Corrosion-Resistant Shaft Sleeves via Metal 3D Printing
Innehållsförteckning
Introduction: Enhancing Marine Durability with 3D Printed Shaft Sleeves
The maritime industry, a cornerstone of global trade and transportation, operates in one of the most demanding environments on Earth. Components used in ships, offshore platforms, and subsea equipment face relentless assault from saltwater corrosion, high pressures, dynamic loads, and abrasive wear. Among these critical components, the shaft sleeve plays a vital, albeit often overlooked, role. Traditionally manufactured through casting or machining from bar stock, these cylindrical parts protect expensive rotating shafts (like propeller shafts or pump shafts) from wear, corrosion, and damage, acting as a sacrificial and replaceable wear surface. However, conventional manufacturing methods often involve long lead times, material waste, design limitations, and challenges in sourcing specific corrosion-resistant alloys, especially for custom or low-volume requirements common in specialized marine applications or urgent repairs.
Enter the transformative power of metalltillsatstillverkning (AM), commonly known as metal 3D-utskrifter. This technology is rapidly moving beyond prototyping and into the realm of functional part production, offering unprecedented solutions for complex industrial challenges. For the marine sector, metal AM presents a revolutionary approach to producing components like shaft sleeves with enhanced performance, tailored designs, and significantly improved supply chain agility. By building parts layer by layer directly from digital models using high-performance metal powders, manufacturers can create intricate geometries, optimize material usage, and select alloys specifically engineered for extreme marine conditions. This capability is particularly crucial for corrosion-resistant shaft sleeves, where material integrity is paramount to operational reliability and longevity. Imagine being able to rapidly produce a replacement shaft sleeve with superior material properties, potentially even incorporating design improvements impossible with traditional methods, directly addressing the urgent needs of a vessel docked for maintenance or an offshore platform requiring critical spares.
This blog post delves into the world of metal 3D printing for marine shaft sleeves, focusing on the significant advantages offered by this technology, particularly when utilizing advanced corrosion-resistant alloys like CuNi30Mn1Fe (Copper-Nickel) och 316L rostfritt stål. We will explore the typical applications, compare AM with traditional manufacturing, discuss material properties, outline design considerations, and provide insights into choosing the right manufacturing partner. For procurement managers, engineers, and designers in the aerospace, automotive, medical, and particularly the maritime and industrial manufacturing sectors, understanding the potential of metal AM for producing critical components like shaft sleeves is key to unlocking new levels of performance, efficiency, and supply chain resilience. Companies seeking reliable B2B marine parts suppliers or exploring advanced manufacturing techniques will find valuable information on how additive manufacturing can provide custom, high-performance solutions. As a leader in additive manufacturing solutions, Met3dp leverages its expertise in both advanced printing technologies and high-quality metal powders to empower industries like marine engineering to harness the full potential of metal 3D printing for demanding applications.
The transition towards additive manufacturing in the maritime sector isn’t just about replacing existing parts; it’s about rethinking how components are designed, produced, and maintained. The ability to create near-net-shape parts reduces material waste and post-processing time, contributing to more sustainable manufacturing practices. Furthermore, the digital nature of AM allows for distributed manufacturing – printing parts closer to the point of need, potentially onboard vessels or in remote ports, drastically reducing logistics complexity and downtime. För wholesale marine component distributors and large fleet operators, this translates into improved inventory management and operational readiness. The focus on highly corrosion-resistant materials like specific grades of copper-nickel alloys and stainless steels directly addresses the primary failure mode for many marine components, extending service life and reducing costly maintenance cycles. This introduction sets the stage for a deeper exploration of how 3D printed shaft sleeves are not just a novelty but a practical, high-value solution for enhancing marine durability and operational efficiency.
Applications: Where are 3D Printed Shaft Sleeves Making Waves?
Shaft sleeves, despite their relatively simple appearance, are indispensable components across a wide spectrum of marine and industrial applications. Their primary shaft sleeve function is to serve as a protective barrier and wear surface for rotating shafts, shielding them from direct contact with abrasive media, corrosive fluids, or the friction generated by packing materials or seals. By concentrating wear and corrosion on the replaceable sleeve, the integrity of the more expensive and critical shaft is preserved, simplifying maintenance and extending the overall lifespan of the machinery. The transition to metal 3D printing opens up new possibilities for enhancing the performance and availability of these essential parts in demanding environments.
Key Application Areas:
- Marine Propulsion Systems:
- Propeller Shafts: Sleeves are commonly used where the propeller shaft passes through the stern tube sealing arrangement. They protect the shaft from seawater corrosion and wear caused by stern tube bearings and seals (e.g., stuffing boxes or lip seals). The constant immersion in seawater, often laden with abrasive particles, makes corrosion resistance and wear resistance paramount. 3D printing allows for the use of highly specialized alloys like CuNi30Mn1Fe, known for its excellent resistance to biofouling and seawater corrosion, potentially outperforming traditional bronze or stainless steel sleeves in certain conditions. The ability to print sleeves quickly is also critical for minimizing vessel downtime during repairs.
- Thruster Shafts: Azimuth thrusters, tunnel thrusters, and other auxiliary propulsion systems also utilize shaft sleeves within their sealing and bearing arrangements. These often operate under demanding conditions and may require custom sleeve designs, making them ideal candidates for additive manufacturing.
- Marine and Industrial Pumps:
- Centrifugal Pumps: Shaft sleeves are crucial in centrifugal pumps used for ballast water management, engine cooling systems, bilge pumping, cargo handling (especially for corrosive liquids), and fire suppression systems. The sleeve protects the pump shaft from the pumped fluid (which can be corrosive or abrasive) and wear from packing or mechanical seals. 3D printing enables the production of sleeves from materials like 316L rostfritt stål for general corrosion resistance or specialized alloys for handling specific chemicals or abrasive slurries. Design optimization through AM can also improve hydrodynamic performance around the seal area or incorporate features for better lubrication or cooling.
- Positive Displacement Pumps: Rotary lobe, screw, and gear pumps used in marine applications (e.g., fuel oil transfer, lubrication systems) also employ shaft sleeves to protect shafts at seal interfaces. The precision required for these pumps benefits from the high dimensional accuracy achievable with modern metal AM processer.
- Subsea Equipment:
- Valves and Actuators: Shafts within subsea valves and actuators operating at significant depths face extreme pressure and highly corrosive conditions. Shaft sleeves made from advanced, corrosion-resistant alloys via 3D printing can offer superior longevity and reliability compared to conventionally manufactured parts. The ability to create complex internal features or optimized geometries can also be advantageous in these space-constrained applications.
- ROV/AUV Components: Remotely Operated Vehicles (ROVs) and Autonomous Underwater Vehicles (AUVs) utilize numerous rotating components in thrusters, manipulators, and sampling systems. Lightweight, corrosion-resistant shaft sleeves produced through AM can contribute to overall vehicle efficiency and mission endurance.
- General Industrial Machinery (Operating in Corrosive Environments):
- Kemisk bearbetning: Pumps and rotating equipment handling aggressive chemicals benefit from shaft sleeves made of highly resistant alloys, which can be readily produced using AM.
- Water Treatment Plants: Equipment exposed to treated or untreated water, often containing chlorides or other corrosive agents, requires durable shaft sleeves. 3D printing offers a route to producing sleeves from suitable materials like 316L or duplex stainless steels.
- Kraftgenerering: Cooling water pumps and other auxiliary systems in coastal power plants face similar challenges to marine applications, making 3D printed corrosion-resistant sleeves an attractive option.
Why AM is Suitable for These Applications:
- Materialets flexibilitet: Allows use of optimal materials (CuNi alloys, various stainless steels, nickel alloys) tailored to specific corrosive/wear environments.
- Customization & Rapid Prototyping: Enables easy production of custom sizes or designs for specific equipment or retrofitting purposes, crucial for wholesale marine components suppliers needing diverse inventory or rapid fulfillment.
- On-Demand-produktion: Reduces the need for large inventories of spares; parts can be printed as needed, shortening lead times for critical repairs.
- Designoptimering: Potential to integrate features like improved sealing surfaces, lubrication channels, or lightweight structures not feasible with traditional methods.
The ubiquity of shaft sleeves in critical rotating machinery, particularly in the harsh marine environment, underscores the need for durable, reliable, and readily available components. Metal 3D printing addresses these needs directly, offering a powerful manufacturing alternative that enhances performance and streamlines the supply chain for industrial pumps och marine propulsion systems.
