Smältningsprocess med elektronstråle
Innehållsförteckning
Översikt över Smältning med elektronstråle
Elektronstrålesmältning (EBM) är en additiv tillverkningsprocess som använder en elektronstrålekraftkälla för att selektivt smälta och smälta metalliskt pulvermaterial lager för lager för att bygga upp komponenter.
Några viktiga detaljer om elektronstrålesmältning inkluderar:
- Använder en elektronstrålepistol under vakuum för att smälta pulvret.
- Bygger uppstår vid höga temperaturer, vilket möjliggör god bindning mellan skikten.
- Används främst för Ti, Ni, Co-legeringar och andra högpresterande material.
- Ger delar med nästan full densitet med egenskaper som motsvarar eller överträffar traditionella medel.
- Stöder komplexa geometrier som inte är möjliga med konventionell tillverkning.
- Används vanligtvis inom flyg-, medicin- och fordonsindustrin.
- Kallas även för elektronstråletillsatstillverkning (EBAM) eller elektronstrålefri formtillverkning (EBF3).
Utrustning för smältning med elektronstråle
Typ | Beskrivning |
---|---|
Elektronstrålepistol | Genererar och fokuserar högenergistråle för att smälta materialet. Nyckelkomponent. |
Pulverbädd | Innehåller pulverlager som krattas av blad eller rullar. Byggd på en flyttbar plattform. |
Vakuumkammare | Hela systemet är under vakuum under byggen. Kritisk för strålfokus. |
Styrsystem | Programvara delar upp och kontrollerar byggparametrar. Ger övervakning och kontroll under processen. |
Hanteringssystem | För lastning/lossning av delar och återvinning av oanvänt pulver. |
Avskärmning | Blyavskärmning krävs runt kammaren på grund av generering av röntgen. |
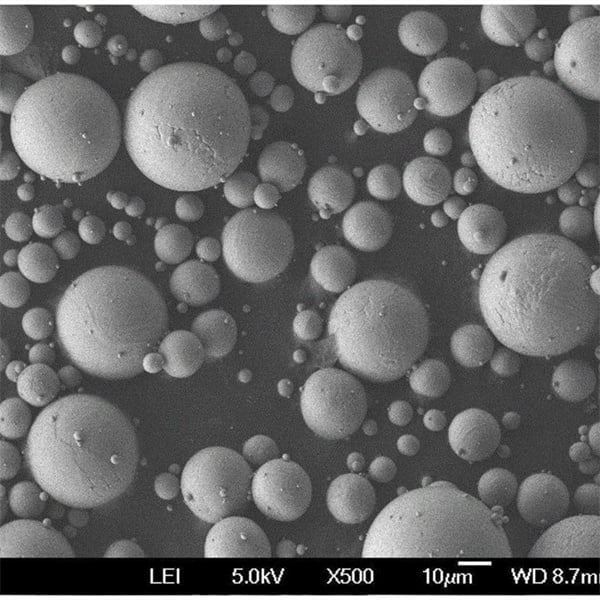
Material som används i Smältning med elektronstråle
Material | Viktiga egenskaper | Typiska tillämpningar |
---|---|---|
Titanlegeringar | Högt förhållande mellan styrka och vikt, biokompatibilitet | Flyg- och rymdindustrin, medicinska implantat |
Nickellegeringar | Korrosionsbeständighet, hög hållfasthet | Turbiner, raketkomponenter |
Kobolt-krom-legeringar | Hårdhet, slitage/korrosionsbeständighet | Medicinska implantat, verktyg |
Rostfritt stål | Bra hållbarhet, lättare bearbetning | Industriella verktyg, formar |
Aluminiumlegeringar | Låg vikt | Flyg- och rymdindustrin, fordonsindustrin |
Ädelmetaller | Mycket kemiskt inert | Smycken, medicinska |
EBM kan bearbeta högpresterande legeringar som är svåra med laserbaserade processer på grund av effektintensitet.
EBM Process Specifikationer
Parameter | Typiskt intervall |
---|---|
Strålkraft | 1-3 kW |
Strålspänning | 30-150 kV |
Bygg storlek | 200 x 200 x 350 mm max |
Höjd på lager | 50-200 μm |
Bygg fart | 5-100 cm3/h |
Strålens storlek | 0,1-1 mm diameter |
Vakuumnivå | 5 x 10-4 mbar |
Strålfokus | 0,1-0,5 mm fläckstorlek |
EBM-system tillåter justering av parametrar som strålkraft, hastighet, fokus etc. för att ställa in efter specifika material.
