Rocket Combustion Chambers: Revolutionizing Aerospace Manufacturing with Metal 3D Printing
Innehållsförteckning
Introduction – The Critical Role of Metal 3D Printed Rocket Combustion Chambers in Aerospace
The relentless pursuit of efficiency and performance in the aerospace industry has consistently driven innovation in propulsion systems. At the heart of these systems lies the rocket combustion chamber, a critical component responsible for generating the thrust that propels spacecraft and missiles. Traditionally manufactured through complex and time-consuming processes, these chambers are now undergoing a transformative shift with the advent of metal additive manufacturing, or metal 3D-utskrifter. This technology offers unprecedented design freedom, reduced lead times, and the potential for enhanced performance characteristics. As the aerospace sector increasingly embraces advanced manufacturing techniques, metal 3D printed rocket combustion chambers are emerging as a game-changer, enabling lighter, more robust, and geometrically optimized designs that were previously unattainable. Companies like Metall3DP are at the forefront of this revolution, providing both cutting-edge 3D printing equipment and high-performance metal powders tailored for demanding aerospace applications. Their commitment to industry-leading print volume, accuracy, and reliability makes them a trusted partner for mission-critical parts.
What is a Rocket Combustion Chamber Used For? – Exploring Applications Across the Aerospace Landscape
The primary function of a rocket combustion chamber is to provide a controlled environment for the combustion of propellant, generating high-pressure, high-temperature gas. This gas is then expelled through a nozzle to produce thrust, the fundamental force that drives rockets and spacecraft. The applications of these critical components span a wide spectrum within the aerospace industry:
- Launch Vehicles: In orbital launch vehicles, combustion chambers are integral to the main stage and upper stage engines, providing the immense power required to escape Earth’s gravity and deliver payloads into orbit. The ability to customize designs through metal 3D printing allows for optimized performance at different atmospheric pressures and flight phases.
- Spacecraft Propulsion: Beyond initial launch, smaller rocket engines with 3D printed combustion chambers are used for in-space maneuvers, including orbit adjustments, station keeping for satellites, and trajectory control for deep-space probes. The reduced weight achievable through additive manufacturing is particularly crucial for extending mission durations and increasing payload capacity.
- Missilsystem: In defense applications, rocket combustion chambers are vital components of missile propulsion systems, demanding high performance and reliability under extreme conditions. Metal 3D printing enables the rapid prototyping and manufacturing of complex geometries tailored to specific mission requirements.
- Hypersonic Vehicles: The development of hypersonic aircraft and missiles relies heavily on advanced propulsion systems with combustion chambers capable of withstanding extreme thermal and mechanical loads. Metal 3D printing facilitates the creation of intricate cooling channels and material combinations necessary for these demanding environments.
- Forskning och utveckling: Metal 3D printing empowers aerospace engineers to rapidly iterate on new combustion chamber designs, facilitating quicker and more cost-effective research and development of next-generation propulsion technologies. Companies like Metall3DP support these efforts by offering advanced metal powders and application development services.
