3D Printed Aerospace Beams in High-Strength Aluminum
Innehållsförteckning
The aerospace industry operates at the pinnacle of engineering, demanding components that are simultaneously lightweight, exceptionally strong, and flawlessly reliable. Every gram saved translates into significant fuel efficiency gains or increased payload capacity, while structural integrity is non-negotiable for safety and mission success. Traditionally, manufacturing complex aerospace components like structural beams involved subtractive methods, often machining parts from solid blocks of metal, leading to significant material waste and design limitations. However, the advent of metal additive manufacturing (AM), or 3D-utskrifter, is fundamentally reshaping how these critical parts are designed and produced. Specifically, the ability to 3D print aerospace beams using high-strength aluminum alloys like Scalmalloy® and AlSi10Mg offers unprecedented advantages in weight reduction, design complexity, and production agility. This technology allows engineers to create optimized, intricate structures previously impossible to manufacture, pushing the boundaries of aircraft and spacecraft performance. Companies like Met3dp, with deep expertise in both advanced metal powders and industrial 3D printing systems, are at the forefront of this revolution, enabling the production of next-generation aerospace components.
Introduction: Revolutionizing Aerospace Structures with 3D Printed Aluminum Beams
The quest for lighter, stronger, and more efficient aircraft and spacecraft is relentless. Structural beams form the skeletal framework of these vehicles, bearing significant loads and dictating overall structural integrity. For decades, aerospace engineers relied on established manufacturing processes, primarily subtractive machining and casting, to produce these vital components. While effective, these methods often impose constraints on design geometry and result in substantial “buy-to-fly” ratios, where a large amount of raw material is purchased relative to the final weight of the part, leading to inefficiency and waste.
Metal additive manufacturing emerges as a disruptive force, offering a paradigm shift in the creation of aerospace structural elements. Instead of carving away material, AM builds parts layer by layer directly from digital models, using specialized metal powders fused by lasers or electron beams. This additive approach unlocks several key benefits crucial for aerospace:
- Oöverträffad designfrihet: AM liberates engineers from the constraints of traditional manufacturing. Complex internal channels for cooling, intricate lattice structures for optimal strength-to-weight ratios, and organically shaped, topology-optimized geometries become feasible. This allows beams to be designed precisely for their load paths, shedding unnecessary mass without compromising performance.
- Significant Weight Reduction (Lightweighting): By enabling optimized designs and utilizing advanced lightweight materials like high-strength aluminum alloys, AM can drastically reduce the weight of structural beams. Topology optimization algorithms, often used in conjunction with AM, mathematically determine the most efficient material distribution to withstand specific loads, resulting in skeletal, yet robust, structures. This weight saving directly impacts fuel consumption, range, emissions, and payload capacity across aviation and space applications.
- Materialeffektivitet: AM is inherently less wasteful than subtractive manufacturing. Material is only placed where it is needed, significantly reducing the buy-to-fly ratio. While unused powder can often be recycled within the AM process, the initial material required is substantially less than a solid billet for machining.
- Del Konsolidering: Complex assemblies previously requiring multiple parts, fasteners, and joining processes can often be consolidated into a single, monolithic component using AM. This simplifies the supply chain, reduces assembly time and labor, eliminates potential failure points at joints, and further contributes to weight reduction.
- Accelerated Prototyping and Production: AM allows for rapid iteration during the design phase. Prototypes can be printed and tested quickly, shortening development cycles. For low-to-medium volume production runs, AM can also offer shorter lead times compared to the tooling and setup required for traditional methods, enabling more agile manufacturing strategies.
High-strength aluminum alloys, particularly Scalmalloy® and AlSi10Mg, are ideal candidates for 3D printing aerospace beams. They offer excellent strength-to-weight ratios, good corrosion resistance, and processability via common AM techniques like Laser Powder Bed Fusion (LPBF) and Electron Beam Melting (EBM – though EBM is less common for these specific Aluminum alloys compared to LPBF or Met3dp’s specialized SEBM). Scalmalloy®, in particular, was developed specifically for additive manufacturing and boasts properties superior to many conventional high-strength aluminum alloys, even after heat treatment.
Met3dp, a leader in metalladditiv tillverkningslösningar, provides both the high-performance metal powders and the advanced printing systems necessary to realize these benefits. Their expertise in powder metallurgy, employing advanced gas atomization and Plasma Rotating Electrode Process (PREP) technologies, ensures the production of spherical, high-purity aluminum powders like AlSi10Mg, optimized for dense, high-quality printing. Coupled with their industry-leading printers known for accuracy and reliability, Met3dp empowers aerospace manufacturers to leverage the full potential of AM for critical structural applications. The transition towards 3D printed aluminum beams isn’t just an incremental improvement; it’s a fundamental step towards the next generation of aerospace design and manufacturing, enabling lighter, faster, and more capable flight.
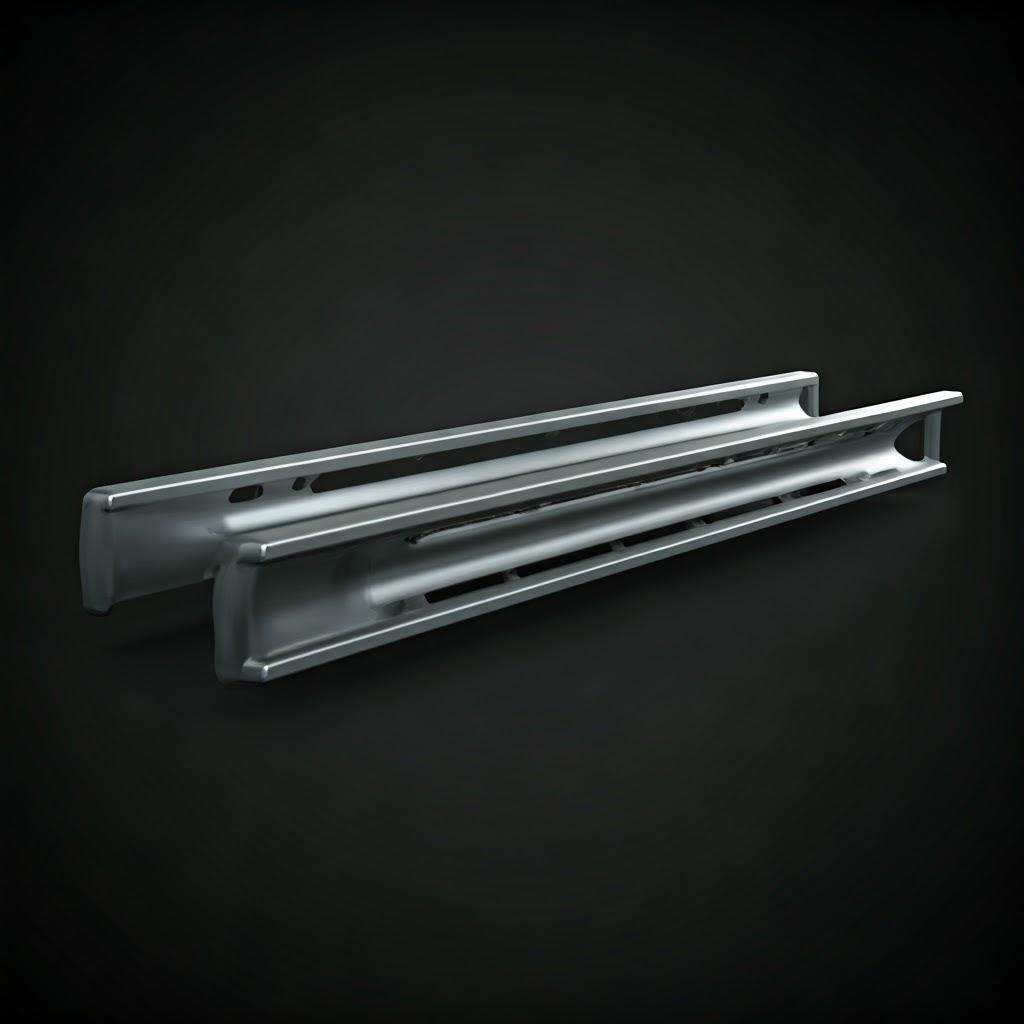
Applications: Where are 3D Printed Aluminum Beams Taking Flight?
The unique advantages of 3D printed high-strength aluminum beams – lightweighting potential, design freedom, and part consolidation – make them suitable for a growing range of demanding aerospace applications. Procurement managers and engineers across the sector are increasingly specifying AM aluminum for components where performance and efficiency are paramount. Key application areas include:
- Airframe Structural Components:
- Ribs and Spars: These internal wing and fuselage components provide structural support and shape. AM allows for topology-optimized ribs and spars that minimize weight while maintaining stiffness and strength, directly contributing to fuel efficiency. Complex internal cutouts and optimized load paths, difficult or impossible to machine traditionally, can be readily incorporated.
- Brackets and Mounts: Aircraft contain numerous brackets for mounting systems, equipment, and wiring. Often complex in shape and needing to withstand specific load vectors, these are prime candidates for AM. 3D printing enables the consolidation of multiple bracket pieces into a single, lighter, and stronger component, reducing part count and assembly time. High-strength aluminum offers the necessary durability.
- Fuselage Frames: Certain frame sections, particularly around doors, windows, or areas with complex load introductions, can benefit from the design optimization enabled by AM. Creating customized, lightweight frames tailored to specific stress distributions is a key advantage.
- Satellite and Spacecraft Structures:
- Bus Structures: The satellite bus houses the primary payload and subsystems. Every gram launched into orbit costs thousands of dollars, making weight reduction paramount. 3D printed aluminum beams and nodes allow for highly optimized, lattice-based bus structures that provide the required stiffness and mounting points at a fraction of the weight of traditionally manufactured counterparts.
- Antenna Supports and Booms: Large deployable antennas and instrument booms require lightweight yet stiff support structures. AM enables intricate, optimized designs for these deployable beams, often incorporating complex hinges or mounting interfaces directly into the printed part. Scalmalloy® is particularly favored here for its high specific strength.
- Optical Benches and Instrument Mounts: Stability and minimal thermal expansion are critical for optical systems. While specialized alloys are often used, certain mounting structures and supporting beams within instrument packages can be made from 3D printed aluminum, benefiting from lightweighting and the ability to integrate vibration-damping features through complex geometries.
- Unmanned Aerial Vehicles (UAVs / Drones):
- Airframes: UAVs, especially those designed for long endurance or high payload capacity, benefit significantly from weight reduction. 3D printed aluminum beams can form key parts of the airframe, offering superior strength-to-weight ratios compared to composites in some applications, or enabling complex integrations not possible with conventional methods.
