3D Printed Corner Blocks for Aerospace Frames
Innehållsförteckning
Introduction: The Critical Role of Corner Blocks in Aerospace Structures
In the demanding world of aerospace engineering, every component matters. From the sprawling wings of a commercial airliner to the intricate framework of a satellite, structural integrity, weight efficiency, and unwavering performance are paramount. Among the many critical components that ensure the safety and reliability of aircraft and spacecraft are frame corner blocks. These seemingly simple parts play a fundamental role in joining structural members, distributing complex loads, and maintaining the overall shape and rigidity of the airframe or spaceframe. Traditionally manufactured through subtractive methods like CNC machining from billet or sometimes casting, the production of corner blocks often involves significant material waste, lengthy lead times, and design limitations imposed by the manufacturing process itself.
However, the advent of Additiv tillverkning av metall (AM), commonly known as metal 3D-utskrifter, is revolutionizing how these crucial components are designed, developed, and produced. By building parts layer by layer directly from digital models using high-performance metal powders, AM offers unprecedented opportunities to create lightweight, complex, and highly optimized corner blocks that were previously impossible or prohibitively expensive to manufacture. This technology allows engineers to rethink structural design, integrating functionality, reducing part count, and ultimately contributing to more efficient, higher-performing aerospace vehicles. For aerospace manufacturers, suppliers, and procurement managers, understanding the potential of 3D printed corner blocks is no longer just an option – it’s becoming a strategic imperative for staying competitive and pushing the boundaries of flight. This article delves into the world of 3D printed aerospace frame corner blocks, exploring their applications, the compelling reasons for adopting AM, the ideal materials like Scalmalloy® and Ti-6Al-4V, and the key considerations for leveraging this transformative technology effectively. We will explore how partners like Met3dp, with their advanced powder manufacturing and printing solutions, are enabling this shift towards next-generation aerospace components.
Applications: Where are 3D Printed Corner Blocks Utilized in Aerospace?
The versatility of metal additive manufacturing allows 3D printed corner blocks to be integrated into a wide array of aerospace structures, serving critical functions across various platforms. Their ability to be customized for specific load paths, geometries, and weight targets makes them invaluable in applications where traditional components might fall short. Key application areas include:
- Commercial Aircraft:
- Fuselage Frames: Joining longitudinal stringers and circumferential frames, providing structural continuity and load transfer points. Optimized designs can significantly reduce weight in these repetitive structures, contributing to fuel efficiency.
- Wing Structures: Connecting ribs and spars, particularly in complex joint areas near the fuselage or engine pylons where loads are high and geometry is intricate.
- Empennage (Tail Structures): Used in the joints of horizontal and vertical stabilizers, ensuring rigidity and aerodynamic stability.
- Interior Structures: Brackets and connectors for cabin monuments, cargo bay frames, and overhead bins, where lightweighting and part consolidation offer benefits. Bulk suppliers often seek cost-effective manufacturing for these numerous internal components.
- Defense Aircraft:
- Airframe Structures: Similar applications as commercial aircraft, but often with more demanding performance requirements regarding strength, fatigue life, and resilience under extreme G-loads.
- Internal Equipment Mounting: Creating custom brackets and nodes for mounting avionics, weapon systems, and other mission-critical equipment, often requiring complex geometries to fit within tight spaces.
- Unmanned Aerial Vehicles (UAVs): Lightweighting is critical for maximizing endurance and payload capacity. 3D printed corner blocks enable highly optimized, skeletal frame designs.
- Spacecraft and Satellites:
- Primary Structure Frames: Joining panels and trusses in satellite buses, landers, and launch vehicle stages. Weight reduction is paramount due to high launch costs.
- Payload Integration: Custom corner blocks and nodes for mounting sensitive instruments, antennas, and solar panels, ensuring precise alignment and structural integrity during launch and in-orbit operations.
- Truss Structures: Enabling the creation of complex, topology-optimized nodes for lattice structures used in booms, deployable systems, and large space frameworks.
- Helicopters and Rotorcraft:
- Cabin Frames: Joining elements of the main cabin structure, absorbing vibration, and providing attachment points.
- Tail Boom Structures: Connecting sections of the tail boom, requiring high fatigue strength and stiffness.
Industries and Functions:
The primary function of these corner blocks, regardless of the specific platform, remains consistent:
- Structural Joining: Securely connecting two or more structural members (beams, frames, spars, stringers, panels) at an intersection, typically a corner.
- Load Distribution: Transferring mechanical loads (tension, compression, shear, bending, torsion) efficiently between the connected members, preventing stress concentrations.
- Maintaining Geometry: Ensuring the structural assembly maintains its intended shape and dimensional stability under operational loads.
- Integration Points: Providing mounting locations for other components, systems, or fasteners.
Procurement managers and engineers in aerospace OEMs, Tier 1 suppliers, and MRO (Maintenance, Repair, Overhaul) organizations are increasingly specifying 3D printed corner blocks for both new designs and retrofitting existing platforms, driven by the performance and supply chain advantages offered by additive manufacturing. The ability to produce these parts on-demand, potentially closer to the point of need, also offers logistical benefits, especially for spare parts and repairs.
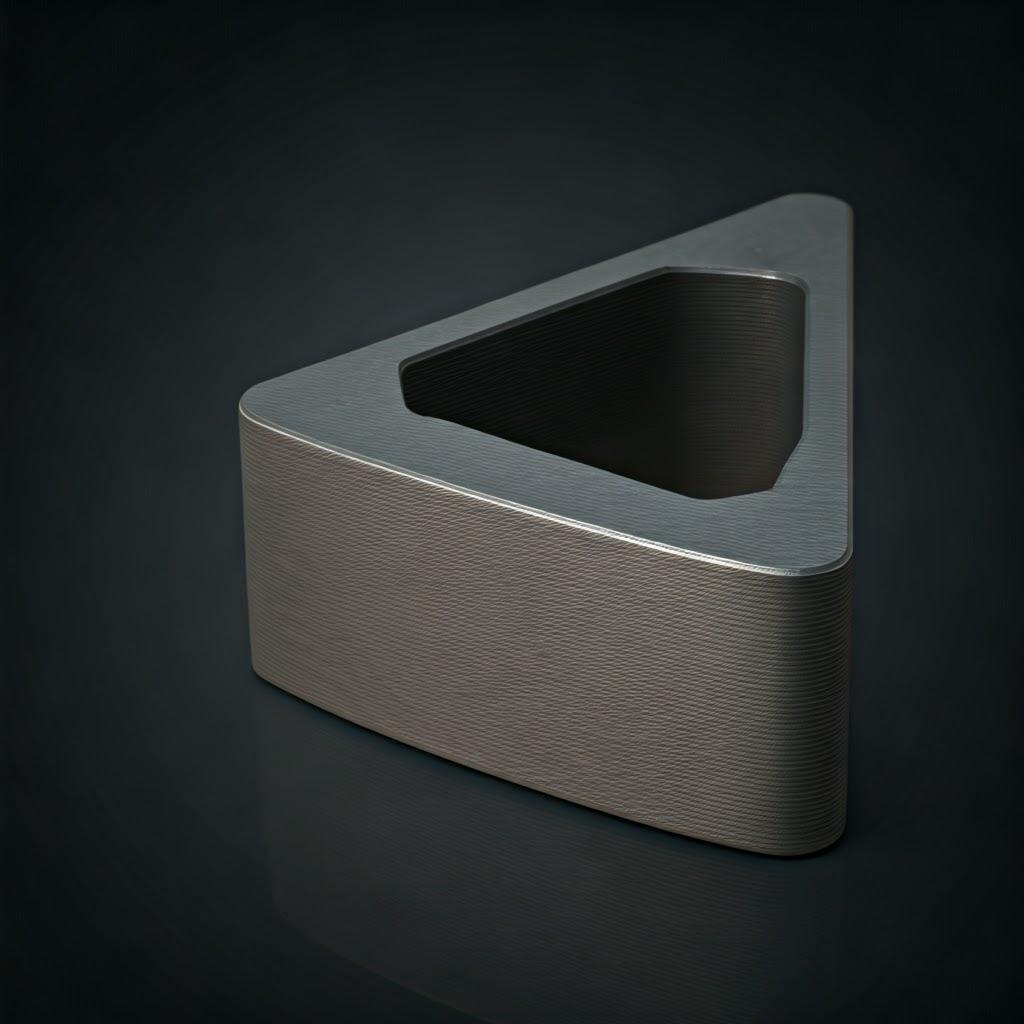
Why Metal 3D Printing for Aerospace Corner Blocks? Unlocking Performance Gains
While traditional manufacturing methods like CNC machining and casting have served the aerospace industry for decades, metal additive manufacturing presents a compelling suite of advantages, particularly for components like frame corner blocks. These benefits translate directly into improved aircraft performance, reduced operational costs, and more agile manufacturing processes.
