3D Printing Lightweight Chassis Parts in Aluminum
Innehållsförteckning
Introduction to Lightweight Aluminum Chassis Components via Additive Manufacturing
The relentless pursuit of performance, efficiency, and sustainability is fundamentally reshaping the automotive landscape. Vehicle manufacturers, from established Original Equipment Manufacturers (OEMs) to agile electric vehicle (EV) startups and high-performance motorsport teams, are locked in a competitive race where every gram counts. Lightweighting – the strategic reduction of vehicle mass – is no longer a niche concern but a core engineering principle. Reducing weight directly translates into tangible benefits: improved fuel economy or battery range, enhanced handling dynamics and acceleration, reduced braking distances, and lower overall emissions. Within this context, the vehicle chassis, the structural foundation upon which the entire car is built, presents a significant opportunity for mass reduction. Traditionally manufactured from steel or cast aluminum alloys using methods like stamping, hydroforming, casting, and extensive machining, chassis components are increasingly being reimagined through the lens of advanced materials and innovative manufacturing processes. Aluminum alloys, already favored for their favorable strength-to-weight ratio compared to steel, become even more potent when combined with the design freedom offered by metall 3D-utskrifter, also known as additive manufacturing (AM).
Metal additive manufacturing, particularly techniques like Laser Powder Bed Fusion (LPBF), enables the creation of highly complex, topology-optimized aluminum chassis parts that were previously impossible or prohibitively expensive to produce. Imagine suspension nodes with intricate internal lattice structures mirroring organic bone growth, consolidating multiple bracket functions into a single, streamlined component, or subframes designed with material only precisely where structural loads demand it. This isn’t science fiction; it’s the reality enabled by AM. By building parts layer-by-layer directly from fine metal powder, guided by a digital design file, engineers can break free from the constraints imposed by traditional subtractive (machining) or formative (casting, forging) methods. This capability is particularly crucial for chassis components – parts like control arms, uprights, subframes, shock towers, and mounting brackets – which are critical for vehicle safety, performance, and integrity.
For engineers, this technology unlocks unprecedented design freedom, allowing them to achieve optimal structural efficiency and performance characteristics. For procurement managers and supply chain strategists within the automotive sector, aluminum additive manufacturing represents a paradigm shift. It offers the potential for on-demand production, reduced reliance on complex tooling supply chains, faster iteration during development, and the ability to source low-to-mid volume, high-complexity parts efficiently. Understanding the capabilities, materials, design considerations, and B2B supply chain implications of 3D printing lightweight aluminum chassis parts is becoming essential for maintaining a competitive edge. This article delves into the specifics of using aluminum alloys like AlSi10Mg and the high-strength A7075 for producing these critical automotive components via AM, exploring the applications, advantages, material choices, design guidelines, and considerations for partnering with a qualified metal AM service provider or powder supplier, ensuring your procurement strategy aligns with cutting-edge manufacturing potential. As a leader in both advanced metal powders and industrial printing systems, Met3dp is at forefront of enabling these automotive innovations.
The significance of lightweighting extends beyond mere performance metrics. In the burgeoning electric vehicle market, reducing chassis weight directly contributes to extending battery range – a critical factor for consumer adoption. Less mass requires less energy to accelerate and maintain speed, maximizing the efficiency of the electric powertrain. Furthermore, as vehicles incorporate more complex sensor suites, larger battery packs, and enhanced safety features, offsetting this added weight through structural optimization becomes paramount. Aluminum, being roughly one-third the density of steel while offering excellent strength and corrosion resistance, is a natural material choice. However, traditional manufacturing methods often limit how effectively aluminum’s lightweighting potential can be realized in complex chassis geometries. Casting requires drafts and uniform wall thicknesses, while machining from billet is material-intensive and generates significant waste (buy-to-fly ratio). Additive manufacturing overcomes these limitations, enabling engineers to place high-strength aluminum alloys precisely where needed, minimizing material usage while maximizing structural integrity. This layer-by-layer approach allows for the creation of internal channels for thermal management (e.g., cooling battery pack interfaces integrated into the chassis structure), complex mounting points, and organically shaped load paths optimized through sophisticated simulation software. The result is chassis components that are not only lighter but potentially stiffer and stronger than their conventionally manufactured counterparts, pushing the boundaries of vehicle design and performance. This shift necessitates a re-evaluation of sourcing strategies, favoring B2B manufacturing partners with deep expertise in aluminum AM processes, material science, and automotive quality standards.
Applications: Where are 3D Printed Aluminum Chassis Parts Used?
The versatility and advantages of metal additive manufacturing have opened doors for its application across a diverse range of automotive chassis components, moving steadily from niche prototyping to functional end-use parts in demanding scenarios. The ability to produce complex geometries with optimized strength-to-weight ratios makes aluminum AM particularly suitable for parts where performance and mass reduction are critical design drivers. Procurement managers seeking innovative solutions and engineers aiming for optimal designs should be aware of these key application areas:
1. Suspension Components:
- Control Arms & Wishbones: These critical links connect the wheel hub to the chassis, managing wheel movement and transferring loads. 3D printing allows for topology-optimized designs that are significantly lighter and potentially stiffer than cast or forged alternatives. Internal lattice structures can be incorporated to further enhance rigidity without adding substantial weight. This is particularly valuable in performance vehicles and motorsport where unsprung mass reduction directly improves handling and responsiveness. Sourcing these optimized components requires suppliers capable of handling complex geometries and ensuring material integrity.
- Uprights / Knuckles: Connecting the suspension arms, steering linkage, brake caliper, and wheel bearing, uprights are complex, load-bearing components. AM enables the integration of multiple mounting points and optimized load paths, reducing part count and weight compared to traditional multi-piece assemblies or bulky castings requiring extensive machining. The ability to rapidly prototype different kinematic designs is also a major advantage during vehicle development.
- Shock Absorber Mounts & Towers: These structures bear significant dynamic loads. 3D printing allows for designs optimized to distribute stress efficiently, potentially integrating features like reservoirs or mounting points for sensors, while minimizing weight high up in the vehicle structure, benefiting the center of gravity.
2. Chassis Structure & Subframes:
- Subframes: Supporting the engine, powertrain, or suspension systems, subframes are large structural elements. While full subframe printing might be limited by build volume for mass production, AM is increasingly used for critical nodes or connection points within hybrid subframe designs (e.g., AM nodes connected by extruded profiles). It’s also highly viable for low-volume or specialized vehicles (performance cars, motorsport) where optimized, lightweight subframes offer significant competitive advantages. Automotive procurement teams for niche vehicles find AM suppliers invaluable here.
- Mounting Brackets & Fixtures: The chassis requires numerous brackets for mounting everything from powertrain components and exhaust systems to wiring harnesses and fluid lines. AM allows for highly customized, lightweight brackets designed specifically for their load case and packaging constraints, often consolidating multiple conventional brackets into a single AM part. This is a prime area for B2B supply of low-to-mid volume custom parts.
- Crossmembers: Providing torsional rigidity to the chassis, crossmembers can be redesigned using topology optimization and AM to maintain or increase stiffness while drastically reducing weight compared to traditional stamped or hydroformed steel sections.
3. Electric Vehicle (EV) Specific Applications:
- Battery Pack Housings & Structural Integration: EV battery packs are heavy, requiring robust yet lightweight support structures. 3D printed aluminum components can form part of the battery enclosure, offering high strength, crash protection, and potentially integrating complex cooling channels directly into the structure for improved thermal management – a critical factor for battery performance and longevity. Sourcing partners with expertise in thermal management and structural optimization are key. Met3dp’s metal 3D printing solutions are well-suited for tackling such complex thermal-structural challenges.
- Motor Mounts: Electric motors have different mounting requirements and NVH (Noise, Vibration, Harshness) characteristics than internal combustion engines. AM allows for the creation of highly optimized motor mounts tailored to specific EV platforms, minimizing vibration transmission while saving weight.
4. Prototyping and Low-Volume Production:
- Functional Prototypes: AM enables the rapid production of functional aluminum chassis prototypes for physical testing (kinematics, durability, crash simulation). This drastically accelerates development cycles compared to waiting for traditional tooling for castings or forgings. Engineers can iterate designs quickly based on real-world test data.
- Niche & Performance Vehicles: For low-volume production runs (e.g., hypercars, motorsport series, specialized utility vehicles), the high cost of traditional tooling (molds, dies) makes AM highly cost-effective. Manufacturers can produce bespoke, highly optimized chassis parts without investing in tooling that may never be fully amortized. This opens opportunities for specialized automotive component distributors focusing on performance aftermarket or limited series production.
- Legacy Part Replacement: In some cases, AM can be used to produce replacement chassis parts for older vehicles where original tooling no longer exists, supporting the restoration and classic car markets.
The common thread across these applications is the drive for lightweighting without compromising strength or safety, leveraging the geometric freedom unique to additive manufacturing. As the technology matures, build speeds increase, and costs decrease, the scope of applications for 3D printed aluminum chassis parts in mainstream automotive production is set to expand significantly, transforming how vehicles are designed, sourced, and manufactured. Engaging with knowledgeable AM powder and equipment suppliers, like Met3dp with its comprehensive solutions, is crucial for navigating this evolving landscape.
