Frames for Aerospace Optical Devices 3D Printed for Stability
Innehållsförteckning
Introduction: The Critical Role of Stability in Aerospace Optical Frames
In the demanding realm of aerospace engineering, precision is not just a goal; it’s a fundamental requirement. Among the most critical components demanding absolute accuracy are optical systems, which serve vital functions ranging from Earth observation and satellite imaging to laser communications and deep-space exploration. At the heart of these systems lies the aerospace optical component frame – the structural backbone responsible for holding lenses, mirrors, sensors, and other delicate optical elements in precise alignment. Failure is not an option when missions cost millions or billions, and the data gathered is irreplaceable.
These frames face extraordinary challenges unlike those encountered in terrestrial applications. Consider the journey of a satellite:
- Launch: Experiencing intense vibrations, acoustic loads, and g-forces capable of shaking components violently.
- Orbit: Subjected to extreme thermal cycles, swinging from intense solar radiation to the freezing cold of space shadow, causing materials to expand and contract.
- Operation: Requiring nanometer-level stability over years or even decades, often while components within the system (like reaction wheels or targeting gimbals) generate micro-vibrations.
Any minute distortion, misalignment, or instability in the optical frame can render a multi-million dollar instrument useless. Traditionally, manufacturing these frames involved complex machining processes from solid billets of materials like aluminum, titanium, or specialized alloys. While effective, this approach often leads to significant material waste, long lead times, and limitations in achieving optimal geometries for both structural integrity and weight reduction – a critical factor in aerospace design where every gram counts.
Det är här metalltillsatstillverkning (AM), allmänt känd som 3D-utskrift av metall, emerges as a transformative technology. By building frames layer by layer directly from metal powder, AM offers unprecedented design freedom. Engineers can create highly complex, topology-optimized structures that are both incredibly stiff and lightweight, perfectly tailored to withstand the harsh aerospace environment. Furthermore, AM enables the integration of features like internal baffling or conformal cooling channels directly into the frame, enhancing performance in ways previously impossible. For procurement managers and engineers seeking reliable B2B aerospace suppliers capable of delivering next-generation performance, understanding the potential of metal AM for optical frames is crucial. Companies like Met3dp, with expertise in high-performance metal powders and advanced printing systems, are at forefront of this revolution, enabling the creation of optical frames with unparalleled stability and performance for mission-critical applications in satellite imaging, laser communication systemsoch därefter.
Applications: Where are 3D Printed Optical Frames Deployed?
The unique advantages of metal additive manufacturing – particularly the ability to create stable, lightweight, and complex structures – have led to its adoption for optical component frames across a diverse range of demanding applications, primarily within the aerospace and defense sectors, but also extending into specialized industrial fields. Understanding these use cases helps procurement managers identify opportunities and highlights the versatility required from an optical frame manufacturer och industrial supplier.
Key Application Areas:
- Satellite Payloads:
- Earth Observation Satellites: Frames holding telescopes, multispectral imagers, and interferometers. Stability is paramount for high-resolution ground imaging. Lightweighting is critical for launch cost reduction.
- Telecommunication Satellites: Mounts for laser communication terminals (LCTs), requiring extreme pointing accuracy and thermal stability to maintain links over vast distances.
- Scientific & Exploration Missions: Structures for deep-space telescopes (like mirror mounts and instrument benches), spectrographs, and planetary lander cameras, where performance under extreme temperatures and long mission durations is vital.
- Unmanned Aerial Vehicles (UAVs) & Drones:
- Surveillance & Reconnaissance: Housings and gimbals for electro-optical/infrared (EO/IR) sensors. AM allows for compact, vibration-resistant designs suitable for the size, weight, and power (SWaP) constraints of UAVs.
- Targeting Pods: Frames for laser designators and rangefinders, demanding rigidity and thermal stability for accurate targeting.
- Manned Aircraft:
- Enhanced Vision Systems (EVS): Mounts for sensors used in pilot assistance systems, requiring reliability and stability in varying flight conditions.
- Heads-Up Displays (HUDs): Supporting structures for optical combiners and projection units.
- Defense Systems:
- Missile Seeker Heads: Optical frames for guidance systems, needing to withstand extreme acceleration and vibration.
- Ground-Based Telescopes & Beam Directors: Large optical benches and mirror cells where stability over changing environmental conditions is key.
- High-End Industrial Metrology:
- Coordinate Measuring Machines (CMMs): Frames and gantries where thermal stability (using materials like Invar) ensures measurement accuracy in controlled environments.
- Optical Comparators & Vision Systems: Stable platforms for high-precision inspection tasks.
Functional Demands Driving AM Adoption:
Application Sector | Primary Functional Demands | Why AM is Suitable | Target Keywords for Sourcing |
---|---|---|---|
Satelliter | Extreme Lightweighting, High Stiffness, Thermal Stability, Low Outgassing | Topology optimization, lattice structures, complex geometries, Ti-6Al-4V, Invar | Satellite optics mounts, Space hardware supplier |
UAVs/Drones | SWaP Constraints, Vibration Resistance, Durability | Compact designs, part consolidation, robust materials (Ti-6Al-4V) | UAV camera housing, Drone sensor frame |
Aircraft | Reliability, Certification, Moderate Lightweighting | Proven materials, process control, reduced part count | Aerospace imaging systems, Avionics structure |
Försvar | Extreme Ruggedness, High G-Load Survival, Thermal Management | Complex internal structures, robust designs, integrated cooling | Laser targeting pod, Defense optics supplier |
Industrial Metrology | Ultimate Thermal Stability, High Precision Machining Interfaces | Low CTE materials (Invar), near-net shape printing reduces machining time | Industrial metrology frames, Precision CMM parts |
Export to Sheets
The ability to tailor the design and material precisely to the application’s unique demands makes metal 3D-utskrifter an increasingly indispensable tool for flyg- och rymdteknik teams developing cutting-edge optical systems. Finding a capable B2B sourcing partner with expertise in these diverse applications is key to leveraging this technology successfully.
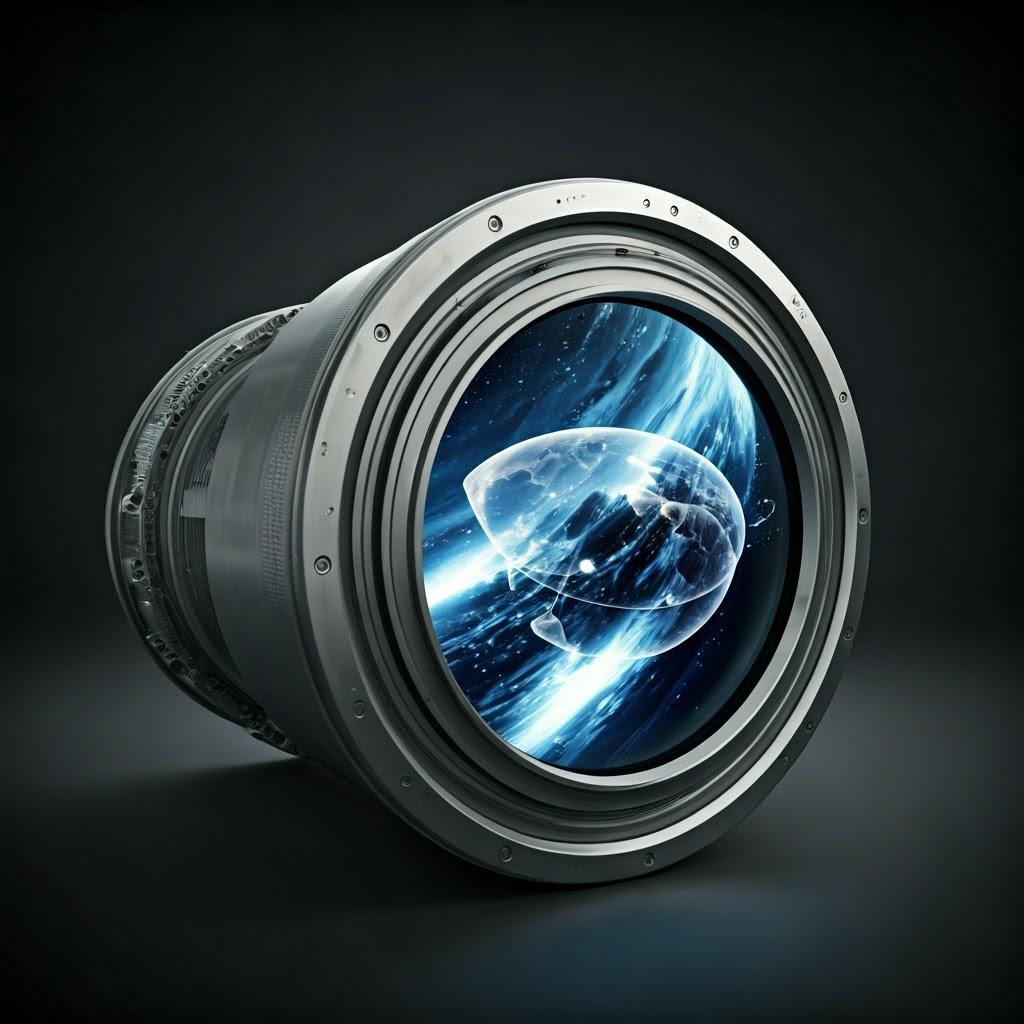
Why Metal 3D Printing for Aerospace Optical Frames? Unlocking Performance Advantages
While traditional manufacturing methods like CNC machining have served the aerospace industry well for decades, metal additive manufacturing offers a compelling suite of advantages specifically beneficial for producing high-stability optical component frames. These benefits often translate directly into improved performance, reduced mission costs, and accelerated innovation cycles. Let’s compare AM with traditional approaches, focusing on the tangible benefits for engineers and procurement decision-makers.