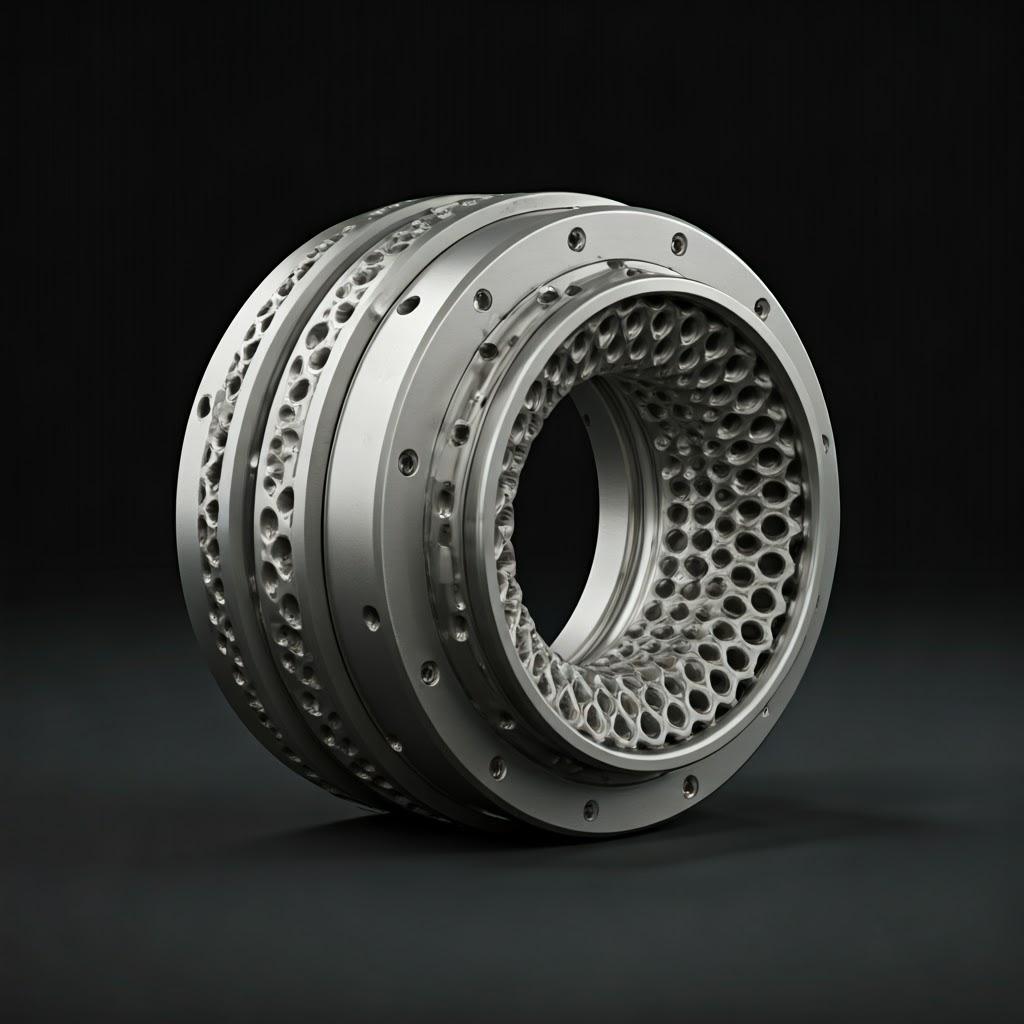
The Additive Advantage: Why Choose Metal 3D Printing for Shaft Sleeves?
While traditional manufacturing methods like casting, forging, and subtractive machining (turning from bar stock) have long been the standard for producing marine shaft sleeves, metalltillsatstillverkning (AM) offers a compelling set of advantages that address many of the inherent limitations of these conventional techniques. For engineers and procurement managers evaluating production methods for critical marine components, understanding these benefits is crucial for making informed decisions that impact performance, cost, and lead time. The choice to adopt AM, particularly for components requiring high corrosion resistance and potentially complex geometries or rapid availability, represents a significant step towards modernization and efficiency.
Comparison: Metal AM vs. Traditional Manufacturing for Shaft Sleeves
Funktion | Metal Additive Manufacturing (e.g., PBF-LB/M) | Traditionell gjutning | Traditional Machining (from Bar Stock) |
---|---|---|---|
Designfrihet | High (complex geometries, internal features, topology optimization possible) | Moderate (limited by mold design, draft angles, wall thickness) | Low (restricted to shapes achievable by turning/milling, subtractive) |
Utnyttjande av material | High (Near-net-shape, less waste, powder recyclability) | Moderate (Requires risers, gating systems; significant machining often needed) | Low (Significant material removal as chips/swarf) |
Lead Time (Low Vol.) | Short (No tooling required, direct from CAD) | Long (Requires pattern/mold making) | Moderate (Depends on material availability and machine time) |
Verktygskostnader | Ingen | High (Pattern and mold costs) | Low/None (Standard cutting tools) |
Suitability for Customization | Excellent (Each part can be unique) | Poor (Requires new tooling) | Moderate (Easy size changes, but geometry limited) |
Val av material | Growing range, including specialized alloys (e.g., specific CuNi grades, Ti-based alloys) | Established range, but new/specialty alloys can be challenging | Limited by available bar stock sizes and alloys |
Initial Part Cost (Low Vol.) | Can be higher due to machine/powder cost | Can be lower if tooling amortized over many parts (but high initial investment) | Can be competitive, depends on material and complexity |
Part Complexity Handling | Utmärkt | Fair (Increases tooling complexity/cost) | Poor (Increases machining time/cost significantly) |
Minsta antal beställningar | Low (Ideal for single parts, prototypes, small batches) | High (Economical only for larger batches due to tooling) | Flexible, but setup costs favor larger runs |
Potential for Lightweighting | High (Lattice structures, topology optimization) | Låg | Mycket låg |
Export to Sheets
Key Advantages of Metal AM for Shaft Sleeves:
- Oöverträffad designfrihet: AM liberates designers from the constraints imposed by molds or the subtractive nature of machining. This allows for:
- Optimized Geometries: Designing sleeves with internal cooling channels (if needed), integrated sensor housings, or specific surface textures to improve lubricant retention or sealing performance.
- Topology Optimization: Reducing material usage and weight while maintaining structural integrity, which can be beneficial in weight-sensitive applications or for reducing rotational mass.
- Del Konsolidering: Potentially integrating adjacent components or features into the sleeve design, reducing assembly complexity.
- Rapid Prototyping and Production: The ability to move directly from a CAD file to a physical part without the need for tooling drastically reduces lead times. This is invaluable for:
- Urgent Repairs: Producing replacement sleeves quickly to minimize vessel or equipment downtime.
- Prototyping: Iterating on designs rapidly to test different materials or geometries before committing to larger production runs.
- Low-Volume Production: Manufacturing custom or obsolete shaft sleeves economically where creating traditional tooling would be cost-prohibitive. This makes AM an ideal solution for custom shaft sleeve krav.
- Material Efficiency and Sustainability: AM processes like Powder Bed Fusion (PBF) typically use only the material needed to build the part and its supports.
- Minskat avfall: Significantly less material waste compared to subtractive machining, which can turn a large portion of expensive bar stock into chips. While powder needs careful handling and some is lost or degraded, overall utilization can be much higher.
- Near-Net Shape: Parts are built close to their final dimensions, minimizing the need for extensive post-machining, saving time and energy.
- Access to Specialized Materials: Metal AM facilitates the use of advanced alloys that may be difficult or expensive to procure in traditional forms (like specific bar stock sizes or casting ingots). This includes high-performance materials specifically chosen for marine environments, such as CuNi30Mn1Fe for superior biofouling and corrosion resistance, or specific grades of duplex or super duplex stainless steels. Met3dp, leveraging its advanced powder manufacturing techniques like gas atomization and PREP, specializes in producing metallpulver av hög kvalitet optimized for additive manufacturing, including innovative alloys tailored for demanding applications.
- Supply Chain Agility and Digital Inventory: AM enables on-demand manufacturing and the concept of a digital warehouse.
- Reducerad lagerhållning: Instead of stocking physical sleeves of various sizes, companies can maintain digital files and print parts as needed, reducing warehousing costs and the risk of obsolescence.
- Distributed Manufacturing: Parts can potentially be printed closer to the point of use, reducing shipping times and logistical complexities, a significant advantage for global marine operations.
While traditional methods remain viable, especially for very high-volume production of simple designs where tooling costs can be amortized, 3D-utskrift av metall offers a compelling value proposition for marine shaft sleeves, particularly where corrosion resistance, customization, complex designs, or rapid availability are critical drivers. It represents a shift towards more flexible, efficient, and performance-oriented manufacturing for demanding maritime industry applikationer.
Material Matters: Selecting CuNi30Mn1Fe and 316L for Marine Environments
The choice of material is arguably the most critical factor determining the success and longevity of a marine shaft sleeve. The relentless corrosive attack of seawater, combined with potential galvanic effects, abrasion from seals or particles, and the need for adequate mechanical strength, demands materials specifically engineered for this environment. Metal 3D printing expands the palette of available options, but two materials stand out for their proven performance and suitability for additive manufacturing in marine applications: CuNi30Mn1Fe (often referred to as 90/10 Copper-Nickel or C71500) och 316L Stainless Steel (UNS S31603). Understanding their properties is key for engineers and B2B metal powders purchasers.
CuNi30Mn1Fe (90/10 Copper-Nickel Alloy): The Marine Specialist
This copper-nickel alloy, nominally containing around 30% nickel, 1% manganese, and 1% iron, is renowned for its exceptional resistance to seawater corrosion and biofouling.
- Motståndskraft mot korrosion:
- Seawater Performance: Forms a stable, adherent, protective surface film upon exposure to seawater. This film provides excellent resistance to uniform corrosion and, crucially, significantly inhibits biofouling (the attachment and growth of marine organisms like barnacles and algae). Biofouling can impede performance, increase drag, and accelerate localized corrosion.
- Flowing Seawater: Exhibits good resistance to erosion corrosion in flowing seawater, making it suitable for propeller shaft sleeves and pump components.
- Polluted Waters: Maintains good performance even in polluted or brackish waters often found in harbors and estuaries.
- Galvanic Compatibility: Generally compatible with other copper alloys and stainless steels often used in marine systems, although careful design is still needed to avoid detrimental galvanic couples.
- Mechanical Properties (Typical for AM):
- Styrka: Offers moderate strength, typically lower than stainless steels, but sufficient for many shaft sleeve applications where wear and corrosion are the primary concerns. AM parts can often achieve properties comparable or even superior to wrought counterparts due to the rapid solidification inherent in the process.
- Duktilitet: Possesses good ductility and toughness, making it resistant to brittle fracture.
- Motståndskraft mot slitage: Provides adequate wear resistance for typical sealing applications, though not as high as hardened steels.
- 3D Printability:
- Copper alloys can be challenging to print due to their high thermal conductivity and reflectivity to laser light used in PBF-LB/M systems. However, process parameters for CuNi alloys like CuNi30Mn1Fe are becoming increasingly well-established. Achieving high density and good metallurgical integrity requires careful control over laser power, scan speed, and atmosphere.
- Requires appropriate support structures and often benefits from specific heat treatments post-printing to optimize microstructure and properties.
- Why Choose CuNi30Mn1Fe for Shaft Sleeves? It is the material of choice when biofouling resistance is critical, alongside excellent general seawater corrosion resistance. Ideal for propeller shaft sleeves, seawater cooling pump components, and parts continuously immersed in biologically active waters. Its established track record in marine engineering provides high confidence.
