Satellite Mounting Frames with Precision Additive Manufacturing
Innehållsförteckning
Introduction: The Critical Role of Satellite Mounting Frames in Space Missions
Satellites, the unsung heroes of modern communication, navigation, Earth observation, and scientific discovery, operate in one of the most hostile environments imaginable: space. Subjected to violent launch vibrations, extreme temperature fluctuations, vacuum conditions, and radiation exposure, every component within a satellite must perform flawlessly. Among the most critical, yet often overlooked, are the satellite mounting frames. These structures form the backbone upon which essential and often delicate payloads – antennas, sensors, cameras, electronics, solar panels – are precisely mounted, aligned, and protected.
Traditionally, manufacturing these frames involved subtractive methods like CNC machining, often starting with large blocks of metal and carving away material. While effective, this approach faces limitations in terms of design complexity, material waste (buy-to-fly ratio), and achieving optimal weight reduction – a paramount concern in aerospace where every gram saved translates into significant launch cost reductions or increased payload capacity.
Skriva in metalltillsatstillverkning (AM), commonly known as metal 3D-utskrifter. This transformative technology is rapidly reshaping how high-performance components, including satellite mounting frames, are designed and produced. By building parts layer by layer directly from fine metal powders like Scalmalloy® -legering och AlSi10Mg, AM unlocks unprecedented design freedom, enables significant lightweighting through topology optimization, and allows for the consolidation of multiple parts into a single, complex component. This shift isn’t just about making parts differently; it’s about making bättre parts – lighter, stronger, more integrated, and often, faster to prototype and produce.
The demands for satellite hardware are exacting:
- Extreme Lightweighting: Reducing mass without compromising structural integrity is crucial for launch economics and mission performance.
- High Stiffness and Strength: Frames must withstand launch G-forces and maintain precise alignment of sensitive instruments in orbit.
- Termisk stabilitet: Materials must perform reliably across vast temperature ranges experienced in space.
- Reliability: Components must function perfectly for the mission duration, often spanning years or decades without possibility of repair.
- Anpassning: Each satellite mission often requires bespoke frame designs tailored to specific payloads and bus architectures.
Meeting these challenges requires advanced manufacturing solutions. Companies specializing in metal additive manufacturing for aerospace, som Met3dp, are at the forefront of this revolution. Leveraging industry-leading printing technologies, advanced powder metallurgy, and deep application expertise, Met3dp provides the capabilities needed to produce mission-critical satellite components that push the boundaries of performance and efficiency. This article delves into the specifics of using metal AM for satellite mounting frames, exploring applications, the advantages over traditional methods, recommended materials, and key considerations for engineers and procurement managers in the space industry.
What Are Satellite Mounting Frames Used For? Key Applications and Functions
Satellite mounting frames are bespoke structural elements designed to securely hold, precisely align, and environmentally protect various subsystems and payloads within a satellite. Their design is intrinsically linked to the satellite’s overall architecture, mission objectives, and the specific requirements of the components they support. Procurement managers sourcing custom satellite hardware and engineers designing aerospace component integration strategies recognize the pivotal role these frames play.
Key Applications:
- Optics and Sensor Mounting: High-precision telescopes, Earth observation cameras, star trackers, and scientific sensors demand exceptionally stable and accurately aligned mounting structures. These frames must minimize distortion from thermal changes or micro-vibrations. AM allows for complex, stiff, and thermally stable designs.
- Antenna Mounting: Communication antennas (ranging from small telemetry antennas to large deployable reflectors) require rigid frames to maintain pointing accuracy. AM enables the integration of features like waveguides or thermal straps directly into the frame structure.
- Solar Panel Deployment Mechanisms: Frames often form part of the hinge and deployment systems for solar arrays, requiring high strength and reliability over numerous cycles. Lightweighting is particularly critical here.
- Electronics Housing and Mounting: Avionics boxes, power distribution units, and onboard computers are mounted using frames that provide structural support, thermal pathways (heat sinking), and sometimes RF shielding. AM allows for conformal shapes and integrated thermal management features.
- Propulsion System Components: Mounting brackets for thrusters, propellant tanks, and associated valves and plumbing must withstand significant vibration and stress. AM can produce robust, lightweight brackets optimized for specific load paths.
- Payload Integration: Supporting diverse scientific instruments or mission-specific payloads often requires highly customized frames that fit within tight volume constraints while providing necessary stiffness and environmental isolation.
Core Functional Requirements:
Beyond simply holding components, these frames serve critical functions:
- Structural Support: They are primary load-bearing elements, transferring static and dynamic loads (launch vibration, maneuvering forces) from the mounted component to the main satellite bus structure. Stiffness is often a key design driver to maintain alignment and prevent detrimental deflections.
- Precise Alignment: Many satellite payloads, particularly optical instruments and antennas, require alignment accuracy measured in arcseconds or micrometers. The mounting frame is fundamental to achieving and maintaining this precision throughout the mission lifetime.
- Vibration Damping/Isolation: Frames can be designed to isolate sensitive components from the harsh vibration environment experienced during launch and satellite operations (e.g., reaction wheel disturbances). AM allows for complex geometries that can enhance damping characteristics.
- Thermal Management Integration: Frames often act as conductive pathways to dissipate heat generated by electronics or absorb heat from external sources. AM enables the creation of integrated cooling channels, optimized thermal straps, or surfaces designed for specific radiative properties, enhancing satellite subsystems integration.
- Electrical Grounding and Shielding: Frames typically provide electrical grounding paths and can contribute to electromagnetic interference (EMI) shielding for sensitive electronics.
The need for custom satellite hardware suppliers capable of producing these complex, mission-specific frames efficiently is driving the adoption of additive manufacturing. AM’s ability to create bespoke, optimized designs without the traditional constraints of tooling and machining makes it an ideal fit for the diverse and demanding world of satellite manufacturing.