Limitations of Traditional Manufacturing (e.g., CNC Machining from Billet):
- Design Constraints: Limited by tool access, making complex internal features, undercuts, or optimized lattice structures difficult or impossible to produce.
- Materialavfall: Subtractive processes often start with a large block of expensive aerospace-grade material (like titanium or Invar), machining away potentially 80-90% of it as chips (buy-to-fly ratio).
- Ledtider: Complex parts may require multiple setups, specialized tooling, and extensive programming, leading to longer production timelines.
- Assembly Complexity: Often, intricate designs must be broken down into multiple simpler parts that are later assembled (bolted, welded, bonded), introducing potential points of failure, added weight, and tolerance stack-up issues.
- Vikt: Achieving significant weight reduction while maintaining stiffness is challenging without resorting to complex, multi-part assemblies or extensive, time-consuming machining passes.
Advantages of Metal Additive Manufacturing for Optical Frames:
- Oöverträffad designfrihet:
- Topology Optimization: Algorithms can dictate the most efficient material placement to achieve maximum stiffness and stability with minimum mass, resulting in organic-looking, highly efficient structures impossible to machine conventionally.
- Gitterstrukturer: Internal lattices can further reduce weight while maintaining structural integrity and potentially improving vibration damping.
- Complex Internal Features: Internal channels for baffling stray light, conformal cooling channels for thermal management of heat-generating components (like laser diodes or sensors), or hidden routing for wiring can be integrated directly into the frame design.
- Lättvikt: Directly addresses the critical need to reduce mass for launch cost savings and improved spacecraft agility. AM enables buy-to-fly ratios much closer to 1, significantly reducing material consumption compared to subtractive methods.
- Del Konsolidering: Multiple components that would traditionally be manufactured separately and assembled can often be consolidated into a single, monolithic 3D printed part. This reduces:
- Assembly time and labor costs.
- Potential points of failure (fasteners, joints).
- Tolerance stack-up issues, leading to inherently higher precision.
- Overall part count and supply chain complexity.
- Rapid Prototyping and Iteration: AM significantly accelerates the design-build-test cycle. Engineers can quickly produce functional prototypes of optical frames, test their performance, and implement design improvements much faster than with traditional tooling-based methods. This is invaluable for flyg- och rymdteknik development programs.
- Enhanced Thermal Management: The ability to design conformal cooling channels precisely where needed allows for more efficient heat dissipation from critical optical elements or electronics integrated near the frame, improving system stability and longevity.
- Materialeffektivitet: AM uses only the material needed to build the part and its supports, drastically reducing waste compared to subtractive manufacturing, especially with expensive materials like Ti-6Al-4V and Invar.
Comparative Overview:
Funktion | Traditionell CNC-bearbetning | Metal Additive Manufacturing (e.g., LPBF, SEBM) | Benefit for Optical Frames |
---|---|---|---|
Designens komplexitet | Limited by tool access | High; complex internal/external geometries feasible | Optimized stability, weight, thermal performance |
Lättvikt | Challenging; often requires excess material removal | Excellent; enables topology optimization, lattices | Reduced launch costs, improved agility |
Konsolidering av delar | Difficult; requires assembly | Straightforward; enables monolithic designs | Increased reliability, reduced assembly time |
Material Avfall | High (subtractive) | Low (additive) | Cost savings, resource efficiency |
Lead Time (Complex) | Potentially long (setups, tooling) | Potentially shorter, especially for prototypes/low vol. | Snabbare utvecklingscykler |
Interna funktioner | Very limited or impossible | Easily integrated (cooling, baffling) | Enhanced functionality, thermal stability |
Export to Sheets
Att välja 3D-utskrift av metall isn’t just about adopting a new manufacturing technique; it’s about unlocking new levels of performance and efficiency for critical aerospace systems. Partnering with an experienced provider like Met3dp, who understands the nuances of AM process control and material science, is key to realizing these advantages for demanding optical frame applications.
Material Focus: Ti-6Al-4V and Invar for Optimal Performance
Selecting the right material is arguably one of the most critical decisions when designing an aerospace optical component frame. The material must meet stringent requirements for structural integrity, stability under varying temperatures, and often, low weight. For metal 3D printed frames, two materials stand out due to their exceptional properties: Titan Ti-6Al-4V och Invar (FeNi36). Understanding their characteristics is essential for engineers making design choices and for procurement specialists sourcing metallpulver av hög kvalitet.
Titanium Ti-6Al-4V (Grade 5): The Aerospace Workhorse
Ti-6Al-4V is perhaps the most widely used titanium alloy, particularly in aerospace, due to its excellent combination of properties:
- Högt förhållande mellan styrka och vikt: Titanium alloys are significantly lighter than steels but offer comparable or even superior strength. This “specific stiffness” is invaluable for reducing launch mass.
- Utmärkt korrosionsbeständighet: Forms a stable, protective oxide layer, making it resistant to various corrosive environments, including residual propellant vapors or outgassing products within a spacecraft.
- Good Mechanical Properties at Moderate Temperatures: Retains strength well up to around 300-400°C, although its stability is temperature-dependent.
- Biokompatibilitet: While less relevant for optical frames, its biocompatibility makes it suitable for medical implants, highlighting its inert nature.
- Weldability/Printability: Ti-6Al-4V is well-characterized and readily processable using common metal AM techniques like Selective Laser Melting (SLM) / Laser Powder Bed Fusion (LPBF) and Electron Beam Melting (EBM).
When to Use Ti-6Al-4V: Ti-6Al-4V is an excellent general-purpose choice for optical frames where a balance of high strength, low weight, and good manufacturability is required, and where moderate thermal stability is acceptable. It’s ideal for structural components in satellites, UAVs, and aircraft where lightweighting is a primary driver.
Invar (FeNi36): The Champion of Thermal Stability
Invar is an iron-nickel alloy (~36% Nickel) renowned for one specific property: an extremely low coefficient of thermal expansion (CTE) around room temperature.
- Exceptionell termisk stabilitet: Invar exhibits minimal expansion or contraction with temperature fluctuations. This is absolutely critical for optical systems where even micron-level shifts due to temperature changes can cause unacceptable misalignment of mirrors, lenses, or lasers. Its CTE is roughly an order of magnitude lower than titanium or aluminum alloys near room temperature.
- God bearbetbarhet: Although gummy, Invar can be machined to high tolerances for critical interface surfaces after printing.
