Aerospace Spacers 3D Printed for Tight Tolerances
Innehållsförteckning
Introduction: Precision Aerospace Spacers Redefined by Additive Manufacturing
In the demanding realm of aerospace engineering, every component, regardless of size, plays a critical role in ensuring flight safety, reliability, and performance. Among these vital parts are aerospace spacers – seemingly simple components tasked with complex responsibilities, from maintaining precise gaps between assemblies to ensuring proper alignment and load distribution. Traditionally manufactured through subtractive methods like CNC machining, the production of custom spacers, especially those with intricate designs or requiring high-performance materials, often faces challenges related to cost, lead time, and geometric limitations. Enter metal additive manufacturing (AM), or 3D printing, a transformative technology that is fundamentally reshaping how aerospace components, including spacers, are designed and produced. For aerospace engineers and procurement managers seeking superior performance, design freedom, and supply chain agility, understanding the capabilities of metal AM is paramount.
Metall 3D-utskrifter allows for the creation of spacers layer by layer directly from digital models, using high-performance metal powders. This approach unlocks unprecedented possibilities:
- Komplexa geometrier: Manufacturing intricate internal channels for cooling or lightweight lattice structures within the spacer body, previously impossible or prohibitively expensive.
- Materialeffektivitet: Utilizing materials like Titanium alloys (e.g., Ti-6Al-4V) and high-strength Stainless Steels (e.g., 17-4PH) with minimal waste compared to subtractive processes.
- Rapid Prototyping & Customization: Quickly iterating designs and producing highly customized spacers tailored to specific application requirements without the need for expensive tooling.
- Consolidation: Redesigning assemblies to integrate spacer functions into larger components, reducing part count, weight, and potential failure points.
- Tight Tolerances: Achieving the high precision demanded by aerospace applications, often rivaling or exceeding traditional methods when combined with appropriate post-processing.
Företag gillar Met3dp are at the forefront of this technological shift. Headquartered in Qingdao, China, Met3dp specializes in industrial metal 3D printing solutions, offering both advanced printing equipment and a wide range of high-performance metal powders optimized for aerospace applications. Our expertise in processes like Selective Laser Melting (SLM) and Electron Beam Melting (EBM), combined with industry-leading gas atomization and Plasma Rotating Electrode Process (PREP) technologies for powder production, ensures that we deliver components meeting the stringent quality and performance standards of the aerospace sector. This post delves into the specifics of using metal 3D printing for custom aerospace spacers, exploring applications, material choices, design considerations, and how to partner with a qualified supplier to leverage this powerful technology. We aim to provide valuable insights for B2B buyers, aerospace suppliers, and engineering teams looking to optimize their component sourcing and manufacturing strategies.
Critical Functions: What Are Custom Aerospace Spacers Used For?
Aerospace spacers are indispensable components found throughout aircraft, spacecraft, and related subsystems. Their primary function is to create and maintain a specific, controlled distance between two other components or surfaces. However, their role often extends beyond simple spacing, encompassing a variety of critical functions essential for structural integrity, system performance, and operational safety. Understanding these diverse applications highlights why precision, material properties, and manufacturing reliability are non-negotiable.
Key Functions and Applications:
- Maintaining Precise Gaps and Clearances:
- Function: Ensuring adequate space for thermal expansion, vibration damping, electrical insulation, fluid flow, or preventing contact and wear between moving parts.
- Applikationer: Mounting electronic boxes (avionics) to structures, separating hydraulic or fuel lines, ensuring clearance in landing gear mechanisms, spacing turbine blades or engine components.
- Importance: Incorrect spacing can lead to overheating, short circuits, fluid leaks, premature wear, or catastrophic mechanical failure.
- Ensuring Accurate Alignment:
- Function: Aligning mating components during assembly, ensuring load paths are correctly distributed, and maintaining the geometric accuracy of complex assemblies.
- Applikationer: Aligning structural bulkheads or fuselage sections, positioning actuators or sensors, ensuring concentricity in rotating machinery mounts, setting bearing preloads.
- Importance: Misalignment can induce stress concentrations, reduce fatigue life, impair aerodynamic efficiency, or cause system malfunctions.
- Load Distribution and Stress Management:
- Function: Distributing concentrated loads over a wider area, preventing localized stress peaks in underlying structures, and acting as a sacrificial element in some cases.
- Applikationer: Underneath fasteners (bolts, rivets) to prevent pull-through or crushing of composite materials, between structural joints, mounting heavy equipment.
- Importance: Prevents damage to critical structures, enhances fatigue resistance, and ensures the assembly can withstand operational loads.
- Thermal and Electrical Insulation:
- Function: Acting as a thermal break to limit heat transfer between components or providing electrical isolation to prevent short circuits or galvanic corrosion.
- Applikationer: Spacers made from materials with specific thermal or electrical properties used near engines, exhaust systems, power distribution units, or sensitive electronics.
- Importance: Protects components from temperature extremes, ensures electromagnetic compatibility (EMC), and prevents electrical system failures.
- Vibration Damping:
- Function: Incorporating specific geometries or materials to help absorb or dampen vibrations transmitted between components.
- Applikationer: Mounting sensitive equipment, reducing resonant frequencies in structural panels, isolating vibrating machinery.
- Importance: Improves passenger comfort, extends the life of sensitive electronics, and enhances overall structural integrity by mitigating fatigue damage.
Industries & Subsystems:
Custom aerospace spacers are ubiquitous across various segments:
- Commercial Aviation: Fuselage structures, wing assemblies, engine pylons, landing gear, cabin interiors, avionics bays.
- Försvar och militär: Fighter jets, transport aircraft, helicopters, missile systems, UAVs – often requiring high-temperature or high-strength materials.
- Utforskning av rymden: Satellites, launch vehicles, space stations – demanding extreme reliability, lightweighting, and resistance to harsh environments (radiation, vacuum, temperature cycling).
- Avionics & Electronics: Mounting circuit boards, connectors, power supplies, and display units.
The need for custom spacers arises from the unique requirements of each application. Factors like specific gap dimensions, complex interfacing geometries, weight constraints, operating temperatures, load profiles, and material compatibility often necessitate tailor-made solutions rather than off-the-shelf parts. This is where the flexibility of metal 3D printing becomes particularly advantageous for aerospace manufacturers and their supply chain partners. Procurement managers sourcing these critical components need reliable suppliers capable of delivering custom parts that meet exacting specifications consistently.
