Additiv tillverkning av metallpulver: En översikt
Innehållsförteckning
Additiv tillverkning, även kallat 3D-printing, används metallpulver som råmaterial för att bygga upp metalldelar och produkter lager för lager. Metallpulvrets egenskaper och karaktäristika har en betydande inverkan på kvaliteten, de mekaniska egenskaperna, precisionen och prestandan hos 3D-utskrivna metallkomponenter. Den här artikeln ger en omfattande översikt över metallpulver för additiv tillverkning.
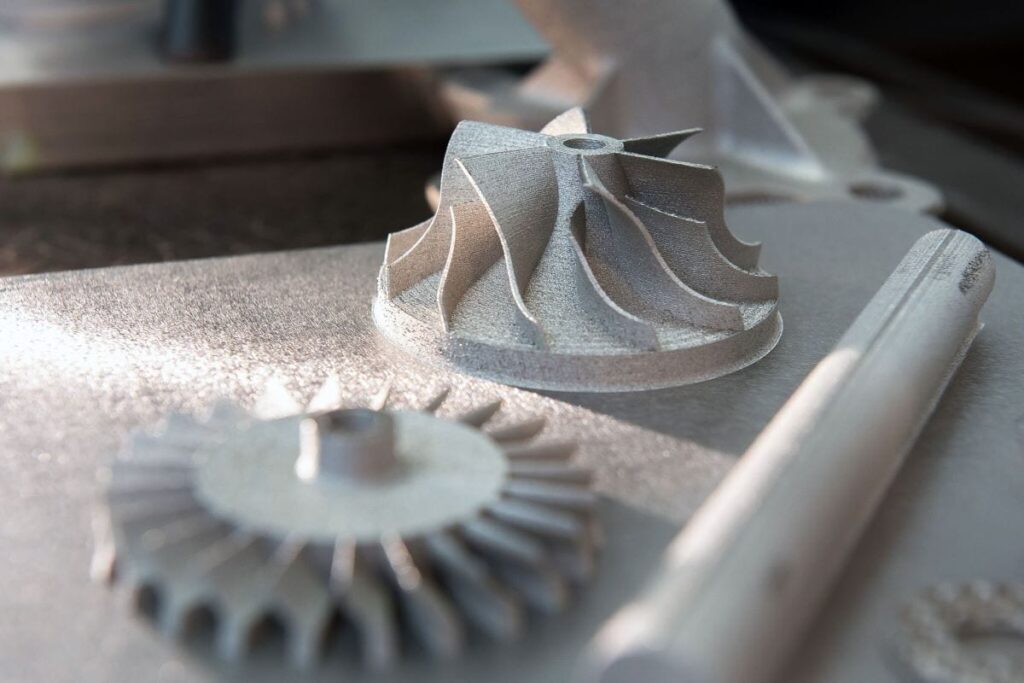
Olika typer av metallpulver för additiv tillverkning
Det finns olika typer av metaller och legeringar i pulverform för användning i 3D-utskriftstekniker. De mest använda metallpulvren inkluderar:
Olika typer av metallpulver för additiv tillverkning
Metallpulver | Viktiga egenskaper |
---|---|
Rostfritt stål | Utmärkt korrosionsbeständighet, hög hållfasthet och hårdhet. Austenitiska, martensitiska, duplexa och utskiljningshärdande kvaliteter tillgängliga. |
Aluminiumlegeringar | Låg vikt, högt förhållande mellan styrka och vikt. Al-Si- och Al-Mg-legeringar används ofta. |
Titanlegeringar | Högt förhållande mellan styrka och vikt, biokompatibilitet. Ti-6Al-4V vanligast. |
Kobolt-krom | Utmärkt slitstyrka och korrosionsbeständighet. Används för biomedicinska implantat. |
Nickellegeringar | Hållfasthet vid höga temperaturer, korrosionsbeständighet. Inconel- och Hastelloy-kvaliteter. |
Kopparlegeringar | Hög termisk och elektrisk ledningsförmåga. Mässing och brons tillgängliga. |
Ädelmetaller | Utmärkt kemisk stabilitet. Guld, silver och platina används till smycken. |
Metallpulvrets partikelform, storleksfördelning, flödesegenskaper och mikrostruktur kan variera avsevärt beroende på produktionsmetod. Detta påverkar packningstätheten, spridningsförmågan och sintringsbeteendet under 3D-utskrift.