- Komponenter till landningsställ: Certain landing gear elements can be redesigned using AM for weight savings and shock absorption optimization, utilizing the properties of alloys like AlSi10Mg.
- Engine and Propulsion System Components:
- Structural Brackets: While high-temperature superalloys dominate the hot sections, numerous structural brackets and mounts exist within the cooler sections of jet engines and rocket propulsion systems. 3D printed aluminum alloys can offer weight savings for these components.
- Housings (Non-critical temperature): Certain gearbox or accessory housings operating at moderate temperatures can be candidates for lightweighting using AM aluminum.
- Interior Components:
- Seat Frames and Supports: While less common for primary structures, opportunities exist for using 3D printed aluminum beams in optimized seat frames or support structures within the aircraft cabin, contributing to overall weight reduction goals.
Industry Adoption Drivers:
- Förbättring av prestanda: The primary driver is the ability to achieve performance levels (especially specific strength and stiffness) unattainable with traditional designs and manufacturing.
- Supply Chain Optimization: Reducing part count through consolidation simplifies logistics, inventory management, and assembly processes – key concerns for aerospace procurement managers.
- Kortare ledtider: For complex or low-volume parts, AM can bypass the need for expensive tooling (like jigs, fixtures, or molds) and long setup times associated with machining, shortening the time from design finalization to part delivery. This agility is crucial in rapid development cycles or for producing spare parts on demand.
- Buy-to-Fly Ratio Reduction: Aerospace manufacturers are constantly seeking ways to reduce material waste. AM significantly improves material utilization compared to machining large billets, lowering raw material costs and environmental impact.
As the technology matures, certifications become standardized (e.g., AS9100 for aerospace quality management), and material databases expand, the adoption of 3D printed aluminum beams is set to accelerate, becoming a standard manufacturing technique for a wider array of critical flight components. Finding a reliable aerospace component supplier with proven expertise in aluminum AM, like Met3dp, is crucial for leveraging these applications effectively.
Why Metal Additive Manufacturing for Aerospace Beams? The AM Advantage
Choosing the right manufacturing process is a critical decision impacting cost, performance, lead time, and design possibilities. For aerospace structural beams, traditionally produced via CNC machining, extrusion, or casting, metal additive manufacturing presents a compelling alternative with distinct advantages that align perfectly with the stringent demands of the industry. Comparing AM, specifically powder bed fusion techniques like LPBF using high-strength aluminum, against traditional methods highlights why AM is increasingly favored for these applications.
Key Advantages of AM for Aerospace Beams:
- Revolutionary Design Freedom & Complexity:
- Traditional: Machining is limited by tool access, requiring components to be designed with considerations for how cutting tools can reach surfaces. Extrusion produces constant cross-sections. Casting requires complex molds and has limitations on internal features and wall thickness.
- AM: Builds parts layer-by-layer, enabling almost limitless geometric complexity. This allows for:
- Topology Optimization: Algorithms determine the most efficient material layout to handle specific loads, resulting in organic, highly optimized shapes that are significantly lighter yet meet structural requirements. This is often impractical or impossible to machine.
- Gitterstrukturer: Internal lattice or cellular structures can be integrated within the beam’s volume, dramatically reducing weight while maintaining stiffness and providing potential for multi-functional properties (e.g., vibration damping, heat dissipation).
- Internal Channels: Cooling channels, conduits for wiring, or fluid passages can be designed directly into the beam structure, eliminating the need for separate components and assembly.
- Del Konsolidering: Multiple simple parts that would traditionally be joined (welded, bolted) can be redesigned and printed as a single, complex monolithic component.
- Significant Lightweighting Potential:
- Traditional: Weight reduction often involves pocketing or removing material where possible within the constraints of the manufacturing process, but large amounts of structurally “inactive” material often remain.
- AM: Directly enables lightweighting through topology optimization and lattice structures, placing material only where functionally required. Combined with high-strength, low-density aluminum alloys like Scalmalloy® and AlSi10Mg, weight savings of 30-60% or even more compared to traditionally designed and manufactured counterparts are achievable for structural beams. This is arguably the single most significant driver for AM adoption in aerospace.
- Reduced Material Waste (Improved Buy-to-Fly Ratio):
- Traditional: CNC machining, especially for complex aerospace parts, starts with a solid block (billet) of material, and a significant portion (often >80-90%) is machined away as chips, representing wasted material and cost. Casting has better material utilization but requires molds and has design limitations.
- AM: Uses powder material, fusing only what is needed for the part and its supports. While some support material is used and some powder requires recycling/refreshing, the overall material utilization is vastly superior to subtractive methods, drastically improving the buy-to-fly ratio and reducing raw material expenditure.
- Shortened Lead Times (Especially for Complex/Low Volume Parts):
- Traditional: Complex parts often require intricate multi-axis CNC programming, custom fixtures, and potentially multiple machine setups. Casting requires mold design and fabrication. These steps add significant time to the manufacturing process, especially for initial production runs or prototypes.
- AM: Moves directly from a digital CAD file to physical part production. While printing itself takes time, the elimination of tooling and complex setup often results in shorter overall lead times, particularly for highly complex geometries or small batch production common in aerospace. This accelerates development cycles and enables faster responses to design changes or demands for spare parts.
- Part Consolidation Benefits:
- Traditional: Complex assemblies require designing, manufacturing, procuring, inventorying, and assembling multiple individual components, including fasteners. Each joint represents a potential failure point and adds weight.
- AM: Allows the consolidation of these multi-part assemblies into a single printed component. This offers numerous advantages:
- Reduced part count simplifies supply chain management and logistics.
- Elimination of assembly labor and time reduces overall manufacturing cost.
- Removal of joints (welds, bolts, rivets) eliminates potential stress concentrations and failure modes, improving structural integrity.
- Further weight reduction by eliminating fasteners.
Comparison Table: AM vs. Traditional Methods for Aerospace Beams
Funktion | Metal Additive Manufacturing (LPBF – Aluminum) | Traditional Manufacturing (CNC Machining, Casting) | Advantage for AM Aerospace Beams |
---|---|---|---|
Designens komplexitet | Very High (Topology optimization, lattices) | Moderate to High (Limited by tooling/molds) | Enables radical lightweighting & functional integration. |
Lättvikt | Excellent (Optimized structures) | Good (Pocketing, material choice) | Significant weight savings (30-60%+) possible. |
Material Avfall | Low (Powder bed fusion, recycling) | High (Machining chips) / Moderate (Casting) | Improved buy-to-fly ratio, lower raw material cost. |
Konsolidering av delar | High Potential | Low Potential | Reduced part count, assembly time, weight, failure points. |
Lead Time (Complex) | Potentially Shorter (No tooling) | Longer (Tooling, setup) | Faster prototyping, agile manufacturing, quicker spares. |
Verktygskostnad | Minimal / None | High (Molds, jigs, fixtures) | Cost-effective for low-volume, high-complexity parts. |
Materialalternativ | Growing (Specialized AM alloys like Scalmalloy®) | Very Broad (Established alloys) | Optimized materials available, though range is still expanding. |
Surface Finish (As-Built) | Moderate to Rough | Good to Excellent (Machining) | Often requires post-processing for critical surfaces. |
Dimensionell noggrannhet | Good to Very Good | Very Good to Excellent | Requires process control; post-machining often needed for high tolerance. |
Export to Sheets
While traditional methods still hold advantages in high-volume production of simpler geometries or where extremely fine surface finishes are required without post-processing, the benefits offered by metal AM for complex, performance-critical components like aerospace beams are undeniable. The ability to fundamentally rethink design, drastically cut weight, and streamline production makes additive manufacturing, supported by expert providers like Met3dp offering advanced tryckmetoder and materials, a cornerstone technology for the future of aerospace manufacturing.
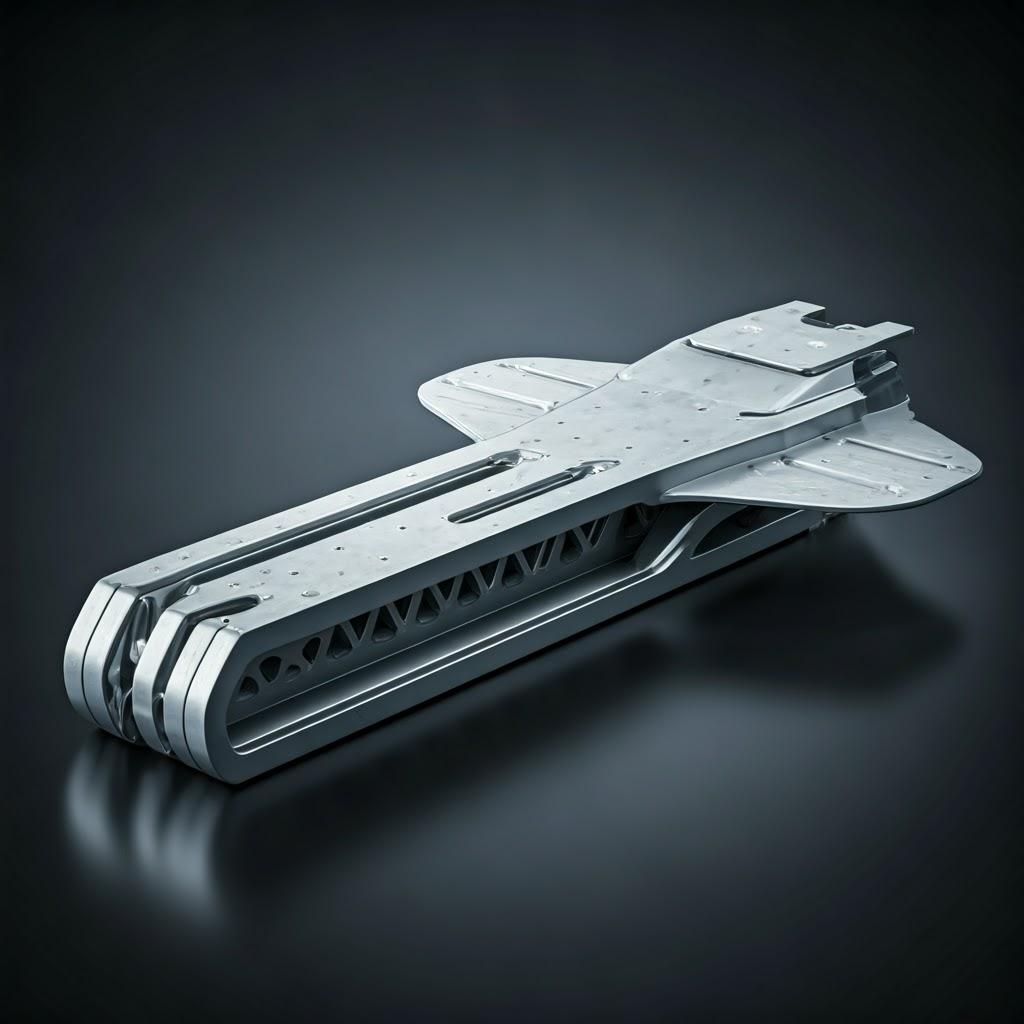
Material Focus: Scalmalloy® and AlSi10Mg for Demanding Aerospace Needs
The performance of a 3D printed aerospace beam is intrinsically linked to the material used. While various metals can be processed via additive manufacturing, high-strength aluminum alloys have emerged as leading candidates for structural aerospace applications due to their favorable combination of low density, high strength, good processability, and corrosion resistance. Among these, two alloys stand out: Scalmalloy® and AlSi10Mg. Understanding their properties and why they are chosen is crucial for engineers and procurement specialists.