- Måttlig styrka: While not as strong as Ti-6Al-4V, its strength is sufficient for many structural frame applications where thermal stability is the overriding concern.
- Densitet: It is denser than titanium (similar to steel), making it less ideal where weight is the absolute primary constraint, but its stability often outweighs the mass penalty for precision optical applications.
When to Use Invar: Invar is the material of choice when the absolute highest degree of dimensional stability across a specific temperature range is paramount. This includes:
- Mounts for large telescope mirrors.
- Optical benches requiring precise, unwavering alignment.
- Frames for laser systems sensitive to thermal drift.
- Structures in metrology equipment where temperature stability directly impacts measurement accuracy.
Material Properties Comparison (Typical Values for AM):
Fastighet | Enhet | Ti-6Al-4V (Annealed) | Invar (FeNi36) (Annealed) | Significance for Optical Frames |
---|---|---|---|---|
Täthet | g/cm³ | ~4.43 | ~8.1 | Weight (Lower is better for launch costs) |
Young’s Modulus (Stiffness) | GPa | ~110-120 | ~140-150 | Structural Rigidity |
Utbyteshållfasthet | MPa | ~830-950 | ~240-280 | Resistance to permanent deformation |
Slutlig draghållfasthet | MPa | ~900-1050 | ~450-500 | Maximum stress before fracture |
CTE (20-100°C) | µm/(m·°C) or ppm/°C | ~8.6 – 9.2 | ~1.2 – 1.6 | Thermal Stability (Lower is better) |
Termisk konduktivitet | W/(m·K) | ~6.7 | ~10 | Heat dissipation capability |
Export to Sheets
Note: Properties can vary based on specific AM process parameters, heat treatments, and build orientation.
The Role of Powder Quality:
The performance of the final 3D printed frame is heavily dependent on the quality of the metal powder used. Factors like:
- Sfäriskhet: Ensures good powder flowability and dense packing during the layering process.
- Fördelning av partikelstorlek (PSD): Affects packing density and melt pool characteristics.
- Renhet: Minimizes contaminants that could compromise mechanical properties or stability.
- Low Oxygen/Interstitial Content: Critical for maintaining the desired properties of reactive materials like Titanium.
Met3dp utilizes industry-leading gasatomisering and Plasma Rotating Electrode Process (PREP) technologies to produce metallpulver av hög kvalitet, including aerospace grades like Ti-6Al-4V. Our advanced powder manufacturing systems ensure high sphericity, controlled PSD, and exceptional purity, providing the ideal foundation for printing dense, reliable, and high-performance aerospace optical frames. Choosing a supplier who controls powder quality, like Met3dp, is essential for achieving consistent and predictable results in demanding applications requiring materials like Ti-6Al-4V or specialized low-CTE alloys comparable to Invar.
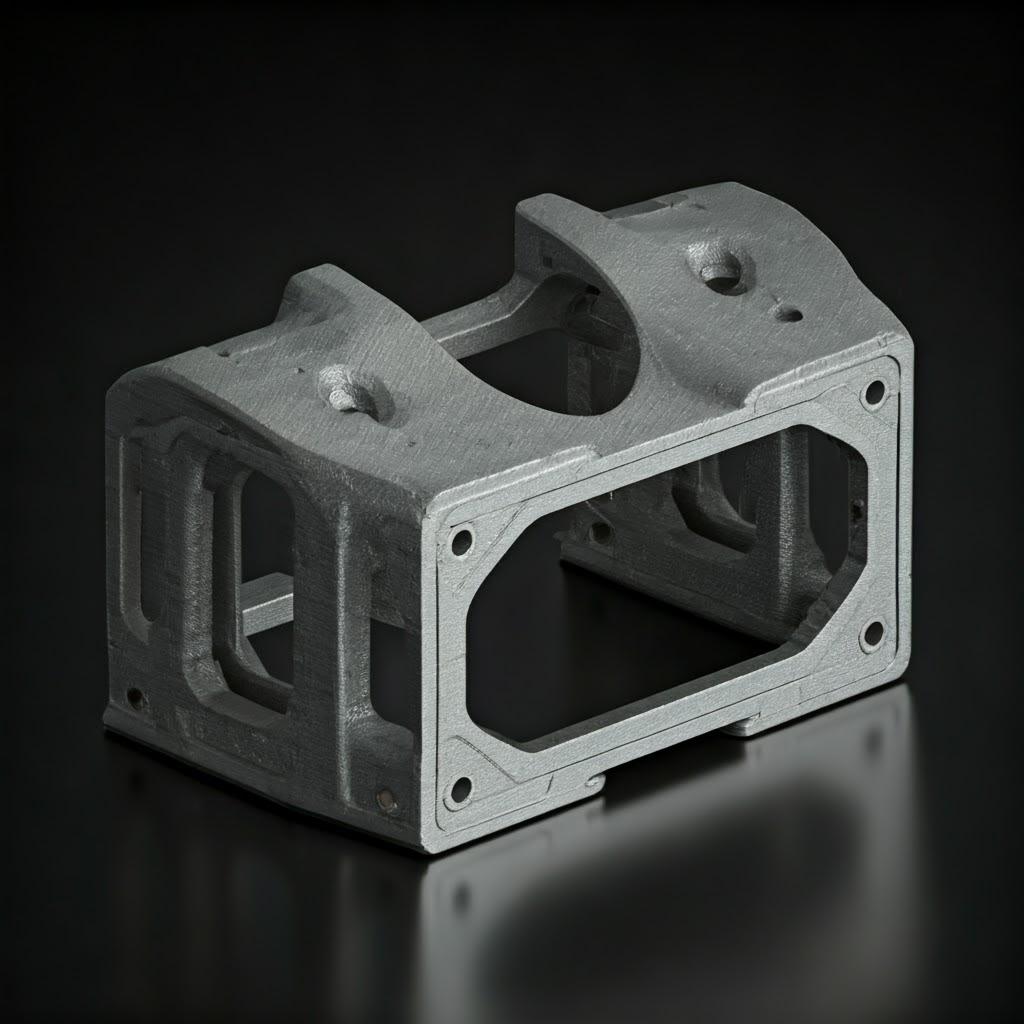
Design for Additive Manufacturing (DfAM): Optimizing Optical Frames for Printing
Simply recreating a design intended for CNC machining using additive manufacturing rarely leverages the full potential of the technology and can even lead to suboptimal results or print failures. Design för additiv tillverkning (DfAM) is a crucial mindset and methodology engineers must adopt to create optical frames that are not only functional but also optimized for the layer-by-layer building process inherent to AM. Applying DfAM principles is key to maximizing stability, minimizing weight, reducing post-processing, and ensuring successful builds. Collaboration between the design engineers and the AM service provider early in the design phase is highly recommended.
Key DfAM Principles for Aerospace Optical Frames:
- Topology Optimization:
- What it is: Using software algorithms to distribute material intelligently within a defined design space, subject to load cases (e.g., vibration, static loads) and constraints (e.g., mounting points, optical path clearances).
- Benefit: Creates highly efficient, often organic-looking structures that achieve maximum stiffness and stability with minimum mass. Ideal for lightweighting critical aerospace components.
- Consideration: Requires specialized software and expertise. The resulting geometry can be complex and may need some smoothing or adaptation for manufacturing constraints.
- Lattice Structures and Infill:
- What it is: Replacing solid volumes with internal lattice structures (e.g., honeycomb, gyroid, truss-like patterns).
- Benefit: Drastically reduces weight and material usage while maintaining significant structural support. Can also influence vibration damping characteristics.
- Consideration: Requires careful analysis to ensure strength. Powder removal from complex internal lattices can be challenging and must be planned for. Design software often incorporates these features.
- Support Structure Strategy (Minimizing Overhangs):
- What it is: AM processes typically require support structures for features that overhang the build plate or previous layers at angles below a certain threshold (often around 45 degrees). DfAM involves designing parts to minimize the need for these supports.
- Benefit: Reduces print time, material usage (supports are waste), and post-processing effort (support removal can be time-consuming and risk damaging the part). Improves surface finish on previously supported surfaces.