316L Stainless Steel: The Versatile Workhorse
316L is an austenitic stainless steel containing chromium, nickel, and molybdenum. The ‘L’ signifies low carbon content (typically <0.03%), which improves weldability and reduces sensitization (the formation of chromium carbides at grain boundaries), thereby enhancing intergranular corrosion resistance after thermal processes like welding or, relevantly, 3D printing and subsequent heat treatments.
- Motståndskraft mot korrosion:
- General Corrosion: Offers excellent resistance to corrosion in a wide range of environments, including marine atmospheres and moderate chloride concentrations found in seawater. The addition of molybdenum (typically 2-3%) significantly enhances its resistance to pitting and crevice corrosion compared to 304 stainless steel.
- Begränsningar: While good, its resistance to pitting and crevice corrosion in warm, stagnant seawater with high chloride levels is not absolute. It can be susceptible under severe conditions or within tight crevices (like under seals if improperly designed or maintained). It does not possess the inherent biofouling resistance of copper-nickel alloys.
- Stress Corrosion Cracking (SCC): Generally resistant to SCC at ambient marine temperatures, but susceptibility can increase at higher temperatures (>60°C) in chloride environments.
- Mechanical Properties (Typical for AM):
- Styrka: Provides good strength and exhibits excellent work hardening potential. AM 316L often shows higher yield strength compared to annealed wrought 316L due to the fine microstructure generated during printing.
- Ductility & Toughness: Excellent ductility and toughness, even at cryogenic temperatures.
- Motståndskraft mot slitage: Offers better wear resistance than copper-nickel alloys, particularly when work-hardened.
- 3D Printability:
- 316L is one of the most common and well-characterized materials for 3D-utskrift av metall, particularly using PBF-LB/M. It is relatively easy to process, allowing for the production of dense, high-quality parts with good surface finish and dimensional accuracy.
- Extensive research exists on optimal print parameters and post-processing heat treatments (like stress relief annealing or solution annealing) to achieve desired microstructures and mechanical properties.
- Why Choose 316L for Shaft Sleeves? It’s an excellent all-around choice offering a balance of good corrosion resistance (especially pitting and crevice), good mechanical strength, wear resistance, and excellent printability. It is often more cost-effective than specialized alloys like CuNi. Ideal for pump shafts, valve components, and general marine hardware where extreme biofouling is less critical or managed through other means (coatings, cleaning). Its wide availability and established AM processing make it a reliable option for many 316L marine applications.
Material Selection Considerations Summary Table:
Funktion | CuNi30Mn1Fe (90/10 CuNi) | 316L rostfritt stål |
---|---|---|
Primary Advantage | Excellent Biofouling Resistance | Balanced Properties, Printability |
Seawater Corrosion | Utmärkt | Good (Excellent Pitting/Crevice Res.) |
Biofouling Resistance | Utmärkt | Dålig |
Mekanisk styrka | Måttlig | Bra |
Slitstyrka | Rättvist | Bra |
3D Printability | Moderate (Requires Expertise) | Utmärkt |
Relativ kostnad | Högre | Lägre |
Typical Use Case | Propeller Shafts, Seawater Pumps | General Pumps, Valves, Hardware |
Export to Sheets
Choosing between CuNi30Mn1Fe and 316L depends heavily on the specific operating conditions – temperature, flow rate, salinity, biological activity, and potential for crevice formation – as well as mechanical demands and budget constraints. Partnering with an experienced metal AM service provider like Met3dp, which understands both the nuances of these materials and the intricacies of the printing process, is essential. Met3dp’s focus on producing high-sphericity, high-flowability powders using advanced atomization techniques ensures the best possible starting material for printing reliable, high-performance marine shaft sleeves. Their expertise extends to advising on material selection and optimizing print strategies for alloys like 316L and potentially developing parameters for challenging materials like copper-nickel alloys, ensuring the final component meets the rigorous demands of the marine environment.
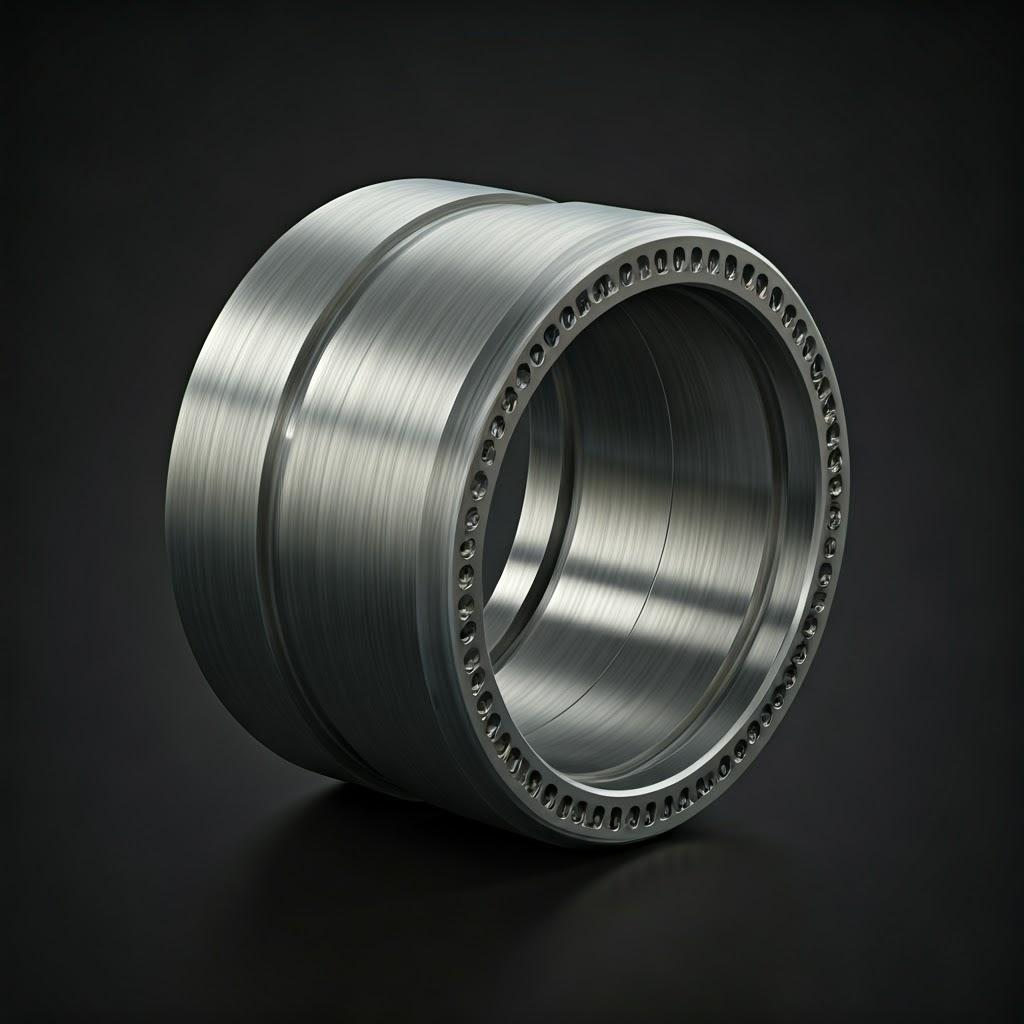
Design for Additive Manufacturing (DfAM): Optimizing Shaft Sleeves for Printing
Simply replicating a design intended for traditional manufacturing often fails to leverage the full potential of metal additive manufacturing and can even introduce new challenges. Designing för additive manufacturing (DfAM) is a crucial paradigm shift that involves optimizing the part geometry not only for its end-use function but also for the layer-by-layer build process itself. For marine shaft sleeves, applying DfAM principles can lead to improved printability, reduced post-processing, enhanced performance, and potentially lower costs, especially when dealing with high-value materials like CuNi30Mn1Fe eller 316L rostfritt stål. Engineers and designers accustomed to subtractive or formative methods must embrace new geometric possibilities and understand the constraints inherent in AM technologies like Powder Bed Fusion (PBF).
Key DfAM Principles for 3D Printed Shaft Sleeves:
- Orientation Optimization:
- Påverkan: The orientation of the sleeve on the build plate significantly affects support structure requirements, build time, surface finish on different faces, and potentially anisotropic mechanical properties (though less pronounced in metals compared to polymers).
- Recommendation for Sleeves: Printing shaft sleeves vertically (along the Z-axis) is often preferred. This typically minimizes supports needed on the critical outer and inner cylindrical surfaces. Supports might still be required for the bottom surface interfacing with the build plate and potentially for overhangs if features like flanges are present. Printing horizontally would require extensive supports along the entire length of the sleeve’s underside, leading to more post-processing and potential surface imperfections on critical diameters after removal.
- Consideration: Vertical orientation increases build height and thus time, but the trade-off for better surface quality and reduced support interaction on functional surfaces is usually worthwhile.
- Support Structure Minimization and Design:
- Syfte: Supports anchor the part to the build plate, prevent warping due to thermal stresses, and support overhanging features (typically angles less than 45 degrees from the horizontal plane).
- Strategy for Sleeves:
- Minimera överhäng: Design flanges or steps with self-supporting angles (typically >45 degrees) where possible. Chamfering edges instead of using sharp overhangs can reduce or eliminate the need for localized supports.
- Optimize Support Contact Points: Design supports that are easy to access and remove without damaging the sleeve surface. Using lightly contacting, easily breakable support structures where possible can simplify removal. Consider where witness marks from support removal are acceptable.
- Internal Supports: Avoid designs requiring extensive internal supports (e.g., complex internal channels not essential for function), as these can be very difficult or impossible to remove completely, potentially trapping loose powder. For standard sleeves, this is less common.
- Wall Thickness Considerations:
- Minimum Thickness: AM processes have limitations on minimum printable wall thickness (often around 0.4-0.8 mm, depending on material and machine). Ensure sleeve walls are sufficiently thick for structural integrity and printability.
- Enhetlighet: Try to maintain relatively uniform wall thickness throughout the part. Abrupt changes in thickness can lead to differential cooling rates, increasing residual stress and potential distortion. Smooth transitions are preferred.
- Material Specifics: Copper alloys like CuNi30Mn1Fe, with their high thermal conductivity, can be more sensitive to issues related to heat dissipation and thin features. Robust wall thicknesses might be more critical compared to 316L.
