Lattice-Optimized Aerospace Parts via Metal AM
Innehållsförteckning
Introduction: Revolutionizing Aerospace Structures with Metal AM Lattices
The aerospace industry operates at the pinnacle of engineering, constantly pushing the boundaries of performance, efficiency, and safety. In this relentless pursuit of innovation, weight reduction is paramount. Every kilogram saved translates directly into lower fuel consumption, increased payload capacity, enhanced maneuverability, and reduced launch costs. For decades, engineers relied on subtractive manufacturing techniques and conventional designs to shave off grams. However, the advent of metalltillsatstillverkning (AM), commonly known as metal 3D-utskrifter, has unlocked unprecedented possibilities, particularly through the creation of intricate lattice structures. These bio-inspired, mathematically defined structures offer an exceptional strength-to-weight ratio, enabling the design of komponenter för flyg- och rymdindustrin that are significantly lighter yet retain, or even exceed, the required mechanical performance.
Lattice structures are essentially three-dimensional networks composed of interconnected struts or nodes, arranged in repeating unit cells. Think of them like micro-trusses, engineered at a scale previously impossible to manufacture economically. This structural optimization capability allows designers to place material precisely where it’s needed for load-bearing and remove it where it’s not, mimicking natural forms like bone structures that have evolved for optimal efficiency. Metal AM technologies, such as Selective Laser Melting (SLM), Direct Metal Laser Sintering (DMLS), and Electron Beam Melting (EBM) – a technology where Met3dp provides leading solutions with its SEBM printers – are uniquely capable of fabricating these complex internal geometries directly from digital models. Unlike traditional machining, which starts with a solid block and removes material, AM builds parts layer by layer, enabling the creation of internal voids, complex curvatures, and intricate lattice networks without the constraints of tool access or draft angles.
The integration of lattice structures into flyg- och rymdteknik represents a paradigm shift. It moves beyond simple lättviktande to multifunctional design. Lattices can be engineered not only for structural support but also for enhanced energy absorption (crashworthiness), vibration damping, thermal management (acting as heat exchangers), and acoustic insulation. This multi-functionality allows for component consolidation, further reducing part count, assembly complexity, and overall system weight. For aerospace manufacturers, suppliers, and procurement managers looking for next-generation solutions, understanding the potential of lattice-optimized metal AM parts is crucial. This technology offers a competitive edge, enabling the development of aircraft, spacecraft, satellites, and unmanned aerial vehicles (UAVs) that are lighter, faster, more fuel-efficient, and capable of higher performance envelopes. As a leader in metal AM equipment and high-performance powders, Met3dp is at forefront of this revolution, providing the tools and materials necessary to turn these advanced designs into reality. This blog post will delve deep into the world of lattice-optimized aerospace components produced via metal AM, exploring applications, materials, design considerations, challenges, and how to leverage this transformative technology effectively.
The Role of Lattice Structures in Modern Aerospace Applications
The application of lattice structures, enabled by metal additive manufacturing, is rapidly expanding across the aerospace sector, addressing critical challenges related to weight, performance, and functionality. Their unique properties make them suitable for a diverse range of aerospace structural parts and multifunctional components. Procurement managers and engineers seeking advanced airframe design solutions or satellite components suppliers are increasingly turning to metal AM lattices.
Key Application Areas:
- Structural Lightweighting: This remains the primary driver for adopting lattice structures.
- Airframe Components: Brackets, hinges, support ribs, nacelle components, and wing structures can be redesigned with internal lattices to drastically reduce mass without compromising structural integrity. For instance, topology optimization software can identify low-stress regions within a solid bracket, which can then be replaced by an engineered lattice, saving potentially 30-60% of the original weight. This directly impacts fuel efficiency and aircraft range.
- Satellite Bus Structures: Satellites operate under extreme launch cost constraints (thousands of dollars per kilogram). Lattice structures are ideal for primary and secondary structural elements, equipment mounting panels, and antenna supports, minimizing launch mass while maintaining stiffness and strength requirements in the harsh space environment. Wholesale suppliers of satellite components are exploring AM lattices to offer competitive solutions.
- UAV Structures: The performance and endurance of Unmanned Aerial Vehicles (UAVs) are highly sensitive to weight. Lattice-based designs for fuselages, wing spars, landing gear components, and sensor mounts contribute to longer flight times, increased payload capacity, and improved agility.
- Enhanced Energy Absorption: Lattice structures can be designed to buckle and deform predictably under impact loads, absorbing significant amounts of kinetic energy.
- Crashworthiness: Components in landing gear, fuselage sections, or protective casings for sensitive equipment can incorporate energy-absorbing lattices to improve survivability during hard landings or impacts. The specific unit cell geometry and strut thickness can be tuned to control the deformation behavior and energy absorption characteristics.
- Impact Protection: Protecting sensitive optics, electronics, or propellant tanks from debris impact (common in space) or bird strikes can be achieved using lattice-based shielding.
- Termisk hantering: The high surface area-to-volume ratio of lattice structures makes them exceptionally effective for heat dissipation or transfer.
- Värmeväxlare: Metal AM allows the creation of highly complex, compact, and efficient heat exchangers with integrated lattice or gyroid structures within the fluid channels. These can be used for cooling avionics, managing engine heat, or in environmental control systems, often combining structural support and thermal function in one part. Companies seeking thermal management aerospace solutions find AM lattices particularly compelling.
- Thermal Protection Systems (TPS): For hypersonic vehicles or re-entry spacecraft, lattices made from high-temperature alloys can form part of the TPS, managing extreme thermal loads through conduction, convection, and radiation, potentially combined with transpiration cooling channels integrated within the lattice.
- Vibration Damping and Acoustic Attenuation: The geometry of lattice structures can be tuned to dampen specific vibration frequencies or attenuate noise transmission.
- Engine Mounts & Equipment Racks: Lattices can be incorporated into mounting structures to isolate sensitive equipment from engine vibrations or aerodynamic flutter, improving reliability and performance.
- Cabin Noise Reduction: Strategically placed lattice panels within the fuselage structure could contribute to reducing cabin noise, enhancing passenger comfort.
- Biomedical Implants (Adjacent Application): While distinct from aerospace, the principles overlap. Porous lattice structures, often made from Titanium alloys like Ti-6Al-4V, are used in orthopedic implants to mimic bone structure, promoting osseointegration (bone ingrowth) and providing a modulus closer to bone, reducing stress shielding. This highlights the versatility of AM lattice technology.
Industry Impact:
The ability to produce these multifunctional, optimized components is driving significant interest from major aerospace OEMs (Original Equipment Manufacturers), Tier 1 suppliers, and specialized aerospace structural parts distributors. The demand for weight reduction aerospace solutions is universal, from commercial aviation aiming for fuel savings to defense applications requiring enhanced performance and payload. Metal AM lattice structures provide a powerful tool to meet these demands, enabling designs that were previously impossible or prohibitively expensive to manufacture. Companies like Met3dp, with their robust SEBM printers capable of handling materials like Titanium alloys and their expertise in producing high-quality metal powders, are crucial partners in realizing these advanced applications. They bridge the gap between innovative design concepts and tangible, flight-worthy hardware. The integration of lattice structures represents a fundamental shift towards more efficient, integrated, and performance-driven aerospace design.
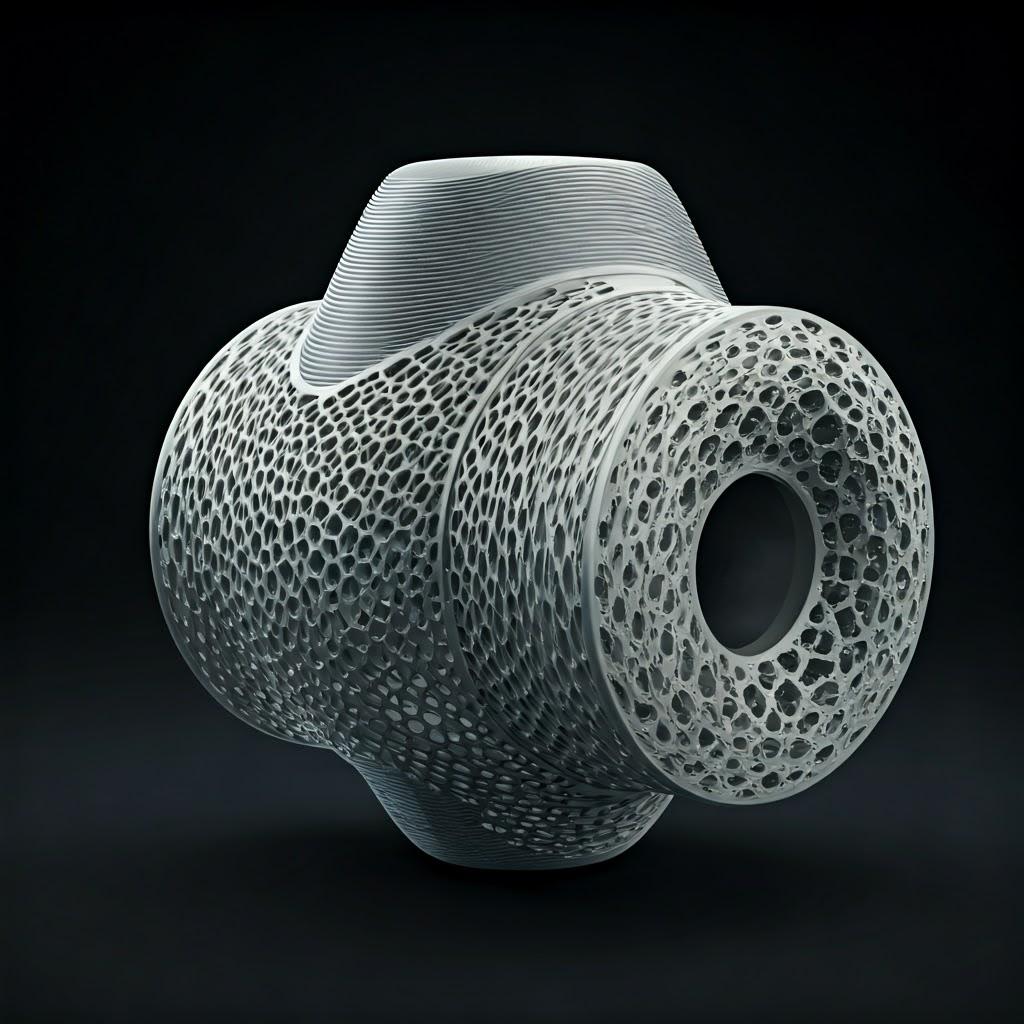
Why Metal Additive Manufacturing is Ideal for Aerospace Lattice Components
Även om concept of lattice structures isn’t new, their practical and economical implementation in critical aerospace applications has been largely enabled by the maturation of metalltillsatstillverkning (AM) technologies. Traditional manufacturing methods, primarily subtractive (machining) or formative (casting, forging), face significant limitations when attempting to create the complex, internal, and often non-uniform geometries characteristic of optimized lattice structures. Metal AM overcomes these hurdles, offering distinct advantages that make it the ideal production method.
