Corrosion-Resistant Enclosures for Underwater Sensors
Innehållsförteckning
Introduction: Protecting Sensitive Equipment in Harsh Marine Environments
The vast, often unforgiving, marine environment holds immense potential for scientific discovery, resource management, and strategic operations. From mapping the deepest ocean trenches to monitoring coastal ecosystems and managing offshore energy platforms, our ability to gather data from beneath the waves is paramount. At the heart of this capability lie sophisticated underwater sensors – the eyes and ears that provide critical insights into this challenging domain. However, these sensitive electronic instruments are incredibly vulnerable. They must operate reliably under conditions that would quickly destroy unprotected equipment: crushing pressures, relentless saltwater corrosion, pervasive biofouling, and potential physical impacts. This is where the underwater sensor enclosure, also known as a subsea sensor housing eller marine equipment enclosure, plays a mission-critical role.
An underwater sensor enclosure is far more than just a box; it is a precisely engineered shield designed to maintain a controlled internal environment, ensuring the sensor’s functionality and longevity. Its primary function is to isolate the delicate sensor components from the hostile external conditions. This involves several key challenges:
- Extreme Hydrostatic Pressure: Water pressure increases dramatically with depth (approximately 1 atmosphere or 14.7 psi for every 10 meters). Enclosures for deep-sea applications must withstand immense forces without leaking or collapsing.
- Aggressive Corrosion: Seawater is a highly corrosive electrolyte, readily attacking many common metals. Galvanic corrosion can also occur when dissimilar metals are in contact in seawater. Preventing leaks and maintaining structural integrity over time demands exceptional material performance and design.
- Biofouling: Marine organisms (algae, barnacles, mussels, etc.) rapidly colonize submerged surfaces. This fouling can impede sensor function (e.g., blocking optical paths), increase hydrodynamic drag, add weight, and even accelerate localized corrosion.
- Physical Impacts: Enclosures may be subject to impacts during deployment, recovery, or from underwater debris or marine life. Robustness is essential.
Traditionally, manufacturing these vital enclosures involved methods like machining from solid billets, casting, or fabricating components from plates and tubes. While effective, these methods often come with limitations, particularly regarding design complexity, material waste (especially with expensive corrosion-resistant alloys), lead times for custom designs, and the number of potential leak paths introduced by joints and seals. Procurement managers and engineers constantly seek more efficient, reliable, and cost-effective solutions, especially when sourcing wholesale marine components or requiring custom enclosure manufacturers.
Skriva in Additiv tillverkning av metall (AM), commonly known as metal 3D-utskrifter. This transformative technology offers a paradigm shift in how we design and produce high-performance components like underwater sensor enclosures. By building parts layer-by-layer directly from metal powder feedstock using processes like Laser Powder Bed Fusion (L-PBF) or Electron Beam Melting (EBM), metal AM overcomes many traditional limitations. It enables the creation of complex geometries, optimizes material usage, allows for rapid design iteration, and facilitates the consolidation of multiple parts into a single, monolithic structure, inherently reducing potential failure points. For demanding applications requiring superior corrosion prevention and reliability in deep-sea technology, 3D-utskrift av metall presents a compelling value proposition, offering enhanced performance, design flexibility, and potentially faster routes to deployment for critical subsea equipment enclosures. Companies seeking reliable additive manufacturing marine application partners are finding significant advantages in leveraging this technology for durable and high-performance underwater hardware.
Applications of Underwater Sensor Enclosures: From Seabed Monitoring to Offshore Energy
The need for robust, reliable underwater sensor enclosures spans a remarkably diverse range of industries and applications. Procurement specialists sourcing components for subsea sensor deployment or engineers designing offshore sensor systems will recognize the critical nature of these housings across multiple sectors. Understanding these use cases highlights the versatility required from enclosure designs and the materials used in their construction. Partnering with a knowledgeable marine monitoring equipment supplier who understands these varied demands is crucial.
Here’s a breakdown of key application areas where high-performance enclosures are indispensable:
- Oceanography and Marine Research: This is perhaps the most foundational application. Scientists deploy a vast array of sensors to study ocean currents, temperature, salinity (using CTD – Conductivity, Temperature, Depth sensors), water chemistry, marine life (via acoustic monitoring or cameras), and geological features of the seabed.
- Exempel på detta: Housings for Acoustic Doppler Current Profilers (ADCPs), deep-sea landers, autonomous underwater vehicles (AUVs), remotely operated vehicles (ROVs), towed sensor arrays, and long-term mooring systems. Reliability is paramount for capturing accurate, long-term datasets.
- Offshore Oil & Gas: The exploration, production, and monitoring of offshore oil and gas fields rely heavily on underwater sensors. Enclosures protect critical equipment used for pipeline monitoring (leak detection, flow metering), structural health monitoring of platforms and subsea infrastructure, environmental monitoring, and controlling subsea production systems.
- Exempel på detta: Enclosures for pressure and temperature sensors, acoustic leak detectors, valve position sensors, corrosion probes, and communication equipment nodes. The demanding environment requires extreme durability and often specific material certifications. Finding reliable offshore technology suppliers är nyckeln.
- Offshore Renewable Energy: The burgeoning offshore wind and tidal energy sectors require extensive underwater monitoring. Enclosures protect sensors used for environmental impact assessments, foundation scour monitoring, structural health monitoring of turbines and cables, and acoustic monitoring for marine mammal activity.
- Exempel på detta: Housings for seabed survey equipment (sonar, magnetometers), turbine foundation sensors (accelerometers, strain gauges), cable integrity sensors, and environmental monitoring packages. Long-term deployment and resistance to biofouling are often critical.
- Aquaculture: Modern fish farming operations utilize underwater sensors to monitor water quality parameters (oxygen levels, temperature, pH, ammonia), fish behavior (using cameras and sonar), and environmental conditions within and around net pens.
- Exempel på detta: Rugged enclosures for water quality sondes, underwater cameras, acoustic feeding response sensors, and environmental data loggers. Resistance to biofouling and ease of cleaning are important considerations for aquaculture technology suppliers.
- Försvar och säkerhet: Naval forces and maritime security agencies use sophisticated underwater sensors for surveillance, reconnaissance, mine countermeasures, and anti-submarine warfare. Enclosures protect highly sensitive sonar equipment, hydrophones, magnetic anomaly detectors, and communication systems.
- Exempel på detta: Housings for towed sonar arrays, hull-mounted sonar domes, seabed sensor networks, submarine sensor systems, and components for unmanned underwater vehicles (UUVs). Extreme ruggedness, acoustic transparency (in some cases), and specific material signatures might be required. Procurement often involves specialized defense sonar housing specifications.
- Marine Construction and Salvage: Underwater construction projects (bridges, tunnels, ports) and salvage operations utilize sensors for positioning, monitoring structural integrity, and surveying work sites.
- Exempel på detta: Enclosures for positioning beacons, sonar imaging systems, environmental monitors, and ROV/diver tool sensors. Durability during deployment and recovery in potentially debris-filled waters is essential.
Types of Sensors Commonly Housed:
The specific sensor dictates certain enclosure design requirements (size, mounting, cable penetrations, potential need for optical windows or acoustic transparency), but common types include:
- Acoustic Sensors: Hydrophones, sonar transducers (side-scan, multi-beam), ADCPs.
- Optical Sensors: Underwater cameras, turbidity sensors, fluorometers.
- Environmental Sensors: CTD probes, dissolved oxygen sensors, pH sensors, pressure sensors, temperature sensors.
- Positioning Sensors: Acoustic transponders, depth sensors.
- Inertial Sensors: Accelerometers, gyroscopes (for AUV/ROV navigation).
Across all these diverse applications, the common thread is the need for enclosures that provide uncompromising protection against the specific challenges of the underwater environment. Whether sourcing standard components in bulk or seeking custom enclosure manufacturers for specialized ROV/AUV components procurement, the reliability of the enclosure directly impacts the success and safety of the entire operation. Metal AM provides a powerful toolset to meet these varied and demanding requirements.
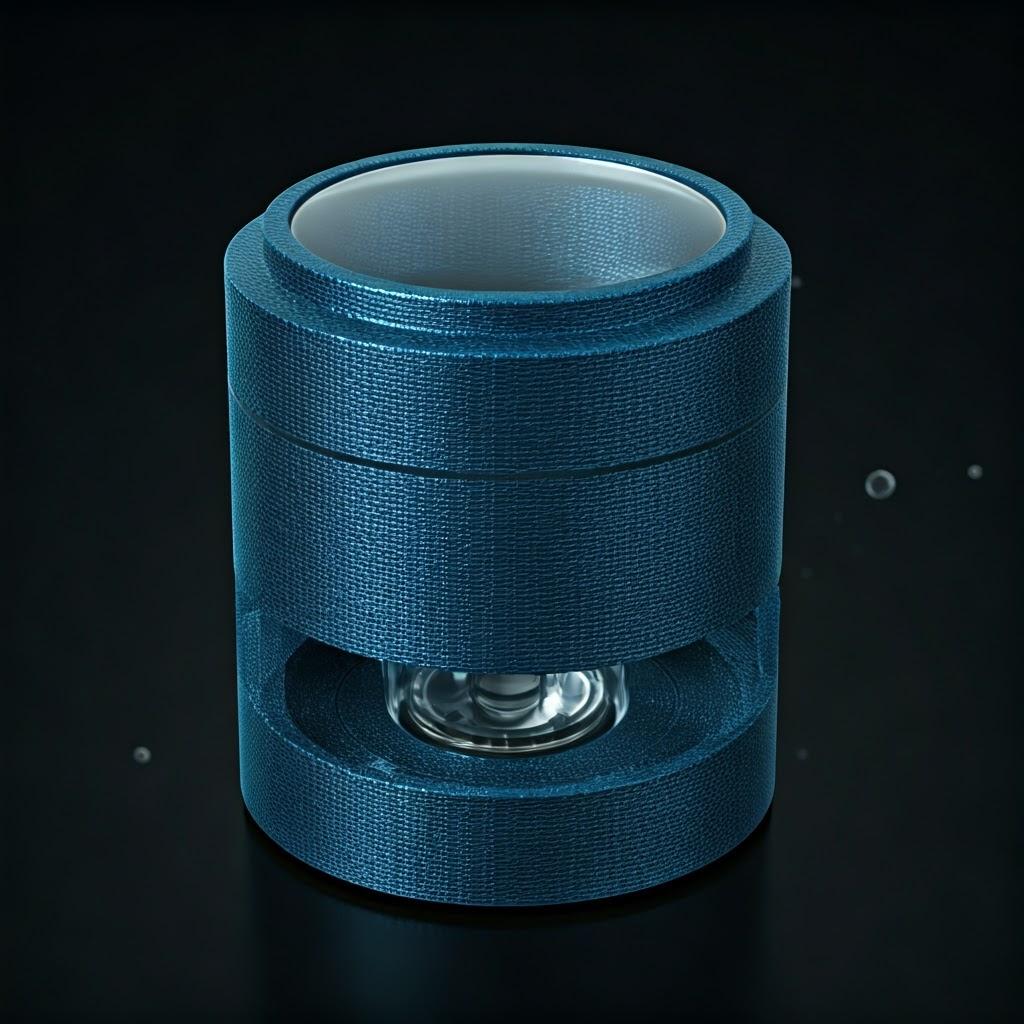
Why Choose Metal Additive Manufacturing for Corrosion-Resistant Enclosures?
