtidigt som det har en mängd fördelar, ger nickel 3D-tryckmetallpulver också några överväganden:
- Kostnad: Tekniken och materialen som används vid 3D-utskrift med nickelpulver kan vara dyra jämfört med vissa konventionella tekniker. Denna kostnadsfaktor minskar gradvis i takt med att tekniken mognar, men det är fortfarande en viktig faktor att ta hänsyn till vid projektbudgetering.
- Krav på efterbearbetning: 3D-utskrivna delar i nickel kan kräva ytterligare efterbehandlingssteg som värmebehandling eller borttagning av stödstruktur. Dessa ytterligare steg kan öka den totala produktionstiden och kostnaden.
- Försiktighetsåtgärder: Nickelpulver kan utgöra en hälsorisk vid inandning. Därför är det viktigt med rätt säkerhetsutrustning och ventilationssystem under 3D-utskriftsprocessen.
- Begränsat materialval: Även om det finns en rad alternativ för nickellegeringar är urvalet av utskrivbara nickelpulver inte lika stort som vissa andra 3D-utskriftsmaterial. Pågående forskning och utveckling utökar dock kontinuerligt de tillgängliga alternativen.
Tillämpningar av Nickel 3D-utskrift Metallpulver
Nickel 3D-skrivande metallpulver används i ett brett spektrum av industrier, var och en drar nytta av dess unika egenskaper:
- Aerospace: Nickellegeringar är jetmotorernas arbetshästar, som uthärdar den brännande hettan och det enorma trycket vid förbränning. LPBF-tryckta nickelkomponenter som turbinblad och brännkammare erbjuder exceptionella styrke-/viktförhållanden, förbättrad effektivitet och möjligheten att skapa intrikata kylkanaler för optimal värmehantering.
- Medicinska implantat: Biokompatibiliteten hos vissa nickellegeringar, särskilt Nitinol (nickel-titan), gör dem idealiska för medicinska implantat. 3D-utskrift med nitinolpulver gör det möjligt att skapa skräddarsydda implantat som stentar, ledproteser och ortodontiska anordningar. Dessa implantat kan skräddarsys efter en patients specifika anatomi, vilket potentiellt kan förbättra passform, funktion och långsiktig framgång.
- Kemisk bearbetning: Nickels exceptionella korrosionsbeständighet gör det till en perfekt passform för de tuffa miljöer som förekommer i kemisk processutrustning. 3D-printade nickelkomponenter som ventiler, pumpar och värmeväxlare tål exponering för aggressiva kemikalier och höga temperaturer, vilket säkerställer utrustningens livslängd och driftsäkerhet.
- Olja och gas: 3D-printade nickelkomponenter gör sig alltmer gällande inom olje- och gasindustrin, från borrverktyg till rör och ventiler. Deras styrka, värmebeständighet och korrosionsbeständighet gör dem idealiska för att klara de krävande förhållanden som uppstår under prospektering och produktion.
- Fordon: Strävan efter lätta och högpresterande fordon driver på användningen av 3D-utskrifter med nickel i fordonsapplikationer. Komponenter som kolvar, vevstakar och till och med invecklade delar i komplexa motorkonstruktioner kan dra nytta av den styrka och designfrihet som 3D-utskrift i nickel erbjuder.
Utöver dessa kärnapplikationer gör nickel 3D-tryckmetallpulver också inbrott i olika framväxande områden:
- Robotik: Möjligheten att skapa lätta men ändå robusta komponenter driver på användningen av 3D-utskrifter med nickel inom robotteknik. Komplexa robotarmar, gripdon och till och med inre växlar kan 3D-printas med nickelpulver, vilket förbättrar styrkan och optimerar prestandan.
- Försvar: Nickels förmåga att motstå tuffa miljöer och ballistiska stötar gör det till ett värdefullt material för försvarsapplikationer. 3D-printade nickelkomponenter kan användas i pansarfordon, vapensystem och till och med i skräddarsydda skyddsutrustningar.
