Advantages of using DED for manufacturing molds and tools
Innehållsförteckning
Imagine a world where complex molds and tools can be built with near-unparalleled freedom of design, reduced lead times, and minimized material waste. This isn’t science fiction; it’s the reality offered by Directed Energy Deposition (DED), a revolutionary additive manufacturing (AM) technology poised to transform the manufacturing landscape.
DED, also known as Laser Metal Deposition (LMD) or Cold Metal Transfer (CMT), works by melting metal powder layer by layer using a high-powered energy source, like a laser or electron beam. This allows for the creation of intricate geometries that would be impossible or highly challenging with traditional subtractive manufacturing methods like machining.
But what makes DED particularly advantageous for mold and tool manufacturing? Let’s delve into the key benefits that make DED a game-changer for this industry.
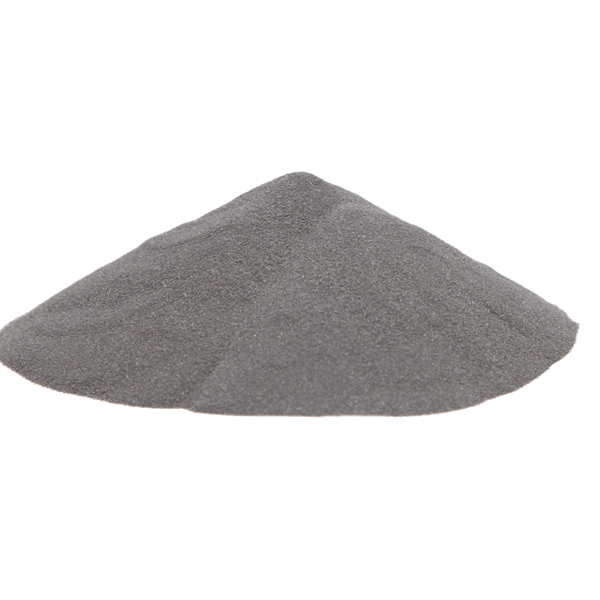
DED can manufacture molds with complex shapes and features
Traditional machining often involves extensive subtractive processes, carving away material from a solid block to achieve the desired mold shape. This approach inherently limits the complexity of achievable geometries. DED, on the other hand, thrives on intricate designs. With DED, internal channels, undercuts, and other complex features can be directly printed, eliminating the need for intricate machining operations.
Think of it like building a Lego model versus sculpting a detailed statue. Traditional machining is like the sculptor, meticulously removing material to reveal the final form. DED acts like the Lego builder, precisely adding each block to create the desired structure. This opens doors for innovative mold designs that were previously unthinkable, leading to advancements in product functionality and performance.
DED can manufacture molds faster than traditional methods
Time is money, especially in the fast-paced world of manufacturing. Traditional mold and tool creation can be a lengthy process, involving design iterations, machining steps, and potential rework. DED significantly streamlines this process. Design changes can be easily incorporated into the digital model, and the additive nature of DED allows for faster build times compared to subtractive machining.
Imagine needing a mold for a new product design yesterday. With DED, the turnaround time can be drastically reduced compared to traditional methods. This translates to faster product launches, reduced time-to-market, and a competitive edge for manufacturers.
DED can manufacture molds
Global supply chains have their advantages, but they also come with potential risks and delays. DED empowers manufacturers to produce molds and tools locally, closer to their production facilities. This reduces reliance on external vendors, minimizes transportation costs, and improves overall production control.
Furthermore, DED can offer cost savings compared to traditional methods. While the DED machines themselves might have a higher upfront cost, the reduced material waste, streamlined process, and potential for local production can lead to significant cost reductions in the long run.