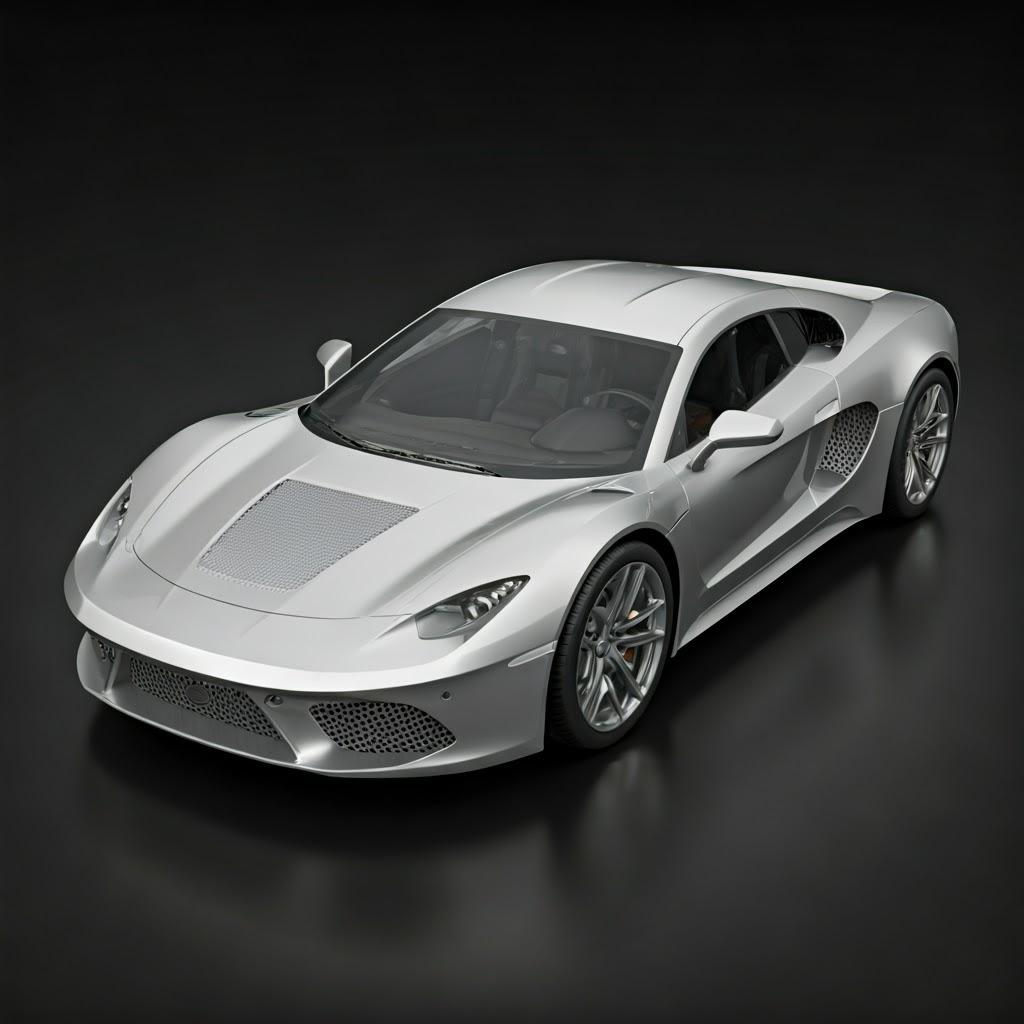
Why Metal 3D Printing for Automotive Chassis Components? Advantages Over Traditional Manufacturing
The decision to adopt metal additive manufacturing for critical components like automotive chassis parts isn’t merely about embracing novelty; it’s driven by compelling technical and business advantages that directly address the limitations of conventional methods like casting, forging, and machining. For engineers striving for optimal performance and procurement managers focused on efficiency and supply chain resilience, understanding these benefits is key to leveraging AM strategically.
1. Unparalleled Design Freedom & Topology Optimization:
- Traditional Constraints: Casting requires draft angles, minimum wall thicknesses, and avoids undercuts, limiting geometric complexity. Machining starts with a solid block and removes material, making complex internal features difficult or impossible and often leading to significant material waste (poor buy-to-fly ratio). Forging offers high strength but is generally limited to simpler shapes and requires expensive, part-specific dies.
- AM Advantage: Metal AM, particularly LPBF, builds parts layer by layer from powder. This additive approach liberates designers from most traditional manufacturing constraints. It enables the creation of:
- Topology Optimized Shapes: Using software tools (e.g., Altair Inspire, nTopology, Autodesk Fusion 360), engineers can define load cases, boundary conditions, and target mass reduction. The software then computationally generates the most efficient material distribution to meet performance requirements. This often results in organic, bone-like structures that are extremely lightweight yet incredibly strong and stiff – geometries impossible to achieve conventionally.
- Internal Lattice Structures: AM allows for the incorporation of complex internal lattices (e.g., gyroids, stochastic foams) within solid components. These lattices significantly reduce weight while maintaining high specific stiffness and providing potential benefits like vibration damping or energy absorption – highly desirable traits for chassis components.
- Integrated Functionality: Features like fluid channels for cooling (e.g., integrating cooling for nearby electronics or powertrain components directly into a chassis bracket), complex sensor mounts, or optimized cable routing pathways can be designed directly into the part, reducing assembly complexity.
2. Part Consolidation:
- Traditional Approach: Complex chassis assemblies often consist of multiple individual components (castings, stampings, machined parts, brackets) that must be joined together using fasteners or welding. Each joint adds weight, introduces potential failure points, and increases assembly time and complexity.
- AM Advantage: The design freedom of AM allows engineers to redesign assemblies as a single, monolithic component. For example, a suspension node assembly comprising a main casting and several bolted-on brackets could potentially be redesigned and 3D printed as one integrated part. This consolidation yields significant benefits:
- Viktminskning: Eliminates fasteners and overlapping material at joints.
- Increased Strength & Stiffness: Monolithic parts often exhibit better structural integrity than assemblies with joints.
- Reduced Assembly Time & Labor: Simplifies the vehicle assembly process.
- Simplified Logistics & Inventory: Fewer part numbers to manage, track, and stock – a key benefit for automotive procurement and supply chain management.
3. Rapid Prototyping & Accelerated Development Cycles:
- Traditional Bottleneck: Creating functional prototypes using traditional methods, especially casting or forging, requires the production of expensive and time-consuming tooling (patterns, molds, dies). Lead times for initial prototypes can stretch for weeks or months, significantly slowing down the design iteration and validation process.
- AM Advantage: Metal 3D printing allows engineers to go directly from a CAD file to a physical metal part, often within days. This facilitates:
- Faster Design Iteration: Multiple design variants can be printed and tested in parallel or rapid succession.
- Early Functional Testing: Prototypes possess material properties representative of the final production intent (especially when using the target alloy like AlSi10Mg or A7075), allowing for meaningful performance, durability, and kinematic testing early in the development cycle.
- Reduced Development Costs: Avoiding iterative tooling costs for prototype stages saves significant budget. This agility is crucial in the fast-paced automotive industry, allowing manufacturers to bring innovations to market more quickly.
4. Reduced Tooling Costs & Viability for Low-to-Mid Volume Production:
- Tooling Investment: The primary cost driver for traditional methods like casting and forging is the upfront investment in tooling. This cost must be amortized over the production volume. For low-to-mid volume applications (e.g., niche vehicles, motorsport, initial production ramps, aftermarket parts), the per-part cost associated with tooling can be prohibitively high.
- AM Advantage: Metal AM is a “tooling-less” process. The primary cost drivers are material consumption, machine time, and post-processing labor. While the per-part cost in AM might be higher than mass-produced cast parts at very high volumes, AM becomes highly cost-competitive or even cheaper for:
- Low-to-Mid Volume Runs: Where tooling amortization dominates traditional costs.
- Highly Complex Parts: Where conventional manufacturing would require multiple complex machining setups or intricate molds.
- On-Demand-produktion: Manufacturing parts only when needed reduces inventory holding costs and waste from obsolescence. This makes AM an attractive option for B2B suppliers offering customized or low-volume automotive components.
5. Material Possibilities & Optimized Material Usage:
- AM Advantage: While traditional methods work well with standard alloys, AM opens the door to potentially utilizing novel alloys or achieving specific microstructures through controlled solidification. Furthermore, the additive nature inherently minimizes material waste compared to subtractive machining, improving the buy-to-fly ratio, which is environmentally and economically beneficial, especially with expensive high-performance alloys. Companies specializing in powder production, like Met3dp with its advanced atomization technologies, play a crucial role in providing the high-quality, consistent powders needed for reliable AM production.
In summary, metal 3D printing offers a compelling value proposition for producing lightweight aluminum chassis components by enabling optimized designs, consolidating parts, accelerating development, eliminating tooling costs for lower volumes, and using material more efficiently. It empowers engineers to design for performance and allows procurement managers to rethink sourcing strategies, making it a transformative technology for automotive manufacturing solutions providers and OEMs alike. Partnering with an experienced B2B manufacturing partner proficient in aluminum AM is essential to fully realize these advantages.
Recommended Aluminum Powders (AlSi10Mg & A7075) and Their Significance
The choice of material is paramount in determining the performance, durability, and suitability of any automotive chassis component. While various metals can be 3D printed, aluminum alloys stand out for lightweighting applications due to their excellent strength-to-weight ratio, good corrosion resistance, and relative abundance. Within the aluminum family, two alloys have gained significant traction for additive manufacturing of structural parts: AlSi10Mg and A7075. Understanding their properties and the importance of powder quality is crucial for engineers specifying materials and procurement managers sourcing them.
The Importance of Powder Quality in Additive Manufacturing:
Before delving into the specific alloys, it’s vital to emphasize that the success of any metal AM process, especially Laser Powder Bed Fusion (LPBF), heavily relies on the quality of the metal powder feedstock. The characteristics of the powder directly impact the printing process stability, the density of the final part, and its resulting mechanical properties. Key powder quality attributes include:
- Fördelning av partikelstorlek (PSD): A controlled PSD ensures good powder bed density and consistent melting behavior. Too many fine particles can lead to poor flowability and potential safety hazards, while too many coarse particles can result in lower part density and poor surface finish.
- Sfäriskhet: Highly spherical powder particles flow easily and pack densely, leading to uniform powder layers and reduced porosity in the final part. Irregularly shaped particles can interlock, hindering flow and packing.
- Flytbarhet: Good flowability (measured by Hall flowmeter or similar methods) is essential for uniformly spreading thin powder layers across the build platform during the LPBF process. Poor flowability leads to defects in the powder bed and subsequent part defects.
- Chemical Purity & Composition: Tight control over the alloy composition and minimizing impurities (like oxygen and nitrogen) is critical for achieving the desired mechanical properties and ensuring consistent performance part after part. Impurities can lead to brittleness or reduced strength.
- Absence of Satellites & Porosity: High-quality powders have minimal “satellites” (smaller particles attached to larger ones) and low internal porosity, both of which can negatively affect flowability and final part density.
Företag gillar Met3dp specialize in producing high-performance metal powders tailored for additive manufacturing. Utilizing advanced manufacturing techniques such as Vacuum Induction Melting Gas Atomization (VIGA) och Process med roterande elektrod och plasma (PREP), Met3dp ensures its powders exhibit high sphericity, excellent flowability, controlled PSD, and high purity. This commitment to powder quality is fundamental to enabling customers to 3D print dense, reliable, high-performance metal parts with superior and consistent mechanical properties – a critical factor for dependable automotive component suppliers. Sourcing powders from reputable manufacturers with robust quality control processes is a key consideration for any B2B procurement strategy in the AM space. Explore Met3dp’s range of high-quality metal powders optimized for AM.
AlSi10Mg: The Workhorse Aluminum Alloy for AM
AlSi10Mg is arguably the most widely used aluminum alloy in metal additive manufacturing, particularly LPBF. It’s essentially an aluminum casting alloy adapted for AM processes. Its popularity stems from a combination of good processability, decent mechanical properties, and good thermal conductivity.
- Sammansättning: Primarily Aluminum (Al), with Silicon (Si) around 9-11% and Magnesium (Mg) around 0.2-0.45%. The Silicon content improves fluidity during melting and reduces solidification shrinkage, making it relatively easy to process via LPBF with fewer defects like hot cracking. Magnesium contributes to strengthening through precipitation hardening during heat treatment.