Produktionsmetoder för metallpulver
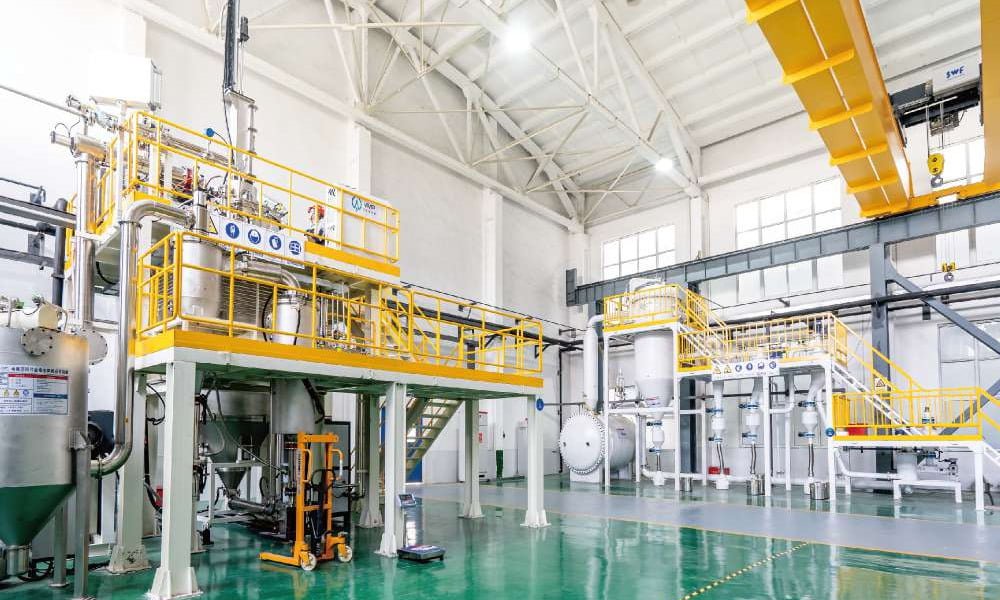
Det finns flera olika produktionstekniker som används för att tillverka metallpulver för additiv tillverkning:
Metoder för produktion av metallpulver
Metod | Beskrivning | Partikelegenskaper |
---|---|---|
Atomisering av gas | Smält metallström finfördelas av inert gas under högt tryck till fina droppar som stelnar till sfäriska pulverpartiklar. | Utmärkt flytbarhet. Kontrollerad partikelstorleksfördelning. Sfärisk morfologi. |
Atomisering av vatten | Smält metallström bryts i droppar av vattenstrålar med hög hastighet. Snabb kylning leder till oregelbundna pulverformer. | Mer föroreningar. Bredare storleksfördelning. Oregelbundna partikelformer med satelliter. |
Plasmaatomisering | Metallpulver som produceras genom att smält metall finfördelas med en plasmastråle. Snabba kylhastigheter ger fina, sfäriska pulver. | Mycket fint, sfäriskt pulver. Kontrollerad storleksfördelning. Används för reaktiva legeringar. |
Induktionssmältning med elektrod | Metalltråd matas in i smältkammaren och smälts av induktionsspolar. Droppar faller genom kammaren och stelnar till pulver. | Medelstora partikelstorlekar. Satellitbildning på partiklar. |
Mekanisk slipning | Grovt metallpulver som framställs genom mekanisk fräsning och slipning. | Bred partikelstorleksfördelning. Oregelbundna partikelformer med inre porositet. |
Dehydrering av metall | Hydrid-dehydridprocessen reducerar metall till fint pulver. Används för titan- och zirkoniumlegeringar. | Spongiösa partiklar med hög inre porositet. Kan behöva jetfräsning. |
Gasatomisering och vattenatomisering är de vanligaste metoderna för att producera fina pulver för 3D-utskriftsprocesser med pulverbäddfusion. Pulverproduktionstekniken påverkar sammansättningen, partikelformen, porositeten, flödesegenskaperna, mikrostrukturen och kostnaden för metallpulvret.
