Custom Aerospace Fasteners via Metal Additive Manufacturing
Innehållsförteckning
Introduction: The Critical Role of Fasteners and the Rise of Additive Manufacturing in Aerospace
In the intricate world of aerospace engineering, components large and small play mission-critical roles. Among the most ubiquitous, yet fundamentally vital, are fasteners. From the smallest screws holding interior panels to the robust bolts securing engine pylons and wing spars, fasteners are the linchpin ensuring structural integrity, operational safety, and overall performance of aircraft, spacecraft, and defense systems. An average commercial airliner relies on hundreds of thousands, sometimes millions, of fasteners, each meticulously designed, manufactured, and installed to withstand extreme conditions – vibration, fatigue, temperature fluctuations, and significant mechanical loads. The failure of even a single critical fastener can have catastrophic consequences, making their reliability non-negotiable.
Traditionally, the manufacturing of these essential components has relied on established subtractive methods like CNC machining from bar stock, forging, or casting, followed by secondary operations like thread rolling and heat treatment. While these methods have served the industry well for decades, delivering high-quality and reliable parts, they are not without limitations, particularly in the context of modern aerospace demands for greater efficiency, customization, and supply chain agility.
Challenges in Traditional Fastener Manufacturing:
- Ledtider: Producing specialized or custom fasteners, especially in low volumes, often involves significant lead times due to tooling requirements (for forging), machine setup, and complex supply chains. This can hinder rapid prototyping efforts and delay maintenance or upgrade schedules.
- Customization Costs: Tooling and setup costs associated with traditional methods make producing small batches of unique or customized fasteners prohibitively expensive. This limits design innovation and makes replacing obsolete fasteners on legacy aircraft a significant challenge.
- Materialavfall: Subtractive processes, primarily machining, inherently generate substantial material waste. Raw material is cut away to achieve the final shape, leading to poor buy-to-fly ratios, especially when working with expensive aerospace-grade alloys like titanium.
- Design Constraints: Certain complex geometries or internal features that could potentially enhance fastener performance or functionality are difficult or impossible to achieve using traditional manufacturing techniques.
Skriva in Additiv tillverkning av metall (AM), often referred to as metal 3D-utskrifter. This transformative technology is rapidly moving beyond prototyping and tooling into the production of flight-critical components, including fasteners. Instead of removing material, AM builds parts layer by layer directly from a digital model using high-performance metal powders. This fundamental difference unlocks a new paradigm for aerospace fastener design, production, and procurement.
Metal AM offers the potential to directly address the limitations of conventional methods. It allows for:
- Oöverträffad designfrihet: Engineers can create fasteners with optimized geometries, reduced weight, and potentially integrated functionalities previously unattainable.
- Snabb iteration: Prototypes can be produced in days, not weeks or months, accelerating design validation and testing cycles.
- Economical Customization: AM is inherently suited for low-volume, high-mix production, making custom and bespoke fasteners economically viable without the need for dedicated tooling.
- Förbättrat materialutnyttjande: Building parts layer by layer significantly reduces material waste compared to subtractive techniques.
As aerospace manufacturers, MRO providers, and suppliers seek competitive advantages through innovation, efficiency, and resilient supply chains, metal additive manufacturing presents a compelling value proposition. Companies like Met3dp, specializing in advanced 3D-utskrift av metall technologies and high-performance metal powders, are at the forefront of this shift, providing the expertise and capabilities needed to leverage AM for demanding applications like aerospace fasteners. This article will delve into the specifics of using metal AM for aerospace fastener production, exploring applications, benefits, material considerations, design principles, and supplier selection criteria.
Applications: Where are Metal 3D Printed Fasteners Making an Impact in Aerospace?
The adoption of metal additive manufacturing for aerospace fasteners is not merely theoretical; it’s a rapidly growing reality across various segments of the industry. Driven by the need for weight reduction, performance enhancement, supply chain optimization, and solutions for obsolescence, engineers and procurement managers are increasingly specifying AM for specific fastener applications where its benefits offer a distinct advantage. The demand spans original equipment manufacturers (OEMs), Tier 1 and Tier 2 suppliers, Maintenance, Repair, and Overhaul (MRO) facilities, and space exploration entities.
Here’s a closer look at key application areas:
1. Airframe and Structural Components:
- Custom Brackets with Integrated Fastening Points: AM allows the consolidation of multiple components into a single, complex part. Imagine a structural bracket designed via topology optimization that includes integrated, non-standard threaded bosses or attachment points, reducing part count, weight, and assembly time.
- Specialized Joint Fasteners: Unique airframe geometries or load paths may necessitate fasteners with non-standard head shapes, shank lengths, or thread forms that are costly or time-consuming to machine traditionally. AM makes the production of these bespoke fasteners feasible.
- Repair and Modification: For aging aircraft, sourcing original fasteners can be challenging due to obsolescence. AM enables the on-demand production of replacement fasteners based on digital scans or legacy drawings, providing a critical solution for MRO providers and extending aircraft service life. Lightweight AM fasteners can also be used in modification programs to reduce overall structural weight.
2. Propulsion and Engine Systems:
- High-Temperature Fasteners: Engine environments demand materials capable of withstanding extreme temperatures. Alloys like Nickel-based superalloys (e.g., Inconel 718, 625) or high-temperature Titanium alloys can be processed via AM to create specialized bolts, studs, and nuts for hot sections, potentially incorporating cooling channels or unique locking features.
- Lightweight Auxiliary Component Fasteners: Clips, clamps, and mounting fasteners for securing wiring harnesses, fluid lines, and engine accessories can be topology-optimized and 3D printed from materials like Ti−6Al−4V to save precious weight without compromising strength.
- Complex Internal Features: Research is exploring fasteners with integrated locking mechanisms, sensor housings, or specific flow channels (e.g., for localized cooling or lubrication), functionalities difficult to achieve conventionally.
3. Cabin Interiors and Non-Structural Fittings:
- Custom Mounting Hardware: Attaching seats, overhead bins, galleys, and other cabin monuments often requires specialized brackets and fasteners. AM allows for the creation of lightweight, customized hardware tailored to specific interior layouts or upgrade packages, often printed from Aluminium alloys or specialized polymers (though this article focuses on metal).
- Aesthetic and Ergonomic Designs: While less critical than structural integrity, AM allows for fastener heads or related fittings with unique aesthetic or ergonomic designs for visible interior applications.
4. Space Exploration (Satellites, Launch Vehicles):
- Extreme Lightweighting: In space applications, every gram counts. AM enables the aggressive optimization of fasteners using topology optimization and advanced alloys like Ti−6Al−4V. Fasteners can be designed to the absolute minimum mass required for their specific load case.
- Bespoke Fasteners for Scientific Instruments: Complex scientific payloads often require unique mounting solutions and fasteners with specific material properties (e.g., low outgassing, non-magnetic). AM provides the flexibility to create these highly specialized components in very low volumes.
- Rapid Prototyping for Launch Systems: Fast iteration cycles enabled by AM are invaluable during the development of new launch vehicles and satellite systems, allowing quick testing of fastener designs.
Addressing Procurement Needs: For aerospace procurement managers and supply chain professionals, metal AM offers solutions to persistent challenges:
- Sourcing Obsolete Parts: Provides a viable path to obtain fasteners no longer in production.
- Reducing Minimum Order Quantities (MOQs): Eliminates the need for large batch orders of specialized fasteners, reducing inventory holding costs.
- Supplier Consolidation: Partnering with a capable AM provider like Met3dp, who handles multiple materials and post-processing, can potentially streamline the supply base.
- Improved Responsiveness: Faster production of prototypes and urgent low-volume requirements, critical in situations like Aircraft on Ground (AOG).
The application landscape for metal 3D printed fasteners is diverse and expanding. As the technology matures, qualification processes become more standardized, and engineers gain more experience with Design for Additive Manufacturing (DfAM), we can expect AM to play an increasingly integral role in how aerospace components are designed, sourced, and manufactured.