Leverantörer av EBM-system
Leverantör | Viktiga detaljer | Startprisintervall |
---|---|---|
Leverantör 1 | Pionjär inom EBM-teknik. Största installerade basen. | $1.2-$1.5 miljoner |
Leverantör 2 | System för mindre delar. Snabbare skanningshastigheter. | $0,8-$1,2 miljoner |
Leverantör 3 | Forskningssystem. Öppna parameterkontroll. | $0,5-$0,8 miljoner |
Systemkostnaderna varierar beroende på byggvolym, stråleffekt, medföljande tillbehör och mjukvarufunktioner.
Hur man väljer en EBM-systemleverantör
Urvalskriterier | Viktiga överväganden | Beskrivning |
---|---|---|
Leverantörsexpertis | Branschkunskap | Har leverantören en bevisad meritlista inom just din bransch? Erfarenhet av liknande applikationer säkerställer en djupare förståelse för dina behov och potentiella utmaningar. |
EBM System Portfolio | Vilket utbud av EBM-system erbjuder leverantören? Leta efter en leverantör med en portfölj som tillgodoser din budget, komplexitet och önskade funktioner. | |
Anpassningsmöjligheter | Kan leverantören anpassa EBM-systemet för att passa dina unika krav? Detta kan innebära att skräddarsy datainmatningar, rapporter eller integrera med befintlig programvara. | |
Tekniska förmågor | Programvarufunktioner | Utvärdera funktionerna som erbjuds av EBM-systemet. Ger den de funktioner du behöver för simulering, optimering och analys? Tänk på funktioner som modellbibliotek, scenarioplanering och visualiseringsverktyg. |
Skalbarhet | Kommer EBM-systemet att kunna hantera dina nuvarande och framtida behov? När ditt företag växer bör EBM-systemet anpassas för att rymma mer komplexa modeller och datavolymer. | |
Integrationsförmåga | Kan EBM-systemet integreras sömlöst med din befintliga mjukvaruinfrastruktur? Sömlös integration säkerställer smidigt dataflöde och eliminerar behovet av manuell datainmatning. | |
Implementering & Support | Implementeringsprocess | Erbjuder leverantören en väldefinierad implementeringsprocess? Leta efter en tydlig färdplan med definierade tidslinjer, milstolpar och träningspass. |
Teknisk support | Vilken nivå av teknisk support erbjuder leverantören? Välj en leverantör med lyhörd och kunnig supportpersonal som kan hantera dina tekniska utmaningar effektivt. | |
Användarutbildning | Tillhandahåller leverantören en omfattande användarutbildning? Utbildning ger ditt team möjlighet att utnyttja EBM-systemet effektivt och maximera dess fördelar. | |
Leverantörens rykte och pålitlighet | Finansiell stabilitet | Undersök leverantörens ekonomiska hälsa. Ett stabilt företag är mer benägna att ge löpande support och underhålla EBM-systemet på lång sikt. |
Referenser från kunder | Begär referenser från befintliga kunder i din bransch. Att prata med nöjda kunder kan ge värdefulla insikter om leverantörens kapacitet och servicekvalitet. | |
Bransch erkännande | Har leverantören fått branschpriser eller erkännande för sina EBM-system? Erkännande indikerar ett starkt rykte för kvalitet och innovation. | |
Kostnad & värde | Licenskostnader | Jämför licenskostnaderna för olika EBM-system. Tänk på kostnaden i förhållande till det värde systemet levererar och dess potentiella avkastning på investeringen (ROI). |
Implementeringskostnader | Ta hänsyn till implementeringskostnaderna, inklusive utbildning och eventuell anpassning. | |
Löpande supportkostnader | Förstå kostnaderna i samband med löpande teknisk support och underhåll. |