Metallpulvers egenskaper och karaktäristik
Egenskaperna hos metallpulver som används vid additiv tillverkning spelar en avgörande roll för att bestämma den slutliga detaljens kvalitet, mekaniska egenskaper, precision, ytfinish och prestanda. Några viktiga egenskaper inkluderar:
Metallpulvers egenskaper för additiv tillverkning
Fastighet | Beskrivning | Betydelse |
---|---|---|
Partikelform | Sfärisk, satellitisk, oregelbunden form | Påverkar flöde, packningstäthet och spridningsförmåga i pulverbädden |
Fördelning av partikelstorlek | Intervall av partikeldiametrar i pulver | Påverkar detaljupplösning, ytfinhet, densitet |
Flytbarhet | Pulvrets förmåga att flöda fritt under tyngdkraften | Påverkar pulverspridning och jämnhet i pulverbädden |
Skenbar densitet | Massa per volymenhet av löst pulver | Påverkar byggvolym, sintringskinetik |
Tappdensitet | Maximal packningstäthet under vibration/tappning | Indikerar spridningsförmåga och förtätning under sintring |
Hall Flödeshastighet | Tid som krävs för att 50 g pulver ska flöda genom en öppning | Mått på flytbarhet och konsistens |
Hausner-kvot | Förhållandet mellan tappdensitet och skenbar densitet | Högre förhållande indikerar mer friktion mellan partiklarna, sämre flöde |
Fukthalt | Vatteninnehåll som absorberas på pulverpartiklarnas yta | För hög fukthalt orsakar agglomerering av pulver |
Syrehalt | Syre som absorberas på pulverpartikelytor | Kan påverka pulvrets flytbarhet och orsaka porositet i den färdiga detaljen |
Mikrostruktur | Kornstorlek, korngränser, förekommande faser | Påverkar mekaniska egenskaper, anisotropi och defekter i den färdiga detaljen |
Att uppfylla de stränga kraven för dessa pulveregenskaper är avgörande för att uppnå hög densitet, goda mekaniska egenskaper och kvalitet för additivt tillverkade komponenter.
Specifikationer för metallpulver
Metallpulver som används vid additiv tillverkning måste uppfylla vissa specifikationer när det gäller sammansättning, partikelstorleksfördelning, flödeshastighet, skenbar densitet och mikrostruktur. Några vanliga specifikationer för metallpulver är t.ex:
Typiska specifikationer för metallpulver för additiv tillverkning
Parameter | Typisk specifikation |
---|---|
Legeringens sammansättning | ± 0,5 wt% av specificerad kemi |
Partikelstorlek | 10-45 μm |
D10 partikelstorlek | 5-15 μm |
D50 partikelstorlek | 20-40 μm |
D90 partikelstorlek | 40-100 μm |
Skenbar densitet | 2,5-4,5 g/cc |
Tappdensitet | 3,5-6,5 g/cc |
Hausner-kvot | <1.25 |
Hall flödeshastighet | <30 sekunder för 50 g |
Fukthalt | <0,2 wt% |
Syrehalt | 150-500 ppm |
Storleksfördelningen är avgörande, med vanliga D10-, D50- och D90-partikelstorlekar mellan 5-100 mikrometer. En snävare fördelning förbättrar pulverbäddens densitet och upplösning. Standarder som ASTM F3049, F3301 och ISO/ASTM 52921 anger strikta regler för metallpulver som används vid additiv tillverkning.