While traditional manufacturing methods like CNC machining from billet, casting, or fabricating welded structures have served the marine industry for decades, they present inherent limitations, especially when dealing with the complex demands of modern underwater sensor enclosures. Procurement managers evaluating CNC machining alternatives or seeking optimized production pathways, and engineers striving for enhanced performance and design flexibility, are increasingly turning to Metal Additive Manufacturing (AM). The advantages offered by metal 3D printing technologies like L-PBF and EBM provide compelling reasons to adopt this approach, particularly when sourcing from an experienced additive manufacturing marine applications provider.
Let’s delve into the specific benefits of using metal AM for crafting these critical components:
- Oöverträffad designfrihet: This is arguably the most significant advantage. Traditional methods are often constrained by tool access, draft angles (casting), or the complexity of welding intricate shapes. AM builds parts layer by layer, freeing designers from many of these constraints.
- Komplexa geometrier: Create highly intricate internal and external features, optimized shapes for hydrodynamic performance, or internal channels for cooling or cable routing that would be impossible or prohibitively expensive to machine or cast.
- Integrated Features: Brackets, mounting points, connector bosses, and even internal structures can be designed directly into the enclosure body, eliminating the need for separate components and assembly steps.
- Conformal Cooling/Heating: For sensors generating heat or requiring temperature stability, internal channels conforming to the enclosure shape can be integrated for efficient thermal management.
- Materialeffektivitet och minskat avfall: Machining intricate enclosures from solid blocks of expensive marine-grade alloys (like Titanium or specific Copper-Nickel grades) generates significant material waste (swarf). Casting can also require large amounts of material for gates and risers.
- Near-Net Shape: AM processes typically use only the material needed for the part and necessary support structures, drastically reducing waste. This is a major cost advantage, especially for high-value materials often required for severe corrosion resistance. This efficiency is attractive for buyers looking for wholesale metal components where material cost is a primary driver.
- Snabb prototypframtagning och design-iteration: Developing and testing subsea equipment is notoriously expensive. AM allows for the rapid production of functional prototypes directly in the end-use metal.
- Faster Cycles: Designs can be quickly tested, modified based on results (e.g., pressure testing, fit checks), and reprinted in days rather than weeks or months, accelerating the development timeline for new sensor systems or custom solutions. This agility is a key benefit for rapid prototyping suppliers.
- Del Konsolidering: Complex assemblies often require multiple machined or fabricated components to be joined together using fasteners and seals. Each joint represents a potential leak path and adds assembly time and complexity.
- Monolithic Structures: AM enables the consolidation of multiple components into a single, printed part. This reduces part count, simplifies assembly, lowers weight, and significantly enhances reliability by minimizing potential leak paths – a critical factor for subsea integrity.
- On-Demand and Customized Production: AM is ideally suited for the low-to-medium volume production runs often associated with specialized underwater equipment.
- Flexibilitet: Easily produce custom variations of an enclosure design without the need for expensive tooling changes (molds or fixtures). This caters well to specific project requirements often encountered by custom enclosure manufacturers.
- Distributed Manufacturing: Potential for parts to be printed closer to the point of need, potentially reducing logistics complexity (though specialized marine applications often benefit from centralized expertise).
Addressing Specific Marine Challenges with AM:
- Pressure Resistance: AM allows for the creation of complex internal ribbing or lattice structures, optimized through topology analysis, to enhance stiffness and pressure resistance without significantly increasing weight. Walls can be designed with variable thickness, adding material only where structurally needed.
- Sealing Surfaces: While post-machining of critical sealing faces is often still required for the highest precision, AM allows for the design of optimized O-ring grooves and mating surfaces directly within the print, minimizing subsequent machining effort.
In summary, metal AM is not just an alternative manufacturing method; it’s an enabling technology. It empowers engineers to design better, more reliable, and more integrated underwater sensor enclosures while offering procurement managers potential benefits in terms of speed, customization, material efficiency, and overall system reliability. Choosing a partner with deep expertise in both additive manufacturing and the demands of the marine environment is key to unlocking these advantages.
Material Focus: 316L Stainless Steel and CuNi30Mn1Fe for Marine Durability
Selecting the right material is absolutely fundamental to the success and longevity of any underwater sensor enclosure. The chosen alloy must withstand the specific corrosive conditions, pressures, and potential biological activity of its intended operating environment. While various materials can be used, metal additive manufacturing particularly excels with high-performance alloys that might be challenging or costly to process traditionally. For many marine applications, two standout candidates available as high-quality powders suitable for AM are 316L rostfritt stål och Copper-Nickel alloys like CuNi30Mn1Fe. Sourcing these materials from a reputable metal 3D printing powder manufacturer like Met3dp, known for its advanced powder production technologies, ensures the optimal characteristics needed for demanding prints.
Let’s examine these two primary options in detail:
1. 316L Stainless Steel (UNS S31603)
- Översikt: 316L is an austenitic chromium-nickel stainless steel containing molybdenum. The “L” designation signifies low carbon content (typically <0.03%), which improves weldability and reduces the risk of sensitization (precipitation of chromium carbides at grain boundaries) during thermal cycles like welding or stress relief, thereby maintaining corrosion resistance. It’s one of the most widely used marine grade stainless steels.
- Viktiga egenskaper:
- Utmärkt korrosionsbeständighet: Offers very good resistance to general corrosion, pitting, and crevice corrosion in typical seawater environments, thanks primarily to its chromium and molybdenum content. It forms a passive chromium oxide layer that protects the underlying metal.
- Good Strength and Ductility: Provides a good balance of mechanical strength and toughness suitable for many enclosure applications.
- Svetsbarhet: The low carbon content makes it readily weldable, although AM processes inherently fuse material layer by layer.
- Availability and Cost-Effectiveness: Generally more available and less expensive than more exotic alloys like Titanium or high-nickel alloys.
- Icke-magnetisk: Typically non-magnetic in the annealed condition, which can be important for applications involving sensitive magnetic sensors.
- Marina tillämpningar: Widely used for enclosures, housings, fasteners, and structural components in moderate marine conditions, including coastal waters, shipboard equipment, and some subsea applications where conditions are not excessively aggressive (e.g., moderate depths, oxygenated waters).
- Begränsningar: While good, its resistance isn’t absolute. In highly corrosive conditions (e.g., stagnant, low-oxygen seawater, high chloride concentrations, elevated temperatures, or environments with specific pollutants), 316L can still be susceptible to severe pitting and crevice corrosion over long deployment periods. It also offers minimal resistance to biofouling.
- AM Considerations: 316L powder is well-characterized and widely available for L-PBF and other AM processes, allowing for the production of dense, high-strength parts with properties comparable to wrought 316L when processed correctly.
Table: 316L Stainless Steel Properties (Typical for AM)
Fastighet | Typical Value Range (Post-Stress Relief) | Enhet | Significance for Enclosures |
---|---|---|---|
Täthet | 7.9 – 8.0 | g/cm³ | Affects overall weight, buoyancy calculations. |
Yield Strength (Rp0.2) | 450 – 550 | MPa | Resistance to permanent deformation under pressure. |
Slutlig draghållfasthet | 550 – 650 | MPa | Maximum stress before fracture. |
Töjning vid brott | 35 – 50 | % | Ductility, resistance to brittle fracture. |
Hårdhet | ~180 – 220 | HV | Resistance to scratching and wear. |
Motståndskraft mot korrosion | Good in general seawater; PREN ~23-28 | – | Resistance to pitting/crevice corrosion (higher PREN better). |
Biofouling Resistance | Dålig | – | Surfaces will likely be colonized by marine organisms. |
Export to Sheets
(Note: Specific properties depend heavily on AM process parameters, build orientation, and post-processing heat treatments. Values are indicative.)
2. Copper-Nickel Alloy: CuNi30Mn1Fe (UNS C71500, often referred to as 90/10 or 70/30 Cupronickel – this specific one is closer to 70/30)
- Översikt: Copper-Nickel alloys are renowned for their exceptional resistance to seawater corrosion and, critically, their inherent resistance to biofouling. The CuNi30Mn1Fe alloy (roughly 70% Copper, 30% Nickel, with additions of Manganese and Iron) offers a superior level of performance in demanding marine environments compared to stainless steels. Procurement managers looking for long-term reliability in challenging waters often specify copper-nickel alloy suppliers.
- Viktiga egenskaper:
- Superior Seawater Corrosion Resistance: Exhibits extremely low general corrosion rates in seawater and excellent resistance to pitting and crevice corrosion, even in polluted or stagnant conditions. It’s particularly resistant to chloride stress corrosion cracking.
- Excellent Biofouling Resistance: Copper ions that slowly leach from the surface are toxic to many marine organisms, significantly inhibiting the settlement of barnacles, algae, and other fouling species. This reduces maintenance, maintains hydrodynamic efficiency, and prevents fouling-induced corrosion.
- Good Strength and Ductility: Offers moderate strength, sufficient for many enclosure designs, combined with good ductility.