Advantages of Metal AM for Lattice Structures:
- Unmatched Design Freedom & Complexity: This is arguably the most significant advantage. AM builds parts layer-by-layer directly from a 3D CAD model. This process is largely agnostic to internal complexity.
- Intricate Internal Geometries: AM can create interconnected networks of fine struts (often sub-millimeter), varying densities within a single part, and complex curvatures that are impossible to machine or cast. This allows for truly optimized lattices tailored to specific load paths and functional requirements.
- Topology Optimization & Generative Design: AM seamlessly integrates with advanced design software that algorithmically generates optimal material distributions, often resulting in organic-looking structures with complex internal lattices. AM is the only practical way to manufacture many of these highly efficient designs.
- Negative Draft Angles & Undercuts: Unlike casting or molding, AM does not require draft angles for part removal, allowing for true design intent replication without compromise.
- Del Konsolidering: Complex assemblies previously made from multiple individual components fastened together can often be redesigned and printed as a single, monolithic part incorporating lattice structures.
- Reduced Part Count: Fewer parts mean simpler supply chains, reduced assembly time and labor, and fewer potential points of failure (e.g., fastener joints).
- Weight Savings: Eliminating fasteners, flanges, and overlapping material further contributes to overall weight reduction beyond the lattice optimization itself.
- Improved Structural Integrity: A single, integrated component can often distribute loads more effectively than an assembly, potentially increasing overall strength and fatigue life. Aerospace procurement teams actively seek part consolidation aerospace opportunities to reduce costs and improve reliability.
- Material Efficiency & Reduced Waste (Buy-to-Fly Ratio): Additive manufacturing generally uses material more efficiently than subtractive methods, which can machine away up to 90% of the initial stock material (high buy-to-fly ratio).
- Near-Net Shape Production: AM creates parts close to their final dimensions, requiring less subsequent machining. While some support structures generate waste, the overall material utilization is typically much better, especially for complex parts made from expensive aerospace alloys like Titanium.
- Powder Reusability: Unfused metal powder in the build chamber can often be sieved and reused in subsequent builds (with appropriate quality control), further improving sustainability and cost-effectiveness. High-quality powder suppliers like Met3dp provide guidelines for powder management and reuse.
- Rapid Prototyping & Iteration: AM allows designers and engineers to quickly produce physical prototypes of lattice-based designs for testing and validation.
- Accelerated Development Cycles: Functional prototypes can be created in days or weeks, compared to months for traditional tooling and manufacturing. This allows for faster design iteration, optimization, and verification.
- Reduced Tooling Costs: AM often requires no part-specific tooling (molds, dies, jigs), making it cost-effective for low-volume production, prototypes, and design revisions. This is a key benefit for businesses seeking rapid prototyping aerospace tjänster.
- Manufacturing Difficult-to-Machine Materials: Aerospace applications frequently utilize high-strength, high-temperature alloys (like Titanium alloys or Nickel superalloys) that are notoriously difficult and expensive to machine conventionally.
- Process Suitability: AM processes like SLM, DMLS, and EBM are well-suited for processing these advanced materials, often achieving near-full density and excellent mechanical properties. Met3dp’s focus on materials like Ti-6Al-4V and its advanced powder production techniques ensure optimal feedstock for printing these challenging alloys.
Why Traditional Methods Fall Short for Lattices:
- Machining (Subtractive): Cannot create internal voids or complex interconnected networks. Tool access is the primary limitation. While possible to machine lattice blocks, integrating them seamlessly within a complex part is usually impossible.
- Casting (Formative): Investment casting can produce some complexity, but creating fine, high-resolution lattices with thin struts, removing the shell/core material from deep internal structures, and ensuring complete filling without defects is extremely challenging and often impractical, especially with reactive metals like Titanium. Achieving consistent material properties can also be difficult.
- Joining/Brazing: Fabricating individual struts and nodes and then joining them is labor-intensive, expensive, introduces potential weak points at the joints, and limits achievable complexity and strut density.
Sammanfattningsvis, metal 3D printing aerospace technologies are not just en option for producing lattice structures; they are the enabling technology. The ability to handle complexity, consolidate parts, efficiently use expensive materials, and rapidly iterate designs makes AM uniquely suited to unlock the full potential of lattice optimization for demanding aerospace applications. Companies searching to buy aerospace lattice parts or find capable metal 3D printing service aerospace providers should prioritize partners with proven expertise in AM processes, materials science, and DfAM for lattice structures, like Met3dp.
Material Focus: AlSi10Mg and Ti-6Al-4V for High-Performance Lattices
The choice of material is critical for the success of any aerospace component, and lattice structures are no exception. The material must not only possess the required mechanical properties (strength, stiffness, fatigue resistance, temperature tolerance) but also be compatible with the chosen metal AM process and suitable for the specific application environment. For many aerospace lattice applications demanding lightweighting and structural performance, two materials stand out: AlSi10Mg (an aluminum-silicon alloy) och Ti-6Al-4V (a titanium alloy). Both are readily processable via laser powder bed fusion (L-PBF) methods like SLM/DMLS, and Ti-6Al-4V is also commonly processed using Electron Beam Melting (EBM/SEBM). Met3dp specializes in producing high-quality spherical powders of these and other advanced alloys, optimized for additive manufacturing processes.
AlSi10Mg: The Lightweight Workhorse
AlSi10Mg is a widely used aluminum casting alloy that has become a staple in metal AM due to its excellent processability, good strength-to-weight ratio, and favorable thermal properties.
- Key Properties & Advantages:
- Låg densitet: With a density of approximately 2.67g/cm3, it offers significant weight savings compared to steels or even titanium alloys.
- Good Strength & Hardness (Post Heat Treatment): While moderate in the as-built state, appropriate heat treatments (like T6 solutionizing and aging) can significantly increase its tensile strength (up to ~300-350 MPa) and hardness, making it suitable for moderately loaded structural parts.
- Utmärkt värmeledningsförmåga: Beneficial for applications requiring heat dissipation, such as heat exchangers or electronics enclosures with integrated lattice cooling structures.
- God korrosionsbeständighet: Offers adequate resistance for many aerospace environments, although surface treatments may be needed for specific applications.
- Excellent Processability in L-PBF: It melts and solidifies predictably under laser exposure, allowing for fine features and relatively high build speeds. It generally requires support structures due to its lower melting point and thermal conductivity compared to titanium.
- Kostnadseffektivitet: Aluminum alloys are generally less expensive than titanium or nickel superalloys, both in terms of raw powder cost and processing time.
- Typical Aerospace Lattice Applications:
- Secondary structural brackets and supports
- Heat exchangers and cold plates
- UAV airframe components
- Environmental Control System (ECS) ducting and components
- Antenna supports and satellite bus structures (where temperatures are moderate)
- Prototype components for fit and form checks
- Överväganden:
- Lower temperature resistance compared to Titanium (softens significantly above 150−200∘C).
- Lower absolute strength and fatigue endurance compared to Ti-6Al-4V.
- Requires careful heat treatment control to achieve optimal properties.
Procurement managers seeking 3D-utskrift av aluminiumlegering solutions for lightweight components often specify AlSi10Mg due to its balance of properties, processability, and cost. Reputable powder suppliers ensure consistent powder characteristics (particle size distribution, morphology, flowability) which are critical for reliable printing.
Ti-6Al-4V (Grade 5): The High-Performance Standard
Ti-6Al-4V (Titanium-6% Aluminum-4% Vanadium), often referred to as Ti64 or Grade 5 Titanium, is the most widely used titanium alloy in aerospace and medical applications, renowned for its exceptional combination of properties.
- Key Properties & Advantages:
- Utmärkt förhållande mellan styrka och vikt: Offers high strength (typically 900-1100 MPa after stress relief or HIP) combined with a moderate density (approx. 4.43g/cm3). This provides superior specific strength compared to aluminum alloys and many steels, making it ideal for critical lightweight structures.
- High Temperature Resistance: Retains good mechanical properties up to around 350−400∘C, suitable for applications near engines or experiencing aerodynamic heating.
- Outstanding Corrosion Resistance: Forms a stable passive oxide layer, providing excellent resistance to corrosion in various environments, including seawater and many industrial chemicals.
- Biokompatibilitet: Widely used for medical implants due to its non-toxic nature and compatibility with human tissue (relevant for life support systems or crewed spacecraft components).
- Good Fatigue Strength: Crucial for aerospace components subjected to cyclic loading. Hot Isostatic Pressing (HIP) is often used post-AM to close internal porosity and significantly improve fatigue properties.
- Processable via L-PBF and EBM/SEBM: Can be processed effectively using both laser and electron beam methods. EBM/SEBM, like the systems offered by Met3dp, typically operates at higher temperatures, reducing residual stress and often eliminating the need for extensive support structures, which is particularly advantageous for complex lattice designs.
- Typical Aerospace Lattice Applications:
- Primary structural components (ribs, spars, bulkheads)
- Engine components (brackets, housings – non-rotating)
- Komponenter till landningsställ
- Satellite structures requiring high stiffness and low mass
- High-performance UAV structures
- Components requiring elevated temperature performance or superior corrosion resistance
- Överväganden:
- Higher material cost compared to AlSi10Mg.
- More challenging to process due to its reactivity (requires inert atmosphere or vacuum) and higher melting point.
- Post-processing (stress relief, HIP, machining) is often critical to achieve desired properties and tolerances.
Engineers designing critical aerospace grade titanium components often specify Ti-6Al-4V produced via AM with subsequent HIP treatment. Partnering with a reliable Ti-6Al-4V powder supplier and an AM service provider with expertise in processing titanium, such as Met3dp, is essential. Met3dp’s utilization of advanced powder manufacturing techniques like gas atomization and Plasma Rotating Electrode Process (PREP) ensures the production of highly spherical, low-oxygen Ti-6Al-4V powders crucial for achieving the high density and mechanical performance required in demanding aerospace applications. Their integrated approach, encompassing both advanced powder production and state-of-the-art SEBM printing technology, provides a comprehensive solution for high-performance titanium lattice structures.