Tillämpningar av metallpulver inom additiv tillverkning
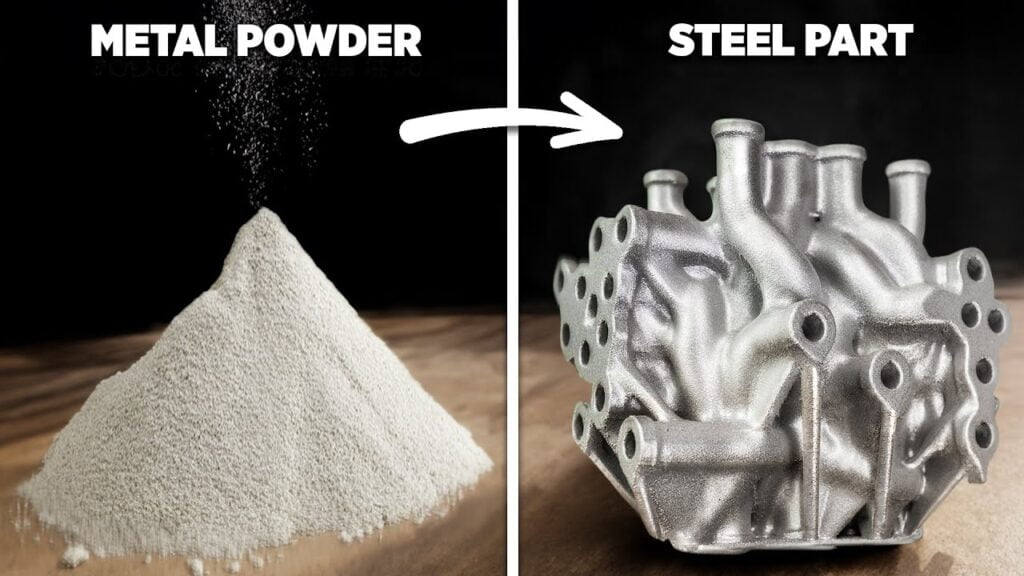
Metallpulver används i olika additiva tillverkningstekniker för att skriva ut funktionella metalldelar inom olika branscher:
Tillämpningar av metallpulver inom additiv tillverkning
Industri | Tillämpningar | Metaller som används |
---|---|---|
Flyg- och rymdindustrin | Turbinblad, raketmunstycken, värmeväxlare | Ti, Ni, Co-legeringar |
Medicinsk | Tandkronor, implantat, kirurgiska verktyg | Ti, CoCr, rostfritt stål |
Fordon | Lättviktsdesign för prototyper och specialtillverkade delar | Al-, stål- och Ti-legeringar |
Industriell | Kylflänsar, grenrörsblock, robotik | Al, rostfritt, verktygsstål |
Smycken | Anpassade smycken, snabb prototyptillverkning | Guld-, silver- och platina-legeringar |
Olja & Gas | Rördelar, ventiler, pumphus | Rostfria stål, Inconel |
Additiv tillverkning med metallpulver är idealisk för att tillverka komplexa, kundanpassade komponenter med förbättrade mekaniska egenskaper och former som inte är möjliga med konventionell tillverkning. Det växande utbudet av tillgängliga metallegeringar fortsätter att öka antalet tillämpningar inom olika branscher.