Funktion | Traditional Manufacturing (CNC Machining/Casting) | Metal Additive Manufacturing (e.g., LPBF) | B2B Advantage |
---|---|---|---|
Designfrihet | Constrained by tool access, draft angles, mold complexity. Complex internal features are difficult/impossible. | Near-limitless geometric complexity. Enables topology optimization, lattice structures, internal channels, conformal designs. | Faster innovation cycles, creation of highly optimized, unique components. |
Viktminskning | Material removal from solid block (machining) leads to waste. Minimum wall thicknesses apply. Casting limitations. | Material added only where needed. Ideal for topology optimization, achieving significant weight savings (often 20-50%+). | Improved fuel efficiency, increased payload capacity, enhanced vehicle agility. |
Konsolidering av delar | Complex assemblies often require multiple parts joined by fasteners. | Ability to print multiple functional elements as a single, monolithic part. | Reduced assembly time/cost, fewer potential failure points (fasteners), simplified logistics & inventory. |
Utnyttjande av material | High “buy-to-fly” ratio (machining removes much material). Casting requires molds/tooling. | High material utilization (“near-net-shape” or net-shape printing), reducing expensive material waste (especially for Ti, Scalmalloy®). | Lower raw material costs, more sustainable manufacturing process. |
Ledande tidningar | Long lead times for tooling (casting), complex machining setups. Dependent on machine availability. | Rapid prototyping and production possible directly from CAD data. Reduced reliance on complex tooling. | Faster time-to-market for new designs, quicker replacement part availability, resilient supply chains. |
Anpassning | Costly and time-consuming for low-volume custom parts. | Ideal for producing unique or low-volume customized parts cost-effectively. | Enables bespoke solutions for specific missions, repairs, or platform variants. |
Leverantörskedjan | Often relies on specialized foundries or machine shops, potentially long supply chains. | Enables distributed manufacturing, potential for on-demand production closer to use. | Increased supply chain flexibility, reduced dependency on single suppliers, potential for digital inventory. |
Export to Sheets
Key Advantages Elaborated:
- Topology Optimization: This is arguably one of the most significant advantages of AM for structural parts like corner blocks. Engineers can use software algorithms to determine the most efficient material distribution to withstand specific load cases. This results in organic-looking, highly optimized shapes that place material precisely where it’s needed for strength and stiffness, while removing it from non-critical areas. This process is perfectly suited to the layer-by-layer nature of AM but often impossible or impractical to achieve with traditional methods. The result is maximum performance for minimum weight.
- Rapid Prototyping and Iteration: Before committing to expensive tooling or lengthy machining processes, AM allows engineers to quickly produce functional prototypes of corner block designs. These can be physically tested and validated, allowing for rapid design iterations and improvements. This accelerates the development cycle significantly, a crucial factor in the fast-paced aerospace sector. Wholesale buyers benefit from faster qualification of parts before committing to larger production runs.
- Handling Complex Geometries: Aerospace structures often involve intricate junctions where multiple members meet at complex angles. Machining these intersections from a solid block can be challenging and require multiple setups, increasing cost and time. AM can handle these complex node geometries inherently, often integrating features like smooth fillets and optimized load paths directly into the printed part.
- Reducing the Buy-to-Fly Ratio: Aerospace materials like titanium alloys and high-strength aluminum alloys (like Scalmalloy®) are expensive. CNC machining can easily result in 80-90% of the initial expensive material block being machined away as chips (a high buy-to-fly ratio). AM, being an additive process, typically uses material far more efficiently, significantly reducing raw material costs and waste, making it more sustainable and cost-effective, especially for complex parts.
For aerospace component suppliers and manufacturers looking to gain a competitive edge, embracing metal 3D printing for components like corner blocks offers a clear pathway to enhanced performance, reduced costs, and a more agile, resilient manufacturing strategy.
Material Focus: Scalmalloy® and Ti-6Al-4V for Demanding Aerospace Needs
The choice of material is critical for any aerospace component, and corner blocks are no exception. They must withstand significant static and dynamic loads, resist fatigue and corrosion, and perform reliably across a wide range of temperatures, all while being as light as possible. Metal additive manufacturing requires specialized metal powders, and for demanding aerospace applications like frame corner blocks, two materials stand out: Scalmalloy® and Ti-6Al-4V (Grade 5 Titanium). The quality and characteristics of the metal powder feedstock are paramount to achieving the desired mechanical properties and consistency in the final printed part.
Importance of High-Quality Metal Powders:
The success of metal AM relies heavily on the quality of the input material – the metal powder. Key powder characteristics influence the printing process and the final part’s properties:
- Sfäriskhet: Highly spherical powder particles ensure good flowability, which is crucial for uniformly spreading thin layers in the powder bed fusion process (like LPBF). Poor flowability can lead to uneven layers, voids, and defects in the final part.
- Fördelning av partikelstorlek (PSD): A controlled PSD ensures high packing density in the powder bed, leading to denser, stronger final parts with better surface finish. Too many fine particles can impede flowability, while too many large particles can lead to poor resolution and surface roughness.
- Purity and Chemistry: Consistent chemical composition, free from contaminants and oxides, is essential for achieving the desired mechanical properties (strength, ductility, fatigue resistance) and corrosion resistance. Impurities can act as crack initiation sites.
- Low Porosity/Gas Content: Powder particles should have minimal internal porosity. Trapped gas (like Argon used in atomization) can lead to porosity in the final part if not controlled, compromising mechanical performance.
Företag gillar Met3dp recognize the critical role of powder quality. Utilizing advanced powder production techniques such as Vacuum Induction Melting Gas Atomization (VIGA) och Process med roterande elektrod och plasma (PREP), Met3dp focuses on producing high-purity, highly spherical metal powders with controlled PSD. Their expertise ensures that the Scalmalloy® and Ti-6Al-4V powders supplied meet the stringent requirements for demanding applications, including aerospace. Their portfolio extends beyond these to include innovative alloys like TiNi, TiTa, TiAl, TiNbZr, CoCrMo, various stainless steels, and superalloys, showcasing their broad materials capability available through their produktutbud.
Scalmalloy®:
Developed specifically for additive manufacturing, Scalmalloy® is a high-performance aluminum-magnesium-scandium alloy. It offers properties superior to many traditional high-strength aerospace aluminum alloys, making it an excellent candidate for lightweight structural components.
- Viktiga egenskaper:
- High Specific Strength: Exceptional strength-to-weight ratio, exceeding that of many traditional aerospace aluminum alloys.
- Utmärkt svetsbarhet: Although primarily used in AM, its composition lends itself to good joining characteristics if needed post-printing.
- Good Ductility and Fatigue Strength: Offers good resistance to crack propagation under cyclic loading, crucial for aerospace components.
- Motståndskraft mot korrosion: Exhibits good resistance to corrosion.
- Utskriftsmöjlighet: Designed specifically for AM processes like LPBF, offering good processability.
- Why Use for Corner Blocks?
- Significant Weight Savings: Its primary advantage is enabling the design of much lighter corner blocks compared to traditional aluminum alloys, directly contributing to fuel savings or increased payload.
- Hög hållfasthet: Capable of handling significant structural loads despite its low density.
- Topology Optimization Synergy: Its properties are ideal for leveraging topology optimization to create highly efficient, complex geometries.
Ti-6Al-4V (Grade 5 Titanium):
This is the workhorse titanium alloy in the aerospace industry, widely used for decades due to its excellent combination of properties. It is readily available in powder form suitable for AM.
- Viktiga egenskaper:
- Högt förhållande mellan styrka och vikt: While denser than aluminum, it offers very high strength, making it efficient on a strength-per-unit-weight basis, especially at elevated temperatures.
- Utmärkt korrosionsbeständighet: Highly resistant to corrosion from jet fuel, de-icing fluids, saltwater, and atmospheric conditions.
- Good High-Temperature Performance: Retains significant strength at moderately elevated temperatures (up to around 300-400°C), better than aluminum alloys.
- Biokompatibilitet: (Though less relevant for corner blocks, it’s a key feature of the alloy).
- Well-Characterized: Extensive data exists on its performance, fatigue life, and behavior, making it a trusted material for critical applications.
- Why Use for Corner Blocks?
- Proven Aerospace Performance: Its long history and extensive use provide high confidence for critical structural applications.
- High Absolute Strength & Stiffness: Suitable for corner blocks subjected to very high loads or requiring high rigidity.