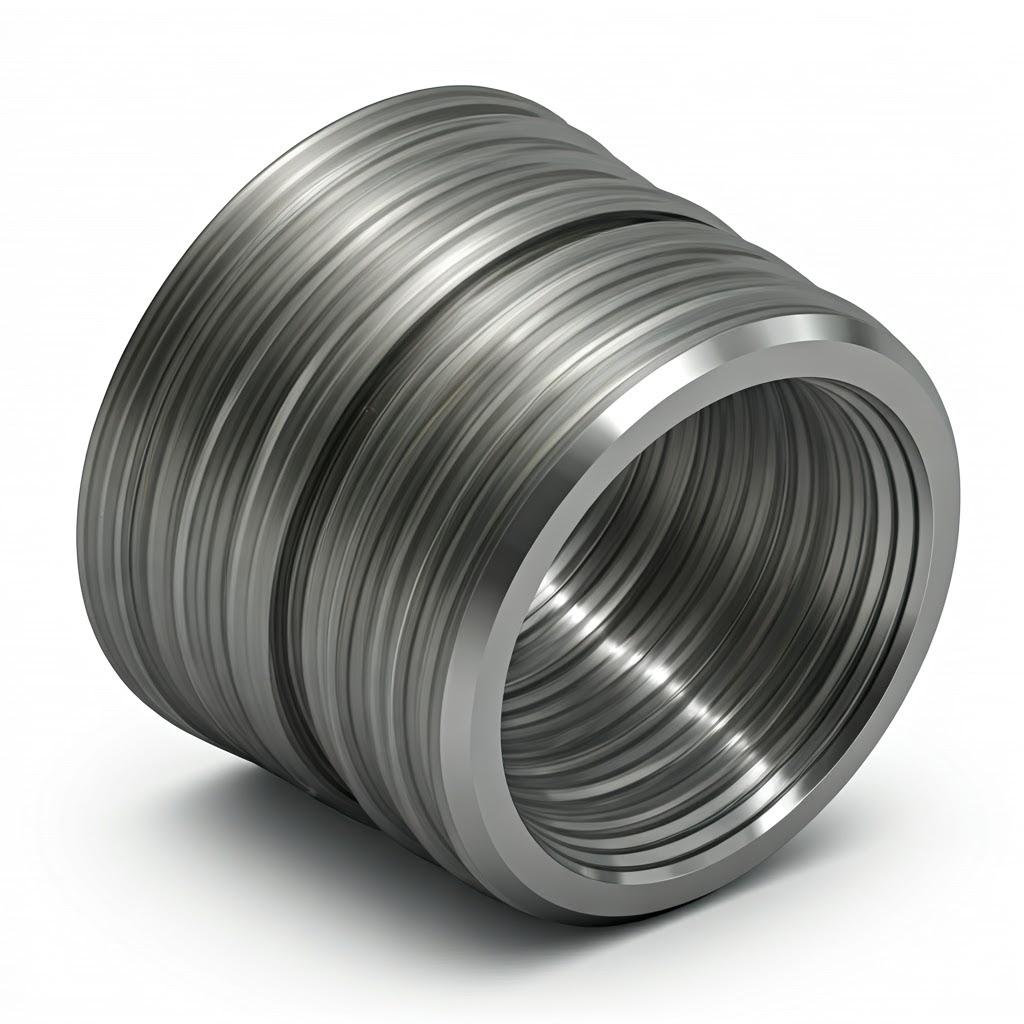
Why Metal Additive Manufacturing for Aerospace Fastener Production?
The decision to adopt a new manufacturing technology, especially for safety-critical components like aerospace fasteners, requires a clear understanding of its advantages over established methods. Metal Additive Manufacturing (AM) offers a compelling suite of benefits that directly address key drivers in the aerospace industry: performance, efficiency, cost-effectiveness (in specific scenarios), and supply chain resilience. Let’s dissect the advantages AM brings compared to traditional techniques like CNC machining, forging, and casting, focusing on aspects crucial for both engineers and procurement managers.
Comparison: Metal AM vs. Traditional Methods for Fasteners
Funktion | Metal Additive Manufacturing (e.g., LPBF, EBM) | CNC Machining (Subtractive) | Forging / Casting (Forming) |
---|---|---|---|
Designfrihet | Very High (Complex geometries, internal features, optimization) | Moderate (Limited by tool access) | Low (Requires dedicated tooling, limited complexity) |
Anpassning | High (Economical for single parts / small batches) | Moderate (Setup time impacts cost for low volumes) | Low (High tooling cost makes customization expensive) |
Lead Time (Proto) | Fast (Days) | Moderate (Days to weeks) | Slow (Weeks to months due to tooling) |
Lead Time (Prod) | Moderate (Depends on volume/complexity) | Fast (High volume) | Fast (High volume, post-tooling) |
Material Avfall | Low (Near-net shape) | High (Significant waste) | Moderate (Flash/gates, but better than machining) |
Verktygskostnad | None / Minimal | Low (Standard cutting tools) | Very High (Dies / Molds) |
Konsolidering av delar | High Potential | Låg | Låg |
Typiska material | Ti Alloys, Ni Alloys, Steels, Al Alloys | Wide Range | Forgeable / Castable Alloys |
Surface Finish (As-Built) | Moderate to Rough | Good to Excellent | Moderate to Rough |
Internal Defects | Potential (Requires process control) | Minimal (From raw material) | Potential (Porosity, inclusions) |
Export to Sheets
Key Advantages of Metal AM for Fasteners:
- Unparalleled Design Freedom & Optimization:
- Topology Optimization: Algorithms can redesign a standard fastener shape to remove material from low-stress areas, creating organically shaped, lightweight components that meet or exceed performance requirements. This is particularly impactful for titanium fasteners where material cost and weight are high.
- Del Konsolidering: AM can integrate fastener features directly into larger components (brackets, housings), reducing part count, assembly complexity, weight, and potential failure points.
- Komplexa geometrier: Features impossible or prohibitively expensive with other methods become feasible. This could include internal locking mechanisms, integrated sensor cavities, or optimized head shapes for specific tools or aerodynamic profiles. Lattice structures within less critical areas could offer further lightweighting.
- Rapid Prototyping, Iteration, and Validation:
- AM drastically accelerates the design-build-test cycle. Engineers can conceive multiple fastener designs, print prototypes within days, and perform functional testing much faster than waiting for machined parts or forging tooling. This speed fosters innovation and reduces development risk.
- Economical Customization & On-Demand Production:
- AM excels where traditional methods struggle: producing highly customized parts in low volumes. Need a unique fastener for a specific repair or modification? AM can produce it without the massive tooling investment of forging or the potentially high setup cost of machining a single complex part.
- Digital Inventory: Instead of stocking vast quantities of physical fasteners (especially slow-moving or obsolete ones), designs can be stored digitally and printed only when needed. This reduces warehousing costs, minimizes waste from scrapped inventory, and improves responsiveness for MRO operations.
- Significant Material Efficiency:
- The “Buy-to-Fly” ratio represents the weight of raw material purchased compared to the weight of the final component. Subtractive machining, especially for complex shapes from expensive materials like Ti−6Al−4V, can have ratios of 10:1 or even higher (meaning 90% of the material becomes waste). AM builds parts near-net shape, drastically reducing this waste, often achieving ratios closer to 2:1 or better depending on support structure needs. This directly translates to cost savings, particularly for premium alloys.
- Performance Enhancement Potential:
- Primarily through lightweighting via topology optimization, AM fasteners can significantly improve the strength-to-weight ratio, contributing to overall aircraft fuel efficiency or payload capacity.
- While requiring careful process control and post-processing, AM parts can achieve mechanical properties comparable or even superior (in certain aspects like fatigue, if post-processed correctly e.g., shot peening) to wrought or cast materials.
- Enhanced Supply Chain Resilience & Agility:
- AM offers the potential for localized, distributed manufacturing. Instead of relying on distant, specialized suppliers with long lead times, certified AM facilities could potentially produce needed fasteners closer to the point of use, reducing shipping times and logistical complexity.
- This agility is crucial for addressing unexpected demands, such as AOG situations where rapid part availability is paramount. The ability to quickly print a certified replacement fastener can significantly reduce aircraft downtime.
While AM is not a universal replacement for all fastener production (high-volume standard fasteners are still typically more economical via traditional methods), its advantages in specific, high-value scenarios are undeniable. For procurement managers evaluating total cost of ownership, lead time impacts, and supply chain risk, and for engineers seeking performance gains and design flexibility, metal additive manufacturing presents a powerful tool for producing the next generation of aerospace fasteners. Leveraging the capabilities of experienced partners like Met3dp, who understand both the intricacies of various tryckmetoder and the demands of the aerospace sector, is key to successfully implementing this technology.
Material Spotlight: Ti−6Al−4V and 17−4PH for High-Performance Fasteners
Material selection is paramount in aerospace design, and nowhere is this truer than for fasteners, which must reliably bear significant loads under demanding operating conditions. Additive Manufacturing expands the possibilities but also requires careful consideration of how materials behave during the layer-by-layer fabrication process and subsequent post-processing. Two workhorse alloys stand out for their frequent use in demanding aerospace applications, including fasteners manufactured via AM: Titanium Ti−6Al−4V (Grade 5) and Stainless Steel 17−4PH. Understanding their properties and AM processing nuances is critical for engineers and procurement specialists.
The Importance of Powder Quality in AM: Before diving into the specific alloys, it’s crucial to emphasize that the quality of the final AM part begins with the quality of the metal powder feedstock. Properties like:
- Sfäriskhet: Smooth, spherical powder particles ensure good flowability and uniform spreading during the AM process, leading to denser parts.
- Fördelning av partikelstorlek (PSD): A controlled PSD is essential for achieving high packing density and predictable melting behavior.
- Renhet: Low levels of impurities, particularly interstitial elements like Oxygen and Nitrogen (especially critical for Titanium), are vital for achieving desired mechanical properties and avoiding defects.
- Flytbarhet: Consistent powder flow ensures uniform layers and stable processing.
Företag gillar Met3dp specialize in producing high-quality, aerospace-grade metallpulver using advanced techniques like vacuum induction melting gas atomization (VIGA) and the Plasma Rotating Electrode Process (PREP). These processes yield powders with high sphericity, controlled PSD, low contamination, and excellent flowability, forming the foundation for reliable and high-performance AM aerospace components, including fasteners made from alloys like Ti−6Al−4V and 17−4PH.