Kostnadsanalys av Metallpulver
Typen av metallpulver och den kvalitet som krävs har en betydande inverkan på materialkostnaden vid additiv tillverkning. Några typiska kostnader för metallpulver är:
Prisintervall för metallpulver för additiv tillverkning
Material | Prisintervall |
---|---|
Aluminiumlegeringar | $50-100/kg |
Rostfria stål | $50-150/kg |
Verktygsstål | $50-200/kg |
Titanlegeringar | $200-500/kg |
Superlegeringar av nickel | $100-300/kg |
Kobolt Krom | $150-250/kg |
Ädelmetaller | $1500-3000/kg för guld, silver |
Priserna varierar beroende på legeringssammansättning, partikelegenskaper, pulverkvalitet och inköpsvolym. Att minska materialavfallet genom att återvinna oanvänt pulver kan förbättra kostnadseffektiviteten vid tryckning med dyra legeringar.
Detaljerad prisuppdelning för metallpulver
Kostnaderna för metallpulver kan utgöra en betydande del av de totala kostnaderna för additiv tillverkning. I detta avsnitt ges mer information om aktuella prisintervall för olika metallegeringar:
Prissättning av titanlegeringspulver
Legering | Pris per kg |
---|---|
Ti-6Al-4V ELI | $350-500 |
Ti 6Al-4V klass 5 | $250-400 |
Ti 6Al-4V klass 23 | $300-450 |
Ti 6Al-4V klass 35 | $250-350 |
Ti-6Al-2Sn-4Zr-6Mo | $400-600 |
Ti-55531 | $500-800 |
Den mest använda Ti-6Al-4V-legeringen för flyg- och rymdtillämpningar varierar från $250-500/kg. Mer avancerade titanlegeringar kan kosta över $800/kg.
Aluminiumlegering Pulver Prissättning
Legering | Pris per kg |
---|---|
AlSi10Mg | $90-120 |
AlSi7Mg | $80-100 |
AlSi12 | $75-90 |
AlSi10Mg med nanopartiklar | $250-500 |
Al 6061 | $100-150 |
Al 7075 | $80-120 |
Aluminiumlegeringar ligger i allmänhet på $80-150/kg med specialiserade sammansättningar och nanoförstärkta pulver som ger premiumpriser från $250-500/kg.
Prissättning av nickellegeringspulver
Legering | Pris per kg |
---|---|
Inconel 718 | $150-300 |
Inconel 625 | $120-250 |
Hastelloy X | $200-350 |
Haynes 282 | $200-400 |
Inconel 939 | $300-800 |
Nickel-superlegeringar varierar från $120-800/kg beroende på legeringssammansättning, partikelegenskaper och bulkordervolymer.
Ädelmetaller som används för smycken och medicintekniska produkter betingar mycket höga priser från $1500-3000/kg för guld-, silver- och platina-legeringar.
Genom att förstå de aktuella prisnivåerna för de vanligaste legeringarna kan man göra välgrundade val av kostnadseffektiva material för specifika applikationer.
Prissättning av pulver av rostfritt stål
Legering | Pris per kg |
---|---|
316L | $50-100 |
17-4PH | $100-150 |
15-5PH | $150-200 |
304L | $30-60 |
420 rostfritt stål | $35-75 |
Pulver av rostfritt stål varierar från $30-200/kg beroende på kvalitet. Mer specialiserade legeringar och sammansättningar med snävare specifikationer ger högre priser.
Prissättning av pulver för verktygsstål
Legering | Pris per kg |
---|---|
H13 Verktygsstål | $90-120 |
Maråldrat stål | $180-250 |
Koppar Verktygsstål | $120-200 |
Verktygsstål för varmbearbetning | $80-150 |
Priserna på pulver av verktygsstål varierar från $80-250/kg beroende på hårdhet, legeringssammansättning och partikelegenskaper.
Prissättning av pulver av kopparlegering
Legering | Pris per kg |
---|---|
Koppar | $100-150 |
Brons | $50-120 |
Mässing | $60-100 |
Pulver av koppar och kopparlegeringar som används för sina termiska och elektriska egenskaper är $50-150/kg.
Prissättning av pulver av kobolt-kromlegering
Legering | Pris per kg |
---|---|
CoCrMo | $170-220 |
CoCrW | $180-230 |
CoCrMoWC | $220-300 |
Kobolt-kromlegeringar av medicinsk kvalitet varierar från $170-300/kg beroende på sammansättning och partikelegenskaper.