- Temperaturbeständighet: Ideal for applications near engines or other heat sources where aluminum alloys might soften.
- Corrosion Environments: Suitable for parts exposed to harsh environmental conditions.
Material Selection Considerations:
Faktor | Scalmalloy® -legering | Ti-6Al-4V | Decision Driver |
---|---|---|---|
Täthet | Lower (~2.67 g/cm³) | Higher (~4.43 g/cm³) | Weight is the absolute priority? Choose Scalmalloy®. |
Specifik styrka | Mycket hög | Hög | Need maximum strength for minimum weight? Scalmalloy® often wins. |
Max Service Temp. | Lower (typically < 150-200°C) | Higher (up to ~350-400°C) | Operating temperature dictates choice; Ti-6Al-4V for higher temps. |
Absolute Strength | High (for Aluminum) | Mycket hög | Extreme load requirements might favor Ti-6Al-4V’s higher ultimate strength. |
Cost (Powder) | High (Scandium content) | High (Titanium) | Both are premium materials; specific quotes needed. Scalmalloy® often higher. |
Maturity (AM Data) | Newer, but growing rapidly | Very Mature, extensive database | Risk aversion or need for deep historical data may favor Ti-6Al-4V. |
Utskriftsmöjlighet | Generally Good (designed for AM) | Good, but requires careful parameter control (residual stress) | Both are printable; process optimization is key for both. |
Export to Sheets
Choosing between Scalmalloy® and Ti-6Al-4V depends heavily on the specific requirements of the corner block application – the load cases, operating environment, weight targets, and cost constraints. Partnering with an experienced AM provider like Met3dp, who understands both the materials and the tryckmetoder, is crucial for making the optimal selection and ensuring the successful production of high-quality, reliable aerospace components. Sources and related content
Design Optimization: Leveraging Additive Manufacturing for Superior Corner Blocks
One of the most transformative aspects of using metal additive manufacturing for aerospace corner blocks lies in the ability to fundamentally rethink component design. Unlike traditional manufacturing methods that impose significant geometric constraints, AM liberates engineers to create forms driven purely by function and performance requirements. This practice, often termed Design for Additive Manufacturing (DfAM), is crucial for unlocking the full potential of 3D printing, especially for weight-critical, load-bearing components like aerospace corner blocks. Moving beyond simply replicating existing designs, DfAM enables the creation of superior components optimized for their specific application.
Key DfAM principles applicable to aerospace corner blocks include:
- Topology Optimization: This is perhaps the most powerful DfAM tool for structural components. Using specialized software (e.g., FEA-based optimization tools), engineers define the design space, load conditions (forces, pressures, moments), boundary constraints (attachment points), and performance targets (stiffness, stress limits). The software then iteratively removes material from non-critical areas, leaving behind an optimized load path structure.
- Benefit: Generates highly organic, lightweight structures that meet or exceed the performance of heavier, traditionally designed parts. Perfectly suited for Scalmalloy® and Ti-6Al-4V corner blocks where strength-to-weight is critical.
- Consideration: Optimized designs can be complex and may require careful validation through simulation and testing. Manufacturing requires precise AM process control.
- Lattice Structures and Infill: AM allows for the incorporation of internal lattice structures or variable density infill within the solid volume of the corner block. These cellular structures can significantly reduce weight while maintaining required stiffness and strength in specific directions.
- Benefit: Further weight reduction beyond surface optimization, potential for energy absorption, vibration damping, or facilitating thermal management if needed.
- Consideration: Designing effective lattices requires specialized software and understanding of their mechanical behavior. Ensuring powder removal from complex internal lattices is crucial during post-processing.
- Del Konsolidering: Analyze the corner block’s interface with adjacent structures. Can brackets, mounting features, or small adjoining parts be integrated directly into the 3D printed corner block?
- Benefit: Reduces part count, eliminates fasteners (potential failure points and weight addition), simplifies assembly, reduces logistical overhead (fewer part numbers to track for suppliers and procurement).
- Consideration: Increases the complexity of the single printed part. Requires careful analysis to ensure integrated features meet all functional requirements.
- Support Structure Minimization: AM processes like Laser Powder Bed Fusion (LPBF), commonly used for Scalmalloy® and Ti-6Al-4V, require support structures for overhanging features (typically below 45 degrees from horizontal) and to anchor the part to the build plate, managing thermal stresses. Designing parts to be self-supporting or minimizing the need for supports is a key DfAM strategy.
- Benefit: Reduces print time, material usage (supports are waste), and post-processing effort (support removal can be time-consuming and risk damaging the part). Improves surface finish on downward-facing surfaces.
- Consideration: May involve orienting the part differently on the build plate or adding features like chamfers and fillets to make overhangs self-supporting. Requires understanding the specific AM process limitations.
- Feature Resolution and Wall Thickness: Understand the minimum printable feature size, hole diameter, and wall thickness achievable with the chosen AM process and material. Design features accordingly.
- Benefit: Ensures manufacturability and prevents features from being lost or distorted during printing.
- Consideration: Minimum wall thickness is typically higher than feature resolution limits to ensure structural integrity and prevent distortion during printing and handling. For Scalmalloy® and Ti-6Al-4V via LPBF, thin walls might typically be in the 0.4mm – 1.0mm range depending on geometry and height.
- Internal Channels and Conformal Cooling: While less common for basic corner blocks, AM allows for the integration of complex internal channels if needed for thermal management, fluid flow, or routing wiring.
- Benefit: Enables multi-functional components where cooling or fluid transport is required near the structural joint.
- Consideration: Requires careful design to ensure channels are printable, inspectable, and easily cleared of residual powder.
- Designing for Post-Processing: Consider how the part will be handled, heat-treated, machined, and inspected after printing. Ensure critical features are accessible for machining or inspection tools. Add sacrificial material (machining allowance) where tight tolerances are required on specific surfaces.
- Benefit: Streamlines the post-processing workflow, reduces costs, and ensures final specifications can be met.
- Consideration: Requires close collaboration between design engineers and the manufacturing/post-processing teams.
By embracing these DfAM principles, engineers and designers working with 3D-utskrift av metall can move beyond simply substituting traditionally manufactured corner blocks and instead create truly innovative, high-performance components optimized for the demanding requirements of the aerospace industry. This requires a shift in mindset but yields substantial rewards in terms of weight, performance, and manufacturing efficiency.
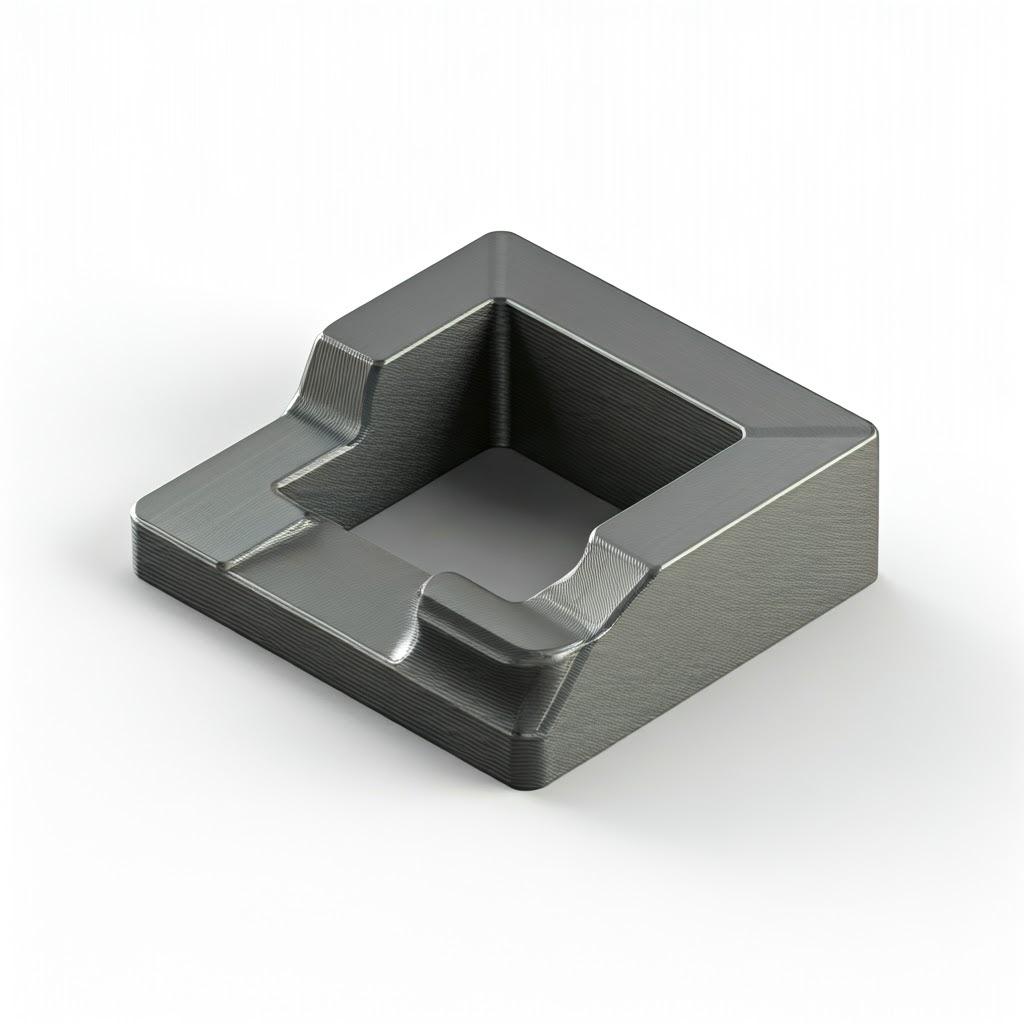
Achieving Precision: Tolerance, Surface Finish, and Dimensional Accuracy in AM
While additive manufacturing offers incredible design freedom, a common question from engineers and procurement managers, especially in the precision-driven aerospace sector, concerns the achievable tolerances, surface finish, and overall dimensional accuracy of 3D printed metal parts. For critical components like frame corner blocks, meeting specified dimensional requirements is non-negotiable. Understanding the capabilities and limitations of AM processes like Laser Powder Bed Fusion (LPBF) – the typical method for Scalmalloy® and Ti-6Al-4V – is essential.