Hur man optimerar EBM Process
Faktor | Beskrivning | Inverkan på delkvalitet | Optimeringsstrategier |
---|---|---|---|
Pulvermaterial | Partikelstorlek, fördelning, kemi | Påverkar direkt smältbeteende, densitet och mekaniska egenskaper | Använd sfäriska pulver med en snäv storleksfördelning för jämn packning och flöde. Välj pulverkemi baserat på önskade slutliga egenskaper (t.ex. styrka, korrosionsbeständighet). Genomför förvärmnings- eller torkningsprocedurer för att avlägsna fukt och förbättra flytbarheten. |
Strålparametrar | Stråleffekt, skanningshastighet, punktstorlek, skanningsmönster | Kontrollera smältdjup, termiska gradienter och kvarvarande spänningar | Finjustera stråleffekten och skanningshastigheten för att uppnå full smältning utan överdrivet stänk eller förångning. Justera skanningsmönster (luckoravstånd, skanningsrotation) för att minimera värmekoncentration och skevhet. Använd strålförskjutningstekniker för att kompensera för krympning under smältning. |
Bygg miljö | Vakuumtryck, kammartemperatur | Bibehåller en ren, kontrollerad atmosfär och minskar oxidation | Upprätthåll höga vakuumnivåer (vanligtvis 10^-4 Pa) för att förhindra gaskontamination. Förvärm kammaren till en temperatur något under pulvrets smältpunkt för att förbättra flytbarheten och minska termisk chock. |
Stödstrukturer | Design, material | Säkerställ korrekt värmeavledning och förhindra att delen kollapsar | Designa minimala men tillräckliga stödstrukturer för att minimera materialanvändning och efterbearbetningstid. Använd gallerstrukturer eller brytstöd för komplexa geometrier. Utforska alternativa stödmaterial (t.ex. vattenlösliga underlag) för att förenkla efterbearbetningen. |
Processövervakning & kontroll | Övervakning av smältbassäng, kontroll av skikttjocklek | Säkerställer konsekvent byggkvalitet och identifierar potentiella defekter | Implementera smältpoolsövervakningssystem i realtid (t.ex. pyrometri, smältbassängavbildning) för att justera processparametrar för optimalt smältbeteende. Använd återkopplingssystem med sluten slinga för att automatiskt justera lagertjockleken baserat på sensordata. |
Efterbearbetningstekniker | Varmisostatisk pressning (HIP), bearbetning, ytbehandling | Förbättra mekaniska egenskaper, dimensionsnoggrannhet och ytkvalitet | Använd HIP för att eliminera inre tomrum och förbättra detaljdensiteten. Implementera spänningsavlastande bearbetningstekniker för att minimera kvarvarande spänningar och förbättra utmattningslivslängden. Använd lämpliga ytbehandlingsmetoder (t.ex. kulblästring, polering) baserat på önskade ytegenskaper. |
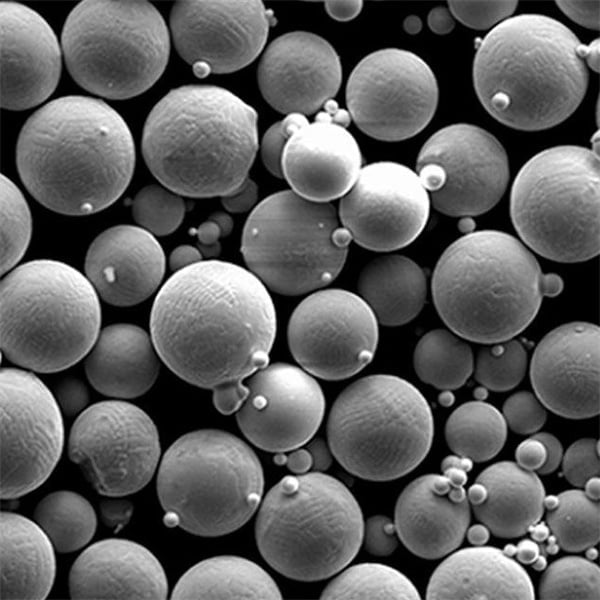
Hur man designar delar för EBM
Funktion | Beskrivning | Fördel för EBM | Överväganden |
---|---|---|---|
Väggens tjocklek | Den minsta tjockleken för en solid funktion i din design. | Möjliggör intrikata detaljer och interna kanaler. | För tunn (< 0,3 mm) kan orsaka dålig upplösning och sprickbildning. Tänk på minsta tjocklek baserat på material och önskade mekaniska egenskaper. |
Överhängsvinklar | Vinkeln med vilken en funktion sticker ut utan stöd. | Uppnår komplexa geometrier. | Vinklar som är brantare än 45° kräver vanligtvis stödstrukturer, vilket ökar efterbearbetningen och eventuellt minskar styrkan. Designa om funktioner med mjukare sluttningar eller använd gallerstrukturer för överhängsstöd. |