Aluminum Alloys in Aerospace AM:
Aluminum alloys offer a significant density advantage over steels and titanium alloys, making them highly attractive for lightweighting initiatives. While traditional wrought aluminum alloys (like 7075 or 6061) are common in aerospace, they can be challenging to process reliably via AM powder bed fusion methods due to issues like hot cracking and achieving consistent properties. This led to the development and adoption of alloys better suited to the rapid melting and solidification inherent in AM.
AlSi10Mg:
AlSi10Mg is one of the most widely used aluminum alloys in metal additive manufacturing across various industries, including aerospace. It’s an aluminum-silicon-magnesium alloy, essentially a casting alloy composition adapted for AM powder production.
- Viktiga egenskaper:
- Good Processability: It generally exhibits good behavior during LPBF, with a relatively wide processing window, making it easier to achieve dense, low-defect parts.
- Good Strength & Hardness: Offers mechanical properties comparable to or exceeding those of traditional A360 cast aluminum after appropriate heat treatment.
- Svetsbarhet: The silicon content contributes to good weldability, which translates to better processability during the layer-wise fusion of AM.
- Motståndskraft mot korrosion: Exhibits good general corrosion resistance.
- Termiska egenskaper: Possesses good thermal conductivity.
- Availability & Cost: Being a widely adopted alloy, AlSi10Mg powder is generally more readily available and cost-effective compared to more specialized AM alloys.
- Aerospace Suitability: AlSi10Mg is suitable for moderately loaded structural components, brackets, housings, heat exchangers, and prototypes where a good balance of strength, weight, and manufacturability is needed. It’s often used when requirements are less extreme than those demanding materials like Scalmalloy® or titanium.
- Met3dp’s Role: Met3dp utilizes advanced powder production techniques like gas atomization to produce high-quality AlSi10Mg powder with controlled particle size distribution (PSD), high sphericity, and low oxygen content. These characteristics are critical for achieving consistent powder flowability in the printer and producing dense, reliable final parts with predictable mechanical properties – essential for meeting aerospace quality standards.
Scalmalloy®:
Scalmalloy® is a patented high-performance aluminum-magnesium-scandium alloy (Al-Mg-Sc-Zr family) developed specifically by APWorks (an Airbus subsidiary) for additive manufacturing. It represents a significant step up in performance compared to standard Al-Si alloys.
- Viktiga egenskaper:
- Exceptional Specific Strength: This is Scalmalloy®’s defining feature. It offers a strength-to-weight ratio significantly higher than AlSi10Mg and comparable or superior to many traditional high-strength wrought aluminum alloys (like 7000 series) and even some titanium grades, especially at room and slightly elevated temperatures. This allows for extreme lightweighting.
- High Ductility & Fatigue Strength: Unlike many high-strength aluminum alloys, Scalmalloy® maintains good ductility and exhibits excellent fatigue performance, crucial for components subjected to cyclic loading in aerospace.
- Microstructure Stability: The addition of Scandium and Zirconium creates fine precipitates that stabilize the microstructure, contributing to its high strength and resistance to grain coarsening during the AM process and heat treatment.
- God korrosionsbeständighet: Offers good resistance to corrosion.
- Processbarhet: While requiring more controlled processing parameters than AlSi10Mg, it is well-suited for LPBF processes.
- Aerospace Suitability: Scalmalloy® is the material of choice for highly loaded, performance-critical aerospace applications where maximum weight reduction is essential. This includes primary and secondary structural components, topologically optimized brackets, satellite structures, suspension parts, and components requiring high fatigue life. Its higher cost compared to AlSi10Mg is often justified by the significant performance gains and weight savings achievable.
- Met3dp’s Role: While Scalmalloy® powder supply is primarily linked to its developer, the ability to process this advanced material effectively requires sophisticated AM systems. Met3dp’s printers, designed for accuracy, reliability, and process control, provide the stable thermal environment and precise energy delivery needed to successfully print high-integrity parts from demanding alloys like Scalmalloy®. Ensuring optimal parameter sets and inert atmospheric conditions, as achievable with Met3dp systems, is key to unlocking the full potential of this high-performance material.
Comparison Table: AlSi10Mg vs. Scalmalloy® for Aerospace AM
Fastighet | AlSi10Mg | Scalmalloy® -legering | Key Consideration for Aerospace Beams |
---|---|---|---|
Primary Elements | Aluminium, kisel, magnesium | Aluminum, Magnesium, Scandium, Zirconium | Different alloying strategies lead to distinct properties. |
Typical Use Case | General purpose AM, moderate loads, housings | High-performance, highly loaded structures | Match material to application demands. |
Specifik styrka | Bra | Exceptionell | Scalmalloy® enables maximum lightweighting. |
Yield Strength (Typical, Heat Treated) | ~230-280 MPa | ~450-500+ MPa | Scalmalloy® offers significantly higher strength. |
Tensile Strength (Typical, Heat Treated) | ~350-450 MPa | ~500-550+ MPa | Scalmalloy® provides higher ultimate strength. |
Elongation (Ductility) | Moderate (~6-10%) | Good (~10-15%+) | Scalmalloy® generally offers better ductility at high strength. |
Utmattningshållfasthet | Fair to Good | Utmärkt | Critical for cyclically loaded parts; Scalmalloy® excels. |
Processability (LPBF) | Generally Easier | Requires Tighter Control | Process parameters must be optimized for each alloy. |
Motståndskraft mot korrosion | Bra | Bra | Both suitable for many aerospace environments. |
Relativ kostnad | Lägre | Högre | Performance benefits of Scalmalloy® must justify cost. |
Tillgänglighet | Mycket tillgänglig | More Specialized | Ensure supply chain availability for production needs. |
Export to Sheets
Why These Materials Matter for Procurement & Engineering:
- Performance Matching: Engineers must select the alloy that meets the specific structural, thermal, and fatigue requirements of the beam. Choosing AlSi10Mg for a highly critical, fatigue-sensitive part might be inadequate, while using Scalmalloy® where AlSi10Mg suffices could unnecessarily increase costs.
- Cost Implications: Procurement managers need to understand the cost difference. Scalmalloy®’s higher raw material cost and potentially more demanding processing translate to higher part prices. Justification relies on demonstrable performance gains (e.g., weight savings translating to fuel efficiency or payload capacity).
- Supplier Capability: Not all AM service providers have validated processes or the necessary equipment control to reliably print high-quality parts from both alloys, especially Scalmalloy®. Partnering with an experienced supplier like Met3dp, who understands the nuances of processing high-performance aluminum powders and offers a range of produkter and services, is essential.
- Certifiering: Aerospace components require rigorous certification. Data packages and process qualification are often specific to the material-process combination. Ensure the chosen supplier can meet the necessary certification requirements for the selected alloy.
In conclusion, both AlSi10Mg and Scalmalloy® are powerful tools in the aerospace engineer’s arsenal for creating 3D printed structural beams. AlSi10Mg provides a reliable, cost-effective solution for many applications, while Scalmalloy® pushes the boundaries of performance for the most demanding, weight-critical components. Leveraging the unique properties of these advanced aluminum alloys through additive manufacturing, supported by expert material and process knowledge from partners like Met3dp, is key to realizing the next generation of efficient and capable aerospace structures.
Design for Additive Manufacturing (DfAM): Optimizing Beams for 3D Printing Success
Simply taking a design intended for traditional manufacturing and sending it to a 3D printer rarely yields optimal results, especially in the demanding aerospace sector. To truly unlock the transformative potential of additive manufacturing for structural beams using Scalmalloy® or AlSi10Mg, engineers must embrace Design for Additive Manufacturing (DfAM). DfAM is not just a set of rules but a mindset shift, focusing on designing components specifically to leverage AM’s strengths and accommodate its unique process characteristics. Applying DfAM principles is crucial for maximizing lightweighting, ensuring printability, reducing post-processing efforts, and ultimately achieving superior performance and cost-effectiveness.
Core DfAM Principles for Aluminum Aerospace Beams:
- Topology Optimization:
- Concept: This is arguably the most powerful DfAM tool for structural components like beams. Using specialized software (e.g., Altair Inspire, nTopology, Autodesk Fusion 360 Generative Design), engineers define load cases, constraints (keep-out zones, mounting points), and performance targets (stiffness, stress limits). The software then iteratively removes material from a design space, leaving only the load-bearing pathways required.
- Benefit for Beams: Results in highly organic, skeletal structures that are significantly lighter (often 30-60%+) than traditionally designed beams while meeting or exceeding performance requirements. It naturally creates forms well-suited for AM production that would be difficult or impossible to machine.
- Överväganden: Requires accurate simulation inputs (loads, boundary conditions). The resulting geometry might need some smoothing or manual adjustment for manufacturability (e.g., ensuring self-supporting angles). Output often requires validation through FEA (Finite Element Analysis).
- Lattice Structure Integration:
- Concept: Replacing solid volumes within a beam’s structure with engineered lattice or cellular structures (e.g., gyroids, diamonds, octet-truss). These structures offer high stiffness and strength at very low densities.
- Benefit for Beams: Provides further lightweighting beyond topology optimization alone. Can be used to infill thicker sections identified by topology optimization or designed directly. Offers multi-functional potential: vibration damping, enhanced heat dissipation, impact absorption.
- Typer:
- Stochastic Foams: Random open or closed-cell structures. Good for energy absorption but less predictable structurally.
- Periodic Lattices: Ordered arrangements of unit cells (beams, surfaces). Offer predictable mechanical properties based on cell type, size, and strut thickness. Examples include BCC (Body-Centered Cubic), Octet, Diamond, Gyroid (surface-based). Gyroids are often favored for self-supporting properties and good all-around performance.