Dimensional Accuracy and Tolerances:
The dimensional accuracy of a metal AM part refers to how closely the final printed component matches the original CAD model dimensions. Several factors influence this:
- Machine Calibration: Regular and precise calibration of the AM system (lasers, scanners, recoater mechanism) is fundamental.
- Process Parameters: Laser power, scan speed, layer thickness, and scan strategy significantly impact melt pool dynamics, shrinkage, and potential distortion. Optimized parameters are crucial for accuracy.
- Thermal Effects: The repeated heating and cooling cycles inherent in AM can cause internal stresses, leading to warping or distortion, particularly in large or complex geometries. Build plate heating, support strategies, and stress relief post-processing are used to mitigate this.
- Part Size and Geometry: Larger parts or those with complex features and varying cross-sections are generally more challenging to print with extremely high accuracy due to cumulative thermal effects and potential shrinkage variation.
- Materialegenskaper: Different alloys exhibit different shrinkage rates and thermal conductivity, influencing final dimensions. Specific parameters are developed for materials like Scalmalloy® and Ti-6Al-4V.
- Part Orientation: How the part is oriented on the build plate affects support needs, thermal gradients, and potential anisotropy, all influencing final dimensions.
Typical Achievable Tolerances (LPBF):
- As-Built: For well-controlled processes, typical achievable tolerances for LPBF-printed metal parts are often in the range of ±0.1 mm to ±0.2 mm for smaller dimensions (e.g., up to 100 mm), with potentially larger deviations (e.g., ±0.2% of the dimension) for larger parts. However, this is highly dependent on the factors listed above.
- Post-Machined: For critical interfaces, mating surfaces, or features requiring tighter tolerances (e.g., bearing bores, precise mounting holes), post-print CNC machining is standard practice. Machining can achieve tolerances typical of conventional subtractive processes (e.g., ±0.01 mm to ±0.05 mm or tighter, depending on the specific requirement). Designers must incorporate machining allowances (extra material) onto these specific features in the CAD model.
Surface Finish (Roughness):
Surface finish, typically quantified by the average roughness (Ra), is another critical characteristic, impacting fatigue life, sealing, and aesthetics.
- As-Built Surface Finish: The surface finish of AM parts depends heavily on:
- Orientation: Top surfaces (facing upwards) are generally smoother. Side walls have a visible layer stepping effect. Downward-facing surfaces (supported) tend to be the roughest due to support contact points.
- Skiktets tjocklek: Thinner layers generally produce slightly better surface finish but increase build time.
- Process Parameters: Optimized parameters can improve surface melt quality.
- Partikelstorlek: Finer powders can contribute to smoother surfaces.
- Typical as-built Ra values for LPBF parts (Scalmalloy®, Ti-6Al-4V) often range from 6 µm to 20 µm (approx. 240 µin to 800 µin). Steeper angles relative to the build plate generally yield rougher surfaces.
- Post-Processed Surface Finish: Various post-processing techniques can significantly improve the surface finish:
- Stöd för borttagning: Initial grinding or cutting leaves local marks.
- Bead Blasting/Sand Blasting: Creates a uniform, matte finish, often improving Ra slightly (e.g., 5-10 µm Ra).
- Tumbling/Vibratory Finishing: Can smooth surfaces and edges, particularly for batches of smaller parts.
- Electropolishing: Can achieve very smooth, bright finishes (e.g., <1 µm Ra) but removes material and may affect tolerances.
- CNC Machining: Provides the best control over surface finish on specific features, easily achieving Ra values below 1.6 µm or 0.8 µm (63 µin or 32 µin) where required.
- Manual Polishing: Used for achieving mirror finishes on specific areas, but is labor-intensive.
Setting Expectations for Aerospace:
Aerospace components often demand tight tolerances on interfacing features and specific surface finish requirements for fatigue-critical areas. It’s crucial for designers and procurement managers to:
- Specify requirements clearly: Indicate critical dimensions with tolerances and required surface finishes on drawings.
- Understand AM limitations: Accept that as-built tolerances and finishes may not meet all requirements directly.
- Plan for post-processing: Factor in necessary machining, polishing, or other finishing steps into the manufacturing plan and cost.
- Collaborate with the AM provider: Discuss requirements early. An experienced provider like Met3dp can advise on achievable accuracy, optimal orientation, support strategies, and necessary post-processing based on their tryckmetoder and material expertise.
By understanding the interplay between the AM process, material choice, and post-processing, aerospace manufacturers can confidently leverage 3D printing to produce corner blocks that meet stringent dimensional and surface quality standards.
Beyond Printing: Essential Post-Processing Steps for Aerospace Corner Blocks
Producing a dimensionally accurate aerospace corner block doesn’t end when the 3D printer stops. For safety-critical applications using high-performance materials like Scalmalloy® and Ti-6Al-4V, a series of essential post-processing steps are required to ensure the component achieves the necessary mechanical properties, reliability, and surface characteristics demanded by the aerospace industry. These steps transform the ‘as-built’ part into a flight-ready component. Skipping or improperly performing these steps can compromise the integrity and performance of the final part.
