3d-skrivare för smältning av elektronstråle
Innehållsförteckning
Översikt of electron beam melting 3d printer
3d-skrivare för smältning av elektronstråle is an additive manufacturing technology commonly used for 3D printing metal parts. An electron beam selectively melts metal powder layer-by-layer based on a CAD model to build complex geometries unmatched by conventional manufacturing.
EBM 3D printers offer benefits like design freedom, mass customization, reduced waste, and lightweighting. Key applications are in the aerospace, medical, dental, and automotive industries. Materials printed on EBM systems include titanium, nickel alloys, stainless steel, aluminum, and cobalt-chrome.
EBM 3D Printer Types
Skrivare | Tillverkare | Byggvolym | Skiktets tjocklek | Beam Power |
---|---|---|---|---|
Arcam EBM Spectra H | GE Additiv | 275 x 275 x 380 mm | 50 μm | 3 kW |
Arcam Q10plus | GE Additiv | ø350 x 380 mm | 50 μm | 3 kW |
Arcam Q20plus | GE Additiv | ø350 x 380 mm | 50 μm | 6 kW |
Sciaky EBAM 300 | Sciaky Inc. | 1500 x 750 x 750 mm | 150 μm | 30-60 kW |
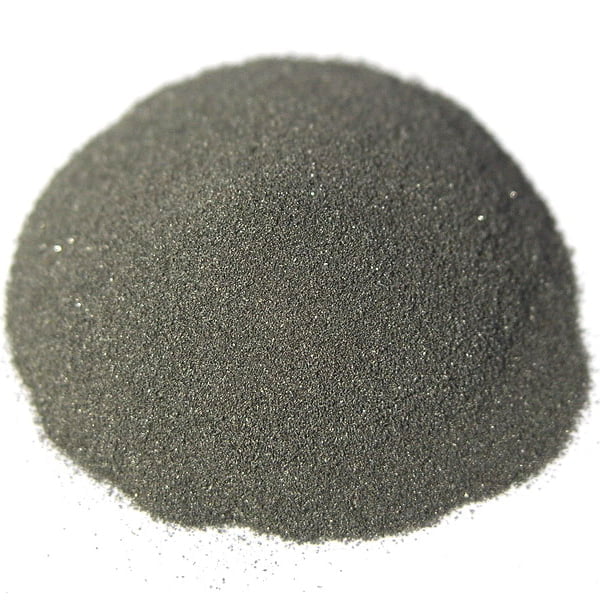
EBM Printing Process
The EBM printing process works as follows:
- Metal powder is evenly distributed onto a build plate using a rake mechanism
- An electron beam selectively preheats the metal powder to around 80% of its melting point, sintering particles together
- The electron beam does a second pass, rapidly melting the material as per the layer geometry
- The build plate lowers and another layer of powder is spread over the build area
- Steps 2-4 repeat until the full part is built up from layers of molten metal
EBM Printer Hardware Components
EBM printers contain the following major hardware components that enable the printing process:
- Elektronpistol: Generates a focused electron beam to selectively melt the metal powder according to CAD data input to the printer. Electrons are emitted from a tungsten filament cathode and accelerated to high kinetic energy. Electromagnets focus and deflect the beam.
- Pulverhantering: Powder hoppers store raw material which is raked onto the build plate before each print layer. Overflow powder is collected and sieved for reuse.
- Build Tank: Sealed chamber where the layer melting takes place at high temperature in a vacuum. Features like heating elements and thermal shields maintain environments up to 1000°C in the build area.
- Styrsystem: Allows operating parameters like speed, beam power, scan patterns, and temperature to be controlled through the printer interface software. Also facilitates loading of CAD models.