Material Selection Summary Table:
Funktion | AlSi10Mg | Ti-6Al-4V (klass 5) | Typical Aerospace Use Case Examples |
---|---|---|---|
Täthet | Low (~2.67g/cm3) | Moderate (~4.43g/cm3) | Lightweighting (Both, Ti64 higher specific strength) |
Specifik styrka | Bra | Utmärkt | Critical structural parts (Ti64), Brackets (Both) |
Max Service Temp. | Moderate (~150−200∘C) | High (~350−400∘C) | Engine proximity components (Ti64), ECS parts (AlSi) |
Termisk konduktivitet | Utmärkt | Låg | Heat Exchangers (AlSi) |
Motståndskraft mot korrosion | Bra | Utestående | Harsh environment exposure (Ti64) |
Processability (L-PBF) | Utmärkt | Good (Requires careful control) | General AM components |
Processability (EBM/SEBM) | Not common | Excellent (Reduced stress, fewer supports) | Complex geometries, Lattice structures (Ti64) |
Relativ kostnad | Lägre | Högre | Cost-sensitive parts (AlSi), Performance-critical (Ti64) |
Behov av efterbearbetning | Heat Treatment (T6) essential for strength | Stress Relief, HIP often required for fatigue | Flight-critical components (Ti64 requires HIP) |
Met3dp Powder Availability | Yes (High-quality variants available) | Yes (Core expertise, Gas Atomized & PREP) | Sourcing high-performance metal powder properties |
Export to Sheets
Selecting the right material involves balancing performance requirements (mechanical loads, temperature, environment), manufacturing considerations (processability, post-processing needs), and cost. Both AlSi10Mg and Ti-6Al-4V offer compelling advantages for specific aerospace lattice applications, and leveraging the capabilities of metal AM with high-quality powders from suppliers like Met3dp enables the realization of truly optimized, next-generation components.
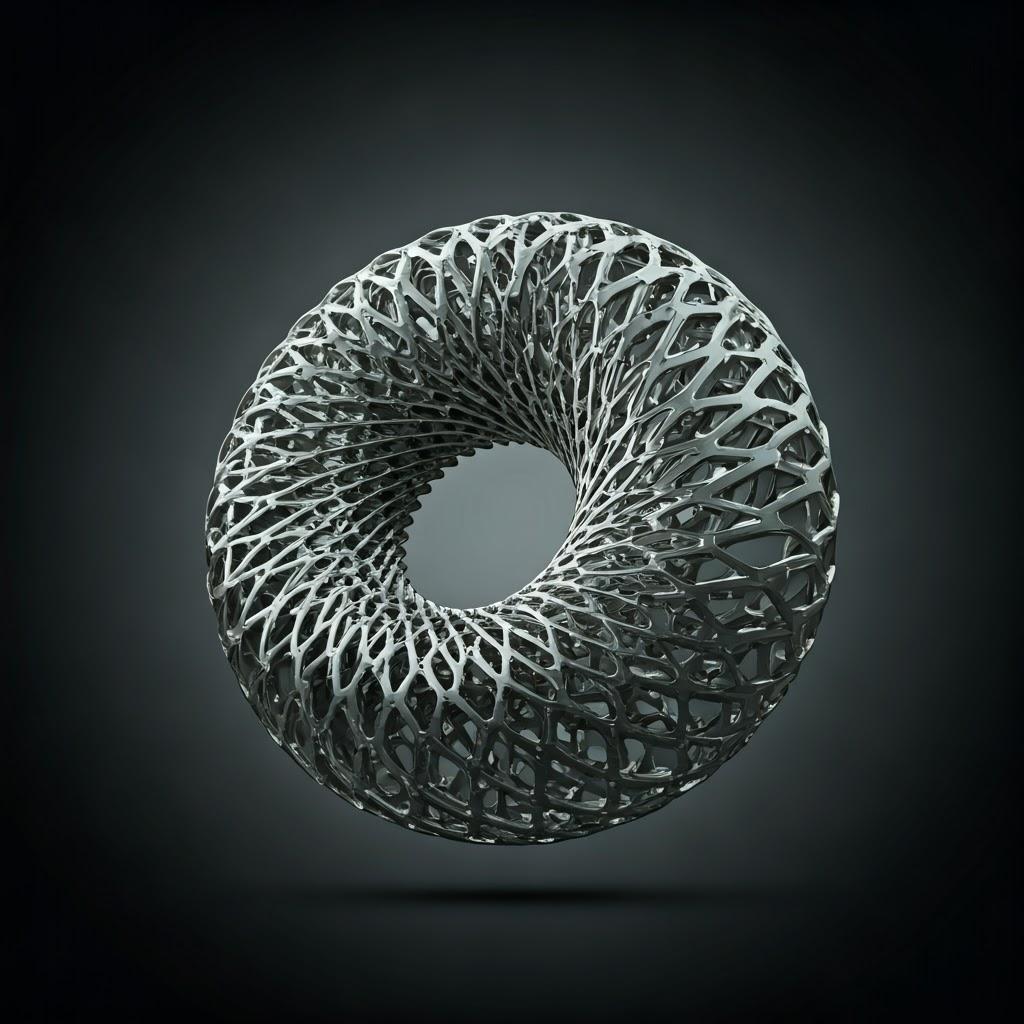
Design for Additive Manufacturing (DfAM) Principles for Optimal Lattice Structures
Creating successful, high-performance aerospace lattice components requires more than simply replacing solid material with a repeating pattern. It demands a sophisticated approach known as Design för additiv tillverkning (DfAM). DfAM for lattices involves leveraging the unique capabilities of AM while respecting its constraints, ensuring manufacturability, functionality, and optimal performance. Engineers and designers must move beyond traditional design thinking and embrace strategies tailored specifically for layer-by-layer fabrication of these complex geometries. Effective DfAM aerospace practices are crucial for unlocking the full potential of lightweighting, thermal management, and energy absorption offered by lattice structures.
Key DfAM Considerations for Metal AM Lattices:
- Lattice Topology and Unit Cell Selection: The fundamental building block of the lattice dictates its overall mechanical, thermal, and acoustic properties.
- Periodic vs. Stochastic Lattices:
- Periodic Lattices: Composed of repeating unit cells (e.g., cubic, octet-truss, diamond). Offer predictable, anisotropic (direction-dependent) or isotropic (uniform) properties based on cell geometry. Easier to model and analyze. Common types include:
- Strut-Based: Body-Centered Cubic (BCC), Face-Centered Cubic (FCC), Octet-Truss (strong and stiff, often used for structural applications).
- Surface-Based (TPMS – Triply Periodic Minimal Surfaces): Gyroid, Schwarz D, Diamond P. Offer smooth, non-tortuous surfaces, high surface area-to-volume ratio, good manufacturability (often self-supporting), and excellent properties for heat transfer and fluid flow. Becoming increasingly popular for multifunctional applications.
- Stochastic Lattices: Random or pseudo-random distribution of pores/struts (like metal foam). Offer isotropic properties but are harder to model precisely and can have wider property variations. Often used for energy absorption or filtration.
- Periodic Lattices: Composed of repeating unit cells (e.g., cubic, octet-truss, diamond). Offer predictable, anisotropic (direction-dependent) or isotropic (uniform) properties based on cell geometry. Easier to model and analyze. Common types include:
- Unit Cell Choice: Selecting the appropriate lattice unit cell design depends heavily on the primary function (structural support, heat transfer, energy absorption). FEA simulations are often used to compare the performance of different unit cells under expected load conditions. Factors include stiffness, strength, buckling resistance, manufacturability (self-supporting angles), and surface area.
- Periodic vs. Stochastic Lattices:
- Density Grading and Homogenization: Lattices don’t need to be uniform. AM allows for graded density, varying the strut thickness or cell size across the part to match local stress distributions identified through topology optimization lattice arbetsflöden.
- Funktionellt graderade material (FGM): Transitioning smoothly from a dense solid region (e.g., for interfaces) to a low-density lattice core maximizes efficiency.
- Homogenization: For analysis purposes, complex lattice regions are often represented in FEA models as homogenized continua with equivalent material properties (effective modulus, Poisson’s ratio, yield strength) derived from unit cell analysis. This simplifies global structural analysis but requires careful validation.
- Strut Size, Wall Thickness, and Minimum Feature Size: AM processes have limitations on the minimum feature size they can reliably produce.
- Minimum Strut Diameter: Typically ranges from 0.3mm to 0.8mm depending on the machine, material (AlSi10Mg vs. Ti-6Al-4V), and process parameters. Designing struts below the machine’s reliable limit leads to manufacturing failures or poor geometric fidelity. Met3dp’s advanced printers aim for high resolution, enabling finer lattice features.
- Väggens tjocklek: For surface-based lattices (like TPMS), minimum wall thickness constraints apply.
- Aspect Ratio: Very long, thin struts can be prone to buckling during the build or under load.
- Build Orientation and Anisotropy: The orientation of the part on the build plate significantly impacts support requirements, surface finish, residual stress, and potentially mechanical properties (anisotropy).
- Stödstrukturer: Lattice overhangs often require support structures, especially for angles below ~45 degrees (process dependent). Designing lattices with self-supporting angles or using processes like EBM/SEBM (which often require fewer supports due to higher build temperatures) can minimize this need. Support structure optimization is critical for complex internal lattices where removal is difficult.
- Property Variation: Mechanical properties can vary slightly depending on the build direction (Z vs. XY plane) due to the layer-wise nature of AM. This anisotropy must be considered in design analysis, especially for fatigue-critical parts.
- Integration with Solid Features: Lattices are rarely standalone; they are typically integrated within a larger component.
- Smooth Transitions: Abrupt transitions between dense solid sections and low-density lattices can create stress concentrations. Smooth, filleted transitions are crucial for durability.
- Interface Design: Ensuring robust interfaces for load transfer (e.g., where bolts attach) is critical. These areas usually remain solid.
- Simulation and Validation (FEA/CFD): Predictive modeling is indispensable for lattice design.
- Structural Analysis (FEA): Finite Element Analysis (FEA) AM is used extensively to predict stiffness, stress distribution, buckling behavior, and fatigue life under operational loads. Both unit cell level and homogenized modeling approaches are used.
- Thermal/Fluid Analysis (CFD): For lattices used in heat exchangers or thermal management, Computational Fluid Dynamics (CFD) is used to simulate fluid flow and heat transfer performance.
- Experimental Validation: Simulation results must be validated through physical testing of representative coupons and full-scale prototypes.
- Powder Removability: This is a crucial, often overlooked DfAM aspect for lattices. Trapped powder adds weight and can compromise performance.
- Design for Drainage: Incorporating drainage holes or ensuring interconnected porosity allows unfused powder to be removed after printing. Blind or isolated cavities must be avoided.
- Unit Cell Connectivity: Choosing unit cells (like Gyroids or Octet-truss) with good interconnectivity facilitates powder removal compared to more tortuous designs.
Leveraging DfAM Tools: Modern CAD and simulation software incorporate modules specifically for generative design aerospace applications, lattice generation, topology optimization, and AM simulation. Utilizing these tools effectively is key to efficient and successful lattice design. Partnering with an AM service provider like Met3dp, which has deep expertise not only in printing but also in DfAM principles, can significantly streamline the development process for complex lattice components. Their understanding of material-process interactions ensures that designs are manufacturable and meet performance targets.