- Överväganden: Requires specialized software for generation. Need to ensure minimum strut/wall thickness is printable. Trapped powder removal from complex internal lattices can be challenging, potentially requiring design features for powder escape. Surface-based lattices (like gyroids) can be easier to de-powder.
- Overhangs and Support Structures:
- Concept: Powder bed fusion processes require support structures for features that overhang the build platform at angles below a certain threshold (typically <45 degrees from horizontal for aluminum alloys). Supports anchor the part, prevent warping due to thermal stress, and provide a base for overhanging features.
- DfAM Strategy: Minimize the need for supports where possible, as they consume extra material, add print time, require manual removal (which can be difficult with ductile aluminum), and can mar the part surface.
- Design Self-Supporting Angles: Orient features and surfaces to be above the critical overhang angle (e.g., >45 degrees).
- Use Chamfers/Fillets: Replace sharp horizontal overhangs with angled chamfers or rounded fillets that are inherently self-supporting.
- Optimize Part Orientation: Choose a build orientation that minimizes the total area requiring support, considering factors like critical surfaces, stress concentration, and ease of removal. This is a critical step in print preparation.
- Integrate Supports into Design: Sometimes, support-like features can be incorporated functionally into the part design itself.
- Considerations for Aluminum: Aluminum alloys often require more robust support strategies than, say, titanium, due to higher thermal conductivity and potential for warping. Support removal can be labor-intensive.
- Minimum Feature Sizes and Wall Thickness:
- Concept: AM processes have limitations on the smallest features (holes, pins, struts) and thinnest walls they can reliably produce. This depends on the machine resolution, laser/beam spot size, powder particle size, and material.
- DfAM Strategy: Adhere to recommended minimums provided by the AM service provider or machine manufacturer for the specific aluminum alloy being used. Typically, wall thicknesses below 0.4-0.8 mm can be challenging. Ensure lattice struts are sufficiently thick to print reliably and carry intended loads.
- Överväganden: Features smaller than the minimum may not resolve correctly or could be prone to defects. Thin walls are more susceptible to thermal distortion.
- Del Konsolidering:
- Concept: Redesigning assemblies consisting of multiple traditionally manufactured parts (often joined by fasteners or welding) into a single, monolithic AM component.
- Benefit for Beams: Reduces part count, eliminates assembly labor, removes failure points at joints, reduces weight (no fasteners), and simplifies the supply chain. Structural beams often interface with numerous brackets or mounting features – these can potentially be integrated directly into the beam design.
- Överväganden: Requires a holistic view of the assembly’s function. The consolidated part might become significantly more complex, requiring careful DfAM application regarding supports and internal features. Access for inspection or post-processing might need consideration.
- Hole Orientation and Shape:
- Concept: Holes printed vertically (along the build Z-axis) tend to be more accurate and round than holes printed horizontally (parallel to the build plate). Horizontally printed holes often require support structures on their upper surfaces, leading to poorer surface finish inside the hole.
- DfAM Strategy: Orient critical holes vertically whenever possible. If horizontal holes are unavoidable, consider designing them as teardrop or diamond shapes, which are self-supporting up to a certain diameter, eliminating the need for internal supports and improving internal finish.
- Designing for Post-Processing:
- Concept: Consider how the part will be handled and finished after printing.
- DfAM Strategy:
- Support Removal Access: Ensure support structures are accessible for tools or machining removal. Avoid placing supports on functionally critical or difficult-to-reach surfaces if possible.
- Machining Allowances: If surfaces require high precision or specific finishes achievable only through CNC machining, add sufficient sacrificial stock material (e.g., 0.5-2 mm) to those features in the design phase.
- Inspection Access: Design the part so critical internal or external features can be accessed for non-destructive testing (NDT) if required.
- Powder Removal: For parts with internal channels or lattices, incorporate strategically placed drainage holes or design features to facilitate the removal of unfused powder after printing.
By thoughtfully applying these DfAM principles, engineers can design aluminum aerospace beams that are not only manufacturable via AM but are also lighter, stronger, and more cost-effective than their traditional counterparts. Collaboration between design engineers and AM specialists, like the team at Met3dp – a company built on deep expertise in additive technologies (learn more om oss) – is often key to maximizing the benefits of DfAM for complex aerospace components.
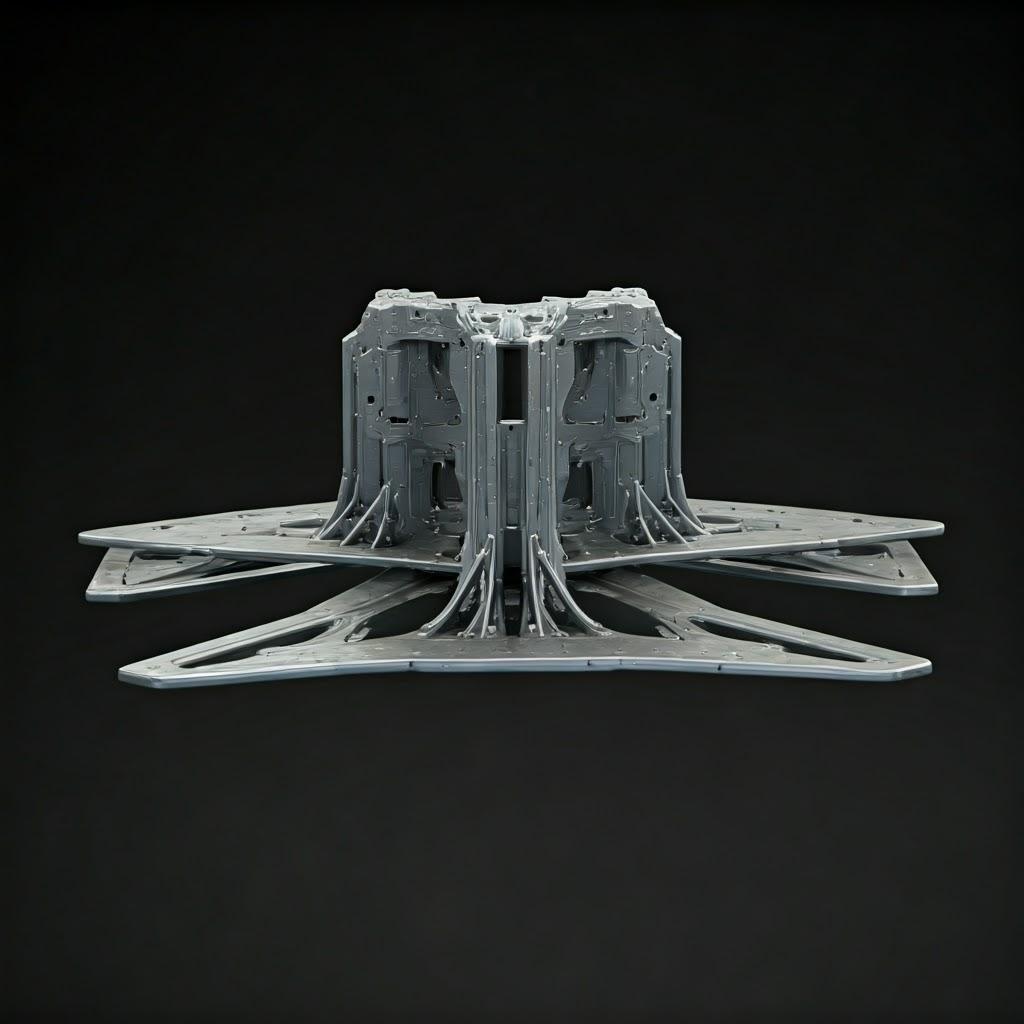
Achievable Precision: Tolerance, Surface Finish, and Dimensional Accuracy in Aluminum AM
While additive manufacturing unlocks incredible design freedom, aerospace applications demand high levels of precision. Structural beams must fit correctly within assemblies, interface accurately with mating parts, and meet stringent dimensional requirements. Understanding the achievable tolerance, surface finish, and overall dimensional accuracy of aluminum parts produced via Laser Powder Bed Fusion (LPBF) or similar AM processes is critical for both design engineers and procurement managers evaluating the technology.
Dimensionell noggrannhet:
Dimensional accuracy refers to how closely the final printed part conforms to the nominal dimensions specified in the CAD model. Several factors influence this in aluminum AM:
- Thermal Effects: The rapid heating and cooling cycles inherent in powder bed fusion induce thermal stresses within the part and the support structures. This can lead to warping, shrinkage, or distortion, especially in large or geometrically complex parts like beams, and particularly with thermally conductive materials like aluminum. Careful thermal management during the build (e.g., build plate heating), optimized scan strategies, and robust support structures are crucial for mitigation.
- Machine Calibration: The accuracy of the laser/electron beam positioning system, galvanometer calibration (in LPBF), layer thickness consistency, and overall machine health directly impact part accuracy. High-quality, well-maintained systems are essential.
- Materialegenskaper: The specific alloy (Scalmalloy® vs. AlSi10Mg), its powder characteristics, and its response to thermal cycling play a role.
- Part Size and Geometry: Larger parts and complex geometries with varying cross-sections are generally more prone to dimensional deviation than smaller, simpler parts.
- Efterbearbetning: Stress relief heat treatments can cause minor dimensional changes. Support removal and subsequent machining steps significantly influence the final accuracy of specific features.
Typical Tolerances:
As a general guideline, for as-built aluminum parts produced via LPBF on industrial-grade machines, typical achievable tolerances are often in the range of:
- ± 0.1 mm to ± 0.3 mm for smaller dimensions (e.g., up to 100 mm).
- ± 0.1% to ± 0.3% of the nominal dimension for larger features.
Important Considerations:
- These are general guidelines; tighter tolerances may be achievable with process optimization and for specific features, while larger deviations might occur on very large or complex parts without careful control.
- Critical dimensions often require post-machining. It is common practice in aerospace AM to print parts slightly oversized (with machining allowance) on critical interfaces, datums, or hole features and then CNC machine them to achieve tolerances tighter than ±0.05 mm or even better, matching conventional machining precision where needed.
- Tolerance expectations should be clearly communicated and agreed upon with the AM service provider early in the design and quoting process.
Surface Finish (Roughness):
Surface finish, typically quantified by the average roughness (Ra), is another key characteristic. The as-built surface finish of PBF parts is inherently rougher than machined surfaces due to the layer-wise nature of the process and the adherence of partially sintered powder particles.
- As-Built Surface Roughness:
- Top Surfaces: Generally the smoothest, often Ra 5-15 µm.
- Vertical Walls (Z-axis): Typically Ra 8-20 µm, influenced by layer thickness and beam parameters.
- Upward-Facing Sloping Surfaces: Finish degrades slightly as the angle decreases from 90 degrees.
