Additiva tillverkningsmaterial av metall: Sammansättning, egenskaper, tillämpningar
Innehållsförteckning
Additiv tillverkning, also known as 3D printing, is revolutionizing manufacturing across industries from aerospace to medical devices. One key area of advancement is in metal 3D printing, which allows complex metal parts to be created directly from 3D CAD models without the need for expensive tooling or molds.
Metal additive manufacturing requires specialized equipment and materials to achieve the extreme temperatures needed to melt and fuse metal powders into solid objects. The most common metal 3D printing technologies used today are powder bed fusion, directed energy deposition, binder jetting, and sheet lamination.
The material properties of parts produced through metal 3D printing depend greatly on the composition and characteristics of the metal powders and alloys used. This article provides an overview of the most common metal additive manufacturing materials, their properties, applications, and suppliers.
Metal Additive Manufacturing Materials Types
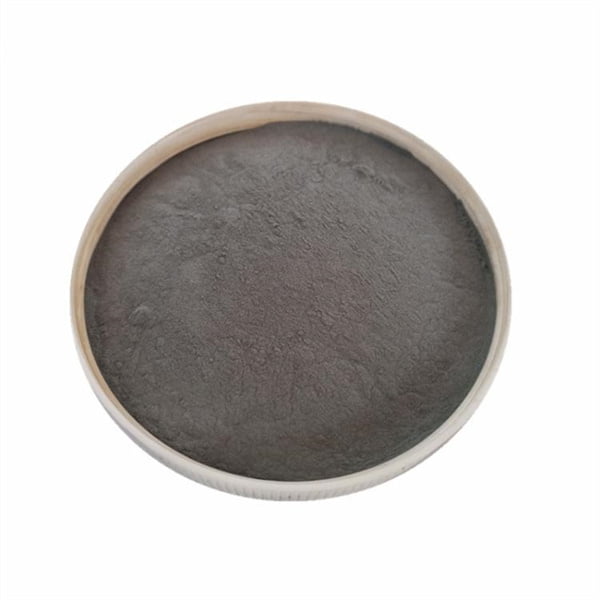
There are a wide range of metal alloys available for powder-based 3D printing. The most commonly used include:
Material | Beskrivning |
---|---|
Rostfria stål | Iron-based alloys with chromium, nickel, manganese, molybdenum, titanium, copper. Corrosion-resistant, high strength. |
Aluminiumlegeringar | Al-Si, Al-Si-Mg alloys. Low density, high thermal conductivity. |
Titanlegeringar | Ti-6Al-4V, Ti-6Al-4V ELI. Excellent strength-to-weight ratio, biocompatibility. |
Nickellegeringar | Inconel 625, 718. Heat and corrosion resistance. Used in aerospace components. |
Kobolt-krom | CoCrMo alloy. Biocompatible, high hardness. Used for dental implants and joints. |
Ädelmetaller | Gold, silver, platinum. Electrical conductivity, corrosion resistance, aesthetics. |
Verktygsstål | H13, maraging steel. High hardness, heat treatable. For tooling and molds. |
Kopparlegeringar | CuZn, bronze alloys. Electrical and thermal conductivity. |
These base materials can be blended and alloyed in various combinations to achieve specific material properties needed for different applications.
Metal Additive Manufacturing Materials Properties
The key properties of metal powders used in additive manufacturing include:
Fördelning av partikelstorlek
- Powder particle size is typically 15-45 microns for powder bed fusion.
- Smaller particles <15 microns improve density but reduce flowability.
- Larger particles >45 microns reduce precision and surface finish.
- Uniform size distribution allows optimal packing density.
Morphology and shape
- Spherical powder shape allows smooth flow and packing.
- Irregular shapes can cause poor bulk density and powder bed uniformity.
Flytbarhet
- Powders must spread evenly across the powder bed for uniform layers.
- Flowability determined by shape, size distribution, surface texture.
- Flow agents may be added to improve powder flow.
Täthet
- Higher packing density of powder leads to reduced porosity in printed parts.
- Apparent density typically 40-60% of true solid density.
- Tapped density indicates flow and packing efficiency.
Renhet
- High purity reduces defects and contamination.
- Oxygen, nitrogen levels kept below 100 ppm.
- Minimal satellites (small particles attached to larger ones).
Fukthalt
- Moisture can cause powder clumping and reduce flow.
- Moisture content kept below 0.02% by weight.
- Powders stored in vacuum or inert gas atmosphere.
In addition to powder characteristics, the composition and microstructure of the bulk metal alloys impart important performance properties to AM parts:
Styrka
- Yield strength 500 MPa to over 1 GPa depending on alloy.