- Consideration: Reorienting the part in the build chamber or using strategic chamfers/fillets instead of sharp overhangs can help. Design self-supporting angles where possible. Discuss critical surfaces with your AM supplier to avoid supports in those areas.
- Wall Thickness Considerations:
- What it is: Defining appropriate minimum and maximum wall thicknesses based on the chosen AM process (LPBF, EBM) and material.
- Benefit: Ensures features are printable without collapsing (too thin) or accumulating excessive thermal stress leading to warping (too thick or large solid sections).
- Consideration: Consult provider guidelines. Thin walls print faster but may lack rigidity. Thick sections need careful thermal management during printing. Uniform wall thickness is often preferred where possible.
- Hole Orientation and Shape:
- What it is: Designing holes considering the build direction. Horizontal holes often require supports, while vertical holes print more accurately. Teardrop shapes can sometimes create self-supporting horizontal holes.
- Benefit: Improves accuracy and reduces support requirements for critical bores or mounting points.
- Consideration: If high precision is needed, holes are often printed undersized and finished with conventional machining.
- Del Konsolidering:
- What it is: Redesigning assemblies of multiple parts into a single, monolithic printed component.
- Benefit: Reduces assembly labor, fasteners, potential leak paths, tolerance stack-up, and overall weight. Improves structural integrity.
- Consideration: Requires rethinking the design from a functional perspective rather than just combining existing CAD files. Ensure internal features remain accessible for inspection or powder removal if needed.
- Designing for Powder Removal:
- What it is: Ensuring that any internal channels, cavities, or complex lattice structures have adequate outlets for trapped metal powder to be removed after printing.
- Benefit: Prevents unsintered powder from remaining inside the part, which adds weight and can be a contamination risk.
- Consideration: Include strategically placed drainage/access holes. Avoid designing features where powder can become permanently trapped. Simulation tools can help visualize powder flow.
Simulation-Driven Design: Utilizing finite element analysis (FEA) and thermal simulation early in the DfAM process is crucial. This allows engineers to:
- Validate the structural integrity and stability of topology-optimized designs under expected loads.
- Predict thermal behavior during operation.
- Simulate the printing process itself to anticipate potential issues like warping or residual stress build-up, allowing for design modifications before printing begins.
By embracing DfAM, engineers can move beyond simply replicating existing designs and truly harness the power of additive manufacturing to create next-generation aerospace optical frames with superior performance and stability. Engaging with knowledgeable AM manufacturers like Met3dp, who understand these principles and can provide feedback on design manufacturability, is a key step in this process.
Achieving Precision: Tolerance, Surface Finish, and Dimensional Accuracy
For aerospace optical component frames, achieving high precision is non-negotiable. Lenses, mirrors, and sensors must be held in exact positions and orientations, often with tolerances measured in microns. While metal 3D printing offers incredible geometric freedom, it’s essential to understand the levels of precision achievable directly from the printer versus what typically requires secondary finishing operations. Managing expectations regarding tolerance, surface finish, and overall dimensional accuracy is vital for both engineers and procurement teams.
Typical As-Printed Capabilities:
- Dimensional Tolerance:
- The general dimensional accuracy of metal AM parts (LPBF, EBM) is often cited in the range of ±0.1 mm to ±0.3 mm or ±0.1% to ±0.2% of the dimension, whichever is larger.
- However, this is highly dependent on the specific machine, material (Ti-6Al-4V vs. Invar have different thermal behaviors), part geometry, size, build orientation, and process parameters used.
- Larger parts or those with significant thermal mass variations may exhibit greater deviation due to thermal stress and potential warping.
- Surface Finish (Roughness):
- The as-printed surface finish is inherently rougher than machined surfaces due to the layer-by-layer process and partially melted powder particles adhering to the surface.
- Typical Ra (average roughness) values:
- Vertical Walls: Often range from 6 µm to 15 µm.
- Top Surfaces (facing up): Can be smoother, sometimes down to 5-10 µm Ra.
- Down-Facing/Supported Surfaces: Tend to be the roughest, potentially 15 µm to 25 µm Ra or higher, due to support structure interaction.
- Internal Channels: Can be difficult to finish and may retain a rougher surface.
- Electron Beam Melting (EBM) typically produces rougher surfaces than Laser Powder Bed Fusion (LPBF) due to higher process temperatures and powder sintering.
Factors Influencing As-Printed Precision:
- AM-process: EBM often has slightly looser tolerances but lower residual stress than LPBF. LPBF generally achieves finer features and better surface finish.
- Machine Calibration: Regular calibration and maintenance of the AM system are crucial.
- Materialegenskaper: Thermal expansion and conductivity affect warping and stress. Powder quality (particle size, shape) influences surface finish. Met3dp’s focus on metallpulver av hög kvalitet directly contributes to better achievable precision.
- Bygg orientering: Affects support needs, surface finish variance (“stair-stepping” on shallow angles), and potential for distortion.
- Termisk hantering: Process parameters (laser power, scan speed, layer thickness) and build strategy influence heat buildup and residual stress.
- Delgeometri: Large flat sections or abrupt thickness changes are more prone to warping.
Achieving High Precision – The Role of Post-Machining:
For critical interfaces, mounting points, optical seating surfaces, or any feature demanding tolerances tighter than standard AM capabilities (e.g., below ±0.1 mm), post-print CNC machining is typically required.
- Process: The near-net shape AM part is precisely fixtured in a CNC mill or lathe, and critical features are machined to final tolerances.
- Fördelar: Can achieve tolerances comparable to fully machined parts (microns, if needed). Provides excellent surface finishes (sub-micron Ra possible). Guarantees accuracy of critical interfaces.
- Överväganden:
- Requires careful planning – sufficient stock material must be left on features intended for machining during the DfAM stage.
- Adds cost and lead time compared to using the part as-printed.
- Fixturing complex AM geometries can be challenging.
Quality Control and Inspection:
Rigorous quality control is essential for aerospace components. Common inspection methods include:
- Coordinate Measuring Machine (CMM): Provides high-accuracy dimensional verification of the final part against the CAD model.
- 3D Scanning: Captures the overall geometry for comparison and deviation analysis.
- Surface Roughness Testers: Quantifies the finish on critical surfaces.
- Icke-förstörande testning (NDT): Methods like CT scanning can be used to inspect internal features and check for porosity or defects, ensuring compliance with aerospace quality standards.
Met3dp understands the critical nature of precision in aerospace. Our process controls, high-quality equipment, and expertise in post-processing ensure that we can deliver optical frames meeting stringent dimensional accuracy and surface finish requirements, whether achieved as-printed or through carefully integrated secondary machining operations. We work closely with clients to define achievable tolerances and develop the most effective manufacturing plan based on the precision optical mount krav.