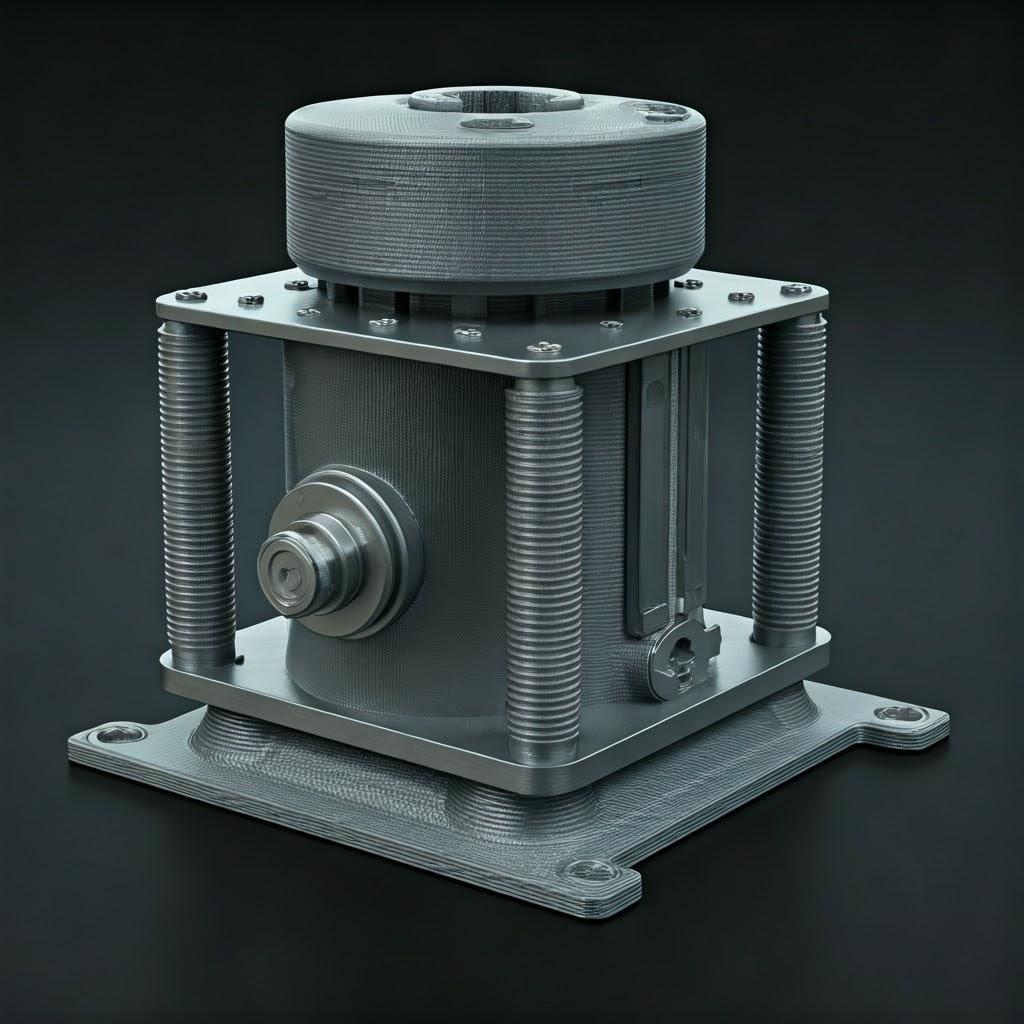
Why Use Metal 3D Printing for Satellite Mounting Frames? Advantages Over Traditional Methods
The decision to adopt 3D-utskrift av metall for critical components like satellite mounting frames stems from a compelling set of advantages over traditional subtractive manufacturing, primarily CNC machining. While CNC machining remains a vital technology in aerospace, AM offers unique capabilities that directly address the core challenges of satellite design: weight reduction, complexity, and rapid development cycles. For procurement teams evaluating aerospace additive manufacturing benefits, the value proposition is becoming increasingly clear.
Let’s compare AM (specifically Laser Powder Bed Fusion – LPBF, a common process for high-resolution metal parts) with CNC machining for producing satellite frames:
Funktion | Metal Additive Manufacturing (e.g., LPBF) | Traditional CNC Machining (Subtractive) | Advantage for Satellite Frames |
---|---|---|---|
Designfrihet | High: Enables complex geometries, internal channels, organic shapes. | Moderate: Limited by tool access, fixturing, multi-axis capabilities. | Allows topology optimization for space, creating highly efficient, lightweight structures impossible to machine. |
Lättvikt | Excellent: Topology optimization, lattice structures reduce mass drastically. | Good: Material removal possible, but optimal shapes often unmachinable. | Significant launch cost savings and/or increased payload mass fraction. Critical for performance. |
Konsolidering av delar | High: Multiple components can be combined into a single printed part. | Low: Complex assemblies often require multiple machined parts & fasteners. | Reduces part count, assembly time, weight (fasteners), and potential failure points (joints). Improves reliability. |
Material Avfall | Low: Uses only the material needed for the part + supports (recyclable). | High: Significant material removed from billet (high buy-to-fly ratio). | More sustainable and cost-effective, especially with expensive aerospace alloys. |
Lead Time (Prototype) | Fast: No tooling required, direct digital manufacturing. | Moderate/Slow: Requires programming, fixturing, potential tooling. | Aktiverar rapid prototyping satellite components, faster design iteration, and quicker response to mission changes. |
Complexity Cost | Less sensitive to complexity; build time is the main factor. | Increases significantly with geometric complexity (more setups, tools). | Makes highly optimized, complex designs economically viable. |
Interna funktioner | Can create intricate internal channels (cooling, fluidics, waveguides). | Very difficult or impossible to create complex internal features. | Enables integrated thermal management, fluid flow, or RF components directly within the structure. |
Export to Sheets
Key Benefits Driving AM Adoption for Satellite Frames:
- Unmatched Lightweighting through Topology Optimization: This is arguably the most significant driver. Software algorithms optimize material placement based on load paths, removing unnecessary mass while maintaining required stiffness and strength. This routinely leads to weight savings of 30-60% or more for lightweight satellite structures compared to conventionally designed and machined parts. Met3dp utilizes advanced simulation and design tools to maximize these benefits for clients.
- Revolutionary Part Consolidation: Imagine a complex mounting assembly requiring 10 separate machined parts, numerous fasteners, and intricate assembly steps. With AM, this can often be redesigned and printed as a single, monolithic component. This simplification dramatically reduces assembly labor, minimizes tolerance stack-up issues, eliminates fastener weight, and increases overall structural reliability by removing joints.
- Geometric Complexity is Free (Almost): AM processes build layer by layer, making the creation of complex, organic shapes, internal lattices, and conformal cooling channels no more difficult than printing a simple block (though build time increases with volume). This freedom allows engineers to design for funktion rather than being constrained by manufacturability limitations inherent in metal 3D printing vs CNC machining debates.
- Accelerated Development and Qualification: The ability to go directly from a CAD file to a physical metal prototype in days, rather than weeks or months, drastically shortens the design-build-test cycle. This agility is invaluable in the fast-paced satellite industry, allowing for rapid design iterations and quicker qualification of flight hardware.
- Materialeffektivitet: Especially with high-cost aerospace alloys like titanium or specialized aluminum alloys (like Scalmalloy®), the high buy-to-fly ratio of CNC machining represents significant wasted expense. AM utilizes material far more efficiently, reducing raw material costs and environmental impact.
While AM is not a universal replacement for machining (machining is often required for final tolerances and surface finishes on AM parts), its ability to fundamentally rethink component design offers transformative potential for satellite mounting frames and other critical aerospace hardware. Partnering with an experienced AM provider like Met3dp ensures access to state-of-the-art equipment and the expertise needed to fully leverage these advantages.
Recommended Materials (Scalmalloy®, AlSi10Mg) and Why They Excel in Space
Choosing the right material is paramount for any aerospace application, and satellite mounting frames are no exception. The material must balance strength, stiffness, weight, thermal properties, and resistance to the harsh space environment. Additive manufacturing opens the door to using advanced alloys specifically developed or well-suited for the layer-by-layer building process. For satellite frames, two materials stand out due to their exceptional properties and proven track record in demanding applications: Scalmalloy® -legering och AlSi10Mg.
Met3dp, leveraging its advanced powder production capabilities including gas atomization and Plasma Rotating Electrode Process (PREP), manufactures a wide range of metallpulver av hög kvalitet optimized for additive manufacturing, including alloys suitable for the most demanding aerospace requirements. Our expertise ensures powders with high sphericity, excellent flowability, and consistent chemical composition, which are crucial for printing dense, reliable, high-performance parts.
Scalmalloy® (AlMgSc Alloy): The High-Performance Champion
Scalmalloy® is a patented high-performance aluminum-magnesium-scandium alloy specifically designed for additive manufacturing. It has rapidly gained prominence in aerospace due to its unique combination of properties that often exceed those of traditional high-strength aluminum alloys.
- Viktiga egenskaper:
- Exceptionellt förhållande mellan styrka och vikt: Offers strength comparable to some 7000-series aluminum alloys but with lower density, making it ideal for lightweighting critical structures.
- High Ductility and Fatigue Strength: Unlike many high-strength aluminum alloys, Scalmalloy® retains good ductility and exhibits excellent fatigue performance, crucial for components subjected to launch vibrations and cyclic loading.
- God korrosionsbeständighet: Shows strong resistance to corrosion, important for ground handling and long-term mission life.
- Utmärkt svetsbarhet: Can be welded, which is advantageous for potential repairs or integration with other structures (though AM often aims to eliminate welding via part consolidation).