- Downward-Facing (Overhang) Surfaces: Roughness increases significantly as the overhang angle decreases towards the critical limit (45 degrees), often Ra 15-30 µm or higher. Surfaces directly supported by structures will bear witness marks after removal.
- Factors Influencing Roughness:
- Layer Thickness: Thinner layers generally produce smoother surfaces but increase build time.
- Powder Particle Size: Finer powders can lead to smoother finishes but may pose challenges for flowability.
- Laser/Beam Parameters: Energy density, scan speed, and strategy affect melt pool dynamics and surface outcome.
- Part Orientation: Significantly impacts the finish of different surfaces based on their angle relative to the build plate.
- Post-Processing for Improved Finish: For applications requiring smoother surfaces (e.g., for fatigue performance, sealing, or aesthetics), various post-processing techniques are employed:
- Media Blasting (Bead Blasting, Sand Blasting): Provides a uniform matte finish, removing loose powder and slightly reducing Ra (e.g., down to Ra 5-10 µm).
- Tumbling/Vibratory Finishing: Uses abrasive media in a rotating or vibrating drum to smooth surfaces and edges, effective for batches of smaller parts.
- Maskinbearbetning: Offers the best control for achieving very smooth finishes (Ra < 1 µm) on specific surfaces.
- Polering: Manual or automated polishing can achieve mirror-like finishes where required.
- Anodizing/Coating: Can provide corrosion protection and alter surface appearance but typically follows initial smoothing steps.
Ensuring Precision in Aerospace:
Achieving the necessary precision for aerospace beams requires a combination of:
- High-Quality AM Systems: Utilizing industrial-grade printers with precise control over the build environment (inert atmosphere, thermal management) and beam delivery. Companies like Met3dp invest in developing printers known for accuracy and reliability, essential for demanding applications.
- Process Control & Optimization: Developing and locking down validated process parameters specific to the alloy (Scalmalloy® or AlSi10Mg) and machine being used. This includes optimizing scan strategies, layer thickness, energy input, and support strategies.
- Rigorös kvalitetskontroll: Implementing dimensional inspection (e.g., CMM – Coordinate Measuring Machines, 3D scanning) and surface finish measurements throughout the manufacturing process (as-built and post-processed).
- Strategic Post-Processing: Integrating post-processing steps like heat treatment and CNC machining intelligently into the workflow to achieve final tolerances and finishes on critical features.
- DfAM Implementation: Designing parts with tolerances and finishes in mind, minimizing reliance on supports on critical surfaces, and adding machining stock where necessary.
Engineers and procurement managers should work closely with their chosen AM supplier to understand their specific capabilities regarding tolerance and surface finish for aluminum alloys. Clear specifications, realistic expectations, and robust quality assurance plans are paramount for successfully implementing 3D printed aluminum beams in critical aerospace structures.
Post-Processing Pathways: Finishing High-Performance Aluminum Beams
Printing an aerospace structural beam using high-strength aluminum alloys like Scalmalloy® or AlSi10Mg is often only the midpoint of the manufacturing journey. Unlike some applications where as-built parts might suffice, aerospace components almost invariably require a series of post-processing steps to meet stringent performance, dimensional, and quality requirements. These steps are crucial for relieving internal stresses, removing support structures, achieving final tolerances and surface finishes, and verifying part integrity. Understanding this pathway is essential for planning production workflows, estimating true costs, and ensuring the final beam meets all specifications.
Typical Post-Processing Workflow for AM Aluminum Aerospace Beams:
While the exact sequence can vary based on the part geometry, alloy, and specific requirements, a common workflow includes:
- De-powdering / Powder Removal:
- Objective: Remove as much unfused powder as possible from the part and build platform immediately after the print finishes, typically within the machine’s build chamber or a dedicated powder handling station.
- Metoder: Vacuuming, gentle brushing, compressed air blowing (in controlled environments). For parts with complex internal channels or lattice structures, specialized equipment or manual effort might be needed to dislodge trapped powder. Designing for powder removal (escape holes) during the DfAM phase is critical.
- Importance: Recovers valuable unfused powder for recycling/reuse. Prevents powder sintering during subsequent heat treatment steps. Safety protocols are vital due to the reactivity of fine metal powders.
- Stress Relief Heat Treatment:
- Objective: Relieve internal stresses built up during the rapid heating and cooling cycles of the layer-wise printing process. These stresses can cause distortion during subsequent steps (like removal from the build plate) or impact the part’s mechanical performance and fatigue life.
- Method: Heating the part (often while still attached to the build plate) in a controlled atmosphere furnace (inert gas like Argon or Nitrogen, or vacuum) to a specific temperature below the alloy’s aging or solutionizing temperature, holding it for a defined period, and then cooling it slowly. Precise temperature control is critical.
- Importance: Absolutely essential for dimensional stability and preventing warping/cracking, especially for complex beams. Required before removing the part from the build plate. Specific cycles depend on the alloy (Scalmalloy® often requires different cycles than AlSi10Mg) and part geometry.
- Part Removal from Build Plate:
- Objective: Separate the printed beam(s) and their support structures from the metal build plate they were printed on.
- Metoder:
- Wire EDM (Electrical Discharge Machining): Precise method, commonly used for aerospace parts. Minimizes mechanical stress on the part.
- Bandsågning: Faster but less precise and induces more mechanical stress. Often suitable for less critical applications or initial rough separation.
- Maskinbearbetning: Milling the interface can also be used.
- Importance: Requires careful handling to avoid damaging the part. The chosen method depends on part complexity, material, and required precision.
- Borttagning av stödstruktur:
- Objective: Remove the temporary support structures required during the printing process.
- Metoder: Can be challenging, especially with ductile aluminum alloys where supports tend to bend rather than break cleanly.
- Manuell borttagning: Using pliers, cutters, grinders, or specialized hand tools. Labor-intensive and requires skilled technicians to avoid damaging the part surface.
- CNC Machining: Milling or grinding away support structures, often preferred for better surface finish and control, especially at the interface points.
- Wire EDM: Can sometimes be used for intricate support removal.
- Importance: Critical step impacting final geometry and surface finish. DfAM strategies to minimize supports and make them accessible are vital. Poor removal can leave witness marks or damage the part.
- Further Heat Treatment (Solutionizing, Aging – Alloy Dependent):
- Objective: Optimize the final mechanical properties (strength, hardness, ductility) of the aluminum alloy.
- Metoder:
- AlSi10Mg: Often undergoes a T6-like heat treatment involving solutionizing (heating to dissolve precipitates), quenching (rapid cooling), and artificial aging (holding at an elevated temperature) to achieve optimal strength and hardness.
- Scalmalloy®: Typically requires an aging treatment (precipitation hardening) after stress relief to develop its characteristic ultra-high strength while maintaining good ductility. Specific temperatures and times are proprietary or defined by aerospace specifications.
- Importance: Tailors the microstructure and mechanical performance to meet application requirements. Requires precise furnace control and adherence to specified cycles. Can cause minor dimensional changes (predictable and accounted for in design).
- Machining for Critical Tolerances and Features:
- Objective: Achieve final high-precision dimensions, tolerances (often tighter than ±0.1 mm), and surface finishes on critical interfaces, mounting holes, datum surfaces, or sealing faces.
- Metoder: CNC milling (3-axis, 5-axis), turning, grinding. Requires careful setup and potentially custom fixtures to hold the complex AM geometry accurately. Machining allowances must have been included in the DfAM phase.
- Importance: Often mandatory for aerospace components to ensure proper fit, assembly, and function. Bridges the gap between as-built AM accuracy and final drawing specifications.
- Ytbehandling:
- Objective: Improve surface roughness, remove support witness marks, enhance fatigue life, prepare for coating, or meet aesthetic requirements.
- Metoder: (As detailed previously) Media blasting (bead, sand), tumbling/vibratory finishing, chemical etching, electropolishing, manual polishing. The choice depends on the required finish level and part geometry.
- Importance: Improves component performance (fatigue), ensures proper sealing, or meets visual standards.
- Surface Treatment / Coating (Optional):
- Objective: Enhance corrosion resistance, wear resistance, or provide specific surface properties.
- Metoder: Anodizing (common for aluminum), chemical conversion coatings (e.g., Alodine), painting, powder coating.
- Importance: Provides protection against the operating environment, extending component life. Requires compatibility with the specific aluminum alloy.
- Cleaning and Inspection:
- Objective: Ensure the part is clean and meets all dimensional, surface, and internal quality specifications.
- Metoder: Final cleaning processes. Dimensional inspection using CMM or 3D scanning. Surface finish measurement. Non-Destructive Testing (NDT) is critical for aerospace:
- Visual Inspection (VT): Basic check for surface defects.
- Dye Penetrant Inspection (PT): Detects surface-breaking cracks.
- Radiographic Testing (RT) / Computed Tomography (CT) Scanning: Detects internal defects like porosity, inclusions, or cracks. CT scanning provides a full 3D view of internal quality, increasingly vital for critical AM aerospace parts.
- Ultrasonic Testing (UT): Can detect internal flaws.
- Importance: Final quality gate before the part is certified for use. Ensures structural integrity and conformance to drawing.
Planning Considerations:
- Integrated Approach: Post-processing should not be an afterthought but an integrated part of the manufacturing plan, considered during DfAM.
- Supplier Capability: Ensure the chosen AM service provider has the necessary in-house capabilities or established partnerships for all required post-processing steps, especially heat treatment, precision machining, and NDT relevant to aerospace standards. A full-service provider simplifies logistics and quality management.
- Cost and Lead Time: Post-processing adds significantly to the total cost and lead time of an AM aerospace part. These factors must be included in project budgeting and scheduling.
Successfully navigating the post-processing pathway is essential for delivering flight-ready 3D printed aluminum beams that meet the extreme demands of the aerospace industry.