- Good Thermal Conductivity: Higher thermal conductivity than stainless steel, which can be beneficial for heat dissipation.
- Weldability/Brazability: Generally considered weldable and brazable.
- Marina tillämpningar: Ideal for critical applications requiring long service life with minimal maintenance in aggressive seawater. Common uses include shipbuilding (piping systems, heat exchangers, hulls), desalination plants, offshore platform cladding and piping, and high-reliability enclosures for sensors deployed long-term, especially where biofouling is a major concern.
- Begränsningar: Generally lower strength and higher cost compared to 316L stainless steel. Its density is also higher. Material selection involves balancing corrosion/biofouling needs with mechanical requirements and budget.
- AM Considerations: While perhaps less common in AM than 316L, high-quality CuNi powders are available and printable. Achieving optimal density and properties requires careful parameter development, often leveraging the expertise of specialized AM providers and powder suppliers like Met3dp who work with advanced alloys. Sourcing CuNi seawater resistance materials in powder form is crucial for leveraging AM benefits.
Table: CuNi30Mn1Fe Properties (Typical for AM)
Fastighet | Typical Value Range (Annealed/Stress Relieved) | Enhet | Significance for Enclosures |
---|---|---|---|
Täthet | ~8.95 | g/cm³ | Higher weight compared to steel or titanium. |
Yield Strength (Rp0.2) | 200 – 350 | MPa | Lower than 316L, may require thicker sections for same pressure. |
Slutlig draghållfasthet | 400 – 550 | MPa | Adequate for many structural applications. |
Töjning vid brott | 30 – 45 | % | Good ductility. |
Hårdhet | ~100 – 150 | HV | Softer than stainless steel. |
Motståndskraft mot korrosion | Utmärkt i havsvatten | – | Superior to 316L in most marine conditions. |
Biofouling Resistance | Utmärkt | – | Significantly reduces marine growth attachment. |
Export to Sheets
(Note: Properties depend on specific composition, AM process, and post-treatment. Values are indicative.)
The Importance of Powder Quality
Regardless of the alloy chosen, the quality of the metal powder feedstock is critical for successful metal additive manufacturing. Key powder characteristics include:
- Sfäriskhet: Highly spherical particles flow better in the printer’s recoating mechanism, leading to uniform powder layers and reducing the risk of voids or defects.
- Fördelning av partikelstorlek (PSD): A controlled PSD ensures good packing density and predictable melting behavior.
- Renhet: Low levels of impurities and oxygen content are crucial for achieving the desired mechanical properties and corrosion resistance in the final part.
- Flytbarhet: Consistent powder flow ensures reliable deposition during the printing process.
Företag gillar Met3dp utilize industry-leading powder production technologies, such as Vacuum Induction Melting Gas Atomization (VIGA) och Process med roterande elektrod och plasma (PREP). These advanced methods produce high-purity, spherical metal powders with controlled particle sizes, optimized for demanding AM processes like Selective Electron Beam Melting (SEBM) and L-PBF. Sourcing high-quality pulver specifically designed for additive manufacturing is a crucial first step in producing reliable, high-performance underwater sensor enclosures.
Material Selection Criteria
Choosing between 316L and CuNi30Mn1Fe (or other potential alloys like Titanium or Duplex Stainless Steels, also printable) depends on a careful evaluation of the application:
- Corrosion Severity: How aggressive is the seawater environment (salinity, temperature, flow rate, pollutants)?
- Biofouling Risk: Is biofouling a significant concern for sensor function or long-term deployment?
- Required Strength & Pressure Rating: What are the mechanical load requirements?
- Deployment Duration: Is it a short-term or multi-year deployment?
- Budget: What is the allowable cost for the enclosure?
- Magnetic Signature: Are there restrictions on magnetic materials?
By carefully considering these factors and leveraging the capabilities of metal AM with high-quality materials like 316L and CuNi30Mn1Fe, engineers and procurement managers can specify and source underwater sensor enclosures offering unprecedented levels of performance and reliability for critical marine applications.
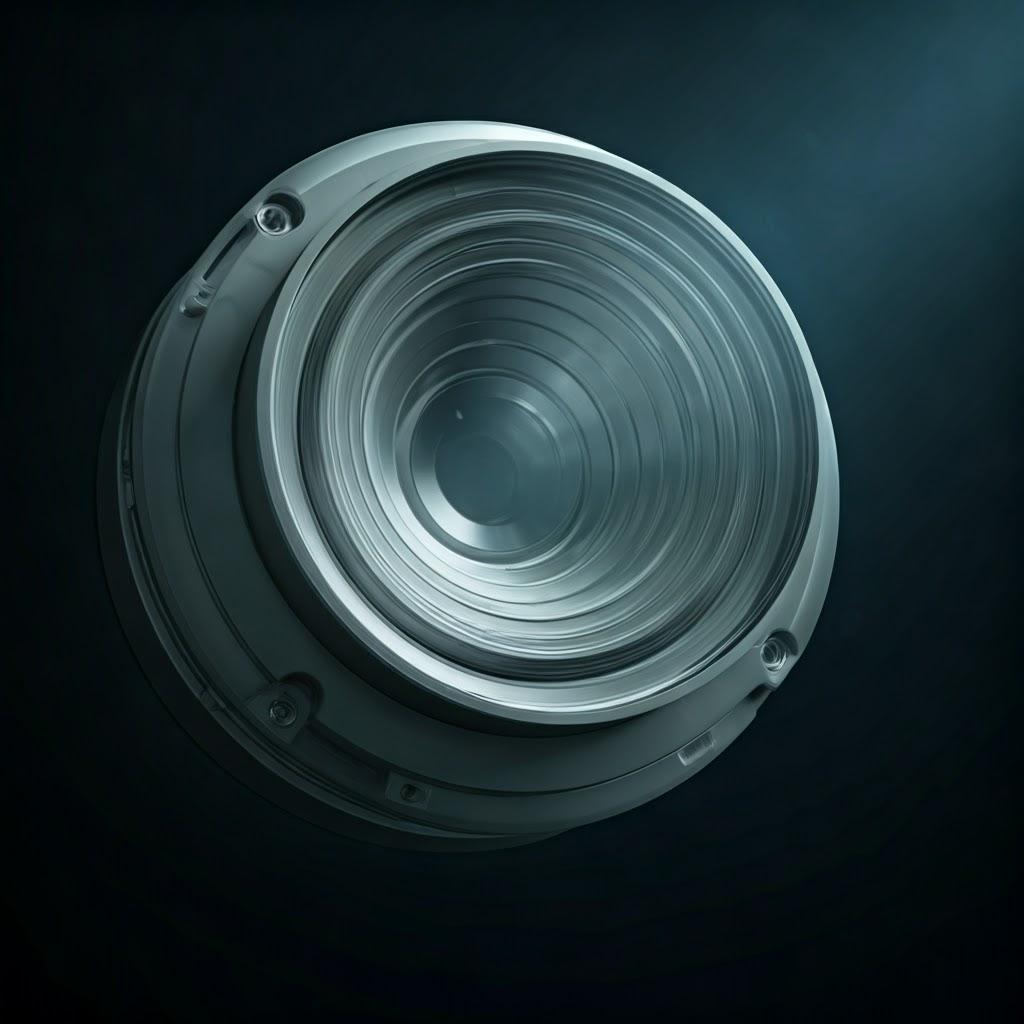
Design Optimization for 3D Printed Underwater Enclosures
One of the most profound impacts of adopting Metal Additive Manufacturing (AM) for underwater sensor enclosures lies in the newfound freedom it grants engineers during the design phase. Unlike traditional subtractive (machining) or formative (casting) processes, AM’s layer-by-layer approach enables the creation of highly complex and functionally integrated components. Harnessing this potential requires embracing Design för additiv tillverkning (DfAM) principles. Applying DfAM not only unlocks unique performance capabilities but also optimizes the part for efficient and reliable printing, ultimately leading to superior underwater housing design and performance. Engineers collaborating with an experienced engineering design services provider specializing in AM can leverage these principles to create truly innovative and robust solutions.
Here are key DfAM considerations specifically tailored for 3D printed underwater sensor enclosures:
- Funktionell integration: Move beyond thinking of the enclosure as just a passive shell. AM allows you to integrate features directly into the structure, reducing part count, assembly time, and potential leak paths.
- Internal Mounting Points: Design custom bosses, brackets, and threaded features directly into the enclosure walls to precisely locate and secure sensors, PCBs, batteries, and connectors without needing separate internal chassis or numerous fasteners.
- Cable Management: Incorporate internal channels or conduits within the enclosure walls or base to route cables cleanly and securely, protecting them from damage and reducing clutter. This is far easier than machining complex internal paths.
- Integrated Heat Sinks: For sensors or electronics generating significant heat, cooling fins or complex internal channel structures for liquid cooling can be printed directly as part of the enclosure body, ensuring efficient thermal management crucial for sensor accuracy and longevity.
- Flow Channels: If the sensor requires interaction with the external water (e.g., flow-through chemical sensors), precisely shaped internal channels with optimized flow paths can be integrated.
- Pressure Resistance Optimization: Designing for deep-sea pressure requires careful structural considerations. DfAM enables sophisticated approaches beyond simply increasing wall thickness.
- Variable Wall Thickness: Apply material strategically, thickening walls only in high-stress areas identified through Finite Element Analysis (FEA), while thinning them elsewhere to save weight and material cost.
- Internal Ribbing and Lattices: Incorporate complex internal rib patterns (isogrids, honeycombs) or internal lattice structures. These are incredibly weight-efficient ways to significantly increase stiffness and buckling resistance under external pressure, often impossible to achieve with conventional methods. Generative design tools can algorithmically create optimal structures based on load conditions.
- Shape Optimization: Move away from purely cylindrical or box shapes if hydrodynamics or pressure distribution favour smoother, more organic forms. AM excels at producing these complex curvatures.
- Sealing Strategies: Ensuring a watertight seal is paramount. While precision machining of sealing faces remains common (see Post-Processing section), DfAM can optimize the design for sealing efficiency.
- Optimized O-Ring Grooves: Design precise O-ring grooves with correct dimensions (width, depth, corner radii) directly into the print, minimizing the amount of post-machining required. Dovetail grooves can help retain O-rings during assembly.