- Microstructure Stability: Maintains stable properties over a range of temperatures relevant to aerospace applications.
- Why it Excels for Satellite Frames: Its high specific strength allows for extremely lightweight yet stiff frame designs through topology optimization. The excellent fatigue resistance provides reliability under dynamic launch loads. Its suitability for AM allows the creation of complex, optimized geometries that fully exploit its material properties. It’s often the material of choice when maximum performance and weight saving are required.
AlSi10Mg: The Reliable Workhorse
AlSi10Mg is a more conventional aluminum-silicon-magnesium casting alloy that has become one of the most widely used materials in metal additive manufacturing due to its excellent printability and well-understood properties.
- Viktiga egenskaper:
- Bra tryckbarhet: Flows and fuses well during the LPBF process, allowing for the reliable production of complex geometries.
- Good Strength and Hardness: Offers a respectable balance of strength and hardness, suitable for many structural applications.
- Utmärkt värmeledningsförmåga: Useful for applications where the frame needs to act as a heat sink for electronics.
- God korrosionsbeständighet: Adequate for many space applications.
- Kostnadseffektivt: Generally less expensive than specialized alloys like Scalmalloy®.
- Why it Excels for Satellite Frames: Its ease of processing and lower cost make it a strong candidate for less critically loaded frames or where thermal conductivity is a primary design driver. It provides a robust and reliable option for a wide range of AlSi10Mg satellite applications, offering significant advantages over traditional manufacturing in terms of design freedom and lead time. It’s often used for prototypes and series production where the absolute highest strength-to-weight ratio of Scalmalloy® isn’t strictly necessary.
Material Property Comparison (Typical Values for AM):
Fastighet | Scalmalloy® (Heat Treated) | AlSi10Mg (Heat Treated) | Enheter | Relevance for Satellite Frames |
---|---|---|---|---|
Täthet | ~2.67 | ~2.67 | g/cm³ | Lower density enables lightweighting. |
Yield Strength (Rp0.2) | > 480 | ~230 – 280 | MPa | Higher strength allows for thinner walls, reducing weight. |
Slutlig draghållfasthet | > 520 | ~330 – 430 | MPa | Overall material strength limit. |
Töjning vid brott | > 12 | ~3 – 10 | % | Ductility measure; higher is better for fatigue/fracture toughness. |
Elasticitetsmodul | ~70 | ~70 | GPa | Stiffness; critical for maintaining alignment. |
Fatigue Strength (R=-1) | High (Specific values depend on test) | Måttlig | MPa | Resistance to failure under cyclic loading (e.g., vibration). |
Termisk konduktivitet | ~110-130 | ~120 – 140 | W/(m·K) | Ability to conduct heat; important for thermal management. |
Export to Sheets
(Note: Exact properties can vary based on AM machine parameters, heat treatment, and build orientation. These are representative values.)
Choosing Between Scalmalloy® and AlSi10Mg:
- Välja Scalmalloy® -legering when:
- Maximum weight reduction is the primary goal.
- High strength and fatigue performance are critical (e.g., primary structures, vibration-prone areas).
- Performance justifies the higher material cost.
- Välja AlSi10Mg when:
- Good all-around performance is sufficient.
- Thermal conductivity is a key design requirement.
- Cost-effectiveness is a major consideration.
- Rapid prototyping or less critical structural components are needed.
Met3dp possesses deep expertise in processing both Scalmalloy® properties aerospace krav och AlSi10Mg satellite applications. Our understanding of powder characteristics, printing parameters, and post-processing ensures that components manufactured from these best metal powders for space meet the stringent quality and performance demands of the aerospace industry.
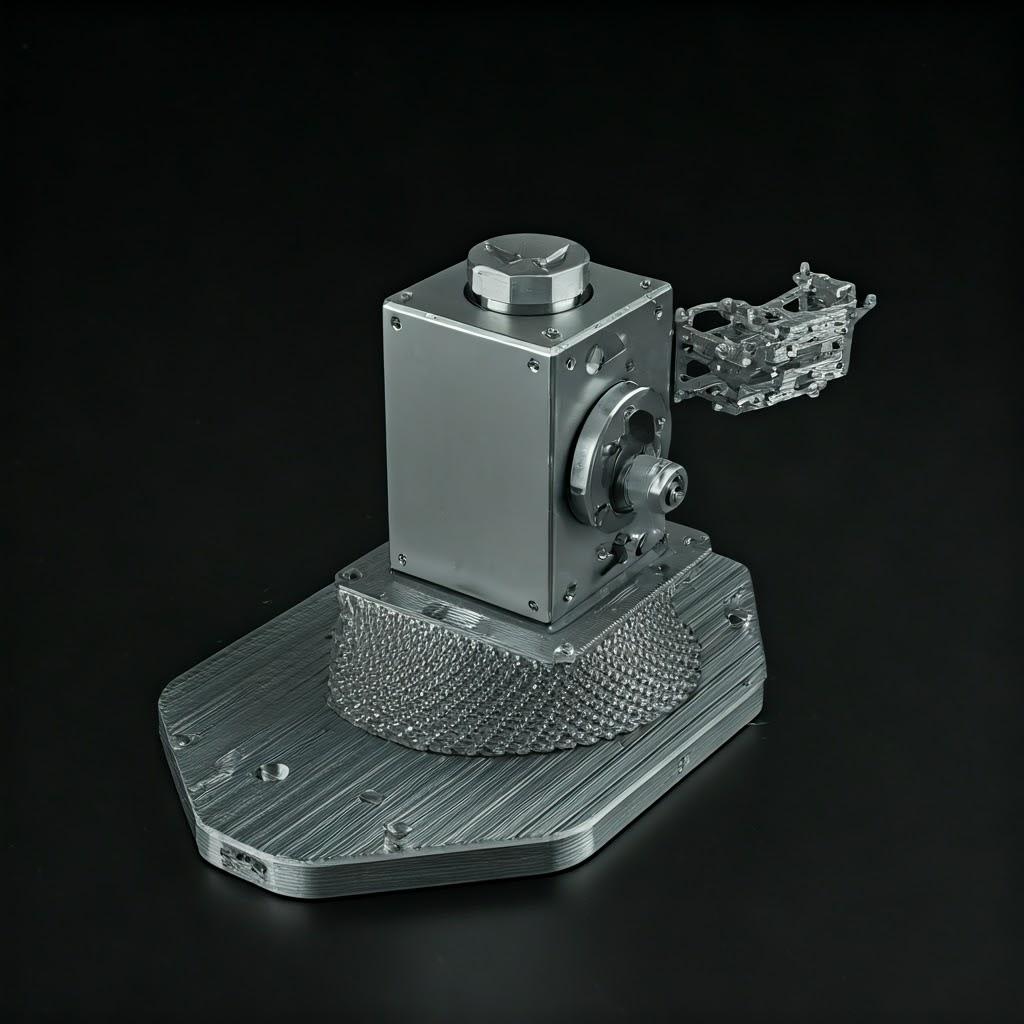
Design Considerations for Additively Manufactured Satellite Frames
Successfully leveraging metal additive manufacturing for satellite mounting frames requires more than just selecting the right material and printer; it demands a fundamental shift in design thinking. Designing for Additive Manufacturing (DfAM) is crucial to unlocking the full potential of the technology, particularly the significant weight savings and performance enhancements possible for satellite component design. Engineers accustomed to the constraints of subtractive manufacturing must embrace new possibilities while understanding the nuances of the layer-by-layer process. Partnering with an AM expert like Met3dp, who offers DfAM support, can significantly shorten the learning curve and optimize outcomes.
Here are key DfAM aerospace considerations for satellite mounting frames:
- Embrace Topology Optimization:
- This is often the starting point for achieving maximum lightweighting. Specialized software analyzes load paths and functional requirements (stiffness, frequency response) to generate highly organic, efficient structures, placing material only where it’s needed.