EBM Printable Materials
Material | Typ | Egenskaper | Tillämpningar | Leverantörer | Pris |
---|---|---|---|---|---|
Titanlegeringar | Ti-6Al-4V (grade 5), Ti 6Al 4V ELI (Extra Low Interstitial) | Excellent strength-to-weight ratio, biocompatibility, corrosion resistance | Aerospace components, medical implants and devices | AP&C, Carpenter Technology | $350-$500 per kg |
Nickellegeringar | Inconel 718, Inconel 625, Inconel 939 | High temperature strength, resistance to corrosion and oxidation | Aerospace engine parts, power generation equipment | Sandvik | $500-$800 per kg |
Rostfria stål | 316L, 17-4PH, 15-5PH, duplex | Hög hårdhet och slitstyrka | Food/medical devices, tooling, automotive | Sandvik, LPW Technology | $90-$350 per kg |
Kobolt krom | CoCrMo | Excellent fatigue strength and wear properties | Dental copings and bridges, medical implants | SLM-lösningar | $270-$520 per kg |
Aluminium | AlSi10Mg | Låg densitet, god värmeledningsförmåga | Aerospace brackets, automotive parts | AP&C | $95-$150 per kg |
Advantages of EBM 3D Printing
Parameter | Förmån |
---|---|
Designfrihet | Complex geometries like lattices, internal channels are printable |
Snabb prototyptillverkning | Iterations created in days vs weeks for traditional methods |
Massanpassning | Same printer can make variety of personalized parts |
Hög densitet | Near 100% dense metal with mechanicals approaching traditional manufacturing |
Minimal Machining | Reduced finishing since as-printed quality is quite good |
Minskat avfall | Only use required amount of material vs subtractive processes |
Konsekvent kvalitet | Fully automated process enables repeatability over builds |
Cost Advantages | Economies of scale by consolidating tooling, assembly, logistics via part consolidation |
Limitations of EBM Printing
Nackdel | Beskrivning |
---|---|
Geometry Constraints | Supported angles limited around 60° overhangs, minimum wall thickness 0.3-0.4 mm |
Avlägsnande av pulver | Internal channels or volumes unexposed to outside air may have trapped powder |
Beam Occlusions | Some concave areas or deep internal features can be unreachable for the electron beam |
Thermal Stresses | Rapid heating/cooling during processing can induce cracking due to thermal gradients |
Efterbearbetning | Some secondary finishing operations still needed for smoother surfaces or tighter tolerances |
Byggstorleksbegränsningar | Components larger than the printer envelope dimensions cannot be printed |
High Equipment Cost | Printers $500,000+, limit adoption by smaller firms and individual users |
Kostnadsfördelning
A cost comparison of building 10cobalt-chrome dental copings on an Arcam EBM printer is shown below:
Kostnader | Total ($) | Per Unit ($) |
---|---|---|
Printer Depreciation | $2,000 | $200 |
Material (CoCrMo powder) | $1,500 | $150 |
Arbete | $100 | $10 |
Totalt | $3,600 | $360 |
In contrast, outsourcing wax pattern fabrication + lost wax casting for 10 units would cost $600 per unit – so EBM offers significant per unit cost reduction especially at higher volumes.
3d-skrivare för smältning av elektronstråle Leverantörer
Some leading EBM printer equipment manufacturers and metal powder material suppliers include:
Företag | Huvudkontor Plats | Printer Models Offered | Material som stöds |
---|---|---|---|
GE-tillsatser | Kanada | Arcam EBM Spectra, Q Series | Ti-6-4, Inconel, CoCr, more |
Sciaky Inc. | Förenta staterna | EBAM 300 Series | Titanium alloys, steels, aluminum |
SLM-lösningar | Tyskland | N/A | CoCr, stainless steel, more |
Snickeriteknik | Förenta staterna | N/A | Ti-6-4, Inconel alloys, stainless steels |
LPW-teknik | Förenade kungariket | N/A | Nickel alloys, aluminum alloy powders |
Sandvik | Sverige | N/A | Osprey® metal powders for EBM |
The average system cost is $500,000 to $1 million including ancillary equipment like powder removal stations. Materials range from $100 per kg for aluminum up to $800 per kg for specialty nickel superalloys.
3d-skrivare för smältning av elektronstråle Standarder och certifieringar
Key standards associated with quality, specifications, and process control for electron beam melting systems include:
Standard | Beskrivning |
---|---|
ISO 17296-2 | Additive manufacturing of metals – Process, materials & geometries |
ASTM F2971 | Standard practice for production of metallic parts by EBM |
ASTM F3184 | Standard for EBM hardware qualification |
ASME BPVC Sec II-C | Defines approved EBM materials specs |
Both the EBM hardware and manufacturer quality system may be certified to ISO 9001. For aerospace applications additional specifications like AS9100D apply.
Electron Beam Melting vs Other Metal AM
Parameter | Smältning med elektronstråle | Laserpulverbäddsfusion | Deposition med riktad energi |
---|---|---|---|
Värmekälla | Accelerated electron beam | High power Yb fiber laser | Focused laser or e-beam |
Atmosfär | Vakuum | Inert gas | Air or inert gas |
Scan Method | Rastering focused spot | Rastering focused laser spot | Rastering or single spot |
Depositionshastighet | 4-8 cm$^3$/hour | 4-20 cm$^3$/hour | 10-100 cm$^3$/hour |
Noggrannhet | ± 0.1-0.3 mm or ± 0.002 mm/mm | Up to ±0.025 mm or ± 0.002 mm/mm | > 0.5 mm |
Ytfinish | 15 μm Ra, 50 μm Rz | Up to 15 μm roughness | > 25 μm roughness |
Kostnad per del | Medium | Medium | Lägst |
Tillämpningar av 3d-skrivare för smältning av elektronstråle
Due to its ability to produce complex geometries in various high performance metals, electron beam melting finds use across industries like:
Aerospace: Lightweighting aerospace components like titanium and nickel alloy brackets and struts offers fuel efficiency benefits. EBM also enables consolidation of fluid routing channels and mounting features into single parts.