- Hole and Internal Channel Design:
- Small Holes: Very small diameter holes, especially horizontal ones, can be challenging to print accurately without supports and may require reaming or drilling post-process. Vertical holes generally print more accurately.
- Self-Supporting Holes: Horizontal holes below a certain diameter (often 6-10 mm) might be self-supporting (forming a teardrop shape at the top), but accuracy can be compromised. Consider designing holes vertically or slightly oversized for later machining if tight tolerance is needed.
- Internal Channels (If Applicable): For custom sleeves with internal features (e.g., lubrication grooves), ensure channels are large enough for powder removal and consider designing them with self-supporting geometries.
- Feature Integration and Part Consolidation:
- Potential: While standard shaft sleeves are relatively simple, AM allows for integrating features that might normally be separate parts. Could a flange, a keyway feature (though likely needing machining for final tolerance), or a sensor mounting point be incorporated directly into the print?
- Benefit: Reduces assembly time and potential leak paths or failure points. Requires careful analysis of function and printability trade-offs.
- Designing for Residual Stress Management:
- Issue: The rapid heating and cooling cycles inherent in PBF processes create internal stresses within the part. Sharp corners, large variations in mass, and component rigidity can exacerbate this, leading to warping or even cracking.
- Mitigation through Design:
- Generous Radii: Use fillets and radii instead of sharp internal corners to distribute stress.
- Uniform Mass Distribution: Avoid large, bulky sections connected to thin sections where possible.
- Stress Relief Features: In some complex parts (less common for simple sleeves), sacrificial ribs or specific geometries might be added to help manage stress during the build, to be removed later.
- Leveraging AM-Specific Advantages (Beyond Basic Sleeves):
- Lattice Structures/Lightweighting: While a solid sleeve is typical for wear resistance, if a specialized application required weight reduction (e.g., high-speed rotating equipment), internal lattice structures could be incorporated, maintainable stiffness while reducing mass. This requires significant engineering analysis.
- Conformal Cooling/Heating Channels: For sleeves operating in extreme temperatures, internal channels following the contour of the sleeve could be designed for fluid cooling or heating, impossible with traditional methods.
DfAM Checklist for Marine Shaft Sleeves:
DfAM Consideration | Recommendation / Action | Rationale |
---|---|---|
Build Orientation | Prefer vertical orientation (along Z-axis). | Minimizes supports on critical OD/ID, better surface finish. |
Stödstrukturer | Minimize overhangs (<45°), use chamfers, design easily removable supports. | Reduce post-processing time and cost, avoid surface damage. |
Väggens tjocklek | Maintain minimum printable thickness (e.g., >0.8mm), aim for uniformity, smooth transitions. | Ensure printability, structural integrity, manage thermal stress. |
Holes/Channels | Orient vertically if possible, allow for post-machining if tight tolerance needed. | Improve accuracy, ensure powder removal from internal features. |
Corners/Edges | Use fillets/radii instead of sharp internal corners. | Reduce stress concentrations, minimize cracking risk. |
Feature Integration | Evaluate potential to consolidate adjacent features (flanges, etc.). | Simplify assembly, potentially improve performance. |
Materialöverväganden | Account for thermal properties (e.g., higher conductivity of CuNi). | Adapt design robustness/features for material-specific behavior. |
Post-Processing Access | Ensure critical surfaces needing machining are easily accessible. | Facilitate finishing operations required for dimensional accuracy/finish. |
Leverage Unique Features | Consider lattices or conformal channels only if functional benefit outweighs complexity. | Utilize AM capabilities for performance gains where appropriate. |
Export to Sheets
By proactively incorporating these DfAM principles, manufacturers can ensure that 3D printed marine shaft sleeves are not just viable replacements but potentially superior components, optimized for both the manufacturing process and the demanding marine environment. Collaborating with a service provider like Met3dp, experienced in 3D-utskrift av metall and DfAM, can provide valuable guidance during the design phase.
Precision and Finish: Tolerances and Surface Quality in 3D Printed Sleeves
While metal additive manufacturing offers remarkable design freedom, achieving the high precision and smooth surface finish required for components like marine shaft sleeves often necessitates a combination of the AM process itself and subsequent post-processing steps. Understanding the typical dimensional accuracy metal AM can achieve and the inherent surface characteristics of 3D printed parts is crucial for setting realistic expectations and planning necessary finishing operations. Shaft sleeves demand tight control over diameters, concentricity, and surface texture, particularly on surfaces interfacing with shafts, seals, or bearings.
Dimensionell noggrannhet:
- As-Built Tolerances: The accuracy of a part directly off the metal 3D printer (PBF-LB/M) is influenced by factors like machine calibration, material properties (shrinkage, thermal expansion), part geometry, orientation, support strategy, and thermal stresses accumulated during the build.
- General Tolerances: Typical achievable tolerances for well-controlled PBF processes are often in the range of ±0.1 mm to ±0.2 mm for smaller dimensions (e.g., up to 100 mm), or ±0.1% to ±0.2% for larger dimensions. However, this can vary significantly. For critical dimensions on a shaft sleeve (e.g., inner and outer diameters), this level of precision is usually insufficient for direct use.
- Geometric Tolerances: Controlling features like cylindricity, concentricity, and runout directly from the printer is challenging. While AM can produce complex shapes, achieving the sub-0.05mm tolerances often required for these geometric features on rotating components typically necessitates post-machining.
- Post-Machining Tolerances: Recognizing the limitations of as-built accuracy, critical features on 3D printed shaft sleeves are almost always finished using traditional CNC machining (e.g., turning, grinding).
- Achievable Precision: Post-machining allows for tolerances comparable to fully machined parts. Achieving ISO tolerance grades like IT6 or IT7 (which correspond to tolerances in the range of micrometers, depending on the nominal size) on critical diameters is standard practice. Concentricity and runout can also be brought within typical engineering specifications (e.g., <0.02 mm) through careful machining setups.
Surface Finish (Roughness):
- As-Built Surface Roughness: The surface finish of as-built metal AM parts is inherently rougher than machined surfaces. This is due to the layer-by-layer process and the partially melted powder particles adhering to the surface.
- Typical Values (Ra): Surface roughness (Ra – arithmetic average roughness) depends heavily on the print parameters, powder particle size, material, and surface orientation relative to the build direction.
- Top Surfaces: Generally smoother, potentially Ra 5-15 µm.
- Vertical Walls: Moderate roughness, often Ra 8-20 µm.
- Upward-Facing Slanted Surfaces: Tend to be smoother than downward-facing ones.
- Downward-Facing Surfaces (Overhangs): Typically the roughest, often exceeding Ra 15-25 µm, heavily influenced by support structures.
- Implications for Sleeves: An as-built Ra of 10-20 µm is generally too rough for dynamic sealing surfaces or bearing interfaces, which often require Ra < 1.6 µm, < 0.8 µm, or even < 0.4 µm depending on the application (e.g., lip seal contact zones).
- Typical Values (Ra): Surface roughness (Ra – arithmetic average roughness) depends heavily on the print parameters, powder particle size, material, and surface orientation relative to the build direction.
- Achievable Surface Finish After Post-Processing: Various techniques can dramatically improve the surface finish.
- Machining (Turning/Grinding): Standard method for achieving smooth, precise cylindrical surfaces. Can easily achieve Ra < 1.6 µm, and with grinding or fine turning/polishing, Ra < 0.8 µm or < 0.4 µm is achievable on both CuNi30Mn1Fe och 316L.
- Polering: Mechanical or electrochemical polishing can further reduce surface roughness for highly critical applications or aesthetic requirements.
- Mass Finishing (Tumbling): Can improve surface finish and remove sharp edges on non-critical surfaces but is less precise than machining for controlling dimensions.
- Shot Peening/Abrasive Blasting: Primarily used to modify surface stress (improve fatigue life) or clean surfaces; can alter roughness but isn’t typically used for achieving fine finishes on sealing surfaces.
Factors Influencing Precision and Finish in AM Shaft Sleeves:
Faktor | Impact on As-Built Precision/Finish | Mitigation / Control Strategy |
---|---|---|
Machine Calibration | Directly affects dimensional accuracy (laser spot size, positioning). | Regular maintenance, calibration routines by the service provider. |
Processparametrar | Laser power, scan speed, layer thickness affect density & roughness. | Optimized parameter sets specific to material (CuNi, 316L) & machine. |
Materialegenskaper | Shrinkage, thermal conductivity influence stress & distortion. | Material-specific parameter tuning, thermal modeling (advanced). |
Part Orientation | Affects support needs, surface roughness anisotropy. | Optimal orientation (often vertical for sleeves) determined in DfAM. |
Support Strategy | Supports prevent distortion but leave witness marks/roughness. | Careful support design, planning for removal and finishing. |
Termisk hantering | Build plate heating, gas flow control minimize warping. | Process control features of the AM system. |
Kvalitet på pulver | Particle size distribution, morphology affect packing & melting. | Use of high-quality, spherical powders (e.g., from Met3dp). |
Post-Build Heat Treat | Relieves stress, which can cause slight dimensional changes. | Account for minor changes during machining allowance planning. |
Export to Sheets
Summary: Procurement managers and engineers should specify required final tolerances and surface finishes based on the functional requirements of the shaft sleeve, understanding that these will typically be achieved through post-machining operations rather than the as-built AM process. The key advantage AM offers is the creation of the near-net shape, potentially with complex features or using specialized materials like CuNi30Mn1Fe, which is then brought to final specification by established finishing techniques. Partnering with a service provider who understands both the AM process and the necessary krav på efterbehandling is essential for success.