1. Titanium Alloy: Ti−6Al−4V (Grade 5)
- Sammansättning: Primarily Titanium, alloyed with approximately 6% Aluminum and 4% Vanadium.
- Viktiga egenskaper:
- Högt förhållande mellan styrka och vikt: This is arguably its most significant advantage in aerospace. It offers strength comparable to many steels but at roughly 56% of the density.
- Utmärkt korrosionsbeständighet: Forms a stable, passive oxide layer providing outstanding resistance to general corrosion, saltwater, and many industrial chemicals.
- Good High-Temperature Performance: Retains useful strength up to approximately 315∘C (600∘F), with some usability up to 400∘C (750∘F).
- Biokompatibilitet: While less relevant for fasteners, its biocompatibility makes it suitable for medical implants.
- Why Ideal for Aerospace Fasteners: Its low density makes it perfect for weight-critical applications in airframes (structural joints, skin attachments), engine mounts, and particularly space structures where mass reduction is paramount. Its corrosion resistance ensures longevity in exposed environments.
- AM Processing Considerations:
- Processes: Commonly processed using Laser Powder Bed Fusion (LPBF, also known as SLM) and Electron Beam Melting (EBM). EBM often results in lower residual stress due to higher processing temperatures but typically yields a rougher surface finish.
- Atmosphere: Requires processing in a high-purity inert atmosphere (Argon) or vacuum (EBM) to prevent contamination, especially oxygen pickup, which can embrittle the material.
- Efterbearbetning: Typically requires stress relief annealing immediately after printing to reduce internal stresses built up during the rapid heating/cooling cycles. Further heat treatments (e.g., Solution Treatment and Aging – STA) can be used to optimize strength and ductility. Machining is often necessary for critical dimensions like threads.
- Typical Mechanical Properties (AM, Heat Treated): (Note: These are approximate values and depend heavily on process parameters, orientation, and heat treatment)
- Ultimate Tensile Strength (UTS): 900−1150MPa
- Yield Strength (YS): 830−1050MPa
- Elongation: 6−15%
- Density: ≈4.43g/cm3
2. Stainless Steel: 17−4PH (Precipitation Hardening)
- Sammansättning: Primarily Iron, alloyed with significant amounts of Chromium (≈15−17.5%), Nickel (≈3−5%), and Copper (≈3−5%).
- Viktiga egenskaper:
- High Strength & Hardness: Can be heat-treated to various strength levels through precipitation hardening, achieving excellent tensile and yield strengths.
- God korrosionsbeständighet: Offers better corrosion resistance than standard martensitic stainless steels (like 410), though generally less resistant than austenitic grades (like 316) or Ti−6Al−4V. Sufficient for many atmospheric aerospace environments.
- Good Toughness: Maintains reasonable toughness even at high strength levels.
- Värmebehandlingsbar: Its properties can be tailored via relatively simple, low-temperature aging treatments after an initial solution annealing.
- Why Ideal for Aerospace Fasteners: Provides a cost-effective solution where high strength and hardness are primary requirements, and the extreme lightweighting of titanium is not necessary. Common applications include landing gear components, actuators, flap tracks, engine pylon fittings, and other structural elements requiring robust performance.
- AM Processing Considerations:
- Processes: Primarily processed using LPBF.
- Atmosphere: Requires an inert atmosphere (Argon or Nitrogen) to prevent oxidation during printing.
- Efterbearbetning: Requires solution annealing followed by an aging (precipitation hardening) heat treatment to achieve desired mechanical properties. Common conditions include H900 (highest strength, lowest ductility) up to H1150 (lower strength, higher ductility and toughness). Machining is frequently needed for threads and tolerance-critical features.
- Typical Mechanical Properties (AM, Heat Treated): (Values vary significantly with heat treatment condition) | Heat Treatment | UTS (Approx. MPa) | YS (Approx. MPa) | Elongation (Approx. %) | Hardness (Approx. HRC) | | :————- | :—————- | :————— | :——————— | :——————— | | H900 | 1350−1500 | 1200−1400 | 5−10% | 40−48 | | H1025 | 1150−1300 | 1050−1200 | 8−12% | 35−42 | | H1150 | 950−1100 | 750−900 | 10−18% | 28−36 |
- Density: ≈7.8g/cm3
Choosing the Right Material: The selection between Ti−6Al−4V and 17−4PH (or other potential AM alloys like Inconel 718/625 for very high temperatures) depends heavily on the specific application requirements:
- Välja Ti−6Al−4V when: Weight saving is critical, operating temperatures are moderately high (up to ≈315∘C), and excellent corrosion resistance is required.
- Välja 17−4PH when: Hög hållfasthet och hårdhet are the primary drivers, cost is a greater concern than weight, and good (but not exceptional) corrosion resistance is sufficient.
By understanding the properties of these key alloys and partnering with knowledgeable AM providers like Met3dp who ensure the highest quality powder feedstock and possess process expertise, aerospace companies can confidently leverage additive manufacturing to produce high-performance, reliable fasteners tailored to the demanding needs of the industry.
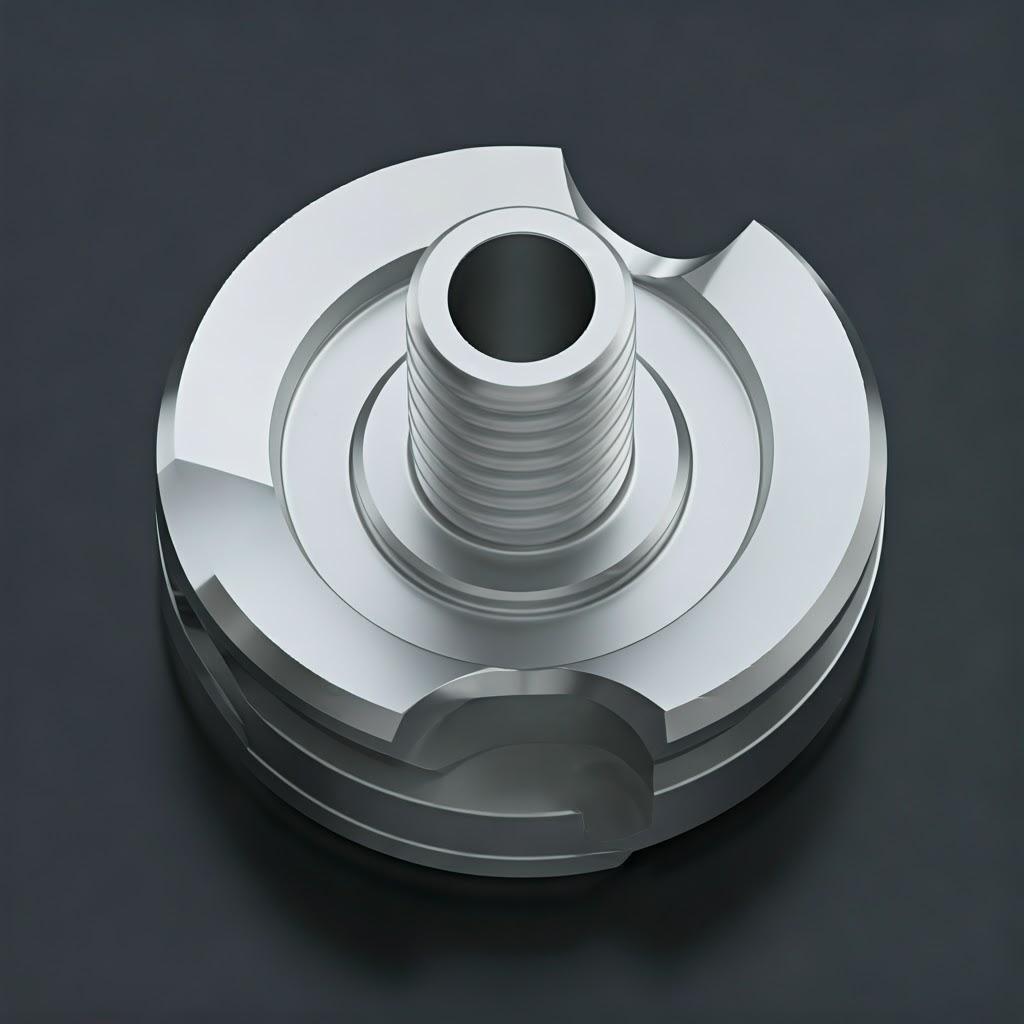
Optimizing Aerospace Fastener Design for Metal Additive Manufacturing (DfAM)
Simply taking a CAD model designed for traditional machining or forging and sending it to a metal 3D printer rarely yields optimal results. To truly harness the power of Additive Manufacturing (AM) for aerospace fasteners, engineers must embrace the principles of Design för additiv tillverkning (DfAM). DfAM involves rethinking component design from the ground up, considering the unique opportunities and constraints of the layer-by-layer building process. Applying DfAM to fasteners can lead to lighter weight, improved performance, reduced print time, minimized post-processing, and ultimately, more cost-effective and reliable components.
Core DfAM Principles Relevant to Fasteners:
- Self-Supporting Angles: AM processes have limitations on the minimum angle a surface can make with the build plate without requiring support structures underneath. This angle varies by material, process (LPBF/EBM), and specific machine parameters, but angles greater than ≈45∘ are often self-supporting. Designing features like chamfers on overhangs instead of sharp 90-degree angles can significantly reduce the need for supports.
