3D Printed Antenna Brackets for UAV Applications
Innehållsförteckning
Introduction: The Critical Role of Antenna Brackets in Modern UAV Systems
Unmanned Aerial Vehicles (UAVs), commonly known as drones, have rapidly transitioned from niche applications to indispensable tools across a vast spectrum of industries. From sophisticated military surveillance and reconnaissance missions executed by advanced defense platforms to the revolutionizing of logistics through autonomous delivery drones, the inspection of critical infrastructure like wind turbines and bridges, and the data-driven optimization of agriculture via precision mapping, UAVs are fundamentally reshaping how we operate, monitor, and interact with the world. Their agility, remote operation capabilities, and increasing autonomy offer unprecedented advantages in efficiency, safety, and data acquisition. As these platforms become more complex and mission-critical, the performance and reliability of every single component are scrutinized more intensely than ever before. Procurement managers and engineers in aerospace, defense, and commercial sectors constantly seek innovative manufacturing solutions that deliver superior performance, reduced weight, and enhanced durability for their UAV parts supply chain.
Central to the operational success of any UAV is its ability to communicate reliably. Whether transmitting real-time video feeds, receiving command and control signals, relaying sensor data, or broadcasting telemetry, the antenna system serves as the vital link between the drone and its ground station or network. The performance of this communication link hinges significantly on the placement, orientation, and stability of the antennas themselves. This is where the antenna bracket comes into play. Far from being a simple piece of hardware, the antenna bracket is a critical structural component responsible for securely mounting the antenna(s) to the UAV airframe. It must maintain precise antenna positioning even under challenging flight conditions involving high speeds, vibrations, and environmental stresses (temperature fluctuations, moisture, G-forces). Furthermore, the bracket’s design and material composition must not interfere with the antenna’s radio frequency (RF) performance, ensuring signal integrity is maintained for mission success. Failure of the bracket can lead to degraded communication, loss of control, or complete mission failure, making its design and manufacture a critical consideration for UAV engineers and B2B suppliers.
In the quest for optimal UAV performance, traditional manufacturing methods for components like antenna brackets – such as CNC machining from billet aluminum or sheet metal fabrication – often face limitations. Machining can be subtractive and wasteful, especially for complex geometries, and can struggle to achieve the ultra-lightweight designs crucial for maximizing flight endurance and payload capacity. Sheet metal fabrication might lack the structural rigidity or geometric complexity required for optimal antenna placement and integration. This is where Additiv tillverkning av metall (AM), also known as metal 3D-utskrifter, emerges as a truly transformative technology. By building parts layer by layer directly from digital designs using high-performance metal powders, AM unlocks unprecedented possibilities for creating lightweight, complex, and highly optimized UAV components. This technology allows engineers to design brackets that are not only structurally sound but also perfectly tailored to the specific aerodynamic and RF requirements of the UAV platform, often consolidating multiple parts into a single, more reliable component. For procurement specialists looking for reliable UAV components wholesale or seeking an advanced leverantör av additiv tillverkning, understanding the potential of metal AM is becoming increasingly crucial.
Among the array of metal powders suitable for additive manufacturing, specific aluminum alloys stand out for UAV applications due to their excellent balance of low density and high strength. In particular, AlSi10Mg and the high-performance alloy Scalmalloy® -legering have become go-to materials for demanding aerospace and drone applications. AlSi10Mg offers a robust combination of mechanical properties, thermal conductivity, and printability, making it a versatile choice for many UAV brackets. Scalmalloy®, an aluminum-magnesium-scandium alloy developed specifically for AM, pushes the boundaries further, delivering specific strength comparable to high-grade aluminum alloys and even some titanium grades, along with exceptional fatigue resistance – critical for components subjected to constant vibration. Ledande metal powder suppliers, like Met3dp, leverage advanced production techniques such as Gas Atomization and Plasma Rotating Electrode Process (PREP) to ensure the high sphericity, flowability, and purity required for printing dense, high-quality parts with these materials, underpinning the reliability demanded in flyg- och rymdteknik and B2B supply chains. This blog post will delve into the specifics of using metal AM, particularly with AlSi10Mg and Scalmalloy®, to produce superior antenna brackets for diverse UAV applications, exploring the benefits, design considerations, material properties, and how to partner with the right metal 3D printing service provider.
Applications and Use Cases: Where are 3D Printed Antenna Brackets Deployed?
The versatility of metal additive manufacturing allows for the creation of custom antenna brackets tailored to the unique demands of various UAV platforms and their specific operational environments. The ability to optimize design for weight, strength, and RF transparency makes 3D printed brackets highly desirable across the entire spectrum of unmanned aerial systems. Procurement managers sourcing parts for diverse drone fleets and engineers designing next-generation platforms can leverage AM to address specific challenges and enhance capabilities.
UAV Platform Types Benefiting from AM Brackets:
- Fixed-Wing UAVs: Often used for long-endurance surveillance, mapping, and reconnaissance missions (ISR), these platforms benefit significantly from weight reduction provided by AM brackets. Optimized bracket designs can seamlessly integrate antennas into the wings or fuselage, minimizing aerodynamic drag while ensuring robust mounting for potentially larger or more complex antenna arrays required for long-range communication or sophisticated sensor suites. B2B suppliers focusing on defense additive manufacturing find significant demand here.
- Multirotor UAVs (Quadcopters, Hexacopters, Octocopters): These platforms are ubiquitous in commercial applications like aerial photography, infrastructure inspection, and public safety. Flight time is often a critical limiting factor. Lightweight AM antenna brackets, often utilizing topology optimization, directly contribute to longer flight endurance or increased payload capacity (e.g., higher resolution cameras, additional sensors). The ability to create complex shapes allows for optimal antenna placement away from rotor downwash and electromagnetic interference (EMI) from motors, crucial for stable data links during close-proximity inspections or dynamic flight maneuvers. Commercial drone components suppliers see high volume potential in this segment.
- Vertical Take-Off and Landing (VTOL) UAVs: Combining the endurance of fixed-wing aircraft with the operational flexibility of multirotors, VTOLs often feature complex designs transitioning between flight modes. AM allows for the creation of brackets that can withstand the unique stresses of transition phases and integrate antennas effectively within hybrid airframes. Custom brackets can support multiple antennas required for diverse communication needs (e.g., satellite communication, line-of-sight data links, GPS) on these versatile platforms.
Industry-Specific Applications Driving Demand:
- Flyg- och rymdindustrin samt försvarsindustrin: This sector represents a primary driver for high-performance AM components.
- ISR Platforms: Require brackets for secure mounting of sensitive SIGINT (Signals Intelligence) or COMINT (Communications Intelligence) antennas, often demanding specific non-conductive or RF-transparent properties achievable through careful material selection and design, potentially incorporating non-metallic AM components alongside metal brackets. Lightweighting is paramount for maximizing operational range and time-on-station.
- Tactical Communication Drones: Need robust brackets capable of withstanding harsh battlefield conditions, vibrations, and potential impacts. Scalmalloy®’s high strength and fatigue resistance are particularly valuable here. Part consolidation through AM reduces potential failure points. Reliable drone parts suppliers with AS9100 certification are essential for this market.
- Target Drones & Swarms: Cost-effective production methods and rapid iteration capabilities of AM are beneficial for manufacturing brackets for expendable or numerous drone platforms.
- Commercial Operations: The commercial drone market is rapidly expanding, creating diverse needs for specialized components.
- Delivery Drones: Require extremely reliable communication links for navigation and control in urban or complex environments. Brackets must be durable for frequent takeoff/landing cycles and lightweight to maximize cargo capacity. Wholesale UAV brackets manufactured via AM offer scalability for growing delivery fleets.
- Infrastructure Inspection (Energy, Utilities, Construction): Drones operating near power lines, wind turbines, or communication towers need precisely positioned antennas with brackets that minimize RF interference. AM allows for custom shapes to fit specific sensor payloads and inspection requirements.
- Precision Agriculture: UAVs mapping fields or monitoring crop health require reliable GPS and data link antennas. Lightweight brackets enhance flight time over large agricultural areas. AM allows for brackets that integrate weather-resistant features.
- Mapping and Surveying: High-accuracy GPS/GNSS antenna mounting is critical. AM can create rigid, stable brackets that maintain antenna orientation for precise georeferencing.
- Forskning och utveckling: Academic institutions and R&D organizations utilize AM for creating brackets for experimental UAV platforms.
- Custom Sensor Integration: Researchers developing novel sensors or communication systems need custom brackets to mount prototype antennas onto testbed drones. AM provides the speed and flexibility for rapid iteration.
- Atmospheric Monitoring & Environmental Science: UAVs carrying sensitive instruments require brackets designed to minimize vibration and environmental impact on measurements.
Functional Requirements Addressed by Additive Manufacturing:
Beyond simple mounting, 3D printed antenna brackets address complex functional needs:
- Optimized RF Performance: AM enables designs with smooth contours, specific dielectric properties (if combined with non-metallic printing), and precise positioning to minimize signal blockage, reflections, or passive intermodulation (PIM), especially critical for sensitive receiver antennas.
- Complex Geometric Integration: Brackets can be designed to conform perfectly to curved UAV fuselages or integrate mounting points for associated cabling and electronics, reducing overall system complexity.
- Vibration Damping: Incorporating lattice structures or utilizing materials with inherent damping properties can help isolate the antenna from airframe vibrations, improving signal stability and reducing mechanical fatigue on the antenna itself.
- Termisk hantering: For antennas integrated with electronics that generate heat, brackets made from materials like AlSi10Mg with good thermal conductivity can act as heat sinks, improving the reliability of the electronics package.
The diverse range of applications underscores the need for adaptable and high-performance manufacturing solutions. Metal AM provides the design freedom and material choices necessary to meet these varied requirements, making it an increasingly essential technology for engineers and procurement specialists in the rapidly evolving UAV industry. Partnering with an experienced additive manufacturing partner like Met3dp, which understands both the materials and the application demands, is key to unlocking these benefits.