Framtiden för metallpulver för 3D-tryckning med nickel är full av potential. I takt med att forsknings- och utvecklingsinsatserna fortsätter kan vi förvänta oss att se ännu mer innovativa tillämpningar dyka upp, som flyttar fram gränserna för design och prestanda i olika branscher.
Välja rätt metallpulver för 3D-utskrift av nickel
Det finns ett växande utbud av metallpulver för 3D-utskrift med nickel och för att välja det lämpligaste alternativet måste man noga överväga flera faktorer:
- Krav för ansökan: Den avsedda användningen av den 3D-utskrivna komponenten är av största vikt. Faktorer som erforderlig styrka, värmebeständighet och korrosionsbeständighet kommer att styra valet av det lämpligaste nickellegeringspulvret.
- 3D-utskriftsprocess: Som diskuterats tidigare är LPBF och EBM de primära processerna för 3D-utskrift av nickel. Den valda processen kan påverka valet av lämpligt nickelpulver på grund av variationer i bearbetningsparametrar och kompatibilitet.
- Egenskaper för pulver: Partikelstorlek, flytbarhet och syrehalt är några viktiga pulveregenskaper att ta hänsyn till. Finare partikelstorlekar möjliggör i allmänhet finare detaljer, medan god flytbarhet säkerställer smidiga tryckprocesser. Syreinnehållet kan påverka de mekaniska egenskaperna hos den slutliga tryckta delen.
- Kostnad: Nickellegeringspulver kan variera avsevärt i kostnad. Genom att förstå budgetbegränsningarna och prestandakraven kan man lättare hitta en balans mellan kostnad och funktionalitet.
Att rådgöra med en kvalificerad leverantör av 3D-printingmaterial och en 3D-printingexpert är avgörande för att välja den optimala nickel 3D-utskrift metallpulver för dina specifika behov.
VANLIGA FRÅGOR
F: Är metallpulver för 3D-utskrift av nickel säkert?
Svar: Nickelpulver kan utgöra en hälsorisk vid inandning. Korrekt säkerhetsutrustning som andningsskydd och välventilerade tryckmiljöer är avgörande för att minska dessa risker.
Q: Hur starka är 3D-printade nickeldelar jämfört med traditionellt tillverkade delar?
A: 3D-printade nickelkomponenter kan uppnå exceptionella styrke-/viktförhållanden, ofta jämförbara eller till och med bättre än för traditionellt tillverkade komponenter.
Q: Kan jag 3D-printa nickelpulver hemma?
S: För närvarande är 3D-utskrift med nickelpulver främst en industriell applikation på grund av den specialiserade utrustningen, säkerhetsöverväganden och materialkostnader.
F: Vilka är miljöfördelarna med 3D-utskrifter med nickelpulver?
A: Jämfört med traditionell tillverkning med mycket skrotmaterial erbjuder 3D-utskrift med nickelpulver ett mer hållbart tillvägagångssätt.
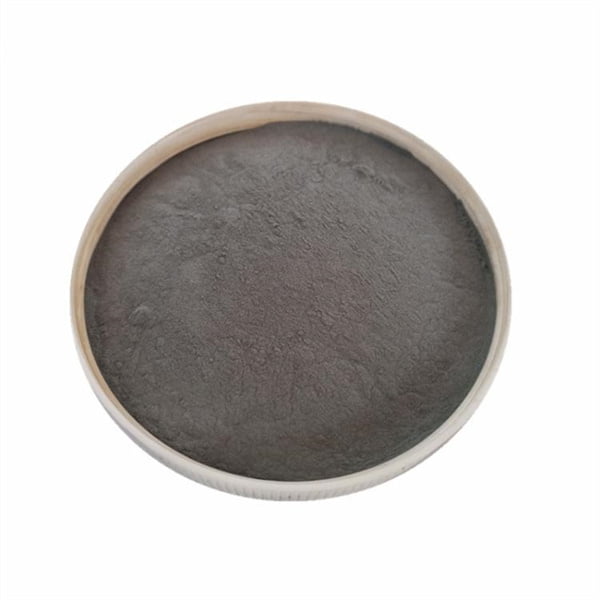
Framtiden för metallpulver för 3D-utskrift av nickel
Världen av metallpulver för 3D-utskrift med nickel är långt ifrån statisk. När forsknings- och utvecklingsinsatserna fortsätter kan vi förvänta oss att se spännande framsteg som ytterligare kommer att frigöra potentialen i denna transformativa teknik:
- Materialinnovation: Utvecklingen av nya formuleringar för nickellegeringar är ett område som ständigt utforskas. Forskarna strävar efter att skapa legeringar med ännu bättre kombinationer av styrka, värmebeständighet och korrosionsbeständighet, vilket flyttar fram gränserna för vad som är möjligt. Föreställ dig nickellegeringar som tål ännu högre temperaturer för nästa generations jetmotorkomponenter, eller legeringar med exceptionell biokompatibilitet för ett bredare utbud av medicinska implantat.