- Key Properties (Typical values for LPBF, after T6 heat treatment):
- Draghållfasthet: 330 – 430 MPa
- Utbytesstyrka: 230 – 300 MPa
- Töjning vid brott: 6 – 10%
- Hårdhet: 100 – 120 HBW
- Densitet: ~2.67 g/cm³
- Fördelar:
- Excellent Processability: Relatively wide processing window in LPBF, leading to high density parts (>99.5%) with good consistency. Less prone to cracking than high-strength alloys.
- Good Balance of Properties: Offers a good combination of strength, ductility, and thermal properties suitable for many structural applications.
- Svetsbarhet: Generally considered weldable, which can be useful for post-processing or integration into larger assemblies.
- Motståndskraft mot korrosion: Good resistance to atmospheric corrosion.
- Värmebehandlingsbar: Can be heat treated (commonly using a T6 cycle: solutionizing followed by artificial aging) to significantly improve strength and hardness.
- Applications in Chassis: Well-suited for moderately loaded structural brackets, housings, suspension components where extreme strength is not the primary driver, heat exchangers integrated into structures, and functional prototypes due to its ease of printing. It often serves as a direct AM replacement or upgrade for parts traditionally made from A356 or similar casting alloys. Wholesale buyers often find AlSi10Mg offers a good cost-performance balance for bulk AM production.
A7075 (Aluminum 7075): High-Strength Performance
A7075 is a high-performance aluminum alloy known for its exceptional strength-to-weight ratio, often comparable to some steels. Traditionally used in aerospace applications and high-stress structural parts, its adoption in AM has been more challenging but offers significant performance benefits where maximum strength is required.
- Sammansättning: Primarily Aluminum (Al), with Zinc (Zn) as the main alloying element (5.1-6.1%), Magnesium (Mg) (2.1-2.9%), and Copper (Cu) (1.2-2.0%). These alloying elements enable significant precipitation hardening, leading to very high strength levels after appropriate heat treatment.
- Key Properties (Potential values for LPBF, after optimized heat treatment, often T6 or similar):
- Draghållfasthet: Potentially exceeding 500 – 570 MPa (Significantly higher than AlSi10Mg)
- Utbytesstyrka: Potentially exceeding 450 – 500 MPa
- Töjning vid brott: Typically lower than AlSi10Mg, often in the 3-8% range (can be a trade-off for the high strength).
- Hårdhet: Can exceed 150 HBW.
- Densitet: ~2.81 g/cm³ (Slightly denser than AlSi10Mg)
- Fördelar:
- Very High Strength: One of the strongest readily available aluminum alloys, making it ideal for highly loaded, performance-critical components where minimizing weight is paramount.
- Utmärkt förhållande mellan styrka och vikt: Enables significant weight savings compared to other materials for the same strength requirement.
- Good Fatigue Strength: Important for components subjected to cyclic loading, common in chassis applications.
- Challenges & Considerations:
- Processbarhet: More challenging to process via LPBF than AlSi10Mg. It has a wider solidification range and is more susceptible to hot cracking and porosity if process parameters are not carefully optimized. Requires precise control over the printing process and often specialized machine parameters or build strategies (e.g., build plate heating).
- Heat Treatment Sensitivity: Achieving optimal properties requires precise multi-stage heat treatment cycles (e.g., T6, T73) which must be carefully controlled.
- Lower Ductility/Toughness: The high strength comes at the expense of reduced elongation and fracture toughness compared to AlSi10Mg. Design considerations must account for this.
- Motståndskraft mot korrosion: Can be more susceptible to stress corrosion cracking (SCC) than AlSi alloys, especially in certain temper conditions (though specific heat treatments like T73 are designed to improve SCC resistance). Surface treatments might be necessary depending on the operating environment.
- Applications in Chassis: Ideal for highly loaded suspension components (e.g., uprights, control arms in racing applications), critical structural nodes requiring maximum stiffness and strength, and any application where the absolute minimum weight for a given high load case is the primary objective. Often considered for direct replacement or upgrade of parts traditionally machined from 7000-series aluminum billet. Sourcing A7075 AM parts requires partnering with suppliers who have demonstrated expertise in processing this challenging alloy, backed by robust quality assurance.
Material Selection Summary Table:
Funktion | AlSi10Mg | A7075 | Considerations for Automotive Chassis |
---|---|---|---|
Primär användning | General purpose, good processability | High-strength, performance-critical | Match alloy to specific load case, weight target, and manufacturing feasibility. |
Draghållfasthet | Good (330-430 MPa, T6) | Very High (500-570+ MPa, T6) | A7075 offers significant strength advantage for highly stressed parts. |
Utbyteshållfasthet | Good (230-300 MPa, T6) | Very High (450-500+ MPa, T6) | Higher yield strength allows for more aggressive lightweighting (thinner sections). |
Duktilitet | Moderate (6-10% Elongation) | Lower (3-8% Elongation) | AlSi10Mg offers more forgiveness; A7075 requires careful design to manage stress concentrations. |
Processbarhet | Excellent (LPBF) | Challenging (Requires optimization) | AlSi10Mg generally easier/faster to print reliably; A7075 requires specialized expertise/parameters. |
Värmebehandling | Standard T6 effective | Requires precise T6/T7x cycles | Both require post-print heat treatment for optimal properties. |
Korrosion Res. | Bra | Moderate (Potential SCC risk, temper dependent) | A7075 may require protective coatings in harsh environments. |
Typical Apps | Brackets, housings, moderate-load suspension | High-load suspension, critical nodes, motorsport | A7075 for ultimate lightweighting where strength is paramount; AlSi10Mg for broader applications. |
Powder Sourcing | Mycket tillgänglig | More Specialized | Crucial to source high-quality powder (e.g., from Met3dp) for both, especially critical for A7075. |
Export to Sheets
Choosing between AlSi10Mg and A7075 depends heavily on the specific requirements of the chassis component – the load cases, the target weight reduction, the operating environment, and the cost sensitivity. AlSi10Mg provides a robust, reliable, and easier-to-process option for a wide range of parts, while A7075 pushes the performance envelope for the most demanding applications, albeit with increased processing complexity and cost. Partnering with a knowledgeable AM service provider or utilizing advanced systems like those from Met3dp, supported by their high-quality powders, is essential to successfully implement either alloy for producing cutting-edge, lightweight automotive chassis components.
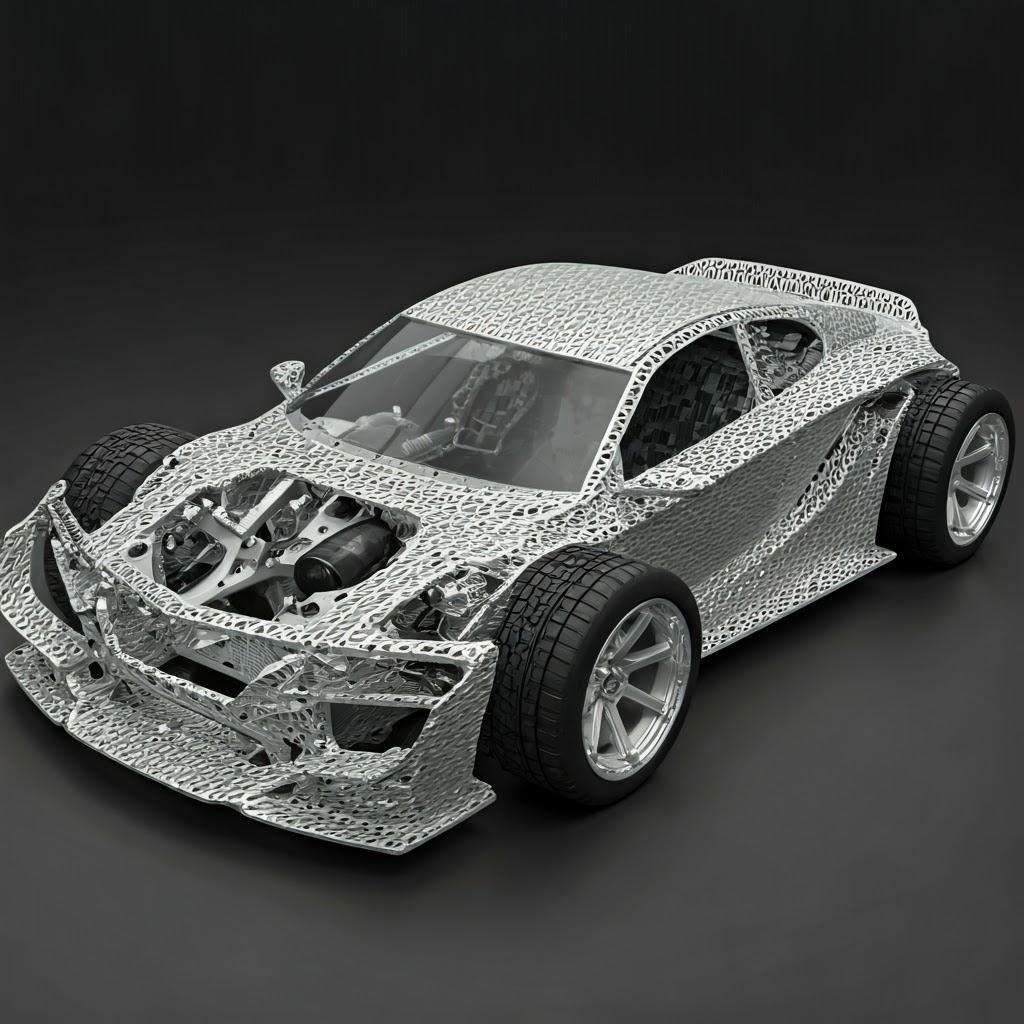
Design for Additive Manufacturing (DfAM) Principles for Lightweight Chassis Parts
Simply replicating a design intended for casting or machining using additive manufacturing rarely unlocks the technology’s full potential. To truly harness the power of 3D printing for lightweight, high-performance automotive chassis components, engineers must embrace Design för additiv tillverkning (DfAM). DfAM is not just a set of rules but a fundamental shift in design thinking, leveraging the unique capabilities of layer-by-layer fabrication while respecting its inherent constraints. For automotive applications where structural integrity, weight optimization, and performance are paramount, applying DfAM principles is non-negotiable. Procurement managers should also recognize that partnering with suppliers offering strong DfAM expertise or dedicated engineering services often leads to superior outcomes and better cost-efficiency in the long run.
1. Embrace Topology Optimization and Generative Design:
- Topology Optimization: This is arguably the cornerstone of DfAM for structural lightweighting. It’s a computational method that optimizes material distribution within a defined design space, subject to specific load cases, boundary conditions, and performance constraints (e.g., maximum stress, minimum stiffness, target mass reduction).
- Workflow: Engineers define the package space (maximum allowable volume), connection points (where the part interfaces with other components), load scenarios (braking, cornering, impact forces), and material properties (e.g., for AlSi10Mg or A7075 after heat treatment).
- Programvara: Tools like Altair Inspire, Ansys Discovery, Siemens NX Topology Optimization, Dassault Systèmes CATIA Generative Design, or Autodesk Fusion 360 Generative Design are commonly used.