Interna funktioner | Kanaler, håligheter och ihåliga sektioner inom delen. | Lättar vikten och skapar utrymme för vätskeflöde eller värmeavledning. | Säkerställ tillräcklig väggtjocklek för interna funktioner för att undvika kollaps under utskrift. Designa kanaler med rundade hörn för att minimera stresskoncentrationspunkter. Stora inre hålrum kan kräva strategiskt placerade dräneringshål för borttagning av överflödigt pulver. |
Draft vinklar | Avsmalningsvinkeln på vertikala sidoväggar. | Främjar lättare borttagning av pulver och minskar ytjämnheten. | Minsta drag på 5-10° rekommenderas för de flesta metaller. Brantare drag kan behövas för komplexa funktioner eller djupa håligheter. |
Stödstrukturer | Tillfälliga strukturer som genereras av programvaran för att hålla uppe överhängande funktioner. | Möjliggör invecklade geometrier bortom naturliga byggvinklar. | Minimera supportanvändningen för att minska efterbehandlingstiden och potentiella problem med borttagning av supportmärken. Design för självbärande funktioner när det är möjligt. När stöd är nödvändiga, välj brytbara eller upplösbara stödtyper för enklare borttagning. |
Gallerstrukturer | Öppna, cellulära strukturer som används internt för viktminskning eller anpassad styvhet. | Optimerar vikt-till-hållfasthet-förhållandet och uppnår specifika mekaniska egenskaper. | Utforska olika gallertyper (t.ex. kubisk, diamant) baserat på önskade lastbärande egenskaper. Säkerställ adekvat stödtjocklek inom gallret för att bibehålla strukturell integritet. |
Ytfinish | Den slutliga strukturen på den tryckta delens yta. | Uppnår önskad estetik eller funktionskrav. | EBM-ytor som tryckts kan vara något grova. För jämnare ytbehandlingar, överväg efterbearbetningstekniker som bearbetning eller polering. Designfunktioner med minimala överhäng för att minska behovet av omfattande ytbehandling. |
Val av material | Den typ av metallpulver som används för utskrift. | Utnyttjar unika egenskaper hos olika metaller. | Vanliga EBM-material inkluderar titanlegeringar, Inconel och CoCr. Tänk på faktorer som styrka, korrosionsbeständighet, biokompatibilitet och termiska egenskaper när du väljer ett material. |
Termisk hantering | Strategier för att minimera värmerelaterade förvrängningar under utskrift. | Bibehåller dimensionell noggrannhet och minskar kvarvarande spänningar. | Använd variationer i väggtjockleken för att fördela värmen jämnt. Design för värmeavledningsvägar genom inre kanaler eller gallerstrukturer. Utforska utskriftsstrategier som optimering av skanningsvägar för att minimera värmekoncentrationen i specifika områden. |
Hur man efterbearbetar EBM-delar
Steg | Beskrivning | Syfte | Tekniker | Överväganden |
---|---|---|---|---|
Depoldering | Det första och väsentliga steget innefattar att avlägsna obundet metallpulver som omger den byggda delen. | Säkerställer säker hantering, förhindrar kontaminering och möjliggör korrekt inspektion och efterföljande efterbehandling. | Mekanisk pulverisering: En mängd olika automatiserade och manuella avpulverstationer använder borstar, tryckluft och vibrationer för att avlägsna löst pulver. Vattenstråle: En högtrycksvattenstråle tar försiktigt bort pulver samtidigt som ytjämnheten minimeras. | Välj pulveriseringsmetod baserat på detaljens geometri och materialegenskaper. Till exempel kan intrikata funktioner kräva vattensprutning för skonsammare borttagning. Säkerställ korrekt ventilation och dammuppsamling under mekanisk avpudring. |
