High-Precision Propeller Hubs for Drones via 3D Printing
Innehållsförteckning
Introduction: The Critical Role of Propeller Hubs in Drone Performance and Reliability
The Unmanned Aerial Vehicle (UAV), or drone, industry is experiencing exponential growth, transforming sectors from logistics and agriculture to surveillance and entertainment. At the heart of every multirotor drone’s propulsion system lies the propeller hub – a seemingly simple component with a profoundly critical function. The propeller hub serves as the central structural interface, securely connecting the motor shaft to the propeller blades. Its primary role is to efficiently transfer the motor’s torque to the blades, generating the thrust necessary for lift, maneuverability, and stable flight.
As drone applications become increasingly sophisticated and demanding – carrying heavier payloads, flying longer distances, operating in challenging environments, and executing precision maneuvers – the performance requirements for every component, especially the propeller hub, escalate significantly. A failure in the propeller hub can lead to catastrophic loss of control, highlighting the need for exceptional strength, durability, and reliability. Furthermore, the hub’s weight directly impacts the drone’s overall efficiency, flight time, and payload capacity. Reducing component mass without compromising structural integrity is a constant engineering challenge.
Traditionally, propeller hubs have been manufactured using methods like CNC machining from billet aluminum or injection molding for lower-end applications. While effective, these methods can present limitations in terms of design complexity, material utilization, and production lead times, particularly for custom or low-to-medium volume requirements often seen in the specialized drone market.
This is where metal additive manufacturing (AM), commonly known as metal 3D-utskrifter, emerges as a transformative technology. Metal AM enables the production of highly complex, lightweight, and robust propeller hubs with geometries previously unattainable through conventional means. It allows for rapid design iteration, part consolidation, and the use of advanced high-performance alloys specifically suited for demanding aerospace and industrial applications. Companies like Met3dp, leveraging deep expertise in metal AM processes and materials, are empowering drone manufacturers and operators to push the boundaries of performance and reliability. By embracing metal 3D printing, businesses can achieve superior component performance, streamline their supply chains, and gain a competitive edge in the rapidly evolving drone market.
What Are Drone Propeller Hubs Used For? Key Applications in Commercial and Industrial UAVs
The drone propeller hub is the linchpin of the propulsion system, fundamentally responsible for translating motor power into aerodynamic thrust. Its precise function involves several key aspects:
- Torque Transmission: Securely gripping both the motor shaft (often via a keyed or press-fit interface) and the propeller blades (typically through bolting patterns or integrated clamps), ensuring efficient transfer of rotational force without slippage.
- Structural Support: Withstanding the significant centrifugal forces generated by rapidly spinning propellers, as well as the bending moments and vibrations inherent in flight dynamics.
- Blade Alignment: Maintaining the precise pitch and alignment of the propeller blades relative to each other and the motor axis, which is critical for balanced operation, efficiency, and minimizing vibration.
- Heat Dissipation: In some high-power applications, the hub can play a role in dissipating heat generated by the motor.
Given these critical functions, propeller hubs are indispensable across the entire spectrum of drone applications, particularly in the demanding commercial and industrial sectors where reliability and performance are paramount. Key application areas include:
- Aerial Surveillance and Security: Drones used for monitoring critical infrastructure, border patrol, or event security require extended flight times and extreme reliability. Lightweight, high-strength hubs contribute to endurance and operational safety. B2B Keyword Focus: Reliable UAV component suppliers, high-endurance drone parts.
- Inspection and Monitoring: UAVs inspecting wind turbines, power lines, bridges, or pipelines operate in challenging environments and require precise maneuverability. Robust hubs ensure operational integrity during close-proximity flights and varying wind conditions. B2B Keyword Focus: Industrial drone inspection parts, durable UAV components.
- Logistics and Delivery: Delivery drones carrying packages demand high payload capacity and operational efficiency. Optimized, lightweight hubs directly contribute to maximizing payload weight and extending delivery range. B2B Keyword Focus: Drone delivery component manufacturing, wholesale drone parts.
- Mapping and Surveying: Drones equipped with high-resolution cameras or LiDAR sensors need stable flight platforms for accurate data acquisition. Balanced and rigid hubs minimize vibrations, improving data quality. B2B Keyword Focus: Geospatial UAV parts supplier, precision drone components.
- Agriculture: Precision agriculture drones used for crop monitoring, spraying, or seeding benefit from durable components that can withstand harsh outdoor conditions and repetitive use. B2B Keyword Focus: Agricultural drone parts manufacturer, robust UAV solutions.
- Flyg- och rymdindustrin samt försvarsindustrin: Military and high-end aerospace drones operate under the most stringent performance and reliability standards. Hubs must withstand extreme G-forces, temperature ranges, and operational stresses. B2B Keyword Focus: Aerospace-grade UAV components, defense drone parts supplier.
- High-Performance Racing and Cinematography: While sometimes considered recreational, professional drone racing and high-speed aerial cinematography push components to their limits, demanding maximum strength-to-weight ratios for agility and responsiveness.
In all these applications, the propeller hub is not just a passive connector but an active contributor to the drone’s overall performance envelope, safety margins, and operational effectiveness. Sourcing high-quality, reliably manufactured hubs is therefore a critical consideration for drone designers, manufacturers, and procurement managers.

Why Use Metal 3D Printing for Drone Propeller Hubs? Unlocking Performance Gains and Supply Chain Advantages
While traditional manufacturing methods like CNC machining have long served the drone industry, metal additive manufacturing offers a compelling suite of advantages specifically beneficial for producing high-performance propeller hubs. Choosing metal AM is not just about adopting a new technology; it’s about strategically leveraging its capabilities to achieve tangible improvements in performance, design freedom, and operational efficiency.
Here’s why forward-thinking drone manufacturers and B2B suppliers are turning to metal 3D printing services:
- Unprecedented Design Freedom & Topology Optimization:
- Utmaning: Traditional methods are constrained by tool access and subtractive processes, often leading to heavier-than-necessary designs.
- AM Solution: Metal 3D printing builds parts layer-by-layer, enabling the creation of intricate internal structures and organic shapes. Engineers can employ topology optimization software to place material only where structurally needed, drastically reducing weight while maintaining or even increasing stiffness and strength. This leads to lighter hubs, translating directly to longer flight times, increased payload capacity, or enhanced agility. Internal cooling channels or integrated sensor mounts become feasible.
- Del Konsolidering:
- Utmaning: Complex hub assemblies might traditionally involve multiple machined components fastened together, increasing weight, assembly time, and potential failure points.
- AM Solution: Metal AM allows multiple functional elements to be integrated into a single, monolithic printed part. This reduces part count, simplifies assembly, lowers overall weight, and inherently increases structural integrity by eliminating joints and fasteners.
- Superior Material Properties & Selection:
- Utmaning: Standard wrought or cast aluminum alloys may not offer the optimal balance of properties required for extreme performance drones.
- AM Solution: Metal 3D printing unlocks the use of advanced alloys specifically designed for additive processes, such as high-strength aluminum alloys (like Scalmalloy®) or even titanium alloys for ultimate performance. These materials offer exceptional strength-to-weight ratios, fatigue resistance, and performance at elevated temperatures, perfectly aligning with the demands of advanced UAV applications. Companies like Met3dp provide access to a wide range of high-quality metal powders optimized for AM.
- Rapid Prototyping and Design Iteration:
- Utmaning: Iterating designs using traditional tooling can be slow and expensive.
- AM Solution: New hub designs can be printed and tested in a matter of days, not weeks or months. This accelerates the development cycle, allowing engineers to quickly validate performance improvements, optimize designs, and respond faster to market needs or custom requirements.