- Engineers define design spaces, keep-out zones, load cases, and performance targets. The software then iteratively removes material, resulting in frame designs that are often impossible to manufacture traditionally.
- Consider using topology optimization for satellite brackets and frames early in the design phase to maximize benefits. Tools like Altair OptiStruct, Ansys Mechanical, or nTopology are commonly used.
- Leverage Lattice Structures:
- For areas requiring stiffness over bulk strength, internal lattice structures can provide excellent structural support with minimal mass. Various lattice types (cubic, octet-truss, gyroid) offer different mechanical, thermal, and fluidic properties.
- They can also be used for vibration damping or integrated into thermal management pathways.
- Design tools need capabilities to generate and validate these complex structures.
- Understand Process Limitations:
- Minimum Feature Size & Wall Thickness: LPBF processes can achieve fine details, but there are limits (typically ~0.3-0.5 mm for robust features, depending on the machine and material). Thin walls are prone to distortion during printing and handling. Design walls thick enough to be structurally sound and reliably printable.
- Överhäng och självbärande vinklar: Features printed over empty space require support structures. However, features angled above a certain threshold (typically 45 degrees from the horizontal, but material/parameter dependent) can often support themselves. Designing with self-supporting angles minimizes the need for supports, reducing post-processing time and cost, and avoiding potential surface marks.
- Hole Orientation: Horizontal holes often print with better circularity than vertical holes due to the layer stepping effect, though small vertical holes are generally fine. Large horizontal holes may require support structures.
- Strategic Support Structure Design:
- While minimizing supports is ideal, they are often necessary for steep overhangs, large horizontal surfaces, and preventing distortion.
- Supports should be designed for effective function (heat dissipation, anchoring the part) och ease of removal. Consider accessibility for tools or EDM (Electrical Discharge Machining) if needed.
- Support contact points will leave witness marks on the surface, requiring finishing if aesthetics or specific surface properties are critical in those areas. Design critical surfaces to be self-supporting or easily accessible for finishing. Following metal AM design guidelines is crucial here.
- Design for Post-Processing:
- Anticipate downstream steps. If critical interfaces require high precision or specific surface finishes achievable only through CNC machining, add extra sacrificial stock (machining allowance, typically 0.5-1.0 mm) to those surfaces in the AM design.
- Ensure features requiring inspection (e.g., internal channels via CT scan) are designed to be inspectable.
- Consider access for powder removal from internal cavities. Design drain/access holes strategically if enclosed voids are unavoidable.
- Integrate Functionality:
- Think beyond just structure. Can thermal management features like heat pipes, channels for fluid cooling, or optimized conductive pathways be integrated directly into the frame design?
- Can mounting points for wiring harnesses, sensors, or RF components be incorporated? AM allows for complex, multifunctional components, enabling optimizing satellite components beyond simple structural roles.
By incorporating these DfAM principles, engineers can move beyond simply replicating machined designs with AM and start creating truly optimized, next-generation satellite hardware.
Achievable Tolerance, Surface Finish, and Dimensional Accuracy
A common question from engineers and procurement managers new to metal AM concerns the level of precision achievable. While 3D-utskrift av metall offers remarkable geometric freedom, it’s essential to have realistic expectations regarding as-built tolerances and surface finish compared to established methods like high-precision CNC machining. Understanding these factors is critical for determining necessary post-processing steps and ensuring components meet the stringent requirements of precision metal fabrication för flyg.
Typical As-Built Tolerances:
- For high-quality Laser Powder Bed Fusion (LPBF) systems, typical dimensional tolerances are often in the range of ±0.1 mm to ±0.2 mm over moderate distances (e.g., up to 100 mm), with an additional tolerance percentage (e.g., ±0.1% to ±0.2%) applied for larger dimensions.
- Electron Beam Melting (EBM) generally produces parts with slightly looser tolerances than LPBF due to higher processing temperatures and powder particle size.
- Factors Influencing Tolerance:
- Machine Calibration: Regular calibration and maintenance are crucial. Met3dp utilizes industry-leading printers known for accuracy and reliability.
- Materialegenskaper: Thermal expansion and shrinkage vary between materials (e.g., Scalmalloy® vs. AlSi10Mg).
- Part Geometry & Size: Large or complex parts with varying cross-sections are more prone to thermal stresses and potential distortion.
- Bygg orientering: The orientation of the part on the build plate affects support needs, thermal history, and layer stepping effects, influencing final dimensions.
- Thermal Stresses: Residual stresses built up during the heating/cooling cycles can cause warping if not managed through careful parameter control and support strategies.
- Efterbearbetning: Stress relief heat treatments can cause minor dimensional changes that need to be accounted for.
As-Built Surface Finish:
- The surface finish of as-built metal AM parts is inherently rougher than machined surfaces. It’s characterized by partially melted powder particles adhering to the outer layers.
- Typical surface roughness (Ra) for LPBF parts is often in the range of 6 µm to 20 µm, depending heavily on the build orientation (upward-facing surfaces are smoother than downward-facing or vertical walls), material, and parameters used. EBM surfaces are generally rougher.
- Factors Influencing Surface Finish:
- Powder Particle Size: Finer powders generally lead to smoother surfaces. Met3dp’s advanced powder production ensures optimized particle size distributions.
- Skiktets tjocklek: Thinner layers typically result in better surface finish on sloped surfaces.
- Bygg orientering: Surfaces parallel to the build plate (up-skin) tend to be the smoothest, while down-skin surfaces requiring support contact are the roughest.
- Laser/Beam Parameters: Energy density and scanning strategy impact melt pool characteristics and surface quality.
Achieving Higher Precision:
- For critical interfaces, mounting points, bearing surfaces, or any feature demanding tolerances tighter than the as-built capability (e.g., < ±0.1 mm) or specific smooth surface finishes (e.g., Ra < 3.2 µm), secondary CNC-bearbetning is typically required.
- This hybrid approach (AM + Machining) leverages the geometric freedom of AM for the overall shape and lightweighting, combined with the precision of machining for critical features. Designing with appropriate machining allowances is key (as mentioned in DfAM).
- Other finishing processes like blasting, tumbling, or polishing can improve the general surface finish but generally do not significantly improve dimensional tolerances.
Metrology and Inspection:
- Verifying dimensional accuracy satellite parts is crucial. Common methods include:
- Coordinate Measuring Machines (CMMs) for high-precision point measurements on defined features.
- 3D Laser Scanning or Structured Light Scanning for comparing the full part geometry against the original CAD model.
- Met3dp incorporates rigorous quality control and inspection processes, utilizing advanced metrology tools to ensure parts meet specified metal 3D printing tolerances aerospace standards. Explore more about Met3dp’s capabilities in 3D-utskrift av metall.
In summary, while as-built AM parts offer good accuracy for many applications, achieving the tight tolerances and smooth finishes often required for critical satellite interfaces usually necessitates planned post-machining operations.
