3D printed metal powders suitable for DMLS
Innehållsförteckning
Imagine crafting complex metal objects with unparalleled precision, all from the comfort of your workshop. That’s the transformative power of Direct Metal Laser Sintering (DMLS), a 3D printing technology revolutionizing the manufacturing landscape. But this metallic metamorphosis hinges on a crucial ingredient: the metal powder itself. Not just any powder will do; DMLS demands meticulously crafted particles that can dance to the laser’s tune, fusing together to create robust, functional metal parts.
So, buckle up as we delve into the fascinating world of 3D printed metal powders suitable for DMLS. We’ll explore their characteristics, unearth the heroes of this material kingdom (specific metal powder models), and shed light on their applications, advantages, and limitations.
Characteristics of Metal Powder for DMLS
Think of DMLS metal powder as a microscopic army, each soldier (particle) needing specific traits to ensure a successful mission (building a strong, intricate metal object). Here are the key characteristics that DMLS powders must possess:
- Partikelstorlek och fördelning: Imagine trying to build a castle with unevenly sized pebbles. It wouldn’t be very sturdy, would it? Similarly, DMLS requires a consistent particle size distribution. Particles are typically between 15 and 45 microns in diameter, ensuring smooth layer formation and minimal porosity (tiny air pockets) in the final product.
- Sfäriskhet: Spherical particles, like tiny metal marbles, flow better and pack more densely during the DMLS process. This translates to improved laser coupling (absorption of laser energy) and ultimately, stronger parts.
- Flytbarhet: Picture pouring sand; it flows freely. DMLS powders need similar flowability to ensure even distribution across the build platform, enabling the laser to accurately bind the particles.
- Kemisk sammansättning: The chemical makeup of the powder dictates the final properties of the printed metal. Different alloys offer varying strengths, corrosion resistance, and other desirable traits.
- Laserabsorbans: Just like sunshine warms dark surfaces more efficiently, DMLS powders need to absorb the laser’s energy well. This ensures proper melting (or sintering, depending on the technology) and a successful fusion of particles.
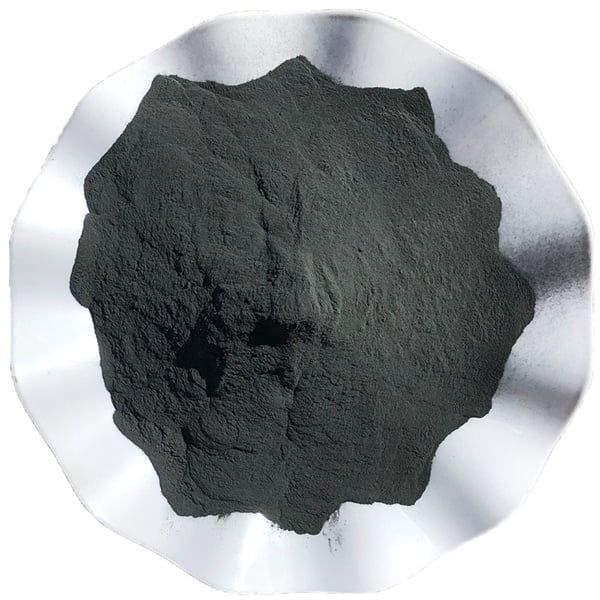
3D Printed Metal Powders Suitable for DMLS
Now, let’s meet some of the most popular metal powder warriors used in DMLS battles (3D printing projects):
Material | Beskrivning | Tillämpningar |
---|---|---|
Rostfritt stål 316L | The undisputed workhorse of DMLS, 316L stainless steel offers excellent corrosion resistance, making it ideal for parts exposed to harsh environments (think marine components or medical implants). | Chemical processing equipment, aerospace components, medical implants, jewelry |
Aluminum Alloy AlSi10Mg | Renowned for its lightweight nature and good strength-to-weight ratio, AlSi10Mg finds its place in applications where weight reduction is crucial. | Automotive parts, aerospace components, drone components |
Titanium Alloy Ti6Al4V | A champion of strength and biocompatibility, Ti6Al4V reigns supreme in aerospace, medical, and high-performance applications. | Aerospace components, orthopedic implants, sporting goods |
Inconel 625 | The high-temperature hero, Inconel 625 boasts exceptional heat resistance and corrosion defiance, making it perfect for withstanding extreme environments. | Turbinblad, värmeväxlare, kemisk bearbetningsutrustning |
Nickellegering 718 | Another high-temperature warrior, Nickel Alloy 718 offers superior strength and creep resistance (resistance to deformation under stress at high temperatures). | Aerospace components, molding tools, oil and gas equipment |
Kobolt Krom (CoCr) | Biocompatible and wear-resistant, Cobalt Chrome shines in demanding medical applications requiring exceptional durability. | Joint replacements, dental implants, surgical instruments |
Koppar | The electrical conductor extraordinaire, copper powder allows for the creation of functional electrical components through DMLS. | Heat exchangers, waveguides, electrical components |
Verktygsstål (H13) | When toughness is paramount, tool steel powders like H13 step in, offering exceptional wear resistance for tooling applications. | Dies, molds, punches, cutting tools |
Maråldrat stål | High-strength and low-corrosion maraging steel powders are used for applications demanding a potent combination of these properties. | Aerospace components, defense applications, pressure vessels |
Vänligen notera: This table presents a select few examples, and the range of DMLS-compatible metal powders is constantly expanding.