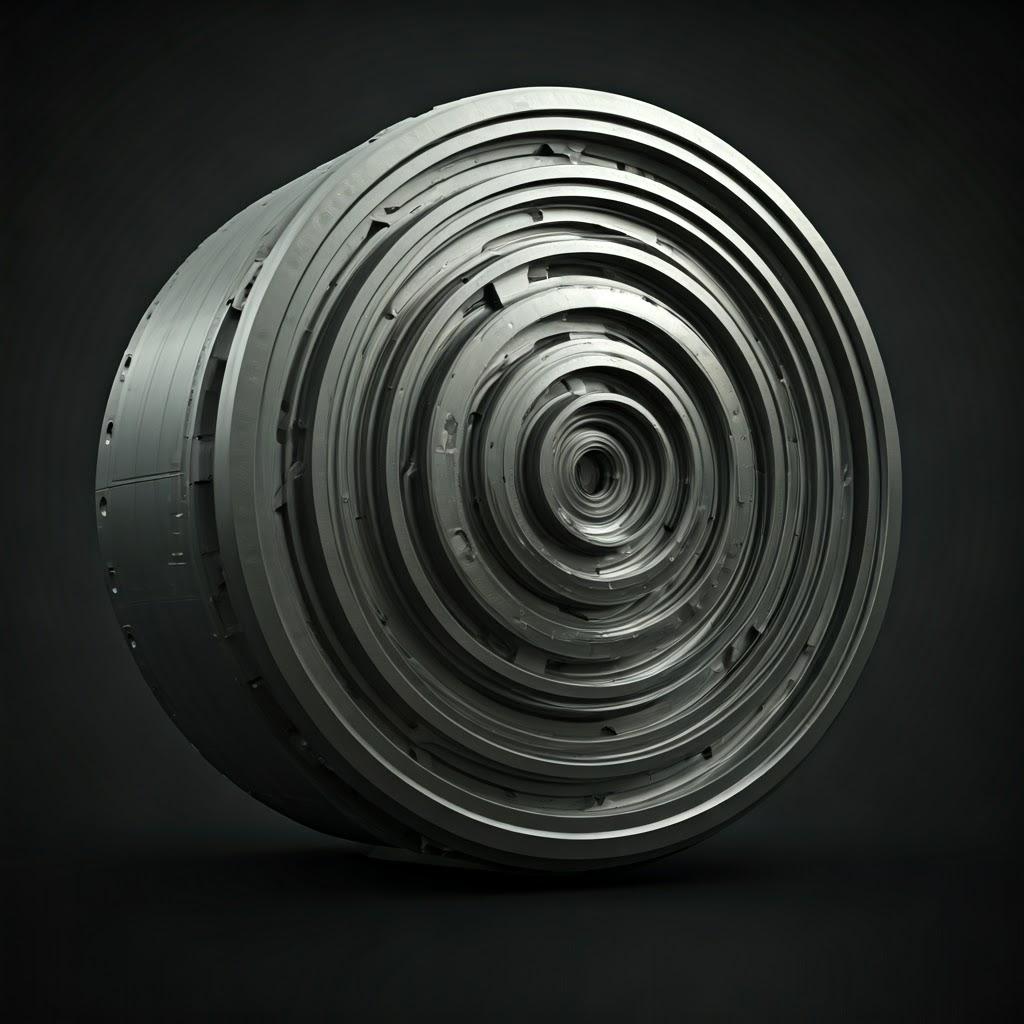
Why Use Metal 3D Printing for Rocket Combustion Chambers? – Advantages Over Traditional Manufacturing Methods
Opting for metal 3D printing over conventional manufacturing techniques for rocket combustion chambers offers a multitude of compelling advantages:
- Design Freedom and Complexity: Additive manufacturing allows for the creation of complex internal geometries, such as intricate cooling channels and lightweight lattice structures, that are virtually impossible or prohibitively expensive to produce using traditional methods like machining or casting. This design flexibility enables engineers to optimize combustion efficiency and reduce weight.
- Materialoptimering: Metal 3D printing facilitates the use of high-performance alloys like IN625 and IN718, which exhibit excellent high-temperature strength, corrosion resistance, and creep resistance – critical properties for rocket combustion chamber applications. Metall3DP offers a wide range of these high-quality metal powders optimized for additive manufacturing processes.
- Kortare ledtider: Traditional manufacturing of complex rocket engine components can involve long lead times due to intricate tooling and multiple processing steps. Metal 3D printing significantly shortens the production cycle, enabling faster prototyping and quicker delivery of finished parts, which is crucial for rapid development cycles and urgent operational needs.
- Cost Efficiency for Low to Medium Volumes: While high-volume production may still favor traditional methods, metal 3D printing offers a cost-effective solution for producing small to medium batches of complex combustion chambers, eliminating the need for expensive tooling and reducing material waste through near-net-shape manufacturing.
- Del Konsolidering: Additive manufacturing allows for the consolidation of multiple components into a single, integrated part. This reduces the number of joints and fasteners, leading to improved structural integrity, reduced assembly time, and lower overall system weight – a significant advantage in aerospace applications.
- Customization and Tailoring: Metal 3D printing enables the customization of combustion chamber designs to meet specific mission requirements or engine configurations without incurring significant additional costs or delays. This agility is invaluable for specialized aerospace applications.
Recommended Materials and Why They Matter – IN625 and IN718 for Extreme Environments
The selection of appropriate materials is paramount for the performance and reliability of rocket combustion chambers, which operate under extreme conditions of high temperature, pressure, and corrosive environments. Two nickel-based superalloys, IN625 and IN718, are frequently recommended for metal 3D printed rocket combustion chambers due to their exceptional properties:
IN625:
- Sammansättning: Primarily composed of nickel, chromium, molybdenum, and niobium, IN625 exhibits excellent strength and toughness over a wide temperature range.
- Viktiga egenskaper:
- High creep and rupture strength at elevated temperatures.
- Excellent corrosion and oxidation resistance, crucial for withstanding the harsh chemical environment within the combustion chamber.
- Good weldability and fabricability, making it suitable for complex 3D printed structures.
- High fatigue strength, essential for components subjected to cyclic thermal and mechanical loads.