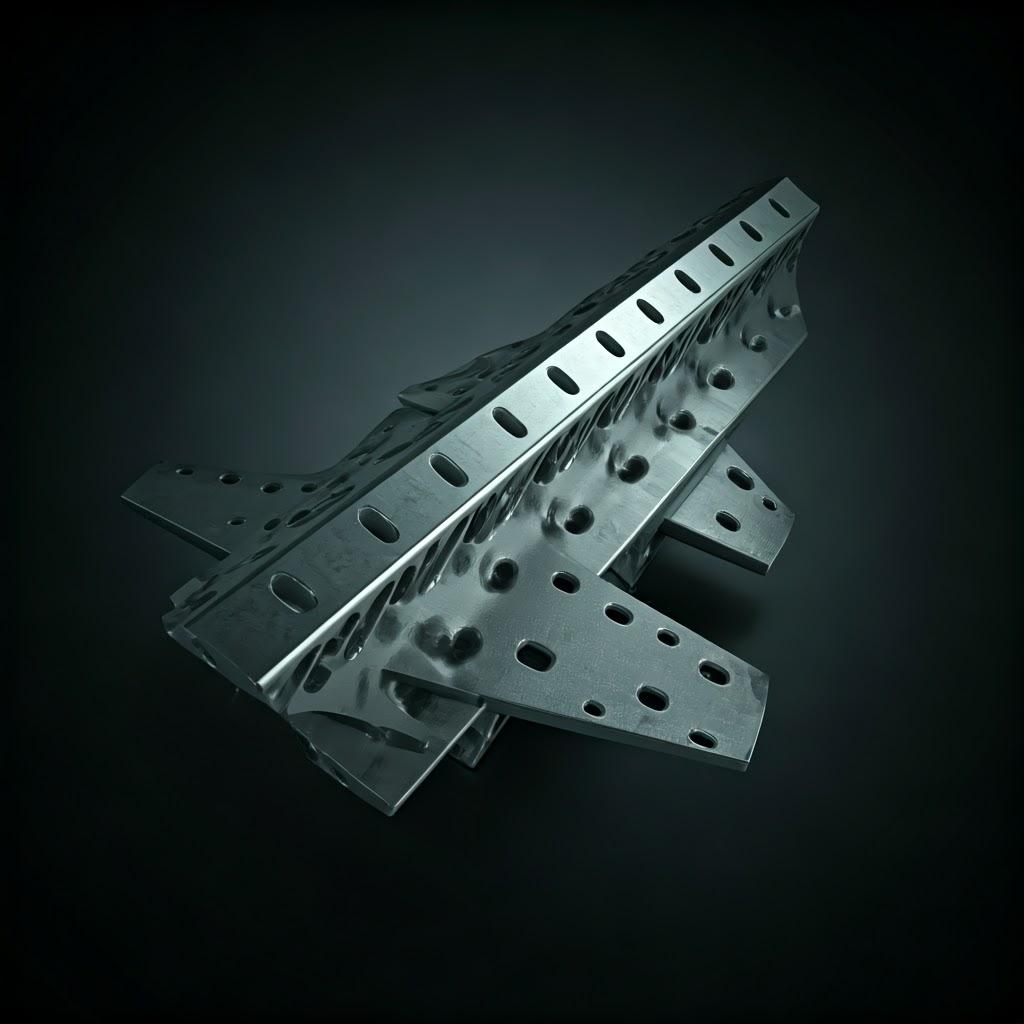
Navigating Challenges: Overcoming Hurdles in Aluminum Beam 3D Printing
While metal additive manufacturing offers significant advantages for producing high-strength aluminum aerospace beams, the technology is not without its challenges. Printing with aluminum alloys like AlSi10Mg and Scalmalloy® using powder bed fusion presents specific hurdles related to material properties, the physics of the process, and quality control. Recognizing these potential issues and implementing effective mitigation strategies is crucial for successful and reliable production. Partnering with experienced AM providers who understand these challenges is key.
Common Challenges and Mitigation Strategies:
- Residual Stress and Warping:
- Utmaning: Aluminum’s high thermal conductivity and coefficient of thermal expansion lead to significant temperature gradients during the rapid melting and solidification of PBF. This creates internal stresses within the printed part. If these stresses exceed the material’s yield strength at elevated temperatures, it can cause warping (distortion) of the part, potentially pulling it away from supports or causing build failures. Large, flat sections or asymmetric geometries are particularly susceptible.
- Mitigation Strategies:
- Build Plate Heating: Pre-heating the build plate (e.g., up to 200°C for aluminum) reduces the temperature gradient between the solidified material and the surrounding powder/plate, lowering stress accumulation.
- Optimized Scan Strategies: Using specific laser/beam scanning patterns (e.g., island scanning, sectoring, alternating directions) helps distribute heat more evenly and manage stress buildup.
- Robust Support Structures: Well-designed supports anchor the part securely to the build plate, resisting warping forces during the build. DfAM plays a role in designing supports that are strong yet removable.
- Stress Relief Heat Treatment: Performing a stress relief cycle immediately after printing and before part removal is essential to relax internal stresses and ensure dimensional stability.
- Geometric Design: DfAM considerations, like avoiding large, unsupported flat areas and incorporating gradual transitions, can help minimize stress concentration.
- Support Structure Design and Removal:
- Utmaning: Aluminum alloys, being relatively ductile compared to titanium or tool steels, make support removal more difficult. Supports tend to bend or smear rather than snapping off cleanly. Accessing supports in complex internal geometries or on delicate features can be problematic. Poor removal can damage the part surface or leave undesirable witness marks.
- Mitigation Strategies:
- DfAM for Support Minimization: Prioritize self-supporting angles (>45°), use chamfers/fillets, and optimize part orientation to reduce the need for supports.
- Optimized Support Design: Utilize support structure software to generate supports that are strong enough to prevent warping but designed for easier removal (e.g., lower density supports, specific interface points, perforation). Tree supports or block supports might be chosen based on geometry.
- Material Choice for Supports (Less Common): In some research, dissimilar materials are explored, but typically supports are the same material as the part.
- Post-Processing Methods: Relying on CNC machining or wire EDM for precise support removal in critical areas, rather than solely manual methods.
- Skilled Technicians: Employing experienced technicians for manual removal steps.
- Porositetskontroll:
- Utmaning: Porosity (small voids or holes within the printed material) is a critical defect that can significantly degrade mechanical properties, particularly fatigue strength, which is vital for aerospace components. Porosity in AM aluminum can arise from two main sources:
- Gas Porosity: Trapped gas (often hydrogen, which aluminum readily absorbs when molten) within the melt pool solidifies into pores. Sources include dissolved gas in the powder or moisture contamination.
- Lack-of-Fusion Porosity: Insufficient energy input or improper melt pool overlap fails to completely fuse adjacent tracks or layers, leaving void-like defects.
- Mitigation Strategies:
- High-Quality Powder: Using powder with low dissolved gas content, low oxygen levels, and controlled sphericity/particle size distribution is paramount. Met3dp’s focus on advanced powder production methods like gas atomization and PREP, ensuring high purity and optimal morphology, directly addresses this. (Visit Met3dp Homepage to learn more).
- Hantering och förvaring av pulver: Storing powder in dry, inert conditions and handling it carefully to prevent moisture absorption and contamination. Implementing powder lifecycle management (testing, sieving, refreshing).
- Optimized Process Parameters: Developing and precisely controlling laser/beam power, scan speed, hatch spacing, and layer thickness to ensure complete melting and fusion and minimize gas entrapment. This often involves extensive parameter development (DoE – Design of Experiments).
- Inert Atmosphere Control: Maintaining a high-purity inert gas environment (Argon) within the build chamber to minimize oxygen pickup and contamination during printing.
- Het isostatisk pressning (HIP): A post-processing step involving high temperature and high pressure inert gas to close internal porosity. While effective, it adds cost and lead time and is typically reserved for the most critical applications.
- NDT Inspection: Using CT scanning or radiography to detect and quantify internal porosity, ensuring it remains below acceptable limits defined by aerospace standards.
- Utmaning: Porosity (small voids or holes within the printed material) is a critical defect that can significantly degrade mechanical properties, particularly fatigue strength, which is vital for aerospace components. Porosity in AM aluminum can arise from two main sources:
- Cracking (Hot Tearing):
- Utmaning: Some aluminum alloys are susceptible to hot tearing or solidification cracking during the rapid cooling phase in AM. This occurs when tensile stresses build up across partially solidified grain boundaries. While AlSi10Mg is generally less susceptible than alloys like 6061 or 7075, and Scalmalloy® is designed for AM robustness, improper processing or contamination can still increase risk.
- Mitigation Strategies:
- Alloy Selection: Choosing alloys designed for AM (like Scalmalloy® and AlSi10Mg) that have compositions less prone to cracking.
- Parameter Optimization: Controlling heat input and cooling rates through optimized scan strategies and parameters.
- Termisk hantering: Build plate heating helps reduce thermal gradients.
- Pulverkvalitet: Ensuring high purity powder free from contaminants that could initiate cracks.
- NDT Inspection: Detecting cracks using methods like dye penetrant testing (surface) or CT scanning (internal).
- Powder Handling and Safety:
- Utmaning: Fine aluminum powder is reactive and potentially flammable or explosive when dispersed in air as a dust cloud, especially in the presence of an ignition source. It also poses respiratory hazards.
- Mitigation Strategies:
- Inert Environments: Performing powder handling (loading, unloading, sieving, recovery) in controlled inert gas environments where possible.
- Grounding and Bonding: Ensuring all equipment is properly grounded to prevent static discharge.
- Appropriate PPE: Using respirators, conductive clothing, safety glasses, and gloves.
- ATEX/NFPA Compliance: Utilizing equipment designed for handling combustible metal powders (e.g., certified vacuum cleaners).
- Utbildning: Ensuring personnel are properly trained on safe powder handling procedures.
Overcoming these challenges requires a deep understanding of material science, AM process physics, rigorous process control, and diligent quality assurance. Aerospace manufacturers and their procurement teams should prioritize partnering with AM service providers who demonstrate expertise in processing high-strength aluminum alloys, possess robust quality management systems (like AS9100 certification), and have proven strategies for mitigating these common hurdles.
Supplier Selection: Choosing the Right Metal AM Partner for Aerospace Components
The success of implementing 3D printed aluminum beams in critical aerospace applications hinges significantly on the capabilities and reliability of the chosen additive manufacturing service provider. Manufacturing flight-critical hardware demands more than just access to a 3D printer; it requires stringent process control, deep materials expertise, comprehensive quality management, and a proven track record. For engineers and procurement managers navigating the AM landscape, selecting the right partner is a crucial step involving careful evaluation against specific criteria tailored to aerospace requirements.
Key Criteria for Evaluating Aerospace AM Suppliers:
- Certifications and Quality Management System (QMS):
- AS9100 Certification: This is the internationally recognized QMS standard for the aviation, space, and defense industries. AS9100 incorporates ISO 9001 requirements and adds specific controls for safety, airworthiness, product conformity, configuration management, and risk management critical to aerospace. Having AS9100 certification is often considered mandatory for suppliers producing flight hardware. It demonstrates a commitment to rigorous quality processes.
- ISO 9001 Certification: A foundational QMS standard, good but generally insufficient on its own for critical aerospace parts.
- Nadcap Accreditation: While AS9100 covers the overall system, Nadcap (National Aerospace and Defense Contractors Accreditation Program) provides specific accreditation for special processes like heat treatment, non-destructive testing (NDT), welding, and increasingly, additive manufacturing itself. Nadcap accreditation for relevant processes adds another layer of assurance.
