De komplicerade egenskaperna hos Bonded Powder
Innehållsförteckning
Bundet pulver, ett avgörande material i olika industriella tillämpningar, erbjuder unika egenskaper och fördelar. Den här artikeln fördjupar sig i detaljerna för bundet pulver, diskuterar dess typer, sammansättning, tillämpningar och mycket mer. Vi kommer också att titta på specifika metallpulvermodeller och tillhandahålla detaljerade beskrivningar och jämförelser för att hjälpa dig förstå deras användbarhet och prestanda.
Översikt över Bonded Powder
Bonded powder-teknologi innebär att man kombinerar olika typer av pulver för att skapa ett kompositmaterial med förbättrade egenskaper. Dessa pulver kan inkludera metaller, keramer eller andra ämnen, och de binds med olika metoder såsom mekanisk legering, termisk spray eller sintring. De resulterande materialen uppvisar förbättrade egenskaper som ökad hållfasthet, korrosionsbeständighet och termisk stabilitet.
Nyckelegenskaper hos Bonded Powder
- Förbättrade egenskaper: Bonded pulver är utformade för att dra nytta av de bästa egenskaperna hos deras ingående material.
- Mångsidighet: Används i många industrier, inklusive flyg, bil, elektronik och medicinsk utrustning.
- Anpassningsbarhet: Pulver kan skräddarsys för specifika applikationer genom att justera deras sammansättning och bindningstekniker.
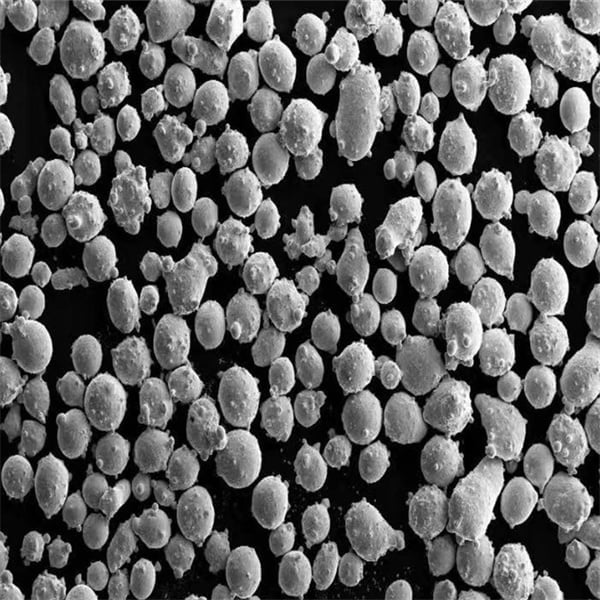
Typer och egenskaper hos Bondade pulver
Nedan finns en tabell som sammanfattar typer, sammansättning, egenskaper och egenskaper hos olika bundna pulver.