Key post-processing stages for AM aerospace corner blocks often include:
Post-Processing Step | Beskrivning | Syfte | Relevance to Scalmalloy® / Ti-6Al-4V |
---|---|---|---|
1. Stress Relief | Heating the part (often while still on the build plate) to a specific temperature below the alloy’s aging or annealing temperature, holding it, and then cooling slowly. | Reduces internal stresses built up during the rapid heating/cooling cycles of the AM process. Prevents distortion or cracking during removal from the build plate or subsequent machining. | Kritisk for both. Ti-6Al-4V is particularly prone to high residual stresses. Scalmalloy® also benefits significantly. |
2. Removal from Build Plate | Separating the printed part(s) from the metal build plate, typically using wire EDM, sawing, or machining. | Physically liberates the part for further processing. | Standard step for both materials. Method depends on part geometry and support structure density at the base. |
3. Support Structure Removal | Removing the temporary support structures required during the build process, using manual breaking, cutting tools, pliers, CNC machining, or sometimes EDM. | Supports are necessary for printing but not part of the final design. Removal required for functionality and aesthetics. | Can be challenging, especially for complex internal supports or tough materials like Ti-6Al-4V. Careful removal needed to avoid part damage. |
4. Heat Treatment (Solution Annealing, Aging, etc.) | Controlled heating and cooling cycles tailored to the specific alloy to achieve desired microstructure and mechanical properties (strength, ductility, hardness, fatigue life). | Optimizes material properties. As-built AM microstructures may not be ideal. Achieves properties comparable to wrought or cast counterparts. | Grundläggande for both to meet aerospace specifications. Specific cycles differ: Scalmalloy® requires aging. Ti-6Al-4V often involves annealing, solution treating & aging (STA). |
5. Hot Isostatic Pressing (HIP) | Subjecting the part to high temperature (below melting point) and high isostatic pressure (using an inert gas like Argon) in a specialized vessel. | Closes internal microporosity (voids) that can sometimes occur during AM. Improves fatigue life, ductility, and fracture toughness. Ensures material consistency. | Highly Recommended/Often Required for critical aerospace parts, especially fatigue-critical Ti-6Al-4V components. Also beneficial for Scalmalloy®. |
6. Machining (Critical Features) | Using CNC machining to achieve tight tolerances, specific surface finishes, or geometric features (e.g., threads, precise holes, mating surfaces) that cannot be achieved adequately by the AM process alone. | Ensures precise interfacing with other components, meets tight drawing tolerances. Creates smooth surfaces for sealing or fatigue resistance. | Commonly Required for interfacing surfaces, fastener holes, and any dimension with tolerance tighter than AM as-built capability. |
7. Surface Finishing | Processes like bead blasting, tumbling, polishing, or coating applied to achieve the desired surface texture, appearance, or functional surface properties (e.g., wear resistance, corrosion protection). | Improves aesthetics, removes support witness marks, enhances fatigue life (shot peening), provides specific surface characteristics. | Bead blasting is common for a uniform finish. Specific polishing or coatings depend on application requirements. |
8. Cleaning | Removing residual powder, machining fluids, oils, and other contaminants from the finished part. | Ensures part cleanliness for final inspection, assembly, and operation. Prevents contamination issues. | Important step before final inspection and delivery. |
9. Non-Destructive Testing (NDT) / Inspection | Using methods like visual inspection, dimensional analysis (CMM, 3D scanning), X-ray Computed Tomography (CT), Fluorescent Penetrant Inspection (FPI), or Ultrasonic Testing (UT). | Verifies part integrity, dimensional accuracy, absence of defects (cracks, porosity), and conformance to specifications before flight use. | Mandatory for critical aerospace components. CT scanning is particularly valuable for AM parts to inspect internal structures and detect defects. |
Export to Sheets
Importance of Integrated Workflow:
Successfully navigating these post-processing steps requires careful planning and execution. It is not merely a sequence of disconnected operations but an integrated workflow that must be considered from the initial design stage. For instance, designing with post-processing in mind (e.g., adding machining stock, ensuring access for support removal and inspection) is crucial. Furthermore, maintaining traceability and process control throughout these steps is vital for aerospace certification (e.g., AS9100). Partnering with an AM provider who has in-house or tightly managed control over these critical post-processing steps ensures quality, consistency, and accountability throughout the entire manufacturing chain, from powder to finished part. Companies aiming for wholesale supply of aerospace components must demonstrate robust post-processing capabilities and quality management.
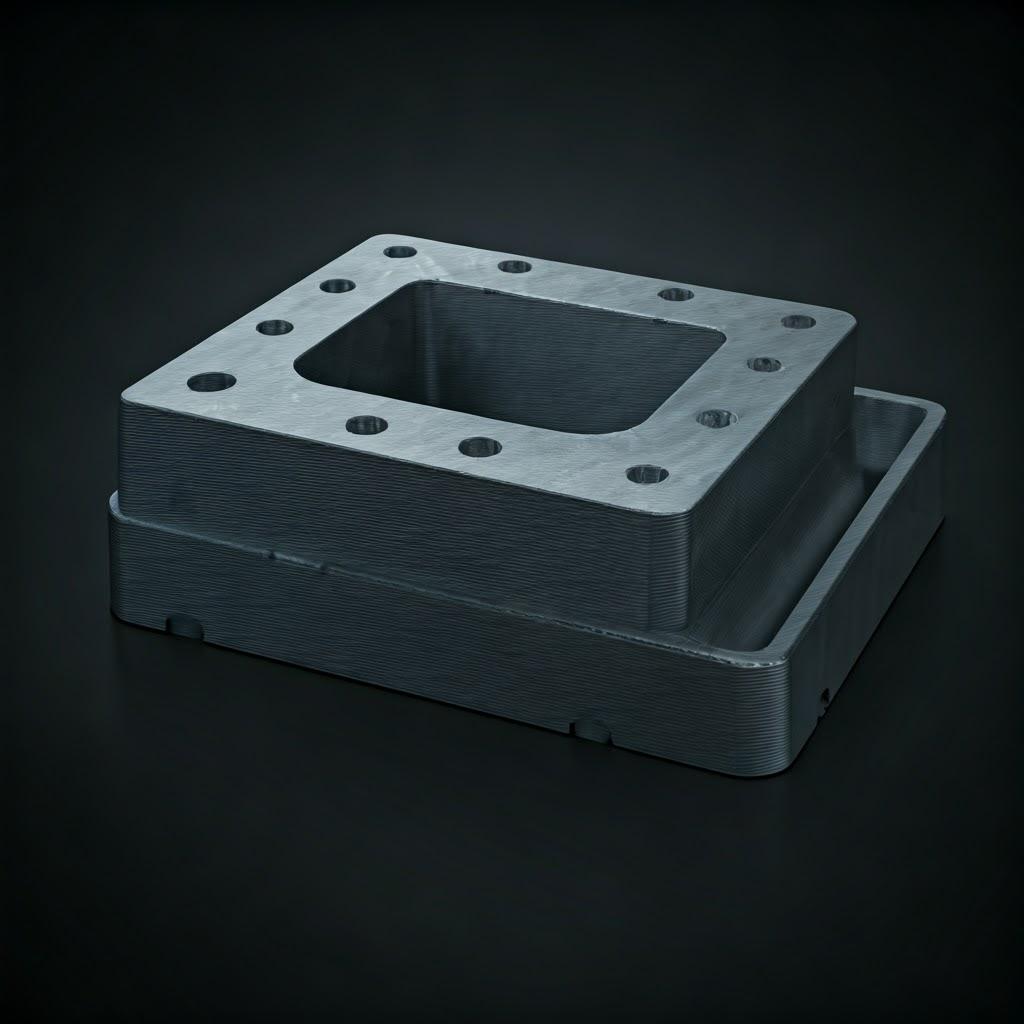
Navigating Challenges: Ensuring Quality and Reliability in AM Corner Blocks
While metal additive manufacturing offers significant advantages for producing aerospace corner blocks, it’s not without its challenges. Achieving the consistent quality, reliability, and repeatability demanded by the aerospace industry requires a deep understanding of the potential pitfalls and the implementation of rigorous mitigation strategies. Engineers and procurement managers should be aware of these common challenges and ensure their chosen AM partners have robust processes in place to address them.
Common Challenges in Metal AM for Aerospace:
- Residual Stresses and Warping:
- Cause: The rapid, localized heating and cooling inherent in layer-by-layer fusion creates thermal gradients, leading to internal stresses within the part. These stresses can cause distortion (warping), especially during printing or after removal from the build plate, or even lead to cracking.
- Mitigation:
- Simulation: Using process simulation software to predict thermal behavior and stress accumulation, allowing optimization of build orientation and support structures.
- Optimized Scan Strategies: Using specific laser scanning patterns (e.g., island scanning, sectoring) to manage heat distribution.
- Build Plate Heating: Maintaining an elevated temperature of the build plate reduces thermal gradients.
- Effective Support Structures: Designing supports not just for overhangs but also to anchor the part and conduct heat away effectively.
- Post-Build Stress Relief: Performing a stress relief heat treatment cycle before removing the part from the build plate is crucial, especially for high-stress materials like Ti-6Al-4V.
- Porositet:
- Cause: Small voids or pores within the printed material. Can originate from gas trapped within the powder particles (Argon from atomization), vaporization of elements during melting, incomplete fusion between layers/tracks, or keyholing (laser penetrating too deep). Porosity degrades mechanical properties, particularly fatigue life.
- Mitigation:
- High-Quality Powder: Using powders with low internal gas porosity and controlled particle size distribution, like those produced via advanced methods employed by Met3dp. Proper powder handling and storage are also vital.
- Optimized Process Parameters: Tuning laser power, scan speed, layer thickness, and hatch spacing to ensure complete melting and fusion without excessive vaporization or keyholing. Parameter development is key.
- Het isostatisk pressning (HIP): As mentioned previously, HIP is highly effective at closing internal gas porosity and improving material density. Often mandatory for critical aerospace parts.
- Cracking:
- Cause: Can result from excessive residual stress exceeding the material’s strength, particularly during cooling. Some alloys are more susceptible (e.g., certain high-strength nickel superalloys or specific aluminum alloys if parameters are not optimized). Can also initiate from defects or impurities.
- Mitigation:
- Stress Management: All techniques used to mitigate residual stress also help prevent cracking.
- Alloy Selection & Parameter Optimization: Choosing alloys with good AM processability and meticulously developing robust process parameters.