- On-Demand Production & Reduced Inventory:
- Utmaning: Maintaining large inventories of various hub designs ties up capital and warehouse space. Minimum order quantities for traditional methods can be prohibitive for custom or low-volume needs.
- AM Solution: Hubs can be printed on-demand, directly from digital files. This facilitates a digital inventory model, reducing warehousing costs and waste. It’s ideal for producing custom hubs tailored to specific drone models or applications, as well as for spare parts management. B2B Keyword Focus: On-demand drone component manufacturing, digital inventory UAV parts.
- Materialeffektivitet:
- Utmaning: CNC machining is a subtractive process that can generate significant material waste (swarf), especially for complex parts starting from large billets.
- AM Solution: Powder bed fusion processes, a common type of 3D-utskrift av metall, typically use only the material needed for the part and supports, with unfused powder being recyclable. This leads to higher material utilization and reduced waste, contributing to more sustainable manufacturing.
Partnering with an experienced metal AM provider like Met3dp ensures access to cutting-edge printing technologies, optimized process parameters, and rigorous quality control, guaranteeing that the theoretical advantages of AM translate into tangible, reliable performance benefits for critical drone components like propeller hubs.
Recommended Materials for 3D Printed Drone Hubs: Comparing AlSi10Mg and Scalmalloy® for Optimal Performance
The choice of material is paramount when designing and manufacturing drone propeller hubs via metal additive manufacturing. The material directly dictates the component’s weight, strength, durability, fatigue life, and resistance to environmental factors – all critical parameters for drone performance and safety. While various metals can be 3D printed, two aluminum-based alloys stand out for their suitability in drone applications: AlSi10Mg och Scalmalloy® -legering.
Met3dp, leveraging its advanced powder manufacturing capabilities including gas atomization and PREP technologies, ensures the availability of high-quality, spherical metal powders crucial for achieving optimal results with these alloys in AM processes like Selective Laser Melting (SLM) or Direct Metal Laser Sintering (DMLS). Understanding the distinct characteristics of each alloy helps engineers and procurement managers select the best option for their specific requirements.
1. AlSi10Mg:
- Beskrivning: A widely used and well-characterized aluminum alloy containing silicon and magnesium. It’s essentially a casting alloy adapted for additive manufacturing, known for its good balance of properties and excellent processability in laser powder bed fusion systems.
- Viktiga egenskaper:
- Lättviktare: Typical density around 2.67 g/cm³.
- Good Strength: Offers respectable tensile and yield strength suitable for many drone applications after appropriate heat treatment.
- Utmärkt värmeledningsförmåga: Beneficial for dissipating heat from the motor.
- God korrosionsbeständighet: Suitable for operation in various environmental conditions.
- Processbarhet: Mature printing parameters are widely available, leading to reliable and repeatable results.
- Kostnadseffektivitet: Generally more economical compared to higher-performance specialty alloys.
- Ideal Use Cases: General aviation drones, commercial delivery/inspection UAVs where a good balance of performance and cost is required, rapid prototyping, applications not pushing the absolute limits of G-force or stress.
2. Scalmalloy®:
- Beskrivning: A patented high-performance aluminum-magnesium-scandium alloy specifically developed for additive manufacturing by APWORKS. It is designed to provide significantly higher mechanical properties compared to traditional aluminum alloys.
- Viktiga egenskaper:
- Very High Strength: Tensile and yield strength approaching that of some titanium alloys, significantly exceeding AlSi10Mg. This allows for even greater weight reduction through optimized designs.
- Excellent Ductility and Fatigue Strength: Offers superior resistance to crack propagation and failure under cyclic loading – critical for the high-vibration environment of propeller hubs.
- Lättviktare: Density is similar to other aluminum alloys (approx. 2.67 g/cm³), resulting in an exceptional strength-to-weight ratio.
- God korrosionsbeständighet: Suitable for demanding operational environments.
- Designed for AM: Optimized microstructure for additive manufacturing processes, yielding fine-grained, robust parts.
- Ideal Use Cases: High-performance drones (racing, heavy-lift, military/aerospace), applications demanding maximum weight savings without compromising strength, components subjected to extreme vibrations or cyclic loads, mission-critical systems where reliability is non-negotiable.
Comparative Overview:
Funktion | AlSi10Mg | Scalmalloy® -legering | Significance for Drone Hubs |
---|---|---|---|
Primär förmån | Balanced properties, cost-effectiveness | Exceptional strength-to-weight ratio, fatigue life | Choose based on performance requirements vs. budget constraints |
Utbyteshållfasthet | Good (e.g., ~230-300 MPa, heat treated) | Very High (e.g., ~450-500 MPa, heat treated) | Higher strength allows for thinner walls, less material, lighter hubs |
Täthet | ~2.67 g/cm³ | ~2.67 g/cm³ | Both offer inherent lightweight advantages of aluminum |
Trötthetsliv | Måttlig | Utmärkt | Crucial for durability under constant vibration and rotation |
Processbarhet | Mature, Widely Available | Requires optimized parameters, specialized know-how | Partnering with experienced providers like Met3dp is key |
Relativ kostnad | Lägre | Högre | Budgetary factor in component sourcing decisions |
Export to Sheets
Why Material Quality Matters:
Regardless of the alloy chosen, the quality of the metal powder feedstock is critical. Factors like particle size distribution, sphericity, flowability, and purity directly impact the density, mechanical properties, and surface finish of the final printed part. Met3dp’s commitment to producing high-quality metal powders using advanced atomization techniques ensures that customers receive components meeting the stringent requirements of drone applications. Accessing reliable material produkter is the foundation of successful additive manufacturing.
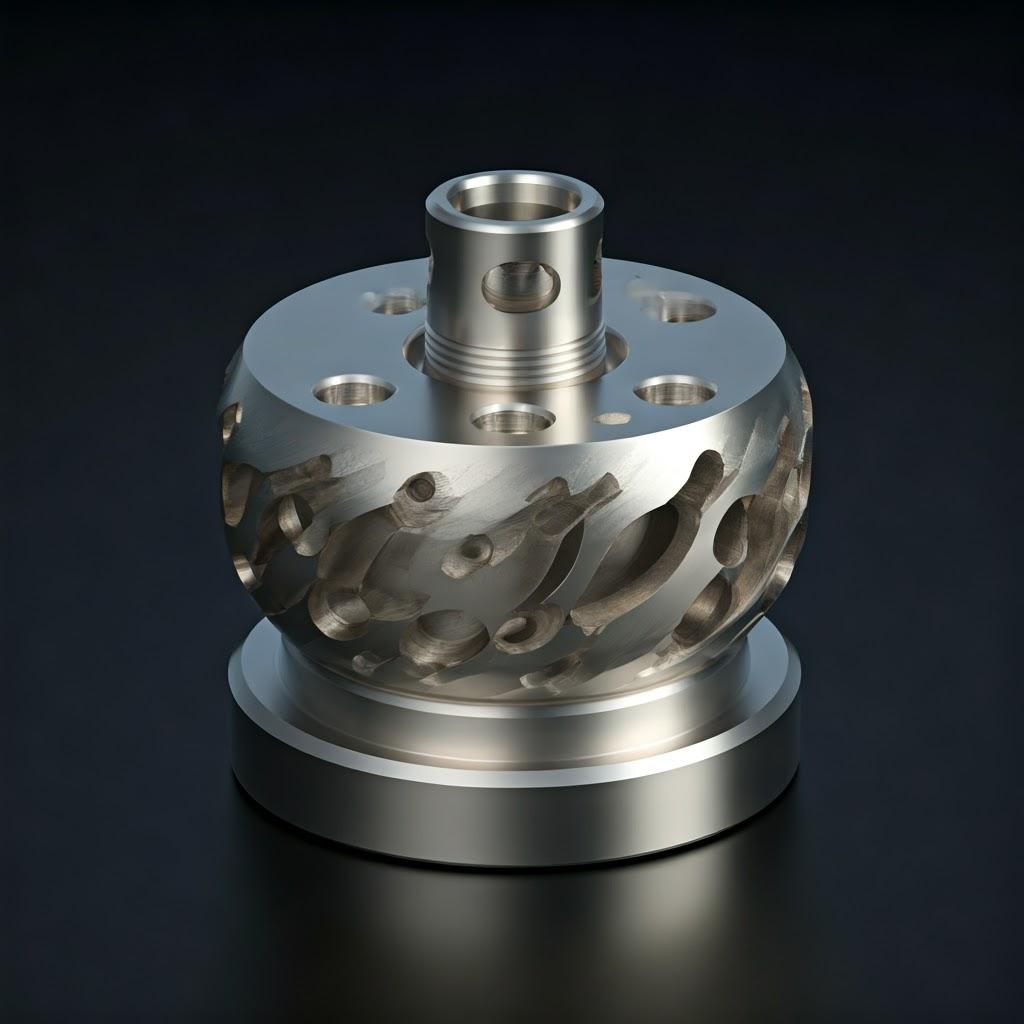
Design Considerations: Optimizing Drone Hub Geometry for Additive Manufacturing Success
Transitioning from traditional manufacturing methods like CNC machining or casting to metal additive manufacturing (AM) requires more than just converting a CAD file. To fully leverage the benefits of metal 3D printing – particularly the lightweighting potential and complex geometry capabilities crucial for drone propeller hubs – engineers must embrace Design for Additive Manufacturing (DfAM). DfAM is a methodology that involves designing parts specifically considering the opportunities and constraints of the layer-by-layer building process used in AM technologies like Selective Laser Melting (SLM) or Electron Beam Melting (EBM). Optimizing a drone hub design for AM ensures better printability, reduced post-processing requirements, lower costs, and ultimately, superior performance.