- Why it Matters for Rocket Combustion Chambers: Its superior corrosion resistance makes it ideal for handling aggressive propellants and combustion byproducts, ensuring long-term durability and performance.
IN718:
- Sammansättning: A nickel-chromium alloy strengthened by additions of niobium, molybdenum, and titanium, IN718 offers exceptional high-temperature strength and creep resistance.
- Viktiga egenskaper:
- Very high yield and tensile strength up to elevated temperatures.
- Excellent creep and stress-rupture properties, critical for maintaining structural integrity under high pressure and temperature.
- Good corrosion resistance, although typically slightly less than IN625 in certain environments.
- Relatively good processability with metal 3D printing techniques.
- Why it Matters for Rocket Combustion Chambers: Its outstanding high-temperature strength allows for the design of lighter and more efficient combustion chambers that can withstand extreme operating conditions.
Metal3DP’s advanced powder making system ensures that their IN625 and IN718 powders possess high sphericity and good flowability, which are essential for achieving dense, high-quality metal parts with superior mechanical properties through various metal 3D printing processes, as detailed on their tryckmetoder sida.
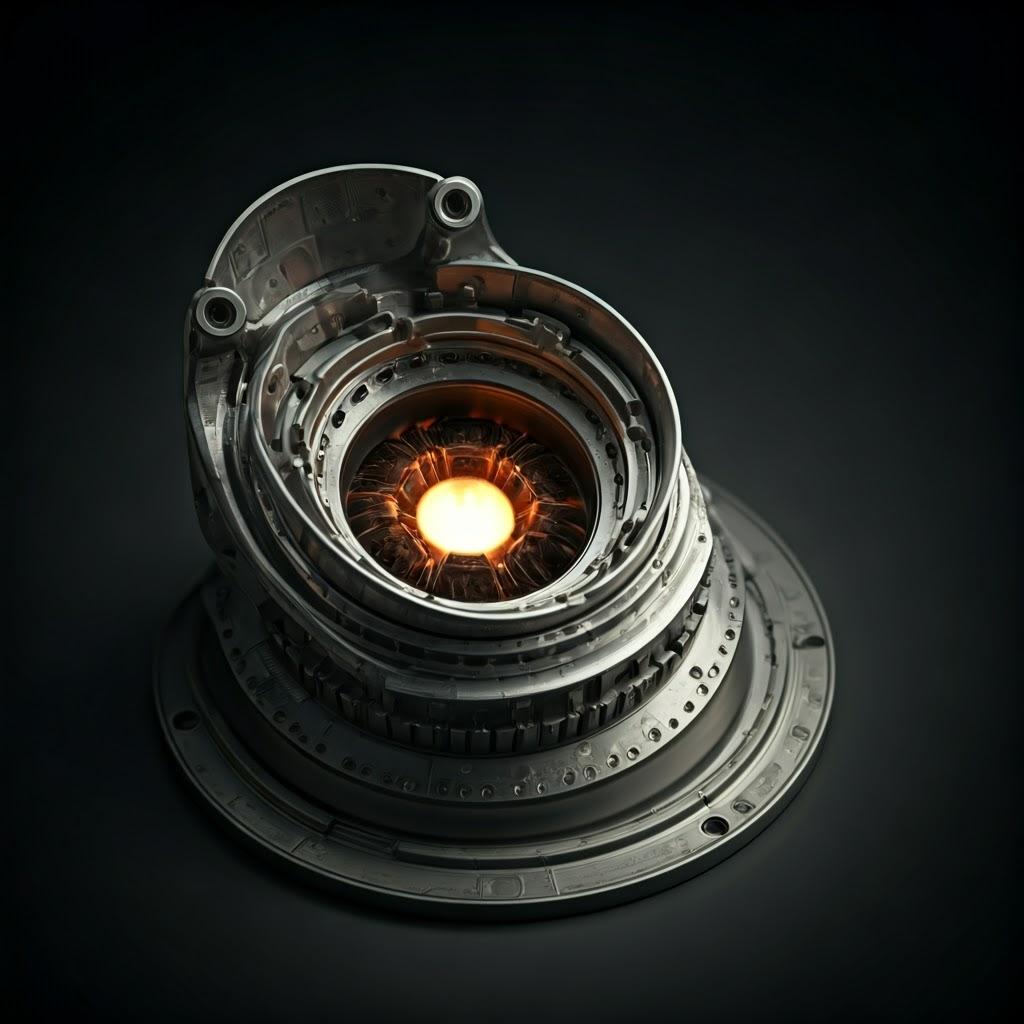
Design Considerations for Additive Manufacturing of Rocket Combustion Chambers
Optimizing the design of rocket combustion chambers for metal 3D printing requires a different mindset compared to traditional manufacturing. Embracing the unique capabilities of additive manufacturing can lead to significant improvements in performance and efficiency. Key design considerations include:
- Topology Optimization: Utilizing software tools to identify and remove material in non-critical areas while maintaining structural integrity. This can lead to significant weight reduction, a crucial factor in aerospace applications. The complex geometries resulting from topology optimization are often only achievable through metal 3D printing.