Priserna på metallpulver spänner över ett brett område baserat på legering, produktionsmetod, kvalitet och ordervolym. Men genom att förstå de aktuella marknadspriserna får man bra vägledning vid produktdesign och materialval för additiv tillverkning.
Inom additiv tillverkning finns det två huvudsakliga metoder för att använda metallpulver som råmaterial: fusionsprocesser med pulverbädd och deponeringsprocesser med riktad energi. I detta avsnitt jämförs de olika kraven och egenskaperna för pulver mellan pulverbädds- och blåspulvermetoderna.
Fusionsprocesser i pulverbädd
I pulverbäddsfusionsprocesser som selektiv lasersintring (SLS) och elektronstrålesmältning (EBM) sprids metallpulvret i tunna lager över en byggplatta och smälts selektivt av en värmekälla lager för lager för att tillverka en detalj. Några viktiga skillnader i pulveregenskaper inkluderar:
Krav på pulver för pulverbäddsfusion
Parameter | Typisk specifikation | Anledning |
---|---|---|
Fördelning av partikelstorlek | Tätare fördelning runt 20-45 μm | För att uppnå jämn skikttjocklek och hög packningstäthet |
Partikelns morfologi | Mycket sfäriska, släta ytor | För att möjliggöra bra flöde och spridbarhet över pulverbädden |
Inre porositet | Minimal porositet eller ihåliga partiklar | För att minska antalet defekter och uppnå hög densitet i tryckta komponenter |
Skenbar densitet | Över 50% av legeringens densitet | För att maximera pulverbäddens densitet och minimera antalet passeringar i ommålaren |
Flödesegenskaper | Jämnt och konsekvent pulverflöde | Avgörande för jämn skiktuppbyggnad och felfria detaljer |
Sfäriska gasatomiserade pulver med kontrollerad storleksfördelning och god flytbarhet är idealiska för AM-processer med pulverbäddsfusion.
Blåsning av pulver med riktad energideposition
I DED-tekniker som LENS (laser engineered net shaping) och EBAM (electron beam additive manufacturing) sprutas metallpulvret direkt in i en smält pool som skapas av en värmekälla med laser eller elektronstråle. Viktiga skillnader mellan pulver och pulverbädd:
Krav på pulver för blåst pulver DED
Parameter | Typisk specifikation | Anledning |
---|---|---|
Fördelning av partikelstorlek | Bredare distribution från 10-150 μm typiskt | För att möjliggöra pulverflödbarhet samt penetration av smältbadet |
Partikelns morfologi | Kan använda oregelbundna former och satelliter | Flytbarhet mindre kritisk än inträngning i smältbadet |
Inre porositet | Kan tolerera mer porositet | Snabb smältning minimerar påverkan på den slutliga detaljdensiteten |
Skenbar densitet | >60% av legeringens densitet | Förbättrat pulverflöde och mixerbelastning |
Flödesegenskaper | Måttlig flytbarhet | Främst för att undvika klumpbildning och säkerställa en jämn pulverström |
Med DED för blåspulver är kraven på pulverråvaran mer flexibla jämfört med fusionsprocesser i pulverbäddar. En viktig fördel med DED är möjligheten att använda pulverproduktionsmetoder till lägre kostnad.
Pulveröverväganden för kvalitet och kostnad
Sammanfattningsvis ställer pulverbäddfusion strängare krav på pulveregenskaper för att förhindra defekter och uppnå detaljer med hög densitet. Detta kräver vanligtvis användning av dyrare gasatomiserade pulver. Blown powder DED ger större flexibilitet att använda billigare pulver, men detta kan påverka de mekaniska egenskaperna och noggrannheten. Detaljstorlek, krav på ytfinish, mekanisk prestanda och budget är nyckelfaktorer vid val av lämplig additiv tillverkningsprocess och pulverråvara.