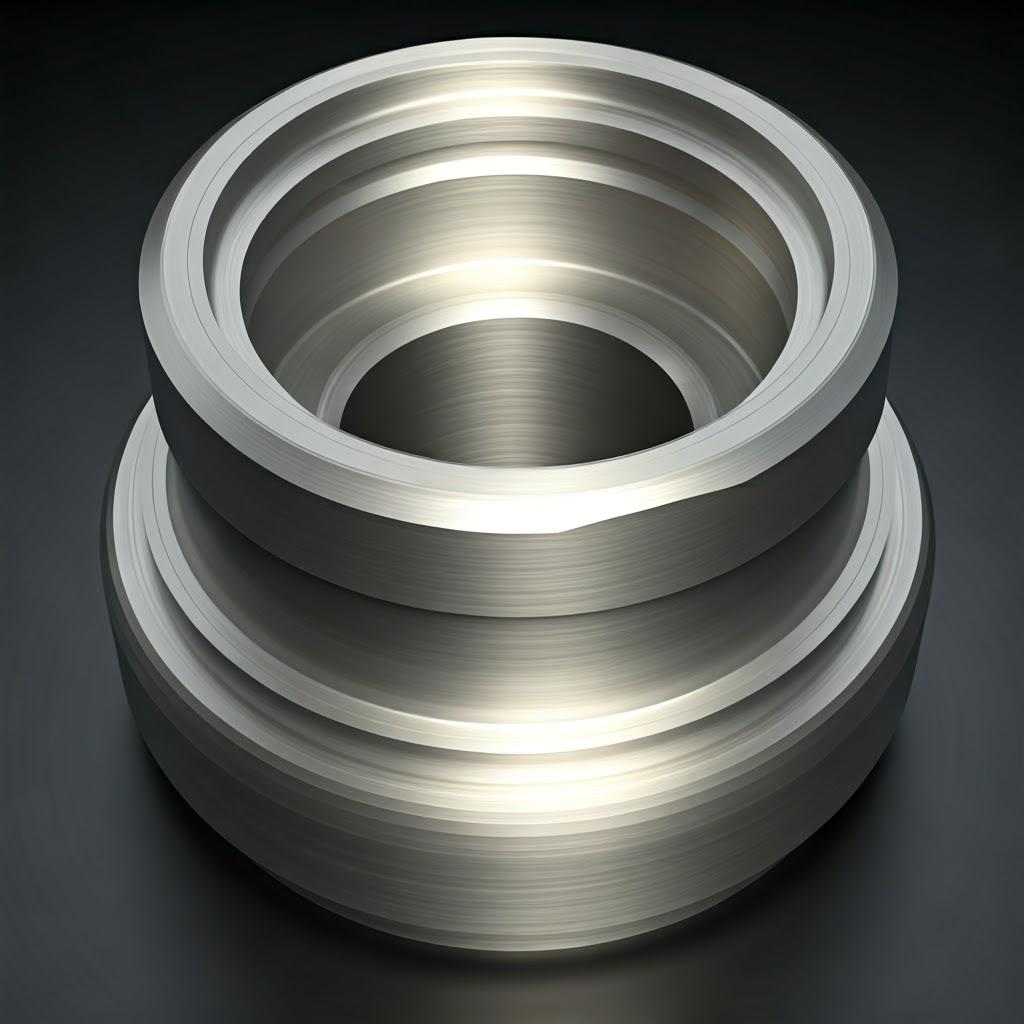
The Additive Advantage: Why Use Metal 3D Printing for Aerospace Spacers?
While traditional manufacturing methods like CNC machining have long been the standard for producing aerospace spacers, metal additive manufacturing offers compelling advantages, particularly for complex, custom, or low-to-medium volume parts. These benefits address key challenges faced by aerospace engineers and procurement professionals, including cost reduction, lead time compression, performance enhancement, and supply chain optimization. Understanding these advantages is crucial for deciding when and why to adopt 3D-utskrift av metall for spacer production.
Comparison: Metal AM vs. Traditional Machining for Spacers
Funktion | Metal Additive Manufacturing (e.g., SLM, EBM) | Traditionell CNC-bearbetning | Key Advantage of AM for Spacers |
---|---|---|---|
Geometrisk komplexitet | High (Internal channels, lattices, organic shapes feasible) | Moderate to High (Limited by tool access, setup complexity) | Enables highly optimized, lightweight designs & part consolidation impossible with machining. |
Material Avfall | Low (Powder reused) | High (Material removed from stock billet) | Significant cost savings for expensive aerospace materials (Ti, Inconel); more sustainable. |
Lead Time (Custom) | Short (No tooling required, direct from CAD) | Moderate to Long (Requires fixtures, programming) | Faster iteration, quicker delivery for urgent needs (AOG) & development cycles. |
Verktygskostnader | Ingen | High (Fixtures, specialized tools) | Economical for low-volume production, prototypes, and highly customized parts. |
Konsolidering av delar | High Potential | Low Potential | Reduces part count, assembly time, weight, and potential failure points by integrating spacers. |
Lättvikt | Excellent (Topology optimization, lattices) | Limited (Primarily pocketing) | Critical for aerospace fuel efficiency and payload capacity; AM enables optimal structures. |
Material lämplighet | Growing range of aerospace alloys (Ti, Ni, Al, Steel) | Wide range of machinable metals | Optimized powders (like those from Met3dp) ensure high-quality AM parts in key aerospace materials. |
Minsta antal för beställning | Low (Economical for single parts) | Higher (Setup costs favor larger batches) | Ideal for bespoke designs, replacement parts, and initial production runs. |
Export to Sheets
Key Benefits Driving AM Adoption for Spacers:
- Oöverträffad designfrihet: AM liberates designers from the constraints of traditional manufacturing. Spacers can be designed with complex internal structures for weight reduction (using topology optimization or lattice structures) without compromising strength. Features like integrated cooling channels or specific vibration damping geometries become feasible.
- Significant Lightweighting Opportunities: Weight is a critical factor in aerospace. Metal AM allows for the creation of spacers that are significantly lighter than their machined counterparts while meeting or exceeding structural requirements. This translates directly to fuel savings, increased payload capacity, or improved performance.
- Reduced Material Waste & Cost: Aerospace materials like Ti-6Al-4V are expensive. Machining can generate substantial waste (up to 80-90% for complex parts). AM processes like powder bed fusion utilize material far more efficiently, melting only the powder needed for the part and supports, with unused powder largely recyclable. This significantly reduces the ‘buy-to-fly’ ratio and lowers material costs, a key consideration for procurement teams.
- Accelerated Development and Production: Bypassing the need for custom tooling (jigs, fixtures) dramatically shortens lead times, especially for new or custom spacer designs. Prototypes can be produced and tested quickly, accelerating the design iteration cycle. For urgent MRO (Maintenance, Repair, Overhaul) needs or low-volume production runs, AM offers much faster turnaround times compared to setting up a traditional machining process.
- Supply Chain Simplification: AM enables on-demand production closer to the point of need, potentially reducing reliance on complex global supply chains and minimizing inventory holding costs. Spare parts, including custom spacers, can be printed as needed.
- Del Konsolidering: In some cases, the function of a spacer and adjacent components can be combined into a single, more complex 3D printed part. This reduces the total number of parts in an assembly, simplifying logistics, minimizing assembly time and labor, and eliminating potential failure points at joints.
Met3dp leverages cutting-edge Tryckmetoder like Selective Electron Beam Melting (SEBM) and Selective Laser Melting (SLM), which are particularly well-suited for processing reactive materials like Titanium alloys commonly used in aerospace. Our printers boast industry-leading build volumes, accuracy, and reliability, ensuring that the theoretical advantages of AM translate into tangible benefits for mission-critical components like aerospace spacers. By partnering with an experienced provider like Met3dp, aerospace companies can confidently harness the additive advantage for their spacer requirements.
Material Matters: Recommended Powders (Ti-6Al-4V & 17-4PH) for Optimal Performance
The choice of material is fundamental to the performance and reliability of any aerospace component, and spacers are no exception. Metal 3D printing offers the capability to work with high-performance alloys that meet the demanding requirements of the aerospace environment. For spacers, two materials frequently stand out due to their excellent balance of properties: Titanium alloy Ti-6Al-4V (Grade 5) och precipitation-hardening stainless steel 17-4PH. Understanding their characteristics is key to selecting the right material for a specific spacer application.
Ti-6Al-4V (Grade 5 Titanium): The Aerospace Workhorse
Ti-6Al-4V is arguably the most widely used titanium alloy in aerospace, renowned for its exceptional strength-to-weight ratio, excellent corrosion resistance, and good performance at moderately elevated temperatures.
- Viktiga egenskaper:
- Högt förhållande mellan styrka och vikt: Significantly lighter than steel (approx. 40-50%) but offers comparable or superior strength, making it ideal for weight-critical applications.
- Utmärkt korrosionsbeständighet: Forms a stable, passive oxide layer providing outstanding resistance to corrosive environments, including saltwater, industrial chemicals, and oxidizing acids.
- Good High-Temperature Capability: Maintains useful strength up to approximately 315∘C (600∘F), suitable for many airframe and engine component applications.