- Lattice Structures: Incorporating internal lattice structures within the combustion chamber walls can enhance stiffness-to-weight ratios and improve heat transfer characteristics. These intricate networks are a hallmark of additive manufacturing.
- Conformal Cooling Channels: Designing cooling channels that closely follow the contours of the combustion chamber walls allows for more efficient and uniform heat dissipation, preventing overheating and extending the lifespan of the component. Metal 3D printing enables the creation of these complex, conformal channels.
- Optimering av väggtjocklek: Additive manufacturing allows for the precise control of wall thickness, enabling designers to tailor the material distribution to withstand varying stress levels throughout the component. This can lead to further weight savings and improved material utilization.
- Support Structure Design: Careful consideration must be given to the design and placement of support structures required during the printing process. These supports help to prevent warping and ensure the accurate fabrication of complex overhangs and internal features. Optimizing support structures minimizes material usage and post-processing effort.
- Feature Integration: Metal 3D printing allows for the integration of multiple features, such as mounting points, sensor housings, and fluid channels, directly into the combustion chamber design. This reduces the need for separate components and assembly steps, leading to improved reliability and reduced manufacturing costs.
Tolerance, Surface Finish, and Dimensional Accuracy of 3D Printed Rocket Combustion Chambers
Achieving the required levels of tolerance, surface finish, and dimensional accuracy is critical for the performance and integration of rocket combustion chambers. Metal 3D printing technologies have made significant strides in these areas:
- Tolerance Capabilities: Selective Laser Melting (SLM) and Electron Beam Melting (EBM), common metal 3D printing processes, can achieve dimensional tolerances ranging from ±0.05 mm to ±0.2 mm, depending on the material, part geometry, and machine calibration. Precision post-processing techniques can further tighten these tolerances.
- Ytfinish: The as-printed surface finish typically ranges from 5 to 20 Ra (roughness average), which may require post-processing, such as machining, polishing, or surface coating, depending on the specific application requirements. The choice of metal powder and printing parameters also influences the final surface finish. Metal3DP’s expertise in optimizing printing parameters contributes to achieving improved surface finishes.
- Dimensionell noggrannhet: Dimensional accuracy is influenced by factors such as thermal expansion and contraction during the printing process, as well as the accuracy of the 3D printer itself. Careful process control, build orientation optimization, and the use of high-quality metal powders contribute to improved dimensional accuracy.
- Post-Processing for Precision: For critical interfaces and functional surfaces, post-processing techniques like CNC machining, grinding, and electrical discharge machining (EDM) can be employed to achieve tighter tolerances and smoother surface finishes than the as-printed state.
- Inspection and Quality Control: Rigorous inspection procedures, including coordinate measuring machines (CMM), laser scanning, and non-destructive testing (NDT), are essential to verify the dimensional accuracy and integrity of 3D printed rocket combustion chambers.