- Mating Surface Design: Ensure mating surfaces are designed to be easily accessible for any necessary post-machining or lapping to achieve the required flatness for face seals. Consider features that aid alignment during assembly.
- Integrated Seal Features: Explore designs where sealing features (e.g., knife edges for specific gasket types) are incorporated directly into the AM part, potentially reducing reliance on traditional O-rings in some areas, though this requires careful validation.
- Support Structure Strategy: Most metal AM processes require support structures to anchor the part to the build plate, support overhanging features, and manage thermal stress. Effective DfAM minimizes the need for and complexity of these supports.
- Design for Self-Support: Orient the part on the build plate and adjust feature angles (typically aiming for angles >45° from the horizontal) to minimize the need for supports on critical or hard-to-reach surfaces.
- Minimize Internal Supports: Supports inside enclosed cavities are extremely difficult or impossible to remove. Design internal features to be self-supporting or provide access ports for support removal if unavoidable.
- Accessible Support Locations: Place necessary supports on non-critical surfaces where removal marks are acceptable or where they can be easily accessed and finished during post-processing. Avoid supports on sealing faces or complex external features if possible.
- Optimized Support Types: Utilize easily removable support structures (e.g., conical or thin-walled supports) where possible, reducing post-processing time and the risk of damaging the part during removal.
- Lightweighting (Topology Optimization & Generative Design): Especially critical for enclosures mounted on AUVs, ROVs, buoys, or other weight-sensitive platforms.
- Topology Optimization: Use software tools to remove material from low-stress areas while maintaining structural integrity under defined load cases (like external pressure), resulting in organic-looking, highly efficient structures.
- Generative Design: Define functional requirements, loads, constraints, and material properties, and let algorithms generate multiple optimized design solutions that meet the criteria, often producing innovative, lightweight concepts unachievable through traditional design intuition. This creates highly efficient lightweight marine components.
- Part Orientation: The orientation of the part on the build platform affects surface finish, the need for supports, dimensional accuracy (due to anisotropic shrinkage), and potentially mechanical properties. Consider orientation early in the design process. Critical features often benefit from being oriented away from supports or in directions known to yield better accuracy or surface finish for the chosen AM process.
By thoughtfully applying these DfAM principles, engineers can move beyond simply replicating traditionally designed enclosures with AM. They can create next-generation subsea equipment enclosures that are lighter, stronger, more functionally integrated, and potentially more reliable than their predecessors. Collaborating with an AM service provider like Met3dp, which possesses deep DfAM expertise alongside advanced printing capabilities, is invaluable for maximizing the benefits of this transformative manufacturing approach for demanding marine component manufacturer behov.
Achieving Precision: Tolerance and Surface Finish in Metal AM Enclosures
While metal additive manufacturing offers incredible design freedom, potential buyers, especially procurement managers and engineers accustomed to the tight tolerances of CNC machining, often have questions about the achievable precision. Understanding the typical tolerances, dimensional accuracy, and surface finish characteristics of metal AM processes is crucial for setting realistic expectations and designing parts appropriately, particularly for components like underwater sensor enclosures where sealing and fit are critical. Partnering with a precision manufacturing supplier experienced in AM ensures these aspects are well-managed.
Tolerances and Dimensional Accuracy:
The precision achievable with metal AM depends on several factors, including the specific process used (e.g., L-PBF, EBM), the machine calibration, the material being printed, the part’s size and geometry, its orientation on the build plate, and the effectiveness of thermal management during the build.
- Typical As-Built Tolerances: As a general guideline, for well-calibrated industrial metal AM systems printing parts like sensor enclosures, typical achievable tolerances might be in the range of:
- L-PBF (Laser Powder Bed Fusion): Often cited around pm0.1 mm to pm0.2 mm for smaller dimensions (e.g., < 100 mm), potentially increasing slightly for larger dimensions (e.g., pm0.1 to pm0.2 of the dimension). Finer features might achieve tighter tolerances locally.
- EBM (Electron Beam Melting): Traditionally considered slightly less accurate than L-PBF for fine features due to the larger beam spot size and higher process temperatures, EBM tolerances might be closer to pm0.2 mm to pm0.4 mm or pm0.3 to pm0.5 of the dimension. However, modern EBM systems are continuously improving accuracy. Met3dp’s focus on SEBM printers pushes the boundaries of what EBM can achieve in terms of precision.
- Factors Influencing Accuracy:
- Thermal Stress & Warpage: The repeated heating and cooling cycles inherent in AM can cause internal stresses, potentially leading to warping or distortion, especially in large or complex parts. Careful process parameter control, support strategies, and post-build stress relief are essential to minimize this.
- Shrinkage: Metal powders shrink upon solidification and cooling. This is compensated for in the machine software, but complex geometries can experience non-uniform shrinkage.
- Bygg orientering: Accuracy can vary slightly between the X, Y, and Z axes due to the layer-wise building process and thermal gradients.
- Machine Calibration: Regular calibration of the laser/electron beam positioning system, powder recoating mechanism, and thermal environment is crucial.
Surface Finish (Roughness):
The as-built surface finish of metal AM parts is inherently rougher than machined surfaces due to the partially melted powder particles adhering to the surface and the layer stepping effect.
- Typical As-Built Surface Roughness (R_a):
- L-PBF: Typically ranges from R_a6 $\mu$m to R_a15 $\mu$m, depending on the material, parameters, and surface orientation (upward-facing surfaces are generally smoother than downward-facing or side walls).
- EBM: Generally produces rougher surfaces than L-PBF, often in the range of R_a20 $\mu$m to R_a35 $\mu$m, due to larger powder particles and higher melt pool energy.
- Significance for Enclosures:
- Sealing: As-built AM surfaces are usually too rough to provide a reliable seal with standard O-rings or face gaskets. Critical sealing surfaces must typically be post-machined or otherwise finished to achieve the required smoothness (often R_a1.6 $\mu$m or better, depending on the seal type).
- Hydrodynamics: Rough surfaces increase hydrodynamic drag, which can be a concern for towed bodies or AUV/ROV components. Post-processing (like polishing) may be needed if smooth flow is critical.
- Fatigue Life: Surface roughness can act as initiation points for fatigue cracks. While less critical for enclosures primarily under static pressure, it’s a consideration for components experiencing cyclic loading.
- Cleaning/Biofouling: Rougher surfaces can be harder to clean and may provide more attachment points for biofouling organisms, although material choice (like CuNi) is the dominant factor for biofouling resistance.
The Role of Post-Machining:
Given the typical tolerances and surface finish limitations of the as-built AM process, post-machining is often an essential step for achieving the required precision on critical features of underwater sensor enclosures.
- Critical Features Requiring Machining:
- Sealing Faces: O-ring grooves, face seal surfaces.
- Mounting Points: Surfaces requiring precise flatness or location for attachment to other structures.
- Threaded Holes: While threads can sometimes be printed, machining often provides better quality, accuracy, and strength.
- Connector Interfaces: Ensuring precise dimensions for mating connectors.
- Bearing/Shaft Interfaces: If the enclosure incorporates moving parts.
Achieving Precision with Met3dp:
Achieving high levels of accuracy and predictable surface finishes requires not only advanced equipment but also deep process knowledge. Met3dp leverages industry-leading printers, known for their accuracy and reliability, combined with extensive expertise in optimizing tryckmetoder and parameters for materials like 316L and specialized alloys. While post-machining is often planned for critical interfaces, Met3dp’s process control aims to minimize the amount of machining required by producing parts with high as-built accuracy and consistency. Collaboration between the design team and the AM provider is key to defining achievable metal 3D printing tolerances and planning necessary finishing steps to meet the stringent dimensional accuracy AM requirements of subsea applications.
Table: Precision Considerations for AM Enclosures
Feature/Parameter | Typical As-Built AM Range | Target Requirement (Example) | Mitigation / Approach |
---|---|---|---|
General Tolerance | pm0.1 to pm0.5 mm / % | pm0.1 mm | Process optimization, potential post-machining. |
Sealing Surface (R_a) | 6 – 35 $\mu$m | < 1.6 $\mu$m | Mandatory post-machining, lapping, or polishing. |
Flatness (Seal Face) | Can vary due to warp | < 0.05 mm | Post-machining. |
Hole Diameter | pm0.1 to pm0.3 mm | pm0.05 mm (H7 fit) | Post-machining (reaming/boring). |
Thread Quality | Often imperfect | Standard thread class | Post-machining (tapping/thread milling). |
Internal Cavity R_a | 6 – 35 $\mu$m (difficult to finish) | Application dependent | DfAM to minimize internal complexity, accept as-built Ra. |
Export to Sheets
By understanding these nuances and incorporating necessary finishing steps into the manufacturing plan, engineers and procurement managers can confidently utilize metal AM to produce highly precise and reliable underwater sensor enclosures.

Essential Post-Processing Steps for Marine-Grade Enclosures
Producing a metal part via additive manufacturing is rarely the end of the story, especially for demanding applications like marine-grade underwater sensor enclosures. The as-built part, fresh off the printer, typically requires several efterbearbetning steps to achieve the final desired dimensions, mechanical properties, surface characteristics, and ultimately, ensure its fitness for purpose in the harsh subsea environment. These steps are integral to the manufacturing workflow and must be planned and budgeted for by engineers and procurement teams when sourcing components from a metal AM service bureau. Failure to properly execute these steps can compromise the integrity and performance of the enclosure.
Here’s a breakdown of common and essential post-processing requirements for 3D printed metal enclosures destined for underwater use:
- Stress Relief / Heat Treatment:
- Why it’s Crucial: The rapid heating and cooling cycles inherent in L-PBF and EBM processes create significant internal stresses within the printed part. These residual stresses can lead to distortion (especially after removal from the build plate), reduced fatigue life, and potentially cracking over time or under load.
- Process: Parts are typically heat-treated in a controlled atmosphere furnace (e.g., vacuum or inert gas like Argon) at temperatures below the alloy’s critical transformation points. This allows the internal stresses to relax without significantly altering the microstructure or bulk mechanical properties (though specific cycles can also be used for annealing, solutionizing, or aging to modify properties if needed).
