Comparison between Material Jetting and Directed Energy Deposition
Innehållsförteckning
Imagine a world where complex objects materialize layer by layer, not through magic, but through the marvels of 3D printing. Within this realm exist two powerful contenders: Material Jetting and Deposition med riktad energi (DED). Both utilize additive manufacturing principles, but their approaches diverge, leading to distinct advantages and limitations. So, which champion reigns supreme for your specific project? Buckle up, as we delve into the intricate dance between these two 3D printing titans.
Unveiling the Materials: A Tale of Two Worlds
The materials of Material Jetting and DED are as different as night and day. Material Jetting, like a meticulous artist, employs photopolymers – liquid resins that solidify upon exposure to ultraviolet (UV) light. These resins come in a dazzling array of colors, boasting exceptional detail and smooth surface finishes. Think intricate jewelry prototypes, dental prosthetics with lifelike aesthetics, and functional microfluidic devices.
Here’s a glimpse into the vibrant world of Material Jetting resins:
Materialtyp | Beskrivning | Tillämpningar |
---|---|---|
Standard Resins | These versatile workhorses offer a balance of mechanical properties and affordability. They’re ideal for rapid prototyping and concept models. | General-purpose prototyping, figurines, architectural models |
High-Temperature Resins | Can withstand temperatures exceeding 130°C (266°F), making them suitable for functional parts that experience heat. | Engine components, housings for electronics |
Biocompatible Resins | Tailored for medical applications, these resins are non-toxic and compatible with human tissue. | Surgical guides, dental models, biocompatible implants (limited) |
Rigid and Flexible Resins | Offer a spectrum of stiffness from rigid for structural parts to flexible for gaskets and seals. | Snap-fit assemblies, living hinges, wearables |
Castable Resins | Can be used to create investment molds for lost-metal casting, enabling the production of metal parts from 3D-printed masters. | Jewelry casting, lost-wax casting for metal components |
On the other hand, DED, a more industrial warrior, wields metal powders. These metallic particles, ranging from common stainless steel to exotic alloys like Inconel, are fused together using a high-powered energy source – typically a laser or electron beam. The result? Robust, high-strength metal parts capable of enduring harsh environments.
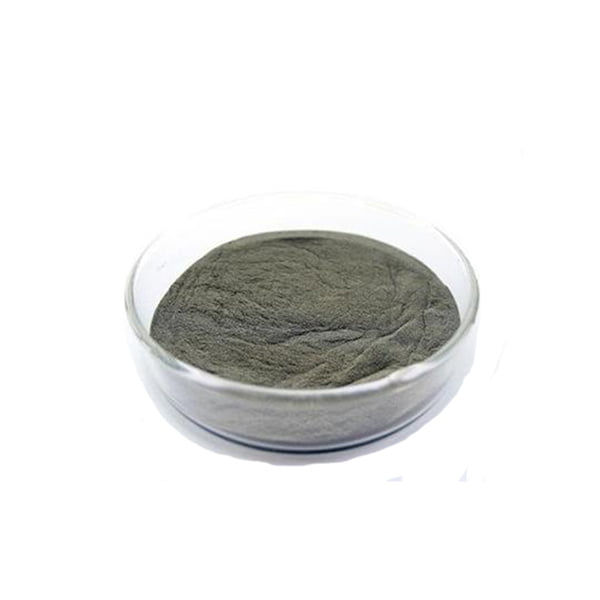
Let’s explore the metallic arsenal of Deposition med riktad energi
Metallpulver | Beskrivning | Tillämpningar |
---|---|---|
Rostfritt stål 316L | The go-to material for DED due to its excellent corrosion resistance, weldability, and biocompatibility. | Komponenter till flyg- och rymdindustrin, medicinska implantat, kemisk processutrustning |
Titan (Ti-6Al-4V) | A lightweight yet strong option favored for its high strength-to-weight ratio and biocompatibility. | Aerospace parts, prosthetics, implant housings |
Inconel 625 | A superalloy renowned for its exceptional resistance to high temperatures, oxidation, and corrosion. | Turbinblad, raketmotorkomponenter, värmeväxlare |
Aluminiumlegeringar | Offer a combination of lightweight properties and good strength, making them suitable for applications requiring weight reduction. | Automotive parts, aerospace components, heat sinks |
Nickellegeringar | Offer superior corrosion resistance and high-temperature performance, ideal for demanding environments. | Chemical processing equipment, marine components, oil and gas applications |
Verktygsstål | Possess high hardness and wear resistance, making them suitable for cutting tools and dies. | Molds, punches, dies, wear plates |
Kobolt Krom (CoCr) | A biocompatible alloy commonly used for orthopedic implants due to its excellent wear resistance. | Hip replacements, knee replacements, dental implants |
Koppar | Highly conductive, making it ideal for applications requiring efficient heat transfer or electrical conductivity. | Heat sinks, electrical components, busbars |
Ädelmetaller | Materials like gold, silver, and platinum can be printed for applications demanding high conductivity, aesthetics, or biocompatibility. | Jewelry, electronics components, biomedical devices (limited) |
This is just a taste of the vast material palette available for both Material Jetting and DED. The specific choice hinges on the desired properties of the final part, be it intricate detail, biocompatibility, high strength, or a combination of these factors.