- Biokompatibilitet: While less relevant for most spacers, its biocompatibility makes it suitable for certain specialized aerospace applications involving human factors or specific environmental controls.
- Good Fatigue Strength: Performs well under cyclic loading conditions common in aircraft structures.
- Why Use It for Spacers?
- Lättvikt: Primary driver; reduces overall aircraft weight.
- Corrosion Prevention: Ideal for spacers used in external locations, near dissimilar metals (reducing galvanic corrosion potential), or in humid/corrosive environments.
- Moderate Temperature Applications: Suitable for spacers near engines or other heat sources within its operating range.
- Structural Alignment: Its high stiffness ensures accurate maintenance of gaps and alignment under load.
17-4PH Stainless Steel: Strength, Hardness, and Corrosion Resistance
17-4PH is a chromium-nickel-copper precipitation-hardening stainless steel known for its high strength, hardness, good corrosion resistance (comparable to 304 stainless steel in many environments), and excellent mechanical properties that can be tailored through heat treatment.
- Viktiga egenskaper:
- Hög hållfasthet och hårdhet: Achieves high tensile and yield strength after appropriate heat treatment (e.g., Condition H900), making it suitable for high-load applications.
- God korrosionsbeständighet: Offers better corrosion resistance than standard martensitic stainless steels (like 410) and is suitable for many atmospheric and chemical environments.
- Good Toughness: Maintains reasonable toughness even at high strength levels.
- Moderate Temperature Capability: Can be used up to around 315∘C (600∘F), similar to Ti-6Al-4V, though strength decreases more significantly at the upper end.
- Magnetisk: It is ferromagnetic.
- Why Use It for Spacers?
- High Load Applications: Ideal for spacers subjected to significant compressive or shear loads where high strength and hardness are paramount (e.g., under large fasteners, in landing gear).
- Kostnadseffektivitet: Generally less expensive than Titanium alloys, making it a good choice when the extreme lightweighting of Ti-6Al-4V is not the primary driver.
- Motståndskraft mot slitage: Its hardness provides good resistance to wear and galling in certain applications.
- Kompatibilitet: Often used when interfacing with other steel components.
Material Property Comparison (Typical Values for AM Parts, Post-Processed):
Fastighet | Ti-6Al-4V (Annealed) | 17-4PH (H900 Heat Treat) | Enhet | Anteckningar |
---|---|---|---|---|
Täthet | ≈4.43 | ≈7.75−7.80 | g/cm3 | Ti-6Al-4V is significantly lighter. |
Slutlig draghållfasthet | ≈950−1100 | ≈1310−1450 | MPa | 17-4PH (H900) is typically stronger. |
Utbyteshållfasthet (0,2%) | ≈830−1000 | ≈1170−1300 | MPa | 17-4PH (H900) has higher yield strength. |
Töjning vid brott | ≈10−18 | ≈10−16 | % | Similar ductility range. |
Hårdhet | ≈30−36 | ≈40−45 | HRC | 17-4PH (H900) is harder. |
Max driftstemperatur | ≈315 (600) | ≈315 (600) | ∘C (∘F) | Similar upper limits, check specific data. |
Motståndskraft mot korrosion | Utmärkt | Bra | – | Ti-6Al-4V generally superior. |
Export to Sheets
Met3dp’s Material Advantage:
Choosing the right material is only part of the equation; the quality of the metal powder used for 3D printing is equally critical. Met3dp excels in this area. We employ branschledande gasatomisering och PREP-teknik to produce highly spherical metal powders with controlled particle size distribution and excellent flowability. This ensures:
- High Density Parts: Minimizing porosity and achieving near-full theoretical density for superior mechanical properties.
- Konsekvent kvalitet: Batch-to-batch consistency crucial for aerospace applications.
- Optimal Printability: Powders designed to perform reliably in SLM and SEBM processes.
Vår Produkt portfolio includes optimized Ti-6Al-4V and 17-4PH powders, alongside other innovative alloys like TiNi, TiTa, CoCrMo, and various superalloys suitable for demanding environments. By utilizing Met3dp’s high-quality powders and advanced printing systems, aerospace companies can confidently manufacture custom spacers that meet stringent performance and reliability requirements using these exceptional materials. Consulting with our material science experts can help select the optimal powder and processing parameters for your specific spacer application, ensuring you leverage the full potential of these advanced alloys.

Design for Additive Manufacturing (DfAM): Optimizing Spacer Geometry
Simply replicating a traditionally designed spacer using metal 3D printing often fails to capitalize on the full potential of additive manufacturing. To truly leverage the benefits of AM – lightweighting, improved performance, and cost-effectiveness – components must be designed för the process. Design for Additive Manufacturing (DfAM) principles are crucial when developing custom aerospace spacers intended for 3D printing. Applying DfAM ensures better printability, reduces the need for extensive support structures, minimizes post-processing efforts, and unlocks performance gains unattainable with conventional designs.
Here are key DfAM considerations for aerospace spacers:
1. Rethink Traditional Design Constraints:
- Embrace Complexity: Unlike machining, complexity in AM doesn’t necessarily equate to significantly higher cost. Consider incorporating features that improve function but were previously too difficult to machine, such as:
- Internal Lattices: Replace solid material with optimized lattice structures (e.g., gyroids, octet trusses) to drastically reduce weight while maintaining required stiffness and strength. Software tools can generate these based on load cases.
- Conformal Channels: Integrate internal channels that follow the spacer’s contours for potential cooling, fluid passage, or housing sensors/wiring, consolidating functions.
- Organic Shapes: Smooth, curved, and topology-optimized shapes are easily produced, allowing for designs that follow stress paths more naturally, improving fatigue life.
2. Minimize Support Structures: Support structures are often necessary in powder bed fusion processes (like SLM and SEBM) to anchor the part to the build plate, support overhanging features, and dissipate heat. However, they consume extra material, increase print time, and require manual removal, adding cost and potentially affecting surface finish.
- Self-Supporting Angles: Design features with angles typically greater than 45 degrees relative to the build plate to minimize the need for supports. Orienting the spacer optimally on the build platform during print preparation is also critical.
- Incorporate Fillets and Chamfers: Smooth transitions between features and avoid sharp overhangs. Replace horizontal overhangs with chamfered or filleted edges where possible.
- Design-In Supports: For features requiring support, consider designing them as integral, easily removable elements rather than relying solely on software-generated lattice supports.
- Bridging: Understand the bridging capabilities of the chosen machine/material system – the maximum horizontal distance the printer can span without supports. Design small gaps or channels accordingly.
3. Optimize Wall Thickness and Feature Sizes: AM processes have limitations on minimum feature sizes and wall thicknesses they can reliably produce.
- Minimum Wall Thickness: Ensure walls are thick enough to print reliably and withstand handling and operational loads. This varies by material and machine but is often in the range of $0.4$mm to $1.0$mm. Extremely thin walls can warp or fail during printing.
- Hole Diameters: Small holes (typically < 6-$8$mm, depending on orientation and depth) may print slightly undersized or with rougher internal surfaces due to melt pool dynamics and powder adhesion. Design holes slightly oversized if tight tolerance is needed as-printed, or plan for post-machining (reaming, drilling). Horizontal holes generally require support or should be designed as teardrop or diamond shapes to be self-supporting.
- Aspect Ratios: Tall, thin features can be prone to vibration or distortion during printing. Consider adding temporary bracing or optimizing the design/orientation if high aspect ratios are unavoidable.
4. Consider Powder Removal: For spacers with internal channels or complex hollow features, ensuring complete removal of unfused powder after printing is critical. Trapped powder adds weight and can pose a risk if dislodged during operation.
- Design Escape Holes: Incorporate sufficiently large openings (escape holes) in strategic locations to allow unfused powder to be easily removed via vibration, compressed air, or flushing.