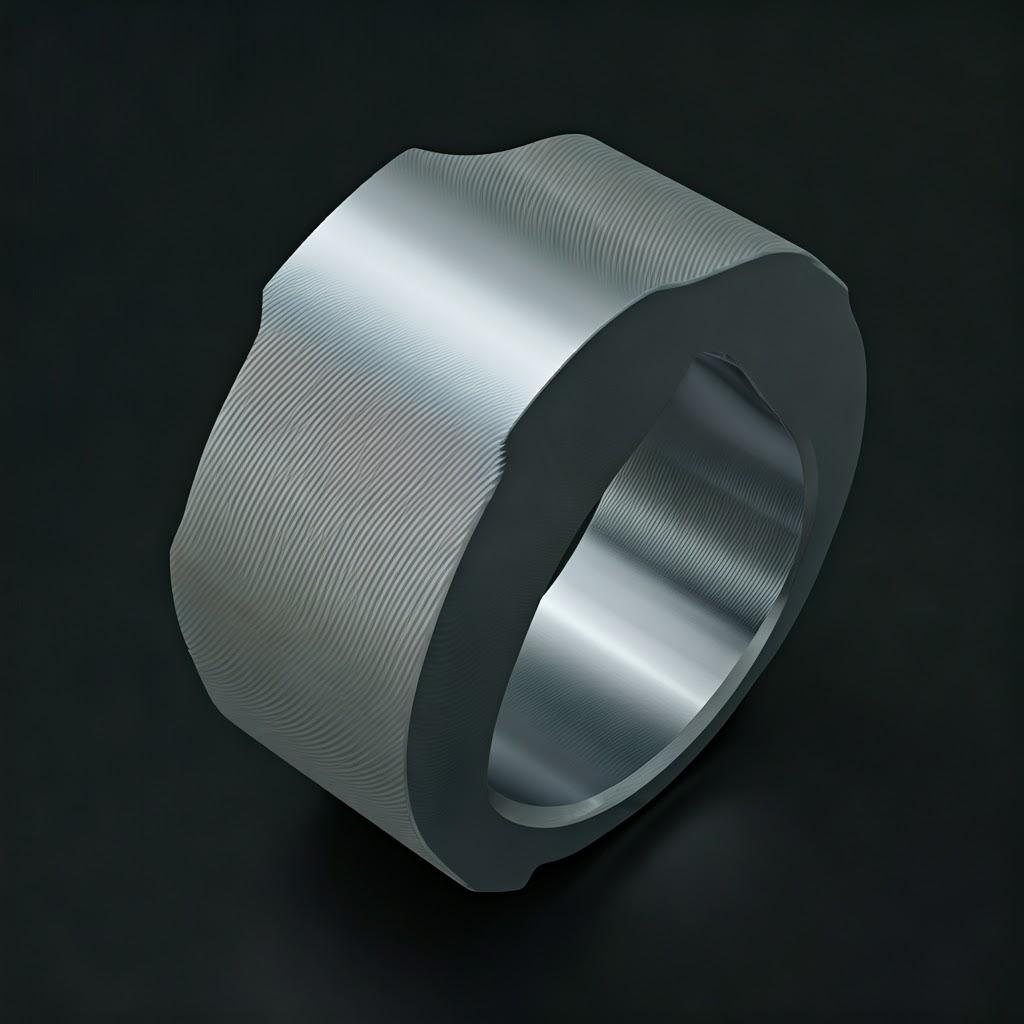
Post-Processing Pathways: Finishing Touches for Optimal Performance
A metal 3D printed part, upon removal from the build chamber, is rarely ready for its end-use application, especially for demanding components like marine shaft sleeves. A series of post-processing steps are typically required to transform the near-net shape AM part into a functional, reliable, and dimensionally accurate component. These steps address residual stresses, remove support structures, achieve required tolerances and surface finishes, and ensure the material possesses the desired microstructure and mechanical properties. The specific pathway depends on the material (CuNi30Mn1Fe vs. 316L), the complexity of the sleeve design, and the final application requirements.
Common Post-Processing Steps for 3D Printed Shaft Sleeves:
- Stress Relief / Heat Treatment:
- Syfte: The rapid heating/cooling cycles during PBF-LB/M create significant residual stresses within the printed part. These stresses can cause distortion (especially after removal from the build plate), reduce fatigue life, and potentially lead to cracking. Heat treatment is crucial to relieve these stresses and homogenize the microstructure.
- Process: Parts are typically heat-treated while still attached to the build plate (if possible and practical) or immediately after removal. The specific cycle (temperature, duration, cooling rate, atmosphere – e.g., vacuum or inert gas like Argon) depends heavily on the alloy:
- 316L rostfritt stål: Common treatments include stress relief annealing (e.g., 650-900°C) or full solution annealing (e.g., 1040-1150°C followed by rapid cooling) to dissolve any detrimental phases (like sigma phase) and restore optimal corrosion resistance and ductility. Low carbon content (‘L’) minimizes sensitization risk, but proper annealing is still vital.
- CuNi30Mn1Fe: Heat treatment protocols are less standardized in AM compared to 316L but typically involve annealing at temperatures appropriate for copper-nickel alloys (e.g., 600-800°C) to relieve stress and potentially improve ductility. Careful control is needed to maintain the desired phase structure and corrosion properties.
- Outcome: Reduced residual stress, improved dimensional stability for subsequent machining, potentially enhanced mechanical properties (though sometimes a trade-off between strength and ductility), optimized corrosion resistance.
- Removal from Build Plate:
- Method: Usually done using wire EDM (Electrical Discharge Machining) or a bandsaw. Wire EDM provides a cleaner cut with minimal mechanical stress.
- Consideration: Access for the cutting tool needs to be considered during build setup.
- Borttagning av stödstruktur:
- Method: Can range from manual breaking/clipping for lightly connected supports to CNC machining or grinding for more robust or intricate support structures. Access can be a major challenge, highlighting the importance of DfAM.
- Utmaningar: Risk of damaging the part surface, incomplete removal (especially internal supports), time-consuming manual labor. Support locations on critical surfaces must be carefully planned to allow for clean-up during machining.
- CNC Machining (Turning/Grinding):
- Syfte: This is often the most critical step for shaft sleeves to achieve the required dimensional accuracy and surface finish on functional diameters (inner bore, outer diameter) and faces.
- Operations:
- Turning: Used to machine outer and inner diameters to precise dimensions and achieve smooth surfaces (e.g., Ra < 1.6 or < 0.8 µm). Creates true cylindrical forms and ensures concentricity.
- Facing: Machining the ends of the sleeve to achieve required length and perpendicularity to the axis.
- Grooving/Keyway Cutting: Adding features like O-ring grooves, lubrication grooves, or keyways if required by the design.
- Slipning: Used when extremely tight tolerances (e.g., IT5/IT6) or very fine surface finishes (e.g., Ra < 0.4 µm) are necessary, particularly on hardened materials (though 316L and CuNi are typically not hardened significantly).
- Consideration: Sufficient machining allowance (stock) must be included in the 3D printed part design (e.g., adding 0.5-1.5 mm to surfaces that will be machined).
- Surface Finishing & Cleaning:
- Syfte: Further improve surface quality beyond machining, remove contaminants, and prepare for inspection or coating.
- Metoder:
- Polering: Mechanical polishing using progressively finer abrasives for mirror-like finishes on specific areas (e.g., seal contact zones). Electropolishing can also be used, especially for 316L, to smooth surfaces and improve corrosion resistance by removing the micro-rough outer layer.
- Mass Finishing (Tumbling, Vibratory Finishing): Can deburr edges and provide a uniform, smooth finish on external surfaces, though less precise than machining.
- Abrasive Blasting (Sandblasting, Bead Blasting): Used for cleaning, creating a uniform matte finish, or surface texturing. Must be carefully controlled to avoid damaging critical surfaces or embedding abrasive media.
- Cleaning: Thorough cleaning using solvents or aqueous solutions to remove machining fluids, loose powder, and other contaminants.
- Inspection and Quality Assurance (QA):
- Syfte: Verify that the finished sleeve meets all specifications.
- Metoder:
- Dimensionell inspektion: Using CMMs (Coordinate Measuring Machines), micrometers, calipers, gauges to verify diameters, lengths, concentricity, etc.
- Surface Finish Measurement: Using profilometers.
- Icke-förstörande testning (NDT): Dye penetrant testing (DPT) or liquid penetrant inspection (LPI) to detect surface-breaking cracks or porosity. Radiographic testing (X-ray) or CT scanning for internal defects (porosity, inclusions), though less common for standard sleeves unless criticality demands it.
- Material Certification: Verifying powder batch certification and potentially testing sample coupons printed alongside the parts for mechanical properties.
- Optional Coating:
- Syfte: Add functionality not inherent in the base material (e.g., enhanced wear resistance, specific lubricity, dielectric properties).
- Exempel på detta: While CuNi and 316L offer good corrosion resistance, specific applications might benefit from thin, hard coatings (like certain ceramics or polymers) on wear surfaces, although compatibility and adhesion must be carefully evaluated.
Post-Processing Workflow Example for a 3D Printed Shaft Sleeve:
- Build Part (Vertical Orientation) with Supports.
- Heat Treatment (Stress Relief) on Build Plate.
- Wire EDM Removal from Build Plate.
- Manual/Machined Support Removal.
- CNC Turning (Outer Diameter, Inner Diameter, Facing Ends).
- CNC Milling (Keyway/Grooves if needed).
- Polishing (Seal Contact Areas if required).
- Deburring/Edge Breaking.
- Cleaning.
- Final Inspection (Dimensional, Surface Finish, NDT if specified).
Understanding this comprehensive post-processing chain is vital for accurately estimating costs and lead times. Collaborating with a full-service provider or having a clear plan for managing these steps is essential for successfully implementing metal component finishing for 3D printed marine shaft sleeves.
Navigating Challenges: Common Issues and Solutions in Printing Shaft Sleeves
While metal 3D printing offers significant advantages for producing marine shaft sleeves, the process is not without its challenges. Awareness of potential metal 3D printing defects and issues, along with strategies for mitigation and resolution, is crucial for ensuring the production of high-quality, reliable components. Many of these challenges are interconnected and can be addressed through careful design (DfAM), precise process control, high-quality materials, and appropriate post-processing.
Common Challenges and Mitigation Strategies:
- Warping and Distortion:
- Issue: Significant thermal gradients during the PBF process lead to expansion and contraction, creating internal stresses. If these stresses exceed the material’s yield strength or the anchoring force of the supports, the part can warp or distort, particularly long, relatively thin cylindrical shapes like sleeves.