DfAM Checklist for Aerospace Lattices:
DfAM Aspect | Viktiga överväganden | Impact if Ignored |
---|---|---|
Unit Cell Selection | Match properties (stiffness, strength, thermal) to function; Consider manufacturability (self-supporting angles). | Sub-optimal performance, build failures, difficult support removal. |
Density/Grading | Use topology optimization; Implement smooth density transitions; Homogenize for analysis. | Inefficient material use, stress concentrations, inaccurate analysis. |
Feature Size | Respect machine limitations (min strut diameter/wall thickness); Check aspect ratios. | Unprintable features, geometric inaccuracies, strut buckling. |
Build Orientation | Minimize supports; Consider anisotropy effects on properties; Optimize surface finish on critical faces. | Excessive post-processing, unpredictable performance, poor surface quality. |
Solid Integration | Ensure smooth transitions; Design robust interfaces for load transfer. | Stress risers, premature failure at interfaces. |
Simulation (FEA/CFD) | Predict performance under load/thermal conditions; Validate models with testing. | Unexpected failures, underperformance, costly design iterations. |
Powder Removability | Design interconnected porosity; Include drainage holes; Avoid enclosed voids. | Trapped powder (added weight, contamination), compromised density/properties. |
Support Strategy | Minimize internal supports; Design accessible supports; Use processes like EBM/SEBM where possible. | Difficult/impossible removal, surface scarring, increased post-processing cost. |
Export to Sheets
By rigorously applying these DfAM principles, engineers can harness the power of metal AM to create truly optimized, lightweight, and functional lattice structures that redefine performance standards in aerospace.
Achieving Precision: Tolerance, Surface Finish, and Dimensional Accuracy in Metal AM Lattices
While metal AM offers unparalleled design freedom, achieving the tight tolerances, specific surface finishes, and high dimensional accuracy demanded by many aerospace applications requires careful control throughout the entire process chain – from design and printing to post-processing and inspection. Understanding the achievable precision levels and the factors influencing them is critical for engineers specifying lattice components and for procurement managers evaluating potential suppliers. Quality control aerospace components produced via AM necessitates a focus on these aspects.
Tolerances in Metal AM:
Metal AM processes, whether L-PBF or EBM/SEBM, produce near-net shape parts, but they are not inherently as precise as high-precision CNC machining in their as-built state.
- Typical As-Built Tolerances:
- L-PBF (SLM/DMLS): Generally offers tighter tolerances. Typical values might be in the range of ±0.1mm to ±0.2mm for smaller dimensions (e.g., < 100mm), and ±0.1% to ±0.2% for larger dimensions. However, this is highly dependent on the material (AlSi10Mg often holds tighter tolerances than Ti-6Al-4V), machine calibration, part geometry, and thermal management during the build.
- EBM/SEBM: Due to the higher processing temperatures and powder-based support, as-built tolerances are typically slightly looser than L-PBF, potentially in the range of ±0.2mm to ±0.4mm or ±0.2% to ±0.4%. However, the reduced residual stress can lead to less distortion, which is beneficial for large or complex parts. Met3dp’s SEBM systems are engineered for high accuracy within the EBM process capabilities.
- Achieving Tighter Tolerances: For critical features, interfaces, or mating surfaces requiring tolerances tighter than the as-built capability, post-process machining is essential. Tolerances achievable with CNC machining (e.g., ±0.01mm to ±0.05mm) can be readily attained on specific features of an AM part.
- Lattice Strut Tolerance: Controlling the precise diameter of individual lattice struts is challenging. Variations can occur due to heat accumulation, powder particle size distribution, and laser/electron beam spot size variations. This variability impacts the effective mechanical properties and must be accounted for in design safety factors or controlled through rigorous process optimization.
Surface Finish (Roughness):
The as-built surface finish of metal AM parts is inherently rougher than machined surfaces due to the layer-wise construction and partially melted powder particles adhering to the surface.
- As-Built Surface Roughness (Ra):
- L-PBF: Typically ranges from 6 µm to 15 µm Ra, depending on material, layer thickness, orientation (upward-facing vs. downward-facing/supported surfaces), and process parameters.
- EBM/SEBM: Generally rougher than L-PBF, often in the range of 20 µm to 40 µm Ra, due to larger powder particle sizes and sintering effects.
- Impact of Roughness: High surface roughness can negatively impact fatigue life (acting as crack initiation sites), fluid flow (increased friction), and sealing capabilities.
- Förbättra ytfinishen: Various post-processing techniques are employed:
- Abrasive Blasting (Bead/Sand Blasting): Provides a uniform matte finish, typically improving Ra slightly (e.g., 5-10 µm Ra) and removing loose powder.
- Tumbling/Vibratory Finishing: Uses media to smooth surfaces, effective for external surfaces and accessible internal channels. Can achieve Ra values down to 1-3 µm.
- CNC Machining: Provides the best surface finish on specific features (down to < 1 µm Ra).
- Polishing (Manual/Electrochemical): Can achieve very smooth, mirror-like finishes but is often expensive and geometry-dependent. Electrochemical polishing can be effective for smoothing complex internal lattice surfaces if accessible.
- Lattice Surface Finish: Achieving a smooth finish inom a complex lattice structure is particularly challenging. The focus is often on ensuring good powder removal and potentially using processes like electrochemical polishing if high internal smoothness is required (e.g., for fluid flow).
Dimensional Accuracy & Metrology:
Ensuring the final part meets the specified dimensions and geometric tolerances (GD&T) requires robust metrology for AM.
- Factors Influencing Accuracy:
- Machine Calibration: Regular calibration of scanners, energy sources, and axes is crucial.
- Process Parameters: Laser/beam power, scan speed, layer thickness, and hatch strategy influence melt pool dynamics and solidification, affecting accuracy.
- Thermal Effects: Residual stress build-up during printing can cause warping and distortion, particularly in large or asymmetric parts. EBM/SEBM inherently minimizes this compared to L-PBF. Stress relief heat treatment is critical before removing parts from the build plate (especially for L-PBF).
- Stödstrukturer: Improperly designed supports can allow part movement or cause distortion during the build or removal.
- Pulverkvalitet: Consistent powder characteristics (particle size, shape, flowability) are vital for predictable melting and solidification. Met3dp’s focus on high-quality powder production contributes directly to dimensional consistency.
- Inspection Techniques:
- Coordinate Measuring Machines (CMMs): Used for high-precision measurement of external features and critical dimensions after post-processing (e.g., machining).
- 3D Scanning (Laser/Structured Light): Provide full-field comparisons of the manufactured part geometry against the original CAD model, identifying deviations and warping. Useful for inspecting complex external shapes.
- Computed Tomography (CT) Scanning: The primary method for non-destructively inspecting internal features, including lattice structure fidelity, strut integrity, internal defects (porosity), and verifying powder removal from complex internal channels. Essential for quality control aerospace components with internal lattices.
Achieving Precision in Practice:
Achieving tight metal AM tolerances aerospace requirements involves a holistic approach:
- DfAM: Design parts considering process limitations, minimize unsupported overhangs, plan for necessary machining stock on critical surfaces.
- Process Simulation: Simulate the build process to predict potential distortion and optimize build orientation and support strategies.
- Machine & Process Control: Use well-maintained, calibrated machines with optimized, validated process parameters for the specific material (AlSi10Mg, Ti-6Al-4V).
- Materialkvalitet: Use high-quality, consistent metal powders from reliable suppliers like Met3dp.
- Termisk hantering: Employ appropriate build plate heating and stress relief cycles.
- Strategic Post-Processing: Plan for necessary machining, HIP, and surface finishing steps.
- Rigorous Metrology: Implement appropriate inspection methods (CMM, 3D scanning, CT scanning) to verify conformance to specifications.
By carefully managing these factors, metal AM can produce complex lattice components that meet the demanding precision requirements of the aerospace industry. Collaboration between designers, manufacturing engineers, and quality assurance teams is key to success.
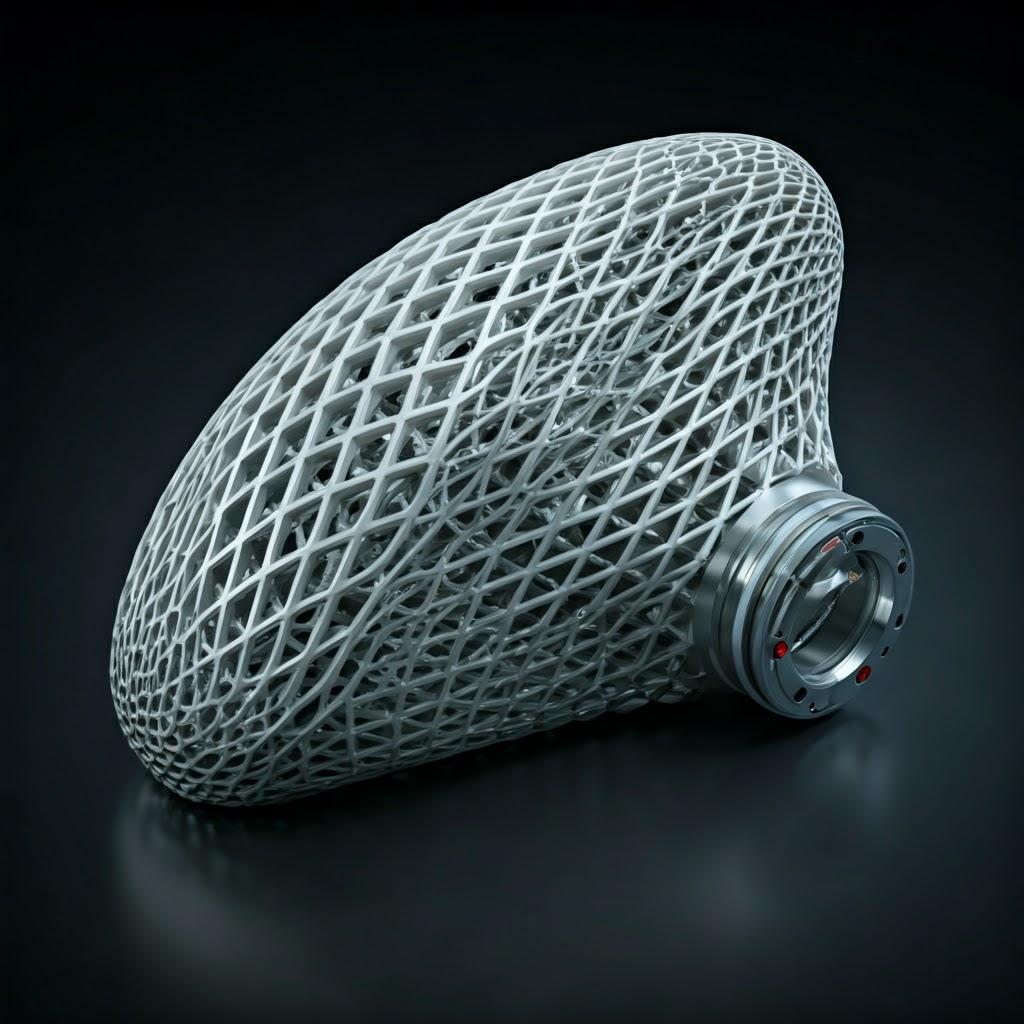
Essential Post-Processing Steps for Aerospace Lattice Components
Additive manufacturing rarely produces a finished part straight out of the machine, especially for demanding aerospace applications. A series of post-processing metal AM steps are typically required to achieve the desired material properties, dimensional accuracy, surface finish, and overall part integrity. These steps are particularly critical for lattice structures due to their complex geometries and the stringent requirements of flight-worthy components. Understanding these steps is crucial for estimating true manufacturing costs and lead times.
