DMLS-teknikens utmaningar
Innehållsförteckning
Direkt metalllasersintring (DMLS), även känd som Selective Laser Melting (SLM), har revolutionerat metallbearbetningen. Föreställ dig att trolla fram komplexa, höghållfasta komponenter från ett kärl med metallpulver med hjälp av en laserstråle – det är magin med DMLS. Men som all kraftfull teknik är DMLS inte utan sina utmaningar. Spänn dig fast när vi gräver in i den intrikata världen av DMLS och utforskar hindren som står mellan det och utbredd adoption.
Metallpulver för DMLS
DMLS frodas på en mångsidig kost av metallpulver, som var och en erbjuder unika egenskaper för specifika tillämpningar. Här är ett smakprov på denna metalliska buffé:
Metal Powders for DMLS: A Diverse Feast
Metall/legering | Sammansättning | Fastigheter | Tillämpningar |
---|---|---|---|
Titan (Ti6Al4V) | 90% Ti, 6% Al, 4% V | Högt förhållande mellan styrka och vikt, utmärkt biokompatibilitet | Komponenter för flyg- och rymdindustrin, biomedicinska implantat, tandproteser |
Rostfritt stål (316L) | 66-70% Fe, 16-18% Cr, 10-14% Ni, 2% Mo | Korrosionsbeständig, goda mekaniska egenskaper | Medicinsk utrustning, bildelar, industrikomponenter |
Inconel 625 | Nickel-krom superlegering | Hög temperaturhållfasthet, utmärkt korrosionsbeständighet | Komponenter till gasturbiner, värmeväxlare, utrustning för kemisk bearbetning |
Aluminium (AlSi10Mg) | 90% Al, 10% Si, 0,5% Mg | Lättvikt, god gjutbarhet | Bildelar, flygkonstruktioner, kylflänsar |
Koboltkrom (CoCrMo) | Kobolt-krom-molybdenlegering | Hög slitstyrka, biokompatibel | Ledersättningar, tandimplantat, skärverktyg |
Koppar (Cu) | 100% Cu | Hög termisk och elektrisk ledningsförmåga | Värmeväxlare, elektriska komponenter, vågledare |
Verktygsstål (H13) | Legerat stål med hög kolhalt | Hög hårdhet, bra slitstyrka | Gjutformar, matriser, skärverktyg |
Nickel (Ni) | 100% Ni | Duktil, bra korrosionsbeständighet | Elektriska komponenter, kemisk bearbetningsutrustning, batterier |
Volfram (W) | 100% W | Hög smältpunkt, utmärkt slitstyrka | Elektroder, värmeelement, ballistisk rustning |
Molybden (Mo) | 100% Mo | Hög smältpunkt, bra korrosionsbeständighet | Högtemperaturapplikationer, elektriska komponenter, kemisk bearbetningsutrustning |
Den här listan skrapar bara på ytan av det ständigt växande DMLS-materialbiblioteket. Varje metall erbjuder en unik kombination av styrka, vikt, korrosionsbeständighet och termiska egenskaper, vilket tillgodoser ett stort antal industrier.
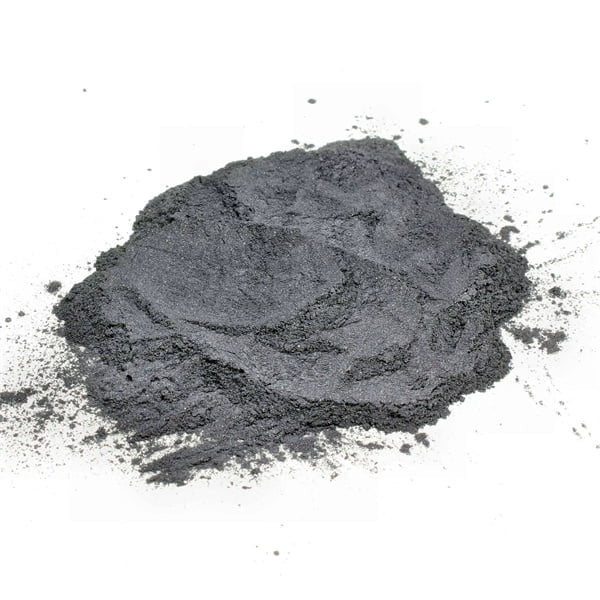
Den höga kostnaden för DMLS Teknik
Ett av de största hindren för DMLS är dess kostnad. DMLS-skrivare i sig är dyra odjur som ofta kostar hundratusentals, ibland till och med miljontals dollar. Men klistermärkeschocken slutar inte där. Metallpulver är heller inget fynd, med vissa exotiska material som kostar flera hundra dollar per kilo. Även efterbearbetningsstegen, som borttagning av stödstruktur och ytbehandling, ökar den totala kostnaden.