- Produktion: The software generates an organic, often skeletal or trabecular structure, showing the most efficient load paths. This raw output usually requires some interpretation and smoothing by the designer to ensure manufacturability (e.g., removing sharp corners, ensuring minimum feature sizes).
- Chassis Application: Ideal for redesigning suspension nodes, control arms, engine mounts, and subframe elements, often achieving weight reductions of 20-50% or more compared to traditional designs while maintaining or even increasing stiffness.
- Generative Design: Takes topology optimization a step further by autonomously generating multiple design solutions that meet the specified constraints. Engineers can explore a wider range of design possibilities, potentially uncovering non-intuitive but highly efficient solutions. It often incorporates manufacturing constraints (e.g., overhang angles for AM) directly into the generation process.
2. Leverage Lattice Structures:
- Concept: AM allows the integration of complex, repeating internal geometric patterns known as lattices within a solid part’s volume or as standalone structures. These are inspired by natural structures like bone or wood.
- Typer:
- Strut-based Lattices: Composed of interconnected beams (e.g., cubic, octet-truss). Good for stiffness-dominated applications.
- Surface-based Lattices (TPMS – Triply Periodic Minimal Surfaces): Smooth, shell-like structures (e.g., Gyroid, Schwarz P). Offer excellent surface area-to-volume ratios, good energy absorption, and smoother stress distributions compared to strut lattices. Often preferred for fluid flow or heat transfer applications if integrated channels are needed, but also highly effective for lightweight structural support.
- Benefits for Chassis Parts:
- Extreme Lightweighting: Significant mass reduction while maintaining tailored stiffness and strength.
- Enhanced Energy Absorption: Potential for improved crash performance in specific applications.
- Vibration Damping: Certain lattice configurations can help damp vibrations traveling through the chassis.
- Termisk hantering: High surface area can aid heat dissipation if designed correctly.
- Överväganden: Requires specialized software for generation (e.g., nTopology, Materialise 3-matic, specialized CAD modules). Printability (minimum strut diameter, powder removal from internal voids) must be carefully considered. Analyzing the mechanical behavior of lattices requires sophisticated simulation techniques.
3. Understand and Design for AM Process Constraints:
- Minimum Wall Thickness/Feature Size: LPBF processes have limitations on the smallest reliable features they can produce. For AlSi10Mg and A7075, minimum printable wall thicknesses are typically in the range of 0.4mm to 1.0mm, depending on the machine, parameters, and feature orientation. Designs must respect these limits to ensure features are fully formed and robust.
- Overhangs and Support Structures: LPBF requires support structures for features that overhang the horizontal plane at angles typically less than 40-45 degrees (relative to the build plate). Designing parts with self-supporting angles (>= 45 degrees) wherever possible significantly reduces the need for supports.
- Why Minimize Supports? Supports consume extra material, increase print time, require laborious post-processing for removal (potentially damaging the surface), and can be difficult to remove from internal channels.
- DfAM Strategies: Orient the part strategically on the build plate; use chamfers instead of sharp overhangs; design internal channels with diamond or teardrop cross-sections instead of circular ones; incorporate sacrificial ribs or features that can be easily machined away later.
- Trapped Powder Removal: For parts with internal cavities or complex channels (common in optimized chassis parts or those with integrated cooling), designers must include strategically placed drainage holes to allow unfused powder to be removed after printing. Trapped powder adds weight and can be a long-term contamination risk.
- Residual Stress Considerations: While largely managed by process parameters and post-processing, designers can help mitigate residual stress by avoiding abrupt changes in cross-sectional area and incorporating smooth transitions and fillets. Very large, flat sections parallel to the build plate can also be prone to warping.
4. Design for Post-Processing:
- Support Removal Access: Ensure that areas requiring support structures are physically accessible for removal tools (manual or CNC). Avoid designing deep, narrow internal features that rely on extensive, inaccessible supports.
- Machining Allowances: Identify critical interfaces, mounting surfaces, and holes that require tight tolerances or specific surface finishes achievable only through post-machining. Add extra material (machining stock, typically 0.5mm to 2mm) to these surfaces in the CAD model to allow for material removal during CNC operations. Clearly define datum features for machining setups.
- Överväganden om värmebehandling: Aim for relatively uniform wall thicknesses where possible to promote even heating and cooling during heat treatment, minimizing distortion risk. Understand that the required T6 or similar cycles for AlSi10Mg/A7075 will affect the entire part.
- Inspection Access: Consider how critical features will be inspected (e.g., CMM probe access, line-of-sight for visual or scanning methods).
5. Collaboration and Iteration:
- Early Supplier Involvement: Engage with your chosen metal AM service provider or leverage internal expertise early in the design process. Experienced AM engineers can provide invaluable feedback on printability, orientation strategy, support minimization, and cost optimization. Companies like Met3dp, with deep roots in both AM equipment and materials science, can offer crucial insights through partnership and application development support.
- Simulation-Driven Design: Utilize Finite Element Analysis (FEA) not only for structural validation but also potentially for build process simulation to predict thermal stresses and distortion, allowing for design adjustments or optimized build layouts before committing to printing.
By integrating these DfAM principles, engineering teams can move beyond simple substitution and create truly optimized, next-generation lightweight aluminum chassis components that deliver significant performance and efficiency gains for automotive applications. This requires a combination of advanced software tools, a deep understanding of the AM process, and often, collaboration with specialized B2B engineering services or AM partners.
Achievable Tolerances, Surface Finish, and Dimensional Accuracy in Aluminum 3D Printing
When designing and procuring 3D printed aluminum chassis parts for functional automotive use, understanding the achievable levels of precision is critical. Engineers need to know what tolerances and surface finishes to expect directly from the printing process, and procurement managers need to specify requirements realistically and understand when secondary finishing operations are necessary. While metal AM offers incredible geometric freedom, it inherently differs from the precision typically associated with CNC machining in its as-built state.
1. Dimensional Tolerances:
- Process Capability: Laser Powder Bed Fusion (LPBF), the most common process for aluminum chassis parts, can achieve reasonably good dimensional accuracy. Typical general tolerances for as-built LPBF metal parts often fall within the range of ISO 2768-m (medium) or sometimes ISO 2768-f (fine) for smaller dimensions.
- Typical Values: This might translate to ±0.1mm to ±0.3mm for features up to 100mm, with tolerance ranges increasing for larger dimensions (e.g., ±0.2% to ±0.5% of the nominal dimension).
- Factors Influencing Tolerance:
- Machine Calibration: Accuracy of the laser scanning system, Z-axis movement, and overall machine health. High-quality, well-maintained printers like those developed by Met3dp are crucial for consistent accuracy.
- Thermal Effects: Heating and cooling cycles during the build cause expansion and contraction, leading to residual stress and potential distortion. Part geometry, size, and orientation significantly impact this.
- Part Size & Geometry: Larger parts and complex geometries are generally more challenging to hold tight tolerances on due to accumulated thermal stress and potential warping.
- Process Parameters: Laser power, scan speed, layer thickness, and scan strategy all influence the melt pool dynamics and resulting accuracy. Optimized parameters are key.
- Material: Different alloys exhibit varying shrinkage and stress behaviors.
- Specification: It’s crucial to clearly define critical tolerances on engineering drawings. Blanket tight tolerances across the entire part will unnecessarily increase cost and potentially lead time. Focus on functional requirements. Discuss achievable tolerances with your AM service provider early in the project.
2. Surface Finish (Roughness):
- As-Built Surface: The surface finish of as-built LPBF parts is inherently rougher than machined surfaces. It’s characterized by partially melted powder particles adhering to the surface and layer lines.
- Typical Ra Values: Surface roughness (Ra – arithmetic average roughness) for AlSi10Mg and A7075 LPBF parts typically ranges from 6 µm to 20 µm (micrometers) or roughly 240 µin to 800 µin (microinches).
- Influencing Factors:
- Surface Orientation: Upward-facing surfaces (looking towards the top of the build) and vertical walls generally have a better finish than downward-facing surfaces (supported surfaces), which tend to capture more partially melted particles and show support contact points after removal.
- Skiktets tjocklek: Thinner layers generally result in slightly better surface finish but increase build time.
- Powder Particle Size: Finer powders can lead to smoother surfaces but may impact flowability.
- Laser Parameters: Energy density affects melt pool stability and surface texture.
- Stödstrukturer: Removal of supports often leaves witness marks or rougher patches that may require further finishing.
- Jämförelse: This as-built roughness is comparable to or sometimes rougher than sand casting or investment casting but significantly rougher than typical machined finishes (which can easily achieve Ra < 3.2 µm or even < 0.8 µm).
- Implications: For non-critical surfaces, the as-built finish may be acceptable. However, for surfaces requiring sealing (e.g., O-ring grooves), smooth fluid flow, fatigue resistance, or precise mating with other components, post-processing surface treatments are almost always necessary.
3. Dimensional Accuracy Verification:
- Importance: Given the critical nature of chassis components, verifying dimensional accuracy is essential.
- Metoder:
- Coordinate Measuring Machines (CMM): Provide high-accuracy point measurements for verifying critical dimensions, GD&T (Geometric Dimensioning and Tolerancing) features, and overall form.
- 3D Scanning (Laser or Structured Light): Capture millions of data points across the entire part surface, allowing for comparison against the original CAD model (color map deviation analysis). Excellent for complex geometries and identifying warpage or distortion. Often used for initial qualification and production part approval processes (PPAP) in automotive contexts.
- Supplier Capability: Ensure your chosen AM service provider has robust quality control processes and the necessary metrology equipment to verify parts against your specifications. This is a key factor in evaluating B2B manufacturing partners.
4. Achieving Tighter Tolerances and Smoother Finishes:
- Post-Machining is Key: For features demanding tolerances tighter than the standard LPBF process capability (e.g., bearing bores, precise mounting holes, flat mating surfaces) or surface finishes smoother than the as-built state, post-process CNC machining is essential.
- Design Consideration: As mentioned in the DfAM section, designers must anticipate this need by adding machining stock to relevant features in the CAD model.
- Procurement Specification: Clearly differentiate between as-built tolerances and final machined tolerances on drawings and in procurement specifications. Understand that requiring extensive post-machining will impact the final part cost and lead time.
In conclusion, while aluminum 3D printing offers moderate dimensional accuracy and a characteristic surface roughness directly from the machine, achieving the tight tolerances and smooth finishes often required for functional automotive chassis interfaces necessitates planned post-processing, primarily CNC machining. Realistic specification, clear communication with the AM provider, and robust quality verification are essential for successfully integrating these advanced components into vehicles. Leveraging reliable, high-accuracy printing systems is the foundation for minimizing downstream effort.