- Necessity: Stress relief is almost always mandatory for dimensionally critical and load-bearing metal AM parts, including pressure vessels like sensor enclosures. It ensures stability during subsequent machining and in service. Experienced heat treatment services providers understand the specific cycles needed for different AM alloys.
- Borttagning av stödstruktur:
- Why it’s Crucial: Support structures are necessary during the build but must be removed afterward.
- Process: This can range from simple manual breaking or cutting (for well-designed supports) to more involved machining (milling, grinding, wire EDM) for supports in intricate or hard-to-reach areas. Care must be taken not to damage the part surface during removal.
- Överväganden: DfAM plays a huge role here (as discussed previously) in minimizing the quantity and difficulty of support removal. Residual marks or ‘witness marks’ where supports were attached may require additional finishing.
- Machining (CNC Milling/Turning):
- Why it’s Crucial: As highlighted in the previous section, as-built AM tolerances and surface finishes are often insufficient for critical features. Machining brings specific areas of the part into required specifications.
- Process: Using CNC mills or lathes, precise features are machined onto the AM part. Common operations include:
- Facing: Creating flat, smooth surfaces for seals.
- Boring/Reaming: Achieving precise hole diameters and roundness for connectors or bearings.
- Tapping/Thread Milling: Creating accurate threads.
- Grooving: Machining precise O-ring grooves to final dimensions.
- Profiling: Ensuring accurate external dimensions or mating features.
- Necessity: Essential for sealing surfaces, critical mounting points, and any feature requiring tolerances tighter than the as-built AM process can achieve. Sourcing from an AM provider with integrated CNC machining supplier capabilities simplifies the workflow.
- Ytbehandling:
- Why it’s Crucial: Improves aesthetics, removes residual powder, enhances cleanability, can improve fatigue life, and prepares the surface for coatings.
- Processes:
- Abrasive Blasting (Sandblasting/Bead Blasting): Provides a uniform matte finish, removes loose powder, and can slightly improve fatigue resistance through compressive stress. Various media (grit, beads) produce different finishes.
- Tumbling/Vibratory Finishing: Uses abrasive media in a rotating or vibrating bowl to deburr edges and provide a smoother, more uniform finish, especially on smaller parts.
- Polering: Mechanical or electrochemical polishing can achieve very smooth, mirror-like finishes ($R\_a \< 0.8$ $\mu$m or even lower) if required for specific sealing types, hydrodynamic performance, or aesthetics.
- Passivation (for Stainless Steels): A chemical treatment (typically using nitric or citric acid) that removes free iron from the surface and enhances the natural chromium oxide passive layer, significantly boosting the corrosion resistance of alloys like 316L. Essential for maximizing the lifespan of passivation stainless steel components in seawater.
- Necessity: Some level of surface finishing (e.g., blasting) is common. Polishing and passivation are application-specific.
- Cleaning:
- Why it’s Crucial: Removes residual powder, machining fluids, fingerprints, and other contaminants before final assembly or coating.
- Process: Typically involves ultrasonic cleaning baths with appropriate detergents, followed by rinsing and drying.
- Necessity: Always required before final inspection and assembly.
- Coating & Painting:
- Why it’s Crucial: Provides an additional layer of protection against corrosion or biofouling, especially for alloys like 316L in aggressive environments or for very long deployments. Can also provide specific colors or surface properties.
- Processes:
- Epoxy Coatings: Common for general corrosion protection in marine environments.
- Anti-fouling Paints: Specifically designed to deter marine growth (often containing biocides like copper compounds – less necessary if using CuNi alloys).
- Specialized Polymer Coatings: Can offer chemical resistance or specific dielectric properties.
- Necessity: Dependent on the base material’s properties, the severity of the environment, and the required deployment life. Often specified for marine coatings applikationer.
- Inspection and Testing:
- Why it’s Crucial: Validates the part meets all specifications before deployment.
- Processes:
- Dimensionell inspektion: Using CMMs (Coordinate Measuring Machines), scanners, or traditional metrology tools to verify tolerances.
- Icke-förstörande testning (NDT): Techniques like CT scanning (Computed Tomography) or X-ray can inspect internal integrity for voids or defects. Dye penetrant or magnetic particle testing can check for surface cracks.
- Pressure Testing (Hydrostatic Testing): Essential for validating the leak-tightness and structural integrity of pressure vessels like sensor enclosures. Parts are typically subjected to pressures exceeding their operational rating (e.g., 1.5x) in a controlled environment. Hydrostatic pressure testing is a critical step for any subsea enclosure.
- Necessity: Comprehensive inspection and pressure testing are mandatory for ensuring reliability and safety in subsea applications, forming a key part of quality control manufacturing.
Integrated Workflow:
Ideally, the chosen metal AM service provider should have capabilities or strong partnerships to manage this entire post-processing chain. This ensures seamless transitions between steps, maintains accountability, and simplifies the procurement process. Met3dp, with its focus on providing comprehensive solutions, understands the importance of these downstream processes in delivering finished, deployment-ready components. Planning for these steps from the outset is critical for accurate cost estimation and realistic lead time projections.
Overcoming Manufacturing Challenges: Ensuring Leak-Proof and Reliable Enclosures
While metal additive manufacturing offers numerous advantages, like any advanced manufacturing process, it is not without potential challenges. Producing high-integrity, leak-proof, and reliable underwater sensor enclosures requires careful control over the entire process, from design and material handling to printing and post-processing. Understanding potential metal 3D printing defects and how experienced providers mitigate them is crucial for engineers and procurement managers aiming to leverage AM successfully. Partnering with a reliable component supplier like Met3dp, which emphasizes process control and additive manufacturing quality assurance, is key to navigating these challenges.
Here are some common challenges in metal AM and the strategies used to overcome them, ensuring the production of robust marine enclosures:
- Porositet: This refers to small voids or pores within the printed metal. It’s a primary concern as porosity can reduce mechanical strength, fatigue life, and potentially create leak paths in pressure-containing components.
- Typer:
- Gas Porosity: Caused by gas trapped within the powder feedstock or dissolved in the melt pool during printing, which forms bubbles upon solidification.
- Lack-of-Fusion Porosity: Irregularly shaped voids caused by insufficient melting and fusion between adjacent melt tracks or successive layers.
- Mitigation Strategies:
- High-Quality Powder: Using powders with low internal gas content and controlled sphericity/PSD (like those produced via Met3dp’s advanced atomization) minimizes trapped gas. Proper powder handling and storage are also vital to prevent moisture pickup.
- Optimized Print Parameters: Extensive process development is required to determine the optimal laser/electron beam power, scan speed, layer thickness, and hatch spacing to ensure complete melting and fusion for a specific alloy and machine. This is a core expertise area for experienced AM providers.
- Process Monitoring: In-situ monitoring tools (e.g., melt pool monitoring) can detect anomalies during the build that might lead to porosity.
- Het isostatisk pressning (HIP): A post-processing step where the part is subjected to high temperature and high inert gas pressure. This can effectively close internal voids (both gas and lack-of-fusion porosity), significantly improving density and mechanical properties. Often used for critical applications.
- Typer:
- Residual Stress and Warpage: As mentioned earlier, thermal stresses are inherent in the process. If not managed, they can cause significant warpage, distortion, or even cracking.
- Mitigation Strategies:
- Optimized Scan Strategies: Using specific scan patterns (e.g., island scanning, alternating hatch directions) helps distribute heat more evenly.
- Preheating (Build Plate/Chamber): EBM processes inherently use high preheating, reducing thermal gradients. L-PBF systems often utilize build plate heating.
- Robust Support Structures: Supports anchor the part and help conduct heat away, reducing stress buildup and preventing distortion during the build.
- Simulation: Thermal simulation tools can predict stress buildup and warpage, allowing for design or process adjustments (e.g., modifying geometry, optimizing orientation, planning supports) before printing.
- Stress Relief Heat Treatment: Essential post-processing step to relax residual stresses.
- Mitigation Strategies:
- Cracking: Can occur during printing or subsequent cooling/heat treatment, particularly in alloys susceptible to hot cracking or those with high residual stress.
- Mitigation Strategies:
- Alloy Selection: Some alloys are inherently more prone to cracking during AM than others.
- Parameter Optimization: Fine-tuning energy input and cooling rates can reduce susceptibility.
- Stress Management: Effective support strategies and prompt stress relief are crucial.
- Preheating: Reducing thermal gradients minimizes cracking risk.
- Mitigation Strategies:
- Surface Finish Issues: Beyond the inherent roughness, issues like dross formation (oxides on the melt pool) or “stair-stepping” on low-angle surfaces can occur.
- Mitigation Strategies:
- Atmosphere Control: Maintaining a high-purity inert gas atmosphere (L-PBF) or high vacuum (EBM) minimizes oxidation.
- Parameter Tuning: Adjusting parameters can influence melt pool stability and surface tension effects.
- Orientation and Design: Orienting critical surfaces optimally and avoiding very shallow angles can minimize stair-stepping.
- Efterbearbetning: Surface finishing techniques (blasting, polishing) address as-built roughness.
- Mitigation Strategies:
- Dimensional Inaccuracy: Deviations from the intended geometry outside of expected tolerances.
- Mitigation Strategies:
- Machine Calibration: Regular and precise calibration is fundamental.
- Shrinkage Compensation: Accurate scaling factors applied in the slicing software.
- Termisk hantering: Consistent preheating and process control.
- Stressavlastning: Performing stress relief before final machining prevents distortion during material removal.
- Iterative Improvement: For highly complex parts, initial prints might inform minor adjustments to the CAD model or process parameters to dial in accuracy.
- Mitigation Strategies:
- Material Quality Control: Ensuring the powder feedstock meets specifications and is handled correctly.
- Mitigation Strategies:
- Powder Certification: Sourcing powder from reputable manufacturers like Met3dp with batch traceability and quality certifications.
- Incoming Inspection: Verifying powder characteristics (PSD, morphology, chemistry).
- Proper Handling & Storage: Using controlled environments to prevent contamination and moisture absorption. Powder recycling protocols must maintain quality.