Den höga kostnaden för DMLS: ett sammanbrott
- DMLS-skrivarkostnad: $100 000 – $1 000 000+ (beroende på storlek, kapacitet och varumärke)
- Metallpulverkostnad: $50 – $500+ per kilogram (beroende på material)
- Kostnader för efterbearbetning: Variabel beroende på detaljens komplexitet och storlek
Denna kostnadshinder gör DMLS mindre tillgängligt för småföretag och nystartade företag. Medan tekniken erbjuder otrolig designfrihet och prestandafördelar, kan förskottsinvesteringen vara en betydande avskräckande effekt.
Noggrannhet och kvalitetskontroll av DMLS-teknik
DMLS lovar exceptionella detaljer och noggrannhet, men att uppnå jämn kvalitet kan vara en utmaning. Processen är mycket känslig för olika parametrar, såsom lasereffekt, skanningshastighet och skikttjocklek. Även mindre variationer i dessa inställningar kan leda till defekter som porositet (små luftbubblor instängda i metallen), sprickbildning och skevhet. Dessa defekter kan äventyra styrkan och funktionaliteten hos den tryckta delen.
Upprätthålla noggrannhet och kvalitetskontroll i DMLS:
- Processparameteroptimering: Finjustera lasereffekt, skanningshastighet och lagertjocklek för varje material och detaljgeometri.
- Pågående övervakning: Använda övervakningssystem i realtid för att upptäcka anomalier under utskriftsprocessen, vilket gör det möjligt att göra justeringar i farten.
- Tekniker för efterbearbetning: Använder tekniker som stressavlastning och het isostatisk pressning (HIP) för att förbättra de mekaniska egenskaperna och minska risken för defekter.
- Rigorös kvalitetskontroll: Implementera ett robust kvalitetskontrollprogram som inkluderar inspektioner, mekanisk testning och oförstörande utvärderingstekniker för att säkerställa att delar uppfyller de önskade specifikationerna.
Att bemästra dessa aspekter kräver betydande expertis och erfarenhet. Medan framsteg inom automation och sensorteknik effektiviserar kvalitetskontrollen, är det fortfarande en betydande utmaning i DMLS att uppnå konsekventa resultat av hög kvalitet.
Materialval av DMLS Teknik
DMLS har ett stort materialbibliotek, men att välja rätt material för en specifik tillämpning är avgörande. Varje metallpulver erbjuder en distinkt uppsättning egenskaper, och att välja fel kan leda till att delar går sönder. Tänk på dessa faktorer när du väljer ett DMLS-material:
- Nödvändiga mekaniska egenskaper: Styrka, duktilitet, utmattningsbeständighet och slitstyrka är alla avgörande faktorer beroende på applikationen.
- Termiska egenskaper: Tänk på faktorer som värmeledningsförmåga och värmeutvidgningskoefficient, särskilt för delar som kommer att uppleva temperaturfluktuationer.
- Motståndskraft mot korrosion: Miljön där delen kommer att verka spelar en avgörande roll. Till exempel kommer en komponent som utsätts för havsvatten att kräva ett material med överlägsen korrosionsbeständighet jämfört med en del som används inomhus.
- Biokompatibilitet: För medicinska implantat är biokompatibilitet av största vikt. Materialet måste vara giftfritt och integreras sömlöst med kroppen.
- Utskriftsmöjlighet: Alla metaller är inte skapade lika för DMLS. Vissa material är mer benägna att spricka eller skeva under tryckprocessen än andra.
Materialval för DMLS
Att hitta den perfekta balansen mellan dessa egenskaper kan vara en utmaning. Till exempel kan ett material med exceptionell hållfasthet ha dålig korrosionsbeständighet. Omvänt kanske ett mycket korrosionsbeständigt material inte är tillräckligt starkt för en viss tillämpning. I vissa fall kan det vara nödvändigt att utforska alternativa tillverkningstekniker eller till och med överväga att designa om delen för att tillgodose begränsningarna hos tillgängliga DMLS-material.
Säkerhets- och miljöpåverkan av DMLS-teknik
DMLS erbjuder spännande möjligheter för att skapa komplexa, högpresterande delar. Men även säkerhets- och miljöhänsyn måste tas upp.