- Avoid Powder Traps: Design internal geometries to be smooth and free-flowing, avoiding sharp internal corners or dead ends where powder can become trapped.
- Simulation: Use simulation tools to predict powder removal challenges early in the design phase.
5. Leverage Topology Optimization and Generative Design: These powerful software tools use algorithms to optimize material distribution based on defined load cases, constraints, and target weight reductions.
- Topology Optimization: Starts with a basic design space and removes material where it’s not needed, resulting in often organic-looking, highly efficient structures. Ideal for lightweighting spacers while maintaining stiffness.
- Generative Design: Explores multiple design solutions based on functional requirements and constraints, offering novel and high-performing options that a human designer might not conceive.
Applying these DfAM principles requires a shift in mindset from traditional design practices. Collaborating closely with an experienced AM service provider like Met3dp early in the design phase is highly recommended. Our engineers possess deep expertise in DfAM and can provide valuable feedback to optimize your spacer design for printability, performance, and cost-effectiveness, ensuring you harness the full additive advantage.
Achieving Precision: Tolerance, Surface Finish, and Dimensional Accuracy in 3D Printed Spacers
Aerospace applications demand high levels of precision. Spacers, despite their apparent simplicity, often have tight tolerances on critical dimensions like thickness, parallelism, flatness, and hole diameters/positions to ensure correct assembly fit and function. While metal 3D printing technology has advanced significantly, understanding the achievable levels of tolerance, surface finish, and dimensional accuracy is crucial for setting realistic expectations and planning necessary post-processing steps.
Tolerances:
- As-Printed Tolerances: The tolerances achievable directly from the printer depend on several factors, including the specific AM process (SLM, EBM), machine calibration, material properties, part size and geometry, and build orientation.
- Typical Values: General tolerances for well-calibrated systems are often cited in the range of $\pm 0.1$mm to $\pm 0.2$mm for smaller dimensions (e.g., up to 100mm), with potentially larger deviations (±0.1% to ±0.2% of the dimension) for larger parts.
- Process Differences: SEBM (Selective Electron Beam Melting), often used by Met3dp for materials like Ti-6Al-4V, operates at higher temperatures, which can help reduce residual stress but may sometimes result in slightly looser as-printed tolerances compared to SLM (Selective Laser Melting). However, both processes can achieve high accuracy.
- Factors Influencing Tolerance: Thermal stresses during printing and cooling, layer thickness, beam spot size, powder characteristics, and support strategy all play a role. Shrinkage during cooling and stress relief heat treatments must also be accounted for.
- Critical Tolerances: For features requiring tolerances tighter than the typical as-printed capabilities (e.g., mating surfaces, precise hole diameters), post-machining (CNC milling, turning, grinding) is usually necessary.
Surface Finish (Roughness):
- As-Printed Surface Finish: Metal AM parts inherently have a rougher surface finish compared to machined components due to the layer-by-layer process and partially melted powder particles adhering to surfaces.
- Typical Values (Ra): As-printed surface roughness (Ra) typically ranges from 5μm to 25μm (200μin to 1000μin), depending heavily on the orientation of the surface relative to the build direction, material, layer thickness, and process parameters. Downward-facing surfaces supported by structures tend to be rougher.
- Internal Surfaces: Internal channels and complex features often have higher roughness values and can be challenging to finish.
- Förbättra ytfinishen: Post-processing is essential for achieving smoother surfaces required for sealing, wear resistance, fatigue performance, or aesthetics. Common methods include:
- Bead Blasting / Shot Peening: Improves uniformity and removes loose particles, typically achieving Ra 3μm−10μm. Shot peening can also induce beneficial compressive stresses.
- Tumbling / Vibratory Finishing: Effective for smoothing external surfaces and deburring edges on batches of smaller parts.
- CNC Machining: Provides the best surface finish on specific features, achieving Ra <1μm.
- Polering: Manual or automated polishing can achieve very smooth, mirror-like finishes (Ra <0.1μm) if required.
Dimensionell noggrannhet:
Dimensional accuracy refers to how closely the final part conforms to the nominal dimensions specified in the CAD model. It is closely related to tolerance but also encompasses form errors like flatness, parallelism, and circularity.
- Achieving Accuracy: Requires careful process control, machine calibration, thermal management simulation (to predict and compensate for distortion), appropriate support strategies, and controlled post-processing (especially stress relief and machining).
- Metrology and Inspection: Rigorous quality control using CMM (Coordinate Measuring Machines), 3D scanning, and other metrology tools is essential to verify that the final spacer meets all dimensional specifications. Aerospace applications demand thorough inspection and documentation.
Managing Expectations:
It’s vital for designers and procurement managers to understand that achieving the tightest aerospace tolerances and finest surface finishes with metal AM typically involves a combination of precise printing and targeted post-processing. Communicating critical dimensions and surface requirements clearly to the AM service provider early in the project is essential. Experienced providers like Met3dp utilize advanced simulation tools, meticulous process control, and integrated post-processing capabilities to deliver custom aerospace spacers that meet demanding precision requirements reliably.
Tolerance and Surface Finish Summary:
Parameter | As-Printed (Typical) | Post-Processed (Typical Range) | Method for Improvement |
---|---|---|---|
Tolerans | ±0.1 to ±0.2 mm / ±0.1−0.2% | <±0.01 to ±0.05 mm (Machined) | CNC Machining, Grinding |
Ytjämnhet (Ra) | 5−25μm | 1−10μm (Blasted/Tumbled) | Bead Blasting, Tumbling, Polishing, Machining |
<1μm (Machined/Polished) | |||
Flatness/Parallelism | Dependent on size/orientation | High (via Machining/Grinding) | Machining, Lapping, Grinding |
Export to Sheets
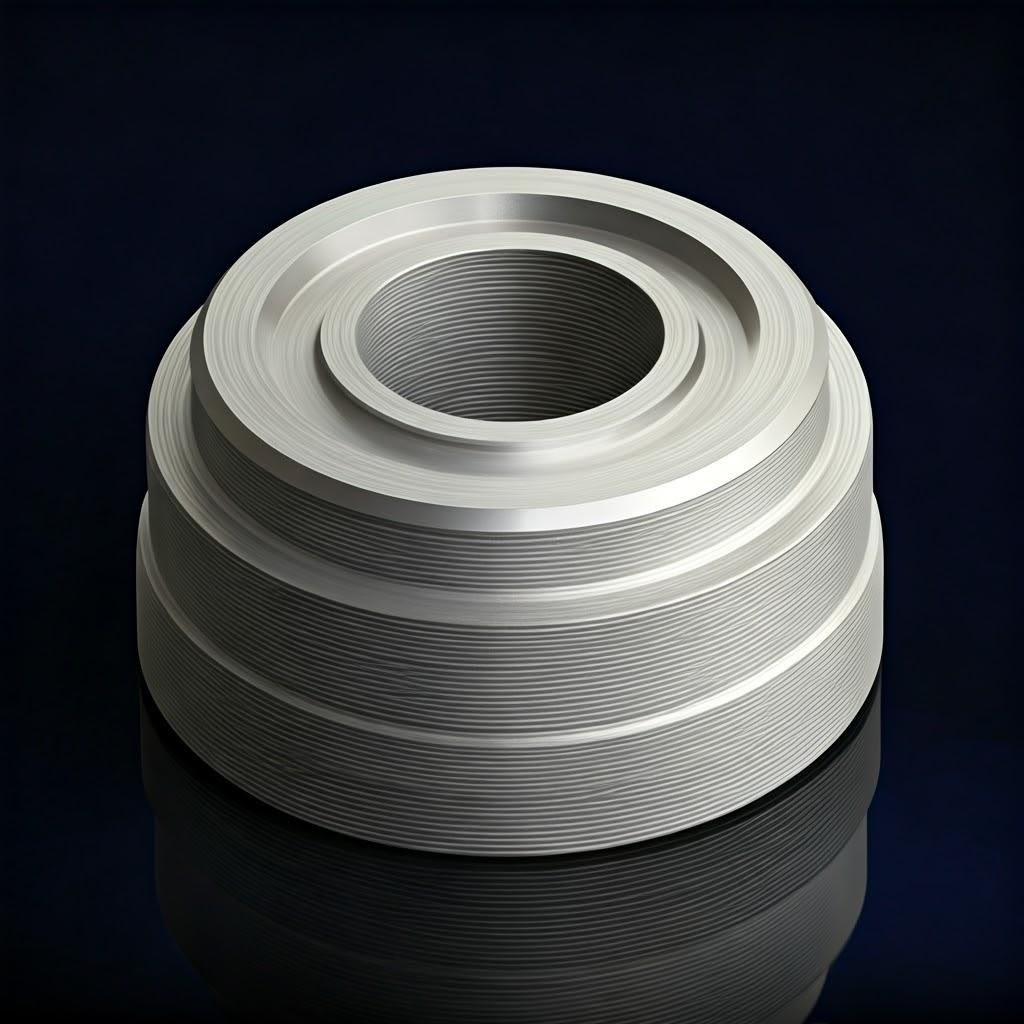
Beyond Printing: Essential Post-Processing Steps for Aerospace Spacers
The journey of a 3D printed metal aerospace spacer doesn’t end when it comes off the build plate. A series of crucial post-processing steps are typically required to transform the as-printed part into a flight-ready component that meets stringent aerospace standards for mechanical properties, dimensional accuracy, surface quality, and safety. Understanding these steps is vital for project planning, cost estimation, and selecting a capable manufacturing partner.