The Dance of Creation: Unveiling the Processes
The processes behind Material Jetting and DED are as distinct as their materials. Imagine Material Jetting as a meticulous painter, meticulously layering photopolymer droplets onto a build platform. A print head, akin to a high-tech inkjet printer, precisely deposits these droplets, solidifying them instantly with UV light. Layer by layer, the object emerges from a bath of liquid resin, boasting exceptional detail and smooth surface finishes.
Here’s a closer look at the Material Jetting process:
- 3D Model Preparation: A digital 3D model of the object is created using CAD software. This model serves as the blueprint for the printing process.
- Printing Setup: The chosen photopolymer resin is loaded into the print head, and the build platform is positioned within the printer chamber.
- Jetting and Curing: The print head traverses the build platform, precisely jetting tiny droplets of resin according to the 3D model data. A UV lamp follows closely behind, curing each layer instantly.
- Stöd för borttagning: Once printing is complete, the build platform is lowered into a bath of cleaning solution to remove any residual resin. Support structures, necessary for overhanging features, are then carefully removed.
- Efterbearbetning: Depending on the resin type, the printed part might undergo additional post-processing steps such as curing under UV light for improved mechanical properties or dyeing for aesthetic purposes.
DED, on the other hand, operates like a sculptor wielding a high-powered laser or electron beam. Metal powder is meticulously deposited onto the build platform, and the energy source melts and fuses the particles together, creating a strong metallic bond. Layer by layer, the object takes shape, capable of withstanding significant loads and harsh environments.
Let’s delve into the intricacies of the DED process:
- 3D Model Preparation: Similar to Material Jetting, a digital 3D model is prepared using CAD software. However, DED processes often require additional considerations for factors like heat distortion and residual stresses.
- Powder Loading and Setup: The chosen metal powder is loaded into a hopper and fed into the DED system. The build platform is positioned and calibrated for optimal laser or electron beam interaction.
- Energy Deposition and Melting: The laser or electron beam focuses onto the build platform, melting the deposited metal powder and fusing it to the previous layer. The print head meticulously follows the 3D model data, building the object one layer at a time.
- Support Structure Management: Unlike Material Jetting, DED often utilizes minimal or no support structures due to the inherent strength of the metallic material. However, complex geometries might necessitate the use of strategically placed support structures, which are removed later through machining or other techniques.
- Efterbearbetning: DED parts typically require post-processing steps like heat treatment to relieve residual stresses and improve mechanical properties. Additionally, machining or grinding might be necessary to achieve the desired surface finish and dimensional tolerances.
Both Material Jetting and DED offer unique advantages in terms of process control and flexibility. Material Jetting excels at producing intricate details and complex geometries due to the precise jetting of photopolymer droplets. DED, on the other hand, provides unmatched freedom in building near-net-shape metal parts with superior strength and high-temperature performance.
Applications that Define the Champions
The applications of Material Jetting and DED are as diverse as their capabilities. Material Jetting shines in prototyping and creating models with exceptional detail. Its smooth surface finishes and wide variety of resins make it ideal for:
- Concept Models and Prototypes: Quickly create physical models for design validation and functional testing.
- Medicinska och dentala tillämpningar: Produce biocompatible models for surgical guides, dental prosthetics, and custom implants.
- Jewelry and Art: Craft intricate jewelry pieces with exceptional detail and a smooth finish, or create unique artistic sculptures with a wide range of color options.
- Microfluidics: Build microfluidic devices with precise channels and features for medical diagnostics, lab-on-a-chip applications, and microneedles.