Säkerhetsproblem i DMLS:
- Stöld av immateriell egendom: Möjligheten att 3D-skriva ut komplicerade komponenter väcker oro över risken för kopiering och förfalskning av upphovsrättsskyddad design.
- Obehörig åtkomst: Att säkra DMLS-skrivare och deras tillhörande data är avgörande för att förhindra obehörig produktion av känsliga delar.
Miljöpåverkan av DMLS:
- Energiförbrukning: DMLS-skrivare förbrukar en betydande mängd energi under drift.
- Metallpulveravfall: Oanvänt metallpulver kan vara en källa till avfall, vilket kräver korrekt hantering och återvinning för att minimera miljöpåverkan.
- Luftkvalitet: Utskriftsprocessen kan generera luftburna partiklar som kräver ordentliga ventilationssystem för att skydda operatörens hälsa.
Dessa problem kräver utveckling av robusta säkerhetsprotokoll och hållbara metoder för DMLS operationer.
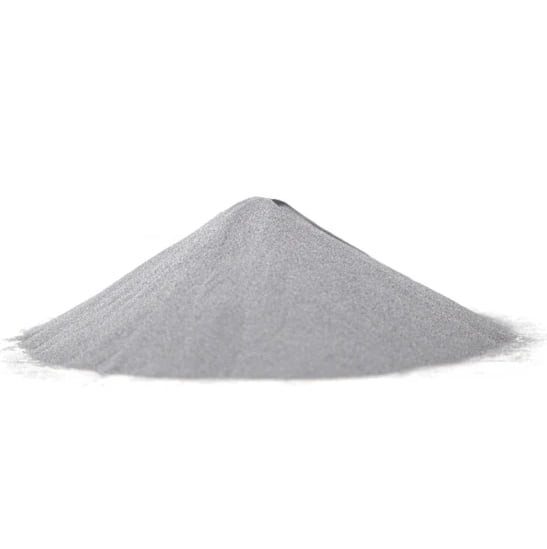
Vanliga frågor
Här är några vanliga frågor om DMLS-teknik, presenterade i ett tabellformat för enkel referens:
Fråga | Svar |
---|---|
Vilka är fördelarna med DMLS? | DMLS erbjuder flera fördelar, inklusive designfrihet, förmågan att producera komplexa geometrier, lättviktsdetaljer och höga hållfasthet-till-vikt-förhållanden. |
Vilka är begränsningarna för DMLS? | De höga kostnaderna för DMLS-skrivare och metallpulver, utmaningar med kvalitetskontroll och ett begränsat urval av material är några av de viktigaste begränsningarna. |
Vilka branscher använder DMLS-teknik? | DMLS används i olika industrier, inklusive flyg-, bil-, medicintekniska produkter och hemelektronik. |
Är DMLS-teknik miljövänlig? | DMLS kan ha en miljöpåverkan på grund av energiförbrukning, metallpulveravfall och luftkvalitetsproblem. Men framsteg inom återvinning och hållbara metoder minimerar denna påverkan. |
Vad är framtiden för DMLS-teknik? | När DMLS-tekniken mognar kan vi förvänta oss att se en kostnadsminskning, ett bredare utbud av material och förbättringar i kvalitetskontroll, vilket gör den mer tillgänglig och allmänt använd. |
DMLS-teknik är ett kraftfullt verktyg med potential att revolutionera tillverkningen. Att erkänna och ta itu med de utmaningar som är förknippade med kostnader, kvalitetskontroll, materialval, säkerhet och miljöpåverkan är dock avgörande för att det ska bli allmänt utbrett. När dessa utmaningar övervinns har DMLS potentialen att låsa upp en ny era av designfrihet och innovation inom olika branscher.
Dela på
MET3DP Technology Co, LTD är en ledande leverantör av lösningar för additiv tillverkning med huvudkontor i Qingdao, Kina. Vårt företag är specialiserat på 3D-utskriftsutrustning och högpresterande metallpulver för industriella tillämpningar.
Förfrågan för att få bästa pris och anpassad lösning för ditt företag!
Relaterade artiklar
Om Met3DP
Senaste uppdateringen
Vår produkt
KONTAKTA OSS
Har du några frågor? Skicka oss meddelande nu! Vi kommer att betjäna din begäran med ett helt team efter att ha fått ditt meddelande.
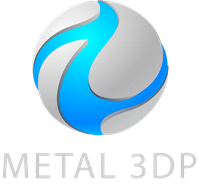
Metallpulver för 3D-printing och additiv tillverkning