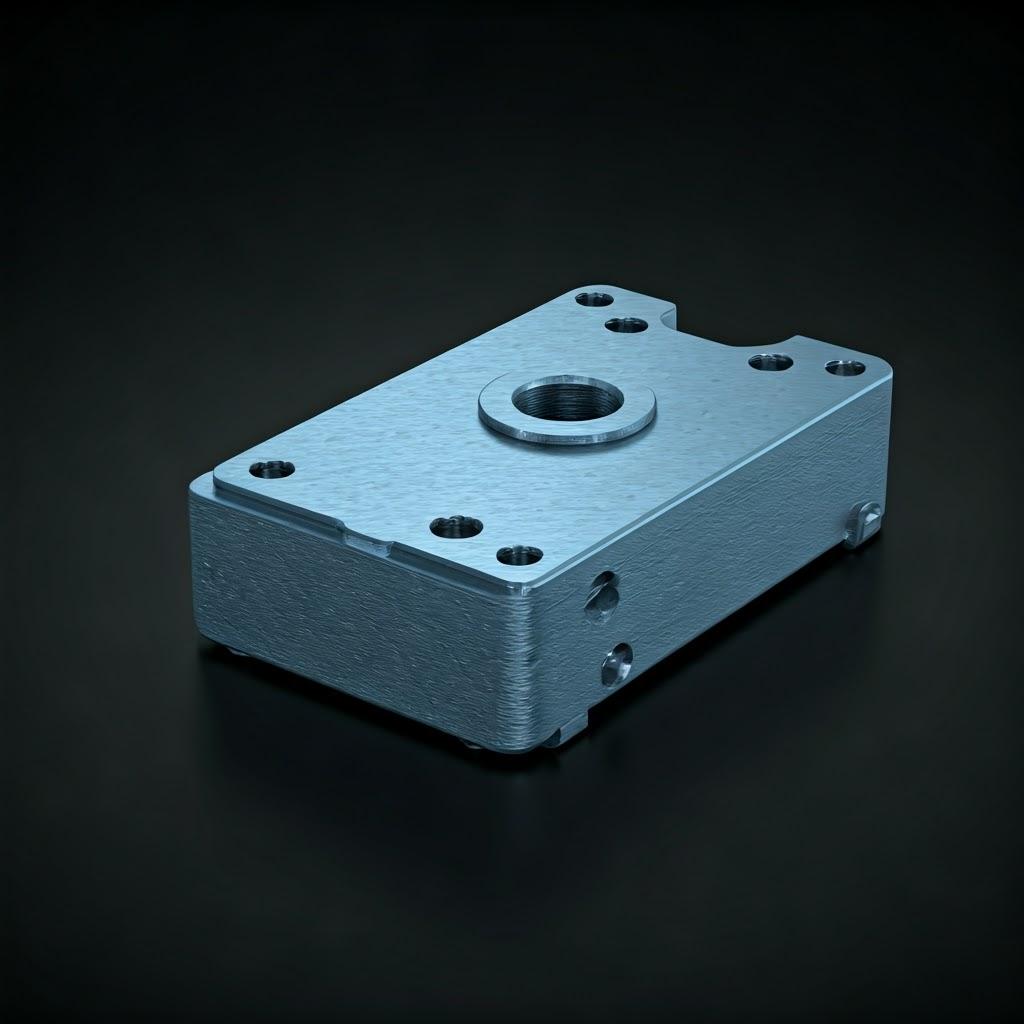
Why Metal 3D Printing for UAV Antenna Brackets?: Key Advantages Over Traditional Methods
While traditional manufacturing methods like CNC machining, sheet metal fabrication, and casting have long been used to produce aircraft components, metal additive manufacturing offers a compelling suite of advantages specifically suited to the demands of modern UAV antenna brackets. For B2B buyers, industriella 3D-utskriftslösningar providers, and engineers aiming for peak performance, understanding these benefits is critical for making informed manufacturing choices. The limitations of traditional methods often become bottlenecks when striving for the lightweight, complex, and highly integrated designs that optimize UAV performance.
Comparison with Traditional Manufacturing:
- CNC Machining:
- Process: Subtractive method, starting with a solid block or billet of metal and removing material using cutting tools.
- Fördelar: High precision, excellent surface finish, wide range of materials.
- Cons for UAV Brackets: Can be wasteful (high buy-to-fly ratio), struggles with complex internal features or highly organic shapes optimal for weight reduction (like lattices or topology optimization), potentially longer lead times for complex parts due to programming and setup, tooling costs for fixtures.
- Sheet Metal Fabrication:
- Process: Cutting, bending, and joining sheets of metal.
- Fördelar: Generally cost-effective for simpler bracket designs, good for producing thin-walled structures.
- Cons for UAV Brackets: Limited geometric complexity, difficulty achieving high stiffness-to-weight ratios compared to optimized 3D shapes, joins/welds can be points of weakness or fatigue, less suitable for highly integrated or load-bearing brackets.
- Casting:
- Process: Pouring molten metal into a mold.
- Fördelar: Good for high-volume production of complex shapes, relatively low part cost at scale.
- Cons for UAV Brackets: High initial tooling costs and long lead times for molds, limitations on wall thickness and feature detail, potential for porosity if not controlled, less design flexibility for iteration, material property limitations compared to wrought or AM materials.
Key Advantages of Metal Additive Manufacturing (LPBF):
Metal AM, particularly Laser Powder Bed Fusion (LPBF) – a core technology utilized by providers like Met3dp – overcomes many limitations of traditional methods, offering significant advantages for UAV antenna brackets:
- Unmatched Weight Reduction: This is arguably the most significant benefit for any airborne component.
- Topology Optimization: Software algorithms can analyze the stress distribution within a bracket design and remove material from low-stress regions, creating highly efficient, organic-looking structures that maintain strength only where needed. This can lead to weight savings of 30-60% or even more compared to traditionally designed brackets, directly translating to longer flight times, increased payload capacity, or improved agility.
- Gitterstrukturer: AM allows the incorporation of internal lattice structures (honeycombs, gyroids, etc.) which drastically reduce material usage and weight while maintaining structural integrity and potentially adding other functionalities like vibration damping. This is virtually impossible to achieve with CNC machining.
- Result: Lighter UAVs fly longer, carry more, or perform more dynamically – a critical competitive advantage sourced through advanced aerospace parts manufacturing tekniker.
- Exceptional Design Freedom: AM liberates engineers from the constraints of traditional manufacturing processes (“Design for Manufacturability”).
- Komplexa geometrier: Create intricate shapes optimized for RF performance (e.g., smooth curves to reduce reflections), aerodynamic efficiency (conformal mounting), or integration with other components. Brackets can feature internal channels for cable routing or conformal cooling if needed.
- Anpassning: Easily produce unique bracket designs tailored to specific antenna types, UAV models, or mission requirements without the need for expensive tooling changes. This is ideal for the diverse and rapidly evolving UAV market.
- Result: Highly optimized brackets that perform better electronically and mechanically, fitting seamlessly into compact UAV airframes. Enables true custom antenna bracket manufacturing.
- Del Konsolidering: A single, complex AM part can often replace an assembly of multiple simpler parts previously joined by fasteners or welding.
- Reduced Part Count: Simplifies inventory management, assembly processes, and quality control.
- Increased Reliability: Eliminates potential failure points associated with joints, welds, and fasteners (e.g., loosening due to vibration).
- Weight Savings: Reduces the need for heavy fasteners (screws, bolts, rivets).
- Result: More reliable, lighter, and easier-to-assemble UAV systems, a key benefit for B2B additive manufacturing partnerships focused on efficiency.
- Rapid Prototyping and Accelerated Iteration: AM excels in quickly turning digital designs into physical parts.
- Hastighet: Move from CAD model to functional metal prototype in days rather than weeks or months associated with tooling for casting or complex CNC setups.
- Flexibilitet: Easily modify designs based on testing feedback (e.g., adjusting mounting points, improving stiffness) and print new iterations quickly.
- Result: Faster development cycles for new UAV platforms and antenna systems, allowing companies to innovate and respond to market needs more rapidly. Critical for competitive rapid prototyping aerospace behov.
- On-Demand Production & Supply Chain Flexibility: AM supports distributed manufacturing and production based on actual demand.
- Low-to-Mid Volume Viability: Economically produce specialized brackets in quantities that might not justify the tooling costs of casting or the setup time of complex machining. Ideal for custom UAVs or initial production runs.
- Reducerad lagerhållning: Manufacture parts as needed (“digital inventory”), reducing warehousing costs and the risk of obsolescence for procurement metal parts strategies.
- Decentralized Manufacturing: Potential to print parts closer to the point of need, shortening supply chains (though quality control remains paramount).
- Result: More agile and resilient supply chains, better suited to the fluctuating demands of the UAV market and offering advantages for wholesale UAV components distribution.
While AM may have higher initial part costs compared to simple machined or sheet metal parts in some cases, a total cost of ownership analysis often reveals significant savings through weight reduction (fuel/energy savings, increased revenue potential), reduced assembly time, improved reliability, and accelerated development cycles. Partnering with a knowledgeable metal 3D printing service provider like Met3dp, equipped with industry-leading printers ensuring accuracy and reliability, allows businesses to fully leverage these advantages for their UAV antenna bracket needs.
Recommended Materials Deep Dive: AlSi10Mg vs. Scalmalloy® for UAV Brackets
The choice of material is fundamental to the success of any engineering component, and this holds especially true for UAV antenna brackets where performance, weight, and environmental resistance are paramount. Metal additive manufacturing offers a growing portfolio of materials, but for lightweight structural applications in drones, aluminum alloys are often the prime candidates. Met3dp, with its deep expertise in metallpulver development and manufacturing using advanced Gas Atomization and PREP technologies, ensures the availability of high-quality, highly spherical powders crucial for achieving optimal results in the AM process. Our focus on powder characteristics like flowability, particle size distribution, and purity translates directly into denser, stronger, and more reliable printed parts for our B2B clients. For UAV antenna brackets, two aluminum alloys stand out: the workhorse AlSi10Mg and the high-performance Scalmalloy®.
Understanding Metal Powders for Additive Manufacturing:
Before diving into the specific alloys, it’s essential to appreciate why powder quality matters so much in Laser Powder Bed Fusion (LPBF), the most common AM process for these materials.
- Sfäricitet och flytbarhet: Highly spherical powder particles ensure uniform spreading across the build platform by the recoater blade. Poor flowability can lead to uneven layers, voids, and defects in the final part. Met3dp’s atomization processes are optimized for high sphericity.
- Fördelning av partikelstorlek (PSD): A controlled PSD ensures good powder bed density, which correlates with the density and mechanical properties of the printed part. Too many fine particles can pose handling risks and affect flow, while too many large particles can hinder melt pool consolidation.
- Purity & Low Oxygen Content: Contaminants and excessive oxygen can lead to embrittlement and porosity, compromising the mechanical integrity and fatigue life of the component. Met3dp employs strict quality control throughout its powder production.
Material Profile: AlSi10Mg
AlSi10Mg is one of the most widely used aluminum alloys in additive manufacturing, essentially an AM-adapted casting alloy known for its excellent printability and balanced properties.
- Sammansättning: Primarily aluminum, with significant additions of Silicon (Si, ~9-11%) and Magnesium (Mg, ~0.2-0.45%). Silicon improves fluidity in the melt pool (enhancing printability) and strength, while Magnesium allows for precipitation hardening through heat treatment (T6 condition).
- Viktiga egenskaper:
- Bra förhållande mellan styrka och vikt: Offers respectable strength after heat treatment, suitable for many structural applications where weight is a concern.
- Utmärkt värmeledningsförmåga: Beneficial if the bracket needs to dissipate heat from adjacent electronics or the antenna itself.
- Bra tryckbarhet: Relatively easy to process using LPBF, with well-understood parameter sets available. Less prone to cracking during printing compared to some other high-strength aluminum alloys.
- God korrosionsbeständighet: Exhibits decent resistance to atmospheric corrosion.
- Kostnadseffektivitet: Generally more affordable than higher-performance alloys like Scalmalloy® or titanium.
- Ideal Use Cases for UAV Antenna Brackets:
- General-purpose commercial or research UAVs where moderate strength is sufficient.