Borttagning av stödstruktur | EBM-delar kräver ofta tillfälliga stödstrukturer under utskrift för att förhindra överhängande detaljer från att kollapsa. | Möjliggör borttagning av stödstrukturer utan att skada den sista delen. | Wire EDM (Electrical Discharge Machining): En exakt metod som använder elektriska gnistor för att skära igenom stödstrukturer. Slipning: Manuell eller CNC-styrd slipning tar bort större stödstrukturer. Kemisk fräsning: Ett kemiskt bad löser upp stödstrukturer gjorda av lösliga material. | Wire EDM erbjuder hög noggrannhet men kan vara tidskrävande för komplexa stöd. Slipningen går snabbare men kräver skickliga operatörer för att undvika att skada delen. Kemisk fräsning är lämplig för stora partier av liknande delar med lösliga underlag. |
Minskning av ytjämnhet | Den inneboende trappstegseffekten från lager-för-lager-utskrift i EBM resulterar i en grov ytstruktur. | Förbättrar delens estetik, funktionella prestanda och tribologiska egenskaper (slitage och friktion). | Slipning och slipning: Slipmedel jämnar ut ytor genom friktion. Vibrerande efterbehandling: Delar vibreras i en mediabädd för övergripande ytförbättring. Polering: Mekanisk eller elektrokemisk polering skapar en spegelliknande finish. | Den valda tekniken beror på önskad ytfinish och geometri. Slipning är effektivt för plana ytor, medan tumling fungerar bra för komplexa former. Polering ger den jämnaste finishen men kan ändra dimensioner. |
Stressavlastning | Den snabba uppvärmningen och nedkylningen under EBM kan införa restspänningar i detaljen. | Minskar risken för vridning, sprickbildning och förbättrar dimensionsstabiliteten. | Termisk glödgning: Delen värms upp till en specifik temperatur och hålls under en kontrollerad tid för att tillåta påfrestningar att slappna av. | Glödgningsparametrar beror på materialet och delens geometri. Felaktig glödgning kan påverka de mekaniska egenskaperna negativt. Samråd med materialexperter rekommenderas. |
Inspektion och kvalitetskontroll | Det sista steget säkerställer att den färdiga delen uppfyller dimensionella toleranser, krav på ytfinish och är fri från sprickor eller defekter. | Verifierar delens överensstämmelse med designspecifikationerna och säkerställer funktionalitet. | Måttmått: Koordinatmätmaskiner (CMM) mäter detaljer med hög precision. Ytgrovhetsmätning: Profilometrar kvantifierar ytstrukturen. Icke-förstörande testning (NDT): Tekniker som röntgenröntgen och ultraljudstestning upptäcker inre sprickor och defekter. | Inspektionsplanen bör upprättas före tryckning |
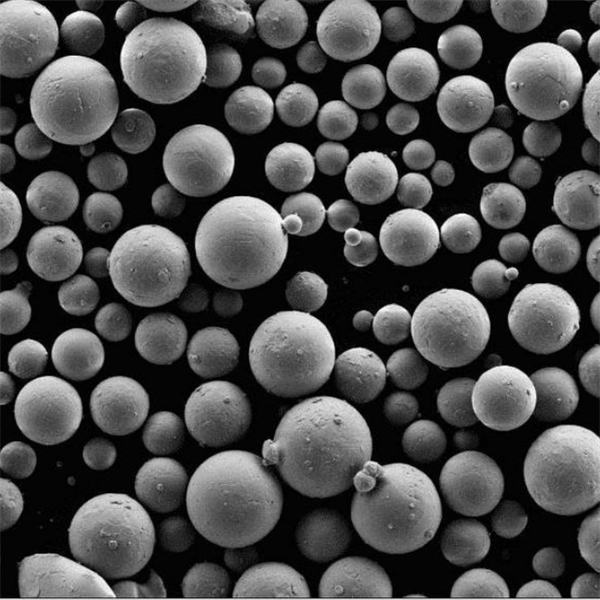
Hur man installerar och integrerar EBM Delar
Steg | Uppgift | Beskrivning | Överväganden |
---|---|---|---|
1 | Förberedelse | Innan du går in i installationen, säkerställ en smidig integrationsprocess. | Identifiera EBM-delar: Definiera tydligt komponenterna för evidensbaserad medicin (EBM) du tänker integrera. Är det kliniska beslutsstödsverktyg, standardiserade protokoll eller patientutbildningsmaterial? Systemkompatibilitet: Verifiera kompatibiliteten mellan EBM-delarna och ditt befintliga elektroniska patientjournalsystem eller plattform. Olika system kan kräva specifika filformat eller integrationsmetoder. Datamappning: Planera hur data från EBM-delarna ska mappas till motsvarande fält inom ditt EPJ-system. Detta säkerställer ett sömlöst informationsflöde och undviker dataredundans. Arbetsflödesanalys: Analysera dina nuvarande arbetsflöden för att identifiera de mest lämpliga punkterna för EBM-delintegrering. Detta minimerar störningar och optimerar användaranpassningen. |