- Heat treatment can increase strength through precipitation hardening.
Hårdhet
- Vickers hardness from 150 HV to over 400 HV.
- Hardness can be tailored locally through heat treatment.
Täthet
- Near full density >99% can be achieved.
- Residual porosity depends on process parameters.
Ytfinish
- As-printed surface is rough 10-25 microns Ra.
- Machining, grinding, polishing required for precision finish.
Utmattningshållfasthet
- Comparable to wrought materials but anisotropic.
- Depends on build orientation, internal defects.
Korrosionsbeständighet
- Varies significantly by alloy composition from low to very high.
Termiska egenskaper
- Conductivity and expansion coefficients close to wrought alloys.
- Depending on build orientation due to microstructure.
Elektrisk resistivitet
- Within 10-20% of wrought materials.
- Higher porosity increases resistivity.
By selecting optimized powders and alloys, metal AM enables the fabrication of dense parts with mechanical properties comparable to traditional manufacturing in many cases. However, properties remain anisotropic depending on build direction.
Metal Additive Manufacturing Materials Applications
The key applications taking advantage of metal additive manufacturing include:
Aerospace: Complex jet engine, rocket, and hypersonic vehicle components. Reduced weight, increased performance.
Medicinsk: Custom orthopedic implants, prosthetics, surgical tools. Biocompatible metals tailored to anatomy.
Fordon: Lightweighting components, performance parts, tooling. Increased strength and functional integration.
Industriell: End-use production parts for pumps, compressors, engines. Reduced lead time and inventory.
Konsument: Jewelry, fashion accessories, small gadgets. Unique high-value geometries.
Försvar: Rugged parts for field use, protective gear, armament. On-demand manufacturing.
Moldmaking: Conformal cooling channels give higher productivity. Direct printing of mold tooling.
Energi: Oil/gas components resist corrosion and perform in extreme environments.
The excellent mechanical properties, accuracy and design freedom enabled by metal AM make it valuable for prototypes, tools, and end-use production parts across many industries.
Metal Additive Manufacturing Process Capabilities
The different metal 3D printing processes have varying capabilities in terms of compatible materials, part sizes, accuracy, surface finish and more:
Process | Material | Noggrannhet | Avsluta | Hastighet |
---|---|---|---|---|
Fusion av pulverbäddar | De flesta legeringar | ±0.1-0.2mm | Rough, porous | Medium |
Deposition med riktad energi | Any alloy | ±0.3-1mm | Grov | Hög |
Binder Jetting | De flesta legeringar | ±0.2mm | Infiltration required | Hög |
Laminering av ark | De flesta legeringar | ±0.1mm | Bra | Långsam |
Fusion av pulverbädd offers the best accuracy and surface finish but slower speeds. Deposition med riktad energi allows large near-net shape parts to be built rapidly but with lower precision. Sprutning av bindemedel is faster but requires infiltration for full density. Laminering av ark is limited to thinner sections.
The optimal process depends on the application requirements – choose based on part size, material options, accuracy, speed and post-processing needs.
Popular Metal Additive Manufacturing Alloy Systems
Here are some of the most common metal alloy systems used in additive manufacturing along with their key characteristics:
Rostfria stål
Legering | Sammansättning | Fastigheter | Tillämpningar |
---|---|---|---|
17-4PH | Cr, Ni, Cu | Hög hållfasthet, korrosionsbeständighet | Flyg, industri |
15-5PH | Cr, Ni | Härdning genom utfällning | Flyg- och rymdindustrin, fordonsindustrin |
316L | Cr, Ni, Mo | Corrosion resistance, bio-compatible | Medicinsk, marin |
304L | Cr, Ni | Korrosionsbeständighet | Konsumentprodukter |
Aluminiumlegeringar
Legering | Sammansättning | Fastigheter | Tillämpningar |
---|---|---|---|
AlSi10Mg | Al, Si, Mg | Low density, good strength | Flyg- och rymdindustrin, fordonsindustrin |
AlSi7Mg | Al, Si, Mg | Low density, high ductility | Automotive, consumer |
A2024 | Al, Cu, Mg | Hög hållfasthet | Strukturer för flyg- och rymdindustrin |
Al6061 | Al, Mg, Si | Medium strength, corrosion resistance | Flyg- och rymdindustrin, marin |
Titanlegeringar
Legering | Sammansättning | Fastigheter | Tillämpningar |
---|---|---|---|
Ti6Al4V | Ti, Al, V | High strength-to-weight | Flyg- och rymdindustrin, medicinteknik |
Ti6Al4V ELI | Low interstitials | Fracture resistance | Flyg- och rymdindustrin |
Ti64 | Ti, Al, V | Heat treatability | Flyg- och rymdindustrin, fordonsindustrin |
Ti klass 2 | Ti | Utmärkt korrosionsbeständighet | Industriell, marin |
Nickellegeringar
Legering | Sammansättning | Fastigheter | Tillämpningar |
---|---|---|---|
Inconel 718 | Ni, Fe, Cr | Hög hållfasthet, korrosionsbeständighet | Flyg- och rymdindustrin, olja och gas |
Inconel 625 | Ni, Cr, Mo | Oxidations- och korrosionsbeständighet | Flyg- och rymdindustrin, kemisk industri |
Hastelloy X | Ni, Fe, Cr | Oxidation resistance, high temp | Flyg, industri |
Kobolt Krom Legeringar
Legering | Sammansättning | Fastigheter | Tillämpningar |
---|---|---|---|
CoCrMo | Co, Cr, Mo | Biokompatibel, hög hårdhet | Medicinska implantat, dentala |
CoCrWNi | Co, Cr, W, Ni | High hardness, strength | Dental, cutting tools |
CoCrMoSi | Co, Cr, Mo, Si | Biocompatible, high fatigue strength | Medicinska implantat |
By selecting the optimal alloy for the application requirements, additive manufacturing enables high performance metal parts to be 3D printed on demand.