Metallpulver för DED
The success of DED hinges on the quality and properties of the metal powders used. Here’s a look at some of the most common metal powders employed in DED mold and tool manufacturing, along with their key characteristics:
Metallpulver | Beskrivning | Fastigheter | Applications in Molds and Tools |
---|---|---|---|
Rostfritt stål 316L | A versatile austenitic stainless steel known for its excellent corrosion resistance | – Good strength and ductility – High weldability | – General-purpose molds for plastic injection molding – Molds for food and medical applications |
Verktygsstål H13 | A high-alloy, hot work tool steel with excellent wear resistance | – High hardness and hot strength – Good toughness | – Molds for hot stamping and blow molding – Dies for forging and forming operations |
Inconel 625 | A superalloy known for its exceptional high-temperature strength and corrosion resistance | – Excellent resistance to oxidation and creep – High strength at elevated temperatures | – Molds for casting high-temperature alloys – Dies for hot forging applications |
Maråldrat stål | A family of high-strength, low-alloy steels known for their exceptional dimensional stability after heat treatment | – High strength-to-weight ratio – Excellent dimensional stability | – Molds for precision casting applications – Dies for forming operations requiring tight tolerances |
Aluminium (AlSi10Mg) | A silicon-magnesium alloy offering a good balance of strength, ductility, and castability | – Lightweight and good thermal conductivity – Excellent machinability | – Prototype molds and low-volume production molds – Molds for applications requiring weight reduction |
Nickel | A pure nickel powder offering good corrosion resistance and electrical conductivity | – High ductility and good brazing properties – Excellent electrical conductivity | – Molds for electroplating applications – Electrodes for various manufacturing processes |
Koppar | A pure copper powder known for its excellent thermal conductivity and electrical conductivity | – High electrical conductivity and good thermal conductivity | – |
Titan (Ti-6Al-4V) | A workhorse titanium alloy offering a good balance of strength, weight, and corrosion resistance | Högt förhållande mellan styrka och vikt Utmärkt biokompatibilitet | Molds for aerospace and medical applications Dies for forming titanium components |
Kobolt Krom (CoCr) | A biocompatible alloy known for its high strength, wear resistance, and corrosion resistance | Excellent wear resistance and biocompatibility Hög hållfasthet och hårdhet | Molds for medical implants and prosthetics Dies for wear applications requiring high durability |
Volframkarbid | An extremely hard and wear-resistant material often used in composite powders | Exceptionell hårdhet och slitstyrka God värmeledningsförmåga | Inserts for molds and dies requiring exceptional wear resistance Molds for abrasive materials processing |
Beyond Common Alloys: Exploring the Potential of DED
The beauty of DED lies in its versatility. While the above metal powders represent some of the most widely used options, DED is compatible with a vast array of other materials. This opens doors for exciting possibilities in mold and tool manufacturing. Here are some glimpses into the future:
- Functionally Graded Materials (FGMs): DED allows for the creation of molds and tools with varying properties throughout their structure. Imagine a mold with a strong, steel base for structural integrity and a wear-resistant tungsten carbide coating on the areas encountering high friction. FGMs created via DED can optimize mold performance and extend service life.