- Applications where cost is a major driver.
- Brackets where thermal dissipation is a required function.
- Prototypes and initial design iterations before potentially moving to a higher-performance material.
- Platforms operating in less demanding environmental or vibration conditions.
- Tillgänglighet: Widely available from reputable metal powder suppliers som Met3dp, ensuring a stable supply chain for B2B manufacturing needs. Procurement managers can rely on established sources for this common AM material.
Material Profile: Scalmalloy®
Scalmalloy® is a patented high-performance aluminum-magnesium-scandium (Al-Mg-Sc) alloy specifically developed by APWorks (an Airbus subsidiary) for the demanding requirements of additive manufacturing in the aerospace industry.
- Sammansättning: Aluminum alloyed with Magnesium (Mg) and Scandium (Sc), along with minor additions of Zirconium (Zr). The Scandium addition is key, forming nano-scale Al3Sc precipitates during heat treatment, which provide significant strengthening effects.
- Viktiga egenskaper:
- Very High Specific Strength: Its strength-to-weight ratio rivals that of high-strength 7xxx series aluminum alloys and is comparable to some titanium alloys (like Ti-6Al-4V) at a significantly lower density. This is its standout feature.
- Excellent Ductility & Fatigue Resistance: Unlike many other high-strength aluminum alloys, Scalmalloy® retains good ductility and exhibits superior fatigue performance, making it ideal for parts subjected to cyclic loading and vibration – a common condition for UAV components.
- Good Weldability/Printability: Designed specifically for AM processes like LPBF, exhibiting good processability.
- Motståndskraft mot korrosion: Offers good corrosion resistance, suitable for typical aerospace and UAV operating environments.
- Microstructure Stability at Elevated Temperatures: Maintains properties better at moderately elevated temperatures compared to conventional aluminum alloys.
- Ideal Use Cases for UAV Antenna Brackets:
- High-performance military, aerospace, or commercial UAVs where minimizing weight while maximizing strength is absolutely critical.
- Brackets subjected to high vibrations or significant cyclic loading.
- Applications requiring the highest possible payload capacity or flight endurance.
- Components operating in more demanding environmental conditions.
- Replacing heavier titanium or complex machined aluminum components for significant weight savings.
- Sourcing Considerations: As a patented alloy, sourcing Scalmalloy® powder requires procurement through licensed suppliers. While potentially higher cost than AlSi10Mg, the performance benefits often justify the investment for demanding applications. Ensuring your chosen leverantör av additiv tillverkning has proven experience and validated process parameters for Scalmalloy® is crucial.
Comparative Analysis:
Funktion | AlSi10Mg (Heat Treated – T6) | Scalmalloy® (Heat Treated) | Significance for UAV Antenna Brackets |
---|---|---|---|
Täthet | ~ 2.67 g/cm³ | ~ 2.66 g/cm³ | Very similar, both offer significant weight savings over steel or titanium. |
Utbyteshållfasthet | ~ 230-290 MPa | ~ 480-520 MPa | Scalmalloy® is significantly stronger (~70-100%+). |
Slutlig draghållfasthet | ~ 330-430 MPa | ~ 520-540 MPa | Scalmalloy® offers higher ultimate strength. |
Specifik styrka | Bra | Excellent (Comparable to Ti-6Al-4V) | Scalmalloy® allows for much lighter designs for the same strength requirement. |
Elongation (Ductility) | ~ 6-10% | ~ 13-19% | Scalmalloy® is significantly more ductile, better for impact/fatigue. |
Utmattningshållfasthet | Måttlig | Utmärkt | Crucial advantage for Scalmalloy® in high-vibration UAV environments. |
Termisk konduktivitet | Good (~130-150 W/m·K) | Moderate (~110-120 W/m·K) | AlSi10Mg is slightly better if heat dissipation is a primary function. |
Utskriftsmöjlighet | Utmärkt | Bra | Both are well-suited for LPBF, AlSi10Mg might be slightly more forgiving. |
Motståndskraft mot korrosion | Bra | Bra | Both suitable for typical atmospheric exposure; consider coatings for harsh environments. |
Relativ kostnad | Lägre | Högre | Significant factor for procurement and project budget considerations. |
Export to Sheets
Att göra ett val:
The selection between AlSi10Mg and Scalmalloy® depends heavily on the specific requirements of the UAV and its mission profile:
- Välja AlSi10Mg when:
- Cost is a primary constraint.
- Moderate strength is sufficient for the application.
- Thermal conductivity is a desirable secondary function.
- The operating environment involves lower levels of vibration or cyclic stress.
- Välja Scalmalloy® -legering when:
- Maximum strength-to-weight ratio is the top priority (maximizing endurance/payload).
- High fatigue resistance is critical due to significant vibration or cyclic loading.
- The bracket is a mission-critical structural component requiring the highest reliability.
- Replacing heavier materials like titanium or steel is the goal.
- The budget accommodates a higher-performance material.
Partnering with an additive manufacturing expert like Met3dp provides access not only to high-quality powders but also to the application engineering support needed to select the optimal material and develop robust printing processes for your specific UAV antenna bracket requirements. Our understanding of both materials science and 3D-utskrift av metall processes ensures that B2B customers receive components that meet stringent performance criteria.
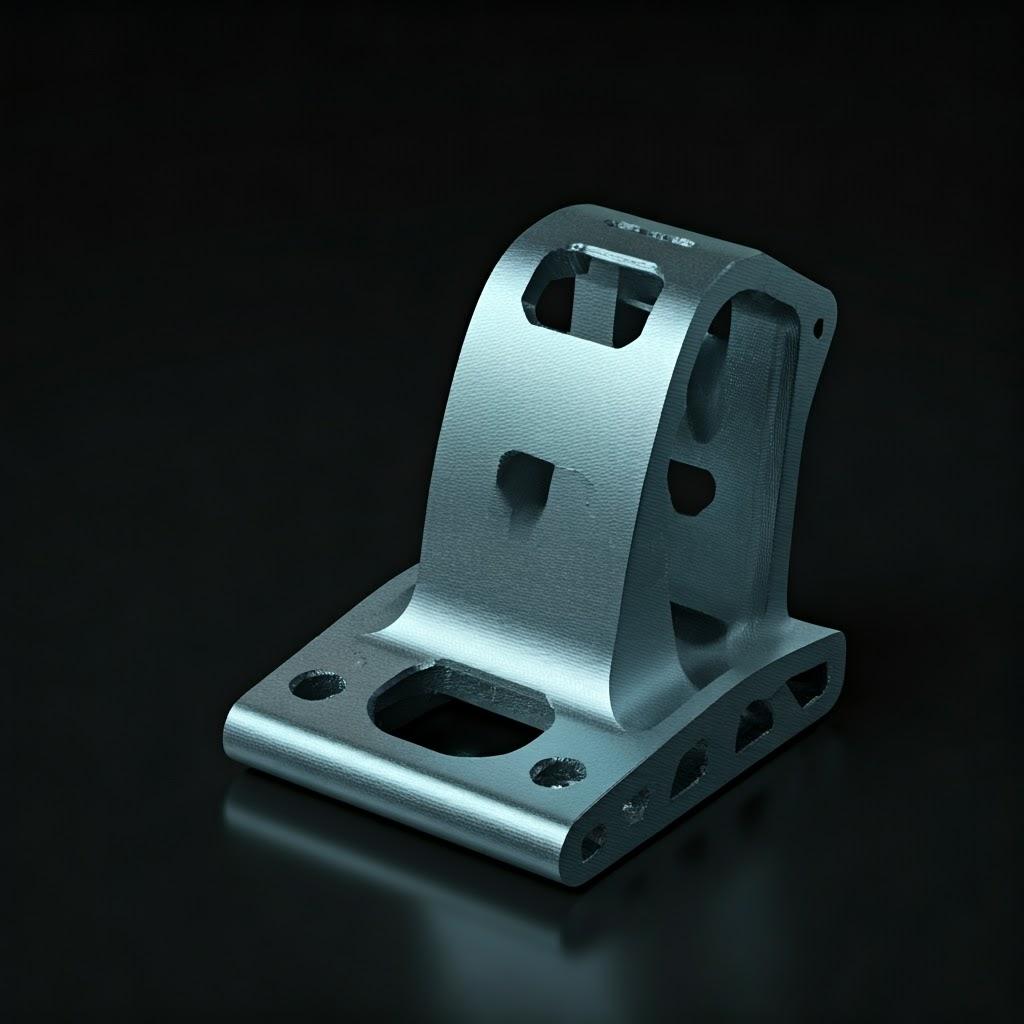
Design for Additive Manufacturing (DfAM): Optimizing UAV Antenna Brackets
Simply replicating a design intended for CNC machining or casting using metal additive manufacturing rarely unlocks the full potential of the technology. To truly leverage the benefits of weight reduction, part consolidation, and performance enhancement offered by AM, engineers must embrace Design för additiv tillverkning (DfAM) principles. DfAM isn’t just a suggestion; it’s a fundamental shift in design thinking required to create successful, cost-effective, and high-performance 3D printed components like UAV antenna brackets. For B2B clients and industriella 3D-utskriftslösningar providers, implementing DfAM effectively is key to maximizing the return on investment in AM technology. Failing to consider DfAM principles early in the design cycle can lead to print failures, excessive post-processing requirements, suboptimal performance, and unnecessarily high costs. Partnering with an AM expert like Met3dp, whose engineers understand DfAM intricacies for materials like AlSi10Mg and Scalmalloy®, can significantly streamline this process and ensure first-time-right manufacturing.
Core DfAM Strategies for UAV Antenna Brackets:
- Topology Optimization: Designing for Lightweight Strength
- Concept: Topology optimization (TO) software uses Finite Element Analysis (FEA) to mathematically determine the most efficient material distribution within a defined design space, subject to specific load cases, constraints (e.g., mounting points, keep-out zones for antenna elements), and performance objectives (e.g., minimize weight, maximize stiffness).
- Workflow:
- Define the maximum allowable design volume (the “space claim”).
- Specify fixed points (e.g., bolt holes for mounting to the airframe, antenna interface points).
- Apply realistic load conditions (e.g., vibration profiles based on UAV operational data, static loads from antenna weight, potential G-forces during maneuvers).
- Define manufacturing constraints (e.g., minimum member size printable by the LPBF process).
- Set the optimization goal (typically minimizing mass while meeting stiffness or stress targets).
- Produktion: The software generates an organic, often bone-like structure that represents the optimal load paths. This raw output usually requires some smoothing and interpretation by the designer to ensure manufacturability and incorporate other design features.
- Benefit for UAV Brackets: Achieves dramatic weight reductions (often 30-60%+) compared to traditional designs, directly improving flight endurance and payload capacity. Ensures structural integrity precisely where needed to maintain antenna pointing accuracy under load. Requires expertise in both structural analysis and AM limitations.
- Lattice Structures: Internal Weight Reduction and Functionality
- Concept: Replacing solid sections of a part with internal, repeating unit cells (lattices) can further reduce weight and material consumption beyond what topology optimization alone might achieve. Different lattice types offer varying properties.