- Causes: High thermal gradients, insufficient support, non-optimal scan strategy, large cross-sectional areas, abrupt geometry changes.
- Mitigation:
- Optimized Orientation & Supports: Vertical orientation helps, robust support structures designed to counteract expected stresses are critical.
- Scan-strategi: Using techniques like island scanning or alternating hatch directions can help distribute heat more evenly.
- Termisk hantering: Utilizing build plate heating (common in PBF machines) reduces thermal gradients.
- Stressavlastning: Prompt post-build heat treatment is essential to relieve accumulated stresses before significant distortion occurs upon removal from the plate/supports.
- Design: Maintaining uniform wall thickness and using fillets helps manage stress concentration.
- Återstående stress:
- Issue: Even if visible warping doesn’t occur, high residual stresses remain locked within the printed part. These can negatively impact fatigue life, dimensional stability during machining, and susceptibility to stress corrosion cracking (though less common for 316L/CuNi at marine temperatures).
- Causes: Inherent to the layer-wise melting and solidification process.
- Mitigation:
- Processparameteroptimering: Fine-tuning laser power, speed, etc., can influence stress levels.
- Mandatory Heat Treatment: Stress relief annealing is the primary method for significantly reducing residual stress to acceptable levels. This is non-negotiable for functional parts.
- Design: Avoiding sharp internal corners helps minimize stress concentration points.
- Porositet:
- Issue: The presence of small voids or pores within the printed material. Porosity can reduce mechanical strength (especially fatigue strength), decrease density, and potentially create leak paths or initiation sites for corrosion.
- Causes:
- Gas Porosity: Trapped shielding gas (e.g., Argon) within the melt pool due to instability or excessive laser power.
- Lack of Fusion Porosity: Insufficient energy density (laser power too low or scan speed too high) leads to incomplete melting between layers or adjacent scan tracks. Keyhole porosity can occur if energy density is too high, causing vapor cavity instability.
- Pulverkvalitet: Entrained gas within powder particles, poor powder morphology, or contamination can contribute.
- Mitigation:
- Processparameteroptimering: Extensive development is done by machine manufacturers and service providers to find optimal parameters (laser power, speed, hatch spacing, layer thickness) that achieve >99.5% density for materials like 316L. Parameters for CuNi alloys require careful tuning due to their thermal properties.
- High-Quality Powder: Using powder with high sphericity, controlled particle size distribution, good flowability, and low internal gas content is crucial. This is an area where suppliers like Met3dp, with their advanced gas atomization and PREP powder production systems, add significant value.
- Machine Conditions: Maintaining a clean build environment with proper inert gas shielding (oxygen levels < 1000 ppm, often much lower).
- Het isostatisk pressning (HIP): A post-processing step involving high temperature and high pressure inert gas. HIP can effectively close internal pores (those not connected to the surface), significantly improving density and fatigue properties. It adds cost and time but may be specified for highly critical components.
- Support Removal Difficulties:
- Issue: Supports, while necessary, must be removed. This can be labor-intensive and risks damaging the part surface, especially if access is poor or supports are fused too strongly.
- Causes: Overly robust support design, complex part geometry hindering access, supports placed on critical surfaces.
- Mitigation:
- DfAM: Design parts to be self-supporting where possible, optimize orientation, use chamfers.
- Smart Support Strategies: Utilize support structures designed for easier removal (e.g., perforated or thin contact points). Software tools often offer various support types.
- Plan for Access: Ensure tools (manual or CNC) can reach support structures.
- Machining Allowance: Leave extra material on surfaces where supports are attached, allowing the witness marks to be machined away during finishing.
- Ytjämnhet:
- Issue: As-built surfaces are generally too rough for sealing or bearing applications. Downward-facing surfaces and areas affected by supports are particularly rough.
- Causes: Layer-wise building, adherence of partially melted powder, support contact points.
- Mitigation:
- Orientation: Print critical surfaces vertically or as upward-facing surfaces where possible.
- Parameter Tuning: Slight adjustments can influence finish, but limitations exist.
- Mandatory Post-Processing: Plan for machining, grinding, or polishing of all critical functional surfaces to achieve the required Ra value.
- Material-Specific Challenges:
- CuNi30Mn1Fe: High thermal conductivity and laser reflectivity make it harder to process consistently than steels. Requires higher laser power and careful parameter control to avoid incomplete fusion or excessive heat buildup. Oxidation potential requires excellent atmospheric control.
- 316L: Generally very printable, but achieving optimal corrosion resistance requires low carbon content (‘L’ grade) and proper heat treatment (solution annealing) to avoid sensitization or formation of detrimental phases like sigma phase, especially if the part experiences elevated temperatures in service.
By understanding these potential hurdles and implementing robust mitigation strategies throughout the design, printing, and post-processing stages, manufacturers can successfully produce high-quality, reliable 3D printed marine shaft sleeves med hjälp av korrosionsbeständig materials like CuNi30Mn1Fe and 316L. Partnering with an experienced AM service provider with deep material and process knowledge is key to navigating these challenges effectively.
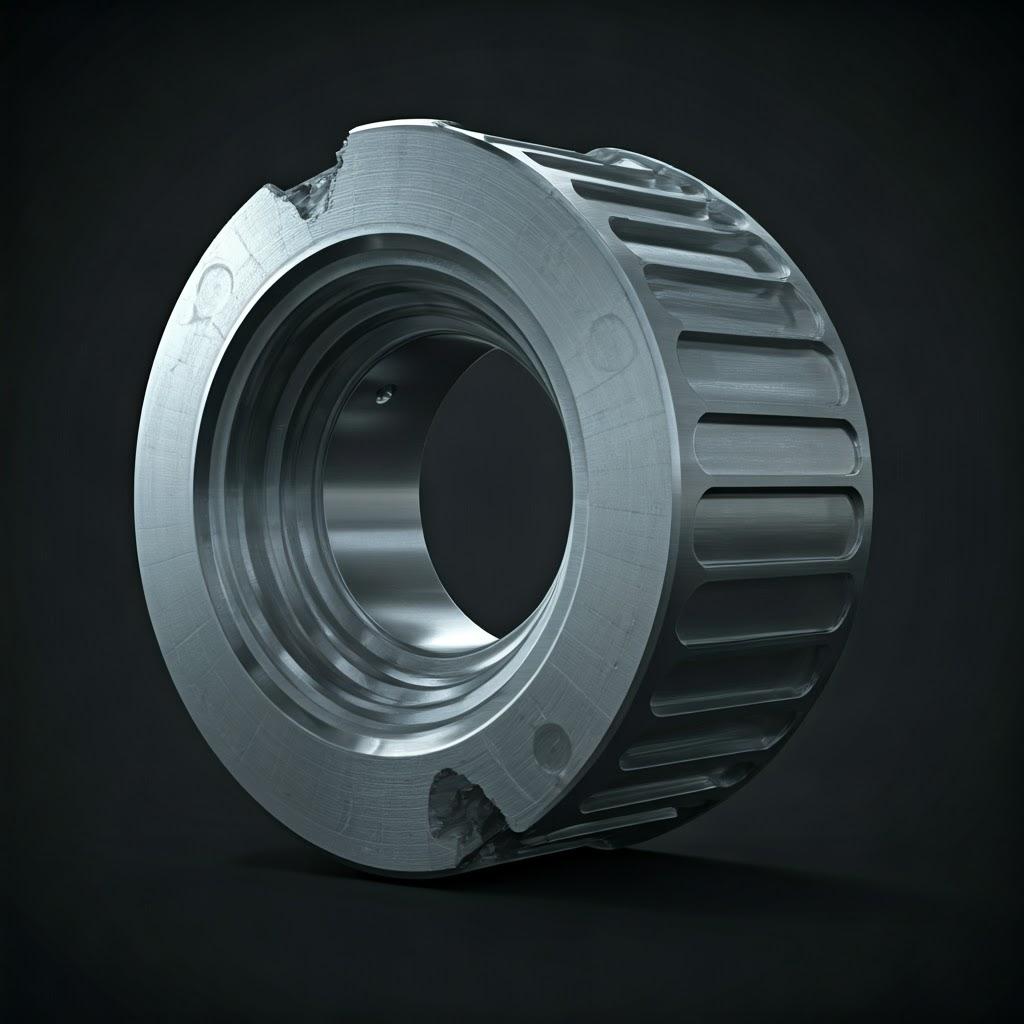
Choosing Your Partner: Selecting the Right Metal 3D Printing Service Provider
The success of utilizing metal additive manufacturing for critical components like marine shaft sleeves hinges not only on the technology itself but significantly on the expertise and capabilities of the chosen metal AM service provider. Selecting the right partner is a crucial decision for engineers and procurement managers, ensuring that the final parts meet stringent quality standards, performance requirements, and delivery timelines. With the growing number of providers, evaluating potential partners requires a systematic approach focusing on technical proficiency, quality systems, material expertise, and overall service capabilities. A mismatch in capabilities or understanding can lead to suboptimal parts, delays, and unexpected costs.
Key Criteria for Evaluating Metal AM Service Providers:
- Technical Expertise and Experience:
- Material Specialization: Does the provider have proven experience working with the specific alloys required, such as CuNi30Mn1Fe och 316L rostfritt stål? Ask for case studies, sample parts, or material property data generated from their processes. Handling challenging materials like copper alloys requires specific expertise beyond common steels or titanium.
- Process Knowledge (PBF-LB/M): Deep understanding of the Powder Bed Fusion process, including parameter optimization for density, accuracy, and surface finish, is essential. They should understand the nuances of thermal management, support strategies, and potential defects associated with the chosen materials and geometries.
- DfAM Consultation: A valuable partner should offer Design for Additive Manufacturing support, helping you optimize your shaft sleeve design for printability, cost-effectiveness, and performance.
- Engineering Support: Availability of engineers to discuss application requirements, material selection trade-offs, and post-processing options.
- Material Quality and Handling:
- Powder Sourcing and Traceability: Where does the provider source their metal powders? Do they use powders from reputable suppliers with clear specifications and batch traceability? Can they provide material certifications? For demanding applications, consistency starts with the raw material. Companies like Met3dp, which manufacture their own metallpulver av hög kvalitet using advanced techniques like gas atomization and PREP, offer a distinct advantage in controlling input material quality and consistency.