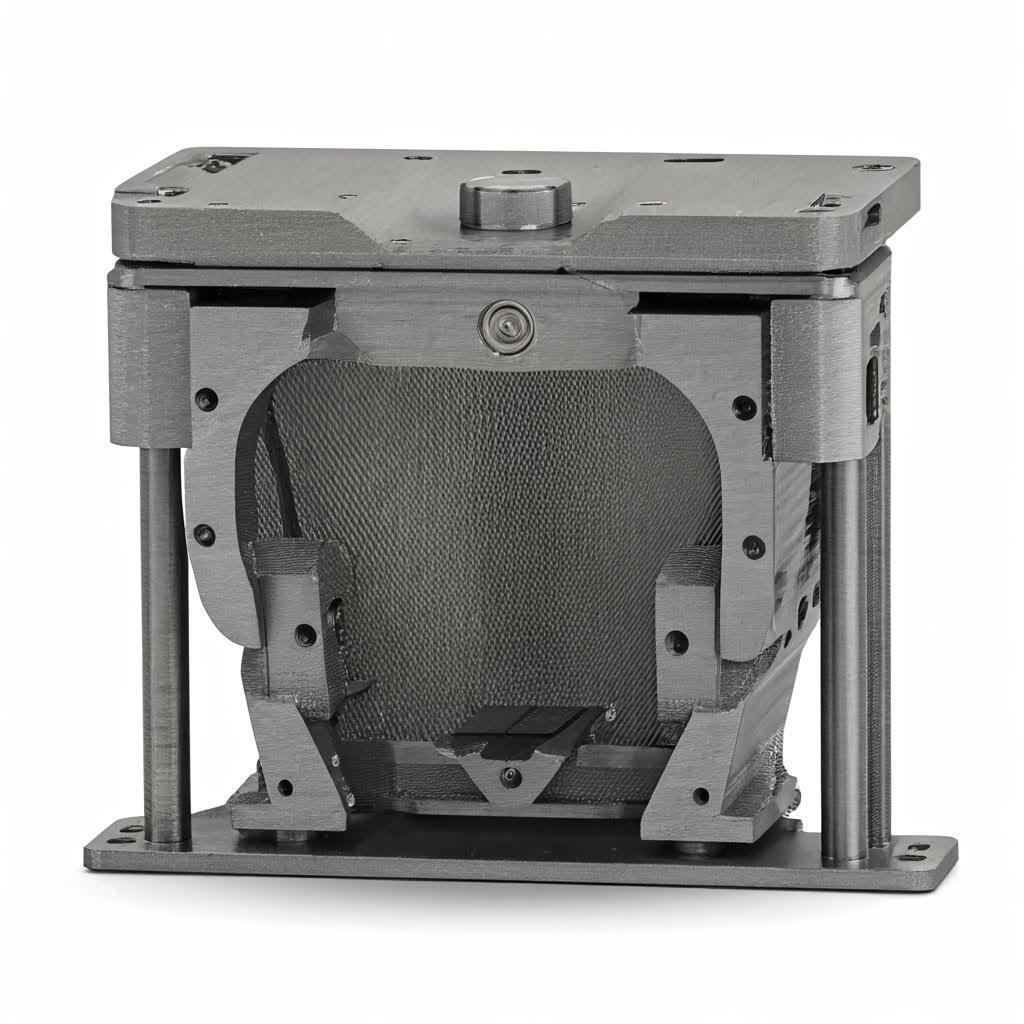
Post-Processing Requirements for Mission-Critical Satellite Frames
Printing the satellite mounting frame is often just the first manufacturing step. A series of crucial post-processing metal AM aerospace operations are typically required to transform the as-built part into flight-ready hardware. These steps are essential for relieving internal stresses, removing support structures, achieving final dimensions and surface characteristics, and ensuring the component’s integrity and performance in the demanding space environment. Procurement managers should factor these steps into project timelines and costs when sourcing AM components.
Common post-processing steps for Scalmalloy® and AlSi10Mg satellite frames include:
- Stress Relief / Heat Treatment:
- Why it’s critical: The rapid heating and cooling inherent in LPBF/EBM creates significant residual stresses within the printed part. These stresses can lead to distortion (especially after removal from the build plate) and negatively impact mechanical properties, particularly fatigue life.
- Process: Parts are typically heat-treated while still attached to the build plate (for stability) or after removal. Specific cycles (temperature, time, atmosphere) depend on the alloy:
- AlSi10Mg: Often involves a stress relief cycle (e.g., ~2 hours at 300°C) followed by a solution treatment and artificial aging (T6 condition) to optimize strength and ductility (e.g., solutionizing around 530°C, quenching, then aging around 160°C).
- Scalmalloy®: Requires a specific aging treatment (e.g., ~4 hours at 325°C) to achieve its high-strength properties through precipitation hardening.
- Importance: Rätt heat treatment Scalmalloy and AlSi10Mg is non-negotiable for aerospace applications to ensure predictable mechanical behavior and dimensional stability.
- Removal from Build Plate & Support Structure Removal:
- Parts are typically cut from the build plate using wire EDM or a bandsaw.
- Support structures, designed to anchor the part and support overhangs, must be carefully removed. This can involve:
- Manual breaking/cutting for accessible supports.
- Machining (milling, grinding) for more tenacious or integrated supports.
- Wire EDM for intricate internal supports or hard-to-reach areas.
- Care must be taken to avoid damaging the part surface during removal.
- Ytbehandling:
- Objective: Improve the as-built surface roughness, remove loose powder particles, and enhance fatigue life or aesthetic appearance.
- Common Methods:
- Abrasive Blasting (Grit/Bead Blasting): Provides a uniform matte finish, removes surface oxides, and can impart compressive residual stresses beneficial for fatigue. Choice of media (e.g., aluminum oxide, glass beads) affects the final texture.
- Tumbling/Vibratory Finishing: Parts are placed in a tumbler with media, smoothing edges and surfaces through friction. Good for batch processing of smaller parts.
- Polishing (Manual/Automated): Used to achieve very smooth, mirror-like finishes where required (e.g., for optical applications or specific thermal coatings), though often labor-intensive.
- The level of surface finishing satellite components depends on the specific functional requirements of each surface.
- Precision Machining:
- As discussed previously, CNC machining 3D printed parts is frequently required for:
- Achieving tight tolerances on critical interfaces, mounting holes, and mating surfaces.
- Creating specific surface finishes (e.g., smooth sealing surfaces).
- Removing support witness marks completely.
- Requires careful fixture design to hold the complex AM geometry securely without distortion.
- As discussed previously, CNC machining 3D printed parts is frequently required for:
- Surface Treatments & Coatings:
- To enhance environmental protection or tailor surface properties:
- Anodizing (Aluminum Alloys): Improves corrosion resistance and wear resistance, can provide thermal control properties, and allows for dyeing (though color stability in space is a concern).
- Chemical Conversion Coatings (e.g., Alodine/Chromate): Enhance corrosion resistance and provide a good base for paint or adhesives. Compliance with environmental regulations (REACH, RoHS) is important here.
- Specialized Space Coatings: Application of thermal control paints or coatings to manage radiative heat transfer in orbit.
- Selection depends on the operating environment and specific functional needs of the aerospace coatings AM parts.
- To enhance environmental protection or tailor surface properties:
- Cleaning & Inspection / Non-Destructive Testing (NDT):
- Thorough cleaning is required to remove residual powder, machining fluids, and contaminants before final inspection and assembly.
- NDT additive manufacturing is critical for flight hardware:
- Computed Tomography (CT Scanning): X-ray based method to detect internal defects like porosity or lack-of-fusion voids and verify internal channel geometry.
- Fluorescent Penetrant Inspection (FPI): Detects surface-breaking cracks or porosity.
- Dimensionell inspektion: Using CMM or 3D scanning to verify final dimensions against specifications.
Met3dp offers comprehensive post-processing capabilities or works with qualified partners to ensure satellite mounting frames meet all necessary finishing, tolerance, and quality assurance requirements for mission success.
Common Challenges in 3D Printing Satellite Frames and How to Mitigate Them
While metal additive manufacturing offers significant advantages, producing complex, mission-critical components like satellite frames is not without its challenges. Understanding potential pitfalls and implementing effective mitigation strategies are key to successfully adopting AM for aerospace applications. Experienced service providers like Met3dp have developed robust processes to overcome these common hurdles.