- Robust QMS Documentation: The supplier should have well-documented procedures for process control, material handling, traceability, operator training, equipment calibration, non-conformance management, and continuous improvement.
- Demonstrated Experience and Expertise:
- Materialkompetens: Proven experience printing the specific aluminum alloys required (Scalmalloy®, AlSi10Mg). This includes having validated, optimized process parameters, understanding material behavior, and managing powder lifecycle effectively. Ask for case studies or examples of similar parts produced in these materials.
- Aerospace Application Experience: Familiarity with aerospace requirements, specifications (e.g., understanding component criticality, documentation needs, typical tolerances, and surface finishes). Experience producing structural components is highly valuable.
- Engineering Support (DfAM): Does the supplier offer DfAM support? Can their engineers collaborate with your team to optimize the beam design for AM, minimize supports, ensure printability, and reduce costs? This collaborative capability can be invaluable.
- Problem-Solving Track Record: Ability to troubleshoot and resolve challenges inherent in aluminum AM (warping, porosity, support removal).
- Equipment and Facility Capabilities:
- Industrial-Grade AM Systems: Utilization of high-quality, well-maintained industrial PBF machines (LPBF or potentially SEBM where applicable) known for reliability and repeatability. Inquire about machine manufacturers, models, build volume sizes, and maintenance schedules. Advanced systems like those developed by Met3dp, focusing on accuracy and process stability, are indicative of a capable supplier. Explore the different tryckmetoder they master.
- Atmosphere Control: Consistent, high-purity inert gas environment (Argon for aluminum) with low oxygen levels (<100-500 ppm) is critical for preventing contamination and ensuring material integrity. Ask about their monitoring and control systems.
- Termisk hantering: Capabilities like build plate heating, crucial for managing residual stress in aluminum parts.
- Pulverhantering: Dedicated, controlled systems for powder storage, handling, sieving, and recycling to maintain powder quality and ensure operator safety. Cross-contamination controls if multiple materials are processed.
- Facility Security: Appropriate security measures if dealing with sensitive or ITAR-controlled aerospace designs.
- Process Control and Monitoring:
- Parameter Control: Strict control and documentation of all critical process parameters (laser power, scan speed, layer thickness, hatch spacing, atmosphere, temperature).
- In-Process Monitoring (Optional but Advantaged): Some advanced systems incorporate melt pool monitoring or thermal imaging to provide real-time insights into build quality, potentially detecting defects layer by layer.
- Build Documentation: Comprehensive records for each build, including machine logs, parameter settings, powder batch information, and operator logs, ensuring full traceability.
- Post-Processing Capabilities:
- In-House vs. Outsourced: Does the supplier perform critical post-processing steps like stress relief, heat treatment (to aerospace specifications in certified furnaces), support removal, and precision CNC machining in-house, or do they rely on qualified subcontractors? In-house capabilities often streamline the workflow, improve quality control, and shorten lead times.
- Range of Services: Ability to provide the full suite of required finishing steps (media blasting, polishing, surface treatments).
- Expertis: Skilled technicians for challenging tasks like manual support removal and complex machining setups for AM parts.
- Inspection and Non-Destructive Testing (NDT):
- Metrology Equipment: Calibrated CMMs, 3D scanners, or other metrology tools for dimensional verification.
- NDT Capabilities: Access to certified NDT methods essential for aerospace part validation, particularly CT scanning for internal defect detection in critical AM parts. Also, PT, RT, UT as required by specifications. Ensure NDT personnel are appropriately certified (e.g., NAS 410 / EN 4179).
- Reporting: Ability to provide detailed inspection reports and Certificates of Conformance (CoC).
- Supply Chain and Communication:
- Capacity and Lead Times: Realistic assessment of their production capacity and ability to meet required lead times.
- Communication: Clear, responsive communication channels. Designated points of contact. Proactive updates on project status.
- Supply Chain Stability: Stable financial standing and reliable sourcing for high-quality powders and other materials.
Supplier Audit:
For critical aerospace components, conducting a supplier audit (either remotely or on-site) is highly recommended. This allows verification of their QMS, facilities, equipment, processes, and overall capabilities beyond just paperwork.
Choosing a supplier is establishing a partnership. Look for transparency, technical competence, a commitment to quality, and a collaborative approach. Companies like Met3dp, which emphasize both cutting-edge powder technology and advanced printing systems, represent the type of integrated expertise beneficial for demanding aerospace projects.
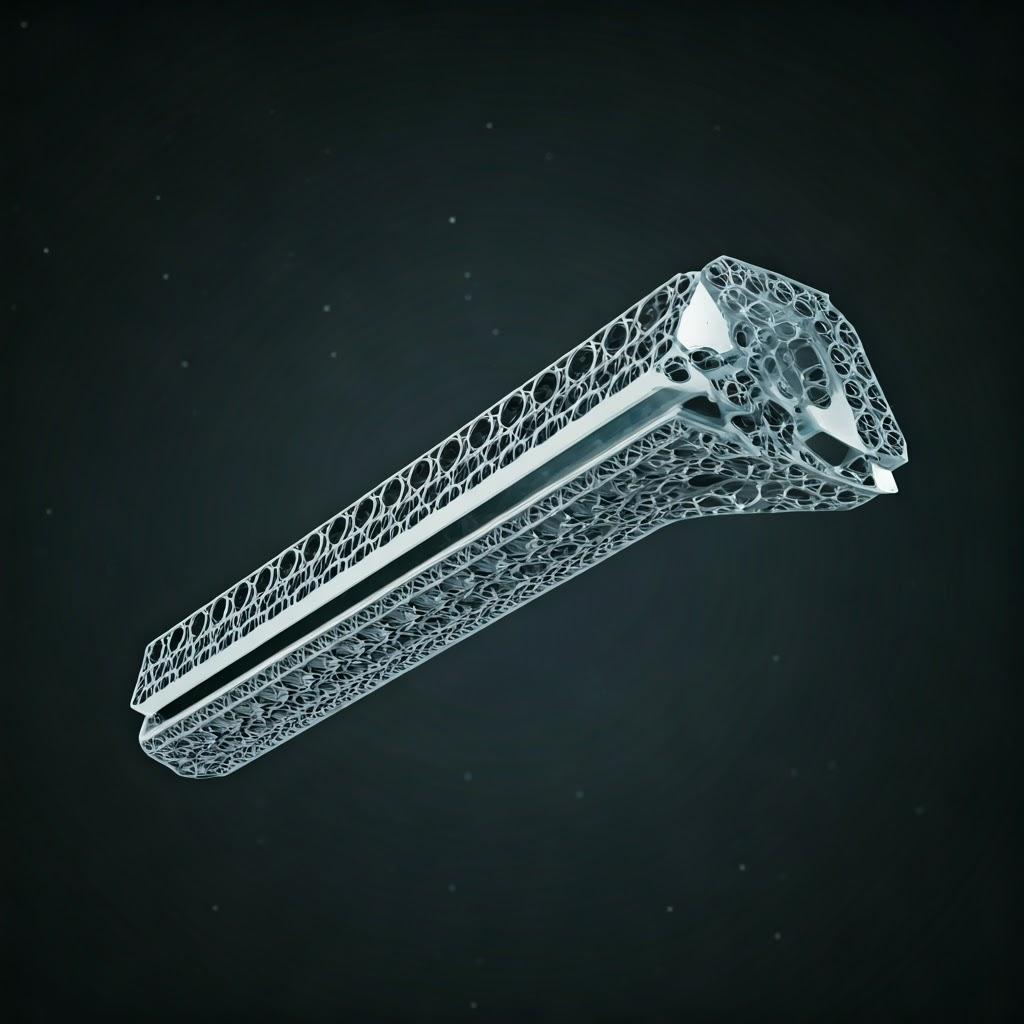
Understanding Investment: Cost Factors and Lead Times for 3D Printed Beams
While the performance benefits of 3D printed aluminum aerospace beams are compelling, understanding the associated costs and production timelines is crucial for project justification and planning. Both cost and lead time are influenced by a complex interplay of factors related to the design, material, manufacturing process, and required post-processing. Procurement managers and engineers need visibility into these drivers to make informed decisions and manage budgets effectively.
Key Cost Drivers for AM Aluminum Beams:
- Material Cost:
- Alloy Type: High-performance alloys like Scalmalloy® have a significantly higher raw powder cost per kilogram compared to more standard AM alloys like AlSi10Mg due to specialized alloying elements (Scandium) and development costs.
- Powder Usage: The total volume/mass of the final part directly impacts material consumption. While AM improves the buy-to-fly ratio, the powder itself is a primary cost component. Recycled powder usage can mitigate costs but requires careful quality control.
- Part Design and Geometry:
- Part Volume/Bounding Box: Larger parts occupy more space on the build plate and generally require more material and longer print times.
- Geometric Complexity: Highly intricate designs, thin walls, or complex internal features can increase print time and potentially require more complex support structures or post-processing. However, complexity achievable through AM might offset costs by eliminating assembly steps (part consolidation).
- Build Height (Z-Height): This is often a major driver of print time. Taller parts require more layers, directly increasing the duration the machine is occupied. Optimizing part orientation to minimize Z-height can reduce cost.
- Tryckningsprocess:
- Maskintid: The total time the AM machine is occupied printing the part(s). This is influenced by build height, part volume, layer thickness (thinner layers = longer time), and scan strategy efficiency. Machine amortization, operating costs (power, inert gas), and maintenance contribute to the hourly rate.
- Build Plate Density: Printing multiple parts simultaneously on a single build plate (nesting) can significantly reduce the per-part cost by distributing the machine setup and operational overheads.
- Stödstrukturer: The volume of material used for supports adds to material cost and print time. More importantly, complex or extensive supports significantly increase the labor required for removal, adding substantial cost.
- Krav på efterbearbetning:
- Labor Intensity: Post-processing steps like manual support removal, hand finishing, and complex machining setups are labor-intensive and can be a major cost component, especially for aluminum parts where support removal is challenging.
- Värmebehandling: Costs associated with furnace time, energy consumption, and controlled atmospheres for stress relief and final aging/solution treatments. Certification of furnaces adds overhead.
- CNC Machining: The extent of machining required for tight tolerances or specific surface finishes adds cost based on machine time, programming, setup, and tooling. 5-axis machining is more expensive than 3-axis.
- Ytbehandling: Costs vary depending on the method (blasting, tumbling, polishing) and the required level of finish.
- NDT and Inspection: Costs associated with performing and documenting required inspections (CMM, CT scanning, PT, etc.). CT scanning, while providing invaluable internal quality data, is a relatively expensive inspection method.