Typ | Sammansättning | Fastigheter | Egenskaper |
---|---|---|---|
Metall-keramiskt bundet pulver | Metall (t.ex. aluminium) + keramik (t.ex. aluminiumoxid) | Hög hållfasthet, slitstyrka | Lämplig för miljöer med höga påfrestningar |
Pulver för termisk sprutning | Nickel, krom, koboltlegeringar | Termisk stabilitet, korrosionsbeständighet | Används i beläggningsapplikationer |
Sintrade pulver | Järn, koppar, volframlegeringar | Förbättrade mekaniska egenskaper | Vanligt i fordonskomponenter |
Kompositpulver | Metallmatriskompositer (MMC) | Överlägsen slitstyrka, lätt | Flyg- och strukturtillämpningar |
Pulver för additiv tillverkning | Titan, rostfritt stål, aluminium | Hög precision, styrka | 3D-utskrift och snabb prototypframställning |
Applikationer av bonded pulver
Bonded pulver kan användas inom olika områden på grund av deras förbättrade egenskaper. Här är en tabell som visar deras typiska användningsområden:
Tillämpning | Exempel | Fördelar |
---|---|---|
Flyg- och rymdindustrin | Turbinblad, strukturella komponenter | Högt förhållande mellan styrka och vikt, termisk stabilitet |
Fordon | Motordelar, bromskomponenter | Slitstyrka, hållbarhet |
Elektronik | Konduktiva pastor, kylflänsar | Värmeledningsförmåga, elektriska egenskaper |
Medicintekniska produkter | Implantat, proteser | Biokompatibilitet, korrosionsbeständighet |
Industriella beläggningar | Skyddsbeläggningar, termiska barriärer | Korrosionsskydd, värmeisolering |
Specifikationer och standarder för bonded pulver
Följande tabell listar olika specifikationer, storlekar, kvaliteter och standarder för bundna pulver:
Specifikation | Detaljer |
---|---|
Partikelstorlek | Spänner från nano- till mikrometerskalor beroende på applikation |
Betyg | Variera beroende på legering och tillämpning (t.ex. Ti-6Al-4V för titanpulver) |
Standarder | ISO, ASTM-standarder specifika för materialtyp och användningsfall |
Renhetsnivåer | Hög renhet (99.9%+) för kritiska applikationer |
Täthet | Skräddarsydd för att möta specifika mekaniska krav |
Leverantörer och prisuppgifter för Bonded pulver
Här är en tabell som sammanfattar nyckelleverantörer och vägledande prisinformation:
Leverantör | Plats | Material levereras | Prisintervall (per kg) |
---|---|---|---|
Höganäs AB | Sverige | Järn, stål, rostfritt stål pulver | $30 – $100 |
Snickeriteknik | USA | Nickel, titan, koboltpulver | $100 – $500 |
Sandvik | Globalt | Metall-keramiska kompositer | $50 – $200 |
Oerlikon Metco | Schweiz | Pulver för termisk sprutning | $200 – $800 |
GKN Additiv | STORBRITANNIEN | Pulver för additiv tillverkning | $150 – $600 |
Jämföra fördelar och nackdelar med bonded pulvertyper
Nedan finns en tabell som jämför fördelarna och begränsningarna med olika bundna pulver:
Typ | Fördelar | Begränsningar |
---|---|---|
Metall-keramik | Hög hållfasthet, slitstyrka | Högre kostnad, bearbetningskomplexitet |
Termisk spray | Utmärkt termisk och korrosionsbeständighet | Kräver specialutrustning |
Sintrad | Goda mekaniska egenskaper, kostnadseffektiv | Begränsad till vissa geometrier |
Sammansatt | Lätt, överlägsen slitstyrka | Dyra råvaror |
Additiv tillverkning | Hög precision, anpassningsbar | Hög initial installationskostnad, långsammare produktionshastighet |
Specifika metallpulvermodeller
Här är en detaljerad titt på tio specifika metallpulvermodeller, som lyfter fram deras unika egenskaper och tillämpningar:
1. Höganäs Ancorsteel 1000
Ett mångsidigt järnbaserat pulver, idealiskt för strukturella delar i fordonstillämpningar på grund av dess utmärkta kompressibilitet och höga grönhållfasthet.
2. Snickare 20Cb-3
Ett nickelbaserat superlegeringspulver känt för sin exceptionella korrosionsbeständighet och höga temperaturprestanda, som vanligtvis används inom flyg- och kemisk industri.
3. Sandvik Osprey 17-4 PH
Ett rostfritt stålpulver som kombinerar hög hållfasthet, god korrosionsbeständighet och utmärkt svetsbarhet, vilket gör det lämpligt för additiv tillverkning och verktygstillämpningar.
4. Oerlikon Metco 73F-NS
Ett termiskt spraypulver bestående av nickel och krom, ger enastående termisk och oxidationsbeständighet, idealisk för beläggning av turbinkomponenter.
5. GKN Titanium Ti-6Al-4V
Ett allmänt använt titanlegeringspulver för additiv tillverkning, känt för sitt höga hållfasthet-till-viktförhållande och biokompatibilitet, flitigt använt i medicinska implantat och flyg- och rymddelar.