1. Warping and Distortion (Residual Stress):
- Utmaning: The rapid localized heating and cooling during printing induce internal stresses. As the part builds, these stresses can accumulate, leading to warping, distortion, or even cracking, especially in large or complex geometries. Residual stress additive manufacturing är ett stort bekymmer.
- Mitigation Strategies:
- Optimized Build Parameters: Careful control of laser power, scan speed, and hatching strategies to manage the melt pool and thermal gradients.
- Thermal Simulation: Using software to predict stress accumulation and potential distortion before printing, allowing for design or orientation adjustments.
- Strategic Support Structures: Well-designed supports anchor the part securely to the build plate and act as heat sinks, helping to manage thermal stresses.
- Optimized Build Orientation: Orienting the part to minimize large flat areas parallel to the recoater and reduce thermal gradients across layers.
- Stress Relief Heat Treatment: An essential post-processing step to relax internal stresses before removing the part from the build plate or supports.
2. Porosity (Gas and Lack-of-Fusion):
- Utmaning: Internal voids or pores can compromise the mechanical integrity (especially fatigue strength) of the part. Porosity can arise from gas trapped within the melt pool (gas porosity) or incomplete fusion between layers or scan tracks (lack-of-fusion). Porosity control AM is vital for structural parts.
- Mitigation Strategies:
- High-Quality Powder: Using spherical, gas-free powder with low moisture content and controlled particle size distribution. Met3dp’s advanced powder production focuses on these characteristics.
- Optimized Print Parameters: Ensuring sufficient energy density to fully melt the material and allow trapped gas to escape, without overheating.
- Controlled Build Atmosphere: Maintaining a high-purity inert gas atmosphere (Argon or Nitrogen) in the build chamber to minimize oxidation and contamination.
- Het isostatisk pressning (HIP): A post-processing step where the part is subjected to high temperature and high inert gas pressure. HIP for 3D printed parts effectively closes internal voids (gas porosity and lack-of-fusion), significantly improving density and mechanical properties. Often mandatory for critical aerospace components.
3. Support Removal Challenges:
- Utmaning: Removing support structures, especially from complex internal channels or delicate features, can be time-consuming, costly, and risk damaging the part. Inaccessible internal supports may be impossible to remove completely.
- Mitigation Strategies:
- DfAM: Designing parts with self-supporting angles wherever possible to minimize the need for supports.
- Optimized Support Design: Using support types (e.g., tree supports, block supports with perforation) and parameters that balance effective support with ease of removal. Utilizing specialized software for support generation.
- Accessibility Planning: Ensuring tools or processes (manual, machining, EDM) can reach support structures. Designing access points if necessary.
- Material Choice: Some materials are easier to remove supports from than others.
4. Achieving Consistent Material Properties:
- Utmaning: Ensuring uniform microstructure and mechanical properties throughout a large or complex part, or from build to build, can be challenging due to variations in thermal history across the component.
- Mitigation Strategies:
- Robust Process Control: Strict adherence to qualified build parameters, regular machine calibration, and environmental monitoring.
- Materialkvalificering: Rigorous testing of material properties from test coupons printed alongside actual parts within each build.
- Standardized Heat Treatment: Applying consistent, validated heat treatment cycles to normalize microstructure and properties.
- Process Monitoring: Utilizing in-situ monitoring tools (melt pool monitoring, thermal imaging) where available to detect potential inconsistencies during the build.
5. Powder Handling and Quality Control:
- Utmaning: Metal powders (especially reactive ones like aluminum alloys) require careful handling to prevent contamination (oxygen, moisture) and maintain consistent particle size distribution. Powder reuse requires careful management and testing.
- Mitigation Strategies:
- Controlled Environment: Handling powders in inert atmospheres or controlled humidity environments.
- Pulversiktning: Regularly sieving powder to remove oversized particles or agglomerates.
- Hantering av livscykeln för pulver: Tracking powder batches, number of reuse cycles, and conducting regular chemical and physical analysis to ensure quality.
- Supplier Qualification: Sourcing high-quality, consistent powders from reputable suppliers like Met3dp.
Overcoming these metal 3D printing defects aerospace challenges requires a combination of advanced technology, process expertise, and rigorous quality management systems – areas where experienced AM service providers specializing in aerospace applications add significant value.
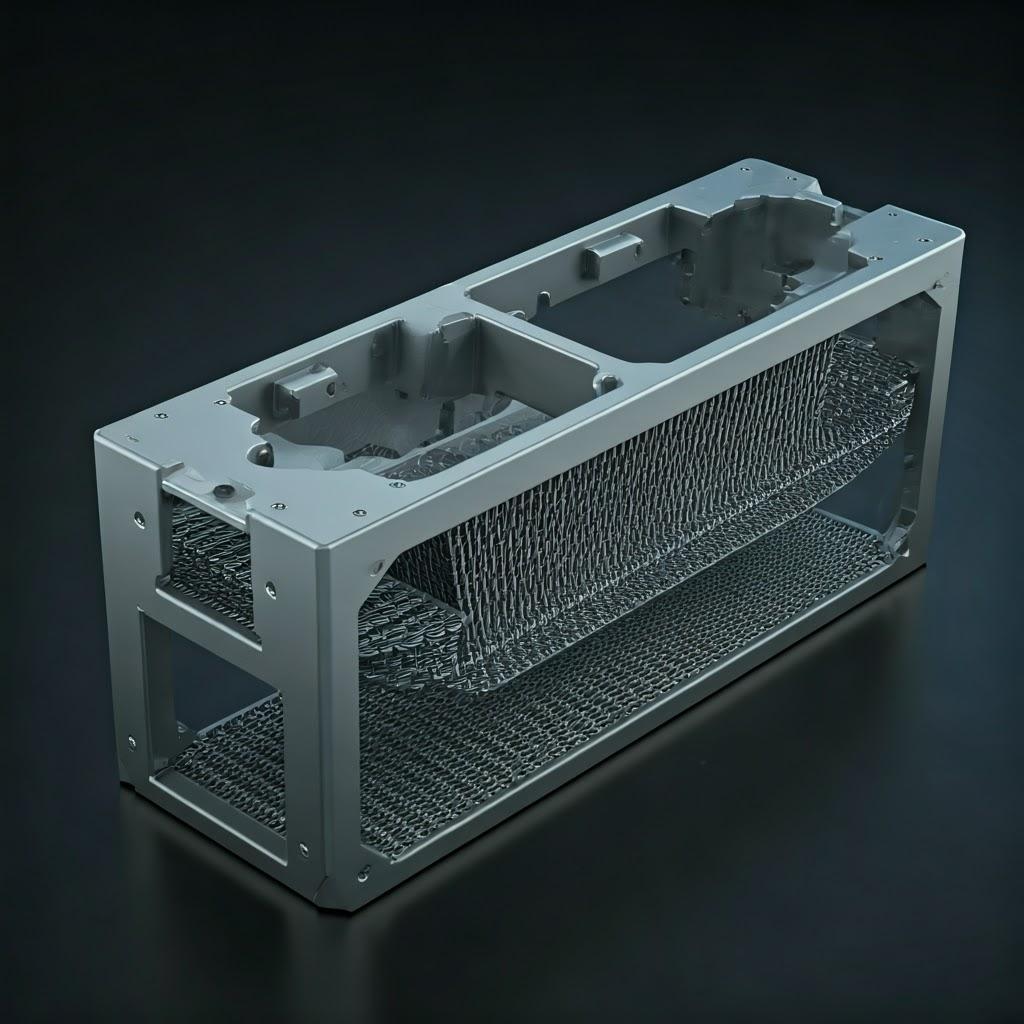
How to Choose the Right Metal 3D Printing Service Provider for Satellite Components
Selecting the right manufacturing partner is as critical as the design and material choice, especially when dealing with mission-critical satellite components. The unique demands of the aerospace industry require a metal 3D printing supplier aerospace specialist with proven capabilities, rigorous quality control, and deep expertise. Not all AM service bureaus are equipped to handle the complexities and stringent requirements of space hardware.