- Types & Benefits:
- Strut-based lattices (e.g., cubic, octet-truss): Good for high stiffness-to-weight ratios.
- Surface-based lattices (TPMS – Triply Periodic Minimal Surfaces, e.g., Gyroid, Schwarz P): Offer smooth surfaces, good manufacturability (often self-supporting), and potential benefits for stress distribution, fluid flow (if applicable), or vibration damping.
- Application in Brackets: Can be used strategically within thicker sections identified by topology optimization or to fill volumes where solid material isn’t structurally necessary but enclosed geometry is desired. Can potentially help dampen vibrations transmitted from the airframe to the antenna.
- Överväganden: Kräver specialiserad lattice structure design software. Ensuring powder removal from internal lattice structures is crucial and must be planned during design (e.g., including drain holes). Requires careful analysis to ensure the lattice provides the required mechanical performance.
- Minimum Feature Size & Wall Thickness: Respecting Process Limits
- LPBF Physics: The Laser Powder Bed Fusion process involves melting fine metal powder with a laser beam. The size of the melt pool, laser spot size, and powder particle size dictate the smallest stable features that can be reliably produced.
- Typical Guidelines (AlSi10Mg/Scalmalloy®):
- Minimum Wall Thickness: Generally around 0.4mm – 0.8mm, depending on the wall height and orientation. Thinner walls might warp or fail to form completely.
- Minimum Feature Size (e.g., pins, holes): Small positive features (pins) might need to be slightly larger (e.g., >0.5mm diameter) than small negative features (holes). Very small holes (<0.5mm) can be difficult to print reliably and may be sealed by powder.
- Aspect Ratios: Tall, thin walls can be prone to distortion or failure during printing.
- Importance: Designing below these limits risks print failure or parts that don’t meet dimensional or strength requirements. Consulting the specific guidelines of the metal 3D printing service provider (like Met3dp) and their machine capabilities is essential.
- Support Structure Strategy: Designing for Printability and Removal
- Why Supports?: In LPBF, overhangs and horizontal surfaces require support structures underneath them. These structures anchor the part to the build plate, prevent warping due to thermal stress, and provide a surface for down-facing features to be built upon. They are sacrificial and removed after printing.
- DfAM for Supports:
- Minimera överhäng: Design parts with self-supporting angles where possible. For aluminum alloys like AlSi10Mg and Scalmalloy®, angles greater than ~45 degrees from the horizontal typically require support. Designing features with chamfers or fillets instead of sharp overhangs can reduce support needs.
- Optimize Part Orientation: Choose a build orientation that minimizes the total volume of required supports, especially on critical or cosmetic surfaces. (See next point).
- Support Accessibility: Ensure support structures can be physically reached and removed without damaging the part. Avoid designs with deep, inaccessible internal cavities requiring support.
- Support Type Selection: Choose appropriate support types (e.g., solid block, thin lines, conical/tree supports) based on the feature being supported and ease of removal. Met3dp utilizes advanced software to generate optimized support strategies.
- Contact Points: Minimize the contact area between the support and the part surface to ease removal and reduce surface scarring (witness marks).
- Påverkan: Poor support strategy leads to difficult/costly post-processing, potential part damage during removal, and compromised surface finish. Effective DfAM significantly reduces these issues.
- Part Orientation: Balancing Competing Factors
- The Decision: How a part is oriented on the build plate significantly impacts several factors. The optimal orientation is often a trade-off.
- Factors Influenced by Orientation:
- Stödstrukturer: Directly affects the amount and location of supports needed.
- Ytfinish: Upward-facing surfaces generally have the best finish, while downward-facing surfaces (supported) have the roughest finish. Vertical walls are intermediate. Critical surfaces should ideally be oriented upwards or vertically.
- Byggtid: Primarily determined by the height of the part in the build direction (Z-axis). Orienting the shortest dimension vertically reduces print time.
- Mekaniska egenskaper: AM parts can exhibit some anisotropy (properties varying slightly with direction) due to the layer-wise build process. Orientation can be chosen to align the strongest direction with the primary load path, although this effect is less pronounced in well-optimized aluminum prints compared to some other materials or processes.
- Thermal Stress & Warping: Orientation can influence heat distribution and the tendency to warp.
- Strategy: Collaborate with your AM provider. Use their expertise and simulation tools to determine the best orientation that balances printability, surface quality requirements, mechanical performance, and cost (build time, support removal). Explore different options early in the design phase.
Effective DfAM is a collaborative process between the designer and the 3D-utskrift av metall service provider. By considering these principles from the outset, engineers designing UAV antenna brackets can fully exploit the advantages of additive manufacturing, resulting in lighter, stronger, more integrated, and ultimately more effective components for demanding aerospace applications.
Achievable Tolerances, Surface Finish, and Dimensional Accuracy
For engineers and procurement managers specifying components like UAV antenna brackets, understanding the achievable precision of metal additive manufacturing is crucial. While AM offers incredible design freedom, it’s not inherently as precise as high-tolerance CNC machining in its as-printed state. Managing expectations and knowing when and where secondary processing might be needed is key to successful implementation. Factors like the specific AM process (LPBF in this case), machine calibration, material properties, part geometry, and post-processing all influence the final tolerances, surface finish, and dimensional accuracy. Leading providers like Met3dp invest heavily in machine calibration, process monitoring, and quality control to deliver consistent and accurate parts within the technology’s capabilities.
Tolerances in Metal Additive Manufacturing (LPBF):
- General Standards: Tolerances for metal AM parts are often discussed in relation to general tolerance standards like ISO 2768 (medium ‘m’ or fine ‘f’ classes) or specific aerospace standards.
- Typical Achievable Tolerances (As-Printed):
- General Linear Dimensions: For well-designed and processed parts using LPBF with AlSi10Mg or Scalmalloy®, typical achievable tolerances are often in the range of ±0.1mm to ±0.3mm for smaller features (e.g., up to 50-100mm), potentially increasing slightly for larger dimensions (e.g., ±0.2% of the nominal dimension).
- Hole Diameters/Positions: Accuracy depends on size and orientation. Small vertical holes might be slightly undersized as-printed. Positional accuracy is generally good but subject to the overall part tolerance.
- Flatness/Parallelism: Large, flat surfaces can be challenging due to potential warping during the print and stress relief cycles. Tolerances might be in the range of 0.1mm – 0.5mm per 100mm, depending heavily on geometry and support strategy.
- Factors Influencing Tolerances:
- Machine Calibration: Regular calibration of the laser scanner system, Z-axis movement, and build platform leveling is critical. Met3dp prioritizes meticulous machine maintenance and calibration for optimal metal 3D printing accuracy.
- Process Parameters: Laser power, scan speed, layer thickness, and scan strategy significantly impact melt pool stability and thus dimensional accuracy. Validated parameters are essential.
- Thermal Stresses: Uneven heating and cooling can cause internal stresses leading to distortion during printing or after removal from the build plate. Simulation tools can help predict and mitigate this.
- Material Shrinkage: Materials shrink upon solidification and cooling; this is compensated for in the build preparation software, but residual effects can remain.
- Stödstrukturer: How the part is supported can influence its final geometry after removal and stress relief.
- Delgeometri: Complex shapes, thin walls, and large flat areas are inherently more challenging to hold tight tolerances on.
Surface Finish (Roughness – Ra):
Surface finish is another critical aspect, affecting aesthetics, fatigue life, friction, and potentially RF performance at very high frequencies. LPBF produces parts with a characteristic surface texture resulting from the layered melting of powder particles.
- Typical As-Printed Ra Values (AlSi10Mg/Scalmalloy®):
- Vertical Walls (XY Plane): Generally offer a relatively good finish, perhaps Ra 6 µm – 15 µm.
- Upward-Facing Surfaces (Top surfaces): Typically the smoothest, potentially Ra 5 µm – 12 µm, depending on parameters and lack of support contact.
- Downward-Facing Surfaces (Supported): Usually the roughest due to contact with support structures. Ra can range from 15 µm to 30 µm or more, depending on support type and removal care. Steeper overhang angles approaching the self-supporting limit also tend to be rougher.
- Förbättra ytfinishen: As-printed finishes are often suitable for non-critical surfaces. However, if smoother finishes are required for aesthetics, fatigue performance (reducing stress concentrators), or specific functional requirements (e.g., sealing surfaces, RF waveguides), post-processing is necessary. Common methods include:
- Bead Blasting / Sand Blasting: Provides a uniform matte finish, typically improving Ra slightly and removing partially melted particles. Ra values might reach 5 µm – 10 µm.
- Tumbling / Vibratory Finishing: Uses abrasive media in a rotating or vibrating bowl. Best for smaller, simpler parts; can smooth edges and surfaces but may struggle with complex internal features.
- Polering: Manual or automated polishing can achieve very smooth, mirror-like finishes (Ra < 1 µm) but is labor-intensive and typically applied only to specific areas.
- Maskinbearbetning: Provides the best control over surface finish and accuracy on specific features.
Dimensional Accuracy and Quality Control:
Ensuring the final bracket meets specifications requires robust quality control processes.
- Defining Critical Dimensions: Engineers must clearly identify critical dimensions, tolerances, and surface finish requirements on drawings or 3D model annotations (PMI – Product Manufacturing Information). Not every dimension needs the tightest tolerance.
- Metrology Methods: Reputable suppliers use various inspection tools:
- Calipers & Micrometers: For basic dimensional checks.
- Coordinate Measuring Machines (CMM): Provide high-accuracy measurements of complex geometries and GD&T (Geometric Dimensioning and Tolerancing) features. Essential for dimensional inspection CMM of critical parts.
- 3D Scanning (Laser or Structured Light): Captures the full geometry of the part, allowing comparison to the original CAD model (part-to-CAD comparison) and generating color maps of deviations. Excellent for verifying complex shapes produced by topology optimization.
- Process Monitoring: Advanced AM systems incorporate in-situ monitoring (e.g., melt pool monitoring, thermal imaging) to detect potential anomalies during the build, providing another layer of quality assurance.
Managing Expectations:
It’s crucial for procurement teams and engineers to understand that achieving tolerances comparable to precision machining (e.g., ±0.01mm) directly from the AM process is generally unrealistic. A hybrid approach is often optimal: leverage AM for complex geometry and lightweighting, then use targeted CNC machining for critical interfaces, mounting holes, or surfaces requiring very tight tolerances or specific finishes. Discussing requirements clearly with your AM provider like Met3dp early on allows for a manufacturing plan that balances cost, lead time, and the required level of precision for your UAV antenna bracket.