2 | Installation | Följ de specifika instruktionerna från EBM-delsleverantören. | Teknisk expertis: Beroende på komplexiteten hos EBM-delarna kan du behöva hjälp från ditt IT-team eller EBM-delsleverantören för installation. Systemavbrottstid: Schemalägg installation under icke-högtrafik för att minimera störningar i pågående kliniska aktiviteter. Testar: Genomför grundliga tester efter installationen för att säkerställa att EBM-delarna fungerar korrekt och integreras sömlöst med ditt EPJ-system. Testa olika scenarier för att identifiera och åtgärda eventuella problem. |
3 | Konfiguration | Skräddarsy EBM-delarna efter dina specifika behov och arbetsflöden. | Användarroller och behörigheter: Definiera användarroller och tilldela lämpliga behörigheter för att komma åt och använda EBM-delarna i ditt system. Anpassningsalternativ: Utforska anpassningsalternativ som erbjuds av EBM-delarna. Detta kan innebära att skräddarsy uppmaningar till beslutsstöd, varningströsklar eller utbildningsinnehåll för att bättre passa din patientpopulation och kliniska praxis. Rapportering och analys: Konfigurera rapporteringsfunktioner för att spåra användningen och effekten av EBM-delarna. Dessa data kan vara värdefulla för att utvärdera effektiviteten och identifiera områden för ytterligare optimering. |
4 | Utbildning och support | Utrusta din personal med kunskap och färdigheter för att effektivt använda EBM-delarna. | Användarutbildning: Utveckla utbildningsmaterial och genomföra sessioner för kliniker och personal för att bekanta dem med funktionerna, fördelarna och begränsningarna hos EBM-delarna. Löpande support: Etablera tydliga kanaler för löpande support från EBM-delsleverantören eller ditt IT-team. Detta säkerställer att användare lätt kan få hjälp när de stöter på problem. |
5 | Övervakning och utvärdering | Utvärdera kontinuerligt effektiviteten av EBM-delarna och identifiera möjligheter till förbättringar. | Prestandaövervakning: Spåra nyckelmått som EBM-delutnyttjandegrad, efterlevnad av protokoll och patientresultat. Användarfeedback: Samla in feedback från kliniker och personal angående deras erfarenhet av EBM-delarna. Detta kan avslöja områden för förbättringar eller lyfta fram oväntade fördelar. Dataanalys: Analysera regelbundet data som samlas in under övervakning för att identifiera trender och bedöma effekten av EBM-delar på klinisk praxis och patientvård. |
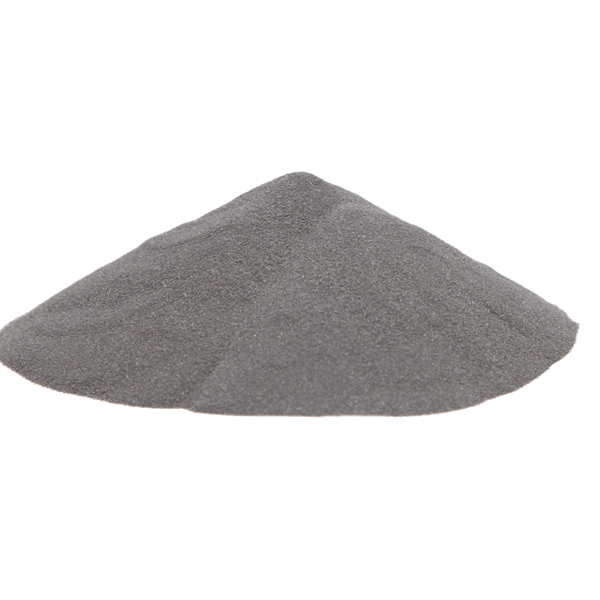
Drift och underhåll av EBM-skrivare
Uppgift | Beskrivning | Frekvens | Resurser |
---|---|---|---|
Laddar media | Se till att rätt mediatyp (etiketter, etiketter, band) är laddade enligt skrivarens specifikationer. Rikta in materialet ordentligt i matarfacket och se till att det matas rakt och att spänningen är lämplig. Justera mediaguiderna för optimal passform. | Före varje utskriftsjobb | Skrivarmanual, Mediespecifikationer |
Ribbon Management | Inspektera bandet för slitage. Byt ut när den är skrynklig, sliten eller närmar sig slutet. Se till att bandtyp (vax, harts, etc.) matchar media och utskriftskrav. | Före varje utskriftsjobb eller när utskriftskvaliteten försämras | Bandspecifikationer, skrivarmanual |