Here are key criteria to evaluate when choosing AM service bureau partners for satellite mounting frames:
- Aerospace Certifications & Quality Management:
- AS9100 Certification: This is the gold standard for aerospace quality management systems. Look for suppliers who are AS9100 certified or demonstrably operate to its stringent requirements, ensuring traceability, process control, and risk management.
- Robust Quality Management System (QMS): Beyond certification, assess their internal quality procedures, documentation practices, operator training, and equipment calibration protocols.
- Proven Experience & Expertise:
- Track Record in Aerospace: Have they successfully produced components for aerospace or, ideally, space applications before? Ask for case studies or examples (non-proprietary).
- Materialkompetens: Specific experience printing and post-processing the required materials (e.g., Scalmalloy® printing service, AlSi10Mg) is essential. They should understand the nuances of heat treatment and achieving desired material properties for these alloys.
- DfAM Support: Do they offer Design for Additive Manufacturing support? A supplier who can proactively advise on design optimization for printability, lightweighting, and cost-effectiveness is invaluable.
- Technological Capabilities:
- Appropriate AM Technology: Ensure they operate well-maintained, industrial-grade LPBF or EBM machines suitable for the required material and part specifications.
- Machine Fleet & Capacity: Consider their machine availability, build volume capabilities (can they print the required frame size?), and redundancy to ensure reliable lead times, especially for series production eller wholesale satellite parts orders.
- Powder Management: Strict protocols for powder handling, storage, testing, and traceability are crucial for consistent part quality.
- In-House Post-Processing & Inspection:
- Comprehensive Capabilities: Does the supplier offer critical post-processing steps like stress relief/heat treatment, precision CNC machining, surface finishing, and NDT (especially CT scanning) in-house or through tightly controlled, qualified partners? Managing multiple vendors increases complexity and risk.
- Metrology Equipment: Access to calibrated CMMs, 3D scanners, and material testing labs for thorough quality verification.
- Material Traceability & Qualification:
- Full traceability of powder batches from source through processing to the final part is mandatory for flight hardware.
- Established processes for material qualification and generating Certificates of Conformance (CoC).
- Responsiveness & Communication:
- Clear communication channels, responsive customer service, and transparent project management are vital for complex projects.
Why Met3dp is Your Trusted Partner:
Met3dp embodies the qualities of a leading aerospace qualified AM supplier. As a company headquartered in Qingdao, China, specializing in both 3D printing equipment and high-performance metal powders, Met3dp offers comprehensive solutions tailored for demanding industries like aerospace.
- Industry-Leading Technology: Our printers deliver exceptional print volume, accuracy, and reliability.
- Advanced Powder Expertise: Leveraging state-of-the-art gas atomization and PREP technologies, we manufacture high-quality spherical metal powders, including innovative alloys like TiNi, TiTa, TiAl, TiNbZr, CoCrMo, stainless steels, superalloys, and the critical Scalmalloy® and AlSi10Mg needed for satellite applications.
- Decades of Collective Expertise: Our team possesses deep knowledge in metal AM, providing comprehensive support from design consultation (DfAM) through production and post-processing.
- Commitment to Quality: While specific certifications should always be verified for project requirements, our foundation in producing high-spec equipment and powders translates into rigorous quality control throughout the manufacturing process.
- End-to-End Solutions: We partner with organizations to implement 3D printing strategies, accelerating digital manufacturing transformations.
Choosing Met3dp means selecting a knowledgeable and vertically integrated partner committed to enabling the production of next-generation satellite components.
Cost Factors and Typical Lead Times for Additively Manufactured Satellite Frames
Understanding the financial and time investments required for additively manufactured satellite frames is crucial for project planning and budgeting. Both cost and lead time are influenced by a multitude of factors related to the part’s complexity, material choice, and processing requirements.
Key Cost Drivers for Metal AM Satellite Frames:
- Material Type & Volume:
- The cost of the metal powder itself is a significant factor. High-performance alloys like Scalmalloy® are considerably more expensive than standard AlSi10Mg or stainless steels.
- The sheer volume of the part (and required support structures) directly impacts material consumption. Topology optimization plays a key role here in minimizing volume.
- Maskintid:
- Often the dominant cost factor. Calculated based on the total time the AM machine is occupied printing the part(s).
- Influenced by:
- Part Height: Primary driver, as printing is layer by layer.
- Part Volume/Density: More material to melt per layer takes longer.
- Komplexitet: Intricate features may require slower scan speeds.
- Nesting Efficiency: How many parts can be efficiently packed onto a single build plate amortizes setup costs.
- Kostnader för arbetskraft:
- Setup: Preparing the build file, loading the machine, powder handling.
- Efterbearbetning: Significant labor involved in part removal, support removal, heat treatment, surface finishing, machining, and inspection. Complexity drives labor time.
- Engineering & DfAM:
- Initial design optimization effort, simulation work (thermal, stress), and build preparation carry associated costs, particularly for complex, topology-optimized parts.
- Post-Processing Complexity:
- Extensive CNC machining, complex surface treatments, or advanced NDT requirements (like CT scanning) add significantly to the final satellite component pricing.
- Quality Assurance & Testing:
- The level of inspection, material testing (witness coupons), and documentation required for aerospace qualification impacts cost.
- Orderkvantitet:
- Prototypes (quantity 1) have high per-part costs due to setup amortization. Series production allows for better nesting and process optimization, reducing the per-part metal 3D printing cost aerospace.
Typical Lead Times:
Lead times can vary significantly based on the factors below, but general ranges are:
- Prototypes (Non-Qualified): Typically 1-3 weeks from order confirmation to shipment, depending on complexity and machine availability.
- Production/Qualified Parts: Often 4-12 weeks or longer, factoring in potentially longer build times (for larger batches or complex parts), extensive post-processing queues, rigorous inspection/testing cycles, and documentation requirements.
Factors Influencing Lead Time:
- Part Complexity & Size: Larger, more complex parts take longer to print and post-process.
- Machine Availability: Service bureau queue lengths and scheduling.
- Krav på efterbearbetning: Heat treatment cycles, machining time, finishing processes, and NDT all add to the overall timeline.
- Qualification & Testing: If extensive qualification testing is needed, this can significantly extend the lead time.
- Materialets tillgänglighet: Ensuring the specific powder batch is available and qualified.
Met3dp works closely with clients to provide transparent quotations outlining these cost factors and realistic additive manufacturing lead time estimates. We strive to optimize production workflows for cost-efficiency and reliable delivery schedules. Contact us via our webbplats to discuss your project specifics.