Common Post-Processing Workflow for AM Aerospace Spacers:
- De-powdering:
- Process: Carefully removing all unfused metal powder from the part and the build chamber, especially from internal channels and complex geometries. This is often done using brushes, vacuum systems, compressed air, and vibration.
- Importance: Ensures no loose powder remains, which could add weight, compromise performance, or become contamination. Critical for parts with internal features.
- Stressavlastning:
- Process: Heating the part (often while still attached to the build plate) in a controlled atmosphere furnace to a specific temperature below the material’s transformation point, holding it, and then cooling slowly.
- Importance: Reduces internal stresses built up during the rapid heating and cooling cycles of the printing process. Minimizes the risk of distortion or cracking during subsequent steps (like removal from the build plate) or later in service. Essential for dimensional stability.
- Part Removal from Build Plate:
- Process: Separating the printed spacer(s) from the build plate. This is typically done using wire EDM (Electrical Discharge Machining), sawing, or machining.
- Importance: Careful removal is needed to avoid damaging the part. The method depends on the part geometry, material, and support strategy.
- Borttagning av stödstruktur:
- Process: Removing the temporary support structures generated during printing. This can involve manual breaking/clipping (for easily accessible supports), machining, grinding, or EDM.
- Importance: Supports are non-functional and must be removed completely. This step requires care to avoid damaging the part surface and can be labor-intensive for complex geometries. DfAM plays a key role in minimizing support needs.
- Heat Treatment (Solution Annealing, Aging, HIP):
- Process: Specific heat treatment cycles tailored to the material (Ti-6Al-4V, 17-4PH) to achieve the desired final mechanical properties (strength, ductility, hardness, fatigue life).
- Solution Annealing & Aging (e.g., for 17-4PH): Dissolves precipitates and then reforms them in a controlled manner to achieve specific strength levels (e.g., H900, H1025).
- Annealing (e.g., for Ti-6Al-4V): Improves ductility and fracture toughness.
- Het isostatisk pressning (HIP): A crucial step for many critical aerospace parts. Involves applying high temperature and high inert gas pressure (Argon) simultaneously.
- Importance:
- Homogenizes Microstructure: Refines the grain structure formed during printing.
- Optimizes Mechanical Properties: Ensures the material meets engineering specifications.
- Closes Internal Porosity (HIP): HIP effectively eliminates residual internal micro-porosity, significantly improving fatigue life, fracture toughness, and overall material integrity – often mandatory for critical aerospace components. Met3dp recommends and can facilitate HIP for demanding applications.
- Process: Specific heat treatment cycles tailored to the material (Ti-6Al-4V, 17-4PH) to achieve the desired final mechanical properties (strength, ductility, hardness, fatigue life).
- Machining (for Critical Tolerances & Features):
- Process: Using CNC milling, turning, grinding, or drilling to achieve final dimensions, tolerances, and surface finishes on specific features that cannot be adequately produced by the AM process alone.
- Importance: Guarantees precision for mating surfaces, bearing interfaces, fastener holes, sealing surfaces, etc. Essential for meeting tight aerospace drawing specifications.
- Ytbehandling:
- Process: Improving the surface quality and removing any marks from support removal or handling. Methods include bead blasting, shot peening, tumbling, polishing, electropolishing, or specialized treatments.
- Importance: Achieves required surface roughness (Ra), improves fatigue performance (shot peening induces compressive stress), ensures cleanability, enhances aesthetics, or prepares the surface for subsequent coatings.
- Cleaning and Inspection:
- Process: Final cleaning to remove any machining fluids, blasting media, or contaminants. Followed by rigorous inspection using techniques like CMM, 3D scanning, visual inspection, NDT (Non-Destructive Testing – e.g., CT scanning for internal integrity, FPI/MPI for surface flaws) as required by aerospace standards.
- Importance: Verifies that the final spacer meets all dimensional, material, and quality requirements before delivery and installation.
The specific sequence and combination of these post-processing steps depend heavily on the spacer’s design complexity, material choice, and application requirements. Partnering with a full-service provider like Met3dp, which has expertise and capabilities (or established partnerships) across the entire workflow from printing to final finishing and inspection, streamlines the process and ensures end-to-end quality control crucial for aerospace procurement.
Navigating Challenges: Common Pitfalls in Metal AM for Spacers and Solutions
While metal additive manufacturing offers significant advantages for producing aerospace spacers, it’s not without its challenges. Understanding potential pitfalls and how experienced providers address them is crucial for ensuring successful outcomes and reliable parts. Awareness helps designers optimize their parts and procurement managers ask the right questions when selecting a supplier.
Common Challenges and Mitigation Strategies:
- Warping and Distortion:
- Utmaning: Uneven heating and cooling during printing induce internal stresses, which can cause the part to warp or distort, especially for large or geometrically complex spacers.
- Solutions:
- Thermal Simulation: Using software to predict stress buildup and distortion, allowing for design adjustments or optimized build orientation and support strategies.
- Optimized Support Structures: Strategically placed supports anchor the part and help manage heat dissipation.
- Process Parameter Control: Fine-tuning laser/electron beam power, scan speed, and layer thickness to minimize thermal gradients.
- Stress Relief Cycles: Implementing appropriate stress relief heat treatments immediately after printing.
- Build Plate Heating: Maintaining an elevated, consistent temperature on the build plate (common in SEBM) reduces thermal gradients.
- Återstående stress:
- Utmaning: Even if warping is controlled, significant residual stress can remain locked within the part, potentially impacting fatigue life, dimensional stability over time, or leading to cracking during post-processing or service.
- Solutions:
- Effective Stress Relief: Performing proper thermal stress relief cycles is paramount.
- Het isostatisk pressning (HIP): HIP is highly effective at relieving residual stresses while also closing porosity.
- Optimized Scan Strategies: Using specific laser/beam scanning patterns (e.g., island scanning, alternating directions) can help mitigate stress accumulation.
- Designöverväganden: Avoiding large variations in cross-sectional area and incorporating fillets can help manage stress concentrations.
- Porositet:
- Utmaning: Small voids or pores can form within the printed material due to trapped gas, incomplete fusion between layers, or powder inconsistencies. Porosity degrades mechanical properties, especially fatigue strength.