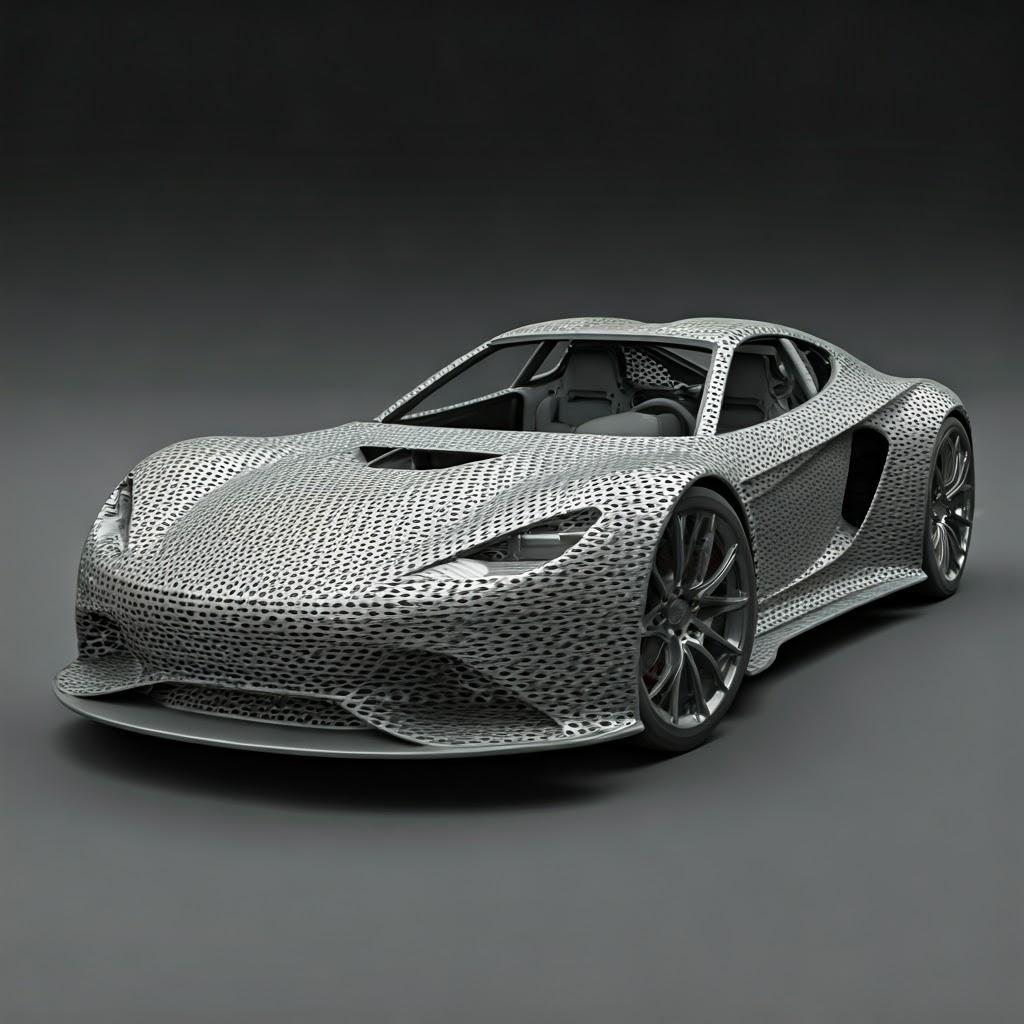
Essential Post-Processing Steps for 3D Printed Aluminum Chassis Parts
Producing a lightweight aluminum chassis part doesn’t end when the 3D printer stops. The “green” part, fresh off the build plate, requires a series of crucial post-processing steps to transform it into a functional, reliable automotive component meeting engineering specifications. These steps are not optional extras; they are integral to the manufacturing workflow and significantly impact the final mechanical properties, dimensional accuracy, surface quality, and overall performance of the part. Understanding this workflow is vital for both engineers designing the parts and procurement teams sourcing them, as post-processing contributes significantly to the final cost and lead time.
Typical Post-Processing Workflow for LPBF Aluminum Parts:
- Stress Relief (Optional but Recommended):
- Syfte: The rapid heating and cooling cycles inherent in LPBF create significant residual stresses within the printed part, particularly when attached to the rigid build plate. These stresses can cause distortion or cracking, especially after the part is removed from the plate or during subsequent machining. A stress relief heat treatment cycle at a moderate temperature helps to relax these internal stresses without significantly altering the microstructure.
- Process: Typically involves heating the part (while still attached to the build plate) in a furnace under a controlled atmosphere (e.g., Argon) to a temperature below the aging temperature (e.g., 200°C – 300°C for AlSi10Mg) for a specific duration (e.g., 1-2 hours), followed by slow cooling. Exact parameters depend on the alloy and part geometry.
- Benefit: Improves dimensional stability for subsequent steps and reduces risk of cracking.
- Removal from Build Plate:
- Process: The part, often printed on a thick metal build plate, needs to be separated. Common methods include:
- Wire Electrical Discharge Machining (Wire EDM): Precise method, minimal force applied to the part, good for delicate structures. Leaves a smooth cut surface.
- Bandsågning: Faster and cheaper for less critical applications or parts with robust bases, but less precise and can induce some stress.
- Maskinbearbetning: Milling the base of the part off the plate.
- Consideration: The chosen method depends on part geometry, required precision, and cost targets.
- Process: The part, often printed on a thick metal build plate, needs to be separated. Common methods include:
- Borttagning av stödstruktur:
- Syfte: Removing the temporary support structures required during the printing process for overhanging features.
- Metoder:
- Manuell borttagning: Breaking off supports using pliers, cutters, or hand tools. Only suitable for easily accessible, non-critical supports. Can leave rough witness marks.
- CNC Machining: Milling or grinding away support structures. More precise, better surface finish, necessary for supports in critical areas or those integrated closely with the part geometry.
- Wire EDM / Grinding: Sometimes used for intricate or hard-to-reach supports.
- Utmaning: Can be labor-intensive and time-consuming, especially for complex parts with extensive internal supports. DfAM principles aimed at minimizing supports pay dividends here. Requires skilled technicians to avoid damaging the part surface.
- Heat Treatment (Critical for Final Properties):
- Syfte: To achieve the desired final mechanical properties (strength, hardness, ductility) specified for the alloy (AlSi10Mg or A7075). The as-built microstructure is typically not optimal.
- Process (T6 Temper Example): The most common temper for these alloys involves:
- Lösningsglödgning: Heating the part to a high temperature (e.g., ~515-540°C for AlSi10Mg, ~460-490°C for A7075) for a specific time (e.g., 1-6 hours) to dissolve alloying elements into a solid solution. Requires precise temperature control and often a controlled atmosphere (inert gas or vacuum) to prevent oxidation.
- Släckning: Rapidly cooling the part (typically in water, sometimes polymer or forced air) to “freeze” the dissolved elements in solution. Quench speed is critical and can affect distortion.
- Artificial Aging (Precipitation Hardening): Reheating the part to a lower temperature (e.g., ~160-180°C for AlSi10Mg, ~120-150°C for A7075 T6, or multi-stage cycles for T7x tempers) for an extended period (e.g., 4-24 hours). This causes fine precipitates of alloying elements to form within the aluminum matrix, significantly increasing strength and hardness.
- Importance: This step is absolutely crucial. Without proper heat treatment, the 3D printed aluminum part will not meet the expected performance characteristics of the alloy. Precise control over temperatures, times, quench rates, and furnace atmosphere is essential. This often requires specialized B2B heat treatment service providers with experience in AM parts. Variations in T6 parameters or alternative tempers (like T7x for improved SCC resistance in A7075) must be clearly specified.
- CNC Machining (for Precision):
- Syfte: To achieve tight dimensional tolerances, specific geometric features (e.g., precisely round holes, flat mating surfaces), and smooth surface finishes on critical interfaces that cannot be achieved by the AM process alone.
- Process: Utilizes multi-axis milling machines, lathes, or grinders to selectively remove material from designated areas (where machining stock was added in the design). Requires careful setup using defined datum features.
- Omfattning: Typically applied to mounting points, bearing bores, sealing surfaces, and any feature requiring GD&T controls beyond the capability of as-built AM.
- Surface Finishing & Cleaning:
- Syfte: To improve surface quality (aesthetics and function), remove loose powder, prepare for coating, or enhance corrosion/wear resistance.
- Common Methods:
- Bead Blasting / Sand Blasting: Propels media (glass beads, ceramic, grit) at the surface to create a uniform, clean, matte finish. Removes minor surface imperfections and residual powder. Most common basic finish.
- Tumbling / Vibratory Finishing: Uses abrasive media in a vibrating or tumbling barrel to deburr edges and achieve a smoother, more uniform finish, especially on smaller parts.
- Polering: Mechanical or electrochemical polishing can achieve very smooth, mirror-like finishes where required (less common for chassis parts unless for specific aesthetic or fluid-flow reasons).
- Anodizing: An electrochemical process that creates a hard, corrosion-resistant oxide layer on the aluminum surface. Can also be dyed various colors. Often specified for improved durability and environmental protection.
- Painting / Powder Coating: Applying organic coatings for corrosion protection and aesthetics. Requires proper surface preparation.
- Cleaning: Final cleaning steps to remove any machining fluids, blasting media, or contaminants before inspection and packaging.
- Inspection and Quality Assurance:
- Syfte: Final verification that the part meets all dimensional, material, and surface specifications outlined in the engineering drawing and procurement requirements.
- Metoder: Dimensional inspection (CMM, 3D scanning), surface roughness measurement, material verification (e.g., Positive Material Identification – PMI), visual inspection, potentially NDT (Non-Destructive Testing, like CT scanning for internal porosity if required for highly critical parts).
The complexity and sequence of these post-processing steps highlight why metal AM is often considered a multi-stage manufacturing solution rather than a single-step process. Each step adds cost and time, emphasizing the importance of DfAM to minimize complexity (e.g., reducing supports) and the need for reliable, capable B2B service providers for heat treatment, machining, and finishing operations. Accurate quoting requires consideration of this entire workflow.
Common Challenges in Aluminum AM for Chassis Parts and Mitigation Strategies
While metal additive manufacturing offers transformative potential for lightweight aluminum chassis parts, it’s not without its challenges. Engineers, operators, and procurement managers should be aware of potential issues that can arise during the printing and processing of AlSi10Mg and A7075. Fortunately, with process understanding, careful control, high-quality materials, and capable equipment, these challenges can be effectively mitigated. Partnering with experienced AM suppliers is often key to navigating these complexities successfully.
1. Residual Stress and Warpage:
- Utmaning: The intense, localized heating by the laser and subsequent rapid cooling creates significant temperature gradients within the part and between the part and the build plate. This leads to internal residual stresses. If these stresses exceed the material’s yield strength at elevated temperature, they can cause:
- Warpage/Distortion: The part bends or twists, deviating from the intended geometry, especially after removal from the build plate. Large, flat sections or asymmetric designs are particularly susceptible.