DED, the champion of strength and functionality, excels in producing metal parts for demanding applications. Its ability to handle various metal powders opens doors to:
- Flyg- och rymdindustrin samt försvarsindustrin: Create lightweight yet strong components for aircraft, satellites, and rocket engines.
- Medicinska implantat: Manufacture custom orthopedic implants with biocompatible materials like titanium and cobalt chrome.
- Tooling and Dies: Produce complex molds and dies for metal forming and plastic injection molding.
- Automotive and Transportation: Fabricate lightweight and high-strength components for cars, motorcycles, and aerospace vehicles.
- Olje- och gasindustrin: Build parts that can withstand harsh environments and high pressures.
The choice between Material Jetting and DED boils down to the specific needs of your project. Consider factors like the desired material properties, level of detail required, and the intended application.
Material Jetting vs. DED: A Comparative Cage Match
Now that we’ve explored the materials and processes behind these two 3D printing titans, it’s time for the ultimate showdown – a feature-by-feature comparison to help you pick the perfect champion for your project.
Materialegenskaper:
- Jetting av material: Restricted to photopolymers, offering a vast array of properties from rigid to flexible, biocompatible to high-temperature resistant. However, these materials generally possess lower strength and heat resistance compared to metals.
- DED: Utilizes a diverse range of metal powders, boasting exceptional strength, high-temperature performance, and superior wear resistance. Ideal for applications demanding durability and functionality in harsh environments.
Level of Detail:
- Jetting av material: Reigns supreme in detail. The precise jetting of photopolymer droplets enables the creation of incredibly intricate features and smooth surface finishes, making it perfect for replicating complex geometries and fine details.
- DED: While capable of producing detailed parts, the inherent nature of melting metal powder limits the level of detail achievable compared to Material Jetting. However, advancements in DED technology are continuously pushing the boundaries of achievable detail.
Dimensionell noggrannhet:
- Jetting av material: Offers good dimensional accuracy, typically within ± 0.1 mm (0.004 inches). However, factors like resin shrinkage and support structure removal can influence final accuracy.
- DED: Dimensional accuracy can vary depending on the DED process and metal powder used. Generally, DED parts might require additional post-processing steps like machining to achieve precise tolerances.
Bygghastighet:
- Jetting av material: Printing speeds can vary depending on the printer model, layer thickness, and part complexity. However, Material Jetting is generally considered a faster process compared to DED, especially for smaller and less complex parts.
- DED: Build speeds in DED are typically slower than Material Jetting. The process of melting metal powder layer by layer is inherently more time-consuming. However, advancements in DED technology are leading to faster printing speeds.
Delstyrka:
- Jetting av material: The strength of printed parts depends on the chosen resin. While some high-performance resins offer good mechanical properties, they generally cannot match the strength of metals used in DED.
- DED: Metal parts produced by DED offer exceptional strength and can withstand significant loads. This makes DED the clear winner for applications requiring high structural integrity.
Kostnad:
- Jetting av material: The overall cost of Material Jetting can vary depending on the chosen resin, printer model, and part complexity. Generally, the cost per part tends to be lower for smaller and simpler prototypes.
- DED: DED printing is typically a more expensive process compared to Material Jetting. The cost of metal powders and the complex nature of the DED process contribute to higher overall costs.
Complexity of Parts:
- Jetting av material: Material Jetting excels at producing parts with intricate geometries and fine details. The ability to jet photopolymers in precise layers allows for the creation of complex internal features and overhanging structures with minimal support requirements.
- DED: While DED can produce complex parts, the molten metal deposition process might limit the creation of extremely fine details and intricate internal features. Support structures might be necessary for complex geometries, adding complexity to the overall process.
Applikationer:
- Jetting av material: Ideal for rapid prototyping, concept modeling, creating detailed models for medical and dental applications, producing intricate jewelry pieces, and fabricating microfluidic devices.
- DED: Shines in manufacturing functional metal parts for aerospace and defense applications, medical implants, tooling and dies, automotive and transportation components, and parts for the oil and gas industry.