- Minimize Support Structures: Supports consume extra material, increase print time, and require removal in post-processing, which adds labor cost and risks damaging the part surface. DfAM aims to minimize or eliminate supports by optimizing part orientation and modifying geometries (e.g., using diamond or teardrop shapes for horizontal holes instead of perfect circles).
- Feature Resolution: AM processes have minimum producible feature sizes (walls, pins, holes). Fine details common in fasteners, like small locking wire holes or fine serrations under the head, must be designed within the capabilities of the chosen AM process and machine.
- Build Orientation Strategy: How a fastener is oriented on the build plate profoundly impacts:
- Ytfinish: Surfaces parallel or at low angles to the build plate exhibit “stair-stepping” effects; vertical walls generally have better finishes.
- Mekaniska egenskaper: Anisotropy (direction-dependent properties) can occur in AM parts. Orientation must consider the primary load directions the fastener will experience.
- Support Requirements: Orienting to minimize overhangs reduces support needs.
- Print Time: Taller builds generally take longer. Nesting multiple fasteners efficiently requires careful orientation planning.
DfAM Considerations Specific to Aerospace Fasteners:
- Thread Design:
- Direct Printing Challenges: Printing fine, standard aerospace threads (e.g., UNJ profile) directly is highly challenging due to accuracy limitations, poor surface finish on thread flanks (especially downward-facing ones), and the difficulty of removing internal support material without damaging the threads.
- Recommended Approach: The most common and reliable strategy is to print the fastener blank either undersized or without threads entirely, then machine the threads post-print using conventional thread cutting or rolling methods. This ensures accuracy, proper surface finish, and adherence to strict aerospace thread specifications.
- Alternative (Less Common for Critical Fasteners): For less critical applications, designing coarser, modified thread profiles with self-supporting angles might be explored, but requires extensive validation. Using standard helical coil inserts (e.g., Heli-Coil®) in printed holes is another viable DfAM approach.
- Fastener Head Optimization:
- Lättvikt: The head is often a prime candidate for topology optimization to remove non-load-bearing material, significantly reducing weight, especially for larger bolts or fasteners made from dense materials.
- Support Reduction: Designing gentle chamfers or radii under the head instead of sharp overhangs can minimize support requirements when printed vertically.
- Tool Engagement: Ensure AM-specific features don’t interfere with standard installation tooling (sockets, wrenches). Consider designing integrated anti-rotation features if consolidating parts.
- Support Structure Strategy:
- Minimization: Beyond orientation and self-supporting angles, clever design can reduce support needs. For example, incorporating sacrificial layers or designing features specifically to support subsequent layers.
- Ease of Removal: Supports should be designed with minimal contact points, strategically placed away from critical surfaces like threads or bearing areas. Utilizing support types designed for easy removal (e.g., perforated or tree supports) is crucial. Poor support removal can easily scrap an otherwise good part. The expertise of the AM service provider, like Met3dp, in designing effective and easily removable support strategies is invaluable.
- Del Konsolidering:
- DfAM encourages looking beyond the fastener itself. Can the fastener’s function be integrated into an adjacent bracket or mounting plate? AM allows the creation of a single, complex component (e.g., a bracket with built-in threaded studs or captive nuts), reducing part count, assembly time, weight, and potential leak paths or failure points associated with joints.
- Internal Features:
- AM enables the creation of internal channels or cavities. While less common in standard fasteners, this could be leveraged for future concepts like integrated health monitoring sensors, self-locking mechanisms activated by specific conditions, or internal cooling passages for very high-temperature bolts (though complexity and cost increase significantly).
By applying these DfAM principles, engineers can move beyond simply replicating traditional fastener designs and start leveraging the unique capabilities of additive manufacturing to create superior, optimized components for demanding aerospace applications. Collaboration between design engineers and AM process experts is key to successful DfAM implementation.
Achievable Tolerances, Surface Finish, and Dimensional Accuracy in 3D Printed Fasteners
A critical aspect for engineers and procurement managers considering metal AM for aerospace fasteners is understanding the achievable levels of precision. Aerospace components demand tight tolerances, specific surface finishes for mating surfaces and fatigue life, and overall high dimensional accuracy. While AM offers design freedom, it’s essential to have realistic expectations about the ‘as-built’ state of 3D printed fasteners and the role of post-processing in meeting final requirements.
As-Built Tolerances and Surface Finish:
- Tolerances: Metal AM processes like Laser Powder Bed Fusion (LPBF) and Electron Beam Melting (EBM) typically achieve dimensional tolerances in the range of ±0.1 mm to ±0.3 mm for smaller features, or around ±0.1% to ±0.2% of the overall dimension for larger parts. These values are general guidelines and can be influenced by:
- Machine Calibration: Accuracy and repeatability of the specific AM system.
- Material: Different alloys exhibit varying shrinkage and thermal behavior.
- Part Geometry & Size: Complex shapes and larger parts are more prone to thermal distortion.
- Orientation: Affects thermal history and potential for warpage.
- Termisk hantering: Build plate heating, process parameters.
- Pulver Egenskaper: Consistent powder leads to more predictable melting and solidification.
- Ytfinish: The as-built surface finish of metal AM parts is inherently rougher than machined surfaces due to the layer-by-layer process and partially melted powder particles adhering to the surface.
- LPBF: Typically achieves surface roughness (Ra) values ranging from 5μm to 25μm. Vertical walls are generally smoother than angled or horizontal surfaces (“up-skins” and “down-skins”).
- EBM: Generally produces rougher surfaces than LPBF, often in the range of 20μm to 50μm Ra, due to larger powder particles and higher processing temperatures causing more sintering.
- Jämförelse: Conventionally machined or ground surfaces often achieve Ra values well below 1μm.
Implications for Aerospace Fasteners: The as-built tolerances and surface finish of AM parts are often insufficient for critical features on aerospace fasteners without secondary processing. Key areas requiring higher precision include:
- Threads: Require precise geometry and smooth flanks for proper engagement, load distribution, and fatigue life.
- Bearing Surfaces: The area under the head that contacts the clamped material needs to be flat and smooth for even load distribution.
- Shank Diameter: Critical for shear load calculations and proper fit in close-tolerance holes.
- Seating Faces: Any surfaces designed to create a seal.
Achieving Aerospace-Grade Precision:
The key takeaway is that post-processing, particularly CNC machining, is almost always necessary to bring critical features of AM fasteners into compliance with stringent aerospace specifications.
- Machining Allowances: DfAM principles include adding extra material (machining stock or allowance, typically 0.5mm – 2mm) to surfaces that will require machining after printing.
- Final Tolerances: After post-machining, the achievable tolerances on AM fasteners are comparable to those achieved through fully traditional manufacturing routes. Tolerances of ±0.01 mm to ±0.05 mm can be readily achieved on machined features.
- Surface Finish Improvement: Machining, grinding, polishing, or even processes like shot peening can significantly improve the surface finish to meet specific Ra requirements and enhance fatigue performance.
Metrology and Quality Verification:
Ensuring that AM fasteners meet dimensional and surface specifications requires robust metrology and inspection techniques:
- Coordinate Measuring Machines (CMMs): Provide high-accuracy point measurements for verifying critical dimensions after machining.
- Optical / Laser Scanning: Capture full 3D geometry for comparison against the original CAD model, useful for complex shapes and verifying overall form, especially before machining.
- Surface Profilometry: Measures surface roughness (Ra, Rz, etc.) to ensure compliance with specifications.
- Traditional Gauges: Thread gauges, micrometers, and calipers are used for standard feature checks post-machining.
- Computed Tomography (CT) Scanning: Increasingly used not just for internal defect detection but also for non-destructive dimensional verification of internal features or complex geometries that are hard to access with other methods.
Achieving the required precision for AM aerospace fasteners depends on a combination of factors: careful DfAM, high-quality metal powders, well-calibrated and reliable AM systems (a focus for providers like Met3dp), optimized process parameters, and, critically, well-planned and executed post-processing operations. Understanding this workflow is essential for setting realistic expectations regarding costs, lead times, and final part quality.