- Cracking: In susceptible alloys (like high-strength A7075) or poorly designed geometries, stress can lead to cracks forming during the build or cooling.
- Build Failure: Severe warpage can cause the recoater blade (which spreads the next powder layer) to collide with the part, potentially damaging both and aborting the build.
- Mitigation Strategies:
- Build Plate Heating: Pre-heating the build plate (a feature on many advanced industrial printers like those offered by Met3dp) reduces the temperature gradient between the part and the plate, significantly lowering residual stress. Temperatures of 100°C – 200°C are common for aluminum.
- Optimized Scan Strategies: Using specific laser scanning patterns (e.g., island scanning, checkerboard patterns) helps distribute heat more evenly and reduce localized stress buildup.
- Support Structure Strategy: Well-designed supports not only anchor the part but also help conduct heat away and resist warping forces.
- DfAM: Avoiding large, unsupported flat areas; incorporating gradual transitions; orienting the part optimally.
- Process Simulation: Software tools can predict areas of high stress and potential distortion, allowing for design or orientation adjustments beforehand.
- Stress Relief Heat Treatment: Performing a stress relief cycle before removing the part from the build plate is highly effective.
2. Porosity:
- Utmaning: The presence of small voids or pores within the printed material. Porosity acts as stress concentrators, degrading mechanical properties, particularly fatigue strength, ductility, and fracture toughness – all critical for reliable chassis components.
- Types and Causes:
- Keyhole Porosity: Caused by excessive laser energy density, which vaporizes metal and creates unstable melt pool dynamics, trapping gas. Often appears as small, spherical pores.
- Lack-of-Fusion Porosity: Caused by insufficient energy density, preventing complete melting and fusion between adjacent scan tracks or subsequent layers. Often appears as irregular-shaped voids.
- Gas Porosity: Caused by dissolved gases (e.g., hydrogen in aluminum alloys, or entrapped Argon from the build atmosphere) coming out of solution during solidification, or from moisture contamination in the powder. Often spherical.
- Mitigation Strategies:
- Processparameteroptimering: Developing and precisely controlling laser power, scan speed, hatch spacing, and layer thickness is crucial to achieve stable melting and full fusion. This requires significant expertise and process development.
- High-Quality Powder: Using powder with high purity, low internal porosity, controlled PSD, good sphericity, and crucially, low moisture content is paramount. Sourcing from reputable suppliers like Met3dp, who utilize advanced atomization (VIGA, PREP) and stringent quality control, minimizes powder-related defects. Proper powder storage and handling (e.g., drying, sieving) are also vital.
- Inert Atmosphere Control: Maintaining a high-purity Argon atmosphere (<1000 ppm Oxygen, ideally lower) in the build chamber prevents oxidation and reduces gas pickup by the melt pool. Proper gas flow dynamics are also important.
- NDT Inspection: For highly critical parts, non-destructive testing methods like X-ray Computed Tomography (CT scanning) can be used to detect and quantify internal porosity, though this adds significant cost.
3. Support Structure Removal Difficulties:
- Utmaning: While necessary, support structures can be challenging and time-consuming to remove, especially from complex internal geometries often found in topology-optimized chassis parts. Improper removal can damage the part surface, leave undesirable witness marks, or even break delicate features.
- Mitigation Strategies:
- DfAM for Support Reduction: Designing self-supporting angles (>45°), using optimal part orientation, and choosing geometries that minimize overhangs.
- Optimized Support Design: Using specialized software to generate supports that are strong enough during the build but easier to remove (e.g., using conical or breakable connection points, varying support density, using specific support types like tree supports).
- Material Choice for Supports: Sometimes, using different parameters or slightly modified material for supports can aid removal (less common in direct metal printing).
- Post-Processing Methods: Utilizing appropriate removal techniques (manual, machining, EDM) based on accessibility and part requirements. Planning for access during the design phase.
4. Powder Handling and Management:
- Utmaning: Fine aluminum powders are reactive and pose a potential flammability or explosion hazard if not handled correctly (especially when dispersed in air). Maintaining powder quality (preventing contamination, moisture pickup, oxidation) throughout its lifecycle (storage, loading, printing, reclaiming/sieving, reuse) is critical for consistent part quality.
- Mitigation Strategies:
- Safety Protocols: Strict adherence to safety procedures for powder handling, storage, and equipment cleaning (grounding, inert atmospheres, appropriate PPE, ATEX-rated vacuum cleaners).
- Powder Management Systems: Utilizing closed-loop powder handling systems (offered with many industrial printers) minimizes operator exposure and contamination risk.
- Powder Quality Control: Regularly testing and monitoring powder properties (PSD, chemistry, flowability, moisture) especially when recycling powder. Establishing clear criteria for powder reuse limits.
- Traceability: Maintaining records of powder batches used for specific builds, crucial for quality assurance in automotive applications. Reliable AM suppliers must demonstrate robust powder management practices.
5. Anisotropy:
- Utmaning: Mechanical properties (e.g., strength, ductility) of AM parts can sometimes vary depending on the direction relative to the build layers (e.g., properties in the Z-direction might differ from those in the XY plane). This is due to the columnar grain structure that can form during solidification and potential micro-porosity alignment.
- Mitigation Strategies:
- Parameter Optimization: Fine-tuning parameters can influence microstructure and reduce anisotropy.
- Värmebehandling: Post-process heat treatments can help homogenize the microstructure and reduce directional property variations.
- Design & Testing: Understanding potential anisotropy and orienting the part such that critical stresses are aligned with the stronger direction. Conducting mechanical testing on coupons printed in different orientations to characterize material behavior accurately.
Successfully navigating these challenges requires a combination of advanced technology, process expertise, high-quality materials, and rigorous quality control. Automotive companies looking to leverage aluminum AM for chassis parts should seek B2B suppliers who demonstrate a deep understanding of these issues and have implemented robust mitigation strategies, ensuring the delivery of reliable, high-performance components.
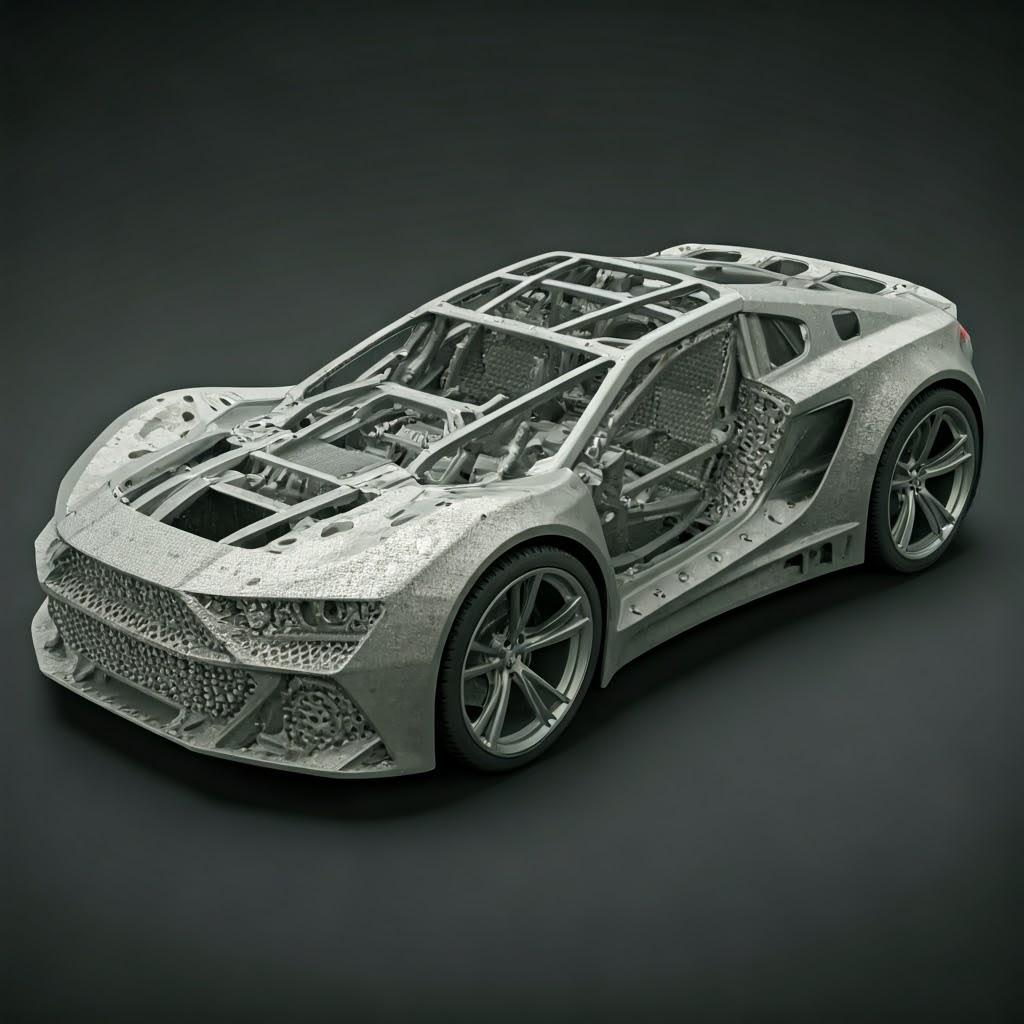
Selecting the Right Metal 3D Printing Service Provider for Automotive Needs
Choosing the right manufacturing partner is a critical decision, especially when adopting advanced technologies like metal additive manufacturing for demanding applications such as automotive chassis components. The quality, reliability, and performance of the final part are directly linked to the capabilities and expertise of the service provider. For procurement managers and engineering teams evaluating potential B2B suppliers for AlSi10Mg or A7075 chassis parts, a thorough qualification process focusing on technical competence, quality systems, and proven experience is essential. Simply choosing the lowest bidder without considering these factors can lead to costly delays, subpar parts, and project failures.