Common Post-Processing Workflow for AM Aerospace Parts (especially Lattices):
- Stress Relief Heat Treatment: This is often the first step after printing, especially for L-PBF parts, and is performed while the part is still attached to the build plate.
- Syfte: To reduce the high residual stresses generated during the rapid heating and cooling cycles of the layer-by-layer process. These stresses can cause warping, distortion (especially after removal from the build plate), and cracking.
- Process: Involves heating the part and build plate in a controlled atmosphere furnace (inert gas like Argon for Ti-6Al-4V, sometimes air for AlSi10Mg depending on the cycle) to a specific temperature below the alloy’s transformation point, holding it for a period, and then slowly cooling. Typical cycles:
- AlSi10Mg: Often stress relieved at around 250−300∘C. Note: This is distinct from the T6 aging treatment for strength.
- Ti-6Al-4V: Typically stress relieved at 600−800∘C.
- Importance for Lattices: The fine struts in lattices can be particularly susceptible to distortion if residual stresses are not managed.
- Part Removal from Build Plate: Once stress-relieved (if necessary), the part is separated from the build plate.
- Metoder: Typically done using wire EDM (Electrical Discharge Machining), sawing, or machining. Care must be taken not to damage the part.
- Borttagning av stödstruktur: AM parts often require support structures to anchor them to the build plate, support overhangs, and manage heat dissipation.
- Challenges with Lattices: Removing supports from intricate internal lattice geometries can be extremely difficult and labor-intensive. Supports might be needed inom the lattice structure itself.
- Metoder: Manual removal (breaking/cutting), CNC machining, EDM. Accessibility is key – DfAM plays a critical role here (designing for support access or using self-supporting lattice designs).
- Påverkan: Incomplete support removal can leave stress-raising remnants, while aggressive removal can damage the part surface. Processes like EBM/SEBM often require fewer dense supports, simplifying this step.
- Powder Removal (Depowdering): This is a critical and potentially challenging step for lattice structures. Unfused powder must be thoroughly removed from the intricate network of struts and nodes.
- Importance: Trapped powder adds weight, can compromise mechanical properties (especially fatigue), prevent effective heat treatment or HIP, and act as contamination.
- Metoder: Compressed air blow-off, vibration tables, ultrasonic cleaning baths, specialized powder recovery systems, potentially gentle chemical flushing for highly complex parts (requires careful material compatibility checks). CT scanning is often used to verify complete powder removal lattice.
- DfAM Link: Designing lattices with good interconnectivity and drainage paths is essential for effective depowdering.
- Het isostatisk pressning (HIP): Primarily used for Ti-6Al-4V and other high-performance alloys intended for critical applications.
- Syfte: To close internal microporosity (gas porosity, lack-of-fusion voids) that can remain after the AM process. This significantly improves mechanical properties, particularly fatigue strength, ductility, and fracture toughness, bringing them closer to wrought material properties.
- Process: Involves subjecting the part to high temperature (just below the melting point, e.g., ~900−950∘C for Ti-6Al-4V) and high isostatic pressure (using an inert gas like Argon, typically 100-200 MPa) simultaneously in a specialized HIP vessel.
- Benefit for Lattices: Enhances the reliability and fatigue performance of the load-bearing struts. HIPing titanium parts is standard practice for many flight-critical AM components.
- Consideration: HIP can cause minor dimensional changes (densification shrinkage) that need to be accounted for in the design phase (e.g., adding HIP compensation factors).
- Solution Annealing & Aging Heat Treatments (e.g., T6 for AlSi10Mg): Performed after HIP (if applicable) or other primary shaping steps to achieve the final desired material microstructure and mechanical properties (strength, hardness, ductility).
- Syfte: To optimize the metallurgical phase distribution. For AlSi10Mg, a T6 treatment (solutionize, quench, age) dissolves precipitates and then re-precipitates them finely to maximize strength. For Ti-6Al-4V, specific annealing cycles might be used to optimize strength vs. ductility trade-offs.
- Process: Requires precise control of temperature, time, and cooling rates in calibrated furnaces, often under vacuum or inert atmosphere for reactive alloys like Ti-6Al-4V.
- CNC Machining: Used to achieve tight tolerances and fine surface finishes on specific features.
- Applikationer: Mating surfaces, bearing bores, threaded holes, sealing faces, critical dimensions identified in the drawing.
- Överväganden: Requires careful fixture design to hold potentially complex AM parts without distortion. Sufficient machining stock must be included in the AM design on features requiring machining. CNC machining AM components requires expertise in handling near-net shape parts.
- Surface Finishing & Cleaning: Final steps to achieve the required surface condition.
- Metoder: Abrasive blasting, tumbling, polishing (as discussed under Tolerances & Surface Finish). Cleaning steps are vital to remove any machining fluids, blasting media, or residues before final inspection or coating.
- Surface Treatment Aerospace: Depending on the application, specific surface treatments like anodizing (for aluminum corrosion/wear resistance), conversion coatings, or painting may be required.
Post-Processing Sequence Example (Ti-6Al-4V Lattice):
- Build Completion (L-PBF or EBM/SEBM)
- Stress Relief (on build plate, esp. L-PBF)
- Part Removal from Plate
- Borttagning av stöd
- Powder Removal (Depowdering)
- Het isostatisk pressning (HIP)
- Final Heat Treatment (Annealing, if required)
- CNC Machining (of critical features)
- Surface Finishing (e.g., Bead Blasting)
- Final Cleaning & Inspection (including CT scan)
The complexity and necessity of each step depend heavily on the specific part design, material, AM process used, and application requirements. Partnering with a full-service provider like Met3dp, which understands the entire workflow from pulver to finished part, ensures that post-processing is appropriately planned and executed for optimal results.
Overcoming Common Challenges in Metal AM Lattice Production
While metal AM unlocks incredible potential for aerospace lattices, the technology is not without its challenges. Successfully producing reliable, flight-worthy lattice components requires anticipating and mitigating potential issues related to the manufacturing process, material behavior, and quality assurance. Addressing these metal AM challenges aerospace proactively is key to leveraging the benefits of the technology effectively.
Key Challenges and Mitigation Strategies:
- Residual Stress, Warping, and Distortion:
- Utmaning: Rapid, localized heating and cooling inherent in L-PBF processes generate significant internal stresses. These stresses can cause parts to warp during the build, distort after removal from the build plate, or even crack. Complex lattice geometries can exacerbate these issues due to uneven heat distribution.
- Mitigation:
- Process Simulation: Predict stress accumulation and distortion to optimize build orientation and support strategy.
- Build Plate Heating: Pre-heating the build plate (common in L-PBF, inherent in EBM/SEBM) reduces thermal gradients.
- Optimized Scan Strategies: Using techniques like island scanning or checkerboard patterns helps distribute heat more evenly.
- Appropriate Support Structures: Provide rigid anchoring and act as heat sinks.
- Immediate Stress Relief: Performing stress relief heat treatment before removing the part from the build plate is crucial for L-PBF.
- EBM/SEBM Advantage: The high build chamber temperature (~600−1000∘C) in EBM/SEBM processes significantly reduces residual stress, often eliminating the need for post-build stress relief and minimizing distortion, making it advantageous for large or complex lattice parts. Met3dp’s SEBM technology leverages this benefit.
- Support Structure Design and Removal:
- Utmaning: Supporting intricate internal lattice features can be difficult. Supports must be strong enough to prevent collapse or distortion but designed for removal without damaging the delicate lattice struts. Access for removal tools is often limited. Support removal intricate parts is a major bottleneck.
- Mitigation:
- DfAM: Design lattices with self-supporting angles (>45°) where possible. Choose unit cell types (e.g., TPMS) that are inherently more self-supporting. Orient the part to minimize downward-facing surfaces needing support.
- Optimized Support Design: Use easily breakable or dissolvable support types where feasible. Design supports with planned access points for tools.
- Process Selection: EBM/SEBM uses sintered powder as support, which is often easier to remove via blasting than the fully melted supports used in L-PBF.
- Post-Processing Expertise: Skilled technicians using appropriate tools (manual, micro-machining) are needed.
- Trapped Powder Removal:
- Utmaning: Ensuring complete removal of unfused powder from deep within complex, tortuous lattice structures is critical but difficult. Trapped powder adds weight, compromises density calculations, can sinter during heat treatment (blocking channels), and act as contamination.
- Mitigation:
- DfAM for Depowdering: Design interconnected porosity, avoid dead-end pockets, include strategically placed drainage/access holes.
- Optimized Unit Cells: Select cells with high connectivity (e.g., Octet-truss, Gyroid).
- Thorough Cleaning Procedures: Utilize multi-step processes involving vibration, rotation, compressed air/inert gas jets, potentially ultrasonic cleaning or gentle flushing.
- Verification: Use methods like weighing the part, endoscopy (if possible), and crucially, CT scanning to confirm complete powder removal.
- Porosity Control and Achieving Full Density:
- Utmaning: Small internal voids (gas porosity from dissolved gas in the powder, or lack-of-fusion voids from incomplete melting) can remain after printing. Porosity significantly degrades mechanical properties, especially fatigue life. Porosity control AM is vital for critical parts.
- Mitigation:
- High-Quality Powder: Use powders with low internal gas porosity, controlled particle size distribution, and high sphericity/flowability. Met3dp’s advanced gas atomization and PREP technologies are designed to produce such high-quality powders.
- Optimized Process Parameters: Develop and validate robust parameter sets (laser/beam power, speed, layer thickness, hatch spacing) for the specific material and machine to ensure complete melting and fusion between layers.
- Inert Atmosphere/Vacuum: Maintain high purity inert gas atmosphere (L-PBF) or high vacuum (EBM/SEBM) during printing to minimize contamination and gas pickup.
- Het isostatisk pressning (HIP): The most effective method to eliminate remaining microporosity, especially for fatigue-critical Ti-6Al-4V parts.