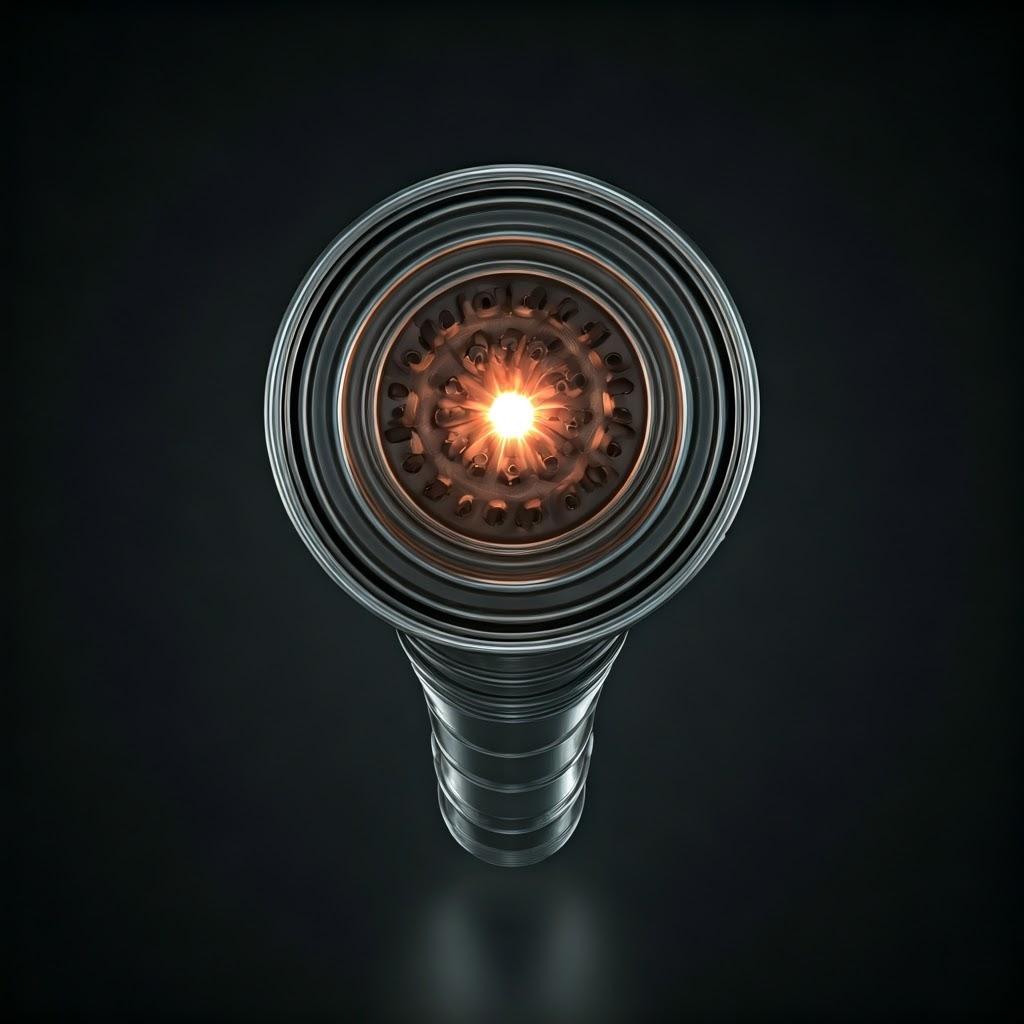
Post-Processing Requirements for Metal 3D Printed Combustion Chambers
While metal 3D printing offers near-net-shape manufacturing, post-processing steps are often necessary to achieve the final functional requirements of rocket combustion chambers:
- Stöd för borttagning: Support structures used during the printing process must be carefully removed without damaging the part. Techniques include manual removal, machining, and chemical dissolution, depending on the support material and part geometry.
- Värmebehandling: Post-printing heat treatment is crucial for relieving residual stresses, optimizing the microstructure, and achieving the desired mechanical properties of the metal alloy. This may involve processes like annealing, stress relieving, or hot isostatic pressing (HIP).
- Ytbehandling: As mentioned earlier, surface finishing processes such as machining, grinding, polishing, or abrasive flow machining (AFM) may be required to achieve the desired surface roughness for optimal performance and fluid flow.
- Beläggning: Applying coatings, such as thermal barrier coatings (TBCs) or oxidation-resistant coatings, can enhance the performance and durability of the combustion chamber in extreme temperature environments.
- Joining and Assembly: In some cases, multiple 3D printed components may need to be joined together using techniques like welding or brazing to create the final combustion chamber assembly.
- Inspection and Testing: Non-destructive testing (NDT) methods, such as ultrasonic testing, radiographic testing, and dye penetrant inspection, are used to ensure the structural integrity and quality of the finished combustion chamber.
Common Challenges and How to Avoid Them in Metal 3D Printing of Combustion Chambers
While metal 3D printing offers numerous advantages, several challenges need to be addressed to ensure successful fabrication of rocket combustion chambers:
- Warping and Distortion: Thermal stresses during the printing process can lead to warping and distortion, particularly in complex geometries. Optimizing build orientation, implementing effective support structures, and controlling process parameters can mitigate these issues.
- Porositet: The formation of pores within the printed part can compromise its mechanical properties. Using high-quality metal powders from reputable suppliers like Metall3DP, optimizing laser or electron beam parameters, and ensuring proper inert atmosphere control are crucial for minimizing porosity.
- Residual Stresses: High residual stresses can lead to cracking or failure of the printed part. Post-printing heat treatment is essential for relieving these stresses.
- Support Removal Damage: Improper support removal can damage delicate features of the combustion chamber. Careful design of support structures and the use of appropriate removal techniques are necessary.
- Ytjämnhet: Achieving a smooth surface finish directly from the printing process can be challenging. Optimizing printing parameters and employing appropriate post-processing techniques are required.