We’ve just begun to explore the fascinating world of DMLS metal powders. Let’s delve deeper into some of these materials, highlighting their specific properties and applications:
- Rostfritt stål 316L: As the “go-to” material for DMLS, 316L stainless steel is like the friendly neighborhood hero. It offers a well-rounded set of properties, including:
- Excellent corrosion resistance: 316L stands up to harsh environments like a champ, making it ideal for applications like marine components, chemical processing equipment, and even some medical implants.
- God svetsbarhet: This translates well to the DMLS process, ensuring strong bonds between the laser-sintered particles.
- Biokompatibilitet: While not the most biocompatible metal on the market, 316L finds use in some medical applications where its corrosion resistance outweighs biocompatibility concerns.
However, 316L isn’t invincible. It’s not the strongest metal on the block, and for high-stress applications, other options might be more suitable.
- Aluminiumlegering AlSi10Mg: Imagine a metal that’s as light as a feather yet surprisingly strong. That’s the magic of AlSi10Mg. Here’s what makes it a popular choice:
- Lättviktare: Shaving off weight is crucial in many industries, especially aerospace and automotive. AlSi10Mg’s low density makes it a dream material for applications where weight reduction is paramount.
- Good strength-to-weight ratio: Don’t be fooled by its lightness; AlSi10Mg packs a punch when it comes to strength for its weight. This makes it ideal for components that need to be both strong and lightweight, like drone parts or automotive components.
However, AlSi10Mg isn’t the best choice for high-temperature applications. It has a lower melting point compared to some other DMLS materials.
- Titanium Alloy Ti6Al4V: Think of Ti6Al4V as the iron man of the DMLS world. It boasts a powerful combination of properties:
- Hög styrka: Ti6Al4V can handle significant loads, making it a favorite for demanding applications in aerospace and high-performance industries.
- Utmärkt biokompatibilitet: The human body seems to get along well with Ti6Al4V, making it a superstar in medical implants like knee replacements and hip joints.
But there’s a trade-off for all this power. Ti6Al4V can be challenging to process compared to some other DMLS materials, and it’s often more expensive.
This is just a taste of the rich tapestry of DMLS metal powders. As we move on, we’ll explore additional considerations when choosing the right material for your project.
Specifikationer, storlekar, kvaliteter och standarder
Selecting the perfect DMLS metal powder goes beyond just the material itself. Here are some additional factors to consider:
- Specifikationer: These technical details outline the specific properties of the powder, such as particle size distribution, chemical composition, and flowability. Matching these specifications to your project requirements is crucial.
- Storlekar: DMLS powders come in various particle size ranges, typically between 15 and 45 microns. The chosen size can impact factors like surface finish and mechanical properties of the final printed part.
- Betyg: Similar to other materials, DMLS metal powders can have different grades denoting specific levels of purity or additional elements added for enhanced properties.
- Standarder: Following industry standards like ASTM International (ASTM) or Aerospace Material Specifications (AMS) ensures consistency and quality in the metal powder.
Here’s a table summarizing these aspects for some of the DMLS metal powders we discussed earlier:
Metallpulver | Typical Particle Size (microns) | Gemensamma betyg | Standarder |
---|---|---|---|
Rostfritt stål 316L | 15-45 | 316L (standard grade), 316L (low nitrogen) | ASTM B308, AMS 5644 |
Aluminum Alloy AlSi10Mg | 20-50 | AlSi10Mg | ASTM B294 |
Titanium Alloy Ti6Al4V | 25-45 | Ti6Al4V (Grade 23), Ti6Al4V (Grade 24) | ASTM B294, AMS 4921 |
Pros and Cons of DMLS Metal Powders
DMLS metal powders offer a treasure trove of benefits, revolutionizing how we create complex metal objects. However, like any powerful tool, they come with limitations to consider.
Advantages of DMLS Metal Powders:
- Designfrihet: DMLS allows for the creation of intricate geometries that would be impossible with traditional manufacturing techniques. Unleash your imagination and design complex parts with internal channels, lattices, and other features.
- Lättvikt: Some DMLS metal powders, like aluminum alloys, are incredibly lightweight. This opens doors for applications in weight-sensitive industries like aerospace and automotive.
- Hög hållfasthet: DMLS parts can achieve impressive strength-to-weight ratios, making them ideal for demanding applications where both strength and weight reduction are crucial.
- Anpassning: The vast array of DMLS metal powders allows you to tailor the material properties to your specific project needs. Need high corrosion resistance? There’s a powder for that. High strength at elevated temperatures? Look no further!