6. Höganäs Astaloy CrM
Ett pulver av järn-krom-molybdenlegering som erbjuder hög härdbarhet och god slitstyrka, som ofta används i högpresterande växlar och bildelar.
7. Snickare Custom 465
Ett martensitiskt rostfritt stålpulver med utmärkt seghet och styrka, som används i flyg- och rymdkomponenter och högpresterande sportartiklar.
8. Sandvik Osprey 625
Ett nickelbaserat superlegeringspulver med utmärkt korrosions- och oxidationsbeständighet, perfekt för marina och kemiska processmiljöer.
9. Oerlikon Metco 307NS
Ett koboltbaserat legeringspulver för termiska sprayapplikationer, känt för sin höga slitstyrka och goda högtemperaturhållfasthet, som används i industriella gasturbiner.
10. GKN Aluminium AlSi10Mg
Ett aluminiumlegeringspulver lämpligt för additiv tillverkning, erbjuder en bra balans mellan mekaniska egenskaper och lättvikt, idealiskt för flyg- och biltillämpningar.
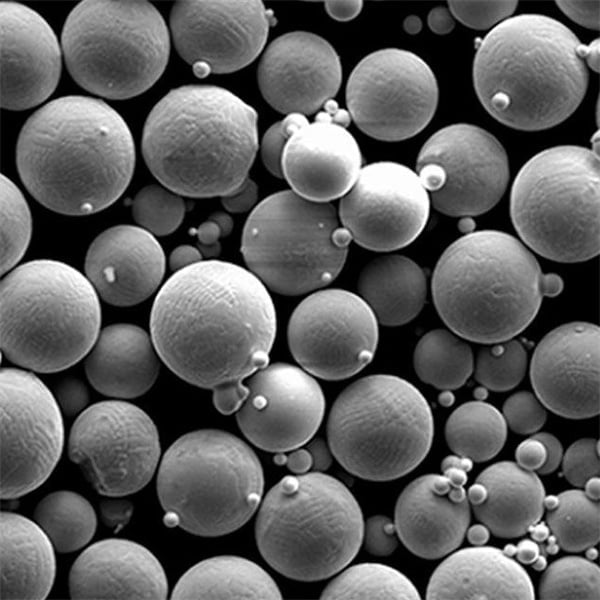
Fördelar och nackdelar med Bonded Powder
Fördelar med Bonded Powder
- Förbättrade egenskaper: Bondade pulver kan uppnå överlägsna mekaniska och fysikaliska egenskaper jämfört med pulver av ett enda material.
- Mångsidighet: De kan användas inom ett brett spektrum av industrier och applikationer, från flyg till medicinsk utrustning.
- Anpassning: Sammansättningen av bundna pulver kan skräddarsys för att möta specifika krav för olika applikationer.
- Förbättrad prestanda: Ökad slitstyrka, termisk stabilitet och korrosionsbeständighet gör dem idealiska för krävande miljöer.
Nackdelar med Bonded pulver
- Kostnad: Produktionen och bearbetningen av bundna pulver kan vara dyrare än traditionella material.
- Komplexitet: Tillverkningsprocesserna som är involverade i att skapa bundna pulver är ofta mer komplexa och kräver specialiserad utrustning.
- Utmaningar vid bearbetning: Att uppnå enhetlig bindning och konsistens kan vara utmanande, vilket potentiellt påverkar kvaliteten och prestandan hos slutprodukten.