Here are key DfAM principles essential for designing successful metal 3D printed drone propeller hubs:
- Support Structures Management:
- Necessity: Metal AM processes require support structures for features that overhang the build plate or previous layers at angles typically less than 45 degrees from the horizontal. Supports anchor the part, prevent warping, and provide a pathway for heat dissipation during printing. Drone hubs often feature bolt holes, mounting interfaces, and potentially internal channels that necessitate supports.
- Design Strategy: The goal is to minimize the need for supports or design them for easy removal.
- Orientation: Choose a build orientation that minimizes down-facing surfaces and overhangs. Critical functional surfaces should ideally face upwards or vertically.
- Self-Supporting Angles: Design features with angles greater than 45 degrees wherever possible.
- Chamfers & Fillets: Replace sharp overhangs with chamfers or fillets that meet the self-supporting angle criteria.
- Internal Channels: Design internal channels with diamond or teardrop cross-sections instead of circular ones to make them self-supporting.
- Påverkan: Extensive supports increase print time, material consumption, and post-processing effort (removal and surface finishing). Poorly designed supports can be difficult to remove without damaging the part.
- Wall Thickness and Feature Size:
- Minimums: AM processes have limitations on minimum printable wall thicknesses (often around 0.4-0.8 mm, depending on the machine, material, and feature height). Designing below these limits can lead to incomplete features or print failures.
- Balancing Act: While AM enables thin walls for lightweighting, walls must still possess sufficient structural integrity to withstand operational loads (centrifugal forces, torque). Avoid abrupt changes in thickness, which can cause stress concentrations and thermal issues. Use topology optimization results as a guide but ensure manufacturability.
- Edges: Avoid designing razor-sharp edges, as they can be difficult to print accurately and may pose handling risks or be prone to damage. Incorporate small radii or chamfers.
- Holes and Channels:
- Orientation: Vertically oriented holes generally print with better accuracy and surface finish than horizontal holes.
- Horizontal Holes: Small horizontal holes (typically < 8-10mm diameter) may print without supports but often exhibit poorer roundness and rougher top surfaces. Larger horizontal holes require supports or should be designed with self-supporting shapes (e.g., teardrops, diamonds).
- Tapped Holes: For threaded holes requiring high precision and strength, it’s standard practice to print pilot holes with extra stock material and then drill and tap them during post-processing CNC machining.
- Topology Optimization and Lattice Structures:
- Lättvikt: This is where AM truly shines for drone components. Use Finite Element Analysis (FEA) and topology optimization software to identify low-stress areas where material can be removed. This results in organic, load-path-optimized shapes that are significantly lighter than conventionally designed counterparts but equally strong or stronger.
- Lattices: Incorporate internal lattice structures within thicker sections to reduce mass while maintaining stiffness and providing potential vibration damping benefits. Various lattice types (cubic, gyroid, octet) offer different structural properties.
- Implementation: Ensure the optimized geometry respects manufacturing constraints (minimum wall thickness, self-supporting angles). Smooth transitions and generous fillets are crucial to reduce stress concentrations in complex geometries.
- Part Orientation Strategy:
- Påverkan: The orientation of the hub on the build plate significantly influences support requirements, surface finish (different roughness on up-facing, down-facing, and vertical walls), print time, and potentially mechanical properties (due to anisotropy, though less pronounced in metals compared to polymers).
- Decision Factors: Prioritize critical features (e.g., mounting faces, bores) to be oriented for best accuracy and finish (often vertical or upwards). Balance this against minimizing support volume and print height (which affects time).
- Thermal Management Considerations:
- Utmaning: The rapid heating and cooling inherent in laser-based AM can induce thermal stresses, leading to warping or cracking, especially in parts with large variations in cross-section.
- Design Strategy: Aim for relatively uniform wall thicknesses where possible. Avoid large, solid blocks of material. Incorporate design features that help dissipate heat evenly during the build. Consult with AM service providers like Met3dp, whose engineers can provide valuable feedback on design manufacturability and thermal considerations. Their Om oss page details their expertise in providing comprehensive solutions.
By proactively incorporating these DfAM principles, engineers can design drone propeller hubs that are not only lighter and stronger but also more efficiently and reliably produced using metal additive manufacturing. This collaborative approach between designers and AM specialists is key to unlocking the full potential of the technology. B2B Keyword Focus: DfAM expert services, additive manufacturing design guidelines, metal AM best practices.
Achieving Tight Tolerances, Superior Surface Finish, and Dimensional Accuracy in 3D Printed Hubs
While metal additive manufacturing unlocks incredible design freedom, it’s essential for engineers and procurement managers to have realistic expectations regarding the achievable precision, surface finish, and overall dimensional accuracy directly off the printer. Understanding these aspects, and how they compare to traditional methods like CNC machining, is crucial for specifying requirements and planning necessary post-processing steps for functional components like drone propeller hubs.
Tolerances:
- Typical As-Built Tolerances: For industrial Laser Powder Bed Fusion (LPBF) systems, typical achievable dimensional tolerances generally fall within the range of ±0.1 mm to ±0.2 mm for smaller features (up to ~50-100mm), or ±0.1% to ±0.2% of the nominal dimension for larger parts. Electron Beam Melting (EBM), another powder bed fusion process offered by providers like Met3dp, might have slightly looser as-built tolerances due to higher processing temperatures but can excel with certain materials like titanium alloys.
- Influencing Factors: Achieving tight tolerances depends on several factors:
- Machine Calibration: Precision and regular calibration of the AM system are fundamental.
- Materialegenskaper: Different alloys exhibit varying shrinkage and thermal behavior.
- Part Geometry & Size: Complex shapes, large parts, and significant variations in thickness can lead to greater deviation due to thermal stresses and shrinkage.