Sjukvård och tandvård: Cobalt chrome and titanium implants with porous surfaces that promote osseointegration can be tailored to patient anatomy via EBM. Significant customization and waste reduction versus traditional stock implant sizes and shapes.
Fordon: Lightweighting parts like aluminum or titanium valve covers and brake calipers reduces vehicle weight for better fuel economy. Short runs of custom turbocharger wheels optimized for racing applications is also economically viable.
Verktyg: Conformal cooling channels can be built into injection mold tooling to accelerate cycle times. Quick turnaround of 10-20 cooling channel layout iterations possible with EBM versus weeks for conventional methods.
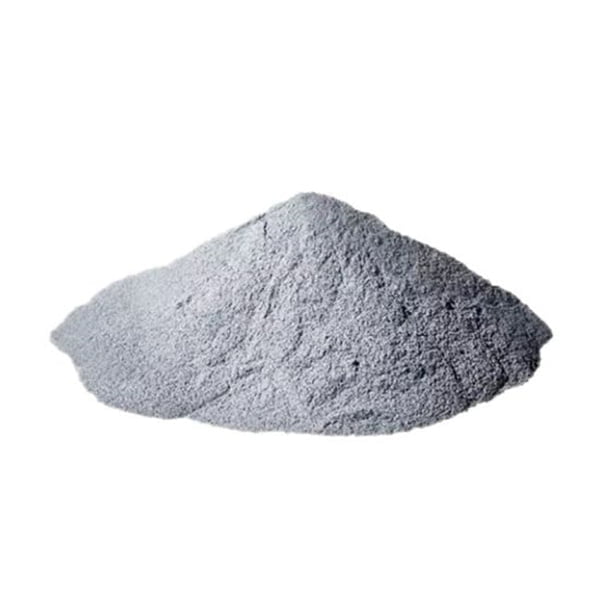
Vanliga frågor
Fråga | Svar |
---|---|
How does part accuracy compare between EBM and traditional manufacturing processes? | Dimensional accuracy and tolerances down to ±0.1 mm are possible for EBM, comparable to casting and forging limits. CNC machining can achieve tighter ±0.01 mm tolerances if needed. |
Does the rough EBM as-printed surface finish require post processing? | Yes the layer-wise staircase effect causes 10-15 μm roughness typically. Tumbling, polishing, blasting, or machining gives smoother finishes down to 0.5 μm if needed. |
Can any metal alloy be used for EBM or are certain compositions unsuitable? | Alloys prone to solid-state cracking from thermal stresses may prove challenging – very high expansion coefficients above 15 μm/(m ̊C) should be avoided. |
What is the main tradeoff between laser and electron beam powder bed fusion processes? | Lasers offer faster build rates up to 100 cm$^3$/hr but maximum beam power is limited to 1 kW. More powerful 8-60 kW e-beams enable deeper penetration in dense metals with higher energy efficiency. |
Sammanfattning
Electron beam melting utilizes a concentrated, high-power electron beam in a vacuum to selectively fuse metal powder particles layer-by-layer until fully dense parts are formed. EBM 3D printers build highly complex geometries unmatched by any other technology, making customization, lightweighting, and part consolidation possible across industries from medical devices to aerospace components. While limited in maximum print volumes compared to other metal additive or conventional techniques, electron beam melting opens new design possibilities and agile manufacturing approaches not previously feasible.
Dela på
MET3DP Technology Co, LTD är en ledande leverantör av lösningar för additiv tillverkning med huvudkontor i Qingdao, Kina. Vårt företag är specialiserat på 3D-utskriftsutrustning och högpresterande metallpulver för industriella tillämpningar.
Förfrågan för att få bästa pris och anpassad lösning för ditt företag!
Relaterade artiklar
Om Met3DP
Senaste uppdateringen
Vår produkt
KONTAKTA OSS
Har du några frågor? Skicka oss meddelande nu! Vi kommer att betjäna din begäran med ett helt team efter att ha fått ditt meddelande.
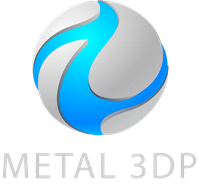
Metallpulver för 3D-printing och additiv tillverkning