- Quality Assurance and Certification:
- The overhead associated with maintaining aerospace certifications (AS9100), performing rigorous process validation, documentation, and traceability adds to the overall cost structure for compliant suppliers.
- Order Volume:
- Stordriftsfördelar: Per-part costs generally decrease with higher volumes due to setup cost amortization, optimized build plate nesting, and potentially dedicated process optimization. However, AM is typically most cost-effective for low-to-medium volume production compared to traditional methods like casting which have high tooling costs but low per-part costs at high volumes.
Cost Comparison Snapshot (Illustrative):
Kostnadsfaktor | Impact on AlSi10Mg Beam Cost | Impact on Scalmalloy® Beam Cost | Anteckningar |
---|---|---|---|
Material Powder | Måttlig | Hög | Scalmalloy® powder is significantly more expensive. |
Print Time | Bas | Base (Similar density/process) | Driven primarily by geometry/size, less by alloy type. |
Borttagning av stöd | Måttlig-Hög | Måttlig-Hög | Labor-intensive for both ductile aluminum alloys. |
Värmebehandling | Standard T6 Cycle | Specific Aging Cycle | Costs may differ slightly based on cycle complexity/duration. |
Maskinbearbetning | As Required | As Required | Driven by tolerance/finish needs, not alloy type. |
NDT (e.g., CT Scan) | Hög | Hög | Driven by criticality, typically similar cost regardless of alloy. |
Overall Estimate | Lägre | Högre | Scalmalloy® parts are generally more expensive due to powder cost. |
Export to Sheets
Lead Time Components:
Lead time refers to the total time from order placement to part delivery. For AM aerospace beams, this typically includes:
- Quoting and Order Confirmation: Review of design, DfAM checks, quotation generation, order processing (Can range from days to weeks depending on complexity).
- Scheduling: Placing the job into the machine schedule based on availability (Can vary significantly based on supplier workload).
- Print Preparation: Finalizing build layout (nesting), generating support structures, slicing the model, machine setup (Typically 1-2 days).
- Tryckning: Actual build time on the AM machine (Can range from 1 day to over a week depending on part size, height, and quantity).
- Cool Down: Allowing the build chamber and parts to cool sufficiently before removal (Several hours).
- Efterbearbetning:
- De-powdering & Stress Relief: ~1 day (including furnace cycle).
- Part Removal & Support Removal: Highly variable, from hours to several days depending on complexity and method (manual vs. machine).
- Heat Treatment (Aging/Solution): ~1-2 days (including furnace cycles).
- CNC Machining: Variable, from hours to days depending on extent.
- Surface Finishing: Variable, from hours to days.
- Inspection and Quality Control: Dimensional inspection, NDT, documentation review (Can take several days, especially if extensive NDT like CT scanning is required).
- Frakt: Transit time to the customer.
Typical Overall Lead Times: For complex, post-processed, and inspected aerospace beams, lead times can range from 3 to 8 weeks or more, depending heavily on the factors above, supplier capacity, and the extent of post-processing and inspection required. Expedited services may be available at a premium cost.
Understanding these cost and lead time drivers allows for better budgeting, realistic project timelines, and more effective discussions with potential AM suppliers when procuring 3D printed aluminum aerospace beams.
Frequently Asked Questions (FAQ) about 3D Printed Aluminum Aerospace Beams
Here are answers to some common questions regarding the use of additive manufacturing for high-strength aluminum aerospace beams:
- Is 3D printed Scalmalloy® actually stronger than traditional high-strength wrought aluminum alloys like 7075?
- In many key aspects, yes. When properly printed and heat-treated, Scalmalloy® exhibits a specific strength (strength-to-weight ratio) that meets or exceeds typical values for high-strength wrought aluminum alloys like 7075-T6. Its yield strength and tensile strength are comparable or higher, and critically, it often demonstrates superior fatigue performance and better ductility at these high strength levels compared to some traditional alloys known for stress corrosion cracking susceptibility. However, properties can be anisotropic (directionally dependent) in AM parts, which must be considered in design and qualification. Always refer to validated material data sheets from the supplier for specific, guaranteed minimum properties based on print orientation and heat treatment.
- What are the essential certifications a supplier needs to produce flight-critical 3D printed aluminum beams?
- The most crucial certification is AS9100. This signifies the supplier adheres to the stringent quality management system requirements specific to the aerospace industry. Additionally, Nadcap accreditation for special processes involved (like heat treatment, NDT, and potentially the AM process itself) provides further assurance of process control and compliance for those specific operations. Individual part qualification processes, often defined by the aerospace prime contractor or regulatory bodies (like FAA, EASA), will also involve rigorous testing and documentation specific to the part, material, and process, going beyond just supplier-level certifications.
- How does the cost of producing an aluminum beam via AM compare to traditional CNC machining?
- It depends heavily on complexity and volume.
- For highly complex geometries (e.g., topology-optimized, lattice-filled beams) or parts requiring significant part consolidation, AM can be more cost-effective, even at low volumes, because it avoids extreme machining times, complex fixtures, and assembly labor. The high buy-to-fly ratio waste in machining complex parts from large billets also favors AM.
- For relatively simple beam geometries that can be easily machined from standard stock with minimal waste, CNC machining is typically much cheaper, especially at higher volumes.
- Tooling costs for traditional methods (like casting molds or complex machining fixtures) are eliminated with AM, making it advantageous for prototypes and low-volume production runs.
- Efterbearbetning costs for AM (support removal, heat treatment, potential machining) must be factored in, which can sometimes negate the printing cost advantages if extensive finishing is needed. A detailed cost analysis comparing AM (including post-processing) with the traditional method is necessary for each specific case.
- What Non-Destructive Testing (NDT) methods are typically used to ensure the quality of AM aluminum aerospace beams?
- Given the criticality, a combination of NDT methods is often employed:
- Computed Tomography (CT) Scanning: Increasingly vital for AM aerospace parts. It provides a full 3D X-ray view, allowing detection and characterization of internal defects like porosity, inclusions, and lack-of-fusion below the detection limits of conventional radiography.
- Dye Penetrant Testing (PT): Used to detect surface-breaking cracks or porosity.
- Radiographic Testing (RT): Traditional X-ray can detect larger internal flaws but may struggle with fine porosity or complex geometries compared to CT.
- Ultrasonic Testing (UT): Can detect subsurface flaws but may be challenging on complex AM geometries and rough surfaces.
- Visual Testing (VT): Basic inspection for surface defects, support removal quality, and overall conformity. The specific NDT requirements are usually dictated by the part’s criticality classification and relevant aerospace standards or customer specifications.
- Given the criticality, a combination of NDT methods is often employed:
- Can internal channels or lattice structures designed into AM beams be reliably cleaned of residual powder?
- This is a significant consideration in DfAM. Complete powder removal from intricate internal passages or dense lattices can be challenging. Strategies include:
- Designing for Removal: Incorporating sufficient escape holes or access points in the design phase.
- Optimizing Lattice Type: Using lattice types (like some surface-based lattices) that are easier to de-powder than complex strut-based lattices. Avoiding very fine, dense lattices if internal cleanliness is paramount.
- Tekniker för efterbearbetning: Utilizing vibration, controlled airflow, or specialized flushing techniques.
- Verification: Using methods like weighing the part or endoscopic inspection (borescope) to verify powder removal. In some cases, CT scanning can also help visualize trapped powder. If 100% powder removal cannot be guaranteed and is critical for the function (e.g., fluid channels), the design may need adjustment, or alternative manufacturing approaches considered for those specific features.
- This is a significant consideration in DfAM. Complete powder removal from intricate internal passages or dense lattices can be challenging. Strategies include:
Conclusion: The Future is Lightweight – Embracing Additive Manufacturing for Aerospace Structures
The journey through the intricacies of 3D printing high-strength aluminum aerospace beams reveals a technology that has firmly moved beyond rapid prototyping into the realm of mission-critical component manufacturing. The ability to leverage advanced alloys like the workhorse AlSi10Mg and the exceptional performer Scalmalloy® through additive manufacturing processes like Laser Powder Bed Fusion opens unprecedented opportunities for the aerospace industry.
The core advantages are undeniable: significant lättviktande through topology optimization and lattice structures translates directly into improved fuel efficiency, increased payload capacity, and enhanced vehicle performance. The designfrihet afforded by AM enables the creation of complex, functionally integrated components and the consolidation of multi-part assemblies, simplifying supply chains and reducing weight and potential failure points. When coupled with potentially kortare ledtider for complex or low-volume parts, AM presents a compelling value proposition.
However, realizing these benefits demands a sophisticated approach. Success requires embracing Design för additiv tillverkning (DfAM) principles from the outset, carefully considering material characteristics, optimizing for printability, and planning for necessary efterbearbetning steps like heat treatment, support removal, precision machining, and rigorous inspection. Navigating challenges such as residual stress, porosity control, and support removal necessitates deep process understanding and robust quality control measures.
Critically, the choice of an AM manufacturing partner is paramount. Suppliers must possess not only advanced equipment but also AS9100 certification, proven expertise with high-strength aluminum alloys, comprehensive quality management systems, and the full suite of post-processing and NDT capabilities required to deliver flight-ready components.
As the aerospace industry continues its relentless pursuit of higher performance, greater efficiency, and more sustainable operations, metal additive manufacturing stands out as a key enabling technology. 3D printed aluminum beams are not just components; they represent a paradigm shift towards optimized, lightweight, and complex structures that were previously unattainable. Companies like Met3dp, dedicated to advancing both metal powder technology and industrial AM systems, are integral to this transformation, providing the materials, equipment, and expertise needed to turn ambitious designs into flight-worthy reality. By offering a comprehensive range of produkter and solutions, Met3dp empowers aerospace innovators to fully harness the power of additive manufacturing and build the future of flight, one optimized layer at a time.
Dela på
MET3DP Technology Co, LTD är en ledande leverantör av lösningar för additiv tillverkning med huvudkontor i Qingdao, Kina. Vårt företag är specialiserat på 3D-utskriftsutrustning och högpresterande metallpulver för industriella tillämpningar.
Förfrågan för att få bästa pris och anpassad lösning för ditt företag!
Relaterade artiklar
Om Met3DP
Senaste uppdateringen
Vår produkt
KONTAKTA OSS
Har du några frågor? Skicka oss meddelande nu! Vi kommer att betjäna din begäran med ett helt team efter att ha fått ditt meddelande.
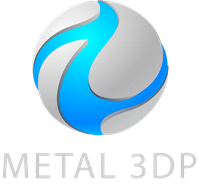
Metallpulver för 3D-printing och additiv tillverkning