- Powder Handling Procedures: Proper storage, handling, sieving, and recycling protocols are critical to prevent contamination (especially cross-contamination between alloys) and moisture absorption, and to maintain powder quality over time. Ask about their procedures.
- Equipment and Technology:
- Machine Platform: Do they operate well-maintained, industrial-grade PBF-LB/M machines suitable for the required materials? Ensure the machine’s build volume is adequate for your sleeve dimensions and potential batch sizes.
- Accuracy and Reliability: Inquire about the typical accuracy and repeatability of their machines and processes. Met3dp, for instance, highlights its printers’ industry-leading print volume, accuracy and reliability for mission-critical parts.
- Technology Breadth: While PBF-LB/M is common for these materials, does the provider offer other potentially relevant metal AM technologies if needed for different components?
- Quality Management System (QMS) and Certifications:
- ISO 9001: This is a fundamental certification indicating a documented and followed quality management system.
- Industry-Specific Certifications: While perhaps not strictly required for all marine sleeves, certifications like AS9100 (Aerospace) or ISO 13485 (Medical) demonstrate a higher level of process control, traceability, and risk management, which can be beneficial for critical applications.
- Processtyrning: Evidence of robust process monitoring, data logging, and part inspection protocols. How do they ensure consistency from build to build?
- Metrology Capabilities: In-house or verified third-party capabilities for dimensional inspection (CMM), surface finish measurement, and potentially NDT.
- Post-Processing Capabilities:
- In-House vs. Outsourced: Does the provider offer essential post-processing steps like heat treatment, CNC machining, and finishing in-house, or do they manage a network of qualified subcontractors? In-house capabilities can sometimes streamline workflow and improve control, but a well-managed external network can also be effective.
- Machining Expertise: Specific experience in machining AM parts is crucial, as they can sometimes behave differently than wrought materials due to their unique microstructure. Ensure they can achieve the required tolerances and surface finishes on critical sleeve diameters.
- Finishing and Testing: Capabilities for polishing, NDT (DPT, X-Ray if needed), and other required finishing steps.
- Capacity, Lead Time, and Responsiveness:
- Produktionskapacitet: Can they handle your required volumes, from single prototypes to potential series production, within acceptable timeframes?
- Realistic Lead Times: Providers should offer transparent and realistic lead time estimates that account for design review, printing, cooling, and all necessary post-processing steps. Request quotes with detailed timelines.
- Communication and Project Management: Responsive communication, clear points of contact, and effective project management are vital for a smooth engagement, especially for B2B manufacturing partners.
- Industry Experience:
- Relevant Sector Knowledge: Has the provider worked on projects in the marine, offshore, oil & gas, or other industries with similar demanding environments and material requirements? This experience translates to a better understanding of application-specific needs and challenges.
Evaluation Checklist Summary:
Kriterier | Key Questions to Ask | Betydelse |
---|---|---|
Teknisk expertis | Experience with CuNi/316L? DfAM support? PBF-LB/M process knowledge? Engineering consultation? | Mycket hög |
Materialkvalitet | Powder source & certs? Handling procedures? Traceability? (Consider integrated powder/print providers like Met3dp) | Mycket hög |
Equipment & Technology | Suitable PBF machines? Build volume? Accuracy claims? Machine maintenance? | Hög |
Quality System (QMS) | ISO 9001? Other relevant certs? Process control methods? Metrology capabilities? | Mycket hög |
Efterbearbetning | In-house/outsourced capabilities (Heat treat, CNC, Finish, NDT)? Experience machining AM parts? Tolerance achievement? | Mycket hög |
Capacity & Lead Time | Volume handling? Realistic timelines? Quote transparency? | Hög |
Service & Communication | Responsiveness? Project management? Point of contact? | Hög |
Erfarenhet av branschen | Marine/Offshore/Industrial project examples? Understanding of harsh environments? | Måttlig till hög |
Export to Sheets
Choosing a metal AM partner is about more than just finding the lowest price; it’s about establishing a relationship with a supplier who can consistently deliver high-quality, functional parts that meet the rigorous demands of the marine environment. Thorough vetting using these criteria will help ensure you select a capable and reliable provider like Met3dp, equipped to handle the complexities of producing corrosion-resistant shaft sleeves via additive manufacturing.
Cost and Time Analysis: Factors Influencing Price and Delivery
One of the most pressing questions for businesses considering metal additive manufacturing is understanding the associated costs and expected delivery times. While AM offers compelling technical advantages, its economic viability compared to traditional methods depends on various factors. For marine shaft sleeves, particularly those made from specialized alloys like CuNi30Mn1Fe or requiring customization or rapid turnaround, AM can be highly competitive. However, a clear understanding of the metal 3D printing cost drivers and lead time components is essential for accurate budgeting and project planning.
Key Cost Factors for 3D Printed Shaft Sleeves:
- Material Cost:
- Powder Price: The cost per kilogram of the metal powder is a significant factor. High-performance alloys like CuNi30Mn1Fe are generally more expensive than standard 316L stainless steel. Prices fluctuate based on market conditions and supplier.
- Material Consumption: This includes the volume of the actual part plus the volume of support structures needed. Efficient DfAM and nesting multiple parts in a build can optimize material usage.
- Återvinning av pulver: While much unused powder can be sieved and reused, there are limits to recyclability, and some material loss occurs during handling. This is factored into overheads or material costs.
- AM Machine Time:
- Hourly Rate: Industrial metal AM machines represent a significant capital investment, leading to relatively high hourly operating rates.
- Byggtid: This is primarily driven by the height of the build (Z-axis). Printing sleeves vertically (often preferred for quality) increases build height and thus time compared to horizontal printing (which requires more support). The volume/cross-sectional area of the part per layer also influences the time taken to scan each layer.
- Nesting Efficiency: Printing multiple sleeves (or other parts) simultaneously in one build significantly reduces the machine time cost allocated per part.
- Kostnader för arbetskraft:
- Pre-Processing: File preparation, DfAM analysis, build setup simulation, and support generation require skilled engineering time.
- Machine Operation: Monitoring the build process.
- Post-Processing Labor: Significant labor is involved in part removal, support removal (can be very time-consuming), cleaning, inspection, and potentially manual finishing steps.
- Kvalitetssäkring: Time for dimensional inspection, NDT, documentation.
- Kostnader för efterbearbetning:
- Värmebehandling: Furnace time, energy consumption, and use of inert atmospheres add cost.
- CNC Machining: Often a major cost component. Depends on the amount of material to be removed, the complexity of the features (diameters, faces, grooves), required tolerances, and surface finish. Machining time on CNC lathes or mills is billed accordingly.
- Specialized Finishing: Polishing, grinding, coating – each adds cost based on time and materials.
- NDT: Costs associated with performing and interpreting non-destructive tests if required.
- Delkomplexitet:
- While AM handles complexity well, highly intricate designs may require more complex support structures (increasing material use and removal time) and potentially longer print times if they have large cross-sections or fine features requiring slower scan speeds.
- Batch Size / Volume:
- Amortization: Setup costs (file prep, machine setup) are amortized over the number of parts in a batch. Larger batches generally result in a lower cost per part.
- Nesting: Printing multiple parts efficiently utilizes the build volume and machine time, reducing per-part cost.
- Wholesale Pricing: For larger volume orders or ongoing contracts, specialized wholesale pricing metal AM structures may be negotiable with service providers. However, AM’s strength often lies in its cost-effectiveness even at low volumes (1-100 parts) compared to methods requiring expensive tooling (like casting).
Lead Time Components:
Lead time is the total duration from order placement to final part delivery. It’s crucial to understand that print time is only one part of this.
- Quoting & Design Review (1-5 days): Initial consultation, file check, DfAM review (if needed), quote generation and approval.
- Queue Time (1-10+ days): Waiting for an available slot on the appropriate AM machine. This can vary significantly based on the service provider’s workload.
- Build Preparation (0.5-1 day): Finalizing the build layout (nesting), generating support structures, slicing the file, and setting up the machine.
- Print Time (1-5+ days): Highly dependent on the sleeve height, volume, and number of parts per build. A tall build with multiple sleeves could take several days.
- Cool Down & Part Removal (0.5-1 day): Allowing the build chamber and parts to cool sufficiently before safe removal and depowdering.
- Post-Processing (3-15+ days): This is often the longest and most variable phase.
- Stress Relief/Heat Treatment: Typically 1-2 days (including furnace time and cooling).
- Support Removal & Basic Finishing: 1-3 days, depending on complexity.
- CNC Machining: 2-7+ days, depending on complexity, tolerances, and machine shop availability (whether in-house or outsourced).
- Specialized Finishing/Coating: Adds further time.
- Inspection/QA: 1-2 days.
- Shipping (1-5+ days): Depends on location and shipping method.
Total Estimated Lead Time: For a batch of 3D printed marine shaft sleeves, a typical lead time might range from 2 till 6 veckor, heavily dependent on the factors above, particularly post-processing complexity and machine queue times. Urgent orders may sometimes be expedited for a premium cost if capacity allows.
Obtaining Accurate Estimates:
- Provide a clear 3D CAD model and technical drawing specifying materials, critical tolerances, surface finishes, and any required testing or certifications.
- Discuss the application and operating environment with the service provider.
- Request a detailed quote that breaks down costs (material, machine time, labor, post-processing) and provides a realistic lead time estimate with key milestones.
By understanding these cost and time dynamics, businesses can better evaluate the feasibility of using metal AM for marine shaft sleeves and engage with service providers more effectively.