- Fatigue Life Prediction and Validation:
- Utmaning: Predicting the fatigue life lattice structures is complex due to intricate geometries, potential stress concentrations at nodes, influence of surface roughness, and sensitivity to defects. Traditional fatigue analysis methods may not be directly applicable.
- Mitigation:
- High-Fidelity FEA: Use detailed models that capture strut-level stress states, considering potential geometric variability.
- Conservative Design: Apply appropriate safety factors, particularly accounting for surface finish effects.
- Post-Processing for Fatigue: Implement HIP (especially for Ti64) and surface finishing techniques known to improve fatigue performance.
- Extensive Testing: Conduct rigorous fatigue testing on representative lattice coupons (under relevant loading conditions – tension, compression, shear, bending) and potentially component-level tests to validate design predictions and process reliability.
- Qualification and Certification:
- Utmaning: Meeting the stringent qualification and certification requirements of the aerospace industry (e.g., FAA, EASA regulations, standards like AS9100) for AM parts, especially flight-critical ones, is a significant hurdle. Demonstrating process stability, repeatability, and robust quality control is essential.
- Mitigation:
- Process Control & Monitoring: Implement rigorous controls over machine parameters, material handling, atmosphere, and post-processing steps. Utilize in-situ monitoring techniques where available.
- Robust Quality Management System (QMS): Adhere to aerospace standards like AS9100. Maintain detailed documentation and traceability throughout the manufacturing process.
- Material & Process Specifications: Develop and lock down detailed specifications for powders and manufacturing procedures.
- Icke-förstörande testning (NDT): Employ comprehensive NDT methods (CT scanning is crucial for internal integrity, FPI/MPI for surface defects after machining).
- Partnering with Certified Suppliers: Work with experienced metal 3D printing service aerospace providers like Met3dp who understand and meet aerospace quality requirements, potentially holding relevant certifications or demonstrating equivalent QMS rigor. Visiting the Om oss page can provide insights into a company’s commitment to quality and expertise.
Addressing these challenges requires a combination of advanced design techniques, precise process control, rigorous post-processing, thorough inspection, and often, close collaboration with experienced AM service providers and material suppliers. By understanding and mitigating these potential issues, the aerospace industry can confidently adopt metal AM lattices to achieve significant performance improvements.
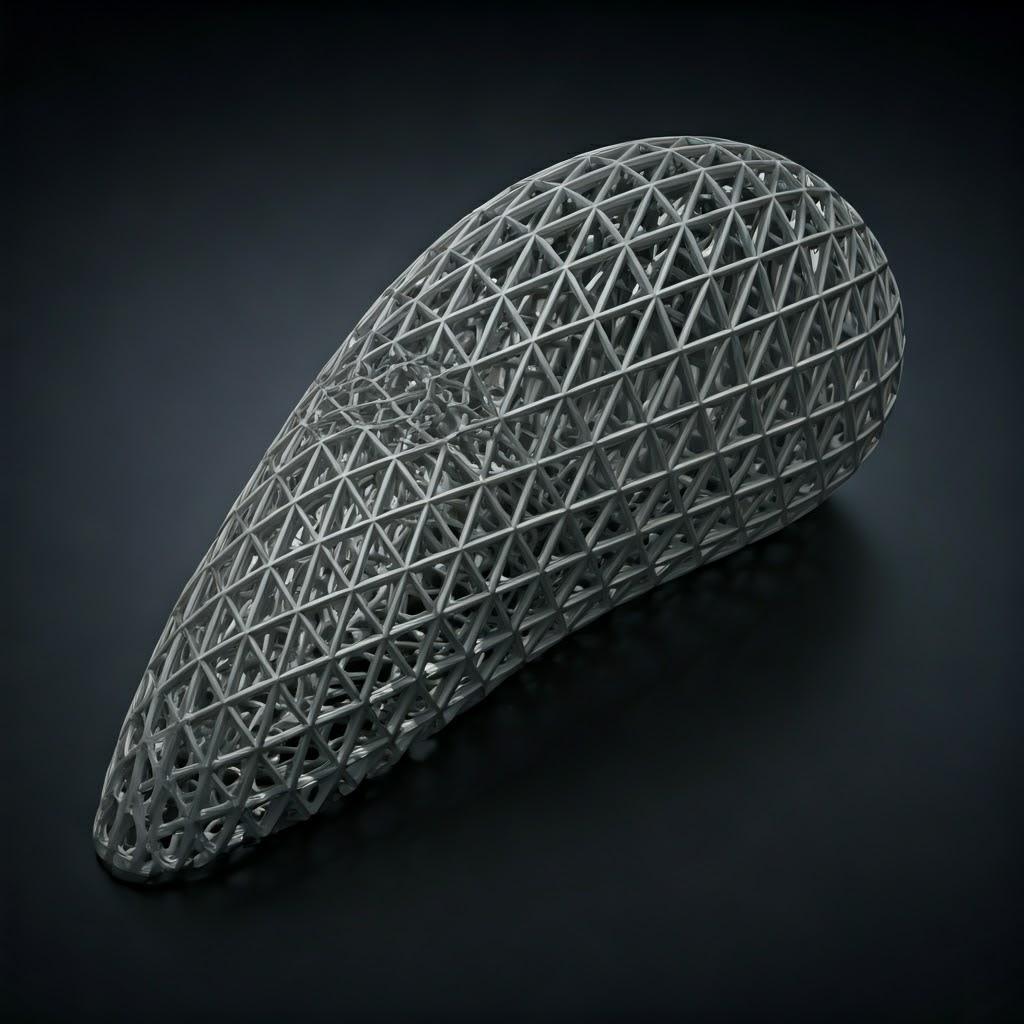
Selecting the Right Metal AM Service Provider for Aerospace Lattice Projects
Choosing the right manufacturing partner is paramount when dealing with critical aerospace components, especially those involving complex geometries like lattice structures produced via metal additive manufacturing. The unique challenges and stringent requirements of the aerospace sector necessitate a provider with specific expertise, certified processes, and a deep understanding of both AM technology and aerospace quality standards. Simply having a metal 3D printer is not enough. Procurement managers and engineering teams looking to source aerospace lattice components must conduct thorough due diligence to evaluate AM providers. Selecting an inadequate supplier can lead to project delays, cost overruns, subpar part quality, and potentially catastrophic failures.
Key Criteria for Evaluating Metal AM Service Providers for Aerospace Lattices:
- Aerospace Certifications and Quality Management System (QMS):
- AS9100 Certification: This is the gold standard QMS for the aviation, space, and defense industries. An AS9100 certified AM supplier demonstrates a commitment to rigorous process control, traceability, risk management, and continuous improvement aligned with aerospace requirements. While not all capable suppliers may hold the certification (especially newer or smaller ones), they must demonstrate an equivalent level of QMS maturity.
- NADCAP Accreditation: For specific special processes like heat treatment, NDT, or welding (if applicable to post-processing), NADCAP accreditation is often required by aerospace primes.
- Robust Internal QMS: Even without formal certification, the provider should have a well-documented QMS covering material handling, machine operation, process validation, operator training, equipment calibration, non-conformance management, and corrective/preventive actions.
- Proven Experience with Aerospace Projects and Lattice Structures:
- Track Record: Look for demonstrated experience in successfully delivering AM parts (ideally lattice structures) for aerospace applications. Case studies, references, and examples of past projects are valuable indicators.
- Lattice Expertise: Ask about their specific experience with designing, simulating, printing, and post-processing lattice structures. Do they understand the nuances of unit cell selection, DfAM for lattices, support strategies, and powder removal for these specific geometries?
- Understanding of Aerospace Requirements: The provider must understand aerospace documentation needs, material specifications (e.g., AMS standards), testing requirements, and the importance of process repeatability.
- Material Expertise and Control:
- Relevant Materials: Ensure the provider has proven experience processing the specific materials required (e.g., AlSi10Mg aerospace applications, aerospace grade titanium like Ti-6Al-4V). This includes validated process parameters for achieving desired densities and mechanical properties.
- Powder Sourcing and Quality Control: How do they source their metal powders? Do they have stringent incoming inspection procedures? Do they manage powder traceability, storage, handling, and recycling protocols to prevent contamination and ensure consistency? Providers like Met3dp, who manufacture their own high-quality powders using advanced methods like Gas Atomization and PREP, offer a significant advantage in material control and consistency.
- Portfolio Breadth: While specialized expertise is good, a provider with a broader portfolio of aerospace-relevant materials might offer more flexibility for future projects.
- Equipment Capabilities and Technology:
- Appropriate AM Technology: Do they operate the right type of machines (L-PBF, EBM/SEBM) for your application and material? EBM/SEBM, offered by Met3dp capabilities, can be advantageous for Ti-6Al-4V lattices due to reduced stress and support needs.
- Machine Fleet: Consider the number, age, condition, and build volume of their machines. A larger, well-maintained fleet suggests higher capacity, redundancy, and potentially better lead times. Look for industry-leading equipment known for reliability and accuracy.
- Process Monitoring: Do their machines incorporate in-situ monitoring capabilities (e.g., melt pool monitoring, thermal imaging)? This can provide valuable data for quality assurance.
- Design for Additive Manufacturing (DfAM) Support:
- Engineering Services: Does the provider offer DfAM expertise? Can they assist with topology optimization, lattice design, build simulation, and support strategy development? A collaborative aerospace AM partner who can provide design feedback is invaluable, especially for teams new to AM.
- Software Tools: Are they proficient with industry-standard CAD, CAM, simulation, and lattice generation software?
- Comprehensive Post-Processing Capabilities:
- In-House vs. Outsourced: Does the provider have in-house capabilities for critical post-processing steps like stress relief, heat treatment (in calibrated, atmosphere-controlled furnaces), HIP (or strong relationships with certified HIP providers), CNC machining, support/powder removal, and surface finishing? Relying heavily on external subcontractors can add complexity, lead time, and risk.
- Expertis: Do they have documented procedures and skilled personnel for these operations, particularly challenging tasks like powder removal from complex lattices?
- Metrology and Inspection Capabilities:
- Essential Equipment: Ensure they possess the necessary inspection tools, including CMMs, 3D scanners, and crucially for internal lattice inspection, Computed Tomography (CT) scanning.
- NDT Expertise: Qualified personnel for Non-Destructive Testing (NDT) interpretation are essential.
- Reporting: Can they provide comprehensive inspection reports documenting dimensional accuracy, internal integrity, and conformance to specifications?
- Project Management and Communication:
- Clear Communication: Look for responsive communication, clear quoting processes, and regular project updates.
- Dedicated Point of Contact: A dedicated project manager or engineer can streamline interactions.
- Transparency: Willingness to discuss challenges openly and collaborate on solutions.