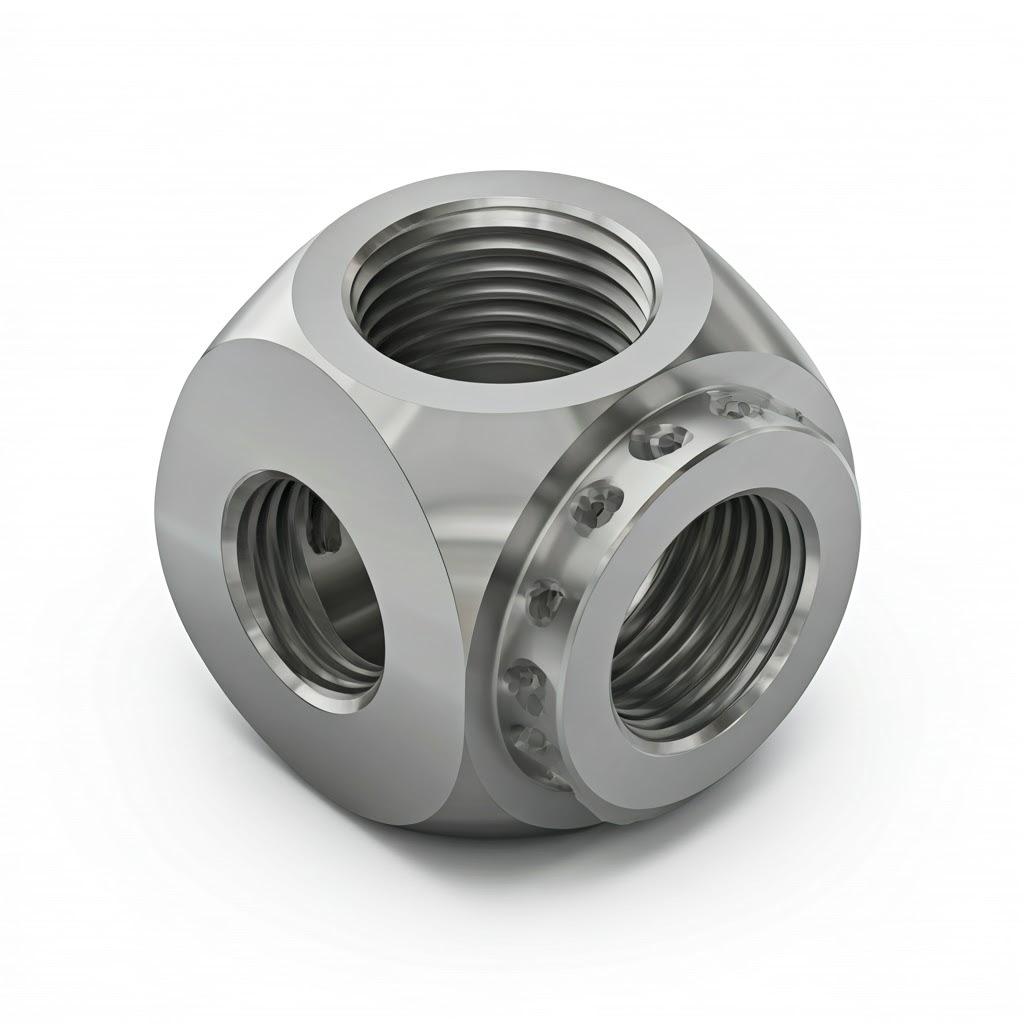
Essential Post-Processing Steps for AM Aerospace Fasteners
The journey of an additively manufactured aerospace fastener doesn’t end when the 3D printer stops. In fact, the post-processing steps that follow are absolutely critical for transforming the raw, as-built part into a flight-worthy component that meets the stringent requirements for strength, fatigue life, dimensional accuracy, and surface integrity demanded by the aerospace industry. Neglecting or improperly executing these steps can compromise the fastener’s performance and safety.
Here’s a breakdown of the essential post-processing stages commonly applied to metal AM fasteners made from alloys like Ti−6Al−4V and 17−4PH:
- Stress Relief / Heat Treatment:
- Syfte: The rapid heating and cooling inherent in AM processes (especially LPBF) induce significant residual stresses within the part. These stresses can cause distortion, cracking, and severely degrade mechanical properties, particularly fatigue life. Heat treatment is essential to relieve these stresses and optimize the material’s microstructure for desired properties.
- Process:
- Stressavlastning: Often performed while the part is still attached to the build plate, typically involving heating the part to a specific temperature (below transformation temperatures), holding it for a set duration, and then slowly cooling. This reduces residual stress without significantly altering the core microstructure.
- Solution Treatment & Aging (STA) / Annealing: These are full heat treatment cycles designed to modify the material’s microstructure to achieve specific strength, ductility, and toughness levels required by aerospace specifications (e.g., AMS standards for Ti−6Al−4V or specific H-conditions like H900, H1025 for 17−4PH). These cycles involve heating to higher temperatures, potentially quenching, and then aging at intermediate temperatures.
- Importance: This is arguably the most critical post-processing step for ensuring the structural integrity and performance of AM aerospace fasteners. Skipping or incorrectly performing heat treatment renders the part unsuitable for critical applications.
- Part Removal & Support Structure Removal:
- Syfte: Separating the printed fastener(s) from the build plate and removing the support structures generated during the build.
- Process: Parts are typically removed from the build plate using wire EDM (Electrical Discharge Machining) or sawing. Support structures are then removed manually (breaking, cutting, grinding) or via CNC machining.
- Utmaningar: Support removal must be done carefully to avoid damaging the part surface, especially near critical features. DfAM plays a crucial role here by minimizing the amount and complexity of supports needed. Access for tools can be difficult in complex geometries.
- CNC Machining:
- Syfte: To achieve the required dimensional accuracy and surface finish on critical features that cannot be met by the as-built AM process.
- Process: Utilizes standard CNC milling, turning, grinding, and threading equipment.
- Key Areas Machined on Fasteners:
- Threads (cutting or rolling)
- Head bearing surfaces (facing)
- Critical shank diameters (turning/grinding)
- Seating faces or chamfers
- Holes (drilling/reaming for locking wire or cotter pins)
- Överväganden: Machining stock must be included in the AM design. The microstructure of AM materials can sometimes differ from wrought counterparts, potentially requiring adjusted machining parameters (speeds, feeds, tooling).
- Surface Finishing & Enhancement:
- Syfte: To improve surface quality beyond basic machining, enhance fatigue life, or apply specific functional coatings.
- Processes:
- Tumbling / Vibratory Finishing: Mass finishing techniques for deburring edges and providing a more uniform, though generally not highly smooth, surface finish.
- Shot Peening: A controlled process that bombards the surface with small spherical media (shot). This induces beneficial compressive residual stresses in the surface layer, significantly improving fatigue life – a critical factor for fasteners under cyclic loading.
- Polishing / Lapping: Used if exceptionally smooth surfaces (low Ra) are required for specific sealing or bearing applications.
- Beläggning: Application of specialized coatings like dry film lubricants (e.g., Molybdenum Disulfide – MoS2, Tungsten Disulfide – WS2) to reduce friction and prevent galling (cold welding) in threads, especially for titanium and stainless steel fasteners. Conversion coatings or passivation may also be applied for enhanced corrosion protection.
- Cleaning & Inspection (including NDT):
- Syfte: To ensure the fastener is free from contaminants, debris (from machining/supports), and defects, and meets all specifications.
- Process: Thorough cleaning procedures are required. Inspection involves:
- Visual Inspection (VT): Basic check for obvious flaws.
- Dimensionell inspektion: Using CMM, scanners, gauges as described previously.
- Icke-förstörande testning (NDT): Critical for aerospace certification to detect surface and internal defects without damaging the part. Common NDT methods for fasteners include:
- Dye Penetrant Inspection (PT): Reveals surface-breaking cracks.
- Magnetic Particle Inspection (MT): Detects surface and near-surface flaws in ferromagnetic materials like 17−4PH.
- Ultrasonic Testing (UT): Can detect internal flaws like porosity or lack-of-fusion.
- Computed Tomography (CT): Provides detailed 3D images of internal structures, highly effective for detecting internal voids/defects and verifying complex geometries.
Successfully navigating these essential post-processing steps requires significant expertise, specialized equipment, and robust quality control systems. Partnering with a vertically integrated AM provider or one with a well-managed network of qualified post-processing partners is crucial for obtaining certified, flight-ready aerospace fasteners.
Mitigating Common Challenges in Metal AM Fastener Production
While metal additive manufacturing offers transformative potential for producing custom aerospace fasteners, it’s not without its challenges. Understanding potential issues during the printing and processing stages, along with effective mitigation strategies, is crucial for ensuring consistent quality, reliability, and cost-effectiveness. Proactive planning and partnership with experienced AM providers are key to navigating these complexities.
Common Challenges and Mitigation Strategies:
- Warping and Distortion:
- Utmaning: Significant temperature gradients during the build process cause expansion and contraction, leading to internal stresses that can warp the part or even detach it from the build plate. Thin features and large flat areas are particularly susceptible.
- Mitigation:
- Thermal Simulation: Using software to predict thermal behavior and stress accumulation during the design phase.
- Optimized Orientation: Orienting the part to minimize large flat surfaces parallel to the build plate and manage heat distribution.
- Robust Support Structures: Well-designed supports anchor the part effectively and help dissipate heat.
- Build Plate Heating: Maintaining an elevated build plate temperature (common in EBM, controllable in LPBF) reduces thermal gradients.
- Processparameteroptimering: Adjusting laser/beam power, scan speed, and scan strategy can influence thermal input.
- Immediate Stress Relief: Performing a stress relief heat treatment cycle directly after the build, often before removal from the plate.
- Porosity (Gas & Lack-of-Fusion):
- Utmaning: Small voids within the printed material. Gas porosity arises from gas trapped within the powder particles or dissolved in the melt pool. Lack-of-fusion porosity occurs when the laser/electron beam energy is insufficient to fully melt and fuse powder particles between layers or scan tracks. Porosity acts as stress concentrators, severely degrading fatigue life and tensile strength.
- Mitigation:
- High-Quality Powder: Using powder with low internal gas content, controlled particle size distribution, and high flowability is critical. Sourcing from reputable suppliers like Met3dp, who utilize advanced atomization techniques (VIGA, PREP) and stringent quality control, significantly minimizes powder-related porosity. Explore the range of solutions available at Met3dp.