Here’s a checklist of key criteria to consider when evaluating and selecting a metal AM service provider for automotive chassis applications:
Supplier Evaluation Checklist for Automotive Aluminum AM:
Evaluation Criterion | Key Considerations & Questions to Ask | Importance (High/Med/Low) | Anteckningar |
---|---|---|---|
1. Technical Expertise & Support | Do they have experienced AM engineers and materials scientists? Can they provide DfAM guidance? Do they understand automotive load cases and requirements? What is their problem-solving process? Do they offer application development? | Hög | Look for partners, not just printers. Expertise in processing challenging alloys like A7075 is crucial. Collaborative partners like Met3dp offer deep expertise stemming from their integrated approach. |
2. Machine Capabilities & Technology | What specific AM technology do they use (LPBF is standard for this)? What machine manufacturers and models? What is the build volume capacity (suitable for chassis part size)? Machine maintenance and calibration records? | Hög | Ensure technology matches requirements. Well-maintained, industrial-grade machines (like Met3dp’s robust systems known for accuracy and reliability) are essential for consistent quality. Explore their specific tryckmetoder. |
3. Material Capabilities & Powder Quality Control | Do they offer the specific alloys needed (AlSi10Mg, A7075)? Where do they source powder? Is it certified? What are their powder handling, storage, testing, and traceability procedures (crucial for quality & safety)? | Hög | Powder quality is non-negotiable. Suppliers with strong powder QC (in-house testing, batch tracking, controlled recycling) are preferred. Met3dp’s advantage lies in manufacturing its own high-quality powders using advanced atomization. |
4. Efterbearbetningsmöjligheter | What steps are done in-house vs. outsourced (Heat Treat, Machining, Finishing)? Equipment calibration (furnaces)? Expertise with specific Al heat treatments (T6, T7x)? Multi-axis CNC capabilities? Finishing options (anodizing)? | Hög | In-house capabilities often allow better control over workflow, quality, and lead time. Verify expertise, especially for critical heat treatment cycles. Ensure machining can meet tolerance requirements. |
5. Quality Management System (QMS) & Certifications | Are they ISO 9001 certified? Is IATF 16949 certification held or pursued (highly desirable for automotive)? AS9100 (if aerospace crossover)? Can they provide material certs, CofCs, inspection reports? PPAP experience? | Hög | Robust QMS demonstrates commitment to quality and process control. Certifications provide external validation. Automotive requires stringent documentation and traceability. |
6. Metrology & Inspection | What inspection equipment do they have (CMM, 3D scanners, surface profilometers)? Calibration records? Can they provide detailed inspection reports against drawings/GD&T? NDT capabilities (CT, FPI) if required? | Hög | Verification is key. Ensure the supplier can measure and validate critical features to the required accuracy. |
7. Track Record & Experience | Have they produced similar parts (size, complexity, material) before? Can they provide relevant case studies or references (respecting NDAs)? Experience in the automotive sector? | Medelhög-Hög | Proven experience reduces risk. Automotive-specific experience implies understanding of sector requirements (quality, timelines). |
8. Capacity, Lead Time & Communication | What is their current capacity? Can they meet your volume requirements and project timelines? How responsive are they to inquiries and technical questions? What is their project management approach? | Medelhög-Hög | Ensure capacity aligns with needs. Realistic lead time estimates and proactive communication are vital for project planning. |
9. Cost & Value Proposition | Is their pricing transparent and competitive? Does the quote clearly break down costs (setup, material, print, post-processing)? Do they offer value beyond just price (expertise, support, reliability)? | Medium | Consider total cost of ownership and value, not just the initial quote. Cheapest is rarely best in high-stakes AM. |
10. Location & Logistics | Where are they located? Does proximity matter for collaboration or shipping times/costs? Do they have experience with international shipping and automotive logistics requirements if applicable? | Låg-Medium | Less critical with global shipping, but proximity can sometimes aid collaboration or reduce transit times. |
11. Partnership Approach & Culture | Are they willing to collaborate closely? Are they transparent about challenges? Do they align with your company’s values regarding quality and innovation? | Medium | A good cultural fit and a true partnership approach can be invaluable for complex projects, fostering innovation and efficient problem-solving. Explore how a company presents itself, for instance, on its Om oss sida. |
Export to Sheets
The Qualification Process:
- Request for Quotation (RFQ): Provide detailed RFQ packages including clear CAD models, technical drawings with tolerances and specifications, material requirements, volume, and delivery timelines.
- Supplier Audit: For critical components, conducting an on-site or thorough virtual audit is highly recommended to verify capabilities, processes, and quality systems firsthand.
- Benchmark Parts: Consider ordering small test parts or benchmark geometries from shortlisted suppliers to directly compare quality, accuracy, and finish before committing to a larger production order.
- References: Check references from other customers, particularly those in the automotive or similar demanding industries.
Selecting the right metal AM service provider is a strategic decision that goes beyond simple procurement. It’s about finding a capable B2B partner who can reliably deliver high-quality, mission-critical components like lightweight aluminum chassis parts, contributing to the overall success of your automotive project. Companies like Met3dp, offering integrated solutions encompassing advanced powder products, industry-leading printers, and deep application expertise, represent the type of comprehensive partner needed to navigate the complexities of automotive AM successfully.
Cost Factors and Lead Time Considerations for 3D Printed Chassis Parts
While the technical advantages of 3D printed aluminum chassis parts are compelling, a realistic understanding of the associated costs and lead times is essential for effective project planning, budgeting, and procurement strategy. Unlike traditional mass production techniques like casting where tooling dominates initial costs, AM costs are primarily driven by material consumption, machine time, and labor-intensive post-processing.
Breakdown of Cost Factors in Metal AM:
- Material Cost:
- Powder Type: High-performance alloys like A7075 are typically more expensive than standard AlSi10Mg due to alloying elements and manufacturing complexity.
- Powder Consumption: This includes the volume of the final part plus the volume of support structures required. Efficient DfAM and orientation strategies minimize support material.
- Powder Condition & Recycling: The cost includes not just virgin powder but also factors related to powder sieving, testing, refreshing (mixing virgin and used powder according to strict ratios), and eventual retirement of powder batches. Strict quality control adds cost but ensures part integrity. Wholesale buyers planning larger volumes should discuss powder lifecycle management with suppliers.
- Maskintid:
- Build Preparation: Time taken for slicing the CAD file, generating support strategies, setting up the build layout (nesting multiple parts if possible), and loading the machine.
- Printing Time: The actual time the machine spends fusing powder layers. Primarily driven by the height of the build (number of layers) and the volume/area to be scanned per layer. Complexity (e.g., intricate lattices) and the number of lasers on the machine also play a role. Larger/taller chassis parts inherently take longer.
- Machine Depreciation & Operational Costs: Industrial metal AM systems are significant capital investments, and their hourly operating rates reflect depreciation, energy consumption, inert gas usage, filters, maintenance, and software licenses.
- Kostnader för arbetskraft:
- Skilled Technicians: Significant skilled labor is involved throughout the process:
- Machine operation and monitoring.
- Build removal and cleanup.
- Support structure removal (often a major labor component, especially for complex parts).
- Post-processing tasks (loading/unloading furnaces, setting up CNC machines, manual finishing, inspection).
- Engineering & Quality Assurance: Time spent by engineers on DfAM, build preparation, process optimization, and by QA personnel on inspection and documentation.
- Skilled Technicians: Significant skilled labor is involved throughout the process:
- Kostnader för efterbearbetning:
- Stress Relief & Heat Treatment: Furnace time, energy, controlled atmosphere gas consumption. Requires specialized, calibrated equipment.
- CNC Machining: Machine time on multi-axis mills or lathes, tooling costs, programming time. Costs increase significantly with the number of features requiring machining and the tightness of tolerances.
- Ytbehandling: Costs associated with bead blasting, anodizing, painting, etc., including labor and materials/chemicals.
- Outsourcing: If certain post-processing steps are outsourced (common for specialized heat treatment or finishing), the supplier’s costs plus margin are included.
- Quality Assurance & Inspection:
- Time and equipment costs for dimensional inspection (CMM, scanning), surface roughness checks, material verification, and any required NDT. Documentation effort (e.g., for PPAP) also adds cost.
- Overheads & Profit: General business operational costs and the supplier’s profit margin.
Factors Influencing Overall Cost:
- Part Complexity & Size: Larger, more complex parts consume more material and machine time. Highly complex topology-optimized or latticed parts may have longer print times and significantly more effort in support removal and inspection.
- Material Choice: A7075 > AlSi10Mg.
- Tolerance & Surface Finish Requirements: Tighter tolerances and smoother finishes necessitate more extensive (and costly) post-machining and finishing.
- Build Orientation & Nesting: Strategic placement on the build plate can minimize support needs and maximize the number of parts per build (nesting), distributing setup costs across more units.
- Order Volume: While AM doesn’t have the dramatic economies of scale seen with casting (due to tooling amortization), some cost efficiencies exist for larger batches through optimized nesting, streamlined post-processing workflows, and distributed setup costs. However, the cost per part tends to plateau rather than drop exponentially.
Lead Time Considerations:
Lead time is the total time from order placement to part delivery. It’s crucial to have realistic expectations, as metal AM involves multiple sequential steps.
Typical Lead Time Breakdown:
- Pre-Processing (1-5 days):
- Order confirmation, final design review, CAD preparation, build simulation (optional), scheduling/queuing.
- Printing (1-7+ days):
- Build setup, actual printing time (can range from <1 day for small parts to many days for large/tall chassis components or full build plates).
- Post-Processing (3-15+ days):
- Cooling, stress relief (if needed, ~1 day).
- Part removal, cleaning, support removal (can be 1-3+ days depending on complexity).
- Värmebehandling: Furnace cycles plus heating/cooling can take 1-3 days. Scheduling into furnace batches can add waiting time.
- CNC Machining: Setup and machining time varies greatly (1-5+ days depending on complexity and features). Scheduling on machines is a factor.
- Ytbehandling: Anodizing, painting etc., add several days depending on the process and outsourcing.
- Quality Inspection & Shipping (1-3 days):
- Final inspection, documentation, packaging, and transit time.
Estimated Total Lead Times (Guideline):
- Prototypes (1-5 parts): Vanligtvis 1 to 3 weeks, depending heavily on size, complexity, and required post-processing.
- Low Volume Production (10-100 parts): Vanligtvis 3 to 6+ weeks, influenced by batching efficiencies, machine availability, and the full extent of post-processing requirements for all parts.
Factors Influencing Lead Time:
- Part size and height (primary driver of print time).
- Part complexity (impacts support removal and potentially machining).
- Required post-processing steps (each adds time).
- Supplier’s current workload and machine availability (queue time).
- Order quantity.
- Clarity and completeness of specifications (reduces delays).
Optimizing Cost and Lead Time:
- DfAM: Designing for minimal supports, self-supporting angles, and reduced complexity where possible.
- Nesting: Efficiently packing multiple parts onto a single build plate.
- Clear Specifications: Providing unambiguous drawings and requirements avoids delays and rework.
- Realistic Tolerances: Specify tight tolerances only where functionally necessary.
- Communication: Maintain open communication with the supplier regarding timelines and potential issues.
Understanding the interplay of these factors allows automotive procurement teams and engineers to budget appropriately, set realistic project timelines, and work collaboratively with their AM partners to achieve optimal results for their lightweight aluminum chassis projects.