- Mitigation Strategies:
Ensuring Reliability through Process Control and NDT:
Overcoming these challenges hinges on rigorous process control and validation. Experienced AM providers implement robust quality management systems (e.g., ISO 9001). Furthermore, Icke-förstörande provning (NDT) plays a vital role in verifying the internal and external integrity of critical components like pressure enclosures.
- Common NDT Methods:
- Computed Tomography (CT) Scanning: Provides a 3D view of the part’s internal structure, capable of detecting and characterizing porosity, inclusions, or internal cracks. Highly effective but can be costly.
- Radiography (X-ray): A 2D imaging technique useful for detecting larger voids or inclusions.
- Dye Penetrant Testing (DPT): Detects surface-breaking cracks or porosity.
- Ultrasonic Testing (UT): Can detect subsurface flaws but can be challenging on complex AM geometries and rough surfaces.
By combining meticulous process control, advanced monitoring, appropriate post-processing (including HIP where necessary), and thorough NDT validation, manufacturers like Met3dp can consistently produce high-reliability, leak-proof metal AM underwater sensor enclosures that meet the stringent demands of the marine industry, providing confidence to engineers and procurement professionals seeking dependable NDT services and manufacturing partners.
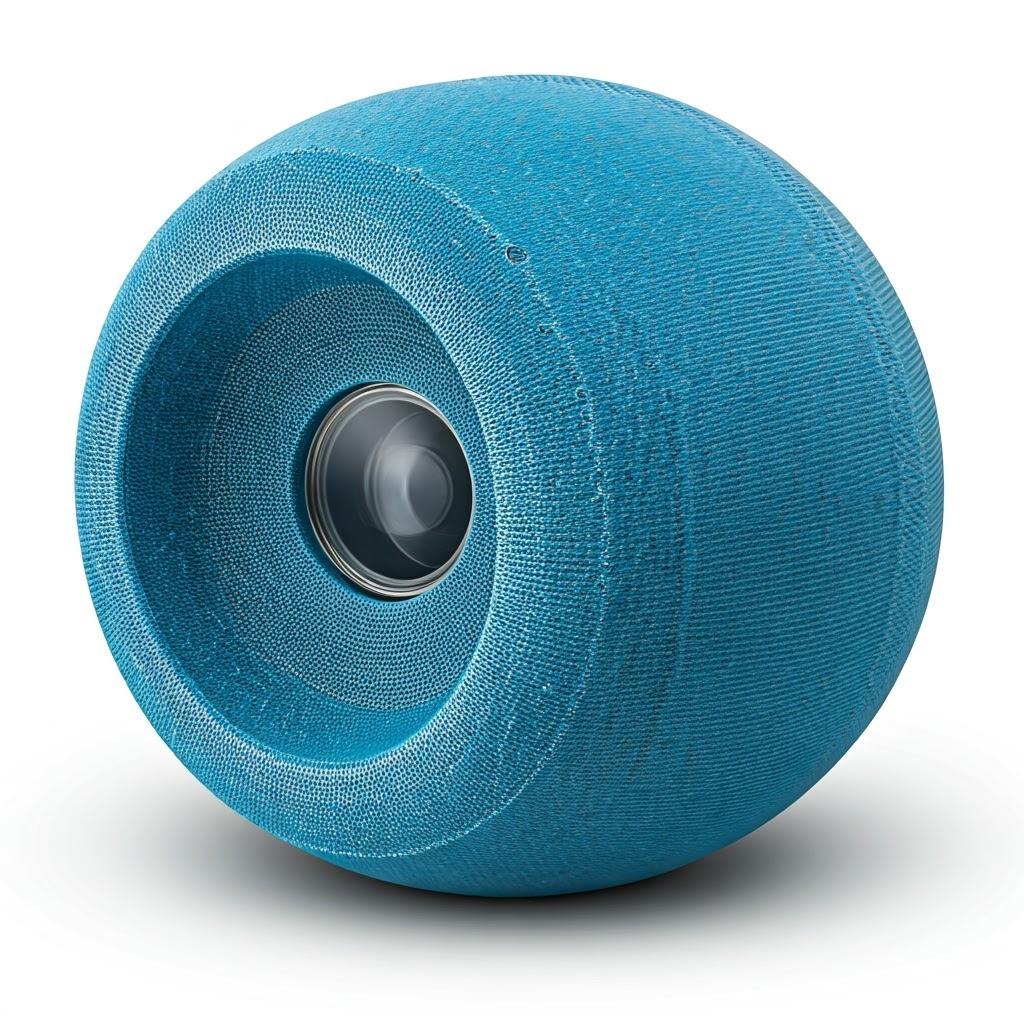
Selecting Your Metal 3D Printing Partner: Key Considerations for Underwater Applications
Choosing the right manufacturing partner is a critical decision in any project, but it takes on heightened importance when dealing with specialized components like underwater sensor enclosures produced via metal additive manufacturing. The success of your project—achieving the required performance, reliability, budget, and timeline—hinges on the capabilities, expertise, and quality systems of your chosen metal AM service bureau. For procurement managers navigating the complexities of sourcing advanced manufacturing services and engineers seeking a collaborator who truly understands the nuances of both AM and marine environments, a structured evaluation process is essential when choosing a 3D printing supplier.
Here are key considerations specifically tailored for selecting a partner for manufacturing marine-grade, corrosion-resistant enclosures:
- Expertise with Marine-Grade Materials: This is non-negotiable. Your potential partner must demonstrate significant experience and proven success in printing with the specific alloys required for your application, such as 316L Stainless Steel, Copper-Nickel alloys (like CuNi30Mn1Fe), Titanium grades, or Duplex/Super Duplex stainless steels.
- Questions to Ask:
- Which marine-relevant alloys do you regularly process?
- Can you provide case studies or examples of similar subsea components you have manufactured?
- What are your established, optimized parameters for these specific alloys?
- Do you have experience managing the specific challenges associated with these materials (e.g., oxidation sensitivity, cracking susceptibility)?
- Why it Matters: Each alloy behaves differently in AM processes. A partner with deep material science knowledge related to marine applications will understand how to optimize parameters for density, microstructure, mechanical properties, and crucially, corrosion resistance.
- Questions to Ask:
- Proven Track Record and Relevant Experience: Look beyond general AM capabilities. Seek evidence of successful projects specifically within the marine, subsea, or offshore sectors.
- Questions to Ask:
- Can you share examples of pressure vessels, sensor housings, or other critical underwater components you have produced?
- Are you familiar with common marine industry standards or certifications (even if not strictly required for your part, familiarity indicates understanding)?
- Do your engineers understand the challenges of designing for hydrostatic pressure, sealing, and corrosion?
- Why it Matters: A partner familiar with the operational environment and typical failure modes of subsea equipment is better equipped to provide valuable DfAM input and ensure the manufacturing process addresses critical requirements. They understand why certain features or quality attributes are essential.
- Questions to Ask:
- Technology and Equipment Assessment: The partner’s available technology must align with your project’s needs in terms of material compatibility, required precision, build volume, and overall quality.
- Key Aspects:
- AM Technology: Do they offer the most suitable process (e.g., L-PBF for fine features and finish, EBM for certain materials like Titanium or for reduced residual stress)? Met3dp’s focus on advanced systems like SEBM provides specific advantages for certain applications.
- Machine Quality & Maintenance: Are their printers industrial-grade, well-maintained, and regularly calibrated?
- Byggvolym: Can their machines accommodate the size of your enclosure?
- Pulverhantering: Do they have robust procedures for powder quality control, storage, and handling to prevent contamination?
- Why it Matters: The quality and suitability of the equipment directly impact the quality, consistency, and reliability of the final part. Access to industry-leading print volume, accuracy, and reliability, as offered by Met3dp, is a significant advantage.
- Key Aspects:
- Comprehensive Post-Processing Capabilities: As discussed extensively, post-processing is integral. An ideal partner should offer a wide range of in-house capabilities or have tightly managed relationships with qualified subcontractors.
- Capabilities to Verify: Stress relief/heat treatment, CNC machining (milling, turning), surface finishing (blasting, polishing), passivation, cleaning, coating services, NDT, and pressure testing.
- Questions to Ask:
- Which post-processing steps do you perform in-house? Which are subcontracted?
- How do you manage quality control for subcontracted processes?
- Can you handle the specific finishing tolerances and surface requirements for our sealing interfaces?
- Do you offer hydrostatic pressure testing services? To what pressure levels?
- Why it Matters: A partner offering a turnkey solution from print to finished, tested part significantly simplifies the supply chain, reduces lead times, and ensures better accountability throughout the process. Managing multiple vendors for different steps increases complexity and risk for the procurement team.
- Quality Management Systems and Certifications: Robust quality control is paramount for critical components. Look for formal quality management systems and relevant certifications.
- Key Indicators:
- ISO 9001 Certification: Demonstrates a commitment to standardized quality management processes.
- Material Certifications: Ability to provide full traceability and material certificates for the powder batches used.
- Process Documentation: Well-defined procedures for printing, post-processing, and inspection.
- Inspection Capabilities: Availability of appropriate metrology equipment (CMMs, scanners) and NDT methods.
- Why it Matters: Certifications and documented processes provide assurance that the supplier can consistently meet specifications and quality requirements. This is crucial for risk management and ensuring the reliability of the final marine component manufacturer.
- Key Indicators:
- Engineering and Design Support (DfAM Expertise): The ideal partner acts as more than just a print service; they should be a collaborator offering valuable design feedback.
- Services to Look For:
- DfAM Consultation: Reviewing your design and suggesting modifications to improve printability, reduce cost, enhance performance, or minimize post-processing.
- Simulation Capabilities: Offering thermal or structural simulation to predict performance and optimize the design or print strategy.
- Problem Solving: Ability to work with your engineers to overcome design or manufacturing challenges.
- Why it Matters: Leveraging the supplier’s DfAM expertise can significantly improve the final product and avoid costly redesigns or manufacturing failures. This collaborative approach is a hallmark of leading additiv tillverkningslösningar providers.
- Services to Look For:
- Capacity, Lead Times, and Scalability: Ensure the supplier can meet your project timelines and potential future volume requirements.
- Questions to Ask:
- What is your current capacity and typical lead time for parts of this size and complexity?
- How do you manage scheduling and prioritize orders?