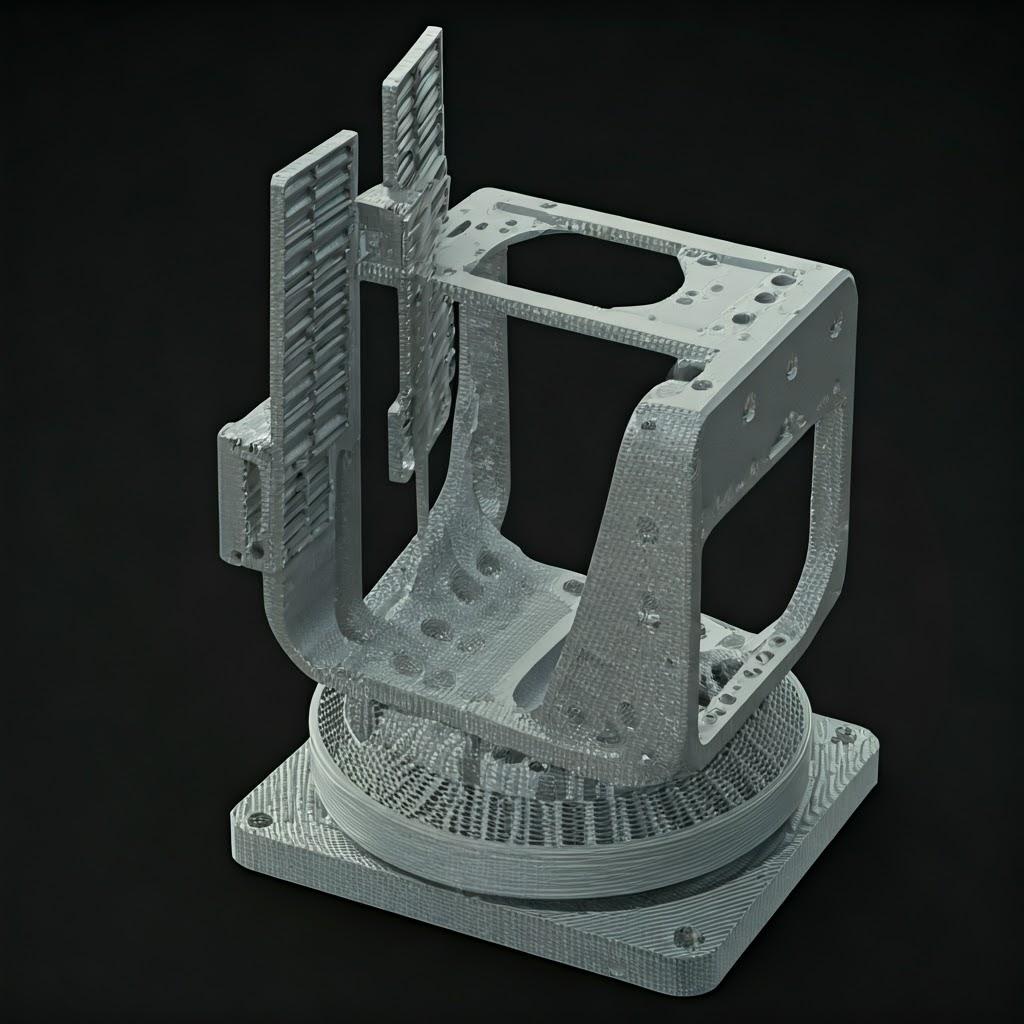
Vanliga frågor och svar (FAQ)
Here are answers to some common questions regarding the use of metal AM for satellite mounting frames:
- Q1: Is 3D printed Scalmalloy® strong enough for primary satellite structures?
- A: Absolutely. When processed correctly (including proper heat treatment), additively manufactured Scalmalloy® exhibits mechanical properties (yield strength, ultimate tensile strength, fatigue strength) comparable to or exceeding high-strength 7000-series aluminum alloys, but at a lower density. Its high specific strength makes it an excellent candidate for primary load-bearing structures where weight saving is paramount, and it has already been flight-proven in various aerospace applications. Met3dp ensures optimal processing to achieve these high-performance properties.
- Q2: What is the typical weight saving achievable with AM for satellite frames compared to traditional methods?
- A: Significant weight savings are a primary driver for using AM. Through topology optimization and design freedom, weight reductions of 30% to 60% or even more are commonly achievable compared to conventionally designed and CNC machined components performing the same function. The exact saving depends heavily on the initial design, load cases, and how aggressively topology optimization can be applied.
- Q3: Can complex internal features like cooling channels be reliably printed and inspected in satellite frames?
- A: Yes, this is a key advantage of AM processes like LPBF. Intricate internal channels for thermal management or fluid flow can be designed and printed directly into the frame. While challenging, reliable printing is achievable with careful design (e.g., ensuring channels are self-supporting or design for powder removal) and optimized print parameters. Inspection of these internal features typically relies on non-destructive methods, primarily industrial CT scanning (Computed Tomography), which can visualize internal geometry and detect potential defects like residual powder or lack-of-fusion.
- Q4: What level of traceability is provided for materials and processes by aerospace AM suppliers like Met3dp?
- A: Full traceability is non-negotiable for flight hardware. Reputable metal AM providers like Met3dp maintain rigorous traceability throughout the entire process. This includes:
- Tracking specific metal powder batches from the manufacturer (including chemistry and particle size distribution data).
- Documenting powder reuse history and testing.
- Linking specific parts to the machine used, the build file, the process parameters employed, and the operator.
- Recording all post-processing steps (heat treatment cycles, machining operations).
- Maintaining records of all inspection and NDT results.
- Providing comprehensive Certificates of Conformance (CoC) summarizing this information for each delivered part.
- A: Full traceability is non-negotiable for flight hardware. Reputable metal AM providers like Met3dp maintain rigorous traceability throughout the entire process. This includes:
Conclusion: Launching the Future of Satellite Design with Metal Additive Manufacturing
The journey to space demands innovation at every level. For satellite mounting frames, metal additive manufacturing represents a paradigm shift, moving beyond the limitations of traditional techniques to unlock new possibilities in performance, efficiency, and design. By enabling the creation of highly optimized, lightweight structures using advanced materials like Scalmalloy® and AlSi10Mg, AM directly addresses the critical need to reduce launch costs and enhance payload capabilities.
The ability to consolidate parts, integrate functionality like thermal management, and rapidly iterate on designs makes additive manufacturing innovation aerospace a powerful tool for satellite engineers. From intricate brackets for sensitive optics to robust frames for propulsion systems, the geometric freedom offered by processes like Laserpulverbäddsfusion allows for solutions previously unimaginable.
However, realizing the full potential of AM requires more than just advanced technology; it demands expertise in materials science, DfAM principles, process control, and rigorous post-processing and quality assurance. Choosing the right manufacturing partner – one with proven aerospace experience, cutting-edge equipment, high-quality materials, and a commitment to quality – is paramount for mission success.
Met3dp stands ready to be that partner. With our comprehensive capabilities spanning advanced metal powder production, industry-leading printing systems, and deep application knowledge, we provide end-to-end solutions for the most demanding satellite component manufacturing challenges.
We invite engineers, procurement managers, and innovators in the space industry to explore how a Met3dp aerospace partnership can help launch your next mission. Contact us today to discuss how precision additive manufacturing can elevate your satellite designs.
Dela på
MET3DP Technology Co, LTD är en ledande leverantör av lösningar för additiv tillverkning med huvudkontor i Qingdao, Kina. Vårt företag är specialiserat på 3D-utskriftsutrustning och högpresterande metallpulver för industriella tillämpningar.
Förfrågan för att få bästa pris och anpassad lösning för ditt företag!
Relaterade artiklar
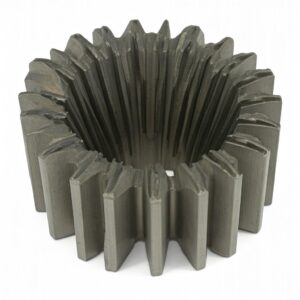
Högpresterande segment för munstycksvingar: Revolutionerande turbineffektivitet med 3D-utskrift i metall
Läs mer "Om Met3DP
Senaste uppdateringen
Vår produkt
KONTAKTA OSS
Har du några frågor? Skicka oss meddelande nu! Vi kommer att betjäna din begäran med ett helt team efter att ha fått ditt meddelande.
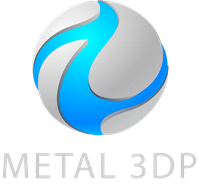
Metallpulver för 3D-printing och additiv tillverkning
FÖRETAG
PRODUKT
cONTACT INFO
- Qingdao City, Shandong, Kina
- [email protected]
- [email protected]
- +86 19116340731