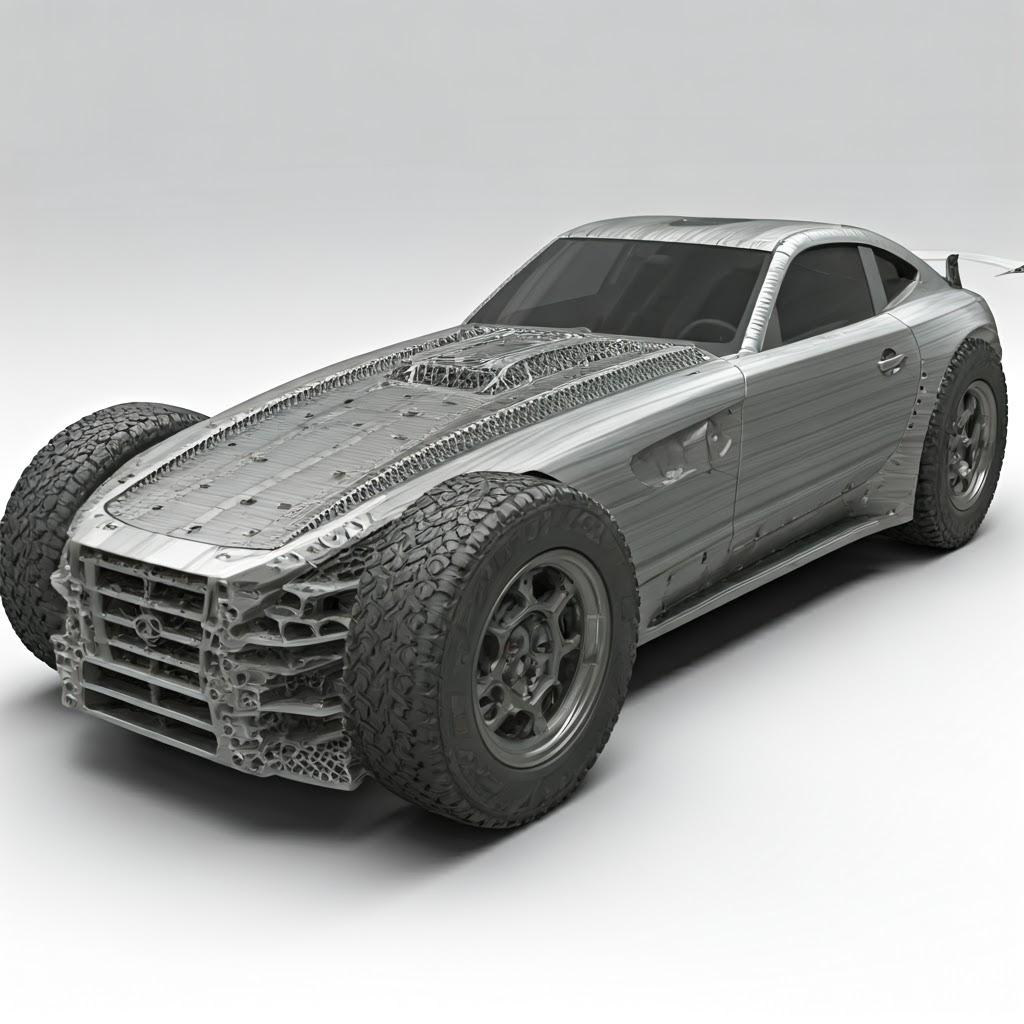
Frequently Asked Questions (FAQ) about 3D Printing Aluminum Chassis Parts
As metal additive manufacturing gains traction in the automotive industry, engineers and procurement managers often have specific questions about its application for critical components like chassis parts. Here are answers to some common queries:
1. Are 3D printed aluminum chassis parts (AlSi10Mg, A7075) strong and reliable enough for automotive use?
- Svar: Yes, when designed, manufactured, and processed correctly, 3D printed aluminum chassis parts can meet and often exceed the performance requirements for demanding automotive applications.
- Materialegenskaper: Post-heat treatment (e.g., T6 temper), AlSi10Mg offers properties comparable to common aluminum casting alloys, while A7075 achieves very high strength levels, approaching those of some steels but at significantly lower weight. These properties (tensile strength, yield strength, fatigue life) are well-characterized.
- Designoptimering: DfAM techniques like topology optimization allow engineers to create parts that are not only lighter but also potentially stiffer and stronger than their conventionally manufactured counterparts by placing material only where it’s needed for load paths.
- Processtyrning: Achieving these properties reliably depends heavily on using high-quality powder (like those from Met3dp), precise process parameter control during printing (using reliable machines), and meticulous execution of post-processing steps, especially heat treatment.
- Validation: As with any critical component, rigorous physical testing and validation (static load tests, fatigue testing, durability cycles, potentially crash testing depending on the part) are essential to confirm performance against design specifications and automotive standards before vehicle integration. Many motorsport teams and specialized vehicle manufacturers already successfully utilize AM aluminum chassis parts in competition and road use.
2. How does the cost of 3D printing aluminum chassis parts compare to traditional methods like casting or machining?
- Svar: The cost comparison depends heavily on part complexity, production volume, and tooling considerations. There’s no single answer, but here’s a general guideline:
- Prototyping & Very Low Volume (1-20 parts): AM is often significantly cheaper and faster than casting or forging because it eliminates the need for expensive tooling (molds, dies). Machining from billet can be competitive for simpler shapes but becomes very expensive for complex geometries due to material waste and machine time. AM excels here.
- Low-to-Mid Volume (20-500 parts): This is often the “sweet spot” where AM remains cost-competitive, especially for complex parts where tooling costs for casting would be high and difficult to amortize over the limited volume. The benefits of part consolidation and lightweighting through AM can also provide added value offsetting a potentially higher per-part price.
- High Volume (1000+ parts): For simpler shapes amenable to casting or forging, traditional methods with amortized tooling costs typically become significantly cheaper per part than AM. AM’s current build speeds and process costs generally make it less economical for true mass production of chassis components unless the design complexity achievable only through AM provides an overwhelming performance or consolidation advantage that justifies the cost.
- Complexity Factor: For extremely complex geometries (e.g., heavily topology-optimized parts with internal lattices), AM might be the only feasible manufacturing method, making direct cost comparison difficult.
3. What is the typical lead time for obtaining prototype or production aluminum chassis parts via AM?
- Svar: Lead times are variable but generally fall into these ranges:
- Functional Prototypes (1-5 units): Vanligtvis 1 to 3 weeks. This allows time for printing, essential post-processing (support removal, heat treatment), and basic inspection. Highly complex parts or those requiring extensive machining will be at the longer end of this range or potentially exceed it.
- Low Volume Production Batches (10-100 units): Usually 3 to 6 weeks or longer. This accounts for potential queue times, batching parts for efficient printing and post-processing (especially heat treatment and finishing), and more rigorous quality assurance procedures often required for production parts. Lead times are highly dependent on the supplier’s capacity and the full post-processing workflow.
- Key Influencers: Part size/height (print time), complexity (support removal/machining time), required post-processing steps, batch size, and supplier workload are the main drivers. Always request specific lead time estimates from potential suppliers based on your final part design and requirements.
4. Can complex internal channels, for example, for cooling or fluid flow, be integrated into 3D printed chassis parts?
- Svar: Absolutely. This is one of the significant advantages of metal additive manufacturing.
- Designfrihet: The layer-by-layer process allows for the creation of intricate internal channels and cavities with complex paths that would be impossible or extremely difficult to produce using traditional methods like casting (requires complex cores) or machining (requires drilling straight holes or splitting/brazing parts).
- Applikationer: This capability can be used to integrate cooling channels directly into structural chassis components near heat sources (e.g., EV battery interfaces, power electronics mounts, integrated heat sinks within brackets), potentially saving weight and space by eliminating separate cooling systems or hoses. Hydraulic fluid pathways could also potentially be integrated.
- Överväganden: Designing these channels requires careful DfAM: ensuring self-supporting geometries or planning for internal support removal (if necessary and accessible), providing powder drainage paths, and considering surface roughness inside the channel which might affect flow characteristics. Post-processing like chemical flushing or abrasive flow machining might be needed to achieve desired internal surface finish.
Conclusion: Accelerating Automotive Lightweighting with Aluminum Additive Manufacturing
The relentless drive towards lighter, faster, more efficient, and sustainable vehicles positions lightweighting as a central pillar of modern automotive engineering. Within this landscape, aluminum additive manufacturing has emerged not just as a prototyping tool, but as a powerful and viable manufacturing solution for producing highly optimized, performance-critical chassis components. By leveraging alloys like the versatile AlSi10Mg and the high-strength A7075, AM enables engineers to break free from the constraints of traditional manufacturing, unlocking unprecedented design freedom.
The ability to employ topology optimization and generative design leads to radically efficient structures, placing material only where necessary, while the integration of lattice structures further pushes the boundaries of stiffness-to-weight ratios. Part consolidation reduces complexity, assembly time, and potential failure points. For development teams, the speed of AM accelerates iteration cycles, allowing for faster validation and time-to-market. For procurement managers, AM offers a tooling-less production route, making low-to-mid volume manufacturing of complex parts economically feasible and enabling more agile supply chain strategies.
However, realizing these benefits demands a holistic understanding of the entire process. Effective Design for Additive Manufacturing (DfAM) is paramount. Careful material selection, meticulous process control during printing, and rigorous, multi-step post-processing – particularly heat treatment and precision machining – are non-negotiable for achieving the required mechanical properties, dimensional accuracy, and surface finish demanded by automotive applications. Navigating potential challenges like residual stress, porosity, and support removal requires expertise and robust quality management.
Choosing the right manufacturing partner becomes a strategic imperative. Look beyond mere printing capabilities to evaluate technical expertise, powder quality control, post-processing proficiency, quality systems, and a collaborative approach.
Metal additive manufacturing is no longer a future promise; it’s a present-day enabler for innovation in automotive chassis design, particularly crucial for enhancing the performance and range of electric vehicles and pushing the limits in motorsport and specialized vehicle segments. As the technology continues to mature, its role in shaping the future of automotive structures will only grow.
For organizations looking to explore or implement aluminum additive manufacturing for lightweight chassis components, partnering with a knowledgeable and comprehensively equipped provider is key. Met3dp stands ready to assist, offering a complete ecosystem that includes industry-leading, reliable printing systems, advanced spherical metal powders manufactured in-house for optimal quality, and deep application expertise. We partner with automotive clients to navigate the complexities of AM, from design optimization to final part qualification, helping you accelerate your lightweighting goals and drive automotive innovation forward.
Contact Met3dp today to discover how our cutting-edge metal additive manufacturing solutions can power your next automotive project. Visit us at https://met3dp.com/ to learn more.
Dela på
MET3DP Technology Co, LTD är en ledande leverantör av lösningar för additiv tillverkning med huvudkontor i Qingdao, Kina. Vårt företag är specialiserat på 3D-utskriftsutrustning och högpresterande metallpulver för industriella tillämpningar.
Förfrågan för att få bästa pris och anpassad lösning för ditt företag!
Relaterade artiklar
Om Met3DP
Senaste uppdateringen
Vår produkt
KONTAKTA OSS
Har du några frågor? Skicka oss meddelande nu! Vi kommer att betjäna din begäran med ett helt team efter att ha fått ditt meddelande.
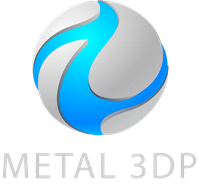
Metallpulver för 3D-printing och additiv tillverkning