- Can you handle prototype quantities as well as potential small-to-medium series production or wholesale 3D printing services?
- Why it Matters: Unreliable lead times can derail project schedules. Understanding capacity ensures the supplier won’t become a bottleneck, especially if bulkorder are anticipated.
- Questions to Ask:
- Communication, Responsiveness, and Project Management: Effective communication is vital throughout the quoting, manufacturing, and delivery process.
- Indicators:
- Clear Quoting Process: Transparent and detailed quotes outlining all costs and steps.
- Dedicated Point of Contact: A project manager or engineer assigned to your project.
- Proactive Updates: Regular communication on project status.
- Responsiveness: Timely answers to technical queries and administrative requests.
- Why it Matters: Good communication prevents misunderstandings, allows for quick resolution of issues, and provides confidence to procurement managers overseeing the project.
- Indicators:
Evaluating Potential Partners:
- Request for Quotation (RFQ): Provide a detailed RFQ package including CAD models, technical drawings specifying critical dimensions and tolerances, material requirements, post-processing needs, and required quantity.
- Technical Discussions: Engage in technical discussions to gauge their understanding of your application and their proposed manufacturing approach.
- Site Visits/Audits: If feasible, visiting the supplier’s facility provides firsthand insight into their operations, equipment, and quality culture.
- References/Case Studies: Ask for references from customers with similar applications.
Selecting a partner like Met3dp, which emphasizes its position as a leading provider of comprehensive additive manufacturing solutions—spanning advanced SEBM printers, high-performance metallpulver, application development services, and decades of collective expertise—aligns well with these critical selection criteria. Exploring their capabilities and company philosophy on their Om oss page can provide valuable insights into their suitability as a strategic partner for demanding underwater applications. Making an informed choice based on these factors is the foundation for successfully leveraging metal AM for your corrosion-resistant sensor enclosures.
Understanding Cost Drivers and Lead Times for Wholesale & Custom Orders
One of the most frequent questions from engineers and procurement managers considering metal additive manufacturing pertains to cost and turnaround time. While AM offers significant advantages, understanding the factors that influence pricing and typical lead times is crucial for accurate project budgeting, planning, and comparing AM to traditional methods. Whether requesting quotes for single prototypes or exploring wholesale pricing for 3D printing, several key elements determine the final numbers. Obtaining a reliable custom metal parts quote requires understanding these drivers.
Major Cost Factors in Metal AM:
The cost of a 3D printed metal enclosure is a composite of several contributing factors:
- Material Type and Volume: This is often a primary cost driver.
- Cost per Kilogram: High-performance marine-grade alloys (e.g., Titanium, certain Copper-Nickels, Duplex steels) are inherently more expensive powder feedstocks than more common materials like 316L stainless steel. The market price of the raw metals fluctuates.
- Part Volume & Weight: The actual amount of material consumed directly impacts cost. Larger, denser parts naturally cost more. DfAM techniques like topology optimization can significantly reduce volume and thus material cost.
- Support Structure Volume: The material used for support structures also contributes to the cost, reinforcing the importance of DfAM to minimize supports.
- Print Time (Machine Occupancy): Industrial metal AM machines represent a significant capital investment, and their operating time is valuable.
- Part Height (Z-Height): Print time is heavily influenced by the number of layers required, meaning taller parts generally take longer to print, irrespective of their volume footprint on each layer.
- Part Volume & Complexity: While height is often dominant, the actual volume scanned by the laser/electron beam per layer also affects time. Very complex geometries with extensive scanning paths per layer can increase print time compared to simpler solid blocks of the same height.
- Machine Occupancy Rate: Suppliers factor in the hourly cost of operating the machine (including energy, gas consumption, maintenance, labor, depreciation). Efficient packing of multiple parts onto a single build plate can help amortize setup costs and improve machine utilization, often leading to lower per-part costs for bulkorder.
- Design Complexity and Features: While AM enables complexity, certain features impact cost.
- Support Requirements: Designs needing extensive or difficult-to-remove support structures increase both print time (for the supports themselves) and post-processing labor costs.
- Fine Features: Extremely small or intricate details might require slower scanning speeds or specific parameters, potentially increasing print time slightly.
- Väggens tjocklek: Very thin walls can sometimes pose printing challenges, requiring careful parameter tuning.
- Post-Processing Intensity: This can be a substantial portion of the total cost, sometimes exceeding the print cost itself for parts requiring extensive finishing.
- Support Removal Labor: Manual or complex support removal takes time.
- Värmebehandling: Furnace time and energy consumption add cost.
- CNC Machining: The amount of setup and machining time required for critical tolerances and surfaces is a major factor. More features requiring machining equate to higher costs.
- Ytbehandling: Blasting is relatively standard, but extensive polishing or specialized coatings add significant cost.
- Inspection & Testing: Dimensional inspection (especially CMM), NDT (like CT scanning), and pressure testing require specialized equipment and skilled labor, adding to the cost.
- Order Quantity (Volume): Economies of scale apply to AM, although perhaps differently than traditional mass production methods like casting or injection molding.
- Setup Costs Amortization: Non-recurring engineering (NRE) costs for build preparation and machine setup are spread over more parts in larger batches, reducing the per-part cost.
- Bulk Material Purchasing: Suppliers may get better pricing on larger powder orders.
- Optimized Build Plates: Printing multiple copies of a part (or multiple different parts) on a single build plate optimizes machine usage. This is key for achieving competitive wholesale pricing 3D printing.
- Learning Curve: For repeat orders, efficiencies may be gained in printing and post-processing.
- Leipa ma Tomai: Skilled engineers and technicians are required for DfAM, print preparation, machine operation, post-processing, and quality control. This expertise contributes to the overall cost but is essential for quality.
Table: Key Cost Drivers & Influences
Cost Driver | Primary Influence | How to Mitigate/Optimize |
---|---|---|
Material | Alloy Type (Cost/kg), Part Volume, Support Volume | Select cost-appropriate material, Use DfAM/Topology Optimization, Minimize Supports |
Print Time | Part Height (Z), Part Volume/Complexity, Machine Rate | Optimize orientation for minimum height, Efficient build plate packing (multi-part builds) |
Designens komplexitet | Support Needs, Feature Density | DfAM for self-support, Simplify non-critical features where possible |
Efterbearbetning | Machining Needs, Finishing Specs, Testing Req. | DfAM to minimize machining, Specify only necessary finishing, Realistic tolerances |
Beställning Antal | Setup Amortization, Build Plate Utilization | Order in batches vs. single pieces where feasible, Consolidate multiple part needs |
Arbetskraft & Expertis | Engineering, Operation, Finishing, QA Time | Partner with efficient, experienced provider; Clear specifications reduce rework |
Export to Sheets
Lead Time Breakdown:
The total lead time for a metal AM enclosure, from order placement to delivery, involves several stages:
- Design Review & Print Preparation (1-5 days): Final design checks, DfAM review (if applicable), support structure generation, build file slicing, and build plate layout planning.
- Queue Time (Variable): Depending on the supplier’s machine availability and backlog, there might be a waiting period before the print starts. This can range from days to weeks.
- Printing (1-7+ days): The actual time the part spends printing in the machine. Highly dependent on Z-height and volume. Complex or tall enclosures can take several days to print continuously.
- Cooling & Depowdering (0.5-2 days): Allowing the build plate and parts to cool down sufficiently before removal from the machine, followed by careful removal of bulk unfused powder.
- Post-Processing (3-15+ days): This is often the longest and most variable part of the timeline. It includes:
- Stress Relief / Heat Treatment (typically 1-2 days including furnace time and cooling).
- Support Removal (can range from hours to days depending on complexity).
- Machining (highly variable, depends on features, can take several days if complex setups are needed).
- Surface Finishing, Passivation, Coating (adds days depending on the process).
- Inspection and Testing (can add 1-3 days, depending on extent).
- Shipping (1-5+ days): Transit time to the customer’s location.
Total Estimated Lead Time: For a typical custom underwater sensor enclosure requiring significant post-processing, total lead times often range from 3 to 8 weeks. This can be shorter for simpler parts or rush orders (at increased cost) and potentially longer for very complex parts, large orders requiring multiple builds, or during periods of high demand at the supplier.
Obtaining Quotes:
When requesting a metal 3D printing cost estimation, provide as much detail as possible:
- 3D CAD model (STEP format preferred).
- 2D drawings indicating critical dimensions, tolerances, GD&T, threads, and sealing surfaces.
- Material specification (e.g., 316L, CuNi30Mn1Fe).
- Required post-processing (heat treatment, machining details, surface finish Ra, passivation, coating type).
- Testing requirements (e.g., pressure test level and duration).
- Required quantity (for prototype, small batch, or grossist- inquiries).
- Desired lead time.
Clear and complete information allows the AM provider to generate an accurate quote and realistic lead time estimate, facilitating effective procurement additive manufacturing planning.