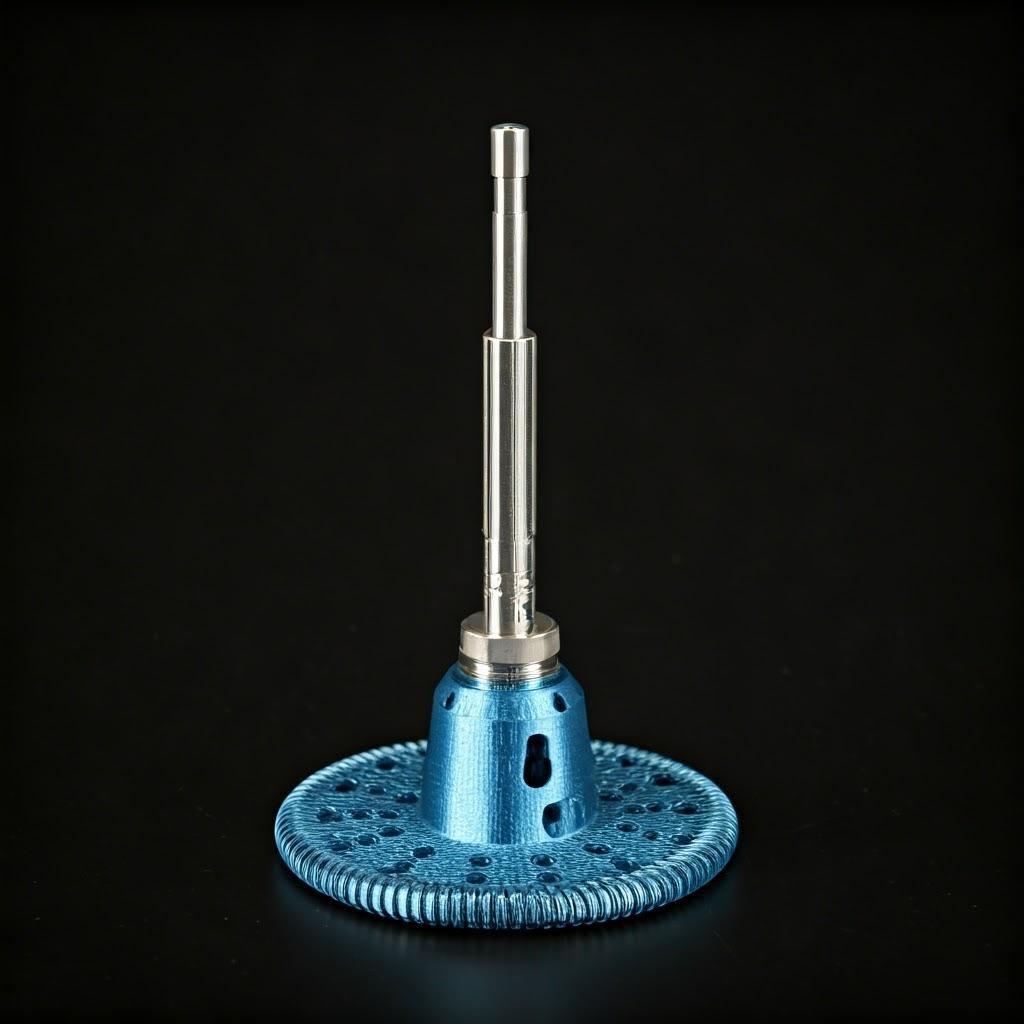
Essential Post-Processing Steps for UAV Antenna Brackets
Additive manufacturing, particularly LPBF, is rarely a single-step process. The “print” itself is just one stage in producing a functional, end-use component like a UAV antenna bracket. Post-processing steps are almost always required to transform the as-printed part into a finished product meeting all engineering requirements. Understanding these steps is vital for accurate cost estimation, lead time planning, and ensuring the final part performs as expected. B2B suppliers and manufacturers like Met3dp often offer integrated post-processing services, providing a streamlined workflow from digital file to finished component. Neglecting or underestimating post-processing can lead to parts with suboptimal mechanical properties, poor fit, or premature failure.
Common Post-Processing Stages for AlSi10Mg and Scalmalloy® Brackets:
- Stress Relief / Heat Treatment: This is arguably the most critical post-processing step for load-bearing metal AM parts.
- Why it’s Needed: The rapid heating and cooling cycles inherent in the LPBF process create significant residual stresses within the printed part. These stresses can cause distortion (especially after removal from the build plate), reduce ductility, and negatively impact fatigue life. Heat treatment relieves these stresses and, crucially, develops the final desired microstructure and mechanical properties (strength, ductility, hardness) for the specific alloy.
- Process for AlSi10Mg: Typically involves a solution treatment followed by artificial aging (precipitation hardening) to achieve the T6 condition. This involves heating to a high temperature (e.g., ~530°C) to dissolve alloying elements, quenching, and then aging at a lower temperature (e.g., ~160°C) for several hours to precipitate strengthening phases (Mg2Si). Precise control of temperature and time is critical.
- Process for Scalmalloy®: Also requires specific heat treatment protocols, often involving solutionizing and aging steps optimized to precipitate the strengthening Al3(Sc,Zr) nano-particles. The exact parameters are often proprietary or recommended by the material developer/supplier and must be followed carefully to achieve the alloy’s high-performance characteristics.
- Importance: Stress relief additive manufacturing and subsequent aging are non-negotiable for achieving the datasheet properties of these alloys and ensuring structural reliability in demanding UAV applications.
- Part Removal from Build Plate: Parts are typically printed on a thick metal build plate.
- Metoder: Common methods include wire Electrical Discharge Machining (EDM), sawing, or sometimes CNC milling. Wire EDM is often preferred as it imparts minimal stress on the part.
- Överväganden: Must be done carefully to avoid damaging the part. The removal method may leave a slightly rougher surface on the base of the part that might require further finishing.
- Borttagning av stödstruktur: The sacrificial supports need to be meticulously removed.
- Techniques: This can be a labor-intensive process.
- Manuell borttagning: Supports are often designed with weakened connection points and can sometimes be broken off by hand or with simple tools (pliers, chisels). Requires care to avoid damaging the part surface.
- Maskinbearbetning: CNC machining or manual grinding/milling may be required to remove stubborn supports or achieve a smooth surface where supports were attached.
- Wire EDM: Can sometimes be used for precise removal of internal or hard-to-reach supports.
- Påverkan: Support removal often leaves “witness marks” or slight blemishes on the part surface. The ease and success of removal are heavily dependent on the DfAM strategies employed earlier (accessibility, support type, contact points). This step significantly impacts the overall cost and lead time.
- Techniques: This can be a labor-intensive process.
- Ytbehandling: As-printed surfaces can be rough (as discussed previously) and may require refinement depending on the application.
- Bead Blasting: The most common method for achieving a uniform, matte finish. Uses compressed air to propel fine beads (glass, ceramic) at the surface, removing loose powder and smoothing minor imperfections. Different media and pressures create different finishes.
- Tumbling/Vibratory Finishing: Suitable for batch processing of smaller parts, using abrasive media to smooth surfaces and round edges. Less effective for large or complex parts with internal features.
- Polering: Manual or automated processes using progressively finer abrasives to achieve smooth (Ra < 1 µm) or mirror finishes. Usually reserved for specific functional areas or aesthetic requirements due to cost.
- Electropolishing: An electrochemical process that removes a thin layer of material, resulting in a very smooth, clean surface. Can be effective for complex shapes but requires specific electrolytes and setup.
- CNC Machining: Often required for critical features demanding tolerances tighter than achievable with as-printed AM.
- Applikationer:
- Mating Interfaces: Ensuring flatness and precise dimensions where the bracket connects to the UAV airframe or the antenna.
- Hole Tolerances & Threading: Machining holes to precise diameters and tolerances, tapping threads for fasteners.
- Critical Dimensions: Achieving specific GD&T requirements (e.g., parallelism, perpendicularity) on certain features.
- Överväganden: Requires careful fixture design to hold the complex AM part securely without distortion. Must account for material removed during machining in the initial AM design. CNC post-processing AM is a common step in producing functional metal parts.
- Applikationer:
- Coating / Anodizing: Applying a surface treatment for enhanced performance or protection.
- Reasons:
- Korrosionsskydd: Especially important for operation in marine or humid environments.
- Motståndskraft mot slitage: For surfaces subject to abrasion.
- Electrical Insulation/Properties: Modifying surface conductivity if required near antenna elements.
- Aesthetics/Color: Applying specific colors.
- Common Options for Aluminum:
- Anodizing (Type II & Type III / Hardcoat): An electrochemical process that grows a durable, corrosion-resistant oxide layer on the aluminum surface. Type III (Hardcoat) is thicker and provides superior wear resistance. Can also be dyed various colors.
- Chromate Conversion Coating (Alodine/Irridite): Provides excellent corrosion resistance and a good base for paint adhesion.
- Painting/Powder Coating: For specific colors or additional environmental protection.
- Reasons:
Integrating these post-processing steps into the overall manufacturing plan is essential. Working with a full-service provider like Met3dp, which understands the entire workflow from powder to finished part, including the nuances of different tryckmetoder and subsequent finishing requirements, ensures a streamlined process and components that meet all specifications for demanding UAV applications.
Common Challenges in 3D Printing Antenna Brackets and Mitigation Strategies
While metal additive manufacturing offers significant advantages, like any advanced manufacturing process, it comes with potential challenges. Awareness of these challenges allows engineers, procurement specialists, and manufacturers to implement mitigation strategies proactively, ensuring successful outcomes for critical components like UAV antenna brackets. An experienced AM partner like Met3dp leverages its deep understanding of materials science, process physics, and quality control—underpinned by high-quality powders from proprietary production methods—to anticipate and overcome these hurdles, delivering reliable parts to its B2B customers.
1. Warping and Residual Stress:
- Utmaning: The rapid heating by the laser and subsequent cooling of the metal powder layer by layer creates significant thermal gradients. This leads to internal stresses building up within the part. These stresses can cause the part to warp or distort during the build, or especially after it’s cut from the build plate and the anchoring effect is removed. Thin features and large, flat sections are particularly susceptible.
- Mitigation Strategies:
- Optimized Part Orientation: Orienting the part to minimize large flat surfaces parallel to the build plate and reduce overall internal stress concentrations.
- Robust Support Structures: Designing effective supports that firmly anchor the part to the build plate, resisting shrinkage forces and conducting heat away more evenly. Met3dp uses simulation tools to optimize support placement and density.
- Optimized Process Parameters: Using validated parameters (laser power, scan speed, hatching strategy) that minimize thermal gradients without compromising density. Pre-heating the build platform can also reduce thermal shock.
- Mandatory Stress Relief: Performing a thermal stress relief cycle immediately after printing and before removing the part from the build plate is crucial for relaxing internal stresses and ensuring dimensional stability.
2. Support Removal Difficulty & Surface Quality:
- Utmaning: Support structures are necessary but can be difficult and time-consuming to remove, especially from complex internal geometries or delicate features. Removal can leave undesirable marks or rough surfaces (“witness marks”) on the part, potentially impacting aesthetics or even fatigue life if located in high-stress areas.
- Mitigation Strategies:
- DfAM for Support Reduction: Designing parts with self-supporting angles (>45°) and features like fillets instead of sharp overhangs minimizes the need for supports in the first place.
- Accessibility Planning: Ensuring during the design phase that all areas requiring support are physically accessible for removal tools. Avoid designing “trapped volumes” needing internal supports that cannot be removed.
- Optimized Support Design: Using specialized support structures (e.g., thin-walled, low-contact-area, tree-like) generated by advanced software, which are designed for easier detachment and minimal surface scarring. Met3dp invests in software and expertise for this.