- Solutions:
- High-Quality Powder: Using powders with high sphericity, controlled particle size distribution, and low internal gas content (like those produced by Met3dp’s advanced atomization). Proper powder handling and storage are also critical.
- Optimized Process Parameters: Dialing in energy density (beam power, speed, hatch spacing) to ensure complete melting and fusion.
- Inert Atmosphere Control: Maintaining a high-purity inert gas environment (Argon or Nitrogen for SLM, Vacuum for EBM) to prevent oxidation and gas entrapment.
- Het isostatisk pressning (HIP): The most effective method for eliminating internal porosity in critical parts.
- Support Removal Difficulties:
- Utmaning: Supports in hard-to-reach areas or on complex surfaces can be difficult and time-consuming to remove without damaging the part’s surface. Residual “witness marks” from supports can affect surface finish.
- Solutions:
- DfAM: Designing parts to be self-supporting as much as possible is the best solution.
- Optimized Support Design: Using specialized support structures (e.g., thin, easily breakable interfaces, tree supports) generated by advanced software.
- Strategic Orientation: Choosing a build orientation that minimizes the need for supports on critical surfaces.
- Tekniker för efterbearbetning: Utilizing appropriate tools and techniques (machining, grinding, blending) for clean removal and surface restoration.
- Surface Finish Consistency:
- Utmaning: Achieving a uniform surface finish across all areas of a complex spacer can be difficult, as roughness varies with surface orientation relative to the build direction.
- Solutions:
- Targeted Post-Processing: Applying appropriate finishing techniques (blasting, tumbling, polishing) based on requirements. Critical surfaces may require machining.
- Bygg orientering: Optimizing orientation can help prioritize finish quality on key surfaces.
- Process Parameter Tuning: Fine-tuning parameters can sometimes influence surface quality, though post-processing is usually the primary method for achieving specific finishes.
- Powder Removal from Internal Features:
- Utmaning: Ensuring complete removal of unfused powder from intricate internal channels or cavities.
- Solutions:
- DfAM: Designing adequate escape holes and smooth internal pathways.
- Thorough Cleaning Procedures: Employing multi-step cleaning processes involving vibration, ultrasonic baths, compressed air, and sometimes solvent flushing.
- Inspection: Using borescopes or CT scanning (for critical parts) to verify complete powder removal.
Successfully navigating these challenges requires a deep understanding of materials science, AM process physics, thermal dynamics, and meticulous process control. This is where partnering with an established expert like Met3dp becomes invaluable. Our decades of collective expertise in metal additive manufacturing, combined with our advanced SEBM printers, high-quality powder production, and robust quality management systems, allow us to anticipate and mitigate these challenges effectively, delivering reliable, high-performance aerospace spacers that meet the toughest industry standards.
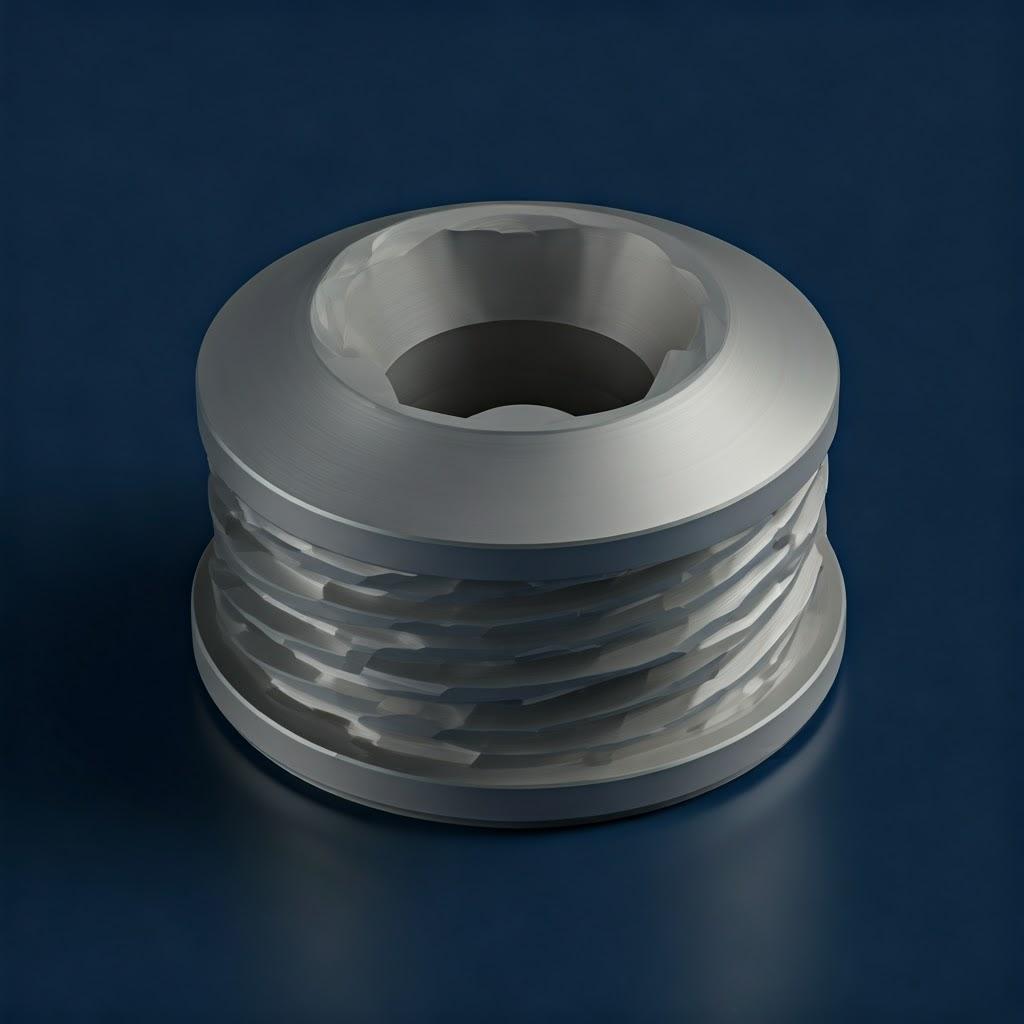
Supplier Selection: How to Choose the Right Metal 3D Printing Service Partner
Selecting the right manufacturing partner is as critical as the technology itself, especially in the aerospace industry where quality, reliability, and traceability are paramount. Not all metal 3D printing service providers are equipped to handle the stringent demands of aerospace component manufacturing. Procurement managers and engineers need a systematic approach to evaluate potential suppliers for custom aerospace spacers.
Key Criteria for Evaluating Metal AM Suppliers:
- Aerospace Certifications and Quality Management System (QMS):
- Requirement: Look for suppliers with relevant aerospace certifications, primarily AS9100. This certification demonstrates a robust QMS tailored to the specific requirements of the aviation, space, and defense industries. ISO 9001 is a baseline, but AS9100 indicates a higher level of process control, traceability, and risk management.
- Verification: Ask for proof of certification and inquire about their quality manual, process control documentation, and lot traceability procedures.
- Material Expertise and Handling:
- Requirement: The supplier must have proven experience working with the specific aerospace alloys required (e.g., Ti-6Al-4V, 17-4PH, Inconels). This includes understanding their unique printing characteristics, required post-processing (especially heat treatments like HIP), and proper handling protocols to prevent contamination.
- Verification: Discuss their experience with your chosen material, review case studies or examples of similar parts they’ve produced, and inquire about their powder sourcing, testing, handling, and recycling procedures. Ensure they maintain material batch traceability.
- Technology and Equipment:
- Requirement: Assess whether their printer fleet (e.g., SLM, SEBM) is suitable for your material and part requirements (size, complexity, accuracy). Ensure they have well-maintained, calibrated industrial-grade machines. Access to necessary post-processing equipment (heat treatment furnaces, HIP units, CNC machines, finishing tools, metrology labs) is also crucial, either in-house or through qualified partners.