- Optimized Process Parameters: Developing and validating robust parameter sets (power, speed, hatch spacing, layer thickness) to ensure complete melting and fusion for the specific material and machine.
- Inert Atmosphere Control: Maintaining high purity in the build chamber (low oxygen/moisture levels) prevents gas pickup during melting.
- Het isostatisk pressning (HIP): A post-processing step involving high temperature and high pressure (using an inert gas like Argon). HIP can effectively close internal voids (both gas and lack-of-fusion), significantly improving density and mechanical properties. However, it adds cost and lead time.
- Cracking:
- Utmaning: Cracks can form during printing or cooling due to high residual stresses, particularly in alloys susceptible to solidification cracking or strain age cracking (e.g., some high-strength nickel alloys or aluminum alloys, though less common in standard Ti−6Al−4V or 17−4PH if processed correctly).
- Mitigation:
- Processtyrning: Careful control over thermal gradients through parameter optimization and heating strategies.
- Material Chemistry: Ensuring powder chemistry is within specification and free from detrimental impurities.
- Stressavlastning: Prompt and appropriate heat treatment.
- DfAM: Avoiding sharp internal corners or features that act as stress risers.
- Support Structure Removal Issues:
- Utmaning: Difficulty in removing supports without damaging the fastener surface, especially threads or bearing faces. Supports that are too dense or have large contact areas can be particularly problematic.
- Mitigation:
- DfAM: Designing parts to be self-supporting where possible, optimizing orientation.
- Smart Support Design: Using specialized support types (e.g., thin, easily breakable interfaces, tree supports) and minimizing contact points on critical surfaces. Requires expertise from the AM service provider.
- Post-Processing Planning: Utilizing appropriate tools (manual, CNC machining, EDM) for removal based on support location and geometry.
- Powder Management and Contamination:
- Utmaning: Metal powders are sensitive to contamination (e.g., cross-contamination between different alloys, oxygen/moisture pickup from the atmosphere) and degradation through repeated use (changes in PSD). Contamination can drastically alter material properties and lead to defects.
- Mitigation:
- Strict Handling Protocols: Dedicated equipment for different alloys, controlled environments (low humidity), proper grounding to avoid static discharge.
- Powder Traceability: Tracking powder batches, usage history, and exposure times.
- Sieving and Conditioning: Regularly sieving powder to remove oversized particles or spatters and potentially conditioning (e.g., drying) reused powder.
- Kvalitetskontroll: Periodic chemical analysis and morphological characterization of virgin and reused powder stock. Met3dp’s integrated approach, encompassing both powder production and printing services, ensures meticulous powder management throughout the process chain.
- Process Consistency and Monitoring:
- Utmaning: Ensuring that every fastener produced meets the same high standards build after build. Variations in machine performance, environmental conditions, or material batches can affect outcomes.
- Mitigation:
- Robust Quality Management System (QMS): Implementing rigorous process controls, documentation, and calibration schedules.
- Machine Calibration & Maintenance: Regular checks and preventative maintenance on AM systems.
- In-Situ Monitoring (Advanced): Utilizing sensors within the AM machine (e.g., melt pool monitoring cameras, thermal sensors) to detect deviations from the norm during the build process, allowing for potential real-time correction or flagging parts for closer inspection.
Successfully producing reliable, high-quality aerospace fasteners via metal AM requires a holistic approach that anticipates and mitigates these potential challenges through careful design, high-quality materials, optimized and validated processes, rigorous post-processing, and stringent quality control. Partnering with an experienced and well-equipped AM service provider is essential for navigating this complex landscape.
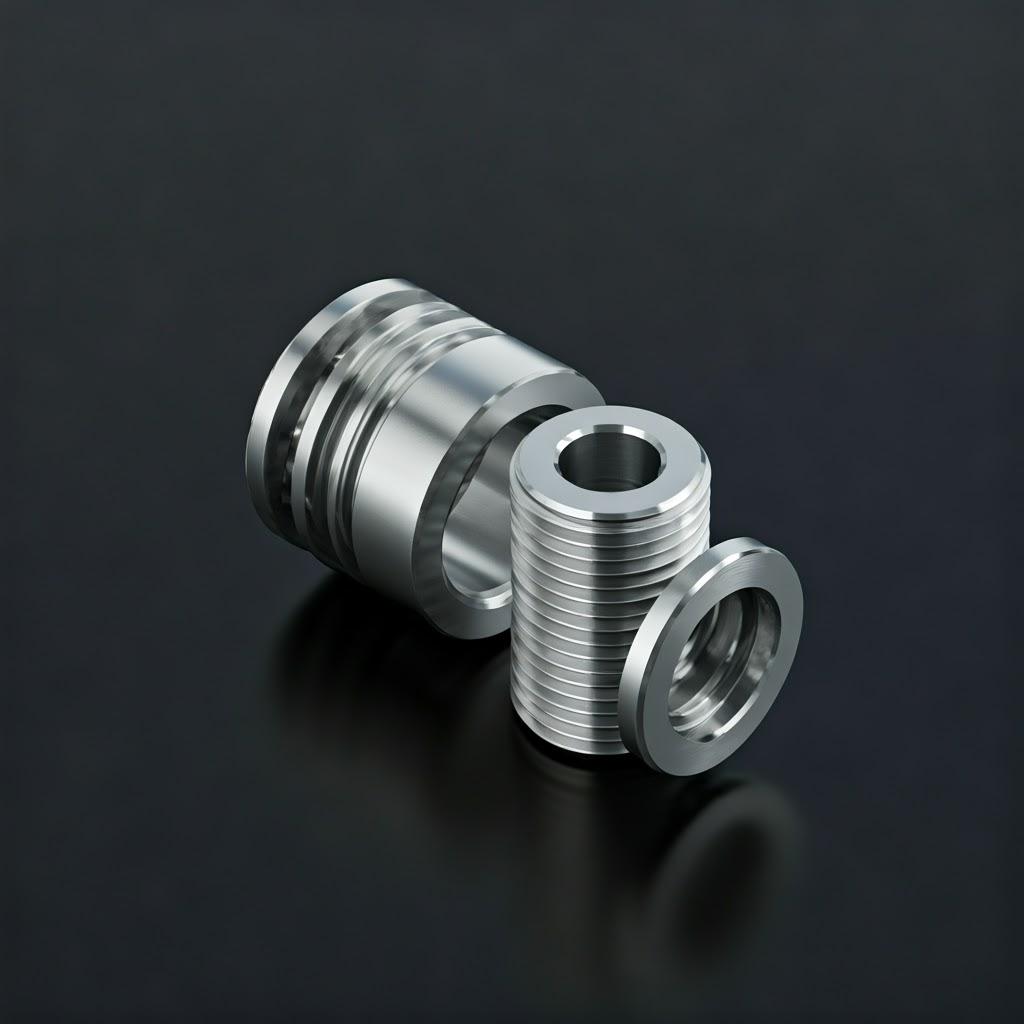
Selecting Your Metal AM Partner: Key Criteria for Aerospace Fastener Suppliers
Choosing the right manufacturing partner is always critical in aerospace, but it takes on even greater significance when adopting a relatively new technology like metal additive manufacturing for safety-critical components such as fasteners. The quality, reliability, and compliance of the final product depend heavily on the expertise, processes, and systems of your chosen AM service provider. For engineers and procurement managers navigating this landscape, evaluating potential suppliers requires a specific set of criteria beyond standard manufacturing assessments.
Key Evaluation Criteria for Metal AM Fastener Suppliers:
- Aerospace Certifications & Compliance:
- AS9100: This is the internationally recognized Quality Management System (QMS) standard for the aerospace industry. Non-negotiable for suppliers of flight-critical hardware. It ensures robust processes for traceability, configuration management, risk management, and continuous improvement. Ask for their current certificate.
- NADCAP: While AS9100 covers the overall QMS, NADCAP (National Aerospace and Defense Contractors Accreditation Program) provides specific accreditation for special processes. If the provider performs heat treatment, non-destructive testing (NDT), or chemical processing in-house, NADCAP accreditation for those specific areas provides additional assurance of process control and technical competence. If they outsource these processes, verify their partners hold relevant NADCAP approvals.
- ITAR/Export Control: If working on defense-related projects, ensure the provider complies with relevant regulations like ITAR (International Traffic in Arms Regulations) in the US or similar controls elsewhere.
- Machine Capabilities & Technology Expertise:
- Relevant Technologies: Do they operate the appropriate AM technology (e.g., Laser Powder Bed Fusion – LPBF, Electron Beam Melting – EBM) best suited for your chosen material (Ti−6Al−4V, 17−4PH) and fastener requirements (e.g., surface finish vs. residual stress)?
- Machine Quality & Maintenance: Are they using industrial-grade AM systems from reputable manufacturers? What are their calibration and preventative maintenance schedules? Consistent machine performance is vital for repeatable results.
- Material-Specific Experience: Have they demonstrated successful production using the exact aerospace alloy you require? Each material behaves differently in AM and requires specific, validated parameter sets.