- Supply Chain Management and Scalability:
- Capacity: Can they handle your required production volumes, both now and potentially for future scaling?
- Risk Management: What are their contingency plans for equipment downtime or other disruptions?
Evaluating Potential Partners Table:
Evaluation Criterion | Key Questions to Ask | Why It Matters for Aerospace Lattices | Ideal Provider Attributes (e.g., Met3dp) |
---|---|---|---|
Certifications & QMS | AS9100 certified? Robust QMS documentation? NADCAP for special processes? | Ensures process control, repeatability, traceability critical for flight safety. | AS9100 or equivalent QMS, commitment to aerospace quality standards. |
Aerospace & Lattice Experience | Examples of aerospace projects? Specific lattice experience? Understanding of AMS specs, testing? | Demonstrates capability to meet industry demands and handle geometric complexity. | Proven track record, deep understanding of lattice DfAM & manufacturing challenges. |
Materialexpertis | Experience with required alloys (AlSi10Mg, Ti-6Al-4V)? Validated parameters? Powder QC procedures? | Guarantees correct material properties and process reliability. | Expertise in target materials, control over powder quality (in-house production like Met3dp is a plus). |
Equipment & Technology | L-PBF/EBM? Build volume? Machine condition/calibration? In-situ monitoring? | Ensures parts can be built accurately, efficiently, and with appropriate technology (e.g., EBM for Ti64). | State-of-the-art, well-maintained machines (e.g., Met3dp’s SEBM printers); suitable build volumes. |
DfAM Support | Offer design optimization/simulation? Provide manufacturability feedback? | Optimizes part performance and ensures designs are producible efficiently. | Strong engineering support, collaborative approach to DfAM. |
Efterbearbetning | In-house heat treat, HIP access, CNC, depowdering, finishing? Expertise in these areas? | Ensures end-to-end quality control, reduces lead time/risk. Critical for achieving final properties. | Comprehensive in-house or tightly controlled external post-processing capabilities. |
Metrology & Inspection | CMM, 3D scanning, CT scanning available? NDT expertise? Comprehensive reporting? | Verifies dimensional accuracy and internal integrity (crucial for lattices). | Advanced metrology including CT scanning, robust inspection protocols. |
Project Management | Clear communication? Dedicated contact? Transparency? | Facilitates smooth project execution and problem-solving. | Professional project management, responsive communication. |
Scalability & Supply Chain | Capacity for current/future volume? Risk management plans? | Ensures reliable supply for production needs. | Sufficient capacity, robust supply chain practices. |
Export to Sheets
Välja rätt metal 3D printing service aerospace provider is a strategic decision. Companies like Met3dp, which offer an integrated solution encompassing advanced powder manufacturing, industry-leading printing equipment (like SEBM), application development services, and a strong focus on quality, represent the type of comprehensive partner needed to successfully implement demanding aerospace lattice projects. Investing time in thorough supplier evaluation significantly increases the likelihood of project success.
Understanding Cost Drivers and Lead Times for AM Lattice Structures
While metal additive manufacturing enables revolutionary designs like lattice structures, it’s essential to have a realistic understanding of the associated costs and production timelines. These factors are influenced by a complex interplay of design choices, material selection, processing steps, and quality requirements. Accurately estimating metal AM cost aerospace projects and managing lead time additive manufacturing expectations is crucial for budgeting, planning, and determining the economic viability compared to traditional methods.
Major Cost Drivers for Metal AM Lattice Components:
- Material Type and Volume:
- Kostnad för pulver: Raw material costs vary significantly. Aerospace-grade titanium alloys (Ti-6Al-4V) are substantially more expensive per kilogram than aluminum alloys (AlSi10Mg) or stainless steels. Nickel superalloys are even more costly. High-quality, AM-optimized powders from reputable suppliers also command a premium but ensure better consistency and performance.
- Part Volume/Mass: The sheer amount of material used directly impacts cost. While lattices reduce mass compared to solid parts, the cost is based on the final printed volume (including supports) and potentially the amount of powder consumed/recycled within the build chamber.
- Support Material Volume: The volume of material used for support structures adds to the cost, as it consumes powder and machine time and requires removal labor. Designing for minimal supports is economically beneficial.
- Machine Time (Build Time): This is often the most significant cost factor.
- Build Height: AM is layer-based, so taller parts take longer to print, regardless of their cross-section. Maximizing the number of parts nested within a single build height (platform utilization) is key to reducing per-part machine time cost.
- Part Volume & Density: Printing denser sections or larger overall volumes takes longer as more material needs to be melted/sintered per layer. Lattice density directly impacts this – lower density lattices print faster than higher density ones, assuming the same bounding volume.
- Number of Parts per Build: Printing multiple parts simultaneously on one build plate amortizes setup time and maximizes machine utilization.
- Machine Type and Parameters: Different machines (L-PBF vs. EBM/SEBM) and specific process parameters (layer thickness, scan speed) influence build speed. Thicker layers generally print faster but may compromise resolution and surface finish.
- Kostnader för arbetskraft:
- Setup & Teardown: Preparing the machine, loading powder, setting up the build file, and then removing the build plate, cleaning the machine, and unpacking parts requires skilled labor.
- Post-Processing Labor: This can be substantial, especially for complex lattices. Manual support removal, powder removal from intricate internal channels, surface finishing, and inspection all require technician time. The difficulty of support/powder removal for lattices is a major labor cost driver.
- Delkomplexitet:
- Geometric Complexity: While AM handles complexity well, highly intricate designs may require more support structures, potentially slower print speeds for fine features, and significantly more effort in post-processing (support/powder removal) and inspection (e.g., complex CT scan analysis).
- Fine Features: Very small struts or thin walls may require specialized parameters or slow down the build.
- Krav på efterbearbetning: Each step adds cost.
- Heat Treatment (Stress Relief, Aging, Annealing): Requires furnace time, energy, and controlled atmospheres.
- Het isostatisk pressning (HIP): A specialized, high-cost process involving expensive equipment and long cycle times. Often essential for critical titanium parts, adding significantly to the piece price.
- CNC Machining: Machining specific features adds cost based on complexity, tolerances, and material machinability.
- Ytbehandling: Techniques like polishing or electrochemical polishing can be labor-intensive and costly.
- Quality Assurance and Inspection:
- Level of Inspection: Basic dimensional checks are standard. More rigorous inspection involving CMM, 3D scanning, and particularly CT scanning for internal lattice integrity adds significant cost due to equipment time and analysis labor.
- Documentation: Generating the extensive documentation required for aerospace traceability and qualification adds overhead.
- Development and Engineering (NRE): Non-recurring engineering costs for design optimization, simulation, process development, and initial qualification builds can be substantial, especially for novel applications.
Factors Influencing Lead Times:
- Prototyping vs. Production: Prototypes can often be produced relatively quickly (days to a few weeks) if machine time is available and post-processing is minimal.
- Byggtid: As discussed, build height, part volume/density, and platform utilization are key drivers. A tall, dense part can take many days or even weeks to print.
- Machine Availability: Queue times at service providers can significantly impact lead times.
- Post-Processing Complexity: Extensive post-processing, especially manual support/powder removal, HIP cycles (which can take a day or more), and multi-axis CNC machining, adds considerable time. Powder removal from complex lattices can be a major bottleneck.
- Kvalitetssäkring: Thorough inspection and documentation cycles add time.
- Batchstorlek: Larger production batches may have longer overall lead times but potentially shorter per-part times if builds are optimized.
- Supply Chain: Availability of specific powder grades or delays at external post-processing suppliers (e.g., HIP facilities) can impact timelines.
Lead Time Estimates (Illustrative):
Etapp | Typical Duration (Simple Part) | Typical Duration (Complex Lattice, e.g., Ti64 with HIP) | Anteckningar |
---|---|---|---|
Quoting & Setup | 1-3 dagar | 2-5 dagar | Depends on complexity, provider responsiveness. |
Build Planning | <1 day | 1-2 dagar | Orientation, support design, nesting. |
Tryckning | 1-3 dagar | 3-10+ days | Highly variable based on size, density, machine. |
Stressavlastning | <1 day | <1 day | If required (esp. L-PBF). |
Removal/Depowder | <1 day | 1-3+ days | Powder/support removal for lattices can be very time-consuming. |
HIP | N/A | 2-4 days | Includes shipping to/from HIP provider if outsourced, plus cycle time. |
Värmebehandling | 1 day | 1-2 dagar | Furnace cycle times. |
Maskinbearbetning | 1-2 dagar | 2-5 dagar | Depends on complexity and number of features. |
Efterbehandling | <1 day | 1-2 dagar | E.g., blasting, tumbling. |
Inspection (QA) | <1 day | 1-3 dagar | CT scanning and analysis take time. |
Total (Approx.) | ~ 1-2 weeks | ~ 3-6+ weeks | Highly dependent on specifics, assumes no major queues/delays. |
Export to Sheets
Cost Comparison Considerations:
While the per-part cost of metal AM can be higher than traditional manufacturing for simple parts produced in high volumes, the equation changes for complex geometries like lattices, especially in aerospace:
- Value of Lightweighting: Reduced weight translates to significant lifetime fuel savings or increased payload capacity, often justifying a higher initial component cost.
- Del Konsolidering: Reducing part count saves on assembly labor, inventory, and potential failure points.
- Performance Gains: Enhanced thermal management or energy absorption enabled by lattices can provide performance benefits unattainable with traditional designs.
- Lead Time for Complex Parts: For highly complex parts, AM can sometimes offer shorter lead times than sourcing multiple components and complex assemblies or waiting for specialized tooling (e.g., investment casting molds).
Understanding these cost and lead time dynamics allows for informed decisions about when and where to apply metal AM for aerospace lattice structures, often revealing a strong business case despite potentially higher upfront per-part costs compared to simpler, conventionally manufactured alternatives. Engaging with experienced providers like Met3dp early in the design process can help optimize for cost and manufacturability.