- Verification: Inquire about their specific machine models, build envelope sizes, maintenance schedules, and calibration procedures. Ask about their in-house vs. outsourced post-processing capabilities.
- Technical Expertise and Engineering Support:
- Requirement: The ideal partner acts as more than just a print bureau. Look for suppliers with experienced engineers and metallurgists who can provide DfAM support, advise on material selection, optimize print orientation and parameters, and troubleshoot potential issues.
- Verification: Discuss your project requirements with their technical team. Gauge their understanding of aerospace challenges and their willingness to collaborate on design optimization. Ask about their team’s background and experience.
- Process Control and Repeatability:
- Requirement: Consistency is key. The supplier must demonstrate rigorous process monitoring and control throughout the entire workflow – from powder handling to printing, post-processing, and inspection – to ensure part-to-part repeatability.
- Verification: Inquire about their build monitoring systems (e.g., melt pool monitoring), data logging, parameter control, and statistical process control (SPC) methods if applicable.
- Inspection and Metrology Capabilities:
- Requirement: The supplier must possess the necessary equipment and expertise to perform thorough dimensional inspection (CMM, 3D scanning) and potentially NDT (Non-Destructive Testing like CT scanning, FPI) to verify part quality and conformance to specifications.
- Verification: Ask about their inspection equipment list, calibration standards, and reporting capabilities. Confirm they can provide required documentation (e.g., Certificates of Conformance, material certifications, dimensional inspection reports).
- Track Record and Reputation:
- Requirement: Look for suppliers with a proven history of successfully delivering high-quality parts for aerospace or similarly demanding industries.
- Verification: Request references, case studies, or testimonials from other aerospace clients. Evaluate their responsiveness, communication, and project management approach.
Why Consider Met3dp?
Met3dp embodies these critical supplier attributes. As a leading provider of additive manufacturing solutions specializing in industrial metal 3D printing, we offer:
- Avancerad teknik: We utilize industry-leading SEBM and SLM printers known for accuracy and reliability, complemented by sophisticated powder production via gas atomization and PREP.
- Materialkompetens: Our portfolio includes a wide range of high-quality metal powders, including aerospace-grade Ti-6Al-4V and 17-4PH, optimized for AM processes. You can learn more Om oss and our commitment to material science.
- Omfattande lösningar: With decades of collective expertise, we provide end-to-end support, from DfAM consultation and printing to post-processing coordination and quality assurance.
- Quality Focus: We are committed to rigorous quality control throughout the manufacturing process, ensuring parts meet demanding specifications. (While specific certifications like AS9100 should be confirmed directly based on current status, our focus aligns with industry best practices).
Choosing the right partner is an investment in quality and reliability. By carefully evaluating potential suppliers against these criteria, aerospace companies can confidently leverage metal AM for producing high-performance custom spacers.
Understanding Investment: Cost Factors and Lead Time for 3D Printed Aerospace Spacers
While metal 3D printing offers numerous advantages, understanding the factors that influence cost and lead time is essential for effective project planning and budgeting, especially for procurement professionals managing aerospace supply chains. Pricing for AM parts is typically more complex than traditional methods and depends on a combination of factors.
Key Cost Drivers for 3D Printed Spacers:
- Material Type and Volume:
- Materialkostnad: High-performance aerospace alloys like Ti-6Al-4V are inherently more expensive than standard steels like 17-4PH. The raw powder cost is a significant factor.
- Part Volume: The actual volume of material used to print the part directly impacts cost. Larger or solid spacers will cost more than smaller or lightweighted designs.
- Powder Reuse: While powder is largely reusable, factors like degradation over cycles and qualification processes add some overhead.
- Part Complexity and Design:
- Geometric Complexity: Highly intricate designs with features like internal lattices or conformal channels may require more sophisticated print strategies and potentially more support, slightly increasing print time and post-processing effort. However, complexity doesn’t scale cost as dramatically as in machining.
- Support Structure Volume: The amount of support material required increases print time and material usage, as well as post-processing labor for removal. Designs optimized using DfAM to minimize supports are more cost-effective.
- Print Time (Machine Time):
- Part Height (Z-Height): Print time is largely driven by the number of layers, meaning taller parts (oriented vertically) take longer to print than flatter parts covering the same area.
- Part Density on Build Plate: How many parts can be nested efficiently onto a single build plate influences machine time allocation per part. Higher nesting density generally reduces cost per part.
- Layer Thickness & Parameters: Thicker layers print faster but result in rougher surfaces and potentially reduced detail resolution. Finer layers increase print time.
- Krav på efterbearbetning:
- Heat Treatments: Stress relief is standard. More complex cycles like solution annealing, aging, or especially HIP add significant cost due to furnace time and specialized equipment requirements.
- Support Removal & Machining: Labor-intensive support removal for complex parts or extensive CNC machining for tight tolerances are major cost contributors.
- Ytbehandling: The level of finish required (e.g., simple bead blast vs. multi-stage polishing) impacts labor and processing time.
- Quality Assurance and Inspection:
- Inspection Level: Basic dimensional checks cost less than comprehensive CMM reports, NDT (CT, FPI), and full aerospace documentation packages. Requirements must be clearly specified.
- Order Volume (Quantity):
- Setup Costs: While AM avoids tooling costs, there are still setup costs associated with preparing the build file, loading the machine, and initial post-processing steps. These costs are amortized over the batch size.
- Bulk/Wholesale Pricing: Producing spacers in larger batches generally reduces the cost per part compared to printing single pieces or very small quantities. Discuss volume discounts with your supplier.
Typical Lead Times:
Lead time for 3D printed aerospace spacers can vary significantly based on the factors above, as well as the supplier’s current capacity.
- Snabb prototypframtagning: Simple spacers with minimal post-processing might be delivered in 1-2 veckor.
- Production Parts (Standard Post-Processing): Parts requiring stress relief, support removal, basic finishing, and standard inspection typically take 3-6 veckor.
- Complex Parts (Extensive Post-Processing): Spacers requiring HIP, significant CNC machining, complex finishing, and rigorous NDT/inspection could have lead times of 6-10 weeks or longer.
Factors Influencing Lead Time:
- Print queue at the service provider.
- Complexity and duration of the printing process itself.
- Availability and scheduling of post-processing equipment (especially HIP and specialized machining).
- Required inspection level and documentation turnaround.
- Shipping logistics.
It is crucial to discuss specific requirements with the AM service provider to get an accurate quote and realistic lead time estimate. Providing a clear statement of work, including CAD models, material specifications, tolerance requirements, surface finish needs, and necessary certifications/documentation, will expedite the quoting process.