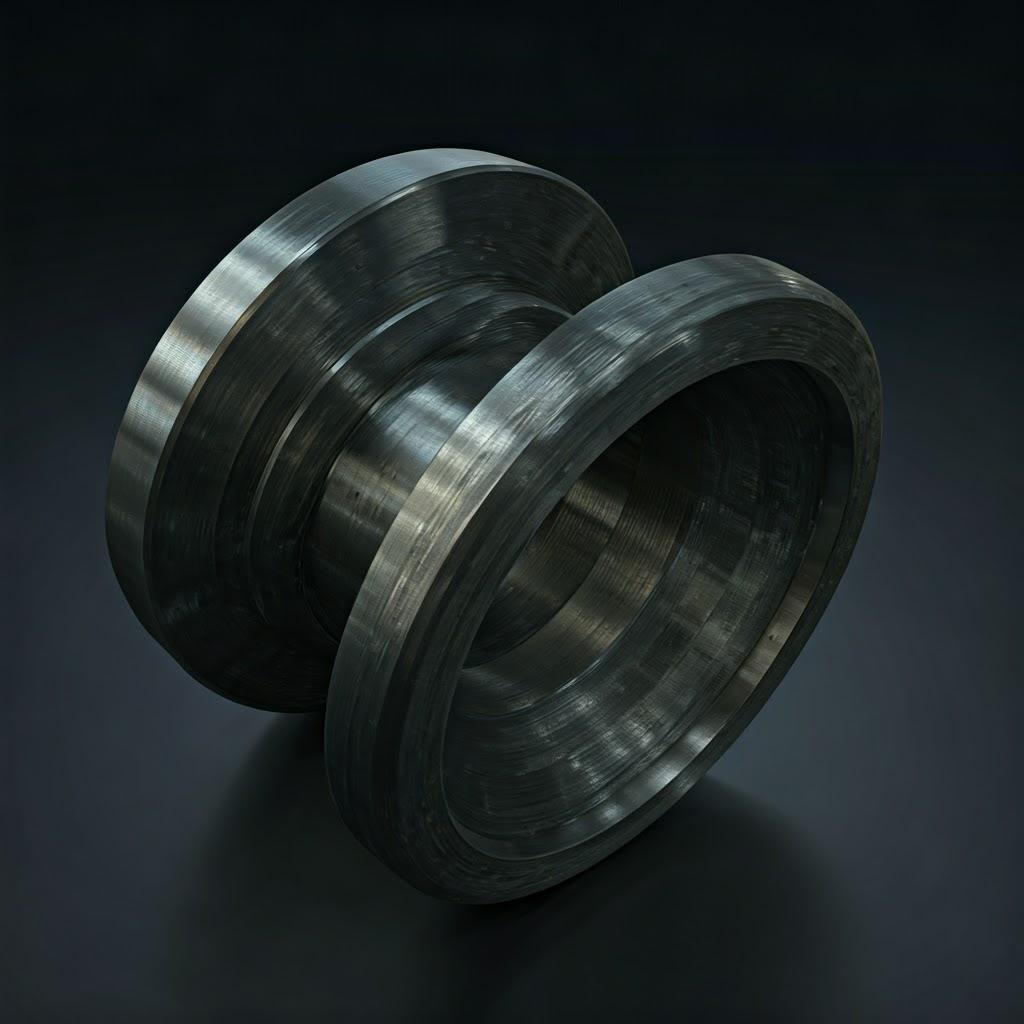
Frequently Asked Questions (FAQ) about 3D Printed Marine Shaft Sleeves
Here are answers to some common questions engineers and procurement managers have about using metal 3D printing for marine shaft sleeves:
- How does the durability and lifespan of a 3D printed shaft sleeve compare to a traditionally manufactured one (cast or machined)?
- The durability is primarily determined by the chosen material and the quality of the manufacturing process (both printing and post-processing). When printed correctly using appropriate materials like CuNi30Mn1Fe eller 316L and properly post-processed (heat treated for stress relief and microstructure, machined to final tolerances), a 3D printed sleeve can exhibit comparable or even superior performance to its traditional counterparts. Metal AM parts can achieve near 100% density and mechanical properties (strength, ductility) that meet or exceed ASTM standards for equivalent wrought or cast materials. Furthermore, AM allows for potential design optimizations (e.g., improved geometry near seals) or the use of specialized alloys that might be difficult to source traditionally, potentially leading to enhanced lifespan in specific corrosive or wear environments. Key is partnering with a quality provider who ensures correct material processing and finishing.
- Is metal 3D printing a cost-effective method for producing shaft sleeves compared to casting or machining from bar stock?
- It depends heavily on several factors:
- Volym: For very high volumes (thousands of identical sleeves), traditional casting or high-speed machining may be more economical due to amortized tooling costs or optimized subtractive processes.
- Komplexitet: For simple sleeve designs, traditional methods are often competitive. However, if the sleeve has complex geometry or integrated features, AM can become more cost-effective by eliminating complex machining setups or assembly steps.
- Material: For standard materials available readily as bar stock (like basic stainless steel grades), machining can be cheap. For specialized alloys like CuNi30Mn1Fe, which might have limited availability or high cost in bar form, AM (printing directly from powder) can be competitive, especially considering reduced material waste.
- Ledtid: If rapid prototyping, urgent spares, or short lead times are critical, AM’s ability to produce parts directly from CAD without tooling offers significant value, often justifying a potentially higher per-part cost.
- Anpassning: For custom, one-off, or low-volume replacement sleeves (e.g., for obsolete equipment), AM is almost always more cost-effective than creating new casting patterns or complex machining setups.
- In summary: AM is most cost-effective for low-to-medium volumes, high-complexity parts, customized designs, specialized materials, and applications where lead time is critical.
- It depends heavily on several factors:
- What are the typical lead times I can expect for a prototype or a small batch (e.g., 5-10 units) of 3D printed marine shaft sleeves?
- As detailed in the previous section, lead times involve more than just printing. A rough estimate for a prototype or small batch would typically be in the range of 2 till 6 veckor. This includes design review/prep (~1 week), printing and cooling (~1 week), and essential post-processing like heat treatment and CNC machining (~1-4 weeks). Factors like material choice (CuNi might require more specialized handling), complexity of machining, required testing (NDT), and the service provider’s current workload can influence this significantly. Always request a specific timeline with your quote.
- What quality certifications or standards should I look for when choosing a metal 3D printing service provider for marine components?
- ISO 9001: This is the baseline certification for a quality management system, indicating documented processes and procedures.
- Material Certifications: Ensure the provider can supply certifications for the metal powder used, confirming its chemical composition and key characteristics, with traceability back to the batch.
- Process Control Documentation: While specific “AM certifications” are still evolving, inquire about their internal process control, validation procedures, and operator training standards.
- Relevant Industry Standards (Optional but beneficial): AS9100 (Aerospace) or ISO 13485 (Medical) certifications suggest a very high level of quality control and traceability, often beneficial even for non-aerospace/medical parts requiring high reliability.
- Testing Compliance: Ensure they can perform or manage required testing (dimensional, NDT, mechanical) according to specified standards (e.g., ASTM, ISO).
- Can I simply send my existing 2D drawing or 3D model of a traditionally designed sleeve and have it printed?
- Yes, you can send your existing design files. However, it is highly recommended to have the design reviewed by the AM service provider’s engineers for DfAM (Design for Additive Manufacturing) suitability. While a direct print might be possible, minor modifications – such as optimizing orientation, adjusting wall thicknesses, adding fillets, or slightly modifying features to reduce support needs – can often improve printability, reduce cost, shorten lead times, and enhance the final part’s performance or reliability. A good partner will provide this feedback as part of the quoting or onboarding process.
Conclusion: Sailing Towards the Future with Additive Manufactured Shaft Sleeves
The maritime industry’s relentless pursuit of durability, efficiency, and operational readiness finds a powerful ally in metal additive manufacturing. As we’ve explored, the production of critical components like marine shaft sleeves med hjälp av 3D-utskrift av metall technologies such as Powder Bed Fusion offers a paradigm shift away from the constraints of traditional manufacturing. The ability to leverage high-performance, korrosionsbeständig legeringar som CuNi30Mn1Fe och 316L rostfritt stål directly from powder allows for the creation of components specifically tailored to withstand the harsh realities of the marine environment.
The key advantages are compelling: unparalleled designfrihet enabling optimization beyond traditional means; rapid production capabilities crucial for minimizing downtime and responding to urgent needs; material efficiency reducing waste of valuable alloys; and the agility offered by a digital tillverkning workflow. For engineers and procurement managers, this translates into opportunities for enhanced component lifespan, streamlined supply chains, reduced inventory holdings through on-demand production, and the ability to source custom or obsolete parts effectively. While challenges in design, process control, and post-processing exist, they are navigable through careful planning and collaboration with knowledgeable partners.
Choosing the right material based on specific corrosion, biofouling, and mechanical requirements, applying DfAM principles, understanding the achievable precision and necessary finishing steps, and selecting a capable metal AM service provider are all critical elements for success. Companies like Met3dp, with their integrated expertise spanning advanced tryckmetoder, high-quality powder production, and a focus on industrial applications, represent the type of partner needed to fully exploit the potential of AM. Their commitment to accuracy, reliability, and material quality provides the foundation for producing dependable, high-performance marine components.
The adoption of metal 3D printing for shaft sleeves is more than just a novel manufacturing technique; it’s a strategic move towards more resilient, efficient, and technologically advanced maritime operations. As the technology continues to mature and material options expand, we can expect to see additive manufacturing play an increasingly vital role in producing not only shaft sleeves but a wide array of complex and critical marine parts, charting a course towards a future of enhanced performance and sustainability on the high seas.
Ready to explore how metal 3D printing can revolutionize your marine component supply? Contact Met3dp today to discuss your specific shaft sleeve requirements and discover the power of additive manufacturing.
Dela på
MET3DP Technology Co, LTD är en ledande leverantör av lösningar för additiv tillverkning med huvudkontor i Qingdao, Kina. Vårt företag är specialiserat på 3D-utskriftsutrustning och högpresterande metallpulver för industriella tillämpningar.
Förfrågan för att få bästa pris och anpassad lösning för ditt företag!
Relaterade artiklar
Om Met3DP
Senaste uppdateringen
Vår produkt
KONTAKTA OSS
Har du några frågor? Skicka oss meddelande nu! Vi kommer att betjäna din begäran med ett helt team efter att ha fått ditt meddelande.
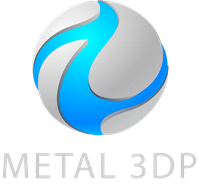
Metallpulver för 3D-printing och additiv tillverkning