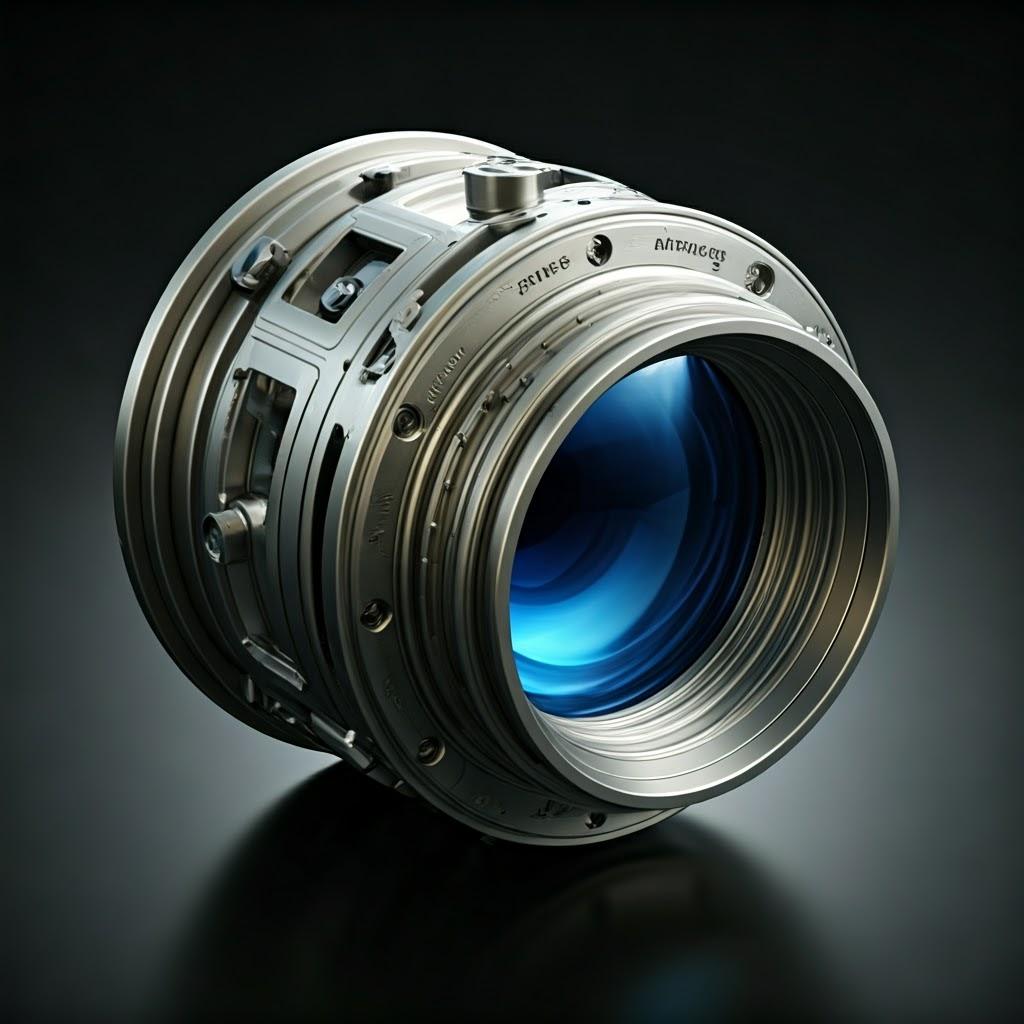
Essential Post-Processing Steps for Aerospace Optical Frames
Creating an aerospace optical frame rarely ends when the 3D printer stops. A series of crucial post-processing steps are typically required to transform the raw printed part into a flight-ready, high-performance component. These steps are vital for ensuring mechanical integrity, dimensional accuracy, surface quality, and long-term stability – all paramount for optical applications. Understanding these requirements is essential for accurate project planning, costing, and lead time estimation by procurement teams and engineers.
Common Post-Processing Workflow:
- Powder Removal / Depowdering:
- Goal: Remove all loose, unsintered metal powder from the part, especially from internal channels, lattice structures, and complex geometries.
- Metoder: Compressed air blowing, vibration, ultrasonic cleaning baths, careful manual brushing. Access holes designed during DfAM are critical here.
- Importance: Residual powder adds weight, can be a source of contamination, and prevents effective subsequent steps like heat treatment.
- Stress Relief / Heat Treatment:
- Goal: Relieve internal stresses built up during the rapid heating and cooling cycles of the AM process. Minimize distortion during subsequent steps (like support removal or machining) and improve long-term dimensional stability. For some materials like Ti-6Al-4V, specific heat treatments can also optimize mechanical properties (e.g., annealing, solution treatment, aging).
- Metoder: Heating the part in a controlled atmosphere furnace (vacuum or inert gas like Argon) to specific temperatures and holding for a defined duration, followed by controlled cooling. Parameters depend heavily on the material (Ti-6Al-4V vs. Invar cycles differ significantly) and desired outcome.
- Importance: Absolutely critical for preventing warping and ensuring the frame remains dimensionally stable under operational thermal loads. Heat treatment aerospace standards must be followed.
- Borttagning av stödstruktur:
- Goal: Carefully detach the part from the build plate and remove all temporary support structures generated during the print.
- Metoder: Band sawing, wire EDM (Electrical Discharge Machining), manual breaking/cutting (for delicate supports), CNC machining. The method depends on the support type, material, and geometry.
- Importance: Supports are necessary for printing but must be removed without damaging the part’s surfaces or features. This can be a labor-intensive step.
- Het isostatisk pressning (HIP):
- Goal: Eliminate internal microporosity, densify the material to nearly 100%, and improve fatigue life, ductility, and fracture toughness.
- Metoder: Subjecting the part to high temperature (below melting point) and high isostatic pressure (using an inert gas like Argon) simultaneously in a specialized HIP unit.
- Importance: Often mandated for critical aerospace components (AS9100 requirements) and parts subjected to high fatigue loads. It significantly enhances material integrity and consistency. Particularly beneficial for improving properties of Ti-6Al-4V.
- CNC Machining (If Required):
- Goal: Achieve final tolerances on critical interfaces, mounting pads, optical seats, or bores that exceed as-printed accuracy. Improve surface finish on specific features.
- Metoder: Using precision CNC milling or turning centers. Careful fixture design is essential for complex AM shapes.
- Importance: Bridges the gap between AM’s geometric freedom and the micron-level precision needed for many optical interfaces.
- Ytbehandling:
- Goal: Improve the as-printed surface roughness for functional (e.g., sealing surfaces) or aesthetic reasons, or to prepare for coatings.
- Metoder: Abrasive blasting (sandblasting, bead blasting), tumbling, vibratory finishing, polishing, electro-polishing. The choice depends on the desired Ra value and part geometry. Polishing optics mounts might involve manual steps for critical areas.
- Importance: Smooth surfaces can reduce stress concentrations and improve fatigue life. Specific finishes may be required for optical stray light control or coating adhesion.
- Cleaning & Inspection:
- Goal: Final cleaning to remove any machining fluids, debris, or contaminants. Comprehensive inspection to verify dimensional accuracy, surface finish, and material integrity.
- Metoder: Ultrasonic cleaning, visual inspection, CMM, 3D scanning, NDT (CT, X-ray, FPI – Fluorescent Penetrant Inspection).
- Importance: Slutlig quality assurance testing ensures the part meets all specifications before delivery or integration.
Post-Processing Considerations Summary:
Post-Processing Step | Syfte | Typical Method(s) | Key Consideration |
---|---|---|---|
Depowdering | Remove loose powder | Air, Vibration, Ultrasonics | Design for powder escape |
Stress Relief/Heat Tx | Reduce stress, improve stability/properties | Controlled Furnace Cycle | Material-specific parameters are critical |
Borttagning av stöd | Detach supports & part from build plate | Saw, EDM, Manual, CNC | Avoid part damage; can be labor-intensive |
HIP | Eliminate porosity, improve properties | High Temp & Pressure (Inert Gas) | Often required for critical parts; adds cost/time |
CNC-bearbetning | Achieve final tight tolerances/finish | Milling, Turning | Design with machining stock; fixture design |
Ytbehandling | Improve Ra, prepare for coating | Blasting, Tumbling, Polishing | Desired finish level; accessibility |
Cleaning & Inspection | Final cleanliness, verify specifications | Cleaning Baths, CMM, NDT | Ensure part meets all requirements |
Export to Sheets
The extent and nature of post-processing significantly impact the final cost and lead time of a 3D printed aerospace optical frame. Met3dp possesses comprehensive in-house and partnered capabilities for managing these essential steps, ensuring a streamlined workflow from raw print to finished, validated component according to stringent aerospace quality standards.
Navigating Challenges in Printing Optical Frames: Solutions and Best Practices
While metal 3D printing offers significant advantages for aerospace optical frames, it’s not without its challenges. Producing high-precision, stable components, especially with complex geometries or demanding materials like Invar, requires deep process understanding and careful control. Anticipating and mitigating potential issues is key to successful manufacturing outcomes and meeting strict aerospace quality standards.
Common Challenges and Mitigation Strategies:
- Warping and Distortion (Residual Stress):
- Utmaning: The rapid heating/cooling cycles inherent in AM generate internal stresses. If not managed, these stresses can cause the part to warp during printing, after removal from the build plate, or during post-processing (especially heat treatment). This is particularly relevant for frames needing high stability.
- Solutions:
- Optimized Support Structures: Well-designed supports anchor the part firmly to the build plate and help dissipate heat.