- Tryckning av flera material: Framtiden är lovande för 3D-utskrifter med flera olika material i en och samma konstruktion. Detta skulle göra det möjligt att skapa komponenter med en kombination av egenskaper, som en lättviktig nickelkärnstruktur innesluten i ett slitstarkt yttre lager. Detta öppnar dörrar för banbrytande tillämpningar inom områden som robotik och rymdfart.
- Skalbarhet och kostnadsreducering: I takt med att 3D-printingtekniken mognar och användningsgraden ökar kan vi förvänta oss att se en minskning av den totala kostnaden för metallpulver för 3D-printing med nickel och själva printprocesserna. Detta kommer att göra tekniken mer tillgänglig för ett bredare spektrum av industrier och applikationer, vilket påskyndar innovation och marknadspenetration.
- Förbättringar av hållbarheten: Fokus på hållbara tillverkningsmetoder driver på forskningen om hur man ytterligare kan minska avfallet och miljöpåverkan vid 3D-utskrifter med nickel. Detta kan innebära framsteg i pulveråtervinningstekniker eller utveckling av helt nya, miljövänliga produktionsmetoder för nickelpulver.
- Standardisering och certifiering: I takt med att användningen av metallpulver för 3D-utskrift av nickel växer blir behovet av standardiserade processer och certifieringar allt viktigare. Detta kommer att säkerställa konsekvent kvalitet, säkerhet och prestanda för 3D-tryckta nickelkomponenter i olika branscher.
Konvergensen av dessa framsteg målar en bild av en framtid där nickel 3D-tryckning metallpulver spelar en ännu mer transformativ roll. Från att revolutionera medicinska behandlingar till att möjliggöra design av lättare och effektivare flygplan är möjligheterna verkligen obegränsade.
Slutsats
Nickel 3D-printing metallpulver är ett kraftfullt verktyg som är redo att omdefiniera tillverkning inom olika branscher. Dess exceptionella kombination av styrka, värmebeständighet och designfrihet öppnar upp en värld av möjligheter för ingenjörer och designers. I takt med att forsknings- och utvecklingsinsatserna fortsätter kommer framtiden för nickel 3D-printing metallpulver att skina av innovation och lova att forma hur vi designar, tillverkar och interagerar med världen omkring oss.
Dela på
MET3DP Technology Co, LTD är en ledande leverantör av lösningar för additiv tillverkning med huvudkontor i Qingdao, Kina. Vårt företag är specialiserat på 3D-utskriftsutrustning och högpresterande metallpulver för industriella tillämpningar.
Förfrågan för att få bästa pris och anpassad lösning för ditt företag!
Relaterade artiklar
Om Met3DP
Senaste uppdateringen
Vår produkt
KONTAKTA OSS
Har du några frågor? Skicka oss meddelande nu! Vi kommer att betjäna din begäran med ett helt team efter att ha fått ditt meddelande.
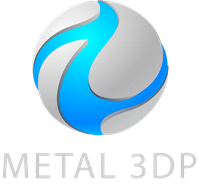
Metallpulver för 3D-printing och additiv tillverkning