- Material Expertise & Handling:
- Powder Quality Control: This is paramount. How do they source, inspect, store, handle, and track their metal powders? What measures are in place to prevent cross-contamination between alloys? How do they manage powder reuse and ensure its properties remain within specification? This is where Met3dp offers a distinct advantage, being both a manufacturer of high-quality spherical metal powders using advanced gas atomization and PREP technologies, and a provider of printing services using SEBM and other AM methods. Their deep understanding of powder characteristics directly translates to better process control and final part quality. Learn more om oss and our integrated approach.
- Materialkvalificering: Do they have experience qualifying AM materials and processes according to aerospace standards or specific customer requirements? Can they provide material certifications and traceability documentation for each batch?
- Integrated Post-Processing Capabilities:
- In-House vs. Outsourced: Does the supplier have in-house capabilities for critical post-processing steps like stress relief/heat treatment, CNC machining, surface finishing, and NDT? If outsourced, how do they manage quality and traceability within their supply chain?
- Seamless Workflow: A provider who can manage the entire workflow from printing through final inspection offers significant advantages in terms of streamlined communication, reduced lead times, and clearer accountability.
- Robust Quality Management System (QMS):
- Beyond Certification: Look deeper than the AS9100 certificate. Inquire about their specific procedures for:
- Lot Traceability: From raw powder batch to final shipped fastener.
- Process Documentation: Detailed build reports, parameter logging, post-processing records.
- Data Management: Secure storage and retrieval of process and quality data.
- Change Control: Managing changes to designs, processes, or materials.
- Inspection Protocols: Clear procedures and calibrated equipment for dimensional and NDT inspection.
- Beyond Certification: Look deeper than the AS9100 certificate. Inquire about their specific procedures for:
- Engineering Support & DfAM Expertise:
- Collaboration: Can their engineering team work collaboratively with yours to optimize fastener designs for additive manufacturing (DfAM)? Do they offer consultation on material selection, orientation strategies, and support structure design? This partnership is crucial for leveraging the full potential of AM.
- Application Development: Can they assist in developing and validating the application of AM fasteners for your specific needs?
- Track Record & References:
- Proven Experience: Ask for case studies or examples of similar aerospace components they have successfully produced. Have they worked with major aerospace OEMs or Tier 1 suppliers?
- References: Request references from other customers, particularly those in high-consequence industries.
Selecting a metal AM partner for aerospace fasteners is a strategic decision. Due diligence across these criteria will help ensure you partner with a supplier capable of delivering compliant, high-quality components that meet the demanding performance and safety standards of the aerospace industry. Look for partners like Met3dp who demonstrate a comprehensive understanding of materials, processes, and quality systems inherent to aerospace additive manufacturing.
Understanding Cost Drivers and Lead Times for Custom AM Fasteners
While metal additive manufacturing unlocks incredible potential for custom aerospace fasteners, it’s essential for procurement managers and engineers to understand the factors that influence production costs and delivery timelines. Unlike traditional mass production where costs are heavily dominated by tooling and cycle time, AM pricing is driven by a different set of variables. Understanding these allows for better budgeting, expectation setting, and optimization strategies.
Key Cost Drivers for AM Fasteners:
- Material Type and Consumption:
- Alloy Cost: The raw powder cost varies significantly between materials. Aerospace-grade Ti−6Al−4V powder is substantially more expensive than 17−4PH stainless steel or aluminum alloys. Nickel superalloys are typically even more costly.
- Part Volume: The actual volume of the final fastener directly determines the amount of powder melted, impacting cost.
- Support Structure Volume: Supports are necessary but represent ‘waste’ material (though often recyclable) and add to the overall powder consumption calculated for the print job. Efficient DfAM minimizes this.
- Machine Time (Print Time):
- Part Height & Volume: Print time is primarily driven by the number of layers (height) and the area/volume to be scanned per layer. Taller and bulkier parts take longer.
- Build Parameters: Using thicker layers speeds up the build but results in a rougher finish and potentially different mechanical properties. Finer layers improve resolution but increase time.
- Nesting Efficiency: How densely multiple fasteners can be packed onto a single build plate significantly impacts the machine time attributable to each part. Efficient nesting, often handled by the AM service provider, reduces per-part print cost.
- Komplexitet:
- Geometric Complexity: While AM handles complexity well, highly intricate designs might require more extensive support structures or more complex scan strategies, potentially increasing print time slightly. Its main impact is often on post-processing (see below).
- Internal Features: Designing complex internal channels or features adds to the data preparation complexity and inspection requirements.
- Krav på efterbearbetning:
- Värmebehandling: Different cycles (stress relief vs. full STA vs. aging) have varying durations and furnace requirements, impacting cost.
- Stöd för borttagning: Labor-intensive manual removal or dedicated machining time adds cost. Complex, hard-to-reach supports increase this significantly.
- CNC Machining: Often one of the most significant cost drivers after printing. The amount of material to remove, the number of features needing machining (threads, heads, shanks), and the required tolerances all influence machining time and cost.
- Ytbehandling: Specific requirements like shot peening, polishing, or specialized coatings add process steps and associated costs.
- NDT & Inspection: The level of required inspection (visual vs. PT/MT vs. UT/CT) and the associated documentation directly impact cost. Full CT scanning, while providing maximum insight, is more expensive than surface inspection methods.
- Orderkvantitet:
- Amortization: While AM avoids tooling costs, there are still fixed costs per build (machine setup, powder loading/unloading, data prep). These costs are amortized over the number of parts in a build. Therefore, printing a single fastener is significantly more expensive per part than printing a full plate of nested fasteners.
- Cost Curve: AM generally has a flatter cost curve than traditional methods. It’s highly cost-effective at very low volumes (prototypes, 1-100 parts), but for very high volumes (thousands), traditional methods like forging often become more economical due to lower cycle times and material costs once tooling is paid off.
- Quality & Certification:
- Stringent aerospace requirements necessitate more process control, documentation, testing, and qualification efforts, all of which contribute to the final cost compared to industrial or non-critical components.
Typical Lead Time Components:
Lead time for AM fasteners is the sum of several stages:
- Quotation & Order Processing: (1-5 days)
- Design Review & Print Preparation: DfAM checks, support generation, build file creation, scheduling. (1-3 days)
- Machine Queue Time: Waiting for machine availability. (Variable: days to weeks, depending on provider workload)
- Tryckning: Dependent on build height/volume. (Hours to several days)
- Cooling & Depowdering: Safely cooling the build and removing loose powder. (Several hours to 1 day)
- Efterbearbetning:
- Stress Relief / Heat Treatment: (1-3 days, including furnace time and controlled cooling)
- Part/Support Removal: (Hours to 1 day)
- Machining: (Variable: 1-5 days, depending on complexity and scheduling)
- Finishing/Coating: (1-3 days per step)
- Inspection & Quality Assurance: (1-2 days)
- Frakt: (Variable based on location and method)
Overall Lead Time: For custom AM aerospace fasteners, typical lead times can range from 1 to 4 weeks, heavily dependent on the factors above, particularly post-processing complexity and provider queue times. While potentially slower than off-the-shelf standard fasteners, this is often significantly faster than sourcing traditionally manufactured custom fasteners, especially for prototypes or low volumes requiring new tooling.
Working with an experienced and integrated AM service provider like Met3dp, who can manage the entire workflow efficiently, is key to optimizing both cost and lead time for your custom aerospace fastener needs.