- Support Strategy: Supports influence thermal behavior and can cause minor distortion upon removal.
- Thermal Effects: Residual stress accumulation and warping during the build.
- Critical Tolerances: For features requiring tolerances tighter than ±0.1 mm (e.g., motor shaft bores, precise bolt hole locations, propeller mounting surfaces), post-process CNC machining is almost always necessary. DfAM principles dictate designing parts with sufficient extra material (machining allowance or stock) on these critical surfaces.
Surface Finish (Roughness):
- As-Built Roughness: Metal AM parts inherently have a textured surface due to the layer-by-layer fusion of powder particles. The typical as-built surface roughness (Ra – arithmetic average roughness) for LPBF ranges from 6 µm to 15 µm, sometimes higher.
- Orientation Dependence: Surface finish is highly dependent on the surface’s orientation relative to the build direction:
- Up-facing Surfaces: Generally offer the smoothest finish as they are fully defined by the laser path on the top layer.
- Vertical Walls: Show distinct layer lines, leading to moderate roughness.
- Down-facing (Overhanging/Supported) Surfaces: Typically exhibit the highest roughness due to contact with support structures or the nature of forming overhangs. Removal of supports can also leave witness marks or scars.
- Påverkan: Surface roughness affects aesthetics, fatigue life (rougher surfaces can be crack initiation sites), friction, and the fit of mating components.
- Improvement: Significant improvements in surface finish are achieved through post-processing steps like bead blasting, tumbling, electropolishing, or machining (which can achieve Ra < 1 µm).
Dimensionell noggrannhet:
- Definition: Refers to how closely the overall geometry and dimensions of the final printed part conform to the original CAD model.
- Utmaningar: Achieving high accuracy requires compensating for material shrinkage, managing thermal stresses to prevent warping, employing effective support strategies, and accounting for any dimensional changes during post-processing (especially heat treatment).
- Verification: Accurate metrology is crucial. This involves using tools like Coordinate Measuring Machines (CMMs), calibrated calipers, micrometers, and 3D laser scanners to verify critical dimensions against specifications. Reputable service providers integrate rigorous quality control and inspection throughout the process.
Achieving Precision – Summary Table:
Parameter | Typical As-Built Range (LPBF) | Key Influencing Factors | Method for Higher Precision |
---|---|---|---|
Tolerans | ±0.1 to ±0.2 mm / ±0.1-0.2% | Machine, Material, Geometry, Size, Thermal, Supports | Post-Process CNC Machining |
Surface Finish (Ra) | 6 – 15 µm | Orientation, Parameters, Supports, Powder | Blasting, Tumbling, Polishing, Machining |
Dimensionell noggrannhet | High, but subject to above | Shrinkage, Warping, Supports, Post-Processing | Process Control, Simulation, Metrology |
Export to Sheets
Partnering with a knowledgeable metal AM provider like Met3dp, which emphasizes process control, utilizes high-quality equipment and materials, and offers integrated post-processing and quality assurance, is essential for reliably achieving the required tolerances and finishes for demanding drone propeller hub applications. B2B Keyword Focus: High-accuracy metal 3D printing, tight tolerance additive manufacturing, metal AM surface quality, UAV component inspection services.
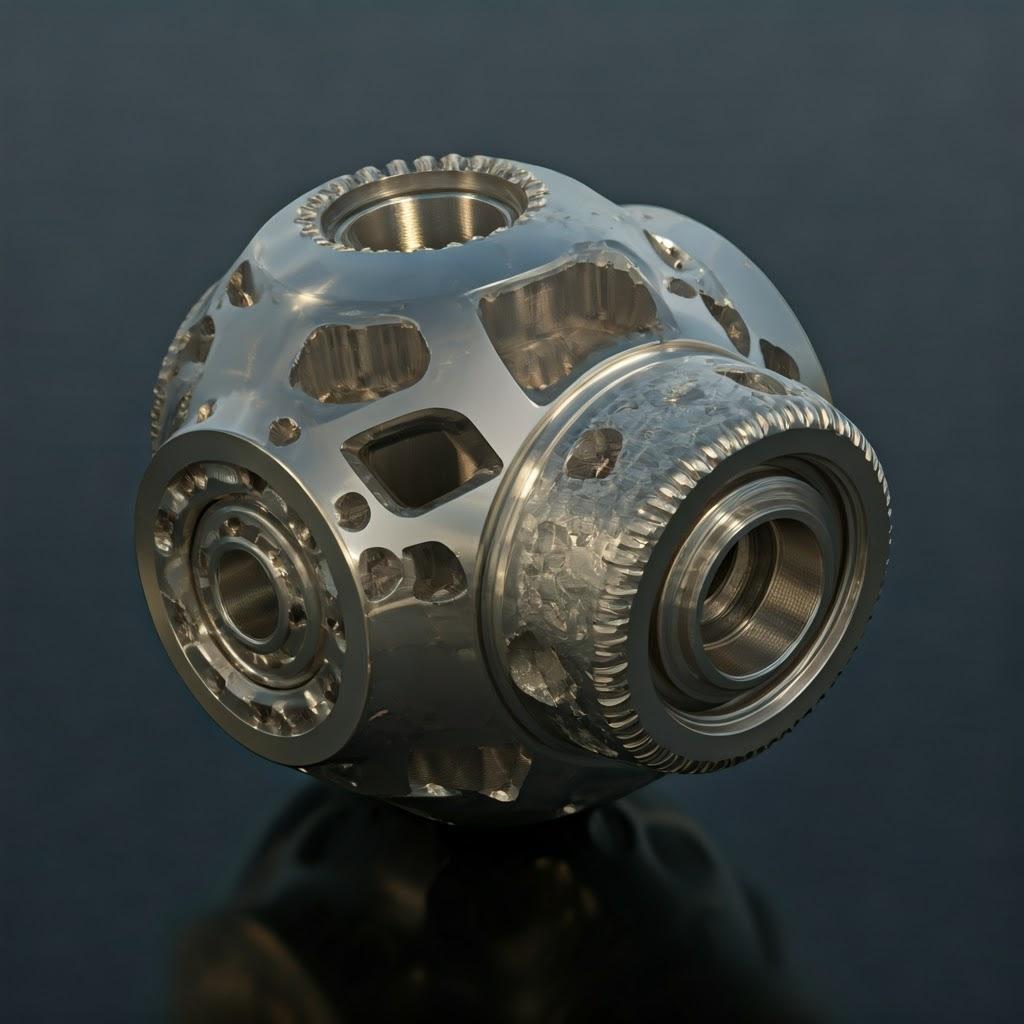
Essential Post-Processing Requirements for Mission-Critical Metal Drone Propeller Hubs
A common misconception about metal additive manufacturing is that parts come off the printer ready for immediate use. In reality, particularly for demanding applications like drone propeller hubs, post-processing is not just recommended – it’s an essential sequence of steps required to transform the as-built part into a functional, reliable component meeting stringent engineering specifications. Neglecting or improperly executing post-processing can compromise mechanical properties, dimensional accuracy, and overall part integrity.
Here are the critical post-processing steps typically required for metal 3D printed drone hubs made from alloys like AlSi10Mg or Scalmalloy®:
- Stress Relief / Heat Treatment:
- Why it’s Critical: The layer-by-layer fusion process involves intense, localized heating followed by rapid cooling. This creates significant internal stresses within the as-built part. These stresses can lead to distortion (especially after removal from the build plate) and can negatively impact the material’s mechanical properties, particularly fatigue life.
- Process: Immediately after printing, often while still attached to the build plate, the hub undergoes a specific heat treatment cycle in a controlled atmosphere furnace. This cycle elevates the temperature sufficiently to allow the material’s microstructure to relax, relieving internal stresses without altering the fundamental shape.