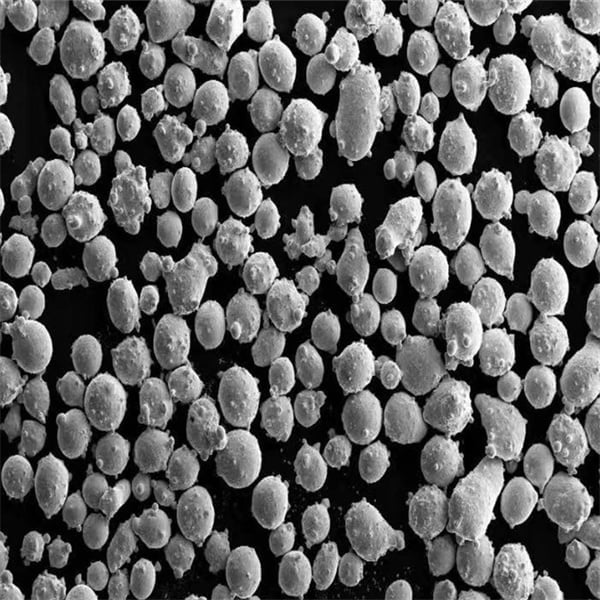
VANLIGA FRÅGOR
Fråga | Svar |
---|---|
Vad är bundet pulver? | Bonded powder hänvisar till kompositmaterial gjorda genom att kombinera olika typer av pulver för att förbättra deras egenskaper. |
Vilka är fördelarna med att använda bondade pulver? | De erbjuder förbättrade mekaniska och fysiska egenskaper, mångsidighet och anpassning för specifika applikationer. |
Var används bundna pulver vanligtvis? | De används i industrier som flyg, bil, elektronik, medicintekniska produkter och industriella beläggningar. |
Vilka är några vanliga typer av bundna pulver? | Metallkeramiska pulver, termiska spraypulver, sintrade pulver, kompositpulver och tillsatspulver för tillverkning. |
Hur tillverkas bundna pulver? | Metoder inkluderar mekanisk legering, termisk spray och sintring. |
Vilka är några utmaningar förknippade med bundna pulver? | Högre kostnader, komplexa tillverkningsprocesser och konsistensproblem under produktionen. |
Slutsats
Bonded pulver representerar en fascinerande och mycket mångsidig klass av material med ett brett spektrum av applikationer inom flera industrier. Genom att förstå typerna, egenskaperna, tillämpningarna och specifika modellerna av bundna pulver kan tillverkare och ingenjörer fatta välgrundade beslut för att optimera sina processer och produkter. Trots de utmaningar som är förknippade med deras produktion och kostnad, gör fördelarna med bondade pulver i form av förbättrade egenskaper och prestanda dem till ett värdefullt val för avancerade tekniska tillämpningar.
Känn dig fri att utforska de specifika metallpulvermodellerna som diskuteras här, var och en erbjuder unika fördelar anpassade till olika industriella behov. Oavsett om du är inom flyg-, bil- eller annan sektor kan bonded pulver vara nyckeln till att låsa upp nya nivåer av prestanda och innovation i dina projekt.
Dela på
MET3DP Technology Co, LTD är en ledande leverantör av lösningar för additiv tillverkning med huvudkontor i Qingdao, Kina. Vårt företag är specialiserat på 3D-utskriftsutrustning och högpresterande metallpulver för industriella tillämpningar.
Förfrågan för att få bästa pris och anpassad lösning för ditt företag!
Relaterade artiklar
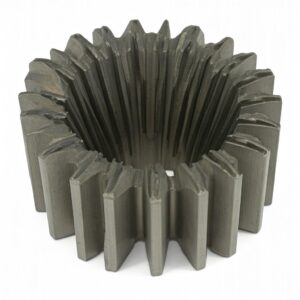
Högpresterande segment för munstycksvingar: Revolutionerande turbineffektivitet med 3D-utskrift i metall
Läs mer "Om Met3DP
Senaste uppdateringen
Vår produkt
KONTAKTA OSS
Har du några frågor? Skicka oss meddelande nu! Vi kommer att betjäna din begäran med ett helt team efter att ha fått ditt meddelande.
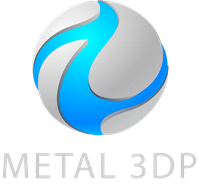
Metallpulver för 3D-printing och additiv tillverkning
FÖRETAG
PRODUKT
cONTACT INFO
- Qingdao City, Shandong, Kina
- [email protected]
- [email protected]
- +86 19116340731