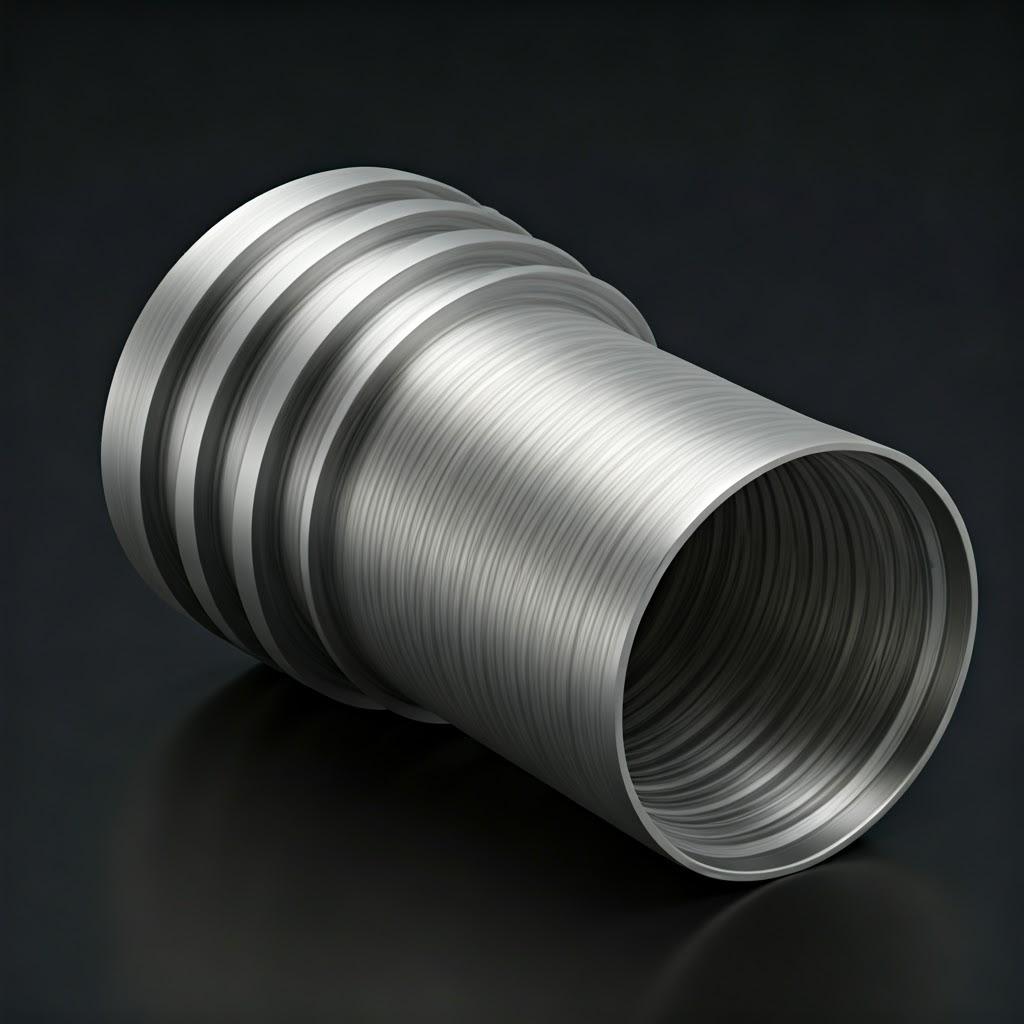
Frequently Asked Questions (FAQ) about 3D Printed Aerospace Fasteners
As metal additive manufacturing becomes increasingly adopted for aerospace components, engineers, designers, and procurement professionals often have questions about the capabilities, limitations, and reliability of 3D printed fasteners. Here are answers to some common inquiries:
Q1: Are 3D printed metal fasteners as strong as traditionally manufactured ones (e.g., forged or machined)?
A: Yes, when produced correctly, metal AM fasteners can meet or even exceed the specified mechanical properties (tensile strength, yield strength, fatigue life) of their traditionally manufactured counterparts. Achieving this requires several key factors:
- Appropriate Material: Using high-quality, aerospace-grade metal powders (like Ti−6Al−4V or 17−4PH) with controlled chemistry and morphology, such as those produced by Met3dp.
- Validated Processes: Utilizing optimized and validated printing parameters on well-calibrated industrial AM systems.
- Processtyrning: Maintaining strict control over the build environment (e.g., inert atmosphere) to prevent defects.
- Essential Post-Processing: Performing necessary heat treatments (stress relief, annealing, aging) to achieve the desired microstructure and mechanical properties, and potentially Hot Isostatic Pressing (HIP) to close any residual internal porosity.
- Designöverväganden: Accounting for potential anisotropy (direction-dependent properties) in the design phase if relevant to the loading conditions. Adherence to aerospace material specifications (e.g., AMS standards) and rigorous testing are essential to verify performance.
Q2: What aerospace standards apply to additively manufactured fasteners?
A: The landscape for AM-specific aerospace standards is rapidly evolving. Currently, compliance typically involves a combination of existing and emerging standards:
- Materialspecifikationer: Existing AMS (Aerospace Material Specifications) for alloys like Ti−6Al−4V (e.g., AMS 4928 for bar stock, with AM equivalents referencing similar properties) and 17−4PH are often used as the benchmark for required chemical composition and mechanical properties. Specific AM material specifications are also being developed (e.g., AMS7000 series).
- Process Specifications: Standards organizations like SAE, ASTM, and ISO are actively developing standards specific to AM processes (e.g., LPBF, EBM), covering aspects like machine qualification, process control, and powder handling.
- Quality Management Systems: AS9100 remains the fundamental QMS requirement for any aerospace supplier.
- OEM Specifications: Major aerospace manufacturers (Boeing, Airbus, Lockheed Martin, etc.) often have their own internal standards and qualification requirements for AM parts, which may exceed general industry standards. Suppliers must typically qualify their specific material-process combination according to these requirements.
- Fastener Standards: Existing standards for fastener dimensions, threads (e.g., MIL-S-8879, ISO standards), and testing remain applicable to the final machined features of the AM fastener.
Q3: Can any existing fastener design simply be 3D printed?
A: While technically possible to print many existing designs, it’s often suboptimal and may not even be feasible without modification. Directly printing a design created for machining or forging fails to leverage AM’s benefits and ignores its constraints. Design för additiv tillverkning (DfAM) is crucial. This involves:
- Optimizing Geometry: Redesigning for lightweighting (topology optimization), part consolidation, or improved performance.
- Addressing Constraints: Modifying features to be self-supporting, ensuring minimum feature sizes are met, planning for support structure placement and removal.
- Considering Post-Processing: Adding machining allowances for critical tolerances and threads. Effective implementation requires collaboration between design engineers and AM experts to adapt or create designs truly suited for the additive process. It’s not a simple “push-button” conversion for critical parts.
Q4: What is the typical minimum order quantity (MOQ) for custom AM fasteners?
A: One of the primary advantages of AM is its suitability for low-volume and on-demand production. Technically, the MOQ can be one single unit. This makes AM ideal for:
- Prototyper
- Highly customized designs
- Replacement parts for obsolete inventory (MRO)
- Small initial production runs before scaling up (if needed) However, it’s important to understand the cost implications. While there’s no tooling cost to amortize, fixed costs associated with setup (data preparation, machine setup, post-processing setup) mean that the per-part cost is significantly higher for a single unit compared to producing a small batch (e.g., 10-100 units) that can be nested efficiently onto a build plate. AM provides flexibility for low quantities, but the most cost-effective use often involves small-batch production rather than individual one-offs, unless the specific need justifies the higher single-unit cost.
Conclusion: Elevating Aerospace Performance and Supply Chains with Additive Manufacturing Fasteners
The aerospace industry perpetually seeks innovation to enhance performance, improve safety, and optimize operational efficiency. Metal additive manufacturing has emerged as a powerful catalyst in this pursuit, offering unprecedented capabilities for the design and production of critical components, including the humble yet vital fastener. As we’ve explored, utilizing AM for aerospace fasteners moves beyond mere novelty; it presents tangible solutions to long-standing challenges.
The key advantages are compelling:
- Oöverträffad anpassning: Producing bespoke fasteners tailored to specific applications, optimizing designs via topology optimization for significant lightweighting, and enabling part consolidation are now within reach.
- Accelerated Development & MRO: Rapid prototyping dramatically shortens design cycles, while on-demand production provides agile solutions for Maintenance, Repair, and Overhaul (MRO) operations, particularly for obsolete parts.
- Supply Chain Evolution: AM fosters greater supply chain resilience through digital inventory, reduced reliance on traditional tooling lead times, and the potential for distributed manufacturing closer to the point of need.
- Materialeffektivitet: Near-net shape production significantly reduces waste compared to subtractive methods, particularly beneficial when using high-cost aerospace alloys.
However, realizing these benefits demands a meticulous and integrated approach. Success hinges on:
- Intelligent Design (DfAM): Rethinking parts specifically for the AM process.
- Superior Materials: Utilizing high-quality, aerospace-grade metal powders with controlled characteristics.
- Robust Process Control: Employing validated parameters on industrial-grade, well-maintained AM systems.
- Critical Post-Processing: Executing essential steps like heat treatment, machining, and surface enhancements correctly.
- Rigorous Quality Assurance: Implementing comprehensive inspection, NDT, and documentation compliant with stringent aerospace standards.
Navigating this complex technological landscape requires expertise and capability. Partnering with a knowledgeable and vertically integrated supplier is paramount. Met3dp stands ready to be that partner. With our deep expertise rooted in both the production of industry-leading spherical metal powders and the operation of advanced additive manufacturing systems like SEBM, we offer comprehensive solutions tailored to the aerospace sector. Our commitment to quality, process control, and customer collaboration ensures we can help you leverage the full potential of AM for your custom fastener requirements.
Whether you are looking to lightweight existing designs, rapidly prototype new concepts, solve obsolescence issues, or enhance the performance of your aerospace systems through optimized fasteners, additive manufacturing offers a pathway.
Ready to explore how metal AM can elevate your aerospace applications? Contact the experts at Met3dp today. Visit our website at https://met3dp.com/ to learn more about our capabilities and discuss your specific project needs with our engineering team. Let us help you manufacture the future, one layer at a time.
Dela på
MET3DP Technology Co, LTD är en ledande leverantör av lösningar för additiv tillverkning med huvudkontor i Qingdao, Kina. Vårt företag är specialiserat på 3D-utskriftsutrustning och högpresterande metallpulver för industriella tillämpningar.
Förfrågan för att få bästa pris och anpassad lösning för ditt företag!
Relaterade artiklar
Om Met3DP
Senaste uppdateringen
Vår produkt
KONTAKTA OSS
Har du några frågor? Skicka oss meddelande nu! Vi kommer att betjäna din begäran med ett helt team efter att ha fått ditt meddelande.
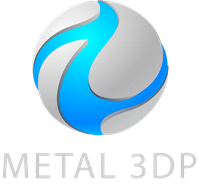
Metallpulver för 3D-printing och additiv tillverkning