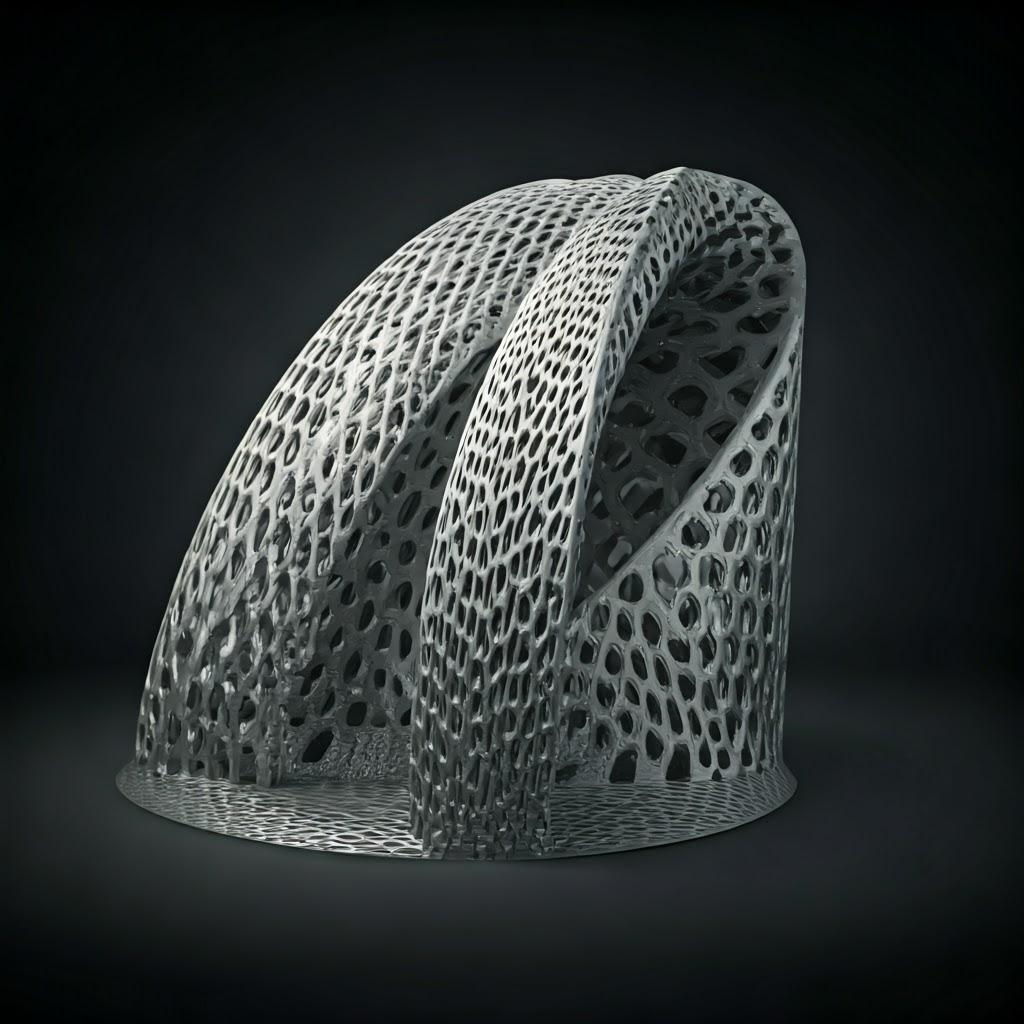
FAQ: Metal AM for Aerospace Lattice Structures
Here are answers to some frequently asked questions regarding the use of metal additive manufacturing for aerospace lattice structures:
1. How strong are 3D printed metal lattices compared to solid parts or traditionally manufactured components?
- Svar: This depends heavily on the lattice design (unit cell, density) and the material used. On a per-weight basis, optimized lattice structures made from materials like Ti-6Al-4V via AM can exhibit exceptionally high specific strength and stiffness, often exceeding that of solid material or traditionally manufactured components designed for the same function but carrying more weight. However, the absolute strength of a lattice structure is typically lower than a solid block of the same overall dimensions because it contains significantly less material. The key benefit is achieving the required strength and stiffness for a specific load case with dramatically reduced weight. Post-processing steps like HIP are crucial, especially for fatigue-critical Ti-6Al-4V parts, to minimize defects and maximize strength, bringing properties closer to wrought material standards. Rigorous simulation (FEA) and experimental testing are essential to validate the strength and fatigue life of any specific lattice design for its intended application.
2. How do you ensure quality and remove all the unfused powder from deep inside complex internal lattice structures?
- Svar: Quality assurance for internal lattice features relies heavily on a combination of process control and advanced inspection techniques.
- Processtyrning: Using high-quality, consistent powder (like those produced by Met3dp), validated machine parameters, and maintaining a controlled build environment minimizes defects like porosity.
- Powder Removal: This requires careful DfAM (designing for drainage, using interconnected cells), optimized build orientation, and meticulous post-processing procedures (vibration, compressed air/gas jets, potentially ultrasonic cleaning). Access holes designed into the part are often necessary.
- Verification: Computed Tomography (CT) scanning is the primary non-destructive method used to verify the internal geometric fidelity of the lattice struts, check for internal defects (voids, cracks), and, crucially, confirm that all unfused powder has been successfully removed from the internal channels. Comparing the part’s weight to the theoretical weight can also provide an indication, but CT scanning offers definitive visual confirmation.
3. Is metal additive manufacturing (AM) cost-effective for producing aerospace lattice components, especially for production runs?
- Svar: Cost-effectiveness depends on several factors and requires a total value assessment, not just per-part cost comparison.
- Komplexitet: AM excels at producing complex geometries like lattices that are difficult or impossible to make traditionally. For such parts, AM can be the only viable manufacturing method, making it cost-effective by default if the functionality is required.
- Lightweighting Value: In aerospace, weight savings have significant economic value over the aircraft’s lifetime (fuel savings) or enable higher performance/payload. This often justifies a higher initial component cost for AM lattice parts.
- Del Konsolidering: Replacing multi-part assemblies with a single AM component reduces assembly labor, fasteners, inventory, and potential failure points, contributing to overall cost savings.
- Volym: For very high production volumes of relatively simple parts, traditional methods like casting or machining are often cheaper. However, for low-to-medium volumes, or where tooling costs for traditional methods are very high, AM can be competitive, especially considering it avoids tooling costs and allows for design updates.
- Ledtid: AM can sometimes offer faster routes to finished complex parts compared to traditional methods involving complex tooling or assembly.
- Optimization: As AM technology matures, costs are decreasing due to faster machines, better software, and improved powder production. Therefore, while maybe not the cheapest option for all parts, metal AM cost aerospace calculations often show significant value and cost-effectiveness for complex, performance-critical components like optimized lattices, especially when considering the total lifecycle benefits.
4. What specific challenges exist for qualifying and certifying metal AM lattice parts for flight-critical aerospace applications?
- Svar:Metal AM qualification aerospace for flight-critical parts, including lattices, faces challenges related to demonstrating consistency, reliability, and understanding failure modes. Key hurdles include:
- Process Repeatability: Ensuring that every part produced has identical properties requires extremely tight control over all process variables (machine, material, parameters, post-processing).
- Material Property Database: Establishing comprehensive databases for the properties of AM materials (especially fatigue, fracture toughness) under various conditions, including the influence of lattice geometry and surface finish, is ongoing.
- NDT for Complex Geometries: Reliably detecting critical defects deep within intricate lattice structures using NDT methods (even CT scanning has resolution limits) requires specialized techniques and expertise.
- Standardisering: While standards for AM processes and materials are developing rapidly (ASTM, ISO, AMS), they are still evolving, particularly for complex structures like lattices.
- Lack of Historical Data: Compared to traditional manufacturing methods with decades of in-service history, AM is relatively new, requiring more extensive initial testing and analysis to build confidence.
- Mitigation: Addressing these challenges involves robust process control, rigorous testing (coupons and full components), advanced simulation, thorough NDT, adherence to emerging standards, and close collaboration between designers, manufacturers (like Met3dp, focused on quality and process control), and certification authorities.
Conclusion: The Future of Aerospace Design with Lattice-Optimized Metal AM Parts
Metal additive manufacturing is not merely an alternative production method; it is a transformative force reshaping the landscape of aerospace design and manufacturing. The ability to create intricate, lightweight, and multifunctional lattice structures from high-performance alloys like AlSi10Mg and Ti-6Al-4V represents a significant leap forward, enabling engineers to overcome traditional constraints and achieve unprecedented levels of performance and efficiency.
As we’ve explored, the benefits metal AM lattice components offer are compelling: dramatic weight reduction through structural optimization, the potential for part consolidation simplifying assemblies, and the integration of functionalities like enhanced thermal management and energy absorption within a single component. These advantages translate directly into tangible benefits for the aerospace industry – lower fuel consumption, increased payload capacity, extended range, improved maneuverability, and reduced environmental impact.
However, realizing this potential requires a holistic approach. Success hinges on embracing DfAM principles tailored for lattices, selecting the appropriate high-quality materials, implementing meticulous process control during manufacturing, executing critical post-processing steps like heat treatment and HIP, and employing rigorous quality assurance methodologies, including advanced NDT like CT scanning. Overcoming challenges related to residual stress, support and powder removal, and fatigue life prediction necessitates expertise and collaboration.
Choosing the right manufacturing partner is crucial. Look for providers with proven aerospace experience, robust quality systems (like AS9100 certification), deep material and process knowledge, comprehensive capabilities spanning DfAM to post-processing and inspection, and a commitment to quality. Companies like Met3dp, with their integrated expertise in advanced powder manufacturing, cutting-edge SEBM printing technology, and application support, exemplify the type of partner needed to navigate the complexities and unlock the full value of metal AM for aerospace. Their focus on producing high-quality spherical powders and reliable printing systems provides a solid foundation for manufacturing demanding aerospace components.
The journey towards widespread adoption of AM lattice structures in flight-critical applications involves ongoing research, standardization efforts, and continuous improvements in technology and process control. Yet, the trajectory is clear. Lattice-optimized components produced via metal AM are moving beyond prototypes and niche applications towards mainstream use in next-generation aircraft, spacecraft, satellites, and UAVs. They represent the future aerospace manufacturing paradigm – one defined by optimized performance, increased efficiency, and unparalleled design freedom.
For engineers and procurement managers aiming to push the boundaries of aerospace innovation, metal additive manufacturing with lattice structures offers a powerful toolkit. By partnering with knowledgeable and capable suppliers, the aerospace industry can continue to leverage this technology to build lighter, faster, stronger, and more sustainable flight systems.
Ready to explore how lattice-optimized metal AM parts can elevate your next aerospace project? Besök Met3dp.com to learn more about our advanced SEBM printers, high-performance metal powders, and comprehensive additive manufacturing solutions, or contact our team of experts today to discuss your specific application requirements. Let’s build the future of aerospace, together.
Dela på
MET3DP Technology Co, LTD är en ledande leverantör av lösningar för additiv tillverkning med huvudkontor i Qingdao, Kina. Vårt företag är specialiserat på 3D-utskriftsutrustning och högpresterande metallpulver för industriella tillämpningar.
Förfrågan för att få bästa pris och anpassad lösning för ditt företag!
Relaterade artiklar
Om Met3DP
Senaste uppdateringen
Vår produkt
KONTAKTA OSS
Har du några frågor? Skicka oss meddelande nu! Vi kommer att betjäna din begäran med ett helt team efter att ha fått ditt meddelande.
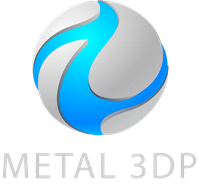
Metallpulver för 3D-printing och additiv tillverkning