Inlämning av utskriftsjobb | Kontrollera att utskriftsinställningarna (upplösning, kvantitet, mediastorlek, orientering) matchar dokumentspecifikationerna. Välj lämplig skrivardrivrutin på datorn. Förhandsgranska utskriftsjobbet för att säkerställa noggrannhet innan du skickar det till skrivaren. | Varje utskriftsjobb | Skrivarprogramvara, programvara för att skapa dokument |
Övervaka utskriftsstatus | Observera skrivarmeddelanden för fel eller varningar (lågt material, problem med färgband, problem med skrivhuvudet). Kontrollera regelbundet skrivarens utdata för kvalitetsproblem (ränder, fläckar, feljustering). | Under utskrift | Skrivarens displaypanel, utskriven utskrift |
Daglig städning | Använd en luddfri trasa för att torka av skrivarens yttre ytor. Rengör skrivhuvudet med en bomullstuss fuktad med isopropylalkohol (se manualen för specifika instruktioner). | Dagligen | Luddfri trasa, isopropylalkohol (rekommenderad koncentration i manualen), skrivarmanual |
Schemalagt underhåll | Följ tillverkarens rekommendationer för periodisk rengöring av utskriftsbanan (rullar, vals). Byt ut slitna skrivhuvud eller andra komponenter vid behov, följ instruktionerna i skrivarhandboken. | Var 3-6 månad (eller enligt instruktionerna i manualen) | Skrivarmanual, reservdelar (se manualen för kompatibilitet) |
Felsökning | Se skrivarhandbokens felsökningsguide för vanliga problem (pappersstopp, utskriftsfel). Kontakta EBMs tekniska support för hjälp med komplexa problem. | Efter behov | Skrivarmanual, EBM teknisk support kontaktinformation (telefonnummer, webbplats) |
För- och nackdelar med Smältning med elektronstråle
Funktion | Proffs | Nackdelar |
---|---|---|
Delkvalitet | Hög densitet: EBM skapar delar med nästan nettotäthet (>99.5%) på grund av att den kraftfulla elektronstrålen smälter metallpulvret helt. Detta översätts till starka, funktionella delar med utmärkta mekaniska egenskaper jämförbara med smidesmetaller. Komplexa geometrier: EBM utmärker sig på att producera intrikata funktioner och interna kanaler tack vare den exakta kontrollen av elektronstrålen. Till skillnad från vissa andra additiv tillverkningsprocesser, finns det inget behov av stödstrukturer för överhängande funktioner. | Ytfinish: Lager-för-lager smältningsprocessen i EBM resulterar i en något grövre ytfinish jämfört med tekniker som Selective Laser Melting (SLM). Detta kan kräva efterbearbetning för applikationer som kräver en jämn estetik. Noggrannhet: Även om den är mycket exakt, är EBM:s elektronstrålediameter i sig större än laserstrålen som används i SLM. Detta kan leda till något mindre exakta dimensionstoleranser jämfört med SLM-tryckta delar. |
Materialkompatibilitet | Brett utbud av metaller: EBM har exceptionell kompatibilitet med en mängd olika reaktiva och eldfasta metaller, inklusive titanlegeringar, Inconel och till och med vissa sällsynta jordartsmetaller. Detta gör den idealisk för applikationer där dessa högpresterande material är avgörande. | Pulverhantering: Reaktiva metaller som används i EBM är mycket känsliga för oxidation och kontaminering. Hela EBM-processen måste ske i en vakuummiljö för att förhindra dessa problem, vilket ökar komplexiteten och kostnaden. |