- Appropriate Removal Techniques: Using the correct tools and techniques (manual breaking, careful machining, EDM) for support removal based on the support type and part geometry.
- Targeted Post-Processing: Planning for secondary finishing operations (e.g., bead blasting, localized grinding or polishing) to address any residual marks on critical surfaces.
3. Porosity (Gas or Lack-of-Fusion):
- Utmaning: Small voids or pores can form within the printed material. Gas porosity arises from gas trapped within the powder or dissolved in the melt pool. Lack-of-fusion porosity occurs when the laser energy isn’t sufficient to fully melt and fuse powder particles or successive layers together. Porosity acts as a stress concentrator, significantly reducing the part’s ductility, fatigue strength, and overall mechanical integrity.
- Mitigation Strategies:
- High-Quality Metal Powder: Using powder with high purity, low trapped gas content, controlled particle size distribution, and excellent flowability is paramount. Met3dp’s investment in advanced Gas Atomization and PREP powder production directly addresses this, ensuring powder quality that minimizes porosity risk.
- Optimized Process Parameters: Rigorously developing and validating LPBF parameters (laser power, scan speed, layer thickness, hatch spacing, focus) for each specific material (AlSi10Mg, Scalmalloy®) to ensure complete melting and fusion. This requires extensive expertise and testing.
- Inert Atmosphere Control: Maintaining a high-purity inert gas atmosphere (e.g., Argon) within the build chamber to minimize oxygen pickup and reactions during melting.
- Quality Control (e.g., Density Checks): Performing density measurements (e.g., using the Archimedes method) or CT scanning on test coupons or critical parts to verify low porosity levels.
4. RF Performance Considerations:
- Utmaning: The antenna bracket, while primarily structural, exists in close proximity to the antenna and operates within its electromagnetic field. The bracket’s material properties, geometry, and even surface finish can potentially impact the antenna’s performance (e.g., signal detuning, absorption loss, passive intermodulation – PIM, pattern distortion).
- Mitigation Strategies:
- Materialval: While AlSi10Mg and Scalmalloy® are conductive, their specific properties are generally well-understood. However, careful consideration during the design phase is needed.
- RF Simulation: Using electromagnetic simulation software early in the design process to model the bracket and antenna together, predicting potential interactions and allowing design modifications (e.g., changing shape, adding cutouts) to minimize negative impacts.
- Geometric Design: Avoiding sharp edges or resonant geometries near antenna elements. Ensuring sufficient clearance between the bracket and radiating parts of the antenna.
- Ytfinish: Very rough surfaces could potentially increase RF losses at higher frequencies, though this is typically a secondary effect for brackets compared to waveguides. Smooth, clean finishes are generally preferred near active antenna regions.
- Consider Non-Conductive Coatings/Materials: If metallic properties are problematic, consider non-conductive coatings or potentially using non-metallic AM materials for certain bracket parts if feasible.
5. Powder Handling and Safety:
- Utmaning: Fine metal powders, especially aluminum alloys, can be reactive and pose fire or explosion hazards if not handled correctly. They also present respiratory hazards if inhaled.
- Mitigation Strategies:
- Strict Safety Protocols: Implementing rigorous procedures for powder loading, unloading, sieving, and disposal, including grounding equipment to prevent static discharge, using appropriate personal protective equipment (PPE) like respirators and gloves.
- Inert Environments: Handling powder in controlled environments, sometimes under inert gas, especially during recycling/sieving operations.
- Supplier Expertise: Partnering with experienced metal powder suppliers and AM service providers like Met3dp who have established safety protocols and trained personnel for handling reactive materials.
By acknowledging these potential metal 3D printing challenges and working with a knowledgeable and well-equipped partner, companies can effectively mitigate risks and reliably produce high-quality, high-performance UAV antenna brackets using AlSi10Mg and Scalmalloy®. Met3dp’s integrated approach, combining advanced powder production, industry-leading printing equipment, and deep process expertise, provides B2B customers with the confidence needed for adopting additive manufacturing for mission-critical components.
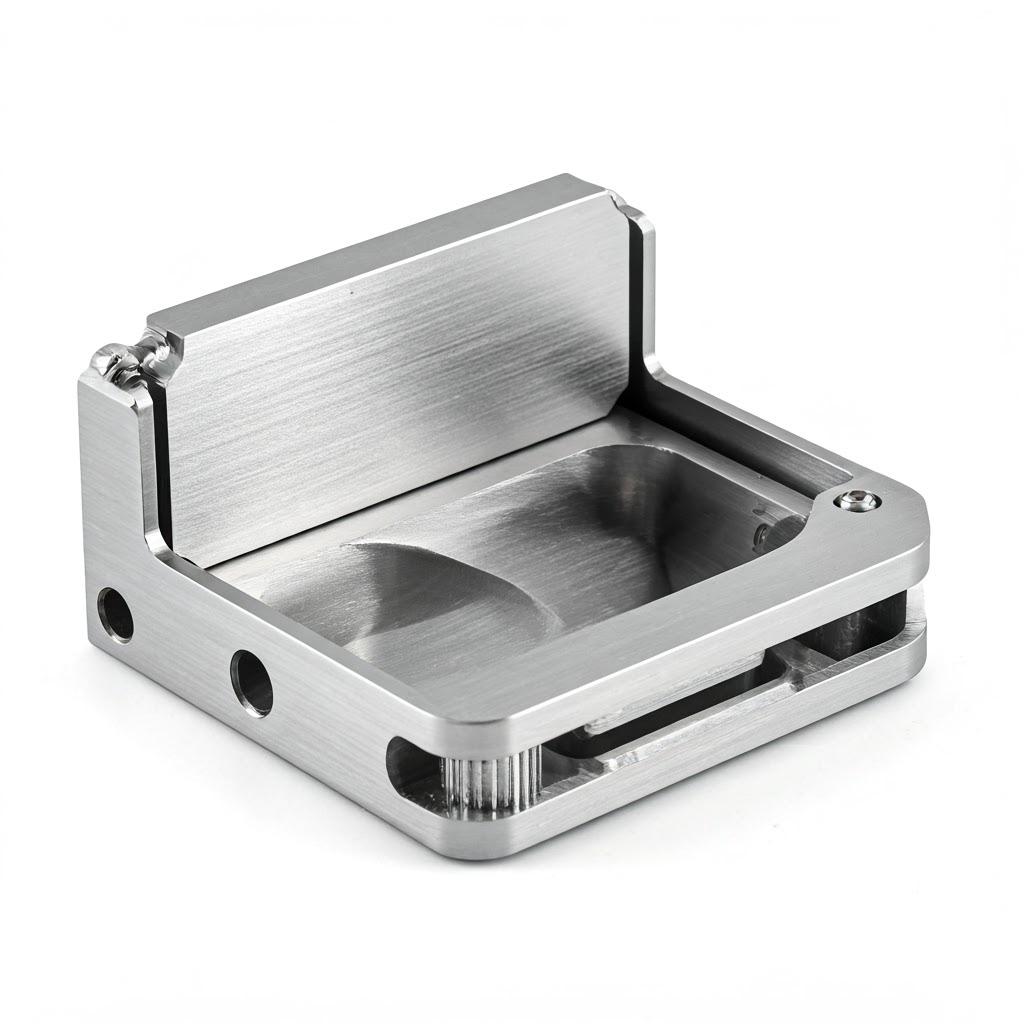
Selecting the Right Metal 3D Printing Service Provider for UAV Components
Choosing the right manufacturing partner is as critical as the design and material selection, especially for demanding applications like UAV antenna brackets destined for aerospace, defense, or high-performance commercial use. The capabilities, expertise, and quality systems of your chosen metal 3D printing service provider will directly impact the success of your project, the reliability of your components, and the efficiency of your supply chain. Not all AM providers are created equal; specialization, particularly in aerospace materials and processes, is key. For engineers and procurement managers navigating the landscape of B2B additive manufacturing, a thorough evaluation process is essential. Here’s a breakdown of key criteria to consider when selecting a partner like Met3dp for producing your AlSi10Mg or Scalmalloy® UAV brackets:
Key Evaluation Criteria for AM Suppliers:
- Technical Expertise & Application Experience:
- Material Specialization: Does the provider have deep, demonstrable experience working specifically with AlSi10Mg and, crucially, the high-performance alloy Scalmalloy®? Ask for case studies or examples of parts produced using these materials. Scalmalloy®, in particular, requires specific process knowledge.
- Fokus på branschen: Do they have experience with the aerospace, defense, or UAV industry? Understanding the stringent requirements, common challenges, and quality expectations of these sectors is vital.
- DfAM Support: Do they offer Design for Additive Manufacturing consultation? Can their engineers collaborate with your team to optimize the bracket design for lightweighting, printability, and performance, potentially avoiding costly redesigns? Met3dp prides itself on its decades of collective expertise in metal AM, offering comprehensive application development services.
- RF Awareness: For antenna brackets, does the provider understand the potential implications of design and material choices on RF performance?
- Equipment, Technology & Capacity:
- Process Capability: Ensure they utilize Laser Powder Bed Fusion (LPBF), the standard for high-resolution aluminum alloy printing.
- Machine Quality & Features: What specific printer models do they operate? Look for providers investing in industry-leading print volume, accuracy, and reliability, like the systems used at Met3dp. Key features include precise laser control, inert atmosphere management, build plate heating, and potentially in-situ monitoring capabilities.
- Byggvolym: Can their machines accommodate the size of your antenna bracket? Consider current needs and potential future requirements for larger components.
- Capacity & Scalability: Do they have sufficient machine capacity to handle your prototype needs och potential future production volumes without significant lead time extensions? Evaluate their ability to scale with your demand.
- Material Quality, Handling & Traceability:
- Powder Sourcing & Quality: Where do they source their AlSi10Mg and Scalmalloy® powders? Do they have stringent incoming quality checks? Providers like Met3dp, who manufacture their own metallpulver av hög kvalitet using advanced Gas Atomization and PREP technologies, offer a distinct advantage in controlling powder quality and consistency.
- Powder Handling Protocols: How do they handle, store, and recycle reactive aluminum powders to prevent contamination and ensure safety? Proper powder management directly impacts part quality.
- Batch Traceability: Can they provide full traceability for the powder batch used to produce your specific parts? This is often a requirement for aerospace components.
- Certifications & Quality Management System (QMS):
- ISO 9001: This certification demonstrates a commitment to a baseline level of quality management and process control. It should be considered a minimum requirement for any professional manufacturing partner.
- AS9100: This is the internationally recognized Quality Management System standard for the Aviation, Space, and Defense (AS&D) industry. If your UAV brackets are intended for these sectors, selecting an AS9100 certified 3D printing provider is often mandatory and provides assurance of rigorous process control, traceability, and risk management. Verify the provider’s certification status and scope.
- Detailed QMS: Ask about their specific quality procedures: process validation, equipment calibration schedules, operator training, inspection methods (including equipment like CMMs, 3D scanners), non-conformance handling, and documentation practices. Robust metal AM quality control är inte förhandlingsbart.