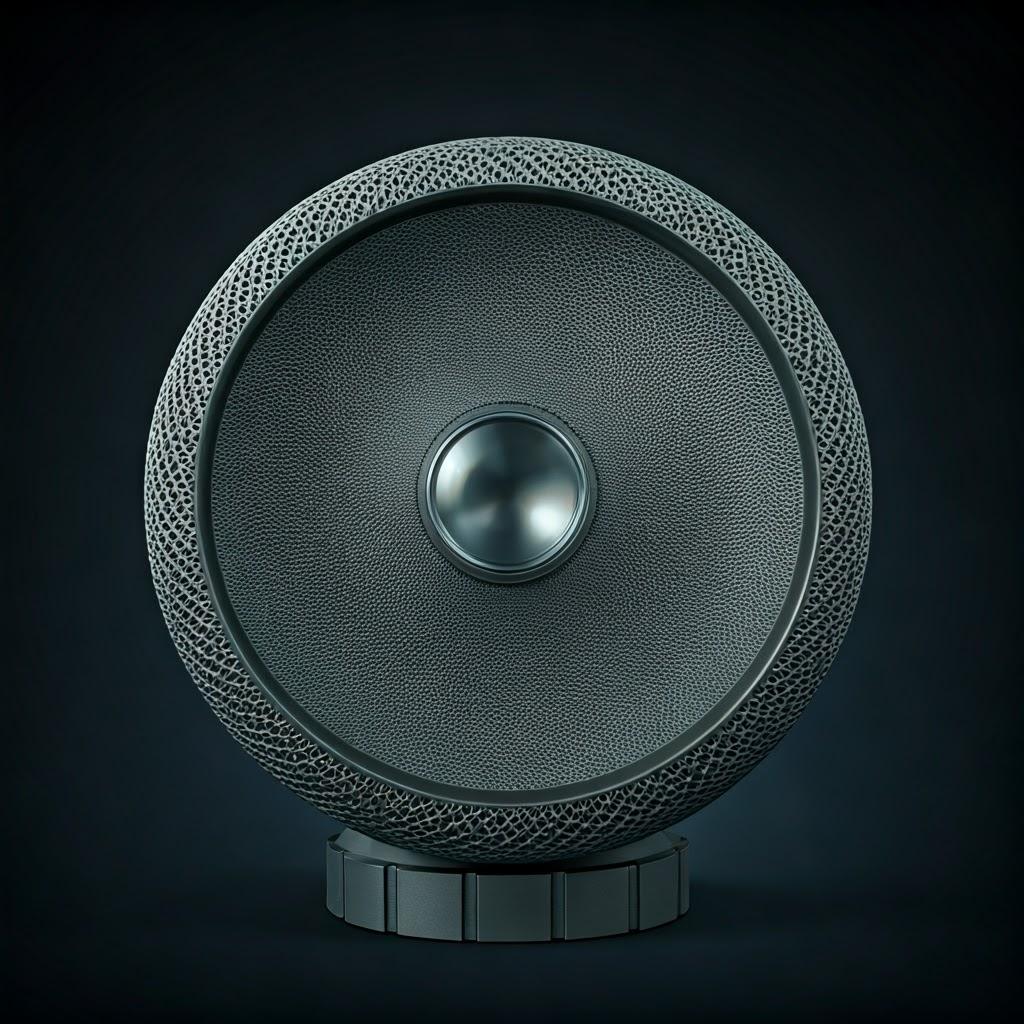
Frequently Asked Questions (FAQ) about 3D Printed Underwater Enclosures
Here are answers to some common questions engineers and procurement managers have when considering metal additive manufacturing for underwater sensor housings:
- Q1: What pressure depths can 3D printed metal enclosures realistically withstand?
- A1: The pressure rating is primarily determined by the enclosure’s design (geometry, wall thickness, features like ribs), the chosen material’s strength (Yield Strength), and the quality of manufacturing (ensuring full density and absence of critical defects). Metal AM parts made from alloys like 316L, Titanium, or high-strength steels, when properly designed and manufactured (including stress relief and potential HIPing), can readily meet requirements for deep-sea applications, often exceeding depths of several thousand meters (capable of handling hundreds of bar or thousands of psi). The design must be validated through Finite Element Analysis (FEA) and confirmed with hydrostatic pressure testing to a factor of safety above the operational depth rating (e.g., 1.5x working pressure). There is no inherent depth limitation imposed by the AM process itself compared to wrought materials, provided the design and material are appropriate.
- Q2: How does the corrosion resistance of 3D printed 316L or CuNi compare to traditional wrought or cast materials?
- A2: When produced using optimized parameters and high-quality powder, metal AM parts can achieve near-full density (>99.5%, often >99.9% with HIP). In this state, the intrinsic corrosion resistance of alloys like 316L or CuNi30Mn1Fe is generally considered comparable to their wrought or cast counterparts. However, factors like surface finish and post-processing are critical. An as-built AM surface, being rougher, might initially exhibit slightly different behavior or be more prone to crevice formation if not properly finished. Proper post-processing, especially passivation for stainless steels, is essential to ensure the passive layer forms correctly and provides the expected level of protection. For CuNi alloys, the inherent biofouling and corrosion resistance derived from the copper content are effectively realized in dense AM parts. Partnering with an experienced provider ensures processes are optimized to maximize corrosion performance.
- Q3: Are 3D printed metal enclosures suitable for long-term deployment (e.g., multiple years) in harsh marine environments?
- A3: Yes, absolutely. Provided the material selection is appropriate for the specific environment (considering factors like seawater chemistry, temperature, flow, potential pollutants, and biofouling severity), the enclosure is designed correctly for the pressure and mechanical loads, and it undergoes proper manufacturing and post-processing (including stress relief, potential HIP, passivation/coatings where needed, and rigorous quality control/testing), 3D printed metal enclosures can offer excellent long-term reliability. The advantages of AM, such as part consolidation (reducing leak paths) and optimized geometries, can even enhance long-term performance compared to some traditional multi-part assemblies. The longevity will depend on the material choice (e.g., CuNi or Titanium generally offer better long-term resistance in harsh conditions than 316L) and the quality of the entire design and manufacturing process. Many AM components are already successfully deployed in long-term subsea applications.
- Q4: Can complex internal features like sensor mounts or integrated channels be reliably produced and are they accessible for cleaning/inspection?
- A4: Metal AM excels at creating complex internal features that are difficult or impossible with traditional methods. Integrated sensor mounts, cable channels, or even cooling passages can be designed directly into the enclosure. However, DfAM is crucial here. Internal features must generally be self-supporting during the build or designed such that any necessary internal supports can be removed via access ports. Completely enclosed internal cavities are difficult to finish and inspect internally after printing. Trapped powder removal from complex internal channels requires careful design and cleaning procedures (e.g., airflow, flushing). While visual inspection of deep internal features is limited, NDT methods like CT scanning can verify the integrity of internal structures if required for critical applications.
- Q5: What quality certifications are most relevant when sourcing marine-grade 3D printed parts?
- A5: While specific project requirements may dictate adherence to certain marine standards (e.g., DNV GL, ABS for specific offshore structures or systems), general quality assurance is often demonstrated through internationally recognized standards. ISO 9001 certification is fundamental, indicating a robust quality management system is in place at the supplier. For industries like aerospace or medical, more stringent certifications (AS9100, ISO 13485) exist, demonstrating higher levels of process control and traceability, which can be beneficial even if not strictly required for all marine parts. Material certifications confirming the powder batch chemistry and traceability are also essential. Evidence of successful hydrostatic pressure testing protocols and NDT capabilities further builds confidence in the supplier’s ability to deliver reliable marine components.
Conclusion: The Future of Marine Sensing with Advanced Metal AM Enclosures
The demanding realm of underwater exploration, monitoring, and operations presents unique challenges for equipment design and manufacturing. Underwater sensor enclosures, the vital shields protecting sensitive instruments from extreme pressure, corrosive seawater, and biological fouling, demand the utmost reliability and performance. As we’ve explored throughout this discussion, Metal Additive Manufacturing has emerged not just as a viable alternative but often as a superior method for producing these critical components.
Metal AM fundamentally changes the equation for designing and manufacturing high-performance enclosures. The ability to:
- Create complex, optimized geometries through DfAM, integrating features and reducing part count.
- Utilize advanced marine-grade materials like 316L and Copper-Nickel alloys efficiently, minimizing waste.
- Achieve part consolidation, inherently reducing potential leak paths and enhancing structural integrity.
- Enable rapid prototyping and design iteration, accelerating development cycles for new sensor systems.
- Produce customized or low-volume parts cost-effectively without dedicated tooling.
These advantages directly address the core challenges of subsea engineering, allowing for the creation of enclosures that are potentially lighter, stronger, more reliable, and more functionally capable than those produced by traditional means. From enhancing the durability of seabed monitoring equipment to enabling more compact and efficient designs for AUV/ROV sensor payloads, the impact of AM is tangible across the marine sector.
However, realizing the full potential of metal AM requires careful consideration of material selection, adherence to DfAM principles, meticulous process control to overcome manufacturing challenges like porosity and residual stress, comprehensive post-processing to achieve required tolerances and finishes, and rigorous quality assurance, including NDT and pressure testing.
Critically, success hinges on partnering with the right manufacturing expert. Selecting a supplier requires evaluating their specific expertise with marine materials, their technological capabilities, their commitment to quality (evidenced by certifications and robust processes), their proficiency in post-processing, and their ability to provide collaborative engineering support.
As a leader in metal AM, Met3dp stands at forefront of this technological advancement. With a foundation built on decades of collective expertise, Met3dp provides comprehensive solutions encompassing cutting-edge SEBM printers, advanced powder manufacturing capabilities delivering high-quality spherical metal powders (including TiNi, TiTa, TiAl, TiNbZr, CoCrMo, stainless steels like 316L, superalloys, and potentially CuNi grades), and dedicated application development services. Our commitment to industry-leading print volume, accuracy, and reliability makes us an ideal partner for organizations seeking to implement 3D printing for mission-critical parts in aerospace, medical, automotive, and demanding marine applications. We partner with organizations to accelerate their digital manufacturing transformations.
The future of marine sensing and exploration is inextricably linked with advancements in manufacturing technology. Metal additive manufacturing offers a powerful pathway to creating the next generation of robust, intelligent, and highly integrated subsea systems. By embracing AM and collaborating with knowledgeable partners, engineers and procurement managers can unlock new levels of performance and reliability for their underwater sensor enclosures, pushing the boundaries of what’s possible beneath the waves.
Ready to explore how metal additive manufacturing can enhance your underwater applications? Contact Met3dp today to discuss your project requirements and discover how our cutting-edge systems and advanced metal powders can power your organization’s additive manufacturing goals.
Dela på
MET3DP Technology Co, LTD är en ledande leverantör av lösningar för additiv tillverkning med huvudkontor i Qingdao, Kina. Vårt företag är specialiserat på 3D-utskriftsutrustning och högpresterande metallpulver för industriella tillämpningar.
Förfrågan för att få bästa pris och anpassad lösning för ditt företag!
Relaterade artiklar
Om Met3DP
Senaste uppdateringen
Vår produkt
KONTAKTA OSS
Har du några frågor? Skicka oss meddelande nu! Vi kommer att betjäna din begäran med ett helt team efter att ha fått ditt meddelande.
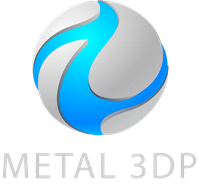
Metallpulver för 3D-printing och additiv tillverkning