- Exotic Alloys: DED isn’t limited to commonly available metals. It can handle more challenging materials like Inconel 718, a superalloy known for its exceptional high-temperature strength. This opens doors for molds used in extreme environments, such as those encountered in aerospace applications.
- Metal Matrix Composites (MMCs): Imagine a mold material that combines the strength of metal with the lightweight properties of a ceramic. DED allows for the creation of MMCs by co-depositing metal powders with ceramic reinforcements. This paves the way for molds with exceptional strength-to-weight ratios, ideal for applications in the transportation industry.
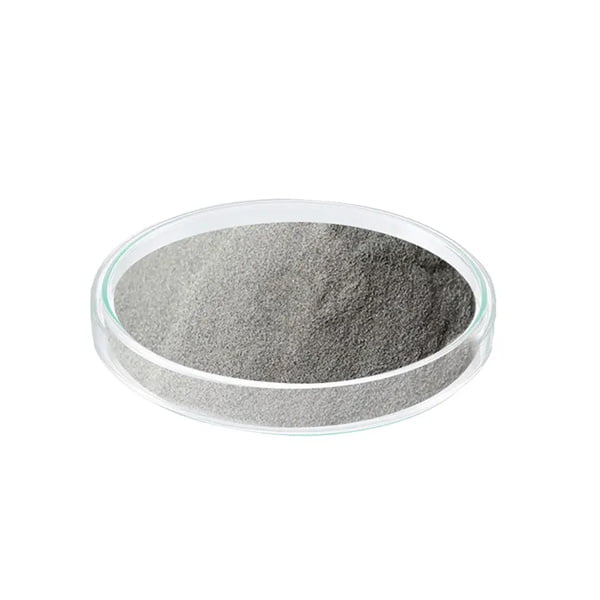
DED vs Traditional Methods
While DED offers numerous advantages, it’s important to acknowledge that traditional methods still hold their place in certain scenarios. Here’s a table comparing DED and traditional methods to help you decide which approach might be best for your specific needs:
Faktor | DED | Traditional Methods (Machining) |
---|---|---|
Designens komplexitet | Excellent for complex geometries | Limited to simpler shapes |
Ledtid | Snabbare handläggningstider | Can be time-consuming for intricate designs |
Material Avfall | Minimalt materialspill | Significant material removal through subtractive processes |
Local Production | Enables local manufacturing of molds and tools | Relies on external vendors in some cases |
Upfront Cost | Higher upfront cost for DED machines | Lower initial investment for machines |
Long-term Cost | Can be cost-effective due to reduced material waste and streamlined process | May be cost-effective for high-volume production runs |
Suitability | Ideal for complex, low-volume molds and prototypes | Well-suited for high-volume production of simpler molds |
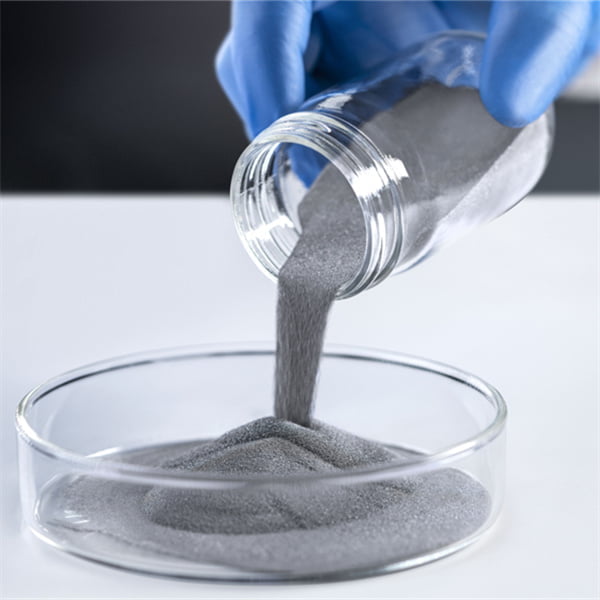
VANLIGA FRÅGOR
Here are some frequently asked questions regarding DED and its application in mold and tool manufacturing, answered in a clear and concise format:
Fråga | Svar |
---|---|
What are the surface finish considerations for DED molds? | DED-produced molds may require post-processing techniques like polishing or machining to achieve the desired surface finish for optimal part quality. |
Can DED be used to repair damaged molds and tools? | Absolutely! DED’s additive nature makes it ideal for repairing localized areas of damage on molds and tools, extending their lifespan and reducing replacement costs. |
How does DED compare to other additive manufacturing technologies for mold and tool manufacturing? | While technologies like Selective Laser Sintering (SLS) are gaining traction, DED offers advantages in terms of producing metal molds with superior strength and high-temperature performance. |
What are the environmental benefits of using DED for mold and tool manufacturing? | DED minimizes material waste compared to traditional machining methods, contributing to a more sustainable manufacturing process. |
Dela på
MET3DP Technology Co, LTD är en ledande leverantör av lösningar för additiv tillverkning med huvudkontor i Qingdao, Kina. Vårt företag är specialiserat på 3D-utskriftsutrustning och högpresterande metallpulver för industriella tillämpningar.
Förfrågan för att få bästa pris och anpassad lösning för ditt företag!
Relaterade artiklar
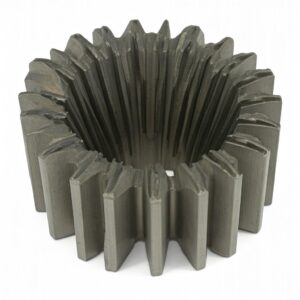
Högpresterande segment för munstycksvingar: Revolutionerande turbineffektivitet med 3D-utskrift i metall
Läs mer "Om Met3DP
Senaste uppdateringen
Vår produkt
KONTAKTA OSS
Har du några frågor? Skicka oss meddelande nu! Vi kommer att betjäna din begäran med ett helt team efter att ha fått ditt meddelande.
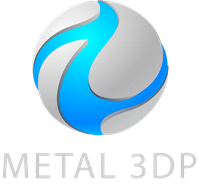
Metallpulver för 3D-printing och additiv tillverkning
FÖRETAG
PRODUKT
cONTACT INFO
- Qingdao City, Shandong, Kina
- [email protected]
- [email protected]
- +86 19116340731