Popular Metal Powder Grades for Additive Manufacturing
Most major metal powder suppliers now provide optimized powder grades specifically for additive manufacturing. Here are some of the most common grades used:
Pulver av rostfritt stål
Material | Pulverkvaliteter | Partikelstorlek | Leverantörer |
---|---|---|---|
17-4PH | Philloy 17-4, 17-4PH NX2 | 15-45 mikrometer | Hoganas, Carpenter Additive |
316L | 316L CX, 316L-Si-dura | 15-45 mikrometer | Linde, Concept Laser |
304L | CL20ES, 304L CX | 15-45 mikrometer | Concept Laser, Carpenter Additive |
Pulver av aluminiumlegeringar
Material | Pulverkvaliteter | Partikelstorlek | Leverantörer |
---|---|---|---|
AlSi10Mg | AlSi10Mg ALEA, AlSi10Mg CX | 25-45 mikrometer | Linde, Concept Laser |
AlSi7Mg | AlSi7Mg AM | 25-45 mikrometer | Linde |
Al6061 | 6061 CX | 15-45 mikrometer | Snickare Tillsats |
Titanium Alloy Powders
Material | Pulverkvaliteter | Partikelstorlek | Leverantörer |
---|---|---|---|
Ti6Al4V | Ti64 ELIT, Ti64 Grade 23 | 15-45 mikrometer | AP&C, Linde |
Ti6Al4V ELI | Ti64-ELI CX | 15-45 mikrometer | Snickare Tillsats |
Pulver av nickellegeringar
Material | Pulverkvaliteter | Partikelstorlek | Leverantörer |
---|---|---|---|
Inconel 718 | 718 ALEA AM, 718-P Powder | 10-45 mikrometer | Linde, Praxair |
Inconel 625 | 625 CX, Inconel 625-Si-dura | 15-45 mikrometer | Carpenter Additive, Concept Laser |
Cobalt Chrome Alloy Powders
Material | Pulverkvaliteter | Partikelstorlek | Leverantörer |
---|---|---|---|
CoCrMo | CoCrMo CX, Digital CobaltChrome | 5-25 mikrometer | Carpenter Additive, Arcam |
CoCrWNi | CC W-Ni CX | 5-25 mikrometer | Snickare Tillsats |
These optimized powder grades ensure high quality and repeatable performance for metal additive manufacturing across common aerospace, medical, and industrial alloys.
Metal Additive Manufacturing Powder Costs
The costs of metal powders for AM can vary significantly depending on alloy composition, purity, particle size distribution, supplier, and purchase volume:
Material | Kostnad per kg |
---|---|
Rostfritt stål 316L | $50 – $120 |
Aluminium AlSi10Mg | $50 – $100 |
Titan Ti64 | $150 – $500 |
Inconel 718 | $150 – $300 |
Kobolt krom | $250 – $500 |
Powder cost is a significant portion of overall part cost in metal AM. Industries adopting AM include aerospace, medical, automotive, and oil and gas where high-value alloys justify the costs. As volumes increase, prices are declining. Reusing waste powder via powder recovery systems also helps reduce overall costs per part.
Metal Additive Manufacturing Post-Processing
Most metal AM processes produce parts with a rough surface finish and some internal porosity. Additional post-processing is typically required:
- Borttagning från byggplattan – Cutting, grinding, or wire EDM to remove supports and separate parts.