- Controlled Heating/Cooling: Utilizing build plate heating and potentially controlled atmosphere management.
- Post-Build Heat Treatments: Appropriate stress relief and annealing cycles.
- Support Removal Difficulties and Damage:
- Cause: Supports, especially dense ones or those in intricate internal locations, can be difficult and time-consuming to remove. Aggressive removal techniques can damage the part surface or introduce stress risers.
- Mitigation:
- DfAM for Support Reduction: Designing parts to minimize support needs (self-supporting angles, optimized orientation).
- Smart Support Design: Using support structures (e.g., tree supports, block supports with easily breakable contact points) that are effective during the build but easier to remove.
- Appropriate Removal Techniques: Using careful manual methods, specialized tools, EDM, or CNC machining for precise support removal.
- Skilled Technicians: Experienced technicians are crucial for effective and non-damaging support removal.
- Surface Finish Deviations:
- Cause: Variations in melt pool stability, layer stepping effects, support contact points (‘witness marks’), and powder particle adhesion can lead to inconsistent or rougher-than-expected surfaces.
- Mitigation:
- Optimized Parameters & Orientation: Fine-tuning process parameters and choosing build orientation carefully.
- Appropriate Post-Processing: Utilizing bead blasting, tumbling, polishing, or machining to achieve the specified surface finish requirements consistently.
- Process Variability and Repeatability:
- Cause: Minor variations in machine calibration, laser performance, powder characteristics (batch-to-batch), or atmospheric conditions can potentially lead to slight differences between builds.
- Mitigation:
- Robust Quality Management System (QMS): Implementing strict process controls, regular machine calibration and maintenance, and powder quality verification (e.g., ISO 9001, AS9100).
- Pågående övervakning: Utilizing sensors and systems to monitor key process variables (melt pool temperature, layer uniformity) in real-time.
- Rigorous Testing: Consistent mechanical testing of samples from production builds to verify properties.
- Standardized Procedures: Documented procedures for every step from powder handling to final inspection.
Overcoming Challenges with Expertise:
Successfully manufacturing reliable aerospace corner blocks via AM requires more than just owning a printer. It demands deep materials science knowledge, expertise in process parameter development, rigorous quality control, and proficiency in post-processing techniques. Partnering with an experienced AM service provider like Met3dp, who emphasizes powder quality, process control, and comprehensive solutions, is key to mitigating these challenges and ensuring the delivery of high-quality, flight-ready components that meet the stringent demands of the aerospace sector. Their focus on industry-leading equipment and advanced materials provides a strong foundation for tackling complex AM projects.
Supplier Selection: Choosing the Right Metal Additive Manufacturing Partner
Selecting the right additive manufacturing partner is as critical as choosing the right material or design for your aerospace corner blocks. The quality, reliability, and airworthiness of the final component depend heavily on the expertise, processes, and quality systems of your chosen supplier. For aerospace applications, particularly involving flight-critical structures, the vetting process must be rigorous. Procurement managers and engineering teams should evaluate potential AM service providers based on a comprehensive set of criteria:
Key Evaluation Criteria for Aerospace AM Suppliers:
- Aerospace Certifications (AS9100):
- Why it matters: AS9100 is the internationally recognized Quality Management System (QMS) standard for the aviation, space, and defense industries. Certification demonstrates a supplier’s commitment to quality, traceability, risk management, and continuous improvement, tailored to the stringent requirements of aerospace. Compliance is often mandatory for suppliers providing flight hardware.
- What to look for: Current AS9100 certification (verify scope covers relevant processes like LPBF, materials, and post-processing). Ask about their QMS documentation, audit history, and non-conformance handling processes.
- Material Expertise and Handling:
- Why it matters: Deep knowledge of the specific alloys being used (Scalmalloy®, Ti-6Al-4V) is crucial. This includes understanding their metallurgy, AM process interactions, required heat treatments, and potential failure modes. Proper powder handling (storage, sieving, testing, traceability) is vital to prevent contamination and ensure consistent feedstock quality.
- What to look for: Demonstrated experience with the specific materials required. Ask about their powder sourcing (do they manufacture or qualify specific suppliers?), powder characterization methods (chemistry, PSD, morphology, flowability), and documented powder handling procedures (e.g., atmosphere control, batch tracking, recycling protocols). Companies like Met3dp, who not only use but also manufacture high-quality metal powders using advanced techniques like Gas Atomization and PREP, possess inherent material expertise. You can learn more about their background and focus om oss.
- Technology, Equipment, and Process Control:
- Why it matters: The quality, calibration, and maintenance of the AM machines (e.g., LPBF systems) directly impact part quality. Robust process control, including validated parameter sets for specific material/machine combinations, is essential for repeatability.
- What to look for: Information on their specific AM equipment (manufacturer, model, age, maintenance schedules). Evidence of process validation and parameter optimization for your required material. Ask about in-process monitoring capabilities and their approach to ensuring build-to-build consistency.
- Post-Processing Capabilities:
- Why it matters: As detailed earlier, post-processing (stress relief, heat treatment, HIP, machining, NDT) is critical for aerospace parts. A supplier with integrated or tightly controlled, qualified partners for these steps ensures a seamless workflow and maintains quality oversight.
- What to look for: In-house capabilities or established relationships with NADCAP-accredited or similarly qualified vendors for essential processes like heat treatment, HIP, and NDT. Ensure clear responsibility and traceability throughout the entire process chain.
- Aerospace Project Experience and Past Performance:
- Why it matters: Experience specifically within the aerospace sector indicates familiarity with industry standards, documentation requirements, and typical component challenges.
- What to look for: Case studies, examples of similar aerospace components produced, customer references (if possible, under NDA). Evidence of successfully navigating aerospace qualification processes.
- Engineering and DfAM Support:
- Why it matters: The ideal partner acts as more than just a print bureau. They should offer Design for Additive Manufacturing (DfAM) expertise to help optimize your corner block design for performance, weight, and manufacturability using AM.
- What to look for: Availability of application engineers or technical staff who can provide design feedback, suggest optimizations, advise on material selection, and help troubleshoot potential issues.
- Capacity, Scalability, and Lead Time:
- Why it matters: Ensure the supplier has the machine capacity and operational efficiency to meet your required volumes (from prototypes to potential production runs) within acceptable lead times.
- What to look for: Number of relevant machines, operational shifts, typical lead times for similar projects, ability to scale production if needed. Transparency regarding production scheduling and communication protocols.
Evaluating Potential Partners:
Criteria Check | Questions to Ask Potential Suppliers | Desired Response Indicator |
---|---|---|
AS9100 Certified? | “Are you AS9100 certified? May we see your certificate and scope?” “How do you manage aerospace traceability & documentation?” | Current certification covering relevant processes. Clear explanation of QMS procedures. |
Material Expertise? | “What is your experience with [Scalmalloy®/Ti-6Al-4V]?” “How do you qualify and handle your metal powders?” | Demonstrated successful projects, detailed powder handling protocols, evidence of powder characterization. |
Process Control? | “What specific LPBF machines do you use?” “How do you ensure build consistency?” “Are your process parameters validated?” | Well-maintained, industry-standard machines. Documented validation, potential for in-process monitoring, clear QC steps. |
Post-Processing? | “What post-processing do you perform in-house?” “How do you qualify external vendors for heat treat, HIP, NDT?” | Clear description of workflow, evidence of qualified internal processes or external NADCAP/equivalent partners. |
Aerospace Experience? | “Can you share examples of aerospace components you’ve produced (respecting NDAs)?” | Relevant examples demonstrating understanding of aerospace requirements and component types. |
DfAM Support? | “Do you offer design support or DfAM consultation?” | Availability of engineers to review designs and provide constructive feedback for AM optimization. |
Capacity/Lead Time? | “What is your typical lead time for a part like this?” “What is your production capacity for [Material X]?” “How do you handle scheduling?” | Realistic lead time estimates, transparent communication about capacity and potential bottlenecks. |
Export to Sheets
Choosing a partner who excels across these criteria significantly increases the probability of successfully implementing 3D printed corner blocks that meet the demanding standards of the aerospace industry. Thorough due diligence during supplier selection is a critical investment.