- Material Property Consistency: Ensuring consistent material properties throughout the printed part is crucial for reliable performance. Careful control of the printing process and the use of well-characterized metal powders are essential. Metal3DP’s decades of collective expertise in metal additive manufacturing contribute to ensuring material property consistency.
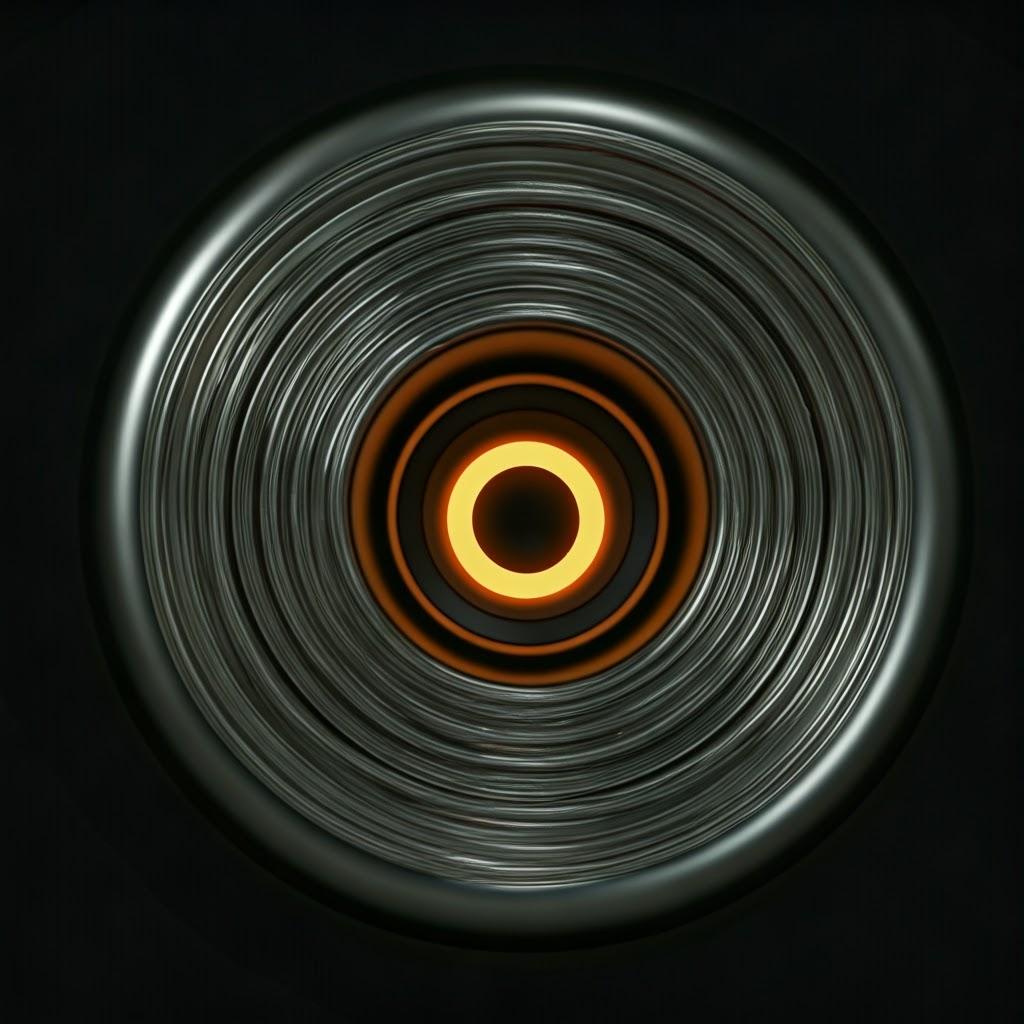
How to Choose the Right Metal 3D Printing Service Provider for Rocket Combustion Chambers
Selecting the appropriate metal 3D printing service provider is a critical decision that can significantly impact the success of your project. Here are key factors to consider 1 when evaluating potential suppliers:
- Material Capabilities: Ensure the provider has experience working with the specific metal alloys required for your combustion chamber, such as IN625 or IN718. Verify their expertise in processing these materials to achieve the desired mechanical properties. Metall3DP boasts a wide range of high-quality metal powders optimized for laser and electron beam powder bed fusion, including innovative alloys relevant to aerospace applications.
- Equipment and Technology: Understand the types of metal 3D printing technologies the provider utilizes (e.g., SLM, DMLS, EBM). Ensure their equipment is well-maintained and capable of meeting the dimensional accuracy and surface finish requirements of your application.