- Solution Heat Treatment & Aging (for Precipitation Hardening Alloys): For alloys like AlSi10Mg and Scalmalloy®, further heat treatment cycles (solutionizing followed by artificial aging) are often required efter stress relief and removal from the build plate. These carefully controlled thermal cycles are necessary to develop the alloy’s final microstructure and achieve the desired high-strength mechanical properties (tensile strength, yield strength, hardness) specified in datasheets. The exact temperature and duration depend heavily on the alloy and target properties.
- Removal from Build Plate & Support Structure Removal:
- Process: Once stress relief is complete, the part is typically cut from the build plate using wire EDM (Electrical Discharge Machining) or a bandsaw. Support structures, which are metallurgically bonded to the part, must then be carefully removed.
- Metoder: This is often done manually using hand tools (pliers, grinders) or sometimes via CNC machining or EDM, depending on the support location and accessibility.
- Överväganden: Support removal can be labor-intensive and requires skill to avoid damaging the part surface. Areas where supports were attached will typically have a rougher surface finish and may require further refinement. DfAM plays a crucial role in designing supports for easier removal.
- Surface Finishing & Refinement:
- Objective: To improve the as-built surface finish for aesthetic reasons, enhanced fatigue performance, or to prepare surfaces for subsequent operations like coating or precise mating.
- Common Methods:
- Abrasive Blasting (Bead/Sand Blasting): Propels abrasive media against the part surface to remove loose powder, create a uniform matte finish, and slightly improve fatigue properties by imparting compressive stress.
- Tumbling/Vibratory Finishing: Parts are placed in a tub with media (ceramic, plastic) that vibrates or tumbles, causing the media to rub against the parts, smoothing surfaces and radiusing edges. Effective for batch processing.
- Manual Grinding/Polishing: For specific areas requiring a smoother finish or removal of support witness marks.
- Precision Machining (CNC):
- Necessity: As discussed previously, achieving tolerances tighter than ~±0.1 mm or very smooth surface finishes (Ra < 3-5 µm) on critical features requires CNC machining.
- Target Features: For drone hubs, this typically includes:
- The central bore for the motor shaft (diameter, concentricity, keyway if present).
- Mounting faces for propeller blades (flatness, parallelism).
- Bolt/screw holes (precise location, diameter, threading).
- Process: The 3D printed hub (after heat treatment and basic finishing) is fixtured in a CNC mill or lathe, and material is precisely removed from designated surfaces using cutting tools. Designing the AM part with adequate machining stock is essential.
- Inspection and Quality Assurance (QA):
- Throughout the Process: QA isn’t just a final step. It includes powder quality verification, process monitoring during the build, and inspections after each major post-processing stage.
- Final Inspection: Comprehensive checks are performed to ensure the finished hub meets all specifications. This includes:
- Dimensional Metrology: Using CMMs, scanners, or gauges to verify all critical dimensions and tolerances.
- Surface Finish Measurement: Using profilometers.
- Material Property Verification: Potentially testing sample coupons printed alongside the parts (tensile testing, hardness testing).
- Icke-förstörande testning (NDT): For highly critical applications (e.g., aerospace), CT scanning (Computed Tomography) might be used to inspect for internal defects like porosity or lack of fusion, ensuring structural integrity.
Choosing a metal AM service provider like Met3dp, which offers or manages a comprehensive suite of post-processing capabilities and integrates rigorous quality control, simplifies the procurement process and ensures that the final drone propeller hubs meet the demanding requirements of their application. B2B Keyword Focus: Full-service metal additive manufacturing, metal AM heat treatment services, precision CNC machining for 3D prints, NDT services additive manufacturing.
Common Challenges in 3D Printing Drone Hubs and Proven Mitigation Strategies
While metal additive manufacturing offers tremendous advantages for producing drone propeller hubs, the process is complex and not without potential challenges. Awareness of these common issues, coupled with proven mitigation strategies employed by experienced service providers, is key to achieving successful outcomes consistently. Procurement managers and engineers should understand these potential hurdles when sourcing AM components.
Here are some common challenges encountered when 3D printing metal drone hubs and how they are typically addressed:
1. Warping and Distortion:
- Utmaning: The significant temperature gradients during printing can cause internal stresses to build up, potentially leading to the part warping or distorting during the build or after removal from the build plate. This compromises dimensional accuracy.
- Mitigation Strategies:
- Optimized Part Orientation: Orienting the part to minimize large, flat surfaces parallel to the build plate and manage thermal gradients.
- Robust Support Strategy: Designing and applying appropriate support structures not only for overhangs but also to anchor the part securely and manage heat dissipation.
- Thermal Simulation: Using simulation software during the design phase to predict areas of high stress and adjust the design or support strategy accordingly.
- Processparameteroptimering: Fine-tuning laser power, scan speed, and layer thickness to minimize residual stress.
- Immediate Stress Relief: Performing a stress relief heat treatment cycle immediately after the build, often before removing the part from the build plate.
2. Support Removal Difficulty and Surface Imperfections:
- Utmaning: Supports, while necessary, can be difficult and time-consuming to remove, especially from intricate internal channels or delicate features. Removal can leave witness marks or scars on the part surface, affecting aesthetics or function.
- Mitigation Strategies:
- DfAM for Support Reduction: Designing parts with self-supporting angles (>45°) and features that minimize the need for supports.
- Optimized Support Types: Using support structures (e.g., thin webs, conical points, block supports) designed for easier breakaway or machining, rather than dense, solid supports where possible.
- Strategic Orientation: Orienting the part so supports are primarily on non-critical surfaces.
- Planning for Finishing: Allocating extra material (machining stock) on surfaces where support contact is unavoidable and a smooth finish is required post-removal.
- Skilled Technicians: Utilizing experienced technicians for manual support removal.
3. Internal Porosity:
- Utmaning: Small voids or pores can form within the printed metal if fusion is incomplete or gas gets trapped during melting. Porosity can significantly degrade mechanical properties, particularly fatigue strength, which is critical for rotating components like propeller hubs.
- Mitigation Strategies:
- High-Quality Metal Powder: Using powders with controlled particle size distribution, high sphericity, good flowability, and low trapped gas content. Met3dp’s advanced powder production systems using Gas Atomization and PREP technology are designed to ensure such metallpulver av hög kvalitet.
- Optimized Print Parameters: Developing and rigorously validating print parameters (laser power, speed, hatch spacing, layer thickness) specific to the material and machine to ensure full melting and fusion.
- Controlled Build Atmosphere: Maintaining a high-purity inert gas atmosphere (Argon or Nitrogen) in the build chamber to minimize oxidation and gas pickup.
- Het isostatisk pressning (HIP): For extremely critical applications requiring maximum density (>99.9%), HIP can be used as a post-processing step. It involves applying high pressure and temperature simultaneously to close internal pores (note: this adds significant cost and lead time).
4. Achieving Tight Tolerances and Desired Surface Finish:
- Utmaning: As discussed earlier, the inherent nature of the layer-wise process limits the achievable as-built tolerances and surface finish compared to precision machining.
- Mitigation Strategies:
- Hybrid Approach (AM + Machining): Embracing a workflow where AM is used for the complex overall shape and lightweighting, followed by precision CNC machining for critical features requiring tight tolerances and smooth finishes.
- Designing for Post-Processing: Explicitly including machining allowances in the CAD model for surfaces that will be machined.
- Process Control & Calibration: Ensuring the AM machine is accurately calibrated and monitored.
- Appropriate Finishing Techniques: Selecting the right combination of blasting, tumbling, or polishing methods to achieve the desired non-critical surface finish.