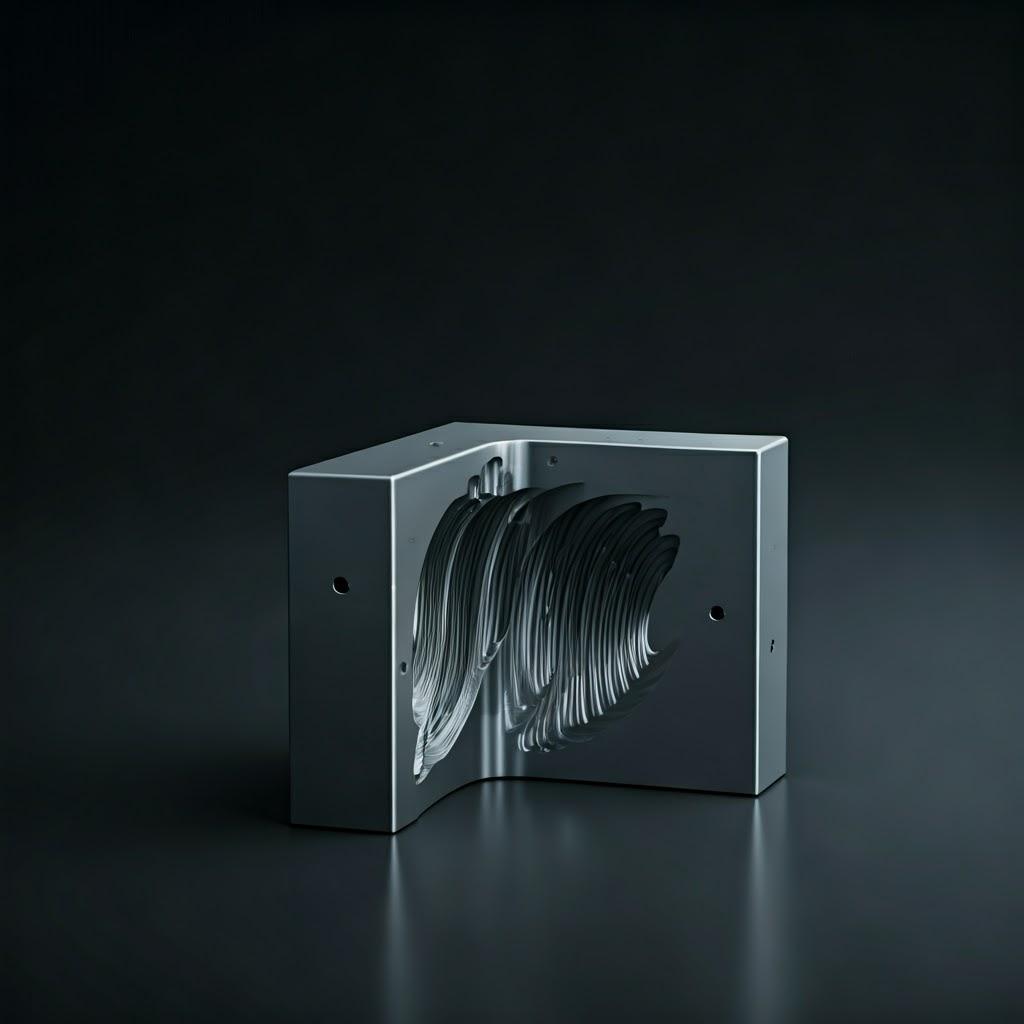
Understanding Costs and Lead Times for 3D Printed Corner Blocks
While the performance benefits of 3D printed aerospace corner blocks using materials like Scalmalloy® and Ti-6Al-4V are compelling, understanding the associated costs and production timelines is crucial for budgeting, project planning, and making informed decisions, especially for wholesale buyers and procurement managers. Several factors influence the final price per part and the time it takes to receive finished components.
Key Cost Drivers for AM Aerospace Corner Blocks:
- Material Cost:
- Powder Price: High-performance aerospace-grade metal powders like Scalmalloy® (containing expensive Scandium) and Ti-6Al-4V are significantly more expensive than standard engineering alloys. The base price per kilogram is a major factor.
- Material Usage: The actual volume of the part, plus any support structures required. DfAM techniques like topology optimization help minimize this.
- Recycling/Waste: While AM is efficient, some powder is inevitably lost or degraded during handling and processing. Sophisticated powder management systems minimize waste but have associated operational costs.
- AM Machine Time:
- Byggtid: This is often the largest single cost component. It depends on the part’s height (number of layers), the total volume to be sintered/melted, the complexity (more intricate scanning takes longer), and the number of parts that can fit onto a single build plate (nesting efficiency).
- Machine Hourly Rate: AM machines represent significant capital investment, and suppliers factor operational costs (energy, gas, maintenance, software, labor for setup/monitoring) into an hourly rate. Rates vary based on machine type, size, and location.
- Kostnader för arbetskraft:
- Setup & Teardown: Preparing the build file, setting up the machine, loading powder, and later removing the build plate and parts require skilled technician time.
- Post-Processing Labor: Manual support removal, inspection, finishing, and part handling all contribute to labor costs. This can be significant for complex parts or those requiring extensive finishing.
- Kostnader för efterbearbetning:
- Specialized Processes: Steps like stress relief, heat treatment, HIP, and advanced NDT (like CT scanning) require specialized equipment and add significant cost. HIP, in particular, can be a substantial cost addition but is often necessary for critical parts.
- Maskinbearbetning: If tight tolerances or specific finishes are required on certain features, the cost of CNC machining (setup, programming, machine time) must be factored in.
- Quality Assurance and Testing:
- Inspection: Dimensional verification (CMM, 3D scanning), surface finish checks, and material testing add to the cost.
- Documentation: Generating the comprehensive documentation and traceability records required for aerospace certification takes time and resources.
- Order Volume:
- Stordriftsfördelar: Setting up a build is largely a fixed cost. Printing multiple copies of a part in a single build (if space allows) or across multiple builds often reduces the cost per part significantly compared to a single prototype. This is a key consideration for wholesale suppliers and bulk orders. However, the high cost of materials means volume discounts might be less dramatic than in traditional high-volume manufacturing.
Typical Lead Times:
Lead time – the duration from order placement to receiving finished parts – is influenced by several factors:
- Quoting & File Preparation: Initial review of the design, DfAM checks (if needed), quote generation, and build file preparation (orientation, supports) can take a few hours to several days, depending on complexity.
- Machine Availability & Scheduling: Access to the appropriate AM machine with the correct material loaded. Suppliers often have queues, so lead time depends on current machine loading. Typical print times can range from 10-20 hours to several days for complex or large corner blocks or full build plates.
- Tryckning: The actual time the part spends being built layer by layer in the machine.
- Efterbearbetning: This can add significantly to the lead time.
- Cooling/Stress Relief: Several hours to a day.
- Build Plate Removal/Support Removal: Hours to days, depending on complexity and quantity.
- Heat Treatment/HIP: Can take several days, including furnace time and potential batching requirements. HIP cycles often require sending parts to specialized facilities, adding logistical time.
- Machining: Depends on complexity and machine shop availability, potentially adding days to weeks.
- NDT/Inspection: Depends on the level of inspection required, from hours for basic checks to days for comprehensive NDT and reporting.
- Frakt: Standard transit times.
Estimated Timelines:
- Prototyper: For a single, relatively simple corner block requiring standard post-processing, lead times might range from 1 to 3 weeks.
- Production Batches: For small-to-medium batches requiring full aerospace qualification (including HIP, extensive NDT, machining), lead times can extend to 4 to 8 weeks or longer, depending on the complexity, quantity, and specific processing required.
Getting Accurate Quotes:
To get an accurate cost and lead time estimate for your specific corner block design, you will need to provide potential suppliers with:
- A 3D CAD model (e.g., STEP format).
- A 2D drawing indicating critical dimensions, tolerances, surface finish requirements, and material specification.
- The desired quantity.
- Any specific aerospace standards or specifications that must be met.
- Required post-processing steps and certifications.
Engaging with knowledgeable suppliers early in the design process can help optimize the part for cost-effective additive manufacturing and provide realistic expectations for budget and schedule.