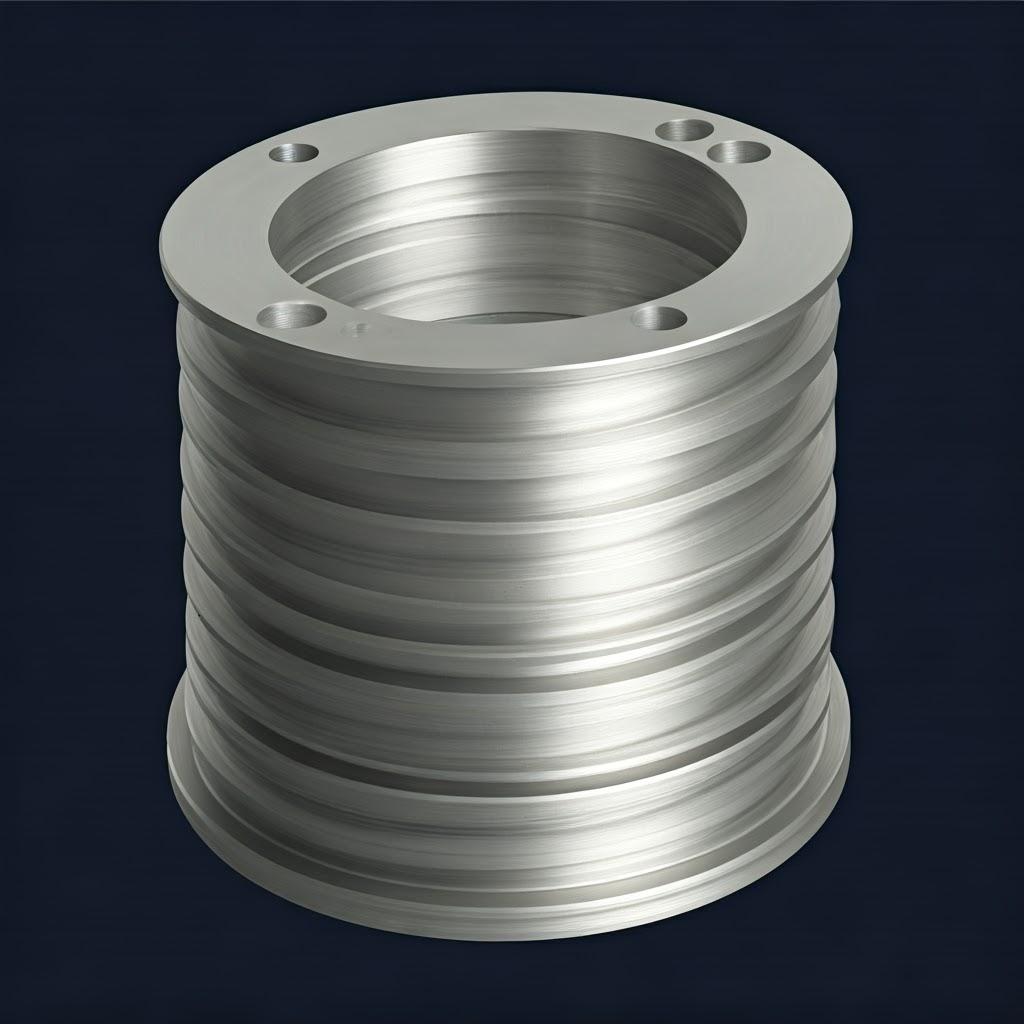
Frequently Asked Questions (FAQ) about 3D Printed Aerospace Spacers
Here are answers to some common questions engineers and procurement managers have about using metal AM for aerospace spacers:
1. What is the typical cost difference between 3D printing and CNC machining for custom aerospace spacers?
- There’s no single answer, as it depends heavily on complexity, material, and quantity.
- For simple spacers in high volumes: CNC machining is often more cost-effective due to established processes and faster cycle times per part once set up.
- For highly complex spacers (e.g., with internal lattices, conformal channels): 3D printing can be significantly cheaper, as these features are difficult or impossible to machine. The material savings from AM (especially with expensive alloys like Titanium) can also make it more competitive.
- For low volumes (prototypes, 1-100 parts): 3D printing is frequently more economical because it avoids the high upfront tooling and programming costs associated with CNC machining.
- Recommendation: Obtain quotes for both methods based on your specific design and quantity requirements for a direct comparison. Consider the total value proposition, including lead time and potential performance benefits (like lightweighting) offered by AM.
2. Can existing spacer designs originally made for machining be directly 3D printed?
- Technically, yes, an existing CAD model can be used to 3D print a spacer. However, this approach often fails to leverage the key advantages of AM. Directly printing a design optimized for machining might:
- Be unnecessarily heavy or bulky compared to an AM-optimized design.
- Require significant support structures that could have been minimized with DfAM.
- Not incorporate performance enhancements possible with AM (e.g., internal features).
- Potentially cost more to print and post-process than necessary.
- Recommendation: While direct printing is possible for quick replacements or initial tests, it’s highly recommended to review and potentially redesign existing spacers using DfAM principles to fully benefit from metal 3D printing’s capabilities, especially for production applications. Collaborating with AM experts like those at Met3dp during this redesign phase is beneficial.
3. What quality documentation is typically provided with 3D printed aerospace spacers?
- The level of documentation depends on the customer’s requirements and the criticality of the application. Common documents include:
- Certificate of Conformance (CoC): Stating that the parts meet the specified drawing requirements and standards.
- Material Certification: Traceability documents confirming the type, specification, and batch/lot number of the metal powder used. Chemical analysis reports for the powder batch may be included.
- Dimensional Inspection Report: Data showing measurements of critical dimensions, often from CMM or 3D scanning, compared against drawing tolerances.
- Heat Treatment Records: Charts or certifications verifying that stress relief, HIP, or other heat treatments were performed according to specified parameters.
- NDT Reports (if applicable): Results from any required Non-Destructive Testing (e.g., CT scan reports showing porosity analysis, FPI reports for surface defects).
- Requirement: Aerospace customers should clearly specify the required documentation package in their purchase order or statement of work. Reputable suppliers accustomed to serving the aerospace industry, like Met3dp, understand the importance of comprehensive documentation and traceability.
Conclusion: Elevate Your Aerospace Designs with Precision Metal 3D Printed Spacers
Custom aerospace spacers, though often small, are critical components where precision, material performance, and reliability are non-negotiable. Metal additive manufacturing has emerged as a powerful technology enabling the production of these vital parts with unprecedented advantages over traditional methods. By leveraging processes like Selective Laser Melting (SLM) and Selective Electron Beam Melting (SEBM), manufacturers can produce spacers from high-performance alloys like Ti-6Al-4V and 17-4PH, achieving:
- Tight Tolerances: Meeting demanding aerospace specifications through precise printing and targeted post-processing.
- Komplexa geometrier: Realizing intricate designs, internal features, and lightweight lattice structures impossible or impractical with machining.
- Optimized Performance: Utilizing topology optimization and advanced materials for superior strength-to-weight ratios and tailored functionality.
- Kortare ledtider: Accelerating prototyping and enabling faster delivery of custom and low-volume production parts without tooling constraints.
- Materialeffektivitet: Minimizing waste, especially with expensive aerospace alloys, contributing to cost savings and sustainability.
Successfully harnessing these benefits requires a combination of smart design (DfAM), careful material selection, controlled processing, meticulous post-processing, and rigorous quality assurance. Partnering with an expert metal AM provider is crucial for navigating the complexities and ensuring flight-ready components.
Met3dp stands ready to be that partner. With our advanced metal 3D printing systems, high-quality spherical metal powders produced in-house, comprehensive post-processing network, and deep expertise in aerospace applications, we provide end-to-end solutions for your custom spacer needs. We help you move beyond the limitations of traditional manufacturing and elevate your designs.
Ready to explore how metal 3D printing can optimize your custom aerospace spacers?
Contact Met3dp today to discuss your project requirements with our technical experts and discover how our capabilities can power your organization’s additive manufacturing goals.
Dela på
MET3DP Technology Co, LTD är en ledande leverantör av lösningar för additiv tillverkning med huvudkontor i Qingdao, Kina. Vårt företag är specialiserat på 3D-utskriftsutrustning och högpresterande metallpulver för industriella tillämpningar.
Förfrågan för att få bästa pris och anpassad lösning för ditt företag!
Relaterade artiklar
Om Met3DP
Senaste uppdateringen
Vår produkt
KONTAKTA OSS
Har du några frågor? Skicka oss meddelande nu! Vi kommer att betjäna din begäran med ett helt team efter att ha fått ditt meddelande.
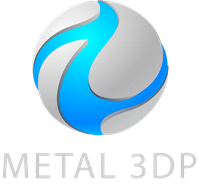
Metallpulver för 3D-printing och additiv tillverkning