5. Material Property Consistency:
- Utmaning: Ensuring that the mechanical properties (strength, ductility, hardness) of the printed part consistently meet specifications across the entire component and from build to build.
- Mitigation Strategies:
- Powder Quality Management: Strict control over powder sourcing, handling, storage, and recycling to prevent contamination and degradation.
- Validated Processes: Using standardized, validated print parameters and heat treatment cycles specific to the alloy.
- Process Monitoring: Utilizing in-situ monitoring tools (melt pool monitoring, thermal imaging) if available, to detect potential anomalies during the build.
- Batch Testing: Including witness coupons with each build for destructive testing (tensile, hardness) to verify material properties.
Successfully navigating these challenges requires a deep understanding of materials science, AM process physics, DfAM principles, and rigorous process control. Partnering with an established metal AM service provider like Met3dp, which possesses the necessary expertise, advanced equipment (including potentially various tryckmetoder), and quality systems, is the most effective way to mitigate these risks and reliably produce high-quality, mission-critical drone propeller hubs. B2B Keyword Focus: Metal AM quality assurance, mitigating additive manufacturing defects, reliable metal 3D printing partners, aerospace additive manufacturing challenges.
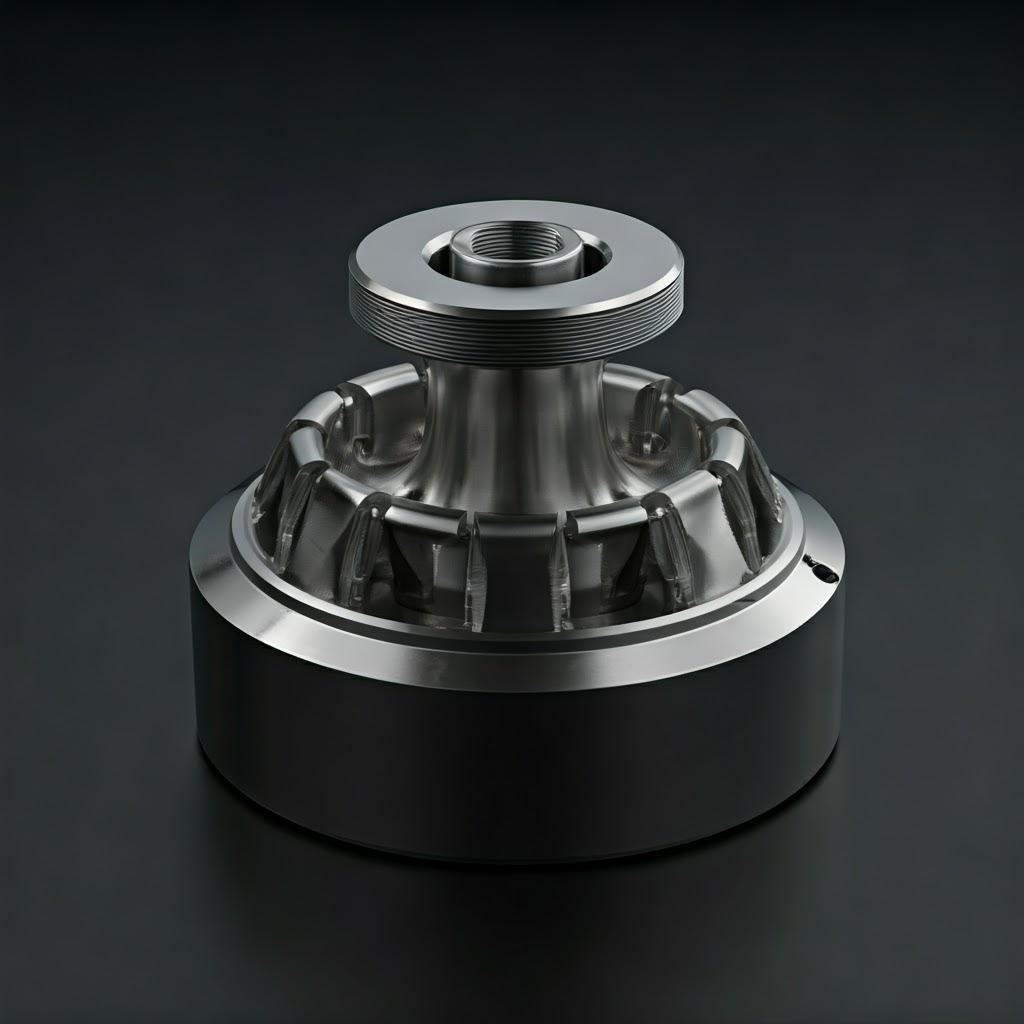
How to Choose the Right Metal 3D Printing Service Provider for Drone Components Manufacturing
Selecting the right manufacturing partner is arguably one of the most critical decisions when sourcing metal 3D printed components, especially for mission-critical parts like drone propeller hubs. The quality, reliability, and performance of the final product are directly linked to the capabilities and expertise of your chosen service provider. While cost is always a factor, focusing solely on the lowest price can lead to compromised quality, missed deadlines, and potentially catastrophic component failures in the field. For engineers and procurement managers in the drone industry, a thorough evaluation based on key criteria is essential.
Here’s what to look for when selecting a metal additive manufacturing service provider for your drone components:
- Demonstrated Technical Expertise and Relevant Experience:
- Material: Does the provider have proven experience printing with the specific alloys you require (e.g., AlSi10Mg, Scalmalloy®)? Ask for evidence like material datasheets derived from their process, case studies, or sample parts.
- Process: Are they proficient in the required AM process (typically Laser Powder Bed Fusion – LPBF/SLM for these alloys)? Do they understand the nuances of parameter optimization for density and mechanical properties?
- Application Focus: Have they worked on similar components or within demanding industries like aerospace, automotive, or medical where precision and reliability are paramount? Met3dp, for instance, highlights its “decades of collective expertise in metal additive manufacturing” and focus on “mission-critical parts.”
- Advanced Equipment and Technology:
- Industrial-Grade Printers: Ensure the provider uses well-maintained, industrial-grade metal AM systems known for accuracy and repeatability. Inquire about their machine park and its capabilities (build volume, laser power, monitoring systems).
- Technology Fit: Understand if their primary technology (e.g., LPBF, EBM) is the best fit for your material and application requirements.
- Material Quality Control and Portfolio:
- Powder Sourcing & Handling: How do they ensure the quality of the metal powders used? Do they have in-house powder production with advanced techniques like Met3dp’s Gas Atomization and PREP, or do they source from reputable suppliers with rigorous batch testing and certification? Proper powder handling, storage, and traceability are crucial.
- Materialområde: Does their portfolio include the specific alloys you need, and potentially others that might be relevant for future projects?
- Comprehensive Post-Processing Capabilities:
- Integrated Workflow: Can the provider manage the entire necessary workflow in-house or through trusted partners? This includes stress relief, heat treatment (critical for Al/Sc alloys), support removal, CNC machining for critical tolerances, surface finishing, and inspection. A seamless process reduces logistical complexity and ensures accountability.
- Robust Quality Management System (QMS):
- Certifieringar: Look for relevant certifications like ISO 9001 (general quality management) or AS9100 (specific to aerospace, often required for high-end drone components). Certifications indicate adherence to standardized processes and commitment to quality.
- Traceability & Documentation: Ensure they have systems for full traceability from powder batch to final part, along with documented process controls and inspection reports.
- Design for Additive Manufacturing (DfAM) Support:
- Collaborative Approach: Does the provider offer DfAM consultation? A good partner will review your design, provide feedback on manufacturability, suggest optimizations for lightweighting or performance, and help you leverage the full potential of AM. Met3dp explicitly mentions providing “application development services.”