Additiv tillverkning av metallmatriskompositer
Metallmatriskompositer (MMC) med keramiska förstärkningar är ett framväxande område inom pulverbaserad additiv tillverkning. Detta avsnitt ger en översikt över tryckning av MMC med hjälp av pulverbäddfusion och deponering med riktad energi från blåspulver.
MMC Additiv tillverkning med hjälp av pulverbäddsfusion
Förstärkningar som karbider, borider och oxider kan blandas med metallegeringspulver för att trycka partikelförstärkta metallmatriskompositer med förbättrade egenskaper:
MMC-pulver för pulverbäddsfusion AM
Matris | Förstärkning | Viktiga egenskaper |
---|---|---|
AlSi10Mg | SiC, Al2O3 | Slitstyrka, högre styvhet |
Ti6Al4V | TiB2, TiC | Ökad styrka och hårdhet |
Inconel 718 | WC, ZrO2 | Förbättrad hållfasthet vid höga temperaturer |
CoCr | WC, TaC | Utmärkt slitstyrka |
316L rostfritt stål | Y2O3, TiO2 | Högre hållfasthet och seghet |
Faktorer som skillnader i smältpunkter, dålig vätbarhet och agglomerering av förstärkningar kan dock orsaka defekter och utmaningar vid tryckning av högkvalitativa MMC-delar. Nanoskaliga förstärkningar och skräddarsydda parametrar för pulverblandning och spridning krävs för att framgångsrikt skriva ut täta, isotropa MMC med hjälp av pulverbäddsfusion AM.
MMC Additiv tillverkning med hjälp av blåst pulver DED
DED-metoder med blåst pulver ger fördelar vid tryckning av MMC:
- Förstärkningarna kan injiceras direkt i smältbadet, vilket undviker problem med agglomerering
- Snabb smältning och stelning förbättrar keramikfördelningen
- Större partikelstorlekar och högre armeringsfraktioner kan användas
Men det är fortfarande en utmaning att kontrollera armeringsinnehållet över hela bygghöjden och uppnå en jämn fördelning. Med hybrida AM-system som kombinerar pulverbäddsfusion och DED kan metaller med hög densitet, som koppar, skrivas ut som en kontinuerlig matris med hjälp av pulverbäddsfusion samtidigt som keramiska förstärkningar injiceras för att lokalt förstärka eller härda regioner.
Sammantaget möjliggör additiv tillverkning tillverkning av komplexa MMC-komponenter i nätform med lokalt skräddarsydda sammansättningar och egenskaper som inte är möjliga med konventionell komposittillverkning. Men utveckling av råmaterialpulver och utskriftsparametrar som är skräddarsydda för specifika metallkeramiska system är avgörande för att förverkliga den fulla potentialen för utskrift av partikelförstärkta MMC med AM.
Vanliga frågor om metallpulver för additiv tillverkning
Här får du svar på några vanliga frågor om metallpulver som används i additiva tillverkningsprocesser:
Vanliga frågor om metallpulver för AM
F: Vilket är det vanligaste metallpulvret för 3D-utskrifter?
A: Aluminiumlegeringar, särskilt AlSi10Mg, är en av de mest populära metallerna för pulverbaserad AM inom flyg-, fordons- och industriapplikationer på grund av deras låga vikt, korrosionsbeständighet och kostnadsfördelar jämfört med titan- och nickellegeringar.
F: Vilket är det dyraste metallpulvret?
S: Ädelmetaller som guld, silver och platina har de högsta materialkostnaderna på $1500-3000 per kilo. Titanlegeringar är också relativt dyra med över $200/kg. Superlegeringar av nickel kostar mellan $100-300/kg beroende på sammansättning.
F: Vad är skillnaden mellan jungfruligt och återvunnet metallpulver?