- Processparameteroptimering: Fine-tuning laser/electron beam power, scan speed, and scan strategy (e.g., sector-based scanning) to minimize localized heat buildup.
- Thermal Simulation: Predicting areas of high stress concentration during the design phase (DfAM) and modifying geometry accordingly (e.g., adding fillets, avoiding large flat sections).
- Appropriate Heat Treatment: Performing stress relief cycles immediately after printing and before support removal is crucial.
- Choosing the Right Process: EBM generally induces lower residual stress than LPBF due to the higher overall build chamber temperature, which can be advantageous for large or complex frames prone to warping.
- Support Structure Removal Difficulty:
- Utmaning: Supports, especially dense ones needed for heavy sections or difficult materials, can be very hard to remove without damaging the part surface or leaving residual marks (“witness marks”). Accessing internal supports can also be problematic.
- Solutions:
- DfAM for Reduced Supports: Designing with self-supporting angles and minimizing overhangs.
- Optimized Support Design: Using support types (e.g., tree supports, conical supports) that are strong yet easier to detach. Software tools offer various strategies. Defining weaker interface layers between the part and support.
- Choosing Appropriate Removal Methods: Using wire EDM for clean cuts on thick supports, or careful manual removal for delicate areas. Post-machining or polishing can remove witness marks on critical surfaces.
- Powder Removal from Internal Channels/Lattices:
- Utmaning: Unsintered powder can become trapped within intricate internal geometries, adding weight and potentially compromising performance or cleanliness requirements.
- Solutions:
- DfAM Planning: Designing clear pathways and sufficiently large drainage/access holes for powder escape.
- Orientation Strategy: Orienting the part during build setup to facilitate powder drainage.
- Thorough Depowdering Processes: Utilizing multi-stage cleaning involving vibration tables, compressed air, and potentially ultrasonic cleaning.
- Inspection: Using methods like CT scanning to verify complete powder removal in critical cases.
- Porositetskontroll:
- Utmaning: Small voids or pores can form within the printed material due to incomplete melting, gas entrapment, or keyholing defects during the AM process. Porosity can degrade mechanical properties (especially fatigue strength) and consistency.
- Solutions:
- High-Quality Powder: Using powder with controlled sphericity, PSD, and low gas content (like those produced by Met3dp’s advanced atomization processes).
- Optimized Process Parameters: Developing and validating robust parameter sets (power, speed, layer thickness, hatch spacing) specific to the material and machine.
- Pågående övervakning: Some advanced AM systems incorporate sensors to monitor the melt pool stability in real-time, potentially detecting conditions likely to cause porosity.
- Het isostatisk pressning (HIP): The most effective method for closing internal pores and achieving full densification, often mandated for critical aerospace parts.
- Achieving Fine Tolerances and Surface Finish:
- Utmaning: As discussed previously, meeting the tightest tolerance and surface finish requirements directly from the printer can be difficult.
- Solutions:
- Process Control & Calibration: Maintaining well-calibrated machines and tightly controlled processes.
- Material-Specific Parameter Sets: Understanding how different materials behave during printing.
- Strategic Post-Processing: Integrating CNC machining and surface finishing operations specifically for critical features, planned during the DfAM stage.
- Build Failure:
- Utmaning: Prints can sometimes fail mid-build due to issues like recoater blade crashes (due to part warping), delamination between layers, or insufficient support leading to part collapse.
- Solutions:
- Robust Simulation & Planning: Simulating the build to anticipate risks.
- Careful Machine Setup & Monitoring: Ensuring proper machine operation and potentially utilizing in-process monitoring tools.
- Experienced Operators & Engineers: Having skilled personnel who understand the nuances of the AM process is invaluable. Partnering with an experienced AM supplier like Met3dp significantly reduces this risk.
Successfully manufacturing aerospace optical frames via metal AM requires a holistic approach, combining robust DfAM practices, careful material selection, validated process parameters, comprehensive post-processing, and rigorous quality control. By understanding and proactively addressing these potential challenges, manufacturers can reliably deliver components that meet the extreme demands of the aerospace industry.
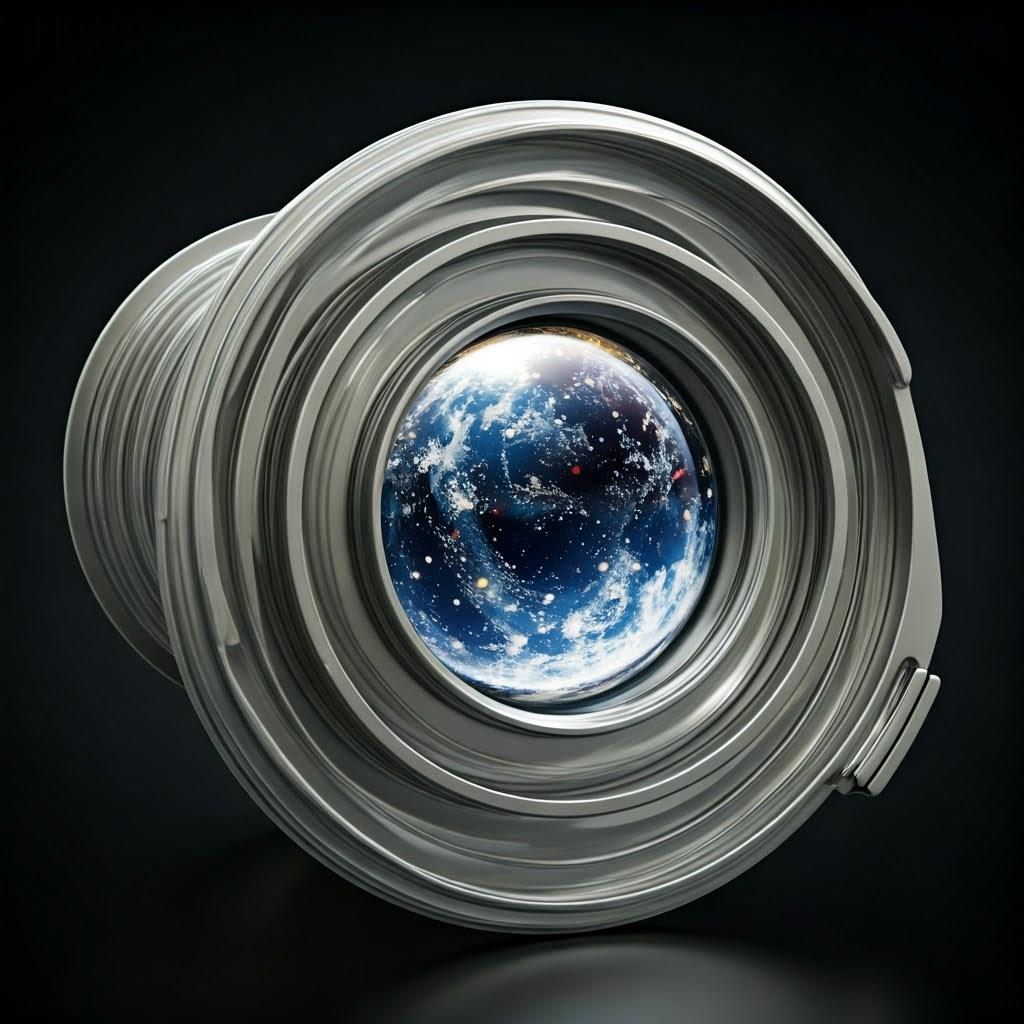
Selecting Your Metal AM Partner: Criteria for Aerospace Applications
Choosing the right additive manufacturing partner is as critical as the design and material selection, especially when dealing with high-stakes aerospace optical components. The difference between a successful project and costly delays or failures often lies in the capabilities, experience, and quality systems of your chosen AM supplier. För procurement managers and engineers involved in B2B sourcing, evaluating potential partners requires looking beyond just price and considering factors crucial to aerospace performance and reliability.
Essential Criteria for Evaluating Metal AM Providers:
- Aerospace Certifications and Quality Management:
- AS9100 Certification: This is the standard quality management system (QMS) for the aviation, space, and defense industries. Compliance or certification to AS9100 indicates the supplier has robust processes for traceability, configuration management, risk management, and process control necessary for aerospace work.