- Quality Assurance and Certifications: Inquire about the provider’s quality management system and relevant certifications (e.g., AS9100 for aerospace). Robust quality control procedures, including material traceability and non-destructive testing, are essential for critical aerospace components.
- Design and Engineering Support: Assess the provider’s ability to offer design optimization for additive manufacturing, including topology optimization, support structure design, and material selection guidance. Experienced engineers can help you leverage the full potential of metal 3D printing.
- Post-Processing Capabilities: Determine if the provider offers in-house post-processing services such as heat treatment, surface finishing, and coating. A comprehensive service offering can streamline the manufacturing process and ensure quality control throughout.
- Experience and Expertise: Look for a provider with a proven track record in manufacturing similar aerospace components. Their experience and expertise can help anticipate and mitigate potential challenges. Metall3DP has decades of collective expertise in metal additive manufacturing, making them a knowledgeable partner for complex projects.
- Lead Times and Production Capacity: Discuss lead times for manufacturing and any potential scale-up requirements. Ensure the provider has the capacity to meet your project timelines and future production needs.
- Cost Competitiveness: Obtain detailed quotes and understand the cost drivers for your project, including material costs, printing time, and post-processing. While cost is a factor, prioritize quality and reliability for critical aerospace components.
Cost Factors and Lead Time for 3D Printed Rocket Combustion Chambers
The cost and lead time for metal 3D printed rocket combustion chambers are influenced by several factors:
- Kostnader för material: The cost of the metal powder (e.g., IN625, IN718) is a significant factor. Specialty alloys used in aerospace applications can be expensive. The volume of material required for the part and support structures also impacts the overall material cost.
- Printing Time: The build time on the 3D printer is a key cost driver. Complex geometries and larger part volumes will require longer printing times, increasing the overall cost.
- Kostnader för efterbearbetning: The extent of post-processing required (e.g., support removal, heat treatment, machining, coating) will add to the total cost and lead time.
- Kostnader för arbetskraft: Engineering design, print setup, machine operation, and post-processing all involve labor costs that are factored into the final price.
- Machine Depreciation and Overhead: Service providers need to account for the cost of their equipment and operational overhead.
- Complexity of the Part: Intricate designs with fine features and tight tolerances will generally be more expensive and may require longer lead times due to increased printing and post-processing complexity.
- Build Volume and Quantity: Larger parts and higher production volumes can sometimes lead to economies of scale, but very small quantities may incur higher per-unit costs.