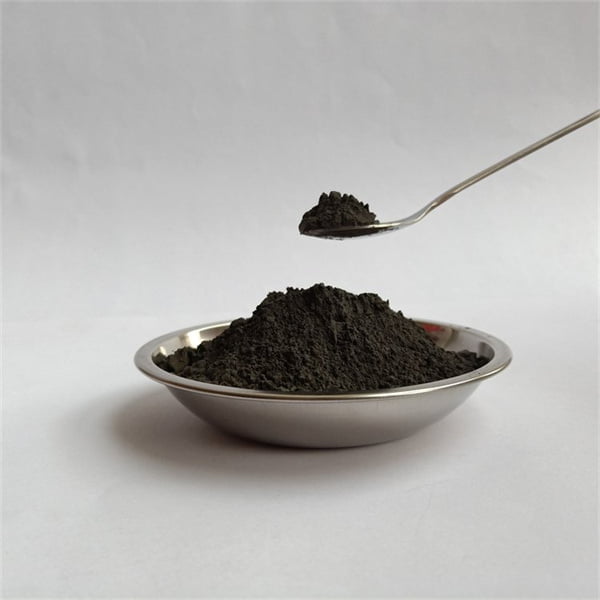
Choosing Your Champion
The victor in this Material Jetting vs. DED battle depends on your specific project requirements. Consider the following factors to make an informed decision:
- Material Needs: Do you require the detail and variety offered by photopolymers, or is the unmatched strength and heat resistance of metals a priority?
- Delkomplexitet: Are intricate details and fine features crucial, or is overall part strength the primary concern?
- Budget: Consider the cost of materials, printing process, and potential post-processing needs.
- Ansökan: What is the intended use of the printed part? This will guide your choice towards the material properties and functionality best suited for the application.
By carefully evaluating these factors, you can crown the perfect champion – Material Jetting for intricate prototypes and detailed models, or DED for robust and functional metal parts. Remember, both 3D printing technologies offer unique advantages, and the best choice lies in understanding their strengths and limitations in the context of your specific project.
VANLIGA FRÅGOR
Here are some commonly asked questions to shed further light on the key differences between Material Jetting and DED:
Q: Can Material Jetting print metal parts?
A: No, Material Jetting is limited to printing with photopolymer resins. While these resins offer a variety of properties, they cannot match the strength and heat resistance of metals used in DED.
Q: Is DED suitable for printing jewelry?
A: DED can technically print with precious metals like gold and silver. However, the level of detail achievable with DED might not be suitable for intricate jewelry designs requiring fine features and smooth surface finishes. Material Jetting would be a better choice for such applications.
Q: Which process is more environmentally friendly?
A: Material Jetting generally has a lower environmental impact compared to DED. Photopolymer resins can be partially bio-derived and often require less energy to process compared to melting metal powders in DED. Additionally, Material Jetting typically produces less waste material.
Q: Can I use both Material Jetting and DED together?
A: In some cases, it might be beneficial to combine both Material Jetting and DED for a single project. For instance, you could use Material Jetting to create a detailed mold or core, and then use DED to print a metal shell around it. This hybrid approach can leverage the strengths of both technologies for unique applications.
Q: What are the future advancements expected in Material Jetting and DED?
A: Both Material Jetting and DED are constantly evolving technologies. Advancements in material science can lead to the development of even stronger and more versatile photopolymer resins for Material Jetting. DED is expected to see improvements in printing speeds, broader compatibility with metal powders, and the ability to achieve finer details, potentially blurring the lines between the two technologies in the future.
Sammanfattningsvis:
Material Jetting and DED are powerful 3D printing technologies, each holding its own ground in the realm of creating objects. By understanding their strengths, limitations, and ideal applications, you can make an informed decision and select the champion that best serves your project needs. Remember, the future of 3D printing is brimming with possibilities, and both Material Jetting and DED are poised to play a significant role in shaping the way we design and manufacture objects in the years to come.
Dela på
MET3DP Technology Co, LTD är en ledande leverantör av lösningar för additiv tillverkning med huvudkontor i Qingdao, Kina. Vårt företag är specialiserat på 3D-utskriftsutrustning och högpresterande metallpulver för industriella tillämpningar.
Förfrågan för att få bästa pris och anpassad lösning för ditt företag!
Relaterade artiklar
Om Met3DP
Senaste uppdateringen
Vår produkt
KONTAKTA OSS
Har du några frågor? Skicka oss meddelande nu! Vi kommer att betjäna din begäran med ett helt team efter att ha fått ditt meddelande.
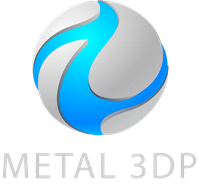
Metallpulver för 3D-printing och additiv tillverkning