- ISO 9001: A fundamental QMS certification, often a prerequisite for AS9100.
- Robust QMS: Even without formal AS9100 certification (which can be costly for smaller suppliers), inquire deeply about their internal quality procedures, documentation practices, and how they ensure consistency and repeatability.
- Material Expertise and Traceability:
- Experience with Specific Alloys: Proven success printing the required materials (Ti-6Al-4V, Invar, or comparable low-CTE alloys) is essential. Ask for case studies or examples.
- Powder Handling and Management: Strict procedures for storing, handling, sieving, and recycling metal powders to prevent contamination and ensure powder quality batch-to-batch.
- Full Material Traceability: Ability to trace the specific powder batch used for a part back to the original powder manufacturer’s certificate of conformity. This is non-negotiable for aerospace components. Met3dp, manufacturing its own metallpulver av hög kvalitet using advanced gas atomization and PREP technologies, offers exceptional control and traceability from raw material to finished part.
- Process Validation and Control:
- Validated Parameter Sets: The provider should have thoroughly developed and validated printing parameters for the specific material/machine combination being used.
- Process Monitoring: Capabilities for monitoring key aspects of the build process (e.g., melt pool monitoring, oxygen levels, temperature) can provide greater assurance of build quality.
- Equipment Calibration and Maintenance: Regular, documented calibration and preventative maintenance schedules for their AM machines are crucial for consistent results.
- Technology and Equipment Capabilities:
- Appropriate AM Technology: Do they have the right process for your needs? Laser Powder Bed Fusion (LPBF/SLM) for fine features and surface finish, or Electron Beam Melting (SEBM) for lower residual stress and potentially faster builds with certain materials like Ti-6Al-4V. Met3dp offers cutting-edge SEBM skrivare known for industry-leading volume, accuracy, and reliability.
- Machine Fleet: Sufficient capacity and potentially redundant machines to ensure timely delivery and mitigate risks associated with machine downtime.
- Post-Processing Capabilities: In-house or tightly managed external capabilities for critical post-processing steps like heat treatment (with aerospace-certified furnaces), HIP, precision CNC machining, and NDT.
- Engineering Support and DfAM Expertise:
- Collaborative Approach: Willingness to work closely with your engineering team during the design phase to provide DfAM feedback and optimize the part for manufacturability, stability, and cost-effectiveness.
- Teknisk expertis: Experienced engineers and metallurgists on staff who understand the nuances of metal AM, material science, and the specific requirements of aerospace applications. Met3dp’s team brings decades of collective expertise in metal additive manufacturing.
- Track Record and Experience:
- Aerospace Project History: Demonstrated experience successfully delivering parts for similar aerospace or high-reliability applications.
- References and Case Studies: Ability to provide relevant examples of past work and potentially client references.
- Confidentiality and Security:
- Handling Sensitive Data: Procedures for managing potentially sensitive or proprietary design data (e.g., ITAR compliance if required for US defense projects).
Evaluation Checklist Summary:
Kriterier | Key Questions to Ask | Why It Matters for Optical Frames |
---|---|---|
Certifications/QMS | AS9100 certified? ISO 9001? Describe your QMS & documentation process. | Ensures process control, repeatability, traceability for reliability. |
Material Expertise/Traceability | Experience with Ti-6Al-4V/Invar? How do you manage/trace powder? | Guarantees material integrity and performance consistency. |
Process Validation/Control | Are parameters validated? What in-process monitoring do you use? | Reduces build failures, ensures desired material properties. |
Equipment/Technology | Which AM process (LPBF/EBM)? Machine capabilities? Post-processing available? | Matches technology to part needs (precision, stress, features). |
Engineering/DfAM Support | Do you offer DfAM consultation? What is your team’s technical background? | Optimizes design for AM, improves performance, reduces cost. |
Track Record/Experience | Can you share relevant aerospace case studies or references? | Demonstrates ability to handle demanding applications. |
Confidentiality/Security | How do you protect sensitive design data? ITAR compliant (if needed)? | Protects intellectual property and meets regulatory needs. |
Export to Sheets
Choosing a partner like Met3dp, which combines advanced powder production, state-of-the-art SEBM printing technology, comprehensive post-processing knowledge, and a strong engineering team focused on application development, provides a solid foundation for producing mission-critical aerospace optical frames.
Understanding Cost Drivers and Lead Times for 3D Printed Frames
While performance and stability are paramount for aerospace optical frames, understanding the factors that influence cost and lead time is crucial for project planning, budgeting, and effective procurement. Metal 3D printing costs are calculated differently than traditional machining, and lead times can vary significantly based on several factors.
Primary Cost Drivers:
- Material Type and Consumption:
- Kostnad för pulver: High-performance metal powders like aerospace-grade Ti-6Al-4V and especially specialized alloys like Invar are expensive raw materials. The cost is directly proportional to the volume (and thus weight) of the final part plus any support structures.
- Buy-to-Fly Ratio: While significantly better than machining, AM still consumes material for supports. Optimized designs minimize this waste.
- Machine Time (Build Time):
- Part Volume & Height: Larger parts or taller parts simply take longer to print layer by layer.
- Komplexitet: Very intricate features or thin walls might require slower printing speeds for accuracy.
- Number of Parts per Build: Utilizing the build chamber volume efficiently by printing multiple parts simultaneously (nesting) can significantly reduce the machine time cost per part. This is key for wholesale 3D printing or batch production.
- AM-process: Build speeds can vary between different machines and technologies (e.g., multi-laser LPBF systems print faster than single-laser ones). Printing methods like SEBM may offer speed advantages for certain materials/geometries.
- Labor and Engineering:
- Setup Time: Preparing the build file (orientation, supports), loading the machine, etc.
- DfAM Support: If significant design consultation or optimization is required from the AM provider’s engineers.
- Post-Processing Labor: Manual tasks like powder removal, support removal, basic surface finishing.
- Post-Processing Complexity:
- Heat Treatment/HIP: These require specialized equipment and add significant time and cost, especially HIP.
- CNC Machining: Cost depends on the number of features, required tolerance, complexity of fixturing, and machining time.
- Ytbehandling: Extensive polishing or specialized coatings add cost.
- Inspection: Advanced NDT like CT scanning or extensive CMM checks increase cost.
- Quality Requirements and Certifications:
- Testing & Documentation: The level of required material testing, process documentation, and final inspection reports (especially for AS9100 compliance) adds overhead cost.
Factors Influencing Lead Times:
- Design & Preparation: Time required for DfAM review, support generation, and build simulation.
- Machine Availability: Queue times for the appropriate AM machine. High-demand machines may have longer queues.
- Print Time: Can range from hours for small parts to many days for large, complex frames or full build plates.
- Efterbearbetning: Each step adds time:
- Heat Treatment/HIP: Typically 1-3 days per cycle (including furnace time, cooling).
- Machining: Highly variable, from hours to days depending on complexity.
- Support/Powder Removal: Hours to days.
- Inspection: Variable.
- Frakt: Transit time to the customer’s facility.
- Order Volume: Larger batch orders may have longer overall lead times but benefit from efficiencies of scale during printing and post-processing. Expedited manufacturing options may be available at a premium cost.
Typical Lead Time Breakdown (Estimation):
Etapp | Estimated Time Range | Anteckningar |
---|---|---|
Order Review & Prep | 1-3 Business Days | Assuming final design is ready |
Machine Queue | 1-10 Business Days | Highly variable based on demand/capacity |
Tryckning | 1-7 Days | Dependent on part size, complexity, nesting |
Depowder/Stress Relief | 1-3 Days | Essential first steps |
Support Removal/HIP | 1-4 Days | HIP adds significant time if required |
CNC-bearbetning | 1-5 Days | Only if required, complexity dependent |
Finishing/Inspection | 1-3 Days | Final checks and basic finishing |
Total (Estimate) | ~2 – 6 Weeks | Highly variable; simpler parts faster, complex parts requiring all steps longer. |
Export to Sheets
It’s crucial to discuss specific project requirements, including tolerances, post-processing needs, and quality documentation, with your chosen AM supplier like Met3dp to get an accurate quote and realistic lead time estimate for your aerospace optical frame project.