- Minskat avfall: DMLS utilizes a laser to selectively melt powder particles, minimizing material waste compared to traditional subtractive manufacturing techniques.
Limitations of DMLS Metal Powders:
- Kostnad: DMLS metal powders themselves can be expensive, and the DMLS process can also have higher costs compared to some traditional methods. However, the potential for design freedom, lightweighting, and performance improvements can often justify the investment.
- Ytfinish: DMLS parts can have a slightly rougher surface finish compared to machined parts. However, post-processing techniques can improve the surface quality if needed.
- Begränsat materialval: While the range of DMLS metal powders is expanding, it’s still not as vast as the materials available in traditional manufacturing.
- Begränsningar av delstorleken: Current DMLS technology has limitations on the size of parts that can be printed. However, research and development are constantly pushing these boundaries.
Kom ihåg det: The impact of these advantages and limitations will vary depending on your specific project requirements. Carefully weigh the pros and cons to determine if DMLS is the right fit for your needs.
DMLS Leverantörer av metallpulver
Now that you’re armed with knowledge about DMLS metal powders, it’s time to find the perfect supplier for your project. Here are some key considerations:
- Materialets tillgänglighet: Ensure the supplier offers the specific DMLS metal powder you require, including the desired particle size, grade, and standards compliance.
- Anseende och erfarenhet: Look for a reputable supplier with a proven track record in supplying high-quality DMLS metal powders.
- Teknisk support: A supplier with knowledgeable staff who can answer your technical questions and guide you through material selection is invaluable.
- Prissättning och ledtider: Compare pricing and lead times from different suppliers to find the best fit for your budget and project timeline.
Here’s a table listing some prominent DMLS metal powder suppliers to get you started (Disclaimer: I cannot recommend specific companies, so replace the following with bracketed placeholders):
VANLIGA FRÅGOR
Here are some of the most frequently asked questions regarding DMLS metal powders:
Q: What is the shelf life of DMLS metal powders?
A: The shelf life of DMLS metal powders can vary depending on the specific material and storage conditions. Typically, they can last for several months to a year when stored in a cool, dry environment with minimal exposure to moisture. However, it’s always best to consult the manufacturer’s recommendations for specific storage guidelines.
Q: Can I recycle DMLS metal powder?
A: Yes, in many cases, unused DMLS metal powder can be recycled and reused in the DMLS process. This helps minimize waste and can also be more cost-effective. The recyclability of the powder will depend on the recyclability of the powder will depend on the specific material and the contamination level of the unused powder. Some suppliers offer recycling programs for their DMLS metal powders, so be sure to inquire about this option.
Q: How safe are DMLS metal powders?
A: DMLS metal powders can pose health risks if inhaled. Proper handling procedures, including using a fume hood and wearing personal protective equipment (PPE) like gloves and respirators, are crucial. Always follow the safety data sheet (SDS) provided by the manufacturer for specific handling recommendations.
Q: What are the future trends in DMLS metal powders?
A: The future of DMLS metal powders is bright! Here are some exciting trends to watch:
- Utveckling av nya material: Researchers are constantly developing new DMLS metal powders with improved properties like higher strength, better corrosion resistance, and even the ability to print at higher temperatures.
- Minskade kostnader för pulver: As the DMLS market continues to grow, we can expect to see a decrease in the cost of DMLS metal powders, making this technology more accessible.
- Improved powder characterization: Advancements in powder characterization techniques will allow for more precise control over the properties of DMLS parts.
Slutsats
DMLS metal powders are the invisible heroes behind the revolutionary world of 3D printed metal objects. With their diverse properties and ever-expanding capabilities, they unlock a universe of possibilities for designers, engineers, and manufacturers alike. From lightweight aerospace components to biocompatible medical implants, the potential applications are truly boundless.
So, the next time you marvel at a complex metal object seemingly conjured from thin air, remember the magic of DMLS metal powders – the tiny building blocks that transform imagination into reality.
Disclaimer: The information provided in this article is for informational purposes only and should not be taken as professional advice. Always consult with a qualified professional for specific guidance related to your DMLS project.
Dela på
MET3DP Technology Co, LTD är en ledande leverantör av lösningar för additiv tillverkning med huvudkontor i Qingdao, Kina. Vårt företag är specialiserat på 3D-utskriftsutrustning och högpresterande metallpulver för industriella tillämpningar.
Förfrågan för att få bästa pris och anpassad lösning för ditt företag!
Relaterade artiklar
Om Met3DP
Senaste uppdateringen
Vår produkt
KONTAKTA OSS
Har du några frågor? Skicka oss meddelande nu! Vi kommer att betjäna din begäran med ett helt team efter att ha fått ditt meddelande.
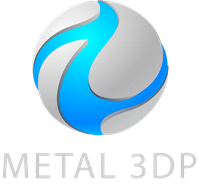
Metallpulver för 3D-printing och additiv tillverkning