- Post-Processing Capabilities:
- Integrated Services: Does the provider offer essential post-processing steps in-house (stress relief/heat treatment, support removal, basic finishing)? Or do they rely heavily on outsourcing? In-house capabilities generally allow for better process control, streamlined workflow, and potentially shorter lead times.
- Range of Services: Can they manage or provide access to required secondary operations like precision CNC machining, specific surface finishes (polishing, anodizing), or specialized testing? Met3dp aims to provide comprehensive solutions covering the entire process chain.
- Heat Treatment Expertise: Confirm they have calibrated ovens and validated cycles specifically for AlSi10Mg (T6) and Scalmalloy® (specific aging) to ensure optimal material properties.
- Lead Time, Communication & Support:
- Quoting Process: Is their quoting process clear, detailed, and timely? Does the quote break down costs adequately?
- Realistic Lead Times: Do they provide transparent and achievable lead time estimates for both prototypes and production runs? Discuss their capacity planning and how they manage scheduling.
- Project Management & Communication: Who will be your point of contact? How do they handle project updates and communication? Responsiveness and clear communication are key to a smooth partnership.
- Customer Support: Are they willing to discuss technical challenges, provide guidance, and offer solutions? Look for a true additive manufacturing partner, not just a print bureau. Explore the provider’s background and capabilities, for instance, by reviewing the Met3dp capabilities page on their website.
Selecting the right supplier is a strategic decision. By carefully evaluating potential partners against these criteria, focusing on technical competence, quality systems, and relevant industry experience, procurement managers and engineers can establish reliable B2B relationships that ensure the successful production of high-performance, mission-critical UAV antenna brackets.
Cost Factors and Lead Time Estimation for 3D Printed Antenna Brackets
Additive manufacturing introduces different cost structures and lead time dynamics compared to traditional manufacturing methods. Understanding these factors is crucial for budgeting, project planning, and making informed decisions when sourcing 3D printed UAV antenna brackets. While AM can offer significant total cost of ownership benefits (e.g., through lightweighting and part consolidation), the per-part cost calculation involves several variables. Similarly, lead times can be rapid for prototypes but require careful planning for production volumes. Getting accurate B2B additive manufacturing quotes requires providing detailed information to potential suppliers like Met3dp.
Breakdown of Cost Drivers:
- Material Cost:
- Powder Price: The raw material cost per kilogram. Scalmalloy® powder is significantly more expensive than AlSi10Mg due to its composition (Scandium is costly) and development/licensing.
- Material Consumption: This includes not only the material in the final part but also the material used for support structures (which can be substantial for complex geometries) and potentially some allowance for powder loss during handling and printing. Efficient DfAM and nesting multiple parts in a build can optimize material usage.
- Maskintid:
- Build Duration: The primary driver is often the total time the AM machine is occupied. This is heavily influenced by:
- Part Height (Z-axis): Printing layer by layer means taller parts take longer. Orientation plays a key role here.
- Part Volume: Larger volume parts require more material to be melted per layer.
- Komplexitet: Intricate details and extensive laser scanning paths per layer increase print time.
- Nesting Efficiency: How many parts can be efficiently packed onto a single build plate affects the amortized machine time per part.
- Machine Rate: The hourly operational cost of the sophisticated metal AM printer, factoring in depreciation, maintenance, energy, and inert gas consumption.
- Build Duration: The primary driver is often the total time the AM machine is occupied. This is heavily influenced by:
- Kostnader för arbetskraft:
- Setup & Teardown: Preparing the machine for a build (loading powder, setting up the file) and cleaning the machine and retrieving parts afterward.
- Stöd för borttagning: This can be a significant labor component, especially for complex parts with extensive or hard-to-reach supports. DfAM is critical to minimizing this cost.
- Post-Processing Labor: Time spent on manual finishing, inspection, heat treatment cycles, CNC setup and operation, etc.
- Post-Processing Complexity:
- Värmebehandling: Oven time and energy costs for stress relief and aging cycles.
- Maskinbearbetning: Costs associated with CNC programming, setup, fixture design (if needed), and machining time. More features requiring tight tolerances increase this cost.
- Ytbehandling: Costs vary widely depending on the method (e.g., bead blasting is relatively inexpensive, extensive manual polishing is costly).
- Ytbeläggningar: Anodizing, painting, or other coatings add material and processing costs.
- Design, Engineering & Quality Assurance:
- DfAM Support: If the service provider assists with design optimization, this engineering time may be factored in.
- Inspection & QA: Costs associated with dimensional inspection (CMM, scanning), material testing (if required), documentation, and certification paperwork. More stringent QA requirements increase costs.
- Order Volume:
- Stordriftsfördelar: While AM is excellent for prototypes and low volumes, some economies of scale exist for larger batches. Full build plates can be processed more efficiently, and setup/teardown costs are amortized over more parts. Discuss potential price breaks for wholesale UAV components orders with your supplier.
Estimating Lead Times:
Lead time is the total time from order placement to receiving the finished parts. It’s a sequence of steps, each contributing to the overall duration:
- Quoting & Order Confirmation: (Typically 1-3 days) Depending on complexity and supplier responsiveness.
- File Preparation & Scheduling: (Typically 1-2 days) Preparing the build file, generating supports, and scheduling the job on an available machine.
- Printing (Machine Time): (Highly variable: Hours to several Days) Depends directly on part height, volume, complexity, and nesting, as discussed under costs. A single bracket might print in hours, but a full plate of complex brackets could take multiple days.
- Cooling & Depowdering: (Typically 4-12 hours) Allowing the build chamber and parts to cool sufficiently before safely removing loose powder.
- Stress Relief / Heat Treatment: (Typically 1-2 days) Including oven ramp-up, soak times (often several hours per step), and cooling.
- Part Removal & Support Removal: (Highly variable: Hours to Days) Depending on the removal method (sawing/EDM) and the complexity/volume of supports. Can be a bottleneck if supports are extensive or difficult to access.
- Secondary Post-Processing (Machining, Finishing, Coating): (Variable: Days to Weeks) Depends entirely on the specific steps required and the supplier’s or subcontractor’s capacity. Machining setup and execution can take several days; coating processes often add multiple days to a week.
- Inspection & Quality Control: (Typically 1-2 days) Depending on the level of inspection required (basic dimensional vs. full CMM/scan report).
- Packing & Shipping: (Typically 1-5 days) Depending on location and shipping method.
Typical Overall Lead Time Ranges:
- Simple Prototypes (minimal post-pro): 5 – 10 working days
- Complex Prototypes / Small Batches (with standard heat treatment & finishing): 2 – 4 veckor
- Larger Batches or Parts Requiring Extensive Post-Processing: 4 – 8 weeks or more
Key Takeaways for Procurement:
- Provide Detailed Information: Accurate quotes and lead time estimates depend on receiving complete information (CAD, material, quantity, tolerances, post-pro specs).
- Factor in Post-Processing: Don’t underestimate the time and cost contribution of post-processing steps.
- Discuss Volume Breaks: Inquire about pricing structures for different order quantities.
- Communicate Deadlines Clearly: Ensure the supplier understands your required delivery dates and confirm their ability to meet them.
- Consider the Full Workflow: An additive manufacturing cost analysis should account for all steps from design to finished part.
Providers like Met3dp strive for efficiency throughout this workflow, aiming to offer competitive 3D printing lead time estimation and transparent pricing for their B2B clients.
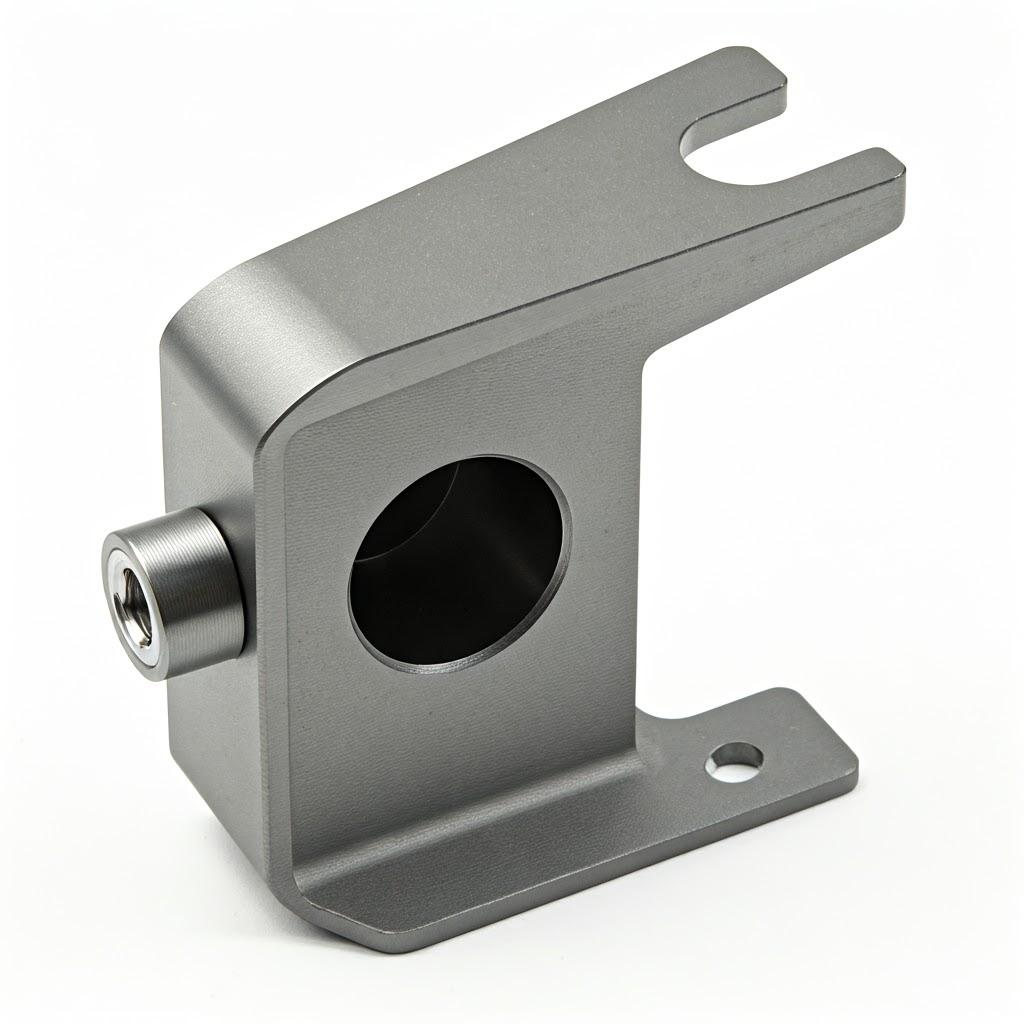
FAQ: Frequently Asked Questions for UAV Antenna Bracket Procurement
When adopting metal additive manufacturing for critical components like UAV antenna brackets, engineers and procurement managers often have specific questions regarding performance, precision, timelines, and costs. Here are answers to some frequently asked questions:
Q1: How does the strength of 3D printed AlSi10Mg or Scalmalloy® brackets compare to machined aluminum (e.g., 6061-T6 or 7075-T6)?