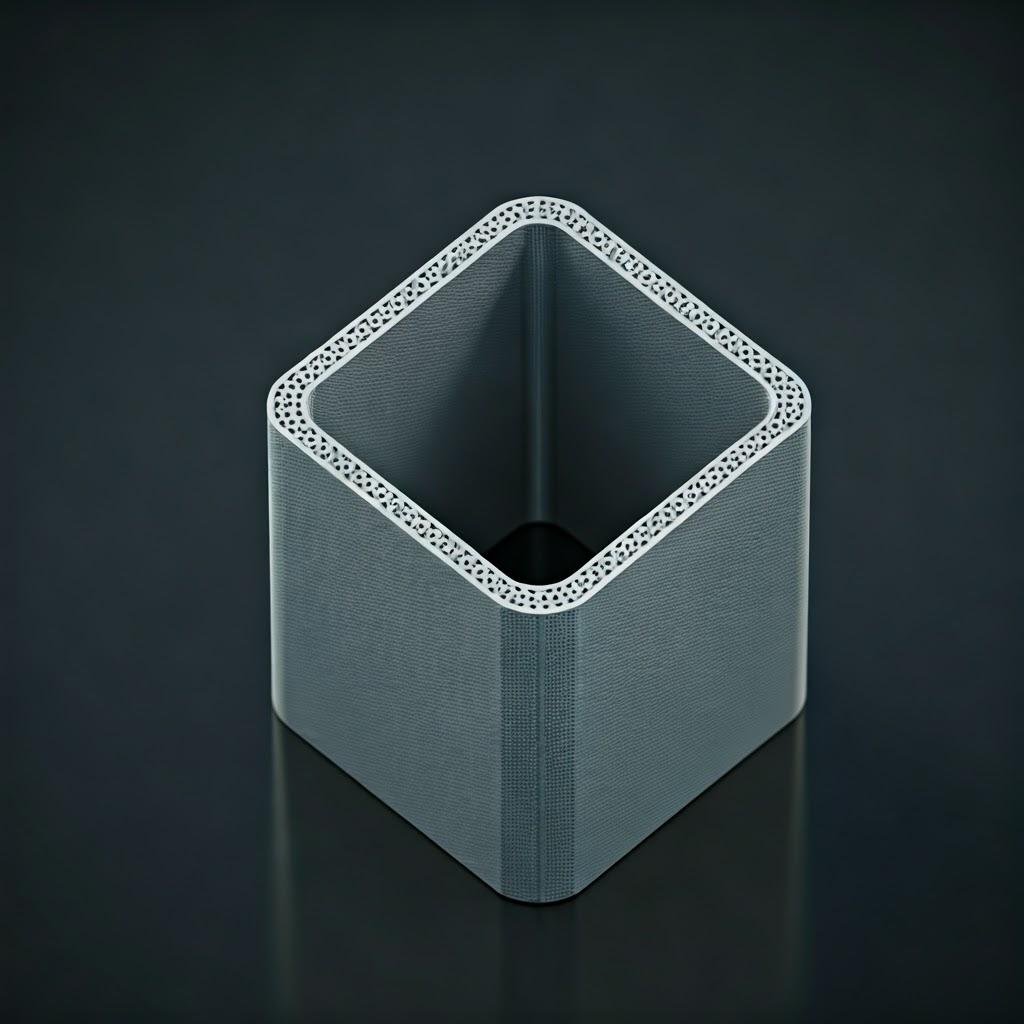
Frequently Asked Questions (FAQ) about 3D Printed Aerospace Corner Blocks
Here are answers to some common questions regarding the use of metal additive manufacturing for aerospace frame corner blocks:
- Are 3D printed corner blocks (Scalmalloy®, Ti-6Al-4V) as strong and reliable as traditionally machined parts?
- Svar: Yes, when produced using qualified processes, high-quality materials, and appropriate post-processing (like heat treatment and HIP), 3D printed components made from Scalmalloy® and Ti-6Al-4V can achieve mechanical properties (like tensile strength, yield strength, fatigue life) that are comparable or even superior to their conventionally manufactured counterparts (cast or wrought/machined). Rigorous process control and post-processing like HIP are key to minimizing defects like porosity and ensuring consistency, leading to reliable, high-performance parts suitable for demanding aerospace applications. Qualification testing specific to the application is always required.
- Can 3D printed metal corner blocks be certified for flight use in aircraft?
- Svar: Absolutely. Metal additive manufacturing is increasingly being adopted for flight-critical components by major aerospace OEMs. The path to certification involves demonstrating process control, material characterization, repeatability, and extensive testing (material coupons, component-level testing) to satisfy airworthiness authorities (like FAA, EASA). Utilizing AS9100 certified suppliers, adhering to established aerospace standards (e.g., MMPDS data development, specific OEM requirements), performing necessary NDT, and thorough documentation are all crucial parts of the certification process. Many AM components are already flying on commercial, defense, and space platforms.
- What kind of cost savings can be expected when using AM for corner blocks compared to CNC machining?
- Svar: Cost comparison depends heavily on part complexity, material, and volume. For highly complex corner blocks requiring extensive 5-axis machining from an expensive billet (like titanium), AM can offer significant cost savings due to reduced material waste (lower buy-to-fly ratio) and potentially reduced machining time (if AM produces a near-net shape). For simpler geometries easily machined from less expensive stock, traditional machining might remain cheaper, especially at high volumes. However, AM’s benefits like weight reduction (leading to operational cost savings) and part consolidation (reducing assembly costs) must also be considered in the total cost equation. A detailed quote comparison for a specific part is recommended.
- How does the fatigue life of AM Scalmalloy® or Ti-6Al-4V compare to wrought materials?
- Svar: With proper process optimization and post-processing, particularly HIP to reduce internal porosity, the fatigue performance of AM Ti-6Al-4V and Scalmalloy® can be excellent and often comparable to wrought equivalents. Surface finish plays a significant role; critical surfaces may require machining or polishing to achieve optimal fatigue life. Extensive testing data is available, and ongoing research continues to refine processes for even better fatigue performance. Specific fatigue requirements should be part of the component specification and validated through testing.
- What information does a supplier like Met3dp need to provide an accurate quote for printing aerospace corner blocks?
- Svar: To provide an accurate quote, suppliers typically need:
- 3D CAD-modell: In a standard format (e.g., STEP, IGES).
- 2D Engineering Drawing: Specifying material (Scalmalloy®, Ti-6Al-4V), critical dimensions, tolerances, surface finish requirements (Ra), and any specific notes or callouts.
- Quantity Needed: Including prototypes and potential production volumes.
- Required Certifications/Standards: Mention any required compliance (e.g., AS9100, specific OEM specs).
- Krav på efterbearbetning: Clearly list necessary steps like heat treatment type, HIP, specific NDT methods, machining details, surface treatments.
- Desired Lead Time: If there are specific schedule requirements.
- Svar: To provide an accurate quote, suppliers typically need:
Conclusion: Elevating Aerospace Structures with Additive Manufacturing
The aerospace industry perpetually seeks innovation to enhance performance, reduce weight, and improve efficiency. Metal additive manufacturing has firmly established itself as a key enabler in this pursuit, offering transformative possibilities for components like aerospace frame corner blocks. By leveraging the power of AM, engineers can break free from the constraints of traditional manufacturing, designing and producing corner blocks that are lighter, stronger, and more complex than ever before.
The use of advanced materials like high-strength Scalmalloy® -legering and the proven workhorse Ti-6Al-4V, combined with AM processes like Laser Powder Bed Fusion, allows for the creation of topology-optimized structures and consolidated designs that were previously unattainable. These advancements translate directly into tangible benefits: reduced aircraft weight leading to fuel savings or increased payload, simplified assemblies reducing manufacturing complexity, and accelerated development cycles enabling faster innovation.
However, realizing these benefits requires navigating the intricacies of the AM process, from meticulous design optimization (DfAM) and precise process control to essential post-processing steps like heat treatment, HIP, and rigorous NDT inspection. The challenges of residual stress, porosity, and achieving tight tolerances necessitate a deep understanding of materials science and manufacturing technology.
This underscores the critical importance of selecting the right manufacturing partner – one with validated aerospace credentials (AS9100), profound material and process expertise, robust quality management systems, and end-to-end capabilities covering design support through final inspection.
Metal 3D printing is no longer a futuristic concept but a present-day reality reshaping aerospace manufacturing. For structural components like frame corner blocks, it offers a powerful pathway to enhanced performance and competitive advantage. By embracing this technology and collaborating with knowledgeable partners, the aerospace industry can continue to push the boundaries of flight, creating safer, lighter, and more capable aircraft and spacecraft for the future.
To explore how advanced metal additive manufacturing solutions, including high-quality powders and industrial printing systems, can benefit your aerospace projects, visit Met3dp.
Dela på
MET3DP Technology Co, LTD är en ledande leverantör av lösningar för additiv tillverkning med huvudkontor i Qingdao, Kina. Vårt företag är specialiserat på 3D-utskriftsutrustning och högpresterande metallpulver för industriella tillämpningar.
Förfrågan för att få bästa pris och anpassad lösning för ditt företag!
Relaterade artiklar
Om Met3DP
Senaste uppdateringen
Vår produkt
KONTAKTA OSS
Har du några frågor? Skicka oss meddelande nu! Vi kommer att betjäna din begäran med ett helt team efter att ha fått ditt meddelande.
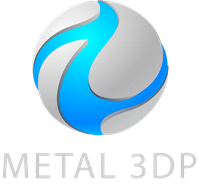
Metallpulver för 3D-printing och additiv tillverkning