- Ledtid: Lead times can vary depending on the complexity of the part, the availability of materials, the service provider’s workload, and the required post-processing steps. Expect longer lead times for highly complex parts or when specialized post-processing is needed. Engaging with a provider like Metall3DP early in the design process can help optimize for both cost and lead time.
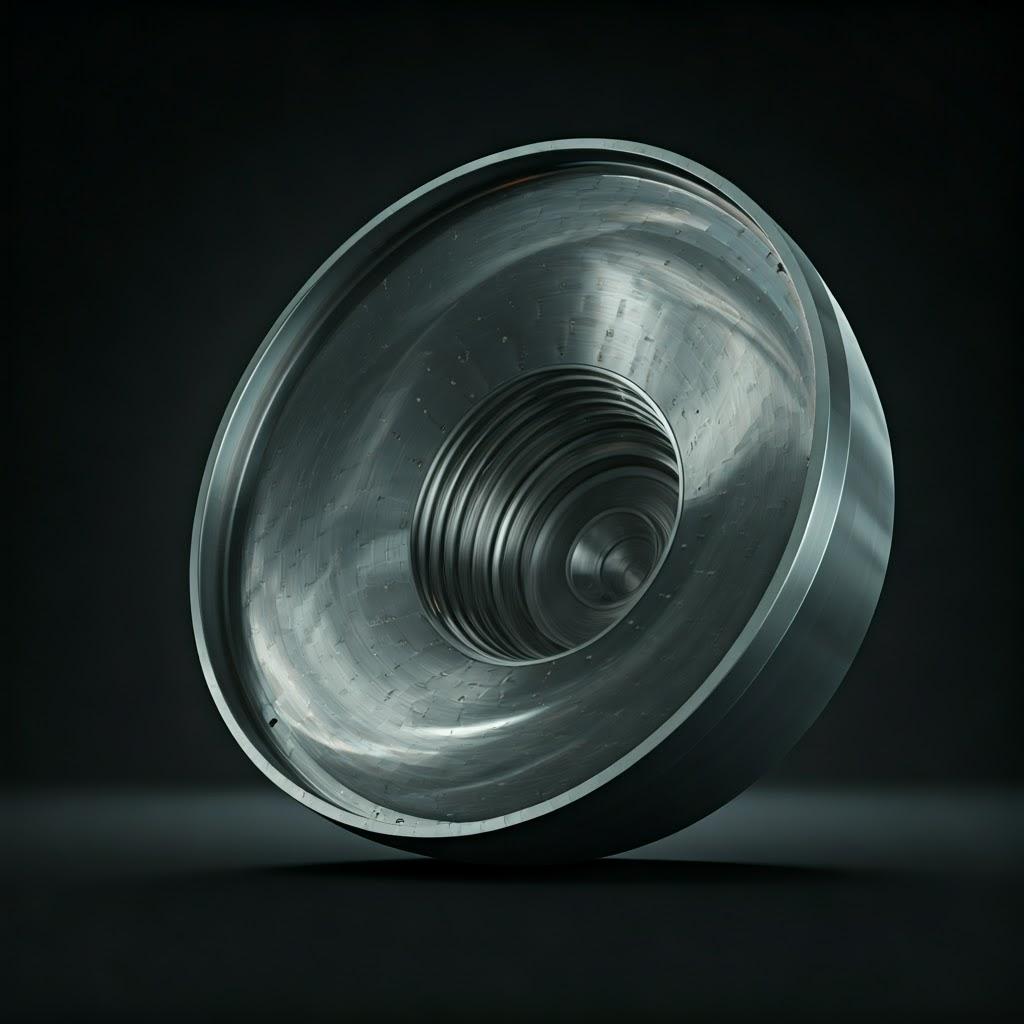
Vanliga frågor och svar (FAQ)
- Can metal 3D printed rocket combustion chambers withstand extreme temperatures and pressures? Yes, when manufactured using high-performance alloys like IN625 or IN718 and processed correctly, metal 3D printed combustion chambers can exhibit excellent high-temperature strength, creep resistance, and pressure containment capabilities required for rocket engine applications.
- What are the typical size limitations for 3D printed rocket combustion chambers? The maximum size is primarily limited by the build volume of the metal 3D printer. However, larger chambers can be manufactured in segments and then joined using welding or other suitable techniques. Metal3DP’s industry-leading print volume allows for the production of larger, more integrated components.
- Is metal 3D printing cost-effective for producing rocket combustion chambers? For low to medium production volumes, complex geometries, and rapid prototyping, metal 3D printing can be more cost-effective than traditional manufacturing methods due to reduced tooling costs and material waste. The overall cost-effectiveness depends on the specific design, material, and production volume.
Conclusion – Embracing the Future of Aerospace Propulsion with Metal 3D Printing
Metal 3D printing is revolutionizing the design and manufacturing of rocket combustion chambers, offering unprecedented opportunities for performance enhancement, weight reduction, and faster development cycles. The ability to create complex internal features, optimize material usage, and rapidly iterate on designs makes additive manufacturing an indispensable tool for the aerospace industry. Companies like Metall3DP are at the forefront of this innovation, providing advanced metal powders, cutting-edge 3D printing equipment, and comprehensive application development services to empower the next generation of aerospace propulsion systems. By embracing metal 3D printing, the aerospace sector can continue to push the boundaries of space exploration and redefine the possibilities of flight.
Dela på
MET3DP Technology Co, LTD är en ledande leverantör av lösningar för additiv tillverkning med huvudkontor i Qingdao, Kina. Vårt företag är specialiserat på 3D-utskriftsutrustning och högpresterande metallpulver för industriella tillämpningar.
Förfrågan för att få bästa pris och anpassad lösning för ditt företag!
Relaterade artiklar
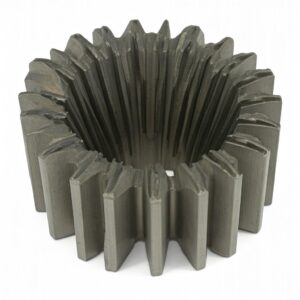
Högpresterande segment för munstycksvingar: Revolutionerande turbineffektivitet med 3D-utskrift i metall
Läs mer "Om Met3DP
Senaste uppdateringen
Vår produkt
KONTAKTA OSS
Har du några frågor? Skicka oss meddelande nu! Vi kommer att betjäna din begäran med ett helt team efter att ha fått ditt meddelande.
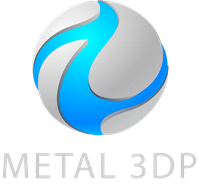
Metallpulver för 3D-printing och additiv tillverkning
FÖRETAG
PRODUKT
cONTACT INFO
- Qingdao City, Shandong, Kina
- [email protected]
- [email protected]
- +86 19116340731