S: Virgin powder är nyproducerat puder som inte har använts i tryck tidigare. Återvunnet pulver är pulver som återvinns efter en tryckning och återanvänds. Återvunnet pulver kan vara 20-30% billigare, men det finns risk för kontaminering och förändringar i egenskaperna efter flera återanvändningscykler.
F: Vad är avgörande för att bestämma metallpulverstorleksfördelningen?
A: En snäv partikelstorleksfördelning är avgörande för pulverbäddsfusion AM för att möjliggöra enhetlig skikttjocklek, hög packningstäthet, bra flöde och upplösning. Typiska fördelningar är D10: 20-40 mikrometer, D50: 20-45 mikrometer, D90 under 100 mikrometer.
F: Hur påverkar fukt i metallpulver AM-processer?
A: Fukt som absorberas av pulverpartiklar kan göra att pulvret klumpar ihop sig och försämrar flödet. Överflödig fukt leder också till porositet i tryckta delar. De flesta processer kräver en fukthalt under 0,2 wt% genom torkning.
F: Vilken roll spelar återvinningsbarhet av pulver i AM?
S: Återvinning av oanvänt pulver efter tryckning minskar materialspill och kostnader, särskilt för dyra legeringar. Men kontaminering kan förekomma efter återanvändning. Processer med inerta atmosfärer eller vakuum minimerar oxidationen och förbättrar återvinningsbarheten.
Fråga: Hur används metallpulver med bimodal fördelning i AM?
S: Bimodala pulver med två distinkta fraktioner av grovt och fint pulver kan förbättra packningsdensiteten och utskriftsupplösningen. Det finare pulvret packas mellan större partiklar. Men sådana pulver kräver expertis för att säkerställa korrekt blandning och hantering.
Q: Tillåter AM användning av billigare pulver av lägre kvalitet jämfört med andra processer?
S: DED AM med pulverblåsning kan använda lågkostnadspulver från andra produktionsmetoder som kanske inte uppfyller de strikta specifikationerna för pulverbäddsfusion. Men detta kan försämra de mekaniska egenskaperna och noggrannheten jämfört med gasatomiserade pulver.
Slutsats
Sammanfattningsvis fungerar metallpulver som ett grundläggande råmaterial för tillverkning av 3D-tryckta metallkomponenter med hjälp av additiv tillverkningsteknik med pulverbäddsfusion och riktad energideposition. Metallpulverråvarans egenskaper och kvalitet har stor betydelse för den slutliga detaljens egenskaper, precision, ytfinish och prestanda inom flyg- och rymdindustrin, medicinteknik, fordonsindustrin och industrin. Gasatomisering och vattenatomisering är de primära produktionsmetoderna. Viktiga pulveregenskaper som partikelstorleksfördelning, morfologi, skenbar densitet, flödesegenskaper och mikrorenhet måste uppfylla stränga specifikationer för AM-processer och krav på slutdetaljer. Fortsatta framsteg inom teknik, modellering och karakterisering av skräddarsydda metallpulver kommer att vara avgörande för att frigöra den fulla potentialen för additiv tillverkning med metaller.
Dela på
MET3DP Technology Co, LTD är en ledande leverantör av lösningar för additiv tillverkning med huvudkontor i Qingdao, Kina. Vårt företag är specialiserat på 3D-utskriftsutrustning och högpresterande metallpulver för industriella tillämpningar.
Förfrågan för att få bästa pris och anpassad lösning för ditt företag!
Relaterade artiklar
Om Met3DP
Senaste uppdateringen
Vår produkt
KONTAKTA OSS
Har du några frågor? Skicka oss meddelande nu! Vi kommer att betjäna din begäran med ett helt team efter att ha fått ditt meddelande.
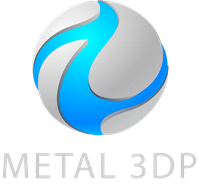
Metallpulver för 3D-printing och additiv tillverkning