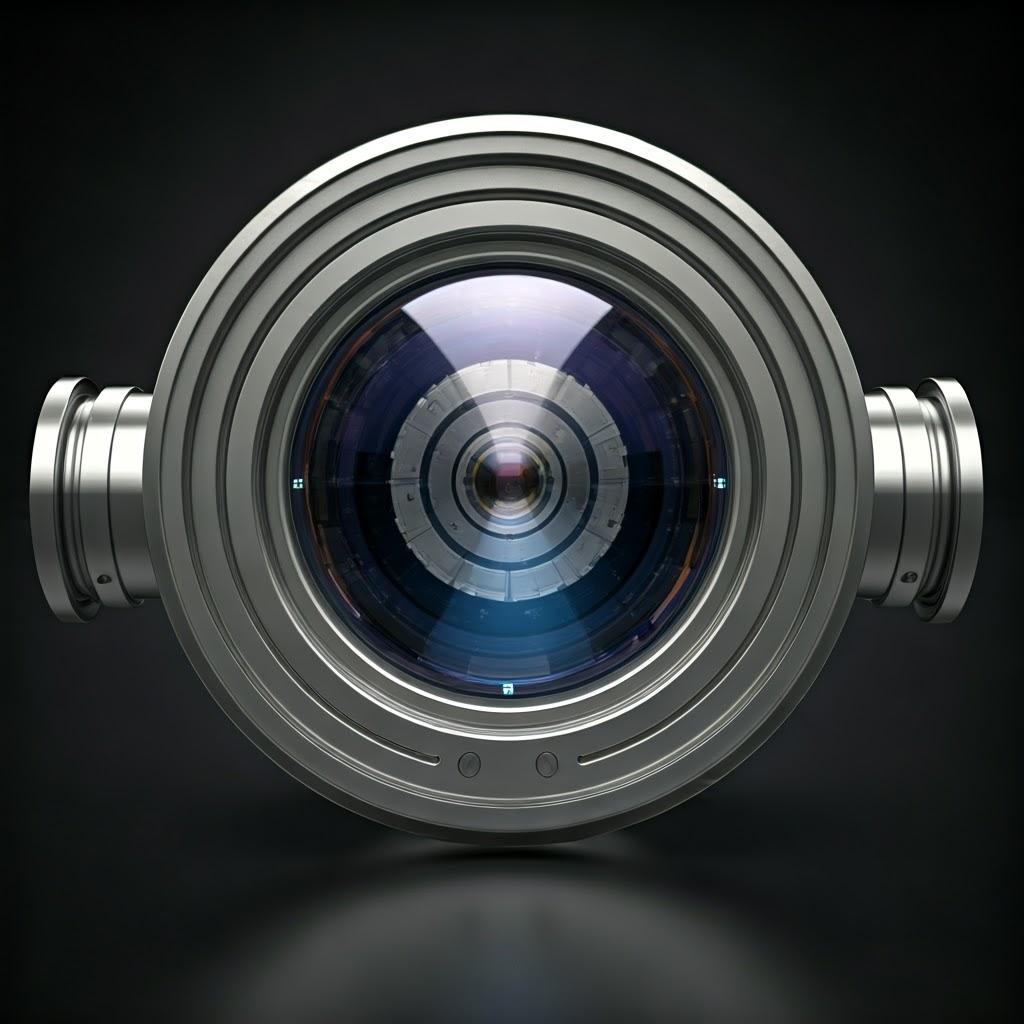
Frequently Asked Questions (FAQ) about 3D Printed Aerospace Optical Frames
Here are answers to some common questions engineers and procurement specialists have about using metal AM for these critical components:
- How does the thermal stability of a 3D printed Invar frame compare to a traditionally machined one?
- When printed using optimized parameters and subjected to appropriate stress relief and potentially HIP processing, a 3D printed Invar (FeNi36) frame can achieve the same extremely low coefficient of thermal expansion (CTE) characteristic of wrought or machined Invar. The key is ensuring full densification and a homogenous microstructure. The AM process itself doesn’t inherently change the fundamental low-expansion property of the alloy, but proper processing is vital to realize it fully. Met3dp’s process control ensures optimal material properties are achieved.
- Is 3D printed Ti-6Al-4V strong enough for demanding aerospace structural applications like optical frames?
- Absolutely. Metal AM processes like SEBM and LPBF, when properly controlled and followed by appropriate heat treatments (like annealing or HIP), can produce Ti-6Al-4V parts with mechanical properties (yield strength, tensile strength, fatigue life) that meet or even exceed those of wrought or cast Ti-6Al-4V specifications (e.g., ASTM F136, ASTM B348). It is widely accepted and used for flight-critical components in aerospace, demonstrating its robustness. Material certification data from the AM provider is crucial verification.
- What is the typical cost comparison between 3D printing an optical frame versus CNC machining it from billet?
- The cost comparison is complex and depends heavily on part geometry, material, and quantity.
- For highly complex geometries with features difficult or impossible to machine (e.g., internal lattices, topology-optimized shapes), AM is often more cost-effective, especially considering the reduced material waste (buy-to-fly ratio).
- For relatively simple geometries that are easily machined from a standard block, CNC machining may still be cheaper, particularly at higher volumes.
- Konsolidering av delar via AM can shift the balance: printing one complex part might be cheaper than machining multiple simple parts and assembling them.
- Material choice matters: The high cost of Invar makes the material savings from AM particularly attractive compared to machining it from a large billet.
- It’s best to get quotes for both methods for your specific part to make an informed decision, considering not just unit price but also lead time and potential performance benefits of an AM-optimized design.
- The cost comparison is complex and depends heavily on part geometry, material, and quantity.
Conclusion: Elevating Aerospace Optics with Additive Manufacturing Stability
The relentless pursuit of higher performance, lower mass, and greater resilience in aerospace systems demands continuous innovation in manufacturing. For aerospace optical component frames, where stability is not just desired but fundamentally mission-critical, additiv tillverkning av metall represents a significant leap forward.
By leveraging the design freedom of AM, engineers can create optical frames optimized for specific stiffness, vibration damping, and thermal stability using advanced materials like high-strength Ti-6Al-4V and ultra-stable Invar. The ability to produce complex, lightweight structures, consolidate assemblies, and integrate thermal management features directly addresses the core challenges faced in satellite imaging, laser communications, and deep-space observation platforms. While challenges exist, solutions like rigorous DfAM, advanced process control, essential post-processing (heat treatment, HIP), and stringent quality verification enable the reliable production of flight-ready components.
Choosing the right manufacturing partner – one with proven aerospace expertise, robust quality systems (like AS9100 awareness), validated processes, advanced equipment, and high-quality materials – is paramount to success.
Met3dp stands at the forefront of this technological shift. With our deep expertise in metal additive manufacturing, vertically integrated capabilities spanning advanced metallpulver production (Gas Atomization, PREP) to cutting-edge SEBM skrivare, and a comprehensive understanding of post-processing and quality assurance, we provide end-to-end solutions for the most demanding aerospace applications. We partner with organizations to unlock the transformative potential of AM, accelerating innovation and enabling the development of next-generation aerospace hardware.
Contact Met3dp today to explore how our capabilities can enhance the stability and performance of your critical aerospace optical systems.
Dela på
MET3DP Technology Co, LTD är en ledande leverantör av lösningar för additiv tillverkning med huvudkontor i Qingdao, Kina. Vårt företag är specialiserat på 3D-utskriftsutrustning och högpresterande metallpulver för industriella tillämpningar.
Förfrågan för att få bästa pris och anpassad lösning för ditt företag!
Relaterade artiklar
Om Met3DP
Senaste uppdateringen
Vår produkt
KONTAKTA OSS
Har du några frågor? Skicka oss meddelande nu! Vi kommer att betjäna din begäran med ett helt team efter att ha fått ditt meddelande.
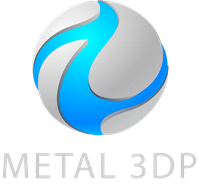
Metallpulver för 3D-printing och additiv tillverkning