Hastighet och effektivitet | Snabbare byggtider: Elektronstrålens höga energitäthet möjliggör snabbare smältning och snabbare byggtider jämfört med SLM, speciellt för större delar. Materialåteranvändning: Oanvänt metallpulver i EBM-kammaren kan återvinnas och återanvändas i hög grad, vilket minimerar avfalls- och materialkostnader. | Lager-för-lager-process: Trots snabbare smältning kan EBM:s inneboende lager-för-lager-natur fortfarande leda till längre byggtider jämfört med additiva metoder som avsätter hela lager på en gång. |
Operativa överväganden | Vakuum Miljö: Behovet av en högvakuummiljö i EBM-kammaren gör systemet mer komplext och kräver specialiserad utbildning för operatörer. Säkerhet: EBM-processer genererar röntgenstrålar på grund av högenergielektronstrålen. Korrekt säkerhetsprotokoll och utrustning är avgörande för att skydda operatörerna. | Kostnad: EBM-maskiner och deras drift tenderar att vara dyrare jämfört med vissa andra additiv tillverkningsteknik. Detta kan vara ett hinder för inträde, särskilt för mindre företag. |
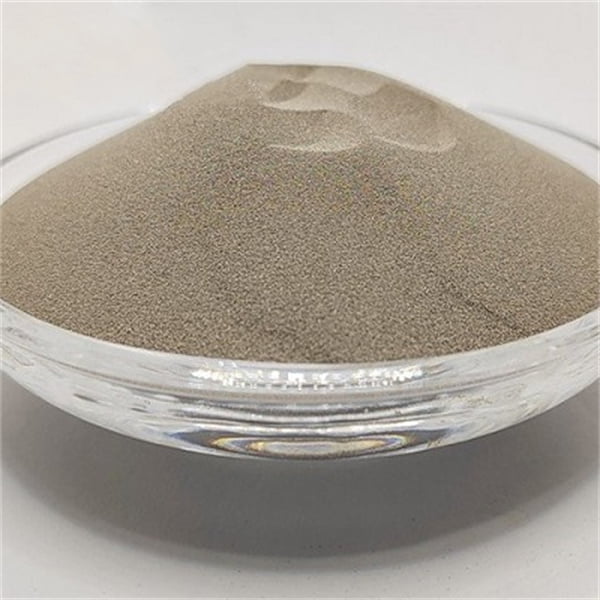
VANLIGA FRÅGOR
F: Vilka material kan du bearbeta med EBM?
S: Framför allt legeringar av titan, nickel, kobolt och rostfritt stål hittills. Forskning utökar materialalternativ inklusive aluminium, verktygsstål, guld, tantal och mer.
F: Vad är den största skillnaden mellan EBM och selektiv lasersmältning (SLM)?
S: EBM använder en elektronstråleenergikälla medan SLM använder en laser. De högre stråleffekttätheterna som kan uppnås med EBM tillåter bearbetning av mer eldfasta metaller.
F: Vilka industrier använder EBM-utskrift?
A: Aerospace är den största tillverkaren hittills för komponenter som turbinblad. Men medicin-, fordons- och industrisektorn ökar också användare av EBM.
F: Tillverkar EBM porösa eller helt täta detaljer?
S: EBM kan uppnå över 99% densitet med optimala parametrar. De höga temperaturbyggnaderna förbättrar diffusionsbindningen mellan skikten.
F: Vilken storlek delar kan du skapa med EBM?
S: Den maximala storleken begränsas av byggkuvertet, vanligtvis cirka 250 x 250 x 300 mm. Större system är under utveckling med inriktning på 500 mm kuber.
F: Hur exakt är EBM jämfört med CNC-bearbetning?
S: EBM kan uppnå toleranser ner till 0,1-0,3 mm när det är väl kalibrerat. Men bearbetning behövs för att nå snävare toleranser under 0,05 mm.
F: Vilka är några av de viktigaste fördelarna med EBM?
S: Designfrihet, delkonsolidering, snabb prototypframställning, höghållfasta legeringar, minskat spill och korta ledtider jämfört med traditionell tillverkning.
F: Vilka säkerhetsåtgärder krävs för EBM?
S: EBM-system genererar röntgenstrålning så adekvat blyavskärmning av byggkammaren är kritisk. Endast utbildad personal får arbeta.
Dela på
MET3DP Technology Co, LTD är en ledande leverantör av lösningar för additiv tillverkning med huvudkontor i Qingdao, Kina. Vårt företag är specialiserat på 3D-utskriftsutrustning och högpresterande metallpulver för industriella tillämpningar.
Förfrågan för att få bästa pris och anpassad lösning för ditt företag!
Relaterade artiklar
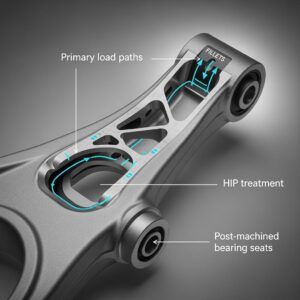
Metal 3D Printing for U.S. Automotive Lightweight Structural Brackets and Suspension Components
Läs mer "Om Met3DP
Senaste uppdateringen
Vår produkt
KONTAKTA OSS
Har du några frågor? Skicka oss meddelande nu! Vi kommer att betjäna din begäran med ett helt team efter att ha fått ditt meddelande.