- Capacity, Lead Times, and Communication:
- Skalbarhet: Can they handle your prototype volumes as well as potential future production runs?
- Transparency: Do they provide realistic and transparent lead time estimates? How do they communicate progress and potential delays?
- Responsiveness: Evaluate their customer service responsiveness during the quoting and evaluation process.
- Logistics and Location:
- Frakt: Consider the logistics involved in shipping parts from the provider’s location (e.g., Met3dp in Qingdao, China) to yours, including costs, time, and any import/export considerations.
By carefully evaluating potential suppliers against these criteria, you can identify a true manufacturing partner – one that possesses the technical capabilities, quality focus, and collaborative spirit necessary to reliably deliver high-performance metal 3D printed drone propeller hubs. A provider like Met3dp, emphasizing its comprehensive solutions from advanced powders to finished parts, represents the type of integrated capability valuable for demanding applications. B2B Keyword Focus: Selecting metal AM bureau, aerospace additive manufacturing certification AS9100, high-quality metal 3D printing services, drone component manufacturing partner.
Understanding Cost Factors and Lead Times for Procuring 3D Printed Drone Propeller Hubs
Budget and delivery timelines are critical considerations for any procurement decision. While metal additive manufacturing offers unique benefits, its cost structure and lead time components differ from traditional methods. Understanding these factors helps set realistic expectations and allows for accurate project planning when sourcing 3D printed drone propeller hubs.
Key Cost Drivers:
The final price of a 3D printed metal hub is influenced by a combination of factors:
- Material Type and Volume: This is often the most significant cost driver. High-performance alloys like Scalmalloy® command a premium price compared to more standard alloys like AlSi10Mg due to raw material costs (especially Scandium) and specialized production. The total volume of powder consumed (part volume + support volume + potential sintered base) directly impacts cost.
- Machine Time (Print Time): Calculated based on the time the expensive AM machine is occupied. This depends on:
- Part Height: More layers mean longer print times.
- Part Volume & Density: Larger, denser parts take longer to fuse.
- Komplexitet: Intricate details require more laser scanning time per layer.
- Nesting: How many parts can be efficiently nested onto a single build plate affects the per-part machine time allocation.
- Kostnader för arbetskraft: Significant labor is involved beyond just pressing ‘print’:
- Pre-processing: CAD file preparation, build layout optimization, support structure generation.
- Efterbearbetning: Build removal, stress relief setup, manual support removal, basic finishing, inspection, packaging.
- Post-Processing Complexity: Each additional step adds cost:
- Värmebehandling: Furnace time, energy consumption, required atmosphere.
- CNC Machining: Machine time, tooling, programming, skilled machinist labor (often the most expensive post-processing step).
- Advanced Finishing: Polishing, coating, specialized surface treatments.
- NDT & Advanced QA: Costs associated with CT scanning, extensive CMM inspection, or specialized testing add up quickly.
- Order Volume: While AM is suitable for low volumes, some economies of scale exist. Setup costs (file prep, build planning) are amortized over more parts in larger batches, potentially reducing the per-part price slightly.
- Provider Overheads & Margin: Standard business costs associated with running an advanced manufacturing facility.
Lead Time Components:
The total time from order placement to receiving finished parts involves multiple stages:
- Order Processing & File Preparation (1-3 days): Initial review, quoting (if not already done), final CAD checks, build file preparation, scheduling.
- Machine Queue Time (Variable: days to weeks): Waiting for an appropriate machine to become available. This is highly dependent on the service provider’s current workload and capacity.
- Printing Time (Hours to Days): The actual time the part spends being built layer-by-layer. A single hub might take several hours; a full build plate could take 1-3 days or more.
- Post-Processing (Variable: days to weeks):
- Cooling & Stress Relief: Typically 1-2 days (including furnace time and controlled cooling).
- Part/Support Removal: Hours to a day.
- Finishing (Blasting/Tumbling): Hours to a day.
- Maskinbearbetning: Highly variable, from hours for simple features to several days for complex multi-axis machining.
- Additional Treatments/Inspection: Adds further time depending on complexity.
- Shipping (Variable: days to weeks): Depends on the distance between the provider and customer, and the shipping method chosen (standard vs. expedited).
Summary Table: Cost & Lead Time Factors
Factor Category | Key Drivers / Components | Påverkan på kostnader | Impact on Lead Time |
---|---|---|---|
Material | Alloy Type (AlSi10Mg vs. Scalmalloy®), Volume Consumed | Major | Minor |
Machine Time | Part Height, Volume, Complexity, Nesting | Significant | Major |
Arbete | File Prep, Build Setup, Support Removal, Basic Finishing | Måttlig | Måttlig |
Efterbearbetning | Heat Treatment, Machining, Finishing, NDT, Advanced QA | Major (if complex) | Major (if complex) |
Volume & Scheduling | Order Quantity, Machine Availability (Queue Time) | Måttlig | Major (Queue) |
Logistics | Shipping Distance & Method | Minor-Moderate | Moderate-Major |
Export to Sheets
Overall Expectation: For a moderately complex metal 3D printed drone propeller hub requiring heat treatment and some precision machining, procurement managers should typically anticipate lead times ranging from 1 to 4 weeks, acknowledging that complex requirements or high quantities can extend this timeframe. Obtaining detailed quotes from potential suppliers based on final designs is essential for accurate cost and lead time planning. B2B Keyword Focus: additive manufacturing cost breakdown, 3D printing lead time estimation, metal AM project scheduling, UAV parts procurement timeline.
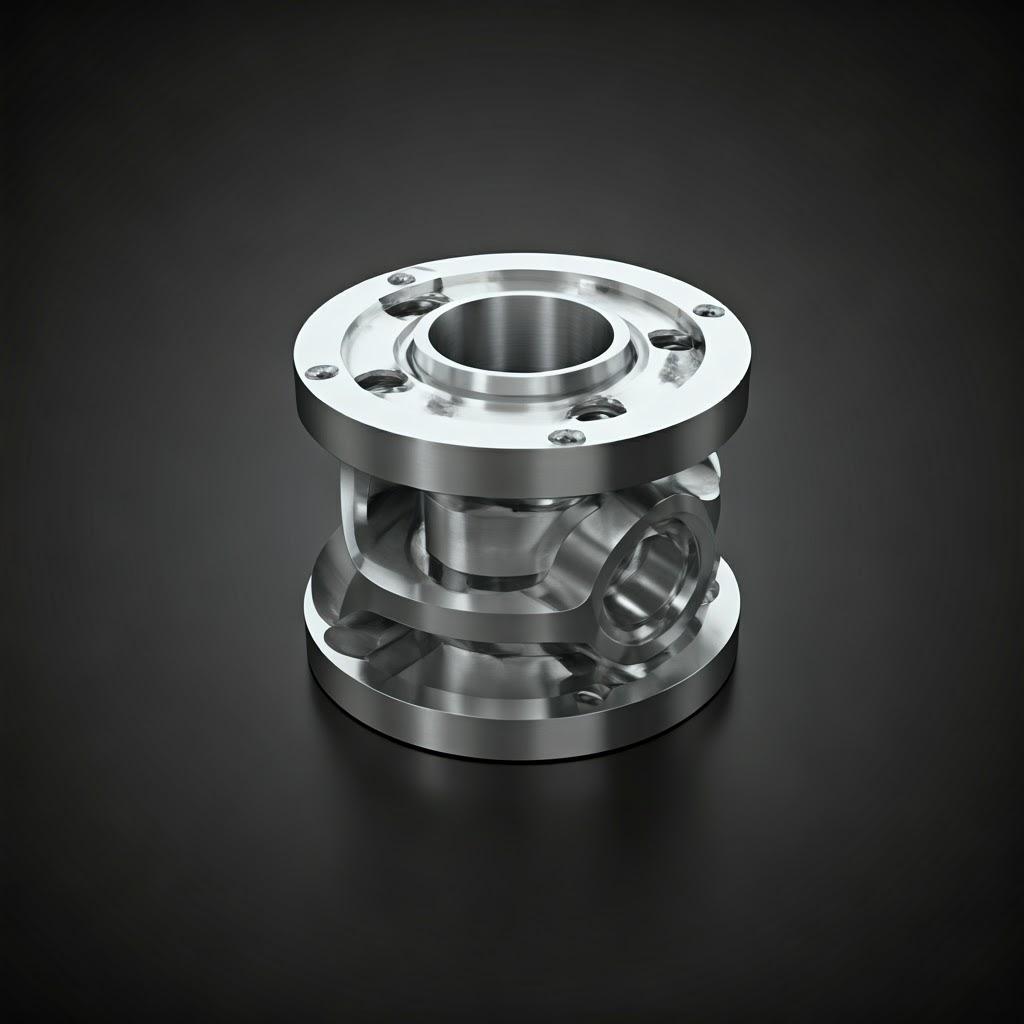
Frequently Asked Questions (FAQ) about Metal 3D Printed Drone Hubs
Here are answers to some common questions engineers and procurement managers have when considering metal additive manufacturing for drone propeller hubs:
1. Is metal 3D printing strong enough for critical drone parts like propeller hubs?
Svar: Yes, absolutely. Modern metal AM processes like Laser Powder Bed Fusion (LPBF/SLM) create parts with very high density (often >99.5%), resulting in mechanical properties that are typically comparable or, in some cases, even superior to traditional casting or billet materials, especially when using advanced AM-specific alloys like Scalmalloy®. Crucial properties like tensile strength, yield strength, and fatigue life meet or exceed the demanding requirements for drone components provided that validated printing parameters and appropriate post-process heat treatments are correctly applied. Partnering with an experienced provider who understands process control and material science is key to ensuring optimal strength and reliability.
2. How does the cost of a 3D printed metal hub compare to a CNC machined one?
Svar: The cost comparison depends heavily on several factors:
- Delkomplexitet: For highly intricate geometries, topology-optimized shapes, or parts with internal features, AM can be more cost-effective as it eliminates complex multi-axis machining setups and reduces material waste.
- Material: High-performance AM alloys can be more expensive than standard aluminum billets used for CNC.
- Volym: For very high production volumes (thousands of identical simple parts), CNC machining from billet is often more economical due to faster cycle times per part once set up. For low-to-medium volumes (prototypes, custom parts, tens to hundreds), or parts designed specifically for AM’s strengths (lightweighting, consolidation), AM often becomes competitive or even advantageous.
- Design (DfAM vs. DfM): A part designed optimally for AM might be significantly cheaper to print than trying to machine the same complex shape, and vice-versa. A detailed Request for Quote (RFQ) with specific design files sent to both AM and CNC providers is the best way to get an accurate comparison for your specific hub design.
3. What information do I need to provide to get an accurate quote for a 3D printed drone hub?
Svar: To receive a timely and accurate quote from a metal AM service provider like Met3dp, you should provide the following information:
- 3D CAD File: A high-quality 3D model, typically in STEP (.stp/.step) format (preferred for dimensional accuracy) or STL (.stl) format (common for AM).
- Material Specification: Clearly state the desired metal alloy (e.g., AlSi10Mg, Scalmalloy®).
- Technical Drawing (Optional but Recommended): A 2D drawing identifying critical dimensions, specific tolerances (GD&T), required surface finishes for key features, and any tapped hole specifications.
- Kvantitet: The number of hubs required (for prototypes or batch production).
- Krav på efterbearbetning: Specify the desired heat treatment condition (e.g., T6), surface finish requirements (e.g., bead blast, as-machined on specific faces), and any mandatory testing or inspection needs (e.g., CMM report, material certification).
- Desired Lead Time: Indicate your required delivery timeline, if applicable.
4. Can existing propeller hub designs originally made for CNC machining be directly 3D printed?
Svar: While technically possible to print a design originally intended for machining, it is generally not recommended for optimal results. Designs created for subtractive manufacturing (CNC) often don’t leverage the unique advantages of additive manufacturing (like complex internal structures, topology optimization for lightweighting) and may even be inefficient or difficult to print (e.g., having features that require excessive support structures). To maximize the benefits of AM – achieving lighter weight, potentially better performance, and efficient printing – it’s highly advisable to review and potentially redesign the hub using Design för additiv tillverkning (DfAM) principles before sending it for printing. Collaboration with the AM service provider’s application engineers can be very beneficial here.
Conclusion: Elevating Drone Capabilities with Advanced Metal Additive Manufacturing Solutions
The drone industry’s relentless pursuit of higher performance, greater endurance, increased payload capacity, and unwavering reliability demands innovation in every component. The propeller hub, a critical linchpin in the propulsion system, is no exception. As we’ve explored, metal additive manufacturing has emerged as a transformative technology, offering powerful solutions to meet these escalating demands.
By leveraging metal AM processes like Laser Powder Bed Fusion, drone manufacturers and suppliers can produce propeller hubs with:
- Optimized Performance: Through topology optimization and the use of advanced, lightweight, high-strength aluminum alloys like AlSi10Mg and the exceptional Scalmalloy®, hubs can be made significantly lighter without compromising structural integrity, directly enhancing flight time and payload capacity.
- Enhanced Design Freedom: AM enables the creation of complex geometries and consolidated parts that are impossible or impractical to produce using traditional methods, opening doors for improved aerodynamic efficiency or integrated functionality.
- Improved Reliability: High-density parts with excellent material properties, particularly fatigue resistance when using alloys like Scalmalloy® and proper post-processing, contribute to safer and more durable drone operations.
- Supply Chain Agility: On-demand production capabilities, rapid prototyping, and digital inventory models offered by AM streamline development cycles and procurement processes.
However, realizing these benefits requires a holistic approach. Success hinges on applying Design for Additive Manufacturing (DfAM) principles, selecting the appropriate high-quality material, understanding and implementing essential post-processing steps like heat treatment and precision machining, and critically, choosing the right manufacturing partner.
An ideal partner, like Met3dp, brings together deep expertise in additive manufacturing, state-of-the-art printing equipment, advanced metal powder production capabilities, comprehensive post-processing services, and a robust quality management system. By collaborating with such a provider, drone companies can confidently integrate metal AM components into their designs, pushing the boundaries of UAV performance and unlocking new possibilities in aerial applications.
Ready to explore how metal additive manufacturing can elevate your next drone project? Contact the experts at Met3dp today to discuss your component requirements, leverage our application development services, and receive a quote for high-precision, reliable 3D printed drone propeller hubs.
Dela på
MET3DP Technology Co, LTD är en ledande leverantör av lösningar för additiv tillverkning med huvudkontor i Qingdao, Kina. Vårt företag är specialiserat på 3D-utskriftsutrustning och högpresterande metallpulver för industriella tillämpningar.
Förfrågan för att få bästa pris och anpassad lösning för ditt företag!
Relaterade artiklar
Om Met3DP
Senaste uppdateringen
Vår produkt
KONTAKTA OSS
Har du några frågor? Skicka oss meddelande nu! Vi kommer att betjäna din begäran med ett helt team efter att ha fått ditt meddelande.
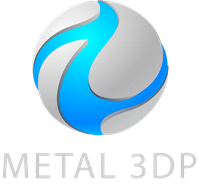
Metallpulver för 3D-printing och additiv tillverkning