- Ytbehandling – Machining, grinding, polishing, blasting to improve surface finish.
- Stresslindrande – Heat treatment to relieve residual stresses from AM build.
- Varm isostatisk pressning – High pressure to eliminate internal voids and increase density.
- Värmebehandling – Precipitation hardening, aging to enhance mechanical properties.
- Ytbeläggningar – Apply functional coatings for wear/corrosion resistance if needed.
With the right post-processing, metal AM parts can achieve extremely high density and precision surface finishes comparable to traditionally manufactured metal components.
Metal Additive Manufacturing Design Guidelines
To take full advantage of metal AM and avoid potential pitfalls, following design guidelines is recommended:
- Minimize overhanging structures requiring supports
- Orient parts to reduce stair-stepping surface finish effects
- Use thin walls, lattices to reduce weight and material use
- Consolidate assemblies into single complex parts
- Incorporate conformal cooling channels and bionic designs
- Design internal channels and voids to be self-supporting
- Allow access holes for unpowdered regions
- Account for anisotropic properties based on build orientation
- Design generous fillets and radii into corners
By adopting a design-for-AM mindset, engineers can fully leverage these innovative capabilities.
Framtiden för additiv tillverkning av metall
Metal additive manufacturing has come a long way in terms of materials, processes, applications and adoption. However, significant opportunities still exist to improve speed, cost, quality, and material options.
Equipment manufacturers are developing larger build envelopes and multi-laser systems to increase productivity. Closed-loop monitoring and advanced quality control systems will help boost consistency and reliability.
Material suppliers are focused on qualifying more alloys optimized for AM, including higher temperature materials like nickel superalloys, tool steels, refractory metals. Functionally graded and composite metal powders will provide more tuning of properties.
Programvara advancements around design, simulation, optimization, machine learning, and automation will make AM more accessible to a wider audience. System connectivity and digital manufacturing approaches will allow more distributed and agile production.
Tillämpningar will continue growing rapidly in aerospace for engines and structural components. Adoption in automotive, oil and gas, medical devices, and consumer electronics will accelerate as costs decrease. Rapid manufacturing and mass customization will become reality.
It is an exciting time in the metal AM industry as new players and novel innovations enter this high growth market estimated to reach over $15 billion by 2028.
Metal Additive Manufacturing – FAQ
Here are answers to some frequently asked questions about metal additive manufacturing materials and processes:
What types of metals can be 3D printed?
Most major industrial alloys are printable including stainless steels, aluminum, titanium, nickel, cobalt chrome, tool steels, precious metals like gold and silver, and copper alloys. New alloys are constantly being qualified.
What kind of accuracy and finish can be achieved?
Dimensional accuracy is typically around ±0.1-0.3% with tolerances of ±0.1-0.2mm. As-printed surface finish is rough at 10-25 μm Ra but can be improved significantly through machining and polishing.
How do the material properties compare to traditional manufacturing?
The microstructure and properties of most additive parts are comparable to cast or wrought material forms. Mechanical properties meet or exceed standards for materials like aerospace-grade titanium and nickel alloys.
How are parts post-processed after 3D printing?
Post-processing includes support removal, stress relieving, surface finishing operations like CNC machining, grinding, and polishing as well as any heat treatment required. Some critical applications may require hot isostatic pressing (HIP) to eliminate internal voids and increase density.
What are some key design principles for metal AM parts?
Design guidelines include minimizing overhangs, optimizing build orientation, incorporating lattices and internal structures, using thin walls, and consolidating assemblies. Performance can be enhanced through bionic and conformal cooling designs.
Dela på
MET3DP Technology Co, LTD är en ledande leverantör av lösningar för additiv tillverkning med huvudkontor i Qingdao, Kina. Vårt företag är specialiserat på 3D-utskriftsutrustning och högpresterande metallpulver för industriella tillämpningar.
Förfrågan för att få bästa pris och anpassad lösning för ditt företag!
Relaterade artiklar
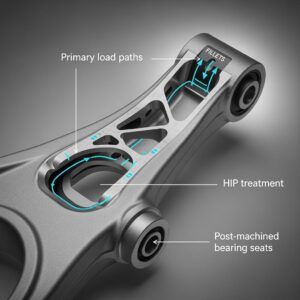
Metal 3D Printing for U.S. Automotive Lightweight Structural Brackets and Suspension Components
Läs mer "Om Met3DP
Senaste uppdateringen
Vår produkt
KONTAKTA OSS
Har du några frågor? Skicka oss meddelande nu! Vi kommer att betjäna din begäran med ett helt team efter att ha fått ditt meddelande.