- Svar: This requires a nuanced comparison, considering the specific alloys and heat treatments:
- AlSi10Mg (AM, T6): Generally exhibits yield strength (~230-290 MPa) and ultimate tensile strength (~330-430 MPa) comparable to or slightly exceeding standard machined 6061-T6 aluminum (~276 MPa YS, ~310 MPa UTS). However, its ductility (~6-10%) is typically lower than 6061-T6 (~12-17%), and its fatigue strength might also be lower unless post-processing (like HIP – Hot Isostatic Pressing, or specific surface finishing) is employed.
- Scalmalloy® (AM, Heat Treated): This is where AM truly shines. Scalmalloy® delivers significantly higher yield strength (~480-520 MPa) and ultimate tensile strength (~520-540 MPa), surpassing 6061-T6 and rivaling or even exceeding high-strength machined 7075-T6 aluminum (~503 MPa YS, ~572 MPa UTS). Crucially, Scalmalloy® achieves this high strength while maintaining excellent ductility (~13-19%, significantly better than 7075-T6’s ~11%) and exhibiting superior Scalmalloy fatigue strength comparison results, making it exceptionally well-suited for high-vibration UAV environments where 7075-T6 might struggle.
- Specific Strength (Strength-to-Weight): Both AM aluminum alloys are significantly lighter than steel. Scalmalloy®’s specific strength is exceptional, often exceeding that of both 7075-T6 aluminum and even commonly used titanium alloys like Ti-6Al-4V.
- Viktig information att ta med sig: Properly processed and heat-treated Scalmalloy® offers superior strength and fatigue performance compared to traditional machined aluminum options at a similar density, enabling significant lightweighting or performance improvements. AlSi10Mg provides a good balance for less demanding applications. Achieving these properties relies heavily on powder quality and correct post-processing, underscoring the importance of experienced suppliers.
Q2: Can metal 3D printing achieve the tight tolerances required for mounting interfaces on UAVs?
- Svar: Metal AM (LPBF) typically achieves tolerances in the range of ±0.1mm to ±0.3mm (or ±0.2% on larger dimensions) in the as-printed and stress-relieved state. While this is sufficient for many features, it may not meet the very tight tolerances (e.g., ±0.01mm to ±0.05mm) often required for precise mounting interfaces, bearing fits, or slip-fit assemblies.
- The Solution – Hybrid Approach: The industry best practice is often a hybrid approach. Use AM to create the complex, lightweight overall shape of the bracket, benefiting from topology optimization and design freedom. Then, design critical interfaces (e.g., mounting holes, mating surfaces) with extra stock material (‘machining allowance’) and use precision CNC machining as a post-processing step to achieve the required tight tolerances and surface finishes only on those specific features.
- GD&T: Experienced AM providers can work with Geometric Dimensioning and Tolerancing (GD&T) callouts on drawings, planning the manufacturing process (including necessary machining) to meet these requirements.
- Viktig information att ta med sig: Don’t expect machining-level tolerances directly off the printer for all features. Plan for targeted post-machining on critical interfaces. Reputable providers like Met3dp can manage this hybrid workflow effectively. Understanding metal AM tolerances explained in this context is crucial for designers.
Q3: What is the typical lead time for a batch of 50 custom UAV antenna brackets?
- Svar: Providing an exact lead time without specific details is difficult, as it depends heavily on several factors:
- Part Size & Complexity: Larger, more complex brackets take longer to print and potentially longer to post-process (especially support removal).
- Material: Print parameters might slightly differ, but material choice mainly impacts cost more than time, unless specific heat treatment cycles are significantly longer.
- Nesting & Build Height: How many of the 50 brackets can fit efficiently onto a single build plate influences the number of print runs required. The total height of each build is a major time driver.
- Krav på efterbearbetning: The extent of support removal, heat treatment, required surface finish, amount of CNC machining, and any coating steps significantly impact the overall time. Machining fixtures might also need to be created for a batch run.
- Supplier Capacity: The chosen provider’s current workload and machine availability play a crucial role.
- Typical Range: For a batch of 50 moderately complex brackets requiring standard heat treatment, bead blasting, and perhaps some minor machining on interfaces, a lead time of 4 to 7 weeks might be a reasonable starting estimate. However, this could be shorter for very simple parts or longer for highly complex parts needing extensive post-processing.
- Viktig information att ta med sig: Always request a specific quote and lead time estimate from your chosen supplier based on the final part design and full specifications. Discussing delivery needs early is vital for UAV component procurement.
Q4: How does the surface finish of a 3D printed bracket affect RF performance?
- Svar: For most UAV antenna brackets operating at typical communication frequencies (MHz to low GHz range), the as-printed surface roughness of metal AM parts (typically Ra 5-15 µm on non-supported surfaces) usually has a negligible impact on the antenna’s far-field performance (gain, pattern). However, there are considerations:
- Very High Frequencies (mmWave): At much higher frequencies, surface roughness can increase conductor losses (RF resistance) and potentially affect performance, particularly if the bracket acts as part of a waveguide or transmission line structure (less common for simple brackets).
- Passive Intermodulation (PIM): Loose or partially sintered powder particles, or sharp edges/burrs sometimes present on as-printed or poorly finished parts, can potentially contribute to PIM, especially in high-power transmitting scenarios. Cleanliness and smooth finishes minimize this risk.
- Near-Field Interactions: The bracket’s geometry and proximity to the antenna radiating elements are far more likely to affect RF performance (tuning, impedance matching, pattern distortion) than the surface finish itself. This should be analyzed using RF simulation during the design phase.
- Viktig information att ta med sig: While generally not a primary concern for typical brackets, ensuring parts are clean, free of loose powder, and have reasonably smooth finishes (e.g., via bead blasting) is good practice, especially near active antenna elements or if PIM is a concern. Geometric design and RF simulation are more critical factors for ensuring electromagnetic compatibility.
Q5: What information do I need to provide a supplier like Met3dp for an accurate quote?
- Svar: To receive a timely and accurate metal 3D printing quote for your UAV antenna bracket, you should provide the following information:
- 3D CAD-modell: A high-quality 3D model in a standard format (e.g., STEP is preferred for accuracy; STL is also common but less precise). Ensure the model is watertight and represents the final desired geometry.
- Material Specification: Clearly state the desired material (e.g., AlSi10Mg or Scalmalloy®).
- Kvantitet: Specify the number of brackets required (e.g., prototype quantity, batch size of 50).
- Tolerance Requirements: Provide a 2D drawing or annotated 3D model (PMI) clearly highlighting critical dimensions and their required tolerances. Use standard GD&T callouts where applicable. If no specific tolerances are called out, the supplier will likely quote based on their standard AM capabilities (e.g., ISO 2768-m).
- Post-Processing Specifications: Detail all required post-processing steps:
- Värmebehandling: Specify the required condition (e.g., AlSi10Mg-T6, Scalmalloy® aged condition).
- Ytfinish: Define the required finish (e.g., as-printed, bead blast matte finish, specific Ra value on certain surfaces, polishing).
- Maskinbearbetning: Clearly indicate which features require post-machining and their tolerances/finishes.
- Ytbeläggningar: Specify any required coatings (e.g., Type II Anodize Clear, Chromate Conversion).
- Testing & Inspection Requirements: Specify any required testing (e.g., material certifications, dimensional inspection reports – basic or full CMM/scan, NDT like CT scanning if needed).
- Desired Delivery Date: Indicate your required timeline to help the supplier assess feasibility based on their capacity.
- Viktig information att ta med sig: Providing comprehensive and unambiguous information upfront allows the supplier to accurately assess the manufacturing complexity, estimate costs, determine the necessary workflow, and provide a reliable quote and lead time estimate, minimizing delays and misunderstandings.
Conclusion: Elevate Your UAV Performance with Advanced Metal 3D Printing
The demanding operational environment of Unmanned Aerial Vehicles necessitates components that are not only reliable and robust but also exceptionally lightweight and precisely engineered. As we’ve explored, the antenna bracket, though seemingly simple, plays a mission-critical role in ensuring stable communication and data links – the lifeline of any UAV. Traditional manufacturing methods, while established, often fall short in delivering the optimized geometries and weight savings required to push the boundaries of UAV endurance, payload capacity, and overall performance.
Metal additive manufacturing, specifically Laser Powder Bed Fusion, has emerged as a powerful and transformative solution for producing next-generation UAV components like antenna brackets. By leveraging DfAM principles, engineers can unlock unprecedented design freedom, creating topology-optimized and lattice-enhanced structures that drastically reduce weight while maintaining or even increasing structural integrity. The ability to consolidate multiple parts into a single, complex component further enhances reliability and simplifies assembly. High-performance materials like AlSi10Mg offer a versatile and cost-effective solution for many applications, while advanced alloys like Scalmalloy® -legering provide exceptional specific strength and fatigue resistance, rivaling titanium and high-strength aluminum alloys, making them ideal for the most demanding aerospace and defense platforms.
Successfully implementing metal AM requires navigating potential challenges related to design optimization, process control, material quality, achievable tolerances, and essential post-processing steps. This underscores the critical importance of selecting the right manufacturing partner. A supplier like Met3dp brings invaluable advantages to the table:
- Deep Materials Expertise: Including in-house production of high-quality, spherical metal powders optimized for AM.
- Advanced Printing Technology: Utilizing industry-leading equipment for superior accuracy, reliability, and build volume.
- Omfattande lösningar: Offering expertise across the entire workflow, from DfAM consultation and printing to integrated post-processing and rigorous quality assurance.
- Fokus på branschen: Understanding the specific needs and stringent requirements of the aerospace, defense, medical, and automotive sectors.
For engineers seeking to reduce mass, enhance structural performance, and accelerate innovation in their UAV designs, and for procurement managers looking for a reliable B2B additive manufacturing partner capable of delivering high-quality, flight-ready components, metal 3D printing offers compelling advantages. By embracing this technology and collaborating with an experienced provider, you can elevate your UAV’s capabilities and gain a competitive edge.
Ready to explore how metal additive manufacturing can revolutionize your UAV antenna brackets or other critical components? Contact the experts at Met3dp today for a consultation or to request a quote for your next project. Let us help you harness the power of additive manufacturing to achieve your most ambitious engineering goals.
Dela på
MET3DP Technology Co, LTD är en ledande leverantör av lösningar för additiv tillverkning med huvudkontor i Qingdao, Kina. Vårt företag är specialiserat på 3D-utskriftsutrustning och högpresterande metallpulver för industriella tillämpningar.
Förfrågan för att få bästa pris och anpassad lösning för ditt företag!
Relaterade artiklar
Om Met3DP
Senaste uppdateringen
Vår produkt
KONTAKTA OSS
Har du några frågor? Skicka oss meddelande nu! Vi kommer att betjäna din begäran med ett helt team efter att ha fått ditt meddelande.
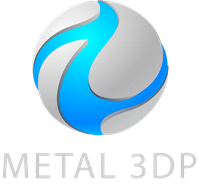
Metallpulver för 3D-printing och additiv tillverkning